8D步骤及实例
8D实例讲解(包括5Y分析和鱼骨法)

人 设备 材料 方法 测量 环境
8D
2.详细的“5M1E”内容
(1)Man人的因素:人员的思想、意识、个体差异、 配合度、能力等。
(2)Machine机器的因素:机器和设备的功能、准 确度、机械能力等。
(3)Material材料是否合格,适合且及时。
(4)Method方法和工艺因素:方法合理、过程受控、 标准化。
8D
1.什么是“8D”
• “8D”:8Disciplines八大纪律制度,即解决问题的八
步骤法,是来自美国三大汽车公司之一的福特 (Ford)汽车公司的做法,现在已流行于全世界。 “8D”与克莱斯勒(Chrysler)汽车公司的“七步 纠正措施”法在本质上是相同的,他们都是解决 现场品质问题最有效、最可靠的方法之一。“8D” 的内容如下: (1)描述问题
教育; 6)其它。
8D
机:1)规定设备/工装/检具--机器相应的更换周期及作业 点检并记录; 2)更改工装或模具或增加新工装新设备等; 3)操作指导书规定相应的条件和参数并按要求执行和 记录; 4)维修和保养,校正计划及作业记录。
料:1)按作业标准选择正确材料; 2)规定材料的搬运、储存、包装方式并对其进 行监督检查。 3)制定相应检测标准及方法控制原材料的不良;
法:1)规定正确合理的作业及工艺流程并按流程执行; 2)作业指导书规定相关内容使其更完善; 3)有效的防错措施。
8D
测:1)检验规范规定相关内容; 2)规定检具的使用、校正周期并作相应的标识; 3)根据标准确定检测方法; 4)规定检测仪器的维修和保养,校正并作相应的记录;
环:采取相应措施改变环境使其能达到作业要求。 16.纠正措施的验证
NG
5.验证
OK
8D实例讲解(包括5Y分析和鱼骨法)

8D
二:5W2H
1.什么是5W2H
what when
何事 何时
5W
where 何地
who
何人
why
为何
How
如何
2H How Mach 几何
8D 2.详细的“5W2H”包括如下内容
(1)What何事:指事情的内容是什么,要抓住实质性的东 西。
(2)When何时:事情发生的时间,有多久,主要强调时间 的因素。
11. 成立小组并确定范围 由接收《8D报告》的责任人填写,成立的小组必须具备解决问题 的技能、知识和权力 。
12. 确定和描述问题 由接收《8D报告》的责任人填写,并确认发出《8D报告》的单位 或人员所描述的状态是否属实。
13. 临时措施 由接收《8D报告》的责任人填写,内容包括:直接的
8D 对策应包括供方、客户及运输中、中间仓库的零件处理及 正常生产的维持 。
8D
2. “8D”的应用方法
(1)描述问题
在写问题报告时要从“5W2H”的角度去描述Leabharlann 问题。When:问题发生的时间
Where:问题发生场所、相关部门
Who:问题发生的当事人
描述问题
What:问题的主要内容是什么
Why:问题为什么发生
How:现在状态怎样
How mach:会导致那些后果和损失
8D
(2)临时措施或紧急措施 问题的当事人或管理者应立即采取紧急措施,并 记录日期和时间。采取紧急措施时应注意下列事 项:
(3)Where何地:事情发生的场所在那里,有无变动和转 移,是否针对了具体的环境和当时的状态。
(4)Who 何人:与事情相关的人,包括责任者、目击者、 协同者等。
2024年8D报告培训教材教程

8D报告培训教材教程1.引言8D报告是一种广泛应用于质量管理和问题解决的方法,其名称来源于8个解决问题的步骤(Disciplines)。
本教材旨在为您提供关于8D报告的全面培训,帮助您掌握8D报告的编写和应用技巧。
2.8D报告的背景和目的8D报告起源于汽车行业,并逐渐被其他行业所采用。
其主要目的是系统地解决问题,防止问题再次发生,并提高产品和服务的质量。
8D报告通常用于处理客户投诉和内部问题,以及推动持续改进。
3.8D报告的8个步骤3.1步骤1:建立团队在开始编写8D报告之前,需要建立一个跨部门的团队,团队成员应具备相关领域的专业知识和经验。
团队应由一名负责人领导,负责协调和推动整个解决问题的过程。
3.2步骤2:问题描述问题描述是8D报告的核心部分,需要清晰地描述问题的现象、影响和发生的时间。
问题描述应尽量具体、准确,并使用数据和事实来支持。
3.3步骤3:临时措施在找到根本原因之前,需要采取一些临时措施来减轻问题的影响。
这些措施应尽快实施,并在报告中详细说明。
3.4步骤4:根本原因分析根本原因分析是解决问题的关键步骤,需要运用各种工具和技术来找到问题的根本原因。
常用的工具包括鱼骨图、5个为什么等。
3.5步骤5:制定行动计划根据根本原因分析的结果,制定详细的行动计划来解决问题。
行动计划应包括具体的行动步骤、责任人和完成时间。
3.6步骤6:实施行动计划按照行动计划,组织资源并实施解决方案。
在实施过程中,需要监控进度,并及时调整计划以确保问题得到有效解决。
3.7步骤7:效果验证在实施解决方案后,需要对效果进行验证,以确保问题得到根本解决。
验证可以通过数据分析、客户反馈等方式进行。
3.8步骤8:预防措施和持续改进为了防止问题再次发生,需要制定预防措施,并对整个问题解决过程进行总结和反思,提出改进建议。
4.8D报告的编写技巧4.1结构清晰8D报告应遵循一定的结构,包括引言、问题描述、临时措施、根本原因分析、行动计划、实施结果、效果验证、预防措施和持续改进等部分。
8D工作方法简介
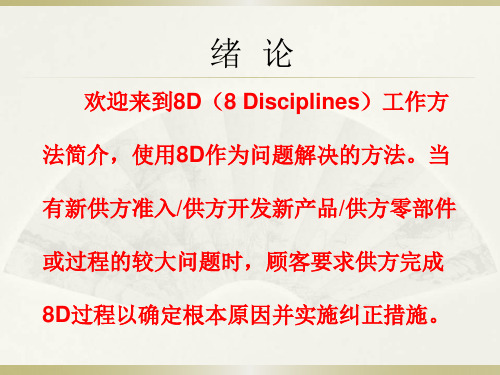
列出完成8D过程的工具(例如,试验设计DOE,统 计过程控制SPC, FMEA, 散点图, 检查单, 控制图等 等).
