设备OEE在线监控软件
设备综合效率OEE控制程序

设备综合效率OEE控制程序
1.目的:
为方便管理者宏观查阅生产状况和了解生产信息,机台设备保持良好的正常运转,发现和减少生产中存在的七大浪费损失,针对问题,分析和改善生产状况及产品质量,最大化提高资源和设备的利用率,挖掘出最大的生产潜力。
2.适用范围:
本公司内部所有生产设备。
3.定义:
OEE:综合效率是Overall Equipment Effectiveness,简称OEE。
一般,每一个生产设备都有自己的理论产能,要实现这一理论产能必须保证没有任何干扰和质量损耗。
OEE就是用来表现实际的生产能力相对于理论产能的比率,它是一个独立的测量工具。
4.设备综合管制过程乌龟图:
5.作业内容:。
设备OEE控制程序
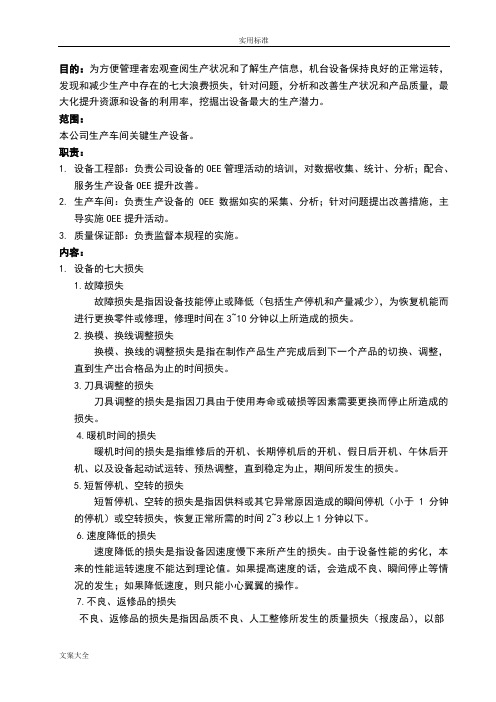
目的:为方便管理者宏观查阅生产状况和了解生产信息,机台设备保持良好的正常运转,发现和减少生产中存在的七大浪费损失,针对问题,分析和改善生产状况和产品质量,最大化提升资源和设备的利用率,挖掘出设备最大的生产潜力。
范围:本公司生产车间关键生产设备。
职责:1.设备工程部:负责公司设备的OEE管理活动的培训,对数据收集、统计、分析;配合、服务生产设备OEE提升改善。
2.生产车间:负责生产设备的OEE数据如实的采集、分析;针对问题提出改善措施,主导实施OEE提升活动。
3.质量保证部:负责监督本规程的实施。
内容:1.设备的七大损失1.故障损失故障损失是指因设备技能停止或降低(包括生产停机和产量减少),为恢复机能而进行更换零件或修理,修理时间在3~10分钟以上所造成的损失。
2.换模、换线调整损失换模、换线的调整损失是指在制作产品生产完成后到下一个产品的切换、调整,直到生产出合格品为止的时间损失。
3.刀具调整的损失刀具调整的损失是指因刀具由于使用寿命或破损等因素需要更换而停止所造成的损失。
4.暖机时间的损失暖机时间的损失是指维修后的开机、长期停机后的开机、假日后开机、午休后开机、以及设备起动试运转、预热调整,直到稳定为止,期间所发生的损失。
5.短暂停机、空转的损失短暂停机、空转的损失是指因供料或其它异常原因造成的瞬间停机(小于1分钟的停机)或空转损失,恢复正常所需的时间2~3秒以上1分钟以下。
6.速度降低的损失速度降低的损失是指设备因速度慢下来所产生的损失。
由于设备性能的劣化,本来的性能运转速度不能达到理论值。
如果提高速度的话,会造成不良、瞬间停止等情况的发生;如果降低速度,则只能小心翼翼的操作。
7.不良、返修品的损失不良、返修品的损失是指因品质不良、人工整修所发生的质量损失(报废品),以部及因人工整修所造成的损失。
在正产运转中制造出没有满足规定品质的不良品或需要修正的不良品,经过修正后还不合格,就当做废品处理。
OEE设备综合效率介绍

OEE设备综合效率介绍OEE的计算方式为:OEE = 设备利用率(Availability)× 性能率(Performance)× 质量率(Quality)设备利用率是指设备实际运行时间与计划运行时间的比值,表示设备的运行稳定程度;性能率是指实际生产数量与理论最大生产数量的比值,反映了设备运行速度和效率;而质量率则是指合格产品数量与实际生产数量的比值,代表了产品质量的好坏。
OEE的优点在于它同时考虑了设备的运行时间、性能和质量三个方面的指标,能够综合评估设备的整体生产效率,从而帮助企业发现生产过程中的瓶颈和问题,并及时采取改善措施。
另外,OEE还可以用来比较不同设备的生产效率,帮助企业选择合适的设备进行生产。
