制程失效模式及后果分析培训
FMEA培训资料潜在失效模式及后果分析

Potential Failure Mode and Effects Analysis
潜在失效后果
• 是指失效模式对系统功能的影响 • 要根据顾客或经理可能发现的情况来描
述失效的后果(顾客可以是内部或外部)
• 应记住不同级别系统、子系统和零件之
间还存在系统层次上的关系
潜在失效的后果
考虑以下方面: 对完成功能的影响 对上级系统和系统内其他零件的影响 对所有顾客的影响(包括使用成本) 对法规的影响 对营销方案/的影响 对可制造性/可装配性的影响
Potential Failure Mode and Effects Analysis
级别
• 是指产品特性分级 • 应用适当的方式进行标识 • 每一个在DFMEA中标识的特性均应在
PFMEA中有特殊的过程控制
级别—特殊特性
特性:产品或零件的尺寸、性能、外观、 重量等可定义的固有的特征。
特殊:一种是与安全和/或法规有关,即该特 性影响安全和/或法规;一种是该特性的波动 会影响到产品或零件的基本性能,但不会影响 到安全和/或法规。
FMEA小组应对评价准则和分级规则达成一致意见。 组织可对准则进行修改,不推荐修改9和10的准则。 严重度的定级可以通过修改设计、使之补偿或减轻失
效的后果来降低。如:“瘪胎”可以减轻突然爆胎的 严重度,“安全带”可以减轻车辆碰撞的严重程度。 “车辆/项目”在用于其他产品时,可理解为“最终产 品/生产产品”。如电视机/显示器、电脑/接线端子等。 9~10:与安全/法规有关,5~8:与性能/功能有关 2~4:与外观和感觉有关 严重度为1的失效模式不应进行进一步的分析。
的SFMEA,也可能没有SFMEA。 针对自行车(系统)、车架(子系统)
功能的DFMEA就是SFMEA,针对“下部 前车管”功能的则是DFMEA。
PFMEA过程失效模式及后果分析

PFMEA过程失效模式及后果分析PFMEA(Process Failure Mode and Effects Analysis)过程失效模式及后果分析是一种常用的质量管理工具,用于评估和改进产品制造过程中的潜在问题和风险。
它旨在预测和预防可能导致产品失效的过程步骤。
1.确定过程步骤:首先,识别和定义产品制造过程中的每个关键步骤,包括原材料采购、加工、装配、测试等。
2.确定失效模式:对于每个过程步骤,识别可能导致失效的模式。
失效模式可以是设备故障、人为错误、材料质量问题等。
3.评估失效后果:对于每个失效模式,评估其可能导致的后果和影响。
后果可以涉及到产品质量问题、安全风险、客户满意度等。
4.定义风险优先级:根据失效模式的严重性、发生频率和检测能力,为每个失效模式分配一个风险优先级。
这可以帮助制定合理的风险控制策略。
5.制定改进计划:对于评估出的高优先级失效模式,制定相应的改进计划和控制措施。
这可能包括优化生产工艺、提供培训和教育、改进设备维护等。
6.实施和监控措施:执行改进计划,并监控其有效性。
定期对PFMEA进行更新,以反映过程改进和新的风险评估。
通过实施PFMEA,可以有效地识别和消除潜在的制造过程问题,并降低产品质量问题的风险。
下面以汽车制造业为例,具体分析PFMEA的应用。
在汽车制造过程中,每个制造步骤都可能存在潜在的失效模式。
例如,原材料采购环节可能存在材料质量问题的风险,加工环节可能存在操作错误或设备故障的风险,装配环节可能存在组装错误或安装不良的风险,测试环节可能存在测试不准确或设备故障的风险。
针对这些潜在问题,可以使用PFMEA来识别并评估其风险。
例如,在加工环节,识别可能的失效模式可能包括不正确的参数设置、设备故障、操作错误等。
然后,评估这些失效模式可能导致的后果和影响,如产品偏差、生产延误、设备故障等。
根据评估结果,确定失效模式的风险优先级,以便制定相应的改进计划和控制措施。
例如,对于评估为高风险的加工失效模式,可以采取以下改进措施:加强对操作员的培训和教育,确保他们正确操作设备和设置参数;增加设备维护和保养频率,以减少设备故障的风险;实施过程监控和自动化控制,以确保稳定的生产环境。
潜在失效模式及后果分析(FMEA)—培训教材.

