分油机控制
分油机操作程序
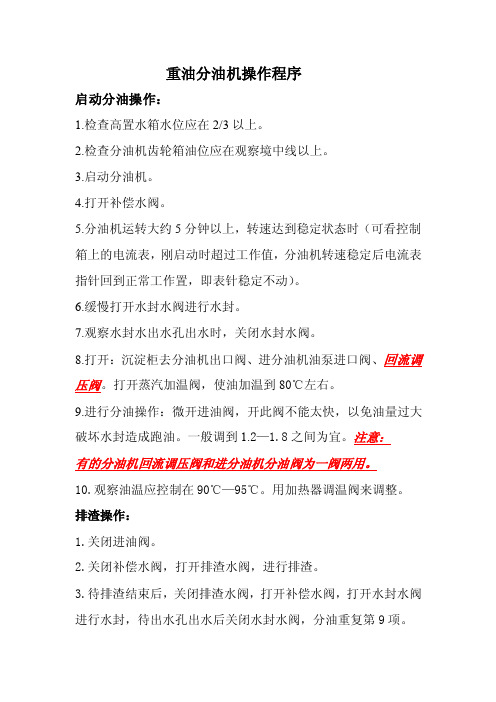
重油分油机操作程序
启动分油操作:
1.检查高置水箱水位应在2/3以上。
2.检查分油机齿轮箱油位应在观察境中线以上。
3.启动分油机。
4.打开补偿水阀。
5.分油机运转大约5分钟以上,转速达到稳定状态时(可看控制箱上的电流表,刚启动时超过工作值,分油机转速稳定后电流表指针回到正常工作置,即表针稳定不动)。
6.缓慢打开水封水阀进行水封。
7.观察水封水出水孔出水时,关闭水封水阀。
8.打开:沉淀柜去分油机出口阀、进分油机油泵进口阀、回流调压阀。
打开蒸汽加温阀,使油加温到80℃左右。
9.进行分油操作:微开进油阀,开此阀不能太快,以免油量过大破坏水封造成跑油。
一般调到1.2—1.8之间为宜。
注意:
有的分油机回流调压阀和进分油机分油阀为一阀两用。
10.观察油温应控制在90℃—95℃。
用加热器调温阀来调整。
排渣操作:
1.关闭进油阀。
2.关闭补偿水阀,打开排渣水阀,进行排渣。
3.待排渣结束后,关闭排渣水阀,打开补偿水阀,打开水封水阀进行水封,待出水孔出水后关闭水封水阀,分油重复第9项。
分 油 机 操 作 规 程
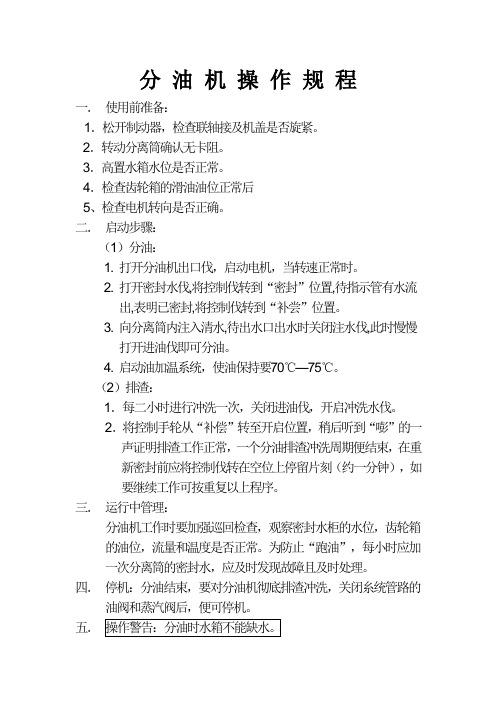
分油机操作规程
一.使用前准备:
1.松开制动器,检查联轴接及机盖是否旋紧。
2.转动分离筒确认无卡阻。
3.高置水箱水位是否正常。
4.检查齿轮箱的滑油油位正常后
5、检查电机转向是否正确。
二.启动步骤:
(1)分油:
1. 打开分油机出口伐,启动电机,当转速正常时。
2. 打开密封水伐,将控制伐转到“密封”位置,待指示管有水流
出,表明已密封,将控制伐转到“补尝”位置。
3. 向分离筒内注入清水,待出水口出水时关闭注水伐,此时慢慢
打开进油伐即可分油。
4. 启动油加温系统,使油保持要70℃—75℃。
(2)排渣:
1.每二小时进行冲洗一次,关闭进油伐,开启冲洗水伐。
2.将控制手轮从“补偿”转至开启位置,稍后听到“嘭”的一声证明排渣工作正常,一个分油排渣冲洗周期便结束,在重
新密封前应将控制伐转在空位上停留片刻(约一分钟),如
要继续工作可按重复以上程序。
三.运行中管理:
分油机工作时要加强巡回检查,观察密封水柜的水位,齿轮箱的油位,流量和温度是否正常。
为防止“跑油”,每小时应加一次分离筒的密封水,应及时发现故障且及时处理。
四.停机:分油结束,要对分油机彻底排渣冲洗,关闭糸统管路的油阀和蒸汽阀后,便可停机。
五.。
分油机自动化控制
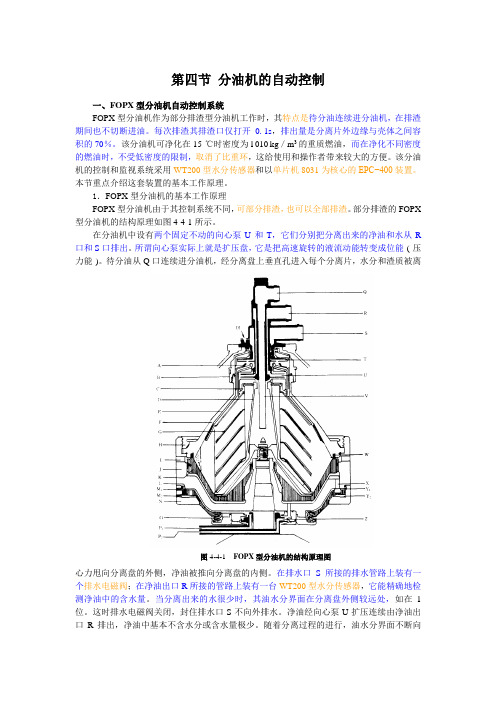
第四节 分油机的自动控制一、FOPX 型分油机自动控制系统FOPX 型分油机作为部分排渣型分油机工作时,其特点是待分油连续进分油机,在排渣期间也不切断进油。
每次排渣其排渣口仅打开0.1s ,排出量是分离片外边缘与壳体之间容积的70%。
该分油机可净化在15 ℃时密度为l 010 kg /m 3的重质燃油,而在净化不同密度的燃油时,不受低密度的限制,取消了比重环,这给使用和操作者带来较大的方便。
该分油机的控制和监视系统采用WT200型水分传感器和以单片机8031为核心的EPC−400装置。
本节重点介绍这套装置的基本工作原理。
1.FOPX 型分油机的基本工作原理FOPX 型分油机由于其控制系统不同,可部分排渣,也可以全部排渣。
部分排渣的FOPX 型分油机的结构原理如图4-4-1所示。
在分油机中设有两个固定不动的向心泵U 和T ,它们分别把分离出来的净油和水从R 口和S 口排出。
所谓向心泵实际上就是扩压盘,它是把高速旋转的液流动能转变成位能 ( 压力能 )。
待分油从Q 口连续进分油机,经分离盘上垂直孔进入每个分离片,水分和渣质被离心力甩向分离盘的外侧,净油被推向分离盘的内侧。
在排水口S 所接的排水管路上装有一个排水电磁阀;在净油出口R 所接的管路上装有一台WT200型水分传感器,它能精确地检测净油中的含水量。
