基于SolidCAM的模具型腔HSM加工研究
SolidCAM 高速铣削(HSM)策略

世界独一无二的高速铣削HSM模块-完全集成于SolidWorks中Solid CAM高速铣削(HSM)是一个非常强大的高速加工模块,经过市场验证其对于模具、工具、冲压模具和复杂3D零件高速加工非常有效,HSM 提供了独一无二的进给和快速走刀的高速轨迹。
SolidCAM高速铣削模块能够光顺切削和退刀路径,维持光顺连续的刀具运动轨迹以满足高速加工中维持高速进给和避免停顿的需求。
在SolidCAM HSM模块中以最小的Z高度退刀,连刀也可以产生倾斜角度、圆弧光顺和尽可能的低退刀——这样有效减少了空切和加工时间。
高速铣削能够产生高效、光滑、防止干涉的刀路轨迹,提高了曲面加工质量、减少刀具载荷、延长刀具和机床寿命。
如今对缩短产品生产周期、降低成本和提高质量的要求下,高速铣削成为加工车间必不可少的需求。
对所有高速切削能力有较高要求的用户来说,SolidCAM HSM模块是都是一个非常强大的解决方案!SolidCAM HSM 模块在多方面是对CAM技术的提升,使真正的高速铣削加工成为可能,高速铣削包括避免刀具路径尖角,使用具尽可能的与零件保持接触,优化空切运动减少空切产生光顺的进退刀。
任何3D高速铣削都能够控制曲面的曲率角度或者加工的边界范围,SolidCAM HSM模块提供了独一无二的边界创建工具,包括最大轮廓线,刀具切除区域边界,平缓区域边界,残料切削理论边界,残料边界和用户自定义边界。
对所有高速切削能力有较高要求的用户来说,SolidCAM HSM模块是都是一个非常强大的解决方案,他能够提高CNC机床的生产效率,减少空切、圆滑连接刀路并产生连续的刀具运动。
HSM 粗加工策略轮廓粗加工轮廓粗加工是高效地去除大量毛坯的有效加工策略。
根据指定的Z值深度自动产生一系列的路径偏移,并自动计算和最大限度地去除坯料。
切削深度可以自动变化保障在平缓的区域加工到位,螺旋下刀和轮廓倾斜下刀都被用来作为进刀模式,无论在不同的刀路之间还是快速连刀都可以自动产生光滑的圆弧,有效的避免刀具停顿、提高刀具进给速度、延长了刀具寿命。
第5章 HSM基础

SolidCAM HSM基础 HSM基础
高速切削加工技术是本世纪的一种先进制 造技术, 造技术,有着强大的生命力和广阔的应用 前景。 前景。 SolidCAM软件高速铣削模块(以下简称 软件高速铣削模块( 软件高速铣削模块 模块” “SolidCAM HSM模块”)在多方面是对 模块 CAM技术的提升,经过市场验证,它使注 技术的提升, 技术的提升 经过市场验证, 塑模具、冲压模具、工具和复杂3D零件 塑模具、冲压模具、工具和复杂 零件 等的真正高速铣削加工成为可能, 等的真正高速铣削加工成为可能, SolidCAM HSM模块提供了独特的加工策 模块提供了独特的加工策 符合现代制造业发展方向, 略,符合现代制造业发展方向,具有广阔 的应用前景。 的应用前景。
5.1 启动HSM操作 启动HSM操作
5.2 SolidCAM HSM 操作界面
SolidCAM HSM加工流程 HSM加工流程
策略定义 几何定义
刀具定义边界Biblioteka 义路径参数定义连接定义
辅助参数定义
5.3 参数和数值
SolidCAM HSM模块中所涉及到的大部分参 模块中所涉及到的大部分参 数都有默认值。 数都有默认值。 每个参数编辑框中, 提供了菜单, 每个参数编辑框中,SolidCAM提供了菜单, 提供了菜单 只需在编辑框中单击鼠标右键即可。 只需在编辑框中单击鼠标右键即可。
The End
HSM与EDM在模具加工中的应用比较

H M 与 E M 在 模 具 加 工 中 的应 用 比较 S D
汪通 悦
( 阴 工 学 院 机 械 工 程 系 江 苏 淮 安 23 0 ) 淮 20 2
摘
要: 介绍了高速加工技术 的起源及 主要优点 , 并根据高速 加工 和电火 花加工特 点 , 二者进 行 了比较 , 对 找出 了各 自的
H M) 以迅 速 发展 并 逐 步推 广 应 用 , 速加 工能 S 得 高
主要 加 工方 法 甚 至 是 唯 一 加 工 方 法 , 模 具 制 造 在
范围内, 因任何 刀 具都 无 法 承 受 太 高 的切 削温 度 , 切 削加工 不可 能进 行 。但 当切 削速 度 超 过 这个 范
中应用 非常 广泛 。如美 国的各种 模具 ,0 都要 用 9% 到电火 花加 工方 法制 造 。
H SM . EDM n M o d & Di a h n n Vs i l eM c ii g
W ANG n — u To g —y e
( e at e t f e hncl n ier g H a i Istt o eh ooy u i ins 2 0 2 C ia D pr n o c aia E gn e n , u i n ntue f c nl ,H aa J gu2 3 0 , hn ) m M i y i T g n a
A src : hs a e t d csteo g n a r rso S bta tT i p p r nr u e h r i a dm j i fH M.B sdo ec aat s c f S n i o i n o me t ae nt hrce t so M a d h i r i H
维普资讯
SolidCAM高效加工解决方案

SolidCAM高效加工解决方案SolidCAM是一种高效的加工解决方案,它结合了SolidWorks CAD软件的功能和CAM模块,为制造业提供了全面的解决方案。
SolidCAM具有智能化的特点,可以帮助用户在短时间内完成复杂的加工任务。
SolidCAM的核心功能包括自动化编程、高速铣削、车削、线切割、多轴加工和模具加工等。
通过这些功能,SolidCAM可以实现高效的加工过程,提高生产效率和产品质量。
自动化编程是SolidCAM的一大特点,它可以根据用户提供的CAD模型自动生成加工路径和刀具路径。
用户只需输入加工参数和工艺要求,SolidCAM就可以自动进行编程,并生成相应的G代码。
这样,用户可以省去繁琐的手工编程过程,节省了大量的时间和精力。
高速铣削是SolidCAM的另一个重要功能。
它采用了先进的刀具路径优化算法,可以实现高速、高效的铣削加工。
通过合理的刀具路径规划和切削参数设置,SolidCAM可以最大限度地提高切削效率,减少刀具磨损和加工时间。
车削功能是SolidCAM的另一个亮点。
它可以实现多种车削加工,包括外圆车削、内圆车削、螺纹车削等。
通过智能的刀具路径规划和切削参数设置,SolidCAM可以实现高精度、高效率的车削加工,提高产品的加工质量和生产效率。
线切割是SolidCAM的又一重要功能。
它可以实现复杂形状的零件加工,如模具、模型等。
通过先进的刀具路径规划算法和切削参数设置,SolidCAM可以实现高精度、高效率的线切割加工,提高产品的加工质量和生产效率。
多轴加工是SolidCAM的又一亮点。
它可以实现多轴联动的加工,如五轴加工、倾斜切削等。
通过智能的刀具路径规划和切削参数设置,SolidCAM可以实现复杂形状的零件加工,提高产品的加工质量和生产效率。
模具加工是SolidCAM的又一重要功能。
它可以实现模具的设计、加工和制造。
通过SolidCAM的模具加工功能,用户可以快速设计和加工各种复杂的模具,提高产品的加工质量和生产效率。
成为制造业的完整cam解决方案服务商

产品评论 | Products View成为制造业的完整CAM 解决方案服务商SolidCAM 中国区经理张朝安老总评论更务SS 彩it 扫描二维码过去大多数制造企业将更多关注点放在硬件设备, 以SolidCAM 的客户为例,他们会选择性能好且功能多样化的机床设备,例如多轴加工中心和多功能的车铳 复合加工中心,而选择对CAM 软件投入更多关注的企业相对较少。
但近年来SolidCAM 中国区经理张朝安先生发现,越来越多与SolidCAM 合作的企业开始增加 对于工业软件的投入,其中中小型企业的力度很大。