決定失效模式
確認效應 確認原因 確認目前控制 評價嚴重度 評價發生度 評價偵測度 三種 評價 完成 ? 否 是 收集數據 進行變更 確認改變 執行改變 收集數據 原因順序 影響要因 確認改變 是 知道如何 影響 遴選最重要 失效模式
嚴重度? 發生度? 偵測度? 否
更新文件 重訂優先順序
CAUSE
MODE
EFFECT
FMEA
潜在失效模式及后果分析
何謂过程 FMEA?
过程的潛在 FMEA 是一種分析技術,係由負責过程的工程師或小組使用,在 儘可能的範圍內用來確保所有潛在的失效模式及其原因/機制均已納入考量並 予以處理。过程潛在 FMEA旨在: • 鑑別过程的機能和要求 • 鑑別潛在的產品和过程有關的失效模式 • 評估失效對顧客的潛在影響 • 鑑別潛在的製造或組裝過程原因和鑑別过程變數 ( Variables ),並 且據以控制降低發生率或失效情況的偵測度。 • 鑑別过程變數,以著眼於过程控制 • 列出潛在失效模式之排序,並據以建立考慮採取預防/矯正措施 的優先順序 • 將製造或組裝過程的結果予以文件化。
偵 測 度
R P N
建議措施
責任與 目標 完成日期
措施結果
嚴 難 偵 R
採行措施 重 檢 測 P
度 度 度 N
效應為何?
有多不好?
功能, 特徵 或要求為何?
原因為何?
其發生 頻率為何?
改善風險程度 能夠做什麼? -- 設計變更 -- 过程變更 -- 特別控制 -- 標準, 程序書 或指引變更 -- 導入防呆措施 -- 加強設備保養 -- 加強參數控制 -- 加強工作技能
FMEA
潜在失效模式及后果分析
FMEA 作業說明(FMEA 團隊遴選及流程)
过程FMEA失效模式及后果分析PPT培训课件

评估失效模式的 后果
确定失效模式的 严重程度…
制定预防和探测 措施
食品加工过程,包括原料 采购、加工、包装和储存 等环节。
例如,原料可能存在农药 残留、微生物污染等问题 ;加工过程中可能出现烘 烤不均匀、切割尺寸不对 等;包装过程中可能出现 标签错误、密封不严等。
例如,农药残留可能导致 消费者健康问题;烘烤不 均匀可能导致食品口感和 质量下降;标签错误可能 导致消费者对产品的误解 。
THANKS FOR WATCHING
感谢您的观看
跟踪实施效果
对改进措施的实施情况进行跟 踪和效果评估,持续改进。
02 过程FMEA的实施过程
确定分析范围和边界
确定分析对象
明确过程FMEA的分析对象,如产品、服务或系统 等,并定义其边界和范围。
确定分析阶段
确定失效模式可能发生的阶段,如设计、制造、 运输、安装等。
确定分析重点
根据分析对象和阶段,确定失效模式分析的重点 和关注点。
如何制定有效的改进措施和行动计划?
制定改进措施和行动计划是FMEA分析的最终目的。
根据风险优先级,选择具有最大潜在改进的失效模式进行改进。这可能包括设计更改、工艺改进、过 程控制强化等。制定行动计划时,应明确责任人、完成时间和检查点,以确保改进措施的有效实施。
如何持续改进FMEA分析?
