动力总成的高效加工与降成本
车辆改造降本增效方案
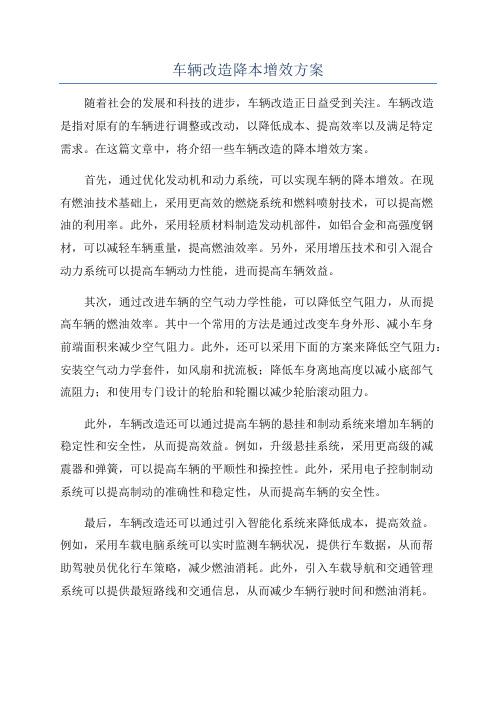
车辆改造降本增效方案随着社会的发展和科技的进步,车辆改造正日益受到关注。
车辆改造是指对原有的车辆进行调整或改动,以降低成本、提高效率以及满足特定需求。
在这篇文章中,将介绍一些车辆改造的降本增效方案。
首先,通过优化发动机和动力系统,可以实现车辆的降本增效。
在现有燃油技术基础上,采用更高效的燃烧系统和燃料喷射技术,可以提高燃油的利用率。
此外,采用轻质材料制造发动机部件,如铝合金和高强度钢材,可以减轻车辆重量,提高燃油效率。
另外,采用增压技术和引入混合动力系统可以提高车辆动力性能,进而提高车辆效益。
其次,通过改进车辆的空气动力学性能,可以降低空气阻力,从而提高车辆的燃油效率。
其中一个常用的方法是通过改变车身外形、减小车身前端面积来减少空气阻力。
此外,还可以采用下面的方案来降低空气阻力:安装空气动力学套件,如风扇和扰流板;降低车身离地高度以减小底部气流阻力;和使用专门设计的轮胎和轮圈以减少轮胎滚动阻力。
此外,车辆改造还可以通过提高车辆的悬挂和制动系统来增加车辆的稳定性和安全性,从而提高效益。
例如,升级悬挂系统,采用更高级的减震器和弹簧,可以提高车辆的平顺性和操控性。
此外,采用电子控制制动系统可以提高制动的准确性和稳定性,从而提高车辆的安全性。
最后,车辆改造还可以通过引入智能化系统来降低成本,提高效益。
例如,采用车载电脑系统可以实时监测车辆状况,提供行车数据,从而帮助驾驶员优化行车策略,减少燃油消耗。
此外,引入车载导航和交通管理系统可以提供最短路线和交通信息,从而减少车辆行驶时间和燃油消耗。
同时,还可以考虑引入无人驾驶技术,以实现自动驾驶和优化车辆调度,进一步提高效益。
总结起来,车辆改造的降本增效方案包括优化发动机和动力系统、改进车辆的空气动力学性能、提高悬挂和制动系统、以及引入智能化系统等。
通过这些方案的实施,可以帮助降低车辆的成本,提高车辆的效益,并满足不同的需求。
随着技术的进步和应用的推广,相信车辆改造领域将会迎来更多的创新和发展。
动力厂降本增加措施
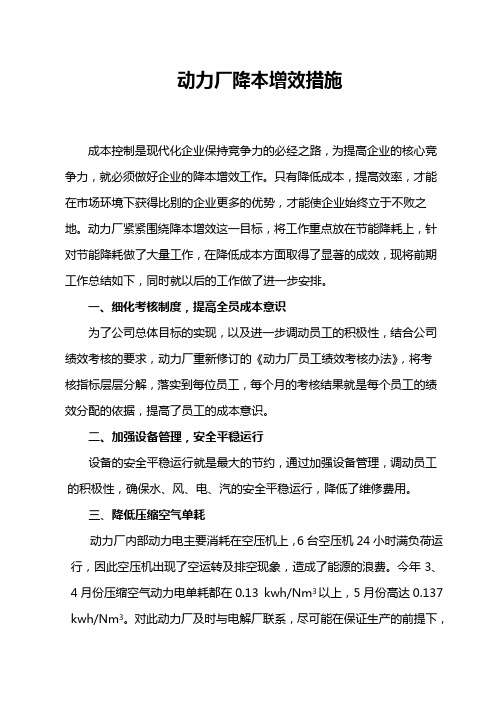
动力厂降本增效措施成本控制是现代化企业保持竞争力的必经之路,为提高企业的核心竞争力,就必须做好企业的降本增效工作。
只有降低成本,提高效率,才能在市场环境下获得比别的企业更多的优势,才能使企业始终立于不败之地。
动力厂紧紧围绕降本增效这一目标,将工作重点放在节能降耗上,针对节能降耗做了大量工作,在降低成本方面取得了显著的成效,现将前期工作总结如下,同时就以后的工作做了进一步安排。
一、细化考核制度,提高全员成本意识为了公司总体目标的实现,以及进一步调动员工的积极性,结合公司绩效考核的要求,动力厂重新修订的《动力厂员工绩效考核办法》,将考核指标层层分解,落实到每位员工,每个月的考核结果就是每个员工的绩效分配的依据,提高了员工的成本意识。
二、加强设备管理,安全平稳运行设备的安全平稳运行就是最大的节约,通过加强设备管理,调动员工的积极性,确保水、风、电、汽的安全平稳运行,降低了维修费用。
三、降低压缩空气单耗动力厂内部动力电主要消耗在空压机上,6台空压机24小时满负荷运行,因此空压机出现了空运转及排空现象,造成了能源的浪费。
今年3、4月份压缩空气动力电单耗都在0.13 kwh/Nm3以上,5月份高达0.137 kwh/Nm3。
对此动力厂及时与电解厂联系,尽可能在保证生产的前提下,随时调整空压机运行台数,以减少压缩空气的排空现象。
空压机运行时间比以前平均减少近500h/月。
压缩空气动力电单耗由最高的0.137kwh/Nm3降低到目前的0.121 kwh/Nm3。
6~8月份的平均单耗为0.1234 kwh/Nm3,月平均供风量为5779万Nm3。
则月平均节约电量为0.0136×5779=78.6万kwh,全年节电943.2万kwh。
若每度电以0.35元计,则每月节约电费为0.35×78.6=27.51万元,全年节约电费330.12万元。
四、提高功率因数,降低无功损耗功率因数是电力部门严格要求的参数,由于整流机组滤波补偿装置没有完全调试完毕,只有部分投运,进一步提高功率因数有很大难度,动力厂结合稳流系统实际情况,在满足系列电流稳定的情况下,调整整流机组档位,降低控制电流,从而有效的提高了功率因数,提高了电能的利用率,降低了用电量。
燃油车动力总成的优化与效率改进
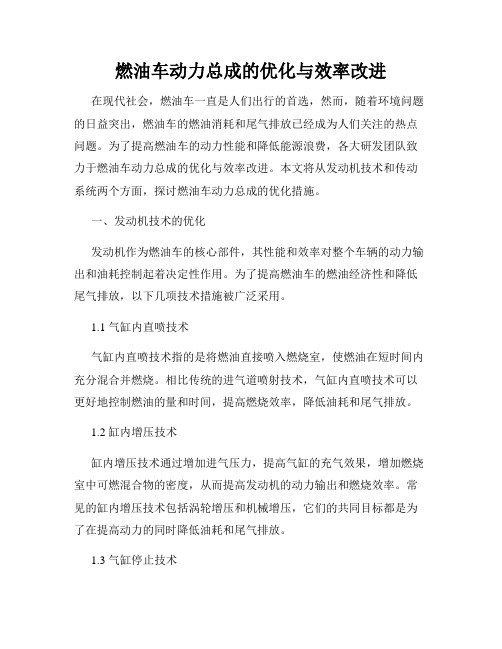
燃油车动力总成的优化与效率改进在现代社会,燃油车一直是人们出行的首选,然而,随着环境问题的日益突出,燃油车的燃油消耗和尾气排放已经成为人们关注的热点问题。
为了提高燃油车的动力性能和降低能源浪费,各大研发团队致力于燃油车动力总成的优化与效率改进。
本文将从发动机技术和传动系统两个方面,探讨燃油车动力总成的优化措施。
一、发动机技术的优化发动机作为燃油车的核心部件,其性能和效率对整个车辆的动力输出和油耗控制起着决定性作用。
为了提高燃油车的燃油经济性和降低尾气排放,以下几项技术措施被广泛采用。
1.1 气缸内直喷技术气缸内直喷技术指的是将燃油直接喷入燃烧室,使燃油在短时间内充分混合并燃烧。
相比传统的进气道喷射技术,气缸内直喷技术可以更好地控制燃油的量和时间,提高燃烧效率,降低油耗和尾气排放。
1.2 缸内增压技术缸内增压技术通过增加进气压力,提高气缸的充气效果,增加燃烧室中可燃混合物的密度,从而提高发动机的动力输出和燃烧效率。
常见的缸内增压技术包括涡轮增压和机械增压,它们的共同目标都是为了在提高动力的同时降低油耗和尾气排放。
1.3 气缸停止技术气缸停止技术是指在车辆行驶过程中,当发动机不需要输出动力时,通过关闭一部分气缸来降低燃油消耗。
通过控制气门和喷油系统,使发动机只工作在所需的气缸数量,可以显著降低低负载情况下的油耗。
二、传动系统的优化除了发动机技术的优化外,传动系统也是提高燃油车动力总成效率的重要环节。