情 况发生变化的原因在于,这些企业已经逐渐意识到工业软件也可以为他们带来效益。
例如CAM 软件就可以 帮助客户更好地实现多功能加工机床的使用价值,一位 SolidCAM 的客户曾表达过:SolidCAM 的软件性能超出了他们之前的预期,它所带来的价值体验是客户使用功能强大的CAM 软件所在。
所以张朝安先生始终认为, 当整个制造业都认识到工业软件的重要价值并全面使用工业软件的时候,工业化进程基本完成。
工业软件的发展一定是根据制造业的发展而定,当然时代在变化,工 业软件也一定会变化,而工业软件也将会成为物联网中的支柱软件之一。
现在的产品类型多样,其生产周期不断加快,为了更好地面对产品多样化和人工成本上升等问题,工业 软件的使用简单化及强大功能,就显得尤为重要,正如 SolidCAM 的iMachining 自适应加工模块,客户在使用时,只需淞酥材槿数等,软件就可以自动根据产 品生成加工程式对设备发出指令,并且能够节省多达70% 的开粗加工时间,所以工业软件是实现无纸化工厂及无人化智能车间必不可少的条件之一。
正因为客户的需求标准 不断提升,工业软件为了满足客户的要求,相关企业必须 研发出功能更强大的软件以支持®造业的发展,而在现代 制造业面临巨対兆战时,ZDL1漱件也正在变得越来越重要。
无缝集成主流计算机辅助设计(CAD )软件SolidCAM 中国区技术经理陆清洋先生以 SolidCAM 软件为例讲述了工业软件的重要性。
基于SolidCAM的模具型腔HSM加工研究

基于SolidCAM的模具型腔HSM加工研究作者:常虹,黄丽来源:《科技创业月刊》 2017年第5期常虹,黄丽(武昌工学院湖北武汉430065)摘要:在分析模具制造现状的基础上,结合绿色制造的发展需求,提出将高速切削加工技术应用于模具制造,并以汽车配件模具型腔为例,采用SolidCAM软件对模具的高速切削加工方式展开研究。
关键词:SolidCAM;模具;HSM;绿色制造中图分类号:TG76文献标识码:Adoi:10.3969/j.issn.1665-2272.2017.05.043在现代工业生产中,模具是制造业重要的基础工艺装备,许多新产品的开发和生产都依赖于模具,大部分模具都是依靠特定的三维模具型腔使材料成型。
模具型腔一般尺寸精度和表面粗糙度要求较高,材料硬度较大,零件结构较复杂且多为单件小批量生产,造价昂贵,制造过程复杂,通常采用数控铣削、磨削、电火花等方式加工。
这种传统的模具加工方式制造周期长,工艺落后,生产效率较低,对生态环境造成的负面影响大,在现代制造业倡导绿色制造理念的背景下,难以满足时代的发展要求,因此,将绿色环保的先进制造技术应用于模具生产显得尤为重要。
HSM(high-speedmachining)即高速切削加工,是20世纪90年代迅速发展起来的先进加工技术,通常切削速度超过传统切削速度5~10倍,主轴转速一般在10000~20000r/min以上,进给速度一般在15~50m/min。
高速切削技术的应用可以解决高硬度模具材料的加工问题,适合表面质量高、精度高、形状复杂的模具加工,减少和避免使用加工效率低的电火花加工。
结合使用数控机床,采用数控高速复合加工,减少装夹的次数,避免重复定位产生的加工误差,表面加工精度可以达到1μm,在提高模具加工质量的同时,也提高了生产效率。
高速切削技术的应用简化了传统模具加工所采用的抛光工序,节约了70%左右的手工研磨工时,降低了30%左右的加工成本。
SolidCAM使用说明
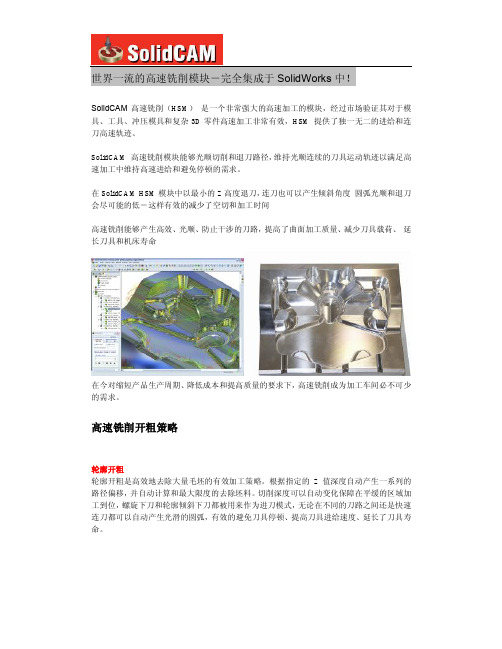
世界一流的高速铣削模块-完全集成于SolidWorks中!SolidCAM高速铣削(HSM)是一个非常强大的高速加工的模块,经过市场验证其对于模具、工具、冲压模具和复杂3D零件高速加工非常有效,HSM 提供了独一无二的进给和连刀高速轨迹。
SolidCAM 高速铣削模块能够光顺切削和退刀路径,维持光顺连续的刀具运动轨迹以满足高速加工中维持高速进给和避免停顿的需求。
在SolidCAM HSM模块中以最小的Z高度退刀,连刀也可以产生倾斜角度圆弧光顺和退刀会尽可能的低-这样有效的减少了空切和加工时间高速铣削能够产生高效、光顺、防止干涉的刀路,提高了曲面加工质量、减少刀具载荷、延长刀具和机床寿命在今对缩短产品生产周期、降低成本和提高质量的要求下,高速铣削成为加工车间必不可少的需求。
高速铣削开粗策略轮廓开粗轮廓开粗是高效地去除大量毛坯的有效加工策略。
根据指定的Z值深度自动产生一系列的路径偏移,并自动计算和最大限度的去除坯料。
切削深度可以自动变化保障在平缓的区域加工到位,螺旋下刀和轮廓倾斜下刀都被用来作为进刀模式,无论在不同的刀路之间还是快速连刀都可以自动产生光滑的圆弧,有效的避免刀具停顿、提高刀具进给速度、延长了刀具寿命。
型芯开粗型芯开粗是从外部加工型芯的优化加工策略,他不是在零件的内部产生特定宽度的切削,所有的刀具路径起始点都是从外部开始,通过给定的切削深度工作在外部轮廓和型芯之间。
如果一个零件既有型芯又有型腔则SolidCAM会自动在一个程序中转换型芯粗加工和型腔粗加工,刀具连接能够最大限度的减少刀具磨损。
残料开粗残料开粗是通过一个较小的刀具工作在之前较大的刀具之后的加工策略,在之前的操作中,有一些刀具没有加工到位的地方,SolidCAM 高速铣削模块能够更新毛坯模型并避免空切,对于大零件您可以通过减小刀具尺寸进行多次残料二次开粗操作。
残料开粗也可以用在铸造零件上以减少切削路径行数,得到相应的毛坯公差。
型腔模具加工工艺设计

对称中心的位置尺寸为± .4t 沟槽及型腔表面粗 0 0 m, x
糙度 值为 R 04 m, 中 型 腔 壁 部 圆 角 半 度 1 2 m, 具几何 形 状不 受 限 0~ 0 模 制 , 工槽 深取决 于 电极 的制 造 , 加工效 率低 。由此 加 但
明: 合理运 用 HS 铣 削加 工与 E M 放 电加 工可 以提 高加工 质量 和生产 率 。 M D
关键词 : 高速 铣削 电火 花N - 模具 型腔 工 艺设计 r
T c n lgc D sg o r c s ig M o l vt e h oo i e in f rP o e sn ud Ca i y
腔 模具加 工 的主要手 段 , 以典 型零件 为例 , 现 分析选 择
必 须 由电火花 加工完 成 。高速 铣削可 以为 电火花加 工 去 除更 多的加 工余 量 , 使放 电加 工 时 电极 与工 件 的加
加 工方法 的影 响 因素 , 究 型 腔模 具 加 工 工 艺设 计 方 研
工 面均匀 放 电 , 电极损 耗均 匀 , 而 提高 加工 效率 。因 从 此, 综合运 用 H M 与 E M 进行 型腔模 具 的加工 , 必 S D 是
a d Elcrct e h oo y, u u 2 0 0, n e tiiy T c n l g W h 41 0 CHN;
@Wu uB saM udC . t. Wu u2 10 , HN) h od o l o ,Ld , h 4 0 0 C
Absr c :Ba e n t n tn e o r c s i g a mo l a ta d t e c a a trsi fa p y n M n ta t s d o he i sa c fp o e sn u d p r n h h r ce itc o p l i g HS a d EDM o t p o e smo l a i r c s u d c v t h sp pe x o n e hemeh d a nay e h e hnqu ftc n lg c d sg y,ti a re p u d d t t o nd a ls d t e tc i eo e h oo i e in
基于MasterCAM和UG的注塑模流道数控加工技术研究

m e t
ho ds lo
s e
te
hn iq
a
u e s
to
de
ta
ile d
po
s
itio
e
.
