可靠性试验设计与5讲述
apqp五个阶段描述
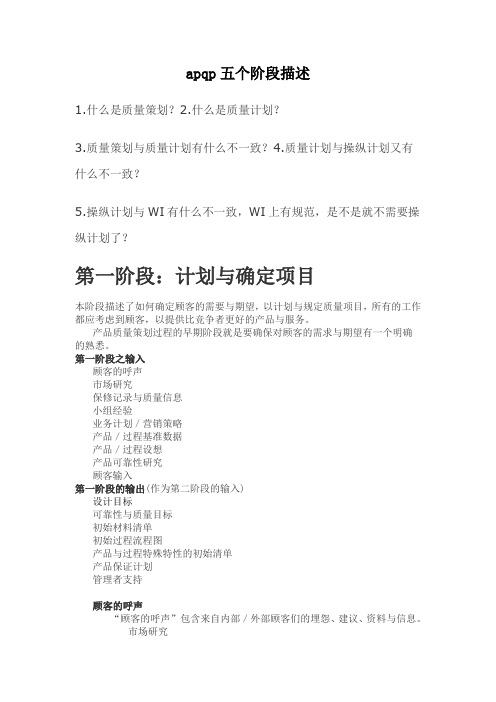
apqp五个阶段描述1.什么是质量策划?2.什么是质量计划?3.质量策划与质量计划有什么不一致?4.质量计划与操纵计划又有什么不一致?5.操纵计划与WI有什么不一致,WI上有规范,是不是就不需要操纵计划了?第一阶段:计划与确定项目本阶段描述了如何确定顾客的需要与期望,以计划与规定质量项目,所有的工作都应考虑到顾客,以提供比竞争者更好的产品与服务。
产品质量策划过程的早期阶段就是要确保对顾客的需求与期望有一个明确的熟悉。
第一阶段之输入顾客的呼声市场研究保修记录与质量信息小组经验业务计划/营销策略产品/过程基准数据产品/过程设想产品可靠性研究顾客输入第一阶段的输出(作为第二阶段的输入)设计目标可靠性与质量目标初始材料清单初始过程流程图产品与过程特殊特性的初始清单产品保证计划管理者支持顾客的呼声“顾客的呼声”包含来自内部/外部顾客们的埋怨、建议、资料与信息。
市场研究对顾客的采访顾客意见征询与调查市场测试与定位报告新产品质量与可靠性研究运行情况良好报告竞争产品质量的研究运行情况良好(TGR)报告保修记录与质量信息为了评定在产品的设计、制造、安装与使用当中再发生不合格的可能性,应制定一份以往顾客所关注问题/需要的清单,这些应作为其它设计要求的扩展来考虑并应包含对顾客需要的分析中。
运行情况不良(TGW)报告保修报告能力指数供方工厂内部质量报告问题解决报告顾客工厂进货与废品现场退货产品分析小组经验小组适当时可利用包含如下内容的任何信息来源:来自更高层体系或者过去质量功能开发(QFD)项目的输入媒介的评论与分析,杂志与报刊报告等顾客的信件与建议运行情况良好(TGR)/运行情况不良(TGW)报告销售商意见车队负责人的意见现场服务报告利用指定的顾客代理所作的内部评价道路行驶体验管理者的意见与指示由内部顾客报告的问题与议题政府的要求与法规合同评审业务计划/营销策略顾客业务计划与营销策略将成为产品质量计划的设定框架。
业务计划可将限制性要求施加给小组(诸如进度、成本、投资、产品定位、研究与开发资源)而影响其执行方向。
可靠性设计与试验

表12-1 半导体分立器件通用质量系数
种类 晶 体 管 二 极 管 π
Q
质量等级 双 极 型 场 效 应 闸 流 单 结 普 通 电流调整 微 波
应力筛选
2.5 失 效 率 2.0
1.5
1.0
100○应力条件 125○应力
0.5
225○应力 100 240小时
例如某厂半导体3DG32加300毫瓦功率进行摸底试 验,得到试验时间与失效率的数据如表
t 单位小时
% /小时
0.1 120
1 26.8
10 0.46
30 0.16
表中看出经 300 毫瓦功率 10 小时可靠性筛 选以后,其失效率可以下降 250 倍。
5t d TS 1464 小时
12.3.电子产品的可靠性预计
• 产品的可靠性预计是在产品定型过程中, 从元器件的可靠性参数,经过试验结果与 理论的分析计算,对产品可能达到的可靠 性水平进行一种预测过程。 • 产品可靠性预计的目的是为了落实产品定 量化的可靠性指标,为使产品达到规定的 可靠性要求,并为今后改进产品的可靠性 提供理论的基础。
2 10 0 1 例12-1:设, 0 , /小时,从100个元件中,其中次 品有10个,求达到系统 S 0.005 /小时和0.0012/小时的
筛选时间。
1 1 1 1 t d 1 10 1 2 3 100(1 0.5 0.33 0.25 0.2 0.164 0.143 0.125 0.111 0.1) 100( 2.928) 292.8小时
可靠性设计内容
• 最大限度地提高固有可靠性,其中包括:原件的选择与管理,降额 设计,参数设计与漂移设计,环境防护,贮备设计,设计的简化与分 析,这些措施都有利于提高系统的固有可靠性。 • 设计中考虑降低生产与使用过程中可靠性的退化问题,进行退化分 析,维修设计措施,包括早期故障的判断,故障分析等。 • 制定元件的筛选或老练方案,可靠性试验。元件选择及管理有以下 几个内容: • 确定完成所需功能元件类型及预期的工作环境。 • 确定元件的临界值,(额定值),如果超过这个值有可能失效而 • 出现危险情况等, • 确定元件的质量等级。 • 可靠性分配与优化设计,重要度分析也是设计中的重要任务。 • 费用设计,费用的估计和分配技术。 • 可靠性分配与优化 • 可靠性审查与评估 • 储备设计方法
《可靠性试验大纲》课件

通过学科交叉融合,将不同领域的理论和技术结合起来,推动可靠性试验的创新 和发展。
THANKS
感谢观看
《可靠性试验大纲》 ppt课件
目录
• 可靠性试验概述 • 可靠性试验的流程 • 可靠性试验的方法 • 可靠性试验的应用领域 • 可靠性试验的挑战与解决方案 • 可靠性试验的发展趋势
01
可靠性试验概述
定义与目的
定义
可靠性试验是对产品在各种环境 条件下进行的一系列试验,以评 估产品的可靠性和性能。
常见的电子产品可靠性试验包括 环境适应性试验、寿命试验、耐
久性试验等。
机械设备