当分离出来的水很少时,其油水分界面在分离盘外侧较远处,如在1位。
这时排水电磁阀关闭,封住排水口S 不向外排水。
净油经向心泵U 扩压连续由净油出口R排出,净油中基本不含水分或含水量极少。
随着分离过程的进行,油水分界面不断向图4-4-1 FOPX 型分油机的结构原理图里移动,水分传感器会感受到净油中含水量的增大。
当油水分界面移动到接近分离盘外侧表面时,净油中的含水量会增加到一个触发值。
这个触发值将送到EPC−400型监控装置,由该装置决定是打开排水电磁阀向外排水,还是打开排渣口I进行一次排渣。
不论是打开排水电磁阀,还是进行一次排渣,油水分界面会迅速外移,净油中含水量也会迅速减少。
分油机的自动控制(个人整理)

分油机的自动控制这篇文章详细介绍一下分油机的工作原理,即分油、排渣、放残等过程,从油路上理清楚在进行这些动作时分油机的状态。
先举个实例,在某轮上分油机的应用,SA876(HFO),SA866(M/E LO),PA605(MDO),PA615(G/E LO),为阿法拉伐的四种机型,具体应用情况如下:在这种S型分油机中,组成其控制系统的重要设备是EPC-50型监控装置。
该装置由两块印刷电路板组成:一块是水分传感器信号处理电路板,它接收装在净油出口管路上MT-50型水分传感器输出的净油中含水量的信号,经由处理后送至主控电路板;另一块是主控电路板,它接收装在分油机进油管路上和净油出口管路上的各种传感器信号,经由分析和处理后,由输出端输出各种信息,可对分油机进行操作,同时分油机的运行状态也可通过在主控电路板上的一系列发光二极管及数字显示窗的数字进行指示。
下面为分油机不同状态转换时的油路示意图。
基本油路分油过程1.工作原理分离过程中,油渣和水聚积在分离桶的周围。
油渣和水经过一定的时间被排出,排渣期间暂不进油。
净油排出分油机,在净油出口有水分检测传感器MT。
检测到的水分含量和控制程序中参考值比较,超过一定差值则水放残。
2.程序启动首先将进油泵、分油机、加热器启动,当温度传感器和转子速度传感器达到规定值后,首先进行一次排渣动作,以保证分离桶内是空的。
控制单元开始运行分离程序。
1)三通阀控制被分离的油进入循环管路。
密封水进入分油桶内,直到达到净油口压力传感器的设定值。
2)控制单元记录进水时间,这个流量值用来后面计算合适的置换水的量。
3)分油机排渣。
4)根据上图中记录的流量,控制单元开启电磁阀向分离桶内注水。
5)三通阀开启使得燃油进入分油机,控制单元将出油口的压力传感器检测到的油压存储并记录时间,以正确地调节进油量。
现在进行的为分离过程,燃油不断地经过供给泵从沉淀柜送到分油机,然后将净油送至日用油柜。
3.排渣一定时间后分油机自动排渣,顺序如下:1)三通阀打到使油循环的位置。
燃油分油机操作程序

燃油分油机操作程序
Fuel oil separator operation procedures
一、起动
1、燃油日用油柜加热至80~90℃,检查分油机油位、打开工
业淡水进水阀(3~4kg)、打开压缩控制空气进气阀(5~6kg),打开分油机加热器蒸汽进出口阀,检查分油机燃油进出口
阀。
2、启动燃油供油泵(feed pump),按下温控器控制按钮PID,
加热器投入工作。
启动分油机运行马达(separator),4
分钟后分油机将达额定转速,separator指示灯常亮。
3、待转速稳定,加热温度进入88~108℃区域,启动程序键
(start)停止闪烁,按下start键,分油机进入分油程序。
进油后,进油口三通气动阀顶红色杆将下行。
4、通过净油出口控制阀调节出口压力(1.5bar),根据供油
需求调节供油量(4~5格,800L∕h左右),观察分油机运
行及泄漏情况。
二、停机
1、按下程序停止按钮(stop),分油程序将全自动停止。
2、程序安全停止后,start灯灭,停分油机马达及供油泵。
3、
关闭相关阀件。
善时轮
欢迎您的下载,
资料仅供参考!
