可编程气缸(伺服气缸)报警处理办法
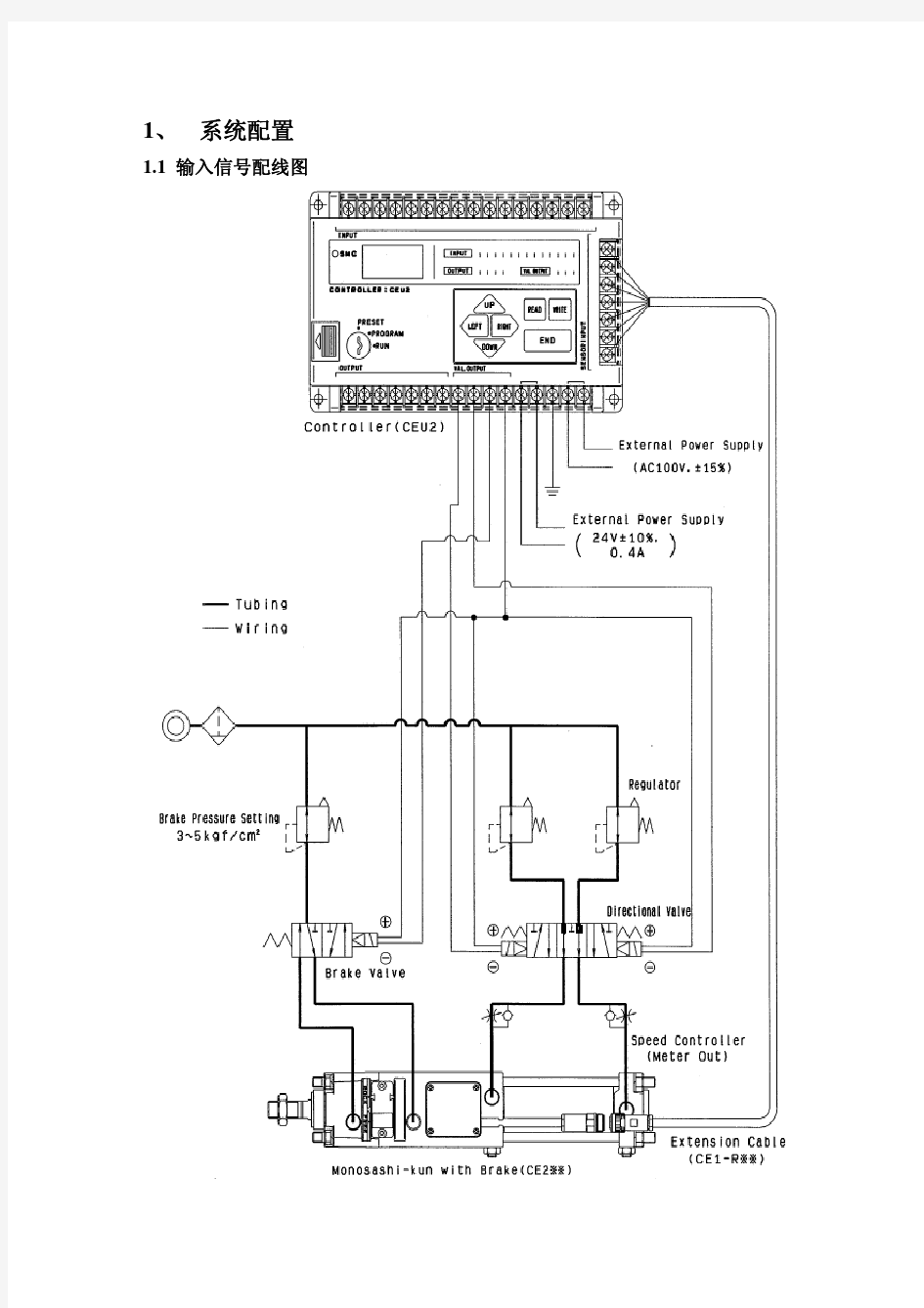
相关主题
- 1、下载文档前请自行甄别文档内容的完整性,平台不提供额外的编辑、内容补充、找答案等附加服务。
- 2、"仅部分预览"的文档,不可在线预览部分如存在完整性等问题,可反馈申请退款(可完整预览的文档不适用该条件!)。
- 3、如文档侵犯您的权益,请联系客服反馈,我们会尽快为您处理(人工客服工作时间:9:00-18:30)。
1、 系统配置
1.1 输入信号配线图
1.2 推荐气动回路
2、 输入信号配线
2.1 输入信号配线内容
外部复位 手动阀 2 手动阀 1 设原点 程序选择 4 程序选择 3 程序选择 2 程序选择 1 紧急停止 临时停止 自动/手动 回原点 启动
屏蔽
外部电源 外部电源
Dip 开关 1、 原点确认 2、 制动设置 3、 计数方向切换 4、 存储清零
外部复位——输入该信号 50ms 以上,系统复位。在异常报警发生时,输入复位 信号解除报警。 2.3 输入部分接线 输入信号包括 13 种。接+24V 电源输入,+5V 通过光电耦合器被绝缘。 信号名称:启动、回原点、手动/自动,临时停止,紧急停止,程序选择 1,程 序选择 2,程序选择 3,程序选择 4,设原点,手动 1,手动 2,外部复位。 输入部分内部电路图如下:
负载(kg)÷ 缸径(cm)× r2 ×π × 使用压力(kgf/cm2) 4
例如:缸径:40mm 负载:20kg(允许动态负载值) 使用压力:5kgf/cm2 则负载率= 20kg ÷ 4 × 4×π × 5 = 31.8 = 30% (四舍五入)
4 P6——制动次数 P7——原点确认时间——设定原点检测时间(t1),
通过端子 13 来重启电源。当还原为初始状态后,将该状态设置回 OFF。
4、驱动
4.1 原点方向的设定 带制动的行程可读气缸的位置检测方式是增量式,请设定原点和机械基准面相
其中,0——输入端子 6~9 和 COM 端开路 1——输入端子 6~9 和 COM 端短路
设原点——当 dip 开关 NO.1 设置为 ON 时,可输入原点信号。当 dip 开关 NO.1 设置为 OFF 时,输入的磁性开关信号不能被识别。 手动 1/手动 2——在手动模式下使用,输入该信号,活塞杆前进或后退。
按 WRITE 键切换到下一设置。屏幕将显示 PRG STEP P2 和当前误差值设定。同时, 第一个小数位将开始闪烁。 接着,再如果 P1 的设置方法一样,完成对 预定误差值的设置。最大的行程误差值是 9.99mm。
举例: 如果输入误差值是 1.0,那么,任何落在设 定值±1.0 将被认为定位成功。如果落在此 范围外,将执行再试凑功能来落到允许的 范围内。 如果在执行完最大的再试凑功能后,仍不 能落到允许的范围内,将显示定位异常报 警信号(Err9)。
许的误差范围内为止。 P3——再试凑——输入再试凑的次数。最大的是 9 次。在设定的次数内,仍不能
落在定位精度公差的场合下,会发生 Err9(定位异常)且系统 停止工作,因此建议最好把再试凑次数设为 9 次。 P4——缸径——输入使用气缸的缸径。 P5——负载率——输入负载率(相对于气缸推力的负载率),计算公式如下:
设定值将如下改变:
注意:CE2 缸径的设定范围从φ40 到φ100mm。 按 WRITE 键切换到下一个设置。屏幕 上显示 PRG STEP P5 和正在闪烁的当 前负载率。接着,选择负载率。
闪烁 没没有有闪闪烁烁