机械设备是可靠性试验的重要 应用领域之一,包括汽车、航 空器、船舶、工业机械等各类 机械设备。
可靠性试验可以帮助机械设备 厂商评估产品的可靠性和安全 性,提高产品的稳定性和使用 寿命。
常见的机械设备可靠性试验包 括振动试验、疲劳试验、负载 试验等。
02
可靠性试验的流程
试验前准备
01
02
03
04
明确试验目的
在开始试验前,需要明确试验 的目的和预期结果,以便为试
验过程提供清晰的方向。
选择试验设备
根据试验需求,选择适合的设 备和工具,确保其性能稳定、
准确度高。
制定试验计划
制定详细的试验计划,包括试 验步骤、时间安排、人员分工
等,确保试验有序进行。
医疗器械
医疗器械是可靠性试验的重要应用领 域之一,包括医用设备、诊断试剂等 各类医疗器械。
常见的医疗器械可靠性试验包括生物 相容性试验、稳定性试验、性能测试 等。
可靠性试验可以帮助医疗器械厂商评 估产品的安全性和有效性,确保产品 在正常使用过程中能够达到预期的性 能和安全性。
“四性”设计与试验

单击此处添加正文,文字是您思想的提炼,请尽量言简意赅地阐述观点。
等在规定条件下的可靠性指标、系统的结构、
靠性。这是一个由局部到整体、自下而上的综
系统的功能以及工作方式等,来推算系统的可
单击此处添加正文,文字是您思想的提炼,请尽量言简意赅地阐述观点。
合过程。
常用的可靠性预计方法主要有:
可靠性进行评价,看其是否满足合同要求。
受试产品从同一批产品中随机抽取,其数
量一般为10%,最多不超过20台(套)。
可靠性鉴定试验应采用与鉴定试验相同的
试验剖面和条件。
试验方案可以选取GJB899中规定的序贯试
b.元器件选用与管理。
耐环境设计 耐热设计 电磁兼容设计 电路容差分析
2.降额设计(GJB/Z35《元器件降额准则》)
(二)可靠性试验
单击此处添加文本具体内容,简明扼要的阐述您的观点,以便观者准确的理解您传达的思想。
01
可靠性试验的目的
是对产品可靠性的各种特征指标 进行测量(摸底)、评定(鉴定)和 验证(验收)。
航空电子产品 “四性”设计与试验
陈国华
2009年06月
需树立的理念
“四性”是武器装备技术、质量的重要属性
“四性”是武器装备战斗力的重要基础
“四性”是效益和效率的重要保证
“四性”是设计、制造的产物
“四性”指标是可以检验、验证的
一、可靠性设计与试验
单击此处添加文本具体内容,简明扼要的阐述您的观点,以便观者准确的理解您传达的思想。
01
元器件计数法—
02
适用于方案论证及初步设计阶段;
03
应力分析法—
04
适用于电子类产品详细设计阶段;
可靠性试验

可靠性试验引言可靠性试验是评估和验证产品或系统在特定条件下的可靠性的过程。
通过设计和执行可靠性试验,可以确定产品或系统在使用寿命内是否能够满足特定的可靠性要求。
本文将介绍可靠性试验的概念、重要性以及试验中需注意的事项。
可靠性试验的概念可靠性试验是一种系统评估的方法,用于确定产品或系统在特定条件下的可靠性水平。
可靠性是指产品或系统在规定时间内正常工作的能力。
可靠性试验通常包括以下几个方面:1.限制条件的设定:在进行可靠性试验之前,需要明确试验的目标、时间、资源等限制条件。
2.试验方案的设计:设计一个科学合理的试验方案,包括试验过程、试验对象、试验方法以及数据采集与分析。
3.试验执行与数据采集:按照试验方案进行试验,并记录相关数据。
试验中要注意环境的控制和数据的准确性。
4.试验结果的分析:对试验结果进行统计与分析,评估产品或系统的可靠性水平。
可靠性试验的重要性可靠性试验对于产品或系统的开发和改进具有重要的意义。
以下是可靠性试验的重要性:1.评估产品或系统的可靠性:通过可靠性试验,可以对产品或系统在正常使用条件下的可靠性进行评估,及时发现存在的问题并加以改进。
2.确定产品或系统的寿命:可靠性试验可以确定产品或系统在设计寿命内的可靠性水平,从而为产品或系统的正常使用提供参考。
3.提高产品或系统的质量:通过可靠性试验,可以及时发现产品或系统在特定条件下的故障模式和失效原因,从而针对性地改进产品或系统的设计和制造工艺,提高产品或系统的质量。
4.降低使用成本:可靠性试验可以预测产品或系统在使用寿命内的维护和修理成本,从而为用户提供更准确的成本预估。
可靠性试验的注意事项在进行可靠性试验时,需要注意以下几点:1.设计合理的试验方案:试验方案需要根据产品或系统的特性和实际使用条件进行设计,确保试验结果具有可靠性和可重复性。
2.控制环境条件:试验过程中需要对环境条件进行严格控制,避免因环境变化引起的误差,确保试验结果的准确性。
可靠性试验报告
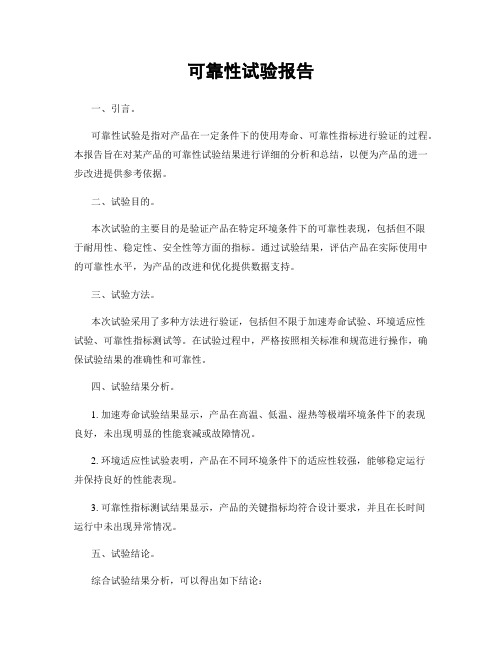
可靠性试验报告一、引言。
可靠性试验是指对产品在一定条件下的使用寿命、可靠性指标进行验证的过程。
本报告旨在对某产品的可靠性试验结果进行详细的分析和总结,以便为产品的进一步改进提供参考依据。
二、试验目的。
本次试验的主要目的是验证产品在特定环境条件下的可靠性表现,包括但不限于耐用性、稳定性、安全性等方面的指标。
通过试验结果,评估产品在实际使用中的可靠性水平,为产品的改进和优化提供数据支持。