致力为企业和个人提供合同协议,策划案计划书,学习资料等等
打造全网一站式需求。
分油机的自动控制
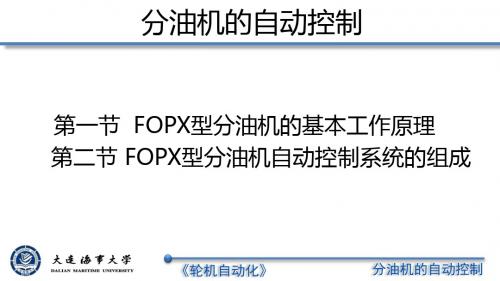
《轮机自动化》
分油机的自动控制
第二节 FOPX型分油机自动控制系统组成
三、基本的控制过程
排渣间隔:10最短不可调,63min最长可调 1、t>63,未到触发值,进置换水,排渣,曲线1; 2、10<t<63,到触发值,排渣,(不进置换水),曲线2; 3、t<10,到触发值,排水一次(20s),若t<10内,又到触发 值,则排渣,曲线3; 4、若3后,t<10又到触发值,则排水120S,若仍大于触发值 ,则再重复3一次,无效后停止程序,声光报警,如曲线4。
《轮机自动化》
分油机的自动控制
第二节 FOPX型分油机自动控制系统组成
三、基本的控制过程
《轮机自动化》
分油机的自动控制
第二节 FOPX型分油机自动控制系统组成
控制系统工作时序表
《轮机自动化》
分油机的自动控制
控制器:EPC-400型监控装置
水分传感器信号处理电路板 主控电路板
一、输入信号
PT1:温度开关:高油温报警 PT3:温度传感器:加热器PI控制、指示油温报警值 PT2:温度开关:低油温报警 FS:低流量开关:滤器堵塞、管路泄漏、泵浦损坏等引起 的进 油流量降低报警
《轮机自动化》
分油机的自动控制
第二节 FOPX型分油机自动控制系统组成
时序程序控制
按预定的时间顺序自动完成一系列预定的各项控制。在 时序程序控制中,指令处理装置根据操作指令和回答信号、 逐个给出时序控制指令。如锅炉自动点火和分油机分油、排 渣控制。
本节学习目标
1、掌握分油机的控制时序 2、掌握分油机控制相关的输入输出元件。
《轮机自动化》
分油机的自动控制
第二节 FOPX型分油机自动控制系统组成
FOPX型分油机自动控制系统
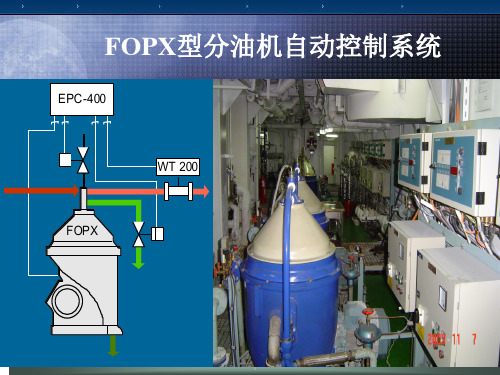
20
21
显示窗、按钮及 显示窗、按钮及LED
22
3.基本的控制过程 .
型装置中, 在EPC-400型装置中,设定了一个最短排渣 型装置中 间隔时间10min及一个最大排渣间隔时间 间隔时间 及一个最大排渣间隔时间 63min (可调 。分油机是以最短的间隔时间 可调)。 可调 打开一次排渣口, 打开一次排渣口,还是以最大的间隔时间 打开一次排渣口, 打开一次排渣口,取决于待分油中含水量 的多少。 的多少。
8
(2)低流量开关 )低流量开关FS
用来监视供油系统的故障。若供油系统有故障, 用来监视供油系统的故障。若供油系统有故障, 如滤器堵塞、管路泄漏、 如滤器堵塞、管路泄漏、泵浦损坏等都会引起进 油量降低,低到下限值时, 的触头闭合 的触头闭合, 油量降低,低到下限值时,FS的触头闭合,把信 号送至EPC-400型装置,发出低流量报警。 型装置, 号送至 型装置 发出低流量报警。
23
基本的控制过程
①如果待分油中含水量极少,从上次排渣算起在 如果待分油中含水量极少, 63min内净油中含水量没有达到触发值,这时 内净油中含水量没有达到触发值, 内净油中含水量没有达到触发值 这时EPC400就决定排一次渣。在排渣前,使电磁阀 就决定排一次渣。 就决定排一次渣 在排渣前,使电磁阀MV l0通 通 电打开,向分油机内注入置换水。 电打开,向分油机内注入置换水。当净油中含水量达 到触发值时,电磁阀MVl5和MVl6同时通电打开,进 同时通电打开, 到触发值时,电磁阀 和 同时通电打开 行一次排渣。 行一次排渣。 ②如果待分油中含有一定量的水,距上次排渣时间超 如果待分油中含有一定量的水, 但不到63min净油中含水量就达到触发值, 净油中含水量就达到触发值, 过10min但不到 但不到 净油中含水量就达到触发值 EPC-400发出排渣信号进行一次排渣,排渣前不需进 发出排渣信号进行一次排渣, 发出排渣信号进行一次排渣 置换水。 置换水。
