现场改善8大明表—日资
8S卓越现场实务推行管理

8s—卓越现场实务推行管理(2天)授课背景我国经过30多年的改革,已经成为世界的经济大国、制造大国和消费大国。
随着市场的多级分布和精细化管理技术的分工要求,企业现场的管理水平也将成为衡量企业核心竞争力的一个重要指标之一。
8s起源于日本,是从2s发展到今天的10So是指在生产现场中对人员、机器、材料、方法、环境、管理等生产要素进行有效的控制和管理。
对于塑造企业的形象、降低成本、提高效率、安全生产、高度标准化、创造令人心旷神怡的工作场所、建立自觉工作的员工关系等方面发挥了巨大作用,逐渐被各国的管理界高度重视。
随着我国经济的发展,8S已经成为工厂、学校、政府、企事业单位等管理的一门必修课,也是从企业家到员工的必修课。
为何企事业单位在推行8s时都是“昙花一现”呢?主要表现在以下几种情况:1.没有全面系统地学习和掌握8s的管理内容2,没有将8s的工作效益化3.没有持续化管理4,没有形成固定的企业文化传播和管理核心价值通过全面系统的了解8S的管理内容,实现塑造企业的形象、美化环境、高度标准化作业、建立自觉的工作关系到企业文化建设、形成可持续改善的动力,成为企业管理中坚固的奠基石学习亮点19年日资企业管理经验,精益生产留学回归派的顶级专家授课+现场咨询诊断+企业家角度咨询顾问本课程是王国超讲师几度去日本学习后,回到国内结合中国文化背景,经过19年的现场实战经验和口本管理大师冈田、长召和小川等多位老师的现场指导,全面而系统地将理论与实战的结合,针对中国企业的实际管理水平,把教学、科研、实践、实战的经验融为一体,让学员轻松愉快地掌握管理的核心知识和管理技术的技巧。
让越来越多的企业从8S管理中获益,同时也能为企业全面提升企业的战略人才储备奠定良好的基础。
具体掌握的知识点:1.完整、科学、适用的管理理念。
让学员了解全面系统的8s理念与运作模式2.课程设计具有专业性和针对性。
重点对企事业单位的现场改善为主导内容3.课程不设强制性认可,鼓励学员大胆提问,现场互动交流。
5S推行技巧解析

BOSSWAY
五、素养的推动重点
BOSSWAY
素
BOSSWAY
素养
1、定义 使每位员工依规定行事,养成习惯,工作主动 乐观,形成良好的企业文化。 2、目的: 养成工作标准认真的习惯,营造团队精神。 3、素养的三守原则 守纪律 守时间 守标准
BOSSWAY
素养推行五要点
要点一:持续推动前4S至习惯化 作为主管应不断教育部署,加强前4S的执行 和改善
BOSSWAY
目视治理的特点
以视觉信号显示为根本手段,大家都能够 看得见。
以公开透亮化为根本原则,尽可能地将治 理者的要求和意图让大家看得见,借助推动 自主治理,自主掌握。
现场工作人员可以通过目视方式,将自己 的建议、成果、感想展现出来,进展相互沟 通。
BOSSWAY
常用的目视治理方法
绿灯行,红灯停 设置“人员去向板”,便利安排工作 有小纸条挂在出风口,显示空调、抽风机 是否在工作 用图表的形式反映工作内容或进度状况 特别信号灯〔红、黄〕 反面实物展现
放在作业现场
三天一用的物品
放在不要移动就可以取到的地方或随身携带
BOSSWAY
要点四:制定废弃物处理方法 设定不要物品的回收制度 设定循环、转让、烧毁、掩埋等处理方法 尽量不要制造不要物品
BOSSWAY
例
不行燃物品
报废的机器、设 备、各种空桶、 过期的报纸等
可燃的垃圾
用议定方法处理
出售
回收垃圾厂或 烧毁、再利用
BOSSWAY
四、清洁的推动重点
BOSSWAY
BOSSWAY