三、试验方法。
本次试验采用了多种方法进行验证,包括但不限于加速寿命试验、环境适应性试验、可靠性指标测试等。
在试验过程中,严格按照相关标准和规范进行操作,确保试验结果的准确性和可靠性。
四、试验结果分析。
1. 加速寿命试验结果显示,产品在高温、低温、湿热等极端环境条件下的表现良好,未出现明显的性能衰减或故障情况。
2. 环境适应性试验表明,产品在不同环境条件下的适应性较强,能够稳定运行并保持良好的性能表现。
3. 可靠性指标测试结果显示,产品的关键指标均符合设计要求,并且在长时间运行中未出现异常情况。
五、试验结论。
综合试验结果分析,可以得出如下结论:1. 产品在特定环境条件下具有较高的可靠性和稳定性,能够满足用户的长期使用需求。
2. 产品的设计和制造工艺符合相关标准和规范要求,能够保证产品的可靠性和安全性。
3. 产品在实际使用中表现良好,未出现明显的性能衰减或故障情况。
六、改进建议。
基于试验结果,提出以下改进建议:1. 进一步优化产品的设计和制造工艺,提高产品的可靠性和耐用性。
2. 加强对产品的质量控制和检测手段,确保产品在生产过程中的一致性和稳定性。
3. 加强对产品的使用说明和维护指南的编写,提高用户对产品的正确使用和维护意识。
七、总结。
本次试验结果表明,产品在特定环境条件下具有较高的可靠性和稳定性,能够满足用户的长期使用需求。
同时,也为产品的进一步改进和优化提供了重要的数据支持。
希望本报告能够为产品的质量提升和市场推广提供有益的参考。
可靠性试验介绍范文

可靠性试验介绍范文可靠性试验是一种通过定量评估产品、设备或系统在特定条件下的可靠性表现的实验方法。
可靠性试验旨在确定产品在一定使用寿命内的故障概率或失败率,并提供对产品寿命的预测,以便进行合适的改进和优化。
本文将介绍可靠性试验的目的、设计和常见可靠性试验方法。
可靠性试验的主要目的是评估产品在特定条件下的可靠性,以确定产品是否符合设计要求和客户的期望。
试验可以识别出产品的薄弱环节和潜在故障模式,以及提供产品寿命的预测和维修需求的预警。
通过结果分析和评价,可以为产品的改进和优化提供依据,并指导后续的可靠性验证工作。
试验样本的选择是试验设计中的核心问题之一、一般来说,样本的规模和代表性对试验结果的可靠性有重要影响。
样本规模的确定需要考虑到试验的时间和资源限制,以及试验能够提供的可靠性信息的数量和质量。
样本的代表性则要求试验样本能够真实地反映出整个生产批次或产品总体的特征。
试验条件的选择应该根据产品的设计目标和预期使用环境来确定。
试验条件通常包括温度、湿度、振动、电磁辐射等因素,这些因素对产品寿命和可靠性有重要影响。
试验条件的选择应该充分考虑到产品在现实使用环境中面临的各种应力和风险。
试验测量指标是评估产品可靠性的关键指标,如故障概率、失效率、失效时间等。
根据不同产品的特点和试验目标,可以选择不同的测量指标来评估产品的可靠性,并确定合理的试验量测方法和数据采集方法。
常见的可靠性试验方法:1.加速寿命试验(ALT):ALT试验通过增加环境应力或加快使用条件来加速产品的老化过程,以预测产品在正常使用条件下的寿命。
通常,采用高温、高湿、高压等试验条件进行ALT试验。
2.应力筛选试验(SS):SS试验是一种对产品在较高的应力条件下进行短期测试的方法,以筛选出存在缺陷或潜在故障的产品。
SS试验通常使用高应力的试验条件,并通过统计分析来评估产品的无故障寿命。
3.成功运行试验(SRT):SRT试验是验证产品在特定条件下连续运行的时间,以评估产品的可靠性。
可靠性设计与寿命实验讲解

由于6个月的老练期,系统设计寿命要增加4年 多。注意由老练期T0带来的可靠度增加只适应于 DFR系统
总结
故障率比故障密度更灵敏的反映了产品故障的变化 速度。
浴盆曲线
产品的故障率在不同的使用时期具有不同的 特点,可以划分为三个不同时期:
➢ (1)早期故障期 ➢ (2)随机(偶然)故障期 ➢ (3)耗损故障期
浴盆曲线
规定 的故 障率
使用寿命
浴盆曲线
浴盆曲线的性质
浴盆曲线
简化的浴盆曲线 对应每个阶段的故障率函数是什么?
间(工作时间),那么压缩机工作100h的可 靠度是多少?
R(100)=0.909
R(tR)=0.95
tR=52.6h
平均故障前时间
平均故障前时间
平均故障前时间
R(tmed)=0.5
tmed=346.6h
f(t)是单调递减且非负函数,因此tmode=0
平均故障前时间
即使两可靠度函数的均值相同,但对应相同工 作时间他们的可靠度也可能是不同的。显然, MTTF不能唯一确定故障分布,因此需要寻找其 他的度量参数。
换试验,试验结果如图(a)所示,在某观测时间 内对三个可修复产品进行试验,试验结果如图 (b)所示。图中“×”均为产品出现故障时的时 间,t为规定时间,求以上两种情况的产品可靠 度估计值。
b
a
可靠度函数——故障的累积分布函数
F(t)=1–R(t)表示什么含义? 故障的累积分布函数(不可靠度):表
平均故障前时间
一般而言,相同的MTTF,我们更喜欢分布 函数的方差小一些,为什么?
