PFMEA 硅胶产品射出成型
塑胶射出PFMEA样本
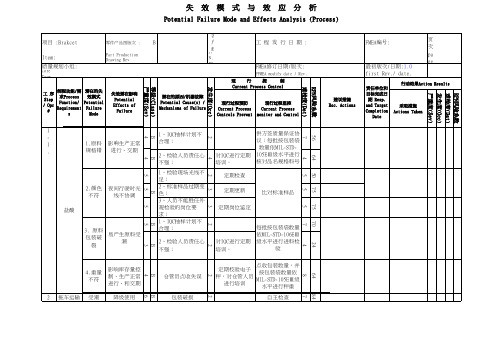
126
98
2 2 3 2
9 8 6 4
7
2
7
112 90 32
受潮 包材储存 数量不 够 受潮 4 拖车运输 包装破 损
降级使用 B 4 B 4 影响生产 B 4 降级使用 原料撒落 B 3 B 3 4 2 2 2 2 2
112 40 32 42 42 48
7 5 4 7 7 8
失
效
模
式
与
效
应
分
析
64
B 4 B 6
2
8
84
包装破损
2
7
失
效
模
式
与
效
应
分
析
Potential Failure Mode and Effects Analysis (Process)
项目 :Brakcet Item: 质量规划小组:
Core Team
零件产品图版次 :
B
客户料号:
P/N.number
工 程 发 行 日 期 :
失
效
模
式
与
效
应
分
析
Potential Failure Mode and Effects Analysis (Process)
项目 :Brakcet Item: 质量规划小组:
Core Team
零件产品图版次 :
B
客户料号:
P/N.number
工 程 发 行 日 期 :
FMEA编号:
页次 page
Part Production Drawing Rev
严重度(Sev)
发生度(Occ)
难检度(Det)
RPN风险系数
射出成型的充填过程
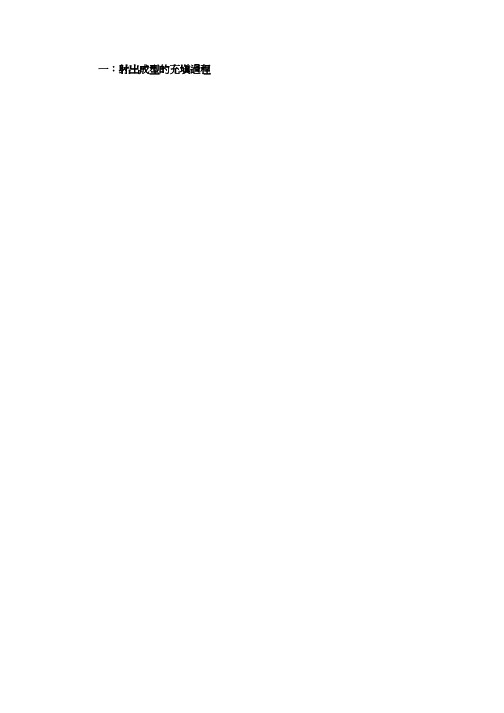
一:射出成型的充填過程射出成型的充填過程(Filling Stage)指的是塑料填模(Mold Filling)的過程。
在射出機的動作上,射出機射嘴(Nozzle)開啟,處於鬆退狀態螺桿向前推進,將位於儲料區(Reservoir)已塑化(Plasticated)完畢而呈現熔膠(Melt )狀態的塑料射進模穴中。
對於單模穴(Single Cavity)模具,塑料熔膠通常透過注道(Sprue,或叫豎流道)由澆口(Gate)填入模穴或模腔(Cavity)中;對於多模穴(Multi-Cavity)模具通常需利用流道系統將塑料分配到各模穴中。
通常螺桿依設定的行程曲線(Ram-Speed Profile)以及射壓曲線(Injection Pressure)前進,由於塑料黏度甚高,因此加工溫度需高於熔點(一般在180oC以上);射壓(指射嘴處壓力)高達150~250MPa (也就是1500~2500 atm 或or 21,000~36,000 psi)。
模溫一般採用冷模(如60oC)。
充填時間短則0.5秒~1秒;長則5~10秒,視模穴數目及模具大小而定。
在充填過程中,由於模穴尚未填滿,塑料前緣為大氣壓狀態(或是抽真空)。
在正常充填過程下,若射壓夠高,塑料將以設定的流量曲線(或是螺桿行程曲線)順利填模。
此階段稱為流率控制 (Flow-Rate Controlling ) 階段。
但隨著充填範圍增加,塑料填模的流動阻力將逐漸增加,反映出來的就是模穴壓力(Cavity Pressure)的增加。
模穴壓力是一種背壓(Back Pressure),是塑料流動阻力的表徵:模穴壓上升越快,代表流動阻力越大。
塑料在充填過程中需能克服流動阻力迅速填滿模穴;否則若射壓不足,射速不夠,流動就會停止造成短射(Short Shot)。
在模穴將填滿時,模穴壓會發生上昇的現象,此時已經難以流率控制螺桿前進。
一般會將操作切換至壓力控制(Pressure-Controlling)階段,而操作過程也切換至保壓(Packing)階段。
射出成型不良对策
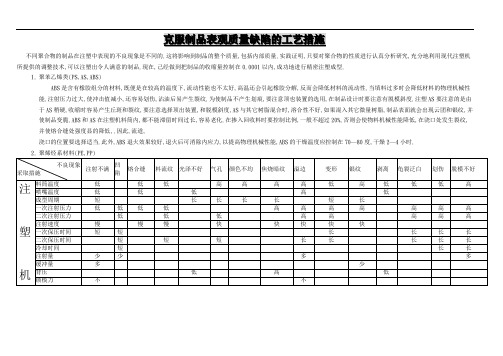
不同聚合物的制品在注塑中表现的不良现象是不同的.这将影响到制品的整个质量,包括内部质量.实践证明,只要对聚合物的性质进行认真分析研究,充分地利用现代注塑机所提供的调整技术,可以注塑出令人满意的制品.现在,己经做到把制品的收缩量控制在0.0001以内,成功地进行精密注塑成型.1.聚苯乙烯类(PS,AS,ABS)ABS是含有橡胶组分的材料,既便是在较高的温度下,流动性能也不太好,高温还会引起橡胶分解,反而会降低材料的流动性.当填料过多时会降低材料的物理机械性能.注射压力过大,使冲击值减小,还容易划伤,沾油后易产生裂纹.为使制品不产生划痕,要注意顶也装置的选用,在制品设计时要注意有脱模斜度.注塑AS要注意的是由于AS稍硬,收缩时容易产生丘斑和裂纹,要注意选择顶出装置,和脱模斜度,AS与其它树脂混合时,溶合性不好,如果混入其它微量树脂,制品表面就会出现云团和银纹,并使制品变脆.ABS和AS在注塑机料筒内,都不能滞留时间过长,容易老化.在掺入回收料时要控制比例,一般不超过20%,否则会使物料机械性能降低,在浇口处发生裂纹,并使熔合缝处强度显的降低,.因此,流道,浇口的位置要选择适当.此外,ABS退火效果较好,退火后可消除内应力,以提高物理机械性能,ABS的干燥温度应控制在70—80度,干燥2—4小时.2.聚烯烃系材料(PE,PP)聚烯烃系材料的流动性能好,PP的流动性比PE更好.加工此类制品要注意,由收缩而引起的翘曲和扭转变形.防止翘曲的办法一般采用多点浇口,保证熔体流畅,在树脂中加入适量的加剂,在制品设计时,要充分地注意克服收缩,翘曲和扭转等要素,要重视制品的冷却方法,,应尽量保证冷却速度的昀匀一致,减少翘曲变形.此外,用退火可消除制件收缩不均,降低型芯温度和提高模腔温度可改善缩颈现象,.制品的翘曲程度还与颜料有关,如加入TAI菁系颜料容易使高分子取向,会加剧收缩.3.丙烯酸酯系材料(PMMA)此类材料粘度较高,流动性较高.充模速率对粘度影响大,但过高的充模速度会产生旋涡,过低的充模速度会使制品的熔合缝明显并发生流纹.PMMA类制品的收缩率随模腔压力变化显.