棒线材厂降低轧辊消耗实践
降低轧辊消耗的几种方法
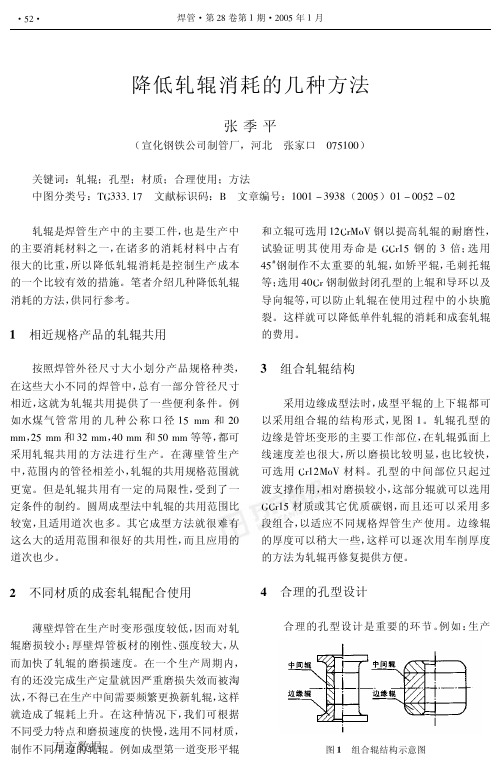
$" 轧辊孔型修复
实施轧辊孔型的再修复是降低辊耗的最有效 措施。轧辊孔型随着生产的持续,磨损加重,当孔 型不能很好地控制管坯时就需要重新修磨。孔型 每修磨一次,表面硬度就会相应有所降低,因而必 须进行表面淬火以恢复硬度。立辊在底径允许的 情况下,可以进行多次修磨,个别上平辊外径修到 一定量后,受到管坯边缘上升调试影响而不能继 续修磨时,可采用对整套辊进行堆焊的方法来解 决这一问题,以期进一步提高轧辊的利用价值。
! ! 轧辊是焊管生产中的主要工件,也是生产中 的主要消耗材料之一,在诸多的消耗材料中占有 很大的比重,所以降低轧辊消耗是控制生产成本 的一个比较有效的措施。笔者介绍几种降低轧辊 消耗的方法,供同行参考。
!" 相近规格产品的轧辊共用
和立辊可选用 %.12345 钢以提高轧辊的耐磨性, 试验证 明 其 使 用 寿 命 是 ’12%$ 钢 的 ( 倍;选 用 0$ 6 钢制作不太 重 要 的 轧 辊,如 矫 平 辊,毛 刺 托 辊 等;选用 0"12 钢制做封闭孔型的上辊和导环以及 导向辊等,可以防止轧辊在使用过程中的小块脆 裂。这样就可以降低单件轧辊的消耗和成套轧辊 的费用。
就轧辊加工工艺而言,有些可用精铸的方法, 如成型开口孔型的上平辊。这些轧辊的形体比较 集中,受力比较均衡,磨损不大,可利用废旧轧辊 做原料,用精铸的方法制做,以降低成本。但是这 种方法不适合下平辊和立辊。在硬度方面,轧辊 表面硬度不够时也会加快轧辊孔型的磨损,所以 热处理时要选取较好的淬火工艺,使轧辊既达到 高硬度,又不发生脆裂,并且保证硬度均匀。
%" 轧辊加工工艺
图 !" “ !”式组合辊结构示意图
确定轧辊外形尺寸时,只要机组的空间允许, 应尽可能地将轧辊的外形尺寸放至最大,特别是 立辊,这样就可以增加轧辊的修复次数,从而达到 降低辊耗的目的。
武钢1700mm热连轧机降低轧辊消耗的实践

武钢1700mm 热连轧机降低轧辊消耗的实践唐本立,陈 刚(武钢热轧带钢厂湖北武汉430083)摘 要:轧辊消耗指标是热连轧机主要技术经济指标之一,对比分析找出武钢1700mm 热连轧机轧辊消耗高的原因,通过开展有针对性的课题攻关,把研究成果运用到生产实践中,获得降低轧辊消耗的明显效果。
关键词:轧辊消耗;改造辊径;综合利用;控制剥落中图分类号:TG 333.17 文献标识码:B 文章编号:1008-4371(2004)01-0025-04Practice on R eduction of R oll Consumption of 1700mmContinuous H ot R olling Mill in WISCOT ANG Ben -li ,CHE N G ang(The H ot R olling S trip M ill of WISC O Wuhan Hubei 430083,China )Abstract :The roll consum ption is one of the critical im portant technical and economic indica 2tors for the continuous hot rolling mill in WISC O have been achieved in reduction of the roll con 2sum ption by way of scientific research in light of the technical problems and application of results of the scientific study in the production.K eyw ords :roll consum ption ;revam p of roll diameter ;com prehensive utilization ;control on peeling off收稿日期:2003-09-02作者简介:唐本立(1954- ),男,湖北仙桃市人,高级工程师. 轧辊消耗指标是热连轧机的主要技术经济指标之一。
棒线材厂降低轧辊消耗实践

棒线材厂降低轧辊消耗实践棒线材厂降低轧辊消耗实践【摘要】针对棒线材厂降低生产成本工作,通过采用新材质轧辊、进行工艺优化和一系列技术改造等措施来降低轧辊消耗为棒线材厂降成本工作做出贡献。
【关键词】轧辊消耗技术改造工艺优化1.前言川威集团威远钢铁有限公司棒线材厂有一条高棒和一条高线两条生产线,其中全连轧高棒生产线以φ550×3、φ450×3、φ380×6、φ320×6(其中三架为平立可转换)轧机组成,轧后设有水冷器冷却系统。
设计年产能力为60万吨,主要产品为φ12mm~φ40mm的热轧带肋钢筋和φ14mm~φ40mm的热轧直条圆钢,产品品种为普通碳素结构钢(Q195~Q275)及低合金钢(20MnSi)等;高线生产线以φ580×4、φ475×5、φ275×4、φ210×10轧机组成,轧后设有水冷器冷却系统。
设计年产能力为30万吨,主要产品为φ5.5mm~φ14mm的热轧带肋钢筋盘条和热轧圆钢,产品品种为普通碳素结构钢(Q195)、低合金钢(20MnSi)及焊条钢和焊丝钢等。
棒线材厂为追求成本最小化,效益最大化,一直致力于本厂的降成本工作,而棒线材厂高棒车间的轧辊消耗和高线车间的辊环消耗作为棒线材厂生产成本中的大头则成为了棒线材厂降成本工作中的重点,通过一系列的技术攻关和工艺优化改进,极大的降低了棒线材厂的辊耗,达到了国内领先水平,为棒线材厂降成本工作做出了巨大贡献。
2.解决措施2.1提高轧辊强度目前高棒车间粗、中轧轧辊直径使用较小,特别是采用无孔轧制新工艺后,轧制量较未采用无孔轧制工艺以前增大50%,同时考虑到今后使用160mm*160mm钢坯后轧制负荷增大,现有轧辊强度不足以满足生产需要,容易造成断辊从而导致生产成本增高。
因此,在满足换辊装配要求的情况下,对高棒粗、中轧轧机进行改造,将轧辊最大使用直径在现有基础上扩大30-40mm以提高轧辊强度,在其使用周期内提高总过钢量,降低轧辊消耗,降低生产成本,同时,将减少断辊机率。
采取综合措施降低轧辊轴承消耗
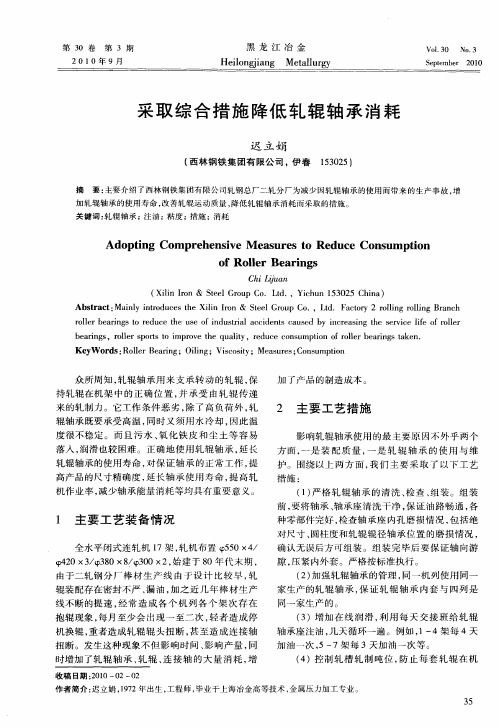
Ad ptng Co pr he sv e s e o Re uc n um pto o i m e n ie M a ur st d e Co s in
o le a i s fRo l r Be r ng
第 3 卷 0
第 3 期
黑 龙 江 冶 金
V0 . 0 13
No 3 .
