PD-FMEA流程20-sep
2.PFMEA工作流程资料

风 险 控顺 测序 度数 D R. P. N
建 议 措 施
责 任 和 目 标 完 成 日 期
措施执行结果
采
R
取 的 措
严 重 度
频 度
探 测 度
. P .
施
N
4
PFMEA 工作流程
成立功能小组
确定工序
详述 失效模式
原因 失效后果
计算风险值
绘制柏拉图
开展纠正措施
5
PFMEA 工作流程
功能小组的成立
10
发生可能性评定
频度
频度是一失效模式在没有任何的监控措施的情况下发生的几率。
发生的可能性
几乎是不可能 很少很少 很少 很低 低 中等 有点高 高 很高 几乎肯定
频度
1
1
2
3
4
4
5
6
7
7
8
9
9
10 10
Cpk 失效几率
备注
Cpk 1.67 5.0 1 / 1,500,000 失效几乎是不可能发生的.
确定工序
详述 失效模式
原因 失效后果
计算风险值
绘制柏拉图
开展纠正措施
6
PFMEA 工作流程
功能小组的成立
跨部门多功能小组
由操作员、技术员、工程师和部门主管组成 指定小组组长
建议为工序责任人
应有足够的授权以便开展工作 必要时,应有专家级人物参加 开始时,由少数人组成的核心小组可能更有利于制定一个框
架。
7
PFMEA 工作流程
功能小组的成立
确定工序
详述 失效模式
原因 失效后果
计算风险值
绘制柏拉图
开展纠正措施
制程FMEA作业程序

制程FMEA作业程序1、目的:透过制程失效模式与效应分析制订、实施、确认制造和装配之间之潜在失效原因与制程变数,制定出应对的改善方法,以降低制程失效的发生风险,达到品质持续改善之目的。
2、范围:适用于本公司全部生产作业制程。
3、名词解释:3.1.PFMEA:制程失效模式与效应分析4、权责:. 生技:失效模式和效应分析之主导与作成。
.产品工程、品管部、生管各相关人员协助失效模式与效应分析之研讨。
5、流程图:无6、内容:6.1 PFMEA实施时机:6.1.1本模式与分析适用于预期、解决、监控(试产/量产阶段)新产品新制程及量产中制程变更之潜在风险评估。
6.2 失效模式的列举与预测:6.2.1 就制造单位而言,制造可能失效的环节不外乎人、机、料、法、环,其考虑失效原因之方向如下:a)参考类似机种及相关制程,以固有技校及经验判断制程中可能发生之不良。
b)考虑外在环境条件(高温、低温、湿度)所可能引起之不良。
c)考虑作业是否合理,是否因不合理之作业而造成不良;是否可简化作业以减少人为疏失或提高效率。
d)总结以上可能失效之原因,较重要之项目予以选定与整理,作成失效模式分析。
6.3 PFMEA 实施程序:6.3.1 使用[失效模式(FMEA)分析表](参照DFMEA作业程序8.1):记录可能失效的项目,预估失效所产生的影响并推测其可能发生原因。
6.3.2发生率、严重度、难检度:评定完成。
6.3.3风险优先指数(RPN)评价:RPN=发生率*严重度*难检度6.3.4建议改善措施与效果确认:A)挑选RPN值高者或单项分数较高者,优先考虑采取对策改善。
B)对策实施效果确认后,就RPN等各项数值重新计算确认改善成效。
6.4 FMEA表填写要领:6.4.1 FMEA表——————资料区:A)FMEA编号:填写FMEA之编号以便追纵管理。
B)FMEA阶段:于样品、试产、量产三选一。
C)机种:说明欲分析之部品所属之产品型号。
FMEA分析流程

FMEA分析流程FMEA(故障模式与影响分析)是一种系统的方法,主要用于识别、评估和控制潜在故障,以降低风险和提高产品或过程的可靠性。
FMEA分析流程基本上可以分为五个主要步骤:确定范围、识别潜在故障、评估故障影响、确定风险优先级和采取纠正措施。
1.确定范围:确定分析的产品或过程的范围,包括具体的系统、组件、部件或流程。
这个步骤有助于限定分析的工作范围,提高分析的效率。
2.识别潜在故障:通过对产品或过程的每个元素进行逐个检查,识别可能存在的故障模式。
可以通过以下方法来进行识别:-经验法:基于以往的经验和专业知识,识别出现过的故障模式。
-功能法:根据产品或过程的功能来思考可能的故障模式。
-失效标准法:参考已有的标准和规范,识别可能存在的故障模式。
-验证法:进行各种实验和测试,识别潜在的故障模式。
3.评估故障影响:对于每个潜在的故障模式,评估其对产品或过程的影响程度。
这包括分析故障模式对安全性、可靠性、效率和顾客满意度等的影响。
可以使用数字量表或评估矩阵来量化故障影响。
4.确定风险优先级:根据故障的严重程度和发生频率,确定每个潜在故障模式的风险优先级。
通常使用一个风险优先级矩阵来进行评估。
风险优先级较高的故障模式应该具有更高的优先级,并且需要更多的关注和纠正措施。
5.采取纠正措施:对于高优先级的故障模式,制定相应的纠正措施。
这些措施可以包括改进设计、制造流程、工艺控制、培训和预防性维护等。
在实施纠正措施后,应进行验证和监控,以确保问题已经得到解决。
此外,还有一些额外的步骤可以增强FMEA分析的效果:-6.控制计划:制定控制计划来监控故障模式的发生,以便及时采取纠正措施。
-7.定期审查:定期审查已经完成的FMEA分析,以便根据实际情况进行更新和改进。
-8.沟通和培训:将FMEA分析的结果和纠正措施与相关人员进行沟通和培训,确保他们对问题和解决方案有清晰的理解。
总之,FMEA分析流程是一个逐步的过程,旨在识别和评估潜在故障,并制定相应的纠正措施。
TS16949过程FMEA控制程序

