Rotating compact objects with magnetic fields
电机英语词汇汇总

电机英语词汇汇总发电机通常由定子、转子、端盖及轴承等部件构成。
定子由定子铁芯、线包绕组、机座以及固定这些部分的其他结构件组成。
转子由转子铁芯(或磁极、磁扼)绕组、护环、中心环、滑环、风扇及转轴等部件组成。
由轴承及端盖将发电机的定子,转子连接组装起来,使转子能在定子中旋转,做切割磁力线的运动,从而产生感应电势,通过接线端子引出,接在回路中,便产生了电流。
Belt pulley 皮带轮stator 定子rotor 转子rotor core 转子铁芯stator core 定子铁芯induction motor 感应电动机winding 绕组solt 槽cast-aluminum rotor 铸铝转子insulation 绝缘ac motor 交流环电动机alloy 合金frequency 频率revolutions per minute 转/ 分motoring 电动机驱动generating 发电no-load 空载full load 满载staor winding 定子绕组full-load torque 满载转矩shunt 并励series 串励modulator 调制器overhauling 检修Polyphase 多相(的) polyphase rectifier 多相整流器shunt 分路器regulator 调节器rotor (stator) winding 转子(定子绕组)rheostat 变阻器subcompact 微型汽车armature coil 电枢线圈rotating commutator 旋转(整流子)换向器commutator-brush combination 换向器-电刷总线mechanical rectifier 机械式整流器dc motor 直流电动机de machine 直流电机time constant 时间常数polyphase rectifier 多相整流器boost 增压螺丝screw 螺杆screw螺母nut螺帽screw cap螺栓bolt螺钉boltsteel (St )铁不锈钢stainlesssteel(SS)Brass(Cu) Bras(Cu) 铜spring spr 弹簧connecting-rod (rod) 连接杆casting die 是用来压铸的摸具Die-Casting (noun) -既可以指过程(动词)也可以指结果self tapping screw 自攻丝Dynamic Balance 动平衡汽缸壁:casing wall 或cylinder wallfan motor 风扇电机electric motor type 电机型号ac motor 交流电动机armature coil 电枢线圈commutator-brush combination 换向器-电刷总线整理文本breakdown 故障brush 刷子,毛刷cable 电缆elastic ring 弹性圈gear 齿轮governor 调节器,调速器gripper 夹具装置jig 夹具joint 接头junction valve 连接阀load 载荷lubrication 润滑lubricating unit 润滑装置machine plane 机加工面main bearing 主轴承maker 生产厂家,制造厂商manhole lid 人行孔盖manifold 阀板molten metal 熔融金属CONTROL BLOCK 接线板Current dividing coil 线圈Ventilation filter 过滤器Steel tank 水箱air valve 气阀气孔air vent孔径bore diameter钻机boring machinering 环,圈支承环梁ring guarderrod 杆,棒弹簧垫spring pad弹簧钢丝spring wire弹簧垫圈spring washer焊接welding焊件weldment钢丝刷wire brush金属网wire net扳手wrench接线板terminal blockopen modeshaft 轴shaft-less 无轴承的电磁开关(Solenoid Switch)push-rod 推杆properalignment 同轴度traceability 可追溯性flywheel 飞轮suppliers 供应商精车fine turning 或finish turning 粗车rough turn精磨前轴凸模punch凸凹模punch-dier 焊接welding焊透complete penetrationcarbon electrode机加工machining多点焊机multiple spot welder 多站电焊机multi-operator welding set 套丝thread chaing 攻丝thread tapping攻丝机threading machine万能铣床niversal milling machine hobbing machine 钻床drilling machine 插床磷化phosphatingbearing cap 轴承drive cover 驱动端盖nameplate 铭牌armature 电枢axis 轴commutator 换向器induction machine 感应式电机horseshoe magnet 马蹄形磁铁magnetic field 磁场eddy current 涡流right-hand rule 右手定则left-hand rule 左手定则slip 转差率rotating magnetic field 旋转磁场induced current 感生电流time-phase 时间相位exciting voltage 励磁电压lamination 叠片laminated core 叠片铁芯short-circuiting ring 短路环squirrel cage 鼠笼bronze 青铜horsepower 马力random-wound 散绕end ring 端环coil winding 线圈绕组form-wound 模绕performa nee characteristic 工作特性per-unit value 标么值breakdown torque 极限转矩breakawayforce 起步阻力wind-driven generator 风动发电机number of poles 极数speed-torque curve 转速力矩特性曲线plugging 反向制动synchronous speed 同步转速percentage 百分数locked-rotor torque 锁定转子转矩prime mover 原动机inrush current 涌流magn etiz ing reaca nee 磁化电抗line-to-neutral 线与中性点间的leakage reacta nee 漏磁电抗iron-loss 铁损complex impedance 复数阻抗rotor resista nee 转子电阻leakage flux 漏磁通locked-rotor 锁定转子chopper circuit 斩波电路separatelyexcited 他励的compounded 复励speed regulation 速度调节armature circuit 电枢电路optical fiber 光纤interoffice 局间的waveguide 波导波导管bandwidth 带宽light emitting diode 发光二极管silica 硅石二氧化硅regeneration 再生, 后反馈放大coaxial 共轴的,同轴的high-performance 高性能的carrier 载波mature 成熟的Si ngle Side Ban d(SSB)单边带coupling capacitor 结合电容propagate 传导传播demodulator 解调器line trap 限波器Amplitude Modulation(AM 调幅Frequency ShiftKeying(FSK) 移频键控tuner 调谐器attenuate 衰减incident 入射的two-way configuration 二线制generator voltage 发电机电压dc generator 直流发电机boost 增压time constant 时间常数forward transfer function 正向传递函数error signal 误差信号stabilizing transformer 稳定变压器time delay 延时direct axis transient time constant 直轴瞬维修网变时间常数transient response 瞬态响应solid state 固体buck 补偿operational calculus 算符演算gain 增益pole 极点feedback signal 反馈信号dynamic response 动态响应voltage control system 电压控制系统mismatch 失配error detector 误差检测器excitation system 励磁系统field current 励磁电流transistor 晶体管high-gain 高增益boost-buck 升压去磁feedback system 反馈系统reactive power 无功功率feedback loop 反馈回路automatic Voltage regulator(AVR)自动电压调整器reference Voltage 基准电压magnetic amplifier 磁放大器amplidyne 微场扩流维修网发电机self-exciting 自励的limiter 限幅器manual control 手动控制block diagram 方框图linear zone 线性区power amplifier 功率放大器compound generator 复励发电机self —excitati on process 自励过程commutation condition 换向状况cumulatively compounded motor 积复励电动机operating condition 运行状态equivale nt T - circuit T 型等值电路winding loss 绕组(铜)损耗prime motor 原动机active component 有功分量reactive component 无功分量electromagnetictorque 电磁转矩retarding torque 制动转矩inductive component 感性(无功)分量armature m.m.f. wave 电枢磁势波Geometrical position 几何位置magnetic torque 电磁转矩spatial waveform 空间波形sinu soidal —den sity wave 正弦磁密度external armature circuit 电枢外电路instantaneouselectric power 瞬时电功率instantaneousmechanical power 瞬时机械功率effects of saturation 饱和效应reluctance 磁阻induction machine 感应式电机horseshoe magnet 马蹄形磁铁magnetic field 磁场eddy current 涡流right-hand rule 右手定则left-hand rule 左手定则slip 转差率induction motor 感应电动机rotating magnetic field 旋转磁场winding 绕组stator 定子rotor 转子induced current 感生电流time-phase 时间相位exciting voltage 励磁电压solt 槽lamination 叠片laminated core 叠片铁芯short-circuiting ring 短路环squirrel cage 鼠笼rotorcore 转子铁芯cast-aluminum rotor 铸铝转子bronze 青铜horsepower 马力random-wound 散绕insulation 绝缘ac motor 交流环电动机end ring 端环alloy 合金coil winding 线圈绕组form-wound 模绕performa nee characteristic 工作特性frequency 频率revolutions per minute 转/ 分motoring 电动机驱动generating 发电per-unit value 标么值breakdown torque 极限转矩breakawayforce 起步阻力overhauling 检修wind-driven generator 风动发电机revolutions per second 转/ 秒number of poles 极数speed-torque curve 转速力矩特性曲线plugging 反向制动synchronous speed 同步转速percentage 百分数locked-rotor torque 锁定转子转矩full-load torque 满载转矩prime mover 原动机inrush current 涌流magn etiz ing reaca nee 磁化电抗line-to-neutral 线与中性点间的staor winding 定子绕组leakage reaeta nee 漏磁电抗no-load 空载full load 满载Polyphase 多相(的) iron-loss 铁损eomplex impedanee 复数阻抗rotor resista nee 转子电阻leakage flux 漏磁通loeked-rotor 锁定转子ehopper eireuit 斩波电路separatelyexeited 他励的eompounded 复励demotor 直流电动机de maehine 直流电机speed regulation 速度调节shunt 并励series 串励armature eireuit 电枢电路optieal fiber 光纤interoffiee 局间的waveguide 波导波导管bandwidth 带宽light emitting diode 发光二极管silica 硅石二氧化硅regeneration 再生, 后反馈放大coaxial 共轴的,同轴的high-performance 高性能的carrier 载波mature 成熟的Si ngle Side Ban d(SSB)单边带coupling capacitor 结合电容propagate 传导传播modulator 调制器demodulator 解调器line trap 限波器shunt 分路器Amplitude Modulation(AM 调幅Frequency Shift Keying(FSK) 移频键控tuner 调谐器attenuate 衰减incident 入射的two-way configuration 二线制generator voltage 发电机电压dc generator 直流发电机polyphase rectifier 多相整流器boost 增压time constant 时间常数forward transfer function 正向传递函数error signal 误差信号regulator 调节器stabilizing transformer 稳定变压器time delay 延时direct axis transient time constant 直轴瞬维修网变时间常数transient response 瞬态响应solid state 固体buck 补偿operational calculus 算符演算gain 增益pole 极点feedback signal 反馈信号dynamic response 动态响应voltage control system 电压控制系统mismatch 失配error detector 误差检测器excitation system 励磁系统field current 励磁电流transistor 晶体管high-gain 高增益boost-buck 升压去磁feedback system 反馈系统reactive power 无功功率feedback loop 反馈回路automatic Voltage regulator(AVR)自动电压调整器reference Voltage 基准电压magnetic amplifier 磁放大器amplidyne 微场扩流发电机self-exciting 自励的limiter 限幅器manual control 手动控制block diagram 方框图linear zone 线性区power amplifier 功率放大器compound generator 复励发电机rheostat 变阻器self —excitati on process 自励过程commutation condition 换向状况cumulatively compounded motor 积复励电动机operating condition 运行状态equivale nt T - circuit T 型等值电路rotor (stator)winding 转子(定子绕组)winding loss 绕组(铜)损耗prime motor 原动机active component 有功分量reactive component 无功分量electromagnetictorque 电磁转矩retarding torque 制动转矩inductive component 感性(无功)分量abscissaaxis 横坐标induction generator 感应发电机synchronous generator 同步发电机automatic station 无人值守电站hydropower station 水电站process of self —excitation 自励过程auxiliary motor 辅助电动机technical specifications 技术条件voltage acrossthe terminals 端电压steady —state condition 瞬态暂态reactive in respect to 相对….呈感性active in respect to 相对….呈阻性synchronous condenser 同步进相(调相)机coincide in phase with 与… .同相synchronous reacta nee 同步电抗algebraic 代数的algorithmic 算法的biphase 双相的bilateral circuit 双向电路bimotored 双马达的corridor 通路shunt displacement current 旁路位移电流leakage 泄漏lightning shielding 避雷harmonic 谐波的potential transformer 电压互感器stabilization network 稳定网络stabilizer 稳定器air-gap flux 气隙磁通saturation effect 饱和效应saturation curve 饱和曲线flux linkage 磁链per unit value 标么值shunt field 并励磁场magnetic circuit 磁路load-saturation curve 负载饱和曲线air-gap line 气隙磁化线polyphase rectifier 多相整流器circuit components 电路元件circuit parameters 电路参数electrical device 电气设备electric energy 电能primary cell 原生电池energy converter 电能转换器conductor 导体heating appliance 电热器direct-current 直流time invariant 时不变的self-inductor 自感mutual-inductor 互感the dielectric 电介质storage battery 蓄电池e.m.f = electromotive fore 电动势unidirectional current 单方向性电流circuit diagram 电路图load characteristic 负载特性terminal voltage 端电压exter nal characteristic 夕卜特性conductance 电导volt-ampere characteristics 伏安特性carbon-filament lamp 碳丝灯泡ideal source 理想电源internal resistance 内阻active (passive)circuit elements 有(无)源电路元件leakage current 漏电流circuit branch 支路P.D. = potential drop 电压降potential distribution 电位分布r.m.s values = root mean square values 均方根值effective values 有效值steady direct current 恒稳直流电sinusoidal time function 正弦时间函数complex number 复数Cartesian coordinates 笛卡儿坐标系modulus 模real part 实部imaginary part 虚部displacement current 位移电流trigonometric transformations 瞬时值epoch angle 初相角phase displacement 相位差signal amplifier 小信号放大器mid-frequency band 中频带bipolar junction transistor (BJT) 双极性晶体管field effect transistor (FET) 场效应管electrode 电极电焊条polarity 极性gain 增益isolation 隔离分离绝缘隔振emitter 发射管放射器发射极collector 集电极base 基极self-bias resistor 自偏置电阻triangular symbol 三角符号phase reversal 反相infinite voltage gain 无穷大电压增益feedback component 反馈元件differentiation 微分integration 积分下限impedance 阻抗fidelity 保真度summing circuit 总和线路反馈系统中的比较环节Oscillation 振荡inverse 倒数admittance 导纳transformer 变压器turns ratio 变比匝比ampere-turns 安匝(数)mutual flux 交互(主)磁通vector equation 向(相)量方程power frequency 工频capacitanceeffect 电容效应induction machine 感应电机shunt excited 并励series excited 串励separatelyexcited 他励self excited 自励field winding 磁场绕组励磁绕组speed-torque characteristic 速度转矩特性dynamic-state operation 动态运行salient poles 凸极excited by 励磁field coils 励磁线圈air-gap flux distribution 气隙磁通分布direct axis 直轴armature coil 电枢线圈rotating commutator 旋转(整流子)换向器commutator-brush combination 换向器-电刷总线mechanical rectifier 机械式整流器armature m.m.f. wave 电枢磁势波Geometrical position 几何位置magnetic torque 电磁转矩spatial waveform 空间波形sinu soidal —den sity wave 正弦磁密度external armature circuit 电枢外电路instantaneouselectric power 瞬时电功率instantaneousmechanical power 瞬时机械功率effects of saturation 饱和效应reluctance 磁阻polyphase rectifier 多相整流器boost 增压time constant 时间常数forward transfer function 正向传递函数error signal 误差信号regulator 调节器stabilizing transformer 稳定变压器time delay 延时direct axis transient time constant 直轴瞬变时间常数transient response 瞬态响应solid state 固体buck 补偿operational calculus 算符演算gain 增益pole 极点feedback signal 反馈信号dynamic response 动态响应voltage control system 电压控制系统mismatch 失配error detector 误差检测器excitation system 励磁系统field current 励磁电流transistor 晶体管high-gain 高增益boost-buck 升压去磁feedback system 反馈系统reactive power 无功功率feedback loop 反馈回路automatic Voltage regulator(AVR)自动电压调整器reference Voltage 基准电压magnetic amplifier 磁放大器amplidyne 微场扩流发电机self-exciting 自励的limiter 限幅器manual control 手动控制block diagram 方框图linear zone 线性区potential transformer 电压互感器stabilization network 稳定网络stabilizer 稳定器air-gap flux 气隙磁通saturation effect 饱和效应saturation curve 饱和曲线flux linkage 磁链no-load 空载full load 满载Polyphase 多相(的) iron-loss 铁损complex impedance复数阻抗rotor resista nee 转子电阻leakage flux 漏磁通loeked-rotor 锁定转子ehopper eireuit 斩波电路separatelyexeited 他励的eompounded 复励de motor 直流电动机de maehine 直流电机speed regulation 速度调节shunt 并励series 串励armature circuit 电枢电路optical fiber 光纤interoffice 局间的waveguide 波导波导管bandwidth 带宽light emitting diode 发光二极管silica 硅石二氧化硅regeneration 再生, 后反馈放大coaxial 共轴的,同轴的high-performance 高性能的carrier 载波mature 成熟的Si ngle Side Ban d(SSB)单边带coupling capacitor 结合电容propagate 传导传播modulator 调制器demodulator 解调器line trap 限波器shunt 分路器Amplitude Modulation(AM 调幅Frequency ShiftKeying(FSK) 移频键控tuner 调谐器attenuate 衰减incident 入射的two-way configuration 二线制generator voltage 发电机电压dc generator 直流发电机induction machine 感应式电机horseshoe magnet 马蹄形磁铁magnetic field 磁场eddy current 涡流right-hand rule 右手定则left-hand rule 左手定则slip 转差率induction motor 感应电动机rotating magnetic field 旋转磁场winding 绕组stator 定子rotor 转子induced current 感生电流time-phase 时间相位exciting voltage 励磁电压solt 槽lamination 叠片laminated core 叠片铁芯short-circuiting ring 短路环squirrel cage 鼠笼rotor core 转子铁芯cast-aluminum rotor 铸铝转子bronze 青铜horsepower 马力random-wound 散绕insulation 绝缘ac motor 交流环电动机end ring 端环alloy 合金coil winding 线圈绕组form-wound 模绕performa nee characteristic 工作特性frequency 频率revolutions per minute 转/ 分motoring 电动机驱动generating 发电per-unit value 标么值breakdown torque 极限转矩breakawayforce 起步阻力overhauling 检修wind-driven generator 风动发电机revolutions per second 转/ 秒number of poles 极数speed-torque curve 转速力矩特性曲线plugging 反向制动synchronous speed 同步转速percentage 百分数locked-rotor torque 锁定转子转矩full-load torque 满载转矩prime mover 原动机inrush current 涌流magn etiz ing reaca nee 磁化电抗line-to-neutral 线与中性点间的staor winding 定子绕组leakage reaeta nee 漏磁电抗per unit value 标么值shunt field 并励磁场magnetie eireuit 磁路load-saturation eurve 负载饱和曲线air-gap line 气隙磁化线polyphase reetifier 多相整流器eireuit eomponents 电路元件eireuit parameters 电路参数eleetrieal deviee 电气设备eleetrie energy 电能primary cell 原生电池energy converter 电能转换器conductor 导体heating appliance 电热器direct-current 直流time invariant 时不变的self-inductor 自感mutual-inductor 互感the dielectric 电介质storage battery 蓄电池 e.m.f = electromotive fore 电动势unidirectional current 单方向性电流circuit diagram 电路图load characteristic 负载特性terminal voltage 端电压exter nal characteristic 夕卜特性conductance 电导volt-ampere characteristics 伏安特性carbon-filament lamp 碳丝灯泡ideal source 理想电源internal resista nee 内阻active (passive)circuit elements 有(无)源电路元件leakage current 漏电流circuit branch 支路P.D. = potential drop 电压降potential distribution 电位分布r.m.s values = root mean square values 均方根值effective values 有效值steady direct current 恒稳直流电sinusoidal time function 正弦时间函数complex number 复数Cartesian coordinates 笛卡儿坐标系self excited 自励field winding 磁场绕组励磁绕组speed-torque characteristic 速度转矩特性dynamic-state operation 动态运行salient poles 凸极excited by 励磁field coils 励磁线圈air-gap flux distribution 气隙磁通分布direct axis 直轴armature coil 电枢线圈rotating commutator 旋转(整流子)换向器commutator-brush combination 换向器-电刷总线mechanical rectifier 机械式整流器armature m.m.f. wave 电枢磁势波Geometrical position 几何位置magnetic torque 电磁转矩spatial waveform 空间波形sinusoidal density wave 正弦磁密度external armature circuit 电枢外电路instantaneouselectric power 瞬时电功率instantaneousmechanical power 瞬时机械功率effects of saturation 饱和效应reluctance 磁阻power amplifier 功率放大器compound generator 复励发电机rheostat 变阻器self excitation process 自励过程commutation condition 换向状况cumulatively compounded motor 积复励电动机operating condition 运行状态equivalent T circuit T 型等值电路rotor (stator) winding 转子(定子绕组)winding loss 绕组(铜)损耗prime motor 原动机active component 有功分量reactive component 无功分量electromagnetictorque 电磁转矩retarding torque 制动转矩inductive component 感性(无功)分量abscissaaxis 横坐标induction generator 感应发电机synchronous generator 同步发电机automatic station 无人值守电站hydropowerstation 水电站process of self excitation 自励过程auxiliary motor 辅助电动机technical specifications 技术条件voltage across the terminals 端电压steady state condition 瞬态暂态reactive in respect to 相对。
阿尔法拉瓦尔NX桶式离心机说明书