清洁
1、定义 将前3S实施的做法制度化标准化,并贯彻执行 及维持成果,连续保持场所及设备等的清洁。 2、目的: 通过制度化来维持成果,并显现“特别”之所 在,并做到特别时的对策方法可视化。 3、清洁的三持原则 维持〔不制造脏乱〕 保持〔不集中脏乱〕 坚持〔不恢复脏乱〕
6S管理

“6S管理”由日本企业的5S扩展而来,是现代工厂行之有效的现场管理理念和方法,其作用是:提高效率,保证质量,使工作环境整洁有序,预防为主,保证安全。
6S的本质是一种执行力的企业文化,强调纪律性的文化,不怕困难,想到做到,做到做好,作为基础性的6S工作落实,能为其他管理活动提供优质的管理平台。
整理(SEIRI)——将工作场所的任何物品区分为有必要和没有必要的,除了有必要的留下来,其他的都消除掉。
目的:腾出空间,空间活用,防止误用,塑造清爽的工作场所。
整顿(SEITON)——把留下来的必要用的物品依规定位置摆放,并放置整齐加以标示。
目的:工作场所一目了然,消除寻找物品的时间,整整齐齐的工作环境,消除过多的积压物品。
清扫(SEISO)——将工作场所内看得见与看不见的地方清扫干净,保持工作场所干净、亮丽的环境。
目的:稳定品质,减少工业伤害。
清洁(SEIKETSU)——维持上面3S成果。
素养(SHITSUKE)——每位成员养成良好的习惯,并遵守规则做事,培养积极主动的精神(也称习惯性)。
目的:培养有好习惯,遵守规则的员工,营造团员精神。
安全(SECURITY)——重视全员安全教育,每时每刻都有安全第一观念,防范于未然。
目的:建立起安全生产的环境,所有的工作应建立在安全的前提下。
因其日语的罗马拼音均以“S”开头,因此简称为“6S”。
6S的关系彼此关联,整理、整顿、清扫是具体内容;清洁是制度化、规范化;清扫指绕开?保持3S水平,素养是养成习惯,遵守纪律、规则、严谨认真;安全是基础,尊重生命,杜绝违章。
整理:区分要与不要,现场只适量留要的,不要的清理掉,节约空间;整顿:对要的东西进行依规定定位,尽量摆放整齐,并准确标识,节约时间;清扫:对工作场所脏污清除,并防止脏污的发生,保持工作场所干净,对设备点检,保养保证品质、效率的技术;清洁:将3S的工作标准化、制度化,并保持成果,持之以恒;素养:人人养成依规定行事的好习惯,追求的最高境界。
《现场改善》PPT课件
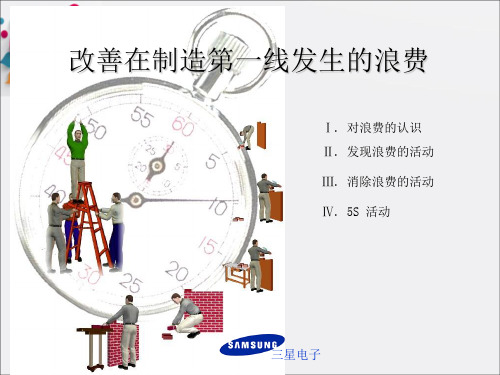
□ 价值
□ 浪费
⑤ 组合PCB
□ 价值
□ 浪费
⑧ 更换箱子
□ 价值 □ 浪费
□ 价值
□ 价值
□ 价值
□ 浪费
⑥ 把螺丝刀拿过来
□ 浪费
□ 浪费
⑨ 挑选出不良产品
Ⅰ. 对浪费的认识
4) 工作和活动
产生净附加价值的动作
• 组装 • 焊接 • 粉刷 • 加工
产生低附加价值的动作
[人] 手工拧紧 KNOW-HOW 工作 追加工作(设计变更) 不良生产
④ 加工本身导致的浪费
工作程序一旦被定下来,工作者就逐渐忘记工作的根本目标而只考虑“工作”
□ 试想在工作方法、环境、条件等方面是否做过多的工作。 □ 试想能否减少或消除现在做的工作。
Ⅰ. 对浪费的认识
⑤ 库存增多导致的浪费
应要抛件、组装品等工厂里的所有物品,也包括仓库和流程过 程的在产品。 ⑥ 动作导致的浪费
用力组装
□ 单纯动作 □ 附带动作 □ 附加价值(非效率性) □ 附加价值(效率性)
按电钮
□ 单纯动作 □ 附带动作 □ 附加价值(非效率性) □ 附加价值(效率性)
Ⅰ. 对浪费的认识
----?
搞不好会 败家的!