过程FMEA实施的具体步骤
过程FMEA小组
4.3.1确定产品制造、装配过程流程。
技术部工程师编制“工艺流程图”确定每个工序的内容、工艺要求,包括产品/过程特性参数、工序生产应达到的质量要求等。
4.3.2确定需要进行过程FMEA分析的工序
过程FMEA小组根据“工艺流程图”对工艺流程中的各个工序进行风险评估。经过风险评估,将各个工序分成低风险、中等风险、高风险工序,只对高风险工序进行过程FMEA分析。
4.3.3列举每个高风险工序的潜在失效模式、起因和潜在失效后果。
4.3.4进行风险分析
按照失效影响的严重程度(严重度S)、发生的频繁程度(频度O)、发现的难医程度(发现难度D)估计风险顺序数。
严重度S、频度O、发现难度D均利用数字1到10来判断其程度高低(参见《过程FMEA潜在失效后果严重程度(S)评价标准》、《过程FMEA潜在失效模式发生频度(O)评价标准》、《过程FMEA潜在失效模式发现难度(D)评价标准》)。
各项数字的连乘积称为风险顺序数(RPN)。
RPN=S×O×D
4.3.5制定控制措施
对风险顺序数RPN≧100或严重度S≧8的项目,过程FMEA小组应制定出控制措施,经生产副总经理批准后实施。
4.3.6填写过程FMEA分析表格—“潜在失效模式及后果分析报告(过程FMEA)”。
4.3.7控制措施的跟踪管理
过程FMEA小组对过程FMEA分析中提出的控制措施进行跟踪并对其效果进行评审。
评审认为效果不理想时,应制定新的控制措施。评审认为有效的方法,过程FMEA小组应将它们纳入到文件中。
以“潜在失效模式及后果分析报告(过程FMEA)”的形式汇总分析和实施的结果,并将结果上报生产副总经理。
4.3.8过程FMEA的更新
FMEA工作步骤及主要内容
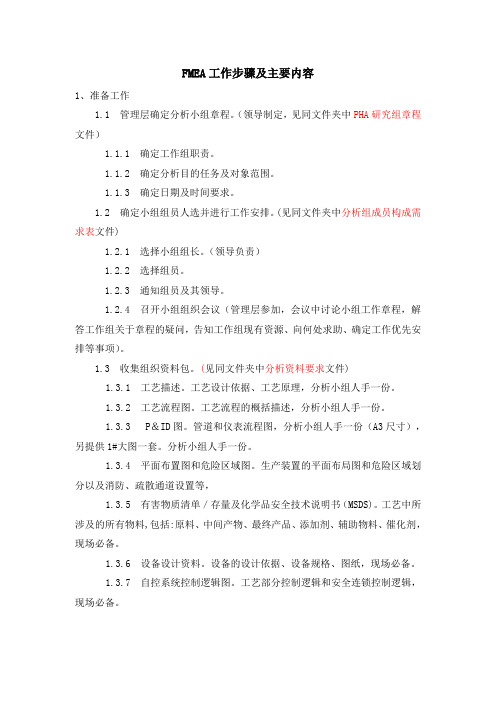
FMEA工作步骤及主要内容1、准备工作1.1 管理层确定分析小组章程。
(领导制定,见同文件夹中PHA研究组章程文件)1.1.1 确定工作组职责。
1.1.2 确定分析目的任务及对象范围。
1.1.3 确定日期及时间要求。
1.2 确定小组组员人选并进行工作安排。
(见同文件夹中分析组成员构成需求表文件)1.2.1 选择小组组长。
(领导负责)1.2.2 选择组员。
1.2.3 通知组员及其领导。
1.2.4 召开小组组织会议(管理层参加,会议中讨论小组工作章程,解答工作组关于章程的疑问,告知工作组现有资源、向何处求助、确定工作优先安排等事项)。
1.3 收集组织资料包。
(见同文件夹中分析资料要求文件)1.3.1 工艺描述。
工艺设计依据、工艺原理,分析小组人手一份。
1.3.2 工艺流程图。
工艺流程的概括描述,分析小组人手一份。
1.3.3 P&ID图。
管道和仪表流程图,分析小组人手一份(A3尺寸),另提供1#大图一套。
分析小组人手一份。
1.3.4 平面布置图和危险区域图。
生产装置的平面布局图和危险区域划分以及消防、疏散通道设置等,1.3.5 有害物质清单/存量及化学品安全技术说明书(MSDS)。
工艺中所涉及的所有物料,包括:原料、中间产物、最终产品、添加剂、辅助物料、催化剂,现场必备。
1.3.6 设备设计资料。
设备的设计依据、设备规格、图纸,现场必备。
1.3.7 自控系统控制逻辑图。
工艺部分控制逻辑和安全连锁控制逻辑,现场必备。
1.3.8 操作规程包括工艺卡片。
操作规程、应急预案、工艺卡片、设备修保规程,现场必备。
1.3.9 技术改造资料。
改造清单、改造原因、改造结果等,现场必备。
1.3.10 以往事故和危害事件分析报告。
事故原因、后果及整改措施,尽可能提供分析小组。
1.3.11 压力释放阀等安全装置的计算书和相关文件。
尽可能提供分析小组。
1.3.12 以往的PHA报告及类似分析文件。
尽可能提供分析小组。
1.3.13 设备设施检维修规程。
FMEA工作流程及说明

FMEA工作流程及说明---1. 背景介绍失效模式与影响分析(Failure Mode and Effects Analysis,简称FMEA)是一种旨在识别和评估潜在失效模式,并采取预防措施以降低风险的方法。
FMEA既可以在产品开发阶段进行,也可以在运营和生产过程中应用。
2. FMEA的目的FMEA的目的是识别潜在的失效模式、评估失效对系统、产品或过程的影响,并制定相应的纠正措施。
通过FMEA,可以提前预防和减少风险,确保产品质量和安全性。
3. FMEA工作流程FMEA通常包括以下步骤:步骤一:确定分析的范围和目标在开始FMEA前,需要明确分析的范围和目标,确定需要评估的系统、产品或过程。
步骤二:组建FMEA团队FMEA团队由相关专业人员组成,包括设计工程师、生产工程师、质量控制人员等。
团队成员应根据自身的专业知识和经验,共同参与FMEA分析。
步骤三:识别失效模式团队成员通过头脑风暴等方法,识别系统、产品或过程可能存在的失效模式,记录下潜在的失效模式。
步骤四:评估失效影响针对每个失效模式,团队成员评估失效对系统、产品或过程的影响程度,包括其严重性、故障频率和检测难度等方面。
步骤五:确定风险优先级根据失效的严重性、故障频率和检测难度等因素,计算每个失效模式的风险优先级,以确定需要优先关注的失效模式。
步骤六:制定纠正措施针对风险优先级较高的失效模式,团队成员制定相应的纠正措施,包括风险预防措施和风险缓解措施。
步骤七:实施纠正措施团队成员负责实施制定的纠正措施,并监控其有效性和实施进度。
4. 总结FMEA是一种有效的风险管理工具,可以帮助企业识别和评估潜在失效模式,并采取预防措施降低风险。
在实施FMEA过程中,要明确分析的范围、组建专业团队、识别失效模式、评估失效影响、确定风险优先级以及制定和实施纠正措施。
通过不断改进和优化FMEA工作流程,可以提高产品质量和安全性,降低生产风险。
PD制程FMEA管理程序

