焊管涡流探伤
涡流探伤的基本概念

涡流探伤的基本概念涡流探伤的定义与原理涡流探伤是一种非破坏性检测技术,用于检测金属表面或近表层的缺陷。
涡流探伤基于电磁感应原理,通过交变电流在导体表面产生涡流,然后检测涡流的改变来判断是否存在缺陷。
这种技术可以广泛应用于工业领域,特别是对于金属材料的缺陷检测和质量控制具有重要意义。
涡流探伤的应用领域涡流探伤技术广泛应用于许多领域,包括航空航天、汽车制造、电力设备、石油石化等行业。
在航空航天领域,涡流探伤被广泛应用于飞机的发动机叶片、机身结构等关键部件的缺陷检测。
在汽车制造领域,涡流探伤被用于检测汽车引擎的缺陷,确保其性能和可靠性。
在电力设备领域,涡流探伤可以用于检测发电机转子、变压器和电力线路等设备的缺陷,保证电力系统的正常运行。
在石油石化行业中,涡流探伤被用于检测管道和储罐的裂纹和腐蚀等缺陷,防止泄漏和事故的发生。
涡流探伤的优点与局限性涡流探伤具有许多优点,使其成为一种被广泛采用的缺陷检测技术。
首先,涡流探伤是一种非接触性的检测方法,无需直接接触被检测物体,减少了对被检测物体的破坏。
其次,涡流探伤适用于对各种导电材料进行缺陷检测,包括铁、钢、铝、铜等金属材料。
此外,涡流探伤对缺陷的检测灵敏度高,可以检测到微小的表面和近表层缺陷。
然而,涡流探伤也存在一些局限性。
首先,涡流探伤只能检测导电材料的缺陷,无法用于非导电材料的检测。
其次,涡流探伤对于较深的缺陷检测灵敏度较低,可能会漏检。
此外,涡流探伤的设备和操作技术相对复杂,需要经过专门的培训和实践才能熟练运用。
涡流探伤的主要设备与工作流程涡流探伤通常使用的设备主要包括涡流探头、发生器、放大器和显示器等。
涡流探头是用于产生涡流的感应线圈,一般由线圈和芯片两部分组成。
发生器通过输入交流电源产生交变电流,驱动涡流探头产生涡流。
放大器用于放大涡流信号,使其能够被显示器正确显示。
工作流程通常包括以下几个步骤:选择合适的涡流探头和参数;对被检测物体进行表面处理,以确保涡流探头能够与其充分接触;通过调整发生器和放大器的参数,使涡流信号最大化;将涡流信号传送到显示器上,通过观察显示器上的信号变化判断是否存在缺陷。
钢管涡流探伤检验方法

钢管涡流探伤检验方法
钢管涡流探伤检验,那可真是个超厉害的技术!想象一下,它就像一位超级侦探,能在不破坏钢管的情况下,找出里面的小毛病。
那它到底咋操作呢?首先,把钢管放在检测设备上,就像把宝贝放在一个特殊的舞台上。
然后,开启涡流探伤仪,这玩意儿就像一个魔法棒,能发出神奇的信号。
这些信号在钢管里穿梭,就像小蚂蚁在寻找食物。
如果钢管里有缺陷,信号就会发生变化,就像小蚂蚁遇到了大石头。
这时候,检测人员就能根据信号的变化,判断出钢管有没有问题。
哇塞,是不是超神奇?
在这个过程中,安全性那是杠杠的!不用担心会对人造成伤害,就像在公园里散步一样安全。
稳定性也没得说,就像一座坚固的城堡,不会轻易被打倒。
那它都能用在啥地方呢?建筑工地上的钢管、石油管道、汽车零件,好多地方都能看到它的身影。
它的优势可多了,速度快得像闪电,一下子就能检测好多钢管。
而且还很准确,就像有一双火眼金睛,不放过任何一个小缺陷。
咱来看看实际案例吧!有一次,在一个大工地上,用涡流探伤检验方法检测了一批钢管。
哇,一下子就找出了几个有问题的钢管,避免了潜在的危险。
要是没有这个方法,说不定哪天就会出大事呢!
所以啊,钢管涡流探伤检验方法真的是太棒了!它就像一个守护天使,保护着我们的安全。
大家一定要重视这个方法,让它为我们的生活带来更多的保障。
GBT7735-2004 钢管涡流探伤检验方法

http://www.industryinspection.com
GB T 3-20 / 7 5 04 7
. 盈L -A-
N 青
中国工业检验检测网
http://www.industryinspection.com
GB T 3-20 / 7 5 04 7
钢管涡流探伤检验方法
1 范围
本标准规定了无缝钢管和焊接钢管( 埋弧焊管除外) 涡流探伤原理、 探伤要求、 探伤方法、 对比试样、
采用不同的涡流探伤技术时的人工缺陷形状, 规定如下:
a 采用穿过式线圈时, ) 试样人工缺陷形状为通孔; b 采用钢管旋转/ ) 扁平式线圈时, 试样人工缺陷形状为通孔或槽 口; c 采用扇形式线圈涡流探伤检测焊缝时 , ) 试样人工缺陷形状为通孔 。 63 对比试样人工缺陷位置 . 63 1 使用穿过式线圈涡流探伤技术时, 比试样上应有 5个径向钻孔 , . . 对 钻透试样钢管的整个壁厚 。 其中位于试样钢管中部且沿圆周方向的 3个孔应彼此间隔 10, 20试样钢管的钻孔在长度方向上相隔距 离应不小于 20 焊接钢管应有 1 0 mm, 个孔位于焊缝上。另一种办法是 , 在试样钢管中部只钻打 1 个孔 ,
涡流检查方法的局限性及其他说明应当注意的是钢管在进行涡流探伤检查时在靠近检测线圈的钢管表面及近表面上其检测灵敏度为最高由于趋肤效应的影响随着与检测线圈之间距离的增加其检测灵敏度将逐渐减小因此对于同样大小的缺陷处于管内壁的缺陷所反应出来的信号幅度将小于外壁上的缺陷检测设备在探测外表面和内表面上缺陷方面的能力是由多种因素所决定的但是最主要取决于被检钢管的壁厚和涡流激励频率及磁饱和强度在一定的磁化强度条件下施加到检测线圈的激励频率决定了所建立的涡流场强度能够穿透钢管壁厚的深度激励频率越高穿透能力越低反之激励频率越低穿透能力越高在选择仪器参数时对被检钢管导电率导磁率等物理参量的影响也应予考虑确切地说采用磁饱和装置的钢管涡流探伤存在着两种检测机理其一是涡流效应其二是漏磁效应此外采用多频涡流检测技术可以在一定程度上兼顾钢管内外壁的检测灵敏度并可同时抑制某些规则的干扰信号如晃动等
钢管涡流探伤报告记录内容

钢管涡流探伤报告记录内容1. 实验目的本次实验的目的是对钢管进行涡流探伤,通过检测和记录涡流探伤过程中的信号变化,判断钢管表面是否存在缺陷,并对缺陷进行定位和表征。
2. 实验装置与仪器- 涡流探伤系统:由发电机、控制器和传感器组成;- 钢管样品:长度1m,直径10cm,材质为无缝钢管;- 计算机:用于接收和分析实验数据。
3. 实验步骤3.1 准备工作使用超声波清洗仪对钢管表面进行清洗,确保表面无杂质和污垢。
3.2 连接涡流探伤系统将传感器插入探头,并将探头放置在钢管表面。
将控制器和发电机与计算机连接,确保实验装置处于正常工作状态。
3.3 开始涡流探伤启动涡流探伤系统,设定合适的探伤参数(频率、电流、增益等),并开始记录实验数据。
3.4 数据采集通过控制器,系统开始发送电流到探头,产生电磁感应作用。
利用传感器感应到的信号,采集数据,并通过传输到计算机进行处理和分析。
3.5 缺陷定位和表征根据实验数据的变化趋势和特征,判断钢管表面是否存在缺陷。
若存在缺陷,通过分析数据得出缺陷的位置、大小和类型,并记录下来。
3.6 实验结果分析与比对将实验记录与钢管样品的实际情况进行比对,分析实验结果的准确性和可靠性。
若需要,可以进行多次实验并比对结果,以提高实验的可信度。
4. 数据处理与分析通过对采集到的实验数据进行处理和分析,可以获取以下信息:- 缺陷的位置和长度;- 缺陷的形状和类型(如裂纹、气孔等);- 缺陷的深度和宽度等特征。
5. 实验结论与建议根据实验结果和数据分析,得出以下结论:- 钢管表面存在缺陷,主要为裂纹和气孔;- 缺陷的位置多集中在钢管的两侧和焊接部位;- 缺陷的长度和宽度多在合理范围内,对钢管的使用安全性没有明显影响。
在后续实验中,可以进一步完善实验参数设置,提高涡流探伤系统的灵敏度和准确性。
同时,加强对实验数据的分析能力,提高对缺陷的判断和评估。
a涡流探伤仪的技术参数