In p a r tic
,
u
la
,
the
M a s t e r CA M
r
,
f CA D
o w
a n
d CA M fu
t
n c
in
c
c o o r
din
t io
v e
n
,
w
hile
c o n ta c t c
在
Ma
s
te r
CA M
,
、
数控编程 软件
, ,
我 国模 具 加 工 厂 家 绝 大 多 数 是 三 轴 数 控
M a s t e r C A M UG
、
等软 件 中 很 难 创 建 与相 应 流道 截 面
,
一
致 的成 形 刀 即
鉴 于此 编程 时
,
机 床 因 此 本 文从
l
的 三 轴 数控 加 工 角 度
。
使 勉 强 创 建 出来 刀 路 也 很 难 运 算 出来 往 往 使 用 骗 刀 法 即用 直 径 为
,
,
。
( 其 它 软 件 类 同 )对 流 道 的 加 工 工 艺 及 方 法 进 行 论 述
Om
m
或
0 1m
.
m
的球 刀 代替
,
流 道 加 工 的工 艺 分 析 流 道 分 为两 种
面 上 流道 ( 即
基于HSM与EDM的模具型腔加工研究
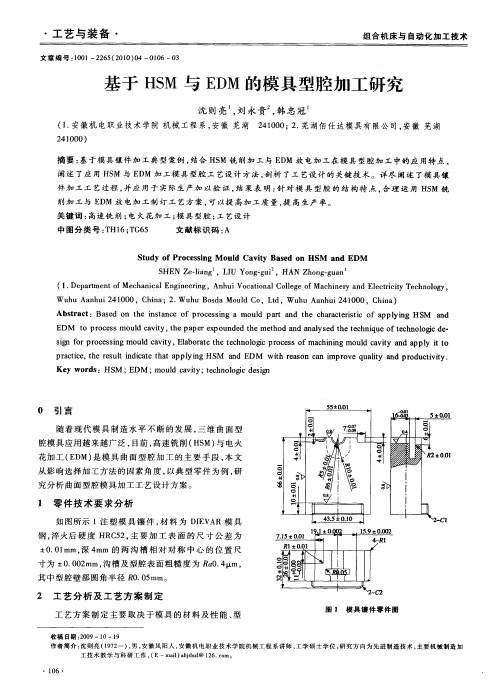
工 艺 与装 备 ・
组合机床与自 动化加工技术
文章 编 号 :0 1 2 5 2 1 )4—00 0 10 —26 (0 0 0 16— 3
基 于 H M 与 E M 的 具 型腔 加 工 研 究 S D 模
沈 则 亮 刘 永贵 韩 忠 冠 ,
,
(. 1 安徽机 电职业技 术 学院 机 械 工程 系 , 徽 安 芜湖
花 加工 ( D 是模 具 曲面型 腔 加 工 的 主要 手 段 , 文 E M) 本 从影 响选 择加 工方法 的 因素角 度 曲面型 腔模具 加工 工艺设 计方 案 。
l 零 件 技 术 要 求 分 析
如 图所 示 I注 塑 模 具 镶 件 , 料 为 D E A 材 IV R模 具 钢, 淬火后 硬 度 HR 5 , 要 加 工 表 面 的 尺 寸 公 差 为 C2 主 4 . 1 i, 4 m 的 两 沟 槽 相 对 对 称 中心 的 位 置 尺 - 0 ml 深 m 0 l 寸为 4 .0 m 沟槽及 型腔 表面 粗糙 度 为 R O 4 - 0 2 m, 0 a . m,
其 中型腔壁部 圆角半径 R .5 0 0 mm。
2 工 艺分 析 及 工艺 方 案 制 定
工 艺方 案 制 定 主要 取 决 于模 具 的材 料及 性 能 、 型
收稿 日期 :0 9—1 20 0—1 9
图 1 模具镶件零件图
作者 简 介 : 则 亮 ( 9 2 ) 男 , 徽 凤 阳人 , 徽 机 电 职 业技 术 学 院 机 械 工 程 系 讲 师 , 学 硕 士 学 位 , 究 方 向为 先 进 制造 技 术 , 要 机 械 制 造 加 沈 17 一 , 安 安 工 研 主 工 技 术 教学 与科 研 工 作 , E— i)hdz 16 cm。 ( ma ajsl 2 .o l @
一种型腔零件的建模及数控仿真加工
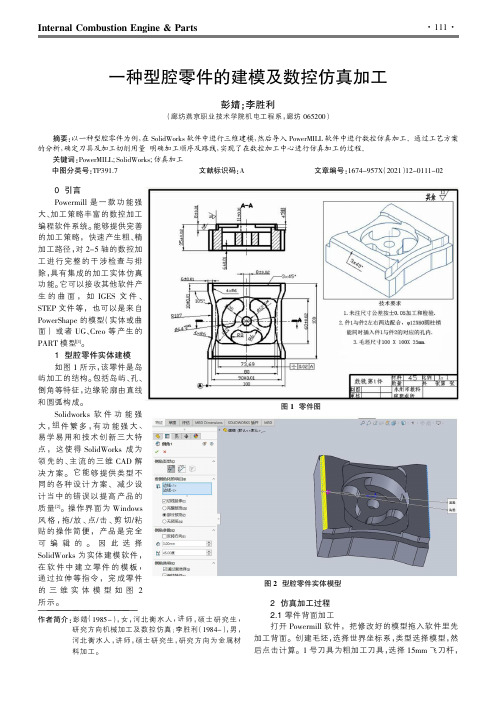
是一款功能强加工策略丰富的数控加工能够提供完善精
轴的数控加工进行完整的干涉检查与排具有集成的加工实体仿真
它可以接收其他软件产、文件等,也可以是来自(实体或曲等产生的该零件是岛
孔、
边缘轮廓由直线有功能强大、为实体建模软件,在软件中建立零件的模板,2仿真加工过程2.1零件背面加工
打开Powermill 软件,把修改好的模型拖入软件里先
加工背面。
创建毛坯,选择世界坐标系,类型选择模型,然
后点击计算。
1号刀具为粗加工刀具,选择15mm 飞刀杆,
河北衡水人,讲师,硕士研究生,
研究方向机械加工及数控仿真;李胜利(1984-),男,
硕士研究生,研究方向为金属材图1零件图
图2型腔零件实体模型
加工方式为偏移所有设置参数[3],点击确定生成粗加工刀路的模型区域清除。
精加工刀具选择直径6mm立铣刀,设置坐标系后应用等高精加工方式,选择排序方式为区域,点击确定生成精加工刀路如图3所示,保存背面加工。
零件正面加工
再次打开软件,把修改的模型拖入准备加工工件正首先计算毛坯,设置模型区域清除参数,生成粗加工
粗加工孔选用11cm钻头加工中间孔,生成钻孔程软件中完成了该类零件仿真模拟加工。
实际生产中,
机床上加工此种零件,要选择合理正确的加工中心设备,用有效的夹具和装夹的方法,制定了合适的工艺路线,
完成标准的零件,满足设计需求。
参考文献:
[1]高晓丽,苑妮,郑家铮.使用PowerMill对复杂加工件进行CAM设计[J].模具制造,2019,19(04):75-78.
