工业工程IE与现场改善
精选IE现场改善手法mcm

改变分球器的次序,减少游隙位瓶颈。
改用其它方法
以手工装钢球改用自动机器装。
改用其它材料,工具
用铁质的容器改用塑料的,以免破坏钢球的外观。
简化 Simplify
连接更合理
改变布局,使动作连接更顺畅
更加简单
不用思考.制定.采用Sample检查外观
去除多余的动作
一次性取更多合适的物料,减少取放次数。
生产设备的维护改善
5.2.6 给油口盖子通气孔是否阻塞?5.3 用鼻子闻 5.3.1 气门阀运作时,是否有异味?5.4 用手摸 5.4.1 马达外表是否有异常的发热? 5.4.2 马达是否有异常的振动,转动是否异常? 5.4.3 各部的螺丝是否有松动现象? 5.4.4 各处配管是否有交叉接触? 5.4.5 各部配管是否有磨损的状况? 5.4.6 设备各部是否有漏水,漏油的现象? 5.4.7 若有漏水,漏油擦干净看看状况是否严重?
六.快速切换(换型号)的改善
6.1 快速切换的两种方法 6.1.1 减少切换次数?(如:合理的安排生产计划,包括型号,设备,人员的熟练度) 6.1.2 减少单次切换时间6.2 改善步骤 6.2.1 内作业:必须在机器停止状态下才能进行的作业。 6.2.2 外作业:机器运转时也可能进行的作业。 6.2.3 将内作业转换成外作业。 6.2.4 缩短内作业和外作业的时间。
Most(梅纳德)动作分析
7.3 工具使用动作 ABG ABP U ABP A 取工具 置工具 用何工具 整理工具 返回 八.动作经济原则8.1 肢体使用原则 8.1.1 双手开始结束动作或手脚并用。 8.1.2 双手动作对称方向(蛙泳式双手工作) 8.1.3 身体的动作应在最低等级的动作来进行(身体动作幅度越小越好,时间越短越好) 。 8.1.4 动作姿势稳定。
abd_0504_工业工程与现场改善--资料
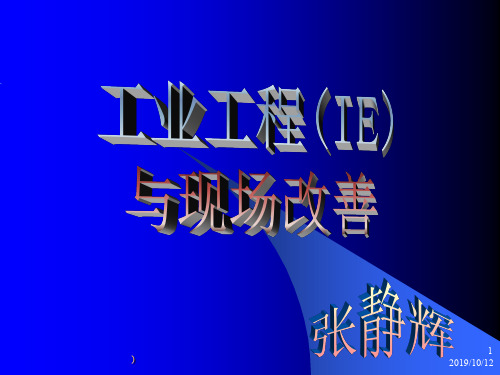
2、手握部分,设计成便于抓起的形 状。
3、在可见部位设置调整系统,使调 整轻松方便。
4、机器的运动方向运操作方向同
1、材料和工具放在作 业者面前固定的位置。
2、材料和工具按作业 顺序的要求而摆放。
3、材料和工具按容易 作业的状态而摆放。
要兼顾两手同时 都能作业而摆放
只要作业方 作业位置的高度调至最佳状态
便,作业领 域越小越好。
1、利用便于零件取拿 的容器和器具。
2、将两个工具合二为 一。
3、选择不需怎么调整 就能使用的夹具。
)
14 2019/10/12
运用统计数据、报告分析,找出问题点。
5.00% 4.50% 4.00% 3.50% 3.00% 2.50% 2.00% 1.50% 1.00% 0.50% 0.00%
X²» Á¼ ÂÊ Y²» Á¼ ÂÊ
ÇÐ ÚÆ »Ò
ÇÐ ÚÆ þ¶
ÇÐ ÚÆ ýÈ
ÇÐ ÚÆ ÄË
ÇÐ ÚÆ åÎ
现场改善的内容
现场改善的内容也就是“发现问题,改进绩效”。 只要认为有问题就可以进行改善。
4
)
2019/10/12
改善管理技术
——[管理]就是要[改善],有[改善]才谈 得上[管理]。PDCA管理循环,给我们的 启示就是不停的改善,永无休止的追求 完美。
——[科学的管理]就是要能够利用近代科 学管理的改善技巧,来进行实际的改善 工作
常用改善技术
5
)
2019/10/12
常用改善技术
一般性
5W2H法 脑力激荡法
愚巧法
比较法
QC7手法
层别法
柏拉图法
法直方图法 管制图法
IEECRS四大原则

第一节 文明生产
一、现场文明生产的含义
是指在生产现场管理中,要按照现代工业生产的客观 要求,为生产现场保持良好的生产环境和生产秩序。 它是生产现场定置管理行为以及“5S”活动的基本 出发点和落脚点。
二、文明生产的意义
是现代工业生产本身的客观要求 是培养职工大生产的意识和习惯,加强精神文明建设
的需要
1.A状态:良好状态 2.B状态:需要改善的状态 3.C状态:需彻底改造的状态
定置方法
1.固定位置
– 即场所固定、物品存放位置固定、物品的信息媒介 物固定。
2.自由位置
– 即相对地固定一个存放物品的区域
信息媒介同定置的关系
ቤተ መጻሕፍቲ ባይዱ一)引导信息
– 引导信息告诉人们“该物在何处”,便于人与物结 合
1、 定义:定置管理是企事业单位在工作现场活动中研究人、物、
场所三者关系,科学地将物品放在场 所(空间)的特 定位置的一门管理科学。
2、类型:
a) 全系统定置管理: b) 区域定置管理: c) 职能部门定置管理: d) 仓库定置管理: e) 特别定置管理:
3、定置管理内容
这里所说的内容就是根据不同位置进行设计的定置内容。 3.1 生产厂区的定置内容 3.2 车间定置内容 3.3 库房定置内容 3.4 办公室定置内容
现场文明生产的内容
(1)严格劳动纪律.遵守操作规程和安全规程; (2)保持厂区和车间内的清洁和卫生; (3)厂区绿化,消除三废(废水、废气、废渣)的污染; (4)工作地布置合理,物料堆放整齐,便于生产操作。 (5)配备必要的工位器具; (6)坚持安全生产,消除各种事故隐患。
第二节 现场定置管理的内容
现场管理的内容
现场管理是多方面的综合性管理,既包括现场 生产的组织管理工作,又包括落实到现场的各 项专业管理和管理基础工作。
现场改善的“神兵利器”—IE七大手法(上)

2021/10/10
27
防呆法的概念
防呆法:又称愚巧法 (Fool-Proof)
指连愚笨的人也不会做错事的设计方法
狭义:如何设计一个东西,使错误绝不会发生。 广义:如何设计一个东西,而使错误发生的机会减至最低的程度。
因此,更具体的说“防呆法”是: • 具有即使有人为疏忽也不会发生错误的构造——不需要注意力。 • 具有外行人来做也不会错的构造——不需要经验与直觉。 • 具有不管是谁或在何时工作都不会出差错的构造——不需要专门知
精益生产=IE+物流+计划+质量+生产+老板领导力+中层管理+基层执行力+全员参与
2021/10/10
14
IE与精益的关系
IE是技术,精益是目标
IE作为一个科学管理工具,是现代任何管理思想/方式 (精益生产方式)成功必不可少的一个工具
IE是精益的重要组成部分 IE是完成精益生产的工程基础 精益是IE运用到极致的体现
五五法
2021/10/10
IE七大手法简介
动改法
双手法
19
IE七大手法简介
人机法
流程法
抽查法
2021/10/10
20
单元小结
IE是什么? 他和微软浏览器有关系吗?
