湿态转干态
660MW超超临界锅炉湿态转干态运行操作探讨
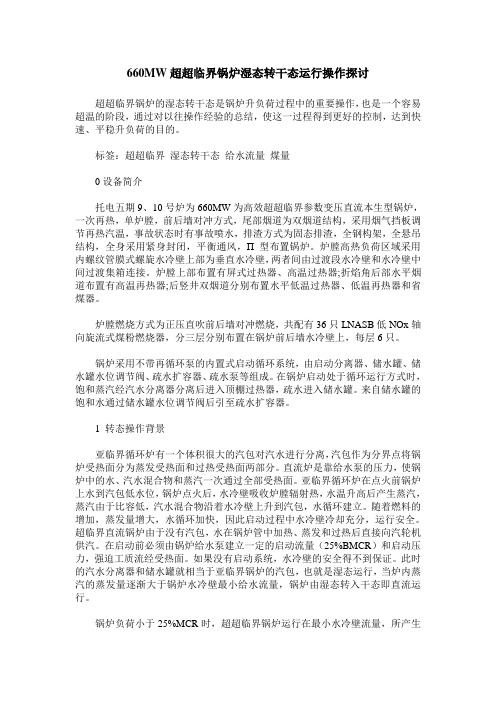
660MW超超临界锅炉湿态转干态运行操作探讨超超临界锅炉的湿态转干态是锅炉升负荷过程中的重要操作,也是一个容易超温的阶段,通过对以往操作经验的总结,使这一过程得到更好的控制,达到快速、平稳升负荷的目的。
标签:超超临界湿态转干态给水流量煤量0设备简介托电五期9、10号炉为660MW为高效超超临界参数变压直流本生型锅炉,一次再热,单炉膛,前后墙对冲方式,尾部烟道为双烟道结构,采用烟气挡板调节再热汽温,事故状态时有事故喷水,排渣方式为固态排渣,全钢构架,全悬吊结构,全身采用紧身封闭,平衡通风,Π 型布置锅炉。
炉膛高热负荷区域采用内螺纹管膜式螺旋水冷壁上部为垂直水冷壁,两者间由过渡段水冷壁和水冷壁中间过渡集箱连接。
炉膛上部布置有屏式过热器、高温过热器;折焰角后部水平烟道布置有高温再热器;后竖井双烟道分别布置水平低温过热器、低温再热器和省煤器。
炉膛燃烧方式为正压直吹前后墙对冲燃烧,共配有36只LNASB低NOx轴向旋流式煤粉燃烧器,分三层分别布置在锅炉前后墙水冷壁上,每层6只。
锅炉采用不带再循环泵的内置式启动循环系统,由启动分离器、储水罐、储水罐水位调节阀、疏水扩容器、疏水泵等组成。
在锅炉启动处于循环运行方式时,饱和蒸汽经汽水分离器分离后进入顶棚过热器,疏水进入储水罐。
来自储水罐的饱和水通过储水罐水位调节阀后引至疏水扩容器。
1 转态操作背景亚临界循环炉有一个体积很大的汽包对汽水进行分离,汽包作为分界点将锅炉受热面分为蒸发受热面和过热受热面两部分。
直流炉是靠给水泵的压力,使锅炉中的水、汽水混合物和蒸汽一次通过全部受热面。
亚临界循环炉在点火前锅炉上水到汽包低水位,锅炉点火后,水冷壁吸收炉膛辐射热,水温升高后产生蒸汽,蒸汽由于比容低,汽水混合物沿着水冷壁上升到汽包,水循环建立。
随着燃料的增加,蒸发量增大,水循环加快,因此启动过程中水冷壁冷却充分,运行安全。
超临界直流锅炉由于没有汽包,水在锅炉管中加热、蒸发和过热后直接向汽轮机供汽。
直流炉干湿态转换研究
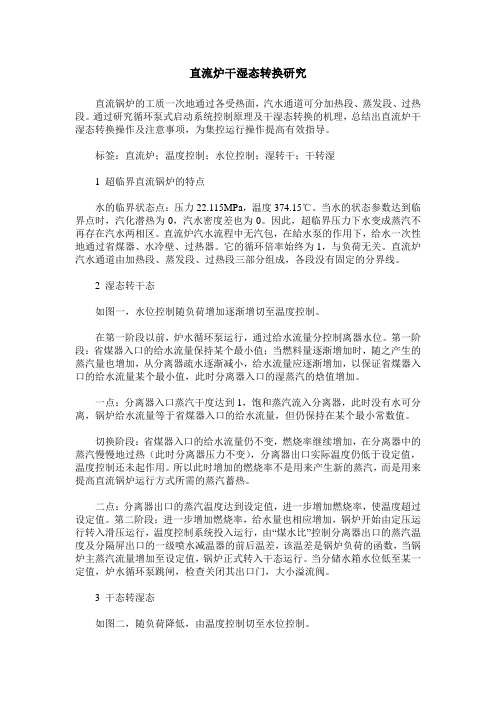
直流炉干湿态转换研究直流锅炉的工质一次地通过各受热面,汽水通道可分加热段、蒸发段、过热段。
通过研究循环泵式启动系统控制原理及干湿态转换的机理,总结出直流炉干湿态转换操作及注意事项,为集控运行操作提高有效指导。
标签:直流炉;温度控制;水位控制;湿转干;干转湿1 超临界直流锅炉的特点水的临界状态点:压力22.115MPa,温度374.15℃。
当水的状态参数达到临界点时,汽化潜热为0,汽水密度差也为0。
因此,超临界压力下水变成蒸汽不再存在汽水两相区。
直流炉汽水流程中无汽包,在給水泵的作用下,给水一次性地通过省煤器、水冷壁、过热器。
它的循环倍率始终为1,与负荷无关。
直流炉汽水通道由加热段、蒸发段、过热段三部分组成,各段没有固定的分界线。
2 湿态转干态如图一,水位控制随负荷增加逐渐增切至温度控制。
在第一阶段以前,炉水循环泵运行,通过给水流量分控制离器水位。
第一阶段:省煤器入口的给水流量保持某个最小值;当燃料量逐渐增加时,随之产生的蒸汽量也增加,从分离器疏水逐渐减小,给水流量应逐渐增加,以保证省煤器入口的给水流量某个最小值,此时分离器入口的湿蒸汽的焓值增加。
一点:分离器入口蒸汽干度达到1,饱和蒸汽流入分离器,此时没有水可分离,锅炉给水流量等于省煤器入口的给水流量,但仍保持在某个最小常数值。
切换阶段:省煤器入口的给水流量仍不变,燃烧率继续增加,在分离器中的蒸汽慢慢地过热(此时分离器压力不变),分离器出口实际温度仍低于设定值,温度控制还未起作用。
所以此时增加的燃烧率不是用来产生新的蒸汽,而是用来提高直流锅炉运行方式所需的蒸汽蓄热。
二点:分离器出口的蒸汽温度达到设定值,进一步增加燃烧率,使温度超过设定值。
第二阶段:进一步增加燃烧率,给水量也相应增加,锅炉开始由定压运行转入滑压运行,温度控制系统投入运行,由“煤水比”控制分离器出口的蒸汽温度及分隔屏出口的一级喷水减温器的前后温差,该温差是锅炉负荷的函数,当锅炉主蒸汽流量增加至设定值,锅炉正式转入干态运行。
干湿态转换操作要点分析
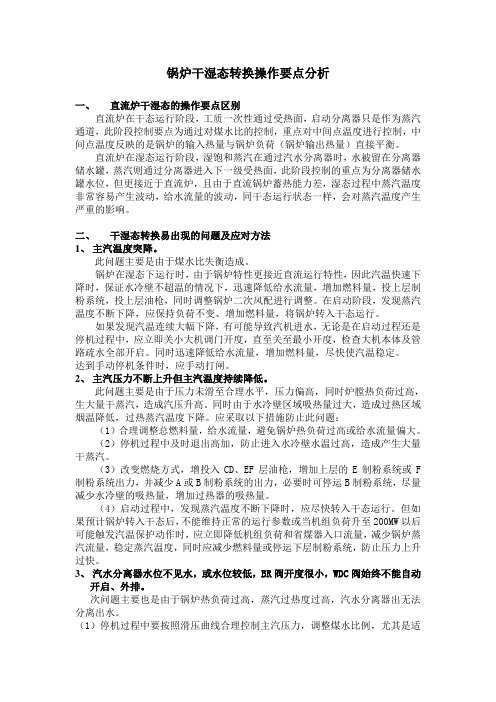
锅炉干湿态转换操作要点分析一、直流炉干湿态的操作要点区别直流炉在干态运行阶段,工质一次性通过受热面,启动分离器只是作为蒸汽通道,此阶段控制要点为通过对煤水比的控制,重点对中间点温度进行控制,中间点温度反映的是锅炉的输入热量与锅炉负荷(锅炉输出热量)直接平衡。
直流炉在湿态运行阶段,湿饱和蒸汽在通过汽水分离器时,水被留在分离器储水罐,蒸汽则通过分离器进入下一级受热面,此阶段控制的重点为分离器储水罐水位,但更接近于直流炉,且由于直流锅炉蓄热能力差,湿态过程中蒸汽温度非常容易产生波动,给水流量的波动,同干态运行状态一样,会对蒸汽温度产生严重的影响。
二、干湿态转换易出现的问题及应对方法1、主汽温度突降。
此问题主要是由于煤水比失衡造成。
锅炉在湿态下运行时,由于锅炉特性更接近直流运行特性,因此汽温快速下降时,保证水冷壁不超温的情况下,迅速降低给水流量,增加燃料量,投上层制粉系统,投上层油枪,同时调整锅炉二次风配进行调整。
在启动阶段,发现蒸汽温度不断下降,应保持负荷不变、增加燃料量,将锅炉转入干态运行。
如果发现汽温连续大幅下降,有可能导致汽机进水,无论是在启动过程还是停机过程中,应立即关小大机调门开度,直至关至最小开度,检查大机本体及管路疏水全部开启。
同时迅速降低给水流量,增加燃料量,尽快使汽温稳定。
达到手动停机条件时,应手动打闸。
2、主汽压力不断上升但主汽温度持续降低。
此问题主要是由于压力未滑至合理水平,压力偏高,同时炉膛热负荷过高,生大量干蒸汽,造成汽压升高。
同时由于水冷壁区域吸热量过大,造成过热区域烟温降低,过热蒸汽温度下降。
应采取以下措施防止此问题:(1)合理调整总燃料量,给水流量,避免锅炉热负荷过高或给水流量偏大。
(2)停机过程中及时退出高加,防止进入水冷壁水温过高,造成产生大量干蒸汽。
(3)改变燃烧方式,增投入CD、EF层油枪,增加上层的E制粉系统或F 制粉系统出力,并减少A或B制粉系统的出力,必要时可停运B制粉系统,尽量减少水冷壁的吸热量,增加过热器的吸热量。
关于湿态转干态的总结
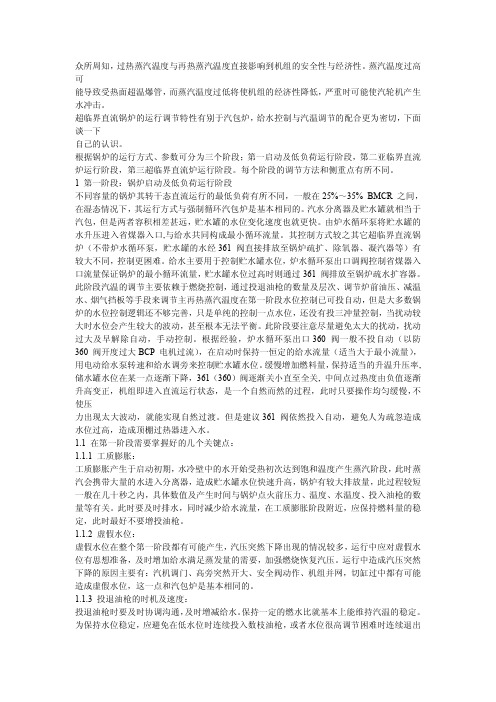
众所周知,过热蒸汽温度与再热蒸汽温度直接影响到机组的安全性与经济性。
蒸汽温度过高可能导致受热面超温爆管,而蒸汽温度过低将使机组的经济性降低,严重时可能使汽轮机产生水冲击。
超临界直流锅炉的运行调节特性有别于汽包炉,给水控制与汽温调节的配合更为密切,下面谈一下自己的认识。
根据锅炉的运行方式、参数可分为三个阶段;第一启动及低负荷运行阶段,第二亚临界直流炉运行阶段,第三超临界直流炉运行阶段。
每个阶段的调节方法和侧重点有所不同。
1第一阶段:锅炉启动及低负荷运行阶段不同容量的锅炉其转干态直流运行的最低负荷有所不同,一般在25%~35%BMCR之间,在湿态情况下,其运行方式与强制循环汽包炉是基本相同的。
汽水分离器及贮水罐就相当于汽包,但是两者容积相差甚远,贮水罐的水位变化速度也就更快。
由炉水循环泵将贮水罐的水升压进入省煤器入口,与给水共同构成最小循环流量。
其控制方式较之其它超临界直流锅炉(不带炉水循环泵,贮水罐的水经361阀直接排放至锅炉疏扩、除氧器、凝汽器等)有较大不同,控制更困难。
给水主要用于控制贮水罐水位,炉水循环泵出口调阀控制省煤器入口流量保证锅炉的最小循环流量,贮水罐水位过高时则通过361阀排放至锅炉疏水扩容器。