分油机操作规程
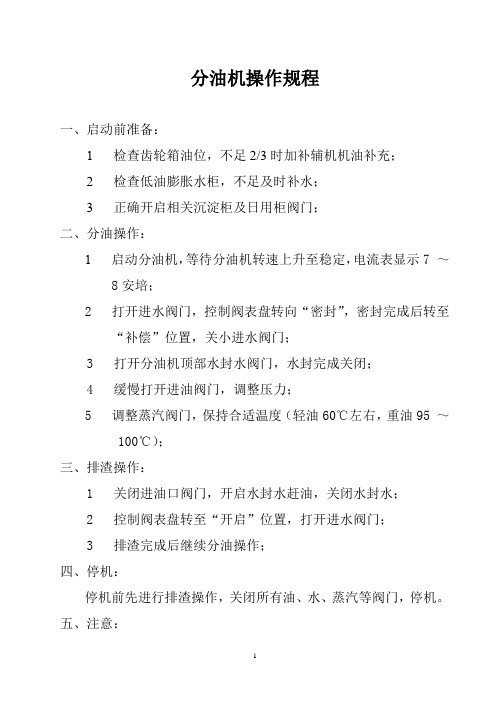
分油机操作规程
一、启动前准备:
1 检查齿轮箱油位,不足2/3时加补辅机机油补充;
2 检查低油膨胀水柜,不足及时补水;
3 正确开启相关沉淀柜及日用柜阀门;
二、分油操作:
1 启动分油机,等待分油机转速上升至稳定,电流表显示7 ~
8安培;
2 打开进水阀门,控制阀表盘转向“密封”,密封完成后转至
“补偿”位置,关小进水阀门;
3 打开分油机顶部水封水阀门,水封完成关闭;
4 缓慢打开进油阀门,调整压力;
5 调整蒸汽阀门,保持合适温度(轻油60℃左右,重油95 ~
100℃);
三、排渣操作:
1 关闭进油口阀门,开启水封水赶油,关闭水封水;
2 控制阀表盘转至“开启”位置,打开进水阀门;
3 排渣完成后继续分油操作;
四、停机:
停机前先进行排渣操作,关闭所有油、水、蒸汽等阀门,停机。
五、注意:
勤检查分油机工况,如有跑油现象及时关闭进油阀门并通知值班轮机员。
分油机操作规程
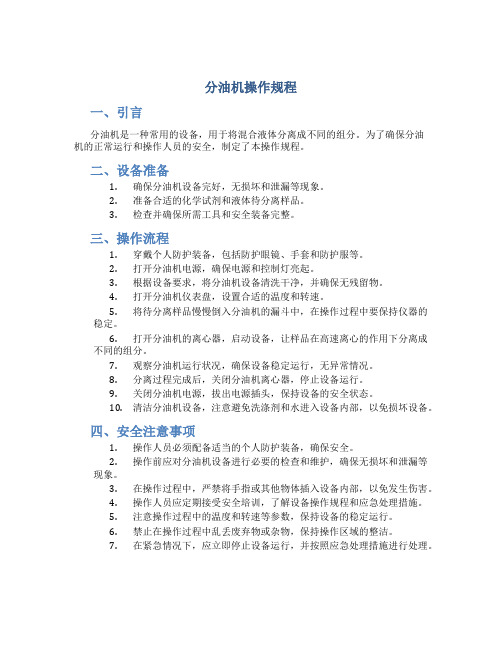
分油机操作规程一、引言分油机是一种常用的设备,用于将混合液体分离成不同的组分。
为了确保分油机的正常运行和操作人员的安全,制定了本操作规程。
二、设备准备1.确保分油机设备完好,无损坏和泄漏等现象。
2.准备合适的化学试剂和液体待分离样品。
3.检查并确保所需工具和安全装备完整。
三、操作流程1.穿戴个人防护装备,包括防护眼镜、手套和防护服等。
2.打开分油机电源,确保电源和控制灯亮起。
3.根据设备要求,将分油机设备清洗干净,并确保无残留物。
4.打开分油机仪表盘,设置合适的温度和转速。
5.将待分离样品慢慢倒入分油机的漏斗中,在操作过程中要保持仪器的稳定。
6.打开分油机的离心器,启动设备,让样品在高速离心的作用下分离成不同的组分。
7.观察分油机运行状况,确保设备稳定运行,无异常情况。
8.分离过程完成后,关闭分油机离心器,停止设备运行。
9.关闭分油机电源,拔出电源插头,保持设备的安全状态。
10.清洁分油机设备,注意避免洗涤剂和水进入设备内部,以免损坏设备。
四、安全注意事项1.操作人员必须配备适当的个人防护装备,确保安全。
2.操作前应对分油机设备进行必要的检查和维护,确保无损坏和泄漏等现象。
3.在操作过程中,严禁将手指或其他物体插入设备内部,以免发生伤害。
4.操作人员应定期接受安全培训,了解设备操作规程和应急处理措施。
5.注意操作过程中的温度和转速等参数,保持设备的稳定运行。
6.禁止在操作过程中乱丢废弃物或杂物,保持操作区域的整洁。
7.在紧急情况下,应立即停止设备运行,并按照应急处理措施进行处理。
五、操作记录操作人员在操作过程中应及时记录相关信息,包括操作时间、设备状态、分离效果等,用于后续的分析和验证。
六、操作异常情况处理在操作过程中发现设备异常情况时,应立即停止设备运行,并及时联系维修人员进行维修和处理。
七、设备维护1.定期对分油机设备进行维护和保养,确保设备的正常运行。
2.清洁设备时,使用适当的洗涤剂和方法,避免损坏设备。
柴油分油机操作程序
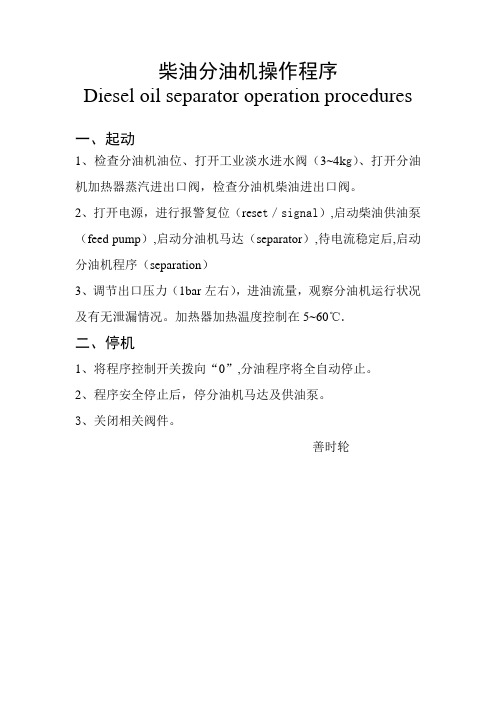
柴油分油机操作程序
Diesel oil separator operation procedures
一、起动
1、检查分油机油位、打开工业淡水进水阀(3~4k g)、打
开分油机加热器蒸汽进出口阀,检查分油机柴油进出口
阀。
2、打开电源,进行报警复位(rese t/signal),启动柴油
供油泵(feed pump),启动分油机马达(separator),待电
流稳定后,启动分油机程序(separation)
3、调节出口压力(1bar左右),进油流量,观察分油机运
行状况及有无泄漏情况。
加热器加热温度控制在5~60℃.
