CP45 12261.7. Board Specifications(-)
847PET手操器中文使用说明

法律事项 Enraf B.V(. 荷兰)公司拥有本手册中所有信息的版权。对于以下原因造成的人员伤害或财产损失,Enraf B.V. 公司概不负责:
3.7 EN-prefix...............................................................................................................................................10 3.8 键盘超时 ...............................................................................................................................................10
3 设置模式 ..........................................................................................................................................................7 3.1 综述 .........................................................................................................................................................7 3.2 显示对比度 .............................................................................................................................................8 3.3 模式选择 .................................................................................................................................................8 3.4 IR 波特率选择 ........................................................................................................................................8 3.5 EN 波特率选择.......................................................................................................................................9 3.6 RS-232 波特率选择 ................................................................................................................................9
CP45 12267.13. Nozzle(-)

2.13. Nozzle2.13.1. Nozzle typesNozzles are largely divided into general nozzles and special nozzles (nozzles for non-standard components). General nozzlesApplicable to all generally used components. These components include chips, SOJ, SOP, PLCC, QFP, etc. Special nozzlesNozzles for non-standard componentsThese are for non-standard components of various shapes such as connectors, sockets, etc. Components with odd shapes can be manufactured and applied. Among nozzles for non-standard components, the diffuser type nozzles (CTP200, CTP400) are for improving visibility of the components requiring for vision treatment.CautionOperating the shutter while a finger is inserted in the ANC could result in severe injury. Do not insert a finger into the ANC Hole.2.13.2. GeneralnozzlesNozzles should be properly selected according to the type and size of the components.The nozzles generally used in the CP-45FV NEO model are identical. Black nozzles areoccasionally used for some components in the flying vision unit and the upward visionunit.The nozzle should be selected correctly since it may cause improper adsorption, orimproper placement problems. The nozzles generally used are shown in “Table 2-8“. Foraccurate pick & place, a proper nozzle should be selected in reference to the minimumsuction area of each component.Table 2-8. General NozzlesTable 2-9. Examples of Applying General Nozzles to ComponentsNozzle nameMinimumcomponentwidthMajor component typesCN030 0.3 ~ 1.5 0603,1005 onlyCN040 0.5 ~ 1.25 1005, 1608, 2012,3216, SOT(Molded part 0.8 X 1.6)CN065 0.8 ~ 2.5 1608, 2012,3216, MELF(Molded part 1.2 X 2.0), SOT23CN140 2.5 ~ 4.0 Aluminum electrolytic capacitor(small), Tantalum capacitor, TrimmerCN220 4.0~7.0 Aluminum electrolytic capacitor(medium), SOP(Narrow), SOJ, ConnectorCN400N 7.0 ~ 10.0 Aluminum electrolytic capacitor(large), SOP(Wide), TSOP, QFP, PLCC, SOJ, ConnectorCN750 10.0 ~ QFP(medium), PLCC(medium)CN110 20.0 ~ QFP(large), PLCC(large)CNT20 CalibrationTool(Nozzle)forFlyingVision2.13.3. Special nozzlesTable 2-10. Special NozzlesCautionThis table simply means that the conventional nozzle of 10-hole ANC has the same inner and outer diameters as those of the nozzle of 20-hole ANC. It does not mean that they can be usedinterchangeably. Only nozzles listed in the above table should be used for each ANC type.CautionThe machine might operate irregularly if standard regular nozzles are not used.1. Failure of nozzle change2. Dislocation of nozzle during operation3. Failure of component pick up Be sure to use standard regular nozzles.Table 2-11. Examples of Applying Special Nozzles to Components Nozzle name Minimum component widthMajor component typesCTP200 2.5 ~ Connectors for which vacuum adsorption is possible CTP4004.5 ~Connectors for which vacuum adsorption is possibleCNT20 - Tool forCalibration2.14. Feeder Station PartComponents can be supplied during operation by placing the component supply device on the feeder base. The part can be used by installing ANC, tape feeder, stick feeder, and stack stick feeder, and on the rear side single-tray feeder and multi-tray feeder can be installed.The ANC, air pressure supply coupling for the stack stick feeder, and power connector are situated on the connector panel at the front side.Figure 2-19. Feeder Station PartSpeed control of a multi-cylinder is possible since a speed control valve is protruded. The multi-cylinder (feeder driving cylinder) is located at the lower side of the feeder base, and is a multiple-drive cylinder driving the lever of a feeder by the piston load.Connector panelFeeder baseSpeed control valve。
赵立鑫一体化多媒体壁板说明书

Page 1 of 2APPLICATIONLeviton patented Single-Gang QuickPlate Tempo Wallplates accept QuickPort ™ snap-in modules to support multimedia station applications. They are ideal for use where portdesignation windows in a one-piece, single-gang, economical flush-mount housing is desired. Wallplates are available with two or four ports.SPECIFICATIONThe wallplate housing shall be a one-piece, single-gang flush-mount style. It shall be available in 2- or 4-port configurations. It shall accept all Leviton QuickPort connectors. Wallplate shall feature clear port ID windows. Wallplate shall connect to the wallboard using Leviton patented design and arm members. It shall be made of high-impact, fire-retardant plastic rated UL 94V-0, and be cULus Listed and compliant with ANSI/TIA-568.0-D specifications.Single-Gang QuickPlate ™ Tempo Wallplates with ID Windows42090-xWSFEATURES•Patented rear wings tighten to wallboard, eliminating the need for a box or mounting brackets and supporting fast,one-step installation with a flush mount•Wings accommodate 5/8 inch and under wallboard thickness•Center lines included as a guide for easy alignment •ID windows act as marking template for cutting hole in wallboard•Includes ID designation window for each wallplate •Patented Design (US Patent 7468487)•Compatible with all individual QuickPort connectors•Individual port configurability allows specification flexibilityDESIGN CONSIDERATIONS•Matches Leviton standard wallplate dimension•Use blanks (41084-0BW) in unused ports for future expansion•To identify ports, use different colored connectors for each application or Leviton pre-printed Port Designation Labels (41080-LEB)STANDARDS & REGULATIONS•cULus Listed (UL 1863 & CAN/CSA-C22.2 No. 182.4)•ANSI/TIA-568.0-DMECHANICAL SPECIFICATIONSDimensions: See page twoMaterials:High-impact, fire-retardant plastic rated UL 94V-0Capacity: Available in 2 or 4 ports Mounting:ScrewsCOUNTRY OF ORIGINUSAWARRANTY INFORMATIONFor Leviton product warranties, go to /warranty42090-2WS42090-4WSRear ViewLeviton is dedicated to designing, developing and manufacturing sustainable high-performance structured cabling and speciality cabling solutions. Network Solutions products are available worldwide in over 100 countries. Visit us online to learn more.NETWORK SOLUTIONS GLOBAL HEADQUARTERS Bothell, WA, USA | /ns(800)824 3005 / +1 (425) 486 2222 | ******************NETWORK SOLUTIONS EUROPEAN HEADQUARTERS Glenrothes, UK | /ns/emea+44 (0) 1592 772124 | *****************************。
奥里安特电机产品操作手册说明书