此阶段汽温的调节主要依赖于燃烧控制,通过投退油枪的数量及层次、调节炉前油压、减温水、烟气挡板等手段来调节主再热蒸汽温度在第一阶段水位控制已可投自动,但是大多数锅炉的水位控制逻辑还不够完善,只是单纯的控制一点水位,还没有投三冲量控制,当扰动较大时水位会产生较大的波动,甚至根本无法平衡。
此阶段要注意尽量避免太大的扰动,扰动过大及早解除自动,手动控制。
根据经验,炉水循环泵出口360阀一般不投自动(以防360阀开度过大BCP电机过流),在启动时保持一恒定的给水流量(适当大于最小流量),用电动给水泵转速和给水调旁来控制贮水罐水位。
缓慢增加燃料量,保持适当的升温升压率,储水罐水位在某一点逐渐下降,361(360)阀逐渐关小直至全关,中间点过热度由负值逐渐升高变正,机组即进入直流运行状态,是一个自然而然的过程,此时只要操作均匀缓慢,不使压力出现太大波动,就能实现自然过渡。
600MW超临界机组直流炉启动中干湿态转换浅析
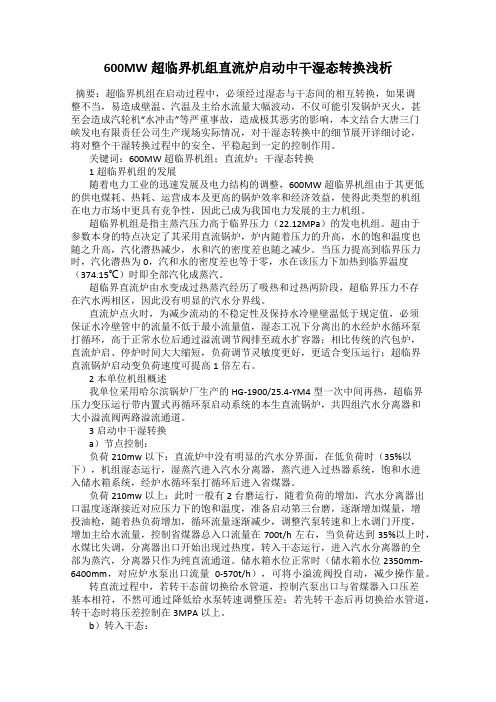
600MW超临界机组直流炉启动中干湿态转换浅析摘要:超临界机组在启动过程中,必须经过湿态与干态间的相互转换,如果调整不当,易造成壁温、汽温及主给水流量大幅波动,不仅可能引发锅炉灭火,甚至会造成汽轮机“水冲击”等严重事故,造成极其恶劣的影响,本文结合大唐三门峡发电有限责任公司生产现场实际情况,对干湿态转换中的细节展开详细讨论,将对整个干湿转换过程中的安全、平稳起到一定的控制作用。
关键词:600MW超临界机组;直流炉;干湿态转换1超临界机组的发展随着电力工业的迅速发展及电力结构的调整,600MW超临界机组由于其更低的供电煤耗、热耗、运营成本及更高的锅炉效率和经济效益,使得此类型的机组在电力市场中更具有竞争性,因此已成为我国电力发展的主力机组。
超临界机组是指主蒸汽压力高于临界压力(22.12MPa)的发电机组。
超由于参数本身的特点决定了其采用直流锅炉,炉内随着压力的升高,水的饱和温度也随之升高,汽化潜热减少,水和汽的密度差也随之减少。
当压力提高到临界压力时,汽化潜热为0,汽和水的密度差也等于零,水在该压力下加热到临界温度(374.15℃)时即全部汽化成蒸汽。
超临界直流炉由水变成过热蒸汽经历了吸热和过热两阶段,超临界压力不存在汽水两相区,因此没有明显的汽水分界线。
直流炉点火时,为减少流动的不稳定性及保持水冷壁壁温低于规定值,必须保证水冷壁管中的流量不低于最小流量值,湿态工况下分离出的水经炉水循环泵打循环,高于正常水位后通过溢流调节阀排至疏水扩容器;相比传统的汽包炉,直流炉启、停炉时间大大缩短,负荷调节灵敏度更好,更适合变压运行;超临界直流锅炉启动变负荷速度可提高1倍左右。
2本单位机组概述我单位采用哈尔滨锅炉厂生产的HG-1900/25.4-YM4型一次中间再热,超临界压力变压运行带内置式再循环泵启动系统的本生直流锅炉,共四组汽水分离器和大小溢流阀两路溢流通道。
3启动中干湿转换a)节点控制:负荷210mw以下:直流炉中没有明显的汽水分界面,在低负荷时(35%以下),机组湿态运行,湿蒸汽进入汽水分离器,蒸汽进入过热器系统,饱和水进入储水箱系统,经炉水循环泵打循环后进入省煤器。
锅炉转态的操作方法及注意事项

锅炉转态的操作方法及注意事项锅炉转态的操作方法及注意事项一、转换的时间由于直流炉没有明显的汽水分界面,所以当燃水比严重失调时干湿态就会转换,而与机组的负荷和蒸汽参数没有严格的关系。
但是为了保证螺旋水冷壁的安全和水动力特性的稳定,一般设计上要求:不带强制循环直流炉在20%MCR左右,带强制循环直流炉在30%MCR左右进行干湿态转换,但是在实际运行中为了充分保证螺旋水冷壁的安全,规定“不带强制循环直流炉在30%MCR左右,带强制循环直流炉在40%MCR左右”进行干湿态转换。
二、转换的方法1、湿态向干态转换当机组负荷到达120MW左右时,此时的燃料量应该是两套制粉系统和2支油枪左右,汽水分离器出口温度已经达到对应压力下的饱和温度,储水箱水位多次呈现下降趋势,此时应该考虑锅炉该转直流运行。
暖第三台磨,保持给水流量不变,投第三台磨,开汽轮机调门,加负荷至140MW以上,观察汽水分离器出口温度已经有过热度,视过热度的大小来确定是否加水。
维持给水的稳定,燃烧的稳定,适当增加燃料,观察过热度与储水箱水位。
转态后开始增加负荷防止反复。
2、干态向湿态转换当机组负荷降到120MW左右时,此时的燃料量应该是三套制粉系统和,汽水分离器出口温度的过热度下降很低甚至没有过热度,分离器偶尔出现水位显示。
此时应该考虑锅炉转湿态运行。
减少一台磨煤机的出力,增投两支油枪,维持锅炉燃烧稳定,维持机组负荷不大幅度下降,此时增加给水,让分离器和储水箱见水,但不能大幅度的加水,流量大概增加50T/H左右,以防止主蒸汽温度骤降。
储水箱见水稳定后,逐步减燃料,降负荷。
三、注意事项1、机组正常运行时,无论什么原因(调度原因、煤质差、原煤仓堵煤、给煤机卡、磨煤机检修等等),都必须保证锅炉的热负荷(燃料量)在130MW以上,否则只要燃料量和给水稍微一扰动就会造成锅炉转湿态,主蒸汽温度会大幅度下降。
2、湿态向干态转换时,增加燃料要迅速,并且燃料量要大些,防止锅炉转换成干态后又返回成湿态。
锅炉转干态分析
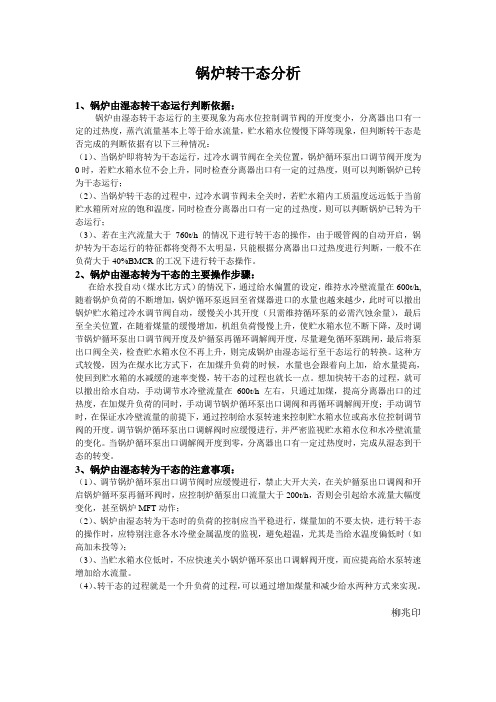
锅炉转干态分析1、锅炉由湿态转干态运行判断依据:锅炉由湿态转干态运行的主要现象为高水位控制调节阀的开度变小,分离器出口有一定的过热度,蒸汽流量基本上等于给水流量,贮水箱水位慢慢下降等现象,但判断转干态是否完成的判断依据有以下三种情况:(1)、当锅炉即将转为干态运行,过冷水调节阀在全关位置,锅炉循环泵出口调节阀开度为0时,若贮水箱水位不会上升,同时检查分离器出口有一定的过热度,则可以判断锅炉已转为干态运行;(2)、当锅炉转干态的过程中,过冷水调节阀未全关时,若贮水箱内工质温度远远低于当前贮水箱所对应的饱和温度,同时检查分离器出口有一定的过热度,则可以判断锅炉已转为干态运行;(3)、若在主汽流量大于760t/h的情况下进行转干态的操作,由于暖管阀的自动开启,锅炉转为干态运行的特征都将变得不太明显,只能根据分离器出口过热度进行判断,一般不在负荷大于40%BMCR的工况下进行转干态操作。
2、锅炉由湿态转为干态的主要操作步骤:在给水投自动(煤水比方式)的情况下,通过给水偏置的设定,维持水冷壁流量在600t/h,随着锅炉负荷的不断增加,锅炉循环泵返回至省煤器进口的水量也越来越少,此时可以撤出锅炉贮水箱过冷水调节阀自动,缓慢关小其开度(只需维持循环泵的必需汽蚀余量),最后至全关位置,在随着煤量的缓慢增加,机组负荷慢慢上升,使贮水箱水位不断下降,及时调节锅炉循环泵出口调节阀开度及炉循泵再循环调解阀开度,尽量避免循环泵跳闸,最后将泵出口阀全关,检查贮水箱水位不再上升,则完成锅炉由湿态运行至干态运行的转换。
这种方式较慢,因为在煤水比方式下,在加煤升负荷的时候,水量也会跟着向上加,给水量提高,使回到贮水箱的水减缓的速率变慢,转干态的过程也就长一点。
想加快转干态的过程,就可以撤出给水自动,手动调节水冷壁流量在600t/h左右,只通过加煤,提高分离器出口的过热度,在加煤升负荷的同时,手动调节锅炉循环泵出口调阀和再循环调解阀开度;手动调节时,在保证水冷壁流量的前提下,通过控制给水泵转速来控制贮水箱水位或高水位控制调节阀的开度。
干湿态转换操作
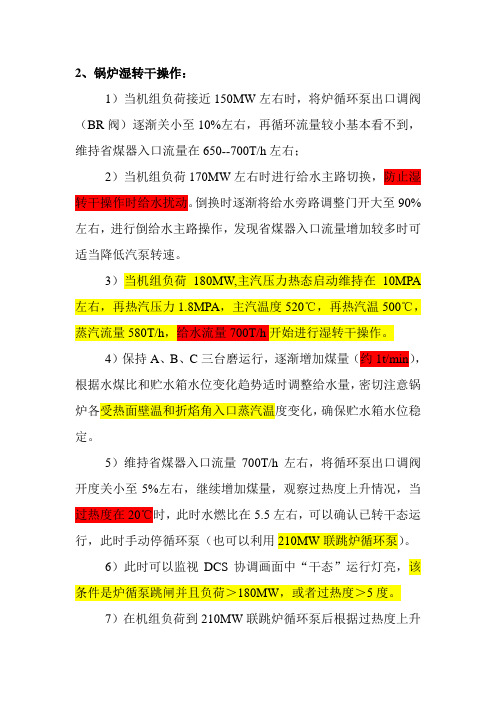
2、锅炉湿转干操作:1)当机组负荷接近150MW左右时,将炉循环泵出口调阀(BR阀)逐渐关小至10%左右,再循环流量较小基本看不到,维持省煤器入口流量在650--700T/h左右;2)当机组负荷170MW左右时进行给水主路切换,防止湿转干操作时给水扰动。
倒换时逐渐将给水旁路调整门开大至90%左右,进行倒给水主路操作,发现省煤器入口流量增加较多时可适当降低汽泵转速。