[2]鲍仲辅,吴任和.Solidworks项目教程[M].北京:
图3背面等高精加工图4正面精加工。
高热导率热冲压模具钢HSM的组织与性能

高热导率热冲压模具钢HSM的组织与性能摘要:本文主要介绍了高热导率热冲压模具钢HSM的组织与性能。
该钢具有高的热导率和优良的强度和延展性能,因此被广泛应用于汽车、家电、通讯等行业中的高精度冲压模具制造。
本文首先简要介绍了HSM的化学成分、热处理工艺,然后详细分析其组织变化规律和力学性能指标。
最后,结合应用实例,评价了HSM在实际应用中的优点和不足,为模具制造企业的决策提供参考和借鉴。
关键词:高热导率;热冲压模具;组织;性能正文:一、引言热冲压模具钢是冲压模具中的一种重要材料,其组织和性能直接影响到模具寿命和加工效率。
因此,在模具制造中,不断地开发具有高强度、高耐磨性、高热导率的模具钢材,逐渐成为模具钢材的重要方向之一。
其中,高热导率热冲压模具钢(HSM)因其具有高的热导率和优良的强度和延展性能,被广泛应用于汽车、家电、通讯等行业中的高精度冲压模具制造。
二、HSM的组成和热处理HSM的化学成分:C 0.36-0.44、Si 0.10-0.60、Mn 0.40-0.90、Cr 1.60-2.20、Mo 0.30-0.60、Ni ≤ 0.30、V ≤ 0.10、Cu ≤ 0.25、Al ≤ 1.50、B ≤ 0.005、N ≤ 0.015、P ≤ 0.030、S ≤ 0.030。
HSM热处理工艺:淬火温度980-1020℃、保温时间10-20min/mm,水冷;回火温度520-560℃,保温时间2-4h,然后空冷。
三、HSM的组织变化规律在热处理过程中,HSM的显微组织发生了明显的变化,主要包括贝氏体和马氏体的变化。
在淬火过程中,钢材中的贝氏体比例逐渐增加,同时马氏体也不断地形成。
在回火过程中,贝氏体开始发生分解,生成少量的回火马氏体和残留的贝氏体,从而提高了模具钢材的强度和韧性。
四、HSM的力学性能HSM的力学性能中,最重要的是其高热导率。
该材料的热导率在任何温度下都高于普通的模具钢,因此在高温环境下,HSM的变形能力以及其它性能指标均得到了有效的保障。
SolidCAM高效加工解决方案

SolidCAM高效加工解决方案SolidCAM是一款基于SolidWorks的CAM软件,为创造业提供高效的加工解决方案。
它通过与SolidWorks的无缝集成,实现了CAD和CAM的高度协同,为用户提供了一种更加高效、智能的加工方式。
SolidCAM的特点和优势:1. 全集成的CAD/CAM解决方案:SolidCAM与SolidWorks无缝集成,使得用户可以在SolidWorks的界面上进行加工操作,无需切换软件,大大提高了工作效率。
2. 全面的加工功能:SolidCAM提供了多种加工功能,包括铣削、车削、铣削车削组合、线切割、线切割车削组合等,满足了不同加工需求。
3. 强大的刀具路径生成能力:SolidCAM采用了先进的刀具路径生成算法,能够自动生成高效、安全的刀具路径,减少了加工时间和刀具磨损。
4. 智能化的加工策略:SolidCAM内置了智能化的加工策略,根据不同的材料和零件特点,自动选择最佳的加工策略,提高了加工效率和质量。
5. 高精度的仿真和验证:SolidCAM提供了强大的仿真和验证功能,可以在加工前对刀具路径进行仿真,减少了碰撞和误差的风险。
6. 灵便的后期处理功能:SolidCAM支持多种后期处理功能,包括刀具修复、刀具路径优化、加工参数调整等,匡助用户进一步提高加工效率和质量。
7. 全面的技术支持和培训:SolidCAM提供全面的技术支持和培训服务,匡助用户快速上手并充分发挥软件的优势。
实际案例:某汽车零部件创造企业使用SolidCAM进行加工,通过SolidCAM的智能化加工策略,将加工时间缩短了30%,大大提高了生产效率。
同时,通过SolidCAM的仿真功能,减少了碰撞和误差的风险,保证了加工质量。
此外,SolidCAM的后期处理功能匡助企业进一步优化刀具路径,减少了刀具磨损,降低了生产成本。
总结:SolidCAM作为一款高效加工解决方案,通过与SolidWorks的无缝集成,提供了全集成的CAD/CAM解决方案。
HSM加工策略

精加工策略
高速加工相等的Z加工(Constant Z machining) 高速加工螺旋加工(Helical machining) 高速加工水平加工(Horizontal machining) 高速加工直线加工(Linear machining) 高速加工射线加工(Radial machining) 高速加工螺旋加工(Spiral machining) 高速加工变体加工(Morphed machining) 高速加工等距加工(Offset cutting) 高速加工边界加工(Boundary machining) 高速加工残余材料加工(Rest machining) 高速加工3D相等宽度加工(3D Constant step over) 高速加工清角加工(Pencil milling) 高速加工平行清角加工(Parallel pencil milling) 高速加工3D拐角平移加工(3D Corner offset) 组合等高加工(Combined strategies)包括:
6.13 高速加工残余材料加工
在半精加工或精加工之后再对前一把刀具未 加工加工
高速加工3D相等宽度加工,即3D等步距精加工是根 据模型产生3D等步距刀具路径的一种加工策略,此 策略产生的刀具路径是沿曲面等步距路径。该策略 非常适合根据边界在模型曲面上产生3D等步距路径 的精加工情况。
6.3 高速加工残余材料粗加工
SolidCAM高效加工解决方案--iMachining解读
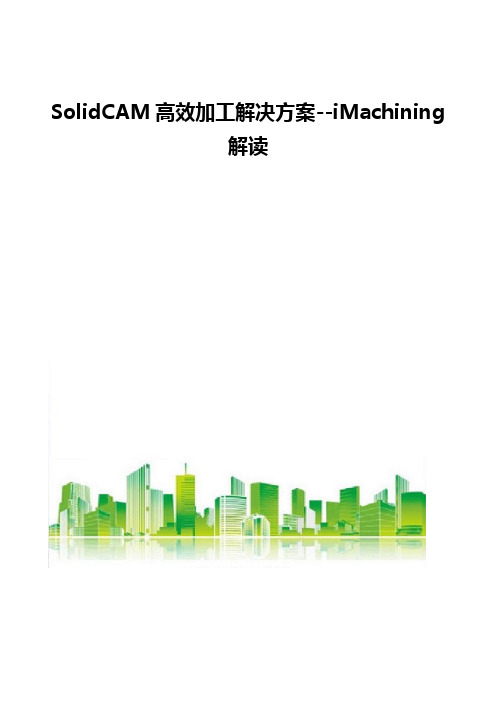
SolidCAM高效加工解决方案--iMachining解读在传统的深切削慢进给加工策略中,由于采用较大的切削深度所以刀具、机床受载荷比较高;较慢的进给速度造成排屑不容易,加工缓慢;所以整体加工效率比较低。
在HSM高速加工中,通常都是以小的切深、大的进给进行加工,就是我们平时所说的小吃快进,HSM可以缩短生产的周期,但是单个加工工序的时间并没有缩短。
iMachining高效加工策略(HPC)可以实现大切深、大进给进行加工,并且可以实现动态调整。
使用iMachining不仅可以缩短我们生产的周期,而且单个工序的加工时间也得到了大幅度的缩短。
高效加工(HPC)与高速加工(HSC)不同的是,他并不只限于提高切削速度和进给速度,而是把优化材料切除率放在首位,旨在通过提高单位时间的材料切除量和降低加工时间(基本时间和辅助时间)来进一步低加工费用。
iMachining生成的所有刀路轨迹都是通过接触角来计算,接触角是指当刀具旋转轴为Z方向时,根据刀具和毛坯材料接触圆弧大小来定义接触角度,刀具会严格按照这个角度进行切削,不会超过我们设定的最大切削角。