平均故障前时间
故障率函数
故障率函数
可靠性工程与风险评估-第5章-可靠性试验

根据应力与寿命的关系曲线(S—N曲线)来选择的 应力水平可以保证失效模型的一致性,能满足加速试验 对试件失效机理不变的要求。
图5—l 应力一寿命关系
如果要对两个零部件进行比较,参阅图5—2(a),A 与两B个零部件具有相互平行的S—N曲线。因此,在加速条件 下进行试验所得出的结论与正常运行条件下所得的结论是 一致的。这样的零部件被认为是可比零部件。如果两个零
下的区域里。然后取许多随机点xi , yi , i 1,2,, n
检验各点的座标是否满足上面的不等式。令满足此不等
式的点的总数为m,投放随机点的总数为n,频率为m ,
有下列关系:
n
lim m I
(5-46)
n n
即当投放的随机点数目足够大时,频率m/n就是式(5-
45)所求积分的近似值。
则
An 83.61n 4.288
Bn 83.61n 5.5055
n
当, xi 83.61n 4.288 判为合格,接受该批; i 1 n
当, xi 83.61n 5.5055 判为不合格,拒绝该批; i 1 n
当83.61n 5.5055 xi 83.61n 4.288 时,继续抽检。 i 1
统计试验法又称随机模拟法或蒙特卡罗法。它是 人为地构造出一种概率模型,使它的某些数字特征恰 好重合于所需要的计算量,而这些数字特征,又可以 通过实验,用统汁方法求出它们的估计值,这些估计 值就可以作为要求量的近似结果。换言之,将随机数 赋于各种适当的物理含义;将各种随机过程的概率特 征与数学分析问题的解答联系起来。
对于本节1中叙述的试验时间与环境应力的关系所 讨论的强化环境应力、缩短试验时间的问题,因为S-N 曲线的获得一船须将各随机变量作统计处理,故列为 “统计性质的加速试验”类中,实质上它是一种物理性 质的加速试验方法,因为它提高了控制因子——增加环 境应力水平,达到加速的目的。
质量管理与可靠性第5章设计质量控制

制
体系的规定的特性或规范的一组过程。”
第一节 设计质量控制概述
第
五 • 设计质量控制就是按规定程序和规范,控制
章
和协调各个阶段的设计工作,以保证产品的
设 计 质 量
设计质量,及时地以最小的耗费完成设计工 作。
• 设计质量控制就是对设计过程的工作质量进 行控制。
控
制
一、设计质量与产品质量
第 五 • 国际标准化组织(ISO)产品质量包括4个方面:
量
控
制
TRIZ理论
第 (6)分离原理与发明原理的关系
五 章
• 解决物理矛盾的分离原理与解决技术矛盾的 发明原理之间存在一定的关系,对于一条分
设 离原理,可以有多条发明原理与之对应。
计
质
量
控
制
三、稳健设计方法(田口方法)
第
五
章
田
口
设
质
计
量 理
质
论 体
量
系
控
制
田口质量观、质量损失函数、信噪比、正交试验法
3. 田口方法
4. 可靠性设计中的故障树分析法(FTA)、失效模式 及影响分析法(FMEA)和失效模式、影响及危害
量
性分析法(FMECA)。
控
制
第三节 设计质量控制技术
第 五 一、质量功能展开(QFD) 章 1、 QFD概述
设
质量功能配置(质量功能展开),是一种在设计阶
计
段应用的系统方法,采用一定的方法保证将来自于
质 量 控
该使设计输出结果的均值和标准差满足以下两个条
件: y y0 条件1: ,一批产品的质量特性均值应恒等于 目标特性S值 1;y
机械可靠性设计第五章演示文稿

第十一页,共101页。
可靠性框图
一、串联系统的可靠性
当一个系统的单元中只要有一个失效,该系统就失效,该系统称为串
联系统
1
2
n
串联系统逻辑图
系统可靠度:
n
Rs (t) R1(t)R2 (t)Rn (t) Ri (t)
i 1
第十二页,共101页。
若每个单元的寿命服从指数分布,λi 为单元的失效率,即有:
构成任务失败的条件:
1个至4个灯泡不亮。
( 2) 确定产品可靠性框图(见图2)
R1
R2
R3
R4
图2
只要1个灯泡失效,产品(系统)就失效; 或灯泡必须全可靠产品才可靠。
第八页,共101页。
(二)四个灯至少亮一个
(1) 产品:同前,仅失效条件为四灯全不亮 。
R1
(2) 可靠性框图(见图3)
R2
只要一个灯泡可靠
g
a
n1
n2
T1
T2
g
b
第二十四页,共101页。
g1
a
g2
b
g3
§7.3可靠性分配
可靠性分配是把设计任务书上规定的系统可靠度指标合理地分 配给组成系统的各个元件。分配的主要目的是确定每个元件合理 的可靠度指标,作为元件设计和选择的依据。
几种常用的可靠性分配方法
一、等分配法 这是最简单的一种分配方法。它是对系统中的全 部元件分配以相等的可靠度。 1.串联系统 如果系统中n个元件的复杂程度与重要性以及创造成本 都较接近,当把它们串联起来工作时,系统的可靠度则为Rsa,各元件 分配的可靠度为Ria ,
第四页,共101页。
可靠性试验概述

4 筛选试验
4.1 筛选试验的意义、特点
筛选试验:就是为了剔除寿命短的早期失效产 品,或为了选择长寿命产品而进行一种或几 种试验。通过可靠性筛选,剔除了早期失效 产品,批产品的使用可靠性便得到提高。
浴盆曲线
故 障 率
环境应力筛选
λ0
0
t0’
t0
t
可靠性筛选具有如下特点:
• (1) 可靠性筛选对于不存在缺陷而性能良好的 产品来说是一种非破坏性试验,而对于有潜在 缺陷的产品来说应能诱发其失效。