验证供方使用了适当的工具。 识别当评审8D报告时需询问的8D问题。 验证供方是否准确执行和文件化了8D过程。 确保供方通过启动和关闭问题已经验证了根本原 因。验证供方已经完成的所有材料包括所有可疑 材料,也包括已经在装配工厂、运输中、仓库 和过程中的零件。
D4: 定义和验证 根本原因和遗漏点(续)
常见性错误
声明的根本原因不是真正的根本原因, 操作者错误、准备的问题,或者是问题的 征兆或结果被作为根本原因给出。
质量工具
因果图 FMEA 是否分析 试验设计(DOE) 稳健设计
实例
S公司通过失效树(FTA)的方法验证根本 原因: 1、验证根本原因
根本原因1
问题
在AIM中顾客 项目的问题点
要求供方8D
供方在24小 时内以临时 纠正措施反应
在AIM 中标识
是 问题点
是供方的 职责吗?
否
在AIM 中关闭
问题的提出
下面的流程图显示了在现行生产中使用质量验收ຫໍສະໝຸດ 统(QR)导致问题的提出问题
QR中工 厂问题点
要求供方8D
供方在24小 时内以临时 纠正措施反应
到供方改 进矩阵
QR问题点
是 问题点
是供方的 职责吗?
否
顾客重新 确定职责
实例
S公司为顾客制造零件,见下图:
A
实例
根据顾客的工程规范,在零件A上必须镀银,否则顾客的 产品无法完成规定功能。有一天,他们收到顾客工厂发来 的问题点如下:
因为没有镀银造成产品缺陷,整批拒收。
8D改善报告应用实例

DISCIPLINE 6(执行效果验证):
①对于已生产出的成品半成品按以 上措施进行返工送至客户处进行装 配OK无其它不良;②对于后续加工 的新产品用检具进行检测后送到客 户处装配没发现该问题发生 。
执行人 蒋良辉
日期
7、预防再发 ❖ 作业导书更新(固化)? ❖ 这一改善是否适用别处? ❖ 系统改善对策是否适用于别处? ❖ 修改过程文件(PMP 等)? ❖ 确定所有预防再发措施完成的责任人和完成日期?
④将客户处所有该物料退回我司,我司将 成品、半成品全数清理出来全部转到机加 组按照此方案进行返工;
⑤工程部根据线路板尺寸做2-3个模拟线路 板样本图交机加组加工出来交品质部对返 工产品进行检测。
执行人
柯拥军 范洪博 廖振青 冠宏QE 蒋良辉
项目 工程师
梁圣强 轩海洋
日期
5、长期措施 ❖ 所有根本原因都有相应对策吗? ❖ 是否按对策的优先次序进行,并验证后实施排除法? ❖ 是否有防呆措施? ❖ 如果无法从系统面来保证就应该建立防呆措施? ❖ 设定所有改善对策完成的日期?
DISCIPLINE 7(防止再发生): 执行人 日期
将此不良项目、注意事项及检测方 法加入到《QC工程图》和《工艺 流程卡》中并将其它两种类似的产 品的工艺文件更改。
柯拥军 轩海洋
❖ 8、恭贺您的团队:
庆贺你的团队,固化共享:经 过小组成品的共同努力此质量 问题得到圆满解决,经验证后 续没有出现类似问题 。
管制图
层别法 查检表
柏拉图
直方图
散布图
❖ a、鱼骨图----用来对一个现象或结果进行原因深入
细致的分析,通常用来找原因入因素,最好同层别法结 合起来使用。
❖ b、柏拉图(排列图)----用来对多种问题或原因
8D报告模板_6

其他
3.供应商内部流出原因(或汽车厂家处未识别出)的初步分析
不合格零件应当在何处被发现?
N
在制造工序中
在制造后(如最终检验)
出货前/汽车厂家入库时
没有被发现的原因
对不良产生原因初步判断/流出原因的分析:
D3-第三步骤:执行临时对策
4.临时对策–立即的
组织相关人员针对此问题开现场分析会。
考虑事项
防止再发生对策报告书―8D
编号:
D1-第一步骤:建立解决问题小组
组长:
组员:
D2-第二步骤: 描述问题
减振器在新车交验过程中损坏:弹簧弹出,减震器失效。
1 问题详情
受影响的数量(或追溯)
2. 向类似零件的展开
该问题在其他零件上发生过吗?