201 0年 9月
H i nj n Mea ug el g a g o i t lry l
Se tmbe 2 0 pe r 01
采 取 综 合 措 施 降低 轧 辊 轴 承 消 耗
迟 娟
r le e rn st e u e t e u e o n u tila c d n s c u e y i c e sn h e vc ie o ol r ol rb a i g o r d c h s fi d sra c i e t a s d b n r a i g t e s r ie lf fr l e be rn s ol rs o o i r v h uaiy,r du e c n u to frle e rn s tk n a i g ,r le p ts t mp o e t e q lt e c o s mp i n o ol rb ai g a e .
机换 辊 , 者造 成轧 辊 辊 头扭 断 , 至 造 成 连接 轴 重 甚 扭 断 。发生 这种 现象 不 但 影 响 时 间 、 响产 量 , 影 同 时增加 了轧 辊 轴 承 、 辊 、 接 轴 的 大 量 消 耗 , 轧 连 增
收 稿 日期 : 1 2 0—0 0 0 2— 2
( )增 加 在 线 润 滑 , 用 每 天 交 接 班 给轧 辊 3 利 轴 承 座注 油 , 天循 环一 遍 。例 如 , 4架 每 4天 几 1— 加 油 一次 , 5—7架 每 3天 加 油一次 等 。 ( )控 制 轧 槽 轧 制 吨位 , 止 每 套 轧 辊 在 机 4 防
热轧生产轧辊降耗实践

关键 词 :热轧 ; 工作辊 ; 辊耗
Y a n g H o n g k a i , L i Q i n g x i a n , Z h a n g S h o u f e n g , X i a n g J u n , Z h a n g Z h i y o n g
( Ho t R o H e d S t r i p S t e e l Mi l l o f A n g a n g S t e e l C o . , L t d . , A n s h a n 1 1 4 0 2 1 , L i a o n i n g , C h i n a )
中图分 类号 : T G 3 3 5
文献 标识 码 : A
文章 编号 : 1 0 0 6 — 4 6 1 3 ( 2 0 1 5 ) 0 5 — 0 0 5 4 — 0 5
P r a c i t c e o f Re d u c i n g Ro l l Co n s u mp i t o n i n Ho t Ro l l e d S t r i p S t e e l P r o d u c t i o n Li n e
Abs t r ac t :Th e ma i n f a c t o r s f o r i n lu f e n c i n g t h e c o n s u mp t i o n r e d u c t i o n o f r o l l s i n t h e 1 7 00
棒线材生产技术与节能减排低成本轧制技术发展探索
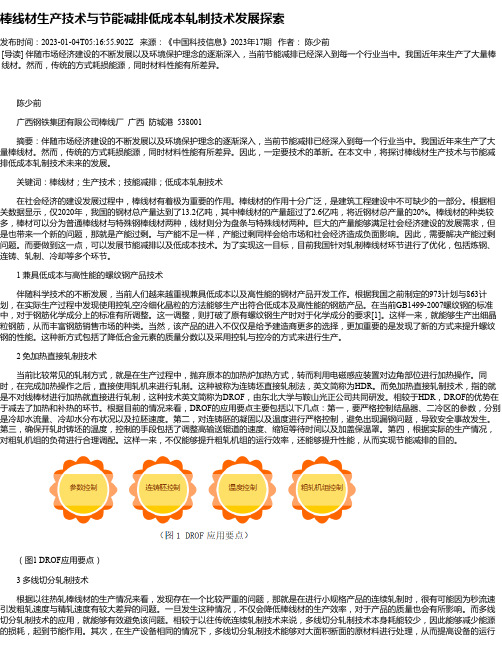
棒线材生产技术与节能减排低成本轧制技术发展探索发布时间:2023-01-04T05:16:55.902Z 来源:《中国科技信息》2023年17期作者:陈少前[导读] 伴随市场经济建设的不断发展以及环境保护理念的逐渐深入,当前节能减排已经深入到每一个行业当中。
我国近年来生产了大量棒线材。
然而,传统的方式耗损能源,同时材料性能有所差异。
陈少前广西钢铁集团有限公司棒线厂广西防城港 538001摘要:伴随市场经济建设的不断发展以及环境保护理念的逐渐深入,当前节能减排已经深入到每一个行业当中。
我国近年来生产了大量棒线材。
然而,传统的方式耗损能源,同时材料性能有所差异。
因此,一定要技术的革新。
在本文中,将探讨棒线材生产技术与节能减排低成本轧制技术未来的发展。
关键词:棒线材;生产技术;技能减排;低成本轧制技术在社会经济的建设发展过程中,棒线材有着极为重要的作用。
棒线材的作用十分广泛,是建筑工程建设中不可缺少的一部分。
根据相关数据显示,仅2020年,我国的钢材总产量达到了13.2亿吨,其中棒线材的产量超过了2.6亿吨,将近钢材总产量的20%。
棒线材的种类较多,棒材可以分为普通棒线材与特殊钢棒线材两种,线材则分为盘条与特殊线材两种。
巨大的产量能够满足社会经济建设的发展需求,但是也带来一个新的问题,那就是产能过剩。
与产能不足一样,产能过剩同样会给市场和社会经济造成负面影响。
因此,需要解决产能过剩问题。
而要做到这一点,可以发展节能减排以及低成本技术。
为了实现这一目标,目前我国针对轧制棒线材环节进行了优化,包括炼钢、连铸、轧制、冷却等多个环节。
1 兼具低成本与高性能的螺纹钢产品技术伴随科学技术的不断发展,当前人们越来越重视兼具低成本以及高性能的钢材产品开发工作。
根据我国之前制定的973计划与863计划,在实际生产过程中发现使用控轧空冷细化晶粒的方法能够生产出符合低成本及高性能的钢筋产品。
在当前GB1499-2007螺纹钢的标准中,对于钢筋化学成分上的标准有所调整。
优化轧辊管理降低辊耗
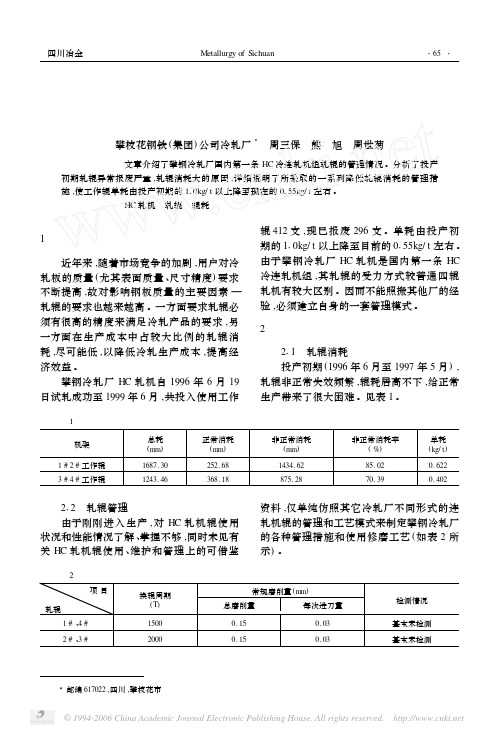
从实际生产反映的情况来看 ,现行的管 理制度能满足要求 ,对把轧辊消耗降低到目 前的 0157kg/ t (见表 7) 和杜绝爆辊起了重要 的作用 。
使用过的工作辊 ,磨工参照《轧辊质量信
息传递记录》并对应实际辊面情况 ,再根据 《工作辊磨下量》中相应的一项确定磨削量 ; 对因有缺陷而重磨的轧辊 ,磨工应根据重磨
辊的缺陷形式和大小以及探伤员的标注确定
磨削量 :当班磨过的每一根轧辊都应在相应 的记录本上做好记录 ,直径和辊号必须与辊 面所标注对应且准确无误 ;缺陷辊还应标注