二、停机
1、将程序控制开关拨向“0”,分油程序将全自动停止。
2、程序安全停止后,停分油机马达及供油泵。
3、关闭相关阀件。
善时轮。
FOPX部分排渣分油机自动控制系统

§4-5 FOPX 型部分排渣分油机自动控制系统系统特点:1、连续式分油机,排渣期间也不要断待分油;2、每次排渣其排渣口仅打开为0.1S ,排出量为分离盘外边沿与壳体间容积的70%;3、可分离密度的1010kg/cm 3重质燃油;4、是以单片机8031为核心组成的控制系统。
一、FOXP 型分油机基本工作原理 1、分油机的几种工况(1)若油中含水较少,油水界面远离分离盘外缘——直接排油,不排水;(2)当油水界面接近分离盘外缘时,WT200检测到油中含水量达成触发值时,EPC400控制待分油进口净油出口 出水口 向心水泵 向心油泵 进油管P 1—MV15控制的操作水进口P 2—MV16控制的补偿水和水封水进口置换水进口出水管上装有排水电磁阀净油出口管上装有WT200型水分传感器器决定打开排水电磁阀或排渣口排渣。
(3)若水分含量很少,达成最大排渣间隔时间(油水界面远离分离盘外侧)时,排渣前先入置换水,使油水界面内移,然后再排渣——防止跑油2、排渣过程的控制¿正常分油期间,滑动底盘被高速转动的工作水动压托起,封住排渣口I(由P2口断续供水补偿工作水的蒸发和泄漏)。
排渣时,P1、P2管同时连续进水,水面内移进入排渣启动室Y1,克服弹簧力使滑动圈下移,打开泄水口X(Y1中的水同时经垂直孔进入封闭水腔Y2),滑动底盘下移排渣口打开排渣;当Y2充满水时,Y1与Y2室压力相等,在弹簧力作用下滑动圈上移,关闭泄水口X,工作水托起滑动底盘,封闭排渣口(P1停水,Y1、Y2中的水经喷咀M1、M2泄放),P2先连续供水后恢复断续供水,以保证工作水面在Z附近。
排渣口排开的时刻及排出量取决于定量环N表面的凹槽大小(即水充满Y2腔的时间长短) P1通操作水的时间为3S,排渣口排开时间为0.1S,排出容量为分离盘外侧容积的70%——部分排渣二、FOPX型分油机的控制系统PT1、PT2——高低油温开关;PT3——油温传感器;FS——低流量开关;PS1——分油机故障开关;PS2——排渣口打开反馈信号;WT200——水分含量传感器;XT1——液体传感器;MV10——置换水控制阀MV5——排水电磁阀;MV15——操作水控制阀;MV16——补偿水和水封水阀。
分油机控制
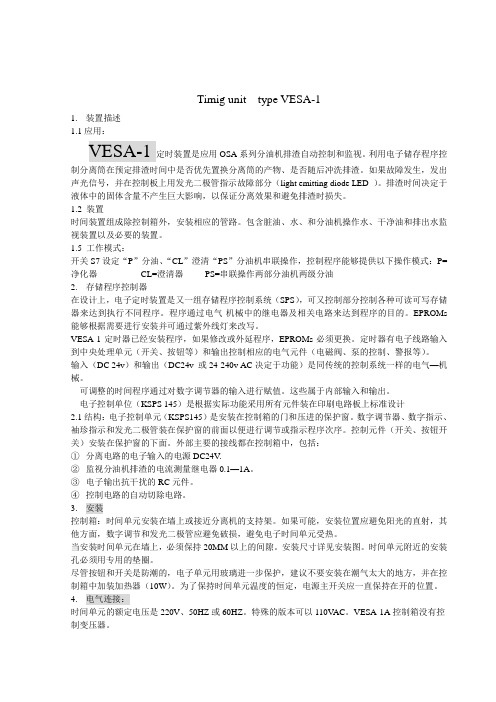
使用时间自动程序,分油速率的变化和燃油中所含杂质来计算分油时间的设定,如果这些参数
没变化,就没有必要进行计算。分油时间决定于燃油中含杂质。
8. 水封水时间设定:分离桶中水量会因蒸发而减少,在分油过程中间隔的补充水以防止分离桶过
早打开。水量的调整是通过合适的时间继电器,它通过控制工作水管线上的电磁阀 V3。另外,
在设计上,电子定时装置是又一组存储程序控制系统(SPS),可又控制部分控制各种可读可写存储
器来达到执行不同程序。程序通过电气-机械中的继电器及相关电路来达到程序的目的。EPROMs
能够根据需要进行安装并可通过紫外线灯来改写。
VESA-1 定时器已经安装程序,如果修改或外延程序,EPROMs 必须更换。定时器有电子线路输入
起动排渣程序:(等待) S4 ‘separating’ 程序 LED 亮,起动 d1。
排放:起动定时器 d2,补水和置换水电磁阀 LED 亮,V2 打开。
排渣:定时器 d3‘排渣’启动,工作水阀打开 V3.
等待:定时器 d4 启动,分离桶速度恢复。
补水:(分油模式)定时器 d5 启动,补水和置换水电磁阀打开,v2.
13. 没有置换和冲洗排渣的总排渣
操作主电源开关:S1 时钟 LED 闪,马达指示灯亮,数字显示器读数为零。
起动排渣程序:(等待) S4 ‘separating’ 程序 LED 亮,起动 d1。
排渣:等待:时间继电器 d4 运行,分离桶速度恢复。
5.5 二位数字调节器 EM08.3.0.1 part no. 0005-4068-010 辅助功能。
5.6 二位数字调节器 EM 07.3.0.1 part no. 0005-4068-020 辅助功能。
6. 排渣程序 对分离桶必须进行定期的排渣,要结合产生物和程序的情况。VESA-1 时间单元通过选择开关来
分油机的操作与管理
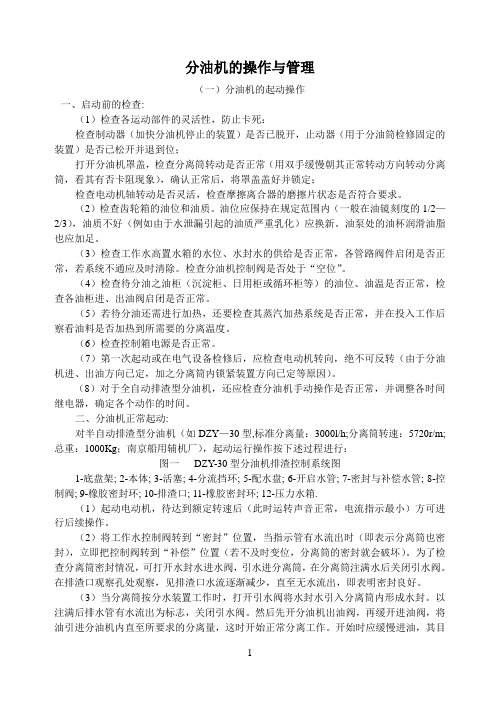
分油机的操作与管理(一)分油机的起动操作一、启动前的检查:(1)检查各运动部件的灵活性,防止卡死:检查制动器(加快分油机停止的装置)是否已脱开,止动器(用于分油筒检修固定的装置)是否已松开并退到位;打开分油机罩盖,检查分离筒转动是否正常(用双手缓慢朝其正常转动方向转动分离筒,看其有否卡阻现象),确认正常后,将罩盖盖好并锁定;检查电动机轴转动是否灵活,检查摩擦离合器的磨擦片状态是否符合要求。
(2)检查齿轮箱的油位和油质。
油位应保持在规定范围内(一般在油镜刻度的1/2—2/3),油质不好(例如由于水泄漏引起的油质严重乳化)应换新。
油泵处的油杯润滑油脂也应加足。
(3)检查工作水高置水箱的水位、水封水的供给是否正常,各管路阀件启闭是否正常,若系统不通应及时清除。