考慮事項
Y
N
备注/ 結果
其他车型零件
同一不良现象覆盖的所有车型。
D8-第八步骤: 团队激励。
处置
OK数
NG数
在制品
中间在库品(半成品)
仓库存品
服务备件
其他
首批交付合格部品如何特殊标识/标记 ?
标牌
D4-第四步骤: 找出问题真正原因
5最终分析
时间
原因
责任部门
生产管理部
生产管理部
D5-第五步骤: 选择永久对策
6.永久対策
措施
负责人
部门
实施时间
D6-第六步骤:执行及验证永久对策
7. 对策确认
Y
N
Y
N
D7-第七步骤: 防止再发。
8.跟踪措施
考慮事项
Yes/No
实施时间
实施部门
工序作业/检查指导书
8d报告培训

8d报告培训8D报告培训。
一、概述。
8D报告是一种针对问题解决和持续改进的方法,它由八个步骤组成,可以帮助团队有效地识别、解决和预防问题。
本次培训将重点介绍8D报告的基本概念、步骤和工具,以及如何在实际工作中应用这些知识来解决问题。
二、8D报告的概念。
8D报告是一种质量管理工具,它起源于美国汽车工业,后来被广泛应用于各个行业。
它的核心思想是通过系统性的方法来解决问题,以确保问题不再发生。
8D报告的八个步骤分别是,明确问题、建立团队、制定临时措施、确定根本原因、制定长期解决方案、实施解决方案、预防措施和确认效果。
每个步骤都有相应的工具和技术支持,可以帮助团队更好地完成任务。
三、8D报告的步骤。
1. 明确问题,首先要明确定义问题,包括问题的性质、影响范围和紧急程度。
这一步需要收集相关数据和信息,确保对问题有全面的了解。
2. 建立团队,确定一个专门的团队来负责解决问题,团队成员需要具备不同的技能和经验,以便全面分析和解决问题。
3. 制定临时措施,在确定长期解决方案之前,需要先采取一些临时措施来减轻问题带来的影响,确保生产和服务的正常进行。
4. 确定根本原因,通过使用工具如5为什么分析、鱼骨图等,找出问题的根本原因,而不是仅仅解决表面问题。
5. 制定长期解决方案,基于对根本原因的分析,制定长期解决方案,并评估其可行性和效果。
6. 实施解决方案,将长期解决方案付诸实施,并监控其进展情况,确保按计划推进。
7. 预防措施,为了避免问题再次发生,需要采取一些预防措施,如改进流程、加强培训等。
8. 确认效果,最后需要对解决方案的效果进行确认,确保问题得到了彻底解决。
四、应用实例。
以某公司生产线上频繁出现的产品质量问题为例,我们可以运用8D报告来解决这一问题。
首先,明确问题是产品质量不达标,影响生产进度和客户满意度。
然后,建立一个由生产、质量、工程等部门成员组成的团队,共同分析问题。
接着,制定一些临时措施来减少不合格品的产生,同时进行5为什么分析,找出问题的根本原因。
8D报告-8d报告

四. 8D步骤-D7效果确认及标准化
验证预防再发对策并监控长期的效果。 水平展开,以防同一问题及类似问题再 度发生。将相关对策形成书面文件(管 理制度、程序文件、作业指导书、表单、 技术文件、工程图纸等)。
四. 8D步骤-D7效果确认及标准化
效果确认 实事求是,以事实和数据为依据,对数据用统计工具处 理后得出相应的结论,不应未做对比分析即判定效果。
16.00% 14.00% 12.00% 10.00%
8.00% 6.00% 4.00% 2.00% 0.00%
slot1
slot2
slot3
slot4
slot5
改善前
改善后
数据点多按日期来建议走势图,数据点少可用上面的柱状图
数据来源: 时 间:
➢关键点一 :改善前后对比,数量及比例。 ➢关键点二: 结果收集的数据来源要说明。
TOYOTA 5-Why?