持续改进FMEA分析可以提高其有效性和可靠性。
明确分析的对象,包括产品、系统、过程等,并对其进行 定义和描述。
列出所有可能的失效模式
全面考虑可能出现的失效模式,并对其进行分类和归纳。
评估失效模式的后果
分析失效模式可能导致的影响和后果,包括对产品、系统 、过程的影响以及对顾客的影响。
确定失效模式的严重程度、发生频率…
制程失效模式与后果分析(PFMEA)》

来料外观不良或者运输
7 和作业过程中发生划伤
和和作业过程中不良。
来料已经有移动颗粒污
7 染,在镜头内部,空间
狭小无法彻底清洁。
8 操作不当
1.25% 0.25%
0.05%
0.25% 0.25% 1.25% 0.05%
马达组装
盖镜头 烘烤 马达焊接 分板 PCBA测试
镜头顶面有划痕、破损
影响产品外观 高
清洁
芯片上有划伤、污点
影响成像质量 高
马达内部较深,无法彻底清 洁,盖镜头后,有移动可见颗 粒。
导致不良,返 工
高
漏粘胶
马达组件脱落 很高
电子千分尺未及时矫
8 正,测量精度误差过大
。
8
来料运输过程中发生污 染
螺纹破损,lens螺牙无 8 法匹配,下旋阻力过
大,无法组装。
设计失效模式与影响分析(PFMEA)
项目 Item
核心团队 Team
项目/功能 Item/Function
手机摄像头 制程 PFMEA
潜在失效模式 Potential Extinct Mode
失效影响 Extinct Affection
严重度(S) Severity
失效原因 Extinct Cause
发生率(O) Occurrence
FMEA编制日期
FMEA Organization Date 关键日期
Key Date 审核
Approve
现行控制方法 Present Control
Method
难检度(D) Detection
风险 Risk RPN
2013/12/9 2014/2/21
建议的措施 Suggestion Action
培训课件潜在的失效模式及后果分析fmea

协作性:
虽然 FMEA 的编制责任通 常都指派到某个人,但是 FMEA 的输入应该是小组的努力。
小组成员应由知识丰富的 人员组成(如设计、分析/试验 、制造、装配、服务、质量及 可靠性等方面的有丰富经验的 工程师)
7
潜在失效模式及后果分析 FMEA
主观性
FMEA 的特点(3)
31
(22)
过程 FMEA 的開發
5 )車型年/車輛類型
填入將使用和/或正被分析的設計所影響的預期車型年
及車輛類型。 (如果已知的話)
过 程 FMEA
系统
X 子系统 ______部件 01.03/车身密封 (2) 车型年/车辆类型 199X/狮牌 4门/旅行车 (5) 核心小组: T.芬德-轿车产品开发部、切利得斯-制造部、J.福特-总
建議 措施
責任及目標 完成日期
措施結果
采取 的措施
R S ODP
N
功能、特性或 要求是什么?
綴彆岆 妦繫ˋ
衄嗣 媎詹ˋ
岆妦繫ˋ
楷汜腔 ˋ
能做些什么? - ??更改 - ?程更改
特殊控制 - ?准、程序或
指南的更改
?有什么??? - ?功能 - 部分功能/功能
?? /功能降? - 功能?歇 - 非?期功能
2
潜在失效模式及后果分析 FMEA
3
潜在失效模式及后果分析
FMEA
4
潜在失效模式及后果分析 FMEA 什么是 FMEA
FMEA 一組系統化的活動
(a)發現、評價產品/過程中潛在的失效及其後果 (b)找出能夠避免或減少這些潛在失效發生的措施 (c)全部過程形成文件
5
潜在失效模式及后果分析 FMEA
FMEA潜在的失效模式及后果分析(培训内容)

1、FMEA 的概念: 指 Potential Failure Mode and Effects Analysis(潜在的
失效模式及后果分析)的英文简称。
P ( Potential ) 潜在的 F ( Failure ) 失效
M ( Mode ) 模式
A ( And ) 及/和 E ( Effects ) 后果 A ( Analysis ) 分析 ■ FMEA 是潜在的失效模式及后果分析的缩写,本应写成P-FMEA, 但由于企业/公司常用D-FMEA表示产品FMEA,用P-FMEA表示过 程FMEA,所以用FMEA表示潜在的失效模式及后果分析,以免混淆。
潜在的失效模式及后果分析概要介绍
10、FMEA 的工作架构:(3/3)
6)当前控制: ■ 你(对现有设计)做了什么?或你(对将来设计)会做什么 以用来评估,消除或减少风险发生? ◆ 避免原因发生 ◆ 提早确定问题存在 ◆ 减少后果及影响 7)风险评估: ■ 将频度(O)、探测度(D)和严重度(S)的结果综合并做 风险评估。 ■ 用RPN(风险顺序数)表示: RPN =(O)×(D)×(S)
8)建议改善措施:无论你对总体风险评估满பைடு நூலகம்与否,你都应写出计划。 9)根据建议的改善措施,你做了什么?