通过对OEE进行监控和分析,企业可以及时了解设备的运行情况,找出影响生产效率的问题和瓶颈,有针对性地进行改善和优化,从而提高设备的生产综合效率,降低生产成本,提升企业的竞争力。
因此,OEE在现代生产管理中具有非常重要的作用,是企业提高生产效率和管理水平的重要工具之一。
OEE(Overall Equipment Effectiveness)是一种广泛应用于制造业的关键绩效指标,它提供了一个全面的视角,帮助企业综合评估设备的生产效率。
通过OEE的监测和分析,制造企业可以更好地了解设备的运行状态,提高设备利用率、性能和产品质量,实现生产成本的优化和效率的提升。
首先,OEE可以帮助企业实现对设备利用率的提高。
设备利用率是指设备实际运行时间与计划运行时间的比值,它反映了设备的运行稳定性和生产中断的程度。
通过对设备的实际运行时间进行监测和分析,企业可以及时发现设备的停机原因和频率,以便有针对性地采取措施进行改善,如提高设备的维护保养质量、减少设备故障率、优化生产计划等,从而提高设备的利用率,减少生产中断,提高生产效率。
其次,OEE还有助于提高设备的性能。
性能率是指实际生产数量与理论最大生产数量的比值,它反映了设备的运行速度和效率。
OEE(设备综合效率)简介

完成停止时间+加班时间
加班时间 实际作业时间
负荷时间:为了完成生产计划、设备必须运转的时间
负荷时间 = 实际作业时间 - 计划停止时间
计划停止时间包含早晚例会、休息时间、始业点检、安全点检、
自主保全、体制展开、试作、计划停止时间等时间
利用时间= 负荷时间-停线时间
负荷时间 实际作业时间
停线时间:工具更换、调整、故障停止、上下流等待、
15
3. 启动/热机调整
• 定义:启动损失是指从设备启动到稳定生产期间发生的质 量损失,损失的大小取决于工序状态的稳定度,设备的 维护水平,操作工的技能水平等。
• 通常在实际生产中,这种损失量还是相当大的,应尽可 能减少到最小程度。
16
4. 短暂停机
• 定义:机器故障停工或换线以外的原因造成的计划停工所损 失的时间。 比如因工件卡堵、倾斜、掉落、污损、不良 警报等,必须进行少于十分钟的停机或空转予以处理的暂停 损失。另外如开工推迟/完工提前等)
OEE(设备综合效率)简介
2014年2月10日
OEE(设备综合效率)的定义
OEE是一个独立的测量工具,它用来表现实际的生产能 力相对于理论产能的比率。其本质就是实际合格产量 与负荷时间内理论产量的比值。
国际上对OEE的定义为: OEE是Overall Equipment Effectiveness的缩写 ,翻 译为设备综合效率,也叫设备整体效率。
14
2. 更换品种(换线)
• 定义 :未经调整的全速的由最后一件产品转入另一种产品的运 作,设备全速运转情况下最后一件良好的产品到另一种第一件 良好的产品间的时间。
• 通过操作员预定系统来测量
• 应对措施 – 运用SMED方法来缩短换线时间(包括运转中更换原材料, 如用新线) – 通过业绩管理来按照标准监控换线时间是否合格 – 实施持续改善行动
生产管理系统软件有哪些

生产管理系统软件有哪些概述在现代企业管理中,生产管理系统软件扮演着重要的角色。
这些软件提供了一种集成化的解决方案,用于管理和监控公司的生产流程。
通过实时监测和分析数据,生产管理系统软件可以帮助企业提高效率、降低成本并优化资源利用率。
本文将介绍一些常见的生产管理系统软件。
1. ERP系统ERP(企业资源规划)系统是一种综合性的软件解决方案,用于整合和管理企业的各个方面,包括生产、销售、采购、库存等。
通过集成不同部门的信息和流程,ERP系统提供了一个统一的平台来监控和管理企业的生产活动。