1W
WHY 问题
2W
WHY 中间原因
3W
WHY 中间原因
4W
WHY 中间原因
5-WHY分析案例1 状态1 一辆汽车出了故障不能行驶(WHY1)
状态2-原因1 引擎故障(WHY2)
状态3-原因2
火花塞不点火(WHY3)
状态4-原因3
3.措施 尽量具 体化。
四. 8D步骤—D6预防再发对策
计划和执行选取的预防再发对策。去除 临时行动。
需要考虑的问题:
1.确定并执行预 防再发对策, 并应注意持续 实施监控,以 确定根因已经 消除。
2.待步入生产阶 段,应即监视 纠正措施之长 期效果,并于 必要时采行补 救措施。
3.验证 预防再发 对策有效 后,可以 停止临时 措施。
PQE培训教材-8D报告

PQE培训教材-8D报告1. 什么是8D报告8D报告是一种问题解决方法,它可以帮助团队追溯和解决问题的根本原因,并制定有效的纠正和预防措施。
它是以8个步骤命名的,每个步骤都有具体的任务和工具,以确保问题得到彻底解决。
以下是8D报告的八个步骤:1.D1:建立问题解决团队2.D2:描述问题3.D3:立即暂时解决问题4.D4:根本原因分析5.D5:制定纠正措施6.D6:实施纠正措施7.D7:验证纠正措施8.D8:预防措施跟踪2. D1:建立问题解决团队在D1阶段,我们需要确定一个问题解决团队,这个团队由不同领域和专业的人员组成,以确保问题得到全面的解决。
团队应包括以下成员:•项目经理:负责整个问题解决过程的组织和协调。
•质量工程师:负责分析和解决质量问题。
•制造工程师:负责分析和解决制造过程中的问题。
•供应链代表:负责协调和解决供应商相关的问题。
•设计工程师:负责分析和解决设计问题。
•生产经理:负责分析和解决生产过程中的问题。
•客户代表:负责与客户沟通并解决与客户相关的问题。
建立问题解决团队后,团队成员需要明确各自的角色和职责,并制定一个工作计划,以确保问题得到及时解决。
3. D2:描述问题在D2阶段,团队成员需要准确地描述问题,并确保问题被充分理解。
问题描述应包括以下内容:•问题发生的具体时间和地点。
•问题的具体表现或症状。
•问题影响的范围。
•对问题的初步评估以及可能的原因。
描述问题时,团队成员应尽量客观和详细,以确保问题不会被误解或忽视。
4. D3:立即暂时解决问题在D3阶段,团队成员需要立即采取措施解决问题的紧急影响。
这些措施是暂时的,旨在缓解问题的影响,但不一定解决问题的根本原因。
暂时解决问题的措施可能包括以下内容:•停机或减少生产。
•调整生产工艺。
•加强质量检查。
•与供应商联系并请求紧急支持。
在采取暂时解决措施后,团队应监控问题,并确保措施的有效性。
5. D4:根本原因分析在D4阶段,团队成员需要进行根本原因分析,以确定问题的根本原因。
8D实施方法含实例

D6、验证纠正措施
1. 换完电线后,至今尚没有发现连接点松动的迹象。 2. 断开电流接触器的电路进行试验,一旦电压不正常,转子 将自动停止工作,直至没电镀的产品从线上取下。 以上工作,小组共同进行了验证,并提请顾客事先的批准。
32
D7、防止再发生的措施
❖电镀工作指导书被修改增加了如下内容: 1)当生产线不正常停止时,操作者不仅要挑选出缺陷产品 ,而且要在工作记录记下数量及当班QC的名字。 2)在电镀线在每天早上启动前,电流接触器的连接点和电 线必须检查。以上,由杨星在12月15日完成。 ❖开发一个包括每天需检查事项的检查清单,例如生产线停 止,不管缺陷产品是否被挑选,制造部和QA需进行审核。 ❖ 依次类推,如果有类似问题,该小组负责纠正并采取适当 的预防措施。
检查数量
状态 缺陷数量
MT001206 19308片
19308片
OK
0
MT001208 14274片
14274片
OK
0
总计
33582片
33582片
OK
0
•2. 我们对操作者进行培训和教育,以让其知道最重要的事情:
•遵守工作程序和指导书以保持顾客产品质量。使其意识到他们在 产品质量保证中的重要职责。我们强调,任何由于不小心引起的错 误是不允许的并且不能重复发生,因为那样将会给顾客带来不必要 的损失。因此我们把给顾客造成损失的错误展示以教育员工。
生管课、销售课、库管课、品保课 • 责属人员:
贾正羽、庄卫年、赵晓明、许 丽
36
D2.问题描述
• 何时 : 1999年11月4日; • 何人 : 浙江精密机械厂; • 何地 : 浙江精密机械厂—包装车间; • 何事 : 包装ALT-5检测器时,使用20μMHT
8D分析法

處理過程
3.实施及确认暂时性的对策 在未查明造成事故原因前,关闭装配生 产 E 线噪音测试房的电源,停止该工作 间的使用和修缮,装配生产 E 线其他的 设备和设施可继续运作生产,所生产产 品的噪音测试工作临时移至其他空闲噪 音测试房进行。
15
處理過程
4.原因分析及验证真因 ( 1 )采用因果分析图,按人、机、料、法、 环类别分别列出导致火灾的各种可能原因,见 上页图。 ( 2 )列表对可能原因进行排查,找出最有可 能的几个原因,见上表。 通过比较分析,得到六个可能造成事故的重要 因素:①荧光灯具;②电气线路老化短路;③ 电气线路接驳方法不当;④电线质量;⑤电气 线路安装方法不当;⑥空调安装方法不当。
上一页
12
三、实例分析
某空调公司装配生产线噪音测试房发生 了一起火灾事故,事后该公司成立火灾 事故改善小组,采用 8D 分析法对造成 事故的原因进行排查,找出真正的事故 原因,制定有效的改善措施杜绝事故再 次发生。
13
處理過程
1.成立改善小组 小组成员和职责表(略)。 2.描述问题 2009年11月30日下午13∶30,装配生产E线噪音测试 房两检验员来到工作岗位,开启测试房内空调、测试 仪等设备约一分钟后,发现空调室内机附近的隔音棉 冒烟,两人冲出测试房。转瞬间,测试房内的电源线 路、空调室内机、隔音棉等相继着火,现场员工迅速 将生产线电源关闭,并用灭火器在10分钟内将火救熄。 由于事故发现及时并采取了有效的抢救措施,火灾没 有蔓延到测试房外的其他地方,事故现场的电气线路、 一台空调室内机、隔音棉和待测试的三台空调室内机
上一页
5
2D. 描述问题
将问题尽可能量化而清楚地表达, 详细说明何时、何地、发生了什 么事、严重程度、目前状态、如 何紧急处理、以及展示照片和收 集到的证物。
8D方法

成果? • 是否采用“头脑风暴”等方法收集纠正措施? • 是否获得了多项纠正措施方案并对其进行了筛选? • 是否需要召开决策评审会或者风险评估会? • 措施是否考虑了问题的时间? • 措施是否充分考虑条件? • 措施是否考虑问题的大小? • 纠正措施的实施是否涉及到顾客?是否与其进行了沟通? • 是否制定了工作进度时间表?