3.6 特别应注意“成功的可靠性增长试验代替可靠 性鉴定试验”时,应至少具备下列条件: ⑴ 具有可靠性鉴定试验所规定的试验环境条件、 故障判定规则,以及试验组织管理; ⑵ 对增长试验过程的跟踪应是严格的,有完整的 故障记录和完善的FRACAS系统,并对故障纠正和验 证过程有详尽的可追溯记录。 ⑶ 对可靠性增长试验结果,评价所用的数学方法 正确,置信水平选取符合要求,产品达到的MTBF水 平达到或超过鉴定试验要求。
T /r
(1)
r为试验中产品发生的责任故障总数
T为所有参试样品有效受试时间的总和,即
n
T ti i 1
(2)
Δ测定试验MTBF置信区间估计值(C为置信度取值)
a.单边估计
下限值:
L
T / T /
fL (c, r 1) fL (c, r)
定时截尾 定数截尾(3)
b.双边估计
下限值:
L
T T
试验方案{T,C}的典型OC曲线
θ1-产品MTBF检验下限;θ0-为产品MTBF检验上限; α-生产方风险;β-使用方风险
2.7 序贯截尾试验方案
序贯截尾试验方案的基本思路是:对于试验中发
产品质量检测中的可靠性实验设计

产品质量检测中的可靠性实验设计产品质量一直是制造业中的重要问题,而可靠性实验设计作为评估产品质量的一种重要方式,在保证产品可靠性方面发挥着关键作用。
本文将就产品质量检测中的可靠性实验设计进行探讨。
一、可靠性实验设计的重要性在产品质量检测中,可靠性实验设计的重要性不容忽视。
产品的可靠性是衡量产品质量的重要指标,同时也是产品能否满足用户需求、达到预期寿命的关键因素。
可靠性实验设计旨在通过模拟产品在实际使用过程中的各种不确定性因素,综合评估产品的可靠性水平。
通过可靠性实验设计,可以发现产品设计、制造、使用中存在的潜在问题,并且为优化产品设计和工艺提供可靠的数据支持。
二、可靠性实验设计的基本原则在进行可靠性实验设计时,有几个基本原则需要遵循。
首先,实验设计应该具有良好的可重复性和可比较性。
这意味着实验过程应该能够被其他人所重复,同时实验结果应该能够与其他实验进行比较,验证实验的准确性和可靠性。
其次,实验设计应该尽可能模拟产品在实际使用环境中的各种不确定性因素,如温度、湿度、振动等。
通过模拟这些因素,可以更全面、准确地评估产品在实际使用中的可靠性。
另外,实验过程应该具有可控性,即实验者能够对实验条件进行精确控制,以保证实验数据的可靠性和可重复性。
最后,实验方案应该具有一定的代表性,即能够充分反映产品在实际使用中的特点和情况,以提供准确的评估依据。
三、可靠性实验设计的方法与技术在可靠性实验设计中,有多种方法和技术可供选择。
其中,寿命试验是常用的一种可靠性实验方法。
该方法通过人工加速实验,模拟产品在正常使用条件下的寿命。
在实验过程中,可以通过监测产品的失效情况,来评估产品的可靠性水平。
此外,还有可靠性建模技术,该技术通过对不同因素的数学建模,以及实验数据的统计分析,预测产品的寿命和可靠性。
同时,还有仿真技术、试验设计技术等也可以应用于可靠性实验设计中。
四、可靠性实验设计的挑战和应对在进行可靠性实验设计时,会面临一些挑战。
可靠性试验介绍

环境应力与失效的关系
❖ 4 机械冲击和振动对产品的影响 机械冲击和振动主要是针对处于剧烈振动环境中的车用电子设备。可是最近由于一般电子设备也因为其便携化 而变得易受振动,因此机械应力的应用范围也广泛了。 机械应力所造成的失效主要是连接器、继电器等连接部件,当然对装配工艺不合理的设计也容易引起元器件的 脱落和引线短裂,对元器件内部工艺不良的产品会引起开路、短路、间歇连接。
环境应力与失效的关系
❖ 铝线中产生腐蚀过程: ① 水气渗透入塑封壳内→湿气渗透到树脂和导线间隙之中 ② 水气渗透到晶片表面引起铝化学反应
❖ 加速铝腐蚀的一些因素(铝金属导线腐蚀反应随着是否施加偏压而变化) ①树脂材料与晶片框架接口之间连接不够好(由于各种材料之间存在膨胀率的差异)。 ②封装时,封装材料掺有杂质或者杂质离子的污染(由于杂质离子的出现)。 ③非活性塑封膜中所使用的高浓度磷。 ④非活性塑封膜中存在的缺陷。
❖ 高温试验 ❖ 产品寿命遵循"10℃规则",因而高温试验作为最常用的试验,用于元器件和整机的筛选、老化试验、寿命试验、
加速寿命试验、评价试验、同时在失效分析的验证上起重要作用。 ❖ 高温试验的技术指标包括:温度、时间、上升速率。 ❖ 注意产品和元器件的最大耐受温度极限。 ❖ 样品放入试验箱内为保持样品的受热均匀性,样品距离箱壁的距离最少为5cm ❖ GB/T 2423.2中高温的试验方法分:散热样品的温度渐变,非散热样品的温度渐变 ❖ 试验结束后需要将样品在箱体内恢复至稳定状态,或将样品放置在常温常湿环境下进行恢复至稳定状态。
❖ :寿命 Ea:活化能 (eV) T :绝对温度 (K) A:常量 k :波尔兹曼系数 ❖ 上述公式显示半导体寿命取决于半导体受到的温度。 ❖ 加速的测试利用这一特性被称为温度加速测试不过例如一些因为热载体的影响导致的失效(高能源载体产生的电
可靠性试验设计与分析5

第四章(45) 可靠性试验设计与分析§4.4可靠性增长试验(Reliability Growth Test)一、概述可靠性增长:通过改正产品设计和制造中的缺陷,不断提高产品可靠性的过程。
产品试制阶段,由于设计缺陷与工艺上的不成熟,其可靠性一定会远低于预计的标准,通过试验发现故障,通过机理分析找出故障源,通过再设计与工艺的更改,以达到消除故障的目的,保证研制期间的可靠性达到预期的指标。
(再)设计试制产品试验故障纠正可靠性增长是不断反复设计、试验、故障、纠正这样一个循环过程。