设定值将如下改变:
按 WRITE 切换到下一个设置,屏幕上 显示 PRG STEP P6 和当前制动次数。 显示值表示制动组件的使用次数已可 被读出。1 单位代表 10.000,该值不可 被设置。 注意:当该值达到 300.0 时,需更换制 动组件。
3.2 程序设定 输入预定的气缸停止位置。
3.2.1 输入方法 将控制器模式切换开关置于 PROGRAM 位置。 注意:各程序的 STEP 0 对应的是 END。 程序数 1 开始闪烁。 按 UP 和 DOWN 键设定程序数。
闪烁
闪烁
闪烁
如下:
闪烁 输入例
上述设定完,按 WRITE 键结束操作。STEP “0”开始闪烁。接着,按 READ 或 WRITE 键继续下面的布置。
用≥10mA 电流作为输入信号。
2.4 输出部分配线 输出信号包括 4 种。+5V 在光电耦合器上被绝缘。 信号名称:测位置、测原点、程序结束、异常报警。 最大端子电压:DC +30V 最大电流:50mA(0°~50°C) 输出部分内部电路图如下:
2.5 电磁阀配线 电磁阀驱动输出信号有 3 种。+5V 在光电耦合器上被绝缘。 信号名称:制动、驱动 A、驱动 B。 最大端子电压:+24V DC 最大电流:80mA(0°~50°C) 电磁阀输出部分内部电路如下:
(10ms 为一个单位,最大是 9.99s) 当输入回原点信号,在 t1 时间内传感器没有收到任何 信号(气缸停止状态)的场合,回原点确认到位。 设定响应时间的时候应考虑到负载、安装条件、气管 长度等。如果使用条件改变,应重新校准响应时间。 当控制器 dip 开关 NO.1 状态为 ON,且磁性开关为 ON 时,回原点确认到位。 P8——Err12(操作错误)确认时间,t2。 输入 Err12 确认时间。 10ms 为一个单位,最大是 9.99s。 输入启动信号后,在时间范围内,如果没有传感器没有任何反馈信号(气 缸停止)将发生 Err12 报警。
测时间。接着,输入预定的操作错误检
测时间。设定值范围为 0~9.99s(1 单
位是 10ms)。设定该值时,请考虑气缸
的使用条件。
当完成了上述所有的设定时,按
WRITE 键结束整个的 PRESET 数据预
闪烁
设置操作。
3.1.2 确认设定数据 将控制器模式切换开关置于 PRESET 位置。 当 P1 闪烁时,用 UP 和 DOWN 键来 闪烁 确认每个预设值正确与否。当输入值 闪烁时,按 READ 键一次可切换操作 闪烁 到 P1。
将控制器模式切换开关置于 PROGRAM 位置。 按 WRITE 两次。显示“End”将被替 换为“0000.0”,进入到 STEP 1 输入。
闪烁
按 LEFT 键两次。第一小数位的“0”开始 闪烁。
闪烁
按 UP 键 5 次就可设定值为 5。
闪烁 闪烁
按 WRITE 键 1 次。按 LEFT 键 3 次来改 变光标闪烁的位置。
显示“End”将被“0000.0”代替,进入到 STEP 1 的输入状态。输入第一个预定位置 到 STEP 1。
接着,按 WRITE 键进入到 STEP 2 的设置。 一步一步的输入预定位置。 当将最后一个值输入到最后一步时,按 WRITE 键结束该程序的设定。 注意:当没有输入 END 时,操作时控制器 将显示 Err7 错误。 当完成上述的输入步骤后,输入程序显示
闪烁 闪烁
按 WRITE 键切换到下一个设置。屏幕 将显示 PRG STEP P3 和最大再试凑次 数。接着,输入预定的最大再试凑次数。 最大可设定值是 9。在初次调整中,执 行预测控制。因此,建议最大再试凑次 数至少 5 次。