着对PMMA类制品要注意对光折射率的要,降低熔体温度,提高注射压力会增加取向效应,产生较大的折射率,既便是退炎也不能改善.但适当地提高模具温度可改善光的折射率.加工PMMA类模具的流道和浇口,应适当地放大些,就这样一方面使熔体流动通畅,同时还起到冷料井的作用.此外,加入回收料不宜太多,一般在20-30%之间,否则会发生银纹等不良现象,回收料和新料都要进行干燥,干燥温度75-90度,干燥4-6小时为宜.4.聚XIAN 胺系(PA类)尼龙类材料熔点明显,熔融温度范围窄,特别是尼龙66,粘度低浇口对粘度景响小,比热容大,因此采用稍大直径的料筒为宜.加工PA系料宜采用阀式喷嘴,这样容易控制流延.由于模具温度较低,传热快,喷嘴处一定要安装加热器.注塑PA制品使模具温度低些,有利于提高制品强度,但制品的尺寸精度会降低.当采用快速充模时,既要考虑排气氯槽,又要注意溢边,模具上附眷的水氯泡必须清除,否则会影响脱模质量.此外,回收料的掺入量可达20%,但吸湿后的边角必须用热风干燥2夜才能使用,PA类料易吸水膨胀,而干燥后又易收缩,为改善收缩常加入玻璃纤维填料.PA类干燥温度一般置于80-90度温度下干燥下20-50小时为宜,用真空干燥效果较好.为了防止飞边适宜使用较精密的模具和控制精度较高的注塑机.5.聚甲醛(POM)POM熔体的温度对流动性能影响小,而提高注射压力和模具温度却对流动性影响较大,因此要设计流动阴力小的流道和浇口,为使喷嘴畅通不要采用伐式喷嘴.POM注塑制口的尺寸误差,除用注塑机的缓冲量,保压时间,模具温度等因素控制外,还要注意模具浇口的尺寸对制品误差有较大的影响,浇口尺寸小误差有加大趋势.聚甲醛制品在浇口附近容易发生缺陷,但提高浇口处的温度或适当降低注射速度能使表面质量得到改善.聚甲醛制品容易产生气泡,必须设计排气口.此外,在清洗聚甲醛余料筒时,要用聚乙烯清洗,但不要用聚氯乙烯,或混入其它酸性颜料清洗,否则会促进聚甲醛分解,聚甲醛在190度友上不能长时间的停留,因为易扫解.聚甲醛物料的干燥温度一般在80-90度,干燥3-6小时.6.聚碳酸酯(PC)聚碳酸酯熔点比较高,因此当注射速度低时,在浇品处易生成波纹.温度控制要严格,尤其在喷嘴和流道中的熔料温度不能降低.模具流道和浇口的阻力要小,模具温度要高些,当模具温度低于80度时,制品的物理机械性能会降低.若脱模困难而用强制顶出时制品容易产生内应力,也会使物理机械性能下降.在聚碳酸酯物料中含有水分时,会严重影响流动性,并性能下降,因此必须干燥:一般在110-120温度下干燥6-15小时,干燥料斗最好在100度恒温下.此外在成型过程中停机时,料筒宜在150度左右关上加热器,成型结束后用聚苯乙烯或乙烯清洗料筒.7.聚氯乙烯系材料( PVC)聚氯乙烯属于热稳定性较差的物料,它的熔融温度矣分解温度很接近,因此必须严格地控制料筒的温度:PVC一般成型温度为198-204度,不要超过215度.特别要注意对料筒中段温度的控制,多数利用螺杆式注塑机加工有利,因为可用螺杆剪切作用产生自生热,用外部加热器补偿热耗散,维持热平衡.注塑 PVC制品时,要尽量使浇口冻封的缓慢些,但熔体温度要太高,低些为宜,可适当提高注射压力而注射速度不可太高,以避免物料产生流纹或分解.要特别注意物料分解,若发现分解时, 应清洗料筒和喷嘴.操作结束时,料筒内的余料要全部挤出后再用PE或PS清洗.操作开始时先对空注射一下再预塑,但不是每次都做.此外,还要注意料筒和模具都容易被氯化氢腐蚀,料筒及模具表面都要镀铬或选用特殊耐腐蚀的材料.8.线型聚酯(PET.PBT)注塑线型聚酯材料时,要注意的是温度比压力对物料流动性能影响大,所以适当地提高熔体温度有利于充模,但注意过高的温度会使物料分解出有害气体,并降低制口物理机械性能,物料在料筒中停留时间不能长.加工线型聚酯时,模具温度要适当提高些,因为在模具温度处在较低情况下得到的制品,在以后较高的温度下使用时会发生翘曲变形,模具温度不合适时,制品表面常出现麻面,使脱模发生困难.模具要开设排气槽,特别注塑玻璃纤维增强的制品时更要开设好,因为玻璃纤维的处理剂容易产生气体.此外,线型聚酯类物料注塑要充分干燥,否则会降低物理机械性能,一般干燥温度在九十至一百四拾度,干燥时间为四至15小时,若使用再生料时,比例应控制在20%.使用后用PE或PP清洗料筒,特别是将要加工PA,PC,PVC类物料时,更要充分地清洗.材料选择:在大多数的塑料制的结构设计中,材料力尝学强度,耐热性能,耐寒性(低温冷脆性),化学稳定性(耐腐蚀性和环境应力开裂性能),吸湿性(吸湿膨胀和吸湿率),收缩率以及颜色和材料价格等都是非常重要的.在选择聚合物的种类和牌号时,首先考虑应该是力学性能:弹性模量(温度,时间,载荷),持久强度.一般注塑制品难以得到象金属制品那样准确的精度,其理由是:热胀系数大,成型收缩,长时间放置有变化,受温度及环影响,通过模具难以控制确定尺寸,受模具制造误差影响.制品主要尺寸的确定1.制品壁厚制品厚度的大小将影响制品的力学性能,收缩程度(尺寸精度),成型周期,材料和能量消耗,最终要决定生产率和生产成本.因此设计原则是满足制品力学性能和良好充模流动前提下,尽可能减小制品厚度.减小零件的平均壁厚是减少其成型周期,提高生产率,补偿较高材料费用消的重要措施.最小壁厚的确定首先应满足力学性能,其次还必须保证聚合物熔体在如此薄的模具型腔内流动,而模具型腔又是低温的,因此制品最小厚度与聚合物熔融粘度,制品大小,流动长度以及注塑工艺条件有关,如果聚合物流动性差,制品小,型腔薄,流道长,则不能充满型腔.在制品的拐角处,圆角R和厚度a 之比称径厚比.径厚比从0.1增至0.6时,则应力集中系数从3降至1.5,也就是说径厚比增加6倍,则应力集中减小50%.0.6为最佳径厚比,考虑具体结构时,径厚比应在0.25-0.6之间取值.2.脱模斜度和筋制品在型腔中冷却后和凸模之间要产生很大的内摩擦力,强制顶出会造成制品变形,内应力也会使表面擦伤,影响表观质量,为此制品应设计一定的拔模斜度,外表面,内表面,孔(深度小于 1.5d),加强筋,凸缘等的斜度与锥度均不同.