板带材生产工艺1
冷轧板带生产工艺流程

冷轧板带生产工艺流程
冷轧板带的生产工艺流程通常包含以下几个步骤:
1. 原料准备:选择适当的冷轧板材料,并进行切割、打底、扫描等预处理工作。
2. 加热处理:将冷轧板加热到适当的温度,以改善材料的塑性和可锻性。
3. 轧制:通过轧制设备将加热后的冷轧板材料进行多道次的轧制,以减小板带的厚度和调整其形状。
4. 高温退火:对轧制后的板带进行高温退火处理,以消除残余应力和改善材料的物理性能。
5. 镀锌处理:对退火后的板带进行镀锌处理,以提高其耐腐蚀性和外观质量。
6. 表面处理:对板带进行清洗、抛光等表面处理工序,以提高外观质量和润滑性能。
7. 检验和修整:对制成的冷轧板带进行尺寸测量、外观检查和质量评估,如果有需要,进行修整或再加工。
8. 包装和出厂:对合格的冷轧板带进行包装,并按照客户要求进行出厂发货。
需要注意的是,具体的生产工艺流程可能会根据不同的生产要求和产品类型有所差异。
上述流程仅为一般的参考。
有色金属压延(一)适用范围

有色金属压延(一)适用范围适用于铜压延加工和铝压延加工的工业企业。
1、铜压延加工:适用于以电解铜、锭坯、卷坯、再生铜原料及再生黄铜原料等为主要原料,生产铜及铜合金板、带、箔、管、棒、线及型材的工业企业。
2、铝压延加工:适用于用铝锭、电解铝液或以外购挤压用圆铸锭、铸轧卷、热轧用大扁锭为原料,重熔生产铝板、带、箔、管、棒、线、型材及表面处理的工业企业。
(二)生产工艺1、铜压延加工(1)主要生产工艺:熔炼、铸造、轧制、挤压、拉伸、退火等。
(2)主要原辅材料:电解铜、再生铜原料、再生黄铜原料、锌锭、镍板、锡锭、硫酸、硝酸、乳化液、拉丝油、清洗剂等。
(3)主要能源:天然气、煤制气、重油、电。
2、铝压延加工(1)铝板带箔生产工艺:熔铸、铸轧、冷轧、切边、铝箔轧制、高速分卷分切、退火等。
铝型材生产工艺:熔铸、挤压、热处理、表面处理(氧化电泳、粉末喷涂、氟碳喷涂)等。
(2)主要原辅材料:电解铝液、重熔铝锭、铝棒、铝卷、铜锭、锰剂、镁锭、速溶硅、锌锭、轧制油、硅藻土、片碱、硫酸、涂料、氟碳漆、电泳漆等。
(3)主要能源:天然气、煤制气、电。
图14-1铜及铜合金板带材典型生产工艺流程图图14-2铝板带箔及型材典型生产工艺流程图(三)主要污染物产排环节1、PM:铜压延加工主要来自熔炼(化)、加热、炉渣破碎等工序;铝压延加工主要来自熔炼、铝灰处理、氟碳喷涂、粉末喷涂等工序。
2、SO2、NO x:主要来自熔炼(化)工序、加热工序。
3、VOCs:主要来自表面处理工序。
(四)绩效分级指标表14-1有色金属压延行业绩效分级指标差异化指标A级企业B级企业C级企业能源类型以电、天然气、煤制气作为能源其他污染治理技术煤制气单元采用硫份低于1%及以下的低硫煤或配备煤气脱硫;电泳喷漆工序采用吸收法、吸附法或燃烧法;粉末喷涂采用袋式除尘其他1、除尘采用覆膜滤料袋除尘等治理技术;2、熔炼炉(电炉除外)脱硝采用低氮燃烧或烟气脱硝等高效工艺;3、氟碳喷涂工序废气采用预处理+吸附浓缩+燃烧方式或预处理+燃烧处理工艺;4、油雾采用多级回收+VOCs治理技术;封闭式熔炼炉烟气单独治理1、除尘采用布袋除尘等设施;2、氟碳喷涂工序废气经收集后采用预处理+吸附;3、油雾采用多级回收治理技术其他排放限值熔炼炉:PM、SO2、NO x排放浓度分别不高于10、50、50mg/m3;加热炉:PM、SO2、NO x排放浓度分别不高于10、50、100mg/m3PM、SO2、NO x排排放浓度分别不高于10、100、100mg/m3达到国家和地方对行业污染物排放限值要求备注:窑炉烟气基准氧含量12%无组织排放1、物料储存:(1)煤、焦粉等燃料储存于封闭(仓、库);粉状物料采用料仓、储罐、带沿口的包装物等方式密闭或封闭储存;(2)涉VOCs物料以及废料(渣、液)应储存在密闭容器,并存放在封闭储存室内;(3)厂区道路应硬化,并采取清扫、洒水等措施,保持清洁;2、物料转移和输送:(1)粉状、粒状等易散发粉尘的物料厂内转移、输送时,应采取密闭;转移、输送、装卸过程中应采取集气除尘措施;(2)除尘器卸灰口应采取密闭措施,除尘灰不得直接卸落到地面;除尘灰采取袋装、罐装等密闭措施收集、存放和运输;(3)转移和输送VOCs物料以及VOCs废料(渣、液)时,应采用密闭管道或密闭容器;3、工艺过程:(1)铝渣搓灰和铜渣分离操作应采用密闭设备或1、物料储存:(1)煤、焦粉等燃料储存场,采用封闭或半封闭(仓、库、棚);料场至少两面有围墙(围挡)及屋顶,并采取喷淋等抑尘措施;(2)涉VOCs物料以及废料(渣、液)应储存在密闭容器,并存放在封闭储存室内,或设置有雨棚、遮阳和防渗设施的专用场地;(3)同A级要求;2、物料转移和输送:(1)粉状、粒状等易散发粉尘的物料厂内转移、输送时,应采取密闭或覆盖等抑尘措施;转移、输送、装卸过程中应采取集气除尘措施,或喷淋(雾)等抑尘措施;(2)同A级要求;(3)同A级要求;3、工艺过程:同A级要求4差异化指标A级企业B级企业C级企业密闭车间内进行,设置废气收集系统,收集粉尘至除尘设备;(2)熔炼炉应设置废气收集系统,收集烟尘至除尘设备监测监控水平重点排污企业的熔炼炉等主要排气口安装CEMS,数