3)当机组负荷180MW,主汽压力热态启动维持在10MPA 左右,再热汽压力1.8MPA,主汽温度520℃,再热汽温500℃,蒸汽流量580T/h,给水流量700T/h开始进行湿转干操作。
4)保持A、B、C三台磨运行,逐渐增加煤量(约1t/min),根据水煤比和贮水箱水位变化趋势适时调整给水量,密切注意锅炉各受热面壁温和折焰角入口蒸汽温度变化,确保贮水箱水位稳定。
5)维持省煤器入口流量700T/h左右,将循环泵出口调阀开度关小至5%左右,继续增加煤量,观察过热度上升情况,当过热度在20℃时,此时水燃比在5.5左右,可以确认已转干态运行,此时手动停循环泵(也可以利用210MW联跳炉循环泵)。
6)此时可以监视DCS协调画面中“干态”运行灯亮,该条件是炉循泵跳闸并且负荷>180MW,或者过热度>5度。
7)在机组负荷到210MW联跳炉循环泵后根据过热度上升情况适当增加给水量,逐渐增加煤量,根据压力升负荷至230MW,过程中密切监视过热度控制在20℃--30℃左右,防止负荷波动转回湿态运行。
8)转干态后会看见储水箱水位缓慢上升现象属于正常,避免误判断为转回湿态运行。
水位最高可以看见上升至19M,此时是假水位,即使有少量水但经过顶棚和低过、屏过以及末过后对主机没有任何影响。
可以通过开启储水箱至二级减温水电动门,消除储水箱的假水位后,储水箱水位变为负水位,关闭储水箱至二级减温水电动门。
9)在增加煤量的同时密切注意分离器出口温度、过热度和锅炉各受热面壁温不可上升过快,如上升过快要及时加大给水量。
1000MW锅炉由湿态转干态的操作步骤及注意事项
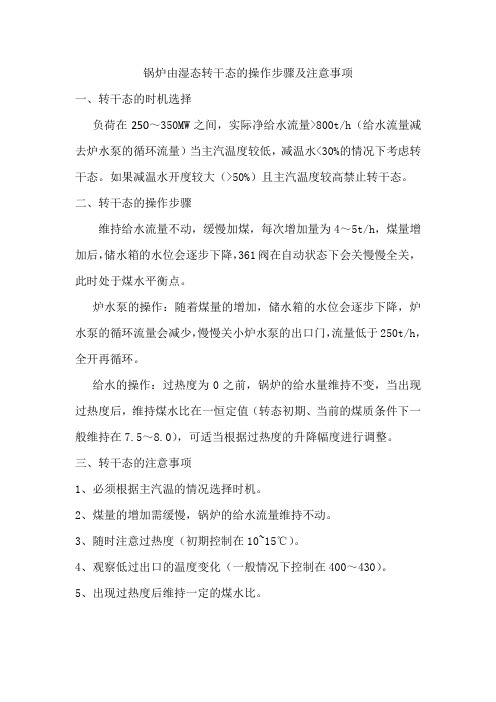
锅炉由湿态转干态的操作步骤及注意事项
一、转干态的时机选择
负荷在250~350MW之间,实际净给水流量>800t/h(给水流量减去炉水泵的循环流量)当主汽温度较低,减温水<30%的情况下考虑转干态。
如果减温水开度较大(>50%)且主汽温度较高禁止转干态。
二、转干态的操作步骤
维持给水流量不动,缓慢加煤,每次增加量为4~5t/h,煤量增加后,储水箱的水位会逐步下降,361阀在自动状态下会关慢慢全关,此时处于煤水平衡点。
炉水泵的操作:随着煤量的增加,储水箱的水位会逐步下降,炉水泵的循环流量会减少,慢慢关小炉水泵的出口门,流量低于250t/h,全开再循环。
给水的操作:过热度为0之前,锅炉的给水量维持不变,当出现过热度后,维持煤水比在一恒定值(转态初期、当前的煤质条件下一般维持在7.5~8.0),可适当根据过热度的升降幅度进行调整。
三、转干态的注意事项
1、必须根据主汽温的情况选择时机。
2、煤量的增加需缓慢,锅炉的给水流量维持不动。
3、随时注意过热度(初期控制在10~15℃)。
4、观察低过出口的温度变化(一般情况下控制在400~430)。
5、出现过热度后维持一定的煤水比。
直流锅炉干湿态转换注意事项

干湿态转换前后注意事项1.目前锅炉在湿态运行过程中,保持省煤器入口流量不超过385T,电动给水泵电流不超212.4A,入口压力不低与0.1Mpa,发现异常及时调整处理。
2.汽动给水泵未并列之前,机组负荷不超80MW,过热蒸汽压力不超8.5Mpa,防止电动给水泵超出力运行。
3.转干态之前,启动分离器水位保持不低于3m,低位361阀开度不低于10%,防止压力突变,瞬间转入干态。
4.目前集水箱水位不准,保持集水箱不低于1400mm,疏水泵自动状态下设定水位1500mm,疏水泵再循环开度50%,注意监视疏水泵出口压力不低于0.03Mpa,如发现异常,及时汇报处理,防止集水箱水位拉空,影响大机凝汽器真空。
5.随着炉膛温度不断升高,煤粉燃烬率不断提高,及时降低给煤量,防止汽压升高,造成分离器水位下降,瞬间转入干态。
6.调整减温水时,注意电动给水泵运行参数,防止给水泵超出力运行。
7.并汽泵时,当汽泵出口压力与电泵出力压力一致时,再开启汽泵出口电动门,观察给水系统运行情况,稳定后,逐步开启电泵再循环门,负荷逐步转至汽泵接待,注意观察给水旁路调节阀自动跟踪情况。
8.当给水旁路调节阀开度大于80%,负荷100MW时,切给水旁路调节阀手动控制,保持开度不变,开启主给水电动门,微调汽泵转速,保持给水流量稳定,给水无扰切至主路运行,稳定后投入给水泵自动。
9.接到转态命令后,保持给水不变(定水调煤),缓慢增加给煤量,观察主蒸汽流量变化,当主蒸汽流量与给水流量一致时,水煤比6.5~7.5,过热度5℃以上,分离器水位到零,判断为转入直流运行。
10.转入直流运行后,及时投入暖管管路。
11.转入直流运行后,汽温、汽压的调整,主要靠水煤比调整为主,手动调整时,先加煤后加水,保持水煤比 6.5~7.5,过热度20℃~30℃。
12.随负荷的逐步增加,增投制粉系统时,要缓慢操作,风粉要同时进行,严禁只加煤不加风,按燃烧调整措施执行。
13.各参数稳定后,尽早投入过热度给水自动,避免人为造成干湿态频繁转换。
干湿态转换操作
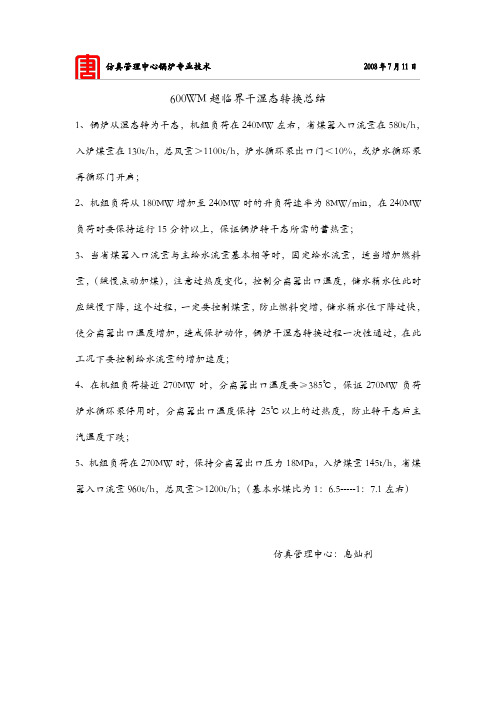
仿真管理中心锅炉专业技术2008年7月11日
600WM超临界干湿态转换总结
1、锅炉从湿态转为干态,机组负荷在240MW左右,省煤器入口流量在580t/h,入炉煤量在130t/h,总风量>1100t/h,炉水循环泵出口门<10%,或炉水循环泵再循环门开启;
2、机组负荷从180MW增加至240MW时的升负荷速率为8MW/min,在240MW 负荷时要保持运行15分钟以上,保证锅炉转干态所需的蓄热量;
3、当省煤器入口流量与主给水流量基本相等时,固定给水流量,适当增加燃料量,(缓慢点动加煤),注意过热度变化,控制分离器出口温度,储水箱水位此时应缓慢下降,这个过程,一定要控制煤量,防止燃料突增,储水箱水位下降过快,使分离器出口温度增加,造成保护动作,锅炉干湿态转换过程一次性通过,在此工况下要控制给水流量的增加速度;
4、在机组负荷接近270MW时,分离器出口温度要≥385℃,保证270MW负荷炉水循环泵停用时,分离器出口温度保持25℃以上的过热度,防止转干态后主汽温度下跌;
5、机组负荷在270MW时,保持分离器出口压力18MPa,入炉煤量145t/h,省煤器入口流量960t/h,总风量>1200t/h;(基本水煤比为1:6.5-----1:7.1左右)
仿真管理中心:息灿利。
直流炉与汽包炉的异同分析
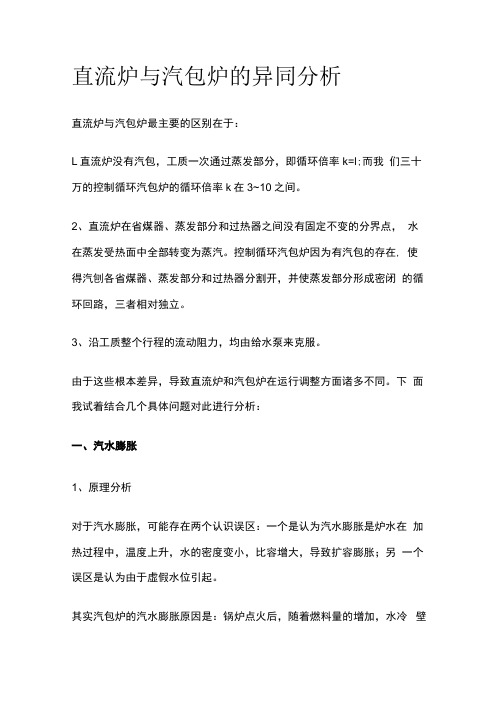
直流炉与汽包炉的异同分析直流炉与汽包炉最主要的区别在于:L直流炉没有汽包,工质一次通过蒸发部分,即循环倍率k=l;而我们三十万的控制循环汽包炉的循环倍率k在3~10之间。
2、直流炉在省煤器、蒸发部分和过热器之间没有固定不变的分界点,水在蒸发受热面中全部转变为蒸汽。
控制循环汽包炉因为有汽包的存在, 使得汽刨各省煤器、蒸发部分和过热器分割开,并使蒸发部分形成密闭的循环回路,三者相对独立。
3、沿工质整个行程的流动阻力,均由给水泵来克服。
由于这些根本差异,导致直流炉和汽包炉在运行调整方面诸多不同。
下面我试着结合几个具体问题对此进行分析:一、汽水膨胀1、原理分析对于汽水膨胀,可能存在两个认识误区:一个是认为汽水膨胀是炉水在加热过程中,温度上升,水的密度变小,比容增大,导致扩容膨胀;另一个误区是认为由于虚假水位引起。
其实汽包炉的汽水膨胀原因是:锅炉点火后,随着燃料量的增加,水冷壁内工质温度逐渐升高,直到某一点形成蒸发点,产生蒸汽。
由于汽水比容差异巨大,造成此处工质体积膨胀,局部压力升高,加速推动蒸发点以后的工质流动,短时间内将大量的水或汽水混合物挤出水冷壁,从而使水冷壁出口流量远大于入口流量。
这才是直流炉的汽水膨胀,是短暂而剧烈变化的过程,而水温变化引起的膨胀是长时间缓慢变化的。