按 WRITE 键切换到下一个设置。屏幕 将显示 PRG STEP P4 和正在闪烁的当 前气缸缸径。接着,选择缸径。
按 WRITE 键 1 次。 按 UP 键 5 次来设置值“5”。
按 LEFT 键 2 次。按 UP 键 3 次来设置值 “3”。
按 WRITE 键进入到 program 8 的最后一 步即 STEP 3 的设置。 按 END 键开始 program 8 的程序设置。
program 8 的程序设定结束。
按 UP 键 3 次可设定值为 3。
闪烁
按 WRITE 键 1 次。按 LEFT 键 2 次来改变 光标闪烁的位置。
闪烁
按 UP 键 3 次可设定值为 3。
闪烁
闪烁
闪烁
按 WRITE 键 1 次进入到 program 1 的最后 一步即 STEP 4 的设置。按 END 键结束 program 1 的设置。
3.1.2 数据设定 将控制器模式切换开关置于 PRESET 位置。
闪烁
P1 将开始闪烁。
闪烁 闪烁
闪烁
按 READ 或 WRITE 键切换到气缸行程的设 定。第一个小数位将闪烁。 用 LEFT 和 RIGHT 键来选择要更改的数据位 置,用 UP 和 DOWN 键来设置预定的参数。
闪烁 参考
误差允许值 设定值
程序结束 测原点信号 异常/报警 测位置信号
2.2 输入信号内容 启动——一旦启动,开始按预置数据作动。每触发一次(需持续 50ms 以上)走 一步动作。 注意:仅当先执行回原点命令,且原点信号被反馈到控制器后,启动信号(需持 续 50ms 以上)才被接收,气缸按照设定程序作动。 回原点——活塞杆回原点后,输入持续 50ms 以上的信号。 自动/手动模式——当端子和 COM 端断路状态下,自动模式开启。反之,短路状 态下,手动模式开启。 自动模式——输入启动信号后,将一步步按设定作动。 手动模式——将手动 1(端子 11)或手动 2(端子 12)与 COM 端短路,来控制 气缸的前进或后退。但动作的方向依配管和接线而异。 临时停止——定位过程中,输入此命令将停止作动。当此命令取消,从临时停止 位置开始继续定位动作。 注意:如临时停止点距离设定点不足 5mm 时,会出现 Err5(操作异常)报警。 紧急停止——定位过程中,此命令会强迫动作立即停止。输入该信号后,会出现 Err10 报警。 注意:紧急停止后,必须执行回原点命令。 程序选择 1,2,3,4——选择程序参照下表(二进制):
2.6 顺序器 由于控制器和顺序器之间的配线问题,在程序内设定脉冲宽度 50ms 不能保证输 出脉冲宽度也是同样的值。因此,为了获得在控制器侧测得的脉冲宽度≥50ms, 应设定相应的脉冲宽度。
3、数据设定
3.1 数据预设 3.1.1 数据设定的种类及内容 P1——气缸行程——输入使用气缸的行程。 P2——定位精度公差——输入定位的允许误差范围。再试凑功能可确保定位到允
NO.2——制动系统的设置 OFF——在该状态下,ON 意味着制动可用。OFF 意味着处于自由状态。 如果控制器断电,将处于自由状态。 如果气缸水平安装,没达到气平衡时,突然断电的情况下,气缸将继续伸出或者 缩回。 如果气缸垂直安装,突然断电的情况下,活塞杆将因自身的重量而落回到底部。 ON——在该状态下,OFF 意味着制动可用。ON 意味着处于自由状态。 如果控制器突然断电,制动锁将处于爬行状态。 注意:请注意配管的问题,这可能导致以上相反的设定。
NO.3——计数方向的切换