8D方法
目录
1 何谓8D 2 何时8D 3 如何8D 4 8D报告 5 8D实例学习
8D(8 Disciplines)又称团队导向问题解 决方法,意思是8个人人皆知解决问题的固定 步骤,是福特公司处理问题的一种方法。它提 供了一套符合逻辑的解决问题的方法,同时对 於统计制程管制与实际的品质提升架起了一座
8、小组祝贺:
• 目的:承认小组的集体努力,对小组工作进行 总结并祝贺 。
• 步骤:1、汇报工作成果(编写案例分析报告;有选择
的保留重要文档;流览小组工作,将心得形成文件;撰写PPT进 行汇报)
2、肯定与奖励(肯定小组对解决问题的集体力
量,及对解决问题作出的贡献;给予必要的物质、精神奖励)
注意:
撰写8D报告,并将所有重要文档归档保存。
端口破损数(卷) 频率(%) 累计频率(%)
A。产品堆放高度过高
12
52.17 52.17
B。包装方式不合理
4
17.39 69.56
C。操作粗心
2
8.69 78.25
D。库房湿度大
1
4.34 82.59
E。速度设定太快
1
8D报告解说及范例
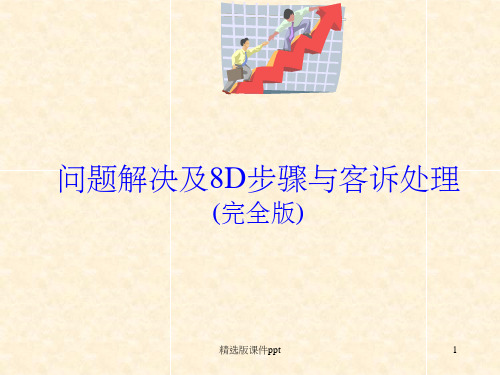
77.95 78.95 7精9.选95版课件p8p0t.95 81.95 82.95 83.9531
柏拉图 (Pareto Chart)
• 目的:为便于判断产品较重要之不良原 因所绘制之图形
• 通常先以层别法与查检表为前置作业
精选版课件ppt
32
• 实例
xx工程不良分析表
项目
不良数 累积不良数 比率 % 累积比率%
表格之依据 • 通常可做为柏拉图及直方图之前置作业 • 重点在设计表格
精选版课件ppt
25
查检表 (Check List)
地区
FAB 1
机
台
项目
ABC
温度不足
压力不足
转速不足 其他
精选版课件ppt
FAB 2 ABC
26
直方图 (Histogram)
• 目的:为便于判断产品质量特性之分配 状态,及其与规格之关系所绘制 之图形
精选版课件ppt
19
壹. 问题篇 2 目标设定
• 决定具有挑战性的目标值 • 决定目标完成期限 • 预估成效
精选版课件ppt
20
壹. 问题篇 设定目标方法
• 根据公司或内部方针及计划,考量目前 水平,由全体自主的设定
• 活用统计方法来决定目标,如柏拉图… • 目标尽可能数量化、明确化 • 不能收集数据时,以文字来叙述欲达成
检测问题 为何100%Q1测试不良 为何测试ok之产品重测4
壹. 问题篇
问题的特性
问题的特性
问题的大小
(Magnitude)
问题的严重性 (Serverity)
发生频率
(Occurance)
侦测性
(Detectability)
8d报告案例

8d报告案例8D报告案例。
在工业生产和质量管理中,8D报告是一种常见的问题解决方法。
它是指通过八个步骤来诊断、纠正和预防问题,以确保产品质量和客户满意度。
下面我们将以一个实际案例为例,来详细介绍8D报告的应用过程。
1. 问题描述。
某汽车零部件制造企业在生产过程中发现了一批产品出现了漏油的质量问题。
经过初步调查,发现该问题主要出现在一条生产线上,而且已经影响到了部分客户的使用体验,需要尽快解决。
2. 组建团队。
为了解决这一质量问题,企业迅速组建了一个由质量工程师、生产人员、技术人员和客户服务人员组成的团队,负责开展8D报告的相关工作。
3. 问题分析。
团队首先对问题进行了深入分析,通过对生产线的检查和产品的测试,确定了漏油问题主要是由于某个关键工艺环节的不合格零部件导致的。
同时,还发现了一些相关的工艺参数和操作规程存在一定的问题,需要进一步改进。
4. 制定临时对策。
为了尽快解决问题,团队制定了一系列临时对策,包括暂停相关生产线的生产、更换不合格零部件、调整工艺参数等,以确保不合格产品不会继续流入市场。
5. 确认根本原因。
通过对生产线和工艺的进一步调查和分析,团队最终确认了漏油问题的根本原因,并针对性地提出了相应的长期解决方案,包括改进零部件制造工艺、优化操作规程、加强质量监控等。
6. 实施长期对策。
在确认了长期解决方案后,团队立即着手实施,对生产线进行了全面的改进和优化,同时加强了对关键工艺环节的监控和管理,以确保类似问题不再发生。
7. 预防措施。
为了预防类似问题的再次发生,团队还对相关的质量管理体系和流程进行了全面的审视和调整,确保漏油问题得到了有效的预防和控制。
8. 总结和表彰。
经过团队的不懈努力,漏油问题最终得到了圆满解决,产品质量得到了有效保障,客户满意度也得到了提升。
企业对团队的成绩给予了充分的肯定和表彰,同时也总结了这次问题解决的经验和教训,为今后的质量管理工作提供了宝贵的参考。
通过这个案例,我们可以清楚地看到8D报告在解决质量问题中的重要作用。
8D解决问题的方法

描述问题
要点:
1、差异描述:现实与标准的对比差异,标准与标准的对 比差异;
2、程度描述:通过量化、细化、比例反应差异的程度;
原则:
1、运用7W5H标准描述问题;
2、不能有主观臆断、判断性词语描述,还原事件的本质;
3、以事实为依据; 4、数据化、量化。
制订和执行围堵措施
D3 制订和执行围堵措施 Implement and Verify Interim (Containment) Actions
制订和执行围堵措施
1、为使外部或内部的客户都不再(或降低)受 到影响,制定并执行临时性的围堵措施,直到已 采取了永久性的改进。 2、暂时对策决定后,即立刻交由团队成员带回 执行。 3、验证所采取围堵措施的效果
目的:围堵/隔离问题,是为了保护你的顾客
制订和执行围堵措施
运用目前已知的信息 以及问题的描述来采 取临时围堵措施 ←选择 ←事先验证 ←执行
产生背景
福 特 汽 车 公 司 使 用 8D 作 为 问 题 解 决 的 方 法 ( 见 QS-9000 要 求 之 4.14.1.1)。当福特的供方具有零件或过程的问题时,福特要求供方完成8D 过程以确定根本原因并实施纠正措施。