常见的ERP系统包括SAP、Oracle ERP等。
2. MES系统MES(制造执行系统)是一种用于管理制造过程的软件系统。
它与ERP系统相辅相成,通过监控工厂的实时生产数据和设备状态,提供了更精确的生产计划和调度。
MES系统还可以帮助企业优化生产资源的利用、提高生产效率,并且能够追踪产品的生产历史和质量信息。
常见的MES系统包括Siemens MES、GE Digital MES等。
3. APS系统APS(高级计划与调度)系统是一种用于优化制造计划和调度的软件。
它基于数学模型和算法,根据订单需求、资源约束和生产能力,自动生成最佳的生产计划。
APS系统可以帮助企业在短时间内做出决策,提高订单交付的准确性和及时性。
常见的APS系统包括PTC FlexNet APS、Optessa APS等。
4. WMS系统WMS(仓库管理系统)是一种用于管理和控制仓库操作的软件系统。
它帮助企业实现高效的货物存储、检索和分发,并提供了实时的库存信息。
WMS系统可以帮助企业减少库存成本、提高订单的处理速度,并确保准确无误地执行物流操作。
常见的WMS系统包括IBM WMS、JDA WMS等。
5. OEE系统OEE(设备效率评估)系统是一种用于评估和改善生产设备效率的软件系统。
它通过监测设备的运行时间、停机时间和生产质量,计算并分析OEE指标,帮助企业识别和解决生产过程中的瓶颈和问题。
最新OEE(设备综合效率)简介
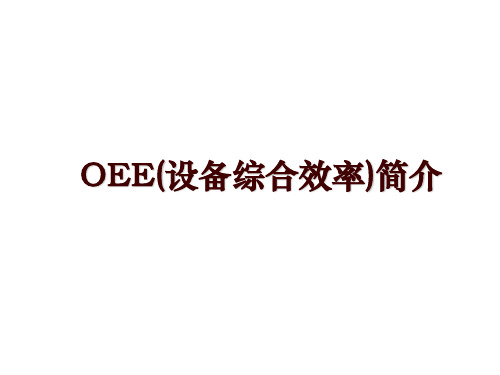
= (产量×实际速度)/利用时间
• 设备性能率
= 速度开动率×净开动率 = (产量×设计速度)/利用时间
*需按照不同设计速度的规格折算
名词说明
计划作业时间=从事生产活动的时间 (上,下班时间)减去午休时间
作业时间 计划作业时间 午休时间
实际作业时间= 计划作业时间-生产
生产完成停止时间
计划不均衡 : 前后计划中由于别的因素引起的作业停止或 者担当设备后工程(设备)的生产数量或者目标 量已达成而停止情况的时间
其 它 : 由以上原因以外的原因引发的设备停止时间
设备综合效率的应用
(1) 适用对象
作业对象 设备 设备 + 人
人
适用范围 一定适用 部分适用 适用不了
备
注
以设备效率为参照的生产力管理
1.计划性停机和试车 2.无生产订单
操作时间
计划性 停产时间
负荷时间
用餐 时间
(有效)利用时间
停机损失
1.故障 2.更换品种 / 清洁
/ 调节/刀具调整 3.启动 / 热机、调整
设备综合效率
时间利用率
净利用时间 性能损失
创造价值 缺陷 的时间 损失
4.短暂停机 / 空转 5.速度减慢损失
6.质量缺陷返工
15
3. 启动/热机调整
• 定义:启动损失是指从设备启动到稳定生产期间发生的质 量损失,损失的大小取决于工序状态的稳定度,设备的 维护水平,操作工的技能水平等。
• 通常在实际生产中,这种损失量还是相当大的,应尽可 能减少到最小程度。
16
4. 短暂停机
• 定义:机器故障停工或换线以外的原因造成的计划停工所损 失的时间。 比如因工件卡堵、倾斜、掉落、污损、不良 警报等,必须进行少于十分钟的停机或空转予以处理的暂停 损失。另外如开工推迟/完工提前等)
ANDON系统在设备故障OEE中的应用

ANDON系统在设备故障OEE中的应用
摘要:生产设备作为一个公司最重要的资产之一,提高设备的利用率及产能,并降低产品的废品率,在目前制造业面临成本逐步提高的形势下,无疑是帮助企业提高利润、降低成本的一个重要途径.而ANDON系统作为车间生产异常监控管理系统,可以对生产设备的故障、停机等问题进行实时监控与报警,是设备管理的一个非常重要的工具.