了解工作(Work)和活动(Move) ( 工作 ≠ 活动 )
一, 二,三。。
嘿呦 嘿呦
活 动
产生附加价值的动作 收款的动作(大)
非效率动作
收款的动作(小)
单纯动作
浪费钱的动作
附带动作
无法收款的动作
Ⅰ. 对浪费的认识
• 工作动作方面的浪费
由于一个工作由多种动作来完成,需要划分动作并找出各动作的浪费因素。
向零件箱子伸手 拿零件
(5S现场管理)5S现场改进表
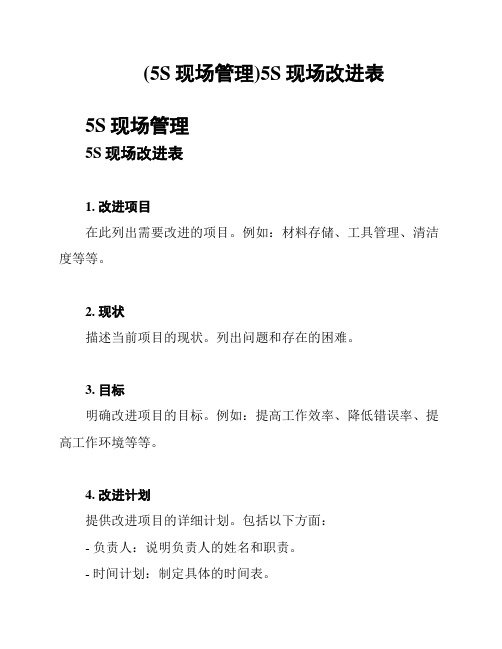
(5S现场管理)5S现场改进表
5S现场管理
5S现场改进表
1. 改进项目
在此列出需要改进的项目。
例如:材料存储、工具管理、清洁度等等。
2. 现状
描述当前项目的现状。
列出问题和存在的困难。
3. 目标
明确改进项目的目标。
例如:提高工作效率、降低错误率、提高工作环境等等。
4. 改进计划
提供改进项目的详细计划。
包括以下方面:
- 负责人:说明负责人的姓名和职责。
- 时间计划:制定具体的时间表。
- 任务分配:将任务分配给相关的人员。
- 资源需求:列出完成改进项目所需的资源。
5. 实施过程
记录改进项目的实施过程。
包括以下内容:
- 实施日期:记录实施改进的具体日期。
- 实施步骤:描述实施改进所采取的具体步骤。
- 难点和解决方法:记录实施过程中遇到的困难,并提供相应的解决方法。
6. 改进结果
记录改进项目的结果。
包括以下方面:
- 改进效果:描述改进项目所带来的具体效果。
- 数据分析:提供相关数据或指标的分析结果。
- 心得体会:记录改进项目的心得和体会。
7. 审核
列出审核改进项目的人员。
包括审核人员的姓名和职务。
8. 改进总结
对改进项目进行总结和评价。
包括以下内容:
- 改进项目的成功与否。
- 改进项目的经验教训。
- 下一步改进的建议和计划。
以上是5S现场改进表的基本内容,根据实际情况进行适当的调整和补充。
CA-QIP介绍
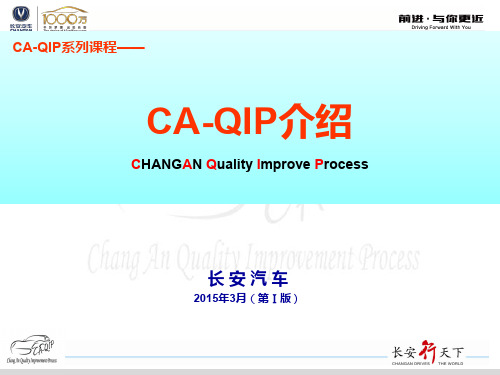
CA-QIP介绍
CHANGAN Quality Improve Process
长安汽车
2015年3月(第Ⅰ版)
CQIS系统
信息流
CA-QIP介绍
质量数据
PJO 严重安全故障 判定指南 召回、FSA、 TSB流程
工具与
ECB、EVB和 顾客柏拉图
流程
CA-QIP 系列课程
组织
行动步骤: 1、建立长安汽车与供应商信息接口,收集质量信息(PPM、R/1000、ECB、三包信息等主要顾客抱怨信息); 2、建立供应商内部过程质量和二级供应商质量信息接口,收集质量信息; 3、设立信息中心,确定各类信息的传递方式,如:看板、邮件、短信等等,通过信息流矩阵进行管理。
信息流矩阵
信息传递流程图
08
07
缺乏有力的激励
CA-QIP目标
长安汽车供应商CA-QIP目标 质量提升目标:PPM同比下降50%,R/1000同比下降50%
分享
压力
动力
目标与顾客需求
顾客的难题就是我们的课题!