孔的最小尺寸:孔太小加工困难,太大则收缩大,螺纹孔的最小尺寸和制品厚度关系略.金属嵌件:因为热塑性聚合物的热膨胀系数约比钢大9-11倍,比铝大4倍,所以金属嵌件会妨碍聚合物熔体的收缩,由此而产生的拉应力引起嵌件处的制品开裂,嵌件周围制品壁厚度应设计大些,应依不同聚合物及其直径大小而异.对于聚苯乙烯,一般不宜设定金属嵌件,聚碳酸酯的嵌件周围物料厚度应大于嵌件直径,聚甲醛则应大于直径一半.1.外观的改善1)壁厚均匀是制品设计最基本要求,要消除局部壁厚过大现象.2)把弧立的筋改为数个小筋,如果连成格子,强度会显著增加.3)厚壁结构改用的筋的结构,使在受力方向延长筋更好1)边框补强,对于箱体制品,改善变形有明显效果.2)对于箱体制品,在上部加边框补强,可减小上边缘的变形.3)形状要对称设计,因为非对称形状制品容易产生收缩不均,应尽量把制品做成对称形状为好.:1)为防止应力集中,应设计有R圆角的过渡,辟免尖角,防止应力集中引起开裂.2)孔距和孔至边距都不可太小,因为孔靠近边缘或离邻孔太近时容易削弱制品强度,应拉开一定的距离.3)开孔的周边要补强,因孔处容易应力集中,在开孔周围增加厚度补强.如加高开孔边缘和开口周围的加强.4)拐角处设圆弧,因在涂料或稀料的作用下容易引起开裂,所以涂漆制品的拐角处应设圆弧.:1)考虑能易脱模,把所开的孔尽可能地做成”U”型孔,或者用模具压出孔,便于脱模.2)防止错位干脆设计成阶梯孔.3)防止尖锐的边缘,不要锐边.4)形状要简单,使模具不复杂.5)采用无熔合缝的浇口,对于杯状制品,底部作浇口较妥.6)要考虑聚全物的取向,为使流动平滑而决定浇口位置.7)按聚合物从厚壁处流向薄壁处的原则来决定浇口和壁厚,阳模脱模斜度过大而有滞留在阴模中的情况时,在阳模上开拉引槽较好.1).为了减小模具复杂程度,可采用制品的后加工方法,2)使分型面与脱模方向垂直.3)分型面表状简单化.4)制口形状应对称,模具加工起来也容易.5)考虑有利于机加工,应尽量采用圆形,因为车削比铣削加工迅速而又方便.6)制品上的文字图样等如果做成凸起形,则模具加工时就简化为铣槽.7)格子面处于表面位置,纵横高度如果设少许高度差,则模具容易加工,特别对精加工方便.:1)嵌件定位应可靠,有螺纹的金属嵌件应将螺纹部分放在制品外部.2)尽量不用金属嵌件,因为金属嵌件与塑料之间热膨胀不同,使制品产生内应力而造成开裂.3)由于金属本身价格高,成型周期长,因此尽量不.4)防止嵌件不牢,易从制品拔出.要采用有嵌件的设计,例如可用自攻孔或螺母锁紧或用螺母代替嵌件1.制品注射不足:1)加大流道 2)加大浇口 3)加大喷嘴 4)浇口位置布置要合理 5)增加浇口数 6)加大冷料穴 7.扩大排气槽2.溢料,飞边1)型腔与腔芯要紧闭对准 2)提高模板平行度 3)增加模板刚性 4)模板平面刮平毛刺 5)排气孔开的适当3.凹痕,气孔1)增大浇口,分流道,主流道,喷嘴 2)排气孔适当 3)浇口流道使充模速率平衡 4)浇口按排厚壁部位 5)减少型腔厚度差值4.接痕1)拼缝处排气要好 2加大主,分流道,浇口及喷嘴直径 3)浇口与拼缝要近或增加辅助浇口 4)增加型腔壁厚 5)型芯要定位防止偏移 6)动,定模要定位准确,防偏, 7)流道,浇口充模速率要平衡5.降解脆化1)型腔不要设计太薄 2)加大浇口和分流道 3)增加加强筋,圆内角6.物料变色1)排气合理 2)加大浇日,主,分流道及喷嘴尺寸7.银丝,斑纹1)增大冷料穴,主,分流道及浇口尺寸 2)改善排气 3)提高型腔光洁度 4)壁厚不能太薄8.浇口处混浊1)增大浇口,分流道,冷料穴尺寸 2)选择合理浇口形状(扇形浇口) 3)改变浇口位置 4)改善排气效果9.翘曲与收缩1)改变浇口尺寸 2)改变浇口位置或增加辅助浇口 3)增加顶也面积 4)保持顶出力平衡 5)增加壁厚,加强制件 6)增加加强筋及圆角10.尺寸不稳定1)提高模腔尺寸精度 2)顶出力均匀稳定 3)浇口及流道尺寸和位置设计合理,使物料充模均匀11.粘贴型腔1)除去模具刻纹,伤痕,提高型腔表面光洁度 2)模具表面动作方向与注射方向一致 3)增加顶出面积,选择顶出位置 4)增加模具刚性,减少型腔变形 5)减小浇口尺,寸增设辅助浇口 6)改变浇口位置减少模腔压力12.粘贴流道1)浇套注口与喷嘴配合好 2)确保喷嘴孔小于浇套入口径 3)增加主流道锥度,调整直度,并抛光主流道 4)增加浇口料的拉出力。
射出成型基本原理.ppt

a.昇高料管溫度 b.昇高模具溫度 c.降低射出速度 d.加寬進澆口(如扇形) e.在豎澆道與橫澆道的接 縫或橫澆道分岐點.設材料 滯流區(冷料區).
九.銀條(起瘡)
原因
解決對策
原料中水份或揮發分.附 著模面的水分等氣化所 致成形機螺桿卷入空氣
a.原料必須依特性及作業 標準卻實除濕乾燥. b.增高模具溫度. c.降低料管溫度. d.減低射出速度. e.降低射出壓力. f.昇高螺桿背壓.
持在和初期粘度幾乎一
壓力降低太多時,就
樣的低粘度之流路設計 (流逆、澆口設計)及 成形條件是最理想的狀
會產生射出不足、縮 孔、焊線等成形不良。
況。
(四)、保壓工程
• •
•
•
模加若會封壓就少施 膛壓澆從前封是必加 而力口澆停人澆須的 造則密口止模口利壓 成壓封部保膛部用力 浪力後消壓內的澆保 費不仍失的。固口持 。會然,話在化密時
程
(三)、射出工程
• 1、適當的前端流動速度
• 通常,被射出的熔融樹脂,會流經澆道、流
道、澆口等流路進入模腔內。此時,為了使澆 道、流道部份之樹脂的前端流動速度對模具溫 度產生最小的影響,且提高剪斷發熱效果,基 本上應該是愈快愈好,但有些澆口方式會使成 形品發生射流,或在模腔部份速度太快或太慢 時,都會發生各式各樣的外觀不良。為了解決 這個問題,每一個流路都要進行射出速度的控 制,所以通常都會使用可以讓前端流動速度維 持在適當速度的多段射出速度控制成型機。
..