4.1当发生下列情况时,多方论证小组应组织实施FMEA:
a.开发新产品/产品更改;
b.生产过程更改;
c.生产环境/加工条件发生变化;
d.材料或零部件变化。
4.2实施FMEA时,多方论证小组首先制定严重度、频度、不易测度评价准则。
4.3品管部按照各评价准则,针对产品的每个过程进行FMEA分析,确定分析项目,失效模式、潜在后果、失效原因以及严重度、频度和不易探测度,计算总的风险顺序数。
3
0.1个 每1000件
2
级低:失效不太可能发生
≤0.01个 每1000件
1
程 序 文 件
制程FMEA控制程序
文 件 编 号
Q/HJE-PD24-2004
版 本
A/0
P 5/5
附件三:探测度评价准则
探测性
准则
检查类别
探测方法的 推荐范围
探测度
A
B
C
几乎
不可能
绝对肯定不可能
探测
X
不能探测或没有检查
10
4.4当某个过程的风险顺序数大于80时,多方论证小组应制定控制措施,减少风险顺序数,一直到风险顺序数小于80。
5 相关/支持性文件
5.1附件一:严重度评价准则;
5.2附件二:频度评价准则;
5.3附件三:探测度评价准则。
6记录
本程序的实施记录及保存要求如下表:
No
记录名称
收集(保存)部门
保存期限
表单编号
审核
批准
程 序 文 件
制程FMEA控制程序
文 件 编 号
Q/HJE-PD24-2004
版 本
A/0
P 2/5
FMEA 过程详解

<BR><style> .Yxn845 { display:none; } </style>1.4 FMEA 过程详解<br />1.4.1 故障模式分析<br />故障是产品或产品的一部分不能或将不能完成预定功能的事件或状态(对某些产品如电<br />子元器件、弹药等称为失效)。
而故障模式是故障的表现形式,如短路、开路、断裂、过度<br />耗损等。
一般在研究产品的故障时往往是从产品的故障现象人手,进而通过现象(即故障模<br />式)找出故障原因。
故障模式是FMECA 分析的基础,同时也是进行其它故障分析(如故障<br />树分析、事件树分析等)的基础之一。
<br />产品的故障与产品所属系统的规定功能和规定条件密切相关,在对具体的系统进行故障<br />分析时,必须首先明确系统在规定的条件下丧失规定功能的判别准则,即系统的故障判据,<br />这样才能明确产品的某种非正常状态是否为该产品的故障模式。
<br />在进行故障模式分析时,应注意区分两类不同性质的故障,即功能故障和潜在故障。
<br />功能故障是指产品或产品的一部分不能完成预定功能的事件或状态。
即产品或产品的一<br />部分突然、彻底地丧失了规定的功能。
<br />潜在故障是指产品或产品的一部分将不能完成预定功能的事件或状态。
潜在故障是一种<br />指示功能故障将要发生的一种可鉴别(人工观察或仪器检测)的状态。
例如,轮胎磨损到一 <div class='Yxn845'></div> <br />定程度(可鉴别的状态),即发生爆胎故障(功能故障)。
图1-2 中给出了某金属材料的功能<br />故障与潜在故障的示例。
汽车行业过程FMEA管理程序

汽车行业过程FMEA管理程序过程FMEA管理程序1.目的在产品质量先期策划阶段组织发现、评价潜在的失效及其后果,采取针对性的纠正措施,保证新产品开发质量。
2.范围适用于所有新零部件制造策划阶段的先期评审和分析,评审内容包括以往问题点、新设备、新材料、新技术、新工艺等。
.3.定义3.1 特殊特性:a)影响产品的安全性或法规要求的符合性的产品特性或过程参数;b) 影响产品的配合/功能的产品特性和过程参数;c) 在验证活动中要求特别关注的特性(如检验与试验、产品与过程审核)。
3.2 顾客:过程FMEA中“顾客”的定义通常是指“最终使用者”。
也可以是随后或下游的制造、装配工序或国家法规。
4.职责4.1 研发部经理负责组建项目组,指定组长人选,指导项目组的业务工作。
4.2 项目经理负责制定FMEA流程,发现可能影响产品质量的因素,采取防错措施,使过程设计和生产工序失效对产品影响降到最低。
4.3 主管工程师负责在过程控制中应用或修改PFMEA,使产品的质量可靠性和公司产品的生产能力达到最高。
5.程序5.1 组建运作机构成立运作小组,小组包括设计、制造、装配、采购、质量、服务等部门参加,小组组长由设计人员担任。
5.2 运作时机做为APQP的一个环节,在产品生产以前完成。
5.3 编制工作表5.3.1 工作表的内容实施PFMEA应编制工作表,工作表的内容主要包括项目名称、车辆类型、小组成员以及项目功能、潜在失效模式、潜在失效后果、严重度、级别、潜在失效起因/机理、频度、现行设计控制、探测度RPN、建议措施、责任目标完成日期、措施的结果(包括采取的措施和S、O、D、RPN)5.3.2 PFMEA工作表中各栏目填制说明:a. PFMEA编号:填入PFMEA文件的编号。
b. 项目:填入正在进行分析的系统、子系统或部件的零件号及零件名称。
c.责任部门:填入整车厂、部门、生产小组,如果知道,还应包括供方的名称。
d.编制者:填入负责准备PFMEA工作的工程师的姓名、电话和所在公司的名称。
PD-FMEA流程20-sep