潜在的失效模式及后果分析概要介绍
11、FMEA 与 FMA 的区别 1)失效模式分析(FMA)的概念和定义: 失效模式分析(Failure Mode Analysis:简称 FMA):指用来分析当 前和以往过程的失效模式数据,以防止这些失效模式将来再发生的正 式的结构化的程序。FMA是一种事后的纠正行为。 2)FMEA — 潜在的失效模式及后果分析,是“事前的预防措施”,并 “由下至上”进行分析。 ■ 关键词:潜在的 — 失效还没有发生 ■ 可能发生 ■ 但不一定会发生 ■ “核心”集中于:预防 — 处理预计的失效,其原因及后果/影响 ■ 主要工作:风险评估 — 潜在失效模式的后果影响 ■ FMEA 开始于产品设计和制造过程开发活动之前,并指导贯穿实施 于整个产品周期 3)FMA — 失效模式分析,是对产品/过程已经发生的失效模式分析其产 生的原因,评估其后果及采取纠正措施的一种活动。FMA是“事后的 纠正措施”。 ■ 关键词:失效 — 已实际发生 ■ 100% 既成事实 ■ “核心”集中于:诊断 — 处理已知的失效 ■ FMA 在生产或范围内实施,指引的是开发和生产
IATF16949 失效模式与后果分析(FMEA)培训课件

▪ 在设计阶段,改进的重点是用于指出设计上的 问题点,改进设计,用以确认产品设计是否满 足顾客要求;(关注客户要求)
▪ 在制造阶段,改进的重点是用于指出加工、装 配、生产、设计方面的问题点,反推至前一过 程或前一阶段,要求进行必须的改进。
可能有何错误? -功能丧失 -部分/全部功能
降低 -功能间歇性中断 -非预期的功能
为有可能 被预防和 探测吗?
可以做什么? -设计变更 -过程变更 -特别的控制 -标准、程序或
指南的更改
探测它 的方法 有多好?
2022/2/10
12
4. TS16949----FMEA类型
▪ 依据产品实现阶段不同可分为:
▪ 事前花时间很好地进行综合的FMEA分析,能够容 易、低成本地对产品或过程进行修改,从而减轻事 后修改的危机
▪ 适当应用FMEA是一个相互作用的过程,永无止境
2022/2/10
21
7. FMEA实施过程中注意事项--关于分值
▪ 同一小组分值要一样; ▪ 分析前的培训和思路的统一很重要; ▪ 不同过程分值可以不同(设计过程与制造过程)
2022/2/10
32
2. DFMEA分析步骤过程
产
每
品
一
或
部
系
分
统
功
能
2022/2/10
失 效 模 式 分 析
依
FMEA 表 逐 项 分 析
33
3. DFMEA分析方法
硬件法
针对零件清单上的每一个零件,一次一个的逐个分析, 直到整个产品分析完
功能法
FMEA(失效模式与后果分析)

苏州生益科技培训教材.huangzz
4.什么时候需要开始做FMEA?
1.当一个新的系统、产品或过程开始设计时 2.当存在的设计或过程需要改变时 3.当设计或过程应用到新的地方或新的环境 4.研究或解决的问题完成后,防止问题再发生 5.设计的产品功能被确定,在产品设计被批准开始制造之前
苏州生益科技培训教材.huangzz
苏州生益科技培训教材.huangzz
诠释FMEA
在设计和制造产品时,通常有三道控制缺陷的防线:避免或消除故障起因、 预先确定或检测故障、减少故障的影响和后果。 FMEA正是帮助我们从第一道防线就将缺陷消灭在摇篮之中的有效工具。
FMEA是一种可靠性设计的重要方法。 它实际上是FMA(故障模式分析)和FEA(故障影响分析)的组合。 它对各种可能的风险进行评价、分析,以便在现有技术的基础上消 除这些风险或将这些风险减小到可接受的水平。 及时性是成功实施FMEA的最重要因素之一,它是一个“事前的行 为”,而不是“事后的行为”。 为达到最佳效益,FMEA必须在故障模式被纳入产品之前进行。 失效模式及后果分析是动态文件。 失效模式及后果分析是一个集体过程而非单一的个人过程。
目视 目视
目视/检具 检具 防错/检具 防错/检具 防错/检具 防错
高
非常高 几乎没问题可 查测出
设计(过程)控制侦测出潜在原因或不良模式的概率高
设计(过程)控制侦测出潜在原因或不良模式的概率很高 设计(过程)控制侦测出潜在原因或不良模式的概率没有问题
3
2 1
苏州生益科技培训教材.huangzz
风险优先系数(RPN)
责任及 目标完 成日期
行动结果
采取 的行 动 S O D R P N
能做些什么? -设计更改 -过程更改 -特殊控制 -标准、程序或 指南的更改
潜在失效模式与后果分析(FMEA)培训