也不同于虚假水位,虚假水位是由于压力波动,导致炉水饱和温度变化引起的。
2、影响因素影响汽水膨胀的主要因素有启动压力、给水温度、锅炉蓄水量、燃料投入量和吸热量分配。
3、危害(1 )、汽水膨胀可能导致分离储水箱满水,引起过热器进水或者锅炉MFT o 由于汽水膨胀过程短暂,只有几十秒钟,并且直流炉没有汽包这样大容量的储水器缓冲吸收,导致分离器储水箱水位急剧上升。
(2 )、汽水膨胀容易导致水冷壁各部分膨胀不均匀,挤压变形。
4、应对方法(1)、锅炉点火后燃料投入率应该平稳缓慢;(2 )、发生汽水膨胀时应该加强WDC阀、水位的监视。
WDC阀投入自动,加强排水。
直流炉干湿态转换过程浅析
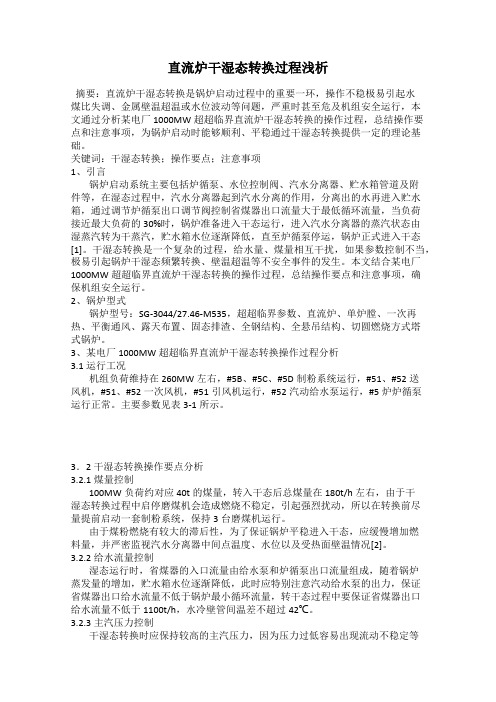
直流炉干湿态转换过程浅析摘要:直流炉干湿态转换是锅炉启动过程中的重要一环,操作不稳极易引起水煤比失调、金属壁温超温或水位波动等问题,严重时甚至危及机组安全运行,本文通过分析某电厂1000MW超超临界直流炉干湿态转换的操作过程,总结操作要点和注意事项,为锅炉启动时能够顺利、平稳通过干湿态转换提供一定的理论基础。
关键词:干湿态转换;操作要点;注意事项1、引言锅炉启动系统主要包括炉循泵、水位控制阀、汽水分离器、贮水箱管道及附件等,在湿态过程中,汽水分离器起到汽水分离的作用,分离出的水再进入贮水箱,通过调节炉循泵出口调节阀控制省煤器出口流量大于最低循环流量,当负荷接近最大负荷的30%时,锅炉准备进入干态运行,进入汽水分离器的蒸汽状态由湿蒸汽转为干蒸汽,贮水箱水位逐渐降低,直至炉循泵停运,锅炉正式进入干态[1]。
干湿态转换是一个复杂的过程,给水量、煤量相互干扰,如果参数控制不当,极易引起锅炉干湿态频繁转换、壁温超温等不安全事件的发生。
本文结合某电厂1000MW超超临界直流炉干湿态转换的操作过程,总结操作要点和注意事项,确保机组安全运行。
2、锅炉型式锅炉型号:SG-3044/27.46-M535,超超临界参数、直流炉、单炉膛、一次再热、平衡通风、露天布置、固态排渣、全钢结构、全悬吊结构、切圆燃烧方式塔式锅炉。
3、某电厂1000MW超超临界直流炉干湿态转换操作过程分析3.1运行工况机组负荷维持在260MW左右,#5B、#5C、#5D制粉系统运行,#51、#52送风机,#51、#52一次风机,#51引风机运行,#52汽动给水泵运行,#5炉炉循泵运行正常。
主要参数见表3-1所示。
3.2干湿态转换操作要点分析3.2.1煤量控制100MW负荷约对应 40t的煤量,转入干态后总煤量在180t/h左右,由于干湿态转换过程中启停磨煤机会造成燃烧不稳定,引起强烈扰动,所以在转换前尽量提前启动一套制粉系统,保持3台磨煤机运行。
20101121锅炉干湿态转换的操作要点
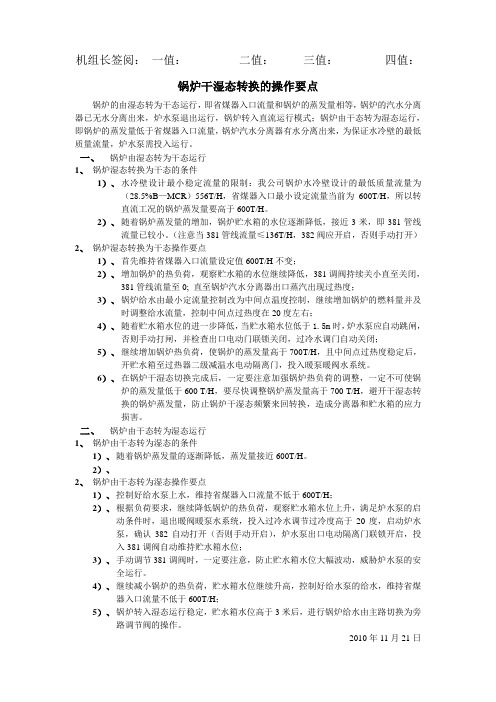
机组长签阅:一值:二值:三值:四值:锅炉干湿态转换的操作要点锅炉的由湿态转为干态运行,即省煤器入口流量和锅炉的蒸发量相等,锅炉的汽水分离器已无水分离出来,炉水泵退出运行,锅炉转入直流运行模式;锅炉由干态转为湿态运行,即锅炉的蒸发量低于省煤器入口流量,锅炉汽水分离器有水分离出来,为保证水冷壁的最低质量流量,炉水泵需投入运行。
一、锅炉由湿态转为干态运行1、锅炉湿态转换为干态的条件1)、水冷壁设计最小稳定流量的限制:我公司锅炉水冷壁设计的最低质量流量为(28.5%B—MCR)556T/H,省煤器入口最小设定流量当前为600T/H,所以转直流工况的锅炉蒸发量要高于600T/H。
2)、随着锅炉蒸发量的增加,锅炉贮水箱的水位逐渐降低,接近3米,即381管线流量已较小。
(注意当381管线流量≤136T/H,382阀应开启,否则手动打开)2、锅炉湿态转换为干态操作要点1)、首先维持省煤器入口流量设定值600T/H不变;2)、增加锅炉的热负荷,观察贮水箱的水位继续降低,381调阀持续关小直至关闭,381管线流量至0; 直至锅炉汽水分离器出口蒸汽出现过热度;3)、锅炉给水由最小定流量控制改为中间点温度控制,继续增加锅炉的燃料量并及时调整给水流量,控制中间点过热度在20度左右;4)、随着贮水箱水位的进一步降低,当贮水箱水位低于1.5m时,炉水泵应自动跳闸,否则手动打闸,并检查出口电动门联锁关闭,过冷水调门自动关闭;5)、继续增加锅炉热负荷,使锅炉的蒸发量高于700T/H,且中间点过热度稳定后,开贮水箱至过热器二级减温水电动隔离门,投入暖泵暖阀水系统。
6)、在锅炉干湿态切换完成后,一定要注意加强锅炉热负荷的调整,一定不可使锅炉的蒸发量低于600 T/H,要尽快调整锅炉蒸发量高于700 T/H,避开干湿态转换的锅炉蒸发量,防止锅炉干湿态频繁来回转换,造成分离器和贮水箱的应力损害。
二、锅炉由干态转为湿态运行1、锅炉由干态转为湿态的条件1)、随着锅炉蒸发量的逐渐降低,蒸发量接近600T/H。
干湿态转换操作要点分析
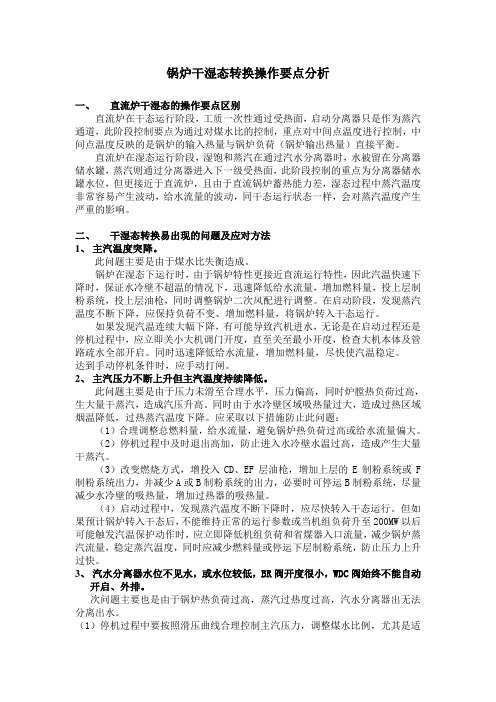
锅炉干湿态转换操作要点分析一、直流炉干湿态的操作要点区别直流炉在干态运行阶段,工质一次性通过受热面,启动分离器只是作为蒸汽通道,此阶段控制要点为通过对煤水比的控制,重点对中间点温度进行控制,中间点温度反映的是锅炉的输入热量与锅炉负荷(锅炉输出热量)直接平衡。
直流炉在湿态运行阶段,湿饱和蒸汽在通过汽水分离器时,水被留在分离器储水罐,蒸汽则通过分离器进入下一级受热面,此阶段控制的重点为分离器储水罐水位,但更接近于直流炉,且由于直流锅炉蓄热能力差,湿态过程中蒸汽温度非常容易产生波动,给水流量的波动,同干态运行状态一样,会对蒸汽温度产生严重的影响。
二、干湿态转换易出现的问题及应对方法1、主汽温度突降。
此问题主要是由于煤水比失衡造成。
锅炉在湿态下运行时,由于锅炉特性更接近直流运行特性,因此汽温快速下降时,保证水冷壁不超温的情况下,迅速降低给水流量,增加燃料量,投上层制粉系统,投上层油枪,同时调整锅炉二次风配进行调整。
在启动阶段,发现蒸汽温度不断下降,应保持负荷不变、增加燃料量,将锅炉转入干态运行。
如果发现汽温连续大幅下降,有可能导致汽机进水,无论是在启动过程还是停机过程中,应立即关小大机调门开度,直至关至最小开度,检查大机本体及管路疏水全部开启。
同时迅速降低给水流量,增加燃料量,尽快使汽温稳定。
达到手动停机条件时,应手动打闸。
2、主汽压力不断上升但主汽温度持续降低。
此问题主要是由于压力未滑至合理水平,压力偏高,同时炉膛热负荷过高,生大量干蒸汽,造成汽压升高。
同时由于水冷壁区域吸热量过大,造成过热区域烟温降低,过热蒸汽温度下降。
应采取以下措施防止此问题:(1)合理调整总燃料量,给水流量,避免锅炉热负荷过高或给水流量偏大。
(2)停机过程中及时退出高加,防止进入水冷壁水温过高,造成产生大量干蒸汽。
(3)改变燃烧方式,增投入CD、EF层油枪,增加上层的E制粉系统或F 制粉系统出力,并减少A或B制粉系统的出力,必要时可停运B制粉系统,尽量减少水冷壁的吸热量,增加过热器的吸热量。
盘式干燥机说明书
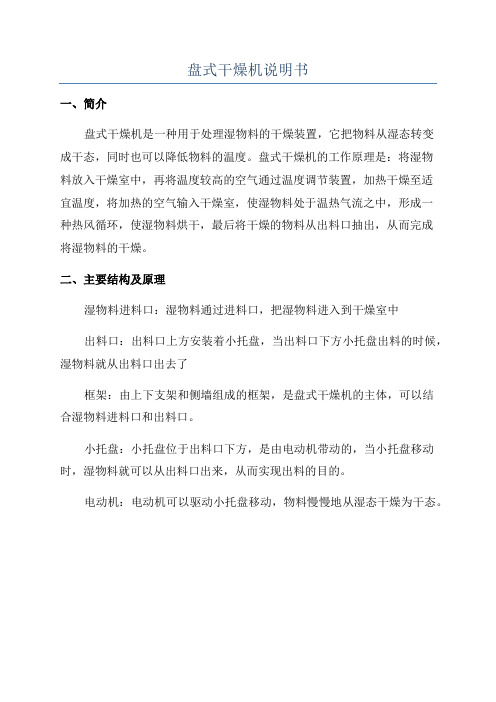
盘式干燥机说明书
一、简介
盘式干燥机是一种用于处理湿物料的干燥装置,它把物料从湿态转变
成干态,同时也可以降低物料的温度。
盘式干燥机的工作原理是:将湿物
料放入干燥室中,再将温度较高的空气通过温度调节装置,加热干燥至适
宜温度,将加热的空气输入干燥室,使湿物料处于温热气流之中,形成一
种热风循环,使湿物料烘干,最后将干燥的物料从出料口抽出,从而完成
将湿物料的干燥。
二、主要结构及原理
湿物料进料口:湿物料通过进料口,把湿物料进入到干燥室中
出料口:出料口上方安装着小托盘,当出料口下方小托盘出料的时候,湿物料就从出料口出去了
框架:由上下支架和侧墙组成的框架,是盘式干燥机的主体,可以结