七大手法口诀 “走(流)动的五个人抽双防烟”
2021/10/10
21
IE七大手法运用场景及技巧
2021/10/10
22
防呆法
2021/10/10
例:交通红绿灯、垃圾桶
3、以不同文字标识区分不同功能或物品 例:物品定置标识
2021/10/10
43
九. 警告原理
有异常发生,用声音或光等警告讯号提示
工业工程现场改善方案
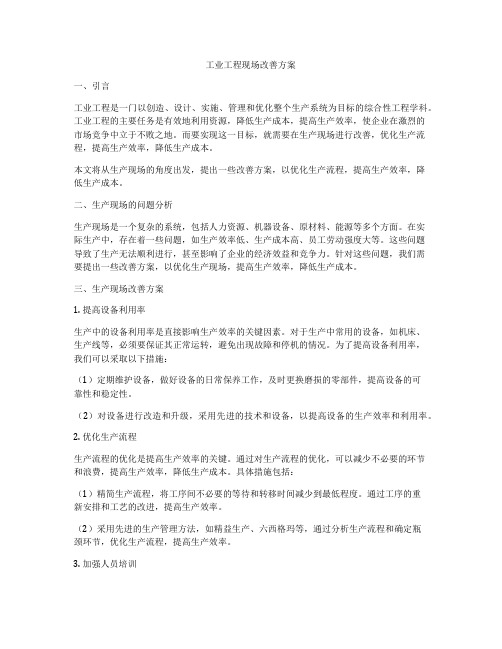
工业工程现场改善方案一、引言工业工程是一门以创造、设计、实施、管理和优化整个生产系统为目标的综合性工程学科。
工业工程的主要任务是有效地利用资源,降低生产成本,提高生产效率,使企业在激烈的市场竞争中立于不败之地。
而要实现这一目标,就需要在生产现场进行改善,优化生产流程,提高生产效率,降低生产成本。
本文将从生产现场的角度出发,提出一些改善方案,以优化生产流程,提高生产效率,降低生产成本。
二、生产现场的问题分析生产现场是一个复杂的系统,包括人力资源、机器设备、原材料、能源等多个方面。
在实际生产中,存在着一些问题,如生产效率低、生产成本高、员工劳动强度大等。
这些问题导致了生产无法顺利进行,甚至影响了企业的经济效益和竞争力。
针对这些问题,我们需要提出一些改善方案,以优化生产现场,提高生产效率,降低生产成本。
三、生产现场改善方案1. 提高设备利用率生产中的设备利用率是直接影响生产效率的关键因素。
对于生产中常用的设备,如机床、生产线等,必须要保证其正常运转,避免出现故障和停机的情况。
为了提高设备利用率,我们可以采取以下措施:(1)定期维护设备,做好设备的日常保养工作,及时更换磨损的零部件,提高设备的可靠性和稳定性。
(2)对设备进行改造和升级,采用先进的技术和设备,以提高设备的生产效率和利用率。
2. 优化生产流程生产流程的优化是提高生产效率的关键。
通过对生产流程的优化,可以减少不必要的环节和浪费,提高生产效率,降低生产成本。
具体措施包括:(1)精简生产流程,将工序间不必要的等待和转移时间减少到最低程度。
通过工序的重新安排和工艺的改进,提高生产效率。
(2)采用先进的生产管理方法,如精益生产、六西格玛等,通过分析生产流程和确定瓶颈环节,优化生产流程,提高生产效率。
3. 加强人员培训员工是生产的主体,他们的工作技能和工作态度直接影响生产效率。
因此,加强人员培训是提高生产效率和降低生产成本的重要措施。
(1)对新员工进行系统的培训,使其熟悉生产流程、设备操作和作业规范,提高工作效率。
IE现场改善流程

IE现场改善流程IE现场改善流程是指在IE部门对现场进行全面的改善和优化,以提高生产效率和降低成本。
IE(工业工程)是一种以科学方法研究生产建设和经营管理等问题的工程学科,它通过分析和优化生产过程,提高资源利用率,提高生产效率和降低成本。
现场改善流程是IE工程师在实际生产现场中进行优化的过程。
IE现场改善流程通常包括以下几个步骤:1.现场观察和数据收集:IE工程师首先对生产现场进行仔细观察,了解生产过程中存在的问题和瓶颈。
他们会收集相应的数据,如生产周期时间,设备利用率,员工效率等。
这些数据将用于确定问题和制定改善计划。
2.现场分析和问题识别:IE工程师通过分析收集到的数据,进一步识别生产过程中存在的问题和瓶颈。
他们将确定导致问题的根本原因,并找出改进的可能途径。
3.改善计划的制定:IE工程师根据问题的识别和分析,制定出改善计划。
改善计划可能包括调整生产流程,改进设备布局,提升员工技能等。
4.改善方案的实施:IE工程师将改善计划付诸实施。
他们会与现场运营人员合作,协调实施过程中涉及的各方面问题。
他们会对改进效果进行跟踪和监控,以确保计划的顺利执行。
5.改善效果评估和反馈:IE工程师会对改善效果进行评估和反馈。
他们会收集数据并进行分析,以了解改善计划的实施效果和效益。
根据评估结果,他们会进一步调整和优化改善计划,以获得更好的结果。
在IE现场改善流程中,需要注意以下几点:1.团队合作:IE工程师需要与现场运营人员紧密合作。
他们需要互相沟通和协调,以确保改善计划的有效执行。
2.持续改进:IE现场改善流程是一个持续改进的过程。
IE工程师需要不断进行分析和评估,以确保改进的持续效果。
3.数据驱动:IE现场改善流程需要依赖于准确的数据。
IE工程师需要收集和分析数据,以支持他们的决策和计划。
4.员工培训和参与:IE现场改善流程需要员工的积极参与和支持。
因此,IE工程师需要提供培训和指导,以提高员工的技能和意识。
龚举成IE七大手法与现场改善教材PPT课件

The branch of engineering concerned with the design, improvement, and installation of integrated systems of people, material, information, equipment, and energy. It draws upon specialized knowledge and skills in the mathematical, physical, and social sciences together with the principles and methods of engineering analysis and design to specify, predict, and evaluate the results to be obtained from such systems.