•
!
不 惜 賜 教 , 謝 謝
講 解 完 畢 , 請 大
20 04 07 14
家
等所 進以
1
行必 1
充須 分以
等
響成直使中 燥 的,未果 射 均 埃
硅胶产品成型工艺
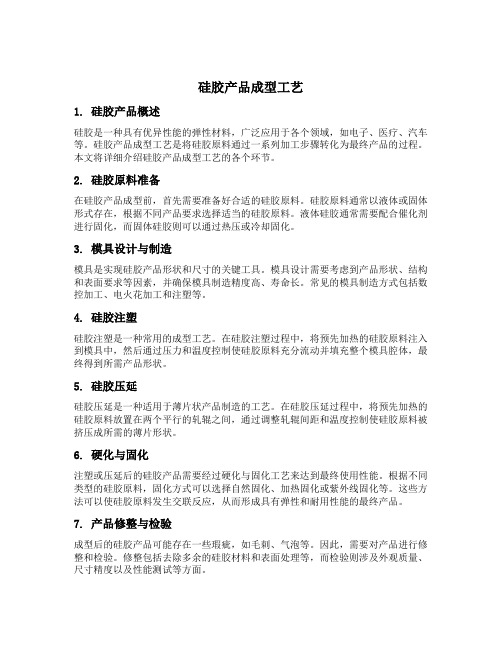
硅胶产品成型工艺1. 硅胶产品概述硅胶是一种具有优异性能的弹性材料,广泛应用于各个领域,如电子、医疗、汽车等。
硅胶产品成型工艺是将硅胶原料通过一系列加工步骤转化为最终产品的过程。
本文将详细介绍硅胶产品成型工艺的各个环节。
2. 硅胶原料准备在硅胶产品成型前,首先需要准备好合适的硅胶原料。
硅胶原料通常以液体或固体形式存在,根据不同产品要求选择适当的硅胶原料。
液体硅胶通常需要配合催化剂进行固化,而固体硅胶则可以通过热压或冷却固化。
3. 模具设计与制造模具是实现硅胶产品形状和尺寸的关键工具。
模具设计需要考虑到产品形状、结构和表面要求等因素,并确保模具制造精度高、寿命长。
常见的模具制造方式包括数控加工、电火花加工和注塑等。
4. 硅胶注塑硅胶注塑是一种常用的成型工艺。
在硅胶注塑过程中,将预先加热的硅胶原料注入到模具中,然后通过压力和温度控制使硅胶原料充分流动并填充整个模具腔体,最终得到所需产品形状。
5. 硅胶压延硅胶压延是一种适用于薄片状产品制造的工艺。
在硅胶压延过程中,将预先加热的硅胶原料放置在两个平行的轧辊之间,通过调整轧辊间距和温度控制使硅胶原料被挤压成所需的薄片形状。
6. 硬化与固化注塑或压延后的硅胶产品需要经过硬化与固化工艺来达到最终使用性能。
根据不同类型的硅胶原料,固化方式可以选择自然固化、加热固化或紫外线固化等。
这些方法可以使硅胶原料发生交联反应,从而形成具有弹性和耐用性能的最终产品。
7. 产品修整与检验成型后的硅胶产品可能存在一些瑕疵,如毛刺、气泡等。
因此,需要对产品进行修整和检验。
修整包括去除多余的硅胶材料和表面处理等,而检验则涉及外观质量、尺寸精度以及性能测试等方面。
8. 包装与出货最后一步是对成品进行包装和出货。
根据产品类型和客户需求,选择合适的包装材料和方式,并确保产品在运输过程中不受损坏。
以上就是硅胶产品成型工艺的全面介绍。
通过对硅胶原料准备、模具设计与制造、注塑或压延、硬化与固化、产品修整与检验以及包装与出货等环节的详细描述,希望读者对硅胶产品成型工艺有更深入的了解。
(新)射出成型简介_

射出成型简介1 射出成形之基本知识。
1.1 射出成形的特征以及组成。
射出成形是将溶融的成形材料以高压的方式填充到封闭的模具内,射出成形的模腔内承受的压力约400KGF/CM2,大约为400个大气压,以这样高的压力来制作产品是它的特征,这是它的优点也是它的缺点。
也就是说模具必须制作得相当坚固,因而模具价格也相当昂贵,因此必须大量生产以便与高价的模具费用互相扣抵,例如每批之生产量必须10000PCS以上才合理,换句话说;射出成形的工作必须以大量生产才行。
成型过程所说几个步骤:1.1.1关门安全门上才开始成型。
1.1.2 锁模将移动侧的移动板前进,使得模具关闭,模具关闭以后确实地把模具锁紧。
1.1.3 射出(包括保压)螺杆快速地往前推进,把熔融之成形材料注入模腔内填充成形,填充之后压力要必须继续保持,这个动作特别取名为“保压”。
在刚充填时模具承受的压力,一般叫做射出压或者叫做“一次压”。
1.1.4 冷却(以及下个动作的可塑化工程)模腔内之成形材料等待冷却凝固之过程叫“冷却”。
在这时候射出装置也准备下次工作,这个过程叫做“可塑化过程”。
放在料斗里的成形材料,流入加热的料管内加热,是依据螺杆旋转把原料变成熔融状态,螺杆像拨取螺丝的原理一样,一面转一面后退,螺杆前端会储存熔融之成形材料,螺杆旋转时,抵抗螺杆向后退的压力称之为螺杆的“背压”。
1.1.5 打开模具将移动侧的移动板向后退,模具跟着打开。
1.1.6 打开安全门安全门打开,这时成形机处于待机中之状能。
1.1.7 取件将成品取出,然后检视确认模具内未残留任何对象再关门.以上整个成形作业叫做一个CYCLE成型。
成品是由模具的形状成形出来。
模具是由母模及公模块合成,公母模模仁之间留有空隙,材料在此流入压缩形成产品。
成型材料要流入公母模之前的通路有主流道(SPRUE)流道(RUNNER)闸门(GATE)等。
1.2 射出成形机射出成形机以较大项目来区分,可分为两项,锁模装置和射出装置。
射出成形问题改善与解决对策指引d
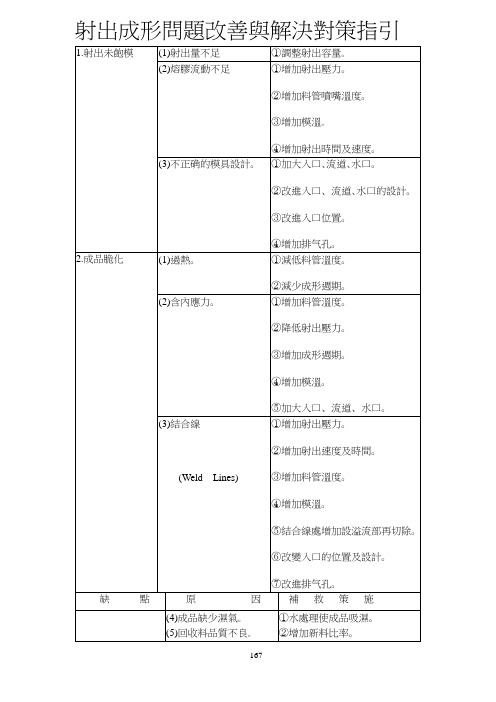
可能的決解辦法
9.多模穴中材料塑流不平均。
9.修正平衡狀況。
10.射料速度不足。
10增加射料速度。
11.進料口太小。
11.加大進料口。
12.射料量大於機器的能量。
12.換機器或減少模穴。
棕色流紋
(BROWN
STREAKS)
1.整個的或部分的料筒過熱。
1.降低加溫器的溫度。
2.料筒或射料咀堵塞。
2.清洗料筒,清洗射料咀,如果必要將料筒拆下並清洗之。
D儘可能使產品的厚度一致。
7.外著脫模劑不足。
7.加入硬酯酸鋅(每一百磅15克),尤其是使用回收料時。
8.外著脫模劑不一致。
8.拉長混料時間,或多加入少許潤滑劑予以混合之。
9.射出速度太快。
9.A增加排气孔。
B減少射出壓力。
C降低料筒溫度。
D降低射料速度。
10.外著脫模劑過多。
10.增加回收料或加入無脫模劑的材料與其混合。
(1)熔膠填充太快。
①降低射出速度。
②改變入口位置及種類,如側異入口。
缺點
原因
補救策施
11.收縮過度
(1)加工條件。
①降低模具溫度。
②增加射出壓力。
(2)入口太小。
①增大入口。
12.層狀分離
(LAMINATION)