据保存一年以上未达到A、B级要求熔炼炉烟气等对应污染治理设施接入DCS,记录企业环保设施运行主要参数和生产过程主要参数,DCS数据保存一年以上;VOCs治理设施安装监控或分表计电未达到A级要求具备对全厂视频监控、CEMS监控、污染物治理设施运行、主要生产设施运行等相关数据集中调控的能力未达到A级要求环境管理水平环保档案齐全:1、环评批复文件;2、排污许可证及季度、年度执行报告;3、竣工验收文件;4、废气治理设施运行管理规程;5、一年内废气监测报告台账记录:1、生产设施运行管理信息(生产时间、运行负荷、产品产量等);2、废气污染治理设施运行管理信息(除尘滤料更换量和时间、脱硫及脱硝剂添加量和时间、含烟气量和污染物出口浓度的月度DCS曲线图等);3、监测记录信息(主要污染排放口废气排放记录(手工监测和在线监测)等);4、主要原辅材料消耗记录;5、燃料(天然气)消耗记录至少符合A级要求中1、2、3项(其中,对DCS的相关要求可通过PLC实现)未达到B级要求人员配置:设置环保部门,配备专职环保人员,并具备相应的环境管理能力人员配置:配备专职环保人员,并具备相应的环境管理能力运输方式1、物料公路运输全部使用达到国五及以上排放标准重型载货车辆(含燃气)或新能源车辆;2、厂内运输车辆全部达到国五及以上排放标准(含燃气)或使用新能源车辆;3、厂内非道路移动机械全部达到国三及以上排放标准或使用新能源机械1、物料公路运输使用达到国五及以上排放标准重型载货车辆(含燃气)或新能源车辆比例不低于80%;2、厂内运输车辆达到国五及以上排放标准(含燃气)或使用新能源车辆比例不低于80%;3、厂内非道路移动机械达到国三及以上排放标准或使用新能源机械比例不低于80%未达到B级要求运输监管参照《重污染天气重点行业移动源应急管理技术指南》建立门禁系统和电子台账未达到A、B级要求5(五)减排措施1、A级企业:鼓励结合实际,自主采取减排措施。
第五章 板带材生产
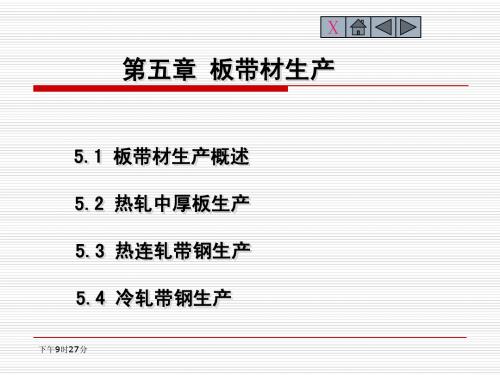
5.2 热轧中厚板生产
5.2 热轧中厚板生产
鞍钢鲅鱼圈中厚板 可生产LP钢板的主要参数
最小厚度 10mm
最大厚度
最大宽度 最大长度 最大重量
300mm
5300mm 25000mm 30.2t
5.2 热轧中厚板生产
5.2 热轧中厚板生产
Ⅹ
5.2 热轧中厚板生产 2.中厚板生产轧机形式、轧机布置 1)轧机形式
二辊式轧机 淘汰
单机架
三辊劳特式轧机
改造
四辊式轧机
39
5.2 热轧中厚板生产
(2)双机架中厚钢板轧机呈纵列式布置,前一架为 粗轧机,后一架为精轧机 四辊式—四辊式
组成型式
二辊式—四辊式
三辊式—四辊式 优点:粗、精轧制道次分配合理、产量高;使进入精 轧机的来料断面较均匀,质量好;粗轧可以独立生产, 较灵活。
外阻也愈重要,尤其高 H<1mm 轧制温度很难保证,轧件质
量很难保证。 采用冷轧的方法,冷轧温度低,内阻外阻都大,主要是降低 外阻。 降低外阻方法:减小工作辊直径;采用轧制润滑油和带张力
轧制。其中最活跃的是减小工作辊直径。由此出现了从二辊
到多辊的各种板带材轧机。
Ⅹ
5.1 板带材生产概述
Ⅹ
5.1 板带材生产概述
Ⅹ
5.2 热轧中厚板生产
2)中厚板生产轧机布置
连铸坯→加热炉→除鳞机→轧机→控制冷却→矫直→冷 床冷却→切头切倍尺→双边剪→定尺剪→表面检查和清理 →垛板→入库→发货
5.2 热轧中厚板生产---宝钢5000宽厚板车间布局
1-板坯二次切割线;2-连续式加热炉 3-高压水除鳞箱;4-精轧机; 5-加速冷 却装置; 6-热矫直机; 7-宽冷床;8-特厚板冷床; 9-检查修磨台架; 10-超 声波探伤装置;11-切头剪;12-双边剪和剖分剪;13-定尺剪;14-横移修磨台 架;15-冷矫直机;16-压力矫直机;17-热处理线;18-涂漆线
轧制厚度及板型控制
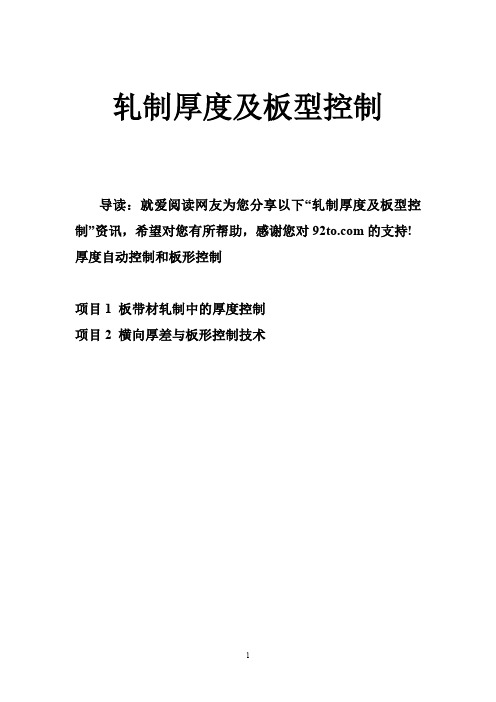
轧制厚度及板型控制导读:就爱阅读网友为您分享以下“轧制厚度及板型控制”资讯,希望对您有所帮助,感谢您对的支持! 厚度自动控制和板形控制项目1 板带材轧制中的厚度控制项目2 横向厚差与板形控制技术项目1板带材轧制中的厚度控制一、厚度自动控制的工艺基础 1.p-h图的建立(1)轧制时的弹性曲线轧出的带材厚度等于理论空载辊缝加弹跳值。
轧出厚度:h=S0 +P/K―――轧机的弹跳方程S0 ――空载辊缝P――轧制压力K――轧机的刚度系数根据弹跳方程绘制成的曲线(近似一条直线)――轧机弹性变形曲线,用A 表示。
A(2)轧件的塑性曲线根据轧制压力与压下量的关系绘制出的曲线――轧件塑性变形曲线,用B表示。
B(3)弹塑性曲线的建立将轧机弹性变形曲线与轧件塑性变形曲线绘制在一个坐标系中,称为弹塑性曲线,简称P-h图。
注意A线与B线交点的纵坐标为轧制力A线与B线交点的横坐标为板带实际轧出厚度2. p-h图的运用由p-h图看出:无论A线、B线发生变化,实际厚度都要发生变化。
保证实际厚度不变就要进行调整。
例如:B线发生变化(变为B‘),为保持厚度不变,A线移值A',是交点的坐标不变。
C线――等厚轧制线作用:板带厚度控制的工艺基础板带厚度控制的实质:不管轧制条件如何变化,总要使A 线和B 线交到C线上。