这种方式与我们之前定义的“行间距”有很大的不同,接触角方式可以使每次切削的毛坯更加的均匀(如图1所示)。
并且所生成的路径步距是不恒定的。
也就是说是以变化的路径步距进行加工。
可以根据我们目标零件的形状自动产生摆线与螺旋组合的刀路轨迹。
高的进给速度可以根据接触角的改变进行动态的调整;并且通过进给速度的调整和优化,保证了大切削深度的安全性。
图1众所周知,在实际加工过程中为了在局部区域内保证最短时间完成加工,通常会使用螺旋的方式来完成切削,这些区域大多是没有加工到的地方,显然摆线加工的方式最为适用。
摆线式高速加工过程中,刀具处于动态的全方位切削,刀体沿周边受力均匀,因此,刀具疲劳破坏的可能性就非常小;刀具向前切削材料也伴随着向后的空走刀,这样刀具有充分的时间冷却,同时,还能自动带走切屑,从而大大改善切削条件,而且摆线刀路可以避免刀具被工件材料包埋时的情况发生,但是摆线方式会延长加工时间,在整个摆线过程中大约会有30%到50%的时间是不切削的,所以为了即提高加工效率又缩短加工时间,iMachining 提供了摆线与螺旋相组合的刀具路径解决方案。
型腔模具加工工艺设计范文

型腔模具加工工艺设计沈则亮①刘永贵②韩忠冠①(①安徽机电职业技术学院机械工程系,安徽芜湖;②芜湖佰仕达模具有限公司,安徽芜湖)摘要:基于模具镶件加工实例,结合HSM铣削加工与EDM放电加工在模具型腔加工中的应用特点,阐述了应用HSM与EDM加工模具型腔工艺设计方法。
剖析了工艺设计的关键技术。
实际生产结果表明:合理运用HSM铣削加工与EDM放电加工可以提高加工质量和生产率。
关键词:高速铣削电火花加工模具型腔工艺设计Technologic Design for Processing Mould CavitySHEN ZeliangⅢ,LIU Yonggui∞,HAN Zhongguan山((重)Department of Mechanical Engineering,Anhui V ocational College of Machineryand Electricity Technology,Wuhu 24 1000,CHN;(室)Wuhu Bosda Mould Co..Ltd.。
Wuhu 。
CHN)Abstract:Based on the instance of processing a mould part and the characteristic of applying HSM and EDM toprocess mould cavity,this paper expounded the method and analysed the technique of technologic designfor processing mould cavity,the result indicate that applying HSM and EDM with reason can improvequality and productivity.Keywords:HSM;EDM;Mould Cavity;Technologic Design目前,高速铣削(HSM)与电火花加工(EDM)是型腔模具加工的主要手段,现以典型零件为例,分析选择加工方法的影响因素,研究型腔模具加工工艺设计方法,提出综合运用HSM与EDM的设计方案,提高加工质量与生产效率。
基于HSCAE和UG的滑盖注塑模设计
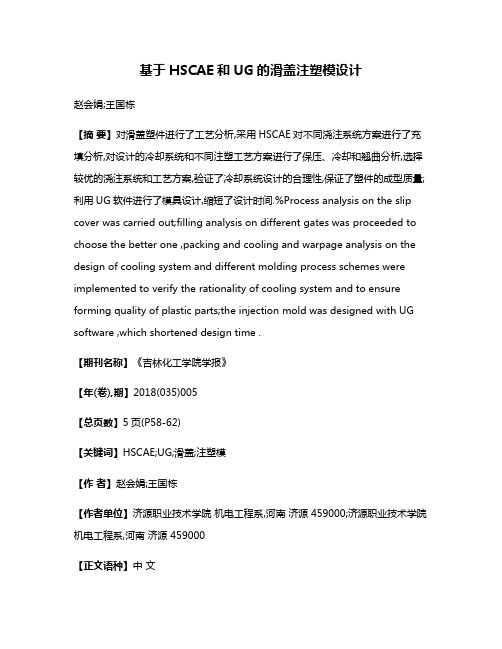
基于HSCAE和UG的滑盖注塑模设计赵会娟;王国栋【摘要】对滑盖塑件进行了工艺分析,采用HSCAE对不同浇注系统方案进行了充填分析,对设计的冷却系统和不同注塑工艺方案进行了保压、冷却和翘曲分析,选择较优的浇注系统和工艺方案,验证了冷却系统设计的合理性,保证了塑件的成型质量;利用UG软件进行了模具设计,缩短了设计时间.%Process analysis on the slip cover was carried out;filling analysis on different gates was proceeded to choose the better one ,packing and cooling and warpage analysis on the design of cooling system and different molding process schemes were implemented to verify the rationality of cooling system and to ensure forming quality of plastic parts;the injection mold was designed with UG software ,which shortened design time .【期刊名称】《吉林化工学院学报》【年(卷),期】2018(035)005【总页数】5页(P58-62)【关键词】HSCAE;UG;滑盖;注塑模【作者】赵会娟;王国栋【作者单位】济源职业技术学院机电工程系,河南济源 459000;济源职业技术学院机电工程系,河南济源 459000【正文语种】中文【中图分类】TQ320.662;TP391.72注塑件的成型品质受多种因素影响,塑件结构、材料、工艺参数、模具设计、工作环境、操作人员经验等这些主观和客观条件共同决定了其成型品质,尤其是厚壁塑件,受收缩和翘曲影响[1],根据经验设计出的模具往往要经过多次试模、修模方能生产出合格塑件,费时费力又增加模具成本.利用华塑CAE模流分析软件可以在模具设计和加工前根据拟定方案进行模拟,分析整个注射成型过程,预测熔体的充填、保压、冷却情况以及塑件中的应力分布、纤维取向、塑件收缩和翘曲变形等情况[2],根据分析结果进行工艺参数、浇注系统和冷却系统的优化设计,从而提高注塑件的成型质量,配合UG软件,可缩短模具开发时间和节约试模成本[3].1 塑件结构工艺性分析在UG软件中对滑盖进行造型,如图1所示.该塑件外形规则,但前后不对称,底部的水平舌形结构外侧及其上方两侧直壁开口处因冷却收缩受阻较小易产生大的翘曲变形,故选择合适的成型工艺参数及设计合理的冷却系统是确保塑件的形状和尺寸精度的关键;另外,底部的水平舌形结构会阻碍塑件沿开模方向顺利脱模,模具上必须设计侧向抽芯机构,抽芯距较大,该机构的设计是本副模具设计的难点.图1 滑盖塑件图2 原料及成型工艺参数选择该滑盖塑件要求外观色泽良好、尺寸精度较高(舌形部位要求MT3),同时应具备一定的强度和耐磨性.ABS无毒、无味,具有优良的综合物理和机械性能,耐磨性和尺寸稳定性好,收缩率较小(0.3%~0.8%),且价格便宜,能满足塑件的成型及使用要求,故选择注塑原料为ABS.因ABS吸湿大,注射前须预热至80°~90°干燥2以上;为保证塑件精度,模温40°~60°,熔体温度220°~240°,其余参数可通过HSCAE软件分析获得并经试模确定.3 模具结构设计3.1 浇注系统的设计CAE网络模型见图2.