·66 ·
1999 年第 5 期
上述措施缺乏针对性和科学性 ,从实际 生产中也发现存在许多问题 。
213 初期暴露的问题 (1) 换辊周期过长 ,磨削量过小 。HC 轧 机由于 中 间 辊 的 轴 向 移 动 以 及 弯 辊 力 的 使 用 ,轧辊受力状况明显区别于普通四辊轧机 , 工作辊辊面局部磨损严重 。其换辊周期相对 于普通轧机必应大大缩短 ,否则容易产生疲 劳裂纹或掉肉 ,且 0115mm 的常规磨削量根 本无法磨净工作辊每次上机轧制后的表面损 伤; (2) 对辊身表面缺陷及其危害的认识了 解不够 。冷轧辊绝大多数的表层剥落 (即爆 辊) 都不是自然产生的 ,而是在一定的时间内 发展形成的 ,通常是以辊身表面微裂纹为其 起点 ,在轧制持续的负荷作用下发展成疲劳 断裂 。所以轧辊表面裂纹的检测 ,在冷轧辊 管理工作中至关重要 ; (3) 轧辊信息传递缺乏严肃性且不畅通 。 在轧辊信息中有重要作用的“换辊单”经常没 有或所填产量 、长度与实际严重不符 ,造成管 理方对该辊的性能无法及时 、准确掌握 ;另磨 工和装配工之间没有轧辊信息的传递 ,磨工 磨辊处于盲目磨削的状态 ; (4) 磨削质量较差 。由于对轧辊不规范 磨削也会产生缺陷的认识不够 ,磨削中普遍 存在大进给量 、快速磨削 、磨削量极少的现 象 。以致磨完的轧辊一是其疲劳层没有除 去 ;二是即使下机的轧辊没有裂纹 ,也会因磨 削方法不当产生烧伤 、裂纹 ; (5) 轧辊的周转处于缺乏监管 、无序 、混
伯恩斯港厂降低轧辊消耗量的措施

伯恩斯港厂降低轧辊消耗量的措施伯恩斯港厂降低轧辊消耗量的措施安赛乐米塔尔集团在全球共运营24 家碳钢热轧带钢厂(HSM),每座带钢厂都有自己特定的产品与用户。
由于每一个厂的历史和当地市场需求的差异,这些带钢厂处在技术的不同发展阶段。
无论发展差异如何,安赛乐米塔尔集团已具备为各种问题交流解决方案的知识与经验。
自2006 年以来,安赛乐米塔尔伯恩斯港厂在热轧带钢生产方面已经与美国国内与国外各厂交流了知识与经验。
随着这一过程进行,在欧洲、南美和北美的三个厂被看成这方面的标杆:Gent(比利时)、Tubarao(巴西)和Dofasco(加拿大),作为这一活动的结果,制定出“结对工程”。
这一对标过程对所有涉及到的热轧带钢厂都非常有益。
通过钢厂总经理和部门经理的研究讨论,进行了一些改进,从而优化轧机稳定性,最终提高了带钢质量。
2008 年,当检查分析伯恩斯港厂HSM 计划外的换辊数量时,发现该厂在轧辊更换方面绩效差。
2009 年内,经过方法论途径,使用源于团队会议、头脑风暴和统计分析产生的理念,改变了轧辊更换频率高的状况。
仅采用几项技术,在没有资本投入的情况下实现了良好结果。
这一结果是通过结构性试验、知识共享以及改善作业而实现的。
以下将具体介绍在2009 年使用的方法和采取的一些技术。
在10 个月的时间内,实现了质量改善与轧辊费用降低。
2010 年,安赛乐米塔尔集团努力维持在2009 年通过标准化和自动化所实施的工艺变更而赢得的利益。
轧辊车间采取系列措施,使轧辊研磨量降低,同时在轧机的最后机架采用耐磨性更好的轧辊,如在F5 用高Cr 轧辊,F4用高速钢复合(HSS-CPC)轧辊等。
1 伯恩斯港厂80 英寸热轧带钢生产线伯恩斯港厂是安赛乐米塔尔在美国最大的钢厂,是一座联合钢铁厂。
该厂有2 座高炉,具备年产500 万t 钢水的能力。
安赛乐米塔尔伯恩斯港厂前身为伯利恒钢厂。
伯恩斯港厂的主要用户为汽车工业,主要产品为热轧、冷轧和涂层薄板。
降低钢铁料消耗实践概要
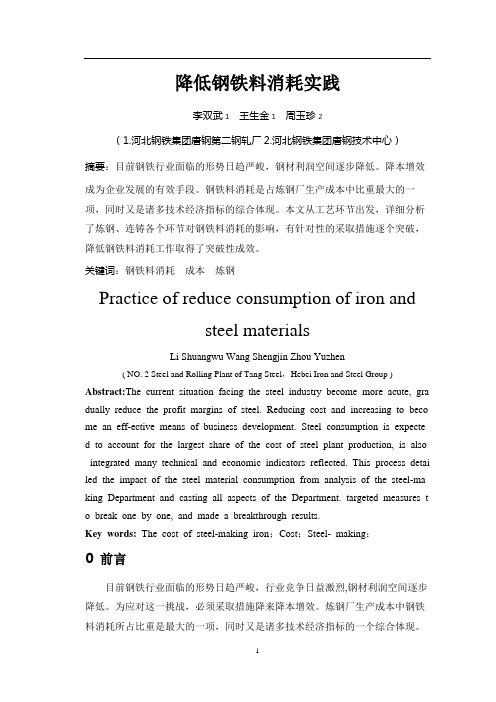
降低钢铁料消耗实践李双武1王生金1周玉珍2(1.河北钢铁集团唐钢第二钢轧厂2.河北钢铁集团唐钢技术中心)摘要:目前钢铁行业面临的形势日趋严峻,钢材利润空间逐步降低。
降本增效成为企业发展的有效手段。
钢铁料消耗是占炼钢厂生产成本中比重最大的一项,同时又是诸多技术经济指标的综合体现。
本文从工艺环节出发,详细分析了炼钢、连铸各个环节对钢铁料消耗的影响,有针对性的采取措施逐个突破,降低钢铁料消耗工作取得了突破性成效。
关键词:钢铁料消耗成本炼钢Practice of reduce consumption of iron andsteel materialsLi Shuangwu Wang Shengjin Zhou Yuzhen( NO. 2 Steel and Rolling Plant of Tang Steel,Hebei Iron and Steel Group ) Abstract:The current situation facing the steel industry become more acute, gra dually reduce the profit margins of steel. Reducing cost and increasing to beco me an eff-ective means of business development. Steel consumption is expecte d to account for the largest share of the cost of steel plant production, is also integrated many technical and economic indicators reflected. This process detai led the impact of the steel material consumption from analysis of the steel-ma king Department and casting all aspects of the Department. targeted measures t o break one by one, and made a breakthrough results.Key words:The cost of steel-making iron;Cost;Steel- making;0 前言目前钢铁行业面临的形势日趋严峻,行业竞争日益激烈,钢材利润空间逐步降低。