描述
幾乎不可能發生 有輕度發生的可能 有可能發生 偶爾發生,但不佔有大 的比例 經常發生 幾乎不可避免
劃分標準 發生率
1/1500K 1/150K 1/15K 1/2K 1/400 1/80 1/20 1/8 1/3 1/2
Cpk ≧1.67 ≧1.50 ≧1.33 ≧1.17 ≧1.00 ≧0.83 ≧0.67 ≧0.51 ≧0.33 <0.33
项目 功能
潜在缺 陷模式
潜在缺 陷后果
潜在缺陷原因
推荐行动
责任者目 标完成日
采取的措施
产品啤塑
产品检验
模具设计
嚴重度(Severity)
• 恒量失效的影響程度 • 失效影響: 產品,模具或制程的某一失效對產品外觀,結構,功能,性 能穩定性,可靠性影響. 或對下一個制程,使用者和設備的影響或對 最終客戶,政府法規,安全,環保的違及. • 劃分標準-----主觀判定 1-----幾乎不會有甚麼影響 嚴重度(S)劃分標準 10---會違及安全,法規
二、模具设计
1,模具结构的合理性 系统合理性 5,模具的整体强度的保证 6,模具的磨损与寿命的控制 7,产品预知缺陷的控制 8,产品的开模可行性保证 9,产品异形导致模具缺陷的控制 10,模具的整体稳定性保证
高
控制有较多机会可探测出
X
X
很高 很高
控制几乎确定能探测出 肯定能探测出
X X
X
2 1
检验类别: 防错 检验类别:A.防错 B. 量具 C.人工检验 人工检验
项目功能:
一、产品啤塑
1,胶厚与缩水事前分析与改良 2,产品因变形而无法保证公差的预防 3,产品的尺寸波动受成型影响的预防 4,产品胶厚不均而产生烘影的预防 5,产品的哪些部位易产生披锋毛刺的预防 6,产品受形状限制而产生缺胶的预防改良 7,产品某些部位易产生断裂的预防改良 8,要求的进胶方式使表面产生流纹的预防改良 9,产品脱模不良的预防改良
FMEA 步骤图
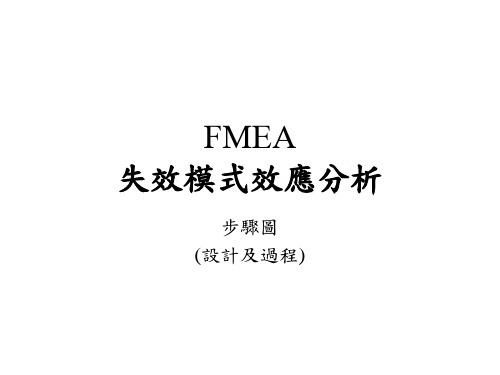
嚴重度Severity
頻度的評份準則
頻度是指具體的失效起因/機理發生的頻率。
頻度Occurrence
步驟 5 確定原因
潛在失效的原因
所謂潛在失效的原因是指一個設計薄弱部 分的跡象,其作用結果就是失效模式。 常用查明失效起因的方法:
– 腦激盪(Brainstorming) – 魚骨圖(Fishbone Diagram) – 實驗設計(Design EA
等與原先產品設定機能的目標不符的情形。這些 狀況的產生會造成顧客對製造者與銷售者的不滿, 可能產生的情形有大有小、也因使用時間有長有 短而發生,對於設計、生產乃至檢驗者而言,都 需要對自己負責的部份將隱藏的失效因素排除。 所以失效是客戶抱怨的主要來源,必頇依照一定 的步驟予以分析解構,將這樣具模組化的作業方 式整合成一種模式,稱之為失效模式分析 (FMEA)。
步驟 6 現行的探測方法/過程控制
現有的措施
列出預防措施,設計確認/驗証或其他活動, 這些活動將保証該設計對於考慮的失效模 式和/或原因來說是恰當的。可從以不三種 控制方法考慮:
1. 防止或減小失效模式出現 2. 查出原因并找到糾正措施 3. 查明失效模式
不易探測度評份準則
不易探測度是指在零部件離開制造工序或 裝配工序之前,於現行的探測方法/過程控 制方法找出失效原因/過程缺陷的可能性的 評份指標。
Power adaptor
Buzzer and earpiece jet for stereo
Earpiece and Off-hook button
Removable earpiece for stereo
Functional block diagram Bluetooth stereo clip headset
FMEA流程简介
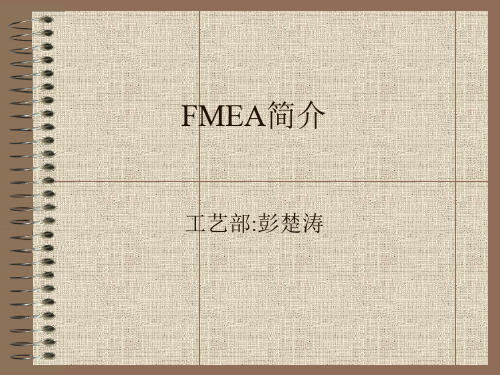
制程FMEA分析表填写要领 (七)
1.20 负责部门与完成日期:负责执行改进措施之部门 或个人,以及完成改正措施之预定日期。 1.21 效果确认:由核心小组执行对策确认完成后,并 知会相关单位;若原对策无效时,应针对不良原因再检 讨FMEA内容。 1.22 已采措施:在采取改进措施之后,应于此字段概 要说明实际采取之行动与有效日期。 1.23 采行实际对策后,此对项不良原因之严重度、发 生率、难检度及RPN,必须重新计算。如果没有采取任 何改进措施,则本字段留空。 1.24 改进后之关键指数:采行实际对策后,此对项不 良原因之严重度、发生率、难检度及RPN,必须重新计 算。如果没有采取任何改进措施,则本字段留空。
制程FMEA分析表填写要领 (四)
1.12 . 分类:填入需要特别处理、管制、或检验之产品特 性分类之任何特殊特性制程(如:主要的、关键的…等) 或依客户指定之重要特性代号(如:◇)加以注记。 1.13. 潜在失效原因:将每一个失效模式说明其可能之原 因,注意应将一切可能之原因尽量列出,且尽可能简要而 完整,以便使改善行动能以适当的原因为对象进行。如: 不适当的扭力-过大或过小、焊接不当、量具不准确、润 滑不当、零件漏装或安装位置错误…等 1.14. 发生率(O):填入潜在不良原因出现之机率,计算 方式如下表: ..\..\发生率计算方法.xls
制程FMEA分析表填写要领 (六)
5.18 改进措施的拟定,当有以下几种不良模式时应采 取对策: 5.18.1严重度评分在8分以上(含8分)。 5. 18.2关键指数(RPN)在150以上 5. 18.3关键指数(RPN)在50以上、149以下时,则由 核心小组决定是否采取对策。 5.18.4一个项目的关键指数列前三位的应采
FMEA概述及步骤
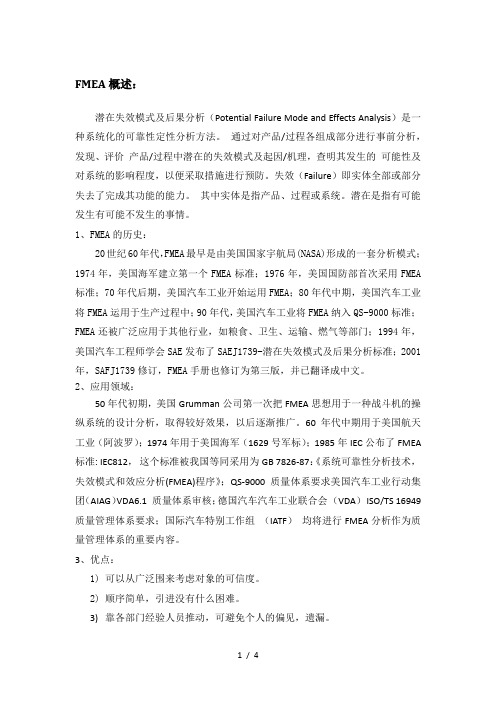
FMEA概述:潜在失效模式及后果分析(Potential Failure Mode and Effects Analysis)是一种系统化的可靠性定性分析方法。
通过对产品/过程各组成部分进行事前分析,发现、评价产品/过程中潜在的失效模式及起因/机理,查明其发生的可能性及对系统的影响程度,以便采取措施进行预防。
失效(Failure)即实体全部或部分失去了完成其功能的能力。
其中实体是指产品、过程或系统。
潜在是指有可能发生有可能不发生的事情。
1、FMEA的历史:20世纪60年代,FMEA最早是由美国国家宇航局(NASA)形成的一套分析模式;1974年,美国海军建立第一个FMEA标准;1976年,美国国防部首次采用FMEA 标准;70年代后期,美国汽车工业开始运用FMEA;80年代中期,美国汽车工业将FMEA运用于生产过程中;90年代,美国汽车工业将FMEA纳入QS-9000标准;FMEA还被广泛应用于其他行业,如粮食、卫生、运输、燃气等部门;1994年,美国汽车工程师学会SAE发布了SAEJ1739-潜在失效模式及后果分析标准;2001年,SAFJ1739修订,FMEA手册也修订为第三版,并已翻译成中文。
2、应用领域:50年代初期,美国Grumman公司第一次把FMEA思想用于一种战斗机的操纵系统的设计分析,取得较好效果,以后逐渐推广。
60年代中期用于美国航天工业(阿波罗);1974年用于美国海军(1629号军标);1985年IEC公布了FMEA 标准: IEC812,这个标准被我国等同采用为GB 7826-87:《系统可靠性分析技术,失效模式和效应分析(FMEA)程序》;QS-9000 质量体系要求美国汽车工业行动集团(AIAG)VDA6.1 质量体系审核;德国汽车汽车工业联合会(VDA)ISO/TS 16949质量管理体系要求;国际汽车特别工作组(IATF)均将进行FMEA分析作为质量管理体系的重要内容。
线束 全工序FMEA 20裁浪管