传动系统主要包括变速器和传动轴,其优化措施如下。
2.1 多档变速器多档变速器通过提供多个齿比选择,使发动机能够在不同车速和负载条件下运行在最佳工作点,提高动力输出的效率。
同时,多档变速器还可以降低发动机的转速,减少燃油消耗。
2.2 混合动力系统混合动力系统将燃油发动机与电动机相结合,使其发挥各自优势,进一步提高燃油车的动力性能和燃油经济性。
电动机可以提供额外的动力输出,并在制动过程中回收能量储存起来,减少能源浪费。
电动汽车系统成本、尺寸减半?TI集成动力总成解决方案做到了
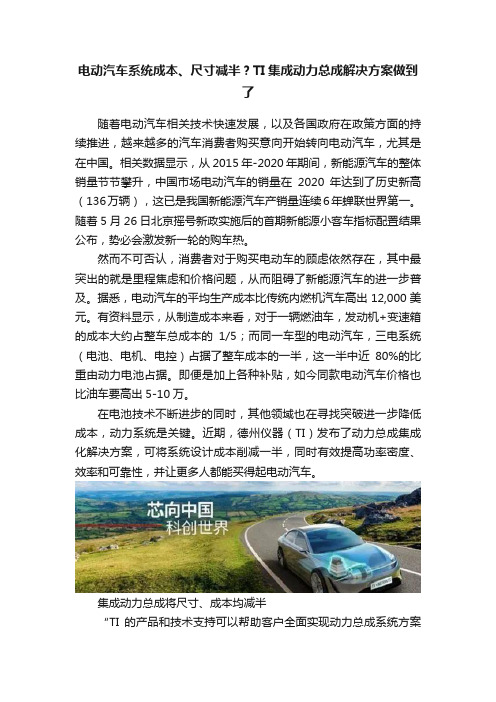
电动汽车系统成本、尺寸减半?TI集成动力总成解决方案做到了随着电动汽车相关技术快速发展,以及各国政府在政策方面的持续推进,越来越多的汽车消费者购买意向开始转向电动汽车,尤其是在中国。
相关数据显示,从2015年-2020年期间,新能源汽车的整体销量节节攀升,中国市场电动汽车的销量在2020年达到了历史新高(136万辆),这已是我国新能源汽车产销量连续6年蝉联世界第一。
随着5月26日北京摇号新政实施后的首期新能源小客车指标配置结果公布,势必会激发新一轮的购车热。
然而不可否认,消费者对于购买电动车的顾虑依然存在,其中最突出的就是里程焦虑和价格问题,从而阻碍了新能源汽车的进一步普及。
据悉,电动汽车的平均生产成本比传统内燃机汽车高出 12,000 美元。
有资料显示,从制造成本来看,对于一辆燃油车,发动机+变速箱的成本大约占整车总成本的1/5;而同一车型的电动汽车,三电系统(电池、电机、电控)占据了整车成本的一半,这一半中近80%的比重由动力电池占据。
即便是加上各种补贴,如今同款电动汽车价格也比油车要高出5-10万。
在电池技术不断进步的同时,其他领域也在寻找突破进一步降低成本,动力系统是关键。
近期,德州仪器(TI)发布了动力总成集成化解决方案,可将系统设计成本削减一半,同时有效提高功率密度、效率和可靠性,并让更多人都能买得起电动汽车。
集成动力总成将尺寸、成本均减半“TI的产品和技术支持可以帮助客户全面实现动力总成系统方案的集成。
我们预计集成化的方案可以帮助整个系统的尺寸和成本都降低一半。
” 德州仪器中国区汽车业务部现场技术应用经理周东宝表示。
如何实现减半的呢?周东宝指出有四个方面:·电驱动系统多合一的集成化的解决方案通过共享外壳的耦合以及冷却系统,减少了连接器的数量;·通过更进一步的共享控制电路以及共享功率电路等方式,有效地降低电驱动系统的体积、重量和成本,同时提高电驱动系统的功率密度;·更好地实现轻量化,有助于延长电动汽车的续航里程;·通过整体上对系统进行热性能的优化,保证系统的可靠性。
机加工降本增效的方法和措施
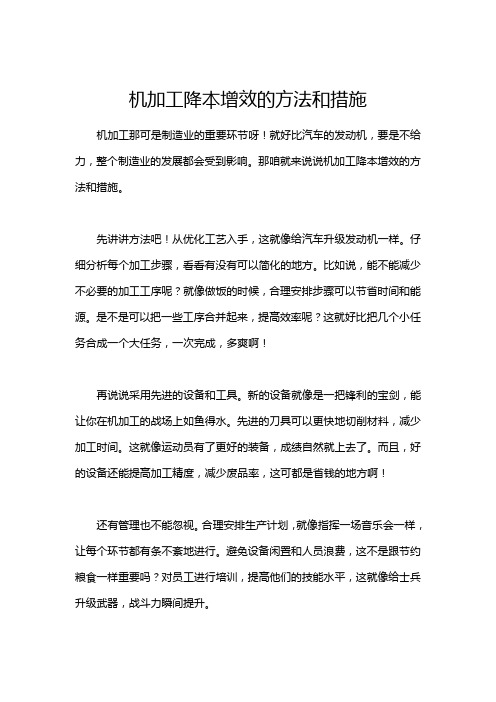
机加工降本增效的方法和措施机加工那可是制造业的重要环节呀!就好比汽车的发动机,要是不给力,整个制造业的发展都会受到影响。
那咱就来说说机加工降本增效的方法和措施。
先讲讲方法吧!从优化工艺入手,这就像给汽车升级发动机一样。
仔细分析每个加工步骤,看看有没有可以简化的地方。
比如说,能不能减少不必要的加工工序呢?就像做饭的时候,合理安排步骤可以节省时间和能源。
是不是可以把一些工序合并起来,提高效率呢?这就好比把几个小任务合成一个大任务,一次完成,多爽啊!再说说采用先进的设备和工具。
新的设备就像是一把锋利的宝剑,能让你在机加工的战场上如鱼得水。
先进的刀具可以更快地切削材料,减少加工时间。
这就像运动员有了更好的装备,成绩自然就上去了。
而且,好的设备还能提高加工精度,减少废品率,这可都是省钱的地方啊!还有管理也不能忽视。
合理安排生产计划,就像指挥一场音乐会一样,让每个环节都有条不紊地进行。
避免设备闲置和人员浪费,这不是跟节约粮食一样重要吗?对员工进行培训,提高他们的技能水平,这就像给士兵升级武器,战斗力瞬间提升。
那注意事项有哪些呢?首先,可不能盲目追求低成本而牺牲质量。
这就好比买东西只看价格不看质量,最后吃亏的还是自己。
要在保证质量的前提下降低成本,提高效率。
其次,要根据实际情况选择合适的方法和措施。
每个企业的情况都不一样,不能生搬硬套别人的经验。
这就像穿衣服,得合身才好看。
说到安全性和稳定性,那可太重要了。
在机加工过程中,安全是第一位的。
就像开车要系安全带一样,操作设备也要严格遵守安全规程。
定期检查设备,确保设备处于良好的运行状态。
这就像给汽车做保养,只有保养好了,才能跑得稳。
如果设备出了故障,不仅会影响生产进度,还可能会造成安全事故。
那可就悲剧了!机加工降本增效的应用场景可广泛了。
无论是汽车制造、航空航天还是机械加工等行业,都能从中受益。
在竞争激烈的市场环境下,谁能降低成本,提高效率,谁就能占据优势。
这就像跑步比赛,谁跑得快谁就能拿冠军。
装备制造机械企业如何提高生产效率与降低成本
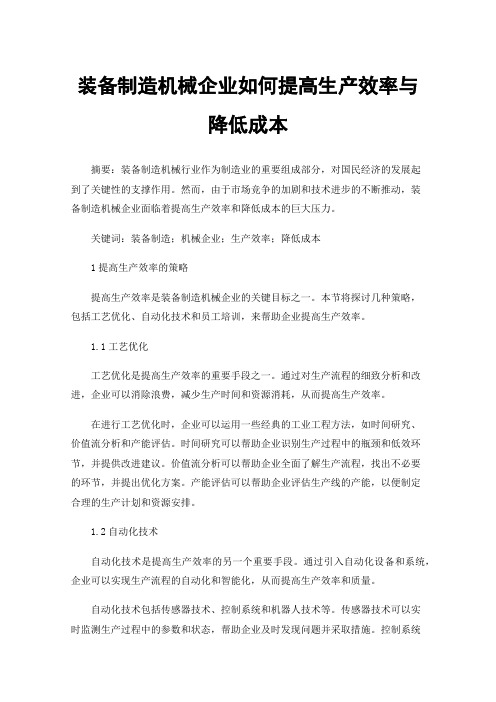
装备制造机械企业如何提高生产效率与降低成本摘要:装备制造机械行业作为制造业的重要组成部分,对国民经济的发展起到了关键性的支撑作用。
然而,由于市场竞争的加剧和技术进步的不断推动,装备制造机械企业面临着提高生产效率和降低成本的巨大压力。
关键词:装备制造;机械企业;生产效率;降低成本1提高生产效率的策略提高生产效率是装备制造机械企业的关键目标之一。
本节将探讨几种策略,包括工艺优化、自动化技术和员工培训,来帮助企业提高生产效率。
1.1工艺优化工艺优化是提高生产效率的重要手段之一。
通过对生产流程的细致分析和改进,企业可以消除浪费,减少生产时间和资源消耗,从而提高生产效率。
在进行工艺优化时,企业可以运用一些经典的工业工程方法,如时间研究、价值流分析和产能评估。
时间研究可以帮助企业识别生产过程中的瓶颈和低效环节,并提供改进建议。
价值流分析可以帮助企业全面了解生产流程,找出不必要的环节,并提出优化方案。
产能评估可以帮助企业评估生产线的产能,以便制定合理的生产计划和资源安排。
1.2自动化技术自动化技术是提高生产效率的另一个重要手段。