R/1000
必备需求
PPM
TGW
单向需求
“顾客是上帝”,如果不能清楚地知晓顾客的需求,是没办法令顾客满意的, 更谈不上“上帝”的感觉了。
目标分解
供应商全员目标
CCC 产品 电动窗开关 车型 S101 产品 电动窗开关 空调控制器 顶灯总成 组合开关 小开关 故障 继电器问题 PCB腐蚀问题 导电橡胶行程问题 导电橡胶异物问题 锁窗卡滞问题 三极管问题 IC连锡问题 组长 周小义 周开宁 刘钧 左大君 尹登森 C/1000 目标 VFG:售后整改小组 推进科 生产 技术 周小义 李云胜 袁刚 周开宁 李云胜 李彬彬 刘钧 叶卫 左大君 贺威 王攀 尹登森 叶卫 幸伟 IQC 陈侠 陈侠 陈侠 陈侠 陈侠 销售 张杰 张杰 张杰 张杰 张杰 采购 汤文丽 汤文丽 汤文丽 汤文丽 汤文丽 项目 李华 李华 李华 李华 李华 质量 工装设备 塑胶部 许大英 程刚 陈一建 李佳 程刚 陈一建 蔡霞 程刚 陈一建 叶琴 程刚 陈一建 蔡霞 程刚 陈一建 责任分担 陈侠 李华 许大英 陈泽友 陈泽友 汤文丽 邓振华 雷星 杨清仙 周小义 雷星
(制造现场チェックシート)期待值管理规定

生産 管理
現 場 管 理
直間の申し送りで、重要な事が伝わるようになっている。 現場管理 重点管理項目(質、量、コスト)を各ライン毎に表示、全員に見えるようにしている。 人員配置板があり、毎日 作業手配が指示されている。 生産数に応じ、人や物の移動が出来る。 多能工化への取組みがある 導入教育のルールがある。 計画的な年休取得を管理している。 QCサークルがあり活動をしている 改善提案(創意くふう等)が出来、フォローがされている。 改善活動 可動率向上活動をしている 正味時間(C/T、MCT)短縮の活動をしている。 関係部署が参画してその日の不具合打合せが行われている(朝市、夕市)。 目標を含め、改善活動の内容が見える化されている(対策、進捗状況、責任者など)。 進捗管理 管理者が目標未達要因を解析し、改善に結びついている。 管理者が活動をフォローしている(毎月)。 段取りの時間の把握が出来ている。 段取り改善 外段取り、内段取りの作業内容が明確。 段取り時間短縮活動をしている。 かんばんが導入されている。
製造現場チェックシート 標準版 (156項目)
は 基本編のチェック項目
こっちが良さそう
2002/8/5 調達技術室
海外仕入先調査時のチェック項目 ライン名: チェック者 日付 / / 海管理 28
チェック項目
品質標準類(品質チェック標準、検査法、等)が有る。 品質標準 品質標準類の内容は適切。(誰が、チェック項目、判定基準、方法、頻度、抜き取り数など) 品質標準類に 見やすい 分かりやすい 工夫がされている。(絵や写真で) 品質チェックの場所が確保され、最新の標準類が掲示されている 品質チェック場の環境は良い。(照明、ほこりなど) 標準の遵守 上位者が、品質チェック状況をフォローすることになっている。 必要な測定具、ゲージがあり、置き場は整理・整頓され使いやすい。 ゲージ類 ゲージは定期的に精度確認され、有効期限が明記されている。 品質標準に記載された限度見本がある。 規定された管理項目について 測定記録をとっている。 品質記録 管理限界を定め、それを超えた時の対応ルールがある。 不良品は決められた箱(赤箱など)に入れられている。 不良品は数が記録され 定期的(1/直、1/日)に片付けられている。 品質異常処置 ポカヨケ 不良発見時の処置ルールがある(止める、呼ぶ、待つ、等)。 不良発見時の処置ルールが機能している。 各所にポカヨケが工夫され設置されている。 (勝手に解除できないなど) ポカヨケの機能チェックが行われている。 (定められた頻度、方法で) 品質改善目標値を決め、全社的な活動を展開している。 改善活動 工程内不良、後工程不良(含事業体受入不良)の要因分析・対策活動をしている 不良実績数や対策状況をグラフ、等で見やすくしている。 真因が追及され、設計・生技での対応の要否を含め対策がなされている。 変更点管理 生産中の変更点が明確に定義され、品質確認がなされる仕組みになっている。 工程内で作業者が検査するようになっている。 品質意識 部品機能を理解している(監督者) 部品がどこに使われているか知っている(技能員) 重要工程はどこか、質問に答えられる。 または明示がある。 重要不良発見者表彰などの工夫はなされている。 設備条件表がある。(溶接、圧入、カシメ、熱処理、塗装、等) 条件表 設備条件の根拠が明確である。 条件が設備側で許容範囲を含め見える化されている。 記録 チェックシートに点検・記録が残されている。(含む職制の定期チェック) 条件どおり稼動させている。 条件変更時のルールがあり、遵守されている 条件変更 異常処置 条件変更時の品質確認を実施している。 条件が簡単に変えられないよう、施錠など工夫している。 条件外れ時の処置ルールがある。 粗材~出荷までのリードタイム(時間)が把握されている。 未然防止活動 過去の不具合について次期製品確認項目に反映され未然防止活動が図られている。
TWI培训-现场监督者技能训练
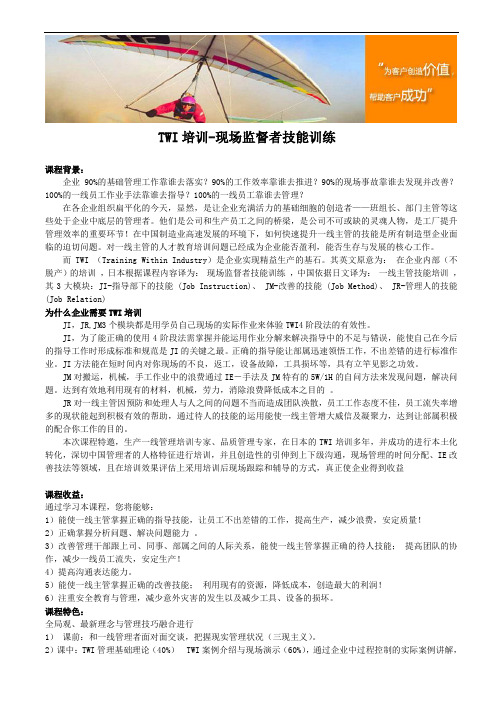
TWI培训-现场监督者技能训练课程背景:企业90%的基础管理工作靠谁去落实?90%的工作效率靠谁去推进?90%的现场事故靠谁去发现并改善?100%的一线员工作业手法靠谁去指导?100%的一线员工靠谁去管理?在各企业组织扁平化的今天,显然,是让企业充满活力的基础细胞的创造者——班组长、部门主管等这些处于企业中底层的管理者。
他们是公司和生产员工之间的桥梁,是公司不可或缺的灵魂人物,是工厂提升管理效率的重要环节!在中国制造业高速发展的环境下,如何快速提升一线主管的技能是所有制造型企业面临的迫切问题。
对一线主管的人才教育培训问题已经成为企业能否盈利,能否生存与发展的核心工作。
而 TWI (Training Within Industry)是企业实现精益生产的基石。
其英文原意为:在企业内部(不脱产)的培训,日本根据课程内容译为:现场监督者技能训练,中国依据日文译为:一线主管技能培训,其3大模块:JI-指导部下的技能 (Job Instruction)、 JM-改善的技能 (Job Method)、 JR-管理人的技能(Job Relation)为什么企业需要TWI培训JI,JR,JM3个模块都是用学员自己现场的实际作业来体验TWI4阶段法的有效性。
JI,为了能正确的使用4阶段法需掌握并能运用作业分解来解决指导中的不足与错误,能使自己在今后的指导工作时形成标准和规范是JI的关键之最。
正确的指导能让部属迅速领悟工作,不出差错的进行标准作业。
JI方法能在短时间内对你现场的不良,返工,设备故障,工具损坏等,具有立竿见影之功效。
JM对搬运,机械,手工作业中的浪费通过IE-手法及JM特有的5W/1H的自问方法来发现问题,解决问题。
达到有效地利用现有的材料,机械,劳力,消除浪费降低成本之目的。
JR对一线主管因预防和处理人与人之间的问题不当而造成团队涣散,员工工作态度不佳,员工流失率增多的现状能起到积极有效的帮助,通过待人的技能的运用能使一线主管增大威信及凝聚力,达到让部属积极的配合你工作的目的。
现场改善的八大利器

怎样进行现场分析和诊断
颜色趣话
用颜色来指路
茶馆店的妙计为什么不灵?