(S)
潜在的失效起因/机 理
频 度 数 (O)
现行过程 控制预防
现行过程 控制ห้องสมุดไป่ตู้测
探
测R
数 (D)
P N
措施结果
建议 措施
责任及 目标完 成日期
采取的 措施
S
O
D
R P
N
过程功要能求
参数设置错误
2 专人调机,首件确认ok后方可生产
1.首件检验. 2.IPQC3PCS/4H抽检. 5 70 NONE
裁浪管尺寸过短 影响产品特性 7
浪管切口不平整 影响后续加工 3
刀模磨损
2
1.刀模5万次复检. 2.检验刀模有磨损、缺口做报废处理.
1.QE每4~5万次复检一
次刀模.
7
2.IPQC3PCS/4H抽检.
42 NONE
CR-036FA2
5
70 NONE
2 专人调机,首件确认ok后方可生产
1.首件检验. 2.IPQC3PCS/4H抽检. 5 60 NONE
裁浪管尺寸过长 影响客户使用 6
量测仪器不良.
2 品保依CP-016CA«仪器校正程序»校验量测仪器
1.首件检验. 2.IPQC3PCS/4H抽检. 5 60 NONE
20 裁浪管
量测仪器不良. 机器设备不良. 参数设置错误
2 品保依CP-016CA«仪器校正程序»校验量测仪器
1.首件检验. 2.IPQC3PCS/4H抽检. 5 70 NONE
2
1.使用CR-011FA设备/设施每日保养纪录表对机器设备 进行点检 2.增加自动送料设备,防止浪管打结.
1.首件检验. 2.IPQC3PCS/4H抽检.
FMEA管理程序

1 目得本程序规定了在产品质量先期策划阶段引进了提供研究失效原因及其影响途径得这种早期得预防管理及改进分析方法、评定每种质量故障失效得严重程度与出现得频率,以及这种故障失效对汽车装配与使用得影响程度,也可以用在预防与纠正措施得实施中,有针对性得进行纠正,提高产品在顾客使用中得满意程度。
2适用范围本程序适用于公司在新产品开发过程中,为工艺得确定提供依据,有助于为顾客服务确定初期得标准;为未来工作提供历史性资料。
3相关文件AIAG FMEA手册4 职责4、1技术质量部就是本办法得归口管理部门。
负责组成多功能小组,多功能小组负责FMEA得编制工作,并在生产过程中应用FMEA,使产品得质量、可靠性与公司产品得生产能力不断提高。
4、2ﻩ在接到新产品之后,技术质量部负责组成多功能小组,根据新产品得特点编制相应得 FMEA表。
4、3ﻩ当产品发生失效模式时,由技术、质量部牵头成立项目小组,负责找出具体失效得原因。
4、4当产品发生失效模式,并找到具体得失效原因时,具体得预防或改进措施由生产部负责贯彻与执行。
5工作程序5、1风险顺序数(RPN)就是严重度(S),频度数(O)与探测数(D)得乘积。
5、1、1 风险顺序数将决定工作中得优先选定,这个值可用于采取对过程中那些担心得事项进行排序。
RPN取值范围就是“1”到“1000”之间。
ﻩ过程设计组对评价准则与分级规则应意见一致,即使因为个别过程得分析作过程设计组对评价准则与分级规则应意见一致,即使因为个别过程得分析作过程设计组对评价准则与分级规则应意见一致,即使因为个别过程得分析作各栏目说明:FMEA编号:填入FMEA文件得编号,以便查询。
项目:填入所分析得系统、子系统或零件得过程名称、编号。
过程责任:ﻩ填入整车厂、部门与小组,如果知道,还应包括供方得名称。
编制着:填入负责准备FMEA工作得工程师得姓名、电话及所在公司名称车型:填入将使用与/或正被分析过程影响得预期得年型及车型(如果已知得话)。
FMEA功能分析步骤 ppt课件