ApplicationDecanter centrifuges are an important component, in the processes used to extract protein from meat, fish and insects. These include rendering and hydrolyzed protein processing.Alfa Laval decanter centrifuges are used in 2- or 3- phases configurations, as an integral part of most rendering processes.•Wet and dry rendering for meat, fish and Insects •Hydrolyzed meat and fish protein•Bones and gelatin processes•Blood meal•Surimi and krill•SkimmingAlfa Laval NX decanter centrifuges benefit from many years of as well as constant innovation and improvement. The product range enables improve and optimize recovery of valuable proteins fractions – as well as fats and oils – in the most efficient manner possible.Benefits•Stable interphase: Open outlets ensure very high levels of purity for each liquid phase.•Baffle disc: Improved separation efficiency as a result of a clear separation between solids and liquid(s) in the bowl.This makes it possible to improve effective defatting and dewatering of the solids and to ensure higher purity for both liquid phases.•Low-speed flush: Easy to clean, due to the open outlets.These can be cleaned- effective by using very little water.•Easy rapid service.Working principleSeparation takes place in a horizontal, cylindrical bowlequipped with a screw conveyor. The feed is led into the bowl through a stationary inlet/feed tube [10] and smoothly accelerated by an inlet distributor [5] in – the feed zone.Centrifugal force causes sedimentation of the suspended solids inside the bowl [4].The conveyor [3] rotates in the same direction as the bowl,but at a different speed – called the differential speed. Thisdifference moves the solids to the conical end, where they are lifted out of the liquid level (pond) into a dry zone (beach). Here the capillary liquid is drained centrifugally, before being dis charged through the solids outlet [7] the casing.Separation takes place over the entire length of the cylindrical part of the bowl. The clarified liquid or liquids leave the bowlby flowing over an adjustable weir into the casing.1: Gearbox 2: Liquid outlet 3: Screw conveyor 4: Wall of the bowl 5: Inlet distributor 6: Conical end7: Cleaned slurry/muck outlet 8: Feed inlet9: Discharge ports 10: Feed tubeDesignNX decanter centrifuges are specially designed with a focus on performance, reliability, efficiency, easy access and quiet running. The cover is fitted with hinges to make access easy.The rotating assembly is mounted on a compact, welded box beam frame with main bearings at both ends. The motors are mounted in-line on the decanter itself to ensure the smallest possible footprint. The bowl is driven at the conical end by an electric motor with a V-belt transmission. NX decantercentrifuges are available in 2-phase or 3-phase configurations that are easy to adapt to the demands associated with a specific operating requirements. Each unit can also be adjusted on site.The centrifuge can be equipped with a CIP bar with nozzles/spray head to clean the bowl exterior and the casing/cover, as well as the inside of the bowl.Drive systemIn all Alfa Laval decanter centrifuges, the bowl is driven towards the conical end by an electric motor and V-belt transmission. Power is transferred to the conveyor via a planetary or Direct Drive gearbox.The speed difference is controlled in different ways, depending on the type of unit:•NX countershaft decanters feature a countershafttransmission, in which pulleys can be changed manually to regulate the input shaft speed of the gearbox, and thereby the differential speed•NX VFD-driven decanters are equipped with an automatic back drive system for the main motor.•The back drive motor is coupled to a Direct Drive (DD)gearbox that continuously adjusts the differential speed during operation.Direct Drive is a unique system developed and manufactured by Alfa Laval, to enable processing at maximum torque, thus resulting in best possible dryness of the solids.MaterialsThe bowl, conveyor, inlet tube, outlets, cover and other parts that are in direct contact with the process media are all made of stainless steel or duplex steel. The frame is made of mild steel with an epoxy enamel finish. The discharge ports,conveyor flights and feed zone are protected with materials that are highly resistant to abrasive solid particles.Solids transportDepending on the application, the inner surface of the bowl features either grooves or ribs. These ensures good solids conveying efficiency and limits how much the product slides along the inner surface on the bowl, which tends to generate abrasion, particularly if the solids are hard.Feed zoneThe feed zone is available with exchangeable wear liners made of tungsten carbide for additional wear protection.360° solids dischargesThe spokes are protected against wear by use of "saddles"made of tungsten carbide. The 360° solids discharge is extremely effective because there is no thing to hinder or restrict scrolling the cake out of the bowl.AutomationDecanter centrifuges equipped with variable frequency drives (VFD) are also available with control solutions to comply with your specific operating requirement. Whether you are looking for a control system that operates the decanter only or to more advanced control systems with additional functionality.Alfa Laval decanter automation can help you achieving your specific process performance goals by easy processadjustments, real-time status feedback, automated process adjustments and automated cleaning cycles.Additional featuresThe specially designed architecture of the bowl and conveyor in Alfa Laval decanter centrifuges makes it possible to effectively separate the solids and liquid phase(s) in order to maximize retention times. Keeping the input material in the bowl longer gives higher level of purity in the liquid’s phase(s) and greater dryness in the solid phase. The open outlets make it possible to maintain a stable interphase, even when the feed flows and composition vary by +/- 20%. A stable interface layer between oil and stick water is important for achieving the best possible separation efficiency in both liquid phases, even with emulsions. Open outlets also help ensure that the bowlcan be kept very clean, and make it easy to carry out visual inspections. This design also simplifiesthe decanter’s flush and CIP sequences. Array Protecting the flightsThe conveyor is protected by a coating that contains micro-grains of tungsten carbide, which aresprayed onto the upper 1/3 of the pushing face of the flights while hot. For particularly abrasiveapplications, the conveyor’s flights can be protected with tungsten carbide tiles and flame sprayedtungsten carbide. ArrayEasy to cleanDecanters fitted with an automation control system can execute a high-speed cleaning mode,followed by a low-speed cleaning mode by using frequency converters on the main and back drivemotors. Cleaning-in-place (CIP) media are introduced inside and outside the bowl. A spray bar(optional) on the cover effectively completes the cleaning by spraying water on the outside of thebowl external face. A CIP program featuring repeated sequences of high- and low-speed modesfor water, caustic and acid cleaning agents ensures supremely effective CIP cycle. The duration ofeach sequence, can be adjusted to your particular operating conditions ArrayLow-speed cleaning-in-placeThis is done by switching the direction in which the bowl rotates, at low speed. As the bowlperiodically changes rotation direction, a wave of liquid moves from one end to the other, cominginto contact with all the internal parts. At the same time, the turbulence resulting from this liquidmovement effectively cleans all the outlets and enhances the overall cleaning effect.The frame casing is a box beam profile, featuring an integral casing fitted with hinges. The casingand cover are made of AISI 316 stainless steel, with stainless steel cladding in the neutral bowl’scompartment. Due to their particularly smart design, Alfa Laval decanter centrifuges can beserviced very quickly. For example, it takes less than 3 hours to remove and replace a completerotating assembly.Connected servicesAlfa Laval decanter centrifuges that feature decanter automation can also be fitted with IoTconnectivity hardware that can provide you with full operating data, along with condition monitoringand process optimization. Please refer to the Alfa Laval website for more information.ServiceInvesting in an Alfa Laval decanter centrifuge solution is the first step towards a unique partnershipwith Alfa Laval Service. Our strong service presence in local market, combined with the capabilitiesof skilled Field Service Engineers, provides you and your operations with the support that you needto maximize processing uptime. A Service Agreement takes this one step further. Contact yourlocal Alfa Laval sales for more information.DimensionsDesignation NX912/913NX3650NX4450NX438NX5040NX5540NX6540NX7240 Length (L) (mm/inches)3,216/126.64,071/155.664,734/186.964,925/193.904,976/195.95,416/215.606,174/246.066,459/254.27 Width (W) (mm/ inches)780/30.7990/39.981,060/41.731,190/46.91,190/46.91,300/51.21,450/57.091,510/59.45 Height (H) (mm/inches)960/37.81,304/51.321,376/54.171,445/56.91,651/651,696/66.81,791/70.511,852/72.91 Gross weight (kg/lbs)1,500/3,3002,300/5,1003,200/7,1004,800/10,5824,900/10,8005,120/11,3006,500/14,3508,300/18,300Technical specificationsDesignation NX912/913NX3650NX4450NX438NX5040NX5540NX6540NX7240 Available angles in °10, 206, 10 or 206, 10 or 20106, 10 or 206, 10 or 206, 10 or 206, 10 or 20 Bowl diameter in mm/inches280/11.02360/14.17440/17.32480 / 18.89500/19.7550/21.65650/25.59720/28.35G-force, max. x g3,0303,5493,5513,5743,6223,5543,4913,384Total weight, net in kg/lbs1,500/3,3502,300/5,1003,200/7,1004,800/10,5824,900/10,8005,120/11,3006,500/14,3508,300/18,300 Sound pressure level1) dB(A) re. 20mPa81798185838383841) In compliance with EN ISO 4871 and EN 12547This document and its contents are subject to copyrights and other intellectual property rights owned by Alfa Laval Corporate AB. No part of this document may be copied, re-produced or transmitted in any form or by any means, or for any purpose, without Alfa Laval Corporate AB’s prior express written permission. Information and services provided in this document are madeas a benefit and service to the user, and no representations or warranties are made about the accuracy or suitability of this information and these services for any purpose. All rights arereserved.200005995-2-EN-GB© Alfa Laval Corporate AB How to contact Alfa LavalUp-to-date Alfa Laval contact details for all countries are always availableon our website at 。
LEYCON Valves 抽真空阀(型号:176.35.01)说明书
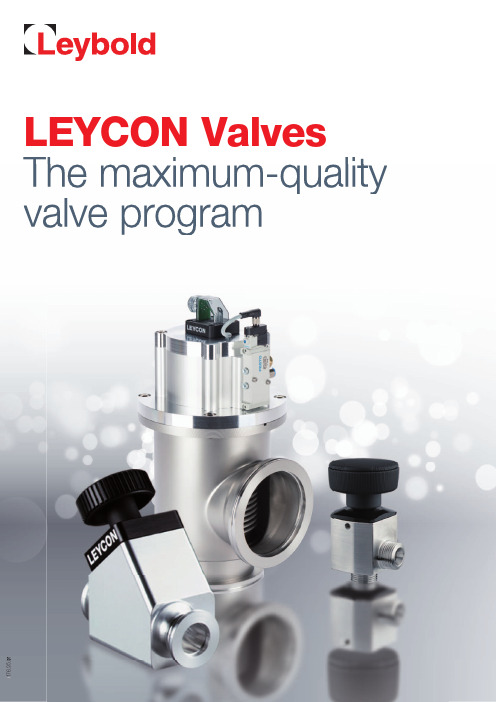
LEYCON Valves 176.35The maximum-quality valve program.01The LEYCON Valve ProgramExceptional quality and extended service lifeLeybold vacuum valves are a byword for exceptional quality.Our LEYCON valves have a proven track record in both research and industry, ensuring reliability and dependability across all processes. See for yourself how our flexible solu-tions can meet and exceed your requirements.With over 50 years’ experience in the field, Leybold is a guarantee of long service life and trouble-free operation.Trust in the quality and reliability of our vacuum systems and see how much time and money you will save. Leybold valves will match your expectations – and then some.All valve types are available in a range of variants pertaining to casing mate-rial and drive type. In the case of drive types, a distinction is made between manual and pneumatic drives, and electropneumatic and electromagnetic drives.User benefitsI Compact, lightweight construction IIntegral leak rate < 10-8 mbar l/sI Extremely low vibration levels I Lubricant-free wetted area due toFPM sealingIOperating range up to 2000 mbarI Very high conductanceIPrincipal dimensions are compatible with Leybold flange components of the same nominal diameterI Reliable operation in any orientationIValves can be operated at various supply voltagesI Optical and electrical positionindicators are integrated in many valve variantsI Pilot valve available for manyvariantsThe product rangeThe LEYCON valve program includesI Micro valves (small valves),bellows-sealedI Right-angle and straight-throughvalves, bellows-sealed, with nominal diameters DN 16 to DN 50 with ISO-KF flangesI Right-angle valves, bellows-sealed,with nominal diameters DN 63 to DN 250 with ISO-K flanges.I Gate valves in ISO-KF, ISO-F andISO-CF variantsI Special valves for specificapplicationsThe LEYCON valve programLEYCONThe right valve for your applicationDrive types I Manual I PneumaticI Electropneumatic I Electromagnetic Casing types I Right-angle valveI Straight-through valve (electromagnetic only)AccessoriesI Adapter (DN 10 ISO-KF flange, ¼” pipe, 6 mm pipe)The “micro” range of valves is the space-saving and efficient solution in a compact size. Various optional connecting adapters guarantee the highest degree of flexibility during system integration.Micro valves overview (right-angle / straight-through valves)Example dimensions for electromagnetic straight-through valve: 2 x 10 KF , approx. 100 mm longAdapter/connector for micro valves (optional)82 mm micro right-angle and straight-through valvesUser BenefitsI Compact constructionI High conductance at the molecularlevelI Long service lifeat > 2 million switching cycles I High switching frequency I Protection class IP 65I High flexibility of installationBellows-sealed, with various drive typesDrive typesIManualIPneumaticI ElectropneumaticI ElectromagneticCasing materialIIUser BenefitsElectropneumaticI Time-saving installation thanks tostandards-compliant electrical andcompressed air connectionsI Low noise and low vibration whenopening and closingI High process efficiency thanks tovery short opening and closing timesI High degree of safety thanks to anormally closed designI Maximum flexibility: any orientationand flow direction is possibleI Optical position indicator for straight-forward process monitoringManualI Simple operability with low physicaleffortI Allows reduced plant ventilation in atargeted mannerI Suitable for use as a coarse variableleak valve for manual flow controlISpace-saving: compact size thanksto efficient constructionI Maximum flexibility: any orientation ispossibleElectromagneticI Ideal for remote control on vacuumunitsI Convenient process monitoringthrough an LED position indicator forvalve open, valve closed and valveerror statesI High process efficiency thanks tovery short opening and closing timesI High degree of safety thanks to anormally closed designI Maximum flexibility: any orientationand flow direction is possibleI Low operating temperatureValves from the ISO-KF range are especially suited to high-vacuum applications such as pump systems, semiconductor technology and research systems. Their rugged and intelligent valve design guarantees a high degree of impermeabilityand particulate resistance.ight-angle and straight-throughAL/L1QDimensional drawing (mm) shows stainless steel right-angle valve, DN ISO-KF, with electromagnetic drive, as an example.The complete program can be found in Chapter 14 of the Oerlikon Leybold Vacuum complete catalogue.Connection pictogramSafety capValve seat sideElectrical connectionPosition indicator connectionFlow directionLeak detection portPosition indicatorDimensions tableDNABCDEFGI SO-KF 16 25 40mm 170.9 193.0 246.0mm 51.4 64.9 92.9mm 40 50 65mm 96.0 112.7 139.0mm 86.0 97.3 119.5mm 59 70 90mm 10.0 15.4 19.5 Right-angle and straight-through valves up to DN 50 ISO-KFThe new ISO-K range offers reliable valves of the very highest quality. Due to their modular construction, these valves arevery easy to maintain and can be adapted to changing requirements almost at will.I ManualI I I User BenefitsManualI Maximum flexibility: any orientation and flow direction is possible I Simple operation thanks to a smooth-running manual drive I Also suitable for use as a coarse variable leak valve for flow control I Modular construction ensures straightforward maintenance and ease of cleaningI Mechanical position indicator for continuous status monitoringI Resistant to magnetic radiation and strong vibrationsElectropneumaticI Very short opening and closing times due to efficient solenoids (available for various different supply voltages)I Modular construction ensures straightforward maintenance and ease of cleaningI Mechanical position indicator for continuous status monitoringI Resistant to magnetic radiation and strong vibrationsI Designed for universal deploymentwith high dependabilityI Ideally suited to processes with high gas throughputI Long service life thanks to a rugged and intelligent valve designI Simple and convenient operation I Valves from the ISO-K range are also available in a soft-start variant. Further details available on request.Dimensional drawing (mm) shows right-angle valve, DN ISO-K, with electropneumatic drive as an example.The complete program can be found in Chapter 14 of the Oerlikon Leybold Vacuum complete catalogue.Right-angle valves up to DN 160 ISO-KConnection pictogramElectrical connection Position indicator connection Position indicator connectionDimensions tableDN AB C D E I SO-K 63 100 160 mm 197 282 366mm 123 170 221 mm 189.5 208 264 mm 88 108 138mm 41.2 14 14 mm 6 6 6Typical constructionof a vacuum valveA comprehensive product programLeybold offers a range of special valves for the most varied of applications.Special ValvesI Pressure relief valvesDN 16 ISO-KFI Power failure venting valvesDN 10 ISO-KFI Coarse variable leak valveswith or without isolation valve DN 10/16 ISO-KFI Venting valves DN 10 ISO-KF I Vacuum locks(DN 16 bis DN 40 ISO-KF)I Sealing valves(DN 16 bis DN 40 ISO-KF)I Ball valves(DN 16 bis DN 40 ISO-KF)I UHV valves (DN 16 bis 63 CF)I Purge gas and venting valvesfor turbomolecular pumps The special valves are described in detail in Chapter 14 of the complete Leybold catalogue.Compact Design and Maximum Safety for your processGate valves are available in aluminum or stainless steel, with ISO-KF, CF and ISO-F flanges. SECUVAC safety valves havebeen specially designed for connecting to rotating vacuum pumps without a built-in inlet valve.Gate ValvesGate valvesSafety valvesSafety ValvesSECUVACI SECUVAC safety valves(DN 16 ISO-KF to DN 100 ISO-KF)with electromagnetic drive24 V DC, 100-115 V AC,200-230 V ACShut-off valve between backing pump and vacuum chamber to prevent venti-lation if a power failure occurs.User BenefitsI Rapid closure high-vacuum shut-offvalveI Can be used as a venting valve I Closes immediately in the case of a power failureI Can only be opened once the intake line has been evacuated I No …air swallowing“el, with ISO-KF, CFum pumps wum or stainles ng to ro Drive types I ManualI ElectropneumaticDrive typesI ElectromagneticTypeDrive type Flange sizes Material HV gate valvesManualDN 63 ISO-F to DN 160 ISO-F Aluminum Flange sizesDN 63 ISO-F to DN 250 ISO-F Aluminum Miniature HV gate valvesManualDN 16, DN 25,DN 40 ISO-KF Aluminum Electropneumatic (24 V DC)DN 40 ISO-KF Stainless steel UHVgate valvesManualDN 63 ISO-CF to DN 200 ISO-CFStainless steelElectropneumatic (24 V DC or 230 V AC)DN 100 ISO-F toDN 250 ISO-F and DN 63 ISO-CF to DN 200 ISO-CF Stainless steel Miniature UHV gate valvesManualDN 40 ISO-CF Stainless steel Electropneumatic (24 V DC or 230 V AC)DN 40 ISO-CFStainless steelGate valvesManualElectro-pneumaticCost-effective gates for industrial applications Compact and light Bellows-sealed designMinimal locking impact and wear Mechanical position indicator Vibration-free actuation Bakeable UHV gate valvesUser BenefitsB C O M _13690/13810.01 176.35.01 0.2.07.16 P D F P r i n t e d i n G e r m a n y o n c h l o r i n e -f r e e b l e a c h e d p a p e r T e c h n i c a l a l t e r a t i o n s r e s e r v e dLEYCON ValvesProven in all applications EYCON Valvesoven in all applicationsThe demands placed on our valves are as varied as their potential applications.LEYCON valves meet those require-ments, for example in the following fieldsI Coating technology- Short switching cycles (e.g. 1.5s) - Very high number of opening and closing cycles (e.g. more than 10 million cycles)I Analytical technology- High conductance - Low integral leak rate (<10-9 mbar l/s)I Lamp and tube manufacture- Temperature resistance- Max. ambient temperature 80 °CI Accelerator technology- Materials are radiation, temperature and corrosion resistantI Metallurgy and furnace manufacture- Rugged and resilient with regard to impuritiesI Chemistry- Selectable wetted casing materialsOther application areas include:I Semiconductor engineering I Quality control while a process isrunningI Refrigeration and air conditioning I Materials researchI Research and development from thelab to Big ScienceI High-vacuum systemsLeybold GmbHBonner Str. 498 · D-50968 Köln T +49 (0) 221-347-0F +49 (0) 221-347-1250****************。