是为达到可靠性增长目的而执行可靠性秩序中所采用的一种试验方法。
可靠性增长的三个主要因素:1).通过分析和试验找出产品的潜在故障源。
2).将存在问题(返馈),采取纠正措施更改设计。
3).对改进后的产品重新进行试验。
图4.23 可靠性增长过程二、可靠性增长试验目的:通过试验诱导出设计不良或工艺不成熟而引起的潜在故障,通过机理分析找出问题,在设计与工艺上加以纠正,从而达到可靠性增长目的。
可靠性增长试验耗费的资源和时间比较多,试验总时间通常为预期的MTBF目标值的5~25倍,所以也并不是所有产品都适宜于安排可靠性增长试验。
其试验大纲按照试验、分析、纠正(Test, Analysis And Fix test简称TAAF)这一过程来制定,为此要选定一个可靠性增长的模型,以便确定试验计划时所需考虑的因素。
1、可靠性增长模型目前在可修产品的增长试验中,普遍使用的杜安(Duane)模型。
有时为了使杜安模型的适合性和最终评估具有较坚实的统计学依据,可用AMSAA模型作为补充。
杜安模型是用于飞机发动机和液压机械装置等复杂可修产品的增长试验的。
模型未涉及随机现象,是确定性模型,即工程模型,而不是数理统计模型。
其基本假设:只要不断进行可靠性试验,系统可靠性增长(用MTBF的提高表示)与累积试验时间在双对数纸上成线性关系,直线的斜率是可靠性增长率的一个度量。
产品设计五性:可靠性、维修性、安全性、测试性及保障性知识讲解
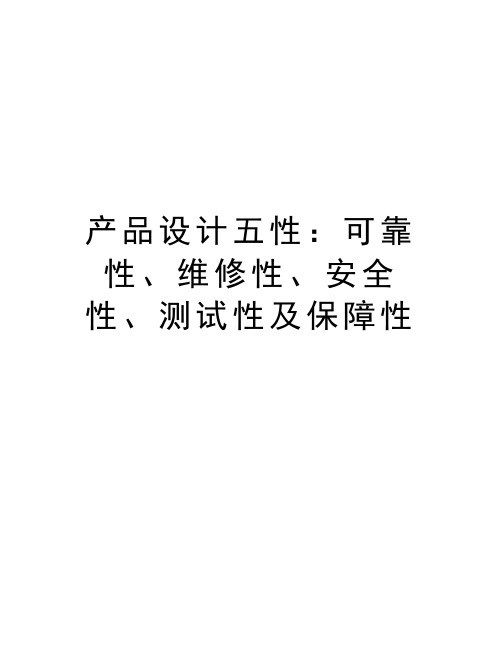
产品设计五性:可靠性、维修性、安全性、测试性及保障性3 “五性”的定义、联系及区别3.1 可靠性产品在规定的条件下和规定的时间内完成规定功能的能力。
可靠性的概率度量称为可靠度(GJB451-90)。
可靠性工程:为达到产品的可靠性要求而进行的一套设计、研制、生产和试验工作。
(GJB451-90) 显然,这个定义适用于各种装备、设备、系统直至零部件的各个产品层次。
可靠性是产品的一种能力,持续地完成规定功能的能力,因此,它强调“在规定时间内”;同时,产品能否可靠地完成规定功能与使用条件有关,所以,必须强调“在规定的条件下”。
为了使产品达到规定的可靠性要求,需要在产品研制、使用开展一系列技术和管理活动,这些工程活动就是可靠性工程。
即:可靠性工程是为了达到产品的可靠性要求而进行的一套设计、研制、生产和试验工作。
(GJB451-90)。
实际上,可靠性工程还应当包含产品使用、储存、维修过程中的各种保持和提高可靠性的活动。
3.1.1可靠性要求3.1.1.1 定性要求对产品的可靠性要求可以用定性方式来表达,满足这些要求使用中故障少、即使发生故障影响小即可靠。
例如,耐环境特别是耐热设计,防潮、防盐雾、防腐蚀设计,抗冲击、振动和噪声设计,抗辐射、电磁兼容性,冗余设计、降额设计等。
其中冗余设计可以在部件(单元)可靠性水平较低的情况下,使系统(设备)达到比较高的可靠性水平。
比如,采用并联系统、冷储备系统等。
除硬件外,还要考虑软件的可靠性。
3.1.1.2 定量要求可靠性定量要求就是产品的可靠性指标。
产品的可靠性水平用可靠性参数来表达,而可靠性参数的要求值就是可靠性指标。
常用的产品可靠性参数有故障率、平均故障间隔时间以及可靠度。
故障率是在规定的条件下和规定的时间内,产品的故障总数与时间(寿命单位总数)之比。
即平均使用或储存一个小时(发射一次或行驶100km)发生的故障次数。
平均故障间隔时间(MTBF)是在规定的条件下和规定的时间内,产品寿命单位(时间)总数与故障总次数之比。
可靠性试验分析及设计
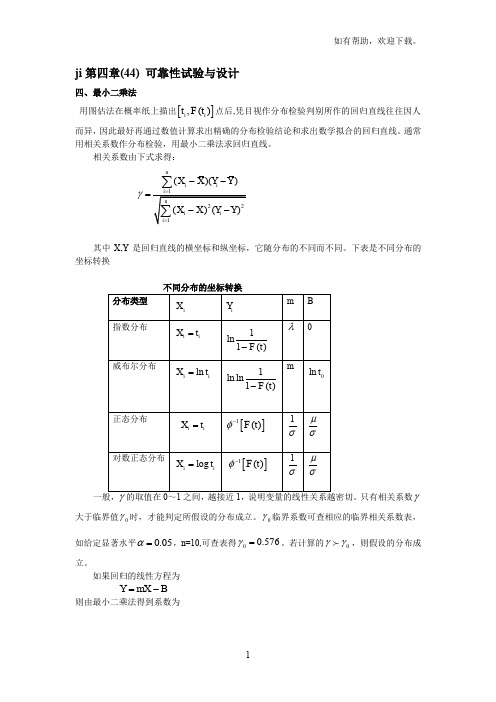
ji 第四章(44) 可靠性试验与设计四、最小二乘法用图估法在概率纸上描出[],()i i t F t 点后,凭目视作分布检验判别所作的回归直线往往因人而异,因此最好再通过数值计算求出精确的分布检验结论和求出数学拟合的回归直线。
通常用相关系数作分布检验,用最小二乘法求回归直线。
相关系数由下式求得:()()nii XX Y Y γ--=∑其中X,Y 是回归直线的横坐标和纵坐标,它随分布的不同而不同。
下表是不同分布的坐标转换只有相关系数γ 大于临界值0γ时,才能判定所假设的分布成立。
0γ临界系数可查相应的临界相关系数表,如给定显著水平0.05α=,n=10,可查表得00.576γ=。
若计算的0γγ,则假设的分布成立。
如果回归的线性方程为 Y mX B =- 则由最小二乘法得到系数为111112211ˆˆ1ˆ1()nni i i i nnn i i i ii i i n ni i i i Y mX BNX Y X Y N m X X N =======-+=-=-∑∑∑∑∑∑∑ 代入上表中的不同的分布,就可以得到相应分布的参数估计值。
五、最好线性无偏估计与简单线性无偏估计 1、无偏估计不同子样有不同的参数估计值ˆq,希望ˆq 在真值q 附近徘徊。
若ˆ()E q q =,则ˆq 为q 的无偏估计。
如平均寿命的估计为ˆit nq=å,是否为无偏估计?Q 1[]ˆ()[]ni ii i t E t E E nnnq qq =====å邋\ ˆq为q 的无偏估计 2、最好无偏估计定义若ˆk q 的方差比其它无偏估计量的方差都小,即ˆ()min ()k k D D q q =,则ˆkq 为最好无偏估计。
3、线性估计定义若估计量ˆq是子样的一个线性函数,即1ˆni i i a q ==C å,则称ˆq为线性估计。