表面加工规范错误 维修保养说明错误
演算法不适当
维修保养说明不适当
16. 发生率(O):在设计的寿命中某一特定失效起 因/机理发生的可能性。描述发生率的级别数重在 其含义,而不是具体的数值。通过设计更改更改 来预防或控制该失效模式的起因/机理是降低发生 率级别数的唯一途径。
确定等级需考虑: 维修历史情况 部件是否全新设计 环境有无变化 用途有何变化 是否采取了预防性控制措施 针对用途,是否作了工程分析(如可靠度)来估计
构成零件
组件 功能件 子系统 系统
人、环境等
零件故障
对组件 的影响
FMEA的分析层次
对功能 件的影响
对子系 统的影响
对系统 的影响
对人和环境 等的影响
图1-1 FMEA的影响分析层次
设计FMEA的一个关系方块图(分析中所考虑的项目)
也可用其他形式的方块图
开关
3
2
灯泡总成
灯罩
4
4
1
极板
电池
弹簧
5
5
连接方法:1.不连接(滑动配合) 2.铆接 3.螺纹连接 4.卡扣连接 5.压紧装接
• “系统”的概念
1、“系统”。系统是指具有全部功能并可达成要求的任务 的产品,如汽车、轮船、飞机等可以称为机械系统;电脑、 卫星、移动电话等可称为电子系统。
2、子系统。子系统是系统的构成部分,能达成系统的部分 功能,如汽车的动力系统、电脑的显示系统等。
3、构成件。构成件是构成子系统和系统的单元,可分为功 能件、组件和零件。
没有特定的RPN值要求强制措施
1、小组的焦点应该定位于严重度最高等级的失效模式,当严重 度等级为9或10时,必须强制确保风险通过存在的设计控制 或建议措施来陈述
过程潜在失效模式及后果分析培训试卷答案
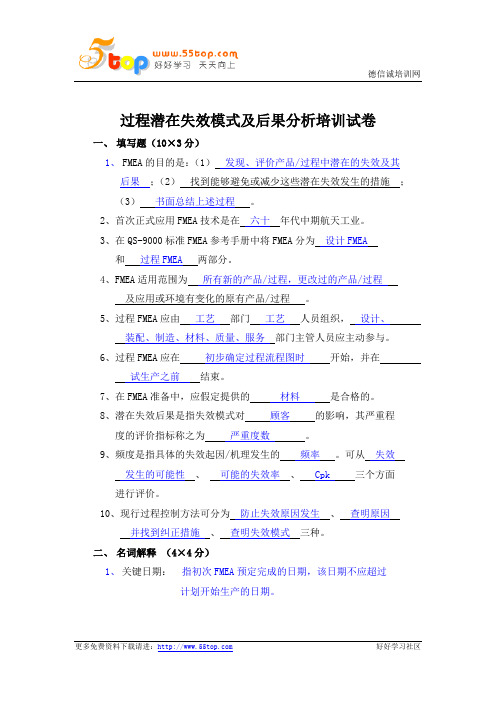
过程潜在失效模式及后果分析培训试卷一、填写题(10×3分)1、FMEA的目的是:(1)发现、评价产品/过程中潜在的失效及其后果;(2)找到能够避免或减少这些潜在失效发生的措施;(3)书面总结上述过程。
2、首次正式应用FMEA技术是在六十年代中期航天工业。
3、在QS-9000标准FMEA参考手册中将FMEA分为设计FMEA和过程FMEA两部分。
4、FMEA适用范围为所有新的产品/过程,更改过的产品/过程及应用或环境有变化的原有产品/过程。
5、过程FMEA应由工艺部门工艺人员组织,设计、装配、制造、材料、质量、服务部门主管人员应主动参与。
6、过程FMEA应在初步确定过程流程图时开始,并在试生产之前结束。
7、在FMEA准备中,应假定提供的材料是合格的。
8、潜在失效后果是指失效模式对顾客的影响,其严重程度的评价指标称之为严重度数。
9、频度是指具体的失效起因/机理发生的频率。
可从失效发生的可能性、可能的失效率、Cpk 三个方面进行评价。
10、现行过程控制方法可分为防止失效原因发生、查明原因并找到纠正措施、查明失效模式三种。
二、名词解释(4×4分)1、关键日期:指初次FMEA预定完成的日期,该日期不应超过计划开始生产的日期。
2、潜在失效模式:是指过程可能发生的不满足过程要求和/或设计意图的形式,是对某具体工序不符合要求的描述。
3、不易探测度:是指在零部件离开制造工序或装配工位之前,第二种现行过程控制方法找出失效起因/机理过程缺陷的可能性的评价指标;或者用第三种过程控制方法找出后序发生的失效模式的可能性的评价指标。
4、风险顺序数:是严重度数(S)、频度数(O)和不易探测度数(D)的乘积。
三、判断题:(10×3分)( N)1、过程FMEA中“顾客”仅指“最终使用者”。
(Y)2、过程FMEA绝不能只由工艺人员个人进行,而应主动联络相关部门人员一起进行。
(Y )3、过程FMEA是一份动态文件,应考虑以单个零件到总成的所有制造工序。
失效模式及后果分析(FMEA)

PFMEA
范围
1)功能模块;2)方块图;3)界面图;4)过程流程图;5)关系矩阵图;
6)示意图;7)材料清单。
功能、要求 和期望
阐明项目设计意图或过程目的,有助于确定每一个属性或功能的潜在失效模式的确定
潜在失效模 式
确定的方式或途径是产品或过程未能满足设计意图或过程要求,一个单一的要求可以 识别出多个失效模式;
1)概念;2)初始设计;3)设计完成;4)样件制造;5)设计/过程确认;6)制造开始。
公司LOGO
FMEA概要介 绍
FMEA 策略、 策划和执行的 概述
DFMEA
PFMEA
范围 重点
4、FMEA实施的影响
新设计、新技术或新制程 这时是完整的设计、技术或制程的FMEA