黄色不一定高贵
紫色能提高效率吗?
抛 弃 成 见,打 破 固 执,勇 于 创 新
怎样进行现场分析和诊断
三个和尚新传
抛 弃 成 见,打 破 固 执,勇 于 创 新
怎样进行现场分析和诊断
•HOW——怎么挑? •WHO—谁来挑? •WHEN—什么时候挑? •WHERE—在哪儿挑? •WHOM—谁来检查? •WHAT—结果如何考核…
---现场改善八大利器
利器一:工艺流程查 利器二:平面图上找 利器三:流水线上算 利器四:动作分析测 利器五:搬运时空压 利器六:人机效率挤 利器七:关键路线缩 利器八:现场环境改
抛 弃 成 见,打 破 固 执,勇 于 创 新
怎样进行现场分析和诊断
一、如何对现场进行分析诊断?如何入手解决问题?主要有五条:
5、分析现场还缺少什么物品和媒介物。这里主要指工位器具(工位辅助工具)
抛 弃 成 见,打 破 固 执,勇 于 创 新
怎样进行现场分析和诊断
你看出问题在哪里?
抛 弃 成 见,打 破 固 执,勇 于 创 新
怎样进行现场分析和诊断
二、企业常见的八大浪费
抛 弃 成 见,打 破 固 执,勇 于 创 新
怎样进行现场分析和诊断
1、从工艺流程入手,分析哪些工艺流程不合理?哪些流程走着走着成了倒流?哪些 可以简化,甚至取消;这是一个总纲。 2、分析一下生产、工作环境,是否即能满足生产工作的要求,同时也能满足人的生 理、心理、身体健康和情绪的需求; 3、分析车间的平面布置和设备、设施的配置是否合理。有无重复和过长的路线;
4、研究作业人员的劳动效率,消除多余的动作,确定合理的操作或工作方法;
生产现场5S管理法

“5S”检查、考核规定为更好的推动工厂“5S”现场管理,创造工厂良好的工作环境,经总经理批准,特制定以下检查、考核规定。
一、工厂“5S”检查工作分为三级检查。
1.工厂级检查:●由厂级检查小组负责。
●检查频次:每周2次。
(由检查领导小组自定)●检查标准:《现场“5S”检查表》●考核标准:对检查发现的问题,第一、二次由检查人员提出整改要求,责任人按要求整改,如在检查时发现同样的问题出现第三次,则予以责任人、责任人班组长、责任人各部门主管20--200元处罚。
2.注塑车间/装配车间/部门级检查:●由车间/部门主管负责。
●检查频次:由各主管自定。
●检查标准:可依据《现场“5S”检查表》转化。
●考核标准:可依据各车间《现场“5S”检查表》。
3.各车间班组级检查:●由各班组长负责。
●检查频次:由各班组长自定。
●检查标准:依据《现场“5S”检查表》。
●考核标准:可依据各车间《现场“5S”检查表》。
●月优秀“5S”管理车间/部门评比:●总经理依据每月汇总的工厂级检查得分,车间480元,仓库50元,装配车间350元(每人10元)。
●按“5S”检查表,奖罚得100分 100% 80分以下 50%90分 50% 70分以下 75%80分 0% 60分以下 100% 特此规定!厂级检查小组:批准:******5S/6S的起源与释义5S/6S起源于日本,是指在现场对人员、机器、材料、方法、环境等生产要素进行有效的管理,是在日本企业广泛流行的一种管理方法。
1955年提出“2S”,即整理、整顿,“安全始于整理,终于整理整顿”,后来生产控制和品质的需要,逐步的提出了另外的3S,即“清扫、清洁、素养”。
1986年日本的5S/6S专著逐渐问世,从而对整个现场管理模式起到了冲击的作用,并掀起了5S/6S的热潮。
现在,5S/6S不但在日本流行,而且已经成为世界企业学习与应用的一种潮流。