HM-9264-2AC Standard Motors Conduit Box TypeInduction MotorThank you for purchasing an Oriental Motor product.This Operating Manual describes product handling procedures and safety precautions.• Please read it thoroughly to ensure safe operation. • Always keep the manual where it is readily available.Before useOnly qualified personnel should work with the product.Use the product correctly after thoroughly reading the section “Safety precautions”.Should you require the inspection or repair of internal parts, contact the Oriental Motor office where you purchased the product. The product described in this manual has been designed andmanufactured for use as an internal component for general industrial equipment, and must not be used for any other purpose. Oriental Motor Co., Ltd. is not responsible for any damage caused through failure to observe this warning.Standard and CE MarkingMotors are recognized by UL. Recognized name are motor model name. Voluntary display of the CE mark conforming to the Low Voltage Directives. StandardsUL 1004, UL 2111, CSA C22.2 No.100, CSA C22.2 No.77 Standards File No. UL File No.E64197 Applications for standardEN 60034-1, EN 60034-5, EN 60664-1A Running Heating Test and a Locked-Rotor Test has beenconducted with a aluminum radiation plate of size indicated below. For the motor with a gearhead, tests has been conducted with a gearhead instead of the radiation plate.First number in motor nameSize [mm (in.)] Thickness [mm (in.)]Material4 135 × 135 (5.31 × 5.31) 5 (40 W) 165 × 165 (6.50 × 6.50) 5 (60 W, 90 W)200 × 200 (7.87 × 7.87)5 (0.20)AluminiumInstallation conditionsOvervoltage category II, Pollution degree 3 (except for the motor mounting surfase and conduit opening), Class I equipment (For EN/IEC standards)When the machinery to which the motor is mounted requiresovervoltage category III specifications, connect to power supply via an isolation transformer.Hazardous substancesRoHS (Directive 2002/95/EC 27Jan.2003) compliant∗ 5IK60GU-FCH , 5IK60GU-ECH , 5IK60GU-SH , 5IK90GU-FCH , 5IK90GU-ECH and 5IK90GU-SH do not comply with the hazardous substances.The precautions described below are intended to prevent danger or injury to the user and other personnel through safe, correct use of the product. Use the product only after carefully reading and fully understanding these instructions.WarningHandling the product without observing theinstructions that accompany a “Warning” symbol may result in serious injury or death.CautionHandling the product without observing theinstructions that accompany a “Caution” symbol may result in injury or property damage.NoteThe items under this heading contain importanthandling instructions that the user should observe to ensure safe use of the product.Warning• Do not use the product in explosive or corrosive environments, in the presence of flammable gases, locations subjected to splashing water, or near combustibles. Doing so may result in fire, electric shock or injury.• Assign qualified personnel the task of installing, wiring,operating/controlling, inspecting and troubleshooting the product. Failure to do so may result in fire, electric shock or injury. • Do not transport, install the product, perform connections or inspections when the power is on. Always turn the power offbefore carrying out these operations. Failure to do so may result in electric shock.• Turn off the power in the event the overheat protection device (thermal protector) is triggered. Failure to do so may result in injury or damage to equipment, since the motor will start abruptly when the overheat protection device (thermal protector) is automatically reset.• To prevent the risk of electric shock, use the motor for class I equipment only.Motore zur Verwendung in Geräten der Schutzklasse I.• Install the motor in an enclosure in order to prevent electric shock or injury.• Install the motor so as to avoid contact with hands, or ground it to prevent the risk of electric shock.Die Gehäuse der Motore sind mit einer Schraube undZahnscheibe sicher mit dem geerdeten Gehäuse des Gerätes zu verbinden.• Keep the input power voltage within the specification to avoid fire and electric shock.• Connect the cables securely according to the wiring diagram in order to prevent fire and electric shock.• Do not forcibly bend, pull or pinch the lead wires. Doing so may result in fire and electric shock.• Turn off the power in the event of a power failure, or the motor will suddenly start when the power is restored and may cause injury or damage to equipment.• Do not touch the connection terminal of the capacitor immediately after the power is turned off (for a period of 30 seconds). Theresidual voltage may cause electric shock.• Do not disassemble or modify the motor. This may cause electric shock or injury.Caution• Do not use the motor beyond its specifications, or electric shock, injury or damage to equipment may result.• Do not touch the motor during operation or immediately after stopping. The surface is hot and may cause a burn.• Do not hold the motor output shaft or motor lead wires. This may cause injury.• Keep the area around the motor free of combustible materials in order to prevent fire or a burn.• To prevent the risk of damage to equipment, leave nothing around the motor that would obstruct ventilation.• To prevent bodily injury, do not touch the rotating parts (output shaft, cooling fan) of the motor during operation.• When an abnormality is noted, turn off the power immediately, or fire, electric shock or injury may occur.• The motor’s surface temperature may exceed70 °C, even under normal operating conditions. Ifa motor is accessible during operation, post thewarning label shown in the figure in aconspicuous position to prevent the risk of skinburn(s).Warning label• To dispose of the motor, disassemble it into parts and components as much as possible and dispose of individual parts/components as industrial waste.Checking the productVerify that the items listed below are included. Report any missing or damaged items to the branch or sales office from which you purchased the product.• Motor...............................................1 unit• OPERATING MANUAL................1 copyChecking the model nameCheck the model number against the number indicated on the product.Model Model Model4IK25GN-FCH 4IK25GN-ECH 4IK25GN-SH4IK25AA-FCH 4IK25AA-ECH 4IK25AA-SH5IK40GN-FCH 5IK40GN-ECH 5IK40GN-SH5IK40AA-FCH 5IK40AA-ECH 5IK40AA-SH5IK60GE-FCH 5IK60GE-ECH 5IK60GE-SH5IK60A-FCH 5IK60A-ECH 5IK60A-SH5IK60GU-FCH 5IK60GU-ECH 5IK60GU-SH5IK90GE-FCH 5IK90GE-ECH 5IK90GE-SH5IK90A-FCH 5IK90A-ECH 5IK90A-SH5IK90GU-FCH 5IK90GU-ECH 5IK90GU-SH Location for installationThe motor is designed and manufactured for installation in equipment.Install it in a well-ventilated location that provides easy access for inspection. The location must also satisfy the following conditions: • Inside an enclosure that is installed indoors (provide vent holes) • Operating ambient temperature−10 to +40 °C (+14 to +104 °F) (non-freezing)−10 to +50 °C (+14 to +122 °F) for three-phase 200 V• Operating ambient humidity 85%, maximum (non-condensing) • Area that is free from an explosive atmosphere or toxic gas (such as sulfuric gas) or liquid• Area not exposed to direct sun• Area free of excessive amount dust, iron particles or the like• Area not subject to splashing water (storms, water droplets), oil (oil droplets) or other liquids• Area free of excessive salt• Area not subject to continuous vibration or excessive shocks• Area free of excessive electromagnetic noise (from welders,power machinery, etc.)• Area free of radioactive materials, magnetic fields or vacuum• 1000 m (3300 ft.) or less above sea levelHow to install the motor• Round shaft typeDrill holes on the mounting plate and fix the motor on the plateusing screws, nuts, and washers (not supplied). Be careful there is nogap between the motor installation surface and the bracket.First number inmotor modelScrew size Tightening torque [N·m (lb-in)]4 M5 2.5(22)5 M6 3.0(26)Do not insert the motor into the mounting hole at anangle or force it in, as this may scratch the flange pilotsection and damage the motor.• Pinion shaft typeDrill holes on the mounting plate and fix the motor and gearhead on the plate using screws supplied with the gearhead. Be careful there is no gap between the motor flange and the gearhead.For details of installation, see the operating manual provided with the gearhead, which is sold separately.Use the gearhead with pinion shaft which is identicalwith one of motor.• Motor with cooling fanWhen installing a motor with cooling fan onto a device, leave10 mm (0.39 in.) or more behind the fan cover or open a ventilation hole so that the cooling inlet on the back of the motor cover is not blocked.Insulate all the wire connections, such as the connection between the motor and the capacitor connection.When the single-phase motor is run in only one direction, unused lead wires should be insulated.Ground the motor using a Protective Earth lead wire (green/yellow). The direction of motor rotation is as viewed from the side of the motor’s output shaft. The motor rotates in a clockwise (CW) and counterclockwise (CCW) direction.• Insulation class of this motor is B. Make sure that themotor case temperature does not exceed 90 °C(194 °F) during operation of the motor. Operationexceeding case temperature 90 °C (194 °F) maysignificantly deteriorate the coils and ball bearings ofthe motor and shorten the motor’s life span. Motorcase temperature can be measured by fixing athermometer on the motor surface. It can also bemeasured using thermo tape or a thermocouple.• To change rotation direction of the single-phasemotor, wait until the motor completely stops.Otherwise its direction may not change or may takemuch time to change.Rotating direction of the gearhead output shaftThe rotating direction of the gearhead output shaft may be opposite that of the motor shaft, depending on the gear ratio. For the rotating direction of the output shaft of a specific gearhead used, refer to the operating manual for the gearhead. Connection method to a terminal box• Open the terminal box and connect wires.• Use applicable cable ground and conduit for conduit opening. • After connecting, close the terminal box with the terminal cover. • Terminal cover screws tightening torqueSingle-phase 25 W, 40 W/Three-phase: 0.3 N·m (2.6 lb-in) Single-phase 60 W, 90 W: 1 N·m (8.8 lb-in)• Single-phase 25 W, 40 W/Three-phase••Connect the motor according to the figure.The connection method will vary, depending on the directionClockwiseLNCounterclockwiseLN∗ NC: Not connect. Three-phase motorsConnect the motor according to the figure.When connected according to the connection diagram, the motor will operate in the clockwise direction (CW) as viewed from the motor’s output shaft. To change the direction of rotation, change any two connections between U, V and W.ClockwiseL2 (S)L1 (R)L3 (T)Motors have a continuous rating.This motor is equipped with the feature listed below to prevent the motor from burning out as a result of abnormal heating which maybe caused by misapplication.• Thermal protection“TP” is stamped on the motor nameplate. The motor has an “auto reset” type thermal protector built into its motor coil. When themotor reaches a predetermined temperature, the internal thermal protector is activated and the motor is stopped.Always turn the power off before performing inspections.Thermal protector activation rangePower is turned off at 130±5 °C (266±9 °F)Power is turned back on at 82±15 °C (180±27 °F)When the motor cannot be operated correctly, refer to the contents provided in this section and take appropriate action. If the problem persists, contact your nearest office.Phenomena CheckitemsMotor does not rotate or rotates slowly. • Check the power supply voltage.• Connect the power supply and the motor correctly.• If terminal blocks or crimp terminals are used, check them for poor connection. • Keep the load at or below the allowable value.Motor sometimes rotates and stops. • Connect the power supply and the motor correctly.• If terminal blocks or crimp terminals are used, check them for poor connection.The motor rotates in the direction opposite to the specified direction. • Connect correctly by referring to “Wiring diagram.”• The rotating direction of the motor output shaft may be different from that of the gearhead output shaft depending on the gear ratio of the gearhead. See the operating manual for the gearhead.• The rotating direction is indicated as viewed from the motor output shaft. Check the reference direction.Motor temperature abnormally high [Motor case temperature exceeds 90 °C (194 °F)] • Check the power supply voltage. • Review the ventilation condition.Noisy operation • Assemble the motor and gearheadcorrectly by referring to the operatingmanual for the gearhead.• Assemble a gearhead of the same piniontype as the motor.• Unauthorized reproduction or copying of all or part of thismanual is prohibited.• Oriental Motor shall not be liable whatsoever for any problems relating to industrial property rights arising from use of anyinformation, circuit, equipment or device provided orreferenced in this manual.• Characteristics, specifications and dimensions are subject tochange without notice.• While we make every effort to offer accurate information in the manual, we welcome your input. Should you find uncleardescriptions, errors or omissions, please contact the nearestoffice.• is a registered trademark or trademark ofOriental Motor Co., Ltd., in Japan and other countries.© Copyright ORIENTAL MOTOR CO., LTD. 2008Printed on Recycled Paper • Please contact your nearest Oriental Motor office for further information.Headquarters Tokyo, JapanTel:(03)3835-0684 Fax:(03)3835-1890Tel:01 47 86 97 50 Fax:01 47 82 45 16Tel:(02)8228-0707 Fax:(02)8228-0708 Technical Support Tel:(800)468-39828:30 A.M. to 5:00 P.M., P.S.T. (M-F)7:30 A.M. to 5:00 P.M., C.S.T. (M-F)E-mail:*****************************Headquarters and Düsseldorf Office Tel:0211-52067-00 Fax:0211-52067-099 Munich Office Tel:089-3181225-00 Fax:089-3181225-25 Hamburg Office Tel:040-76910443 Fax:040-76910445Tel:01256-347090 Fax:01256-347099Tel:02-93906346 Fax:02-93906348Tel:(6745)7344 Fax:(6745)9405KOREATel:(032)822-2042~3 Fax:(032)819-8745Tel:(03)22875778 Fax:(03)22875528Tel:66-2-254-6113 Fax:66-2-254-6114。
淼田电子有限公司LQG15HH系列芯片电感说明书
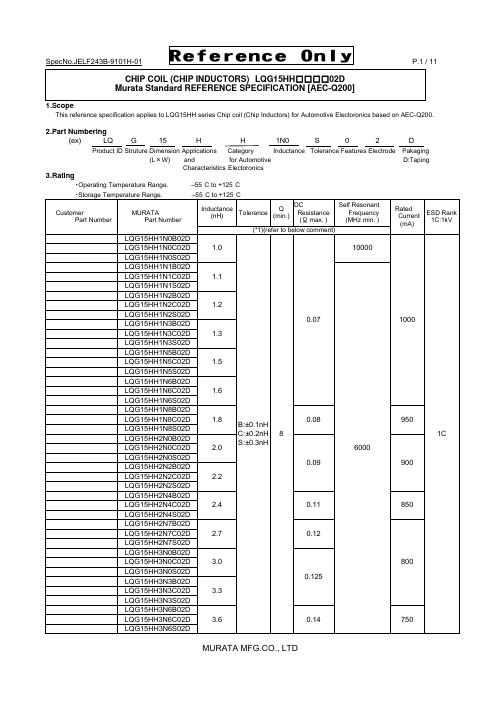
SpecNo.JELF243B-9101H-01 P.1 / 11Reference OnlyCHIP COIL (CHIP INDUCTORS) LQG15HH □□□□02DMurata Standard REFERENCE SPECIFICATION [AEC-Q200]1.ScopeThis reference specification applies to LQG15HH series Chip coil (Chip Inductors) for Automotive Electoronics based on AEC-Q200.2.Part Numbering(ex) LQ G 15 H H 1N0 S 0 2 DProduct ID Struture Dimension Applications Category Inductance Tolerance Features Electrode Pakaging(L ×W) and for Automotive D:TapingCharacteristics Electoronics3.Rating・Operating Temperature Range. –55°C to +125°C ・Storage Temperature Range. –55°C to +125°CCustomer Part Number MURATAPart NumberInductance (nH) ToleranceQ(min.)DC Resistance (Ω max. ) Self ResonantFrequency (MHz min. )Rated Current (mA)ESD Rank 1C:1kV(*1)(refer to below comment)LQG15HH1N0B02D1.0B:±0.1nHC:±0.2nH S:±0.3nH8 0.07 10000 10001CLQG15HH1N0C02D LQG15HH1N0S02D LQG15HH1N1B02D1.1 6000 LQG15HH1N1C02DLQG15HH1N1S02D LQG15HH1N2B02D 1.2 LQG15HH1N2C02D LQG15HH1N2S02DLQG15HH1N3B02D1.3 LQG15HH1N3C02DLQG15HH1N3S02D LQG15HH1N5B02D1.5 LQG15HH1N5C02DLQG15HH1N5S02D LQG15HH1N6B02D 1.6 LQG15HH1N6C02D LQG15HH1N6S02D LQG15HH1N8B02D 1.8 0.08 950LQG15HH1N8C02D LQG15HH1N8S02DLQG15HH2N0B02D2.0 0.09 900LQG15HH2N0C02DLQG15HH2N0S02DLQG15HH2N2B02D 2.2 LQG15HH2N2C02D LQG15HH2N2S02D LQG15HH2N4B02D2.4 0.11 850 LQG15HH2N4C02DLQG15HH2N4S02D LQG15HH2N7B02D 2.7 0.12 800 LQG15HH2N7C02D LQG15HH2N7S02D LQG15HH3N0B02D 3.0 0.125LQG15HH3N0C02D LQG15HH3N0S02DLQG15HH3N3B02D3.3 LQG15HH3N3C02DLQG15HH3N3S02D LQG15HH3N6B02D3.6 0.14 750 LQG15HH3N6C02DLQG15HH3N6S02DCustomer Part Number MURATAPart NumberInductance (nH) ToleranceQ(min.)DC Resistance (Ω max. ) Self ResonantFrequency(MHz min. )RatedCurrent(mA)ESD Rank 1C:1kV(*1)(refer to below comment)LQG15HH3N9B02D3.9 B:±0.1nHC:±0.2nHS:±0.3nH8 0.14 6000 7501CLQG15HH3N9C02DLQG15HH3N9S02DLQG15HH4N3B02D 4.3 LQG15HH4N3C02D LQG15HH4N3S02D LQG15HH4N7B02D 4.7 0.16 700LQG15HH4N7C02D LQG15HH4N7S02DLQG15HH5N1B02D5.1 0.18 5300 650LQG15HH5N1C02DLQG15HH5N1S02DLQG15HH5N6B02D5.6 4500 LQG15HH5N6C02DLQG15HH5N6S02D LQG15HH6N2B02D6.2 0.20 600LQG15HH6N2C02DLQG15HH6N2S02DLQG15HH6N8G02D6.8 G:±2%H:±3%J:±5%0.22 LQG15HH6N8H02DLQG15HH6N8J02D LQG15HH7N5G02D 7.5 0.24 4200 550LQG15HH7N5H02D LQG15HH7N5J02DLQG15HH8N2G02D 8.2 3700 LQG15HH8N2H02D LQG15HH8N2J02DLQG15HH9N1G02D 9.1 0.26 3400500LQG15HH9N1H02D LQG15HH9N1J02DLQG15HH10NG02D10 LQG15HH10NH02D LQG15HH10NJ02D LQG15HH12NG02D12 0.28 3000 LQG15HH12NH02DLQG15HH12NJ02DLQG15HH15NG02D15 0.32 2500 450 LQG15HH15NH02DLQG15HH15NJ02D LQG15HH18NG02D18 0.36 2200 400 LQG15HH18NH02DLQG15HH18NJ02D LQG15HH22NG02D 22 0.42 1900 350 LQG15HH22NH02D LQG15HH22NJ02D LQG15HH27NG02D 27 0.46 1700 LQG15HH27NH02D LQG15HH27NJ02D LQG15HH33NG02D33 0.58 1600 LQG15HH33NH02DLQG15HH33NJ02D LQG15HH39NG02D39 0.65 1200 300 LQG15HH39NH02DLQG15HH39NJ02DCustomer Part Number MURATAPart NumberInductance (nH) Tolerance Q(min.) DC Resistance (Ω max. ) Self Resonant Frequency (MHz min. )Rated Current (mA)ESD Rank 1C:1kV(*1)(refer to below comment)LQG15HH47NG02D 47 G:±2%H:±3%J:±5%8 0.72 1000 3001CLQG15HH47NH02D LQG15HH47NJ02DLQG15HH56NG02D 56 0.82 800 250LQG15HH56NH02D LQG15HH56NJ02DLQG15HH68NG02D68 0.92 LQG15HH68NH02DLQG15HH68NJ02D LQG15HH82NG02D82 1.20 700 200 LQG15HH82NH02DLQG15HH82NJ02D LQG15HHR10G02D100 1.25 600 LQG15HHR10H02DLQG15HHR10J02DLQG15HHR12G02D120 1.30 LQG15HHR12H02DLQG15HHR12J02DLQG15HHR15G02D 150 2.99 550 150LQG15HHR15H02D LQG15HHR15J02DLQG15HHR18G02D 180 3.38 500 LQG15HHR18H02D LQG15HHR18J02D LQG15HHR22G02D 220 3.77 450 120 LQG15HHR22H02D LQG15HHR22J02D LQG15HHR27G02D270 4.94 400 110 LQG15HHR27H02DLQG15HHR27J02D(*1) Standard Testing Conditions《Unless otherwise specified 》 《In case of doubt 》Temperature : Ordinary Temperature / 15°C to 35°C Temperature: 20°C ± 2°CHumidity :Ordinary Humidity / 25%(RH) to 85%(RH) Humidity : 60%(RH) to 70%(RH) Atmospheric Pressure : 86kPa to 106 kPa4. Appearance and Dimensions■Unit Mass (Typical value)6.Q200 Requirement6.1.Performance (based on Table 5 for Magnetics(Inductors / Transformer)AEC-Q200 Rev.D issued June 1. 2010AEC-Q200 Murata Specification / Deviation No Stress TestMethod3 HighTemperatureExposure 1000hours at 125 deg CSet for 24hours at roomtemperature, then measured.Meet Table A after testing.Table A4 TemperatureCycling 1000cycles-40 deg C to +125 deg CSet for 24hours at roomtemperature,thenmeasured.Meet Table A after testing.7 Biased Humidity 1000hours at 85 deg C, 85%RHunpowered.Meet Table A after testing.8 Operational Life Apply 125 deg C 1000hoursSet for 24hours at roomtemperature, then measuredMeet Table A after testing.9 External Visual Visual inspection No abnormalities10 Physical Dimension Meet ITEM 4(Style and Dimensions)No defects12 Resistanceto Solvents PerMIL-STD-202Method 215Not ApplicableAppearance No damageInductanceChange(at 100MHz)Within ±10%AEC-Q200 Murata Specification / Deviation No Stress TestMethod13 Mechanical Shock Per MIL-STD-202Method 213Condition C : 100g’s(0.98N),6ms, Half sine, 12.3ft/sMeet Table A after testing.14 Vibration 5g's(0.049N) for 20 minutes,12cycles each of 3 oritentationsTest from 10-2000Hz.Meet Table A after testing.15 Resistanceto Soldering Heat No-heatingSolder temperature260C+/-5 deg CImmersion time 10sMeet Table A after testing.Pre-heating 150C +/-10 deg C, 60s to 90s17 ESD Per AEC-Q200-002 ESD Rank: refer to the Item3 (Rating).Meet Table A after testing18 Solderbility Per J-STD-002 Method b : Not Applicable90% of the terminations is to be soldered.19 ElectricalCharacterizationMeasured : Inductance No defects20 Flammability Per UL-94 Not Applicable21 Board Flex Epoxy-PCB(1.6mm)Deflection 2mm(min)Holding time 60s Meet Table B after testing.Table BAppearance No damage DCresistanceChangeWithin ±10%22 Terminal Strength Per AEC-Q200-006A force of 17.7Nfor 60s Murata Deviation Request: 5N No defects7.Specification of Packaging(in mm)7.2 Specification of Taping(1) Packing quantity (standard quantity)10,000 pcs. / reel(2) Packing MethodProducts shall be packed in the cavity of the base tape and sealed by top tape and bottom tape.(3) Sprocket holeThe sprocket holes are to the right as the tape is pulled toward the user.(4) Spliced pointBase tape and Top tape has no spliced point.(5) Missing components numberMissing components number within 0.1 % of the number per reel or 1 pc., whichever is greater,andare not continuous. The Specified quantity per reel is kept.0.8m ax.7.3 Pull StrengthTop tape5N min.Bottom tape7.4 Peeling off force of cover tapeSpeed of Peeling off 300mm/min Peeling off force0.1N to 0.6N(minimum value is typical)7.5 Dimensions of Leader-tape,Trailer and ReelThere shall be leader-tape ( top tape and empty tape) and trailer-tape (empty tape) as follows.7.6 Marking for reelCustomer part number, MURATA part number, Inspection number(*1) ,RoHS Marking(*2), Quantity etc ・・・*1) <Expression of Inspection No.> □□ OOOO ⨯⨯⨯(1) (2) (3)(1) Factory Code (2) Date First digit : Year / Last digit of yearSecond digit: Month / Jan. to Sep. → 1 to 9, Oct. to Dec. → O, N, D Third, Fourth digi : Day(3) Serial No.*2) <Expression of RoHS Marking> ROHS – Y (△)(1) (2)(1) RoHS regulation conformity parts. (2) MURATA classification number7.7 Marking for Outside package (corrugated paper box)Customer name, Purchasing order number, Customer part number, MURATA part number, RoHS Marking(*2) ,Quantity, etc ・・・7.8. Specification of Outer CaseOuter Case Dimensions(mm)Standard Reel Quantityin Outer Case (Reel)W D H 186 186 93 5* Above Outer Case size is typical. It depends on a quantity of an order.F165to 180degreeTop tape Bottom tapeBase tapeWDLabelH8. △!Caution8.1 Caution(Rating)Do not exceed maximum rated current of the product. Thermal stress may be transmitted to the product and short/open circuit of the product or falling off the product may be occurred.8.2 Fail-safe Be sure to provide an appropriate fail-safe function on your product to prevent a second damage that may becaused by the abnormal function or the failure of our product.8.3 Limitation of ApplicationsPlease contact us before using our products for the applications listed below which require especially high reliability for the prevention of defects which might directly cause damage to the third party's life, body or property.(1) Aircraft equipment (6) Transportation equipment (trains, ships, etc.) (2) Aerospace equipment (7) Traffic signal equipment(3) Undersea equipment (8) Disaster prevention / crime prevention equipment (4) Power plant control equipment (9) Data-processing equipment (5) Medical equipment (10) Applications of similar complexity and /or reliability requirements to the applications listed in the above9. NoticeProducts can only be soldered with reflow. This product is designed for solder mounting.Please consult us in advance for applying other mounting method such as conductive adhesive.9.1 Land pattern designinga 0.4b 1.4 to 1.5c 0.5 to 0.6(in mm)9.2 Flux, Solder・Use rosin-based flux.Don’t use highly acidic flux with halide content exceeding 0.2(wt)% (chlorine conversion value). Don’t use water-soluble flux. ・Use Sn-3.0Ag-0.5Cu solder.・Standard thickness of solder paste : 100μm to 150μm.Resist9.3 Reflow soldering conditions・Inductance value may be changed a little due to the amount of solder.So, the chip coil shall be soldered by reflow so that the solder volume can be controlled.・Pre-heating should be in such a way that the temperature difference between solder and product surface is limited to 150°C max. Cooling into solvent after soldering also should be in such a way that the temperature difference is limited to 100°C max.Insufficient pre-heating may cause cracks on the product, resulting in the deterioration of products quality. ・Standard soldering profile and the limit soldering profile is as follows.The excessive limit soldering conditions may cause leaching of the electrode and / or resulting in the deterioration of product quality.・Reflow soldering profileStandard Profile Limit Profile Pre-heating 150°C ~180°C 、90s ±30s Heating above 220°C 、30s ~60s above 230°C 、60s max. Peak temperature 245°C ±3°C 260°C,10s Cycle of reflow 2 times 2 times9.4 Reworking with soldering ironThe following conditions must be strictly followed when using a soldering iron.Pre-heating 150°C,1 min Tip temperature 350°C max. Soldering iron output 80W max. Tip diameter φ3mm max. Soldering time 3(+1,-0)sTime 2 timesNote :Do not directly touch the products with the tip of the soldering iron in order to prevent the crack on the products due to the thermal shock.9.5 Solder Volume・ Solder shall be used not to be exceed the upper limits as shown below.・ Accordingly increasing the solder volume, the mechanical stress to Chip is also increased. Exceeding solder volume may cause the failure of mechanical or electrical performance.1/3T ≦t ≦TT :thickness of product9.6 Mount ShockOver Mechanical stress to products at mounting process causes crack and electrical failure etc.Limit ProfileStandard Profile 90s±30s 230℃260℃245℃±3℃220℃30s~60s 60s max.180150Temp.(s)(℃)Time.9.7 Product’s locationThe following shall be considered when designing and laying out P.C.B.'s.(1) P.C.B. shall be designed so that products are not subjected to the mechanical stress due to warping the board.[Products direction ]Products shall be located in the sideways direction (Length:a <b) to the mechanical stress.(2) Components location on P.C.B. separation. It is effective to implement the following measures, to reduce stress in separating the board.It is best to implement all of the following three measures; however, implement as many measures as possible to reduce stress.Contents of MeasuresStress Level (1) Turn the mounting direction of the component parallel to the board separation surface. A > D *1 (2) Add slits in the board separation part.A >B (3) Keep the mounting position of the component away from the board separation surface. A > C*1 A > D is valid when stress is added vertically to the perforation as with Hand Separation.If a Cutting Disc is used, stress will be diagonal to the PCB, therefore A > D is invalid.(3) Mounting Components Near Screw HolesWhen a component is mounted near a screw hole, it may be affected by the board deflection that occurs during the tightening of the screw. Mount the component in a position as far away from the screw holes as possible.9.8 Cleaning ConditionsProducts shall be cleaned on the following conditions.(1) Cleaning temperature shall be limited to 60°C max.(40°C max for IPA.)(2) Ultrasonic cleaning shall comply with the following conditions with avoiding the resonance phenomenon at the mounted products and P.C.B.Power : 20 W / l max. Frequency : 28kHz to 40kHz Time : 5 min max.(3) Cleaner1. Alcohol type cleanerIsopropyl alcohol (IPA)2. Aqueous agentPINE ALPHA ST-100S(4) There shall be no residual flux and residual cleaner after cleaning. In the case of using aqueous agent, products shall be dried completely after rinse with de-ionized water in order to remove the cleaner. (5) Other cleaning Please contact us.〈Poor example 〉〈Good example 〉ba9.9 Resin coatingThe inductance value may change and/or it may affect on the product's performance due to highcure-stress of resin to be used for coating / molding products. So please pay your careful attention whenyou select resin.In prior to use, please make the reliability evaluation with the product mounted in your application set.9.10 Handling of a substrateAfter mounting products on a substrate, do not apply any stress to the product caused by bending ortwisting to the substrate when cropping the substrate, inserting and removing a connector from thesubstrate or tightening screw to the substrate.Excessive mechanical stress may cause cracking in the product.Bending Twisting9.11 Storage and Handing Requirements(1) Storage periodUse the products within 6 months after deliverd.Solderability should be checked if this period is exceeded.(2) Storage conditions・Products should be stored in the warehouse on the following conditions.Temperature: -10°C to 40°CHumidity: 15% to 85% relative humidity No rapid change on temperature and humidityDon't keep products in corrosive gases such as sulfur,chlorine gas or acid, or it may causeoxidization of electrode, resulting in poor solderability.・Products should be storaged on the palette for the prevention of the influence from humidity, dust and so on.・Products should be storaged in the warehouse without heat shock, vibration, direct sunlight and so on.・Products should be storaged under the airtight packaged condition.(3) Handling ConditionCare should be taken when transporting or handling product to avoid excessive vibration or mechanical shock.10.△!Note(1) Please make sure that your product has been evaluated in view of your specifications with our product being mounted to your product.(2) You are requested not to use our product deviating from the reference specifications.(3) The contents of this reference specification are subject to change without advance notice.Please approve our product specifications or transact the approval sheet for product specificationsbefore ordering.Reference OnlySpecNo.JELF243B-9101H-01 P.11 / 11。
CP45 12252.3. Mechanical Specifications(-)