降低中厚板辊底式热处理炉能耗的生产实践

第 4期
赵房亮等: 降低中厚板辊底式热处理炉能耗的生产实践
述 了改进 的方法和过程 , 在使用 中效果 良好 。 关键词 辊底式热处理炉
Pr d c i n P a t e o d c n e g n u p i n o u to r c i f Re u i g En r y Co s m to c
o l r He r h He t Tr a m e tFu n c f Ro l a t a e t n r a e e f r M e i m n a y Pl t o du a d He v a e
值 和压力 波动较 大 , 烧 嘴 及煤 气 管 道 造 成严 重 对
腐蚀 或堵 塞 , 不利 于 煤气 的完 全 燃 烧 。燃 烧 系统 采 用 自身 预热式 烧嘴 , 种烧 嘴 自带燃烧 室 , 燃 这 且
烧后 废气 喷 出速 度 >10m s故 嘴前 空气 煤气 压 0 / , 力 相互影 响较大 , 就 是这 种 烧 嘴 空 气 与煤 气 配 也 比对 压力 波动敏 感 。这 种煤气 经 常导致 煤气 管道 被焦 油严 重堵塞 , 阀体前 后管 径缩 径 , 空气 阀门过
必 经之 路 。新 钢 公 司 中 厚 板 厂 热处 理 生 产 线 于 20 0 9年 2月投 产 , 3座辊 底式 热 处理 炉 , 中 , 有 其
配 型不 合 理 , 密封 效果 极 差 , 钢板 进 、 在 出料 时不
能形成 隔 热层 , 炉气 外 溢 , 热 面过 大 , 成热 量 散 造
・
第 1 8卷第 4期 2 ‘ 21 0 0 2年 8月
降低轧辊辊耗的有效方式
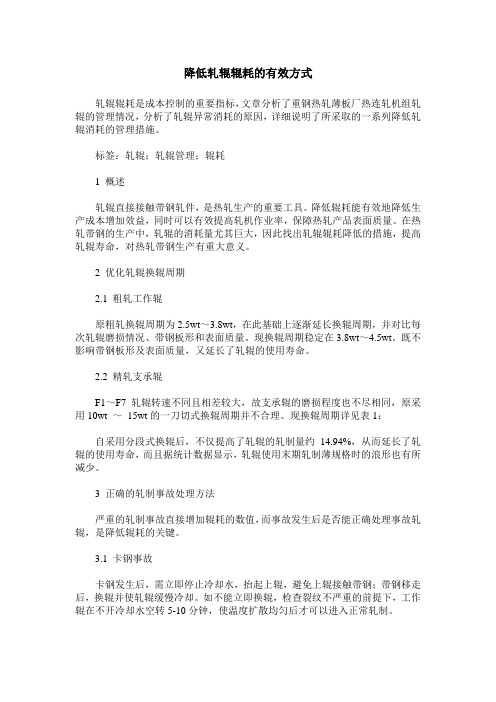
降低轧辊辊耗的有效方式轧辊辊耗是成本控制的重要指标,文章分析了重钢热轧薄板厂热连轧机组轧辊的管理情况,分析了轧辊异常消耗的原因,详细说明了所采取的一系列降低轧辊消耗的管理措施。
标签:轧辊;轧辊管理;辊耗1 概述轧辊直接接触带钢轧件,是热轧生产的重要工具。
降低辊耗能有效地降低生产成本增加效益,同时可以有效提高轧机作业率,保障热轧产品表面质量。
在热轧带钢的生产中,轧辊的消耗量尤其巨大,因此找出轧辊辊耗降低的措施,提高轧辊寿命,对热轧带钢生产有重大意义。
2 优化轧辊换辊周期2.1 粗轧工作辊原粗轧换辊周期为2.5wt~3.8wt,在此基础上逐渐延长换辊周期,并对比每次轧辊磨损情况、带钢板形和表面质量。
现换辊周期稳定在3.8wt~4.5wt。
既不影响带钢板形及表面质量,又延长了轧辊的使用寿命。
2.2 精轧支承辊F1~F7轧辊转速不同且相差较大,故支承辊的磨损程度也不尽相同,原采用10wt ~15wt的一刀切式换辊周期并不合理。
现换辊周期详见表1:自采用分段式换辊后,不仅提高了轧辊的轧制量约14.94%,从而延长了轧辊的使用寿命,而且据统计数据显示,轧辊使用末期轧制薄规格时的浪形也有所减少。
3 正确的轧制事故处理方法严重的轧制事故直接增加辊耗的数值,而事故发生后是否能正确处理事故轧辊,是降低辊耗的关键。
3.1 卡钢事故卡钢发生后,需立即停止冷却水,抬起上辊,避免上辊接触带钢;带钢移走后,换辊并使轧辊缓慢冷却。
如不能立即换辊,检查裂纹不严重的前提下,工作辊在不开冷却水空转5-10分钟,使温度扩散均匀后才可以进入正常轧制。
3.2 粘钢事故首先清除粘钢。
后应对粘钢区域进行详细检查,包含:硬度、裂纹、探伤等,必须清除此粘钢影响区,保证辊面硬度均匀、无裂纹。
4 创新轧辊缺陷修磨对策从2015年8月至2016年4月非计划换辊统计可以看出事故轧辊占总换辊量的69%。
因此轧制事故发生后,及时正确地处理轧辊,可最大程度的减少轧辊不必要损伤,延长轧辊使用寿命,降低辊耗。
降低中厚板轧机工作辊消耗的方法

降低中厚板轧机工作辊消耗的方法李 明(河北钢铁股份有限公司 )摘 要 论述工作辊消耗高的原因 、改进措施及实施效果 ,通过优化工作辊材质和硬度 ,改进操作 ,提高磨 削质量 ,优化辊型设计和完善轧辊的无损检测 ,保证轧辊使用安全 ,最终达到保证正常生产 、提高产品质量 、降 低生产成本的目的 。
关键词 工作辊 硬度检测 超声波探伤M ethods of Reduc i n g W ork Roll W ear i nM ed i u m and Heavy Pl a t e Producti o nL i M i ng( H B IS H a ndan Ir on and Stee l Co , L td )A b s tra c t Th i s p a p e r m a i n l y ex p a t ia t e s on va r i o u s a s p e c t s of cau s e s of h i g h wo r k r o l l wea r , co r rec t ive m e a s u r e s and the ir i m p lem en t ing effec ts .B y op ti m izing the m a te ria l and ha rdne ss of wo rk ro lls, i m p roving the ir u sag e, enhan 2 c ing the grind in g qua lity, op ti m izing ro ll p r ofile de sig n and i m p r oving the nonde struc tive de tec tion and en su ring o p e r a 2 ti o n safe t y, no r m a l p r oduc t i o n, p r oduc t qua l ity and lowe r p roduc t i o n co s t have been fina l ly m a i n t a i ned .Keyword s W o r k r o l ls, H a r dne s s te s t, U ltra s on i c flaw de t ec t ion0 前言用后期成为裂纹源 ,最终造成轧辊剥落 ;工作层厚 度较薄 ,轧辊使用后期接近结合层时 ,受轧制过程中交变应力的作用 ,使缺陷扩展 ,造成剥落 。