OFF——伸出方向将作为计数增大的方向。
缩回端
伸出
原点将设置在缩回端。
伸出端
原点设置在伸出端。
缩回
注意:请注意接线的问题,这可能导致以上相
反的设定。
NO.4——存储清零:清除输入数据,还原为初始设定值 通常,设定该状态为 OFF。如果输入数据要求清零,设定该状态为 ON。接着,
3.2.2 输入数据的确认 将控制器模式切换开关置于 PROGRAM 位置。
闪烁
当 PRG “1”开始闪烁时,用 UP 和 DOWN 键
来选择预定的程序来检验。其次,按 READ
键进入到程序的 STEP “1”的Leabharlann Baidu认。接着,用
UP 和 DOWN 键来检验确认每一步。
3.3 DIP 开关的选择
NO.1——原点确认 OFF——当气缸停止时,如果在 t1 时间内(即预置数据.P7)没有信号从传感器 中反馈回,计数值将复位到“0”,且原点位置被确认。 通常来说,原点一般设置在行程末端。如果需在行程内设定原点,在预定的原点 位置处安装机械限位器。 ON——当气缸停止在原点时,在原点位置设置磁性开关或限位开关,在确认传 感器信号输入 t1 时间内没有反馈,数值复位为 0.0,则原点设定完成。
按 WRITE 切换到下一个设置,屏幕上 显示 PRG STEP P7 和当前原点确认时 间。接着,输入设定的原点确认时间。
设 定 值 范 围 为 0~9.99s ( 1 单 位 是 10ms)。设定该值时,请考虑气缸的使 用条件。
闪烁
按 WRITE 切换到下一个设置,屏幕上
显示 PRG STEP P8 和当前操作错误检
program 1 的程序编辑结束。
闪烁
按 UP 键到 PRG “8”来设置程序号到 8。
闪烁
按 WRITE 键 2 次。
显示“END”将被代替为“0000.0”,进入
到 STEP 1 的设置。
闪烁
闪烁 闪烁
闪烁
闪烁
闪烁 闪烁
首先,按 LEFT 键 1 次。其次,用 DOWN 来设置值“8”。 按 LEFT 键一次。接着,用 DOWN 键来 设置值“6”。
1.1 输入信号配线图
1.2 推荐气动回路
2、 输入信号配线
2.1 输入信号配线内容
外部复位 手动阀 2 手动阀 1 设原点 程序选择 4 程序选择 3 程序选择 2 程序选择 1 紧急停止 临时停止 自动/手动 回原点 启动
屏蔽
外部电源 外部电源
Dip 开关 1、 原点确认 2、 制动设置 3、 计数方向切换 4、 存储清零
外部复位——输入该信号 50ms 以上,系统复位。在异常报警发生时,输入复位 信号解除报警。 2.3 输入部分接线 输入信号包括 13 种。接+24V 电源输入,+5V 通过光电耦合器被绝缘。 信号名称:启动、回原点、手动/自动,临时停止,紧急停止,程序选择 1,程 序选择 2,程序选择 3,程序选择 4,设原点,手动 1,手动 2,外部复位。 输入部分内部电路图如下:
负载(kg)÷ 缸径(cm)× r2 ×π × 使用压力(kgf/cm2) 4
例如:缸径:40mm 负载:20kg(允许动态负载值) 使用压力:5kgf/cm2 则负载率= 20kg ÷ 4 × 4×π × 5 = 31.8 = 30% (四舍五入)
4 P6——制动次数 P7——原点确认时间——设定原点检测时间(t1),
通过端子 13 来重启电源。当还原为初始状态后,将该状态设置回 OFF。
4、驱动
4.1 原点方向的设定 带制动的行程可读气缸的位置检测方式是增量式,请设定原点和机械基准面相
其中,0——输入端子 6~9 和 COM 端开路 1——输入端子 6~9 和 COM 端短路