修改现有的设计或制程 这时是FMEA的焦点在修改设计或制程,以及由于在 修改过程中设计、制程而导致的相互作用
1、背景
FMEA概要介 绍
FMEA 策略、 策划和执行的 概述
DFMEA
PFMEA
FMEA的基 本结构
FMEA展开 的主题
1)功能、要求和产品的可交付性或需要分析的过程; 2)当功能要求不符合时的失效模式; 3)后果和失效模式的结果; 4)失效模式的潜在要因; 5)对所述失效模式的要因的措施和控制; 6)预防失效模式发生的措施。
提供公开的讨论形式
针对建议和跟踪降低风险 的措施等方面的内容;
06
为后续的提供参考
例如售后市场关切情况, 评价设计更改及开发先 进的设计;
05
01
DFMEA
04
02
建立设计改进、开发和验证 试验/分析的优先系统
通过对“顾客”的影响进 行分级列表;
过程失效模式及后果分析-教程

过程失效模式及后果分析-教程
PFMEA过程失效模式和影响分析
PFMEA的主要目的 ----消除或减少制造风险:
1 帮助分析 新的/更改的(或需要改进的)制造和装配过程。 2 确保已知的和潜在的制造/装配过程失效模式和影响都得到了
考虑。 3 确定过程缺陷,提出可能的原因,针对原因提出控制措施。 4 消除或降低生产不可接受产品的频率。 5 增强对不可接受产品的可探测度。 6 确定关键特性和重要特性,以便编制完整的过程控制计划。 7 建立过程改进(风险降低)的优先顺序。 8 提供过程开发文件,为今后开发制造/装配过程提供指导。
PPT文档演模板
过程失效模式及后果分析-教程
PFMEA 过程输入
编制PFMEA,多功能小组可应用的数据和参考文件: · 过程FMEA-AIAG参考手册 · 特性矩阵(产品VS过程) · 以往SPC记录 · 保修信息 · 顾客抱怨和产品退回数据资料 · 纠正或预防措施 · 过程流程图、现场布置图、操作描述 · 系统和/或设计 FMEA · 类似产品/过程的 PFMEA · 其他,如供应商/物流分包商关注的问题等
– 问“如果出错,影响有多大”? 参考 AIAG 手册严重度表 – 问“怎么会出错”? 列出所有可能造成产品/过程特性未或未被正确制
造的原因 – 问“这些失效原因发生有多频繁”? 参考 AIAG 手册发生频度表 – 问“这些失效模式是如何探测的”? 参考 AIAG 手册探测度分级表
PPT文档演模板
过程失效模式及后果分析-教程
•Misassembly •17%
•Worn/Broken •Tooling •26%
PPT文档演模板
过程失效模式及后果分析-教! • 我们没有时间!! • 我们不知道如何做!! • 我们没有工具!! • ……
FMEA(潜在失效模式及后果分析)培训教材

三、怎样做FMEA——表单填写
9)探测度(D):
填入对采用“现行控制”方法来控制时,该潜在问题可以被检查出来的 难易程序的评价。
探测度采用1-10分制,得分愈高则愈难以被检出。 探测度是对现行控制方法有效性的评估。 依据《探测度对照表》进行评分。
6
低
生产线破坏不严重,产品需要100%返工,产品/系统能运行,但有些舒用性或方便性 项目性能下降,客户有些不满意。
5
很低
生产线破坏不严重,产品经筛选,部分(少于100%)需要返工,产品规格不符合要 求,多数客户发现有缺陷。
4
轻微
生产线破坏较轻,部分(少于100%)需要在生产线上其它工位返工。产品规格不符 合要求,有一半客户发现有缺陷。
3
很轻微
生产线破坏轻微,部分(少于100%)产品需要在生产线上原工位返工。产品规格不 符合要求,很少客户发现有缺陷。
2
无
无可辨视的影响。
1
三、怎样做FMEA——表单填写
5)级别:
填入特殊特性的标识符号。 凡是识别为特殊特性,需要特殊过程控制的项目应当以适当的符号在 此栏中标识,使用顾客或公司规定的符号。 产品特性以▲标识,过程特性以▼标识。 特殊特性依据《特殊特性明细表》和《特殊特性矩阵图》进行识别。
三、怎样做FMEA——表单填写
三、怎样做FMEA——表单填写
5.2 表单部分:
1)功能要求 2)潜在失效模式 3)潜在失效后果 4)严重度(S) 5)级别 6)潜在失效起因/机理 7)频度(O) 8)现行控制 9)探测度(D) 10)风险顺序数(RPN) 11)建议措施 12)责任及目标完成日期 13)措施结果
充分发挥小组的经验,采用头脑风暴法,对可能的原因进行归纳分析。
DFMEA培训资料

关键特性和特 性的控制
典型的汽车产品发展的三步曲