老外电子制作实例大全
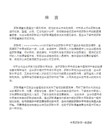
设计一个4通道A / D (模数转换器)转换器与pic12c671
Ser-Key 10-Key Serial Keypad Encoder
2线接口的液晶显示器用pic16cf84
PIC16F84的串行输入/输出-膨胀picbasic
摄像头远程控制系统的使用基本邮票
多芯片编程器
本文来自: 电子工程师之家
Alarms and security related schematics
Proximity alarm
Electronic lock
Electronic door codelock (PIC16F84)
几个Atmel公司的AVR编程器集成电路
12c508智能锁
基本杜绝基于高度表
接口EEPROM中的一个基本邮票
自制基本杜绝工程
接口该max186八通道ADC向bsii
该接口的ADC器MAX187向bsii测量电压
射频远程控制的基础上的基本邮票
80c31步进马达控制器
I2C LCD接口
afsk 1200个调制解调器基于pic16c620
皮孔-隐蔽电台发射机控制器
PIC16F84的声发生器及源代码
PIC16F84的声发生器
PIC16F84的声发生器 (6-Bit)
AVR单片机的灯塔,超级的keyer
AVR单片机的频率计数器
AVR单片机数字电压表
谈知情同意-基于s p0256
夏普gp2d02接口,以PIC单片机
夏普gp2d05接口,以PIC单片机夏普gp2d05接口,以PIC单片机
串行到并行转换器采用AT89C2051的
卡莫兹工业应用产品系列 QP-QPR 气动致动器说明书
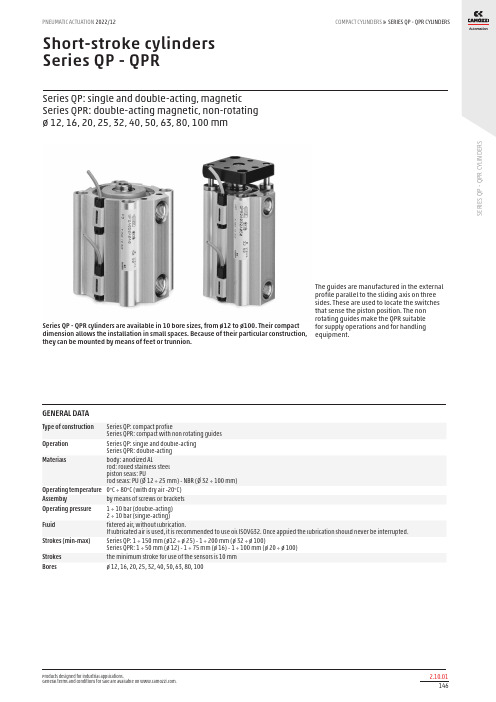
S E R I E S Q P - Q P R C Y L I N D E R SShort-stroke cylinders Series QP - QPRSeries QP: single and double-acting, magnetic Series QPR: double-acting magnetic, non-rotating ø 12, 16, 20, 25, 32, 40, 50, 63, 80, 100 mmSeries QP - QPR cylinders are available in 10 bore sizes, from ø12 to ø100. Their compact dimension allows the installation in small spaces. Because of their particular construction, they can be mounted by means of feet or trunnion.The guides are manufactured in the external profile parallel to the sliding axis on three sides. These are used to locate the switches that sense the piston position. The non rotating guides make the QPR suitablefor supply operations and for handling equipment.GENERAL DATAType of construction Series QP: compact profileSeries QPR: compact with non rotating guides Operation Series QP: single and double-acting Series QPR: double-actingMaterialsbody: anodized ALrod: rolled stainless steel piston seals: PUrod seals: PU (Ø 12 ÷ 25 mm) - NBR (Ø 32 ÷ 100 mm)Operating temperature 0°C ÷ 80°C (with dry air -20°C)Assemblyby means of screws or brackets Operating pressure 1 ÷ 10 bar (double-acting) 2 ÷ 10 bar (single-acting)Fluidfiltered air, without lubrication.If lubricated air is used, it is recommended to use oil ISOVG32. Once applied the lubrication should never be interrupted.Strokes (min-max)Series QP: 1 ÷ 150 mm (ø12 ÷ ø 25) - 1 ÷ 200 mm (ø 32 ÷ ø 100)Series QPR: 1 ÷ 50 mm (ø 12) - 1 ÷ 75 mm (ø 16) - 1 ÷ 100 mm (ø 20 ÷ ø 100)Strokes the minimum stroke for use of the sensors is 10 mm Boresø 12, 16, 20, 25, 32, 40, 50, 63, 80, 100S E R I E S Q P - Q P R C Y L I N D E R SSTANDARD STROKES FOR SHORT-STROKE CYLINDERS SERIES QP AND QPR■ = Double-acting ✖ = Single-acting ● = Non-rotatingSTANDARD STROKES Ø510152025303540455060758010012■ ✖ ●■ ✖ ●■ ✖ ●■ ✖■ ✖ ●■ ●■■■16■ ✖ ●■ ✖ ●■ ✖ ●■ ✖ ●■ ✖ ●■ ●■ ●■ ●■ ●■ ●■ ●■ ●■■20■ ✖ ●■ ✖ ●■ ✖ ●■ ✖ ●■ ✖ ●■ ●■ ●■ ●■ ●■ ●■ ●■ ●■ ●■ ●25■ ✖ ●■ ✖ ●■ ✖ ●■ ✖ ●■ ✖ ●■ ●■ ●■ ●■ ●■ ●■ ●■ ●■ ●■ ●32■ ✖ ●■ ✖ ●■ ✖ ●■ ✖ ●■ ✖ ●■ ●■ ●■ ●■ ●■ ●■ ●■ ●■ ●■ ●40■ ✖ ●■ ✖ ●■ ✖ ●■ ✖ ●■ ✖ ●■ ●■ ●■ ●■ ●■ ●■ ●■ ●■ ●■ ●50■ ✖ ●■ ✖ ●■ ✖ ●■ ✖ ●■ ✖ ●■ ●■ ●■ ●■ ●■ ●■ ●■ ●■ ●■ ●63■ ✖ ●■ ✖ ●■ ✖ ●■ ✖ ●■ ✖ ●■ ●■ ●■ ●■ ●■ ●■ ●■ ●■ ●■ ●80■ ✖ ●■ ✖ ●■ ✖ ●■ ✖ ●■ ✖ ●■ ●■ ●■ ●■ ●■ ●■ ●■ ●■ ●■ ●100■ ✖ ●■ ✖ ●■ ✖ ●■ ✖ ●■ ✖ ●■ ●■ ●■ ●■ ●■ ●■ ●■ ●■ ●■ ●CODING EXAMPLEPNEUMATIC SYMBOLSThe pneumatic symbols which have been indicated in the CODING EXAMPLE are shown below.S E R I ESQ P - Q P R C Y L I N D E R SACCESSORIES FOR SHORT-STROKE CYLINDERS SERIES QPFoot mount Mod. B Male trunnion Mod. LAll accessories are supplied separately.S E R I E S Q P - Q P R C Y L I N D E R STORQUE MOMENT ACCORDING TO STROKE CTORQUE MOMENT ACCORDING TO STROKE CS ERI E SQ P - Q P R C Y L I N D E R STRANSVERSAL LOAD ACCORDING TO PROJECTION “ X “F = transversal forceTRANSVERSAL LOAD ACCORDING TO PROJECTION “ X “S E R I E S Q P - Q P R C Y L I N D E R SFor single-acting cylinders ø 12, 16, 20 and 25 add 5mm to G+, G1+ and N+ dimensions.+ = add the strokeS E R I E S Q P - Q P R C Y L I N D E R S+ = add the stroke once + = add the stroke twiceS E R I E S Q P - Q P R C Y L I N D E R S+ = add the strokeS E R I E S Q P - Q P R C Y L I N D E R SShort-stroke cylinder Series QPR - through-rodNote:The cylinder’s end stop must be provided externally.+ = add the stroke once ++ = add the stroke twiceS E R I E S Q P - Q P R C Y L I N D E RSMale trunnion bracket Mod. LMaterial: AluminiumSupplied with: 1x trunnion 4x screws+ = add the strokeFeet bracket Mod. BMaterial: zinc-plated steel.Supplied with: 2x feet 4x screws+ = add the stroke。
硅钢片在电机里的作用英语
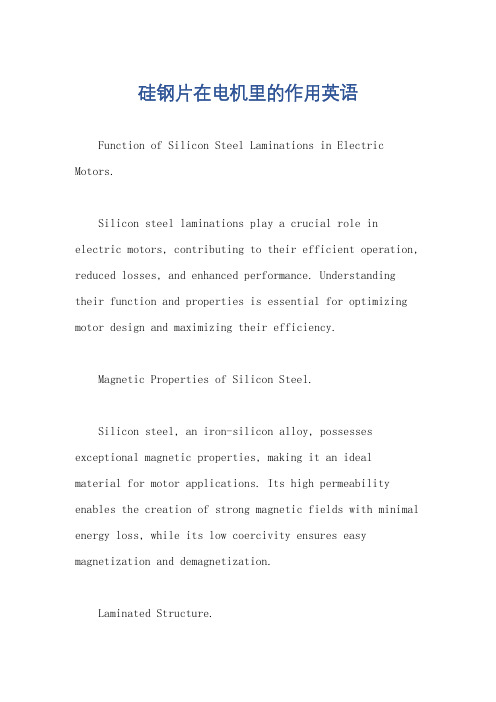
硅钢片在电机里的作用英语Function of Silicon Steel Laminations in Electric Motors.Silicon steel laminations play a crucial role in electric motors, contributing to their efficient operation, reduced losses, and enhanced performance. Understanding their function and properties is essential for optimizing motor design and maximizing their efficiency.Magnetic Properties of Silicon Steel.Silicon steel, an iron-silicon alloy, possesses exceptional magnetic properties, making it an ideal material for motor applications. Its high permeability enables the creation of strong magnetic fields with minimal energy loss, while its low coercivity ensures easy magnetization and demagnetization.Laminated Structure.Silicon steel laminations are thin sheets of silicon steel that are stacked together to form the motor's magnetic core. This laminated structure serves several critical purposes:Reduced Hysteresis Loss: Hysteresis loss occurs when the magnetic field in the core is reversed, causing energy dissipation. Laminations reduce hysteresis loss by confining magnetic domains within individual sheets, preventing the formation of large eddy currents that contribute to energy loss.Minimized Eddy Current Losses: Eddy currents are circular electrical currents that flow within the core due to the changing magnetic field. Laminations disrupt the flow of eddy currents by providing a high-resistance path, reducing their magnitude and associated energy losses.Improved Magnetic Field Distribution: The laminated structure ensures a more uniform distribution of the magnetic field within the core, reducing magneticsaturation and optimizing motor performance.Construction of Motor Cores.In electric motors, the stator and rotor cores are constructed from silicon steel laminations. The stator core is the stationary part that creates the rotating magnetic field, while the rotor core rotates within the stator field to generate torque. The laminations are stacked and interlocked to form the core, providing the required magnetic properties and mechanical strength.Types of Silicon Steel Laminations.Various grades of silicon steel are available, each with specific magnetic properties and applications. Common types include:Grain-Oriented Silicon Steel (GOSS): Highlyanisotropic material with excellent magnetic properties along the grain direction, used for high-efficiency motors.Non-Grain-Oriented Silicon Steel (NGO): Isotropic material with good magnetic properties in all directions, suitable for general-purpose motors.High Silicon Steel (HSS): Contains a higher silicon content, resulting in lower hysteresis and eddy current losses, used in high-performance motors.Benefits of Silicon Steel Laminations in Motors.The use of silicon steel laminations in electric motors offers numerous benefits, including:Enhanced Efficiency: Reduced energy losses due to hysteresis and eddy currents improve motor efficiency, saving energy and reducing operating costs.Lower Operating Temperatures: Minimized losses prevent excessive heating of the motor, extending its lifespan and enhancing reliability.Reduced Noise and Vibration: Laminations suppressmagnetic noise and vibrations, contributing to quieter and smoother motor operation.Optimized Performance: Improved magnetic field distribution and reduced losses result in optimal motor performance, including increased torque and reduced speed fluctuations.Compact Size and Weight: Laminated cores allow for compact motor designs without sacrificing performance, enabling space-saving applications.Conclusion.Silicon steel laminations are essential components of electric motors, providing the necessary magnetic properties to ensure efficient operation and enhanced performance. Their laminated structure effectively reduces energy losses, improves magnetic field distribution, and contributes to the overall reliability and durability of motors. By understanding the function and properties ofsilicon steel laminations, engineers can optimize motor designs to meet specific application requirements.。
核磁共振波普仪器专业词汇英汉翻译

APT Attached Proton Test 质子连接实验ASIS Aromatic Solvent Induced Shift 芳香溶剂诱导位移BBDR Broad Band Double Resonance 宽带双共振BIRD Bilinear Rotation Decoupling 双线性旋转去偶(脉冲)COLOC Correlated Spectroscopy for Long Range Coupling 远程偶合相关谱COSY ( Homonuclear chemical shift ) COrrelation SpectroscopY (同核化学位移)相关谱CP Cross Polarization 交叉极化CP/MAS Cross Polarization / Magic Angle Spinning 交叉极化魔角自旋CSA Chemical Shift Anisotropy 化学位移各向异性CSCM Chemical Shift Correlation Map 化学位移相关图CW continuous wave 连续波DD Dipole-Dipole 偶极-偶极DECSY Double-quantum Echo Correlated Spectroscopy 双量子回波相关谱DEPT Distortionless Enhancement by Polarization Transfer 无畸变极化转移增强2DFTS two Dimensional FT Spectroscopy 二维傅立叶变换谱DNMR Dynamic NMR 动态NMRDNP Dynamic Nuclear Polarization 动态核极化DQ(C) Double Quantum (Coherence) 双量子(相干)DQD Digital Quadrature Detection 数字正交检测DQF Double Quantum Filter 双量子滤波DQF-COSY Double Quantum Filtered COSY 双量子滤波COSY DRDS Double Resonance Difference Spectroscopy 双共振差谱EXSY Exchange Spectroscopy 交换谱FFT Fast Fourier Transformation 快速傅立叶变换FID Free Induction Decay 自由诱导衰减H,C-COSY 1H,13C chemical-shift COrrelation SpectroscopY 1H,13C 化学位移相关谱H,X-COSY 1H,X-nucleus chemical-shift COrrelation SpectroscopY1H,X-核化学位移相关谱HETCOR Heteronuclear Correlation Spectroscopy 异核相关谱HMBC Heteronuclear Multiple-Bond Correlation 异核多键相关HMQC Heteronuclear Multiple Quantum Coherence异核多量子相干HOESY Heteronuclear Overhauser Effect Spectroscopy 异核Overhause效应谱HOHAHA Homonuclear Hartmann-Hahn spectroscopy 同核Hartmann-Hahn谱HR High Resolution 高分辨HSQCHeteronuclear Single Quantum Coherence 异核单量子相干INADEQUATE Incredible Natural Abundance Double Quantum Transfer Experiment 稀核双量子转移实验(简称双量子实验,或双量子谱)INDOR Internuclear Double Resonance 核间双共振INEPT Insensitive Nuclei Enhanced by Polarization 非灵敏核极化转移增强INVERSE H,X correlation via 1H detection 检测1H的H,X核相关IR Inversion-Recovery 反(翻)转回复JRES J-resolved spectroscopy J-分解谱LIS Lanthanide (chemical shift reagent ) Induced Shift 镧系(化学位移试剂)诱导位移LSR Lanthanide Shift Reagent 镧系位移试剂MAS Magic-Angle Spinning 魔角自旋MQ(C) Multiple-Quantum ( Coherence ) 多量子(相干)MQF Multiple-Quantum Filter 多量子滤波MQMAS Multiple-Quantum Magic-Angle Spinning 多量子魔角自旋MQS Multi Quantum Spectroscopy 多量子谱NMR Nuclear Magnetic Resonance 核磁共振NOE Nuclear Overhauser Effect 核Overhauser效应(NOE)NOESY Nuclear Overhauser Effect Spectroscopy 二维NOE谱NQR Nuclear Quadrupole Resonance 核四极共振PFG Pulsed Gradient Field 脉冲梯度场PGSE Pulsed Gradient Spin Echo 脉冲梯度自旋回波PRFT Partially Relaxed Fourier Transform 部分弛豫傅立叶变换PSD Phase-sensitive Detection 相敏检测PW Pulse Width 脉宽RCT Relayed Coherence Transfer 接力相干转移RECSY Multistep Relayed Coherence Spectroscopy 多步接力相干谱REDOR Rotational Echo Double Resonance 旋转回波双共振RELAY Relayed Correlation Spectroscopy 接力相关谱RF Radio Frequency 射频ROESY Rotating Frame Overhauser Effect Spectroscopy 旋转坐标系NOE谱ROTO ROESY-TOCSY Relay ROESY-TOCSY 接力谱SC Scalar Coupling 标量偶合SDDS Spin Decoupling Difference Spectroscopy 自旋去偶差谱SE Spin Echo 自旋回波SECSY Spin-Echo Correlated Spectroscopy自旋回波相关谱SEDOR Spin Echo Double Resonance 自旋回波双共振SEFT Spin-Echo Fourier Transform Spectroscopy (with J modulation)(J-调制)自旋回波傅立叶变换谱SELINCOR Selective Inverse Correlation 选择性反相关SELINQUATE Selective INADEQUATE 选择性双量子(实验)SFORD Single Frequency Off-Resonance Decoupling 单频偏共振去偶SNR or S/N Signal-to-noise Ratio 信 / 燥比SQF Single-Quantum Filter 单量子滤波SR Saturation-Recovery 饱和恢复TCF Time Correlation Function 时间相关涵数TOCSY Total Correlation Spectroscopy 全(总)相关谱TORO TOCSY-ROESY Relay TOCSY-ROESY接力TQF Triple-Quantum Filter 三量子滤波WALTZ-16 A broadband decoupling sequence 宽带去偶序列WATERGATE Water suppression pulse sequence 水峰压制脉冲序列WEFT Water Eliminated Fourier Transform 水峰消除傅立叶变换ZQ(C) Zero-Quantum (Coherence) 零量子相干ZQF Zero-Quantum Filter 零量子滤波T1 Longitudinal (spin-lattice) relaxation time for MZ 纵向(自旋-晶格)弛豫时间T2 Transverse (spin-spin) relaxation time for Mxy 横向(自旋-自旋)弛豫时间tm mixing time 混合时间τc rotational correlation time 旋转相关时间。
双离合器-变速器系统-外文文献翻译
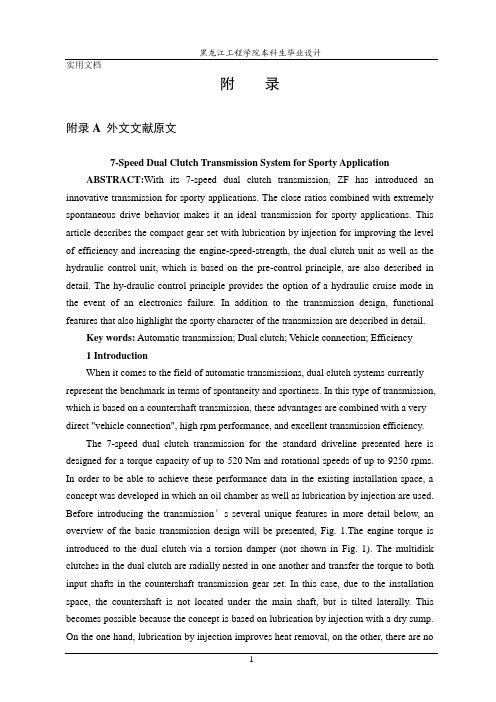
附录附录A外文文献原文7-Speed Dual Clutch Transmission System for Sporty Application ABSTRACT:With its 7-speed dual clutch transmission, ZF has introduced an innovative transmission for sporty applications. The close ratios combined with extremely spontaneous drive behavior makes it an ideal transmission for sporty applications. This article describes the compact gear set with lubrication by injection for improving the level of efficiency and increasing the engine-speed-strength, the dual clutch unit as well as the hydraulic control unit, which is based on the pre-control principle, are also described in detail. The hy-draulic control principle provides the option of a hydraulic cruise mode in the event of an electronics failure. In addition to the transmission design, functional features that also highlight the sporty character of the transmission are described in detail.Key words: Automatic transmission; Dual clutch; Vehicle connection; Efficiency1 IntroductionWhen it comes to the field of automatic transmissions, dual clutch systems currently represent the benchmark in terms of spontaneity and sportiness. In this type of transmission, which is based on a countershaft transmission, these advantages are combined with a very direct "vehicle connection", high rpm performance, and excellent transmission efficiency.The 7-speed dual clutch transmission for the standard driveline presented here is designed for a torque capacity of up to 520 Nm and rotational speeds of up to 9250 rpms. In order to be able to achieve these performance data in the existing installation space, a concept was developed in which an oil chamber as well as lubrication by injection are used. Before introducing the transmission′s several unique features in more detail below, an overview of the basic transmission design will be presented, Fig. 1.The engine torque is introduced to the dual clutch via a torsion damper (not shown in Fig. 1). The multidisk clutches in the dual clutch are radially nested in one another and transfer the torque to both input shafts in the countershaft transmission gear set. In this case, due to the installation space, the countershaft is not located under the main shaft, but is tilted laterally. This becomes possible because the concept is based on lubrication by injection with a dry sump. On the one hand, lubrication by injection improves heat removal, on the other, there are nonoticeable losses due to the gears splashing in the oil pan. The oil is supplied to the transmission via an internal gear pump which is driven by a spur gear train behind the dual clutch. With the help of a spur gear train, the drive unit has the advantage that, via different gear ratio phases and depending on the intended use, the flow rate and the max. speed of the pump can be adapted. An additional advantage is that based on theresulting I proved installation space, an optimal ratio between the pump width and the pump diameter can be achieved for the pump′s level of efficiency. The hydraulic control unit is arranged under the gear set. The hydraulic unit supplies the clutch, based on need, with pressure and cooling oil as well as shift actuators. The latter are arranged laterally to the gear set and work with double-acting cylinders. The sensor for detecting the position of the gearshifts is attached directly onto the four gearshifts. The transmission has an external control unit.Fig.1Overview dual clutch transmission (DCT)2 Seven speeds with sophisticated stepping-a concept for extrme sporti- nessThe gear set concept of the dual clutch transmission introduced here was developed in house taking into consideration the following requirements:High power densityHigh speed endurance strength up to 9250 rpm Variability and modular designRepresentation of transmission-ratio spreads of about 4.7 and 6.8 with 7 speedsUse of existing synergies for manual transmissionsAfter extensive systematic development of the gear set in which many thousands of variants were produced and compared, the gear set concept that is illustrated in Fig. 2 is the final variant and the ideal concept for achieving the goals specified.The gear set selected is based on the constant drive concept and consists of two concentric drive shafts each of which are driven by one of the two multidisk clutches in theFig.2Gear set scheme of 7D variantdual clutch, two countershafts also concentric to one another, a main shaft and an output shaft. The gear ratios are engaged by the four synchronizer units A/B, C/D, E/F, and G/H, which are arranged on the main shaft and on the hollow countershaft and these are connected to the loose wheels or the adjacent shafts. An important feature in the gear set is the connectability of both countershafts through the C/D synchronizer unit. In the D shift position, the gear ratios selected in this way can be doubly used which reduces construction costs compared to conventional dual clutch gear sets. Similarly, this feature is used in first gear because then the vehicle is started up using the more powerful K1 clutch. Because of this dual use of the last gear level in the transmission for the first and second gear, the desired ratio step 1-2 is achieved through the transmission ratios of both constant drive phases.The use of the K1 clutch for starting up in first gear results inevitably in the direct gear also being assigned to the odd subsection. In this case, the fifth and seventh gears can be selected as a direct drive. With this feature, it was possible to develop a modular gear set which, on just a few changes,contains two different transmission gear ratio variants with fundamentally different characters.For the first version, with an overall spread of about 4 . 