p-h图二、板带厚度变化的原因和特点影响板带厚度变化的因素:1、轧件温度、成分和组织性能不均匀的影响温度↑→变形抗力↓→轧制压力↓→轧机弹跳↓→板厚度变薄↓变形抗力对轧出厚度的影响2、来料厚度不均匀的影响来料厚度↓→压下量↓→轧制压力↓→轧机弹跳↓→板厚度变薄↓来料厚度对轧出厚度的影响3、张力变化的影响张力↑→变形抗力↓→轧制压力↓→轧机弹跳↓→板厚度变薄↓张力对轧出厚度的影响4、轧制速度变化的影响通过影响摩擦系数和变形抗力来改变轧制压力。
摩擦系数↓→变形抗力↓→轧制压力↓→轧机弹跳↓→板厚度变薄↓摩擦系数对轧出厚度的影响5、原始辊缝的影响原始辊缝减小,板厚度变薄。
板带钢生产工艺学

板带钢生产工艺学
板带钢是一种重要的金属材料,其生产工艺是指将原料经过多道工序加工和处理,最终形成具有一定厚度和宽度的板带状材料的过程。
板带钢生产工艺主要包括原料准备、精炼冶炼、连铸连轧、热轧、冷拉平、冷轧、退火、分切整平等工序。
下面,我们将详细介绍这些工艺。
1. 原料准备:在板带钢的生产过程中,主要原料是钢坯,其它辅助材料包括添加剂、脱氧剂、合金元素等。
这些原料需要经过筛分、破碎、配料等工序,以保证原料的质量和配比的准确性。
2. 精炼冶炼:将原料放入高炉中进行冶炼,通过高炉的高温、高压等条件,将炉料中的杂质和不良元素去除,使得冶炼后的钢液质量更加纯净。
3. 连铸连轧:冶炼好的钢液通过连铸机连续浇铸成板坯,然后经过连轧机的轧制,使板坯逐渐变细,形成带钢。
4. 热轧:将连铸机得到的板坯经过加热,然后在热轧机上进行轧制,使板坯变细、变宽,形成所需的板带钢。
5. 冷拉平:将热轧的板带钢经过拉拔机进行拉拔,使其进一步细长,同时提高其机械性能。
6. 冷轧:将冷拉平的板带钢通过冷轧机进行轧制,使其更加细小和光滑,提高其表面质量和尺寸精度。
7. 退火:将冷轧后的板带钢进行退火处理,通过加热和保温,使其晶体结构发生变化,降低其硬度和脆性,提高其延展性和塑性。
8. 分切整平:将退火后的板带钢进行剪切和整平,使其尺寸和平整度符合要求。
以上是板带钢的主要生产工艺。
通过这些工艺的处理,原料可以被加工成具有一定厚度和宽度的板带形式,方便后续加工和应用。
同时,这些工艺还能够提高板带钢的质量和性能,满足不同领域的需求。
材料成型概论第六讲板带材生产工艺

材料成型概论第六讲板带材⽣产⼯艺材料成型概论第⼀讲第⼆讲第三讲第四讲第五讲第六讲第七讲第⼋讲第九讲第⼗讲材料成型概述炼钢炼铁⽣产材料塑性成型的基础钢坯型钢⽣产线棒材⽣产板带钢⽣产钢管⽣产挤压拉拔⽣产锻压冲压⽣产材料成型的发展及应⽤第六讲板带材⽣产6.1 6.2 6.3 6.4 6.5 板带材⽣产的⼀般概念板带材的品种及分类热轧中厚板⽣产热轧板带钢⽣产冷轧板带钢⽣产6.1 板带材⽣产的⼀般概念板带材(Finished sheet/plate and strip)是指形状为平板状断⾯基本为矩形宽度远⼤于厚度的⾦属材,B/H可达5000以上,少数达到10000。
⼀般将单张供应的板材和成卷供应的带材总称为板带材。
板材的主要尺⼨是厚度H、宽度B与长度L;带钢或板卷⼀般只标出厚度H与宽度B,再附以卷重G。
6.1 板带材⽣产的⼀般概念6.1 板带材⽣产的⼀般概念在⽣产上,板带钢宽⾼⽐⼤,散热⾯积⼤,温降快且波动明显;对不均匀变形⾮常敏感;变形量⼤,特别是薄规格⽣产,轧制压⼒⼤。
所以⽣产时要特别注意板型,减少轧制压⼒。
尺⼨要求精确:特别是厚度最主要板型要求良好:平坦、⽆浪形和瓢曲。
表⾯要求光洁:不得有⽓泡、结疤、拉裂、刮伤、折叠、裂缝、夹杂和压⼊氧化铁⽪。
性能要求较⾼:⼒学性能、⼯艺性能和某些钢板的特殊物理和化学性能。
6.1 板带材⽣产的⼀般概念为达到上述要求,采⽤了⼤量现代轧制技术,板带钢⽣产技术可以反映轧钢⽣产的技术⽔平。
对⼯业发达国家,⼀般板带钢产量占钢材总产量的50-60%以上。
6.1 板带材⽣产的⼀般概念板带材轧制指采⽤纵轧⽅式在由上下平轧辊构成的辊缝中将扁锭或板坯轧制成板带材的成型⽅法。
轧制板带材的轧机⼤多是四辊轧机,轧制箔材(极薄带)⽤六辊或多辊轧机。
粗轧机也采⽤⼆辊可逆式或万能式轧机。
板带材的轧制⽅法有单⽚轧制、成卷轧制、单机架可逆轧制、连续式轧制、多辊轧制等⼏种。
板带材的轧制⽅法(a)单机架四辊可逆轧制;(b)五机架四辊连续轧制;(c)单机架多辊可逆轧制6.1 板带材⽣产的⼀般概念板带材⽣产的特点:厚度H.长度B.宽度L外形特点:①形状扁平,断⾯简单,宽厚⽐⼤;②单位体积的表⾯积⼤。
板带生产工艺

板带生产工艺1 概论1.1 板带产品特点、分类及技术要求1.1.1 板带产品的外形特点:扁平,宽厚比大,单位体积的表面积也很大;1.1.2 板带材的使用特点:(1)表面积大,故包容覆盖能力强,在化工、容器、建筑、金属制品、金属结构等方面都得到广泛应用;(2)、可任意剪裁、弯曲、冲压、焊接、制成各种制品构件,使用灵活方便,在汽车、航空、造船及拖拉机制造等部门占有极其重要的地位;(3)、可弯曲、焊接成各类复杂断面的型钢、钢管、大型工字钢等结构件,故称为“万能钢材”。