为何5S/6S知易却行难?绝大多数公司在实施5S/6S管理之初,都充满了热情和信心,可是一段时间后,都是热情渐减,直到最后消失殆尽!这是为什么呢?难道5S/6S就不适合他们公司吗?典型案例:这5S/6S管理怎么就效果不佳?李大明是A公司生产经理,来A公司已经快2年了,近来公司面临越来越剧烈的市场竞争,连他这个生产经理都感受到了:经常因紧急订单的问题和销售部掐上,每次老总总要他顾全大局,最近公司决定大力改善生产管理,要全面推行5S/6S管理,他也觉得这是一个改善现场管理水平的良好的契机,积极配合,但在每次的例行检查中他发现了很多问题,推委会成员似乎都是老江湖,怕得罪人,相互打分都差不多,同时5S/6S也变成了突击行为,每周三检查时大家应付一下,平时现场还是挺乱的,工人也觉得这不是他们的工作,他们照常拿他们的计件工资,下面的班组长甚至也这么认为,李经理有点动摇了:5S/6S是不是不适合A 公司啊?其实5S/6S管理作为被众多优秀企业使用的一种有效管理工具,已经被证明是一种成功、有效的管理方法,适合于任何企业,包括制造业、服务业,甚至政府等非赢利组织,很多企业在执行过程中出现了各种各样的问题,是因为在推行5S/6S管理中走入了不同的误区,主要表现如下:误区一:各级管理者对5S/6S管理理解不深,甚至很肤浅。
生产现场八大浪费分析改善对应表
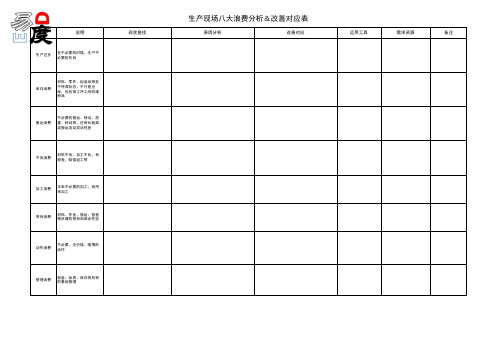
浪费说明现状查找原因分析改善对应运用工具需求资源备注
生产过多在不必要的时候,生产不必要的东西
库存浪费材料、零件、组装品等处于停滞状态,不只是仓库,也包括工序之间的堆积品
搬运浪费不必要的搬运、移动、放置、转动等,还有长距离或搬运流动灵活性差
不良浪费材料不良、加工不良,有检查,赔偿返工等
加工浪费本来不必要的加工,而用来加工
等待浪费材料、作业、搬运、检查等所谓的等待和闲余作业
动作浪费不必要、无价值、缓慢的动作
管理浪费检查、品质、库存等所有
的事后管理
生产现场八大浪费分析&改善对应表。
一线主管的现场改善、问题解决与安全管制1.doc

一线主管的现场改善、问题解决与安全管理1一线主管的现场改善、问题解决与安全管理主办:上海普瑞思管理咨询有限公司时间:2011年02月25-26日北京;2011年3月18-19日天津费用:¥2380元/人(含课程费、证书、午餐、参考资料等)【课程背景】车间管理干部承担着现场管理和制造过程控制的重任,必须有效的管理现场的进度、质量、成本、人员等要素,还要协同其他部门共同处理现场的各种问题。
然而,随着订单交货期日益缩短,品种变化多端,不断有新品种上线,给车间管理人带来无穷的困惑。
作为车间干部,您是否经常被以下问题弄得焦头烂额?²员工很娇气,不好管,管严了抱怨,管松了任务完不成²同样的事故总是重复发生,再三叮嘱也没有用²现场材料乱堆乱放混放、需要的物料不知到哪去找,不需要的一大堆²工人流动性大,刚成熟又离辞了,现场总是在救火²布置下去的工作总是得不到很好的执行,与自己的期望有差距²团队士气不高,激发不起现场人员的工作热情²自己忙得象“驴”一样,仍然不断有问题产生……等等如何搭建起现场管理者的“黄金屋”?如何打造起一支钢铁般基层队伍,在短时间内提升生产的质量、效率、士气、设备、5S等各项核心指标?2天的《TWI一线班组长技能提升训练》将告诉你一套系统而实用的现场管理方法。
案例全部来自于真实的生产现场,再配以录像和动画教学,寓教于乐!【课程收益】通过学习本课程,您将能够:1)能使一线主管掌握正确的指导技能,让员工不出差错的工作,提高生产,减少浪费,安定质量!2)正确掌握分析问题、解决问题能力。
3)改善管理干部跟上司、同事、部属之间的人际关系,能使一线主管掌握正确的待人技能;提高团队的协作,减少一线员工流失,安定生产!4)提高沟通表达能力。
5)能使一线主管掌握正确的改善技能;利用现有的资源,降低成本,创造最大的利润!6)注重安全教育与管理,减少意外灾害的发生以及减少工具、设备的损坏。
日本丰田公司5s卫生内容及现行标准

(第一期)第一章5S概论篇5S的起源5S起源于20世纪50年代的日本;当时只是为了确保作业空间和生产安全而提出了整理和整顿两个概念;并宣传:安全始于整理整顿,终于整理整顿;后来因为生产控制和品质控制的需要,而逐步提出了后面的清扫、清洁、素养三个概念。