Features and Scope of Equipment 1-71.3. Mechanical Specifications1.3.1. Size and weight of the equipmentWidthIncluding conveyer cover: 1,650mmLength: 1,540mmHeight (Under the condition that the height of the PCB upper surface is 900 mm)Up to the upper surface of cover: 1,420mmUp to the upper surface of monitor (LCD): 1,735 mm (1,740 mm)Up to the upper surface of tower lamp: 2,015mmWeight: 1,380 kg1.3.2. Requirements for air pressurePressurePrimary pressure: 5.0 ~ 7.0 kgf/§Secondary pressure: 4.5 ~ 5.5 kgf/§Air Consumption: Maximum 160 N/min Dry Air: air dew point of -17¡or less1.3.3. Environmental conditionsDuring operationTemperature: +10¡~ +35¡Humidityà Less than 50% RH (35¡) à Less than 90% RH (20¡) During shipment or storage (in states other than during operation)Temperature: -10¡ ~ +60¡Humidity: 20% RH ~ 90% RH (non-condensation state)Samsung Component Placer CP-45F(V) NEO /CP-45FS NEO Operations Manual 1-8 1.3.4. NoiseThe CP-45F/V NEO and the CP-45FS NEO machine has a noise level not exceeding 80 dB with the front and rear covers closed. The noise is measured at the upper surfaces of the front and rear feeder bases while operating the equipment at 100% speed and driving all x-axis, y-axis, and z-axis to the maximum stroke.1.4. Electrical Specifications1.4.1. Power requirementsV oltageSingle phase AC 220V10 % AC 100V¡10 % / 110V¡10 % / 120V¡10 % / 200V¡10 % / 220V¡10 % /230V¡10 % / 240V¡10 % (shall be changed the terminal of the transformer) Power Consumption: 6.3 KV A (Maximum)Frequency: 50 / 60 HzFigure 1-3. The solution for switching the power terminal connection of a transformer。
aurora_64b66b_protocol_spec_sp011