图2 CAE网格模型根据注射模具结构中选取分型面时应保证塑件质量且便于脱模的总原则[4],将分型面选在顶部大平板结构的下表面处.由于塑件批量大,精度要求高,型腔布局采用一模两腔,结合该塑件的结构特征,可采用的浇口形式有侧浇口,潜伏式浇口和点浇口.侧浇口浇注系统采用两板模结构,模具结构简单,成型塑件的适应性强,但塑件连同流道凝料一起,从同一分型面中取出,需人工切除;点浇口浇注系统采用三板模结构,进料位置灵活,塑件和流道凝料从不同的分型面取出,自动分离,但模具结构复杂,成本较高,且浇注系统较长[5].潜伏式浇口由点浇口演变而来,它兼具点浇口和侧浇口的优点,同等条件下,提高了模具精度、产品质量和生产效率,简化了模具结构,但潜伏式沿斜向进人型腔,因此加工较为困难.本文拟从侧浇口和潜伏式浇口两种方案中选定.在HSCAE网格管理器中对塑件的STL模型进行网格划分,边长3 m,生成的网格模型见图2.顶点数7 417,面片数14 830,配对率90.04%,符合CAE分析要求.设主流道长80 mm,小端直径3.5 mm,大端直径8 mm,分流道为圆形,直径6 mm,侧浇口矩形1.5 mm高×2 mm宽×3 mm长,潜伏式浇口进料口直径1.5 mm,锥角10°,倾斜角45°,见图3.图3 (1)侧浇口(2)潜伏式浇口在HSCAE中选取生产厂家Kumho Chemicals Inc的ABS 780,最大许可剪切应力0.3 MPa,最大许可剪切速率50 000/s.充填设计工艺条件选用软件数据库中推荐值,进行充填分析,V/P转换点处的分析结果见表1.表1 两种浇口充填分析结果中V/P转换点相关数据浇口形式V/P转换点时间/s充填体积/%压力/MPa锁模力/KN剪切力/MPa剪切速率/s侧浇口0.3199.0436.29124.681.88360841潜伏式浇口0.4299.1039.60126.141.73323116由表1可以看出,二者的时间和充填体积差别很小,潜伏式浇口虽然压力和锁模力略大,但浇口处剪切应力和剪切速率都略小于侧浇口,更有利于避免出现表面粗糙、起伏不平甚至熔体破裂现象,从而有利于提高塑件表面质量.综上所述,选用潜伏式浇口.3.2 侧向抽芯机构的设计斜导柱侧向分型与抽芯机构利用斜导柱把开模力传递给侧型芯或侧向成型块,使之产生侧向运动完成抽芯与分型动作,特点是结构紧凑、动作安全可靠、加工方便,是注射模侧向抽芯时最常用的机构,一般使用于抽芯力不大及抽芯距小于60~80 mm的场合[6].本塑件底部的水平舌形结构侧向开口,其抽芯距S比塑件上的侧凹的深度S1大2~3 mm[7],即35.4+(2~3)mm,取38 mm.故采用斜导柱抽芯机构.抽芯力Fc=chp(μcosα-sinα)=180×35.8×10(0.2×1-0)=12.89 kN其中c为侧型芯成型部分的截面平均周长(mm);h为侧型芯部分的高度(mm);p 为塑件对侧型芯的收缩应力,一般情况下模内冷却的塑件为8~12 MPa,取10 MPa;μ为塑料与模具钢摩擦系数,约为0.1~0.3,取0.2;α为侧型芯的脱模斜度和倾斜角,该塑件为0°[8].结合塑件的结构形状,将斜导柱安装在定模而滑块安装在动模.斜导柱倾斜角α=15°,抽芯时斜导柱所受弯曲力Fw=Fc/cosα=12.89/0.97=13.29 kN,其中α为斜导柱的倾斜角.侧型芯滑块受到脱模力的作用线与斜导柱中心线交点到斜导柱固定板间的距离Hw 为30 mm,查表得斜导柱直径25 mm[9].楔紧块的斜角α′=18°.侧滑块的抽芯距离采用两个限位螺钉来限位,利用UG NX的Moldwizard的滑块库中加载相应参数的斜导柱机构和螺钉标准件,如图4所示.图4 斜导柱侧抽机构3.3 冷却系统设计和工艺参数选择本塑件平均壁厚2.7 mm,直壁部分圆角处最大达4.12 mm,壁厚偏大,需要通过冷却系统来缩短成型周期;在冷却的过程中壁厚变化处尤其是直壁拐角部分可能会因为收缩不均匀而产生内应力,从而造成翘曲.模具冷却系统的设计和注塑工艺参数的选择直接影响塑件的质量和生产效率[10-12].考虑到该塑件的结构,并避免冷却系统与侧抽系统产生干涉,在HSCAE设计冷却系统如图5所示,设定模具材料P20,环境温度20 ℃,管道直径8 mm,冷却介质为水,温度25 ℃.注塑工艺参数方案一:设定注射时熔体温度230 ℃,模具温度40 ℃,单级保压,0~20 s内保压力为80%注射压力,顶出温度79 ℃,冷却时间为“系统优化,可顶出面积比95%”.分析结果如图6所示,出口水温比入口升高1.46 ℃,在5 ℃以内,冷却介质雷诺数10 155.0,达到较好的紊流度,以上两个结果参数表明冷却系统的设计较为合理;但冷却时间28.64 s,时间较长,且塑件上最大翘曲发生在舌形前端达8.25 mm,舌根部位变形最大4.47 mm,上表面角部变形最大约1.95 mm,显然不满足塑件的质量要求,须进一步优化.(a) 冷却介质温度(b) 冷却介质雷诺数(c) 冷却时间(d) 翘曲图5 注塑工艺参数方案一分析结果提高熔体温度和模具温度,降低充模压力和充模速率,能不同程度地减小塑件的残余应力,从而减小塑件的翘曲变形;延长塑件的冷却时间也可使塑件内应力减小[13];另外,由于初始方案中保压曲线是恒定的,致使浇口附近过保压而远端保压力不足,可试调整注塑成型工艺参数中的保压曲线来改善[14].调整注塑工艺参数到方案二:注射时熔体温度240 ℃,模具温度50 ℃;把保压时间从20 s缩短到8 s,单级保压改为二级保压,0~3 s内保压力为50%注射压力,4~8 s内保压力为30%;冷却条件设置中降低顶出温度70 ℃,冷却时间设定为“系统优化,可顶出面积比100%”.再次分析后发现,冷却介质雷诺数与方案一相同,但冷却介质出口温度比入口上升仅0.07 ℃,由于保压时间缩短,冷却时间变为18.59 s,比方案一减少了10.05 s;翘曲最大值降至0.3 mm效果非常显著,如图6所示.故采用注塑工艺方案二.(a) 冷却介质温度(b) 冷却时间(c) 翘曲图6 注塑工艺参数方案二分析结果图7 推杆推出机构3.4 推出机构设计常用的推出机构有推杆推出机构、推管推出机构和推件板推出机构以及多元推出机构.该塑件结构简单,壁厚偏大,虽然直壁部分高度稍大但且直壁部分设有适当的拔模斜度,ABS材料具有较好的弹性和韧性,结合前述注塑工艺条件中冷却时间为达到可顶出面积比100%,决定采用最简单的推杆顶出机构.直壁外侧顶杆直径Φ8 mm,内侧推杆直径Φ6 mm,每个塑件下推杆共16根,沿轮廓均匀分布,如图7所示.由于推出行程较大,本模具内采用推板导套和推板导柱对推出动作进行导向.3.5 模具工作原理利用UG NX的Moldwizard进行分模设计后,加载龙记LK_SG,CI型标准模架3 545,添加斜导柱侧滑块抽芯机构、冷却水路、顶杆、浇注系统等标准件,得到完整的模具,如图8所示.1.浇注系统凝料2.推杆3.拉料杆4.复位弹簧5.推杆固定板6.推板7.动模座板8.推板导柱9.推板导套 10.限位螺钉11.侧滑块+侧型芯12.唧嘴13.复位杆 14.