浅谈降低热轧轧辊消耗的有效方式

浅谈降低热轧轧辊消耗的有效方式摘要:通过系统分析轧辊车间运行数据,针对热轧轧辊辊耗偏高问题,分析异常消耗的原因,制定相应措施,在保障热轧产线稳定生产的同时,提高轧辊在机使用性能。
关键词:爆边;辊耗;倒角;机封Abstract: Based on the comprehensive analysis of the operation data of the roll workshop,in view of the high consumption of hot rolling rolls, the causes of abnormal consumption are analyzed.At the same time corresponding measures are formulated to improve the in-service performance of the rolls while ensuring the stable production of the hot rolling production line.Key words:burst the edge;roll consumption;chamfer;machine seal轧辊是热轧连续性生产的重要工艺件。
柳钢中金900mm不锈钢热连轧精轧机组由 9 台四辊轧机组成。
在生产过程中一直存在精轧支撑辊、工作辊爆边及轴承烧结故障,导致辊耗高于同行,严重影响热轧产线设备作业率。
本文通过分析异常辊耗原因,制定改善措施,提出有效降低辊耗的方式方法,同时提高热轧带钢的表面质量。
1 辊耗偏高的主要原因轧辊在使用过程中异常失效,是导致辊耗偏高的主要原因,我们分析了2021年1月-2022年6月轧辊使用数据,共计有20支轧辊异常失效导致的提前报废;因支撑辊辊身边部剥落型裂纹、辊面起皮、辊面针眼缺陷而失效分别为11支、1支、4支;因工作辊边部剥落失效4支,另因支撑辊轴承烧结导致修磨量增加共计41次。
炼钢全流程降低钢铁料消耗的实践攻关
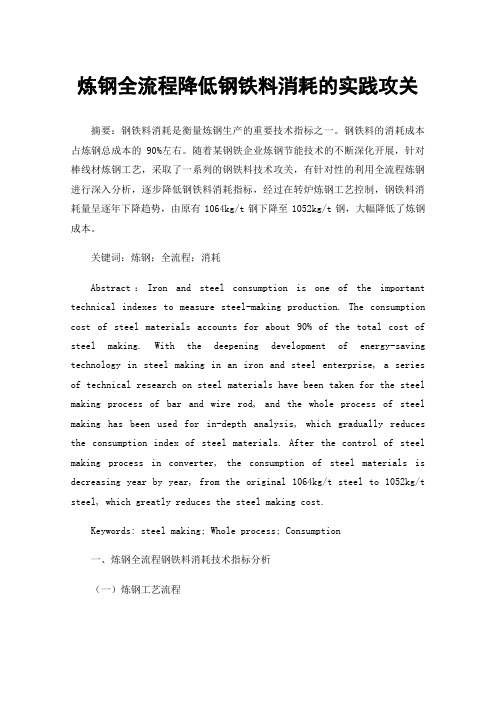
炼钢全流程降低钢铁料消耗的实践攻关摘要:钢铁料消耗是衡量炼钢生产的重要技术指标之一。
钢铁料的消耗成本占炼钢总成本的90%左右。
随着某钢铁企业炼钢节能技术的不断深化开展,针对棒线材炼钢工艺,采取了一系列的钢铁料技术攻关,有针对性的利用全流程炼钢进行深入分析,逐步降低钢铁料消耗指标,经过在转炉炼钢工艺控制,钢铁料消耗量呈逐年下降趋势,由原有1064kg/t钢下降至1052kg/t钢,大幅降低了炼钢成本。
关键词:炼钢;全流程;消耗Abstract:Iron and steel consumption is one of the important technical indexes to measure steel-making production. The consumption cost of steel materials accounts for about 90% of the total cost of steel making. With the deepening development of energy-saving technology in steel making in an iron and steel enterprise, a series of technical research on steel materials have been taken for the steel making process of bar and wire rod, and the whole process of steel making has been used for in-depth analysis, which gradually reduces the consumption index of steel materials. After the control of steel making process in converter, the consumption of steel materials is decreasing year by year, from the original 1064kg/t steel to 1052kg/t steel, which greatly reduces the steel making cost.Keywords: steel making; Whole process; Consumption一、炼钢全流程钢铁料消耗技术指标分析(一)炼钢工艺流程图1 某钢铁企业炼钢工艺流程简图(二)钢铁料消耗统计分析某钢铁企业第二钢扎厂钢铁料消耗统计口径如下:钢铁料消耗(kg/t)=(铁水+废钢)(kg)/合格钢坯产量(t)。
中型轧钢厂减少断辊的措施
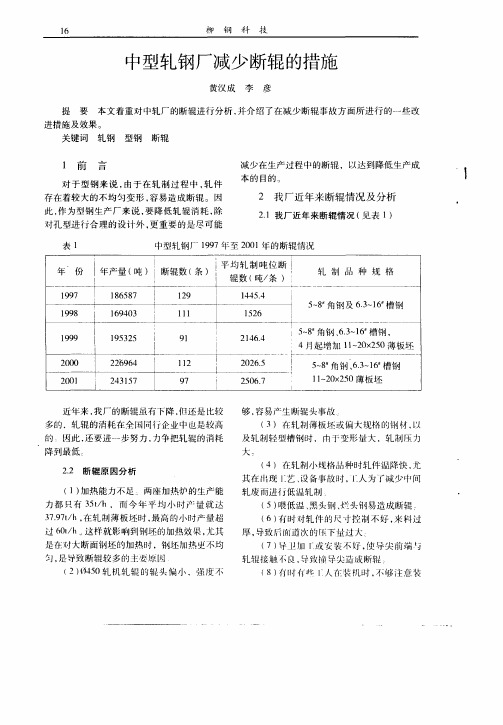
3 减 少 断 辊 的措 施
31改进 轧机 的零部 件 .