aurora_64b66b_protocol_spec_sp011Aurora 64B/66B Protocol SpecificationSP011 (v1.2) July 23, 2010Xilinx is disclosing to you this Specification (hereinafter "the Specification") for use in the development of designs in connection with semiconductor devices. Xilinx expressly disclaims any liability arising out of your use of the Specification. Xilinx does not convey any license under its patents, copyrights, or any rights of others in connection with the Specification. Y ou are responsible for obtaining any rights you may require for your use or implementation of the Specification. Xilinx reserves the right to make changes, at any time, to the Specification without notice and at the sole discretion of Xilinx. Xilinx assumes no obligation to correct any errors contained in the Specification or to advise you of any corrections or updates. Xilinx expressly disclaims any liability in connection with technical support or assistance that may be provided to you in connection with the Specification.THE SPECIFICA TION IS DISCLOSED TO YOU "AS-IS" WITH NO WARRANTY OF ANY KIND. YOU BEAR THE ENTIRE RISK AS TO ITS IMPLEMENTA TION AND USE. YOU ACKNOWLEDGE AND AGREE THA T YOU HAVE NOT RELIED ON ANY ORAL OR WRITTEN INFORMATION OR ADVICE, WHETHER GIVEN BY XILINX, ITS EMPLOYEES OR CONTRACTORS. XILINX MAKES NO OTHER WARRANTIES, WHETHER EXPRESS, IMPLIED, OR STA TUTORY, REGARDING THE SPECIFICATION, INCLUDING ANY WARRANTIES OF MERCHANTABILITY, FITNESS FOR A P ARTICULAR PURPOSE, OR NONINFRINGEMENT OF THIRD-PARTY RIGHTS.IN NO EVENT WILL XILINX BE LIABLE FOR ANY CONSEQUENTIAL, INDIRECT, EXEMPLARY, SPECIAL, OR INCIDENTAL DAMAGES, INCLUDING ANY LOSS OF DA TA OR LOST PROFITS, ARISING FROM OR RELATING TO YOUR USE OF THE SPECIFICA TION, EVEN IF YOU HAVE BEEN ADVISED OF THE POSSIBILITY OF SUCH DAMAGES.2008, 2010 Xilinx, Inc. All rights reserved.XILINX, the Xilinx logo, the Brand Window, and other designated brands included herein are trademarks of Xilinx, Inc. All other trademarks are the property of their respective owners.Revision HistoryThe following table shows the revision history for this document.Date Version Revision03/31/08 1.0Initial Xilinx release.09/19/08 1.1Minor typographical edits. Changed block codes to blocks. Removed Not Ready blocks from Simplex in Table4-1, page36. Clarified simplex Aurora channel bonding inSection4.2.2“Channel Bonding,” page36. Added Appendix1, “References.”07/23/10 1.2Updated Section1.2“Scope” and Section8.1“Overview.”Deleted Sections 8.4 Transmitter Specifications, 8.5 Receiver Specifications, and 8.6Receiver Eye Diagrams.Table of ContentsSchedule of Figures. . . . . . . . . . . . . . . . . . . . . . . . . . . . . . . . . . . . . . . . . . . . . . . . . . . . . . . . . . 7 Schedule of Tables. . . . . . . . . . . . . . . . . . . . . . . . . . . . . . . . . . . . . . . . . . . . . . . . . . . . . . . . . . . 9Preface: About This SpecificationSpecification Contents . . . . . . . . . . . . . . . . . . . . . . . . . . . . . . . . . . . . . . . . . . . . . . . . . . . . . . 11Conventions . . . . . . . . . . . . . . . . . . . . . . . . . . . . . . . . . . . . . . . . . . . . . . . . . . . . . . . . . . . . . . . .12 Typographical. . . . . . . . . . . . . . . . . . . . . . . . . . . . . . . . . . . . . . . . . . . . . . . . . . . . . . . . . . . . 12Online Document. . . . . . . . . . . . . . . . . . . . . . . . . . . . . . . . . . . . . . . . . . . . . . . . . . . . . . . . . 12State Diagram Conventions . . . . . . . . . . . . . . . . . . . . . . . . . . . . . . . . . . . . . . . . . . . . . . . . 14 Section1: Introduction and Overview1.1:Introduction . . . . . . . . . . . . . . . . . . . . . . . . . . . . . . . . . . . . . . . . . . . . . . . . . . . . . . . . . . . . 17 1.2:Scope . . . . . . . . . . . . . . . . . . . . . . . . . . . . . . . . . . . . . . . . . . . . . . . . . . . . . . . . . . . . . . . . . . . 17 1.3:Overview . . . . . . . . . . . . . . . . . . . . . . . . . . . . . . . . . . . . . . . . . . . . . . . . . . . . . . . . . . . . . . . 17 Section2: Data Transmission and Reception2.1:Overview . . . . . . . . . . . . . . . . . . . . . . . . . . . . . . . . . . . . . . . . . . . . . . . . . . . . . . . . . . . . . . . 21 2.2:Block Codes. . . . . . . . . . . . . . . . . . . . . . . . . . . . . . . . . . . . . . . . . . . . . . . . . . . . . . . . . . . . . 21 2.3:Frame Transmission Procedure. . . . . . . . . . . . . . . . . . . . . . . . . . . . . . . . . . . . . . . . . . 23 2.3.1:Link-Layer Frame Delineation . . . . . . . . . . . . . . . . . . . . . . . . . . . . . . . . . . . . . . . . 242.3.2:64B/66B Encoding . . . . . . . . . . . . . . . . . . . . . . . . . . . . . . . . . . . . . . . . . . . . . . . . . . 242.3.3:Serialization and Clock Encoding. . . . . . . . . . . . . . . . . . . . . . . . . . . . . . . . . . . . . . 24 2.3.4:Multi-Lane Transmission. . . . . . . . . . . . . . . . . . . . . . . . . . . . . . . . . . . . . . . . . . . . . 242.4:Frame Reception Procedure . . . . . . . . . . . . . . . . . . . . . . . . . . . . . . . . . . . . . . . . . . . . . 25 2.4.1:Deserialization. . . . . . . . . . . . . . . . . . . . . . . . . . . . . . . . . . . . . . . . . . . . . . . . . . . . . . 25 2.4.2:64B/66B Decoding . . . . . . . . . . . . . . . . . . . . . . . . . . . . . . . . . . . . . . . . . . . . . . . . . . 25 2.4.3:Control Block Stripping. . . . . . . . . . . . . . . . . . . . . . . . . . . . . . . . . . . . . . . . . . . . . . 262.4.4:Multi-Lane Reception. . . . . . . . . . . . . . . . . . . . . . . . . . . . . . . . . . . . . . . . . . . . . . . . 262.5:Data and Separator Block Format. . . . . . . . . . . . . . . . . . . . . . . . . . . . . . . . . . . . . . . . 26 Section3: Flow Control3.1:Overview . . . . . . . . . . . . . . . . . . . . . . . . . . . . . . . . . . . . . . . . . . . . . . . . . . . . . . . . . . . . . . . 29 3.2:Native Flow Control Operation. . . . . . . . . . . . . . . . . . . . . . . . . . . . . . . . . . . . . . . . . . 293.3:Native Flow Control Latency . . . . . . . . . . . . . . . . . . . . . . . . . . . . . . . . . . . . . . . . . . . . 30 3.4:Native Flow Control Block Format. . . . . . . . . . . . . . . . . . . . . . . . . . . . . . . . . . . . . . . 303.5:User Flow Control Operation. . . . . . . . . . . . . . . . . . . . . . . . . . . . . . . . . . . . . . . . . . . . 30 3.6:User Flow Control Message Format. . . . . . . . . . . . . . . . . . . . . . . . . . . . . . . . . . . . . . 31Section4: Initialization and Error Handling4.1:Overview . . . . . . . . . . . . . . . . . . . . . . . . . . . . . . . . . . . . . . . . . . . . . . . . . . . . . . . . . . . . . . . 33 4.2:Aurora Channel Initialization . . . . . . . . . . . . . . . . . . . . . . . . . . . . . . . . . . . . . . . . . . . 344.2.1:Lane Initialization. . . . . . . . . . . . . . . . . . . . . . . . . . . . . . . . . . . . . . . . . . . . . . . . . . . 344.2.2:Channel Bonding. . . . . . . . . . . . . . . . . . . . . . . . . . . . . . . . . . . . . . . . . . . . . . . . . . . . 36 4.2.3:Wait For Remote . . . . . . . . . . . . . . . . . . . . . . . . . . . . . . . . . . . . . . . . . . . . . . . . . . . . 374.3:Error Handling. . . . . . . . . . . . . . . . . . . . . . . . . . . . . . . . . . . . . . . . . . . . . . . . . . . . . . . . . . 384.4:CRC . . . . . . . . . . . . . . . . . . . . . . . . . . . . . . . . . . . . . . . . . . . . . . . . . . . . . . . . . . . . . . . . . . . . 38 Section5: PCS Layer5.1:Overview . . . . . . . . . . . . . . . . . . . . . . . . . . . . . . . . . . . . . . . . . . . . . . . . . . . . . . . . . . . . . . . 395.2:Aurora Encoding. . . . . . . . . . . . . . . . . . . . . . . . . . . . . . . . . . . . . . . . . . . . . . . . . . . . . . . . 395.2.1:Block Codes in 64B/66B. . . . . . . . . . . . . . . . . . . . . . . . . . . . . . . . . . . . . . . . . . . . . . 395.2.2:Idle/Not Ready/Clock Compensation/Channel Bonding Block Code. . . . . . 405.2.3:Native Flow Control Block Code . . . . . . . . . . . . . . . . . . . . . . . . . . . . . . . . . . . . . . 425.2.4:Data Block Code for Frame Data . . . . . . . . . . . . . . . . . . . . . . . . . . . . . . . . . . . . . . 425.2.5:Separator Block Code. . . . . . . . . . . . . . . . . . . . . . . . . . . . . . . . . . . . . . . . . . . . . . . . 425.2.6:Separator-7 Block Code . . . . . . . . . . . . . . . . . . . . . . . . . . . . . . . . . . . . . . . . . . . . . . 435.2.7:User Flow Control Block Code . . . . . . . . . . . . . . . . . . . . . . . . . . . . . . . . . . . . . . . . 435.2.8:Data Block Code for User Flow Control Message . . . . . . . . . . . . . . . . . . . . . . . . 445.2.9:User K-Block Codes . . . . . . . . . . . . . . . . . . . . . . . . . . . . . . . . . . . . . . . . . . . . . . . . . 445.3:64B/66B Scrambling. . . . . . . . . . . . . . . . . . . . . . . . . . . . . . . . . . . . . . . . . . . . . . . . . . . . . 455.4:64B/66B Gearbox . . . . . . . . . . . . . . . . . . . . . . . . . . . . . . . . . . . . . . . . . . . . . . . . . . . . . . . . 455.5:Channel Bonding . . . . . . . . . . . . . . . . . . . . . . . . . . . . . . . . . . . . . . . . . . . . . . . . . . . . . . . 455.6:Clock Compensation . . . . . . . . . . . . . . . . . . . . . . . . . . . . . . . . . . . . . . . . . . . . . . . . . . . . 45 Section6: Channel Control6.1:Overview . . . . . . . . . . . . . . . . . . . . . . . . . . . . . . . . . . . . . . . . . . . . . . . . . . . . . . . . . . . . . . . 476.2:Idle Block Striping. . . . . . . . . . . . . . . . . . . . . . . . . . . . . . . . . . . . . . . . . . . . . . . . . . . . . . 476.2.1:Not Ready Blocks . . . . . . . . . . . . . . . . . . . . . . . . . . . . . . . . . . . . . . . . . . . . . . . . . . . 476.2.2:Idle Blocks . . . . . . . . . . . . . . . . . . . . . . . . . . . . . . . . . . . . . . . . . . . . . . . . . . . . . . . . . 476.2.3:Clock Compensation Blocks . . . . . . . . . . . . . . . . . . . . . . . . . . . . . . . . . . . . . . . . . . 476.2.4:Channel Bonding Blocks . . . . . . . . . . . . . . . . . . . . . . . . . . . . . . . . . . . . . . . . . . . . . 476.3:Native Flow Control Striping. . . . . . . . . . . . . . . . . . . . . . . . . . . . . . . . . . . . . . . . . . . . 476.4:Frame Data Striping. . . . . . . . . . . . . . . . . . . . . . . . . . . . . . . . . . . . . . . . . . . . . . . . . . . . . 486.5:Strict-Alignment Frame Data Striping . . . . . . . . . . . . . . . . . . . . . . . . . . . . . . . . . . . 486.6:User Flow Control Striping. . . . . . . . . . . . . . . . . . . . . . . . . . . . . . . . . . . . . . . . . . . . . . 486.7:Strict-Alignment User Flow Control Striping . . . . . . . . . . . . . . . . . . . . . . . . . . . . 486.8:User K-Block Striping. . . . . . . . . . . . . . . . . . . . . . . . . . . . . . . . . . . . . . . . . . . . . . . . . . . 48 Section7: PMA Layer7.1:Overview . . . . . . . . . . . . . . . . . . . . . . . . . . . . . . . . . . . . . . . . . . . . . . . . . . . . . . . . . . . . . . . 497.2:Bit and Byte Ordering Convention. . . . . . . . . . . . . . . . . . . . . . . . . . . . . . . . . . . . . . . 497.3:Serialization . . . . . . . . . . . . . . . . . . . . . . . . . . . . . . . . . . . . . . . . . . . . . . . . . . . . . . . . . . . . 49Section8: Electrical Specifications8.1:Overview . . . . . . . . . . . . . . . . . . . . . . . . . . . . . . . . . . . . . . . . . . . . . . . . . . . . . . . . . . . . . . . 518.2:Signal Definition . . . . . . . . . . . . . . . . . . . . . . . . . . . . . . . . . . . . . . . . . . . . . . . . . . . . . . . 518.3:Equalization . . . . . . . . . . . . . . . . . . . . . . . . . . . . . . . . . . . . . . . . . . . . . . . . . . . . . . . . . . . . 52 Appendix1: ReferencesSchedule of FiguresPreface: About This SpecificationFigure P-1:Properties of Literals. . . . . . . . . . . . . . . . . . . . . . . . . . . . . . . . . . . . . . . . . . . . . . . . 13Figure P-2:State Machine Diagram Conventions . . . . . . . . . . . . . . . . . . . . . . . . . . . . . . . . . 15Section1: Introduction and OverviewFigure 1-1:Aurora Protocol Overview . . . . . . . . . . . . . . . . . . . . . . . . . . . . . . . . . . . . . . . . . . . 18Figure 1-2:A Simplex Connection Between a Pair of Aurora Lanes . . . . . . . . . . . . . . . . . 18Figure 1-3:A Single-Lane, Simplex Aurora Channel . . . . . . . . . . . . . . . . . . . . . . . . . . . . . . 19Figure 1-4:A Multi-Lane, Simplex Aurora Channel. . . . . . . . . . . . . . . . . . . . . . . . . . . . . . . 19Figure 1-5:A Single-Lane, Full-Duplex Aurora Channel. . . . . . . . . . . . . . . . . . . . . . . . . . . 20Figure 1-6:A Multi-Lane, Full-Duplex Aurora Channel . . . . . . . . . . . . . . . . . . . . . . . . . . . 20Section2: Data Transmission and ReceptionFigure 2-1:Mapping Frames to Encoded Block Codes for Transmission. . . . . . . . . . . . . 23Figure 2-2:Receiving Data from an Aurora Channel . . . . . . . . . . . . . . . . . . . . . . . . . . . . . . 25Figure 2-3:Data Block Used for Frame Data. . . . . . . . . . . . . . . . . . . . . . . . . . . . . . . . . . . . . . 26Figure 2-4:Separator Block. . . . . . . . . . . . . . . . . . . . . . . . . . . . . . . . . . . . . . . . . . . . . . . . . . . . . 26Figure 2-5:Separator-7 Block. . . . . . . . . . . . . . . . . . . . . . . . . . . . . . . . . . . . . . . . . . . . . . . . . . . 27Figure 2-6:Example of Frame Data Transfer through a Single-Lane Channel . . . . . . . . 27Figure 2-7:Example of Frame Data Transfer through a Multi-Lane Channel . . . . . . . . . 27Section3: Flow ControlFigure 3-1:NFC Block . . . . . . . . . . . . . . . . . . . . . . . . . . . . . . . . . . . . . . . . . . . . . . . . . . . . . . . . . 30Figure 3-2:UFC Block with UFC Header. . . . . . . . . . . . . . . . . . . . . . . . . . . . . . . . . . . . . . . . . 31Figure 3-3:Data Block Used to Carry UFC Message Data . . . . . . . . . . . . . . . . . . . . . . . . . . 31Figure 3-4:Example UFC Messages for Single-Lane Channel . . . . . . . . . . . . . . . . . . . . . . 31Figure 3-5:Example UFC Messages for a Multi-Lane Channel. . . . . . . . . . . . . . . . . . . . . . 32Section4: Initialization and Error HandlingFigure 4-1:Initialization Overview. . . . . . . . . . . . . . . . . . . . . . . . . . . . . . . . . . . . . . . . . . . . . . 34Figure 4-2:Block Sync State Machine . . . . . . . . . . . . . . . . . . . . . . . . . . . . . . . . . . . . . . . . . . . 35Section5: PCS LayerFigure 5-1:Idle/Not Ready/NFC Block Code . . . . . . . . . . . . . . . . . . . . . . . . . . . . . . . . . . . . . 41Figure 5-2:Native Flow Control Block Code . . . . . . . . . . . . . . . . . . . . . . . . . . . . . . . . . . . . . 42Figure 5-3:Data Block Code Carrying Frame Data . . . . . . . . . . . . . . . . . . . . . . . . . . . . . . . . 42Figure 5-4:Separator Block Code . . . . . . . . . . . . . . . . . . . . . . . . . . . . . . . . . . . . . . . . . . . . . . . 42Figure 5-5:Separator-7 Block Code. . . . . . . . . . . . . . . . . . . . . . . . . . . . . . . . . . . . . . . . . . . . . . 43Figure 5-6:User Flow Control Block Code . . . . . . . . . . . . . . . . . . . . . . . . . . . . . . . . . . . . . . . 43 Figure 5-7:Data Block Code Carrying User Flow Control Message Data. . . . . . . . . . . . . 44 Figure 5-8:User K-Block Code Format. . . . . . . . . . . . . . . . . . . . . . . . . . . . . . . . . . . . . . . . . . . 44Section6: Channel ControlSection7: PMA LayerFigure 7-1:Serialization Order for Aurora 64B/66B Block Codes. . . . . . . . . . . . . . . . . . . . 49Section8: Electrical SpecificationsFigure 8-1:Differential Peak-To-Peak Voltage of Transmitter or Receiver. . . . . . . . . . . 51Appendix1: ReferencesSchedule of TablesPreface: About This SpecificationTable P-1:Radix Specifics of Literals . . . . . . . . . . . . . . . . . . . . . . . . . . . . . . . . . . . . . . . . . . . . 13Table P-2:Examples of Extended Values. . . . . . . . . . . . . . . . . . . . . . . . . . . . . . . . . . . . . . . . . 13Section1: Introduction and OverviewSection2: Data Transmission and ReceptionTable 2-1:Aurora 64B/66B Blocks Summary. . . . . . . . . . . . . . . . . . . . . . . . . . . . . . . . . . . . . . 21Table 2-2:Normal Aurora 64B/66B Block Transmission Priority . . . . . . . . . . . . . . . . . . . . 22Table 2-3:Aurora 64B/66B Block Transmission Priority during Flow Control Countdown 23 Section3: Flow Control Section4: Initialization and Error HandlingTable 4-1:Required Block Transmission during Lane Initialization. . . . . . . . . . . . . . . . . 36Table 4-2:Required State Transition after Lane Initialization . . . . . . . . . . . . . . . . . . . . . . 36Table 4-3:Required State Transition after Successful Channel Bonding. . . . . . . . . . . . . 37Section5: PCS LayerTable 5-1:Valid Block Type Field Values in Aurora 64B/66B. . . . . . . . . . . . . . . . . . . . . . . 40Table 5-2:Valid Octet Count Field Values for Separator Block Code. . . . . . . . . . . . . . . . 43Table 5-3:Valid Block Type Field Values for User K-Blocks . . . . . . . . . . . . . . . . . . . . . . . 44 Section6: Channel Control Section7: PMA LayerSection8: Electrical SpecificationsAppendix1: ReferencesPreface About This SpecificationThis specification describes the Aurora 64B/66B protocol. Aurora is a lightweight link-layer protocol that can be used to move data point-to-point across one or more high-speed serial lanes. Aurora 64B/66B is a version of the protocol using 64B/66B encoding instead of 8B/10B.Specification ContentsThis manual contains the following:Section1, “Introduction and Overview”provides an overview of the Aurora 64B/66B protocol.Section2, “Data Transmission and Reception”describes the procedures for transmitting and receiving data using an Aurora 64B/66B Channel.Section3, “Flow Control”describes the optional flow control features in the Aurora64B/66B protocol.Section4, “Initialization and Error Handling”describes the procedure used to preparean Aurora channel for operation.Section5, “PCS Layer”specifies the functions performed in the physical coding sub-layer (PCS) of the Aurora 64B/66B protocol.Section6, “Channel Control”defines the striping rules for using multi-lane channels. Section7, “PMA Layer”specifies the functions performed in the PMA layer of the Aurora 64B/66B Protocol.Section8, “Electrical Specifications”describes the AC specifications, covering both single- and multi-lane implementations.ConventionsThis document uses the following conventions.T ypographicalThe following typographical conventions are used in this document:Online DocumentThe following conventions are used in this document:NumericalConventionMeaning or UseExampleItalic fontReferences to other manualsSee the Development System Reference Guide for more information.Emphasis in textIf a wire is drawn so that itoverlaps the pin of a symbol, the two nets are not connected.To emphasize a term the first time it is used The state machine uses one-hot encoding.REG[FIELD]Abbreviations or acronyms for registers are shown in uppercasetext. Specific bits, fields, or ranges appear in bracketsREG[11:14]ConventionMeaning or UseExampleBlue textCross-reference link to a location in the current document See the section “AdditionalResources” for details.Refer to “Title Formats” inSection 1 for details.Red textCross-reference link to a location in another document See Figure 2-5 in the Virtex-II Platform FPGA User Guide.Blue, underlined textHyperlink to a website (URL)Go to /doc/10fb3b7b1711cc7931b716ea.htmlfor the latest speed files.Convention Meaning or Usen A decimal value[n:m ]Used to express a numerical range from n to m x Unknown value zHigh impedanceValues of LiteralsLiterals are represented by specifying three of their properties as listed and shown in Figure P-1 and in Table P-1 and Table P-2:1.Width in bits 2.Radix (Base)3.ValueTable P-1 shows the Radix specifics:All values are extended with zero except those with x or z in the most significant place; they extend with x or z respectively. A list of examples is shown in Table P-2:Figure P-1:Properties of LiteralsTable P-1:Radix Specifics of LiteralsRadix SpecifierRadixb Binary d Decimal h Hexadecimal oOctalTable P-2:Examples of Extended ValuesNumber Value Comment8’b000000000An 8-bit binary number with value of zero. (Zero extended to get 8 bits.)8’bx xxxxxxxxAn 8-bit binary number with value unknown. (x extended to get 8 bits.)8’b1x 0000001x An 8-bit binary number with value of 2 or 3, depending on the value of x.8’b0x 0000000x An 8-bit binary number with value of 0 or 1, depending on the value of x.8’hx xxxxxxxx An 8-bit hexadecimal number with value unknown.(x extended to get 8 bits.)8’hzx zzzzxxxx An 8-bit hexadecimal number with the upper four bits not driven and the lower four bitsunknown.8’b100000001An 8-bit binary number with value of one.8’hz1zzzz0001An 8-bit hexadecimal number with the upper four bits not driven and the lower four bits having value of one.8’bx1xxxxxxx1An 8-bit binary number that is odd.8’bx0xxxxxxx0An 8-bit binary number that is even.State Diagram ConventionsThis section describes the conventions used in the state diagrams for this document. The numbered sections correspond to the call-outs shown in the state machine diagram in Figure P-2, page 15.States1. A state is represented by a rectangle.2.The name of the state is indicated in bold.State T ransitions3.State transition is indicated by an arrow annotated in italics.State Machine OutputsOutputs are shown in plain text. Outputs can be shown inside of state rectangles or can be part of the annotation associated with a transition arrow. If a signal is not listed in a state rectangle or on a transition arrow, its value at that time is 0 (not asserted). If a registered output does not appear in the state rectangle or transition arrow annotation, then its value is unchanged from the previous value.Output T ypesOutputs are divided into three classes as shown in the examples below.4.Asserting control signals:go = 1link reset = 15.Register initialization:XYZ Register = 78New Counter = 0xmit = /SP/ (an ordered set)6.Incrementing or decrementing a register:XYZ Register = XYZ Register + 1New Counter = New Counter – 68’hz zzzzzzzz An 8-bit hexadecimal number with value not driven. (z extended to get 8 bits.)8’h0z 0000zzzzAn 8-bit hexadecimal number with upper nibble specified and the lower not driven.11’d n n An 11-bit decimal number with value n .6’h n nA 6-bit hexadecimal number with value n .w’b101(101)A binary number with value 5 and an unknown width.Table P-2:Examples of Extended Values (Cont’d)Number Value CommentFigure P-2:State Machine Diagram ConventionsSection1 Introduction and Overview1.1IntroductionAurora is a lightweight link-layer protocol that can be used to move data point-to-pointacross one or more high-speed serial lanes. Aurora 64B/66B is a version of the protocolusing 64B/66B encoding instead of 8B/10B.1.2ScopeThe Aurora 64B/66B Protocol Specification defines the following:Electrical specifications: This includes signaling levels for an Aurora serial link.PMA layer: This includes specification for serialization bit ordering and byteordering.Physical coding sub-layer (PCS): This includes specification for data encoding anddecoding, data scrambling, the 64B/66B gearbox, clock compensation and channelbonding.Channel control: This includes specifications for multi-lane striping and forscheduling the transmission of data and control information.Cyclic redundancy check (CRC): The Aurora protocol recommends a CRCmechanism compatible with the standard 64B/66B scrambling algorithm.1.3OverviewThe Aurora protocol (Figure1-1, page18) describes the transfer of user data across anAurora channel, consisting of one or more Aurora lanes. Each Aurora lane is a serial dataconnection, either full-duplex or simplex. Devices communicating across the channel arecalled channel partners.Aurora interfaces allow user applications to transfer data through the Aurora channel. Theuser interface on each Aurora interface is not defined in this specification and can bedecided independently for each implementation of the protocol.Aurora channels have the following properties:Data is transferred through the Aurora channel in frames.Frames share the channel with control information such as flow control messages,clock compensation sequences and idles.Frames can be of any length, and can have any format. Only the delineation of framesis defined in this specification.Frames in Aurora do not have to be contiguous — they can be interrupted at any time by flow control messages or idles.There is no gap required between frames in Aurora.Figure 1-1:Aurora Protocol OverviewFigure1-2 shows a simplex connection between a pair of Aurora lanes, depicting the functional blocks comprising the PCS and PMA layers of an Aurora connection. These blocks are specified in detail in this document.Figure 1-2: A Simplex Connection Between a Pair of Aurora LanesAurora interfaces allow applications to communicate using Aurora channels. Aurora interfaces are made up of one or more Aurora lanes, either simplex or full-duplex. The four possible configurations of Aurora interfaces are shown in Figure1-3, Figure1-4,Figure1-5, page20, and Figure1-6, page20.Figure1-3 shows a single-lane, simplex Aurora interface transmitting to another single-lane, simplex Aurora interface. In this configuration, each interface uses a single lane to transmit or receive from the Aurora channel. Channel control in each interface initializes the channel passing control to the user application.Figure 1-3: A Single-Lane, Simplex Aurora ChannelFigure1-4 shows a multi-lane, simplex Aurora interface transmitting to another multi-lane, simplex Aurora interface. In multi-lane configurations, the channel control bonds the lanes to eliminate skew between channels as a part of the channel initialization procedure. During normal operation, the channel control logic distributes data and control information across all the lanes in the channel.Figure 1-4: A Multi-Lane, Simplex Aurora Channel。
pcr仪八连管产品标准