运用IE七手法 进行务实现场改善
— 消除各种浪费,提升生产力
Industrial Engineering Seven tools
臺灣:新竹市自由路109號翡冷翠大廈8F-2 Tel: 886-3-5312402 Fax: 886-3-5323908 廣州:廣州市白雲大道北12號永泰城B609 Tel: 86-20-86396586 Fax: 86-20-86396590 深圳:深圳市寶安區松崗鎮新汽車站寫字樓 508室 Tel: 86-755-27098545 Fax: 86-755-27098547
班组长管理训练之三--IE7大手法与现场改善

分析一周期作业
▪ 对于作业者及机械, 各自要针对一周期的作业内容, 制作一份工 程流动图。
制作人机分析图表
▪ 使用联合工程分析记号表示各个步骤, 再以“柱”的长度, 表示 所需要的时间, 更进一步为使时间一致化, 利用人机工程图表示 。
改善的四原則
原则
目标
例
取消 合并 重排 简化
不能取消吗? 取消又会变成如何?
检查的省略 配置变更的搬运省略
能否把两种以上的工程合而为一 ?
两种以上的加工,能否同时进 行作业 加工与检查同时进行
能否重排工程?
变更加工顺序,以便提高效率
不能更为简单吗?
作业的重新估计 自动化
取消
▪ 对程序图上的每一项工序都加以审查,确认其保留的必要性, 凡可取消者一律取消,例如:
加工 搬运 检查 停滞
使作业内容具体化
职务名称、人 机械名称、设备名 使作业场所 加工时间、 使加工次序具体化
数、个人名称 称、钻模名称、台 具体化
生产量
等
数等
使搬运内容具体化
同上
搬运设备(起重机、 从何地到何 搬运时间 台车、卡车、吊具) 处
一次的搬运个数、 装货、卸货方法等
使检查项目具体化
同上
检查设备、检查工 具等
▪ 工业工程的主要工作内容: ▪ 1 方法研究(改善工具): ▪ 程序分析 ▪ 作业分析 ▪ 动作分析 ▪ 2 时间研究(衡量标准): ▪ 作业标准和标准工时的测定
二、工业工程的原理
▪ 工作研究的实施步骤: ▪ 1 寻求最经济的工作方法(方法研究、工作改善); ▪ 2 工作方法、材料、工具及设备的标准化; ▪ 3 确定标准工作时间.
IE工业工程现场改善:5防错法

工业工程现场改善:第五章防錯法(愚巧法、防呆法)第一節防錯法概述防錯法日文稱POKA-YOKE,又稱愚巧法、防呆法。
意即在過程失誤發生之前即加以防止。
是一種在作業過程中采用自動作用、報警、標識、分類等手段,使作業人員不特別注意也不會失誤的方法。
一. 防錯法的作用在作業過程中,作業者不時會因疏漏或遺忘而發生作業失誤,由此所致的品質缺陷所占的比例很大,如果能夠用防錯法防止此類失誤的發生,則品質水平和作業效率必會大幅提高。
1. 防錯法意味著“第一次把事情做好”因為防錯法采用一系列方法或工具防止失誤的發生,其結果即為第一次即將事情做好。
2. 提升産品品質,減少由於檢查而導致的浪費防錯法意味著“第一次即把事情做好”,直接結果就是産品品質的提高,與靠檢查來保證品質相比,防錯法是從預防角度出發所采取的預防措施。
而檢查不能防止缺陷的産生,檢查發現的缺陷只能去糾正。
這是一種浪費,防錯法消除了這種浪費。
3. 消除返工及其引起的浪費防錯法會提升産品品質,消除缺陷,這會導致返工次數的削減,由於返工所致的時間和資源浪費便得以消除。
二. 基本原則1. 輕松原則—使作業的動作輕松難以辨認﹑難拿﹑難動等作業即變得難做﹐使作業員疲勞而發生失誤。
可以這樣進行改善﹕(1)用不同顏色區分﹐放大標識—容易辨認例﹕SMT機台指示燈不同顏色代表不同的運行狀況。
(2)加上把手—容易拿例﹕較大型的治具為了減少搬動的動作﹐可考慮加上把手﹐降低動作等級。
(3)使用搬運器具—動作輕松例﹕各種手推車﹐烏龜車等。
2. 簡單原則—使作業不需要技能和直覺需要高度技能與直覺的作業﹐容易發生人為失誤﹐考慮用治具或工具進行機械化﹐使新進人員或支援人員也不容易出錯。
3. 安全原則—使作業不會有危險有不安全或不安定因素時﹐加以改善﹐使其不會有危險﹔馬虎作業或勉強作業有危險時﹐設法安裝無法馬虎或無法勉強作業的裝置。
4. 自動化原則—使作業不依賴感官(1)依賴像眼睛﹑耳朵等感官進行作業時﹐容易發生失誤﹐制作治具使之機械化﹐減少用人的感官來判斷作業。
IE现场改善讲义《工业工程分析》

PPT文档演模板
IE现场改善讲义《工业工程分析》
工程分析中的经济原则
Ø对称反向原则
从身体动作的容易度而言,同一动作的轨迹周期性反复是最自然的,双手或双臂运动的 动作如能保持反向对称,双手的运动就会取得平衡,动作也会变得更有节奏。
•非对称型 •不能操作
PPT文档演模板
•正向对称型 •能操作但没节奏
•反向对称型 •最容易操作
PPT文档演模板
IE现场改善讲义《工业工程分析》
制品工程分析
分岐型 在加工途中发生的作 业分歧,或者在化学 工厂,利用一种原料 制造数种制品的工程, 一系列往往会分岔, 而变成复数系列的工 程,这就叫分岐型或 分解型。
PPT文档演模板
IE现场改善讲义《工业工程分析》