▪ 指出某时间某空间内组件间的相互作用;
▪ 组件相互作用时产生哪些有用作用?
▪ 组件相互作用时产生哪些有害作用?
2021/3/26
FMEA功能分析步骤 ppt课件
19
结构模型模板——结构矩阵
板
2021/3/26
FMEA功能分析步骤 ppt课件
20
结构模型模板——结构表
板
2021/3/26
FMEA功能分析步骤 ppt课件
练习
『练习』可乐瓶
『练习』签字笔
2021/3/26
FMEA功能分析步骤 ppt课件
36
技术系统 子系统
技术系统组件 子系统组件
2021/3/26
FMEA功能分析步骤 ppt课件
8
实例——系统组件层级分析
符号
超系统
超系统 技术系统
镜片
鼻子
镜框
耳朵
技术系统 子系统
镜腿
眼睛
金属杆
光线
塑料套
2021/3/26
系统组件:矩形框
超系统组件:六菱形
系统作用对象:圆角矩形
FMEA功能分析步骤 ppt课件
21
结构模型模板说明
2021/3/26
FMEA功能分析步骤 ppt课件
22
实例——分析组件关系
实例:眼镜与鼻子和耳朵的关系是物质关系,双向的; 眼镜与眼睛的关系是场关系,单向的。
2021/3/26
FMEA功能分析步骤 ppt课件
23
实例——结构模型
技术系统
组件模型
主要功能: 折射光线
镜框 镜片 镜腿 耳朵 眼睛 鼻子
9
实例——建立组件模型
组件模型
FMEA失效分析的步骤与方法

书山有路勤为径, 学海无涯苦作舟
四、失效分析技术
•红外热像仪
•液晶
书山有路勤为径, 学海无涯苦作舟
四、失效分析技术
• 7、电子扫描(SEM)及能谱分析(EDX)
– 原理:利用阴极所发射的电子束经阳极加速, 由磁透镜聚焦后形成一束直径为几百纳米的电 子束流打到样品上激发多种信息(如二次电子 ,背散射电子,俄歇电子,X射线),经收集 处理,形成相应的图象,通常使用二次电子来 形成图象观察,同时通过特征X射线可以进行 化学成分的分析。
– 分析人员须考虑潜在的损坏和每项分析的目的
书山有路勤为径, 学海无涯苦作舟
记住木匠遵循的规律:测量两次才锯一次
四、失效分析技术
• 高级的DE-CAP设备原理图(一般用于集成电路)
书山有路勤为径, 学海无涯苦作舟
四、失效分析技术
• 6、定位技术(HOT SPOT)
– 红外热像仪,液晶探测
• 原理:将失效的芯片通电,在失效点附近会有大的 漏电通过,这部分的温度会升高,利用红外热像仪 或芯片表面涂液晶用偏振镜观察(可以找到失效点 ,从而可以进一步针对失效点作分析
例:DF-M的焊锡气孔(手动与自动制程的差异 )
书山有路勤为径, 学海无涯苦作舟
四、失效分析技术
•手动制程
•自动制程
书山有路勤为径, 学海无涯苦作舟
四、失效分析技术
• C-SAM
– 原理:利用超声脉冲探测样品内部的空隙缺陷 等,超声波对于不同的介质都会产生发射波, 如果遇到空气即100反射,该技术是对器件分层 最有效的检测方法
四、失效分析技术
• 扫描电镜的应用
– 用来观察光学显微镜下观察不到的细微结构, 如观察芯片击穿点的立体形貌,针孔等
FMEA工作步骤及主要内容