TS16949:2009——8.5.2.1对解决问题的方法要求: 1.组织应有一个确定的过程用于解决问题,使根本原因得到识别 并消除。 2.若有顾客规定的解决问题的方式,则组织应采用此方式。
成立团队
团队的构成因素与类型
构成因素
目标 人员 岗位 权限(资源) 计划
类型
◇问题解决型团 ◇职能管理型团 ◇多功能型团队 问题解决型团队的核心点是提 高生产质量、提高生产效率、 改善企业工作环境等。
8D实例讲解(包括5Y分析和鱼骨法)[精制材料]
![8D实例讲解(包括5Y分析和鱼骨法)[精制材料]](https://img.taocdn.com/s3/m/ff27e9c2804d2b160b4ec0a8.png)
实操应用
10
8D
3. “8D”流程示意图
2.紧急措施
1.描述问题 3.根本原因分析
选择最佳处理方案 NG
检验处理方案效果
OK 4.实施永久措施
NG
5.验证
OK
7.预防
NG 6.控制
OK
8.嘉奖实操、应关用闭
11
8D
4.实施8D的好处
●杜绝处理问题中的拖拉现象
处理问题拖拖拉拉是现场人员经常易犯的毛病。也许因
实操应用
6
8D
(2)临时措施或紧急措施
问题的当事人或管理者应立即采取紧急措施,并 记录日期和时间。采取紧急措施时应注意下列事 项:
●紧急措施只针对现时的症状和结果,可能不会从 根本上解决问题;
●可能时,分析根本原因最好与采取紧急措施同步 进行;
●紧急措施应予以规定为临时使用,并指出具体的 临时期限,如果期限已到而还没有永久措施产生, 就需要对临时期限再作规定,但这个规定只能是 被迫形成的。
实操应用
2
8D
1.什么是“8D”
• “8D”:8Disciplines八大纪律制度,即解决问题的八
步骤法,是来自美国三大汽车公司之一的福特 (Ford)汽车公司的做法,现在已流行于全世界。 “8D”与克莱斯勒(Chrysler)汽车公司的“七步 纠正措施”法在本质上是相同的,他们都是解决 现场品质问题最有效、最可靠的方法之一。“8D” 的内容如下: (1)描述问题
实操应用
16
8D
8. 零件名称 填入发生不良零件的图纸上的零件名称或车型。
实操应用
5
8D
2. “8D”的应用方法
(1)描述问题
在写问题报告时要从“5W2H”的角度去描述
8D实例分析

案例:事由:出租屋内,一日早晨,小王正在水龙边洗脸准备上班,刚洗完脸,突然家中打来电话,于是把脸帕一挂就去屋内接电话,接完电话就去上班。
下午下班回家时发现家中全部被水淹了。
铺在地上的草席和被子全都漂在水中。
D1-成立改善小组:马上叫上住在隔壁的几个同事,组成事故处理小组。
小组成员:张三、李四、王五。
D2(第二步):问题描述王五家中被水淹,家中所有摆放在地上的物品都浸在水中(不良率100%)。
如:草席、被子和书本等。
D3(第三步)-暂时围堵行动(即应急对策或叫临时对策)1、马上与小组成员一起把家中的水设法排放出去。
负责人:张三2、立即把浸在水中的物品捞起并摊开到阳台去凉干。
负责人:李四D4(第四步)---根本原因分析:1、早晨洗完脸时,接听家中突然打来的电话,然后忘记关水,造成水淹小屋。
下水道出口太小,而且都采用网格式的盖子盖住。
昨天洗菜洗出来的小片烂蔬菜叶梗在网格上,致使下水道出水很慢,长时间积累后,大量未及时排放出去的水把小屋淹了。
分析人:王五审核:王五妻子D5(第五步)---制订永久对策(即长期对策)1、把下水道出口上的网格式盖子去掉,以便加大出水口,不会造成被水淹的情况。
责任人:王五D6(第六步)---实施/确认经过王五实际操作,把下水道出口加大后,小片蔬菜叶不会再梗在出水口处,堵住废水往外流。
并且即使把水龙头打开到最大,水仍能及时地从下水道出水口完全地流出去。
现确认此永久对策有效,并已经执行。
验证人:王五D7(第七步)---防止再发生(即采取预防措施)早晨上班出门前一定要检验水龙头是否关闭。
以后洗蔬菜时一定要把烂蔬菜叶丢到垃圾筐里,并且要把地面清理干净。
早晨洗脸时不能带电话在身上。
在洗脸过程中,就算电话铃响起也不能接。
直到洗漱完毕后才能接听手机。
责任人:王五预计完成时间:2007D8(第八步)---结案并祝贺:此问题已经完全处理清楚,可以结案(close)。
并且今天晚上叫张三、李四、王五老婆一起去‘毛家饭店’庆祝团队成功。
8D分析报告
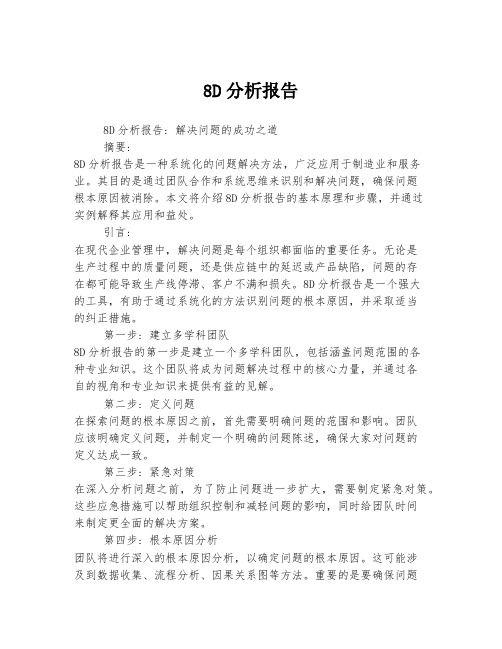
8D分析报告8D分析报告: 解决问题的成功之道摘要:8D分析报告是一种系统化的问题解决方法,广泛应用于制造业和服务业。
其目的是通过团队合作和系统思维来识别和解决问题,确保问题根本原因被消除。
本文将介绍8D分析报告的基本原理和步骤,并通过实例解释其应用和益处。
引言:在现代企业管理中,解决问题是每个组织都面临的重要任务。
无论是生产过程中的质量问题,还是供应链中的延迟或产品缺陷,问题的存在都可能导致生产线停滞、客户不满和损失。
8D分析报告是一个强大的工具,有助于通过系统化的方法识别问题的根本原因,并采取适当的纠正措施。
第一步: 建立多学科团队8D分析报告的第一步是建立一个多学科团队,包括涵盖问题范围的各种专业知识。
这个团队将成为问题解决过程中的核心力量,并通过各自的视角和专业知识来提供有益的见解。
第二步: 定义问题在探索问题的根本原因之前,首先需要明确问题的范围和影响。
团队应该明确定义问题,并制定一个明确的问题陈述,确保大家对问题的定义达成一致。
第三步: 紧急对策在深入分析问题之前,为了防止问题进一步扩大,需要制定紧急对策。
这些应急措施可以帮助组织控制和减轻问题的影响,同时给团队时间来制定更全面的解决方案。
第四步: 根本原因分析团队将进行深入的根本原因分析,以确定问题的根本原因。
这可能涉及到数据收集、流程分析、因果关系图等方法。
重要的是要确保问题的根本原因被准确地识别,以便为后续的纠正措施奠定基础。
第五步: 纠正措施一旦根本原因被确定,就需要制定纠正措施来消除问题。