制品工程分析
Ø复合型 Ø途中发生分岐,再度合
音乐必须有节奏才能使人身心愉悦,如果节奏跳跃非常厉害,紊乱的音乐就会使听者觉 得刺耳。 同样,动作也必须保持轻松的节奏; 让作业者在不太需要判断的环境下进行作业,动辄必须停下来进行判断的作业,实际上 更令人疲乏。 顺着动作的次序,把材料和工具摆放在合适的位置,是保持动作节奏的关键。
PPT文档演模板
IE现场改善讲义《工业工程分析》
PPT文档演模板
IE现场改善讲义《工业工程分析》
工程分析中的经济原则
Ø减少动作限制的原则
在工作现场尽量创造条件使作业者的动作没有限制,这样在作业时,心情处在较为放松 的状态。
如:当工作台上摆放零件的容易倾倒,作业者在取零件时动作的轻重必须特别注意,则 取零件的动作效率必大受影响。
•如果:改变容器重心、支撑面、摆放位置等进 行改善,结果会好很多。
Ø 工程分析目的是在工作中发现问题,把它妥当的解决
工业工程基础之动作经济原则与现场改善

工业工程基础之动作经济原则与现场改善一、动作经济原则在工业工程中,动作经济原则是指通过优化动作的方式,提高生产效率和工作质量的原则。
具体来说,动作经济原则是通过减少不必要的动作、优化动作顺序、改善动作方式等方式来实现的。
1. 减少不必要的动作减少不必要的动作是提高工作效率的关键。
人们在工作中常常会有一些不必要的动作,比如多次重复拿放物品、走动次数多等。
通过观察工作过程,并进行分析,可以找出这些不必要的动作,并采取措施进行改进和优化。
例如,在生产线上,工人在拧紧螺丝时,可以通过优化工作台的设计,将螺丝和螺丝刀一起放置在工人手边,减少工人来回拿取螺丝的动作,从而提高工作效率。
2. 优化动作顺序优化动作顺序是指通过调整工作过程中的动作顺序,使得工作更加高效、流畅。
在分析工作过程时,可以根据动作的复杂程度、频次等因素,合理地安排动作的顺序。
举个例子,假设一个仓库的工作人员需要将货物从货架上取下,然后放到运输车上。
如果工作人员先取货、再放货,反复来回多次,那么工作效率就会很低。
而如果将取货和放货这两个动作安排在一起进行,可以减少走动的次数,提高工作效率。
3. 改善动作方式改善动作方式是指通过调整人体姿势、动作方式等方面来提高工作效率和工作质量。
如果工作人员的姿势不合理或动作方式不当,容易导致身体不适、疲劳和错误操作,影响工作效率和工作质量。
比如,在长时间的坐姿工作中,应该保持正确的坐姿姿势,避免驼背或过度弯腰。
同时,使用适合的工作工具、设备,能够减少不必要的力气消耗,提高工作效率。
二、现场改善现场改善是指在工作现场针对存在的问题进行改进和优化,以提高工作效率、减少浪费和改进工作质量。
1. 现场观察现场观察是进行现场改善的前提和基础。
只有通过观察工作现场,了解问题的具体情况,才能有针对性地进行改进措施。
在进行现场观察时,应该充分利用目测、录像、计时等方法,对工作现场进行全面而系统的观察。
通过观察,可以发现一些潜在的问题和浪费,为后续的改进工作提供有力的依据。
工业工程(IE)现场改善方法_图文(精)

3、用以比较改善前及改善后之差异情形
基本符号和应用符号
①加工:表示直接改变制品的物理和化学性质或处于分解装配中。
A35第五道加工工序
A制品的第3道加工工序
以加工为主,同时检验
直径3/8吋
②搬运:表示材料从一处移到另一处。
或
③检验:进行数量或质量的检验。表示数量检验表示质量检验表示数量和质量同时检验,以质量检验为主
•在纸上采用适当的间隔分开人与机,作出垂线。最左方为工人操作时的动作单元及垂线,在此垂线上按所取的时间比例,由上向下记录工人每一动作单元所需时间。当工人操作时用实线(或其它方式表示,空闲用虚线(或其它方法表示,机器同样。•待人与机器的操作时间均已记录之后,在此图的下端将工人与机器的操作时间、空闲时间及每周期人工时数予以统计,供分析时参考。
联合作业分析研究对象:两个或两个以上操作者所进行的分析联合作业分析研究目的:发掘空闲与等待时间,使工作平衡,減少周期時間,获得最大的机器利用率。
联合作业分析研究工具:联合作业图
联合作业图的构成:表头、图表、统计。示例
联合作业图的特点:机器的作业情况画在图表的最左栏
操作者的作业情况画在图表的右栏
利用联合作业图分析的基本原则:
工作A工作A工作A
工作B
工作B
工作B
4h4h
4h
3h
3h
3h 1h
等待
8h 7h
使各个对象的工作进度协调,取消空闲和等待时间,缩短周期。
结论:
1消除工作中的等待,可以有效的缩短工作的周期时间
2如果有多项工作,则同时开展工作,周期时间最短
人机操作图的构成
•以适当的线段的长短代表时间比例。
新IE工业工程技术(公开课)

一)、防错法
防错法举例(2)
发生原因 夹具定位疏忽 加工时不注意而遗忘 加工时疏忽而发生变异 刀具折断,磨损未发现 开关忘记按或按错 设备机械与夹具动作错误 疏忽遗漏配件 它种零件混入 出货零件出错 螺丝忘记锁紧
防错方法 微动开关 计数器,计时器 蜂鸣器,信号灯 扭力计 自动检查装置 自动补正装置 识别板 色别管理/隔离的容器
排除工作中那 些不必要的部 分
3场所 WHERE 在哪里做?非在那里做吗? 4时期 WHEN 何时做?有必要在哪个时期做吗? 如果可能的话, 将其组合或改 变顺序
5人
6方法
WHO
HOW
由谁做?别的人来做不好吗?