通过引入自动化设备和系统,企业可以实现生产流程的自动化和智能化,从而提高生产效率和质量。
自动化技术包括传感器技术、控制系统和机器人技术等。
传感器技术可以实时监测生产过程中的参数和状态,帮助企业及时发现问题并采取措施。
控制系统可以对生产设备进行精确控制,提高生产过程的稳定性和一致性。
机器人技术可以代替人力完成繁重、危险或重复性工作,提高生产效率和安全性。
1.3员工培训员工培训是提高生产效率的关键因素之一。
通过为员工提供系统的培训和学习机会,企业可以提高员工的技能水平和工作效率,从而推动整个生产过程的改善和提高。
员工培训可以包括技术培训、管理培训和团队合作培训等。
技术培训可以帮助员工掌握先进的生产技术和操作方法,提高工作效率和质量。
管理培训可以帮助员工提升管理和领导能力,更好地组织和协调生产活动。
如何提高动力系统的工作效率
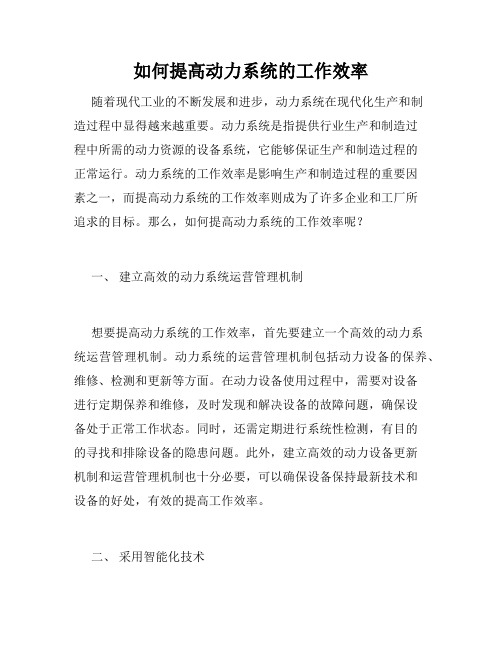
如何提高动力系统的工作效率随着现代工业的不断发展和进步,动力系统在现代化生产和制造过程中显得越来越重要。
动力系统是指提供行业生产和制造过程中所需的动力资源的设备系统,它能够保证生产和制造过程的正常运行。
动力系统的工作效率是影响生产和制造过程的重要因素之一,而提高动力系统的工作效率则成为了许多企业和工厂所追求的目标。
那么,如何提高动力系统的工作效率呢?一、建立高效的动力系统运营管理机制想要提高动力系统的工作效率,首先要建立一个高效的动力系统运营管理机制。
动力系统的运营管理机制包括动力设备的保养、维修、检测和更新等方面。
在动力设备使用过程中,需要对设备进行定期保养和维修,及时发现和解决设备的故障问题,确保设备处于正常工作状态。
同时,还需定期进行系统性检测,有目的的寻找和排除设备的隐患问题。
此外,建立高效的动力设备更新机制和运营管理机制也十分必要,可以确保设备保持最新技术和设备的好处,有效的提高工作效率。
二、采用智能化技术为了提高动力系统的工作效率,企业应采用智能化技术,实现动力系统的智能化精益化运行。
智能化技术对动力系统进行物联网技术的应用、数据统计和分析,可以帮助企业实现整体设备健康诊断,减少设备故障,提高生产效率,提供科学有效的数据支撑。
此外,采用智能化技术,还可以通过预测分析,为企业提供科学的决策依据,优化动力系统的运行状态,提高动力系统的工作效率。
三、加强动力设备的能量回收利用动力系统中的能量回收利用是提高工作效率的重要手段之一。
在生产制造过程中,许多动力设备中存在着浪费能源的情况,通过加强动力设备的能量回收利用,可以大幅度减少浪费,提高动力系统的工作效率。
例如,可以采用污水回收利用、热能回收、风能回收、光能回收等方式,有效地降低系统运行成本,延长设备使用寿命,提高整体效益。
四、动力设备的合理化管理提高动力系统的工作效率还需要采取合理化的设备管理策略。
企业可以通过科学的设备配备和工艺优化,降低运行成本和能源消耗,并结合设备运行状态对设备运用工艺进行进一步优化和合理安排。
动力系统的节能与优化设计
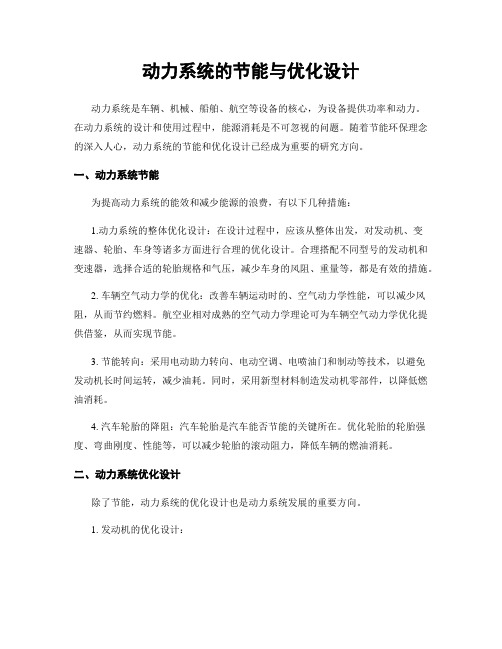
动力系统的节能与优化设计动力系统是车辆、机械、船舶、航空等设备的核心,为设备提供功率和动力。
在动力系统的设计和使用过程中,能源消耗是不可忽视的问题。
随着节能环保理念的深入人心,动力系统的节能和优化设计已经成为重要的研究方向。
一、动力系统节能为提高动力系统的能效和减少能源的浪费,有以下几种措施:1.动力系统的整体优化设计:在设计过程中,应该从整体出发,对发动机、变速器、轮胎、车身等诸多方面进行合理的优化设计。
合理搭配不同型号的发动机和变速器,选择合适的轮胎规格和气压,减少车身的风阻、重量等,都是有效的措施。
2. 车辆空气动力学的优化:改善车辆运动时的、空气动力学性能,可以减少风阻,从而节约燃料。
航空业相对成熟的空气动力学理论可为车辆空气动力学优化提供借鉴,从而实现节能。
3. 节能转向:采用电动助力转向、电动空调、电喷油门和制动等技术,以避免发动机长时间运转,减少油耗。
同时,采用新型材料制造发动机零部件,以降低燃油消耗。
4. 汽车轮胎的降阻:汽车轮胎是汽车能否节能的关键所在。
优化轮胎的轮胎强度、弯曲刚度、性能等,可以减少轮胎的滚动阻力,降低车辆的燃油消耗。
二、动力系统优化设计除了节能,动力系统的优化设计也是动力系统发展的重要方向。
1. 发动机的优化设计:发动机是动力系统的核心,优化设计可以实现轻量化、小型化、高效化等,从而达到提高功率、减少功率消耗和降低机械损耗的目的。
发动机进气系统的流量、排气量和排放量的均衡及系统的控制能力也是优化设计的关键。
2. 变速器的优化设计:变速器是动力系统的重要组成部分,其优化设计可以实现自动化、轻量化、高度物理技术等,从而减少机械损耗。
另外,变速器的寿命和性能也是优化设计的关键,如果能够延长寿命和提高性能,能够为设备提供更长的使用寿命和更好的应用性能。
3. 车辆结构的优化设计:车辆结构的优化设计包括车身结构、轮组结构等等,可以实现降低车重、提高车身硬度、减少燃料消耗等目的。
动力系统优化与能源消耗降低
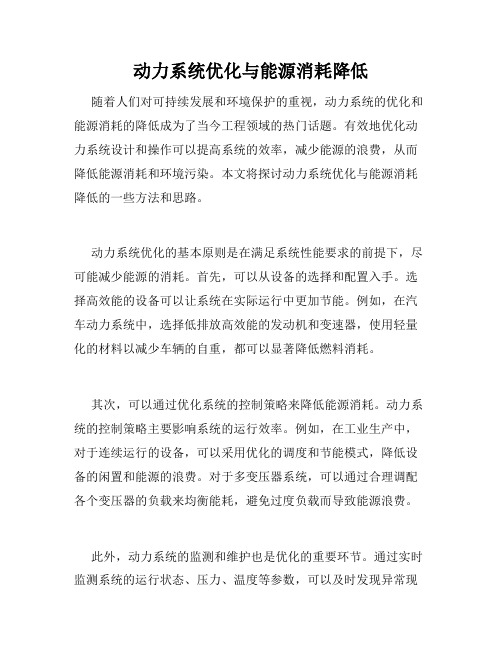
动力系统优化与能源消耗降低随着人们对可持续发展和环境保护的重视,动力系统的优化和能源消耗的降低成为了当今工程领域的热门话题。
有效地优化动力系统设计和操作可以提高系统的效率,减少能源的浪费,从而降低能源消耗和环境污染。
本文将探讨动力系统优化与能源消耗降低的一些方法和思路。
动力系统优化的基本原则是在满足系统性能要求的前提下,尽可能减少能源的消耗。
首先,可以从设备的选择和配置入手。
选择高效能的设备可以让系统在实际运行中更加节能。
例如,在汽车动力系统中,选择低排放高效能的发动机和变速器,使用轻量化的材料以减少车辆的自重,都可以显著降低燃料消耗。
其次,可以通过优化系统的控制策略来降低能源消耗。
动力系统的控制策略主要影响系统的运行效率。
例如,在工业生产中,对于连续运行的设备,可以采用优化的调度和节能模式,降低设备的闲置和能源的浪费。