a涡流探伤仪的技术参数摘要:一、涡流探伤仪简介二、涡流探伤仪的主要技术参数1.频率范围2.增益3.相位4.驱动电压5.采样频率6.滤波方式7.报警方式8.探头类型9.显示模式10.平衡方式11.存储功能12.通讯功能13.内置电源14.外部电源15.外形尺寸和重量正文:一、涡流探伤仪简介涡流探伤仪是一种利用涡流原理进行无损检测的仪器,广泛应用于金属材料和零部件的探伤。
它具有探伤、涂层测厚和电导率测量功能,可以对各种金属材料和零部件进行缺陷检测,如焊缝裂纹、铜管、无缝钢管、不锈钢管的折叠、结疤、凹坑、列横、导板划痕、横裂或离层等。
二、涡流探伤仪的主要技术参数1.频率范围:涡流探伤仪的工作频率一般在50Hz至10MHz之间,频率的选择会影响到探伤深度。
较低的频率适用于浅层检测,而较高的频率适用于深层检测。
2.增益:增益是控制信号强度的一个重要参数,可以在0至80dB之间调整。
增益的大小影响到检测信号的灵敏度,增益越大,灵敏度越高,但同时噪声也会增加。
3.相位:相位是涡流探伤仪的一个关键参数,可以进行359步进1的调整。
相位的变化会影响到显示效果,合适的相位设置可以使缺陷信号更加清晰。
4.驱动电压:驱动电压是激励探头产生涡流的动力来源,可以通过八档可调的方式进行调整。
适当的驱动电压可以提高探头的灵敏度和检测范围。
5.采样频率:采样频率决定了检测信号的分辨率,涡流探伤仪的采样频率通常为40MHz,12位数据采集,可以实现高精度的信号处理。
6.滤波方式:滤波方式采用数字滤波技术,可以有效消除噪声和干扰信号,提高检测信号的质量。
7.报警方式:报警方式包括幅度和相位报警,报警域为3个,分别为A、B、C。
当检测到异常信号时,仪器会发出报警通知。
8.探头类型:涡流探伤仪采用发射式、差分式、绝对式探头,不同类型的探头适用于不同的检测场景。
9.显示模式:显示模式包括阻抗平面显示和时基扫描显示,方便用户实时观察检测信号的变化。
BS EN10246-3无缝 焊接钢管涡流探伤.

钢管非破坏性试验---第3部分: 无缝钢管和焊接钢管(埋弧焊除外)的自动涡流探伤欧洲标准EN 10246-3: 1999 为英国标准状态.国家标准前言该英国标准为官方英语版本的EN10246-3:1999.该英国标准包含BS 3889-1:1983的元素. 标准附件A中完整列出EN 10246的部分. 该标准部分代替了BS 3889-1:1983, 并且当所有相关部分被发布时BS 3889-1: 1983将被撤回.英国参与的准备工作被委托给技术委员会,承压用钢的ISE/73, 承压钢管的ISE/73/1, 责任如下:---协助咨询者理解文本---向负责的欧洲委员会提交任何关于解释或改变建议的查询, 并保持英国的利益通报---监视相关的国际和欧洲发展并在英国发布它们代表该委员会的组织架构清单可以通过向委员会秘书要求获得相关引用本文所提及到的国际或欧洲出版实施的英国标准可以在BSI 标准中”国际标准对照索引”中找到, 或者通过使用BSI 标准文件电子目录的”查找”设置找到.仅英国标准不意味着包括合同所有必须的条款.符合英国标准本身并不赋予法律义务的豁免权页面摘要这份文件包括封面, 封二和EN标准的标题页第2至第14页, 封三及封底文档最后一次发行时显示BSI版权声明发布以来下达的修改修改编号日期意见钢管非破坏性试验---第3部分: 无缝钢管和焊接钢管(埋弧焊除外)的自动涡流探伤该欧洲标准于1999年10月6日被CEN通过CEN成员必须遵守CEN/CENELEC 内部规定,保证赋予本欧洲标准的国家标准状态没有发生改变.该欧洲标准拥有三种官方版本(英语, 法语, 德语). 其他任何语言的版本需由CEN成员负责翻译并且知悉中央秘书处的状态和官方版本一致.以CEN 成员为国家标准主体的有, 澳大利亚, 比利时, 捷克, 丹麦, 芬兰, 法国, 德国, 希腊, 冰岛, 爱尔兰, 意大利, 卢森堡, 荷兰, 挪威, 葡萄牙, 西班牙, 瑞典, 瑞士和英国.内容前言 (3)1 范围 (4)2 引用标准 (4)3 一般要求 (4)4 试验方法 (4)5 参考标准 (7)6 设备校准和检查 (10)7 接收标准 (11)8 检测报告 (12)附件A(信息) EN 10246标准的钢管非破坏性试验部分的表格 (13)附件B(信息) 与涡流探伤方法有联系的限制准则 (14)本欧洲标准已由技术委员会ECISS/TC 29 “钢管和钢管用配件”处编制, 其秘书由UNI担任.本欧洲标准将被赋予国家标准地位且在2000年5月前以相同文本附件的形式发布. 和国家标准有冲突的将在2000年5月前被撤销.本欧洲标准已由欧盟委员会和欧洲自由贸易协会按CEN授权制备. 本欧洲标准被认为是这些应用和产品标准的支持标准. 这些应用和产品本身支持一些新方法指令的安全性要求, 同时提供参考给本欧洲标准.按照CEN/CENELEC内部规定, 下面国家标准的组织成员必须遵守本欧洲标准: 澳大利亚, 比利时, 捷克, 丹麦, 芬兰, 法国, 德国, 希腊, 冰岛, 爱尔兰, 意大利, 卢森堡, 荷兰, 挪威, 葡萄牙, 西班牙, 瑞典, 瑞士和英国.这部分EN 10246 标准规定了无缝管和焊管自动涡流试验的要求, 除埋弧焊管的探伤外. 本标准规定了接收等级, 过程校准并且给出了测试局限的指导.这部分EN 10246标准应用于外径大于等于4mm管件的检查.欧洲标准EN 10246 “钢管的非破坏性试验”包含部分体现在附件A中.2 引用标准这部分EN 10246 包含了已标记日期和未标记日期的参考文件, 来源于其他出版文献. 这些引用标准被引用于文本中适当的地方, 并且在后面列出其出版文献. 对已标记日期的, 近期有变更或任何应用于EN 10246这部分标准的出版文献的变更, 只有当文件变更或修改时才被包含. 对于未标记日期的参考, 出版物最新版本将被引出应用.EN 20286-2 极限和适用情况的ISO系统–第2部分: 标准公差等级表和孔及杆极限偏差表(ISO 286-2: 1988)ENV 10220 无缝管和焊接管- 尺寸及单位长度重量.ISO 235 Parallel shank jobber and stub series drills and Morse taper shank drills.3一般要求3.1这部分EN 10246标准覆盖的涡流试验通常在管件完成初加工过程后实施.3.2用于试验的管件应当被充分校直并且没有外界杂物影响试验的有效性.4试验方法4.1管件将采用以下适当的技术通过涡流试验方法进行探伤:a)同芯带卷技术- 全范围(见图表1);b)管件旋转/展平带卷技术- 全范围(见图表2);c)分割带卷技术- 仅焊接管(见图表3).意识到管件两端可能有一短截无法测试. 任何未测试的端部将按照适用的产品标准要求处理.注意: 涡流试验方法的限制指导见附件B.4.2当测试的管件使用同芯带卷技术时, 最大测试管件外径严格规定为177.8 mm.测试中的相关速度变化范围不得超过+ 10%.注意1: 这里强调测试灵敏度最大值位于邻近测试带卷的管件表面并且随着壁厚的增加而减小(见附件B).注意2: 结构用方管和矩形管, 其最大尺寸的对角线为177.8mm时可用此方法进行测试.4.3当测试的管件使用旋转/展平带卷技术时, 管件和展平的带卷应当相对移动, 那样整个管件表面能被扫描到.测试中的相对移动速度变化不得超过+ 10.注意: 这里强调只有外表面破裂缺陷能被这种技术探测到.4.4当测试的管件使用分割带卷技术时, 测试带卷应当保持焊缝成适合队列, 那样整个焊缝能被扫描到. 这里对使用此技术的最大管件外径没有严格要求.测试中的相应速度变化不得超过+ 10%.注意: 这里强调测试灵敏度最大值位于邻近测试带卷的管件表面并且随着壁厚的增加而减小(见附件B).4.5 设备应当有能力区分可接受或有疑问的管件, 通过将喷码和/或分拣系统联系到触发/警报水平.1= 副线圈1 2=基本带卷3= 副线圈2 4=管件注意: 上面图表由多带卷输送简化而来, 它包括例如分离基本带卷, 差速带卷, 校准带卷图表1: 同芯带卷技术简化图(a) 旋转展平带卷技术( b) 旋转管件技术(线性管件通过旋转展平带卷集中移动) (管件螺旋运动过程中,线性展平带卷沿管件长度或固定带卷方向穿过)1= 展平带卷旋转; 2=展平带卷; 3=管件4= 管件旋转5=固定展平带卷6=转动辊注意: a) 和b)中的展平带卷可以有不同形态, 例如: 单带卷, 不同配置的多带卷, 取决于所用的设备和其他因素.图表2: 旋转/展平带卷技术简化图(螺旋扫描)1= 焊缝2=副线圈3=基本线圈4= 副线圈2 5=管件6= 带卷注意: 上面图表中的带卷分割可以有不同形态, 取决于所用设备和将要检测的产品.图表3: 焊缝的分割带卷测试方法简化图5参考标准5.1通则5.1.1这部分EN 10246标准中定义的参考标准为校准非破坏性试验设备的便捷标准. 这份标准的尺寸不应被翻译成用这些设备可探测缺陷的中等尺寸.5.1.2使用参考标准出台成管状试件的检测设备应进行校准. 试验样件应指定相同的管件直径, 壁厚和表面粗糙度, 并具有相似的电磁特性.注意: 在特殊案例中, 例如测试热管或使用包含连续生产线, 可以修改校准或使用校准检查程序, 按照协议.5.1.3各种测试技术所用参考标准如下:a)采用同芯带卷技术时参考孔定义如5.2b)采用分割带卷技术时参考孔定义如5.3c)采用旋转/展平带卷技术时参考孔定义如5.45.2同芯带卷技术5.2.1当使用同芯带卷技术时, 测试工件应当含有三个圆孔, 圆孔呈放射状钻穿全工件厚度. 这三个孔圆周分布且每个孔之间间隔120度, 同时在试件的端部须有足够的纵向分离, 以便获得清晰可辨的信号指示.或者, 只有一个孔时应钻通全部试件厚度, 同时在校准和校准检查中, 工件应通过与定位孔成0度, 9度, 18度和27度的设备.5.2.2用来生产这些孔的钻具直径取决于表1所示管件的外径.参考孔的直径应当被验证并且钻具直径小于1mm时指定钻孔直径不能超过0.1mm, 钻具直径大于或等于1mm时指定钻孔直径不能超过0.2mm.表1: 接收等级和相应的管件直径尺寸的外头生产基准孔(同芯带卷技术)指定外径D1)mm钻具尺寸接收等级2) mm 指定外径D1)mm钻具尺寸接收等级2)mmE1H E2H E3H E4HD<=1010<D<=20 20<D<=44.5 44.5<D<=76.1 76.1<D<=177.8 177.8<D 3)0.60.70.81.01.21.20.70.81.01.21.41.40.81.01.31.62.02.0D<=26.926.9<D<=48.348.3<D<=63.563.5<D<=114.3114.3<D<=139.7139.7<D<=177.8177.8<D 3)1.21.72.22.73.23.73.71)按照ENV 102202)公差按照ISO 235(工作系列) 和EN 20286-2(h8)3)该表格仅应用于分割带卷技术5.3分割带卷技术5.3.1当使用同芯带卷技术时, 测试工件应当含有一个单独圆孔, 圆孔呈放射状钻穿全工件厚度.5.3.2基准孔应与试件端部有充分距离, 以便获得清晰可辨的信号指示.5.3.3用来生产这些孔的钻具直径取决于表1所示管件的外径. 基准孔应按表5.2进行验证.5.4旋转展平带卷技术5.4.1当使用旋转展平带卷技术时, 试件的外表面应包含一个纵向参考缺口.5.4.2基准孔应与试件端部有充分距离, 以便获得清晰可辨的信号指示.5.4.3参考缺口应为”N”形(参见图4), 并应平行于管件轴向. 两边应平齐, 同时底部与边部成直角.w= 宽度d=深度图表4: “N”形缺口5.4.4参考缺口应通过机械加工、电火花腐蚀或其他方法来成形.注意: 可以是圆形底部或者缺口底角是圆形的.5.4.5缺口尺寸应当如下:a)宽度w(见图表4)不应大于参考缺口的深度b)深度d(见图表4)应在表2中给出, 具有以下限制:-最小缺口深度: 0.5 mm-最大缺口深度: 1.5 mmc) 缺口深度公差参考+ 15%.d) 长度应当至少为每个独立传感器宽度的两倍,最大50mm。
涡流探伤原理