1.1.3 板带材的生产特点:(1)板带材是用平辊轧出,故改变产品规格较简单容易,调整操作方便,易于实现全面计算机控制的自动化生产;(2)带钢的形状简单,可成卷生产,且在国民经济中用量最大,故必须而能够实现高速度的连轧生产;(3)由于宽厚比和表面积都很大,故生产中轧制压力很大,可达数百万至数千万牛顿,不仅使轧机设备复杂庞大,而且使产品厚、宽尺寸精度和板形控制技术及表面质量控制技术变得十分困难和复杂。
1.2 板带材的分类及技术要求1.2.1 板带材产品分类板带:一般将单张供应的板材和成卷供应的带材总称。
分类:(1)、按材料种类分:钢板钢带、铜板铜带和铝板铝带等;(2)、按产品尺寸规格一般可分为厚板(包括中板和特厚板)、薄板和极薄带材(箔材)三类;厚板:中板: 4~20mm厚板: 20~60mm特厚板: >60mm以上,最后可达500mm 薄板:4.0~0.2mm(热轧薄至1.2mm)极薄带材(箔材):<0.2mm,目前箔材最薄可达0.001mm日本:规定3~6mm为中板,6mm以上为厚板(3)、板带钢按用途又可分为造船板、锅炉板、桥梁板、压力容器板、汽车板、镀层板(镀锡、镀锌板等)、电工钢板、屋面板、深冲板、焊管坯、复合板及不锈、耐酸耐热等特殊用途钢板等有关品种规格可参看国家标准1.2.2板带材产品的技术要求对板带材的技术要求具体体现为产品的标准,板带材的产品标准一般包括有品种(规格)标准、技术条件、试验标准及交货标准等。
轧制原理二
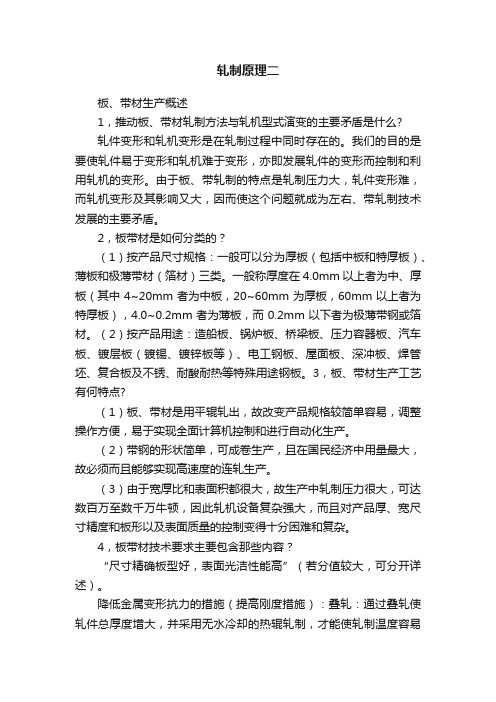
轧制原理二板、带材生产概述1,推动板、带材轧制方法与轧机型式演变的主要矛盾是什么?轧件变形和轧机变形是在轧制过程中同时存在的。
我们的目的是要使轧件易于变形和轧机难于变形,亦即发展轧件的变形而控制和利用轧机的变形。
由于板、带轧制的特点是轧制压力大,轧件变形难,而轧机变形及其影响又大,因而使这个问题就成为左右、带轧制技术发展的主要矛盾。
2,板带材是如何分类的?(1)按产品尺寸规格:一般可以分为厚板(包括中板和特厚板)、薄板和极薄带材(箔材)三类。
一般称厚度在4.0mm以上者为中、厚板(其中4~20mm者为中板,20~60mm为厚板,60mm以上者为特厚板),4.0~0.2mm者为薄板,而0.2mm以下者为极薄带钢或箔材。
(2)按产品用途:造船板、锅炉板、桥梁板、压力容器板、汽车板、镀层板(镀锡、镀锌板等)、电工钢板、屋面板、深冲板、焊管坯、复合板及不锈、耐酸耐热等特殊用途钢板。
3,板、带材生产工艺有何特点?(1)板、带材是用平辊轧出,故改变产品规格较简单容易,调整操作方便,易于实现全面计算机控制和进行自动化生产。
(2)带钢的形状简单,可成卷生产,且在国民经济中用量最大,故必须而且能够实现高速度的连轧生产。
(3)由于宽厚比和表面积都很大,故生产中轧制压力很大,可达数百万至数千万牛顿,因此轧机设备复杂强大,而且对产品厚、宽尺寸精度和板形以及表面质量的控制变得十分困难和复杂。
4,板带材技术要求主要包含那些内容?“尺寸精确板型好,表面光洁性能高”(若分值较大,可分开详述)。
降低金属变形抗力的措施(提高刚度措施):叠轧:通过叠轧使轧件总厚度增大,并采用无水冷却的热辊轧制,才能使轧制温度容易保持及克服轧机弹跳的障碍,保证轧制过程的进行。
连续轧制:单层轧制薄而长的钢板时温降很快,不叠轧就必须快速操作和成卷轧制,争取有较高和较均匀的轧制温度。
炉卷轧机:优点:可用较少的设备投资和较灵活的工艺道次生产出批量不大而品种较多的产品,尤其适合生产塑性较差、加工温度范围较窄的合金钢板带。
板带轧制数模及控制1
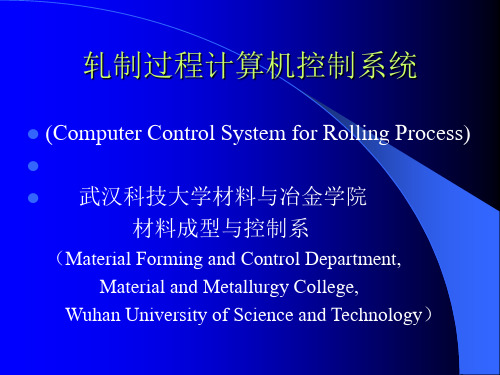
(1) CSP工艺 由德国西马克公司研制,第一条生产线 于1989年在美国的Nucor Crawfordsville 厂投产,生产线全长约300米。目前大约 2/3的薄板坯连铸连轧生产工艺为CSP线。 一机一流生产能力大约90万吨/年;两机 两流为180万吨/年。最小热轧卷厚度为 1.0mm。产品厚度为1.0~12.7mm
(5) TSP(Tippins-Samsung Process)工艺 1993年美国Tippins公司推出了TSP工艺,它将 中厚板连铸机与斯特克尔轧机结合起来,在投 资很低的情况下,即可获得40万~200万吨/年的 产量,厚度为1.5~2.0mm。 (6) CPR(Casting Pressing process) CPR工艺即铸压轧由德国西马克公司、蒂森公 司和法国Usinor Sacilor公司共同开发,用于生 产厚度小于25mm的合金钢和普碳钢热轧带材。 德国蒂森公司的杜伊斯堡厂CPR机组1998年投 产,热轧带钢厚度为0.8~1.0mm。
(3) FTSRQ(FTSC) (Flexible Thin Slab Rolling for Quality)工艺 FTSRQ(后该为FTSC)称为生产高质量产品的灵 活性薄板坯轧制,由意大利达涅利公司开发。 第一条生产线于1997年在加拿大的Algoma钢厂 投产。产品厚度为1.0~16.0mm。 (4) CONROLL (CONtinuous ROLLing)工艺 该工艺由奥钢联工程技术公司(VAI)开发,第 一 条 生 产 线 于 1995 年 4 月 在 美 国 的 Armco Mansfiled钢厂投产。生产能力90~180万吨/年 (1×1流,2×2流),产品厚度1.8~12.7mm。