对于多变压器系统,可以通过合理调配各个变压器的负载来均衡能耗,避免过度负载而导致能源浪费。
此外,动力系统的监测和维护也是优化的重要环节。
通过实时监测系统的运行状态、压力、温度等参数,可以及时发现异常现象并采取相应的措施。
定期对设备进行维护保养,保证其处于最佳运行状态,也能够有效降低能源的消耗。
动力系统优化的另一个重要方面是能源的回收利用。
在系统运行过程中产生的废热、废气、废水等可以通过适当的工艺和设备来进行回收再利用。
例如,在发电厂中,可以利用烟气余热发电,提高系统的整体能效。
在工业生产中,可以将废水经过处理后再次利用,减少对自来水的需求。
这些回收利用的举措不仅能够减少能源的浪费,还可以降低对环境的污染,实现资源的循环利用。
此外,现代科技的进步也为动力系统的优化和能源消耗的降低提供了新的手段。
例如,将人工智能技术应用于动力系统的控制中,可以实现智能化的优化和调度,提高系统的效率和能源利用率。
利用大数据分析和模拟仿真技术,可以对系统的运行情况进行全面的监测和分析,找出系统中存在的问题和短板,提出相应的改进方案。
动力车间能源管理优化与成本节约
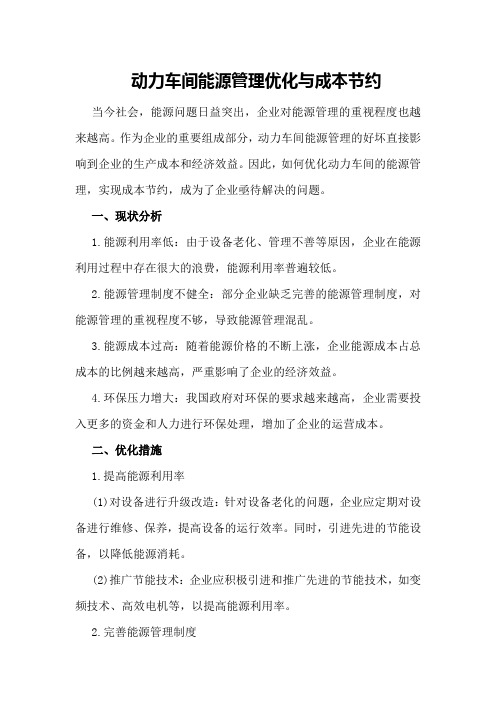
动力车间能源管理优化与成本节约当今社会,能源问题日益突出,企业对能源管理的重视程度也越来越高。
作为企业的重要组成部分,动力车间能源管理的好坏直接影响到企业的生产成本和经济效益。
因此,如何优化动力车间的能源管理,实现成本节约,成为了企业亟待解决的问题。
一、现状分析1.能源利用率低:由于设备老化、管理不善等原因,企业在能源利用过程中存在很大的浪费,能源利用率普遍较低。
2.能源管理制度不健全:部分企业缺乏完善的能源管理制度,对能源管理的重视程度不够,导致能源管理混乱。
3.能源成本过高:随着能源价格的不断上涨,企业能源成本占总成本的比例越来越高,严重影响了企业的经济效益。
4.环保压力增大:我国政府对环保的要求越来越高,企业需要投入更多的资金和人力进行环保处理,增加了企业的运营成本。
二、优化措施1.提高能源利用率(1)对设备进行升级改造:针对设备老化的问题,企业应定期对设备进行维修、保养,提高设备的运行效率。
同时,引进先进的节能设备,以降低能源消耗。
(2)推广节能技术:企业应积极引进和推广先进的节能技术,如变频技术、高效电机等,以提高能源利用率。
2.完善能源管理制度(1)建立健全能源管理制度:企业应制定完善的能源管理制度,明确各部门、各岗位的能源管理职责,确保能源管理工作的有序进行。
(2)加强能源监管:企业应加强对能源使用的监管,定期对能源消耗情况进行检查,对违反能源管理制度的行为进行严肃处理。
3.降低能源成本(1)优化能源结构:企业应根据自身的生产特点,合理配置能源结构,优先使用价格低、效益高的能源。
(2)开展能源采购竞争:企业应积极参与能源采购竞争,争取到更优惠的能源价格,降低能源成本。
4.加大环保投入(1)提高环保意识:企业应提高员工的环保意识,让每个人都认识到环保的重要性,形成全员参与的环保氛围。
(2)引进先进的环保技术:企业应引进先进的环保技术,减少废气、废水等污染物的排放,降低环保成本。
优化动力车间的能源管理,实现成本节约,是提高企业经济效益、降低环保压力的重要途径。
动力电池技术的成本分析与降低策略
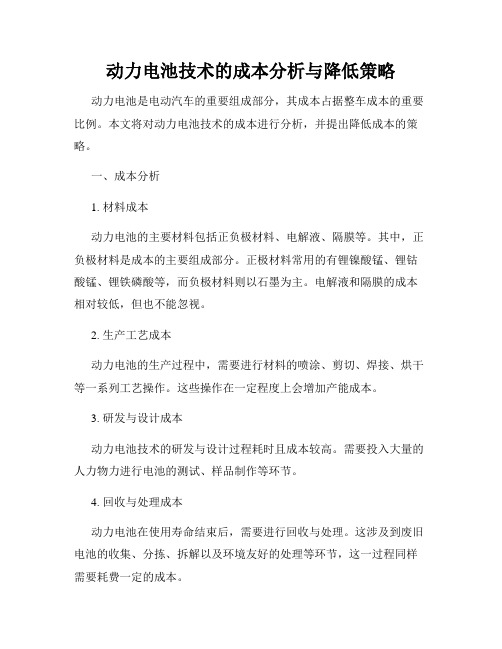
动力电池技术的成本分析与降低策略动力电池是电动汽车的重要组成部分,其成本占据整车成本的重要比例。
本文将对动力电池技术的成本进行分析,并提出降低成本的策略。
一、成本分析1. 材料成本动力电池的主要材料包括正负极材料、电解液、隔膜等。
其中,正负极材料是成本的主要组成部分。
正极材料常用的有锂镍酸锰、锂钴酸锰、锂铁磷酸等,而负极材料则以石墨为主。
电解液和隔膜的成本相对较低,但也不能忽视。
2. 生产工艺成本动力电池的生产过程中,需要进行材料的喷涂、剪切、焊接、烘干等一系列工艺操作。
这些操作在一定程度上会增加产能成本。
3. 研发与设计成本动力电池技术的研发与设计过程耗时且成本较高。
需要投入大量的人力物力进行电池的测试、样品制作等环节。
4. 回收与处理成本动力电池在使用寿命结束后,需要进行回收与处理。
这涉及到废旧电池的收集、分拣、拆解以及环境友好的处理等环节,这一过程同样需要耗费一定的成本。
二、降低成本策略1. 研发与设计策略通过提高电池的能量密度,对正负极材料进行优化,选择更加廉价的材料,并利用合理的设计来减少电池的制造成本。
同时,加强电池的循环寿命测试,以提高电池的使用寿命和可靠性,降低售后维修成本。
2. 生产工艺策略优化生产过程,通过自动化设备和智能制造技术降低生产成本。
同时,提高工艺的稳定性,减少废品率,以提高生产效率。
3. 循环经济策略建立动力电池回收与再利用的体系,将废旧电池进行收集、拆解和资源化利用,以减少电池生产的原材料成本,同时降低回收处理的成本。
政府和企业应该加大对电池回收的投入和力度。
4. 制造规模策略通过扩大电池的生产规模,实现经济的规模效应,从而降低材料采购、制造和生产成本。
此外,通过建立与供应商的长期稳定合作关系,实现对材料供应链的有效管理,以降低采购成本。
5. 创新技术策略加大对动力电池技术的研发投入,积极探索新的电池材料、新的生产工艺和新的储能技术,以实现成本的进一步降低。
结论:动力电池技术的成本分析与降低策略对于电动汽车产业的可持续发展具有重要意义。
乘用车动力总成成本核算
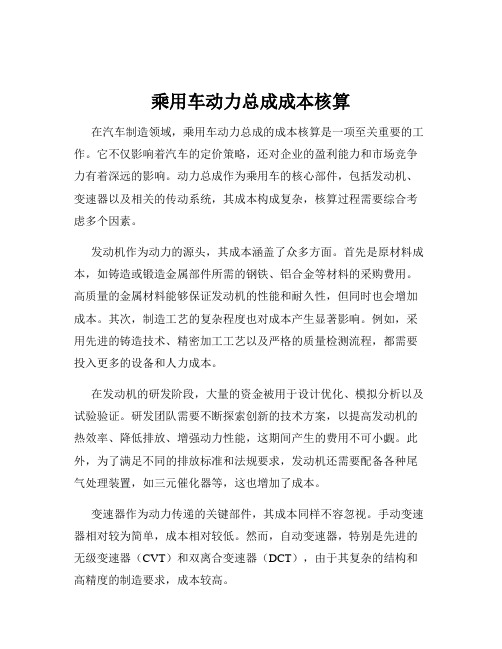
乘用车动力总成成本核算在汽车制造领域,乘用车动力总成的成本核算是一项至关重要的工作。
它不仅影响着汽车的定价策略,还对企业的盈利能力和市场竞争力有着深远的影响。
动力总成作为乘用车的核心部件,包括发动机、变速器以及相关的传动系统,其成本构成复杂,核算过程需要综合考虑多个因素。
发动机作为动力的源头,其成本涵盖了众多方面。
首先是原材料成本,如铸造或锻造金属部件所需的钢铁、铝合金等材料的采购费用。