涡流探伤原理涡流探伤是一种常用的无损检测方法,它通过利用涡流感应原理来检测材料中的缺陷和异物。
涡流探伤原理的核心是利用交变磁场产生涡流,通过检测涡流感应电阻的变化来判断材料是否存在缺陷。
本文将从涡流探伤的基本原理、应用领域和优缺点等方面进行介绍。
涡流探伤的基本原理是利用交变磁场在导体中产生涡流的现象。
当导体材料表面存在缺陷或异物时,其导电性会发生变化,从而影响涡流感应电阻的大小。
通过测量涡流感应电阻的变化,可以判断材料中的缺陷情况。
涡流探伤可以对导电性材料进行检测,如金属、合金等,对于非导电性材料则需要进行表面导电处理后才能进行检测。
涡流探伤在航空航天、汽车制造、铁路运输、核工业等领域有着广泛的应用。
在航空航天领域,涡流探伤常用于飞机发动机叶片、机身结构等零部件的缺陷检测,可以及时发现隐藏在材料内部的裂纹、气孔等缺陷,确保飞机的安全飞行。
在汽车制造领域,涡流探伤可以用于发动机零部件、制动系统等的缺陷检测,提高汽车的质量和安全性。
涡流探伤的优点是检测速度快、无损伤、对表面涂层无影响,可以实现自动化检测,提高工作效率。
然而,涡流探伤也存在一些局限性,如只能检测表面附近的缺陷,不能检测材料内部的缺陷;对于非导电性材料需要进行特殊处理才能进行检测;对材料的形状和尺寸有一定的要求。
总的来说,涡流探伤是一种非常有效的无损检测方法,可以广泛应用于工业生产中,帮助生产企业提高产品质量,确保产品安全。
随着科学技术的不断发展,涡流探伤技术也在不断完善,相信在未来会有更多的应用场景和更高的检测精度。
通过本文的介绍,相信读者对涡流探伤的原理、应用领域和优缺点有了更深入的了解。
涡流探伤作为一种重要的无损检测方法,对于工业生产具有重要的意义,希望能够得到更广泛的应用和进一步的发展。
涡流探伤原理及应用

涡流探伤原理及应用涡流探伤是一种非破坏性检测方法,通常用于检测导电材料中的表面缺陷。
它基于涡流感应现象,在导体中产生感应电流,通过检测感应电流的变化来判断材料的缺陷。
涡流探伤具有高灵敏度、高速度和无接触等优点,被广泛应用于航空、汽车、电力和制造业等领域。
涡流探伤的原理是基于法拉第电磁感应定律。
当导体中有交变电流通过时,会产生变化的磁场。
这个磁场又会在导体表面诱导出涡流。
涡流的密度和深度取决于导体的电导率和磁场的频率。
当涡流通过缺陷时,由于缺陷处的电导率不同于周围材料,导致涡流的分布和密度发生变化。
通过测量这些变化,可以判断出材料中的缺陷。
涡流探伤通常使用交流电源来产生交变电流,并通过线圈或探头将磁场引入导体中。
感应线圈测量感应电流的大小和方向,从而得出涡流的分布情况。
常见的涡流探伤仪器包括传统的涡流探头和现代的涡流阵列探头。
传统涡流探头通常采用线圈绕组,适用于检测各种形状和尺寸的缺陷。
新型涡流阵列探头则可以同时测量多个点的涡流信号,从而实现更高的检测速度和精度。
涡流探伤广泛应用于各个领域。
在航空领域,涡流探伤常用于检测飞机发动机叶片、涡轮盘和航空电缆等关键部件的缺陷。
利用涡流探伤技术,可以及时发现潜在的影响安全的缺陷,避免事故的发生。
在汽车行业,涡流探伤可用于检测发动机缸体、曲轴和传动轴等零部件的裂纹和疲劳损伤。
此外,涡流探伤还广泛应用于电力领域,用于检测电力设备如发电机转子、变压器和电力线路的缺陷。
在制造业中,涡流探伤可用于检查金属管道、焊接接头和铸件等工件的缺陷,以确保产品质量和可靠性。
涡流探伤具有许多优点。
首先,它是一种非接触性检测方法,不会对材料造成损伤。
其次,涡流探伤对漏磁体不敏感,能够检测细小缺陷。
此外,涡流探伤灵敏度高,可以检测到微小的缺陷,如微裂纹、夹杂和孔洞等。
同时,涡流探伤还具有高检测速度和自动化程度高的特点,适用于批量生产和在线检测。
最后,涡流探伤还可以适应复杂的工作环境,如高温、高压和腐蚀等。
最新实用在线高频焊管涡流探伤技术