4、最好线性无偏估计当子样数25n £时,通过变换具有()F msC -形式的寿命分布函数,其,m s 的最好线性无偏估计为:1ˆ(,,)rj i D n r j X m==åˆ(,,)j C n r j X s=å其中(,,),(,,)D n r j C n r j 分别为,m s 的无偏估计,有了,,n r j 后,可有专门表格查无偏系数(,,),(,,)D n r j C n r j 。
- 1、下载文档前请自行甄别文档内容的完整性,平台不提供额外的编辑、内容补充、找答案等附加服务。
- 2、"仅部分预览"的文档,不可在线预览部分如存在完整性等问题,可反馈申请退款(可完整预览的文档不适用该条件!)。
- 3、如文档侵犯您的权益,请联系客服反馈,我们会尽快为您处理(人工客服工作时间:9:00-18:30)。
第四章(45) 可靠性试验设计与分析§4.4可靠性增长试验(Reliability Growth Test)一、概述可靠性增长:通过改正产品设计和制造中的缺陷,不断提高产品可靠性的过程。
产品试制阶段,由于设计缺陷与工艺上的不成熟,其可靠性一定会远低于预计的标准,通过试验发现故障,通过机理分析找出故障源,通过再设计与工艺的更改,以达到消除故障的目的,保证研制期间的可靠性达到预期的指标。
可靠性增长是不断反复设计、试验、故障、纠正这样一个循环过程。
是为达到可靠性增长目的而执行可靠性秩序中所采用的一种试验方法。
可靠性增长的三个主要因素:1).通过分析和试验找出产品的潜在故障源。
2).将存在问题(返馈),采取纠正措施更改设计。
3).对改进后的产品重新进行试验。
图4.23 可靠性增长过程二、可靠性增长试验目的:通过试验诱导出设计不良或工艺不成熟而引起的潜在故障,通过机理分析找出问题,在设计与工艺上加以纠正,从而达到可靠性增长目的。
可靠性增长试验耗费的资源和时间比较多,试验总时间通常为预期的MTBF目标值的5~25倍,所以也并不是所有产品都适宜于安排可靠性增长试验。
其试验大纲按照试验、分析、纠正(Test, Analysis And Fix test简称TAAF)这一过程来制定,为此要选定一个可靠性增长的模型,以便确定试验计划时所需考虑的因素。
1、可靠性增长模型目前在可修产品的增长试验中,普遍使用的杜安(Duane)模型。
有时为了使杜安模型的适合性和最终评估具有较坚实的统计学依据,可用AMSAA 模型作为补充。
杜安模型是用于飞机发动机和液压机械装置等复杂可修产品的增长试验的。
模型未涉及随机现象,是确定性模型,即工程模型,而不是数理统计模型。
其基本假设:只要不断进行可靠性试验,系统可靠性增长(用MTBF 的提高表示)与累积试验时间在双对数纸上成线性关系,直线的斜率是可靠性增长率的一个度量。
图4.24 可靠性增长曲线上述描绘了杜安可靠性增长模型。
其增长率范围在0.3~0.7之间,若增长在0.3以下,说明纠正措施不够有力,在0.7以上表明采用了强有力的纠正措施。
从曲线上还可表明,制定可靠性增长大纲所需要的四个因素:(1).系统固有的MTBF 值P q 与要求的MTBF 值s θ关系:p θ在设计时用预测的方法确定,而s q (可接受值)比P q 低些,这是验证试验之前应增长到的值。
(2).增长曲线的起始MTBF 值0q :当P q 预期值为200h £时,增长线以100试验小时(横坐标)与10%P q (纵坐标)为起始点。
当200P h q >,则以100h 试验与50%P q 为起始点。
(3).关于MTBF 增长率a :取决于大纲要求,如制定合理并执行严格,增长率可达0.6,没有特殊考虑时可取0.1a =。
(4).增长所要求的总时间: 增长线与指标要求的MTBF 值的水平线交点所对应的总试验时间即为预计总试验时间。
美国军用标准有个试验指南:当固定的试验持续时间为规定的MTBF (s q )的10~25倍时,该时间完全可以满足达到50~2000hMTBF 内预期的设备可靠性增长需要。
当规定的MTBF 在2000h 以上时,其持续试验时间取决于设备的复杂性和大纲要求,但至少应是要求的MTBF 的一倍。
无论任何情况下,持续时间试验都不得少于2000h 或不多于10000h 。
2、可靠性增长监测将试验所得的累积的MTBF 值(其数值为累积试验时间除以到那个时间为止所发生的总故障次数)点在大纲所确定的可靠性增长模型图上,并与原计划增长率作比较,下述情况认为有关故障分析和纠正措施的活动是良好的。
(1).真实增长线高于计划增长线;(2).真实增长线与要求的MTBF 值交点所对应的总试验时间与计划的总试验时间相等或小于比值。
三、杜安模型及模型参数估计设增长试验的开始时间0t =,t 为试验过程中某个时刻的累积试验时间,()r t 为(0,)t 时间内受试产品的故障数。
()r t 实际是非连续函数,因故障计数只能非负整数。
杜安模型在规定的前提下,把()r t 当作连续函数处理。
杜安模型引入累积故障率的概念,用l S 表示,定义为:()r t tl S =它是一个计算值,没有具体物理意义。
但它随着累积试验时间t 增加,其中蕴含着产品可靠性变化规律。
杜安通过数据分析发现,l S 对于累积试验时间t 在双边对数坐标纸上趋于一条直线,即:瞬时故障率:()()(1)r t Kt tdr t K t dt a a l l a -S -ìï==ïïíïï==-ïïî1()r t Kt a-?式中:λ∑为累积故障率,λ为瞬时故障率,r(t) 为t 期间发生的故障次数,t 为总的实验时间,α为增长率。