合湿物料进料口和出料口。
小托盘:小托盘位于出料口下方,是由电动机带动的,当小托盘移动时,湿物料就可以从出料口出来,从而实现出料的目的。
电动机:电动机可以驱动小托盘移动,物料慢慢地从湿态干燥为干态。
火电机组深度调峰操作及其注意事项
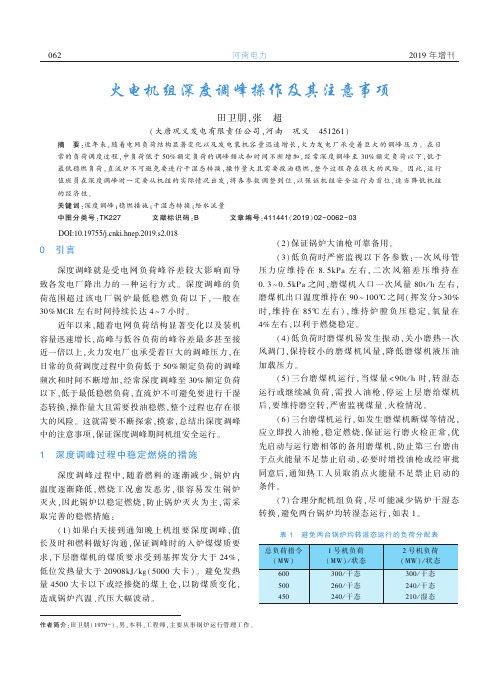
062㊀河南电力2019年增刊火电机组深度调峰操作及其注意事项田卫朋,张㊀超(大唐巩义发电有限责任公司,河南㊀巩义㊀451261)作者简介:田卫朋(1979-),男,本科,工程师,主要从事锅炉运行管理工作㊂摘㊀要:近年来,随着电网负荷结构显著变化以及发电装机容量迅速增长,火力发电厂承受着巨大的调峰压力㊂在日常的负荷调度过程,中负荷低于50%额定负荷的调峰频次和时间不断增加,经常深度调峰至30%额定负荷以下,低于最低稳燃负荷,直流炉不可避免要进行干湿态转换,操作量大且需要投油稳燃,整个过程存在很大的风险㊂因此,运行值班员在深度调峰时一定要从机组的实际情况出发,将各参数调整到位,以保证机组安全运行为首位,适当降低机组的经济性㊂关键词:深度调峰;稳燃措施;干湿态转换;给水流量中图分类号:TK227㊀㊀㊀㊀文献标识码:B㊀㊀㊀㊀文章编号:411441(2019)02-0062-030㊀引言深度调峰就是受电网负荷峰谷差较大影响而导致各发电厂降出力的一种运行方式㊂深度调峰的负荷范围超过该电厂锅炉最低稳燃负荷以下,一般在30%MCR 左右时间持续长达4~7小时㊂近年以来,随着电网负荷结构显著变化以及装机容量迅速增长,高峰与低谷负荷的峰谷差最多甚至接近一倍以上,火力发电厂也承受着巨大的调峰压力,在日常的负荷调度过程中负荷低于50%额定负荷的调峰频次和时间不断增加,经常深度调峰至30%额定负荷以下,低于最低稳燃负荷,直流炉不可避免要进行干湿态转换,操作量大且需要投油稳燃,整个过程也存在很大的风险㊂这就需要不断探索,摸索,总结出深度调峰中的注意事项,保证深度调峰期间机组安全运行㊂1㊀深度调峰过程中稳定燃烧的措施深度调峰过程中,随着燃料的逐渐减少,锅炉内温度逐渐降低,燃烧工况愈发恶劣,很容易发生锅炉灭火,因此锅炉以稳定燃烧,防止锅炉灭火为主,需采取完善的稳燃措施:(1)如果白天接到通知晚上机组要深度调峰,值长及时和燃料做好沟通,保证调峰时的入炉煤煤质要求,下层磨煤机的煤质要求受到基挥发分大于24%,低位发热量大于20908kJ /kg(5000大卡)㊂避免发热量4500大卡以下或经掺烧的煤上仓,以防煤质变化,造成锅炉汽温㊁汽压大幅波动㊂(2)保证锅炉大油枪可靠备用㊂(3)低负荷时严密监视以下各参数:一次风母管压力应维持在8.5kPa 左右,二次风箱差压维持在0.3~0.5kPa 之间,磨煤机入口一次风量80t /h 左右,磨煤机出口温度维持在90~100ħ之间(挥发分>30%时,维持在85ħ左右),维持炉膛负压稳定,氧量在4%左右,以利于燃烧稳定㊂(4)低负荷时磨煤机易发生振动,关小磨热一次风调门,保持较小的磨煤机风量,降低磨煤机液压油加载压力㊂(5)三台磨煤机运行,当煤量<90t /h 时,转湿态运行或继续减负荷,需投入油枪,停运上层磨给煤机后,要维持磨空转,严密监视煤量㊁火检情况㊂(6)三台磨煤机运行,如发生磨煤机断煤等情况,应立即投入油枪,稳定燃烧,保证运行磨火检正常,优先启动与运行磨相邻的备用磨煤机,防止第三台磨由于点火能量不足禁止启动,必要时增投油枪或经审批同意后,通知热工人员取消点火能量不足禁止启动的条件㊂(7)合理分配机组负荷,尽可能减少锅炉干湿态转换,避免两台锅炉均转湿态运行,如表1㊂表1㊀避免两台锅炉均转湿态运行的负荷分配表总负荷指令(MW)1号机负荷(MW)/状态2号机负荷(MW)/状态600300/干态300/干态500260/干态240/干态450240/干态210/湿态DOI:10.19755/ki.hnep.2019.s2.0182019年增刊田卫朋,等:火电机组深度调峰操作及其注意事项063㊀㊀㊀机组湿态运行,负荷接近160MW时,为维持燃烧稳定,在不减少总燃料的情况下,降低负荷主要依靠分离器疏水大量外排,这部分疏水水质不合格的情况下,无法回收,除盐水补水量很难维持凝汽器水位,因此湿态运行的最低负荷要控制在160MW以上㊂另外,根据各机组凝汽器平均背压情况,保留一台真空泵运行,开启机侧主蒸汽管道疏水手动门㊁气动门,维持凝汽器平均背压为8~12kPa,这样机组的煤耗虽然增加了,却避免处于干湿态临界状态时被迫转湿态运行,同时降低了机组的电负荷而保证机组的热负荷,有利于锅炉稳定燃烧㊂这期间要注意大机轴向位移㊁低缸排汽温度等,当凝汽器背压超过12kPa,应及时启动备用真空泵运行㊂(8)如果出现锅炉金属管壁超温情况,要果断增加给水量,适当减少煤量,温度回头后及时恢复总燃料量㊂通过调整燃烧器上下摆角(低负荷时保持水平位置禁止操作)㊁二次风档板㊁磨煤机进口风量等手段调节,操作幅度不可过大,以免导致燃烧不稳锅炉灭火㊂(9)深调峰过程中运行人员应随时作好锅炉灭火的事故预想㊂学习防止锅炉灭火的技术措施,锅炉MFT后的吹扫㊁点火程序及方法,极热态㊁热态启动注意事项㊂2㊀深度调峰过程中防止给水流量低的措施深度调峰过程中随着负荷的降低,四抽压力以及给水流量也在不断地降低,为防止给水流量低MFT,在调峰期间要严密监视给水流量的变化,采取防止给水流量低的措施㊂(1)邻机辅汽联络管道㊁辅汽联箱㊁辅汽至小机管道充分疏水暖管,防止小机进汽参数低,汽泵转速突降造成给水流量低㊂(2)深度调峰过程中机组负荷小于250MW要求对小机汽源切换,切汽源过程尽量在负荷高时进行,切换汽源时冷再至辅汽管道要充分疏水暖管,冷再至辅汽电动门必须采取缓慢间断开启方式进行,必要时手动操作,检查小机进汽调门动作正常,小机转速,流量稳定㊂注意防止冷再㊁四抽在切换过程中串汽造成小机不出力,导致给水流量低保护动作,严防辅汽压力突升造成小机超速㊂(3)深度调峰过程中给水一般维持在700~800t/h,省煤器进口流量低,汽泵再循环阀自动开启过程中极易造成给水流量大幅波动,导致给水流量低MFT,因此当负荷330MW时,若需继续减负荷,要可提前开启汽泵再循环阀至固定开度(30%),以达到稳定给水的目的㊂3㊀深度调峰时的其他注意事项(1)干态运行要注意中间点过热度至少5ħ以上;湿态运行,出现主再热蒸汽温度突降,分离器水位高,要及时调节大气扩容器溢流阀,必要时快速增加燃料量,开启机侧主㊁再热蒸汽管道疏水;严防汽轮机水冲击㊂(2)机组向240MW以下减负荷时,维持锅炉侧燃料不变,进行转湿态操作前,提前开启锅炉大气扩容器进口1㊁2号溢流阀前电动门,大气扩容器溢流阀开启5%开度,分离器见水后,逐步增大给水流量,增加大气扩容器外排量以降低机组负荷㊂(3)因转湿态前注意凝汽器水位提前补水至高水位,防止大气扩容器大量外排时凝汽器水位低㊂(4)在减负荷时应注意凝结水再循环调门在自动或提前手动开启㊂(5)注意轴封压力和温度,必要时投入轴封供汽电加热器,稍开辅汽至轴封供汽旁路电动门㊂(6)及时投入0号高加,提高脱硝进口烟气温度,促使烟气温度达到SCR催化剂运行要求㊂当脱硝进口烟温任一测点低于300ħ时,申请解除脱硝入口烟温低保护,如脱硝催化剂入口烟温任意两个测点低于295ħ时,在脱硝进口温度保护解除前,暂停降负荷,避免NOx超标㊂(7)加强对石子煤系统的排放,如有石子煤带粉㊁堵塞等现象及时处理,防止磨煤机堵煤,严重时引起一次风机喘振的发生㊂4㊀深度调峰时的干湿态转换及注意事项深度调峰尽量避免进行锅炉的干湿态转换,但当无法避免时,就要对干湿态转换的过程熟记于心,以应对各种突发状况㊂4.1㊀转换的时间由于直流炉没有明显的汽水分界面,所以当燃水比严重失调时干湿态就会转换,而与机组的负荷和蒸汽参数没有严格的关系㊂但是为了保证螺旋水冷壁064㊀河南电力2019年增刊的安全和水动力特性的稳定,一般设计上要求:不带强制循环直流炉在20%MCR左右,带强制循环直流炉在30%MCR左右进行干湿态转换㊂但是在实际运行中,为了充分保证螺旋水冷壁的安全,规定 