过程的流向及清 单
检查客户的要 求
注意:FMEA=还 应当包含对产品特 殊特性的评估。
仔细考虑控制计划的 各个阶段: -样板 -试产 -量产
选择每一个“关 键”的过程到 FMEA表中
评估每一个过程 的FMEA项目
发展包含了特殊 特性的控制计划
• Software packages make flow chart production easy.
怎样做PFMEA?
4. 把出对产品的特殊特性有影响的过程先 标出来,这些过程应当优先评估。
5。把对下道工序有影响的工序标出来, 这些过程也应当优先评估。
6。把每道工序的功能写下来。 思考:想一下,为什么??
怎样用FMEA评估过程的风险?
• 失效模式的严重度 (S)
•一般用S(严重度)来表示产品的缺陷对 最终使用,或下道工序,以及客户满意度 的影响程度。D最小为1, 最大是10。D 越大,产品的缺陷越严重, 缺陷造成的
后果 越严重。
怎样用FMEA评估过程的风险?
• 失效模式的发生频率 (O)
•用 O(发生频率)来表示产品的缺陷的 可能性。 O最小为1, 最大是10。O越大, 产品的缺陷发生的可能性越大。
仔细考虑所选 的“关键”过 程
用适当的RPN数值 和一些别的意见来 决定关键的特性 (过程)
发展针对特殊特 性的控制机制
Some Key FMEA Terms
• Customer Input • Team - Team Selection (Cross-Functional) • Ranking - Ranking of Decisions • Risk Priority Assessment • Design Process • Production Process
- 1、下载文档前请自行甄别文档内容的完整性,平台不提供额外的编辑、内容补充、找答案等附加服务。
- 2、"仅部分预览"的文档,不可在线预览部分如存在完整性等问题,可反馈申请退款(可完整预览的文档不适用该条件!)。
- 3、如文档侵犯您的权益,请联系客服反馈,我们会尽快为您处理(人工客服工作时间:9:00-18:30)。
What is an FMEA? 什麼是FMEA?
Group of activities 系統化的活動 • Recognize & evaluate potential failure of product/process
认可并评价产品/过程中的潜在失效
• Identify actions to reduce the chance of the failure occurring 确定能消除或减少潜在失效发生机会的措施
• Reviewing Design/Process FMEA, special FMEA applications and control plan
对设计/过程FMEA、FMEA的特殊应用以及控制计划进行评审
13
When to update of FMEA? 何時更新FMEA?
•FMEA is a living document and should always reflect the latest level, latest relevant actions, including those occurring after the start of production. FMEA是一份动态文件,始终反映最新水平以及最近的相关措 施,包括生产以后发生的。
尋找方 法及解 決問題 預防
7
FMEA Implementation FMEA的实施
Because of the general industry trend to continually improve products and processes whenever possible, using the FMEA as a disciplined technique to identify and help minimize potential concern is as important as ever. Studies of vehicle campaigns have show that fully implemented FMEA programs could have prevented many of the campaigns. 因为一般的企业趋向于使用FMEA确定和帮助使潜在问题最小化来达到产 品和制程持续改善的目的.汽车行业的研究表明FMEA的执行将能防止很 多问题.