PCR仪八连管产品标准1. 范围本标准规定了PCR仪八连管产品的技术要求、试验方法、检验规则、标志、包装、运输和贮存等要求。
本标准适用于以塑料材料为主要组件,用于在PCR仪中进行DNA/RNA扩增分析的八连管产品。
2. 规范性引用文件下列文件对于本文件的应用是必不可少的。
凡是注日期的引用文件,仅注日期的版本适用于本文件。
凡是不注日期的引用文件,其最新版本(包括所有的修改单)适用于本文件。
GB/T 191 包装储运图示标志GB/T 2828.1-2012 计数抽样检验程序第1部分:按接收质量限(AQL)检索的逐批检验抽样计划3. 术语和定义3.1 PCR仪八连管product of PCR eight-tube strip以塑料材料为主要组件,用于在PCR仪中进行DNA/RNA扩增分析的八连管产品。
3.2 外观appearance产品的外观质量,包括管壁的均匀性、透明度,以及有无气泡、裂纹、变形等缺陷。
3.3 尺寸dimension产品的几何尺寸,包括管径、管长等。
3.4 热稳定性thermal stability产品在规定温度下保持一段时间后,其物理、化学性能的稳定程度。
3.5 耐高温性能high-temperature resistance产品在高温条件下保持其原有性能的特性。
3.6 耐低温性能low-temperature resistance产品在低温条件下保持其原有性能的特性。
4. 产品结构PCR仪八连管由塑料材料制成的各个单管组成,每个单管的一端封口,另一端设有开口,八个单管连为一体,整体呈扁平的“田”字形结构。
5. 技术要求5.1 外观要求PCR仪八连管的外观应光滑、透明,无气泡、裂纹和变形等缺陷。
管壁应均匀,无明显厚薄不均现象。
封口应严密,无漏液现象。
5.2 尺寸要求PCR仪八连管的尺寸应符合设计图纸要求。
管径、管长等参数应在规定范围内。
5.3 热稳定性要求PCR仪八连管应在规定的热稳定性试验条件下保持一定时间,无明显变形、开裂等现象,且各项性能指标均符合要求。
TPS2554 and TPS2555 Evaluation Module User's Guide
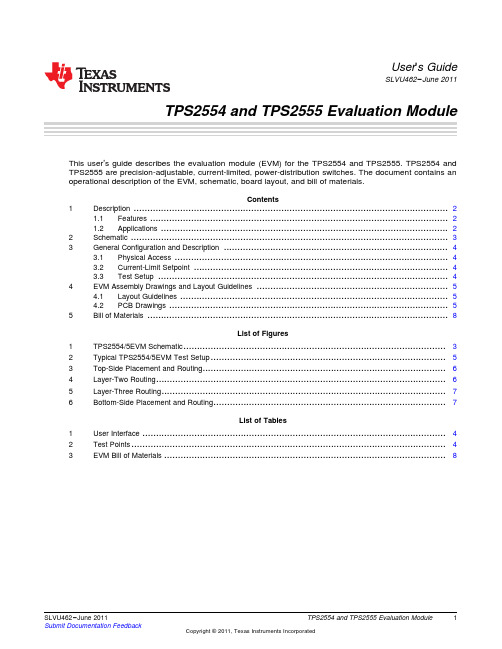
User's GuideSLVU462–June2011TPS2554and TPS2555Evaluation Module This user’s guide describes the evaluation module(EVM)for the TPS2554and TPS2555.TPS2554and TPS2555are precision-adjustable,current-limited,power-distribution switches.The document contains an operational description of the EVM,schematic,board layout,and bill of materials.Contents1Description (2)1.1Features (2)1.2Applications (2)2Schematic (3)3General Configuration and Description (4)3.1Physical Access (4)3.2Current-Limit Setpoint (4)3.3Test Setup (4)4EVM Assembly Drawings and Layout Guidelines (5)4.1Layout Guidelines (5)4.2PCB Drawings (5)5Bill of Materials (8)List of Figures1TPS2554/5EVM Schematic (3)2Typical TPS2554/5EVM Test Setup (5)3Top-Side Placement and Routing (6)4Layer-Two Routing (6)5Layer-Three Routing (7)6Bottom-Side Placement and Routing (7)List of Tables1User Interface (4)2Test Points (4)3EVM Bill of Materials (8)1 SLVU462–June2011TPS2554and TPS2555Evaluation Module Submit Documentation FeedbackCopyright©2011,Texas Instruments IncorporatedDescription 1DescriptionThe TPS2554EVM-010evaluation module allows reference circuit evaluation of the Texas Instruments TPS2554and TPS2555power-distribution switches.1.1Features•Precision adjustable,current-limited,power-distribution switch•Fast overcurrent response–1µs typical•80-mΩ,high-side MOSFET•Operating range:4.5V to5.5V1.2Applications•USB ports/hubs•Notebook personal computers(PC)2TPS2554and TPS2555Evaluation Module SLVU462–June2011Submit Documentation FeedbackCopyright©2011,Texas Instruments IncorporatedGeneral Configuration and Description 3General Configuration and Description3.1Physical AccessTable1lists the TPS2554/5EVM connector functionality,and Table2describes the test point availability.er InterfaceConnector Label DescriptionJ1VIN Input connectorJ2VOUT Output connectorJ3J3Input voltage jumper.Shunt can be removed to measure input current.J4J4Output voltage jumper.Shunt can be removed to measure output current.J5EN Enable jumper.Leave open to enable TPS2554and install shunt to enable TPS2555.J6ILIM_SEL Current limit select.Install shunt to select ILIM0(2.4A nominal),and remove shunt toselect ILIM1(1.2A nominal).D1(RED)FLT Fault LEDTable2.Test PointsTest Point Color Label DescriptionTP3RED IN Power switch input(IC side of J3shunt)TP4BLK GND Power switch input groundTP1WHT FLT Fault pin outputTP2RED VOUT Power switch outputTP5BLK GND Power switch output groundTP6WHT EN Enable pin input3.2Current-Limit SetpointR4and R5configure the current-limit setpoint for ILIM0and ILIM1,respectively(see J6in Table1).ILIM0or ILIM1setpoint can be adjusted using the following example by substituting R4or R5for RILIMx .In thisexample IOS=2A.The following example is an approximation only and does not take into account the resistor tolerance or the variation of ILIM.For exact variation of ILIM,see the TPS2554/TPS2555data sheet,SLVSAM0.IOS=48000/RILIMx=2ARILIMx=48000/IOS=48000/2=24000ΩChoose RILIMx=23.7kΩIOS=48000/23700=2.03A3.3Test SetupFigure2shows a typical test setup for TPS2554/5EVM.4TPS2554and TPS2555Evaluation Module SLVU462–June2011Submit Documentation FeedbackCopyright©2011,Texas Instruments IncorporatedV INOscilloscope EVM Assembly Drawings and Layout GuidelinesFigure2.Typical TPS2554/5EVM Test Setup4EVM Assembly Drawings and Layout Guidelines4.1Layout Guidelines•TPS2554/55placement:Place the TPS2554/55near the USB output connector and the150-µF OUT pin filter capacitor.Connect the exposed pad to the GND pin and the system ground plane using a viaarray.•IN pin bypass capacitance:Place the100-nF bypass capacitor near the IN and GND pins,and make the connection using a low-inductance trace.•ILIM0and ILIM1pin connections:Current-limit accuracy can be compromised by stray current leakage from a higher voltage source to the ILIM0or ILIM1pins.Ensure that adequate spacing existsbetween IN pin copper/trace and ILIM0pin trace to prevent contaminate buildup during the PCBassembly process.If a low-current-limit setpoint is required(RILIMx >200kΩ),use ILIM1for this case,as it is further away from the IN pin.4.2PCB DrawingsThe Figure3through Figure6show component placement and layout of the EVM.5 SLVU462–June2011TPS2554and TPS2555Evaluation Module Submit Documentation FeedbackCopyright©2011,Texas Instruments IncorporatedEVM Assembly Drawings and Layout Guidelines Figure 3.Top-Side Placement and RoutingFigure yer-Two Routing6TPS2554and TPS2555Evaluation ModuleSLVU462–June 2011Submit Documentation FeedbackCopyright ©2011,Texas Instruments Incorporated EVM Assembly Drawings and Layout Guidelinesyer-Three RoutingFigure6.Bottom-Side Placement and Routing7 SLVU462–June2011TPS2554and TPS2555Evaluation Module Submit Documentation FeedbackCopyright©2011,Texas Instruments IncorporatedEvaluation Board/Kit Important NoticeTexas Instruments(TI)provides the enclosed product(s)under the following conditions:This evaluation board/kit is intended for use for ENGINEERING DEVELOPMENT,DEMONSTRATION,OR EVALUATION PURPOSES ONLY and is not considered by TI to be a finished end-product fit for general consumer use.Persons handling the product(s)must have electronics training and observe good engineering practice standards.As such,the goods being provided are not intended to be complete in terms of required design-,marketing-,and/or manufacturing-related protective considerations, including product safety and environmental measures typically found in end products that incorporate such semiconductor components or circuit boards.This evaluation board/kit does not fall within the scope of the European Union directives regarding electromagnetic compatibility,restricted substances(RoHS),recycling(WEEE),FCC,CE or UL,and therefore may not meet the technical requirements of these directives or other related directives.Should this evaluation board/kit not meet the specifications indicated in the User’s Guide,the board/kit may be returned within30 days from the date of delivery for a full refund.THE FOREGOING WARRANTY IS THE EXCLUSIVE WARRANTY MADE BY SELLER TO BUYER AND IS IN LIEU OF ALL OTHER WARRANTIES,EXPRESSED,IMPLIED,OR STATUTORY,INCLUDING ANY WARRANTY OF MERCHANTABILITY OR FITNESS FOR ANY PARTICULAR PURPOSE.The user assumes all responsibility and liability for proper and safe handling of the goods.Further,the user indemnifies TI from all claims arising from the handling or use of the goods.Due to the open construction of the product,it is the user’s responsibility to take any and all appropriate precautions with regard to electrostatic discharge.EXCEPT TO THE EXTENT OF THE INDEMNITY SET FORTH ABOVE,NEITHER PARTY SHALL BE LIABLE TO THE OTHER FOR ANY INDIRECT,SPECIAL,INCIDENTAL,OR CONSEQUENTIAL DAMAGES.TI currently deals with a variety of customers for products,and therefore our arrangement with the user is not exclusive.TI assumes no liability for applications assistance,customer product design,software performance,or infringement of patents or services described herein.Please read the User’s Guide and,specifically,the Warnings and Restrictions notice in the User’s Guide prior to handling the product.This notice contains important safety information about temperatures and voltages.For additional information on TI’s environmental and/or safety programs,please contact the TI application engineer or visit /esh.No license is granted under any patent right or other intellectual property right of TI covering or relating to any machine,process,or combination in which such TI products or services might be or are used.FCC WarningThis evaluation board/kit is intended for use for ENGINEERING DEVELOPMENT,DEMONSTRATION,OR EVALUATION PURPOSES ONLY and is not considered by TI to be a finished end-product fit for general consumer use.It generates,uses,and can radiate radio frequency energy and has not been tested for compliance with the limits of computing devices pursuant to part15 of FCC rules,which are designed to provide reasonable protection against radio frequency interference.Operation of this equipment in other environments may cause interference with radio communications,in which case the user at his own expense will be required to take whatever measures may be required to correct this interference.EVM Warnings and RestrictionsIt is important to operate this EVM within the input voltage range of0V to5.5V and the output voltage range of0V to5.5V. Exceeding the specified input range may cause unexpected operation and/or irreversible damage to the EVM.If there are questions concerning the input range,please contact a TI field representative prior to connecting the input power.Applying loads outside of the specified output range may result in unintended operation and/or possible permanent damage to the EVM.Please consult the EVM User's Guide prior to connecting any load to the EVM output.If there is uncertainty as to the load specification,please contact a TI field representative.During normal operation,some circuit components may have case temperatures greater than85°C.The EVM is designed to operate properly with certain components above85°C as long as the input and output ranges are maintained.These components include but are not limited to linear regulators,switching transistors,pass transistors,and current sense resistors.These types of devices can be identified using the EVM schematic located in the EVM User's Guide.When placing measurement probes near these devices during operation,please be aware that these devices may be very warm to the touch.Mailing Address:Texas Instruments,Post Office Box655303,Dallas,Texas75265Copyright©2011,Texas Instruments IncorporatedIMPORTANT NOTICETexas Instruments Incorporated and its subsidiaries(TI)reserve the right to make corrections,modifications,enhancements,improvements, and other changes to its products and services at any time and to discontinue any product or service without notice.Customers should obtain the latest relevant information before placing orders and should verify that such information is current and complete.All products are sold subject to TI’s terms and conditions of sale supplied at the time of order acknowledgment.TI warrants performance of its hardware products to the specifications applicable at the time of sale in accordance with TI’s standard warranty.Testing and other quality control techniques are used to the extent TI deems necessary to support this warranty.Except where mandated by government requirements,testing of all parameters of each product is not necessarily performed.TI assumes no liability for applications assistance or customer product design.Customers are responsible for their products and applications using TI components.To minimize the risks associated with customer products and applications,customers should provide adequate design and operating safeguards.TI does not warrant or represent that any license,either express or implied,is granted under any TI patent right,copyright,mask work right, or other TI intellectual property right relating to any combination,machine,or process in which TI products or services are rmation published by TI regarding third-party products or services does not constitute a license from TI to use such products or services or a warranty or endorsement e of such information may require a license from a third party under the patents or other intellectual property of the third party,or a license from TI under the patents or other intellectual property of TI.Reproduction of TI information in TI data books or data sheets is permissible only if reproduction is without alteration and is accompanied by all associated warranties,conditions,limitations,and notices.Reproduction of this information with alteration is an unfair and deceptive business practice.TI is not responsible or liable for such altered rmation of third parties may be subject to additional restrictions.Resale of TI products or services with statements different from or beyond the parameters stated by TI for that product or service voids all express and any implied warranties for the associated TI product or service and is an unfair and deceptive business practice.TI is not responsible or liable for any such statements.TI products are not authorized for use in safety-critical applications(such as life support)where a failure of the TI product would reasonably be expected to cause severe personal injury or death,unless officers of the parties have executed an agreement specifically governing such use.Buyers represent that they have all necessary expertise in the safety and regulatory ramifications of their applications,and acknowledge and agree that they are solely responsible for all legal,regulatory and safety-related requirements concerning their products and any use of TI products in such safety-critical applications,notwithstanding any applications-related information or support that may be provided by TI.Further,Buyers must fully indemnify TI and its representatives against any damages arising out of the use of TI products in such safety-critical applications.TI products are neither designed nor intended for use in military/aerospace applications or environments unless the TI products are specifically designated by TI as military-grade or"enhanced plastic."Only products designated by TI as military-grade meet military specifications.Buyers acknowledge and agree that any such use of TI products which TI has not designated as military-grade is solely at the Buyer's risk,and that they are solely responsible for compliance with all legal and regulatory requirements in connection with such use. TI products are neither designed nor intended for use in automotive applications or environments unless the specific TI products are designated by TI as compliant with ISO/TS16949requirements.Buyers acknowledge and agree that,if they use any non-designated products in automotive applications,TI will not be responsible for any failure to meet such requirements.Following are URLs where you can obtain information on other Texas Instruments products and application solutions:Products ApplicationsAudio /audio Communications and Telecom /communicationsAmplifiers Computers and Peripherals /computersData Converters Consumer Electronics /consumer-appsDLP®Products Energy and Lighting /energyDSP Industrial /industrialClocks and Timers /clocks Medical /medicalInterface Security /securityLogic Space,Avionics and Defense /space-avionics-defense Power Mgmt Transportation and /automotiveAutomotiveMicrocontrollers Video and Imaging /videoRFID Wireless /wireless-appsRF/IF and ZigBee®Solutions /lprfTI E2E Community Home Page Mailing Address:Texas Instruments,Post Office Box655303,Dallas,Texas75265Copyright©2011,Texas Instruments Incorporated。
45971中文资料