不带强制循环直流炉在30%MCR(198MW)左右,带强制循环直流炉在40%MCR(264MW)左右 进行干湿态转换㊂4.2㊀转换的方法4.2.1㊀湿态向干态转换(1)湿态向干态转换㊂当机组负荷到达210~ 240MW左右时,此时的燃料量应该是两套制粉系统100t/h左右和部分投入油枪的油量折算煤量的总和㊂㊀㊀㊀(2)汽水分离器出口温度已经达到对应压力下的饱和温度(10MPa对应311ħ),储水箱水位多次呈现下降趋势,此时应该考虑锅炉转直流运行㊂(3)暖第三台磨,必要时增投对应磨煤机的两支油枪,保持给水流量不变(700~800t/h),投第三台磨,开汽轮机调门㊂(4)随着负荷逐渐增加,分离器出口产生10~ 20ħ的过热度,分离器水位逐渐降低直到消失,注意大气扩容器液控阀逐渐关小直到关闭㊂(5)视过热度的大小来确定是否增加给水流量,稳定中间点温度㊁过热器出口汽温㊁汽压㊂(6)转直流运行后,投溢流管道暖管㊂4.2.2㊀干态向湿态转换(1)当机组负荷降到300MW左右时,燃料量应该是三套制粉系统㊂(2)减少一台磨煤机的出力,必要时投入油枪,维持锅炉燃烧稳定,维持给水流量稳定(700~800t/h),机组负荷不大幅度下降㊂(3)逐渐减少给煤量,让分离器和储水箱见水,逐步开启大气扩容器液控阀,维持在5~8米㊂随着燃料量减少,分离器外排水量增加,注意观察机组负荷逐渐下降(可提前开启大气扩容器液控阀5%开度,以防液控阀前后差压高卡涩)㊂(4)转湿态后,退出大气扩容器溢流管道暖管㊂4.2.3㊀干湿态转换注意事项(1)干湿态转换过程中,若遇到煤质差㊁给煤机堵煤㊁断煤等,都必须及时投油稳燃,必要时启动备用制粉系统,保证锅炉的热负荷稳定㊂(2)通过大气扩容器液控阀调节分离器水位在5~8米之间,防止水位大幅波动㊂水位过高,易引起锅炉汽温突降,过热器产生极大的热应力而损坏,严重时造成汽轮机水冲击㊂水位过低,分离器大量蒸汽外排,溢流管振动,引起扩容器损坏㊂另外,进入过热器的蒸汽减少,会使过热器壁温超温,即所谓 蒸汽走短路 ㊂若大气扩容器液控阀自动控制,会闭锁其开启,不利于分离器水位控制㊂(3)湿态向干态转换时主汽压力一般在9~ 10MPa,此时增加燃烧量,主汽压力增长较快,会使压力高于正常值,对水位的修正增大,影响对水位的显示㊂适当降低主汽压力,有助于过热度的产生,同时也可防止压力高闭锁液控阀开启㊂(4)湿态向干态转换时,增加燃料要迅速,并且燃料量要大些,防止锅炉转换成干态后又返回成湿态,造成汽温㊁汽压波动㊂增加燃料,特别是需要增启第三台磨煤机时,要注意监视水冷壁壁温,尤其是后墙悬吊管的金属壁温㊂(5)相应地干态向湿态转换时,最低稳燃负荷以下,要适当的增投油枪,维持锅炉燃烧稳定,维持给水稳定,逐渐减小燃料量使储水箱见水,并维持水位㊂必要时可适当增加给水量,但不能太大,否则主蒸汽温度会急剧下降㊂(6)干态向湿态转换之前,确认集水箱排污管工业冷却水手动门开启㊂(7)锅炉的干湿态转换只是一个平稳的过渡过程,以中间点过热度和水位来判断干湿态转换是否成功,切换过程中不要造成锅炉主再热汽温㊁汽压大幅度的变化,机组的出力大幅度变化㊂5㊀结语深度调峰的技术措施和注意事项,是在不断总结调峰经验中得出的㊂在深度调峰时,不可避免地会遇到上述问题,行之有效的控制措施会使机组设备能够最大限度地保持良好的状态㊂如果控制措施不得力,就会使设备受损㊁MFT事故发生㊂所以运行值班员在深度调峰时一定要从机组的实际情况出发,将各参数调整到位,以保证机组安全运行为首位,适当降低机组的经济性㊂收稿日期:2018-07-10。
660MW超超临界机组锅炉湿态转干态简析
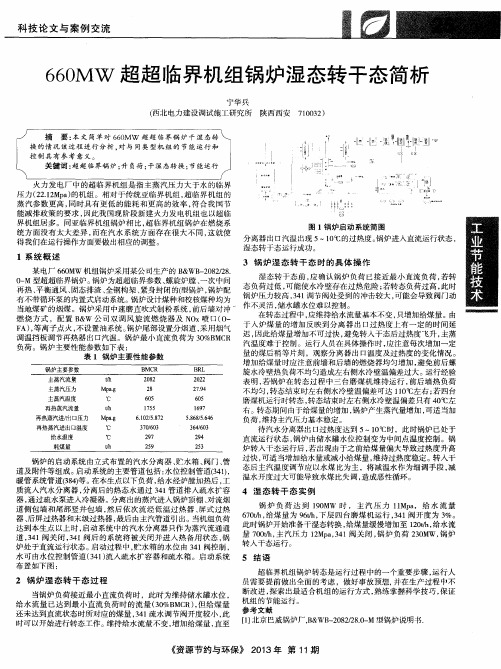
3 锅 炉湿态 转 干态 时的具体 操作
湿 态转干态 前, 应确认 锅炉负荷 已接近最小直 流负荷 , 若转 态负荷过低 , 可能使水冷壁存 在过热危险 ; 若转态 负荷过高 , 此时 锅炉压力较高 , 3 4 1 调节阀处受 到的冲击较大 , 可能会导致 阀门动 作不灵活 , 储水罐水位难 以控制。 在转态过程中, 应维持给水流量基本不变 , 只增加给煤量 。由 于 人炉煤 量 的增加反 映到分离 器出 口过热度 上有一定 的时间延 迟, 因此给煤量增加不可过快 , 避免转入 干态后过热度 飞升 , 主蒸 汽温度难于控制 。运行人员在具体操作 时, 应注意每次增 加一定 量 的煤后稍等片刻 ,观察分离器 出 口温度及过热度 的变化情况 。 增加给煤量时应注意前墙和后墙的燃烧器均匀增加 , 避免前后 螺 旋水冷壁热负荷不均匀造成左右侧水 冷壁温偏差过大。运行经验 表 明, 若锅炉在转 态过程 中三 台磨煤机维 持运行 , 前后墙热 负荷 不均匀 , 转态结束时左 右侧水冷壁温偏差可达 1 1 0 %左右 ; 若 四台 磨煤机运行 时转态 , 转态结束时左右侧水冷壁温偏差 只有 4 0  ̄ C 左 右。转态期间 由于给煤量 的增加 , 锅炉产生蒸汽量增加 , 可适当加 负荷 , 维持主汽压力基本稳定 。 待汽水分离器 出口过热度达 到 5 ~1 0  ̄ C 时 ,此时锅炉 已处 于 直流运行状态 , 锅炉 由储水罐水位控制 变为中间点温度控制 。锅 炉转人干态运行后 , 若 出现 由于之前给煤量偏大 导致过热度升 高 过快 , 可适当增 加给水量或减小给煤量 , 维持过热度稳定 。转入 干 锅炉的启动 系统 由立式布置 的汽水 分离器 、 贮水箱 、 阀门 、 管 态后主汽温度调节应以水煤 比为主 ,将减温水作为细调手段 , 减 道及附件等组成 。 启 动系统 的主要管道包括 : 水位控制管道( 3 4 1 ) , 温水 开度过大可能导致水煤 比失调 , 造成 恶性循环 。 暖管系统管道( 3 8 4 ) 等。 在本生点 以下负荷 , 给水经 炉膛加热后 , 工 质流入汽水分离器 , 分离后 的热态水通过 3 4 1 管道排人疏水 扩容 4 湿 态转 干态 实例 器, 通过疏水泵进入冷凝器 。 分 离 出 的 蒸 汽 进 入锅 炉顶 棚 、 对 流 烟 锅 炉 负荷 达 到 1 9 0 MW 时 ,主 汽 压 力 1 1 Mp a ,给 水 流 量 道侧包墙 和尾部竖井包墙 , 然后 依次流经 低温过 热器 、 屏式过热 6 7 0 t / h , 给煤量为 9 6 t / h , 下层 四台磨煤 机运行 , 3 4 1阀开度为 3 %。 器、 后屏过热器和末级过热器 , 最后 由主汽管道引 出。当机组 负荷 此时锅炉开始准备干湿态转换 , 给煤量缓慢增加至 1 2 0 t / h , 给水流 达到本生点 以上时 , 启动系统中的汽水分离器 只作 为蒸汽 流通通 0 0 t / h , 主汽压力 1 2 Mp a , 3 4 1阀关 闭 , 锅炉 负荷 2 3 0 MW, 锅炉 道, 3 4 1阀关 闭 , 3 4 1阀后 的系统 将被关 闭并进入热备 用状态 , 锅 量 7 转人干态运行 。 炉处于直流运行状态 。 启动过程 中, 贮水箱 的水位 由 3 4 1阀控制 , 水 可 由水位控制管道 ( 3 4 1 ) 流人疏水扩容器和疏水箱 。启动 系统 5 结 语 布 置如下图 : 超临界机组锅炉转态是运行过程 中的一个重要步骤 , 运行人 2 锅 炉湿 态转 干 态过 程 员需要提 前做 出全 面的考虑 ,做好事故 预想, 并在生产过程 中不 探索出最适合机组的运行方式 , 熟 练掌握科 学技 巧 , 保证 当锅炉 负荷 接近最小直流负荷时 ,此时 为维持储水罐水位 , 断改进 , 机 组 的节 能 运 行 。 给水流量 已达到最小 直流负荷 时 的流 量( 3 0 %B MC R) , 但 给煤量 还未达 到直流状态时所对应的煤量 , 3 4 1 疏水调节阀开度较 小 , 此 参 考 文 献 … 北京 巴威锅炉厂, B &WB 一 2 0 8 2 / 2 8 . 0 一 M 型锅炉说 明书. 时 可以开始进行转态工作 。 维持 给水 流量不变 , 增加给煤量 , 直至