(1)含有不相熔的異物。
①檢查樹脂,特別是使用回收料時。
(2)充填模穴導致高應力。
①增加模溫、料管溫度。
5.限制流經進料口的塑料儘可能在接近主流道處限壓。
6.頂出系統設計不良或操作不良。
6.重新設計。
7.模溫不一致。
7.維持模面於同一溫度。
8.進料口周圍填擠材料太多。
硅橡胶射出成型加工工艺的优化研究
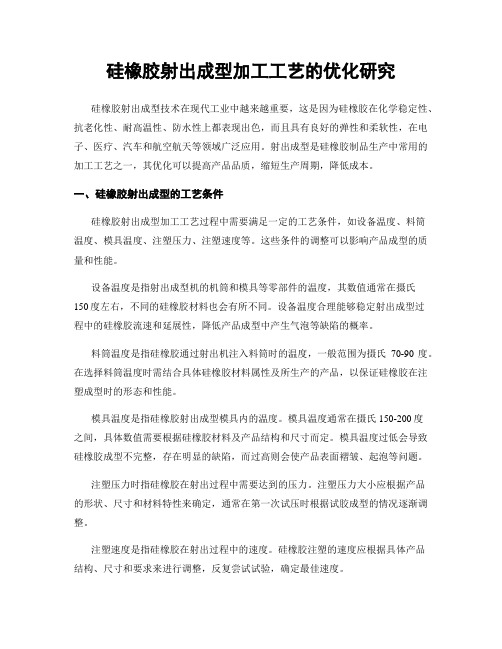
硅橡胶射出成型加工工艺的优化研究硅橡胶射出成型技术在现代工业中越来越重要,这是因为硅橡胶在化学稳定性、抗老化性、耐高温性、防水性上都表现出色,而且具有良好的弹性和柔软性,在电子、医疗、汽车和航空航天等领域广泛应用。
射出成型是硅橡胶制品生产中常用的加工工艺之一,其优化可以提高产品品质,缩短生产周期,降低成本。
一、硅橡胶射出成型的工艺条件硅橡胶射出成型加工工艺过程中需要满足一定的工艺条件,如设备温度、料筒温度、模具温度、注塑压力、注塑速度等。
这些条件的调整可以影响产品成型的质量和性能。
设备温度是指射出成型机的机筒和模具等零部件的温度,其数值通常在摄氏150度左右,不同的硅橡胶材料也会有所不同。
设备温度合理能够稳定射出成型过程中的硅橡胶流速和延展性,降低产品成型中产生气泡等缺陷的概率。
料筒温度是指硅橡胶通过射出机注入料筒时的温度,一般范围为摄氏70-90度。
在选择料筒温度时需结合具体硅橡胶材料属性及所生产的产品,以保证硅橡胶在注塑成型时的形态和性能。
模具温度是指硅橡胶射出成型模具内的温度。
模具温度通常在摄氏150-200度之间,具体数值需要根据硅橡胶材料及产品结构和尺寸而定。
模具温度过低会导致硅橡胶成型不完整,存在明显的缺陷,而过高则会使产品表面褶皱、起泡等问题。
注塑压力时指硅橡胶在射出过程中需要达到的压力。
注塑压力大小应根据产品的形状、尺寸和材料特性来确定,通常在第一次试压时根据试胶成型的情况逐渐调整。
注塑速度是指硅橡胶在射出过程中的速度。
硅橡胶注塑的速度应根据具体产品结构、尺寸和要求来进行调整,反复尝试试验,确定最佳速度。
二、硅橡胶射出成型加工工艺的优化方案硅橡胶射出成型加工工艺在实践中存在一些缺陷,如容易产生气泡、裂痕等,会影响产品的质量和效率。
优化硅橡胶射出成型加工工艺方案,可以从以下几个方面入手:1. 硅橡胶材料性能分析:根据硅橡胶的特点和应用领域,选取符合要求的硅橡胶材料;2. 射出成型设备优化:选用高质量的射出成型设备,尽量减少加工沙粒等杂物的引入;3. 设备调整:合理调整设备温度、料筒温度、模具温度、注塑压力、注塑速度等参数,提高硅橡胶在射出成型工艺中的稳定性;4. 模具设计与制造:设计和制造符合硅橡胶射出成型工艺要求的模具结构,避免尺寸过大、过小或是结构异常的问题出现。
射出成型的5大要素

射出成型條件
成形條件是指,為了獲得所需的成形品,而設定的 成型機的料筒溫度、注射速度、模具溫度等組合成 無數個不同的成型條件。根據這些成型條件所得到 的成型品在外觀,尺寸,機械物性等方面有變化時, 我們必須依賴以往的技術和經驗找出最佳的成型條 件。
成型的五大要素 ☉溫度 ☉壓力 度 ☉時間 ☉位置
原料乾燥不完全而在高溫射出時氣化而產生 排氣不良所致,模腔內熱氣經過壓縮導致部品焦化變黑 模仁漏水,漏油
脫模劑噴太多阻檔空氣排出
瓦斯氣堆積阻礙排氣槽/一次部品過飽模或膠位太多阻礙排氣 料管過大,餘料過多,使原料在料管內過度熔融導致輕微劣解
對策:
使原料在成型前充份乾燥,含水值達到生產要求/選擇適當及排氣功能佳的料管
困氣或燒焦處加開排氣槽或透氣塊/流道加排氣槽 更換防水圈(O型環),一般或高溫防水圈依實際生產需要選擇使用 檢查是否模仁裂/水(油)循環系統裂
噴脫模劑以不影響品質為原則
模具定時保養 調整一次部品成型條件或一次部品減膠
流紋
原因1(噴射紋):
塑料或模具溫度太低,造成塑膠進入模腔快速冷卻 射速過快或進膠口徑太小,形成噴射紋 增加料溫及模溫 降低射速,使原料經過進膠口處,再以高速充填成型 加大進膠口徑(一般改為扇形較佳)
對策:
進點殘留
原因:
射出時間不當,太長或太短都可能造成進點殘留 豎膠道放電與模仁型腔距離太遠 進膠點太大 模具溫度過高
對策:
Leabharlann 調整成型條件 豎膠道放電加深,縮短細部長度 調整進膠點大小(縮小)/加深波仔 調整模具溫度
困氣/燒焦
原因:
射出成型的介绍(一)

一、射出成型机的认识介绍
第一章
一、射出成型的特征: 射出成型是把成型材料以主压方式充填到模具腔内,射出
成型的模具腔内承受之压力约400KG.F/CM2大约为400个大气压。 以这样高的压力来制作产品,是射出成型的特征,这是它
的优点,也是它的缺点,也就是部模具必须制作得相当坚固,困而 模具价格也相当昂贵,因此必须多量生产,以便于高价之模具费用, 互相扣抵,换句话说,射出成型之工作,必须大量生产才行。 二、射出成型的过程(一个CYCLE循环)
OFF,ON—OFF……7~8次,听到马达转换为Y之声音后,启动马达之动作,便完成。 12、启动后,让PUMP(泵)空转约3~5分钟后再浪各油路动作。 13、启动后,马达的声需费1小时的时间),成型机才能达
到安定的状态,生产出来的产品品质才会稳定。
整个射出成型的循环中时间内容可分为三大部分: 1、射出时间 2、静止时间 3、开关模时间
第二章 一、塑胶射出成型机的分类:
1、依射出量来区分 2、依锁模力来区分 3、依锁模方式来区分 二、塑胶射出成型机旬部的构造分为: 1、锁模装置单元 2、射出装置单元 3、机座装置单元 三、塑胶射出成型机各部位名称及功能:
1、操作控制箱 功能:是各种开启开关及操作开关。如:装模手动、半自动、全自动、顶