OEE系统功能
•设备数据采集:自动采集的数据类型包括:产量信息、设备的停机信息(如停机时间、停机次数等);
•数据的监控及分析:采用各类的统计方法,对数据进行现场的即时监控及分析;
•汇总看板:采用大尺寸显示终端(如液晶电视)在公共办公区域对所有汇总信息以看板的方式进行显示;
•管理报表工具:对历史及当前数据进行汇总查询,为管理者提供决策依据;
ANDON系统在OEE中的应用
在OEE设备管理中,我们可以利用ANDON系统来收集设备的故障、停线等异常问题,一旦出现设备异常时,ANDON系统能及时报警通知相关设备维护人员到现场解决问题,不但可以减少设备停机时间,而且可以提高整个生产设备的利用率及产能.
说明:
•计划生产时间:在数据采集模块中,通过点击生产任务开始、结束,记录计划生产时间;
•异常停机时间:当异常产生时,点击异常相关按钮,触发异常开始时间,当解除异常,点击异常关闭,记录异常停止时间;OEE与ANDON系统相结合应用于生产车间应用示例图:。
设备OEE计算方法介绍

设备OEE计算方法介绍设备OEE的计算方法主要包括三个部分:设备的利用率(Availability)、生产质量(Quality)和生产速度(Performance)。
首先是设备的利用率,它指的是设备实际运行时间与计划运行时间之比。
设备的实际运行时间包括设备的开机时间、停机时间和换线时间等,而计划运行时间则是设备在生产计划中应该运行的时间。
设备的利用率可以通过下面的公式来计算:设备利用率=(设备实际运行时间/计划运行时间)*100%。
其次是生产质量,它指的是设备生产的合格产品数量与实际生产产品数量之比。
生产质量可以通过下面的公式来计算:生产质量=(合格产品数量/实际生产产品数量)*100%。
最后是生产速度,它指的是设备实际生产速度与标准生产速度之比。
生产速度可以通过下面的公式来计算:生产速度=(设备实际生产速度/标准生产速度)*100%。
综合考虑设备的利用率、生产质量和生产速度,设备的OEE可以通过下面的公式来计算:设备OEE=设备利用率*生产质量*生产速度*100%。
通过计算设备OEE,企业可以发现设备的运行效率问题并采取相应的改进措施,从而提高设备的生产效率和降低生产成本。
因此,设备OEE计算是企业生产管理中非常重要的一项工作。
设备OEE(Overall Equipment Effectiveness)是一项非常重要的生产管理指标,它可以帮助企业全面评估生产设备的运行效率,并发现潜在的瓶颈和改进点。
设备OEE计算是企业生产管理中的一项关键工作,通过计算设备OEE,企业可以进一步优化生产流程、提高设备利用率、增强生产质量、降低成本和改进生产速度。
下面将继续介绍相关内容。
设备OEE计算方法的特点是综合评估设备运行效率的各个方面,从设备利用率、生产质量和生产速度这三个方面来进行全面评估,从而提供了一个全面的视角来了解设备的实际运行情况。
因此,设备OEE是综合性指标,需要全面收集和分析各项数据。
企业需要建立完善的数据采集和统计系统,确保能够准确、及时地获取设备的运行数据。
OEE(设备综合效率)分析与管理ppt课件

运行缓慢
库存水平
最新课件
OEE衡量的是礁 石的大小,说明 应该先从哪块暗 礁着手处理。
24
8.OEE可带来的管理效益
1.企业规划: A、可以为企业规划提供客观科學的決策依据。 B、可以为企业提供很多的增值意見和建议。
2.生产管理: A、现场实时数据的收集,建立监控管理系统。 B、对OEE数据分析,规避潜在风险,降低设备六大损失,挖
掘设备最大潜能。 C、为企业精益生产管理提供可视化的生产報告。
最新课件
25
三、OEE的计算方法
2012-8-22
最新课件
26
1.一般企业的时间分类
最新课件
27
1.一般企业的时间分类
最新课件
28
1.一般企业的时间分类
最新课件
29
2.OEE时间分析
最新课件
30
3.设备的六大损失和OEE的关系
最新课件
9
设备运转过快容易造成故障
最新课件
10
您是不是正在制造一个不合格产品
最新课件
11
早晨机器的启动需要花去一定的时间
最新课件
12
二、OEE的定义及开展目的
最新课件
13
1.OEE是什么?