这些纠正措施应基于对问题原因的深入理解,并经过仔细的分析和评估。
此外,这些纠正措施应是可持续的,以防止问题重新发生。
第六步: 预防措施在纠正措施实施后,团队需要制定预防措施来预防类似问题的再次发生。
这些措施可能包括流程改进、员工培训和设备维护等。
重要的是要确保团队通过系统思维来制定可行的预防措施。
第七步: 检查效果在纠正和预防措施实施后,团队应该对效果进行检查和评估。
- 1、下载文档前请自行甄别文档内容的完整性,平台不提供额外的编辑、内容补充、找答案等附加服务。
- 2、"仅部分预览"的文档,不可在线预览部分如存在完整性等问题,可反馈申请退款(可完整预览的文档不适用该条件!)。
- 3、如文档侵犯您的权益,请联系客服反馈,我们会尽快为您处理(人工客服工作时间:9:00-18:30)。
8D 步骤D1-第一步骤: 建立解决问题小组若问题无法独立解决,通知你认为有关的人员组成团队。
团队的成员必需有能力执行,例如调整机器或懂得改变制程条件,或能指挥作筛选等。
D2-第二步骤: 描述问题向团队说明何时、何地、发生了什么事、严重程度、目前状态、如何紧急处理、以及展示照片和收集到的证物。
想象你是FBI的办案人员,将证物、细节描述越清楚,团队解决问题将越快。
D3-第三步骤: 执行暂时对策若真正原因还未找到,暂时用什么方法可以最快地防止问题?如全检、筛选、将自动改为手动、库存清查等。
暂时对策决定后,即立刻交由团队成员带回执行。
D4-第四步骤: 找出问题真正原因找问题真正原因时,最好不要盲目地动手改变目前的生产状态,先动动脑。
您第一件事是要先观察、分析、比较。
列出您所知道的所有生产条件(即鱼骨图),逐一观察,看看是否有些条件走样,还是最近有些什么异动?换了夹具吗?换了作业员?换了供应商?换了运输商?修过电源供应器?流程改过? 或比较良品与不良品的检查结果,看看那个数据有很大的差?,尺寸?重量?电压值?CPK?耐电压?等等不良的发生,总是有原因,资料分析常常可以看出蛛丝马迹。
这样的分析,可以帮助您缩小范围,越来越接近问题核心。
当分析完成,列出您认为最有可能的几项,再逐一动手作些调整改变,并且观察那一些改变可使品质回复正常及影响变异的程度,进而找到问题真正的原因。
这就是著名田口式方法最简单而实际的运用。
D5-第五步骤: 选择永久对策找到造成问题的主要原因后,即可开始拟出对策的方法。
对策的方法也许有好几种,例如修理或更新模具。
试试对可能的选择列出其优缺点,要花多少钱?多少人力?能持续多久? 再对可能的方法作一最佳的选择,并且确认这样的对策方法不会产生其它副作用。
D6-第六步骤: 执行及验证永久对策当永久对策准备妥当,则可开始执行及停止暂时对策。
并且对永久对策作一验证,例如观察不良率已由4000 PPM降为300 PPM,CPK由0.5升为1.8等,下游工段及客户己能完全接受,不再产生问题。
D7-第七步骤: 防止再发对类似的其它生产,虽然尚未发生问题,亦需作同步改善,防止再发,即我们说的”他石攻错”。
同时这样的失效,也应列入下一产品研发段的FMEA中予以验证。
D8-第八步骤: 团队激励对于努力解决问题之团队予以嘉勉,使其产生工作上的成就感,并极乐意解决下次碰到的问题。
无论是产发段发现的问题,或是量产、客诉问题,若公司每年有近百项的工程问题依照8D的方式来解决,对工程人员实力的培养着实可观,成为公司重要的资产,这也是很多公司将8D制式化的原因。
8D的运用,其实不只在工程上,您工作上,生活上碰到的很多问题,不妨也用8D的逻辑来思考看看实例1. Form the TeamDate Started: Sep. 22, 2002Internal team member: A, B, CExternal team member: N/A2. Describe the ProblemOne field failed unit of XXX model was returned from the customer on Sep.20. The failure occurred at the end-user’s site with the symptom described as ‘The unit burned when powered on with line and could not be powered on again.’3. Describe the Root Cause3.1 What FoundAfter carefully investigation it is found that components listed below in the XXX circuit are damaged:Part Spec. DescriptionD5,D6,D7,D8 XX A/XX V Rectifier Diode3.2 Circuit Schematic2.3 Fishbone Diagram3.4 Experiments to Reproduce the Failure3.4.1 D5-D8 temperature measurementCondition: 1) The unit operates at ambient temperature; 2) Connecting a xx Ohm resistor between positive and negative terminals of the battery to stimulate very low battery voltage.Result: Case temperature of the diodes stabilizes at about 60 degree Celsius which is much lower than the maximum rating with adequate margin.3.4.2 Battery short circuitCondition: Short circuit the battery and measure the current passes through D5-D8 with current probe.Result: The current is zero3.4.3 Low battery voltageThe unit operates with the DC power provided by a xx V(which is much lower than the nominal xx V) battery. Measure the current passes through D5-D8 and no over-current is found.3.4.4 Over-current through D5-D8 when power on with nominal I/P AC voltage The DC power is provided by a battery with nominal voltage. Measure the current passes through D5-D8 with current probe at the moment when power on the unit with nominal AC input voltage. Over-current is found.3.4.5 High input AC voltage and low battery voltage when power on Connect a xx Ohm resistor between positive and negative terminals of the battery to stimulate very low battery voltage. Measure the current passes through D5-D8 with current probe at the moment when power on the unit with xx AC. The current reaches xx A which is much larger than the maximum ratingxx A and that can easily destroy the diodes.3.5 ConclusionBased on the above experiments, the root cause is that at the moment when power on the unit, especially with low battery voltage and high input AC voltage, out-of-spec current through the diodes presents.4. Containment PlanFix the unit, replace damaged components5. Permanent C/A Plan1) Change Cxx from xx μF/xx V electrolytic capacitor to xx uF/xx V X-Cap to reduce the current through the rectifier when power on the unit.2) Use an integrated rectifier to replace D5-D8.3) RD release ECR for customer approval of the above engineering changes after the effectiveness is verified.4) RD release ECN to validate the changes after the ECR is approved.6. Verify the effectiveness of C/A1) Measure the current through the integrated rectifier at the same condition of 2.4.5, no over-current is found.2) Perform power cycling on 10 engineering changed units under the condition described at 2.4.5 for 48 hours, no failure was found.7. Prevent RecurrenceUpdate the Standard Circuit Design Procedure (Doc. #: xxxxxxxx). Add an item in Section 11 – xx Circuit Design Standard, to require: 1) using X-Cap rather than electrolytic capacitor parallel with the rectifier, and, 2) using integrated rectifier rather than individual diodes in xx circuit design.8. Congratulate the TeamThe ECR has been sent to XXX (the customer name) for approval on Sep. 25. and the updated procedure will be released formally by DCC immediately when receive the approval. Thanks for the excellent work of the team. Date Closed: Sep. 26, 2002。