出、射出座前、退油压中子,等开关。 2、成型条件调整控制盘 功能:是调整压力、速度行程、料量、时间等射出成型条件。 3、侦(监)测器 功能:可以由侦监测器查出机器的异常点及高定时间功能。 4、温度高定控制器 功能:是调整料管温度,控制料管温度、各段料管温度、灌嘴(NOZZLE)
温度分开单独设定,调整、控制。
5、锁模单元: 功能: 将模具关闭、打开的作用。 6、顶出油压单元 功能: 系模具打开后,将产品由模具内顶出来,以利人手去取拿,或自行落下,
硅胶成型方法

硅胶成型方法硅胶是一种高分子材料,常用于制造各种硅胶制品,如硅胶手环、硅胶手机壳等。
硅胶成型方法主要包括模具设计、原料配比、混合搅拌、注塑成型、固化硬化等步骤。
下面将详细介绍硅胶成型的具体步骤。
1. 模具设计:首先,需要根据所要制造的硅胶制品的形状和尺寸,设计相应的模具。
模具可以根据需要使用CAD软件进行绘制,确保模具的准确度和精度。
2. 原料配比:硅胶成型的关键是原料的配比。
通常,硅胶是由硅酮聚合物和交联剂组成的。
在配比过程中,需要根据具体要求确定硅胶和交联剂的配比比例,以保证制品的性能和质量。
3. 混合搅拌:将硅胶和交联剂按照配比比例倒入混合搅拌机中,进行充分的搅拌,使两者充分混合均匀。
搅拌的时间和速度需要根据具体情况进行调整,以确保搅拌均匀。
4. 注塑成型:将混合好的硅胶注入到模具中,注塑成型。
可以使用手动注塑机或自动注塑机进行注塑操作。
在注塑过程中,需要注意控制注塑的速度和压力,以避免气泡和缺陷的产生。
5. 固化硬化:注塑完成后,需要将模具放置在恒温环境中进行固化硬化。
固化的时间和温度需要根据硅胶的类型和硬化剂的性质进行调整。
通常情况下,硅胶的固化时间为数小时至数十小时。
6. 模具脱模:硅胶固化后,需要将模具取出,进行模具脱模。
在脱模过程中,需要注意避免对制品造成损坏或变形。
可以使用专用的脱模剂来帮助模具脱离硅胶制品。
7. 后处理:模具脱模后,可以对硅胶制品进行一些后处理。
例如,可以进行清洗、修整、抛光等工艺,以提高制品的表面光滑度和质感。
总结:硅胶成型方法是一项复杂而精细的工艺过程。
通过模具设计、原料配比、混合搅拌、注塑成型、固化硬化等步骤,可以制造出各种形状和尺寸的硅胶制品。
在整个成型过程中,需要掌握合理的操作技巧和严格的质量控制,以确保制品的性能和质量。
同时,还可以根据具体需求进行后处理,使硅胶制品达到更高的质量要求。
射出成型的工艺流程

射出成型的工艺流程下载温馨提示:该文档是我店铺精心编制而成,希望大家下载以后,能够帮助大家解决实际的问题。
文档下载后可定制随意修改,请根据实际需要进行相应的调整和使用,谢谢!并且,本店铺为大家提供各种各样类型的实用资料,如教育随笔、日记赏析、句子摘抄、古诗大全、经典美文、话题作文、工作总结、词语解析、文案摘录、其他资料等等,如想了解不同资料格式和写法,敬请关注!Download tips: This document is carefully compiled by theeditor. I hope that after you download them,they can help yousolve practical problems. The document can be customized andmodified after downloading,please adjust and use it according toactual needs, thank you!In addition, our shop provides you with various types ofpractical materials,such as educational essays, diaryappreciation,sentence excerpts,ancient poems,classic articles,topic composition,work summary,word parsing,copy excerpts,other materials and so on,want to know different data formats andwriting methods,please pay attention!陶瓷地砖楼面的施工工艺流程一、准备工作阶段在进行陶瓷地砖楼面的施工之前,需要进行一系列准备工作。
射出成型现场实用手册

PC+ABS: 含玻纖材料: POM:塑鋼
Polyoxymethylene , polyacetal
03'01'04
模具簡介-兩板模
03'01'04
兩板模運作原理
"A" Plate
Standard Two Plate Mold
Sprue Bushing
Ejector Plate
Support Plate
內部加強肋厚度
03'01'04
成型品設計的原則-肉厚
一般肉厚建議需均勻
肉厚不均容易造成縮水.產生內應力.變形
能否有效均勻分散衝擊作用力 構造強度是否充分
03'01'04
資料來源
Tom‘s 硬體指南 公用資料夾 實用塑膠模具學-全華出版社 射出成型現場實用技術手冊 3C產業材料暨精密塑膠射出加工技術交 流會
03'01'04
塑膠射出製程
將粒狀的ABS塑膠樹脂倒入機器中,並 熔化這些樹脂,然後將其注入模具中以 形成塑膠零件。
03'01'04
塑膠射出製程
射出場必須用到許 多模具架來存放塑 膠射出模具。
03'01'04
塑膠射出製程
射出機器將塑膠熔化後注入模具中。等 到塑膠冷卻並從模具中取出時,便可得 到塑膠成品。
03'01'04
塑膠射出製程
工作人員正在進 行品管檢查。檢 查的重點是射出 品的品質。在這 個步驟中,工作 人員必須確定射 出品完全符合規 格。