( 为提 高下 辊轧 槽 的冷却 效 果 , 们在 3) 我  ̄5  ̄ 0轧机 机座下安 装 了冷却 水管 , 5 以提 高轧槽 的冷 却效 果。
33 加大 辊头直 径 。 用材质 好 的轧 辊 _ 选
中型轧钢 厂 l9 9 7年至 2 0 年的断 辊情况 01 年 产量 ( ) 断辊数 ( ) 平 均 轧 制 吨 位 断 吨 条 辊数 ( 条 ) 吨/ 轧 制 品 种 规 格
l 97 9 l 98 9
l 65 7 8 8 l9 3 6 40
l9 2 ll l
( )针 对 某 些 品 种 的一 些 道 次 容 易造 成 1 撞 导尖的 问题 , 导尖进 行改 进 , 对 并制 定措施 严 格控 制导尖 的加工 制作 质量 。 ( ) 对胶木 瓦冷却 水槽 的形式 进行改 进 。 2 即将 原胶 木瓦 的 “ ” 形 冷却 水槽 改 为斜 交 井 字 叉 冷却水槽 , 对瓦 座及进水 孔 等进 行改进 , 并 以 避免 因冷却不 好而导 致烧坏 辊脖 或辊脖 产生裂 、
对 于 型 钢来 说 , 于 在轧 制 过 程 中 , 件 由 轧 存在着 较 大的 不 均匀 变 形 , 易造 成断 辊 。 因 容
2 我厂近年来断辊情况及分析
21我厂 近年来 断辊情 况 ( 表 1 . 见 )
此 , 为 型钢 生产 厂来 说 , 降低 轧辊 消耗 , 作 要 除
对孑 型进 行合 理 的设 计 外 , 重要 的是尽 可 能 L 更 表 l 年 份
、
1 - 0 2 0薄 板坯 2x5 1
近年来 , 厂的 断辊虽 有下 降 , 我 但还 是 比较 多的 ,轧辊 的消 耗在 全 闰同行 企业 中也是较 高 的:因此 , 还要进 一 步努 力 , 力争 把轧辊 的 消耗 降 到最低 :
降低冷轧工序能耗方案措施

降低冷轧工序能耗方案措施引言随着工业化进程的加快,冷轧工序已经成为金属加工领域中不可或缺的一环。
然而,冷轧工序在能耗方面存在一定的挑战,如何有效降低冷轧工序的能耗成为了工程师和研究人员们亟待解决的问题。
本文将基于现有的研究成果和经验,提出一些降低冷轧工序能耗的方案措施。
优化轧制参数1.轧制力控制轧制力是冷轧工序中非常重要的参数,它直接影响到轧制负荷和能耗的大小。
合理地控制轧制力,可以降低能耗的同时确保成品质量。
2.辊缝控制辊缝是冷轧工序中另一个关键参数,辊缝的大小和形状直接决定了轧制过程中的变形程度和能耗。
通过优化辊缝的设计和控制,可以降低能耗并提高产品质量。
加强设备维护和管理1.设备巡检和保养及时发现和修复设备故障是降低能耗的关键。
工厂应建立健全的设备巡检和保养机制,定期对冷轧设备进行检查和维护,确保设备的正常运行。
2.设备合理配置冷轧工序中涉及很多设备,合理配置设备能够提高生产效率,降低能耗。
工厂可以通过优化生产线布局和设备使用方案,来达到降低能耗的目的。
推行节能技术1.节能照明系统冷轧车间通常需要24小时持续运行,采用高效节能照明系统可以大幅度降低照明能耗,提高能源利用效率。
2.节能传动系统冷轧设备在运行过程中需要大量的传动设备,采用高效的节能传动系统可以减少能源损耗,降低能耗。
优化工序管理1.优化排产计划合理的排产计划可以降低设备闲置时间和能耗。
工厂可以通过制定合理的排产计划,充分利用设备,提高生产效率,降低能耗。
2.设备大数据分析通过对设备运行数据的采集和分析,可以发现设备运行中的不稳定因素和能耗波动的原因。
利用大数据技术,可以进行智能化的设备管理和能耗优化。
结论通过对冷轧工序能耗的分析和总结,本文提出了一些降低冷轧工序能耗的方案措施。
通过优化轧制参数、加强设备维护和管理、推行节能技术和优化工序管理,可以降低冷轧工序能耗,提高生产效率,实现可持续发展。
希望本文可以为冷轧工序能耗的改善提供一些启示和借鉴。
棒材生产线降本增效实践

棒材生产线降本增效实践发布时间:2022-06-15T08:29:55.565Z 来源:《科学与技术》2022年2月4期作者:常德君郜剑赵天喜[导读] 随着我国经济的不断发展,节能环保、绿色低碳、高效高质量成为钢铁企业未来的发展方向常德君郜剑赵天喜新疆天山钢铁巴州有限公司摘要:随着我国经济的不断发展,节能环保、绿色低碳、高效高质量成为钢铁企业未来的发展方向。
受整体产能过剩的影响,钢企利润降低,企业降低成本提升经营质量是一个经久不衰的话题。
相较于其它行业,钢铁行业降本增效是一项长期的工作,除在工艺装备提升,节能技术推广运用之外,企业也从生产各环节进行降本增效。
生产过程控制从高附加值经济技术指标,过程指标管控方面着手,降低企业生产成本,提升产品综合竞争实力。
关键词:降本增效;工艺优化;产量提升;成材率;能耗;1 巴州钢铁棒材线简介巴州钢铁轧钢棒材生产线,全线有18架轧机,采用平立交替轧制。
轧机布局形式“6+6+6”,即粗轧区、中轧区、精轧区均为6架次轧机组成,铸坯尺寸为160mm×160mm×12000mm。
主要生产φ12~φ36mm热轧带肋钢筋,其中φ12~φ16mm为四切分,φ18~φ22mm为双切分,其余规格采用单线轧制,配套有高压水除鳞、事故剪、活套、120米冷床、1200t冷剪、收集平台及打包机,生产具备110万吨/年的生产能力。
2 相关经济技术指标分析以2018年1月份生产以来各项指标与同行业比较,巴州钢铁目前整体偏低。
如:1~5月份平均成材率在97.386%;1~5月份电耗平均为78.4kWh/t;1~5月加工费平均在134元/吨;1~5月轧废平均50根,轧废率0.5%。
通过以上数据分析,我们从以下几个切入点进行优化:(1)加强学习岗位技能.工艺流程,进一步对料型的控制、导卫使用尺寸匹配.(2)优化料型,使料型标准化(3)速度匹配,优化料型同时速度同步(4)对导卫上线做技术要求,对导卫润滑进行改造(5)通过主控对所有剪切长度控制3 改进实践3.1标准化作业方面:由于前期生产各班组间料型没有标准化,料型偏差粗轧在3mm,中轧在1.5~2.0mm。
QC小组成果_轧辊消耗要点

3、找出不合理配辊图图纸,进行修正或重新绘制。
4、将重新绘制的图纸与加工人员一起讨论修正,最终形成新的配辊图集。
2
2、人员技术责任心不强,在轧辊加工和预装及调整方面造成了轧辊的一些不必要浪费和损失
加强检查力度。
利用技术课堂、分析会议等时机,分期分岗位对工作人员进行技术指导和岗位责任意识教育。
否