7 , the seventh gear is selected as a direct gear (called the 7D variant). Fig. 2 shows the relevant gear set diagram with the performance flows in all speeds. Due to its sophisticated gear steps, this transmission is highly suitable for very sporty vehicles that need only a "little" transmission stepping due to the high rotating engine. Optimal tractive power can be provided at any time duringvehicle operation.The second version is based on the 7D variant, however, fifth gear was selected as the direct drive. When maintaining the torque multiplication ratio and in adapting the transmission ratio of several lower gear levels, you get the 5D variant with a considerably higher transmission-ratio spread for vehicles with increased comfort demands and simultaneously reduced consumption.Fig. 3 illustrates the design of the 7D variant. The main similarity with existing manual transmissions for standard transmissions is noticeable. Due to the compact gear set design, the sufficient shaft dimensioning and the favorable arrangement in proximity of the bearing of the high transmitting ratios, central bearing glasses were not necessary despite the proportionally large bearing clearance.Overall, only two housing bearing levels are necessary where the front level is located behind both constant gears. In addition, a very compact and inexpensive transmission design could be implemented based on the bearing concept selected, especially in the area of the hollow shaft.Fig.3Sectional Drawing of 7D variant3 The dual clutchThe central module of this highly topical transmission concept is the wet dual clutch. With a broad spectrum of technical features, it implements the functional provisions of the transmission control unit and thus distinguishes the special character of this transmission concept.Very fast delay times, low inertia and good, comfortable friction value progressions facilitate, very sporty handling with highly dynamic gear shifting and comfortable cruising at a high level of efficiency. The dual clutch placed directly on the transmission input accepts the engine torque from thtorsion damper and feeds it to one of the two subsections, depending on the situation.Safety considerations have led to a "normall open" design.The radial arrangement of the multidisk pack age represents the best combination of performanc and installation space need, Fig. 4.Fig.4Dual clutchCareful lining and oil selection as well as intensive enhancement of this tribological system are the requirements for comfort and performance of this clutch throughout its service life.Through intense testing and detailed calculations, it was possible to achieve a very high therma loading capacity. As part of the process, the lining type, dimensioning, and grooving as well as equal distribution of thermal load and oil flow in the multidisk package are decisive design features.Low torque drag even with low temperatures as well as high speed endurance strength support comfort and a high level of sportiness, but are also important safety requirements.Rotating, centrifugal force-compensating clutch cylinders with hysteresis optimized gaskets make the clutches easy to control. Integrated plate springs reliably accept rapid piston resetting even at high speeds.In the case of an open clutch, only transmission input shafts with very low additional mass inertia are used. This supports rapid synchronizing sequences and a long service life of the synchronizer units.4 The hydraulic control unitIn the present dual clutch transmission, the hydraulic control unit fulfills the following tasks:Actuating the dual clutchShifting the gearshifts, i. e. engaging/synchronizing the gearCooling the dual clutchGear lubricationEmergency stop function in case of complete failure of transmission electronicsSeveral features in the hydraulic control unit as well as criteria for the selection of the control concept are going to be described in more detail below.4.1 PerformanceThe use of the dual clutch transmission in sporty vehicles demands high performance from the hydraulic control unit, especially with regard to the first two tasks because the timely "handling" of these tasks come into play in gear shifting and gear shifting times.That is why particular value is placed on the selection of the right control unit concept as part of the system design. During the decision process, the choice was made, in principle, between two concepts, Fig. 5.Fig.5Control concept direct control / precontrolPrecontrol of the valvesDirect control of the valves (so-called cartridge valves)In case of direct control, the valve that is used for pressure control, e.g. a clutch, is directly connected to the power-generating proportional solenoids and provides the main pressure to the corresponding clutch pressure.The precontrol uses the pressure that is supplied by a pressure controller, for example, to actuate an additional valve that supplies the clutch pressure from the main pressure.To assess the performance of both concepts, a larger number of compared measurements were performed with different systems, of which two systems shall be considered here:ZF hydraulic control unit with precontrol for DCT standard driveComparative hydraulic control unit with direct controlA reference clutch was used as the clutch to engage. Criteria for assessing the performance were (see also Fig. 6):Fig.6Delay, increase/rise, and fall times. Red curve: Power /Electric current. Green curve: ClutchpressureDelay time, 1 to 4Time of step response until clutch inflation pressure, 1 to 2Time of the step response up to 90% of the main pressure 1 to 3Time of pressure drop (emptying times), 5 to 6Fig. 6 shows, as an example, the times for a transmission oil temperature of + 20°C to be reached. One notices that the direct control first in dicates a lower delay time (14.3 ms) compared to the precontrol (30.1 ms), see also time of brand 1to 4.For increase to clutch inflation pressure or to 90% of the main pressure shows, however, the advantage of the precontrolled system (see also summarizing tab 1).Emptying times, also present a disadvantage for direct control. Trans-mission oil temperature of -20°C also show comparable results for step responses and fall times.All of the tests support the statement that direct control has an advantageous effect with small oil volumes. However, if large oil volumes have to be transported, precontrol valves are to be preferred due to larger opening cross-sections.4.2 Operational safetyOperational safety is determined essentially due to the soiling tendency because the so-called silting can lead to the valves getting jammed. Provocation tests with transmission-specific environmental conditions (dirty oil) demonstrated the influences of soiling on the characteristic curves. Technical, trouble-free characteristic curve progressions could be illustrated only with a high dither amplitude in valve actuation, which leads, in turn, to increased valve wear-and-tear due to the micro movements that it causes. The increased tendency toward soiling can result needing a fine filter.4.3 CostsIn addition to the delay time comparison as well as assessing the operational safety, the costs were relevant for a final evaluation. The compari son with regard to the hydraulic and electro-mag netic components shows that a precontrol system has cost benefits compared to a direct control system. Added to this are the higher flows with the actuation of direct control valves, which, in turn, result in a more expensive TCU. Furthermore, in opting for precontrol, ZF is able to "pool" together pressure controllers in large quantities because these, too, are used in the automatic ZF planetary gear set.4.4 Emergency stop functionIn case there is a complete outage in the transmission electronics, a hydraulic emergency stop function is actuated in the transmission. The clutch that is pressurized with a larger amount of pressure in the event of a system outage will continue to be pressurized. This condition is maintained until an adjustable engine speed threshold is achieved, then the clutch opens in order to prevent the engine from being choked. It is not possible to re-start this system.5 Sporty functionsFor function developers, the dual clutch transmission offers the opportunity to combine the comfort of a stepped automatic transmission with the dynamics and sportiness of a countershaft transmission. Connected, therefore, are typical " catalog values," such as time from zero to 100 kilometers per hour or the time from 80 to 120 kilometers per hour with correspondingly fast kick-down shifting, but also subjective acceleration sensitivity during a shifting sequence where the purist among the manual transmission drivers still wants to feel that jolt of acceleration.One function especially designed for the dual clutch transmission in sports cars is the "race start"function. The race start is a function used to achieve optimal acceleration from astandstill, i.e. in the shortest time from 0 to 100 km/h. The sequence progresses as follows: The engine is brought to a suitably high rpm with the clutch engaged in first gear. The driver simultaneously actuates the brakes with the lef foot so that the clutch can already be lightly engaged and the gas pedal (full throttle) in order to bring the vehicle up to the target speed. By simultaneously pressing and holding an operating element, such as the selector lever or a push button on the steering wheel, the race start intention is conveyed to the system, the engine speed adjusted and the start up prevented until the driver releases the brake. During the race start, the clutch is closed under the control of the wheel slip with which the optimal acceleration is achieved and by exploiting the dynamic engine torque (inertia torque). The entire procedure progresses automatically once the driver releases so that even an inexperienced drivercan achieve the best possible drive performance figures. Obviously, the driver can cancel the procedure by removing his/her foot from the gas pedal or touching the brakes. Also, the system recognizes when the street conditions do not permit a race start, such as wet roads, for example. Due to the optimal start-up and a shifting sequence into second gear free of traction interruption (see also sports shifting), the race start function enables the acceleration time of 0 to 100 km/h to be improved by an average of 0.2 sec compared to a car with a manual transmission. At the same time, this functionality helps avoid improper use and resulting clutch overload.The top chart in Fig. 7 illustrates the engine and transmission input shaft speed, the lower chart shows the vehicle′s longitudinal acceleration. Starting with a cranking speed of 6,800 rpm, the clutch begins to close, which leads to an engine pressure up to about 4,000 rpm. The dynamic engine torque used to achieve this results in an acceleration of 0.7-0.9 g. In the process, noticeable vibrations in the transmission input shaft speed signal develop due to the wheel slip regulation. After about 1.2 sec, the vehicle is accelerated only by the engine torque with approx. 0.5 g. It must be mentioned here that this test was performed using a vehicle with very high traction. In most cases, a starting speed of only up to about 4,000 rpm is reasonable.A further function developed for the dual clutch transmission is so-called sports shifting. This is described in more detail below.In general, a gear-shift change by the driver is only perceived acoustically by the change in the engine speed. The transition from the acceleration level of the original gear toFig.7Measurement of a race starthe new gear should be made smoothly and continuously. This also corresponds to the standard shifting sequences in auto-matic and dual clutch transmissions. However, many drivers of sporty cars wish that they had the option of both distinctive comfort shifting sequences as well as sporty shifting sequences, which, besides the haptic response (acceleration jolt), also have an acceleration advantage as a result. To this end, the dynamic engine torque can also be used again. The requirement for this is the torque capacity of the dual clutch which has to be able to transmit this torque increase. As the possible torque increase depends on the gradients of the engine speed, this can be used particularly effectively in shifting gears with a large speed difference with the target gear (large ratio spread/ratio step), which is why the gear changes 1-2, 2-3, and 3-4 are offered. In the process, sports shifting from the frst to second gear can serve as a supplement to the ace start for improving the acceleration time from to 100 km/h. As the use of the dynamic torque is pure application topic, we distinguish, as a rule,between three shifting systems. Fig. 8 illustrates he stylized differences and features between the hifting systems, Fig. 9 shows an original measurement from a prototype vehicle.The top chart shows the respective engine and ransmission speed, the bottom chart shows the orques from both clutches. The bottom line in the hart represents the clutch from the target gear that is used to achieve the torque increase during engine sp eed adjustment and thereby acceleration gains.Fig.8Simplified depiction of acceleration procedures with Fig.9Measurement of sports shift 2-3 in the vehicle附录B外文文献翻译运动型7速双离合器变速器系统摘要:ZF公司的7速双离合器变速器是一款创新型的、适用于运动型车辆的变速器。
机械行业工具量具术语-中英文对照

中文名称 pressure machine vice parallel sets Tee-bolt washer magnetic tables magnetic handing engineer's files diamond riffler files burrs
英文名称
磁性工作台 磁性手柄 锉刀 金刚石修模锉刀 打磨头 打磨头和抛光头 纱布带 打磨片(磨砂片) 磨砂片 磨砂带片 硬毛打磨片(去毛刺刷) 通用研磨砂块 砂布薄片和附件 砂带 油石(磨石) 粗砂轮 砂轮 金属丝圆形打磨刷 钢丝刷(手用) 洗瓶刷、管道刷、钳工刷 毛刷 钢锯条 圆锯片 开口扳手 双端梅花双头扳手 套筒扳手 螺母扳手系列 螺丝起子 六角扳手 可调钩型扳手 套筒套装系列带有方形 电子扭力校正器 电子扭力扳手 扭矩扳手 带表盘扭矩扳手(数显式) 扭矩扳手(可调节) 扭矩扳手(快速的调节) 螺丝刀 VAE绝缘组合钳
序号中文名称虎钳pressuremachinevice垫圈washer磁性工作台magnetictables磁性手柄magnetichanding锉刀engineersfiles金刚石修模锉刀diamondrifflerfiles打磨头burrs10打磨头和抛光头grindingandpolishingpoints11纱布带sanderbands12abrasivediscflapdisc13磨砂片flapwheels14磨砂带片cleanandstripdiscs15bristlecleaningdiscstooling16通用研磨砂块universalabrasivecleaners17砂布薄片和附件sheetsofabrasiveclothandaccessories18linishingbeltsendless19油石磨石oilstoneshones20粗砂轮roughgrindingdisc21砂轮grindingwheels22金属丝圆形打磨刷circularwirebrushessteel23钢丝刷手用wirehandscratchbrushes24洗瓶刷管道刷钳工刷25毛刷paintbrushes26钢锯条hacksawblade27圆锯片circularsawbladescarbidetipped28开口扳手openendedspanners29双端梅花双头扳手doubleendedringspanners30套筒扳手boxspannerssocketwrenches31螺母扳手系列nutspannersetinwallet32螺丝起子screwdrivers33六角扳手hexagonkeylwrenchsets34可调钩型扳手adjustchookpinspanners35套筒套装系列带有方形socketsetswith14and12squaredrive36电子扭力校正器electronictorqueanalysers37电子扭力扳手electronictorquewrenches38扭矩扳手rotationalanglewrenches3940torquewrencheswithadjustmentscaleautomatictrigger41torquewrencheswithquickadjustment42螺丝刀bladescrewdrives43heavydutycombinat
rca滚环复制原理