硅胶制品中常见的几种成型工艺介绍
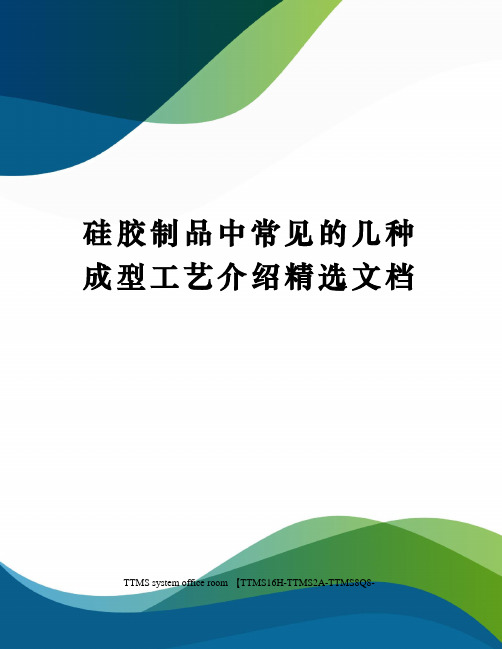
硅胶制品中常见的几种成型工艺介绍精选文档 TTMS system office room 【TTMS16H-TTMS2A-TTMS8Q8-硅胶做为一种环保性原材料,以其各种优越性能被广大人们所喜爱。
它的柔软性与无毒性被广泛用于工业密封与医疗器械。
特别是它的工作温度:-60至250摄氏度是塑胶无法比拟的。
利用硅胶包住金属件或塑胶件形成一些新的性能更是让产品软硬有度,比如,硅胶包钢的厨具铲,它的环保受到消费者喜爱。
硅胶与塑胶不同,硅胶是一种热成型的材料,硅胶原料在一定温度作用下,固化形成我们要的产品。
硅胶制品常用的有以下几种成型工艺:1、挤出成型工艺就像我们挤牙膏一样,挤出机头也是产品的截面形状,有一定长度,在力与温度的作用下,机头出来产品已经硫化成型。
此工艺成型的产品一般是条形的产品,产品截面可以各种各样。
譬如,矩形长条,环形硅管,等。
2、滴胶工艺硅胶原料为液态状,原料装在针筒里面,用气动加人工操作把原料滴到模具上,加热硫化成型。
此工艺属于手工化工艺,需要人工的地方多。
所以产能不高。
它有一个特点,一个产品可以依要求滴上多种颜色。
所以这种工艺多为制作工艺品。
如,多色的硅胶手环,各种颜色图案的硅胶手机套,等。
3、固态热压成型工艺此种工艺是利用油压机的温度与压力,借助模具把产品硫化成型出来。
这种工艺相对成本低,产量高,应用比较普遍。
它多用于单色的硅胶产品。
也可应用于双色双硬度的产品或是多色多硬度,但是产品的结构不灵活,受限制。
它也可以应用于包塑胶与包金属,同样在结构上不灵活,而且对所包物件有温度要求,一般要求所包物件要耐180摄氏度不变形。
4、液态射出成型工艺此种工艺要求的设备有硅胶射出机、压料机。
它的原料是水稠状,分A、B两组分。
它的原理是:利用压料机把A、B组分的原料按照1:1压到射出机的料筒里混合,通过射嘴再把它压进热模具型腔成型。
此种工艺成型温度相对较低,130度就可以。
它可以用于不太耐高温的塑胶包胶成型,这一点比固态热压成型有优势。
注塑标准pfmea模板
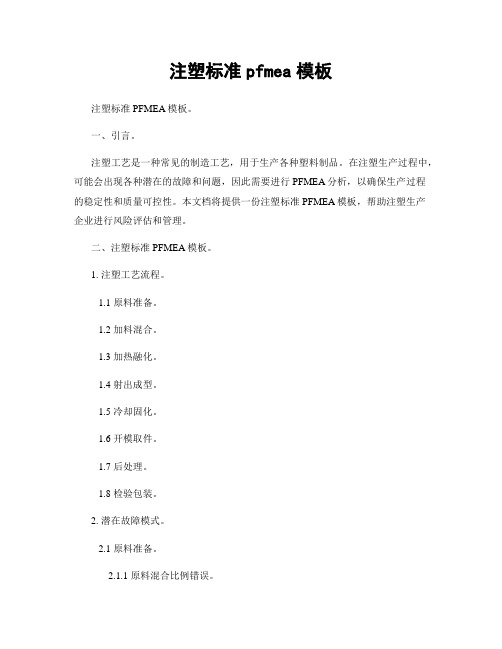
注塑标准pfmea模板注塑标准PFMEA模板。
一、引言。
注塑工艺是一种常见的制造工艺,用于生产各种塑料制品。
在注塑生产过程中,可能会出现各种潜在的故障和问题,因此需要进行PFMEA分析,以确保生产过程的稳定性和质量可控性。
本文档将提供一份注塑标准PFMEA模板,帮助注塑生产企业进行风险评估和管理。
二、注塑标准PFMEA模板。
1. 注塑工艺流程。
1.1 原料准备。
1.2 加料混合。
1.3 加热融化。
1.4 射出成型。
1.5 冷却固化。
1.6 开模取件。
1.7 后处理。
1.8 检验包装。
2. 潜在故障模式。
2.1 原料准备。
2.1.1 原料混合比例错误。
2.1.2 原料受潮变质。
2.2 加料混合。
2.2.1 加料过多或过少。
2.2.2 加料不均匀。
2.3 加热融化。
2.3.1 温度控制失效。
2.3.2 压力控制不当。
2.4 射出成型。
2.4.1 射出压力不稳定。
2.4.2 模具磨损变形。
2.5 冷却固化。
2.5.1 冷却时间不足。
2.5.2 冷却水温度异常。
2.6 开模取件。
2.6.1 模具卡料。
2.6.2 取件机械故障。
2.7 后处理。
2.7.1 后处理工艺不当。
2.7.2 后处理设备故障。
2.8 检验包装。
2.8.1 检验工具不准确。
2.8.2 包装破损。
3. 潜在故障影响。
3.1 产品质量下降。
3.2 生产效率降低。
3.3 安全事故发生。
3.4 成本增加。
3.5 客户投诉增加。
4. 现有控制措施。
4.1 原料准备。
4.1.1 严格控制原料混合比例。
4.1.2 原料存储防潮防潮。
4.2 加料混合。
4.2.1 定期校准加料设备。
4.2.2 加料设备定期清洁。
4.3 加热融化。
4.3.1 定期检查加热系统。
4.3.2 设置温度和压力报警。
4.4 射出成型。
4.4.1 定期维护模具。
4.4.2 实施射出压力控制。
4.5 冷却固化。
4.5.1 设定合理的冷却时间。
4.5.2 监控冷却水温度。
4.6 开模取件。
- 1、下载文档前请自行甄别文档内容的完整性,平台不提供额外的编辑、内容补充、找答案等附加服务。
- 2、"仅部分预览"的文档,不可在线预览部分如存在完整性等问题,可反馈申请退款(可完整预览的文档不适用该条件!)。
- 3、如文档侵犯您的权益,请联系客服反馈,我们会尽快为您处理(人工客服工作时间:9:00-18:30)。
R P N
/
供應商的制程或使 用原材料不符合有 害物質管控的要求
1
1. 随来料确认 限用物質檢測报告. 2.定期送外檢驗來料 的原材料是否有超 標的現象
1.IQC按《進料驗收 單》進行驗收2.根據 供應商提交的檢測報
告進行确認
4
1. 随来料确认 限用物質檢測报告. 36 2.定期送外檢驗來料 的原材料是否有超標 的現象
試硬度
2011.04.22
度
8
2
4
64
測試硬度
第 1 頁,共 11 頁
编号
严
工程描述 潜在失效模式 失效的潜在影响
重 度
S
含油量有誤
影响產品性能,不符 合客戶使用要求
8
原料批号錯誤
混料、混放、建错 ERP品号、领错料
3
进料 (硅膠)
分 类
频 失效的潜在原因 度
O
现行控制预防
现行控 制探测
探 测 度 D
R P N
推荐对策
责任者及 完成日期
对策效果
实施的对策