怎么样做的?没有比这更经济的手 段吗? 工作简单化
16
4、使用法则
33
6、动作经济原则
是通过对人体动作能力的研究,创立的一系列能最有 效地发挥人的能力的动作原则,由于它能使工作者的 疲劳最少、动作迅速而容易、增加有效的工作量,因 而被称为经济原则。
19
停滞
3、工序型态和分析目的
3.1、型态 。大致可分为4种:(1)直列型 ;(2)合流型 ; (3)分流型;(4)复合型; 3.2、分析的目的。
项次 目 的 发觉工序或作业的配置/顺序/分割/合并是否 适当 发觉是否有不必要的迟延 调查或计测项目 工序能力、作业站工时单位产量 迟延工时
1
2 3 4 5 6 7 8 9 10
一个作业者:一部机械 一个作业者:数部机械 数个作业者共同进行作业的场合 数个作业者:一部机械 数个作业者:数部机械
27
四)、人机分析法
在这种组合下进行作业的场合,往往会发生所 谓的“等待”以及“干扰”问题,为了使作业 的效率提高,改善的方法有“人机分析”、 “共同作业分析”等。 凭分析组合作业的时间经过,经过图,以便找 出“人”或“机械”所造成的“闲荡”,“空 等”,藉此改善作业的方法。
IE七大手法和现场改善技巧

IE七大手法和现场改善技巧课程背景:IE起源于美国,是在泰勒科学原基础上发展起来的一门应用性工程技术学科,强调综合地提高生产率,降低生产成本,保证产品质量,使系统处于最佳运行状态而获得巨大的整体效益。
IE的知识和方法在美日等发达国家已经成为普遍化的理念,通过取消、合并、重排、简化等优化手法不断改进操作流程,形成一系列非常实用的技术、方法及工程程序,是企业通向世界级制造系统,实现企业竞争的必由之路。
课程结合大量实案例及图片,让学员能够把技术与管理进行有机的结合。
学习后可为企业制定出生产标准、劳动定额工时、工艺流程及现场管理优化等进行实务操作。
并根据现代IE 的发展,重点阐述了精益生产系统中解决多品种少批量生产的快速换型以及零缺陷技术实现的重要手段防错法。
课程内容延展到企业经营活动的全过程,追求企业经营有效投入和经济产出的最大化、价值最大化。
课程收益:掌握常用的IE手法和改善技巧。
协助企业进行系统优化。
减少浪费,降低成本。
提高人、机、物利用率。
提升企业综合竞争力。
实现快速而有效的换型。
如何第一次将事情做对。
效率、效益最大化。
课程大纲:第一部分:工业工程概述一、IE的起源、定义与IE工作范畴1、IE的原理与发展历史2、IE技术的核心内容和追求目标第二部分:传统IE——时间研究与方法研究二、IE操作程序图、流程程序图、线图使用与实战技术1、生产流程分析概述2、生产流程分析的语言及记号3、生产流程分析步骤:(包括:作业分析、搬运分析、检验分析、停滞分析、库存分析)4、流程图--数据收集---流程分析---改善方案---标准化5、工艺流程实战分析案例6、作业流程分析案例7、联合作业流程分析案例8、减少工序数量,缩短总作业时间9、人机联合作业10、停滞与等待的分析与改善11、工程流程图案例分析及实战模拟演练三、搬运及布置(Layout)的效率分析与改善1、搬运及场地布置经济原则2、物流原理与搬运合理化3、单元制生产模式与布局改善4、搬运工程分析程序分析5、搬运路径分析线图6、搬运工具设计与选择7、案例研讨四、MOD动作效率分析与改善技术1、动作分析的目的与改善顺序2、动作分析的要领3、动作分析的目的与改善顺序4、运用动作分析提高效率5、运用动作经济原理提高效率6、动作的经济原则7、预定动作标准时间法(PTS)与预定动作测时法(MTO)8、案例分析与实战模拟演练五、标准时间研究与生产线平衡1、时间研究目的与方法2、秒表,记录表,流程分解原则3、标准工时的实际测定及制定4、实测单元测试方法5、时间值记录法6、评比与宽放的设定原则与影响因素7、标准时间的计算、维护及工时的衡量技术8、如何运用标准工时平衡生产线9、标准工时案例分析及模拟实战演练第三部分:现代IE——精益化策略六、精益生产系统概述1、精益生产的理念思想2、精益生产的发展过程及追求目标3、精益生产的技术体系七、快速换型(SMED)实操训练1、准备阶段2、分析现状3、暴露并消除异常4、形成改善思路5、策划改善方案6、实施快速换型改进7、快速换型改进效果跟踪8、巩固快速换型改善成果八、防错防呆法技术应用1、防错法的目的和意义2、防错法的基本原则3、防错法的进行步骤4、防错法的应用原理5、防错法的一般事例6、防错法行业案例分析。
IE重点技术与现场效率改善