12、车床设备加工精度低
加工班部分车床使用年限较久,车床的数控水平较低,造成轧辊加工过程中的精度控制不好,孔型尺寸与设计尺寸之间存在较大误差,使得连轧关系调整存在困难。
是
小组对要因逐一进行了确认,找出了7主要要因,并采取了相应对策。
制定对策
序号
要因
对策
目标
措施
完成
时间
负责人
1
1、配辊图图纸不合理
(1)技改前旧图纸与新工艺不合
避免轧机轴承缺油状况,解决8V立轧机常出现轴承烧损问题。
1、厂里成立专门的攻关队对立轧机轴承保护进行攻关研究。
2、建立轧机预装台帐与大修记录,保证预装质量。
7
7、车床加工精度低、车刀硬度不足耐磨性差
引进新车床,制作新的样板,考虑使用新型轧辊加工刀具。
提高孔型加工尺寸精度。
1、购置新的车床,用来车加工大规格轧辊。
2008年下半年以及2010年1月,我厂连续进行两次技改,完成了生产线由半连轧向全连轧的转变,实现了轧制150方并兼容200方的轧制工艺布局,增加了轧制线的适应性。年设计产能由30万吨增加到60万吨,产能扩大一倍,随着我厂产量的不断提高,轧机架次的增加,轧辊的数量、轧辊的总消耗量也随之大幅增加,轧辊消耗成为考核轧钢生产的一个重要技术经济指标,通过与外部优秀同行的辊耗指标进行对比,发现我厂的辊耗偏高,分析原因主要有:
轧钢棒材生产工艺中的节能减排技术探讨
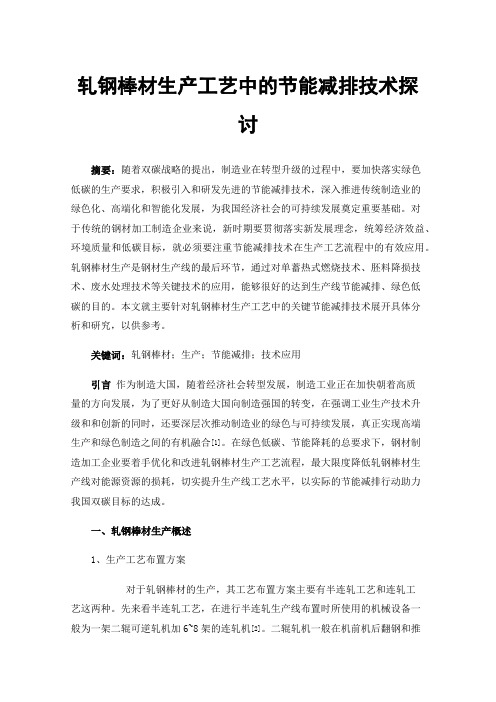
轧钢棒材生产工艺中的节能减排技术探讨摘要:随着双碳战略的提出,制造业在转型升级的过程中,要加快落实绿色低碳的生产要求,积极引入和研发先进的节能减排技术,深入推进传统制造业的绿色化、高端化和智能化发展,为我国经济社会的可持续发展奠定重要基础。
对于传统的钢材加工制造企业来说,新时期要贯彻落实新发展理念,统筹经济效益、环境质量和低碳目标,就必须要注重节能减排技术在生产工艺流程中的有效应用。
轧钢棒材生产是钢材生产线的最后环节,通过对单蓄热式燃烧技术、胚料降损技术、废水处理技术等关键技术的应用,能够很好的达到生产线节能减排、绿色低碳的目的。
本文就主要针对轧钢棒材生产工艺中的关键节能减排技术展开具体分析和研究,以供参考。
关键词:轧钢棒材;生产;节能减排;技术应用引言作为制造大国,随着经济社会转型发展,制造工业正在加快朝着高质量的方向发展,为了更好从制造大国向制造强国的转变,在强调工业生产技术升级和和创新的同时,还要深层次推动制造业的绿色与可持续发展,真正实现高端生产和绿色制造之间的有机融合[1]。
在绿色低碳、节能降耗的总要求下,钢材制造加工企业要着手优化和改进轧钢棒材生产工艺流程,最大限度降低轧钢棒材生产线对能源资源的损耗,切实提升生产线工艺水平,以实际的节能减排行动助力我国双碳目标的达成。
一、轧钢棒材生产概述1、生产工艺布置方案对于轧钢棒材的生产,其工艺布置方案主要有半连轧工艺和连轧工艺这两种。
先来看半连轧工艺,在进行半连轧生产线布置时所使用的机械设备一般为一架二辊可逆轧机加6~8架的连轧机[2]。
二辊轧机一般在机前机后翻钢和推床,连轧机一般为平立布置。
再来看连轧工艺,连轧工艺的生产线布置方式一般为4~6架轧机组成的粗轧机组以及第一中轧机组、第二中轧机组、精轧机组、减定径机组联合布置。
2、生产中存在的能源资源损耗问题在轧钢棒材生产环节,存在一定的能源资源损耗问题,具体表现在以下三个方面:一是在进行坯料轧制的过程中,设备生产设备大多处于连续运转的状态,加热炉经常会进行超负荷作业,一定程度上会缩短加热炉的使用寿命,同时由于超负荷运转在一定程度上会增加对胚料的消耗量,并降低生产效率,增加生产能耗。
- 1、下载文档前请自行甄别文档内容的完整性,平台不提供额外的编辑、内容补充、找答案等附加服务。
- 2、"仅部分预览"的文档,不可在线预览部分如存在完整性等问题,可反馈申请退款(可完整预览的文档不适用该条件!)。
- 3、如文档侵犯您的权益,请联系客服反馈,我们会尽快为您处理(人工客服工作时间:9:00-18:30)。
棒线材厂降低轧辊消耗实践
【摘要】针对棒线材厂降低生产成本工作,通过采用新材质轧辊、进行工艺优化和一系列技术改造等措施来降低轧辊消耗为棒线材厂降成本工作做出贡献。
【关键词】轧辊消耗技术改造工艺优化
1.前言
川威集团威远钢铁有限公司棒线材厂有一条高棒和一条高线两条生产线,其中全连轧高棒生产线以φ550×3、φ450×3、φ380×6、φ320×6(其中三架为平立可转换)轧机组成,轧后设有水冷器冷却系统。
设计年产能力为60万吨,主要产品为φ12mm~φ40mm的热轧带肋钢筋和φ14mm~φ40mm的热轧直条圆钢,产品品种为普通碳素结构钢(Q195~Q275)及低合金钢(20MnSi)等;高线生产线以φ580×4、φ475×5、φ275×4、φ210×10轧机组成,轧后设有水冷器冷却系统。
设计年产能力为30万吨,主要产品为φ5.5mm~φ14mm的热轧带肋钢筋盘条和热轧圆钢,产品品种为普通碳素结构钢(Q195)、低合金钢(20MnSi)及焊条钢和焊丝钢等。
棒线材厂为追求成本最小化,效益最大化,一直致力于本厂的降成本工作,而棒线材厂高棒车间的轧辊消耗和高线车间的辊环消耗作为棒线材厂生产成本中的大头则成为了棒线材厂降成本工作中的重点,通过一系列的技术攻关和工艺优化改进,极大的降低了棒线材厂的辊耗,达到了国内领先水平,为棒线材厂降成本工作做出了巨大贡献。
2.解决措施
2.1提高轧辊强度
目前高棒车间粗、中轧轧辊直径使用较小,特别是采用无孔轧制新工艺后,轧制量较未采用无孔轧制工艺以前增大50%,同时考虑到今后使用160mm*160mm钢坯后轧制负荷增大,现有轧辊强度不足以满足生产需要,容易造成断辊从而导致生产成本增高。
因此,在满足换辊装配要求的情况下,对高棒粗、中轧轧机进行改造,将轧辊最大使用直径在现有基础上扩大30-40mm以提高轧辊强度,在其使用周期内提高总过钢量,降低轧辊消耗,降低生产成本,同时,将减少断辊机率。
轧机改造后,提高了现有轧辊的最大使用直径:φ550mm轧机轧辊由现用最大φ550mm提高到φ580mm, φ450mm轧机轧辊由现用最大φ455mm提高到φ480mm, φ380mm轧机轧辊由现用最大φ405mm提高到φ430mm。
高棒粗、中轧轧辊消耗也降低了10%,每年降低辊耗12万元。
2.2 提高轧辊综合利用率