rca滚环复制原理The RCA (Radio Corporation of America) drum is a unique and innovative mechanism used in early television and computer systems for the purpose of storing and reproducing images and data. The drum consists of a rotating cylinder with a magnetic coating, onto which the information is written and read. The principle behind the RCA drum's operation is based on the concept of magnetic recording and playback. When information is written onto the drum, the magnetic particles on the surface of the drum become aligned in a specific pattern, representing the data. When the drum rotates and the information is read, the magnetic particles' alignment is detected and converted back into the original data.The process of duplicating information using the RCA drum involves several key steps. First, the original data is written onto the drum using a magnetic recording head, which applies a magnetic field to the drum's surface, aligning the magnetic particles according to the data. Oncethe information is stored on the drum, it can be reproduced by rotating the drum and using a magnetic playback head to detect the alignment of the magnetic particles and convert it back into the original data. This process allows for the replication of the original information, as the magnetic alignment on the drum's surface can be read and used to recreate the data.One of the key advantages of the RCA drum's replication principle is its ability to store and reproduce information in a relatively compact and efficient manner. Unlike other storage and replication methods of the time, such as tape-based systems, the RCA drum offered a higher data density and faster access times, making it a popular choice for early television and computer systems. Additionally, the ability to duplicate information using the drum allowed for the creation of multiple copies of the same data, enabling widespread distribution and sharing of content.From a technical perspective, the RCA drum'sreplication principle relies on the precise alignment and detection of magnetic particles on the drum's surface. Theaccuracy and consistency of the magnetic recording and playback heads are crucial to ensuring the faithful reproduction of the original data. Additionally, the speed and stability of the drum's rotation play a critical rolein the successful replication of information. Anydeviations or inconsistencies in these factors can resultin errors or data corruption during the duplication process.In conclusion, the RCA drum's replication principle isa fundamental concept in the storage and reproduction of information in early television and computer systems. By leveraging the principles of magnetic recording and playback, the drum allows for the efficient duplication of data, enabling widespread distribution and sharing of content. The technical aspects of the replication process, including the precision of the recording and playback heads, as well as the stability of the drum's rotation, arecrucial to ensuring the accurate reproduction of theoriginal information. Overall, the RCA drum's replication principle represents a significant advancement in thehistory of data storage and replication technology.。
(完整版)农机专业英语

第一单元assembly drawing 装置图balloon 零件序号detail drawing零件图view视图convention规范patternmaker模型工machinist机械工carftsman工人full -section view全剖视图sketch drawing草图broken -sectional view 局部视图cutting -plane剖切面Internchangeable可交换的exploded drawing分解示图第五单元pulley滑轮torque扭矩sheave 槽轮disassembly 分解spline 花键axle 轮轴woodruff key 月牙键bushing 轴衬Involute spline 渐开线花键spindle 主轴groove 沟residual stress 剩余应力coupling 联轴器distortion 变形misalignment 非对中referred to as第六单元component零件chassis底盘transmission变速器lubrication润滑ignition点火装置carburetor化油器combustible易燃的hood 发动机罩capacity生产量suspension悬架differential差速器clutch离合器hydraulic液压的pedal 踏板spark-ignition engine点燃式发动机storage battery蓄电池charging circuit充电电路motor oil机油sheet metal金属板gnition coil点火线圈compression -ignition engine压燃式发动机第九单元small volume production小批量生产screw 丝杆servo motor 伺服电机saddle 滑板bedway 导轨shuttle 梭子conventional 一般的、惯例的horizontal 卧式的vertical 立式的spindle 轴第十五单元computer -integrated manufacturing 计算机集成制造automatic storage and retrieval systems 自动储存和检索系统database 数据库integrity完好性、完好第十六单元deploy 使用、配置mineral deposit矿床manipulator 机械手joint 接头、接合处gripper 钳子roll 转动articulated 相关节的、铰接的hydraulic actuator液压制动器link连杆。
意维丝铜线资料

4
ESSEX ITALY
Superior Essex Inc. is one of the largest wire and cable manufacturers in the world. The Essex European Group is a world leader in the field of wires for electrical equipment windings. The product range is exceptionally wide and ranges from fine enamel-coated wires to large conductors for transformers. Its considerable industrial strength has been traditionally oriented towards the technological development and service to customers. This effort is the strongest guarantee of an increasingly wider co-operation with customers and of a far-reaching international future. ESSEX is internationally present through a wide marketing and distribution organisation, with the complete range of magnet wires and a well known record for products quality, process technology and customer service.
FESTO旋转驱动器ERMS系列产品介绍说明书

Rotary drive units ERMSThis product is also available as a modular mechanical systemRotary drive ERMO2d Internet: /catalogue/...Subject to change – 2023/06Rotary drive units ERMSKey featuresAt a glancePlug and work with the Simplified Motion SeriesThe simplicity of pneumatics is now combined for the first time with the advantages of electric automation thanks to the Simplified Motion Series.These integrated drives are the perfect solution for all users who are looking for an electric alternative for very simple movement and positioning tasks between two mechanical end positions, but don't want the commissioning process for traditional electric drive systems that can often be quite complex. There is no need for any software since operation is simply based on the "plug and work" principle. Digital I/O (DIO) and IO-Link are always automatically included – a product with two types of control as standard.IntegratedEasyStandardisedConnectedThe integrated electronics in the drive are at the heart of the Simplified Motion Series.For commissioning, simply set all rele-vant parameters directly on the drive:• Speed and force• Reference end position and cushioning• Manual operationElectrical connection via M12 plug design• Power (4-pin): power supply for the motor• Logic (8-pin): control signal, sensor signal and power for the integrated electronicsUse of extended functions possible via IO-Link:• Remote configuration of motion parameters• Copy and backup function for transferring parameters• Read function for extended p rocess parameters• Freely definable intermediate position• Firmware updateThe functions of the Simplified Motion Series Basic profile for movement between two end positions: Extended motion profile for simplified press-fitting and clamping functions: v v• • Proximity switches are required in order to implement any intermediate positions.• With the intermediate position that can be freely configured via IO-Link, movements can be stopped at a freely defined point between the end positions, without the need for proximity switches or external stopsRotary drive units ERMS Key featuresAt a glance• Without external servo drive: all the necessary electronic components arecombined in the integrated drive• Two control options integrated as standard: digital I/O and IO-Link• Complete solution for simple movements between mechanical end positions• Simplified commissioning: all parameters can be manually set directly on thedrive• No special expertise required for commissioning• End-position feedback similar to that of a conventional proximity switch isintegrated as standard• Sealed hollow shaft for the integrated through-feed of cables and tubing• Standardised mounting interface for direct connection to the electric minislides EGSL, EGSC and EGSSThe products in the Simplified Motion SeriesElectric cylinder unitEPCEElectric cylinder unitEPCSElectric cylinder unit with parallelmotor mountingEPCSMini slide unitEGSS-BS-KFMini slide unit with parallel motormountingEGSS-BS-KFSpindle axis unitELGS-BS-KFSpindle axis unit with parallel motormountingELGS-BS-KFToothed belt axis unitELGS-TB-KFToothed belt axis unitELGERotary drive unitERMSModular and flexible with motor, motor mounting kit and servo driveThis product is also available within the Optimised Motion Series as rotary drive ERMO:Rotary drive and motor in one unit. Compact and powerful rotating and swivelling with no limits. S turdy and precise thanks tobacklash-free ball bearing.• Rotary drive in 4 sizes for torque of up to 5 Nm• Hollow shaft for energy through-feed for attachments• Optional pneumatic or electric energy chain• Optional proximity switch for homing or position sensing• Holding brake optional• Modular: individual combinations with servo drive3 2023/06 – Subject to change d Internet: /catalogue/...Rotary drive units ERMSKey features4d Internet: /catalogue/...Subject to change – 2023/06Rotary drive units ERMS Type codes5 2023/06 – Subject to change d Internet: /catalogue/...6d Internet: /catalogue/...Subject to change – 2023/06Rotary drive units ERMSPeripherals overviewCable outlet direction Standard[L] Left [R] RightControl elements[1] Pushbutton actuators for parameterisation and control72023/06 – Subject to changed Internet: /catalogue/...Rotary drive units ERMSPeripherals overview8d Internet: /catalogue/...Subject to change – 2023/06Rotary drive units ERMSDatasheet-N- Size 25, 32-Y-Rotation angle 90°, 180°1) Adjustable increments of 10%2) Unchangeable parameter 3) Without load in new condition92023/06 – Subject to changed Internet: /catalogue/...Rotary drive units ERMSDatasheetRotary drive units ERMSDatasheet10d Internet: /catalogue/...Subject to change – 2023/06Rotary drive units ERMSDatasheetMaterials Sectional viewPin allocation Power supplyLogic interfacePlugPlugRotary drive units ERMSDatasheetSizing exampleApplication data:• Mass moment of inertia: 100 kgcm2• Mounting position: horizontal• Rotation angle: 180°• Max. permitted positioning time: 1 s (one direction)Step 1: Selecting the possible size from the table a page 890°180°a Max. speed level for payload: level 10a Min. positioning time for 180° at level 10: 0.5 sResultThe application can be implemented using ERMS-32-180. A minimum positioning time (one direction) of 0.5 s is achieved. Longer positioning times can be selected at any time using a lower speed level.Rotary drive units ERMS DatasheetMass moment of inertia m as a function of speed level vSize 25Size 32Positioning time t as a function of speed level v and rotation angleSize 25Size 3290°180°90°180°Torque M as a function of force level F1ERMS-25ERMS-32Rotary drive units ERMSDatasheetMax. permissible axial and radial force Fx/FzMax. dynamic axial force F x as a function of lever arm lMax. dynamic radial force F z as a function of lever arm lERMS-25ERMS-32ERMS-25ERMS-32Rotary drive units ERMS DatasheetAxial eccentricity and concentricityAxial eccentricity ConcentricityMeasured on the surface of the rotating plate at the plate edge, in new condition.Measured at the centring hole of the rotating plate, when new.Rotary drive units ERMS DatasheetRotary drive units ERMS DatasheetRotary drive units ERMS Ordering dataRotary drive units ERMS Ordering data – Modular product systemRotary drive units ERMS Accessories1) Packaging unit212023/06 – Subject to change d Internet: /catalogue/...Rotary drive units ERMS Accessories。
产品零件英语
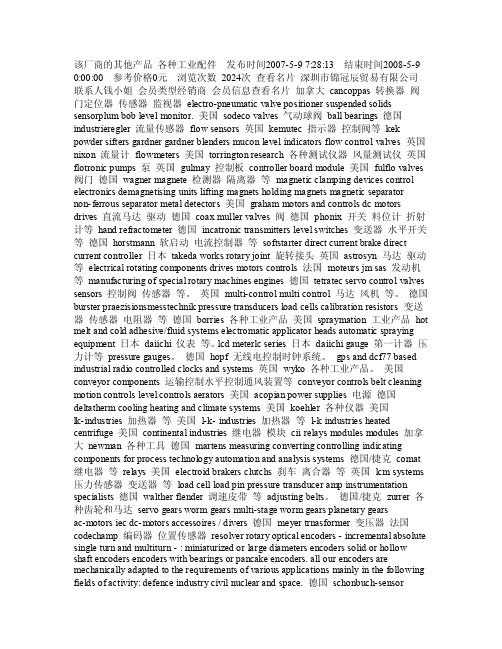
该厂商的其他产品各种工业配件发布时间2007-5-9 7:28:13 结束时间2008-5-9 0:00:00 参考价格0元浏览次数2024次查看名片深圳市锦冠辰贸易有限公司联系人钱小姐会员类型经销商会员信息查看名片加拿大cancoppas 转换器阀门定位器传感器监视器electro-pneumatic valve positioner suspended solids sensorplum bob level monitor. 美国sodeco valves 气动球阀ball bearings 德国industrieregler 流量传感器flow sensors 英国kemutec 指示器控制阀等kek powder sifters gardner gardner blenders mucon level indicators flow control valves 英国nixon 流量计flowmeters 美国torrington research 各种测试仪器风量测试仪英国flotronic pumps 泵英国gulmay 控制板controller board module 美国fulflo valves 阀门德国wagner magnete 检测器隔离器等magnetic clamping devices control electronics demagnetising units lifting magnets holding magnets magnetic separatornon-ferrous separator metal detectors 美国graham motors and controls dc motors drives 直流马达驱动德国coax muller valves 阀德国phonix 开关料位计折射计等hand refractometer 德国incatronic transmitters level switches 变送器水平开关等德国horstmann 软启动电流控制器等softstarter direct current brake direct current controller 日本takeda works rotary joint 旋转接头英国astrosyn 马达驱动等electrical rotating components drives motors controls 法国moteurs jm sas 发动机等manufacturing of special rotary machines engines 德国tetratec servo control valves sensors 控制阀传感器等。
约翰逊电机产品说明书
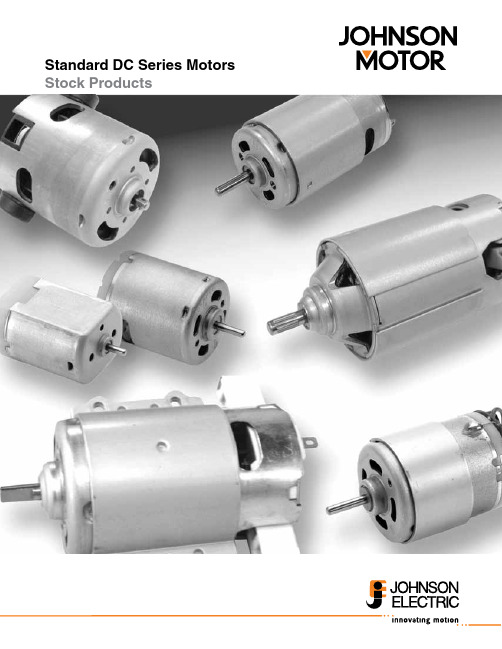
Standard DC Series Motors Stock ProductsJohnson Electric is the global leader in Micro motors, Motion Sub-systems, Human Machine Interfaces, and Infrastructure Control Systems.We serve a broad range of industries including Automotive, Business Equipment, Building Automation, Home Technologies, Medical Devices, Power Tools, Optical Devices and Industrial Automation.Established in 1959, Johnson Electric ships its products to more than 30 countries for use in hundreds of different product applications. Innovation and product design centers are located in Hong Kong, China, Switzerland, Germany, Italy, Israel, Japan, the UK and the USA. We employ more than 40,000 employees in over 23 countries.The Group’s business strategy is based on the twin pillars of providing “technology leadership” and being the “safe choice” for our customers. We support our long term customers through their complete product life from new product introduction to mature high volume production. Our customers’ newproducts and new growth segments are addressed by providing technically differentiated new products and superior service.Our unique “Productizing Process” and the “Johnson Electric Production System” combine to deliver product differentiation and supply chain performance to our customers. Johnson Electric is the safe choice for global brand companies that demand performance leadership, high reliability, and assurance of supply.The Company has been listed on the Stock Exchange of Hong Kong since 1984, and has a sponsored American Depositary Receipt (ADR) program in the USA.JohnSon eleCtriC CoMPany ProfileinDuStry ProDuCtS GrouPIndustries ServedThe Industry Products Group (IPG) provides motion products and customized solutions for various commercial and industrial applications, including home appliances, power tools, business equipment, personal care products, building automation, security, audio-visual and other industrial products.The IPG product line comprises the following brands: Johnson Motor for DC motors (Standard DC, Compact DC, and brushless DC product lines), and AC motors; Saia Motor for stepper motors and synchronous motors; Ledex and Dormeyer for solenoids; and Saia, Bär, Burgess, th-contact forswitches.Building Automationand SecurityBusiness MachinesCamera and OpticalFood and BeverageEntertainment andGamingHome TechnologiesIndustrial AutomationSnow BlowersHVACPersonal CarePower Equipment Medical DevicesThe data used in this Product Overview may be used as a guideline only. Specific operational characteristics of our products may vary according to individual applications. It is strongly recommended that specific operating conditions are clarified with Johnson Electric before application. JohnsonElectric Terms and Conditions of Sale apply. All data may be subject to change without notice.Standard DC Series - Low Voltage DC MotorsPage Dia. (mm)DC Motor PlatformInput Voltage (V)No Load Speed (rpm)Maximum Efficiency (%)Stall Torque (mNm)Maximum Output Power (W)Application Examples Part Number Series Standard DC Series - High Voltage DC MotorsPage Dia. (mm)DC Motor PlatformInput Voltage (V)No Load Speed (rpm)Maximum Efficiency (%)Torque @ Maximum Efficiency (mNm)Speed @ Maximum Efficiency (rpm)Application Examples Part Number Series200200 249Ø 20.0 – 24.9 mm200 249200 249Ø 20.0 – 24.9 mm200 249Ø 20.0 – 24.9 mm200 249Ø 20.0 – 24.9 mm200 249Ø 20.0 – 24.9 mm200 249Ø 20.0 – 24.9 mm250 299Ø 25.0 – 29.9 mm250 299Ø 25.0 – 29.9 mm250 299Ø 25.0 – 29.9 mm250 299Ø 25.0 – 29.9 mm250 299Ø 25.0 – 29.9 mm250 299Ø 25.0 – 29.9 mm250 299Ø 25.0 – 29.9 mm250 299Ø 25.0 – 29.9 mm250 299Ø 25.0 – 29.9 mm400 449Ø 40.0 – 44.9 mm450 499Ø 45.0 – 49.9 mm450 499Ø 45.0 – 49.9 mm450 499Ø 45.0 – 49.9 mm450 499Ø 45.0 – 49.9 mmHC615SG-011High Voltage DC Motors350 399。
容积式热交换器工作原理与结构
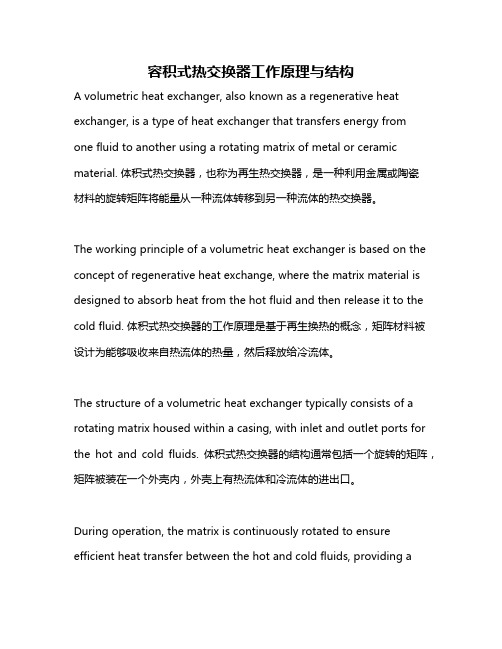
容积式热交换器工作原理与结构A volumetric heat exchanger, also known as a regenerative heat exchanger, is a type of heat exchanger that transfers energy fromone fluid to another using a rotating matrix of metal or ceramic material. 体积式热交换器,也称为再生热交换器,是一种利用金属或陶瓷材料的旋转矩阵将能量从一种流体转移到另一种流体的热交换器。
The working principle of a volumetric heat exchanger is based on the concept of regenerative heat exchange, where the matrix material is designed to absorb heat from the hot fluid and then release it to the cold fluid. 体积式热交换器的工作原理是基于再生换热的概念,矩阵材料被设计为能够吸收来自热流体的热量,然后释放给冷流体。
The structure of a volumetric heat exchanger typically consists of a rotating matrix housed within a casing, with inlet and outlet ports for the hot and cold fluids. 体积式热交换器的结构通常包括一个旋转的矩阵,矩阵被装在一个外壳内,外壳上有热流体和冷流体的进出口。
During operation, the matrix is continuously rotated to ensure efficient heat transfer between the hot and cold fluids, providing ahigh level of thermal energy recovery. 在运行过程中,矩阵会不断地旋转,以确保热流体和冷流体之间的高效换热,提供高水平的热能回收。
SIEMENS Process Compressors