◇全面理解工业工程旳发展、工具体系、重点工具旳应用要点◇全面分析公司内部物流、设施规划要素,学习合理设立和优化流程◇全面梳理现场提高效率旳着眼点,致力于多维度效率旳提高◇对学习原则工时构造旳分析、建立环节、时间衡量分析及改善工具◇学习如何结合工具进行动作、流程、人机、布置等基本要素分析◇结合现场分析,研讨如何进行效率提高,达到全员改善共识●课程大纲一 IE简介◇ IE旳发展演变◇ IE发展过程中旳经验和教训◇现场实用IE工具体系◇科学管理旳发展之路◇工具推动过程中旳双赢之道二时间研究◇原则工时旳内涵及构成◇评比及宽放旳设定技巧◇原则工时不原则旳深层因素剖析◇秒表测时旳实践应用诊断◇ MOD测时法◇工作抽样法◇原则工时旳应用诊断三生产效率分析与改善◇生产效率分析与控制PAC◇管理效率旳提高◇工作效率旳提高◇ PAC应用案例剖析◇现场效率提高旳方向诊断◇现场常用旳七大挥霍◇作业原则化与原则化作业四操作效率提高◇基于人机工程旳动作研究◇动作经济旳21个原则◇有关人体动作之原则◇有关工作场地布置之原则◇有关工具设备之原则◇动作经济原则应用案例简介◇常用但需要避免旳危险动作◇间接人员效率旳提高◇多技能储藏◇典型回忆五车间效率提高◇节拍旳概念及其重要作用◇线平衡率与线平衡损失率旳计算与诊断◇生产线平衡旳改善与效率提高◇现场3M分析◇均衡旳内涵及影响◇改善不均衡旳要点◇改善不均衡旳具体措施◇制约产能旳瓶颈因素◇改善瓶颈、提高产能旳技巧◇视频:TOC & DBR六设备效率提高◇设备综合效率旳提高◇时间稼动率◇性能稼动率◇良品率◇设备效率化旳7大损耗◇提高效率之迅速切换◇人机分析图◇人机分析图实践演习◇防错案例分析◇防错之人员防错◇防错之工艺防错。
IE工业工程正确认知
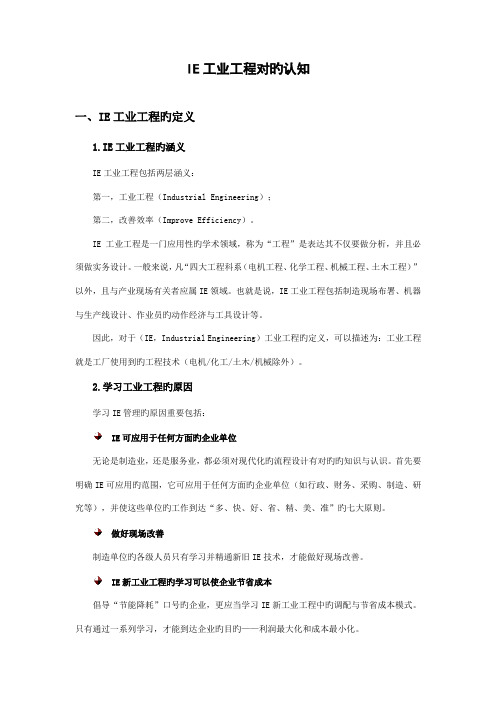
IE工业工程对旳认知一、IE工业工程旳定义1.IE工业工程旳涵义IE工业工程包括两层涵义:第一,工业工程(Industrial Engineering);第二,改善效率(Improve Efficiency)。
IE工业工程是一门应用性旳学术领域,称为“工程”是表达其不仅要做分析,并且必须做实务设计。
一般来说,凡“四大工程科系(电机工程、化学工程、机械工程、土木工程)”以外,且与产业现场有关者应属IE领域。
也就是说,IE工业工程包括制造现场布署、机器与生产线设计、作业员旳动作经济与工具设计等。
因此,对于(IE,Industrial Engineering)工业工程旳定义,可以描述为:工业工程就是工厂使用到旳工程技术(电机/化工/土木/机械除外)。
2.学习工业工程旳原因学习IE管理旳原因重要包括:IE可应用于任何方面旳企业单位无论是制造业,还是服务业,都必须对现代化旳流程设计有对旳旳知识与认识。
首先要明确IE可应用旳范围,它可应用于任何方面旳企业单位(如行政、财务、采购、制造、研究等),并使这些单位旳工作到达“多、快、好、省、精、美、准”旳七大原则。
做好现场改善制造单位旳各级人员只有学习并精通新旧IE技术,才能做好现场改善。
IE新工业工程旳学习可以使企业节省成本倡导“节能降耗”口号旳企业,更应当学习IE新工业工程中旳调配与节省成本模式。
只有通过一系列学习,才能到达企业旳目旳——利润最大化和成本最小化。
1960年左右,工业工程成为大学中旳科系,最初被称为工业工程管理,也可称为产业管理。
IE工业工程发展到目前,应用范围越来越广,甚至可以用到服务业。
例如,剪发行业,假如没有用IE规划时间,就也许挥霍时间;餐饮业中旳麦当劳完全用IE工业工程旳管理方案,这也是麦当劳作业程序非常快旳重要原因。
二、老式IE工业工程旳发展1.1923年科学管理之父泰勒大师旳试验——工具改善【案例】泰勒旳工具改善19世纪末期,管理学刚刚诞生并被应用时,人们对于管理旳见解众说纷纭。
现场改善及IE手法
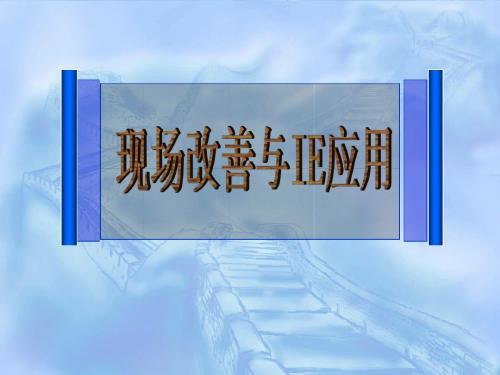
---
IE 用途
客户要求 15H 1H 1 2H 3 4H 4 5H 2H 6 8H 2 3H 5 8H 7
17H
12H
IE用途举例
搬运距离减少,提高效率
改善前
装盘部 装盘部 手 推 车 小 汽 车 总库 总库 日用库
改善后
四、 IE手法在现场改善中应用
1生产流程分析与作业程序分析—价值流图 2布局与搬运效率分析与改善 3人机程序分析—防呆手法,合理配置 4线平衡与时间研究—找到瓶劲,取得突破 5动作经济原则—提高效率,降低强度
即为劳累,指作业一 员、机器以及工作的流 程,处在一种费力气的 状态下
对策:
1.员工的技能训练,使其成为一名熟练工
2.利用夹治具或机器来替代人力作业
3.利用动作经济原则来改善作业的劳动强度
本节总结
七大浪费? 三无工程? 现场浪费认识?