斜导柱15.动模板导柱 16.楔紧块17.定模板 18.定模座板 19.浇口套 20.定位圈21.滑盖塑件 22.动模板图8 模具工作原理图模具的工作原理是:开模时,注塑机开合模机构带动动模从分型面处与定模分离向后运动,塑件包裹在型芯上,浇注系统凝料1在拉料杆3的作用下随动模一起后退;侧滑块11在斜导柱14的驱动下一边向后运动,一边带动侧型芯水平向外侧移动,直到限位螺钉10位置处,侧抽芯动作完成;动模部分继续后退到接触注塑机推杆时,模具的推出机构与注塑机推杆发生相对运动,推杆组2将塑件22从型芯中顶出,同时拉料杆3将浇注系统凝料与塑件在浇口处断开,塑料与凝料同时都推离分型面,实现了自动化生产.合模时,注塑机的开合模机构带动动模向前运动,当斜导柱进入侧滑块导柱孔时,驱动侧滑块带着侧型芯水平向内复位,复位杆13接触到定模侧分型面后被向后推动,带动推出机构复位直到模具闭合锁紧.4 结论利用HSCAE进行了浇注系统分析和保压、冷却、翘曲分析,选择了较优的浇注系统和注塑工艺参数以确保塑件成型质量满足要求,确定了所设计冷却系统的合理性;借助于UG NX软件的Moldwizard模块进行了滑盖塑件的注塑模设计,提高了模具设计效率.【相关文献】[1] 贺圣颜,楚纯朋,邓娇,等.基于CAE的厚壁塑件注塑工艺参数优化[J].中国塑料,2016,30(12):58-62[2] 赵会娟,李秀副,张军民,等.Moldflow翘曲分析在吹风机外壳成型优化中的应用[J].吉林化工学院学报,2016,33(7):30-34.[3] 李瑞垞.尾灯座注塑CAE分析与模具UG设计[J].塑料,2015,44(6):93-36.[4] 郭继祥,李会.注塑模具结构中的分型面设计[J].电加工与模具,2010(6):48-50,63.[5] 周铭杰,蔡菊.带点浇口转侧浇口浇注系统的注塑模设计[J].中国塑料,2012,26(7):101-104.[6] 李锦胜.端盖注射模侧向抽芯机构设计[J].模具制造,2017(7):44-46.[7] 李云义,赵利平,侯贤州,等.一种薄壁塑料铲侧向抽芯机构研究及模具设计[J].模具制造,2017(5):52-56.[8] 周登攀,李桂芹.塑料成型工艺与模具设计[M].北京:北京邮电大学出版社,2016.[9] 杨占尧.塑料成型工艺与模具设计[M].北京:航空工业出版社,2017.[10] 汤小东.基于CAE开口管件注塑模具冷却系统的研究与分析[J].塑料科技,2016,44(12):55-58.[11] 王蕾,孙育竹.CAE分析在注塑模具冷却系统设计中的应用[J].橡塑技术与装备(塑料),2016,42(6):106-107.[12] 张书魁,孙首群.汽车开关面板注射成型工艺参数优化[J].轻工机械,2016,34(1):9-13.[13] 熊毅.外壳注塑CAE工艺优化及模具CAD[J].塑料工业,2016,44(2):71-74,82.[14] 赵会娟.Moldflow在接油盒模具成型优化设计中的应用[J].吉林化工学院学报,2016,33(11):63-67.。
SolidCAM高效加工解决方案
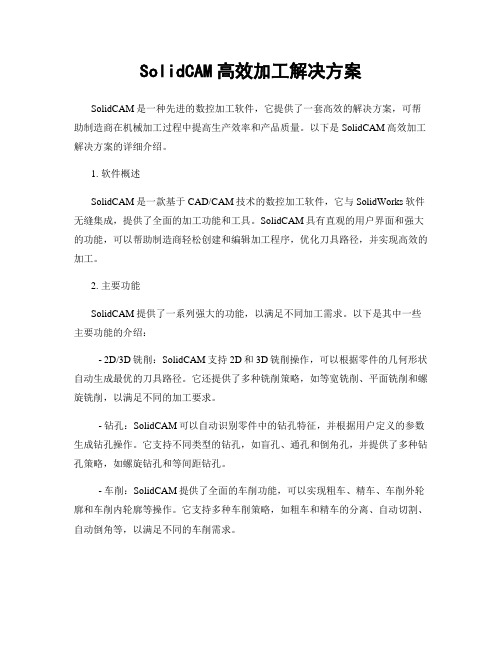
SolidCAM高效加工解决方案SolidCAM是一种先进的数控加工软件,它提供了一套高效的解决方案,可帮助制造商在机械加工过程中提高生产效率和产品质量。
以下是SolidCAM高效加工解决方案的详细介绍。
1. 软件概述SolidCAM是一款基于CAD/CAM技术的数控加工软件,它与SolidWorks软件无缝集成,提供了全面的加工功能和工具。
SolidCAM具有直观的用户界面和强大的功能,可以帮助制造商轻松创建和编辑加工程序,优化刀具路径,并实现高效的加工。
2. 主要功能SolidCAM提供了一系列强大的功能,以满足不同加工需求。
以下是其中一些主要功能的介绍:- 2D/3D铣削:SolidCAM支持2D和3D铣削操作,可以根据零件的几何形状自动生成最优的刀具路径。
它还提供了多种铣削策略,如等宽铣削、平面铣削和螺旋铣削,以满足不同的加工要求。
- 钻孔:SolidCAM可以自动识别零件中的钻孔特征,并根据用户定义的参数生成钻孔操作。
它支持不同类型的钻孔,如盲孔、通孔和倒角孔,并提供了多种钻孔策略,如螺旋钻孔和等间距钻孔。
- 车削:SolidCAM提供了全面的车削功能,可以实现粗车、精车、车削外轮廓和车削内轮廓等操作。
它支持多种车削策略,如粗车和精车的分离、自动切割、自动倒角等,以满足不同的车削需求。
- 五轴加工:SolidCAM具有强大的五轴加工功能,可以实现复杂零件的加工。
它支持多种五轴加工策略,如表面铣削、轮廓铣削和螺旋铣削,可以实现高效、精确的五轴加工。
3. 优势和特点SolidCAM的高效加工解决方案具有以下优势和特点:- 高度集成:SolidCAM与SolidWorks软件无缝集成,可以直接在SolidWorks 界面中进行加工操作,减少了学习和操作的难度。
- 智能化工具路径生成:SolidCAM可以根据零件的几何特征和加工要求自动生成最优的刀具路径,提高了加工效率和质量。
- 全面的加工策略:SolidCAM提供了多种加工策略,可以满足不同的加工需求,如铣削、钻孔和车削等。
hsm工艺技术

hsm工艺技术HSM(High Speed Machining)工艺技术是一种先进的数控加工技术,它以高速切削和高速进给为特点,可以大幅提高加工效率和加工精度。
下面我将详细介绍HSM工艺技术。
HSM工艺技术的特点在于高速切削。
相比传统的切削加工方式,HSM采用较高的切削速度,能够更快速地切削工件,提高加工效率。
同时,高速切削还可以减小切削力和切削温度,延长刀具寿命,提高切削精度。
HSM适用于各类工件的加工,如模具、航空航天零部件等。
HSM工艺技术的另一个特点是高速进给。
高速进给是指在相同时间内切削工件的距离更长,进给速度更快。
这样可以减小加工时间,提高生产效率。
同时,高速进给还可以减小切削力和切削温度,减少切削震动,提高切削质量。
HSM工艺技术中,通常采用大切削深度切削、斜角切削等方法,结合高速进给,可以得到优异的加工效果。
HSM工艺技术的实现离不开先进的数控系统和高精度机床。
数控系统通过预先输入加工参数和路径,自动控制刀具的切削速度和进给速度,确保加工精度和工件质量。
高精度机床具备高刚性和高稳定性,能够承受高速切削和高速进给带来的惯性力和振动,保证刀具和工件的稳定性。
HSM工艺技术的应用非常广泛。
在航空航天领域,HSM常被用于加工航空发动机零部件和飞机结构件,以满足轻量化和高强度的要求。
在汽车工业中,HSM可以用于加工发动机缸体、底盘结构件等。
在模具制造领域,HSM可以加工复杂的零件结构,提高生产效率和加工精度。
然而,HSM工艺技术也面临一些挑战。
首先,高速切削和高速进给带来的惯性力和振动会对切削质量产生影响,需要采取一些振动补偿措施。
其次,高速切削和高速进给要求刀具具备耐磨性和耐热性,需要使用高性能的刀具材料。