• OEE代表整体设备效能; • 这是一种严格的机器总体性能的衡量手段,揭示时间浪费存
在于哪里,统计各种时间浪费,目的在于实现改进。
最新课件
48
故障是冰山的一角
“如果我们问一问为什么会发生这样的情况——为什么、为什 么、—— 我们通常能找出问题,以及解决问题的方法。
最新课件
49
故障是冰山的一角
故故障障
•灰•灰尘尘、、污污垢垢、、原原料料粘粘附附 •磨•磨损损、、偏偏斜斜、、松松动动、、泄泄露露 •腐•腐蚀蚀、、变变形形、、伤伤痕痕、、裂裂纹纹 •温•温度度、、震震动动、、声声音音等等异异常常
EZVMS客户端用户手册User_Manual_CS_EZVMS_Chs_B200

说明,对操作内容的描述进行必要的补充和说明
ii
目录
1 产品介绍·························································································································1 2 安装·······························································································································1
i
7.3 界面介绍····················································································································19 7.4 录像查询····················································································································20 7.5 智能检索····················································································································20 7.6 事件录像回放··············································································································21 7.7 智能录像回放··············································································································22 7.8 录像播放····················································································································23 7.9 回放控制····················································································································23
OEE 简介

随着市场竞争的日益激烈,制造商要想持续的获得高的经济效益,最大化的挖掘和改善。
生产车间的生产效率显得极其重要,在某些方面,它甚至成为企业是否可以赢利的决定性因素。
然而,在现在的制造业中,看似良好运作的生产车间实际上并没有以最好的状态进行工作,设备和操作人员的价值存在很大的改善空间,这无形中为企业带来了巨大的损失。
为了解决这一问题,国际制造业提出了全局设备效率(OEE)的概念。
什么是设备综合效率OEE?设备综合效率是Overall Equipment Effectiveness,简称OEE。
一般,每一个生产设备都有自己的理论产能,要实现这一理论产能必须保证没有任何干扰和质量损耗。
它是一种严格的机器总体性能的衡量手段,提示时间浪费存在于哪里,统计各种时间浪费的目的在于实现改进。
OEE的应用范围1、机台设备的OEE(单个的设备)•单个设备所对应的相同机种相同工序•单个设备所对庆的不同机种相同工序•单个设备所对应的相同机种不同工序2、非机台设备的OEE(一条生产线、一个工作站),以人为标准:•相同机种相同工序;•不同机种相同工序;•相同机种不同工序。
3、整个工厂的综合效率实行OEE的作用•方便领导宏观查阅生产状况和了解生产信息。
•使机台设备保持良好的正常运转。
•使人力与机台设备科学配合,发挥出最大化的潜能。
•可以帮助管理者发现和减少生产中存在的六大损失。
•可以征对问题,分析和改善生产状况及产品质量。
•能最大化提高资源和设备的利用率,挖掘出最大的生产潜力。
实行OEE的效益1、企业规划:•可以为企业规划提供客观科学的决策依据。
•可以为企业提供很多的增值意见和建义。
2、生产管理:•能收集到生产线的实时数据,以便建立车间监控管理系统。
•能分析/跟踪生产线设备的有效利用情况,以便最大化挖掘设备生产潜力。
•能分析/跟踪产在线的潜在风险和六大损失,以便降低生产成本、提高生产力。
•能为企业精益生产管理提供可视化的生产报告。
OEE(设备整体效能)

面反映设备的综合表现。
03
OEE的计算公式为:OEE = 时间利用率 * 性能指数 *
质量指数。
OEE的重要性
01
02
03
提高生产效率
通过提高设备的OEE,可 以减少停机时间和浪费, 提高生产效率。
降低生产成本
OEE的提高意味着设备利 用率的提高,从而降低生 产成本。
提高产品质量
通过提高设备的性能和效 率,可以减少不良品和废 品,提高产品质量。
OEE的组成部分
时间利用率
01
衡量设备可用性的指标,反映了设备在计划停机时间和非计划
停机时间内的表现。
性能指数
02
衡量设备性能的指标,反映了设备在单位时间内完成的有效工
作量。
质量指数
03
衡量设备生产出的产品质量水平的指标,反映了设备生产出的
产品合格率。
02 影响OEE的主要因素
设备故障
故障频率
备件管理和库存优化
合理管理备件库存,确保备件供应及时可靠,减少因备件不足或等 待时间过长而导致的停机时间。
THANKS FOR WATCHING
感谢您的观看
通过实验和数据分析,优化设备运行参数, 提高设备运行效率。
自动化与智能化
引入自动化和智能化技术,减轻人工操作负 担,提高设备运行精度和稳定性。
工艺改进
不断改进和优化工艺流程,提高产品质量和 生产效率。
标准化操作
制定标准操作规程,规范操作人员的操作行 为,确保设备稳定运行。
提升产品质量控制
严格把控原料质量
制定改进计划
根据数据分析结果和改进措施,制定详细的改进计划, 包括改进目标、实施步骤、时间安排等。
实施改进计划
OEE(设备综合效率)简介

群蛙中没有谁相信这些小小的青蛙会到达塔顶,
• 应对措施 – 通过往常和不断的数据记录和分析了解工艺流程的变化特征 – 运用根源问题解决工具(如5个为什么,问题解决表,鱼骨表以 及PDCA) – 向造成质量问题的有关人员反馈质量问题
19
使用OEE时的注意事项
!