Process Compressors Designed to optimize your businessAnswers for energy.A wide range of products and a wealth of experienceWith our unrivalled competence in comple-te compressor train solutions from a single source, Siemens offers an extensive range of standard or customized compressor solutions (Siemens Turbocompressors – STC TM ). Our standard units with predefi-ned engineering options ensure low in-vestment costs and short delivery times. For the more complex processes such as Gas-to-Liquids (GTL), Coal-to-Liquids (CTL), methanol and integrated gasification com-bined cycle plants (IGCC), we provide a uniquely tailored solution.Air separation, petrochemical plants & refi-neries, catalyst regeneration and synthetic fiber production are amongst the most common applications for our compression solutions.Catering for mega-scale applications As a technology of the future, GTL is worth a mention in its own right. This complex process demands a considerable variety of very large rotating machinery.Siemens offers compression and power generation packages for air separation, the syngas process and the refinery pro-cess with its own steam turbine, gas tur-bine or electric motor drive.Siemens has successfully supplied the largest air compressors and the largest mechanical drive steam turbines ever made. This experience makes Siemens the partner of choice for all compression and power requirements in all sections of the GTL process up to a complete power island.Siemens offers a full range of turbocompressors to meet the needs of the oil and gas and process industries: in-line, axial or axial-radial, or integrally geared compressors can be matched with a range of drivers – steam turbine, gas turbine or electric motor – in a solution to match each unique customerTurbocompressors from Siemens – covering the complete spectrum1. STC-SRSiemens axial-radial flow compressor 2. STC-SXSiemens axial flow compressor3. STC-SVSiemens single-shaft centrifugal compressor with vertically split casing 4. STC-SHSiemens single-shaft centrifugal compressor with horizontally split casing1. 2. 3. 4.5.6.7.8.5. STC-SPSiemens single-stage axial inlet overhung centrifugal turbocompresor6. STC-GCSiemens compact integrally geared centrifugal turbocompressor7. STC-GVSiemens integrally geared centrifugal turbocompressor8. STC-GTSiemens integrally geared process gas radial turbineThe optimum solution for blast furnace air The STC-SX series are axial-flow compressors designed to handle large volume air flows and other clean gases within relatively small casings. This axial-flow turbocompressor is typically an uncooled straight-through compressor, designed for discharge temperatures up to 350°C. Out-standing blading technology and unique material usage result in optimized performance and reliability.Technical data• Flow rates from 50,000 to 1,300,000 m3/h• Pressure ratio between 1.9 and 6.0• Driver of your choiceFields of application• Blast furnace air• FCC air (Fluid Catalytic Cracking)Features• Excellent efficiency• Modular design principle• Extended operation range• Highest quality standards• Casings with axial inlets• Up to 19 axial compression stages The allrounderThe STC-SV is a single-shaft centrifugal compressor with vertically split barrel-type casing, designed for direct drive concepts in accordance with API 617. All compressor internals are assembled into one bundle for easy installation and maintenance. The STC-SV allows for perfect matching of compressor performance and rotor dynamics and is the per-fect solution to compress gases of any molecular weight.The single-stage STC-SV (S) is a packaged-unit concept – compressor, driver and auxiliaries form one single lift unit which facilitates transport and reduces site installation work to a minimum. Technical data• Flow rates from 250 to 480,000 m3/h• Discharge pressure up to 1,000 bar• Driver of your choiceFields of application• On/offshore oil and gas• Petrochemicals• Methanol• Natural gas distribution and storage• Refineries• Fertilizers• FPSOFeatures• Wide variety of sealing systems• Can be operated with any drive system• High part-load efficiencies• Suitable for light gases and high pressures• Can be designed for up to four process stages and with up to 10 impellersThe perfect match for large air volume flows Siemens STC-SR axial-radial isothermal turbocom-pressors are the perfect solution to handle large volume air flows whilst maintaining excellent efficiencies.The STC-SR series is ideal for applications requi-ring higher pressure ratios and intercooling. The design incorporates an axial process stage follo-wed by one or more centrifugal process stages. STC-SR compressors combine excellent efficiency with highest quality due to proven components and compliance with API standards.Technical data• Flow rates from 50,000 to 1,300,000 m3/h• Pressure ratio between 5.8 and 16• Driver of your choiceFields of application• Large-volume air separation plants e.g. for– GTL (Gas-to-Liquids)– CTL (Coal-to-Liquids)– MethanolFeatures• Highest degree of efficiency• Modular design principle• Also available with overhung design• Up to 10 axial and 3 radial compression stagesThe comprehensive portfolioSTC-SR STC-SVSTC-SXRobust and dependableThe STC-SH is a centrifugal compressor with hori-zontally split casing. All compressor internals are easily accessed by simply lifting the upper casing. The flexible single-shaft STC-SH compressors are designed according to API 617 and can be used for most process applications and a wide range of gases of any molecular weight, including toxic and hazardous applications.Technical data• Flow rates from 500 to 480,000 m3/h• Discharge pressure for oxygen and inert gas up to 100 bar• Discharge pressure for other process gases up to 50 bar• Driver of your choiceFields of application• On/offshore oil and gas• Petrochemicals• Fertilizers• Olefins• Refineries• General chemicals• Dry chlorine gasFeatures• Flexible design concept• Wide variety of sealing systems allowingdry-dry (oil-free) operation• Can be operated with any drive system• High part-load efficiencies• Can be designed for up to four process stages and with up to 10 impellers Efficient operation and maintenanceThe STC-SP is a single-stage axial inlet overhungcentrifugal compressor, designed in accordancewith API 617. It offers a wide operating rangethanks to its custom-designed impellers andvaneless diffusers. STC-SP is designed for easymaintenance, the rotor cartridge being accessiblewithout disassembly of the process pipe work.The standard ranges ensure highest reliability,quick availability and cost efficiency.STC-SP (P) is a well-proven fully parametric aero-dynamic design concept that allows the perfectmatching of compressor performance and rotordynamics for any pipeline application.Technical data• Flow rates from 200 to 130,000m3/h• Pressure ratio 1.01-1.45 depending on gascharacteristics and driver speed• Casing pressure ratings up to 50 bar• Driver of your choiceFields of application• Polyethylene plants• Polypropylene plants• Gas boosting• Ethylene oxide plants• Ethylene glycol plants• Oxo plantsFeatures• Advanced dry-gas sealing– With oil-lubricated bearings (dry-wet)– With active magnetic bearings (dry-dry)• Adjustable inlet guide vanes to improvepart-load performance• Barrel-type designThe compact solution for air separationThe STC-GC is an integrally geared compactturbocompressor available in several differentframe sizes and with a wide range of options ina compact single-lift unit. The STC-GC series isthe standard version of the customized integral-ly geared compressor series STC-GV, the trustyworkhorse of the air separation and processindustries.Technical data• Flow rates from 3,600 to 120,000m3/h• Pressure ratio up to 20• Driver: Electric motorFields of application• Air separation• Compression of process air• Compression of nitrogenFeatures• Standardized design• Standardized, pre-engineered components foreconomy and reliability• Compact, single-lift unitSTC-GCSTC-SHSTC-SPProven concept for direct power recovery The STC-GT is an integrally geared process gas radial turbine used for direct power recovery. Medium or high-temperature gas can be used di-rectly to drive a compressor or electric generator without additional heat exchange or steam gene-ration equipment. STC-GT’s sophisticated design is in accordance with both API 617 and API 672.Technical data• Discharge volume from 3,000 to 600,000 m 3/h • Expansion ratio 4Fields of application• Synthetic fibers, especially – Pure Terephthalic Acid (PTA) – Dimethyl Terephthalate (DMT)• Nitric acidFeatures• Adjustable inlet nozzle for economic part-load operation• Uses many of the proven components from the integrally geared centrifugal compressor concept• Radial inlet to each stageThe robust multitalentThe STC-GV integrally geared centrifugal com-pressors feature a multi-shaft arrangement with different speeds and up to eight compressor stages around a central bull gear, forming acompact unit for the multi-stage compression of a wide range of gases. These trains are typically supplied as complete packages, including all rota-ting equipment, intercoolers and oil console.With STC-GV (S), the GV turbocompressor is also available with one single-stage spur gear resul-ting in minimized installation site work.The STC-GVT is an integrally geared multi-stage compressor comprising expander stages, designed in accordance with both API 617 and API 672.Technical data• Flow rates from 800 to 480,000m 3/h • Discharge pressure up to 100 bar • Driver of your choice Fields of application • Air separation • Hydrocarbons • Ethylene oxide • Refineries• Ammonia• Synthetic fibers • Petrochemicals• Metal makingFeatures STC-GV• High efficiency due to tailored aerodynamics • Wide operating range due to adjustable guide vane units• Multi-service capability due to finely-graded standard components• Package design significantly reduces on-site installation time• Up to eight compression stagesFeatures STC-GVT• Inlet guide vane unit in front of each stage• Interheating between each stageSTC-GTSTC-GV/STC-GVTIndustrial steam turbines – the ideal drive for process industrySiemens steam turbines (SST™) are the ideal driver for process industries with exothermic processes where the heat can be used to generate steam. Steam turbines can be used in a multitude of ways to generate electrical energy or to drive compressors, blowers and pumps. Some fifty percent of the compressors used in cracking and refining processes are driven by steam turbines.As a solution provider for the petro-chemical industry, Siemens satisfies more customers of high power me-chanical drive steam turbines thanany other manufacturer.We offer not only the steam turbine, but also the associated field-proven high-tech products, including instrumentation and controls and various auxiliary systems.Industrial gas turbines – indefatigableand flexible pipeline driversSiemens gas turbines (SGT™) are theobvious choice of driver where naturalgas is available to fuel the turbine. Thegas turbine is thus the driver of choice forpumping and compression for pipe-line gas transportation. It also has theadvantages of being compact and light-weight for installation on offshore plat-forms. The gas turbine also can be usedto generate electricity to power an elec-tric motor, as is frequently the case onFloating Production, Storage and Off-loading (FPSO) vesselsElectric motors – the individual drivesolutionWhere energy has to be purchased – i.e.there is no source of natural gas or steamarising from the process – electric motorsare the clean and economical alternative.The increasing significance of powersaving, environmental requirements andthe desire for a wide variable speed bandhave led to the application of electricmotors.This has resulted in our individual drivesolution for specific customer require-ments in the industry sector.An important application for this variablespeed electric drive is for refrigerationcompressors in Liquefied Natural Gas(LNG) plants, the first such “all-electric”drive system having been successfullybuilt and tested in 2003. Electric drivesystems of this class are always customengineered for the customer’s specificapplication, allowing the compressor tobe optimized in capacity and speed forthe process on hand.From our comprehensive portfolio ofcompressors and drives we can recom-mend the exact configuration that bestsuits your project requirements.The driver of choice From our comprehensive portfolio of compressors and drives we can recommend the exact configuration that best suits your project requirements.Published by and copyright © 2008: Siemens AGEnergy SectorFreyeslebenstrasse 191058 Erlangen, GermanySiemens AGEnergy SectorOil & Gas DivisionWolfgang-Reuter-Platz47053 Duisburg, GermanySiemens Energy, Inc.10730 Telge RoadHouston, Texas 77095, USAFor more information, please contactour Customer Support Center.Phone: +49 180 524 70 00Fax: +49 180 524 24 71(Charges depending on provider)E-mail:**************************Oil & Gas DivisionOrder No. E50001-G420-A109-V3-4A00 Printed in GermanyDispo 05400 c4bs No 1388, 4497 S WS 10085. Printed on elementary chlorine-freebleached paper.All rights reserved.Trademarks mentioned in this documentare the property of Siemens AG, its affiliates,or their respective owners.Subject to change without prior notice.The information in this document containsgeneral descriptions of the technical optionsavailable, which may not apply in all cases.The required technical options should thereforebe specified in the contract./energy。
Handy-Mag I 手提磁铁手册说明书

474 E. 105th StreetCleveland, OH 44108-1378(216) 681-7400 • Fax (216) 681-7009 • ****************************800-446-4402Table of ContentsWarranty ................................................................................................................1Safety Precautions ................................................................................................2General Information ...............................................................................................3Specifications ........................................................................................................3Grounding Instructions/Extension Cords ...............................................................4Getting Started ......................................................................................................5Before the Cut .......................................................................................................6Making the Cut ......................................................................................................7After the Cut ..........................................................................................................7Maintenance ..........................................................................................................8Troubleshooting .....................................................................................................9Parts List.........................................................................................................10-11Parts Breakdown . (13)Handy-MagIGeneral InformationThe Cleveland Steel Tool Handy-Mag I is a lightweight, compact drilling system that features:•A capacity up to 1-1/2" diameter through 2” material*Drilling stacked material requires a special STACKED GEOMETRY cutter.• Positive slug ejection system• Internal cutter lubrication for increased tool life• Powerful motor with cast aluminum housing• Adjustable motor slide ways• Complete coolant system• Safety Chain• Chip shield• Rugged carrying caseSPECIFICATIONS:• Annular cutter range: 7/16” thru 1-1/2”• Annular cutter depth range: 0-2”• Twist drill capacity: 1/2”• Weight: 26 lbs.• Height: 15”• Voltage: 110v AC only, 10 amps, 1200 watts, earth ground & double insulation• Frequency: 50-60 HZ• RPM No Load: 550 RPM• Magnetic Holding Deadlift: 2200 lbs.