摘要全面论述了在线高频焊管涡流探伤的原理,现场问题和解决方法,简要介绍ET一258全数字电脑焊管涡流探伤仪的技术性能,旨在为广大焊管在线涡流探伤操作人员提供一份实用技术讲座资料。
1.问题的提出涡流探伤为电焊钢管生产过程中控制焊缝质量提供了一个简捷、有效的检测手段,供生产操作人员评判,及时调整焊接工艺参数,杜绝缺陷产生。
除了穿透性通孔,涡流探伤还包括一些用水压试验无法发现的缺陷,如夹杂、未焊透、沙眼、内毛刺、内壁较大的焊瘤及焊缝不平等缺陷。
涡流探伤可快速检测、报警、打标和剔除,能满足连续生产10%地检查,且设备安装在生产机组上占地面积小,操作人员少、设备投资低,无污染等,使得涡流探伤作为质量控制和代替水压作产品质量检验的手段,已日渐为众多电焊钢管生产厂家所接受,成为电焊钢管生产工艺流程中不可缺少的组成部分。
但是,从这几年的情况看,电焊钢管在线涡流探伤设备还存在一些问题,从而抑制了涡流探伤方法在电焊钢管领域的推广应用,归纳起来,主要有如下几个方面:.1.1检测问题由于国标GB 7735和GB 3092采用人工钻孔为对比试样标准缺陷,现行涡流探伤设备大都采用灵敏度很高的差分式(id f re e n )t或自比差分式(d riv er·p ik o一o u p)检测线圈。
在仪器电路设计方面,则采用高Q值带通滤波器。
而车间现场除了孔状缺陷外,较常出现的往往是成段隙缝,未焊透,开口裂纹以及未焊上的长通伤和缓变伤等轴向缺陷。
这些缺陷采用上述方法除了缓变伤无法测出外,仪器也只能在缺陷的起点和未端产生一个信号,稍逝而过,无法反映缺陷的全长,如图1。
1.2现场问题电焊钢管生产车间的环境比较恶劣,水汽、高温、粉尘、高频干扰、钢管生产过程的抖动、焊缝偏转和速度变化等无一不在干扰仪器检测,影响检测结果。
如图2,电焊钢管在生产运行过程产生的径向抖动,造成幅值很大的涡流信号(提离效应),大大降低缺陷信号的信噪比,有时甚至淹没了较小的缺陷信号。
铜管、铝管、钛管、不锈钢管涡流探伤技术

非铁磁性管/棒涡流探伤技术探伤方法的选择铜、铝、不锈钢、钛等材料归属于非铁磁性材料,高精度的非铁磁性管棒(以下简称金属管棒)表面质量要求不得有裂缝、裂纹、孔洞、焊缝未熔焊等缺陷,不得有超标的划痕、压伤等缺陷。
涡流探伤在生产企业总体分为在线和离线两种模式。
金属管棒在生产线上(简称在线)具有连续、快速生产的特点,利用制管机组的传动和固定,涡流探头直接安装在生产线上进行探伤(即在线探伤),在线探伤影响因素较多,常见有振动、高频等干扰。
在线生产速度较快,一般每分钟在几十到几百米不等,一方面因速度引起的振动会具有一定的干扰,这对生产设备要求较高,需要保证探伤位置工件平稳。
另一方面因为在线速度快,涡流探伤检测频率不能太低,这样采样率下降导致漏检,一般在线探伤选择相对较高的频率检测(致使检测深度浅)。
金属管棒下线后(简称离线),可以单独制作一套机械装置配合涡流仪进行探伤(即离线探伤),具备自动上下料、自动检测、自动报警、打标、分选等功能。
此种方法可以有效避免在线检测中的各种干扰因素,检测效果比较好,检测可靠性高,有利于成品质量控制。
不足之处是,检测速度相对在线较慢,需要单独场地和自动化设备进行辅助,一般厂家设置检测车间。
厂家可以根据自身实际情况进行选择探伤方法。
无论在线探伤还是离线探伤,系统都可以实现缺陷的实时检测、记录、报警及延时打标/报警功能,检测报告数据可以长期保存在电脑硬盘里,如需要可以进行打印输出。
焊管局部在线探伤铜棒穿过式在线探伤探头的选择不论在线探伤还是离线探头,主要涉及的探头有两种:穿过式(针对整个圆周)和局部式(只针对焊管焊缝)两种。
穿过式是指管棒从探头内孔穿过,可对管棒整个圆周面进行检测,一般多采用普通差动式线圈结构。
此种方式优点在于焊缝和母材可同时检测,但灵敏度上有所欠佳。
我司针对这个缺点,进行了系统升级,首先探伤机软硬件部分进行了信号的优化,其次把探头结构进行可改进,使信号有了两次优化放大。
BS EN10246-3无缝 焊接钢管涡流探伤