日本企业将5S运动作为其工厂管理的基础,并在这个基础上推行了一系列品质管理手法,使日本产品的品质得到了迅猛提升,从而奠定了日本经济大国的地位。
日本的产品遍布世界各个角落。
5S的起源1986年,随着第一本5S著作的问世,对整个日本现场管理模式起到了冲击作用,并由此掀起了5S热潮。
当时它是日资企业独特的一种管理方法;它主要是对生产现场的人员 (Man)、设备(Machine)、物料(Material)、方法(Method)等生产要素进行有效管理;它对企业员工的日常行为提出要求,倡导从小事做起,力求使每位员工都养成事事“讲究”的习惯,从而达到提高整体工作质量的目的。
5S的起源在日本丰田公司的倡导推行下, 5S对于现场改善方面的巨大作用逐渐被各国管理界所认识,并随着世界经济的发展,已成为工厂管理的一股新潮流。
日本为何能成为经济大国?团队意识强:1个中国人>1个日本人3个中国人<3个日本人做事不但认真而且用心:认真做事只能把事情做对用心做事才能把事情做好日本为何能成为经济大国?日本工厂给我的印象从厂外的环境花草、通道,包括汽车的停放,和入厂内不论办公场所、工作场所、储物仓库,从地板、墙板、地上物到天花板,所看到的均是亮亮丽丽、一尘不染、整洁无比。
目视化管理的各种标识让人清清楚楚、一看便知。
从某种程度上说这就是日本这样一个自然资料缺乏的国家,在短短二三十年的时间内跻身世界经济强权的道理。
他们始终认为,整洁的工作人员及工作环境是减低浪费、提高生产力、降低产品不良率重要的基础工程,它可以消除由于种种不良现象而产生的浪费,这些浪费包括:资金的浪费、场地的浪费、人员的浪费、士气的浪费、形象的浪费、效率的浪费、品质的浪费、成本的浪费等。
5s管理演讲

5s管理演讲篇一:比较好的5S管理演讲文章比较好的5S管理演讲文章中国加入WTO之后,已经发生了根本的变化。
过去,我们的竞争对手可能只局限在国内的同行,而现在,由于关税壁垒的消除,国外很多企业已涌入我们的市场。
我曾经在《中外管理》杂志看到一篇张瑞敏的文章,提到“与狼共舞”,必须先练成狼。
但是还有一个问题,就是你能不能变成狼? 海尔可以,海尔现在就是狼,有可能是老虎,可能会吃掉国外的一些不太好的企业。
但是我们的大多数企业,有没有可能在很短的时间内把我们的管理、我们的制造、我们的效益提高到和发达国家水平一样?为此,今天我为大家介绍5s管理。
5s管理方法起源于日本,风靡全世界。
我们为什么要研究5s? 我们是在探讨怎么比别人跑得快的方法,5s可以提高我们的管理水平,可以使我们的成本大幅下降,可以提高企业的核心竞争力。
实施5S管理的目的是什么?时代要求我们的企业。
在激烈的竞争中具备强大的竞争力,而企业的竞争力其实来自于两个方面:第一是品质,第二是成本。
日本的企业管理有一个极其重要的特点。
就是使用最低成本指导产品生产,他们会把好的产品制造得非常便宜。
我觉得目前中国管理水平的落后,比技术水平、产品水平落后的程度要大得多。
因此我们要先从管理上来解决问题。
很多企业做5s之所以失败,最主要的原因就是大家不明白为什么要推5S。
其实推动5s没有别的,就是两个目的:第一提高产品质量;第二降低成本。
日本的企业在20世纪50年代以后能够迅速崛起有两大法宝:第一个法宝就是品质圈活动(QCC)。
让全员参与来解决工商管理当中的问题,最终达到管理水平越来越高;第二个法宝就是5S。
5s代表整理、整顿、清洁、清扫和素养。
前面4个s是手段。
最后一个S是目的。
养成员工认真规范的工作习惯。
我们通过做5S,可以达到这样的目标:*工厂整齐有序。
使人的精神面貌焕然一新;*实现员工的自主管理。
大家知道人是管理方面最主要的因素。
通过5s的实施。
将使人的素质得到迅速提升。