• Magnet dimensions: 6-1/2" x 3" footprintWarning:Improperly connecting the grounding wire can result inthe risk of electrical shock. Check with a qualified electri-cian if you are in doubt as to whether the outlet is properly grounded. Do not modify the plug provided with tool. Never remove the grounding prong from the plug. Do not use tool if the cord or plug is damaged. Have it repaired before using. If the plug will not fit the outlet, have a proper outlet installed by a qualified electrician. The Handy-Mag I must be plugged into an appropriate outlet, properly installed and groundedin accordance with all codes and ordinances. The rigid ear or lug extending from the adapter must be connected to a permanent ground such as a properly grounded outlet box or receptacle. Simply remove the center screw from the outlet,insert the adapter and reattach the screw through the greengrounding ear to the outlet. If in doubt of proper grounding, call a qualified electrician.Extension CordsUse only 3-wire extension cords that have 3-prong ground-ing type plugs and 3-pole receptacles that accept the tool’s plug. Replace or repair damaged cords. Make sure your ex-tension cord is in good condition. When using an extension cord, be sure to use one heavy enough to carry the current your product will draw. An undersized cord will cause a drop in line voltage resulting in loss of power and overheating. If in doubt, use the next heavier gage. The smaller the gage number, the heavier the cord.Drip Loop: To help prevent fluids from travel-ing the power cord and contacting the powersource, tie a drip loop in the power cord.Getting StartedYour Handy-Mag I package should contain the following parts:QTY Part# Description1 Handy-Mag I1 Carrying Case1 Owners Manual1 MEHTA44 Chuck Adapter1 MEHTA51 1/2" Chuck1 ME3517 Coolant connector1 ME3542 Coolant Tank1 ME3544 Coolant Tube3 ME3562 Crank Handle1 ME3577 Wrench 8mm1 ME3578 2.5mm Hex Key1 ME3579 4mm Hex Key1 ME3582 Safety Guard1 ME3583 Safety ChainAssemble 3 crank handles (ME3562) to the crank spindle (ME3561). The crank spindle is mounted on the right side of the machine frame, if necessary it can be reversed for lefthand operation. Attach the coolant tube (ME3544) to the coolant tank (ME3542). Attach coolant tube (ME3544) to coolant connector (ME3517).What You Need To KnowType of material to be drilled, Brinell or Rockwell hardness, material thickness and position should all be determined to ensure proper selection of Handy-Mag I cutting tools, RPM, coolant and drilling time.Remove any excessive mill scale or rust from the surface to be drilled.When drilling materials under 3/8” thick, an additional steel plate may be required to achieve proper magnetic adhesion.Drilling stacked material requires a special STACKED GEOMETRY cutter.Material that has been flame cut may have become heat treated and therefore difficult to drill. Avoid drilling near such areas whenever possible.Drilling with the Handy-Mag I in horizontal positions requires a special lubrication for Handy-Mag I cutters. Consult The Cleveland Steel Tool Co. for details.Before the Cut1. Select the correct pilot pin and place it in the cutter shank from the rear. Align the flats on the cutter shank with the arbor body set screws. Insert cutter shank into the arbor body.2. Tighten the set screws securely on the cutter shank flats. Note: The set screws should be recessed in the arbor body when tight.3. Place the Handy-Mag I machine on work piece with pilot pin over the center of hole to be drilled.4. Connect machine to power source.5. Lower Handy-Mag I cutter to surface of material to be cut. Fill coolant tank with a water soluble cool-ant. Open coolant tap (ME 3543) to release coolant. Note:Coolant flow starts when pilot pin contacts work surface. Coolant flow can be stopped by lifting pin off work surface.6. Safety chain must be securely fastened to machine and around the work being drilled. Note: Safety chain is intended only to secure drill to work piece in case of emergency, such as a loss of power to the magnetic base.7. Attach safety guard (ME 3582) to machine with butterfly screws (ME 3581) and washers.Caution!Do not use the Handy-Mag I for work other than it’s intended use. The Handy-Mag I is designed to work only with the tooling provided.Use of other tooling may cause damage to the drill, cause personal injury and void the warranty.CAUTION: Always use safety chain. Failure to do so could result in personal injury and/or damage to the Handy-Mag I drilling machine.⇨Changing the Arbor to Optional Drill ChuckTo convert the Handy-Mag I from annular cutters to twist drill chuck: 1. Unscrew arbor (ME3502) from motor spindle.2. Remove the 3 arbor support screws and the arbor support bracket (ME3573).3. Fit chuck adapter (MEHTA44) and drill chuck (MEHTA51) to motor spindle.NOTE: Store arbor and arbor support bracket in the carrying case. To convert back to annular cutters, reverse the process.Making the CutCAUTION: Always use chip shield.1. Move magnet switch to “On” position, panel lamp should illuminate indicating power is on. Magnetic base should be firmly secured to work piece at this time.2. Start drill motor by depressing green motor “On” button.3. Using the feed handles, advance cutter into material until Handy-Mag I cutter has established an external groove in the material, during the remainder of cut apply, smooth constant pressure without overloading motor. NOTE: Handy-Mag I cutters are designed for uninterrupted cutting, chips are evacuated during the cut. Do not peck drill when using Handy-Mag I cutters.CAUTION: If drill motor should stall or stop before a complete cut is made, always shut the motor off and remove the cutter from the hole before attempt-ing to restart the motor. Failure to do so could result in personal injury and/or damage to the Handy-Mag I drilling machine or cutter.After the Cut1. After the Handy-Mag I cutter has finished the cut, the “slug” or uncut center portion of material will be expelled when motor is returned to the full up position.Beware of slugs ejected at end of cut. They become HOT during the cut.2. Return the machine to a full upright position and depress red motor “OFF “ button. Wait until motor completely stops.3. Move magnet switch to “OFF” position when ready to release magnetic base from work surface.Maintenance1. Adjusting motor slide tension:The motor slide assembly may become loose and require adjustment after the machine has been in service. Wrenches are provided in the tool kit for performing adjustments. • Using the feed handles, position motor and slide assembly in the full up position. • Loosen 5 jam nuts (ME3548) and equally tighten 5 adjustment screws (ME3547) using 2.5mm and 8mm combination wrench and hex key. • Do not over tighten adjustment screws. Excessive slide tension can damage the machine. Properly adjusted, the motor/slide assembly should have no side to side movement and remain positioned without drifting down.2. Inspecting magnet base:Keep bottom of magnet clean, free of chips, burrs, nicks, oil and other contaminants. Inspect magnet face to insure surface is flat and square. A worn magnet surface dramatically reduces magnetic holding force.3. Lubricating motor slideways:Periodically clean and lubricate motor slide ways with lithium base grease.4. Inspecting arbor support system:Visually inspect arbor, sleeve and support bracket for wear.Caution: Always remove cutter from arbor body before measuring runout, never use hands or fingers to rotate arbor or motor spindle.5. Checking arbor runout:Arbor runout should not exceed .0035 per revolution. This is most accurately measured by placing a dial indi-cators needle inside of arbor bore and rotating arbor while observing indicator.6. Motor brush inspection:Inspect motor brushes and replace as needed during extended periods of heavy machine usage.CAUTION: Never operate machine with worn or missing parts.Troubleshooting1. Magnetic base is not holding securely:• Material being drilled must be a minimum of 3/8" thick for proper magnetic adhesion.• Surface of material should be free of chips, debris, rust and mill scale.• Verify size of cutter. It should not exceed machines capacity.• Check magnet face for unevenness, nicks and burrs.• Welding equipment should not be connected to material being drilled.2. Drill motor is running, arbor and spindle is not turning:• Spindle key (HM3506) could be sheared.3. Motor slows when drilling:• Check extension cord requirements if one is being used. (pg. 4)• Excessive downfeed pressure during drilling cycle will cause motor to slow and overheat.• The cutting tool may need to be resharpened.4. Coolant system not working:• Coolant system is gravity dependent. Machine must be in an upright position to operate properly.• Consistency of coolant mixture is too thick.• Check for the correct pilot pin.5. Slugs not ejecting from cutter:• Lack of coolant can cause slugs to expand in cutter bore.• Check for correct pilot pin.• Check for broken internal arbor parts.*Drilling stacked material requires a special STACKED GEOMETRY cutter.6. Breaking cutters:• Coolant must be applied to the interior of the cutter.• Excessive downfeed pressure when cutter contacts work surface can cause breaks.• Confirm material hardness.• Drilling stacked material with improper cutter. (Drilling stacked material requires special cutters)• Dull cutters and dull or chipped cutting edges require excessive feed pressure resulting in breakage.• Excessive arbor runout. (see pg.8 for maintenance)• Motor spindle is bent or there is a worn arbor sleeve.• Motor slide is improperly adjusted. (see pg.8)7. Oversized or rough holes:• Insufficient coolant.• Excessive feed pressure.• Dull cutter.• Worn support bracket roller bearing or arbor body sleeve.• Bent motor spindle.• Motor slide improperly adjusted.Parts List QTY 211111121211114111111121122244121121112121111115521111121141121331QTYParts List 4411312111521112211211111411211111QTY 1111111QTYP a r t s B r e a k d o wn an d y -M a g I。
指南针的介绍英语200词

指南针的介绍英语200词The compass is a time-honored navigational tool that hasrevolutionized human exploration and travel since itsinception. This compact instrument, based on the Earth'smagnetic field, serves as a steadfast guide for determiningdirection, particularly North and South, enabling users toorient themselves accurately in both familiar and unfamiliarterritories.Originating in ancient China, the compass initiallyconsisted of a magnetized needle floating on water orsuspended by a thread, aligning itself with the Earth'smagnetic poles. Over time, it evolved into the modern form werecognize today: a portable device housing a freely rotatingmagnetized needle or card, marked with cardinal points(North, East, South, West) and often degrees for preciseangular measurements.At its core, the functioning principle of a compass isrooted in magnetism. The Earth behaves like a giant magnet,with a magnetic North and South pole. The compass needle,being magnetized itself, aligns itself with the Earth's magneticfield lines, pointing Northward due to magnetic attraction andrepulsion forces. This property ensures that regardless ofgeographical location or weather conditions, the compass consistently indicates true North, providing an invaluable reference for navigation.Beyond its fundamental role in maritime and land-based navigation, the compass has found applications in various fields, including surveying, outdoor recreation, and even as a symbolic representation of direction and guidance in literature and art. Its simplicity, reliability, and universality make the compass an enduring testament to human ingenuity and a vital tool in our ongoing quest to understand and traverse the world around us.。
施托伯异步电机操作手册说明书

1 07/2014WEKEEPTHINGSMOVING ID 442577_en.01This operating manual contains information on the transport, installation and commissioning of STÖBER asynchronous motors as components of the STÖBER MGS system (modular gear system); see the current MGS catalog.In the event of any unclear points, we recommend that you contact STÖBER with the model designation and serial number, or have the installation and maintenance work carried out by a STÖBER service partner.1Operation in accordance with its intended useThe motors may be used only for the operation of machinery and equipment, and under certain conditions also in combination with frequency converters. It is necessary to comply with the mechanical and electrical limits defined by the technical data. The motors may not be used in explosive atmospheres. If the motors are to be used for lifting or holding loads, the machine design engineer must determine whether additional safety measures are necessary.On grounds of operational safety, the motors may be used only for the purpose for which they were configured (see configuration aids in the STÖBER catalogs). Any overload to the drives is deemed non-intended use.The fulfillment of any warranty claims requires exact compliance with the information and instructions in this operating manual. Modifications to the motors will void the warranty.Observe the safety and hazard information in this operating manual and all supplementary documents on motors and other components, such as gear units and drive controllers!2Technical dataThe technical data for the motors or geared motors and the drive controllers used is specified on the respective rating plates. Further technical data and dimensional drawings can be found in the resp. catalog.The relevant standards and regulations are listed in the EC Declaration of Conformity, ID 441454. A delivery based on special regulations (e.g. classification regulations, regulations for explosion protection) is possible.Acceleration / shock load in operation:The following value for the shock load indicates the value upto which the motor can be operated without loss of functionality: 50 m/s² (5 g), 6 ms (maximum value as per DIN EN 60068-2-27).Brace the motor connection cable close to the motor so that vibrations of the cable are not transferred to the motor.When connecting the motors to drive units such as gear units or pumps, take into consideration the permissible shock loadsand tilting torques of the units.2.1Protection typeThe protection type for the motors is specified on the rating plate. Auxiliary equipment that is connected may have a different protection type than the motor. Please take this into account when installing the motors.Motors installed outdoors must be protected against direct exposure to weather conditions. (e.g. freezing of the fan through direct exposure to rain, snow and ice).2.2DesignsThe design of the motor is specified in the order confirmation. Take measures to prevent foreign objects from falling into the fan cover, especially in case of mounting positions with a perpendicular shaft.2.3Thermal winding protectionSTÖBER asynchronous motors can be equipped with thermal winding protection on request. Note the information in the MGS catalog!For PTC thermistors, the regulations of DIN 44081 and DIN 44082 apply, in addition to the instructions of the manufacturers of triggering devices used. The thermistor is a low-voltage sensor with a maximum supply voltage of 7.5 VDC. Higher voltages will destroy the thermistor and the motor winding.InformationIf brakes are installed, the holding torques maybe reduced by the shock load!2ID 442577_en.01W E K E E P T H I N G S M O V I N G07/2014CAUTION!Overheating of the motor!If the thermal winding protection is not connected, the motor may overheat as a result.Possible consequences: destruction of the motor, danger of fire.X You must also take precautions to ensure that no hazardcould occur after the thermal winding protection has responded and the motor has then cooled off by unintentional automatic switching on of the motor again!Always connect to the thermal winding protection. If the thermal winding protection is not connected, the warranty is rendered void!2.4Encoder systemsIncremental encoders and multi-turn absolute encoders (SSI) are connected via separately attached plug connectors.For the pin configuration, see the motor connection diagram. Further information can be found in the operating manual for the incremental encoder. Further information on multi-turn absolute encoders can be found in the Heidenhain operating manual.This product contains components that can be damaged or destroyed by electrostatic discharges.X Do not touch the pin contacts with your fingers!2.5BrakeThe brake operates according to the closed-circuit principle: interruption of the circuit results in braking, and closing the circuit releases the rotors. The rectifier located in the terminal box (model 160 and higher) or in the switch cabinet is connected with the excitation coil of the brake on the DC side. Depending on the number of circuits in the brake, the working air gap must be checked regularly and adjusted, if necessary. See the separate operating manual “Asynchronous motor brakes”. When the brake lining has worn down to the minimum thickness, it is no longer possible to adjust the air gap and the brake has to be replaced.Always keep brake linings and friction surfaces free of greaseand oil.CAUTION!Check the function of the brake before operating the motor!2.6External coolingExternal cooling is optional and can be retrofitted, due to the modular design, so that drive units can be optimized at a later time. For technical data, see the rating plate and catalog.Lack of cooling, for example due to accumulation of dirt or a breakdown of the fan, causes overheating of the motor, which can damage or destroy the winding.X Therefore, check the function of the external fan duringcommissioning and at regular intervals thereafter.2.7Motors with integrated drivecontroller (e.g. compact drives VEM300)Power connection: Always use a 4-wire, shielded cable for connection to the power supply. This cable must have the correct dimension, with the following specification: copper wire, class 1, 75 °C.In addition, the operating manuals / technical documentation for the respective drive controller and their options apply.3Safety informationIn addition to the information in this operating manual, you must also comply with the applicable national, local andfacility-specific regulations.WARNING!- Danger of electrical shock if unpainted parts conducting voltage are touched.