此外,HSM 工艺技术需要准确的切削参数和路径规划,对操作人员的技术要求也相对较高。
总结起来,HSM工艺技术以高速切削和高速进给为特点,可以大幅提高加工效率和加工精度。
它需要先进的数控系统和高精度机床的支持,广泛应用于航空航天、汽车、模具等行业。
- 1、下载文档前请自行甄别文档内容的完整性,平台不提供额外的编辑、内容补充、找答案等附加服务。
- 2、"仅部分预览"的文档,不可在线预览部分如存在完整性等问题,可反馈申请退款(可完整预览的文档不适用该条件!)。
- 3、如文档侵犯您的权益,请联系客服反馈,我们会尽快为您处理(人工客服工作时间:9:00-18:30)。
图 2 汽车配件凹模模型
传 统 的 模 具 型 腔 加 工 主 要 根 据 设 计 图 纸 ,采 用 数 控 机 床 、电火花及钳工抛光研配等方式制造,制造周期 长 ,模具生产的零件精度低。采用高速切削加工技术可 根据模具型腔设计要求选用经过淬硬的模具钢作为毛 坯 材 料 ,加工时采用立方氮化硼材料的刀片直接加工 零 件 的 模 具 钢 材 料 ,在 获 得 一 定 尺 寸 精 度 和 形 位 精 度 的 同 时 ,达 到 较 高 的 表 面 粗 糙 度 要 求 ,省 去 传 统 模 具 生 产 时 使 用 的 电 火 花 加 工 和 研 磨 、抛 光 加 工 等 工 序 ,简 化 了 加 工 工 艺 流 程 ,在 缩 短 模 具 制 造 周 期 的 同 时 ,提高 了模具加工精度。
程如图1 所示。
图 2 为用 Solidworks
建立的已经过完善的汽
车配件锻造凹模三维模
型 ,该模具型腔结构较简 单 ,几何形状较规则,力口
图 1 SolidCAM加工流程图
* 基金项 目 :湖北省教育厅科学技术研究计划指导性项目“计 算 机 辅 助 4C 系统在模具绿色制造领域的应用研究冶(项目编号:B2015274)
应用技术
基 于 S olidC A M 的模具型腔H S M 加工研究
常虹黄丽
(武 昌 工 学 院 湖 北 武 汉 430065)
摘 要 :在 分 析 模 具 制 造 现 状 的 基 础 上 ,结合绿色制造的发展需求,提出将高速切削加工技
术应用于模具制造,并以汽车配件模具型腔为例,采 用 SolidCAM软件对模具的高速切削加工方
式展开研究。
关键词:SolidCAM;模 具 ;HSM;绿色制造
中图分类号:TG76
文献标识码:A
doi:10.3969/j.issn,1665-2272.2017.05.043
在 现 代 工 业 生 产 中 ,模 具 是 制 造 业 重 要 的 基 础 工 艺 装 备 ,许多新产品的开发和生产都依赖于模具,大部 分 模 具 都 是 依 靠 特 定 的 三 维 模 具 型 腔 使 材 料 成 型 。模 具 型 腔 一 般 尺 寸 精 度 和 表 面 粗 糙 度 要 求 较 高 ,材 料 硬 度 较 大 ,零件结构较复杂且多为单件小批量生产,造价 昂贵 ,制造过程复杂,通常采用数控铣削、磨 削 、电火花 等方式加工。这种传统的模具加工方式制造周期长,工 艺 落 后 ,生产效率较低,对生态环境造成的负面影响 大 ,在现代制造业倡导绿色制造理念的背景下,难以满 足时代的发展要求,因此 ,将绿色环保的先进制造技术 应用于模具生产显得尤为重要。
收 稿 日 期 :2017-01-17
NO.5 PIONEERING W ITH SCIENCE & TEC H N O LO G Y M O N TH LY
2017 123
科技创业刊
PIONEERING WITH SCIENCES TECHNOLOGY MONTHLY
基 于 SolidCAM的模具型腔HSM加工研究
m 到 1滋 ,在提高模具加工质量的同时,也提高了生产效
率 。高速切削技术的应用简化了传统模具加工所采用 的抛光工序,节约了 70豫左右的手工研磨工时,降低了 30豫左右的加工成本。
采 用 数 控 机 床 加 工 模 具 时 ,高 速 加 工 切 削 速 度 很 大 ,背 吃 刀 量 很 小 ,在模具加工余量一定的情况下,必 须通过增加走刀次数才能完成加工,因 此 ,零件粗加工 和 半 精 加 工 编 程 的 计 算 量 大 大 增 加 ,加 之 模 具 型 腔 通 常 具 有 较 复 杂 的 曲 面 结 构 ,且 高 速 切 削 加 工 工 艺 要 求 *
严 格 ,需进行多种不同加工方案的对比分析,进一步增
加 了 数 控 编 程 的 工 作 量 ,致 使 模 具 高 速 加 工 难 以 用 手
工编程的方式实现数控程序的编写,必 须 借 助 CAD/ CAM技术进行模具加工的自动编程。
作 为 CAD/CAM —体化集成的SolidCAM软 件 ,以 插 件 的 形 式 实 现 与 SolidWorks软 件 无 缝 对 接 ,并且具 有 HSM高速加工方式,能够实现模具型腔高速铣削加
工时选择的毛坯形状为立方体,上 、下底面及周边已加 工 ,只需要加工模具型腔。
ห้องสมุดไป่ตู้
构 未 加 工 ,因此还需进行半精加工— 残余材料粗加 工 ,按加工模具型腔最小凹圆弧尺寸和最窄加工部位 的尺寸要求使用一把直径尽可能大的牛鼻刀进行铣 削 ,并为后续加工预留均勻的余量。残余材料粗加工的 走刀轨迹及加工后的轮廓如图4 所示。
并 生 成 刀 具 路 径 ,最 后 校 验 刀 具 路 径 ,检 查 走 刀 过 程 是
否会与工件、夹具产生干
涉 ,是否会产生过切和欠
切 现 象 ,经 过 修 改 ,模拟
加 工 确 认 无 误 后 ,将计算
出的刀轨按机床规定的
格 式 转 化 为 NC代码输 出保存。使 用 SolidCAM
软件进行模具加工的流
工 的 自 动 编 程 。首 先 根 据 加 工 零 件 的 结 构 和 技 术 要 求
设计模具,并 应 用 SolidWorks软件创建模具的三维造
型 ,然后在对模具模型进行分析的基础上,规划加工工
艺 路 线 和 制 定 加 工 工 艺 方 案 ,完 成 相 关 工 艺 卡 片 的 制
作 ,其次根据加工工艺分析的情况,对创建的模具CAD 模 型 作 适 合 于 CAM程 序 编 制 的 处 理 ,进一步完善模 型 ,接 着 利 用 SolidCAM插件设置加工参数,计算刀轨
HSM(high-speed machining)即高速切削加工,是
2 0 世 纪 9 0 年代迅速发展起来的先进加工技术,通常切 削 速 度 超 过 传 统 切 削 速 度 5耀1 0 倍 ,主轴转速一般在
10000~20000I■/min以上,进给速度一般在15~50m/min。
高速切削技术的应用可以解决高硬度模具材料的加工 问题 ,适合表面质量高、精 度 高 、形状复杂的模具加工, 减 少 和 避 免 使 用 加 工 效 率 低 的 电 火 花 加 工 。结合使 用 数 控 机 床 ,采用数 控 高 速 复 合 加 工 ,减 少 装 夹 的 次 数 , 避 免 重 复 定 位 产 生 的 加 工 误 差 ,表 面 加 工 精 度 可 以 达