检查分油机控制阀是否处于“空位”。
(4)检查待分油之油柜(沉淀柜、日用柜或循环柜等)的油位、油温是否正常,检查各油柜进、出油阀启闭是否正常。
(5)若待分油还需进行加热,还要检查其蒸汽加热系统是否正常,并在投入工作后察看油料是否加热到所需要的分离温度。
(6)检查控制箱电源是否正常。
(7)第一次起动或在电气设备检修后,应检查电动机转向,绝不可反转(由于分油机进、出油方向已定,加之分离筒内锁紧装置方向已定等原因)。
(8)对于全自动排渣型分油机,还应检查分油机手动操作是否正常,并调整各时间继电器,确定各个动作的时间。
二、分油机正常起动:对半自动排渣型分油机(如DZY—30型,标准分离量:3000l/h;分离筒转速:5720r/m;总重:1000Kg;南京船用辅机厂),起动运行操作按下述过程进行:图一DZY-30型分油机排渣控制系统图1-底盘架; 2-本体; 3-活塞; 4-分流挡环; 5-配水盘; 6-开启水管; 7-密封与补偿水管; 8-控制阀; 9-橡胶密封环; 10-排渣口; 11-橡胶密封环; 12-压力水箱.(1)起动电动机,待达到额定转速后(此时运转声音正常,电流指示最小)方可进行后续操作。
PLC课程分析方案-分油机的自动控制
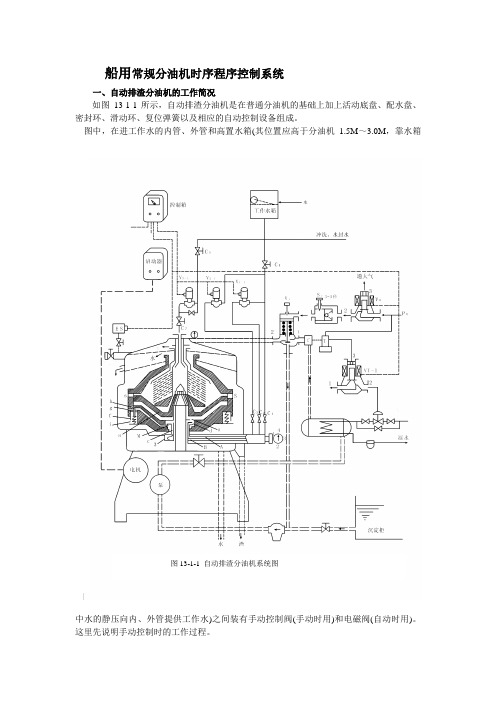
船用常规分油机时序程序控制系统一、自动排渣分油机的工作简况如图13-1-1所示,自动排渣分油机是在普通分油机的基础上加上活动底盘、配水盘、密封环、滑动环、复位弹簧以及相应的自动控制设备组成。
图中,在进工作水的内管、外管和高置水箱(其位置应高于分油机1.5M~3.0M,靠水箱图 13-1-1 自动排渣分油机系统图中水的静压向内、外管提供工作水)之间装有手动控制阀(手动时用)和电磁阀(自动时用)。
这里先说明手动控制时的工作过程。
手动控制阀有四个位置:“1”位——开排渣口;“2”位——空位放水;“3”位——封闭排渣口;“4”位——正常分油。
可以通过手动控制阀位以进入不同的工况。
自动控制时,则是通过控制电磁阀V1-1和V2-1通电或断电来实现上述功能。
下面以手动控制来说明:1.开排渣口:当手动控制阀放在“1”位时,外管进水而内管断水,外管的水压使左侧的滑动环f下压,打开左侧和活动底盘相通的垂直出水口h,活动底盘下部空间的工作水经H 和出水口i排出,导致活动底盘下落打开排渣口S,使分离筒中的渣油和水一起从排渣口S 排出。
此为开排渣口过程。
2.空位放水:当排渣完毕后,将手动控制阀打至“2”位,此时外管和内管均断水,原积存于分离筒内的水从左边的g口排出,复位弹簧使滑动环向上复位,关闭和活动底盘下部空间相连的垂直出水口h,但排渣口S仍为打开状态,此为空位放水状态。
如果不再分油,则各有关部件一直处于此状态。
3.封闭排渣:若要继续分油,则将手动控制阀打至“3”位,使外管和内管同时进水,大量的工作水使活动底盘下面的空间充满水,随分离筒一起高速旋转的水产生动压使活动底盘迅速托起,封闭排渣口S,为分油作好准备,此为封闭排渣口工况。
4.正常分油应注意,外管进水的时间不能过长,否则过量的水会使左边和活动底盘相连的垂直出水口h打开,导致活动底盘下面空间的水经h和i泄出而使活动底盘再次落下,故经一定时间(约5秒)后,应将手动控制阀打至“4”位。
4.滑油分油机操作程序

LF13-2钻采平台
滑油分油机(DPP-X-7006)操作程序文档号:LF13-2DPP-XXX 版本:0
日期:2011年4月7日共1页,第1页批准:
滑油分油机操作程序
1.起动前准备
1.1 检查分油机润滑油位在正常位置。
(油位应在观察中线上面)
1.2 检查系统各阀处于正常开闭状态。
2.起动程序
2.1 电源开关放”ON”位置。
2.2 启动供油泵(压力0.8-2Bar)后再启动加热器—“heater”,等待滑油加热到设定温度值。
(显示灯转绿)
2.3 启动分油机程序开关—“separation”(该灯闪烁)。
2.4 面板显示“START SEPARA TOR”,启动分油机马达并观察振动,噪音正常,确定电流稳定在额定值(5A)。
2.5 当分油机达到全速时面板会显示“STANDBY”。
2.6 当供油温度达到设定值(90°)面板上报警红灯变绿时,按程序启动按钮—“separation”(该灯常绿)。
2.7 分油机进入正常分油程序后,检查,调整出口压力到0.15MPA左右,检查电流是否在正常值。
2.8 检查进口油压/出口油压,油温,水压,气压是否在正常的范围内,有无报警出现。
2.9 检查是否有漏油(必要时打开排渣柜堵头观察),检查漏水及震动和噪音。
3.停机
3.1 按程序停机按钮—STOP, 分油机自动进入停机程序。
3.2 等待面板显示”STANDSTILL”时,分油机停止转动,关闭加热器。
3.3应急关停:按下现场盘红色应急关停按钮,再次启动前需复位。
分油机管理
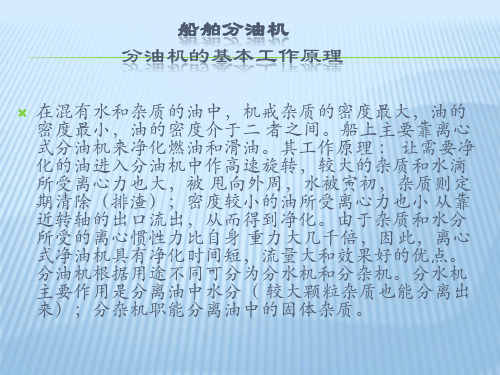