1.3.3 轧制过程计算机系统配置典型结构 为了满足冷、热连轧计算机控制系统对于高 速控制和高速通讯的要求,国外大电气公 司都设计有针对性的大型分布式计算机控 制系统。但从系统的拓朴结构上看基本上 可归纳为两类系统,即区域控制群结构和 超高速网结构。
板带材生产工艺之总复习
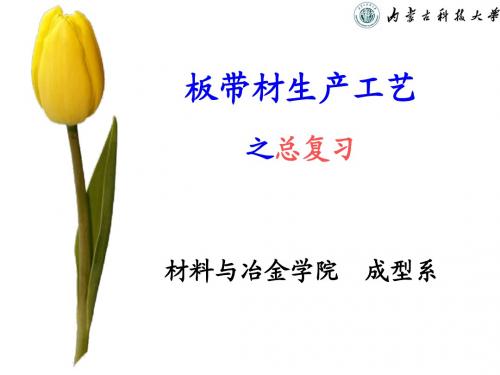
之总复习
材料与冶金学院
成型系
板带钢生产工艺课程的凝炼
板带生产工艺
尺寸精确板形好 表面光洁性能高
热轧 厚规格 薄规格
冷轧 薄规格
2
第一章 板带材生产概述
• 1、板带产品的外形、使用与生产特点 • (1)板带材是用平辊轧出,故改变产品规格较简 单容易,调整操作方便,易于实现全面计算机控制 的自动化生产 • (2)带钢的形状简单,可成卷生产,且在国民经济 中用量最大,故必须而且能够实现高速度的连轧生 产 • (3)由于宽厚比和表面积都很大,故生产中轧制 压力很大,可达数百万至数千万牛顿,不仅使轧机 设备复杂庞大(轧机之王),而且使产品厚、宽尺 寸精度和板形控制技术及表面质量控制技术变得十 分困难和复杂
3
2、板带材的分类及技术要求
• 厚度分类: • 在4.0mm以上者为中厚板(其中4~20mm 者为中板,20~60mm者为厚板,60mm 以上者为特厚板,特厚板可厚至500mm 以上,最宽可达5000mm) • 宽度分类:(宽带、窄带) • 技术要求 • “尺寸精确板型好”:(第五章) • “表面光洁性能高”:(第二、三、四 章)
21
第五章 板带材高精度轧制及板形控制
• • • • • 高精度:厚度精度 P-h图的运用——板带厚度控制的基础 厚度控制方法 板形和辊型 辊型设计(影响辊缝形状的因素)
22
14
第三章 热轧薄板带钢生产
• • • • • • 热连轧带钢生产☆ 1、原料选择与加热 2、粗轧 3、精轧 4、轧后冷却及精整 5、热带连轧机工艺流程与车间布置
15
新技术
• 热装:将连铸坯或初轧坯在热状态下 装入加热炉,热装温度越高,则节能 越多。热装对板坯的温度要求不如直 接轧制严格 • 直接轧制:是板坯在连铸或初轧之后, 不再入加热炉加热而只略经边部补偿 加热,即直接进行的轧制 • CSP(薄板坯连铸连轧)
H68(Y)板材工艺卡片
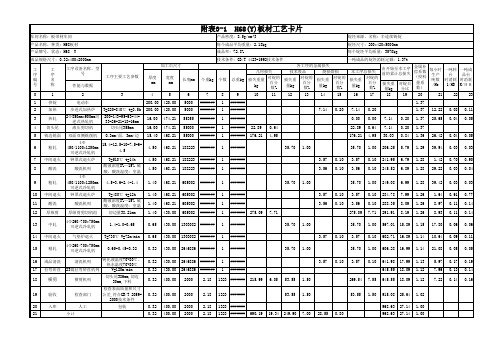
损失重 量kg
对锭的 百分 数%
本工序总损失
损失重 量kg
对锭的 百分 数%
由开始至本工序 前的累计总损失
损失重 对锭百 量kg 分比
金属补 偿系数 (投料
量系 数)
每小时 生产 吨数 /Hb
一吨料 台
时消耗 1/HB
一吨成 品台 时消耗 K/HB
0
1
2
3
4
5
6
7
8
9
10
11
12
13
14
15
16
17
4.50 468.21 188223 ####### 1 #######
8
酸洗
酸洗机列
酸液浓度8%—15% 硫 酸,酸洗温度:室温
4.50
468.21 188223 #######
1
#######
4Φ
9
粗轧 450/1100*1250mm 4.5-3.6-2.4-1.4 1.40 468.21 605002 ####### 1 #######
3.57 0.10 3.57 0.10 602.71 16.89 1.14 10.64 0.09 0.11
15
精轧
4Φ260/700*750mm 可逆式冷轧机
0.65-0.45-0.32
0.32 430.00 2646886 #####
35.70 1.00 606.28 16.99 1.14 21.08 0.05 0.05
6
粗轧
4Φ 450/1100*1250mm
可逆式冷轧机
15.4-12.5-10-7.5-64.5
4.50
468.21 188223 #######
板带材生产工艺及设备 pdf

板带材生产工艺及设备 pdf板带材生产工艺及设备是指制造金属板材和带材的工艺流程和所需设备的总称。
其生产工艺主要包括原材料准备、热轧、酸洗、轧制、裁切、检验等环节,整个生产过程必须进行严格的质量控制,以确保生产出的产品符合国家标准和客户要求。
整个板带材生产工艺可以分为三个主要阶段:前处理、轧制和后处理。
前处理主要包括原材料准备和热轧;轧制阶段包括酸洗、轧制和裁切;后处理包括检验、包装和发货。
前处理阶段的原材料准备包括金属矿石的选矿、冶炼、加工和调配等工艺,以获得符合产品要求的金属原料。
热轧过程是将金属块材加热至合适的温度,然后通过轧机将其压成具有一定尺寸和厚度的板材或带材的加工工艺。
轧制阶段主要包括酸洗、轧制和裁切。
酸洗是将热轧后的板材浸泡在酸液中进行腐蚀,以去掉表面氧化铁皮采用的处理方法。
轧制是将酸洗后的板材或带材,放入轧机中进行轧制,压缩其厚度和宽度,以获得符合产品规格的材料。
裁切是将轧制后的板材或带材切割成用户需求的尺寸。
后处理阶段主要包括检验、包装和发货。