钢管非破坏性试验---第3部分: 无缝钢管和焊接钢管(埋弧焊除外)的自动涡流探伤欧洲标准EN 10246-3: 1999 为英国标准状态.国家标准前言该英国标准为官方英语版本的EN10246-3:1999.该英国标准包含BS 3889-1:1983的元素. 标准附件A中完整列出EN 10246的部分. 该标准部分代替了BS 3889-1:1983, 并且当所有相关部分被发布时BS 3889-1: 1983将被撤回.英国参与的准备工作被委托给技术委员会,承压用钢的ISE/73, 承压钢管的ISE/73/1, 责任如下:---协助咨询者理解文本---向负责的欧洲委员会提交任何关于解释或改变建议的查询, 并保持英国的利益通报---监视相关的国际和欧洲发展并在英国发布它们代表该委员会的组织架构清单可以通过向委员会秘书要求获得相关引用本文所提及到的国际或欧洲出版实施的英国标准可以在BSI 标准中”国际标准对照索引”中找到, 或者通过使用BSI 标准文件电子目录的”查找”设置找到.仅英国标准不意味着包括合同所有必须的条款.符合英国标准本身并不赋予法律义务的豁免权页面摘要这份文件包括封面, 封二和EN标准的标题页第2至第14页, 封三及封底文档最后一次发行时显示BSI版权声明发布以来下达的修改钢管非破坏性试验---第3部分: 无缝钢管和焊接钢管(埋弧焊除外)的自动涡流探伤该欧洲标准于1999年10月6日被CEN通过CEN成员必须遵守CEN/CENELEC 内部规定,保证赋予本欧洲标准的国家标准状态没有发生改变.该欧洲标准拥有三种官方版本(英语, 法语, 德语). 其他任何语言的版本需由CEN成员负责翻译并且知悉中央秘书处的状态和官方版本一致.以CEN 成员为国家标准主体的有, 澳大利亚, 比利时, 捷克, 丹麦, 芬兰, 法国, 德国, 希腊, 冰岛, 爱尔兰, 意大利, 卢森堡, 荷兰, 挪威, 葡萄牙, 西班牙, 瑞典, 瑞士和英国.内容前言 (3)1 范围 (4)2 引用标准 (4)3 一般要求 (4)4 试验方法 (4)5 参考标准 (7)6 设备校准和检查 (10)7 接收标准 (11)8 检测报告 (12)附件A(信息) EN 10246标准的钢管非破坏性试验部分的表格 (13)附件B(信息) 与涡流探伤方法有联系的限制准则 (14)本欧洲标准已由技术委员会ECISS/TC 29 “钢管和钢管用配件”处编制, 其秘书由UNI担任.本欧洲标准将被赋予国家标准地位且在2000年5月前以相同文本附件的形式发布. 和国家标准有冲突的将在2000年5月前被撤销.本欧洲标准已由欧盟委员会和欧洲自由贸易协会按CEN授权制备. 本欧洲标准被认为是这些应用和产品标准的支持标准. 这些应用和产品本身支持一些新方法指令的安全性要求, 同时提供参考给本欧洲标准.按照CEN/CENELEC内部规定, 下面国家标准的组织成员必须遵守本欧洲标准: 澳大利亚, 比利时, 捷克, 丹麦, 芬兰, 法国, 德国, 希腊, 冰岛, 爱尔兰, 意大利, 卢森堡, 荷兰, 挪威, 葡萄牙, 西班牙, 瑞典, 瑞士和英国.这部分EN 10246 标准规定了无缝管和焊管自动涡流试验的要求, 除埋弧焊管的探伤外. 本标准规定了接收等级, 过程校准并且给出了测试局限的指导.这部分EN 10246标准应用于外径大于等于4mm管件的检查.欧洲标准EN 10246 “钢管的非破坏性试验”包含部分体现在附件A中.2 引用标准这部分EN 10246 包含了已标记日期和未标记日期的参考文件, 来源于其他出版文献. 这些引用标准被引用于文本中适当的地方, 并且在后面列出其出版文献. 对已标记日期的, 近期有变更或任何应用于EN 10246这部分标准的出版文献的变更, 只有当文件变更或修改时才被包含. 对于未标记日期的参考, 出版物最新版本将被引出应用.EN 20286-2 极限和适用情况的ISO系统–第2部分: 标准公差等级表和孔及杆极限偏差表(ISO 286-2: 1988)ENV 10220 无缝管和焊接管- 尺寸及单位长度重量.ISO 235 Parallel shank jobber and stub series drills and Morse taper shank drills.3一般要求3.1这部分EN 10246标准覆盖的涡流试验通常在管件完成初加工过程后实施.3.2用于试验的管件应当被充分校直并且没有外界杂物影响试验的有效性.4试验方法4.1管件将采用以下适当的技术通过涡流试验方法进行探伤:a)同芯带卷技术- 全范围(见图表1);b)管件旋转/展平带卷技术- 全范围(见图表2);c)分割带卷技术- 仅焊接管(见图表3).意识到管件两端可能有一短截无法测试. 任何未测试的端部将按照适用的产品标准要求处理.注意: 涡流试验方法的限制指导见附件B.4.2当测试的管件使用同芯带卷技术时, 最大测试管件外径严格规定为177.8 mm.测试中的相关速度变化范围不得超过+ 10%.注意1: 这里强调测试灵敏度最大值位于邻近测试带卷的管件表面并且随着壁厚的增加而减小(见附件B).注意2: 结构用方管和矩形管, 其最大尺寸的对角线为177.8mm时可用此方法进行测试.4.3当测试的管件使用旋转/展平带卷技术时, 管件和展平的带卷应当相对移动, 那样整个管件表面能被扫描到.测试中的相对移动速度变化不得超过+ 10.注意: 这里强调只有外表面破裂缺陷能被这种技术探测到.4.4当测试的管件使用分割带卷技术时, 测试带卷应当保持焊缝成适合队列, 那样整个焊缝能被扫描到. 这里对使用此技术的最大管件外径没有严格要求.测试中的相应速度变化不得超过+ 10%.注意: 这里强调测试灵敏度最大值位于邻近测试带卷的管件表面并且随着壁厚的增加而减小(见附件B).4.5 设备应当有能力区分可接受或有疑问的管件, 通过将喷码和/或分拣系统联系到触发/警报水平.1= 副线圈1 2=基本带卷3= 副线圈2 4=管件注意: 上面图表由多带卷输送简化而来, 它包括例如分离基本带卷, 差速带卷, 校准带卷图表1: 同芯带卷技术简化图(a) 旋转展平带卷技术( b) 旋转管件技术(线性管件通过旋转展平带卷集中移动) (管件螺旋运动过程中,线性展平带卷沿管件长度或固定带卷方向穿过)1= 展平带卷旋转; 2=展平带卷; 3=管件4= 管件旋转5=固定展平带卷6=转动辊注意: a) 和b)中的展平带卷可以有不同形态, 例如: 单带卷, 不同配置的多带卷, 取决于所用的设备和其他因素.图表2: 旋转/展平带卷技术简化图(螺旋扫描)1= 焊缝2=副线圈3=基本线圈4= 副线圈2 5=管件6= 带卷注意: 上面图表中的带卷分割可以有不同形态, 取决于所用设备和将要检测的产品.图表3: 焊缝的分割带卷测试方法简化图5参考标准5.1通则5.1.1这部分EN 10246标准中定义的参考标准为校准非破坏性试验设备的便捷标准. 这份标准的尺寸不应被翻译成用这些设备可探测缺陷的中等尺寸.5.1.2使用参考标准出台成管状试件的检测设备应进行校准. 试验样件应指定相同的管件直径, 壁厚和表面粗糙度, 并具有相似的电磁特性.注意: 在特殊案例中, 例如测试热管或使用包含连续生产线, 可以修改校准或使用校准检查程序, 按照协议.5.1.3各种测试技术所用参考标准如下:a)采用同芯带卷技术时参考孔定义如5.2b)采用分割带卷技术时参考孔定义如5.3c)采用旋转/展平带卷技术时参考孔定义如5.45.2同芯带卷技术5.2.1当使用同芯带卷技术时, 测试工件应当含有三个圆孔, 圆孔呈放射状钻穿全工件厚度. 这三个孔圆周分布且每个孔之间间隔120度, 同时在试件的端部须有足够的纵向分离, 以便获得清晰可辨的信号指示.或者, 只有一个孔时应钻通全部试件厚度, 同时在校准和校准检查中, 工件应通过与定位孔成0度, 9度, 18度和27度的设备.5.2.2用来生产这些孔的钻具直径取决于表1所示管件的外径.参考孔的直径应当被验证并且钻具直径小于1mm时指定钻孔直径不能超过0.1mm, 钻具直径大于或等于1mm时指定钻孔直径不能超过0.2mm.5.3分割带卷技术5.3.1当使用同芯带卷技术时, 测试工件应当含有一个单独圆孔, 圆孔呈放射状钻穿全工件厚度.5.3.2基准孔应与试件端部有充分距离, 以便获得清晰可辨的信号指示.5.3.3用来生产这些孔的钻具直径取决于表1所示管件的外径. 基准孔应按表5.2进行验证.5.4旋转展平带卷技术5.4.1当使用旋转展平带卷技术时, 试件的外表面应包含一个纵向参考缺口.5.4.2基准孔应与试件端部有充分距离, 以便获得清晰可辨的信号指示.5.4.3参考缺口应为”N”形(参见图4), 并应平行于管件轴向. 两边应平齐, 同时底部与边部成直角.w= 宽度d=深度图表4: “N”形缺口5.4.4参考缺口应通过机械加工、电火花腐蚀或其他方法来成形.注意: 可以是圆形底部或者缺口底角是圆形的.5.4.5缺口尺寸应当如下:a)宽度w(见图表4)不应大于参考缺口的深度b)深度d(见图表4)应在表2中给出, 具有以下限制:-最小缺口深度: 0.5 mm-最大缺口深度: 1.5 mmc) 缺口深度公差参考+ 15%.d) 长度应当至少为每个独立传感器宽度的两倍,最大50mm。
国产涡流探伤
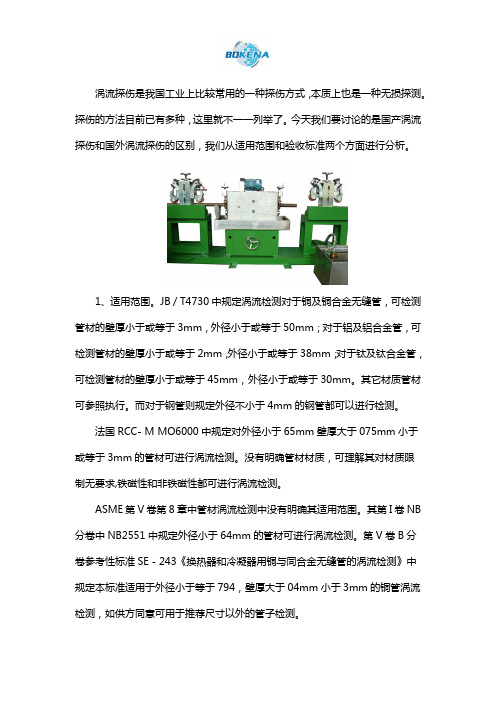
涡流探伤是我国工业上比较常用的一种探伤方式,本质上也是一种无损探测。
探伤的方法目前已有多种,这里就不一一列举了。
今天我们要讨论的是国产涡流探伤和国外涡流探伤的区别,我们从适用范围和验收标准两个方面进行分析。
1、适用范围。
JB / T4730中规定涡流检测对于铜及铜合金无缝管,可检测管材的壁厚小于或等于3mm,外径小于或等于50mm;对于铝及铝合金管,可检测管材的壁厚小于或等于2mm,外径小于或等于38mm;对于钛及钛合金管,可检测管材的壁厚小于或等于45mm,外径小于或等于30mm。
其它材质管材可参照执行。
而对于钢管则规定外径不小于4mm的钢管都可以进行检测。
法国RCC- M MO6000中规定对外径小于65mm壁厚大于075mm小于或等于3mm的管材可进行涡流检测。
没有明确管材材质,可理解其对材质限制无要求,铁磁性和非铁磁性都可进行涡流检测。
ASME第V卷第8章中管材涡流检测中没有明确其适用范围。
其第I卷NB 分卷中NB2551中规定外径小于64mm的管材可进行涡流检测。
第V卷B分卷参考性标准SE - 243《换热器和冷凝器用铜与同合金无缝管的涡流检测》中规定本标准适用于外径小于等于794,壁厚大于04mm小于3mm的铜管涡流检测,如供方同意可用于推荐尺寸以外的管子检测。
从上面的描述中可以看出,RCC- M 的叙述比较明确,ASME的较为灵活,而B/ T4730中没有规定壁厚下限,对检测的选择可能会产生一定的影响,应加以注意。
2、验收标准。
JB/ T4730、RCC- M和ASME标准都规定涡流检测管材的信号低于对比试样人工缺陷的的信号时,管材是可接受的,但对其的附加说明却各有强调之处。
JB/ T47306中823规定:经检验发现有尺寸(包括深度)超过验收标准缺陷的管材,可复探或应用其他检测方法加以验证。
若仍然有超过验收标准的缺陷,则该管材为涡流检测不合格品。
也就是说,即使有超过人工缺陷的信号,只要可以确定不是缺陷产生的信号(采用其他方法),管材就可以继续使用。
涡流探伤检测的原理和应用