高质量的金属材料能够保证发动机的性能和耐久性,但同时也会增加成本。
其次,制造工艺的复杂程度也对成本产生显著影响。
例如,采用先进的铸造技术、精密加工工艺以及严格的质量检测流程,都需要投入更多的设备和人力成本。
在发动机的研发阶段,大量的资金被用于设计优化、模拟分析以及试验验证。
研发团队需要不断探索创新的技术方案,以提高发动机的热效率、降低排放、增强动力性能,这期间产生的费用不可小觑。
此外,为了满足不同的排放标准和法规要求,发动机还需要配备各种尾气处理装置,如三元催化器等,这也增加了成本。
变速器作为动力传递的关键部件,其成本同样不容忽视。
手动变速器相对较为简单,成本相对较低。
然而,自动变速器,特别是先进的无级变速器(CVT)和双离合变速器(DCT),由于其复杂的结构和高精度的制造要求,成本较高。
自动变速器中的核心零部件,如液力变矩器、行星齿轮组、离合器片等,其材质和制造精度都对性能和可靠性有着关键影响,因此采购成本较高。
同时,变速器的研发投入也颇为可观,包括软件开发、换挡逻辑优化以及耐久性测试等方面。
除了发动机和变速器这两个主要部件,传动系统的成本也需要纳入考量。
传动轴、万向节、差速器等部件的材料选择、制造工艺以及质量控制都会影响成本。
此外,一些高端车型配备的四驱系统或者电子限滑差速器等先进的传动技术,也会大幅增加成本。
在进行动力总成成本核算时,不能仅仅关注零部件的采购和制造成本,还需要考虑到生产过程中的间接成本。
例如,工厂的设备折旧、厂房租赁、水电费等运营成本,以及工人的工资、福利和培训费用等人力成本。
汽车动力电池的成本控制及降低方案探究
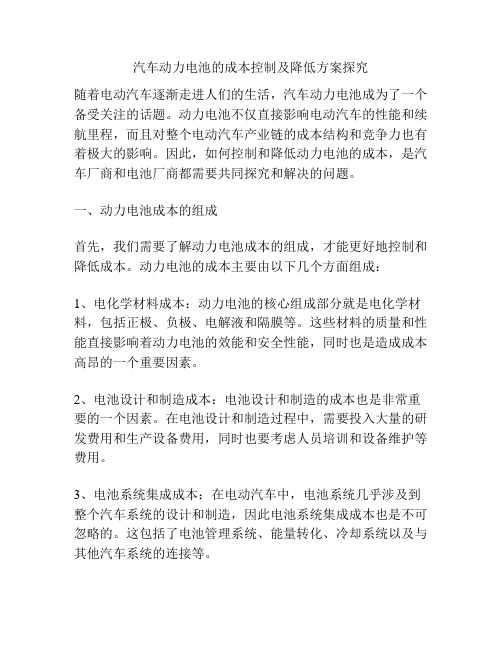
汽车动力电池的成本控制及降低方案探究随着电动汽车逐渐走进人们的生活,汽车动力电池成为了一个备受关注的话题。
动力电池不仅直接影响电动汽车的性能和续航里程,而且对整个电动汽车产业链的成本结构和竞争力也有着极大的影响。
因此,如何控制和降低动力电池的成本,是汽车厂商和电池厂商都需要共同探究和解决的问题。
一、动力电池成本的组成首先,我们需要了解动力电池成本的组成,才能更好地控制和降低成本。
动力电池的成本主要由以下几个方面组成:1、电化学材料成本:动力电池的核心组成部分就是电化学材料,包括正极、负极、电解液和隔膜等。
这些材料的质量和性能直接影响着动力电池的效能和安全性能,同时也是造成成本高昂的一个重要因素。
2、电池设计和制造成本:电池设计和制造的成本也是非常重要的一个因素。
在电池设计和制造过程中,需要投入大量的研发费用和生产设备费用,同时也要考虑人员培训和设备维护等费用。
3、电池系统集成成本:在电动汽车中,电池系统几乎涉及到整个汽车系统的设计和制造,因此电池系统集成成本也是不可忽略的。
这包括了电池管理系统、能量转化、冷却系统以及与其他汽车系统的连接等。
4、电池循环寿命和安全性能成本:长时间使用和频繁充电循环会对动力电池产生一定的影响,这需要对电池进行严格的测试和监测,以保证其循环寿命和安全性能。
二、降低动力电池成本的方案控制和降低动力电池成本需要综合考虑上述几个方面,以下是一些可行的方案:1、提高电化学材料的性能和降低成本:电化学材料是动力电池的核心组成部分,因此研发高性能、低成本的电化学材料是解决电池成本问题的重要手段。
目前,一些电池厂商已经开始研制低成本的电化学材料,比如钴镍锰氧化物(NCM)和钴铝氧化物(CAO)等,这些材料的成本比传统的钴酸锂还要低。
2、推广标准化的电池设计和制造技术:标准化的电池设计和制造技术可以降低设计和制造成本,同时还有助于提高电池性能和可靠性。
目前,一些电池厂商已经开始推广标准化的电池设计和制造方法,比如模块化和可重复使用的电池组件等。
动力车间“降本增效”实施方案

“动力车间降本增效实施方案”一、问题分析1.能源浪费:动力车间在生产过程中,能源消耗巨大,但存在严重的浪费现象。
如设备老化、操作不规范等。
2.设备维护成本高:设备维护是保证生产顺利进行的关键,但高昂的维护成本让车间承受着巨大的压力。
3.人力资源配置不合理:车间现有的人力资源配置存在不合理现象,如部分岗位人员过剩,而部分岗位人员不足。
4.管理不规范:车间管理存在漏洞,如生产计划执行不力、物料采购不规范等。
二、降本增效措施1.提高能源利用效率(1)对车间设备进行升级改造,提高设备运行效率。
(2)加强能源管理,定期检查设备运行情况,确保设备在最佳状态下运行。
(3)优化生产流程,减少不必要的生产环节,降低能源消耗。
2.降低设备维护成本(1)建立设备维护档案,定期对设备进行保养和维修。
(2)提高操作人员的技能水平,减少设备故障率。
(3)采用先进的设备维护技术,降低维护成本。
3.优化人力资源配置(1)对车间现有人员进行岗位调整,确保人力资源得到合理利用。
(2)开展培训,提高员工综合素质,提升生产效率。
(3)建立健全激励机制,激发员工工作积极性。
4.规范车间管理(1)完善生产计划,确保生产任务按时完成。
(2)加强物料采购管理,降低采购成本。
(3)建立质量管理体系,提高产品质量。
三、实施方案1.成立降本增效工作小组,明确各成员职责。
2.制定详细的降本增效计划,明确时间节点和任务分工。
3.开展培训和宣传,提高员工对降本增效的认识和重视。
4.对车间设备进行升级改造,提高设备运行效率。
5.加强能源管理,降低能源消耗。
6.优化人力资源配置,提高生产效率。
7.规范车间管理,提高产品质量。
8.定期对降本增效成果进行评估,对存在的问题进行整改。
四、预期效果4.车间管理水平提升,产品质量稳定。
5.员工收入增加,工作满意度提高。
在这个方案的实施过程中,我们将不断调整和完善,确保动力车间在生产过程中实现降本增效。
让我们共同努力,为企业的可持续发展贡献力量!实施这个方案时,可得注意几个关键点,别看漏了。
汽车动力总成的能量管理与优化

汽车动力总成的能量管理与优化随着汽车工业的不断发展,汽车动力总成的能量管理与优化已经成为汽车制造商及消费者关注的重要话题。