FEATURES AND SPECIFICATIONS1.27 by 1.27mm (.050 by .050”) Pitch SEARAY* Connector 45970 Plug45971 ReceptacleSPECIFICATIONSn M olex’s unique and patented, solder- attach method is more cost effective and reliable than BGA attach methodsn D ata rates of up to 10Gbps have excellent signal clarity and large bandwidth for customer requirements in high-speed designsn F lexible tooling design with multiple stack heights and circuit sizes provides ease in tooling a new circuit size or stack-height version n P opular footprint is compatible with other products in the market: 1.27 by 1.27mm (.050 by .050”); and allows ease in multiple sourcing with other common productsn R obust contact design prevents stubbing and damage in mating interfaceFeatures and BenefitsThe SEARAY board-to-board connector is designed for applications with high pin-count devices or memory modules that are mounted on mezzanine or module PCBs. The unique, Molex-patented, solder-charge technology results in better process yields and a lower-applied cost versus equivalent Ball Grid Array (BGA) connector products. Solder-charge technology is a patented Molex process, which provides optimized PCB adhesion and immense mechanical retention force.The SEARAY connector provides numerous benefits. It allows customers to simplify PCB routing without sacrificing performance. Customers will avoid the expense of large, complex, multi-layer boards and utilize space better within a given card slot area. Option cards may be added or upgraded to increase flexibility in design, production and testing. The SEARAY connector design has superior electrical and mechanical features that are cost competitive. For additional information, please visit: / product/searay.html.Reference InformationProduct Specification: PS-45970-001Packaging: Tray UL File No.: TBD CSA File No.: TBD Designed in: InchesElectricalVoltage: 250V AC per contact Current: 1.0A per contactContact Resistance: 25 milliohms nominal Dielectric Withstanding Voltage: 500V DC Insulation Resistance: 5000 Megohms min.MechanicalMating Force: 50g max. per contact Un-mating Force: 30g max. per contact Normal Force: 82g max. per contact Durability: 100 cyclesPhysicalHousing: Glass-filled LCP , UL 94V-0Contact: Copper (Cu) Alloy Plating: Contact Area – 0.75µm Gold (Au) min. Solder Tail Area – 3.80µm Tin (Sn) min.U nderplating – 1.25µm Nickel (Ni) min. overall Operating Temperature: -55 to +105°CThe SEARAY connector accommodates low-profile applications with stack heights of 7.00 to 15.00mm (.276 to .591”) for the large and growing, high-density, high-performance mezzanine connector marketSEARAY mezzanine solutions pack many high-speed signals in very dense spaces with stack heights of 7.00 to 15.00mm(.276 to .591”)*SEARAY is a trademark of Samtec, Inc.Americas Headquarters Lisle, Illinois 60532 U.S.A.1-800-78MOLEX amerinfo@Asia Pacific North Headquarters Yamato, Kanagawa, Japan 81-462-65-2324feninfo@ Asia Pacific South Headquarters Jurong, Singapore 65-6268-6868fesinfo@ European Headquarters Munich, Germany 49-89-413092-0eurinfo@Corporate Headquarters 2222 Wellington Ct.Lisle, IL 60532 U.S.A.630-969-4550 Fax:630-969-1352Visit our website at /product/searay.htmlOrder No. 987650-0863Printed in USA/JI/2007.04©2007, Molex1.27 by 1.27mm (.050 by .050”) Pitch SEARAY* Connector 45970 Plug45971 ReceptacleAPPLICATIONSORDERING INFORMATIONn H igh and Mid-Range Computers - Servers n M edical- Scanning equipmentn M ilitary- Radar or topographical equipment n N etworking and Telecommunications - N etwork routers and switches - Mobile base stationsNotes1) Refer to the product sales drawing for mated stack-height options 2) Please contact inside sales for other circuit sizes and stack heights 3) Please contact inside sales for parts with Tin/Lead solder charges*SEARAY is a trademark of Samtec, Inc.SEARAY ReceptacleSEARAY PlugPlug Order No.CircuitsStack HeightReceptacle Order No.45970-91611147.00mm (.276”)45971-916145970-231120010.00mm (.393”)45971-231145970-31812407.00mm (.276”)45971-318145970-32133008.00mm (.314”)45971-311345970-31113007.00mm (.276”)45971-311345970-431140011.00mm (.433)45971-4411。
电闸说明书

Eaton 274199Eaton Moeller® series DILM Contactor, 380 V 400 V 265 kW, 2 N/O, 2 NC, 220 - 240 V 50/60 Hz, AC operation, Screw connection DILM500-S/22(220-240V50/60HZ)General specificationsEaton Moeller® series DILM Contactor 274199DILM500-S/22(220-240V50/60HZ)4015082741990216 mm 219 mm 160 mm 8.58 kg CSA Class No.: 3211-04 IEC/EN 60947-4-1UL Category Control No.: NLDX UL 60947-4-1 VDE 0660UL File No.: E29096 UL/CSACSA file No. 012528North America (UL listed, CSA certified) EN 45545: Fire protection on railway vehiclesIEC 61373: Vibration and shock, tested for category 1 class B CE markingProduct NameCatalog Number Model CodeEANProduct Length/Depth Product Height Product Width Product Weight CertificationsCatalog Notes Contacts according to EN 50012Also tested according to AC-3e up to 500 V.Also suitable for motors with efficiency class IE3.EN 45545 - Fire protection on railway vehicles: Fire protection class of all plastics according to UL94: V-0 /Fitting options auxiliary contacts: on the side: 2 x DILM820-XHI11(V)-SI; 2 x DILM820-XHI11-SAContactors for MotorsScrew terminalsIP00Designed for operation in industrial environments. Its use in residential environments may cause radio-frequency interference, requiring additional noise suppression.Suppressor circuit in actuating electronics100,000 Operations (at Condensor operation)7,000,000 Operations (AC operated)2000 mechanical Operations/h (AC operated)200 Operations/hIII3ContactorsFinger and back-of-hand proof with terminal shroud or terminal block, Protection against direct contact when actuated from front (EN 50274)8000 V AC500 mΩ (Admissible transitional contact resistance - of the external control circuit device when actuating A11)-40 °C60 °C40 °C40 °C40 °C80 °CDamp heat, cyclic, to IEC 60068-2-30Damp heat, constant, to IEC 60068-2-78Suppressor circuit in actuating electronics100,000 Operations (at Condensor operation)7,000,000 Operations (AC operated)2000 mechanical Operations/h (AC operated)200 Operations/hIII3ContactorsFinger and back-of-hand proof with terminal shroud or terminal block, Protection against direct contact when actuated from front (EN 50274)8000 V ACAccessoriesApplicationConnectionDegree of protectionElectromagnetic compatibilityFitted with:Lifespan, electricalLifespan, mechanicalOperating frequencyOvervoltage categoryPollution degreeProduct categoryProtectionRated impulse withstand voltage (Uimp) Resistance Ambient operating temperature - minAmbient operating temperature - maxAmbient operating temperature (enclosed) - min Ambient operating temperature (enclosed) - max Ambient storage temperature - minAmbient storage temperature - maxClimatic proofingFitted with:Lifespan, electricalLifespan, mechanicalOperating frequencyOvervoltage categoryPollution degreeProduct categoryProtectionRated impulse withstand voltage (Uimp)8 g, N/C auxiliary contact, Mechanical, according to IEC/EN 60068-2-27, Half-sinusoidal shock 10 ms10 g, N/O auxiliary contact, Mechanical, according to IEC/EN 60068-2-27, Half-sinusoidal shock 10 ms10 g, N/O main contact, Mechanical, according to IEC/EN 60068-2-27, Half-sinusoidal shock 10 msAC-3: Normal AC induction motors: starting, switch off during runningAC-1: Non-inductive or slightly inductive loads, resistance furnacesAC-4: Normal AC induction motors: starting, plugging, reversing, inching 500 mΩ (Admissible transitional contact resistance - of the external control circuit device when actuating A11)8 g, N/C auxiliary contact, Mechanical, according to IEC/EN 60068-2-27, Half-sinusoidal shock 10 ms10 g, N/O auxiliary contact, Mechanical, according to IEC/EN 60068-2-27, Half-sinusoidal shock 10 ms10 g, N/O main contact, Mechanical, according to IEC/EN 60068-2-27, Half-sinusoidal shock 10 msAC-3: Normal AC induction motors: starting, switch off during runningAC-1: Non-inductive or slightly inductive loads, resistance furnacesAC-4: Normal AC induction motors: starting, plugging, reversing, inching30 mm width, Main connectionFixing with flat cable terminal or cable terminal blocks; See terminal capacity for cable terminal blocks50 - 240 mm²1 x (0.75 - 2.5) mm², Control circuit cables2 x (0.75 - 2.5) mm², Control circuit cables2 x (0.75 - 2.5) mm², Control circuit cables1 x (0.75 - 2.5) mm², Control circuit cables18 - 14, Control circuit cables2/0 - 500 MCM, Main cables70 - 240 mm²16 mm Max. 30 x Ie (peak)5000 A5000 A5000 A5000 A950 A1000 V5500 A177 A at 690 V (Individual compensation, three-phase capacitors, open)307 A at up to 525 V (Individual compensation, three-phase capacitors, open)Shock resistance Utilization category ResistanceShock resistance Utilization categoryTerminal capacity (busbar)Terminal capacity (copper band) Terminal capacity (flexible with cable lug) Terminal capacity (flexible with ferrule) Terminal capacity (solid)Terminal capacity (solid/stranded AWG) Terminal capacity (stranded with cable lug) Width across flatsScrew size Inrush currentRated breaking capacity at 220/230 VRated breaking capacity at 380/400 VRated breaking capacity at 500 VRated breaking capacity at 660/690 VRated breaking capacity at 1000 VRated insulation voltage (Ui)Rated making capacity (cos phi to IEC/EN 60947) Rated operational current (Ie)M3.5, Terminal screw, Control circuit cablesM10, Terminal screw, Main connections2, Terminal screw, Control circuit cables, Pozidriv screwdriver1.2 Nm, Screw terminals, Control circuit cables24 Nm, Main cable connection screw/bolt 800 A 500 A 500 A 500 A 500 A 325 A 95 A 360 A 360 A 360 A 260 A 95 A 170 kW 250 kW 290 kW 132 kW 112 kW 122 kWScrewdriver size Tightening torque Rated operational current (Ie) at AC-1, 380 V, 400 V, 415 V Rated operational current (Ie) at AC-3, 220 V, 230 V, 240 V Rated operational current (Ie) at AC-3, 380 V, 400 V, 415 V Rated operational current (Ie) at AC-3, 440 VRated operational current (Ie) at AC-3, 500 VRated operational current (Ie) at AC-3, 660 V, 690 V Rated operational current (Ie) at AC-3, 1000 VRated operational current (Ie) at AC-4, 220 V, 230 V, 240 V Rated operational current (Ie) at AC-4, 440 VRated operational current (Ie) at AC-4, 500 VRated operational current (Ie) at AC-4, 660 V, 690 V Rated operational current (Ie) at AC-4, 1000 VRated operational power at AC-3, 240 V, 50 HzRated operational power at AC-3, 380/400 V, 50 HzRated operational power at AC-3, 415 V, 50 HzRated operational power at AC-3, 1000 V, 50 HzRated operational power at AC-4, 220/230 V, 50 HzRated operational power at AC-4, 240 V, 50 HzRated operational power at AC-4, 415 V, 50 Hz216 kW 229 kW250 kW240 kW1000 V132 kW1000 V AC, Between coil and contacts, According to EN 611403900 A, LRA 480 V 60 Hz 3-ph, 100,000 cycles acc. to UL 1995, (UL/CSA)635 A, FLA 480 V 60 Hz 3-ph, 100,000 cycles acc. to UL 1995, (UL/CSA)3120 A, LRA 600 V 60 Hz 3-ph, 100,000 cycles acc. to UL 1995, (UL/CSA)520 A, FLA 600 V 60 Hz 3-ph, 100,000 cycles acc. to UL 1995, (UL/CSA)600 A, max. CB, SCCR (UL/CSA)30 kA, SCCR (UL/CSA)800 A, max. Fuse, SCCR (UL/CSA)30/100 kA, Fuse, SCCR (UL/CSA)100 kA, CB, SCCR (UL/CSA)800/600 A, Class J, max. Fuse, SCCR (UL/CSA)600 A, max. CB, SCCR (UL/CSA)600 A, max. CB, SCCR (UL/CSA)800/600 A, Class J, max. Fuse, SCCR (UL/CSA)30/100 kA, Fuse, SCCR (UL/CSA)30 kA, CB, SCCR (UL/CSA)250 A gG/gL630 A gG/gL630 A gG/gL200 A gG/gL500 A gG/gL500 A gG/gL177 A at 690 V (Individual compensation, three-phase capacitors, open)307 A at up to 525 V (Individual compensation, three-phase capacitors, open)800 A500 A500 ARated operational power at AC-4, 440 V, 50 HzRated operational power at AC-4, 500 V, 50 Hz Rated operational power at AC-4, 660/690 V, 50 Hz Rated operational voltage (Ue) at AC - maxRated operational power at AC-4, 1000 V, 50 Hz Safe isolationSpecial purpose rating of definite purpose rating Short-circuit current rating (basic rating)Short-circuit current rating (high fault at 480 V)Short-circuit current rating (high fault at 600 V)Short-circuit protection rating (type 1 coordination) at 1000 V Short-circuit protection rating (type 1 coordination) at 400 V Short-circuit protection rating (type 1 coordination) at 690 V Short-circuit protection rating (type 2 coordination) at 1000 V Short-circuit protection rating (type 2 coordination) at 400 V Short-circuit protection rating (type 2 coordination) at 690 V Rated operational current (Ie)Rated operational current (Ie) at AC-1, 380 V, 400 V, 415 V Rated operational current (Ie) at AC-3, 220 V, 230 V, 240 V Rated operational current (Ie) at AC-3, 380 V, 400 V, 415 V500 A500 A 325 A 95 A 360 A 360 A 360 A 260 A 95 A 170 kW 250 kW 290 kW 132 kW 112 kW 122 kW 216 kW 229 kW 250 kW 1500 A600 A682 A1625 A630 A gG/gL630 A gG/gL200 A gG/gL500 A gG/gL500 A gG/gL550 A, Maximum motor rating (UL/CSA)1 A, 250 V DC, (UL/CSA)15 A, 600 V AC, (UL/CSA)P300, DC operated (UL/CSA)A600, AC operated (UL/CSA)1625 ASealing - Pick-up phase (0 - 0.7 x Uc min: Contactor does not switch onRated operational current (Ie) at AC-3, 440 VRated operational current (Ie) at AC-3, 500 VRated operational current (Ie) at AC-3, 660 V, 690 V Rated operational current (Ie) at AC-3, 1000 VRated operational current (Ie) at AC-4, 220 V, 230 V, 240 V Rated operational current (Ie) at AC-4, 440 VRated operational current (Ie) at AC-4, 500 VRated operational current (Ie) at AC-4, 660 V, 690 V Rated operational current (Ie) at AC-4, 1000 VRated operational power at AC-3, 240 V, 50 HzRated operational power at AC-3, 380/400 V, 50 HzRated operational power at AC-3, 415 V, 50 HzRated operational power at AC-3, 1000 V, 50 HzRated operational power at AC-4, 220/230 V, 50 HzRated operational power at AC-4, 240 V, 50 HzRated operational power at AC-4, 415 V, 50 HzRated operational power at AC-4, 440 V, 50 HzRated operational power at AC-4, 500 V, 50 HzRated operational power at AC-4, 660/690 V, 50 Hz Conventional thermal current ith (1-pole, enclosed) Conventional thermal current ith (3-pole, enclosed) Conventional thermal current ith at 55°C (3-pole, open) Conventional thermal current ith of main contacts (1-pole, open) Short-circuit protection rating (type 1 coordination) at 400 V Short-circuit protection rating (type 1 coordination) at 690 V Short-circuit protection rating (type 2 coordination) at 1000 V Short-circuit protection rating (type 2 coordination) at 400 V Short-circuit protection rating (type 2 coordination) at 690 VSwitching capacity (main contacts, general use)Switching capacity (auxiliary contacts, general use)Switching capacity (auxiliary contacts, pilot duty) Conventional thermal current ith of main contacts (1-pole, open) Behavior in marginal and transitional conditions240 kW1000 V132 kW1000 V AC, Between coil and contacts, According to EN 611403900 A, LRA 480 V 60 Hz 3-ph, 100,000 cycles acc. to UL 1995, (UL/CSA)635 A, FLA 480 V 60 Hz 3-ph, 100,000 cycles acc. to UL 1995, (UL/CSA)3120 A, LRA 600 V 60 Hz 3-ph, 100,000 cycles acc. to UL 1995, (UL/CSA)520 A, FLA 600 V 60 Hz 3-ph, 100,000 cycles acc. to UL 1995, (UL/CSA)Sealing - Voltage drops (0.6 - 0.7 x Uc min: Contactor remains switched onSealing - Excess voltage (1.15 - 1.3 x Uc max): Contactor remains switched onSealing - Pick-up phase (0.7 x Uc min - 1.15 x Uc max): Contactor switches on with certaintySealing - Voltage drops (0.2 - 0.6 x Uc min ≤12 ms: Time is bridged successfullySealing - Voltage drops (0.2 - 0.6 x Uc min) > 12 ms: Drop-out of the contactorSealing - Voltage interruptions (0 - 0.2 x Uc min ≤ 10 ms: Time is bridged successfullySealing - Voltage interruptions 0 - 0.2 x Uc min) > 10 ms: Drop-out of the contactorAC operated: 0.2 x US max - 0.4 x US min, AC operatedAC operated: 0.25 x US max - 0.6 x US min, AC operated100 %0.85 - 1.1 V AC x UsControl transformer with uk ≤ 10%715 VA, Pull-in power, Coil in a cold state and 1.0 x Us645 W, Pull-in power, Coil in a cold state and 1.0 x Us715 VA, Pull-in power, Coil in a cold state and 1.0 x Us645 W, Pull-in power, Coil in a cold state and 1.0 x Us4 W, Coil in a cold state and 1.0 x Us6.8 VA, Coil in a cold state and 1.0 x Us4 W, Coil in a cold state and 1.0 x Us6.8 VA, Coil in a cold state and 1.0 x Us220 V240 V220 VRated operational voltage (Ue) at AC - maxRated operational power at AC-4, 1000 V, 50 HzSafe isolationSpecial purpose rating of definite purpose ratingDrop-out voltageDuty factorPick-up voltagePower consumptionPower consumption, pick-up, 50 HzPower consumption, pick-up, 60 HzPower consumption, sealing, 50 HzPower consumption, sealing, 60 HzRated control supply voltage (Us) at AC, 50 Hz - minRated control supply voltage (Us) at AC, 50 Hz - maxRated control supply voltage (Us) at AC, 60 Hz - min240 V0 V0 V 55 ms 50 ms 150 HP200 HP400 HP500 HPControl transformer with uk ≤ 10%715 VA, Pull-in power, Coil in a cold state and 1.0 x Us 645 W, Pull-in power, Coil in a cold state and 1.0 x Us715 VA, Pull-in power, Coil in a cold state and 1.0 x Us 645 W, Pull-in power, Coil in a cold state and 1.0 x Us4 W, Coil in a cold state and 1.0 x Us6.8 VA, Coil in a cold state and 1.0 x Us4 W, Coil in a cold state and 1.0 x Us6.8 VA, Coil in a cold state and 1.0 x Us220 V240 V220 V240 V0 V0 V55 msRated control supply voltage (Us) at AC, 60 Hz - maxRated control supply voltage (Us) at DC - minRated control supply voltage (Us) at DC - maxSwitching time (AC operated, make contacts, closing delay) - maxSwitching time (AC operated, make contacts, opening delay) - max Assigned motor power at 200/208 V, 60 Hz, 3-phase Assigned motor power at 230/240 V, 60 Hz, 3-phase Assigned motor power at 460/480 V, 60 Hz, 3-phase Assigned motor power at 575/600 V, 60 Hz, 3-phasePower consumptionPower consumption, pick-up, 50 HzPower consumption, pick-up, 60 HzPower consumption, sealing, 50 HzPower consumption, sealing, 60 HzRated control supply voltage (Us) at AC, 50 Hz - minRated control supply voltage (Us) at AC, 50 Hz - maxRated control supply voltage (Us) at AC, 60 Hz - minRated control supply voltage (Us) at AC, 60 Hz - maxRated control supply voltage (Us) at DC - minRated control supply voltage (Us) at DC - maxSwitching time (AC operated, make contacts, closing delay) - max50 ms22220 W0 W19.33 W500 A3.3 WMeets the product standard's requirements.Meets the product standard's requirements.Meets the product standard's requirements.Meets the product standard's requirements.Meets the product standard's requirements.Does not apply, since the entire switchgear needs to be evaluated.0 W0 W19.33 W500 A3.3 WMeets the product standard's requirements.Meets the product standard's requirements.Meets the product standard's requirements.Meets the product standard's requirements.Meets the product standard's requirements.Does not apply, since the entire switchgear needs to be evaluated.Switching time (AC operated, make contacts, opening delay) -maxNumber of auxiliary contacts (normally closed contacts)Number of auxiliary contacts (normally open contacts)Number of contacts (normally closed contacts)Number of contacts (normally open contacts)Equipment heat dissipation, current-dependent PvidHeat dissipation capacity PdissHeat dissipation per pole, current-dependent PvidRated operational current for specified heat dissipation (In) Static heat dissipation, non-current-dependent Pvs10.2.2 Corrosion resistance10.2.3.1 Verification of thermal stability of enclosures10.2.3.2 Verification of resistance of insulating materials to normal heat10.2.3.3 Resist. of insul. mat. to abnormal heat/fire by internal elect. effects10.2.4 Resistance to ultra-violet (UV) radiation10.2.5 Lifting Equipment heat dissipation, current-dependent PvidHeat dissipation capacity PdissHeat dissipation per pole, current-dependent PvidRated operational current for specified heat dissipation (In) Static heat dissipation, non-current-dependent Pvs10.2.2 Corrosion resistance10.2.3.1 Verification of thermal stability of enclosures10.2.3.2 Verification of resistance of insulating materials to normal heat10.2.3.3 Resist. of insul. mat. to abnormal heat/fire by internal elect. effects10.2.4 Resistance to ultra-violet (UV) radiation10.2.5 LiftingDoes not apply, since the entire switchgear needs to be evaluated.Meets the product standard's requirements.Does not apply, since the entire switchgear needs to be evaluated.Meets the product standard's requirements.Does not apply, since the entire switchgear needs to be evaluated.Does not apply, since the entire switchgear needs to be evaluated.Is the panel builder's responsibility.Is the panel builder's responsibility.Is the panel builder's responsibility.Is the panel builder's responsibility.Is the panel builder's responsibility.The panel builder is responsible for the temperature rise calculation. Eaton will provide heat dissipation data for the devices.Is the panel builder's responsibility. The specifications for the switchgear must be observed.Is the panel builder's responsibility. The specifications for the switchgear must be observed.The device meets the requirements, provided the information in the instruction leaflet (IL) is observed.Does not apply, since the entire switchgear needs to be evaluated.Meets the product standard's requirements.Does not apply, since the entire switchgear needs to be evaluated.Meets the product standard's requirements.Does not apply, since the entire switchgear needs to be evaluated.Does not apply, since the entire switchgear needs to be evaluated.Is the panel builder's responsibility.Is the panel builder's responsibility.Is the panel builder's responsibility.Is the panel builder's responsibility.Is the panel builder's responsibility.The panel builder is responsible for the temperature rise calculation. Eaton will provide heat dissipation data for the devices.Is the panel builder's responsibility. The specifications for the switchgear must be observed.Is the panel builder's responsibility. The specifications for the switchgear must be observed.The device meets the requirements, provided the information in the instruction leaflet (IL) is observed.10.2.6 Mechanical impact10.2.7 Inscriptions10.3 Degree of protection of assemblies10.4 Clearances and creepage distances10.5 Protection against electric shock10.6 Incorporation of switching devices and components 10.7 Internal electrical circuits and connections10.8 Connections for external conductors10.9.2 Power-frequency electric strength10.9.3 Impulse withstand voltage10.9.4 Testing of enclosures made of insulating material 10.10 Temperature rise10.11 Short-circuit rating10.12 Electromagnetic compatibility10.13 Mechanical function 10.2.6 Mechanical impact10.2.7 Inscriptions10.3 Degree of protection of assemblies10.4 Clearances and creepage distances10.5 Protection against electric shock10.6 Incorporation of switching devices and components 10.7 Internal electrical circuits and connections10.8 Connections for external conductors10.9.2 Power-frequency electric strength10.9.3 Impulse withstand voltage10.9.4 Testing of enclosures made of insulating material 10.10 Temperature rise10.11 Short-circuit rating10.12 Electromagnetic compatibility10.13 Mechanical functionBrochuresBrochure - Safe switching of high currents. DILM and DILH contactors CataloguesProduct Range Catalog Switching and protecting motorsSwitching and protecting motors - catalogCharacteristic curveeaton-contactors-short-time-loading-dilm-characteristic-curve-002.eps eaton-contactors-component-dilm-characteristic-curve-002.eps eaton-contactors-component-dilm-characteristic-curve-003.eps eaton-contactors-component-dilm-characteristic-curve.eps Declarations of conformityDA-DC-00004804.pdfDA-DC-00004796.pdfDrawingseaton-contactors-mounting-dilm-dimensions-002.epseaton-contactors-mounting-dilm-dimensions.epseaton-contactors-dilm-dimensions-009.epseaton-contactors-mounting-dilm-3d-drawing-002.epseaton-contactors-dilm-3d-drawing-005.epseCAD modelDA-CE-ETN.DILM500-S_22(220-240V50_60HZ)Installation instructionsIL03406005ZmCAD modelDA-CD-dil_m500_570DA-CS-dil_m500_570System overvieweaton-contactors-system55-dilm-explosion-drawing.epsWiring diagramseaton-contactors-contact-dilm-wiring-diagram-004.epsEaton Corporation plc Eaton House30 Pembroke Road Dublin 4, Ireland © 2023 Eaton. All rights reserved. Eaton is a registered trademark.All other trademarks areproperty of their respectiveowners./socialmedia。
CP45 12254.5. Control System Specifications(-)