涡流探伤检测的原理和应用1. 原理介绍涡流探伤检测是一种无损检测技术,通过利用涡流感应原理来检测材料中的缺陷和表面裂纹。
涡流探伤检测主要适用于导电材料,如金属材料。
涡流探伤的原理基于法拉第电磁感应定律。
当交变电流通过线圈时,会在线圈周围产生交变磁场。
当磁场与导体相互作用时,会产生涡电流。
这些涡电流在导体中形成闭合回路,并且会导致磁场中的感应电动势。
涡流的大小和方向取决于导体的电导率和磁场的变化。
在涡流探伤中,线圈会在被检测的材料表面移动。
当线圈接近缺陷或表面裂纹时,由于局部磁场的变化,涡流的大小和分布会发生变化。
这种变化可以通过检测磁场中的感应电动势来识别和定位缺陷。
2. 涡流探伤的应用涡流探伤广泛应用于各个工业领域,主要用于以下几个方面:2.1 缺陷检测涡流探伤可用于检测材料中的缺陷,如裂纹、松动部分和孔洞等。
通过检测涡流的变化,可以判断缺陷的位置、形状和大小。
这对于确保材料的质量和安全性非常重要。
2.2 表面质量检查涡流探伤也可以用来检查材料表面的质量,如表面裂纹、划痕和氧化等。
通过对表面涡流的变化进行分析,可以快速发现表面缺陷,并及时采取修复措施。
2.3 零部件排序和分级在制造业中,涡流探伤可以用来对零部件进行排序和分级。
通过检测涡流的变化,可以判断零部件是否符合规格要求,并将其按照质量等级进行分类。
这有助于提高生产效率和产品质量。
2.4 腐蚀检测涡流探伤也可用于检测材料表面的腐蚀情况。
由于腐蚀会改变材料的电导率,涡流探测能够检测到这种电导率的变化,并通过分析涡流的特征来确定腐蚀的程度和位置。
3. 涡流探伤的优势涡流探伤具有以下几个优势:•无需接触被检测材料,非破坏性检测•可对复杂形状的零部件进行检测•检测速度快,可以实现自动化检测•检测结果直观易读,可进行定量化分析4. 涡流探伤的局限性涡流探伤也存在一些局限性:•只适用于导电材料,无法用于非导电材料的检测•线圈的质量和设计对检测结果有较大影响•检测深度有限,无法检测材料内部的缺陷•检测结果受材料的性质和表面状态影响较大5. 结论涡流探测作为一种非破坏性检测技术,具有广泛的应用前景。
钢管涡流探伤报告记录内容
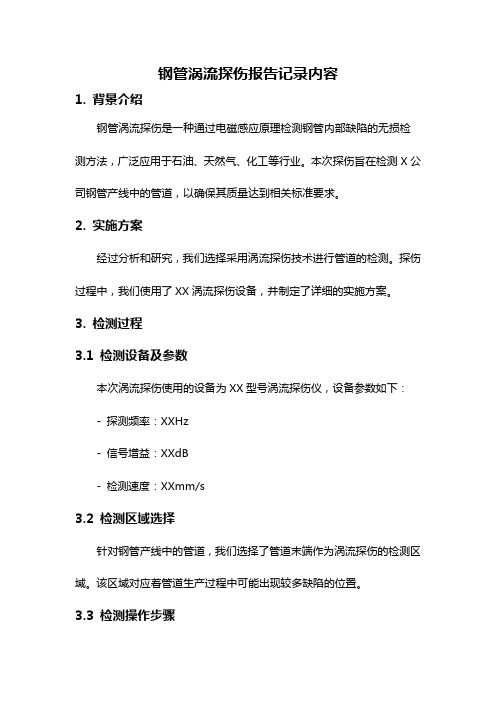
钢管涡流探伤报告记录内容1. 背景介绍钢管涡流探伤是一种通过电磁感应原理检测钢管内部缺陷的无损检测方法,广泛应用于石油、天然气、化工等行业。
本次探伤旨在检测X公司钢管产线中的管道,以确保其质量达到相关标准要求。
2. 实施方案经过分析和研究,我们选择采用涡流探伤技术进行管道的检测。
探伤过程中,我们使用了XX涡流探伤设备,并制定了详细的实施方案。
3. 检测过程3.1 检测设备及参数本次涡流探伤使用的设备为XX型号涡流探伤仪,设备参数如下:- 探测频率:XXHz- 信号增益:XXdB- 检测速度:XXmm/s3.2 检测区域选择针对钢管产线中的管道,我们选择了管道末端作为涡流探伤的检测区域。
该区域对应着管道生产过程中可能出现较多缺陷的位置。
3.3 检测操作步骤1. 将涡流探伤仪的传感器对准钢管末端,并确保与钢管表面的接触良好。
2. 调整探测频率、信号增益等参数,以获取最佳的涡流信号。
3. 沿着管道末端轴向,以相同的检测速度进行涡流探测,确保对整个区域均有覆盖。
4. 检测结果及分析4.1 缺陷分析经过涡流探伤,我们获取了钢管末端区域的涡流信号,并进行了进一步分析。
根据涡流信号的强度和变化情况,我们确定了以下几类缺陷:1. 表面裂纹:通过信号强度的突变,我们发现了数处表面裂纹,其中最严重的一处裂纹长度达到了Xmm。
2. 内部气泡:在涡流信号的幅值和频率变化中,我们发现了一些可能为内部气泡的缺陷。
根据涡流信号的变化规律,我们初步估计其大小和分布情况。
4.2 缺陷等级划分根据钢管涡流探伤的相关标准要求,我们对检测到的缺陷进行了等级划分。
具体划分如下:1. 表面裂纹:- 等级A:裂纹长度小于Xmm;- 等级B:裂纹长度在Xmm至Xmm之间;- 等级C:裂纹长度大于Xmm。
2. 内部气泡:- 等级1:气泡大小小于Xmm;- 等级2:气泡大小在Xmm至Xmm之间;- 等级3:气泡大小大于Xmm。
5. 结论与建议针对本次涡流探伤的结果,我们得出以下结论与建议:1. 钢管末端存在多处表面裂纹,其中一处裂纹长度较大。
焊管常用探伤方法及技术