• OEE要应用在一台机器上(可视为一台机器的 生产线)而不能应用在整个生产线或全厂上,这 样才有意义
设备综合效率 = 时间利用率 ×设备性能率 ×合格率 = 0.88 × 0.909 × 0.95 × 100 = 75.9%
提升设备综合效率
时间利用率
➢设备短暂停工零化 ➢TPM改善活动 ➢设备开动损失递减 ➢换模调整损失递减 ➢设备故障零化
设备性能率
合格率
➢临时停止、速度损 失显现化活动
➢性能提升改善活动
< 设备综合效率的计算 例2>
单独设备 INPUT(投入)
设 备 OUTPUT(产出)
2月 2日 作业日报
A MODEL
理论 Cycle Time : 2分 制订者 : ○○○
作业时间 : 580分
负荷时间 : 500分
80分
教育 : 60分, 工休 : 20分
利用时间 : 440分 60分
故障 : 30分, 更换治具: 30分
• 净开动率
= (产量×实际速度)/利用时间
• 设备性能率
= 速度开动率×净开动率 = (产量×设计速度)/利用时间
*需按照不同设计速度的规格折算
名词说明
计划作业时间=从事生产活动的时间 (上,下班时间)减去午休时间
设备总效率—OEE
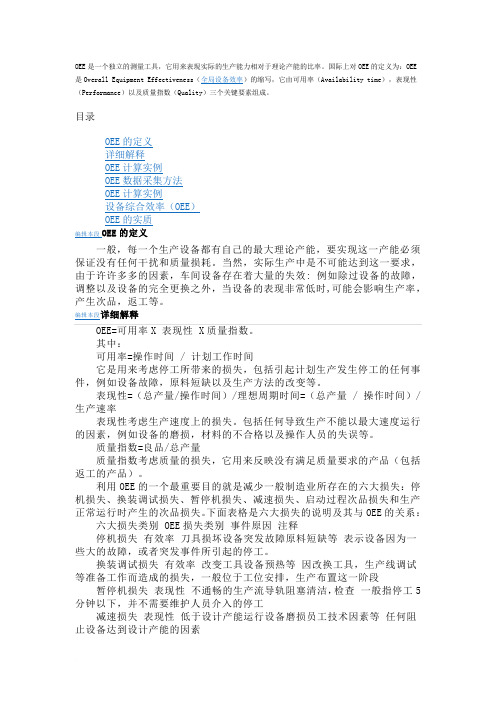
OEE是一个独立的测量工具,它用来表现实际的生产能力相对于理论产能的比率。
国际上对OEE的定义为:OEE是Overall Equipment Effectiveness(全局设备效率)的缩写,它由可用率(Availability time),表现性(Performance)以及质量指数(Quality)三个关键要素组成。
目录OEE的定义详细解释OEE计算实例OEE数据采集方法OEE计算实例设备综合效率(OEE)OEE的实质编辑本段OEE的定义一般,每一个生产设备都有自己的最大理论产能,要实现这一产能必须保证没有任何干扰和质量损耗。
当然,实际生产中是不可能达到这一要求,由于许许多多的因素,车间设备存在着大量的失效: 例如除过设备的故障,调整以及设备的完全更换之外,当设备的表现非常低时,可能会影响生产率,产生次品,返工等。
编辑本段详细解释OEE=可用率X 表现性 X质量指数。
其中:可用率=操作时间 / 计划工作时间它是用来考虑停工所带来的损失,包括引起计划生产发生停工的任何事件,例如设备故障,原料短缺以及生产方法的改变等。
表现性=(总产量/操作时间)/理想周期时间=(总产量 / 操作时间)/ 生产速率表现性考虑生产速度上的损失。
包括任何导致生产不能以最大速度运行的因素,例如设备的磨损,材料的不合格以及操作人员的失误等。
质量指数=良品/总产量质量指数考虑质量的损失,它用来反映没有满足质量要求的产品(包括返工的产品)。
利用OEE的一个最重要目的就是减少一般制造业所存在的六大损失:停机损失、换装调试损失、暂停机损失、减速损失、启动过程次品损失和生产正常运行时产生的次品损失。
下面表格是六大损失的说明及其与OEE的关系:六大损失类别 OEE损失类别事件原因注释停机损失有效率刀具损坏设备突发故障原料短缺等表示设备因为一些大的故障,或者突发事件所引起的停工。
换装调试损失有效率改变工具设备预热等因改换工具,生产线调试等准备工作而造成的损失,一般位于工位安排,生产布置这一阶段暂停机损失表现性不通畅的生产流导轨阻塞清洁,检查一般指停工5分钟以下,并不需要维护人员介入的停工减速损失表现性低于设计产能运行设备磨损员工技术因素等任何阻止设备达到设计产能的因素启动过程次品损失质量指数报废、重工等设备预热,调节等生产正式运行之前产生的次品生产过程次品损失质量指数报废、重工等生产稳定进行时产生的次品表一六大损失与OEE的关系编辑本段OEE计算实例我们举一个例子来说明OEE的计算方法:设某设备某天工作时间为8h, 班前计划停机15min, 故障停机30min,设备调整25min, 产品的理论加工周期为0.6 min/件, 一天共加工产品450件, 有20件废品, 求这台设备的OEE。