设原点——当 dip 开关 NO.1 设置为 ON 时,可输入原点信号。当 dip 开关 NO.1 设置为 OFF 时,输入的磁性开关信号不能被识别。 手动 1/手动 2——在手动模式下使用,输入该信号,活塞杆前进或后退。
按 WRITE 键切换到下一设置。屏幕将显示 PRG STEP P2 和当前误差值设定。同时, 第一个小数位将开始闪烁。 接着,再如果 P1 的设置方法一样,完成对 预定误差值的设置。最大的行程误差值是 9.99mm。
举例: 如果输入误差值是 1.0,那么,任何落在设 定值±1.0 将被认为定位成功。如果落在此 范围外,将执行再试凑功能来落到允许的 范围内。 如果在执行完最大的再试凑功能后,仍不 能落到允许的范围内,将显示定位异常报 警信号(Err9)。
许的误差范围内为止。 P3——再试凑——输入再试凑的次数。最大的是 9 次。在设定的次数内,仍不能
落在定位精度公差的场合下,会发生 Err9(定位异常)且系统 停止工作,因此建议最好把再试凑次数设为 9 次。 P4——缸径——输入使用气缸的缸径。 P5——负载率——输入负载率(相对于气缸推力的负载率),计算公式如下:
设定值将如下改变:
注意:CE2 缸径的设定范围从φ40 到φ100mm。 按 WRITE 键切换到下一个设置。屏幕 上显示 PRG STEP P5 和正在闪烁的当 前负载率。接着,选择负载率。
闪烁 没没有有闪闪烁烁
设定值将如下改变:
按 WRITE 切换到下一个设置,屏幕上 显示 PRG STEP P6 和当前制动次数。 显示值表示制动组件的使用次数已可 被读出。1 单位代表 10.000,该值不可 被设置。 注意:当该值达到 300.0 时,需更换制 动组件。
3.2 程序设定 输入预定的气缸停止位置。
3.2.1 输入方法 将控制器模式切换开关置于 PROGRAM 位置。 注意:各程序的 STEP 0 对应的是 END。 程序数 1 开始闪烁。 按 UP 和 DOWN 键设定程序数。
闪烁
闪烁
闪烁
如下:
闪烁 输入例
上述设定完,按 WRITE 键结束操作。STEP “0”开始闪烁。接着,按 READ 或 WRITE 键继续下面的布置。
用≥10mA 电流作为输入信号。
2.4 输出部分配线 输出信号包括 4 种。+5V 在光电耦合器上被绝缘。 信号名称:测位置、测原点、程序结束、异常报警。 最大端子电压:DC +30V 最大电流:50mA(0°~50°C) 输出部分内部电路图如下:
2.5 电磁阀配线 电磁阀驱动输出信号有 3 种。+5V 在光电耦合器上被绝缘。 信号名称:制动、驱动 A、驱动 B。 最大端子电压:+24V DC 最大电流:80mA(0°~50°C) 电磁阀输出部分内部电路如下:
(10ms 为一个单位,最大是 9.99s) 当输入回原点信号,在 t1 时间内传感器没有收到任何 信号(气缸停止状态)的场合,回原点确认到位。 设定响应时间的时候应考虑到负载、安装条件、气管 长度等。如果使用条件改变,应重新校准响应时间。 当控制器 dip 开关 NO.1 状态为 ON,且磁性开关为 ON 时,回原点确认到位。 P8——Err12(操作错误)确认时间,t2。 输入 Err12 确认时间。 10ms 为一个单位,最大是 9.99s。 输入启动信号后,在时间范围内,如果没有传感器没有任何反馈信号(气 缸停止)将发生 Err12 报警。
测时间。接着,输入预定的操作错误检
测时间。设定值范围为 0~9.99s(1 单