分水机和分杂机主要结构相同,差别是: 1.分水机盘架有一圈分配孔,分杂机盘架无 孔; 2.分水机有比重环和出水口,出油口;分杂 机只有出油口,不需要比重环。 3.因此,二者只需更改个别元件即可互换。例 如:分杂筒的无孔盘架 有孔盘架 (分水筒), 分杂机的厚颈盖 和分杂机的分杂颈盖 分水 机的颈盖和比重环, 就可以将分杂机改装为 分水机。
分油机的核心部件是分离筒,分离筒本体由立 轴带动高速旋转(一般转速为6000-- 8000 rpm),分离筒内有若干不锈钢分离盘,盘厚 为0.4--1.5mm,盘的间距约0.5 mm---1.0mm,迭 套在盘架上。盘架于分离筒底盘,本体间彼此 有销固定,以其旋转 分离筒成伞状,其中心 角 2a=60--100度之间。分水机的分离盘靠外 边缘附近开 有若干分配孔。
柴油 40度 润滑油(无添加剂) 65--75度 重柴油 40--60度 燃料油 75----95度 分油机分燃油时,燃油密度最好小于0.98。 若燃 油密度接近于1.0 ,为了便于分 离水分,再分油 机前应使用疏水添加剂去掉油中的乳化泡沫。由 于某种原因燃油 中水分较多,特别是当燃油中混 入海水时,乳化泡沫非常多。,呈黄褐色粘稠状 分油机根本无法分离。出现这种情况应使用疏水 添加剂。
分水机的盘架在距离外边缘1/3径向长度处有分 配孔,正好与分离盘上的分配孔相 对,大颗粒杂 质和水滴被甩向外边,净油流到转轴中心排出分 离筒。在高速旋转的 分离筒中,油和水必定分层, 形成油水分界面;一般认为油水分界面在靠近分 离盘 的外边缘处是最适宜的,因为这样分离过程 的流动距离可以较长。但是,油水分界 面实际上 是以转轴中心线为轴线,以分离盘外边缘到轴线 的距离为半径的圆柱面。 实际分油过程由于工作 条件的变化,会引起油水分界面向轴心移动或向 外移动。
- 1、下载文档前请自行甄别文档内容的完整性,平台不提供额外的编辑、内容补充、找答案等附加服务。
- 2、"仅部分预览"的文档,不可在线预览部分如存在完整性等问题,可反馈申请退款(可完整预览的文档不适用该条件!)。
- 3、如文档侵犯您的权益,请联系客服反馈,我们会尽快为您处理(人工客服工作时间:9:00-18:30)。
1.2 装置 时间装置组成除控制箱外,安装相应的管路。包含脏油、水、和分油机操作水、干净油和排出水监
视装置以及必要的装置。
1.5 工作模式:
开关 S7 设定“P”分油、“CL”澄清“PS”分油机串联操作,控制程序能够提供以下操作模式:P=
净化器
CL=澄清器 PS=串联操作两部分油机两级分油
2. 存储程序控制器
Timig unit type VESA-1
1SA 系列分油机排渣自动控制和监视。利用电子储存程序控
制分离筒在预定排渣时间中是否优先置换分离筒的产物、是否随后冲洗排渣。如果故障发生,发出
声光信号,并在控制板上用发光二极管指示故障部分(light emitting diode LED )。排渣时间决定于 液体中的固体含量不产生巨大影响,以保证分离效果和避免排渣时损失。
以完成的次数或已经过的预设时间,预设的程序时间决定于电源的频率。
5.1 一位数字调节和显示器 EM 09.1.01 PART NO. 005-4067-020 该调节器是不排渣冲洗程序的排渣次数。
5.2 两位数字调节器和数字显示器 EM 10.1.0.1 PART NO. 0005-4067—040
① 电源供给板:电源提供部分
② 控制部分:装要 EPROM 记忆存储的程序。 ③ 一个或多个外部输入板
④ 一个或多个外部输入板 ⑤ 一个或多个内部输入和输出电路。
5. 模块装置: ① 电源部分: NT 015-220 part NO. 0005-3788-020 (220V)
输入电压 220V,40—60HZ +10%/-20% 输出电压: 12VDC 电源消耗:50VA
设定水封水脉冲时间间隔,以保证分离筒的密封。 5.3 三位数字调节器和数字显示器 EM 11.1.0.1 part no. 0005-4067-010
设定分离时间,总排渣之间的时间间隔。
5.4 三位数字调节器 EM 05.1.2.1 part no. 0005-4068-000
工作水脉冲时间,总排渣期间分离桶打开的时间。
工作水脉冲:打开脏油之前的工作水脉冲,剩余的预定时间。
分油:起动分油时间计时,工作水脉冲计时。给油阀打开。
15. 没有排放,冲洗排渣的的总排渣:
操作主电源开关:S1,时钟 LED 闪,马达指示灯亮,数字显示器读数为零,接通 S3‘冲洗’。
起动排渣程序:(等待) S4 ‘separating’ 程序 LED 亮,起动 d1。
13. 没有置换和冲洗排渣的总排渣
操作主电源开关:S1 时钟 LED 闪,马达指示灯亮,数字显示器读数为零。
起动排渣程序:(等待) S4 ‘separating’ 程序 LED 亮,起动 d1。
排渣:
时间继电器 d3 工作水阀 LED 亮,分离桶通过工作水排渣。
等待:时间继电器 d4 运行,分离桶速度恢复。
D4 22sec 22sec 25sec 等待,分离桶速度的恢复,
D5 3sec 3sec
3sec
补水,分离桶补水时间,V2 亮
D6 30sec 30sec 30sec 过渡时间,排渣后误警报的过渡时间
D7 30sec 30sec 30sec 延时,激发误警报的延时.