棒线材厂有高棒和高线两条生产线,使用的轧辊规格多,有φ600、φ550、φ490、φ455、φ380、φ330、φ350。
因此如何做好轧辊的综合利用从而大幅度降低轧辊消耗,降低生产成本是一项重要工作,棒线材厂通过以下措施提高轧辊综合利用率:
(1) 改进高线车间φ600和φ490轧辊传统订货方式,由原来的平辊改为带刻孔订货,提高轧槽的耐磨性即提高单槽轧制量从而降低辊耗。
(2) 改进Ф550、455轧辊材质。
由原来的中镍铬钼常化铸铁轧辊改为中镍铬钼离心铸铁轧辊,提高轧辊的强度和耐磨性。
(3) 高线车间1H、2H机架所用轧辊必须先由3H、4H机架使用一次后改成;5H、7H
机架所用轧辊必须先由9V机架使用一次后改成;6H机架所用轧辊必须先由8H机架使用一次后改成;10H、11V机架所用轧辊必须先由12H、13V机架使用一次后改成的轧辊车削准备工作。
规范高棒车间Ф550、Ф455、Ф380轧辊使用顺序,后机架轧辊使用后再用于前面机架使用的轧辊车削准备工作。
通过提高对棒线材厂轧辊的综合利用率,极大的降低了轧辊消耗,每年可降低轧辊消耗100万元以上。
2.3 采用新材质轧辊
全国高速棒材生产线精轧机轧辊正在向合金化方向发展,特别是切分轧制的切分K3和预切分K4道次通常采用高速钢类的组合轧辊。
高棒车间轧制Ф12~14×3mm规格的切分K3、预切分K4和成品道次K1现用的轧辊为贝氏体轧辊,切分楔损坏严重,工艺事故多,单槽过钢量低,换槽换辊频繁,致使严重影响生产作业率、成材率的提高,也增加了轧辊消耗。
通过到国内同行业的学习、交流,在轧制Ф12~14×3mm 规格三切分时,切分K3、预切分K4和成品道次K1引进使用高硼高速钢轧辊,使用后切分K3预切分K4和成品道次K1的单槽轧制量分别由现在的300吨/槽、600吨/槽、100吨/槽提高到2000吨/槽、2400吨/槽、200吨/槽,通过引进使用新材质的高硼高速钢轧辊,每年降低辊耗80万元以上,而且也提高了经济技术指标和稳定的负偏差控制。
497
2.4轧机横梁改造
高线车间粗、中轧的轧辊冷却效果及其不好,水量和水压严重不足。
通过分析是由于高线粗、中轧的轧机横梁设计不合理,为了満足能够冷却轧辊的全部轧槽,原横梁上设计了两组一起供水的冷却水管。
造成没有使用的轧槽也在用水,这样就有50%左右冷却水被浪费。
为了充分利用水资源,提高轧辊的使用寿命和提高单槽轧制量减少轧辊消耗,对高线车间现用的轧机横梁进行改造,对冷却水管管路进行优化设计,轧机横梁改造完后,粗、中轧的轧辊的单槽轧制量提高了20%,同时减轻了热裂纹的产生减少了重车量,相应轧辊消耗降低了20%,每年降低辊耗16万元。
2.5 螺纹辊环装配改造
碳化钨硬质合金螺纹辊环是高速线材生产线生产螺纹盘条的关鍵和主要工艺消耗备件,碳化钨硬质合金螺纹辊环是一种硬度高,耐磨性、韧性、抗热裂纹性能都较好的一种工具材料,但是价格昂贵,占生产成本的比例很大。
我厂高线车间使用的Ф210×72的螺纹辊环采用现有装配方式时,一个辊环上Ф8~Ф12mm规格螺纹辊环只能开两个轧槽,而我厂年产螺纹钢盘条产量很大,2009年全年产材57万吨其中生产螺纹盘条34.5万吨,占全年产的60.63%。
通过对现使用螺纹辊环的强度进行校核后,对现有螺纹辊环装配方式进行改进,Ф8mm螺纹辊环开4个轧槽,Ф10~Ф12mm开3个轧槽,极大的提高了螺纹辊环的有效利用率,大幅度降低螺纹辊环的消耗,可降低33.3%以上,每年降低螺纹辊环消耗70万元以上。
2.6 孔型工艺优化
高线车间目前的主要品种规格为Ф6.5mm、Ф8.0 mm、Ф10.0 mm、Ф12.0 mm盘条,原孔型设计Ф6.5 mm、Ф8.0 mm和Ф10.0 mm三个规格与Ф12.0mm规格盘条中轧13V和预精轧17#轧机出口料型尺寸不一致,每次换轧Ф12.0mm盘条时,中轧14#-17#轧机辊环须全部更换,工作量大,换辊时间长,约2-3小时左右。
且换下来的辊环,锥套需要清洗,工人劳动强度大。
有时改轧其它规格时,预精轧有的辊环单槽过钢量还未达到规定使用要求就换下来(换下的同样得修复后使用),造成预精轧机辊环消耗高。
针对此种情况进行工艺优化改进,完成高线轧制Ф6.5mm、Ф8.0mm和Ф10.0mm三个规格盘条与轧制Ф12.mm规格盘条时预精轧机孔型的共用设计,不但节约了换辊时间,提高了生产作业率,也降低了辊耗,每年降低辊耗10万元以上。
2.7 其它措施
高线车间生产线预精轧机组和精轧机组使用的辊环分别为高速钢辊环和碳化钨辊环,价格昂贵,每年辊耗在350万元左右, 由于辊环碎裂、辊环掉块、辊环内孔磨损等原因造成的辊环非正常消耗是主要消耗因素之一。
辊环非正常消耗原因很多,其中主要是预精轧和精轧机发生工艺堆钢事故、单槽轧制量过高、辊环冷却不良、辊环加压不当、导卫安装不当、辊箱平衡缸卸压、辊轴下沉、水冷线堆钢等。
为减少由于以上原因产生的辊环非正常消耗,高线车间采取以下措施进行控制:
(1) 修订辊环使用的技术规程和加工修复标准。
(2) 加强对操作人员进行技术培训。
(3) 提高各工序的工作质量:辊环组要将锥套、辊环清洗干净,认真检查锥套质量(锥套锈蚀情况、变形情况),严格按工艺要求进行辊环的配辊,严格按加工修复标准进行加工;生产大班员工在更换辊环时要严格按技术规程操作,注意辊环、辊轴和锥套的卫生,严格按规定加压值匀速加压安装辊环,各道次严格按规定的轧制量进行轧制。
(4) 加强对辊环使用的跟踪,针对不同情况下线的辊环采用不同的加工方式。
(5) 改进废料箱,将废料箱内空改大,增设事故检测线。
(6) 改进预精轧机组和精轧机组辊环冷却水管,增设其金属软管保护装置。
通过对员工的技术培训和严格的工艺监督管理以及有效、合理的措施,高线车间辊环非正常消耗得到了有效控制,由3.57片/万吨减少到平均2片/万吨,年降低辊耗30万元以上。
3.结语
棒线材厂根据本厂高棒车间和高线车间的工艺条件和设备实际状况,从降低轧辊消耗上分析具体原因,采取提高轧辊强度和综合利用率,配合采用新材质轧辊以及通过改造轧机横梁和螺纹辊环装配、优化孔型等措施,极大的降低了棒线材厂的辊耗,高棒车间辊耗为2.1元/吨钢,高线车间辊耗为4.1元/吨钢,在全国同行业处于领先水平,为棒线材厂降成本工作做出了巨大贡献。
参考文献
[1] 高速钢复合轧辊的研制及生产,钢铁,1998.3。
[2] 高线精轧机WC辊环的使用和维护,轧钢,1998.4。
498。