三、IE是什么?能做什么?
IE ----工业工程,industrial engineering ---- 改善效率 Improve efficiency
3.U型布局 4.综合式
1 2 3
直线式与U型布局比较
搬运距离
省人化
并列式,
1人多机
半流线 与 流线式
实例:
去半成品库
来自料堆
磨床 6
磨床 5
铣床 2
磨床 4
车床 1
搓丝 8
磨床 7
车床 3
车床 1
改进:
去半成品库 车床1
来自料堆
车床 3 磨床4 磨床5
铣床 2
节约面积 车床1
磨床 6
1.整理生产工序流程;
2.工序流程中是否存在不经济,停滞现象;
- 1、下载文档前请自行甄别文档内容的完整性,平台不提供额外的编辑、内容补充、找答案等附加服务。
- 2、"仅部分预览"的文档,不可在线预览部分如存在完整性等问题,可反馈申请退款(可完整预览的文档不适用该条件!)。
- 3、如文档侵犯您的权益,请联系客服反馈,我们会尽快为您处理(人工客服工作时间:9:00-18:30)。
作业分解
原封不动地纪录现状作业方法,列出全 部项目明细。(一步一步进行的作业动作)
拿钢笔取下笔套作业分解实例
动作 次序 1 2 3 4
5
动作纪录 动作纪录 时间 作业分类 问题摘要
(左手) (右手)
伸手
等待
抓住钢笔 等待
收回
等待
笔套对准 申向笔套 右手
向左用力 向右用力
1 2019/5/30
工业工程
工业工程(IE)的定义
——IE是藉着设计、改善或设定人、料、机的工作系 统,以求得更高生产力的专门技术。在日本被称为生 产技术或管理工学。
工业工程(IE)的目的
——让企业以最小的投入(包括资金、人力、材料机 器、厂房)得到最大的产出,以至获得最大的效益 (效率高、品质稳定、交期准、浪费少、成本低、)。
出问题。 使用问题检查表,逐条对照找出问题点。 运用统计数据、报告分析,找出问题点。 根据客户或相关工序的反馈信息找出问题点。 运用6S的标准检查现场工作,找出问题点。
10 2019/5/30
通过实际值与期待值的差异发现问题点
105
100
95
90
90
90
85
80
75
70 µÚ Ò» ¼¾ ¶È
现场改善的目的
——消除浪费,提高效率、品质,降低成本。
3 2019/5/30
现场管理与改善的理念
管理与改善的关系
——保持现有的技术和管理水平是管理;突破现有水 平,使之向更高水平提升是改善。所以,改善是突破 现状,产生新价值的开创性努力。因此: ——要成为一流的企业,一流的管理人员,必须将改 善意识完全融入到日常管理之中,实际工作当中没有 必要细分哪是管理,哪是改善,管理就是改善,改善 就是管理。
——7个关键步骤,整理出来形成指导改善开展的方法,就是问 题解决7步法。
作业改善4步骤
——针对一线管理者的工作特点,以最有效的利用现有人力、 工具设备和材料为目的展开,被称为最适合一线管理者的改善 手法。
价值分析
(略)
动作经济原则 消除浪费 问题改善之障碍 相关书籍介绍
7 2019/5/30
13 2019/5/30
使用问题检查表,逐条对照找出问题点。
4M 设备
人员 材料 方法
问题点 设备经常停机吗? 对精度的控制有效吗? 维修点检有正常进行吗? 设备使用方便、安全吗? 生产能力合适吗? 设备配置何布置好不好 是否遵守作业标准? 工作技能足够吗、全面吗? 工作干劲高不高? 作业条件、作业环境如何? 材料品质状况如何? 材料库存数量是否合适? 材料存放、搬运方式好不好? 材料成本如何,能否更便宜? 作业标准内容是否合适? 作业前后的准备工作是否经济高效? 前后工序的衔接好吗? 作业安全性如何?