由于可修产品的可靠性参数常用MTBF 表示,因此运用杜安模型时,派生出两个术语:累积MTBF :11()K t a q l -S S==瞬时MTBF :11()[(1)]K t a q a l-==-在故障间隔时间序列服从指数分布的假设下,这两个MTBF 与相应的故障率互为倒数关系。
这两个MTBF 表达式式是杜安模型的重要结论之一,当,K a 确定后,就表述了可靠性增长试验中的变化规律。
另一个结论是由上式导出的(两式相除),整理得: (1)q q a S=- (说明瞬时θ是累积θ∑的1/(1-α))两边取对数:1ln ln ln1q q aS =+- (在对数坐标上θ比θ∑高出一个常值ln(1/(1-α)))由于q S (累积)在试验时间很容易计算出来,利用上式就容易求瞬时MTBF q ,从而使杜安模型方便地运用。
其在图上模型如下图所示:试验中假设有n 个故障数据12,,,n t t t 鬃鬃鬃,代入ˆit n q =å,就可得一系列ˆ()(1,2,,)()i ii t t i n n t q ==鬃鬃鬃,()i n t 表示i t 时刻总的试验样本数。
从而在双对数坐标纸上画出{}log ,log i i t q 的直线,由该直线对于任意一个时刻t 得到增长率a :00(log log )(log log )t t t a q q =--t 为累积试验时间,t q 为t 时刻观察到的MTBF 值,0q 为最初测定的MTBF 值。
从理论上讲,杜安模型有明显不足之处,从1[(1)]K t aq a -=-,画出,当0t ®,MTBF q 0®,这是模型虚构情况。
实际产品的瞬时q 不可能为零,同样t ,MTBF q ,这又是不可能的。
但这两点不足,实践证明并不影响增长试验的应用。
其最大的不足在于模型中未考虑随机现象,因而对最终结果不能提供数理统计的评估。
四、AMSAA 模型把增长过程中的故障数的累积过程建立在随机过程理论上,认为累积故障过程就是一个非齐次泊松过程,即在(0,)t 时间内,受试产品发生的故障数()r t 是一个随机变量,t 在增加中,()r t 也发生变化,这种变化反映在()r t的统计特性上。
主要是它的数学期望和方差。
这样就形成一个随机过程(又称为计数过程){}(),0r t t ³表示。
在给定时刻t ,发生n 个累积故障数服从非齐次Poisson 过程。
{}()[()]()!n r t r t P r t n e n S -S ==式中: 0()[()]()tr t E r t t dt l S ==ò,为累积故障数的数学期望,()t l 叫故障强度函数。
()r t S 有二个条件:①.它是递增的,即故障数不会减少,即只要21t t >,必有21()()r t r t >。
②. ()r t S 的增量是独立的,即21()()r t r t -的分布不受1()r t 取值影响,也服从Poisson 分布。
{}21()()2121[()()]{[()()]},1,2,!nr t r t r t r t P r t r t n e n n -+--==?鬃鬃鬃 当()t l 与t 为无关的常量时,上述随机过程为齐次Poisson 过程。
当()t l 是t 的函数时,上述随机过程为非齐次Poissongch 。
AMSAA 模型认为增长过程中,累积故障数是一个非齐次泊松过程,其故障强度函数为:1()b t a b t l -=鬃 (*)0a >, 称为尺度参数,0b >,称为形状参数。
与杜安模型相似:(1)r Kt t dr Kt dt a a l l a -S -ìï==ïïïíï==-ïïïî只要用1b a =-,a K =代入(*)式,即可得到杜安模型。
由此可见,杜安模型是非随机变量的累积故障数,而AMSAA 是依据随机过程,其故障数是随机过程的数学期望,它们两者的函数表达式却是完全相同的,因此通常说AMSAA 是杜安模型的概率解释。
AMSAA 模型与杜安模型有同样的不足:0t ®或t ,其故障率也分别趋于零和无穷大,与工程实际不符。
§4。
5可靠性验证试验(Reliability Compliance Test)目的:确定产品是否符合规定的可靠性指标要求,作为定货方接受产品的依据。
包括:可靠性鉴定试验(Reliability Qualification Test)――为了验证产品设计是否达到规定的最可接受的可靠性要求。
一般用于定型鉴定,是产前的试验,为生产决策提供管理信息。
可靠性验收试验(Reliability Acceptance Test)――可交或已交付产品在规定条件下所作的试验,其目的是确定产品是否规定的可靠性要求对整批产品进行逐个检验,一般是在经济上是不可行的,因此,仅抽取部分样品(一批中)进行有关试验,鉴定其可靠性指标是否满足要求,故又称可靠性抽样试验。
抽样试验特点:以样品特性值来估计总体的特性值。
所以验证试验属于统计试验。
所以可靠性验证试验涉及抽样、试验和判定等内容。
一、抽样试验的一般原理一次抽样(Single Sampling Inspection):根据从批中一次抽取得样本的检验结果,决定是否接受这批产品叫“一次抽样检验”。
结论为:接受“Acceptance ”;或“拒收” “Rejection ”。
典型的一次抽样检验方案思路如下:随机抽取一个样本量为n 的样本进行试验,其中有r 个故障,规定一个合格判定数C : 若r C £,认为该批产品可靠性合格,可接受。