1.5. Control System SpecificationsEmbedded in the CP-45F/V NEO and the CP-45FS NEO is a high-speed CPU thatprovides the production and production management information of PCB, and isdesignated for creating and editing the production program as well. The system operationcan reading be learned by using the MMI based on Windows 98.production1.5.1. PCBProgram selectionThe CP-45F/V NEO and the 45FS NEO has large-capacity hard disk (over 10.2 GB).Data can also be stored in a 3.5-inch floppy disk. The user can store the program ordata either in a hard disk or a floppy disk.Continuous production of PCBThe number of completed PCB's produced is shown on the screen while PCB's arebeing produced. The number of PCB's to be produced and the number of componentsto be placed can be inputted, and the number of PCB's currently being produced onthe production management page can be shown on the screen.Test driving functionsThe correct coordinates of a component position can be obtained by temporarilyplacing the component and inputting the correct coordinates through a teaching boxby tracking the position with a camera. In this case, the coordinates are adjustedrelative to each other.Production management informationThe CP-45F/V NEO and the CP-45FS NEO provides the following basic productionmanagement information:Number of completed PCB'sOperating time (actual running time)Stop timeNumber of successfully placed componentsNumber of bad-marked PCB'sNumber of components supplied from each feeder1.5.2. Creation and editing of production programThe production program (Man-Machine Interface, MMI) is composed of the following data parts:PCB data: data related to PCBPlacement data: data on the components to be placed on PCB including theirpositions (coordinates)Component data: data related to the components Feed data: data related to the feederVision data: data related to vision recognition1.5.3. Input/Output device 1.5.3.1. KeyboardThe CP-45F/V NEO and the CP-45FS NEO has keyboard on the upper position of the cover. They are used for operating Window 98 and creating and editing data on MMI.1.5.3.2. Teaching boxA teaching box is used for teaching the pickups position or placement position. The box has a switch for selecting an object for teaching, X-Y control button, up-and-down motion button along the Z-axis, and a rotation button. These switches and buttons are arranged individually on the teaching box, and there is an LED for indicating the buttonWarningDuring teaching, the operator or people near the operator could be injured due to operation error or insufficient checking of surroundings.Before start teaching, check the device to teach one more time, and check whether there is any worker near the machine.presently being used. For more detailed description on the operation of the teaching box, please refer to “3.3 Button Manipulation of Teaching Box (page 3-4)”.1.5.3.3. MouseThe mouse facilitates the operation of Windows and MMI.1.5.3.4. MonitorThe CP-45F/V NEO and the CP-45FV NEO has a color monitor for showing how the production program is created and edited and how the system is operated.Also the CP-45F/V NEO and the CP-45FV NEO has color monitors for camera teaching.1.5.4. Number of data that can be handled by MMINumber of steps placed: 3,000 Step (maximum)Number of programs PCB production: more than 1,000 (maximum) Number of component data: 200 (maximum) Number of feeder dataTape Feeders: 104 Stick Feeders: 100 Lane Matrix Tray Feeder: 3Number of component marks: 2 per component Number of PCB marks: 2 per componentCautionIf two monitors are placed side by side, the life span of monitors could be affected.Leave an interval of 30 cm or more between two monitors.1.5.5. Connections with peripheral units 1.5.5.1.Signals and interfaceTable 1-6. Signals and Interface SignalItemSpecificationsRemark PIN No.1: (+)Input SignalLess than 24 V/10mA Busy Input(In)PIN No.2: (-)Ground PIN No.3: Contact output Board Available Output(Out) PIN No.4: Contact outputAMP 206043-1Machine Side From Next M/CConnector AMP 206044-1External Connection PIN No.1: Contact output BusyOutput(Out)PIN No.2: Contact output PIN No.3: (+) Input Signal Less than 24 V/10mA Board AvailableInput(In)PIN No.4: (-)Ground AMP 206043-1 Machine Side In-LineSignalFromPerviousM/C ConnectorAMP 206044-1External ConnectionFigure 1-4. Interface1.5.5.2. ConnectorsSocket for tray feeder: 25 pin D-sub Socket for RS232C: 25 pin D-sub Socket for printer: 25 pin D-sub Teaching box connector: HR10A-7R-6S Connector for ANC: 6 pin round typeConnector for stick feeder: 4 pin round typeConnector for stage visionCamera: 12 pin round typeIllumination: 6 pin round typeConnector for auxiliary device interface: HR10A-7R-6S Connector for LAN: RJ-45 jackConnector for MODEM: RJ-11 jack。
CP45 12272.2. Standards for Lighting Signal Tower(-)

Panel Operations EMG (Emergency Stop) switchThis is an emergency stop switch. Operation of this equipment is immediatelysuspended if this switch is pressed in case of an emergency. Supply of all powersexcept for the power to a computer is ceased. The emergency stop status can bereleased by turning the <EMG> switch in the direction of the arrow and pressing the<Stop> and <Reset> switch.3.2. Standards for Lighting Signal TowerThis equipment comes with a signal tower for indicating the present status of theequipment. The signal tower indicates the following:Lighting of a red lampIndicates the stop status through self-diagnosis of the system. Warning sounds ringcontinuously and messages are indicated as the red lamp is lighted.Flashing of a red lampIndicates either the pressing of the <EMG> switch or the emergency stop statusthrough self-diagnosis of the system. Warning sounds ring continuously andmessages are indicated as the red lamp is flashed.Lighting of a blue lampIndicates the standby status of operation.Flashing of a blue lampIndicates either component shortage in the tray feeder or adsorption error. Warningsounds ring continuously and messages are indicated as the yellow lamp is flashed.Lighting of a green lampIndicates that this equipment is currently being operated automatically.Flashing of a green lampIndicates temporary stop status. Automatic operation can be resumed by pressing the<Start> switch.3-3Samsung Component Placer CP-45F(V) NEO /CP-45FS NEO Operations Manual3-4Figure 3-2. Signal Tower3.3. ButtonManipulation of Teaching BoxA teaching box is used for manipulating the head, or returning to the original position. Ateaching box also can be used only when the yellow lamp in the signal tower. The buttonson the teaching box are explained below:Figure 3-3. Teaching Box。
CP45错误信息中英文对照表
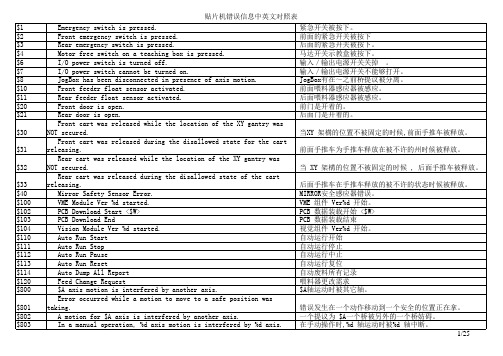
保护它! 7接口防静电保护器说明书

SpecificationsProtect It! 7-Outlet Surge Protector, 6 Right-Angle Outlets, 4 ft. (1.22 m) Cord, 1080 Joules,Diagnostic LED, Black HousingMODEL NUMBER: TLP74RBSafeguard your computer, printer, scanner, router, modem and other small home electronics against dangerous surges, spikes and line noise. Recommended for any desktop, network or home application requiring AC line protection.Features1080-Joule Surge Protection for Home or Office Electronics Protects your computer, printer, scanner,router, modem and other small home electronics against surges and spikesRecommended for anydesktop, network or home electronics application requiring AC line protectionFull normal mode (H-N) and common mode (N-G/H-G) line surge suppressionFilters out disruptive EMI/RFI line noise that can cause equipment damage or data lossExceeds IEEE 587 Category A and B surge suppression specifications 7 Outlets Accept Wide Range of Electronic Devices 6 NEMA 5-15R AC outlets placed at a right angle to simplify cord managementSpecial end outlet designed for bulky transformers without blocking other outletsPremium Safety Features Lighted on/off switch provides one-touch control over connectedequipmentAutomatic shutoff permanently cuts power to outlets if protection circuit is incapacitated,preventing equipment damage and indicating replacement is requiredDiagnostic LED confirms protection status at a glanceConforms to current UL 1449 3rd Edition safety standardsFits Effortlessly Into Your Workstation 4-ft. (1.22 m) AC power cord with NEMA 5-15P plug reaches nearby outletsKeyhole slots on bottom panel provide convenient wall or desk mounting optionsBlack plastic housing designed for long lifeBacked by Ultimate Lifetime Insurance $25,000 Ultimate Lifetime Insurance covers any connected components damaged by power surge (U.S., Canada and Puerto Rico only)Highlights6 right-angle NEMA 5-15R outlets (7 total)q1080-joule surge protection ratingqFilters out threatening EMI/RFI line noiseq15A resettable circuit breaker prevents dangerous overloads q4 ft. AC power cord with NEMA 5-15P plugqPackage IncludesTLP74RB Protect It! 7-Outlet Surge Protector, Black Housing qOwner’s manualq© 2023 Eaton. All Rights Reserved. Eaton is a registered trademark. All other trademarks are the property of their respective owners.。
NetDirector USB Server Interface Unit(B055-001-USB