设备综合效率(OEE)

型号
A B C D
产能(个/分 ) 63 60 60 79
生产数量
12600 12000 15000 13790
不良品
180 160 150 188
设备 LOSS的构造和指标
设备
6大 LOSS
管理指标
作业时间
负荷时间
计划 维持
开动时 间
停止 LOSS
纯开动时间
速度 LOSS
价 值 不良 加动时间 LOSS
通过8大损失计算TEEP
设备
八大损失
利用率计算
负荷时间
计划停机 外部因素
设备 利用率
=
工作时间 开动时间
停
开动时间
机 损
失
净开动
速
时间
度
损
失
设备故障 安装调整
空转短暂 停机 速度降低
时间 开动率
=
性能 开动率
=
有价 废 值开 品 动时 损 间失
加工废品
初期未 达产
合格 品率
=
产能利用率TEEP=设备利用率×OEE
间
管理损失
运作损失
生产线管理损失
后勤和运输
测量和调节损失
能源损失
成
备品备件损失
原材料损失
本
联合利华世界500强在经过近10年的OEE的管理,2010年 才从12大损失向16大损失迈进。
其中它是先做6大损失到9大损失到12大损失不断的摸索中 才有今天的成绩。数据显示联合利华洗衣粉的产量从2004年 日产260T/D到2010年日产近1000T/D。其中生产机器只增加 了50%。在OEE的数据支撑下结合一些优良的管理方法再 加上公司员工的群策群力下设备的效率平均提高了48.6%。
OEE设备综合效率
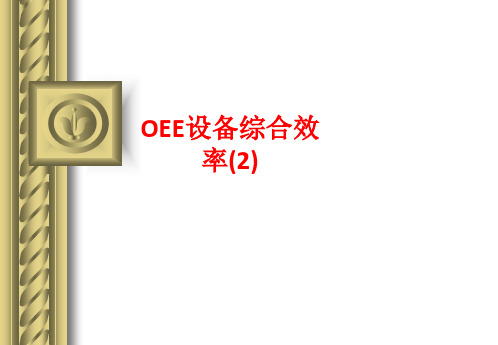
50 0
811 3.0 3.0
0 808
A6
98.63
97.81
72.57
72.73
99.52 71.23
99.63 70.88
Line A
292 318 246880 248178 1298
小时
4320
72
3276
55
1044
17
38
1
0
0
16
00Leabharlann 02200
0
0
0
1006
17
225
4
按照日本工程师学会(JIPE),TPM有如下定义:
(1)以最高旳设备综合效率为效率目旳;
(2)确立以设备一生为目旳旳全系统旳预防维修;
0
0
69
1
57
1
0
0
780
13
4
0
4
0
0
0
776
13
Line A
96.32
77.58
99.48 74.34
速度以有效操作时间为 权重加权计算
时间以合格品产量为权 重加权计算
OEE 新系统
OEE 新系统
OEE 新系统
为何要使用OEE
TPM 能够称为“全员参加旳生产力旳
管理和维护”或“带有日本特色旳美式旳 生产维修”。
OEE 旳时间利用表达图
720 总时间
690 操作时间
计划停 产时间
660 负荷时间 630 利用时间
停产时 间
吃饭时 间
600 净利用时间
效率停 产时间
有价值时间 590
不合格质量 停产时间
oee产品数据采集待机定义

oee产品数据采集待机定义一、OEE的作用1、通过设备数据采集,实时获取设备的运行信息,监控所有联网设备的状态变化过程2、并通过统计分析,展示设备工作历时数据,以支持设备管理人员分析设备利用率情况,制定对应的的改善策略二、设备生产总时间的组成Productive:Machine Running OutputEngg:Engineering TimeSchedule D/T:PM / MSA(计划保养)No WIP:No MaterialStandby:Stand ByIdle:Idle TimeSetup:Setup / ConversionQA:Quality AssuranceDowntime:Machine Repair Time三、OEE是什么呢OEE - Overall Equipment Efficiency(设备综合效率)OEE的计算公式生产的实际时间=Productive + Engg总时间=Productive + Engg + Schedule D/T + No WIP + Standby + Idle + Setup + QA + DowntimeOEE=生产的实际时间 / (总时间 - Schedule D/T Downtime)四、OPE是什么呢OPE-Overall Production Efficiency(整体生产效率)OPE的计算公式生产的实际时间=Productive + Engg总时间=Productive + Engg + Schedule D/T + No WIP + Standby +I dle + Setup + QA + DowntimeOPE=生产的实际时间 / (总时间-Schedule D/T Downtime-No WIP Time)五、OEE / OPE 公式Total Time = 24 HLoading Time(计划生产时间) = Total Time - Schedule D/T - No WIP - Power Off - EnggOperating Time(总的作业) = Loading Time - Waiting for Repair - Repair - QA - Waiting for Setup - Setup Nett Operating Time(最终实际作业) = Operating Time - Idle - Alarm - Stoppages - MFG LossUtilization(设备总利用率) = (Loading Time * 100 ) / Total TimeAvailability(设备实际利用率) =(Operating Time * 100) / Loading TimePerformance Efficiency(设备作业效率) =(Nett OperatingTime * 100)/ Operating Time。
- 1、下载文档前请自行甄别文档内容的完整性,平台不提供额外的编辑、内容补充、找答案等附加服务。
- 2、"仅部分预览"的文档,不可在线预览部分如存在完整性等问题,可反馈申请退款(可完整预览的文档不适用该条件!)。
- 3、如文档侵犯您的权益,请联系客服反馈,我们会尽快为您处理(人工客服工作时间:9:00-18:30)。
设备OEE在线监控软件
摘要:为方便设备管理人员能在办公室中随时掌握设备状况,及时进行设备的维护,这时我们有必要引入一套设备OEE在线监控软件来实现对设备的全面管理,保证提高设备的综合使用效率。
为了将工厂传统的人工记录OEE改成在线自动记录,大部分企业都开始引入一套OEE在线监控软件,希望可以满足以下基本功能:
∙自动记录追踪每次停机;
∙将OEE损失原因归类并进行分析;
∙自动产生OEE日报表;
∙OEE数据与ERP系统连接。
QSmart OEE在线监控软件,是由太友科技研发的一套成熟的设备管理监控软件,以精益生产、TPM、JIT 等先进理论为基础,用于监控与分析制造车间的生产设备。
其网络结构示意图如下:
∙自动代替人工:代替大多数工厂手工记录与统计OEE的方式,用自动采集与统计的方式获得准确真实的生产数据;
∙实时监测,资源共享:管理人员在办公室就可实时监控生产状况,随时查询报表,发现生产异常;∙报表全面,提供明确改善方向:包括设备综合效率总报表、设备停机报表、设备损失分析报表、设备停机时间明细报表等。