- Moving and rotating parts can cause injuries- Touching the gear unit and motor housing may cause burns (surface temperatures of over 100°C are possible)X The machine manufacturer must provide suitableprotective measures. The connector or terminal box cover of the motor must remain closed during operation. All work on the drive must only be performed when no current is present.3.1Personnel requirementsAll work on the electrical equipment of the drive units must be performed by qualified electricians. Installation, maintenance and repairs of mechanical parts must be performed by fitters, industrial mechanics or persons with comparable qualifications.307/2014W E K E E P T H I N G S M O V I N GID 442577_en.013.2In the event of disruptionsChanges compared to normal operation indicate that the function has been impaired. This includes:- Higher power consumption, temperatures or vibrations - unusual noises or odors - Leaks on the gear unit- Monitoring devices respondingX If any of these occur shut down the machine as quickly aspossible and notify the responsible qualified specialist without delay.3.3Safety during installation andmaintenanceDamage to the motor.X Prevent undue force on the motor such as impact, shock,pressure or high acceleration.Before switching on the motor, ensure that •all safety regulations are observed •the machine is properly installed and aligned •all mounting parts and earthing connections are tight •the auxiliary and supplementary devices are functioningand correctly connected •the fitting keys of a second shaft end are secured againstspinning off If the motor is disconnected from the power supply or drive controller for maintenance, take special care to ensure that any auxiliary power circuits (e. g. stand-by heaters, external fans, brakes) are also disconnected from the power supply.If it is necessary to dismount the motor for maintenance•remove the sealing compound on the centeringshoulders•use a suitable motor sealing compound (e.g. Curil T) during assembly•replace existing copper gaskets with new ones andalways make sure not to omit them3.4Safe function and EMC of the drivesystemThe motors were checked as dependant components for conformity with the EMC standards. Ensure that machines or equipment as a whole comply with the relevant standards for electromagnetic compatibility.The motor, cables and drive controllers, if applicable, must be matched. Each product has its own electrical properties that affect the other components. If not properly matched, excessive voltage peaks can occur in the motor and drive controller, resulting in destruction of the motor and malfunction of the system. Furthermore, the statutory regulations for EMC (electromagnetic compatibility) must be observed.In order to ensure this compliance, STÖBER offers matched cables with suitable shielding technology and cable construction for the power connection and the various encoder systems.The use of other connecting cables or drive controllers can void the warranty.4Transport, storage and preservationThe motors must not be exposed to acceleration levels or working times of more than 300 m/s² (30 g) as an individual shock load during transport as per EN 60 068-2-27. The values for operation apply to long-term shock loads.When transporting the motors make certain not to damage the shafts and bearings with impacts.The motors may only be stored in enclosed, dry rooms. Storage in open air areas with a roof is only permitted for brief periods. Protect the motors from all damaging environmental effects and mechanical damage.Avoid extreme temperature fluctuations with high relative humidity when the motors are being stored temporarily to prevent formation of water from condensation. If long-term storage is planned, protect the bare parts of the motor against corrosion. Before placing a motor in operation again, have the winding checked for its insulation resistance by an electrical specialist.Do not use the fan cover for transport or storage of the motors. For transport, use the eyebolts on the motors, together with suitable slings.Eyebolts are provided only for lifting the motor without additional attachments. When you remove the eyebolts after installation, the threaded holes must be permanently closed corresponding to the protection type of the motors.4.1Removing the transport safeguard•For motors with a transport safeguard (roller bearing), loosen the hexagon bolt securing the transport safeguard and remove it together with the transport safeguard.•Then screw the bearing cap bolt (packed in a bag in the terminal box) into the bearing cap.For some motors, a lock washer is included in the bag:•Insert the washer on the bearing cap bolt before inserting the bolt.5Mounting Completely remove all corrosion protection on the shaft ends prior to installation.NOTICEThe lip seals of the shaft seal rings can be damaged by the use of solvents.X When removing the corrosion protection, make sure thatthe lip seals of the shaft seal rings do not come into contact with solvents.Do not fasten or allow contact of temperature-sensitive parts to the motors.4ID 442577_en.01W E K E E P T H I N G S M O V I N G07/2014For models IMB14 and IMB34, do not exceed the following maximum screw-in depth (otherwise, the winding will be damaged!):Keep the ventilation openings free and maintain the specified minimum clearances in order not to disrupt the flow of the cooling air (see above). Make sure that the blown-out, heated coolant is not sucked in again.The fitting key in the shaft end is secured by the shaft sleeve only for transport and storage. Commissioning or a test run in this condition is strictly prohibited, due to the danger of the fitting key spinning out!Use mounting tools when mounting the power transmission element (such as coupling, pinion or pulley) or heat the part to be mounted. For mounting, the shaft ends have centering devices with threaded holes according to DIN 332, Part 2.Damage to the bearing race.X Avoid all impacts to the output shafts.Carefully balance all elements to be mounted on the shaft end, corresponding to the balancing system of the motor (whole or half fitting key). The rotors of the motors are balanced with half fitting keys.If directly coupled with the driven machine, make sure to align the components exactly. The axes of both machines must be aligned. Adjust the shaft center height by shimming the driven machine.The relatively high radial forces of belt drives strain the motor. When dimensioning belt drives, do not exceed our specifications for the maximum radial force through belt pull and pre-tension on the shaft end of the motor (note maximum forces in the catalog). (Also observe the regulations and calculation programs of the belt manufacturers). During installation, set the belt tension exactly according to the specifications of the belt manufacturer. 5.1Draining condensation waterAlways position the condensation water openings at the lowest point of the motor.In installation locations where condensation water in the interior of the motor is to be expected, it must be ensured that the liquid can drain unhindered.The protection type can be limited by the permanently open condensation water holes. However, this will not affect the function of the motor.NOTE: If motors are designed with closed condensation water holes, they have to be opened occasionally to allow drainage of any condensation water that has accumulated!6CommissioningElectrical connections provided by the customer must comply with applicable regulations.Note:The electrical connection diagram and safety regulations are with the delivery documents of the motor. Comply exactly withthe information and safety regulations therein.WARNING!Danger of injury from moving parts.Before commissioning the drive unit, ensure that...X no one will be endangered by startup of the machine.X all protective guards and safety equipment have beenproperly installed, also for a test run!X the drive unit is not blocked.X the brakes have been bled.X the direction of rotation is correct.Xcomponents mounted on the power take-off end are sufficiently secured against centrifugal force (e.g. fitting keys, coupling elements, etc.)First compare the voltage and frequency of the mains power supply with the data on the rating plate of the motor. Adapt thedimensions of the connecting wires to the rated currents ofthe motor.The designation of the connecting points of the motorcorresponds to DIN EN 60034, Part 8. For the connection of auxiliary and protective devices (e.g. stand-by heating), an additional terminal box can be provided, for which the sameregulations apply as for the main terminal box. Operate the motors with overcurrent protection that is setaccording to the rated data of the motor. Otherwise, damage to the winding will not be covered by the warranty. Check the motor for the correct direction of rotation. If the power connections with the phase sequence L1, L2 and L3 are connected to the connecting points U, V, W, the motor will rotate clockwise when looking at the end of the shaft. You can change the direction of rotation by switching the connections of 2 phases. The maximum torques for the terminal board bolts are listed in the following table:Size max. screw-in depth IMB14/34 [mm]min. clearance for cooling air [mm]63 6.514717.014808.0169010.01610010.02011210.020132-35160-35180-35200-35225-40507/2014W E K E E P T H I N G S M O V I N GID 442577_en.01Before closing the terminal box, always make sure that -connections correspond to the wiring diagram -all terminal box connections are tight-all minimum values for the air gaps have been maintained (> 8 mm up to 500 V, > 14 mm up to 1000 V)-the inside of the terminal box is clean and free of foreign objects-unused cable entries are closed and the plug screws with gasket are tight-the gasket in the terminal box lid is clean and tight.6.1Insulation inspection and replacement of grease/bearingsDuring the first commissioning and especially after extended storage, measure the insulation resistance of the winding to ground and between the phases. The maximum applied voltage is 500 V. Dangerous voltages occur at the terminals during and directly after the measurement. Never touch the terminals. Consult the operating manual of the insulation measuring instrument!Maintain the following minimum values, based on the rated voltage U N at a winding temperature of 25 °C:Dry the winding properly if the values fall below the minimum values, until the insulation resistance corresponds to the required value. The motors are equipped with sealed bearings. Replace the bearings with new ones of the same type after a storage period of four years.7Maintenance7.1Bearings, lubrication and sealThe roller bearings of the standard motors are lubricated at the factory, those with covered bearings by the bearing manufacturer, using roller bearing grease.If the bearings need to be replaced due to wear, use only replacement bearings of the quality specified by the motor manufacturer.Motors for MGS gear units are equipped with an FKM shaft seal ring. If replacement is necessary, the bearing surface of the shaft must be inspected and, if necessary, polished smooth. Use only sealing rings from the motor manufacturer.7.2CleaningClean all parts of the motor regularly in order to maximize the effect of the cooling air. Usually it is sufficient to blow out the motor with compressed air that is free of water or oil. Especially the ventilation openings and spaces between the fins should be kept clean. We recommend that the electric motors be included in regular inspections of the driven machine.8TroubleshootingIn the event of a malfunction of the drive unit, call the STÖBER service department at 07231 582-1190 (-1191, -1224, -1225) in order to locate the nearest STÖBER service partner for further action.In urgent cases outside of normal business hours, you can call the STÖBER 24-hour service hotline at 01805 786323 / 01805 STOEBER9Spare partsInclude the following when ordering replacement parts:–item no. of the part according to the replacement parts lis–model designation according to the rating plate –serial number according to rating plateYou can reach the STÖBER replacement parts service by phone: 07231 582-1190 (-1191, -1224, -1225), or fax: 07231 582-1010.Important notice: The replacement parts lists are not assembly instructions! They are not binding for assembly of the gear unit. Use only original replacement parts from Stöber. Otherwise we will provide no guarantee and will assume no liability for resulting damages!10DisposalThis product contains recyclable materials. Observe local applicable regulations for disposal.Terminal board Connecting bolts thread max. torque [Nm]16 A M41,2 +0,525 A M52,5 ±0,563 A M64,0 ±1100 AM87,5 ±1,5Rated power P N [kW]Insulation resistance in relation to rated voltage k Ω/V 1 < P N ≤ 106,310 < P N ≤ 1004,0100 < P N2,5。
- 1、下载文档前请自行甄别文档内容的完整性,平台不提供额外的编辑、内容补充、找答案等附加服务。
- 2、"仅部分预览"的文档,不可在线预览部分如存在完整性等问题,可反馈申请退款(可完整预览的文档不适用该条件!)。
- 3、如文档侵犯您的权益,请联系客服反馈,我们会尽快为您处理(人工客服工作时间:9:00-18:30)。
Anshu Gupta∗ , Amruta Mishra† , Hiranmaya Mishra, A.R. Prasanna
Theory Division, Physical Research Laboratory, Navrangpura, Ahmedabad -380 009, India
II. ROTATING NEUTRON STARS IN HARTLE THORNE APPROXIMATION
The description of rotating compact objects in the framework of general relativity is a complicated task. In what follows, we shall be using the method of Hartle and Thorne [3], appropriate for slowly rotating objects. Here a perturbative solution is formulated over the Schwarzschild metric for the nonrotating stars given as ds2 = −eν0 dt2 + (1 − 2GM/r )−1dr 2 + r 2 (dθ2 + sin2 θdφ2 ) (1)
Typeset using REVTEX
∗ E-mail: † E-mail:
anshu@prl.ernet.in am@prl.ernet.in
1
I. INTRODUCTION
The study of structure and dynamics of neutron stars is an interesting and challenging theoretical problem. The system here is quite complicated. The large density in the interior of such stars can lead to a possibility of melting the baryons to form a deconfined quark core [1]. Observations of rotating neutron stars with a period in the millisecond range has renewed the interest in the study of the influence and implications of rotation on the bulk properties of such objects [2]. Further the neutron stars are also known to possess strong magnetic fields. Their polar field strengths are deduced from the observed spin slowdown of pulsars via the magnetic dipole breaking model with most of the young pulsars having a surface field, B ≈ 1012 gauss [4]. Each one of the above facets of neutron stars poses interesting theoretical challenges. The fascinating possibility of a deconfined phase of matter in the interior of neutron stars has stimulated the work of many authors proposing different signals of existence of such a core of quark matter. These studies mostly have been done for considering nonrotating stars. The treatment of massive compact rotating objects in the framework of general theory of relativity is a rather complicated task. However, for slow rotation this can be done in the framework of Hartle and Thorne [3]. Further, the magnetic field structure outside the neutron star has been studied in connection with pulsar emission mechnism [5]. In a nonrelativistic approach, the generation and evolution of internal magnetic fields have been studied recently [6]. A relativistic treatment to include structure of magnetic field in the interior of neutron stars by solving coupled Einstein Maxwell’s equations has been done numerically in ref. [7]. It is therefore interesting to incorporate all these effects together in its totality to the extent possible and the present work is a step in that direction. We shall consider rotating stars endowed with magnetic fields. The effects of rotation is taken into account in the framework of Hartle and Thorne where rotation effect is treated as a perturbation over the Schwartzchild solution and is valid naturally for slowly rotating stars [3,8]. The field structure shall be assumed to be poloidal and axisymmetric. The 2
In the above ω is the angular velocity of the star’s fluid in a local inertial frame and depends on the radial coordinate r . The difference ω ¯ = Ω − ω is the angular velocity with which the 3
The metric function is expanded in terms of the star’s rotational frequency, Ω, the angular velocity of the star’s surface relative to an observer at infinity and is given as ds2 = −e2ν dt2 + e2λ dr 2 + e2µ dθ2 + e2ψ (dφ − ωdt)2 (2)
arXiv:astro-ph/9805146v1 12 May 1998
Abstract
We consider here the structure of rotating compact objects endowed with a magnetic field in general relativity as models of pulsars. We discuss first the structure of rotating stars in the framework of Hartle taking different realistic equations of state and study their effects on bulk properties of the star. We consider the possibilty of rotating stars with a quark matter core. We further analyse the structure of the magnetic field in the interior of the star as affected by different equations of state as well as due to rotation.
effect of rotation of the star on the magnetic field structure is included, but not the reverse, amounting to the fact that the magnetic field energy is not strong enough to affect the space time geometry. We shall also take into account the effects of different equations of state on the gross properties of the star and on the magnetic field in the interior. We organise the paper as follows. In section II, we give a short description of treating rotating compact objects in general relativity in the approximations of Hartle and Thorne [3]. In section III, we discuss Maxwell’s equations in curved space time with Hartle metric and set up the differential equations for electromagnetic fields. Here we obtain the boundary conditions on the dipole magnetic field structure taking corrections due to rotation upto O (Ω2 ). Using these boundary conditions, we integrate them from the boundary to the interior of the star. In section IV, we discuss different equations of state and their effects on the bulk properties of the star along with the field structure in the interior. Section V summarizes the results and discussions.