焊管常用探伤方法及技术摘要:介绍了焊管常用的3种探伤方法(漏磁探伤、涡流探伤和超声波探伤)及技术。
分析了3种探伤方法的优缺点:漏磁探伤灵敏度高,能很好地分辨出焊管内外壁缺陷,但长管体、大壁厚管在漏磁探伤后需做消磁处理;涡流探伤检测速度快,但受趋肤效应的限制,很难发现工件深处的缺陷;超声波探伤穿透能力强、缺陷定位准确、成本低、速度快,但探伤操作需经耦合,在北方严冬环境下耦合时焊管易冻结,给探伤作业带来不便。
在焊管的制造和使用过程中,为保证焊缝质量而进行的无损检测是尤为重要的。
焊管常用的无损检测方法有:适用于距焊管表面5 mm以上的离线全管体漏磁探伤、涡流探伤和超声波探伤;验证距焊管表面5 mm以上焊接质量的在线漏磁探伤和涡流探伤;适用于厚壁焊管的离线焊缝全管体超声波探伤;验证厚壁焊管焊接质量的超声波探伤。
本文将结合生产经验,对焊管常用的探伤方法及技术作简要介绍,并对其优缺点进行分析比较。
1 焊管全管体漏磁探伤漏磁探伤是指铁磁材料被磁化后,其表面和近表面缺陷在材料表面形成漏磁场,通过检测漏磁场发现缺陷的无损检测技术。
漏磁探伤对管材的表面状态要求不高,检出深度较大,在国外的焊管检测中被大量使用,国内特别是石油用焊管的检测也已普遍采用。
在生产检测中,曾出现过漏磁探伤检测不出焊管透壁大孔洞的现象,除了管理及人员因素外,这与仪器、探头性能及缺陷尺寸形状等都有关系。
笔者根据实践经验,总结出影响焊管全管体漏磁探伤精度的主要因素有以下几点。
(1)磁化强度。
当磁化强度较低时,漏磁场偏小,且增加缓慢;当磁感应强度达到饱和值的80%左右时,缺陷漏磁场的峰值随着磁化强度的增加会迅速增大,但当铁磁材料进入磁饱和状态时,外界磁化强度的增大对缺陷磁场强度的影响不大。
因此,磁路的设计应尽可能使被测材料达到近饱和磁化状态。
(2)缺陷的方向、位置和尺寸。
缺陷的方向对漏磁检测精度的影响很大,当缺陷主平面与磁化磁场方向垂直时,产生的漏磁场最强。
不锈钢管 涡流探伤标准
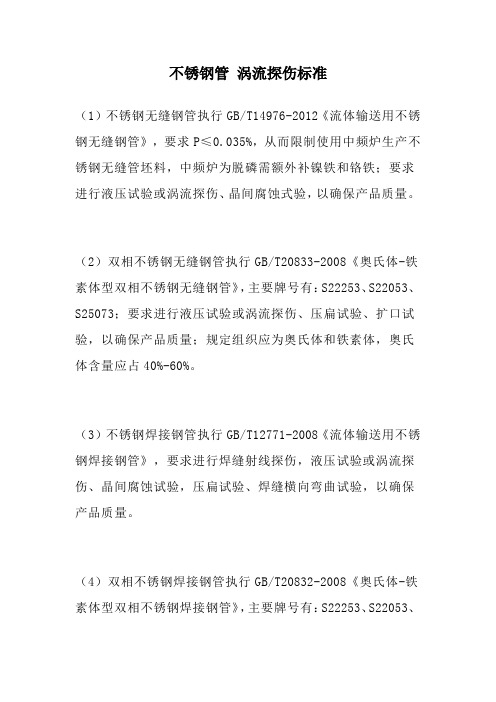
不锈钢管涡流探伤标准
(1)不锈钢无缝钢管执行GB/T14976-2012《流体输送用不锈钢无缝钢管》,要求P≤0.035%,从而限制使用中频炉生产不锈钢无缝管坯料,中频炉为脱磷需额外补镍铁和铬铁;要求进行液压试验或涡流探伤、晶间腐蚀式验,以确保产品质量。
(2)双相不锈钢无缝钢管执行GB/T20833-2008《奥氏体-铁素体型双相不锈钢无缝钢管》,主要牌号有:S22253、S22053、S25073;要求进行液压试验或涡流探伤、压扁试验、扩口试验,以确保产品质量;规定组织应为奥氏体和铁素体,奥氏体含量应占40%-60%。
(3)不锈钢焊接钢管执行GB/T12771-2008《流体输送用不锈钢焊接钢管》,要求进行焊缝射线探伤,液压试验或涡流探伤、晶间腐蚀试验,压扁试验、焊缝横向弯曲试验,以确保产品质量。
(4)双相不锈钢焊接钢管执行GB/T20832-2008《奥氏体-铁素体型双相不锈钢焊接钢管》,主要牌号有:S22253、S22053、
S25073;要求进行焊缝射线探伤,液压试验或涡流探伤、压扁试验、焊缝横向弯曲试验,以确保产品质量;规定组织应为奥氏体和铁素体,奥氏体含量应占40%-60%。
高频焊管直焊缝涡流在线探伤技术

高频焊管直焊缝涡流在线探伤技术高频焊接钢管(简称焊接钢管或焊管)在流体输送、建筑构件和五金家具制作上有广泛的用途。
焊缝中不得有裂缝、裂纹、未熔焊等缺陷,表面不得有超标的划痕、压伤等缺陷。
由于焊管在生产线上(简称在线)具有连续、快速生产的特点,因此,焊管质量仅靠人工事后检验是很难保证的;而涡流探伤检验方法则具有检测速度快,无需要与工件表面耦合,检测灵敏度等优点,适合于焊管生产的质量控制和质量检验。
焊管的在线涡流探伤是指在生产线上与生产过程同步的探伤,主要用生产过程的质量控制;焊接钢管涡流探伤执行GB/T7735-2004《钢管涡流探伤检验方法》标准,探伤结果借助于对比试样中人工缺陷与自然缺陷显示信号的幅值对比进行判断,对比试样的钢管与被检钢管的公称尺寸应相同,化学成分、表面状态、热处理状态相似,即应有相似的电磁特性。
在线探伤系统可以实现缺陷的实时检测、记录、报警及延时打标功能,检测报告数据可以长期保存在电脑硬盘里,如需要可以进行打印输出。
一、探伤方式的选择高频焊接钢管的生产是在生产线上进行的,简称在线生产。
焊管焊缝涡流探伤方法选择局部磁化探伤。
局部式采用平面焊缝探头针对焊缝纵向的扫查。
局部检测法适用于各种规格的焊管机组,以前的检测技术需要机组需要保证焊缝不发生偏转,因为平面或扇形探头有效覆盖范围有限,一旦焊缝发生偏转探伤仪将无法有效检测。
经过实践改进后,局部式探伤可以适应焊缝±45°的偏转范围,提高了现场检测的可靠性和通用性。
局部磁化检测法不要处理接头和大的开裂,只需现场人员进行探头部位的提升即可,过了接头处再降下来即可继续检测。
二、探伤仪的选择针对焊管在线检测方面,涡流探伤仪要有单通道和双通道可以选,选择哪一种仪器都可以满足GB7735《钢管涡流探伤检验方法》中的要求。
一般ZM-26A双通道涡流仪器配合局部式检测方法比较有优势,平面或扇形扫查探头做成绝对、差动双通道型式,差动通道一般检测短小、突变型缺陷,绝对通道对缓变型缺陷可以起到一定的作用。
CCKJ涡流探伤仪的工作原理和应用领域

CCKJ涡流探伤仪的工作原理和应用领域CCKJ涡流探伤仪的工作原理和应用领域CCKJ涡流探伤仪常用于军工、航空、铁路、工矿企业,可在野外或现场使用,是具有多功能、实用性强、高性能、价格比特点的仪器,广泛应用于各类有色金属、黑色金属管、棒、线、丝、型材的在线、离线探伤。
对金属管、棒、线、丝、型材的缺陷,如表面裂纹、暗缝、夹渣和开口裂纹等缺陷均具有较高的检测灵敏度。
CCKJ涡流探伤仪是一种基于涡流检测原理来探测钢铁棒材、板材是否存在裂纹、气孔等缺陷的设备,它具有抑制干扰信号、拾取有用信息的功能,该仪器由振荡器、探头线圈、信号检波装置、测量比较电路、信号处理报警显示及电源等几部分组成,主要用于金属材料的无损探伤。
CCKJ涡流探伤仪是无损探伤仪中,最受器械行业欢迎的一款仪器,具有的高实用性,高性比价的优点,得到了广大工程应用者的喜爱。
CCKJ涡流探伤仪工作原理:涡流检测是许多NDT(无损检测)方法之一,它应用电磁学基本理论作为导体检测的基础。
涡流的产生源于一种叫做电磁感应的现象。
当将交流电施加到导体,例如铜导线上时,磁场将在导体内和环绕导体的空间内产生磁场。
涡流就是感应产生的电流,它在一个环路中流动。
之所以叫做涡流,是因为它与液体或气体环绕障碍物在环路中流动的形式是一样的。
如果将一个导体放入该变化的磁场中,涡流将在那个导体中产生,而涡流也会产生自己的磁场,该磁场随着交流电流上升而扩张,随着交流电流减小而消隐。
因此当导体表面或近表面出现缺陷或测量金属材料的一些性质发生变化时,将影响到涡流的强度和分布,从而我们就可以通过一起来检测涡流的变化情况,进而可以间接的知道导体内部缺陷的存在及金属性能是否发生了变化。
影响涡流场的因素有很多,诸如探头线圈与被测材料的耦合程度,材料的形状和尺寸、电导率、导磁率、以及缺陷等等。
因此,利用涡流原理可以解决金属材料探伤、测厚、分选等问题,如:裂缝、缺陷检查;材料厚度测量;涂层厚度测量;材料的传导性测量等。
涡流探伤作业指导书