化学水汽监督新标准
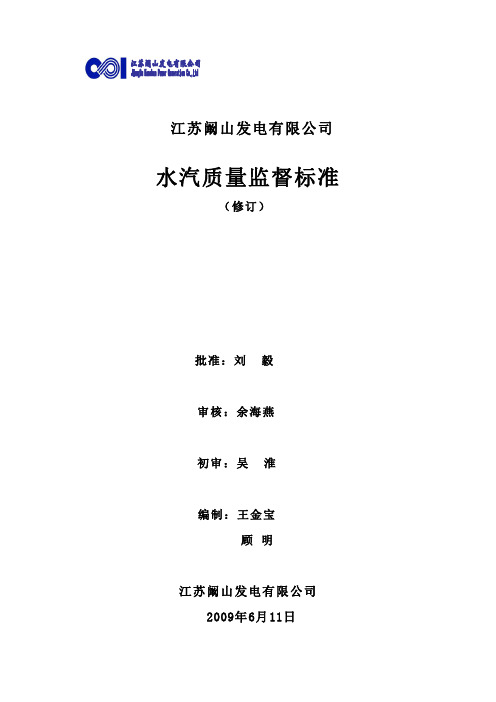
江苏阚山发电有限公司水汽质量监督标准(修订)批准:刘毅审核:余海燕初审:吴淮编制:王金宝顾明江苏阚山发电有限公司2009年6月11日修编说明因原规程《化水运行规程(B版)》依据的“GB/T12145-1999火力发电机组及蒸汽动力设备水汽质量”标准已进行修订,为更好地保证本厂超超临界机组水汽质量、机组安全,特依据新颁发“GB/T12145-2008火力发电机组及蒸汽动力设备水汽质量”对原规程中水汽质量监督标准进行修编。
一、范围:1、机组启动水汽质量标准2、加氨工况AVT(O)水汽质量标准3、加氧工况CWT水汽质量标准4、水汽劣化处理标准值二、依据:1、GB/T12145-2008火力发电机组及蒸汽动力设备水汽质量2、DL/T912—2005超临界火力发电机组水汽质量标准3、同类型超超临界机组水汽质量标准三、实施与作废:本修编的水汽质量监督标准2009.08.01开始实施,原《化水运行规程(B版)》中水汽质量监督标准同时作废。
第一部分水汽质量标准1机组启动水质标准注:1、* 表示参考项目2、汽机冲转后8小时内蒸汽应达到正常运行水质标准。
3、热启动时2小时内、冷启动时8小时内给水应达到正常运行时水质标准2加氨工况[AVT(O)]水汽质量标准:(正常运行)3加氧工况(CWT)水汽质量标准(正常运行)第二部分水汽劣化处理1 处理原则1.1热力设备水汽质量劣化时,应加强分析,根据分析情况,会同有关专业共同分析,判断出劣化原因,决定处理方法,尽快使水汽品质恢复正常。
1.2发现水汽质量异常,化学人员应首先检查取样化验的准确性,药品的质量和取样的代表性,检查给水各组成部分的水质变化情况,确定判断无误后,立即向主值、值长汇报。
1.3若经多方处理,水汽质量仍不能改善并继续迅速劣化时应及时向有关领导汇报,若可能导致设备损坏,严重威胁安全运行时,应向有关领导申请降低出力或停止运行,并进行消缺,当有关领导做出决定后,主值应立即安排值班人员做好善后工作。
运行操作技术措施(锅炉干、湿态转换注意事项)
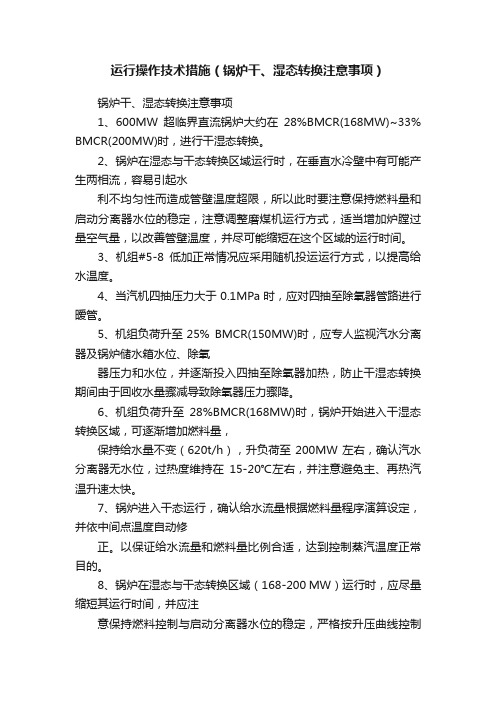
运行操作技术措施(锅炉干、湿态转换注意事项)锅炉干、湿态转换注意事项1、600MW超临界直流锅炉大约在28%BMCR(168MW)~33% BMCR(200MW)时,进行干湿态转换。
2、锅炉在湿态与干态转换区域运行时,在垂直水冷壁中有可能产生两相流,容易引起水利不均匀性而造成管壁温度超限,所以此时要注意保持燃料量和启动分离器水位的稳定,注意调整磨煤机运行方式,适当增加炉膛过量空气量,以改善管壁温度,并尽可能缩短在这个区域的运行时间。
3、机组#5-8低加正常情况应采用随机投运运行方式,以提高给水温度。
4、当汽机四抽压力大于0.1MPa时,应对四抽至除氧器管路进行暧管。
5、机组负荷升至25% BMCR(150MW)时,应专人监视汽水分离器及锅炉储水箱水位、除氧器压力和水位,并逐渐投入四抽至除氧器加热,防止干湿态转换期间由于回收水量骤减导致除氧器压力骤降。
6、机组负荷升至28%BMCR(168MW)时,锅炉开始进入干湿态转换区域,可逐渐增加燃料量,保持给水量不变(620t/h),升负荷至200MW左右,确认汽水分离器无水位,过热度维持在15-20℃左右,并注意避免主、再热汽温升速太快。
7、锅炉进入干态运行,确认给水流量根据燃料量程序演算设定,并依中间点温度自动修正。
以保证给水流量和燃料量比例合适,达到控制蒸汽温度正常目的。
8、锅炉在湿态与干态转换区域(168-200 MW)运行时,应尽量缩短其运行时间,并应注意保持燃料控制与启动分离器水位的稳定,严格按升压曲线控制汽压的稳定,以防止锅炉受热面金属温度的波动。
9、锅炉转入纯直流运行后启动系统集水箱水位逐渐降低,此时应将疏水泵往凝汽器管道上阀门置于闭锁状态,防止由启动系统漏空气导致凝汽器真空降低而影响机组的正常运行。
10、锅炉在纯直流运行之后,汽水分离器出口温度是最能及时反映煤水比的参数,因此要做重点监视。
在保证汽水分离器出口的蒸汽温度具有足够的过热度。
在燃料量、蒸发量(负荷)和炉管外侧污染系数不变的条件下,改变启动分离器出口温度能改变炉膛受热面吸热和锅炉尾部受热面的比例。
- 1、下载文档前请自行甄别文档内容的完整性,平台不提供额外的编辑、内容补充、找答案等附加服务。
- 2、"仅部分预览"的文档,不可在线预览部分如存在完整性等问题,可反馈申请退款(可完整预览的文档不适用该条件!)。
- 3、如文档侵犯您的权益,请联系客服反馈,我们会尽快为您处理(人工客服工作时间:9:00-18:30)。
众所周知,过热蒸汽温度与再热蒸汽温度直接影响到机组的安全性与经济性。
蒸汽温度过高可能导致受热面超温爆管,而蒸汽温度过低将使机组的经济性降低,严重时可能使汽轮机产生水冲击。
超临界直流锅炉的运行调节特性有别于汽包炉,给水控制与汽温调节的配合更为密切,下面谈一下自己的认识。
根据锅炉的运行方式、参数可分为三个阶段;第一启动及低负荷运行阶段,第二亚临界直流炉运行阶段,第三超临界直流炉运行阶段。
每个阶段的调节方法和侧重点有所不同。
1 第一阶段:锅炉启动及低负荷运行阶段不同容量的锅炉其转干态直流运行的最低负荷有所不同,一般在25%~35% BMCR 之间,在湿态情况下,其运行方式与强制循环汽包炉是基本相同的。
汽水分离器及贮水罐就相当于汽包,但是两者容积相差甚远,贮水罐的水位变化速度也就更快。
由炉水循环泵将贮水罐的水升压进入省煤器入口,与给水共同构成最小循环流量。
其控制方式较之其它超临界直流锅炉(不带炉水循环泵,贮水罐的水经361 阀直接排放至锅炉疏扩、除氧器、凝汽器等)有较大不同,控制更困难。
给水主要用于控制贮水罐水位,炉水循环泵出口调阀控制省煤器入口流量保证锅炉的最小循环流量,贮水罐水位过高时则通过361 阀排放至锅炉疏水扩容器。
此阶段汽温的调节主要依赖于燃烧控制,通过投退油枪的数量及层次、调节炉前油压、减温水、烟气挡板等手段来调节主再热蒸汽温度在第一阶段水位控制已可投自动,但是大多数锅炉的水位控制逻辑还不够完善,只是单纯的控制一点水位,还没有投三冲量控制,当扰动较大时水位会产生较大的波动,甚至根本无法平衡。
此阶段要注意尽量避免太大的扰动,扰动过大及早解除自动,手动控制。
根据经验,炉水循环泵出口360 阀一般不投自动(以防360 阀开度过大BCP 电机过流),在启动时保持一恒定的给水流量(适当大于最小流量),用电动给水泵转速和给水调旁来控制贮水罐水位。
缓慢增加燃料量,保持适当的升温升压率,储水罐水位在某一点逐渐下降,361(360)阀逐渐关小直至全关, 中间点过热度由负值逐渐升高变正,机组即进入直流运行状态,是一个自然而然的过程,此时只要操作均匀缓慢,不使压力出现太大波动,就能实现自然过渡。
但是建议361 阀依然投入自动,避免人为疏忽造成水位过高,造成顶棚过热器进入水。
1.1 在第一阶段需要掌握好的几个关键点:1.1.1 工质膨胀:工质膨胀产生于启动初期,水冷壁中的水开始受热初次达到饱和温度产生蒸汽阶段,此时蒸汽会携带大量的水进入分离器,造成贮水罐水位快速升高,锅炉有较大排放量,此过程较短一般在几十秒之内,具体数值及产生时间与锅炉点火前压力、温度、水温度、投入油枪的数量等有关。
此时要及时排水,同时减少给水流量,在工质膨胀阶段附近,应保持燃料量的稳定,此时最好不要增投油枪。