通过有效管理和优化动力总成的能量利用,可以实现更高的燃油效率和更低的排放,从而降低对环境的影响,提升驾驶体验。
本文将探讨汽车动力总成的能量管理与优化的相关技术和方法,并分析其对汽车行业的影响。
一、动力总成的能量管理动力总成是汽车的核心组成部分,包括引擎、变速器、传动系统等。
能量管理是指如何在不同驾驶工况下合理分配动力总成的能量供给,以达到最佳的燃油效率和性能表现。
1.1 扭矩分配策略扭矩分配策略是能量管理的关键。
在不同驾驶工况下,合理分配引擎输出的扭矩可以提高汽车的燃油效率和性能。
例如,在高速行驶时,可以通过限制引擎的扭矩输出来保持较低的燃油消耗;而在加速或爬坡时,可以充分利用引擎的扭矩输出,提供更好的动力。
1.2 能量回收利用能量回收利用是另一项重要的能量管理策略。
通过采用制动能量回收系统和发动机启停技术,可以利用行驶过程中产生的废能量,如制动时的能量和怠速时的能量,将其转化为电能储存起来或直接供给车辆使用,提高能量利用效率。
二、动力总成的能量优化除了能量管理外,动力总成的能量优化也是汽车制造商追求的目标。
通过优化动力总成的构造和控制系统,可以实现更高效、更环保的能量利用,提升汽车性能和用户体验。
2.1 轻量化设计轻量化设计是能量优化的重要手段之一。
通过采用轻量化材料,如高强度钢、铝合金等,可以减轻车辆自重,降低车辆在行驶过程中的能量消耗。
同时,轻量化设计还可以提高车辆的加速性能和操控性。
2.2 智能控制系统智能控制系统是能量优化的关键技术之一。
通过引入先进的传感器和控制算法,可以实时监测和调节动力总成的工作状态,以实现最佳的能量利用效果。
例如,智能燃油喷射系统可以根据驾驶工况和发动机负荷实时调整燃油喷射量,提高燃烧效率;智能变速器控制系统可以根据驾驶条件自动选择合适的挡位,提供更好的动力输出和燃油经济性。
48V动力系统的效率和成本优化

48V动力系统的效率和成本优化Wolfgang Schoffmann;Helfried Sorger;Michael Weissback;刘瑞庭【摘要】随着燃油排放法规的进一步收紧,发动机需要进行一系列的电气化来减少对能源的消耗。
48V动力系统架构相对纯混合动力系统,能在保持相对低廉成本的同时,还能达到更好的节能减排的要求,是实现未来法规节能减排要求性价比最高的方案之一。
【期刊名称】《汽车制造业》【年(卷),期】2017(000)015【总页数】3页(P46-48)【关键词】混合动力系统成本优化排放法规节能减排电气化发动机性价比燃油【作者】Wolfgang Schoffmann;Helfried Sorger;Michael Weissback;刘瑞庭【作者单位】不详;不详;不详;不详【正文语种】中文【中图分类】U469.11随着燃油排放法规的进一步收紧,发动机需要进行一系列的电气化来减少对能源的消耗。
48 V动力系统架构相对纯混合动力系统,能在保持相对低廉成本的同时,还能达到更好的节能减排的要求,是实现未来法规节能减排要求性价比最高的方案之一。
随着48 V系统的出现,使得电动机功率也可以相应地增大,我们需要对现有的混合动力系统布置方案重新进行评估。
现有的各种布置方案:P0——电动机安装在内燃机的皮带传动系统上;P1——电动机直接安装在内燃机的曲轴上;P2——电动机安装在内燃机和变速器之间,中间使用离合器耦合;P3——电动机安装在变速器中;P4——电动机安装在后驱动轴上。
现有的皮带传动起动发电机系统(P0)已经实现了直接耦合和扭力增强的功能,并且还能非常高效地支持电子增压系统。
随着飞轮起动发电机(P2)的应用,进一步提供了额外的可能,如纯电动行驶一定的距离、简化传统传动带发动机的结构等。
每种电动机布置系统都有各自的优缺点,这点对于48 V系统架构将来与汽油、柴油内燃机系统布置匹配都非常重要。
研究证实,使用20 kW高能电动机的48 V动力系统可以减少CO2的排放,同时还能增强纯电动驾驶的能力和增加能量回收最重要的一种配置。
动力车间降本增效工作总结

动力车间降本增效工作总结
近年来,随着经济竞争的加剧,企业降本增效已成为企业发展的重要战略。
作
为动力车间的管理者,我们深知降本增效对企业的重要性,因此我们不断探索创新,努力提高生产效率,降低生产成本,取得了一定的成绩。
在此,我将对动力车间降本增效工作进行总结。
首先,我们注重技术创新,引进先进的生产设备和技术,提高生产效率。
通过
引进自动化设备和智能化生产线,大大提高了生产效率,减少了人力成本,降低了生产成本。
同时,我们还加强了员工的技术培训,提高了员工的技术水平和工作效率,为企业的降本增效工作奠定了坚实的基础。
其次,我们优化生产流程,提高生产效率。
通过对生产流程进行全面的分析和
优化,我们发现了一些不合理的地方,并进行了改进。
我们采取了精细化管理,提高了生产效率,减少了浪费,降低了生产成本。
同时,我们还加强了原材料的管理,优化了供应链,降低了采购成本,提高了供应链的效率。
最后,我们加强了成本管理,降低了生产成本。
我们对生产成本进行了全面的
分析,找出了一些不必要的支出,并进行了精准的控制。
通过降低生产成本,我们提高了企业的盈利能力,增强了企业的竞争力。
总的来说,动力车间的降本增效工作取得了一定的成绩,但也存在一些不足之处。
我们将继续努力,不断探索创新,提高生产效率,降低生产成本,为企业的可持续发展做出更大的贡献。
动力车间“降本增效”实施方案
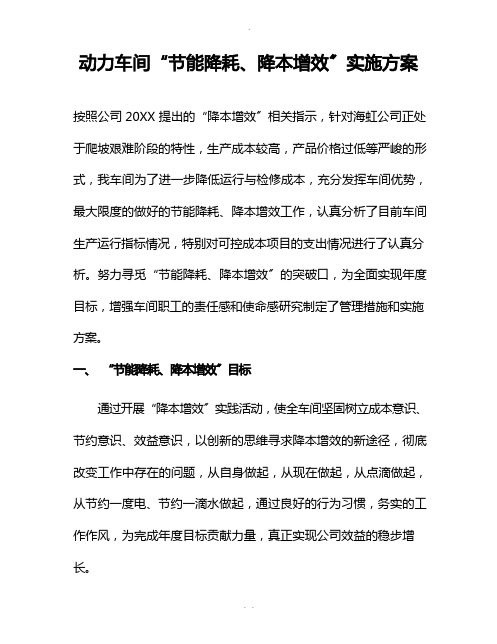
按照公司 20XX 提出的“降本增效〞相关指示,针对海虹公司正处于爬坡艰难阶段的特性,生产成本较高,产品价格过低等严峻的形式,我车间为了进一步降低运行与检修成本,充分发挥车间优势,最大限度的做好的节能降耗、降本增效工作,认真分析了目前车间生产运行指标情况,特别对可控成本项目的支出情况进行了认真分析。
努力寻觅“节能降耗、降本增效〞的突破口,为全面实现年度目标,增强车间职工的责任感和使命感研究制定了管理措施和实施方案。