位是 10ms)。设定该值时,请考虑气缸
的使用条件。
当完成了上述所有的设定时,按
WRITE 键结束整个的 PRESET 数据预
闪烁
设置操作。
3.1.2 确认设定数据 将控制器模式切换开关置于 PRESET 位置。 当 P1 闪烁时,用 UP 和 DOWN 键来 闪烁 确认每个预设值正确与否。当输入值 闪烁时,按 READ 键一次可切换操作 闪烁 到 P1。
将控制器模式切换开关置于 PROGRAM 位置。 按 WRITE 两次。显示“End”将被替 换为“0000.0”,进入到 STEP 1 输入。
闪烁
按 LEFT 键两次。第一小数位的“0”开始 闪烁。
闪烁
按 UP 键 5 次就可设定值为 5。
闪烁 闪烁
按 WRITE 键 1 次。按 LEFT 键 3 次来改 变光标闪烁的位置。
显示“End”将被“0000.0”代替,进入到 STEP 1 的输入状态。输入第一个预定位置 到 STEP 1。
接着,按 WRITE 键进入到 STEP 2 的设置。 一步一步的输入预定位置。 当将最后一个值输入到最后一步时,按 WRITE 键结束该程序的设定。 注意:当没有输入 END 时,操作时控制器 将显示 Err7 错误。 当完成上述的输入步骤后,输入程序显示
闪烁 闪烁
按 WRITE 键切换到下一个设置。屏幕 将显示 PRG STEP P3 和最大再试凑次 数。接着,输入预定的最大再试凑次数。 最大可设定值是 9。在初次调整中,执 行预测控制。因此,建议最大再试凑次 数至少 5 次。
按 WRITE 键切换到下一个设置。屏幕 将显示 PRG STEP P4 和正在闪烁的当 前气缸缸径。接着,选择缸径。
按 WRITE 键 1 次。 按 UP 键 5 次来设置值“5”。
按 LEFT 键 2 次。按 UP 键 3 次来设置值 “3”。
按 WRITE 键进入到 program 8 的最后一 步即 STEP 3 的设置。 按 END 键开始 program 8 的程序设置。
program 8 的程序设定结束。
按 UP 键 3 次可设定值为 3。
闪烁
按 WRITE 键 1 次。按 LEFT 键 2 次来改变 光标闪烁的位置。
闪烁
按 UP 键 3 次可设定值为 3。
闪烁
闪烁
闪烁
按 WRITE 键 1 次进入到 program 1 的最后 一步即 STEP 4 的设置。按 END 键结束 program 1 的设置。
3.1.2 数据设定 将控制器模式切换开关置于 PRESET 位置。
闪烁
P1 将开始闪烁。
闪烁 闪烁
闪烁
按 READ 或 WRITE 键切换到气缸行程的设 定。第一个小数位将闪烁。 用 LEFT 和 RIGHT 键来选择要更改的数据位 置,用 UP 和 DOWN 键来设置预定的参数。
闪烁 参考
误差允许值 设定值
程序结束 测原点信号 异常/报警 测位置信号
2.2 输入信号内容 启动——一旦启动,开始按预置数据作动。每触发一次(需持续 50ms 以上)走 一步动作。 注意:仅当先执行回原点命令,且原点信号被反馈到控制器后,启动信号(需持 续 50ms 以上)才被接收,气缸按照设定程序作动。 回原点——活塞杆回原点后,输入持续 50ms 以上的信号。 自动/手动模式——当端子和 COM 端断路状态下,自动模式开启。反之,短路状 态下,手动模式开启。 自动模式——输入启动信号后,将一步步按设定作动。 手动模式——将手动 1(端子 11)或手动 2(端子 12)与 COM 端短路,来控制 气缸的前进或后退。但动作的方向依配管和接线而异。 临时停止——定位过程中,输入此命令将停止作动。当此命令取消,从临时停止 位置开始继续定位动作。 注意:如临时停止点距离设定点不足 5mm 时,会出现 Err5(操作异常)报警。 紧急停止——定位过程中,此命令会强迫动作立即停止。输入该信号后,会出现 Err10 报警。 注意:紧急停止后,必须执行回原点命令。 程序选择 1,2,3,4——选择程序参照下表(二进制):