FMEA工作步骤及主要内容FMEA工作步骤及主要内容1、准备工作1.1 管理层确定分析小组章程。
(领导制定,见同文件夹中PHA 研究组章程文件)1.1.1 确定工作组职责。
1.1.2 确定分析目的任务及对象范围。
1.1.3 确定日期及时间要求。
1.2 确定小组组员人选并进行工作安排。
(见同文件夹中分析组成员构成需求表文件)1.2.1 选择小组组长。
(领导负责)1.2.2 选择组员。
1.2.3 通知组员及其领导。
1.2.4 召开小组组织会议(管理层参加,会议中讨论小组工作章程,解答工作组关于章程的疑问,告知工作组现有资源、向何处求助、确定工作优先安排等事项)。
1.3 收集组织资料包。
(见同文件夹中分析资料要求文件)1.3.1 工艺描述。
工艺设计依据、工艺原理,分析小组人手一份。
1.3.2 工艺流程图。
工艺流程的概括描述,分析小组人手一份。
1.3.3 P&ID图。
管道和仪表流程图,分析小组人手一份(A3尺寸),另提供1#大图一套。
分析小组人手一份。
1.3.4 平面布置图和危险区域图。
生产装置的平面布局图和危险区域划分以及消防、疏散通道设置等,1.3.5 有害物质清单/存量及化学品安全技术说明书(MSDS)。
工艺中所涉及的所有物料,包括:原料、中间产物、最终产品、添加剂、辅助物料、催化剂,现场必备。
1.3.6 设备设计资料。
设备的设计依据、设备规格、图纸,现场必备。
1.3.7 自控系统控制逻辑图。
工艺部分控制逻辑和安全连锁控制逻辑,现场必备。
1.3.8 操作规程包括工艺卡片。
操作规程、应急预案、工艺卡片、设备修保规程,现场必备。
1.3.9 技术改造资料。
改造清单、改造原因、改造结果等,现场必备。
1.3.10 以往事故和危害事件分析报告。
事故原因、后果及整改措施,尽可能提供分析小组。
1.3.11 压力释放阀等安全装置的计算书和相关文件。
尽可能提供分析小组。
1.3.12 以往的PHA报告及类似分析文件。
尽可能提供分析小组。
FMEA教程
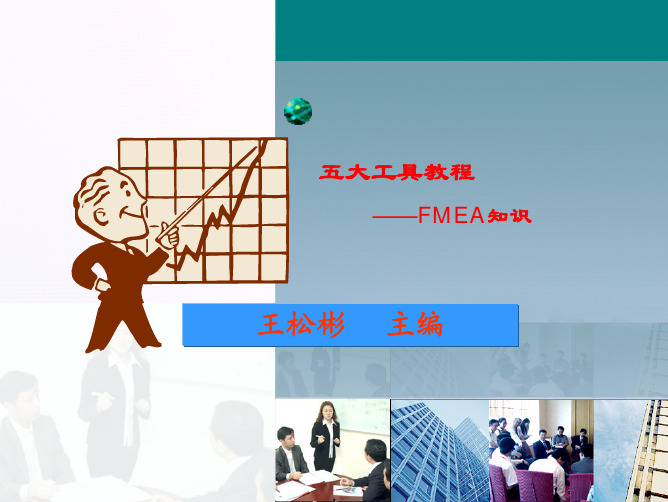
wsb
6
FMEA概述
•虽然FMEA的编制责任通常都指派到某个 人,但是FMEA的输入应是小组的努力。 小组应由知识丰富的人员组成(如设计 、分析/试验、制造、装配、服务、回收 、质量及可靠性等方面有丰富经验的工 程师)。FMEA由责任单位的工程师开始 启动,责任单位可能是原设备制造厂( OEM,即生产最终产品)、供方或分承包 方。
wsb
24
设计潜在失效模式
•典型的失效模式可包括,但不限于:
•裂纹、变形
•松动、泄漏
•粘结、氧化
•断裂、不传输扭矩
•打滑(不能承受全部扭矩)、无支撑(结
构的)
•支撑不足(结构的)、刚性啮合
•脱离太快、信号不足
•信号间断、无信号
•漂移
wsb
25
设计潜在失效模式
•注:潜在失效模式应以规范化或技术术语来 描述,不必与顾客察觉的现象相同
FMEA编号 1234 ①
X子系统
(设计FMEA)
共 1 页,第 1 页
部件 01.03/车密封 ② 设计责任 车身工程部队
③ 编制人 泰特-X6412-车身工程师 ④
车型年/车辆类型 199X/狮牌 4门/旅行车 ⑤ 关键日期 9X年03 01
⑹ FMEA日期(编制)8X 03 22修订 8X
07 14⑦
wsb
7
FMEA 之沿革
Chrysler, Ford GM, ASQ, AIAG
1993出版FMEA手冊 1995出版FMEA手冊 2001出版FMEA手冊
Grumman Aircraft Company
1950 FMEA飛機主 操縱系統失效分析
Boeing & Martin Marietta Aerospace Company
过程FMEA管理程序