通过开展“降本增效〞实践活动,使全车间坚固树立成本意识、节约意识、效益意识,以创新的思维寻求降本增效的新途径,彻底改变工作中存在的问题,从自身做起,从现在做起,从点滴做起,从节约一度电、节约一滴水做起,通过良好的行为习惯,务实的工作作风,为完成年度目标贡献力量,真正实现公司效益的稳步增长。
组长:林占宏副组长:孙炳宗钟彪马效农尹享军 X 利武组员:常华 X 文智吉福家裴少鹏都文明 X 毅刚X 睿桢姚卫国肖利云代致林姚鹏飞袁文彦杨进财 X 廷奎汪海华严宝春王万保徐志良魏全才郭红平沈元秀1.靠管理降低成本要降低成本,必须抓住管理这个纲。
动力车间仪表工段将强化成本核算,在温度变送器、阀门垫片、螺栓、工器具易耗品〔螺丝刀套组、扳手、万用表、内六角套组〕、电线电缆、盘根、就地仪表等各个环节加强管理,把生产检修中所用的材料、备品备件等细化到每项检修工作成本中,形成全员、全过程、全方位的成本控制格局,使降低成本落实到每一个职工的具体行动中。
在此基础上要加强材料、物资存放管理,车间要对入库的配件进行联合验收,并要求供货商提高备品备件的质量与精度,同时车间对领回的材料、配件进行定制摆放,对轻度有问题仪表要重点保护,避免仪表光使用,不维护,防止仪器仪表损坏程度达到不可维修的程度,造成不必要的成本损失。
2.靠技术改造降低成本车间要树立技术改造是降低成本重要途径的观念,通过技术改造,采用新技术、新工艺、新材料,提高检修质量和效率,开辟降低生产成本的途径。
动力厂深挖设备潜力 千方百计降低成本
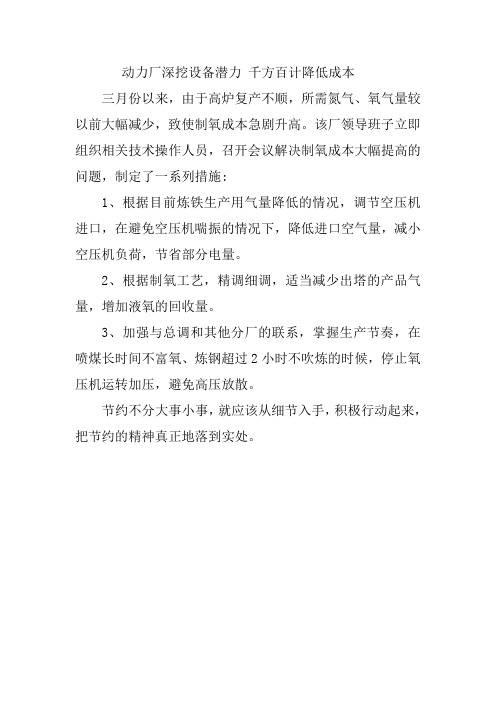
动力厂深挖设备潜力千方百计降低成本
三月份以来,由于高炉复产不顺,所需氮气、氧气量较以前大幅减少,致使制氧成本急剧升高。
该厂领导班子立即组织相关技术操作人员,召开会议解决制氧成本大幅提高的问题,制定了一系列措施:
1、根据目前炼铁生产用气量降低的情况,调节空压机进口,在避免空压机喘振的情况下,降低进口空气量,减小空压机负荷,节省部分电量。
2、根据制氧工艺,精调细调,适当减少出塔的产品气量,增加液氧的回收量。
3、加强与总调和其他分厂的联系,掌握生产节奏,在喷煤长时间不富氧、炼钢超过2小时不吹炼的时候,停止氧压机运转加压,避免高压放散。
节约不分大事小事,就应该从细节入手,积极行动起来,把节约的精神真正地落到实处。
XX化学纤维公司动力车间“节能降耗降本增效”实施方案
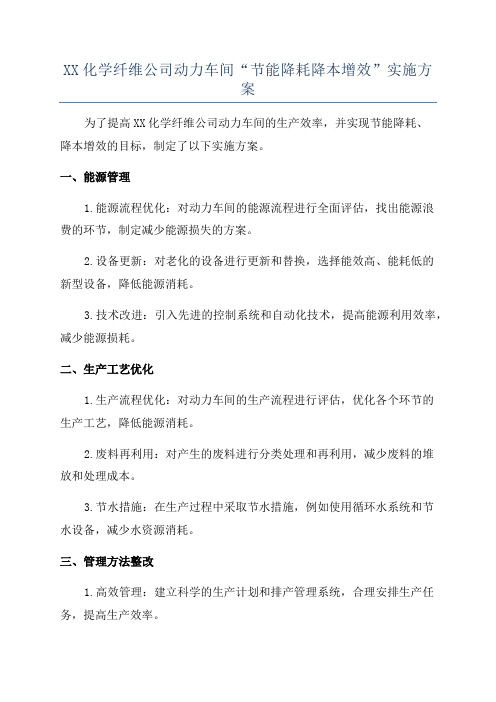
XX化学纤维公司动力车间“节能降耗降本增效”实施方案为了提高XX化学纤维公司动力车间的生产效率,并实现节能降耗、降本增效的目标,制定了以下实施方案。
一、能源管理1.能源流程优化:对动力车间的能源流程进行全面评估,找出能源浪费的环节,制定减少能源损失的方案。
2.设备更新:对老化的设备进行更新和替换,选择能效高、能耗低的新型设备,降低能源消耗。
3.技术改进:引入先进的控制系统和自动化技术,提高能源利用效率,减少能源损耗。
二、生产工艺优化1.生产流程优化:对动力车间的生产流程进行评估,优化各个环节的生产工艺,降低能源消耗。
2.废料再利用:对产生的废料进行分类处理和再利用,减少废料的堆放和处理成本。
3.节水措施:在生产过程中采取节水措施,例如使用循环水系统和节水设备,减少水资源消耗。
三、管理方法整改1.高效管理:建立科学的生产计划和排产管理系统,合理安排生产任务,提高生产效率。
2.培训和激励:对动力车间的员工进行培训,提高员工的技能水平和工作意识,激励员工提出并执行节能降耗的创新方案。
3.数据分析和监控:建立监控系统,实时监控能源的使用情况和生产效率,通过数据分析找出问题所在,并及时解决。
四、宣传和倡导1.能源意识宣传:通过内部宣传和培训活动,提高员工的节能意识和能源使用效率。
2.奖励机制:建立奖励机制,激励员工提出节能降耗的创新方案,并对其进行奖励和表彰。
3.合作共赢:与供应商和客户紧密合作,共同推动节能降耗的目标,建立长期合作关系。
五、监督和评估1.定期检查:定期对动力车间的能源消耗情况进行检查和评估,及时发现问题,并采取相应的措施加以解决。
2.绩效评估:建立绩效评估机制,对动力车间的节能降耗和降本增效情况进行评估,对绩效突出的个人和团队进行奖励和激励。
3.持续改进:根据评估结果,对方案进行优化和改进,确保方案的持续有效性和可持续性。
通过以上实施方案,XX化学纤维公司动力车间将能够有效地实现节能降耗、降本增效的目标,提高生产效率,降低能源消耗和生产成本,提升公司的竞争力和可持续发展能力。
- 1、下载文档前请自行甄别文档内容的完整性,平台不提供额外的编辑、内容补充、找答案等附加服务。
- 2、"仅部分预览"的文档,不可在线预览部分如存在完整性等问题,可反馈申请退款(可完整预览的文档不适用该条件!)。
- 3、如文档侵犯您的权益,请联系客服反馈,我们会尽快为您处理(人工客服工作时间:9:00-18:30)。
动力总成的高效加工与降成本
先进刀具在动力总成生产线广泛应用的事实,有力证明了充分、合理发挥先进刀具的性能是动力总成的高效加工中降低成本的最重要的手段之一。
合理地利用先进加工刀具,可以不断提高生产效率,在降低制造成本的同时满足用户日益增长的需求。
汽车制造业的发展和进步,离不开生产制造技术及装备的提升与革新。
中国汽车工业针对性地提出的“提高效率,降低成本”的要求,汽车制造业及其制造装备供应商都在各个方面不断改进加以适应。
其中先进刀具的应用就是最重要的手段之一。
本文主要在动力总成的高效加工方面,就发挥先进刀具的性能与动力总成生产线的提高效率和降低成本之间的关系谈一些想法。
目前现代汽车动力总成生产线具有以下明显的特点:多品种、中批量生产;高效率;节拍快;低成本。
其中的高效率和低成本,需要设备与刀具的合理匹配。
因此,在应用先进刀具时,在规划的设备上,为了达到高效率和节拍平衡,要求使用高速度、高进给的刀具;规划时往往会牺牲刀具寿命来满足节拍要求,但同时又要求保证最低要求的刀具寿命;设备规划时仅在节拍允许的范围内,才可能考虑延长刀具寿命。
因此,在动力总成的高效加工中,充分、合理发挥先进刀具的性能是最重要的手段之一。
先进刀具在提高效率中的关键作用