2.6 顺序器 由于控制器和顺序器之间的配线问题,在程序内设定脉冲宽度 50ms 不能保证输 出脉冲宽度也是同样的值。因此,为了获得在控制器侧测得的脉冲宽度≥50ms, 应设定相应的脉冲宽度。
3、数据设定
3.1 数据预设 3.1.1 数据设定的种类及内容 P1——气缸行程——输入使用气缸的行程。 P2——定位精度公差——输入定位的允许误差范围。再试凑功能可确保定位到允
NO.2——制动系统的设置 OFF——在该状态下,ON 意味着制动可用。OFF 意味着处于自由状态。 如果控制器断电,将处于自由状态。 如果气缸水平安装,没达到气平衡时,突然断电的情况下,气缸将继续伸出或者 缩回。 如果气缸垂直安装,突然断电的情况下,活塞杆将因自身的重量而落回到底部。 ON——在该状态下,OFF 意味着制动可用。ON 意味着处于自由状态。 如果控制器突然断电,制动锁将处于爬行状态。 注意:请注意配管的问题,这可能导致以上相反的设定。
NO.3——计数方向的切换
OFF——伸出方向将作为计数增大的方向。
缩回端
伸出
原点将设置在缩回端。
伸出端
原点设置在伸出端。
缩回
注意:请注意接线的问题,这可能导致以上相
反的设定。
NO.4——存储清零:清除输入数据,还原为初始设定值 通常,设定该状态为 OFF。如果输入数据要求清零,设定该状态为 ON。接着,
3.2.2 输入数据的确认 将控制器模式切换开关置于 PROGRAM 位置。
闪烁
当 PRG “1”开始闪烁时,用 UP 和 DOWN 键
来选择预定的程序来检验。其次,按 READ
键进入到程序的 STEP “1”的Leabharlann Baidu认。接着,用
UP 和 DOWN 键来检验确认每一步。
3.3 DIP 开关的选择
NO.1——原点确认 OFF——当气缸停止时,如果在 t1 时间内(即预置数据.P7)没有信号从传感器 中反馈回,计数值将复位到“0”,且原点位置被确认。 通常来说,原点一般设置在行程末端。如果需在行程内设定原点,在预定的原点 位置处安装机械限位器。 ON——当气缸停止在原点时,在原点位置设置磁性开关或限位开关,在确认传 感器信号输入 t1 时间内没有反馈,数值复位为 0.0,则原点设定完成。
按 WRITE 切换到下一个设置,屏幕上 显示 PRG STEP P7 和当前原点确认时 间。接着,输入设定的原点确认时间。
设 定 值 范 围 为 0~9.99s ( 1 单 位 是 10ms)。设定该值时,请考虑气缸的使 用条件。
闪烁
按 WRITE 切换到下一个设置,屏幕上
显示 PRG STEP P8 和当前操作错误检
program 1 的程序编辑结束。
闪烁
按 UP 键到 PRG “8”来设置程序号到 8。
闪烁
按 WRITE 键 2 次。
显示“END”将被代替为“0000.0”,进入
到 STEP 1 的设置。
闪烁
闪烁 闪烁
闪烁
闪烁
闪烁 闪烁
首先,按 LEFT 键 1 次。其次,用 DOWN 来设置值“8”。 按 LEFT 键一次。接着,用 DOWN 键来 设置值“6”。