检验是对裁切好的板材或带材进行尺寸、质量等方面的检测,以确保产品符合设计要求和客户要求。
包装是将检验合格的产品进行包装,以便于运输和存储。
发货则是指将产品交付给用户。
板带材生产设备包括热轧机、酸洗线、轧机、裁切机、检测设备、包装设备等。
不同规格和品种的板带材生产设备也有所不同,但总体上都遵循相似的生产工艺流程。
总之,板带材生产工艺及设备是制造金属板材和带材的重要工序,要严格遵循生产质量标准,运用先进的技术和设备,以确保生产出符合客户需求和国家标准的高质量产品。
板材生产工艺流程(带动画演示)ppt课件
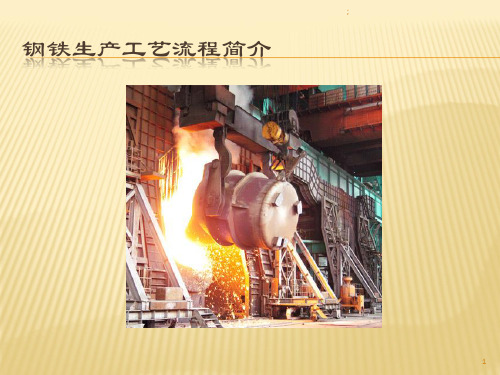
投掷法: 将脱硫剂投入铁水中 喷吹法: 将脱硫剂喷入铁水中 搅拌法(KB法): 将通过中空机械搅拌器向铁水内加入脱硫剂,
搅拌脱硫
13
;
三、转炉炼钢
转炉炼钢:是以铁水、废钢、铁合金为主要原料,不借助
外加能源,靠铁液本身的物理热和铁液组分间化学反应产生 热量在转炉中完成的炼钢过程。转炉按耐火材料分为酸性和 碱性,按气体吹入炉内的部位有顶吹、底吹和侧吹;按气体 种类为分空气转炉和氧气转炉。碱性氧气顶吹和顶底复吹转 炉由于其生产速度快、产量大,单炉产量高、成本低、投资 少,为目前使用最普遍的炼钢设备。
特殊铁水预处理 特殊铁水预处理是针对铁水中含有特殊元素进行提纯精炼或 资源综合利用如铁水提钒、提铌、脱铬等预处理工艺
铁水预处理——脱硫
铁水在进入转炉冶炼前进行脱硫具备最佳的反应条件: 铁水中含有大量Si、C、Mn等还原性好的元素,其还原性有 利于脱硫反应,(强脱硫剂Ca、Mg等烧损少); 铁水中C、Si能大大提高S在铁水中的活度系数,致使硫较易 脱到低的水平;
炉外精炼的种类很多,大致可分为常压下炉外精炼和真空下炉外精炼两 类。按处理方式的不同,又可分为钢包处理型炉外精炼及钢包精炼型炉外 精炼等。
以钢种为中心,正确选择精炼设备
CAS-OB是最简单的非真空精炼设备,多适用于普碳钢、低合金钢等以化学成分交 货的钢种;
LF有很强的清洗精炼和加热功能,适宜冶炼低氧钢、低硫钢和高合金钢; VD脱碳能力弱(受钢包净高度的限制),具备一定的钢渣精炼功能,适宜生产重轨、轴
延成钢带,并以层流冷却系统喷水冷却至适当温度,再由盘卷机 卷成钢卷。
24
; 25
;
五、轧制
热轧工艺流程:坯料准备---加热---除鳞---粗轧--切头---除鳞---精轧---冷却---卷曲---精整---交 付
冷轧工艺简介

2021/5/28
23
冷轧生产技术的发展
▪ 联合式全连轧机
▪ 单一全连轧机再与其它生产工序(或其它机组)联合,称为联合式全连 轧机。酸洗冷轧联合机组,冷轧退火联合机组。
酸洗冷轧联合机组发展较快。目前世界上已有近20套酸洗-轧机联合机 组,我国的本钢第一套酸洗-轧机联合机组。
▪ 酸洗联合式轧机能得以发展的共存条件:产量基本相当;酸洗机组出 口段速度与轧机的入口速度基本匹配;两个机组的利用率基本相当; 二个机组的设备使用寿命基本相当。设计、操作、机电设备以及自动 控制等方面进行技术改进。
▪ 卷重: max. 38 t
2021/5/28
6
轧机区主要设备简介
轧机入口段设备:
▪ 焊缝检测仪 ▪ 测张辊 ▪ 带钢夹紧装置 ▪ 横切剪 ▪ 测厚仪 ▪ 卷扬机 ▪ 带钢侧导
2021/5/28
7
轧机区主要设备简介
轧机段设备:
▪ 机架 ▪ 液压调整系统 ▪ 楔形调整系统 ▪ 中间辊窜辊系统 ▪ 轧辊 ▪ 换辊装置 ▪ 乳化液喷淋装置 ▪ 防缠导板
▪ 5) 边部减薄
▪ 边部减薄(E)是指带钢与轧辊接触处的轧辊压扁在板带边部由于过渡区而造 成的带钢边部减薄的现象。
▪ E =he-hE
▪ 式中hE为带材实际边部的厚度。
2021/5/28
16
冷轧工艺基本概念
6) 楔形 ▪ 楔形(CT)即左右边部标
志点厚度之差,如下图所示: CT=her - hel
▪ 近年来, 冷轧带钢生产的连续化方面进展很快 。以往冷轧带钢的生产需经酸洗、冷轧、电 解清洗、退火、冷却、平整和精整等七道工 序,为了缩短生产周期,节约投资,人们力图把 这一个个的单体工序连接起来。随着技术的 发展,在实际生产中已经实现了冷轧带钢生产 的连续化。按连续化的程度,世界上冷轧带钢 生产可分为三种情况:
板带钢生产工艺课件.pptx

的生产工艺;掌握轧制力矩的计算和
压下规程的制定方法,为今后从事专
业技术工作、解决生产实际问题及学
习新的科学技术奠定必要的基础。
轧制产品根据断面形状分为四大类:
板带钢 型钢 钢管 特殊类型钢材
板带钢生产特点
• 一、热轧板带材短流程、高效率化。
体现在三方面:
1.常规生产工艺的革新 2.薄板坯连铸连轧技术 3.薄带连续铸轧技术
置。
§1.3 板带材轧制技术的发展
• 1)技术发展的关键: • 降低轧制压力,使板带钢易于变形。 • 2)途径:
• 1.降低板带钢本身的变形抗力; • 2.改变应力状态,减少应力状态影响系数,减
少外摩擦等对金属变形的影响(减少外阻)。 • 3.控制轧机的变形:增强和控制机架的刚性和
辊系的刚性,采用厚度自动控制等技术控制轧辊 的变形。
•
T H E E N D 17、一个人如果不到最高峰,他就没有片刻的安宁,他也就不会感到生命的恬静和光荣。下午8时53分1秒下午8时53分20:53:0120.10.18