SpecificationsNetDirector USB Server Interface Unit (B064-Series)MODEL NUMBER: B055-001-USBDescriptionThis USB Server Interface Unit connects a USB server to a B064-Series NetDirector® KVM switch using Cat5e/6 cabling. Use of Cat5e/6 cables frees up space in server cabinets that would otherwise be filled by traditional, bulkier KVM cable kits. Compliant with the Federal Trade Agreements Act (TAA) for GSA Schedule purchases.Note: SIU's that were purchased prior to that of your KVM switch may require a firmware upgrade in order for them to work properly (see Maintenance under OSD Operation section of your B064-Series KVM Owner's Manual for details)FeaturesEliminates the need for thicker, heavier KVM cable kits q Compact, lightweight design q Plug and Play; no software required q No power supply requiredq 164 ft. (50 m.) distance from KVM switchq Compliant with the Federal Trade Agreements Act (TAA) for GSA Schedule purchasesqNote: Support documentation for the B055-001-USB is under the B064 series, as this is an accessory for those models.HighlightsNeeded to connect a USB server to a B064-Series NetDirector KVM switch via Cat5e/6 cableqEasy to install; no software neededqAllows a maximum distance of 164 ft. (50 m.) from KVM to server via Cat5e/6 cable qCompact and lightweight design q Compliant with the FederalTrade Agreements Act (TAA) for GSA Schedule purchasesqSystem RequirementsServer or CPU with a HD15connector and USB type A connectorqA B064-Series NetDirector Cat5KVM Switch qCat5e/6 cableqPackage Includes1 USB Server Interface Unitq© 2023 Eaton. All Rights Reserved. Eaton is a registered trademark. All other trademarks are the property of their respective owners.。
毛萨CP-104EL-A系列4口RS-232 PCI Express串口板特点与功能说明书

CP-104EL-A Series4-port RS-232PCI Express serial boardsFeatures and Benefits•PCI Express1.0compliant•921.6kbps maximum baudrate for fast data transmission•128-byte FIFO and on-chip H/W,S/W flow control•Low-profile form factor fits small-sized PCs•Drivers provided for a broad selection of operating systems,includingWindows,Linux,and UNIX•Easy maintenance with built-in LEDs and management softwareCertificationsIntroductionThe CP-104EL-A is a smart,4-port PCI Express board designed for POS and ATM applications.It is a top choice of industrial automation engineers and system integrators,and supports many different operating systems,including Windows,Linux,and even UNIX.In addition,each of the board’s 4RS-232serial ports supports a fast921.6kbps baudrate.The CP-104EL-A provides full modem control signals to ensure compatibility with a wide range of serial peripherals,and its PCI Express x1classification allows it to be installed in any PCI Express slot.Smaller Form FactorThe CP-104EL-A is a low-profile board that is compatible with any PCI Express slot.The board requires only a3.3VDC power supply,which means that the board fits any host computer,ranging from shoebox to standard-sized PCs.Drivers Provided for Windows,Linux,and UNIXMoxa continues to support a wide variety of operating systems,and the CP-104EL-A board is no exception.Reliable Windows and Linux/UNIX drivers are provided for all Moxa boards,and other operating systems,such as WEPOS,are also supported for embedded integration.SpecificationsSerial InterfaceComm.Controller16C550C compatibleBus PCI Express1.0Connector DB44femaleFIFO128bytesMax.No.of Boards per PC8No.of Ports4Serial Standards RS-232Baudrate50bps to921.6kbps(supports non-standard baudrates)Data Bits5,6,7,8Stop Bits1,1.5,2Parity None,Even,Odd,Space,MarkFlow Control None,RTS/CTS,XON/XOFFSerial SignalsRS-232TxD,RxD,RTS,CTS,DTR,DSR,DCD,GNDSerial Software FeaturesLinux Drivers Linux kernel2.4.x,Linux kernel2.6.x,Linux kernel3.x,Linux kernel4.x,Linux kernel5.x Windows Drivers DOS,Windows95/98/ME/NT/2000,Windows XP/2003/Vista/2008/7/8/8.1/10(x86/x64),Windows2008R2/2012/2012R2/2016/2019(x64),Windows Embedded CE5.0/6.0,Windows XP EmbeddedUNIX Drivers QNX6,Solaris10,UnixWare7,SCO OpenServer5,SCO OpenServer6Power ParametersInput Current805mA@3.3VDCPhysical CharacteristicsDimensions67.21x103mm(2.65x4.06in)LED InterfaceLED Indicators Built-in Tx,Rx LEDs for each portEnvironmental LimitsOperating Temperature0to55°C(32to131°F)Storage Temperature(package included)-20to85°C(-4to185°F)Ambient Relative Humidity5to95%(non-condensing)Standards and CertificationsEMC EN55032/35EMI CISPR32,FCC Part15B Class BEMS IEC61000-4-2ESD:Contact:4kV;Air:8kVIEC61000-4-3RS:80MHz to1GHz:3V/mIEC61000-4-4EFT:Power:1kV;Signal:0.5kVIEC61000-4-5Surge:Power:2kVIEC61000-4-6CS:150kHz to80MHz:3V/m;Signal:3V/mIEC61000-4-8PFMFDeclarationGreen Product RoHS,CRoHS,WEEEMTBFTime3,601,447hrsStandards Telcordia(Bellcore)Standard TR/SRWarrantyWarranty Period5yearsDetails See /warrantyPackage ContentsDevice1x CP-104EL-A Series serial boardCable1x M44to4x DB9-M cable,50cm(CP-104EL-A-DB9M)1x M44to4x DB25-M cable,50cm(CP-104EL-A-DB25M)Documentation1x quick installation guide1x warranty cardDimensionsOrdering InformationModel Name Serial Standards No.of Serial Ports Included CableCP-104EL-A-DB25M RS-2324CBL-M44M25x4-50 CP-104EL-A-DB9M RS-2324CBL-M44M9x4-50 Accessories(sold separately)CablesCBL-M44M9x4-50DB44male to DB9male serial cable,50cmCBL-M44M25x4-50M44to4x DB25male serial cable,50cmCBL-F9M9-150DB9female to DB9male serial cable,1.5mCBL-F9M9-20DB9female to DB9male serial cable,20cm©Moxa Inc.All rights reserved.Updated Sep16,2021.This document and any portion thereof may not be reproduced or used in any manner whatsoever without the express written permission of Moxa Inc.Product specifications subject to change without notice.Visit our website for the most up-to-date product information.。
合福850封口机说明书

4.1 故障排除清单 .................................................................................................................................................18 4.2 错误信息 .........................................................................................................................................................20 4.3 客户服务部 .....................................................................................................................................................20 4.4 维修/校准 ........................................................................................................................................................20 4.5 备件服务部 .....................................................................................................................................................21 4.6 备件订购 – 商品代码归类..............................................................................................................................24 4.7 更换磨损件和备件的说明..............................................................................................................................25 4.8 调整过程参数设置与打印机设置..................................................................................................................29
Compact Circuit Protector UL Class CC数据手册说明书

UL Class CC, Midget and IEC 10x38 fusesSpecifications:•Box Lug and Spade Terminal suitable for line, load or accessory connection •Box Lug Connection:- 18-6 AWG (1 to 16mm 2) single or dual rated, solid or stranded – 75°C or higher - Cu only- 4 AWG (25mm 2) single – 75°C or higher - Cu only •Spade Terminal Connection:- Max. 30A suitable for use with #8-32 UNC (M4) screw •Torque:- 18-10 AWG 20 Lb-In (1-6mm 2/3.4Nm)- 8-4 AWG 35 Lb-In (10-25mm 2/5.8Nm)•Lockout/tagout: 4mm shank lock or standard pin-out devices •35mm DIN rail mount•Dimensionally compliant to DIN 43880•Local indication minimum operating voltage:– 90Vac for AC version – 12Vdc for DC versionAgency Information:UL Class CC fuse version• UL 98 Listed, File E302370, Guide WHTY• cULus to CSA Standard 22.2 No. 4-04, File 302370, Guide WHTY7• CE CompliantUL Midget fuse version • UL 508 Listed• cULus Certified 22.2 No. 14-05• CE Compliant10X38 IEC Class aM and gG/gL fuse version • IEC 60947-3 AC23A • IEC 60947-3 DC23A • CE CompliantShipping Weight:• 2.84 lbs (1.29kg) per carton Carton Quantity:• 12 polesEnvironmental Data• Storage and operating temperature: -20°C to 75°C**• Flammability rating: UL 94V0**For fuse performance under or above 25°C, consult fuse performance derating charts in the Cooper Bussmannpublication titled Selecting Protective Devices (SPD) reorder #3002.The revolutionary Cooper Bussmann ®CCP is 1/3 the footprint of a molded case circuit breaker. The level ofprotection provided by the CCP is up to three times the Short-Circuit Current Rating (SCCR) at full voltage than a molded case circuit breaker while providing disconnecting means.Product Features and Benefits•Extremely compact design at 17.5mm wide per pole •High Short-Circuit Current Ratings up to 200kA (UL) and 120kA (IEC)•Disconnect rated to provide means for load isolation.•Full voltage rated up to 600Vac or 80Vdc•Class CC version is UL 98 Listed and horsepower rated ,and suitable for branch circuit disconnect and branch circuit protection•IEC 10x38 version complies with IEC 60947-3 andsuitable for branch circuit disconnect and branch circuit protection•Suitable for global installations, the units comply with UL,cULus, and IEC standards accepting UL Class CC, Midget or IEC aM and gG/gL fuses •Open Fuse Indication- Local fuse indication lights* are standard.- Optional wired remote open fuse indication can be utilized to signal a PLC and open a contactor to de-energize all phases, if required.•IP20 finger-safe with 10 AWG (6mm 2) or larger wire •Built-in switch interlock capability prohibits removing the fuse under load•Padlockable handle for lockout/tagout procedures •Available in 1-, 2- and 3-pole versions*Circuit must be closed for indication light to illuminateUL Class CC, Midget and IEC 10x38 fusesLightTechnical Ratings*Rating may be lower depending on installed fuse. Refer to fuse data sheet.UL Class CC, Midget and IEC 10x38 fusesMotor Sizing ChartNote: NEMA motors only (no IEC or Design B Energy Efficient). Minimum size if no more than 1start/hour. Code max if low to moderate reverse/jog/plug applications. Heavy start permitted only ifCode Max does not allow motor start-up. For high reverse/jog/plug applications or largerhorsepower motors, Class J fuses are recommended. See CCP with CUBEFuse®.CUBEFuse ®Specifications:• Box Lug and Spade Terminal suitable for line, load or accessory connection • Box Lug Connection:-18-6 AWG (1 to 16mm 2) single or dual rated, solid or stranded – 75°C or higher - Cu only- 4 AWG (25mm 2) single – 75°C or higher - Cu only• Spade Terminal Connection: Max. 30A suitable for use with #8-32 UNC (M4) screw • Torque:- 18-10 AWG 20 Lb-In (1-6mm 2/3.4Nm)- 8-4 AWG 35 Lb-In (10-25mm 2/5.8Nm)• Lockout/tagout: 4mm shank lock or standard pin-out devices.• 35mm DIN rail mount• Local indication minimum operating voltage:- 90Vac/115VdcAgency Information:• UL 98 Listed, File E302370, Guide WHTY• cULus to CSA Standard 22.2 No. 4-04, File 302370, Guide WHTY7• CE CompliantShipping Weight:• 2.03 lbs (0.92kg) per cartonCarton Quantity:• 6 polesEnvironmental Data:• Storage and operating temperature: -20°C to 75°C**• Flammability rating: UL 94V0**For fuse performance under or above 25°C, consult fuse performance derating charts in the Cooper Bussmann publication “Selecting Protective Devices” (SPD)reorder #3002.The revolutionary Cooper Bussmann ®CCP is 1/3 the footprint of a circuit breaker. The level of protectionprovided by the CCP is up to three times the Short-Circuit Current Rating (SCCR) at full voltage than a molded case circuit breaker while providing disconnecting means.Product Features and Benefits•Uses Class CF finger-safe Low-Peak®CUBEFuse®with Class J electrical performance•Extremely compact design at 25.4mm (1 inch) wide per pole •High Short-Circuit Current Ratings at 200kA•Disconnect rated to provide means for load isolation•Full voltage rated at 600Vac for 30A, 60A and 100A versions •125Vdc rated for 40A versions•UL 98 Listed and suitable for branch circuit disconnect and branch circuit protection•1-, 2- and 3-pole versions are horsepower rated •Complies with UL and CSA •Open Fuse Indication:- Local fuse indication lights* are standard- Optional wired remote open fuse indication can be utilized to signal a PLC and open a contactor to de-energize all phases, if required•Additional open fuse indication can be provided by the CUBEFuse ®•IP20 finger-safe construction with 10 AWG (6mm 2) wire or larger•Built-in switch interlock capability prohibits removing the fuse under load•Padlockable handle for lockout/tagout procedures*Circuit must be closed for indication light to illuminateCompact Circuit Protector (CCP)CUBEFuse ®Circuit Marking AreaLockout ProvisionConnection*Class CF with Class J electrical performance.Fuse HolderTechnical RatingsCompact Circuit Protector (CCP) CUBEFuse®CUBEFuse®Motor Sizing TableCompact Circuit Protector (CCP) AccessoriesUL Class CC, Midget and IEC 10x38 fuses, and CUBEFuse®Recommended Lockout DevicesAccessories for use with Class CC, Midget, IEC 10x38 and CUBEFuse®CCPCCP-AUX CCP-PLC-IND(Includes spade terminals)Auxiliary Contact – CCP-AUXUL Class CC, Midget and IEC 10x38 fuses, and CUBEFuse®CCP-AUX installed on a CCP-3-xxDescriptionNO+NC contact output to indicate the status of the switching mechanism on the CCPSpecifications:•Rated Ampacity: 5A•Rated Voltage:240Vac•NC/NO contacts are closed/open when the CCP switchis in the “ON” position (closed)•Flammability Rating: UL94V0•For use with up to and including 60A CCPAgency Information:•UL98 File E155130, Guide WHTY2•cULus to CSA Standard 22.2 No. 4-04•IEC 60947-5-1•For use with up to and including 60A CCPWiring:•20-16 AWG (1 to 2.5mm2) wire•Torque 5 Lb-In (0.68Nm)•For use with only 75°C Cu wirePackaging:•The CCP-AUX is packaged individually•A single unit is capable of mounting to a1-, 2-, or 3-pole CCP Installation Technique:•Mounts on the right side of the CCP, and mechanically interlocks with the CCP switch handle with hardware providedIP20 Rating:YesEnvironmental Data:•Storage and Operating Temperature: -20°C to 75°CDe-energize all circuits before installing or removing any CCP-AUX devices and follow all prescribed safety procedures.UL Class CC, Midget and IEC 10x38 fuses, and CUBEFuse ®DescriptionA resetable three-phase remote fuse monitor thatintegrates with a Programmable Logic Controller (PLC) or other monitoring and control equipment Specifications:•Power Input : 24Vdc / 5mA•Output Signals : Digital 0Vdc (Low), 24Vdc (High)- 0Vdc Low – Fuse is good- 24Vdc High – Fuse has openedWhen the fuse opens, the output signal is sent high and will remain high until the unit is reset •Rated Impulse Voltage : 8kV•Local Indication : Two distinct LEDs indicate unit power (green) and open fuse (red). Open fuse LED is resetable upon the replacement of the fuse and the actuation of the reset switch•Flammability Rating : UL 94V0•For use with up to and including 60A CCPWiring:•For power, signal and ground connections use 22-24AWG (0.25mm2) 300V rated wireEmissions and Immunity Testing:•Electrostatic Discharge IEC 61000-4-2•Electrical Fast Transient/Burst IEC 6100-4-4•Surge Immunity IEC61000-4-5Packaging:•The CCP-PLC-IND is packaged individually•A single unit monitors up to three phases. Package includes 0.110” (2.8mm) quick connects for power, signal and ground connectionsMinimum Circuit Voltage:•Minimum circuit voltage required across the CCP is 100Vac for the remote indication device to operateInstallation Technique:•Mounts on the left side of the CCP and mechanically interlocks with the CCP switch handle with hardware providedIP20 Rating:Yes Environmental Data:Storage and Operating Temperature:-20°C to 75°C Agency Information:•UL 98 File E155130, Guide WHTY2•cULus to CSA Standard 22.2 No. 4-04PLC Programming:•The CCP-PLC-IND signal line is designed to provide a digital input to a PLC I/O card. In this case, aProgrammable Logic Control program must be written to properly interpret the input signal to the PLC. The PLC pro-gram should check for consecutive high signals before tak-ing action on a critical process.CCP-PLC-IND installed on a CCP-3-xxDe-energize all circuits before installing or removing any CCP-PLC-IND devices and follow all prescribed safety procedures.Connection from CCP-PLC-IND to CCP Connect leads from CCP-PLC-IND to the terminals as shown. There is a dedicated terminal on the CCP to accept the spade connectors from the CCP-PLC-IND. NOTE: When monitoring a 1-pole or 2-pole CCP, trim unused leads.Circuit MonitoringLeads from CCP-PLC-IND(100Vac – 600Vac) Circuit Monitoring LeadsMonitoring Device.UL Class CC, Midget and IEC 10x38 fuses, and CUBEFuse®Connections for CCP-PLC-IND from a CCP-3 to a remote monitoring deviceCompact Circuit Protector (CCP)UL Class CC, Midget and IEC 10x38 fuses, and CUBEFuse®©2011 Cooper Bussmann0211BU-SB101428Form P Page 11 of 11Data Sheet 1157The only controlled copy of this Data Sheet is the electronic read-only version located on the Cooper Bussmann Network Drive. All other copies of this document are by definition uncontrolled. This bulletin is intended to clearly present comprehensive product data and provide technical information that will help the end user with design appli-cations. Cooper Bussmann reserves the right, without notice, to change design or construction of any products and to discontinue or limit distribution of any products. Cooper Bussmann also reserves the right to change or update, without notice, any technical information contained in this bulletin. Once a product has been selected, it should be tested by the user in all possible applications.CCP-AUXCCP with CUBEFuse®CCP-PLC-INDDimensions - in (mm)CCP。