严 重 度 S
频 度 O
检 出 度 D
R P N
1.按硅橡胶<<允收标准一
原料供應商制程管 控品质异常
2
供应商每批提供材 IQC根据随附的材质
質報告
证明进行驗證
4
1..IPQC在生產產品24 制造課程偉 览表>>进判定,并追踪确认 64 小時後觀察出油狀況 品管课甘建鋒 2.IPQC在生產產品24小時
1.退料且要求供应 商改善 2.不定期的送外檢及加強 對供應商的監控
3
2
4
24
确認
包裝破損 材料污染后報廢
8
/
供應商運輸損壞
2
指定合格運輸供应 1.IQC按《進料驗收
商
單》進行驗收
5
品管甘建鋒
80
通知廠商進行补写或 修正注意事项
采購石艷芳 2011.04.22
通知廠商進行补写或修正 注意事项
8
2
5
80
原料所含物质 不符合Rohs要
求
不符合客戶及法律 法規对有害物质的 要求,會造成客戶及 相關組織罰款的可
9
能
/
1.隔离所有不符合要
供應商的制程或使 用原材料不符合有 害物質管控的要求
1
求的產品并要求供 1.IQC按《進料驗收
應商立即調查2.供應 單》進行驗收2.根據
商重新生產合格的 供應商提交的檢測報
2
供应商每批提供材 IQC根据随附的材质
質報告
证明进行驗證
4
64
通知廠商改善
品管甘建鋒 PMC黃發明 2011.04.22
按硅橡胶<<允收标准一览 表>>进判定,并追踪确认
8
2
4
64
硫化速度有誤
影響成形及產品尺 寸等問題
8
/
原料供應商制程管 控品质异常
2
供应商每批提供材 IQC根据随附的材质
質報准一览 表>>进判定,并追踪确认
8
2
4
64
进料 (硅膠)
硬度有误
影響成形及影响產 品性能
8
原料供應商制程管 控品质异常
2
1.IQC根据随附的材
供应商每批提供材 质证明进行驗證
質報告
2.IQC根據檢驗標準
4
制造課程偉
64
每批原料熱壓1PCS測 品管课甘建鋒 每批原料熱壓1PCS測試硬
2
使用時核對產品顏 IQC根据随附的材质
品管甘建鋒 PMC黃發明 2011.04.22
1.退料且要求供应 商改善 2.不定期的送外檢及加強 對供應商的監控
9
1
4
36
/
供應商發錯料或原 料標識錯誤
2
由供應商廠商對材 料標識進行防錯措
施
1.IQC按《進料驗收 單》進行驗收2.核對 材質報告及原材料外 箱標識
4
64
通知廠商進行根本的 預防及防錯措施
产品或工程名称/编号: IRI-98047B 设计责任: 開發课 CFT:
编号
严
工程描述 潜在失效模式 失效的潜在影响
重 度
S
原料所含物质 不符合Rohs要
求
不符合客戶及法律 法規对有害物质的 要求,會造成客戶及 相關組織罰款的可
9
能
材料錯誤
造成無料可用及停 产的危险
8
数量错误 影響入帳及成本 2
关键生产日期:
產品并提交合格的
告進行确認
5
檢測報告
45
1. 随来料确认 限用物質檢測报告.2. 定期送外檢驗來料的 原材料是否有超標的
現象
品管甘建鋒 PMC黃發明 2011.04.22
1.退料且要求供应 商改善 2.不定期的送外檢及加強 對供應商的監控
9
1
5
45
顏色错误 产品颜色不符要求 5
/
原料供應商制程管 控品质异常
品管甘建鋒 PMC黃發明 2011.04.22
通知廠商進行根本的預防 及防錯措施
8
2
4
64
/
厂商出貨數量不符 要求
2
依采购订单检查
IQC进行驗證
7 28
通知廠商補數
品管甘建鋒 PMC黃發明 2011.04.22
发出<<厂商改善对策书>> 对改善结果进行追踪确认
2
2
7
28
1
进料 (硅膠)
顏色错误 产品颜色不符要求 8
進行出油量的判定 2011.04.22 後觀察出油狀況進行出油
8
2
4
64
量的判定
1.IQC按《進料驗收
/
供應商原料標識錯 誤
2
由供應商廠商對材 料標識進行防錯措
施
單》進行驗收2.核對 材質報告及原材料外 箱標識3.根據供應商 提交的檢測報告進行
4
24
通知廠商進行根本的 自检、預防及防范措
施
品管甘建鋒 PMC黃發明 2011.04.22
/
原料供應商制程管 控品质异常
2
供應商廠商出貨核 對材料標識及顏 色,無誤后出貨
IQC根据随附的材质 证明进行驗證
4
64
通知廠商改善
品管甘建鋒 PMC黃發明 2011.04.22
发出<厂商改善对策书通知 厂商,并进行追踪确认
8
2
4
64
缩水率有误
影響成形及產品尺 寸等問題
8
/
原料供應商制程管 控品质异常
搬运、運輸不 造成无料可用及人
当
身危险
3
/
供應商出货前无注 明或漏写注意事项
2
1.IQC按《進料驗收
通知供应商立即处 單》進行驗收2. IQC
理
原料檢驗規範和督促
3
搬运人员安全.
18
通知廠商進行补写或 修正注意事项
品管甘建鋒 采購石艷芳 2011.04.22
通知廠商進行补写或修正 注意事项
3
2
3
18
4
64
通知廠商改善
品管甘建鋒
PMC黃發明 按硅橡胶<<允收标准一览 2011.04.22 表>>进判定,并追踪确认
8
2
4
64
撕破強度不合 影響成形及產品尺
格
寸等問題
8
/
原料供應商制程管 控品质异常
2
供应商每批提供材 IQC根据随附的材质
質報告
证明进行驗證
4
64
通知廠商改善
品管甘建鋒 PMC黃發明 2011.04.22
潜在失效模式及效果分析(PFMEA)
PFMEA NO./编号: EC710120 制定: PFMEA 日期(原稿) :
EC71001-01A
修订:
分 类
频 失效的潜在原因 度
O
现行控制预防
现行控 制探测
探 测 度 D
R P N
推荐对策
责任者及 完成日期
对策效果
实施的对策
严 重 度 S
频 度 O
检 出 度 D