谢谢观看
2.铸坯温度保证与输送技术
• 铸坯输送与温度保证技术如图1-3所示。 • 利用液芯潜热,使铸坯保持更高更均匀的温
度; • 在保证充分冷却不致拉漏的前提下,合理控
制钢流速度和冷却制度来保加热温度,将铸 坯完全凝固的时刻控制在连铸机冶金长度的 末端,否则还要降温。 • 具体方法:采用上部强冷,下部缓冷的变化 冷却制度,提高整体温度; • 不对板坯的边部喷水,使液芯尾端两侧呈凸 起形(通常中心呈凸形),提高边角温度; • 边部减少冷却水量,中部适当加大水量,消
• 2、开发的目的 • 大幅度降低轧制压力;增大压下量,减少道
次与轧程(冷轧有轧程);生产薄带;提高板 带的厚度精度。
- 1、下载文档前请自行甄别文档内容的完整性,平台不提供额外的编辑、内容补充、找答案等附加服务。
- 2、"仅部分预览"的文档,不可在线预览部分如存在完整性等问题,可反馈申请退款(可完整预览的文档不适用该条件!)。
- 3、如文档侵犯您的权益,请联系客服反馈,我们会尽快为您处理(人工客服工作时间:9:00-18:30)。
第一章 板带材生产概述
98%的钢铁材料是采用轧制方法生产的,轧材中 30%~60%以上是板带材
板带钢产品薄而宽的断面决定了板带钢产品在生 产上和应用上有其特有的优越条件
生产上:板带钢生产方法简单,便于调整、便于改 换规格
应用上:钢板的表面积大,是一些包覆件(如油罐、 船体、车厢等)不可缺少的原材料,钢板可冲、可 弯、可切割、可焊接,使用灵活。板带钢在建筑、 桥梁、机车车辆、汽车、压力容器、锅炉、电器 等方面得到广泛应用
连续式轧机:粗轧机组可使用二辊、四辊轧机或全 部使用四辊轧机,精轧机组多使用四辊轧机
行星式轧机:现在已很少使用,受轧制产品质量的
影响,通常不作为成品轧机使用,而是作为粗轧机
使用,轧后要配置一台四辊或六辊轧机作为精轧机
生产成品
35
(4)冷轧带钢轧机
单机架可逆式和连续式两种方式 单机架可逆式轧机:多使用四辊、六辊和二十辊轧
17
(2)板型要好
板型要平坦,无浪形瓢曲:对普通中厚板,其每 米长度上的瓢曲度不得大于l5mm,优质板不大于 10mm,对普通薄板原则上不大于20mm。
板带钢既宽且薄,对不均匀变形的敏感性特别大, 所以要保持良好的板型很不容易。
板带愈薄,其不均匀变形的敏感性越大,保持良 好板型的困难也就愈大。板型的不良来源于变形 的不均,而变形的不均又往往导致厚度的不均, 因此板型的好坏往往与厚度精确度也有着直接的 关系
(3)可弯曲、焊接成各类复杂断面的型钢、
钢管、大型工字钢等结构件,故称为“万 能钢材”
6
板带材的生产特点
(1)板带材是用平辊轧出,故改变产品规格较简
单容易,调整操作方便,易于实现全面计算机控 制的自动化生产
(2)带钢的形状简单,可成卷生产,且在国民经
济中用量最大,故必须而且能够实现高速度的连 轧生产 (3)由于宽厚比和表面积都很大,故生产中轧制 压力很大,可达数百万至数千万牛顿,不仅使轧
16
(1)尺寸精度要求高
尺寸精度主要是厚度精度,因为它不仅影响到使用 性能及连续自动冲压后步工序,而且在生产中难 度最大
厚度偏差对节约金属影响很大。板带钢由于B/H很 大,厚度一般很小,厚度的微小变化势必引起其 使用性能和金属消耗的巨大波动。
故在板带钢生产中一般都应力争高精度轧制,力争 按负公差轧制(在负偏差范围内轧制,实质上就 是对轧制精确度的要求提高了一倍,这样自然要 节约大量金属,并且还能使金属结构的重量减轻 )
冷轧商品板卷 0.25~3 ×960~1540
CQ;DQ;DDQ;HSLA
冷轧板厂 热镀锌卷 0.25~2.5 ×960~1540
CQ;DQ;FH;HSS
彩涂板 * 0.25~1.5 ×960~1540
CQ;DQ;HSS
碳素钢带钢 183~438 ×1.6~4.5
Q195~Q235
低合金钢带钢 183~438 ×1.6~4.5
18
(3)表面质量要好
板带钢是单位体积的表面积最大的一种钢材,又 多用作外围构件,故必须保证表面的质量
无论是厚板或薄板表面皆不得有气泡、结疤、拉 裂、刮伤、折叠、裂缝、夹杂和压入氧化铁皮, 这些缺陷不仅损害板制件的外观,而且往往败坏 性能或成为产生破裂和锈蚀的策源地,成为应力 集中的薄弱环节
轧钢工艺学—板带生产工艺
材料成型与控制工程系
主要内容
板带材生产概述 中厚钢板生产
热轧薄板带钢生产 冷轧板带钢生产
板带材高精度轧制及板形控制
2
参考书
《板带钢生产》、赵家骏 《板带钢生产工艺学》、宋佩莼 《板带生产工艺学》、冯光纯 《板带材生产原理与工艺》、王廷溥
电子资料
中文:CNKI,超星数字图书管 英文:ELSEVIER、EBSCO、Springer
28
异步驱动
上、下辊异 步传动
异步驱动
上、下工作 辊异步传动
为了降低轧 制力,采用 上、下辊圆 周速度不同 的传动方式
为了降低轧 制力,采用 上、下工作 辊圆周速度 不同的传动 方式
29
3、按轧机组成分类
单机架可逆式轧机:在单一的机架上完成多道次 往复轧制。在开坯和厚板轧制时,轧件通过轧前辊 道和轧后辊道将轧件输送到轧机中进行往复轧制, 在轧制薄轧件时,轧前和轧后设置有卷取机,进行 往复轧制