汽车工业的动力总成生产中关于提高效率的要求,就是使用尽可能少的机床在单位时间内生产尽可能更多的零件。
具体到先进刀具应用上,就是提高单位时间的金属切削率,减少机床非切削的辅助时间,提高机床的开动率。
先进刀具提高机床单位时间的金属切削率,主要通过先进刀具的高切削速度、高进给来实现。
动力总成生产线追求高效率带来了高速CNC机床的大量应用,同时也要求刀具具备高速切削的能力。
刀具本身大量应用高速切削的材质如PCD、CBN、陶瓷、硬质合金及复合涂层等。
先进刀具刀柄大多应用具有很好的平衡性能的高转速的HSK系列刀柄设计来适应刀具的高速切削。
以上条件保证了刀具在加工中的高切削速度和高进给应用。
如典型的由铝合金铸造的发动机缸体,其缸盖结合面如图1所示,有20个连接螺栓孔需要加工,在底孔加工中选用先进刀具和传统刀具将对生产线加工效率有着极大的影响(见表1)。
图1 发动机缸盖结合面
表1 在底孔加工中选用先进刀具和传统刀具的比较
通过表中的数据对比,可以知道在加工该工艺底孔时,传统刀具的加工时间是先进刀具加工时间的370%,如以生产线的规划节拍为75s来计算,选用传统刀具至少需要2台机床同时加工该工艺底孔才有可能满足节拍要求。
而选用先进刀具只需要1台机床加工该工艺底孔就可以满足且可有富裕时间加工其他工艺要求。
由此可见,刀具的高速度、高进给保证了生产中对加工效率越来越高的要求。
先进刀具通过组合刀具的合理、大量使用来减少机床非切削的辅助时间,达到提高动力总成生产线生产效率的目的。
先进刀具中的组合刀具具有如下特点:高效率、高质量和高稳定性。
组合刀具一般是将几个加工内容组合在一把刀具上,从而只通过一次进给,便可完成全部的加工内容。
这样不仅减少了加工时间,同时也减少了如换刀等辅助时间,提高了生产节拍和生产效率,在现代汽车动力总成制造中的应用越来越广泛。
如在动力总成中常见的20个螺纹M10X1.5的底孔加工时,往往需要倒角或有沉孔(见图2)。
图2 螺纹刨面图
比较采用一般的D8.5钻头+倒角钻二次加工与组合加工的台阶钻一次加工的结果,表2的结论清楚地表明,采用一次加工的组合台阶钻比钻头+倒角钻二次加工可以节约的辅助时间占总加工时间的17%。
当然,不同的加工状况会有一定的差异,但上述结论说明先进的组合刀具在动力总成提高效率中能够起到重要的作用。
因此,为了尽可能减少辅助时间,提高加工效率,汽车动力总成加工中大量应用先进组合刀具才能满足高效率的要求。
表2 传统加工工艺与组合加工的比较
先进刀具的优化应用,可提高刀具寿命,减少生产中刀具换刀频次,提高机床的开动率,从而提高生产线的生产效率。
例如某铝合金缸体上的水泵孔粗加工(见图3),原方案采用硬质合金刀片,刀具寿命80件,每班需换2次刀,每次换刀时间15min,对机床的开动率有较大的影响。
新方案采用PCD焊接刀片,刀具寿命1 000件,极大地减少了换刀时间。
图3 某铝合金缸体上的水泵孔粗加工
两种方案的比较如表3所示,先进刀具的方案相比较原方案仅在换刀时间上就可为生产线每年节省1个月时间,如可以充分利用该时间,在不增加设备和人员的前提下每年可以多生产约2万个零件,这将极其有效地提高生产线的生产效率。
表3 选用硬质合金刀片与PCD焊接刀片的加工比较
先进刀具在降低成本中的主导作用
汽车行业的成本统计中,刀具成本仅占动力总成总成本的3%~5%,但它却能影响总成本的20%~30%。
这主要来自于先进刀具带来的生产效率的提高而导致生产线生产成本的下降。
先进刀具不仅能直接降低动力总成的刀具成本,而且能间接带来生产成本的显著降低,符合“精益生产”原则——用
最小投资赢得最大经济效益。
先进刀具在动力总成降低成本的主导作用,主要体现在降低设备投资、降低零件单件刀具消耗费用和减少生产费用等方面。
先进刀具在项目规划时可以降低动力总成生产线的设备投资。
生产降低成本的要求从发动机生产线的立项开始就贯穿发动机项目全过程,始终如一。
积极应用先进加工刀具就具有减少设备投资,赢得最大经济效益的作用。
例如图1中的工艺分析,采用先进刀具的方案将比采用传统刀具的方案减少1台机床的投资,如果整个项目都应用先进刀具,尽可能减少机床设备的投资,就可以达到用最小投资赢得最大经济效益的目的。
再如缸体的启动电机面的加工(见图4),由于被加工面与CNC机床主轴平行,传统方案是使用专机来加工,成本约百万级人民币,且设备柔性差。
现可以使用铣削用角度头,直接在标准CNC机床上使用,投资约十万级人民币,并且设备柔性好。
很明显,在满足同样的工艺要求前提下,设备投资的下降是非常可观的。
图4 缸体的启动电机面的加工
降低零件单件刀具消耗费用
先进刀具在降低零件单件刀具消耗费用方面也有着不俗的表现。
先进刀具的价格往往相对比较昂贵,但先进刀具的性能可比传统刀具有很大提高,综合零件单件刀具消耗费用一般有明显的下降。
例如,同尺寸规格的硬质合金铰刀和PCD铰刀在发动机铝合金零件上的加工比较,价格上PCD铰刀一般是硬质合金铰刀的3~5倍,刀具寿命上PCD铰刀一般是硬质合金铰刀的10倍,而采用PCD铰刀,零件单件刀具消耗费用一般可以下降50%或更多。
对于现有生产线,刀具技术的不断发展使刀具成本在其性能充分发挥的前提下仍能不断下降。
先进刀具的新材质、新涂层,相对于原来的刀具,其寿命往往有10%~30%的提高,而价格一般相差无几。
减少生产费用
先进刀具在生产中可以持续地减少生产费用。
先进刀具的干式加工和MQL已逐渐成为未来加工的方向,通过不用和微量使用冷却液,一般可以节约15%的制造成本,另外还可通过减少零件的单位加工时间、减少换刀损失、增加机床开动率、降低刀具管理成本和延长刀具寿命降低刀具的库存费用来降低生产成本。
据报道,有部分企业采购了大量的进口高性能机床,但却选用传统的低性能的高速钢
刀具,机床的性能只发挥出10%~20%,由于刀具寿命短而机床频繁停机换刀,表面上看刀具成本可能是比较低的,但如从零件的生产成本来看,由于设备的折旧费用摊到较少的零件上,零件的成本势必会大幅上升。
因此,明智的选择应该是应用先进刀具,最大程度地提高机床的单位时间产出,从而尽可能地降低生产成本。