1.1.2 虚假水位:虚假水位在整个第一阶段都有可能产生,汽压突然下降出现的情况较多,运行中应对虚假水位有思想准备,及时增加给水满足蒸发量的需要,加强燃烧恢复汽压。
运行中造成汽压突然下降的原因主要有:汽机调门、高旁突然开大、安全阀动作、机组并网,切缸过中都有可能造成虚假水位,这一点和汽包炉是基本相同的。
1.1.3 投退油枪的时机及速度:投退油枪时要及时协调沟通,及时增减给水。
保持一定的燃水比就基本上能维持汽温的稳定。
为保持水位稳定,应避免在低水位时连续投入数枝油枪,或者水位很高调节困难时连续退出油枪。
1.1.4 并网及初负荷:机组并网及负荷过程中负荷上升很快,此时应加强燃烧,及时增加给水。
必要时手动关小高旁,稳住汽压避免汽压下降过大。
1.1.5 给水主旁路切换:此时应保持锅炉负荷稳定,切换过程中匀速稳定,保持省煤器入口足够流量及贮水罐水位的稳定,必要时排放多余给水。
水位下降时及时提高电泵转速,开大调门。
建议切换时就地手动开大给水主电动门,每开一点,就关小一点旁路门,可以在相当长的时间内保持给水主旁路都有一定的开度,这样调节起来裕度较大,安全性更高。
1.1.6 投入制粉系统:投入煤粉后负荷会升的很快,贮水罐水位波动很大,很难控制。
此时最重要的是要控制好给煤量和一次风量,避免进入炉膛的煤粉过多。
同时控制好升负荷速度,及时控制给水,必要时退掉油枪(尤其是上层油枪)。
起磨时提前打开主再热蒸汽减温水手动门,联系热工解除减温水负荷闭锁,必要时投入减温水控制汽温,防止超温及主机差胀增大。
1.1.7 切换给水泵:切换给水泵时,保持锅炉负荷稳定,减少扰动。
匀速提高待并泵的转速升高泵出口压力,在泵出口压力接近于母管压力时打开出口电动门开始供水,同时减少另一台泵的转速,降低出口流量,两台泵的增减速度要协调,保持稳定的一个给水流量,加减转速,不可太快、太猛,防止其出口压力激增造成另一台泵出口逆止门关闭给水流量剧减。
切换过程中注意监视泵的再循环阀(最小流量阀)自动动作正常,时刻注意给水流量的变化,发现异常及时手动调整。
两台汽动给水泵并列运行时尽量保持两台小机转速相同,偏差不要太大。
特别要注意的是任何情况下并泵时都要解除给水泵的自动,防止给水平衡模块起作用造成给水流量剧减。
1.2 锅炉点火后要密切监视过热器、再热器的金属壁温和出口汽温,具体应注意以下三点:出口汽温忽高忽低,说明还有积水,应加强疏水;出口汽温稳定上升,说明积水已经消除。
各受热面的金属壁温在点火后会出现不均匀现象,如水冷壁一般中间温度高,两侧温度低。
这时不应再增加燃料,当所有温度均超过该汽压下对应的饱和温度40℃,以及各管间最大温差在50℃以内时,才允许增加燃烧强度。
从增加省煤器入口给水流量到贮水罐水位增加要经过比较长的时延,所以在手动控制给水时重在提前干预,根据水位变化速度,蒸汽流量(主汽流量及高旁流量)变化,燃烧情况等提前调节,否则很难调平衡。
此时361 阀可投自动,炉水循环泵出口调阀手动保持一定开度,单调给水,控制水位,必要时可有一定排放。
给水旁路调阀前后保持一定压差,但也不应太高,以免造成调门开度过小工作在非线性区域,使调门工作环境恶劣减少使用寿命。
此过程中要始终保持省煤器入口流量在大于锅炉MFT 流量以上的一个数值,一般来说高出100t/h 就可以。
随着负荷逐渐上升,炉水循环泵出口流量逐渐减少直至再循环电动门打开,应注意出口流量突然变化对省煤器入口流量的影响。
现阶段电泵转速还是手动控制,所以要及时调整电泵转速,尤其在大幅度调整给水流量时,同时要防止电泵过负荷,加强对电泵的监视,防止电机绕组温度、油温、瓦温过高、振动过大。
2 第二阶段:亚临界直流运行阶段在负荷大于25%~35%BMCR 以上时锅炉即转入直流运行方式。
此后锅炉运行在亚临界压力以下。
锅炉进入直流状态,给水控制与汽温调节和前一阶段控制方式有较大的不同,给水不再控制分离器水位而是和燃料一起控制汽温即控制燃水比B/G。
如果燃水比B/G 保持一定,则过热蒸汽温度基本能保持稳定;反之,燃水比B/G 的变化,则是造成过热汽温波动的基本原因。
因此,在直流锅炉中汽温调节主要是通过给水量和燃料量的调整来进行。
但在实际运行中,考虑到上述其它因素对过热汽温的影响,要保证B/G 比值的精确值是不现实的。
特别是在燃煤锅炉中,由于不能很精确地测定送入炉膛的燃料量,所以仅仅依靠B/G 比值来调节过热汽温,则不能完全保证汽温的稳定。
一般来说,在汽温调节中,将B/G 比值做为过热汽温的一个粗调,然后用过热器喷水减温做为汽温的细调手段。
对于直流锅炉来说,在本生负荷以上时,汽水分离器出口汽温是微过热蒸汽,这个区域的汽温变化,可以直接反映出燃料量和给水蒸发量的匹配程度以及过热汽温的变化趋势。
所以在直流锅炉的汽温调节中,通常选取汽水分离器出口汽温做为主汽温调节回路的前馈信号,此点的温度称为中间点温度。
依据该点温度的变化对燃料量和给水量进行微调。
大多数直流炉给水指令的控制逻辑是这样的:给水量按照燃水比跟踪燃料量,用中间点温度对给水量进行修正。
直流锅炉一定要严格控制好水煤比和中间点过热度。
一般来说在机组运行工况较稳定时只要监视好中间点过热度就可以了,不同的压力下中间点温度是不断变化的,但中间点过热度可维持恒定,一般在10℃左右(假设饱和温度最高不是374℃,过临界后仍然上升),中间点过热度是水煤比是否合适的反馈信号,中间点过热度变小,说明水煤比偏大,中间点过热度变大,说明水煤比偏小。
在运行操作时要注意积累中间点过热度变化对主汽温影响大小的经验值,以便超前调节时有一个度的概念。
但在机组出现异常情况时,如给煤机、磨煤机跳闸等应及时减小给水,保持水煤比基本恒定,防止水煤比严重失调造成主蒸汽温度急剧下降。
总之,水煤比和中间点过热度是直流锅炉监视和调整的重要参数。
从转入直流到锅炉满负荷,水燃比因煤质变化、燃烧状况不同、炉膛及受热面脏污程度等不同有较大变化,一般从7.6~9.0 不等。
如果机组协调性能不好,可在锅炉转入直流状态后手动控制,通过手动增减小机转速来调节给水,控制中间点温度。
负荷变动过程中,利用机组负荷与主蒸汽流量做为前馈粗调,主蒸汽流量是根据调节级压力计算出来的不是很准确,推荐使用机组负荷做为前馈粗调整用。
一般用机组负荷(万kW)乘以30t,得出该负荷所对应的大致给水流量,然后根据分离器出口温度细调给水流量。
调整分离器出口温度时,包括调节给水时都要兼顾到过热器减温水的用量,使之保持在一个合适的范围内,不可过多或过少,留有足够的调节余地。
同时还要监视好再热汽温度、受热面壁温等,严防超温,汽温也不可过低。
锅炉升降负荷过程中,燃料变化很快锅炉的负荷波动也较大。
当使用双进双出钢球磨时,从启动给煤机加煤到磨制出煤粉需要20 分钟左右的时间,停止给煤后磨煤机内仍有较多的存粉,因此给煤量并不等于实际进入炉膛的煤量,不易及时判断出此时的升降负荷速度。
推荐看分离器压力及其变化速度来控制给水流量。
分离器出口温度建议看到小数点后的位数,做曲线时区间尽量小一些。
再热汽温主要靠烟气挡板来调整,时滞性较大,一定要提前调整,在投停高加时要加强对主再热汽温的调整。
3 第三阶段:超临界直流运行阶段在机组负荷达75%MCR 左右时转入超临界状态。
从理论上讲,机组过临界时存在一大比热区,蒸汽参数如比容、比热变化较大,实际运行情况是基本上无明显变化,原因是锅炉的蓄热减缓了影响,而且协调方式下参数的自动调整在一定程度上弥补了波动。
第三阶段运行调节情况和第二阶段无明显区别。
其实干转湿,湿转干都一样,最最主要的一点就是在转换的过程中,保持给水流量平稳。
这是最核心的因素。
如果要湿转干,就加煤,慢慢就转干了,干转湿,就减煤,慢慢就转湿了。
其实很多东西想过去很复杂,其实把握住核心的东西,就很简单了。
我厂转干态跳泵的负荷设定为240MW,在负荷210-240MW之前,随着蒸发量的增加,分离器溢流阀逐渐关小,分离器水位逐渐下降。