8
FMEA Implementation FMEA的实施 Key Success Factors 成功因素 • Timeliness 时间性 “Before the event” Not “After the fact” “事件发生前”不是“事实出现后”
• Follow up 跟踪
Ensure all actions have been implemented • 确保所有行动已执行
情形1:新设计、新技术或新制程.范围是全部的设计、技术或制程.
Case 2:Modifications to existing design or process.The scope should focus on the modification to design or process,possible interactions due to the modification. 情形2:对现有设计或制程的修改.范围是侧重于对设计和制程的修改及修改可能带来 的相互作用. Case 3:Use of existing design or process in a new environment,location,or application, The scope is the impact of the new environment,location on the existing design or process. 情形3:将现有的设计或制程用于新的环境、场所或应用,范围是新的环境、场所对现 10 有设计和制程的影响.
• Initially adopted in the automotive industry in the 1970s focusing on safety issues.最初於20世紀70年代應用於汽車工業,主要針對安全問題
• In 1994, all automotive suppliers were required use of FMEA under QS9000 standard. It is a major element of Advanced Product Quality Planning Process. 1994年,所有汽車行業處於QS9000標準下的供應商均被 要求使用FMEA。 FMEA 是產品質量先期策劃的一個主要部分 • Now adopted by many other industries.現已被許多其它工業應用
PROCESS FAILURE MODE AND EFFECT ANALYSIS TRAINING 制程失效模式及後果分析培訓
April ,2010 TM-002 , Rev:00 Prepared By : HenryLi
1
HISTORY OF FMEA FMEA的歷史
• It was formalized in the aerospace industry during the Apollo program in the 1960s.形成於20世紀60年代航空工業的阿波羅計劃
12
How to follow Up
怎樣跟踪
The responsible engineer has several means of assuring that recommended actions are implemented. They include,but are not limited to the following:责任工程师有几种方 法但不局限于下列几种方法来确保建议的措施被执行. •Reviewing designs, processes and drawing to ensure the recommended actions have been implemented. 对设计、过程及图样进行评审以确保建议的措施被执行 • Confirming the incorporation of changes to design/assembly/manufacturing documentation 确认更改已纳入到设计/装配/制造文件中
• is a summary of the team’s thoughts as a process is developed. 是制程開發過程中小組思想的總結 • it includes an analysis of items that could go wrong based on experience past performance,and quality performance indicators (i.e yield,In-process QA & OQA LAR/PPM, Cpk, etc.) •它對可能會出錯的項目進行分析,這些分析以經驗、以往性能和質量性能指 標(如產量、制程QA和去貨QA的批量接收率/每百萬壞品率、制程能力指標 等)为基礎 • it formalizes the mental discipline that an engineer normally goes through in any manufacturing planning process. 它總結了一般情況下工程師在策劃任一個制程時所要經歷的邏輯順序和背景
• Document entire process
将全部过程形成文件
6
COPQ at different stages 各阶段纠正问题的成本
成本 1000 100 10 1
Customer complaint客戶投訴 Manufacturing & Assembly製造及裝配 Design Approval 設計核準 FMEA Product planning Design Manufacturing Application 產品策劃 設計 製造 應用 時間
Who Edit FMEA ? 誰編制FMEA?
• Although responsibility for the preparation of the FMEA usually
assigned to individual, FMEA input should be a team effort. FMEA的编制责任通常都指派到某个人,但是FMEA的输入应是工作小組的努力
14
PFMEA简介
A process potential FMEA is an analytical technique used by a manufacturing /assembly-responsible engineer/team as a means to ensure that,to the extent possible,potential failure modes and their associated causes/mechanisms have been considered and addressed.An FMEA is a summary of the team’s thoughts. 过程FMEA是由负责制造/装配的工程师/小组主要采 用的一 种分析技术,用以最大限度地保证各种潜在的失效模式及其 相关的起因/机理已得到充分的考虑和论述。 FMEA是团队思 想的总结。
recommended actions have been implemented or adequately addressed.
责任工程师负责确保所有的建议措施都得到实施或充分的强调 • A thoroughly thought-out and well-developed FMEA will be of limited value without positive and effective preventive/corrective actions. 一个经过彻底思考、周密开发的FMEA,如果没有积极有效的预防/纠正 措施,其价值将是非常有限的。