D8 5sec 5sec
5sec
使用时间自动程序,分油速率的变化和燃油中所含杂质来计算分油时间的设定,如果这些参数
没变化,就没有必要进行计算。分油时间决定于燃油中含杂质。
8. 水封水时间设定:分离桶中水量会因蒸发而减少,在分油过程中间隔的补充水以防止分离桶过
早打开。水量的调整是通过合适的时间继电器,它通过控制工作水管线上的电磁阀 V3。另外,
达 电流增加。测量继电器在预定时间内监视增加的电流。如果油渣量不增加,那么是工作水量
不 足(电磁阀 V3 故障,水压太低,滤器脏)或摩擦片磨损过大。这种故障可以从“工作水”
故障指 示出来。同时程序中断,给油电磁阀切断,并发出声光警报。
11.2 调整值:
① 监视时间:分离桶开始排渣和检测马达电流峰值之间的时间,增加一秒作为监视时间 d8。
监视排渣,如果故障 LED V3 闪亮
12. 时间单元的设定和操作
当主电源开关闭合,发光二极管 ‘~’闪亮指示时间单元处于可用状态.此时数字指示器指示灯发亮
并指示为零。在主开关闭合的同时警报系统投入。
起动程序前必须设定分油机操作模式:
① 选择开关 S7 在 P、CL 或 PS。
② 选择开关 S2 在‘DISPLACEMENT’如果在程序要求在总排渣之前进行置换。
排渣开始后电流恢复时间 4 秒,设定 d8 为 5 秒。
② 测量继电器 K1: 测量继电器是电位计“AN”调整动作值“AB”调整释放值。
‘AN’0.1-1A 电流峰值 IMAX=20A IAN=IMAX-2=18A。 ‘AN’的调整值 EAN=IAN/r=18/50=0.36A
‘AB’ 0.5—0.95 EAB=0.95XEAN=0.95X0.36=0.342A ③ 时间继电器的设定:
6.1.2 排渣调节的条形图:
a) 总排渣没有置换和冲洗排渣
分油
等待 d1
置换 d2
排渣 d3
等待 d4(分离桶速度恢
复)
给油 d5
b) 总排渣定期置换,没有冲洗排渣
分油
等待 d1
置换 d2
排渣 d3
等待 d4(分离桶速度恢
复)
给油 d5
c) 总排渣定期置换,随后冲洗排渣
分油
等待 d1
置换 d2
排渣 d3
继
基本设定
电 器 OSA7- OSA-20 OSA-35
功能
D1 10sec 10sec 10sec 等待,S4 动作开始排渣程序,LED 发亮
D2 5sec 5sec
1sec
置换,用水对分离桶进行置换 V2 发亮
D3 10 sec 10sec 10sec 排渣,在总排渣期间分离桶打开的时间 V3 亮 工作水
工作水脉冲领先于给油阀动作。
9. 选择“冲洗排渣” 选择开关 S3 置于“冲洗”位置。当 S3 置于 ON 位置,每次总排渣后没必
要进行冲洗。预设排渣次数在一位数字调节器中显示冲洗前总排渣次数。
10. 选择监视排渣
11. 1 监视排渣的目的:当采用总排渣操作时,分离桶中的固体物质增加会导致分离桶速度下降,马
到中央处理单元(开关、按钮等)和输出控制相应的电气元件(电磁阀、泵的控制、警报等)。
输入(DC 24v)和输出(DC24v 或 24-240v AC 决定于功能)是同传统的控制系统一样的电气—机
械。
可调整的时间程序通过对数字调节器的输入进行赋值。这些属于内部输入和输出。
电子控制单位(KSPS 145)是根据实际功能采用所有元件装在印刷电路板上标准设计 2.1 结构:电子控制单元(KSPS145)是安装在控制箱的门和压进的保护窗。数字调节器、数字指示、 袖珍指示和发光二极管装在保护窗的前面以便进行调节或指示程序次序。控制元件(开关、按钮开
起动排渣程序:(等待) S4 ‘separating’ 程序 LED 亮,起动 d1。
排放:起动定时器 d2,补水和置换水电磁阀 LED 亮,V2 打开。
排渣:定时器 d3‘排渣’启动,工作水阀打开 V3.
等待:定时器 d4 启动,分离桶速度恢复。
补水:(分油模式)定时器 d5 启动,补水和置换水电磁阀打开,v2.
排渣:定时器 d3‘排渣’启动,工作水阀打开 V3.
5.5 二位数字调节器 EM08.3.0.1 part no. 0005-4068-010 辅助功能。
5.6 二位数字调节器 EM 07.3.0.1 part no. 0005-4068-020 辅助功能。
6. 排渣程序 对分离桶必须进行定期的排渣,要结合产生物和程序的情况。VESA-1 时间单元通过选择开关来
等待 d4(分离桶速度复)
给油 d5
d) 总排渣没有置换,随后冲洗排渣
分油 等待 d1 置换 d2 排渣 d3 等 待 d4( 分 离 桶 速 度 恢 复) 给油 d5
6.2 选择操作模式 6.2.1 单台操作: a) 开关 S7 置于 “P” 时间单元使分油机处于分油程序。 b) 选择开关 S7 置于“CL”:时间单元按照“澄清”程序,排渣程序中给油顺序是自动的。 c) 选择开关 S7 置于 “PS”对于单台操作按照 a)。 7. 分离时间的设定:
关)安装在保护窗的下面。外部主要的接线都在控制箱中,包括: ① 分离电路的电子输入的电源 DC24V. ② 监视分油机排渣的电流测量继电器 0.1—1A。 ③ 电子输出抗干扰的 RC 元件。 ④ 控制电路的自动切除电路。 3. 安装 控制箱:时间单元安装在墙上或接近分离机的支持架。如果可能,安装位置应避免阳光的直射,其
八路无延时 输入正极信号 24vDC, -20/+10%,16mA 24V 输入开关电压 17V DC 电流信号是通过光电偶合传输, ⑤ 输出模板 4.02.200.209 part NO.0005-4037-010
八路输出,八个正常开路和一个共用,开关容量:电阻负载 6A≤250vAC 感性负载 2.5A≤250V ⑥ 输出模板:4.02.200.207 part NO.005-4037-000
这个插入摸板,覆盖散热片,提供电源给电子控制装置。同时有元件监视工作状况和功能。保
证在工作时散热片覆盖。
② 控制部分 KSTE-KS-1K-SM:PART NO. 0005-4055-010 中央逻辑单元(CLU) 石英时钟脉冲发生器,1024 字容量,周期 5MS, 数据或程序:紫外线擦写
EPROM。 ③ 输入模板 4.02.200.212 part no. 005-4043-000
注水:时间继电器 d5 有电,补水和置换水电磁阀有电,给油在分油程序。