涡流探伤作业指导书涡流探伤作业指导书涡流探伤—薄壁焊管技术札记涡流探伤作业指导书参照GB/T7735-20041 样管制备1.1 用于制备对比试样的钢管应与被检验钢管的公称尺寸相同、化学成分、表面状态、热处理状态相似,或具有相似的电磁特性。
一般在被测钢管中选取。
1.2 对比试样应平直,表面不沾有异物,且无影响校准的缺陷。
1.3 对比试样钢管的长度根据涡流探伤设备的要求,一般以2.0m为宜。
1.2 对比试样的人工缺陷1.2.1 对比试样人工缺陷形状按如下规定:a) 穿过式线圈时,试样人工缺陷形状为通孔;b) 扇形式线圈涡流探伤检测焊缝时,试样人工缺陷形状为通孔1.3 对比试样人工缺陷位置1.3.1 使用穿过式线圈涡流探伤技术时,对比试样上应有5个径向钻孔,钻透试样钢管的整个壁厚。
通孔位于试样钢管中部且沿圆周方向的3个孔应彼此间隔120?,试样钢管的通孔在长度方向上相隔距离应不小于200mm,其中有1个孔位于焊缝上。
在距对比试样钢管两端不大于200 mm处再各加工1个相同钻透壁厚的通孔,以检查端部效应。
1.3.2 使用扇形式线圈涡流探伤技术检测焊接钢管焊缝时,在对比试样焊缝上钻1个穿透钢管整个壁厚的通孔。
1.4 对比试样人工缺陷尺寸1.4.1对比试样通孔尺寸分为验收等级A和验收等级B,其钻孔直径尺寸如表1所示。
涡流探伤—薄壁焊管技术札记表 1 验收等级A和验收等级B的通孔直径单位为毫米验收等级A 验收等级B 钢管外径D 通孔直径钢管外径D 通孔直径D?27 1.20 D?6 0.5027<="" 1.70="" 6<="" bdsfid="94" d?19="" p="">48<="" 4260<="" bdsfid="98" p="">76<="" bdsfid="100" p="">D>180 根据客户要求 114<="" bdsfid="102" p="">152<="" bdsfid="104" p="">D>180 根据客户要求 1.4.2 对不锈钢焊管检测缺陷或作为水压密实性检验的替代方法,其通孔直径根据钢管尺寸规定。
涡流探伤的磁饱和工作原理

涡流探伤的磁饱和工作原理第一篇:涡流探伤的磁饱和工作原理涡流探伤的磁饱和工作原理涡流检测适用于导电材料探伤,常见的金属材料可分为两大类:非铁磁性材料和铁磁性材料。
后者为铜、铝、钛及其合金和奥氏体不锈钢;前者为钢、铁及其合金。
它们的本质差别是材质磁导率μ约为1或远大于1。
在发电厂,除復水器等少量管道使用铜、钛、奥氏体不锈钢非铁磁性材料外,大量管道都采用钢管等铁磁性材料,典型的应用有省煤器、水冷壁等。
常规涡流探伤应用于非铁磁性管子,已是非常成熟的技术,它不单能探测出缺陷,并可以利用阻抗平面技术分析出缺陷所在的位置与深度。
然而,将它简单地应用于铁磁性材料的钢管,却得不到预期的结果,其原因何在?这是由于铁磁性材料μ>>1,根据涡流标准渗透公式:δ=503.3/√fμrσ 可知在这种情况下,涡流只能集中在表面,无法渗透到材料的内部。
除此以外,铁磁性材料的磁畴结构,将对涡流检测信号产生极大的干扰,足以把缺陷信号完全淹没,而无法得到有用的信息。
克服铁磁性金属磁导率对探伤影响的方法有两种:其一,采用远场涡流检测方法;其二,对钢管进行饱和磁化后再探伤。
前一种方法需要更新仪器,后一种方法只需在原有常规仪器的基础上增加磁饱和装置即可对钢管等进行探伤,具有投资少的优点。
经过磁饱和处理后的铁磁性材料可以以非铁磁材料对待。
通常钢管涡流探伤采用通过式磁饱和器。
它是由通有直流电的线圈来产生稳恒强磁场,并借助于导套等高导磁部件将磁场疏导到被检测钢管的探伤部位,使之达到磁饱和状态。
为了充分利用线圈产生的磁场,装置一般都有由铁磁性材料(如纯铁)制作的外壳。
由于纯铁的μ值很大,磁阻很小,泄漏在空间中的磁力线会被铁壳收集,也被疏导到钢管的检测部位。
由于强大的磁化电流通过磁饱和器线圈,会使线圈发热,因此要有良好导热措施,以防线圈烧毁。
磁饱和装置除了用来产生强大的直流磁场外,检测线圈也常常用它来夹持,所以磁饱和装置的结构与检测线圈的外形有着密切关系。
- 1、下载文档前请自行甄别文档内容的完整性,平台不提供额外的编辑、内容补充、找答案等附加服务。
- 2、"仅部分预览"的文档,不可在线预览部分如存在完整性等问题,可反馈申请退款(可完整预览的文档不适用该条件!)。
- 3、如文档侵犯您的权益,请联系客服反馈,我们会尽快为您处理(人工客服工作时间:9:00-18:30)。
所谓焊管涡流探伤,是利用涡流技术对焊管进行检测,这类检测是以无损为前提的。
同时,我们需要明确的是,焊管通俗来讲,就是我们平时常常说的钢管,是通过焊接的钢管。
对于涡流探伤技术,我们来详细了解一下。
1、涡流探伤的定义:
涡流探伤是利用交流电磁线圈在金属构件表面感应产生的涡流遇到缺陷会产生变化的原理,来检测构件缺陷的无损探伤技术。
利用电磁感应原理用激磁线圈使导电构件内产生涡电流,借助探测线圈测定涡电流的变化量,从而获得构件缺陷的有关信息。
涡流探伤是以交流电磁线圈在金属构件表面感应产生涡流的无损探伤技术。
它适用于导电材料,包括铁磁性和非铁磁性金属材料构件的缺陷检测。
由于涡流探伤,在检测时不要求线圈与构件紧密接触,也不用在线圈与构件间充满藕合剂,容易实现检验自动化。
但涡流探伤仅适用于导电材料,只能检测表面或近表面层的缺陷,不便使用于形状复杂的构件.在火力发电厂中主要应用于检测凝汽器管、汽轮机叶片、汽轮机转子中间孔和焊缝等。
2、涡流探伤的原理:
交流电通入线圈时,若所用的电压及频率不变,则通过线圈的电流也将不变。
如果在线圈中放入一金属管,管子表面感生周向电流,即涡流。
涡流磁场
方向与外加电流的磁化方向相反,因此将抵消一部分外加电流,从而使线圈的阻抗、通过电流的大小相位均发生变化。
管的直径、厚度、电导率和磁导率的变化以及有缺陷存在时,均会影响线圈的阻抗。
若保持其他因素不变,仅将缺陷引起阻抗的信号取出,经仪器放大并予检测,就能达到探伤目的。
涡流信号不仅能给出缺陷的大小,同时由于涡流探伤时可以根据表面下的涡流滞后于表面涡流一定相位,采用相位分析能判断出缺陷的位t(深度)。
3、涡流探伤的分类
检测线圈在涡流检验中,为了适应不同探伤目的,按照检测线圈和被检构件的相互关系分为穿过式线圈、内通式线圈和放里式线圈三大类。
如需将工件插入并通过线圈检测时采用穿过式线圈。
对管件进行检测时,有时需把线圈放入管子内部进行检验,则采用内通式线圈。
采用放t式(点式)线圈时,把线圈放置于被查的工件表面进行检测。
这种线圈体积小、线圈内部一般带有磁芯,灵敏度高,便于携带,适用于大型构件以及板材、带材等表面裂纹检验。
按照检测线圈的使用方式,可分为绝对线圈式、标准比较线圈式和自比较式等三种型式。
只用一个检测线圈称为绝对线圈式,用两个检测线圈接成差动形式,称为标准比较线圈式。
采用两个线圈放于同一被检构件的不同部位,作为比较标准线圈,称自比较式,是标准比较线圈式的特例。
墓本电路由振荡器、检测线圈信号输出电路、放大器、信号处理器、显示器和电源等部分组成。
4、涡流探伤技术的发展状况
涡流探伤技术是常规无损探伤技术之一,现在多频涡流、脉冲涡流及低频涡流等探伤方法已获得成功应用。
我国从60年代中期开始研究此项技术,70
年代中期发展较快,到80年代已能研制成套的涡流探伤仪器设备,并制定了探伤标准。
目前,我国涡流探伤技术已应用于冶金、机械、航空、航天、电力、化工、军用及民用各个部门,其作用与应用范围日趋扩大。
南京博克纳自动化系统有限公司总部位于美丽的中国古都南京,是国内专业研制无损检测仪器及设备的高科技企业。
公司致力于涡流、漏磁和超声波仪器及各种非标设备的研制,已拥有自主研发的多项国家专利。
产品被广泛应用于航天航空、军工、汽车、电力、铁路、冶金机械等行业。
产品出口:美国、俄罗斯、德国、新加坡、泰国、印度、香港、南非、台湾、越南、哈萨克斯坦、伊朗、日本、韩国、巴西。
博克纳科技作为无损检测仪器及设备、传感器开发的公司,一直是研发和制造高质量、高性能无损检测仪器及设备的创新厂家。
我们以客户为中心提供设计服务,以满足用户的不同应用需求。
公司与国内有名的院校、科研所组成了社会化科研协作网络,具有强大的研发、生产能力。
保证了公司的工业无损检测技术国内、国际过硬的技术地位。