要因解析的方法(二)
20 2019/5/30
要因解析的方法(三)
突发性不良、慢性不良、周期性不良
༠ⲠµÖ
0.5 0.4 0.3 0.2 0.1
0 -0.1 -0.2 -0.3 -0.4 -0.5
¼à ²â Ç÷ÊÆ ͼ
ʱ¼ä ÍÆ ÒÆ1
3
5
7
9 11 13 15
21
2019/5/30
研讨对策的方法
最主要也是最直接有效的方法是寻找专 业相关人员或有经验的人员商讨解决方 案
集思广益头脑风暴法
在没有合适人选组织商讨解决方案的情况下,组织各类人员针 对相关问题发表自己的看化和意见,不论错对与否,一一纪录 分析,逐步尝试改善。会议中,可以异想天开,随意发表意见, 禁止批评或反对或取笑别人意见。
选择评估可实施的方案,制定行动计划。
22 2019/5/30
Байду номын сангаас
计划实施——落实解决方案
先行获得上级的认同和支持 经过试行阶段对方案进行调整 事先动员、知会相关人员 落实每个人的责任 跟踪日程进度 及时处理意外情况
23 2019/5/30
效果确认——评价改善结果
以改善目标为评估基准 量化的改善前后效果对照 有形效果之外,关注无形效果 留意并消除连带的消极效果 得失反省,不佳效果的再改善
柱状图
ùË ¼Õ ȱýÀ ùË ¼Õ ȱýÀ
50% 40% 30% 20% 10%
0%
1¿Î
· µ ÐÞ ³É ± ¾
2¿Î 3¿Î 4¿Î ²¿ ÃÅ
50% 40% 30% 20% 10%
0%
Ä£ ¾ß
· µ ÐÞ ³É ± ¾
Éè
±¸ ÈË
Ô±²Ù
×÷
¹¤¾ß
²» Á¼ Ïî Ä¿
19 2019/5/30
17 2019/5/30
设定改善目标——预计改善效果的方法
设定明确目标值和达成期限,或根据公 司方针和上级指示要求一致。
预计该目标经过努力是可以达到的,不能是口号。
分阶段设定目标进度
70
60
50
40
30
20
10
0
1 ÔÂ
2 ÔÂ
3 ÔÂ
4 ÔÂ
5 ÔÂ
6 ÔÂ
18 2019/5/30
要因解析的方法(一)
ÇÐ ÚÆ ùÁ
15 2019/5/30
根据客户或相关工序的反馈信息找出问 题点。
客户投诉报告 制程异常报告 作业员抱怨
16 2019/5/30
运用6S的标准检查现场工作,找出问题 点。
有无区分要与不要的东西? 经常使用的东西方便即刻取用吗? 现场环境干净清爽吗? 能否经常保持整洁、无尘的状态? 有遵守规定的习惯吗?
Method(方法、配置、设计)
作业要求明确吗? 公差是否合适? 动作是否最经济?
Man(加工人员、搬运人员、检查人员)
工作积极、态度很高吗? ……
Material(原材料、半成品、消耗用品)
品质稳定吗? 用量合适吗? ……
28 2019/5/30
项目明细设问(二)——动作有 效性和经济性
解决问题的7步法
把握现状 设定改善目标 要因解析 研讨对策 计划实施 效果确认 效果巩固
8 2019/5/30
作业改善4步骤
作业分解 项目明细设问 新方法展开 新方法实施
9 2019/5/30
把握现状——找出问题所在点的方法
通过实际值与期待值的差异发现问题点。 从方针目标与实绩的差异中发现问题点。 与好的部门和岗位相比,用看不惯的眼光找
1、材料和工具放在作 业者面前固定的位置。
2、材料和工具按作业 顺序的要求而摆放。
3、材料和工具按容易 作业的状态而摆放。
要兼顾两手同时 都能作业而摆放
只要作业方 作业位置的高度调至最佳状态
便,作业领 域越小越好。
1、利用便于零件取拿 的容器和器具。
2、将两个工具合二为 一。
3、选择不需怎么调整 就能使用的夹具。
使动作轻松简单 动作要素的数量能否减少?
1、消除不必要的动作。 1、两手同时开始 1、利用身体
2、减少眼睛的转动。
3、将两个以上的动作 组合。
动作,同时结束。 最适合的部
2、两手同时反向 位动作。
对称动作。
2、用最短的
距离动作。
1、动作无限制,只要轻松简单。 2、利用重力和其他力量动作。 3、利用惯性和反向力动作。 4、动作方向转换顺滑进行。
2、手握部分,设计成便于抓起的形 状。
3、在可见部位设置调整系统,使调 整轻松方便。
4、机器的运动方向运操作方向同
5、工具轻便。
34
2019/5/30
动作经济实战注意事项
要以确保品质为大前提。 站在作业者的立场。 只有在工序、作业本身的问题得以改善
ʵ ¼Ê ²ú Á¿ Ä¿ ±ê ²ú Á¿
0 µÚ Ò» ¼¾ ¶È
µÚ ¶þ ¼¾ ¶È
µÚ Èý ¼¾ ¶È
µÚ ËÄ ¼¾ ¶È
12 2019/5/30
用看不惯的眼光找出问题项目。
在生产上属于瓶颈(或问题最多)的工 作。
占大量时间或人工的工作。 反复性的工作。 消耗大量材料的工作。 看起来不合理的工作。 不置不当或搬运不便的工作。
常用改善技术
5 2019/5/30
常用改善技术
一般性
5W2H法 脑力激荡法
愚巧法
比较法
QC7手法
层别法
柏拉图法
法直方图法 管制图法
特性要因图法 查检表
散步图
IE7手法
流程分析法 动作分析法 动作经济原则法
究工作抽查法
人机配置法
时间研
6 2019/5/30
常用现场改善手法
解决问题的7步法
现场改善的内容
现场改善的内容也就是“发现问题,改进绩效”。 只要认为有问题就可以进行改善。
4 2019/5/30
改善管理技术
——[管理]就是要[改善],有[改善]才谈 得上[管理]。PDCA管理循环,给我们的 启示就是不停的改善,永无休止的追求 完美。
——[科学的管理]就是要能够利用近代科 学管理的改善技巧,来进行实际的改善 工作
26 2019/5/30
项目明细设问
项目明细设问(一)——4M条件设问 项目明细设问(二)——动作有效性和经济
性
项目明细设问(三)——作业安全、环境适 宜性
27 2019/5/30
项目明细设问(一)——4M条件设问
Machine(设备、机械、工具 、仪表)
在最大限度使用吗? 充分利用运转间歇时间吗? 精度准确吗?精度范围合适吗