8
板带材产品分类
我国: 中厚板:厚度在4.0mm以上 (其中4~20mm者为中
板,20~60mm者为厚板,60mm以上者为特厚板,特 厚板可厚至500mm以上,最宽可达5000mm)
薄板:4.0~0.2mm 极薄带钢(箔材):0.2mm以下,目前箔材最薄可
达0.001mm 日本: 规定3~6mm为中板,6mm以上为厚板
21
四、板带轧机
1、按辊系分类(最常用、最基本) 常用的轧机:二辊、三辊、四辊、六辊、八辊、
十二辊、二十辊以及偏八辊、非对称式八辊、行 星式轧机等 特点:由一对工作辊和多个支持辊构成。一般而 言,随辊数增加,工作辊径减小。 特殊 行星轧机:多个工作辊按行星方式布置在 支持辊的周围。这是一种特殊形式的轧机,能将板 坯一次轧制成薄板
机,轧机前后设置有卷取机,在单机架上完成多道 次轧制。 连续式轧机:多采用4~6架轧机连轧,一般多使用 四辊或六辊轧机。
36
(5)平整机
为改善钢板的平坦度和表面质量,有时为了调整力 学性能,在钢板轧后或钢板热处理后,在平整机上 进行一道小压下量轧制。
不同规格的钢板平整机有二辊、四辊、六辊等不 同形式的轧机
减小辊径:能降低轧制压力,减小弹性压扁,有利于轧制薄 轧件
为防止细而长轧辊的弯曲变形和断辊,可采用增设支撑辊 的方法。从防止工作辊的垂直弯曲和水平弯曲的目的出发, 演变出各种板带钢轧件的辊系。
24
25
26
2、按轧辊驱动方式分类
最基本的驱动方式:直接驱动一对工作辊。
由于轧制更薄、更硬材料的需求增加,为了降低轧 制压力,工作辊的辊径变小,传递轧制力矩的辊头 尺寸小,受轧辊强度、刚度限制不能直接驱动工作 辊,因此发展了传动辊径大的支持辊的间接传动方 式和其他驱动方式
有关品种规格可参看国家标准
11
包钢板厂产品大纲
冷轧用钢板 1.2~8 ×980~1560
SPCC;SPCD;SPCE
管线用钢板 1.2~20 ×980~1560
X42;X52;X56;X60;X65
热轧结构用板 1.2~12 ×980~1560
SPHC;SPHD;Q345C;SM490;SM520
主要形式:双机架轧机布置方式 粗轧和精轧分别在粗轧机(二辊或四辊
轧机)和精轧机(多为四辊轧机)上完成 也有在一台轧机上完成粗轧和精轧全
部轧制过程
34
(3)热轧带钢轧机
一般轧制过程分为粗轧和精轧两个阶段
可逆式带钢轧机:粗轧机使用四辊轧机,精轧机使 用四辊或六辊轧机,由于单机架轧制速度低,钢板 温降大,特别是钢板边部温降大,采用把卷取机放 在加热炉内的炉卷轧机生产
31
轧机组成分类
32
4、按轧机用途分类
(1)开坯轧机 采用钢锭生产钢板时,要将钢锭轧制成
板坯,作为成品轧机的原料。 由于开坯时一般压下量大,所以使用大
辊径的二辊开坯轧机。 近年来板坯连铸生产技术发展很快,采
用开坯机生产板坯的量已很少
33
(2)中厚板轧机
中厚板生产多采用板坯为原料,经粗轧 和精轧轧制成成品板材。
22
行星轧机机组
行星轧 机
张力控 制辊
23
辊系的演变:
板带钢轧件宽而薄 轧制压力大,轧制压力大的结果影响 到轧辊的刚度和强度,使轧辊产生弯曲变形影响到产品的 尺寸精度,以致发生断辊。
增大辊径:可提高轧辊的刚度和强度,但是轧制压力也因 辊径的增大而增大,同时轧辊的弹性压扁增加,难以轧制薄 轧件
热轧板厂 集装箱用板 1.2~10 ×980~1560
SPAH;SM400;SS400
汽车大梁用板 1.2~12.7 ×980~1560
BG510L
压力容器用板 1.2~20 ×980~1560
HP245;HP295;HP345
耐候用钢 1.2~12 ×980~1560
09CuPTiRE;09CuPCrNi
例如:硅钢片表面的氧化铁皮和表面的光洁度就 直接败坏磁性,深冲钢板表面的氧化铁皮会使冲 压件表面粗糙甚至开裂,并使冲压工具迅速磨损, 至于对不锈钢板等特殊用途的板带,还可提出特 殊的技术要求
19
(4)性能要好
主要包括机械性能、工艺性能和某些钢板的特殊 物理或化学性能
一般结构钢板:具备较好的工艺性能,例如,冷 弯和焊接性能等,而对机械性能的要求不很严格
用途:带有卷取机的可逆式带钢轧机是冷轧带钢 用轧机的主要形式之一,而在热轧带钢轧制时使用 的炉卷轧机,轧前、轧后的卷取机安装在加热炉内, 用于生产变形温度区间窄的不锈钢、硅钢等产品
多机架连续式板带轧机:当今热轧带钢和冷轧带 钢生产的主要轧机
30
炉卷轧机
1、保温炉 2、卷筒 3、夹料辊 4、导入板
间接驱动方式带来的问题:在水平方向上对工作
辊作用有切向力,使工作辊产生水平弯曲。因此要
有防止工作辊水平方向挠曲的装置。像十二辊、
二十辊轧机结构具有防止工作辊水平方向挠曲的
作用,而轧辊垂直布置的四辊、六辊轧机没有防止
工作辊水平方向挠曲的作用,在工作辊径小时要考
虑添加防止工作辊水平方向挠曲的装置
27
甲类钢钢板:要保证性能,有一定的强度和塑性
重要用途的结构钢板:要求有较好的综合性能, 除要有良好的工艺性能,甚至除了一定的强度和 塑性以外,还要求保证一定的化学成分,保证良 好的焊接性能、常温或低温的冲击韧性,或一定 的冲压性能、一定的晶粒组织及各向组织的均匀 性等等