a)为了减小失效发生的可能性,需要修改过程和/或设计;
b)只有修改设计和/或过程,才能减小严重度数;
文件名称
过程FMEA管理程序
页次
5/5
c)为了增加探测的可能性,需要修改过程和/或设计;
d)积极的纠正措施是制定永久性的改进措施,以及采用统计过程控制(SPC)方法指定预防缺陷发生的措施。
文件名称
过程FMEA管理程序
页次
2/5
潜在失效的后果。在FMEA准备中,应假定提供的零件/材料是合格的。
4.4.11潜在失效后果:是指失效模式对顾客的影响。在这里顾客可以是下道工序、后续工序或工位、代理商、最终用户。当评价潜在失效后果时,应依据可能顾客注意到的或经历的清苦青年感来描述失效的后果。对最终用户来说失效的后果应一律用产品或系统的性能来描述(噪音、发热、工作不正常或间隙性工作、外观不良、不起作用等);若顾客是下道工序、后续工序或工位,失效的后果应用过程/工作性能来描述(如无法安装、不匹配、危害操作者、加工余量过大或过小、损坏设备等)。
可以考虑三种类型的过程控制/特性,即:
a)组织失效起因/机理或失效模式/后果的发生,或减小其出现率;
b)查明起因/机理并找到纠正措施;
c)查明失效模式。
如有可能,应优先运用控制方法a);其次使用方法b);最后使用方法c)。
4.4.17探测度(D):是指零部件(含半成品、成品)在制造或装配过程中,利用控制方
6
低
产品需100%返工,整机能运行,有较多缺陷,顾客有些不满
5
很低
产品经筛选,部分需要返工,外观质量有缺陷,多数顾客能发现
4
轻微
部分产品需要在生产线上原工位返工,外观质量缺陷很轻微,很少顾客发现有缺陷
- 1、下载文档前请自行甄别文档内容的完整性,平台不提供额外的编辑、内容补充、找答案等附加服务。
- 2、"仅部分预览"的文档,不可在线预览部分如存在完整性等问题,可反馈申请退款(可完整预览的文档不适用该条件!)。
- 3、如文档侵犯您的权益,请联系客服反馈,我们会尽快为您处理(人工客服工作时间:9:00-18:30)。
高
控制有较多机会可探测出
X
X
很高 很高
控制几乎确定能探测出 定能探测出
X X
X
2 1
检验类别: 防错 检验类别:A.防错 B. 量具 C.人工检验 人工检验
项目功能:
一、产品啤塑
1,胶厚与缩水事前分析与改良 2,产品因变形而无法保证公差的预防 3,产品的尺寸波动受成型影响的预防 4,产品胶厚不均而产生烘影的预防 5,产品的哪些部位易产生披锋毛刺的预防 6,产品受形状限制而产生缺胶的预防改良 7,产品某些部位易产生断裂的预防改良 8,要求的进胶方式使表面产生流纹的预防改良 9,产品脱模不良的预防改良
等級/評分(Rank) 劃分標準(Criteria)
1-2 (Minor) 幾乎不會對產品或模具有任何影響,即使有影響,客戶亦不會注意.
3~4(Low)
客戶可能會注意,可能會對客戶造成外观、裝配和使用上的輕微不便及不 满意.可能會使下道工站輕微的重工.精明的客户能观察到该种失效. 會造成客戶的不滿意,造成客戶抱怨,甚至會導至重工動作發生.普通客户 能观察到到该种失效. 可能造成客戶很不滿意,並導致客戶重大抱怨,以致客戶退货并对公司的信 誉度下降,但不會導致安全事故或違及政府法規. 導致客戶停線或對產品或模具有致命性的功能性影響以致客户的丢失或可 能導致安全事故,或違及政府法規.
描述
幾乎不可能發生 有輕度發生的可能 有可能發生 偶爾發生,但不佔有大 的比例 經常發生 幾乎不可避免
劃分標準 發生率
1/1500K 1/150K 1/15K 1/2K 1/400 1/80 1/20 1/8 1/3 1/2
Cpk ≧1.67 ≧1.50 ≧1.33 ≧1.17 ≧1.00 ≧0.83 ≧0.67 ≧0.51 ≧0.33 <0.33
二、产品检验
1,公差要求高的产品根据实际加工能力 进行评估控制 2,产品的不可测量度预先设计制做治具 3,产品的测量基准的明确保证可测量度 4,探测出在测量条件不能测量的尺寸开 模前评估 5,确保尺寸标注明确清晰 6,外观面、等级、功能面注明 7,特殊的外观要求在图纸上备注说明 8,标注量产重点寸法 9,水口位加工的高度标准明确 10,特殊加工收货标准 11,测定产品的冷却要求 12,样品检验的程序明确
项目 功能
潜在缺 陷模式
潜在缺 陷后果
潜在缺陷原因
推荐行动
责任者目 标完成日
采取的措施
产品啤塑
产品检验
模具设计
嚴重度(Severity)
• 恒量失效的影響程度 • 失效影響: 產品,模具或制程的某一失效對產品外觀,結構,功能,性 能穩定性,可靠性影響. 或對下一個制程,使用者和設備的影響或對 最終客戶,政府法規,安全,環保的違及. • 劃分標準-----主觀判定 1-----幾乎不會有甚麼影響 嚴重度(S)劃分標準 10---會違及安全,法規
5~6(Moderate)
7~8(High) 9~10(Very High)
發生率(Occurrence)
• • 某一原因而導致失效發生的幾率 劃分標準: Cpk 主觀判定 統計資料 1----幾乎不會發生 10---幾乎肯定會發生
發生率(O)劃分標準
等級/評分
1(Remote) 2(Very Low) 3(Low) 4(Moderate) 5(Moderate) 6(Moderate) 7(High) 8(High) 9(Very High) 10(Very High)
Lintall Electrical Appliances Plastic Mfg.Co.
先豪家電塑膠制品廠
客户 穴数
机种 编制
品名 审核
品号 日期
材 料
客户确认
潜在缺陷模式和影响分析(D。P-FMEA)
先豪公司 客户名称: 产品名称: 模具编号: 严 重 度 (S) 设计/过程责任: 关 键 日 期: 主要参加人: 发 可 生 侦 风险 概 现行设计控制 测 系数 率 度 RPN (O) (D) 工程/工模/成型/品质 FMEA编号: 页 码: 编 制 人: 编制日期: 严 重 度 (S) 发 可 生 侦 风险 概 测 系数 率 度 RPN (O) (D)
二、模具设计
1,模具结构的合理性 2,模具浇注系统合理性 3,模具冷却系统合理性 4,模具顶出系统合理性 5,模具的整体强度的保证 6,模具的磨损与寿命的控制 7,产品预知缺陷的控制 8,产品的开模可行性保证 9,产品异形导致模具缺陷的控制 10,模具的整体稳定性保证
二、模具设计
1,模具结构的合理性 2,模具浇注系统合理性 3,模具冷却系统合理性 4,模具顶出系统合理性 5,模具的整体强度的保证 6,模具的磨损与寿命的控制 7,产品预知缺陷的控制 8,产品的开模可行性保证 9,产品异形导致模具缺陷的控制 10,模具的整体稳定性保证
一、产品啤塑
1,胶厚与缩水事前分析与改良 2,产品因变形而无法保证公差的预防 3,产品的尺寸波动受成型影响的预防 4,产品胶厚不均而产生烘影的预防 5,产品的哪些部位易产生披锋毛刺的预防 6,产品受形状限制而产生缺胶的预防改良 7,产品某些部位易产生断裂的预防改良 8,要求的进胶方式使表面产生流纹的预防改良 9,产品脱模不良的预防改良
二、产品检验
1,公差要求高的产品根据实际加工能力 进行评估控制 2,产品的不可测量度预先设计制做治具 3,产品的测量基准的明确保证可测量度 4,探测出在测量条件不能测量的尺寸开 模前评估 5,确保尺寸标注明确清晰 6,外观面、等级、功能面注明 7,特殊的外观要求在图纸上备注说明 8,标注量产重点寸法 9,水口位加工的高度标准明确 10,特殊加工收货标准 11,测定产品的冷却要求 12,样品检验的程序明确
難檢度(Detection)
• • 在現行的控制措施下,偵測失效發生的能力 劃分標準 主觀判定 統計資料 1----肯定能探测出 10----绝/肯定不可能探测 探测性 准则 A 几乎不可 能 很微小 微小 很小 小 中等 中上 绝/肯定不可能探测 控制方法可能探测不出来 控制有很少的机会能探测出 控制有很少的机会能探测出 控制可能能探测出 控制可能能探测出 控制有较多机会可探测出 X X X X 检查类别 B C X X X X X 不能探测或没有检查 只能通过间接或随机检验来实现控制 只通过目测检查来实现控制 只通过双重目测检查来实现控制 用制图的方法,如SPC来实现控制 当零件离开工位后的计量测量的控制,或者零件离 开工位后100% 的G/NG量具测量。 在后续工位上的误差探测,或在作业准备时进行测 量和首件检查(仅适用于作业准备的原因) 在工位上的误差探测,或利用多层验收在后续工序 上进行误差探测:供应、选择、安装、确认。不能 接受有差异零件。 在工位上的误差探测(自动测量并自动停机)。不能 通过有差异的零件。 由于有关项目已通过过程/产品设计采用了防错措施, 有差异的零件不可能产出 。 探测方法的推荐范围 探测 度 10 9 8 7 6 5 4 3