材料成型及控制工程专业英语--2.-HEAT-TREATMENT-OF-STEEL分析
材料成型及控制工程专业英语
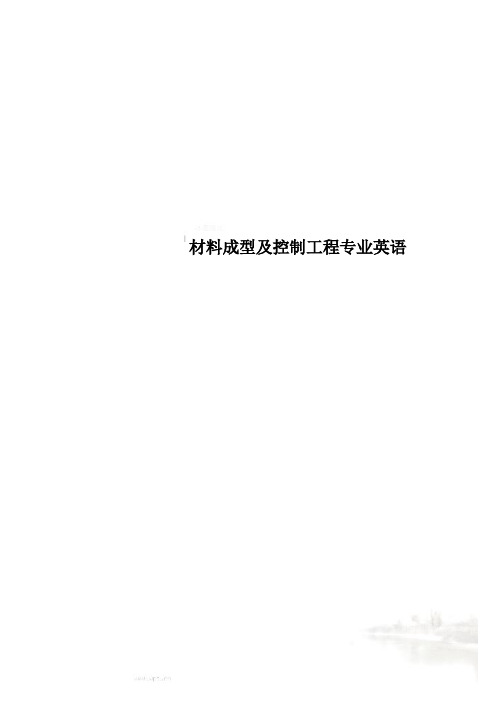
材料成型及控制工程专业英语Mechanical property机械性能austenitic奥氏体的martensite 马氏体Plastic deformation塑性变形stress concentrator应力集中点bar棒材beam线材sheet板材ductile可延展的stress relief应力松弛austenitie奥氏体 martensite马氏体normalize正火temper回火anneal正火harden淬火close-die forging模锻deformation rate变形速度diffusion扩散overheat过热Work hardening加工硬化dislocation density位错密度die模具residual strain残留应变as-forged锻造的injection mold注射模molding shop成型车间clamping force合模力grind磨削drop stamping锤上模锻nickel-base superalloy镍基合金insulation 隔热burr毛刺injection capacity注射容量deterioration变化、退化discrete不连续的abrasive磨损welding焊接metallurgical 冶金的Formation of austenite奥氏体转变The transformation of pearlite(珠光体)into austenite can only take place at the equilibrium critical point(临界温度)a very slow heating as follows from the Fe-C constitutional diagram(状态图). under common conditions, the transformation is retarded and results in overheating,i.e.occurs at temperatures slightly higher than those indicated in the Fe-C diagram.The end of the transformation iS characterized by the formation of austenite and the dis—appearance of pearlite(ferrite+cementite).This austenite is however inhomogeneous even in the volume of a single grain.In places earlier occupied by lamellae(层片)(or grains)of a pearlitic cementite,the content of carbon is greater than in places of ferritic lamellae.This is why the austenite just formed is inhomogeneous.In order to obtain homogeneous (均匀的)austenite,it is essential on heating not only to pass through the point of the end of pearlite to austenite transformation,but also to overheat the steel above that point and to allow a holding time to complete the diffusion(扩散) processes in aus-tenitie grains.为了获得均匀的奥氏体,在加热过程中通过珠光体的结束点向奥氏体转变是必要的,而且对过热刚以上的点,允许持续一定时间来完成奥氏体晶粒的扩撒过程。
广东工业大学材料成型及控制工程专业英语2
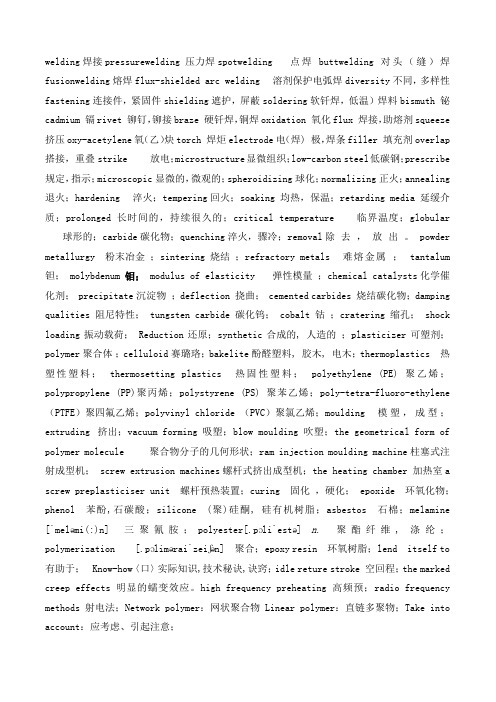
welding焊接pressurewelding 压力焊spotwelding 点焊buttwelding对头(缝)焊fusionwelding熔焊flux-shielded arc welding 溶剂保护电弧焊diversity不同,多样性fastening连接件,紧固件shielding遮护,屏蔽soldering软钎焊,低温)焊料bismuth 铋cadmium 镉rivet 铆钉,铆接braze 硬钎焊,铜焊oxidation 氧化flux 焊接,助熔剂squeeze 挤压oxy-acetylene氧(乙)炔torch 焊炬electrode电(焊) 极,焊条filler 填充剂overlap 搭接,重叠strike 放电;microstructure显微组织;low-carbon steel低碳钢;prescribe 规定,指示;microscopic显微的,微观的;spheroidizing球化;normalizing正火;annealing 退火;hardening 淬火;tempering回火;soaking 均热,保温;retarding media 延缓介质;prolonged长时间的,持续很久的;critical temperature 临界温度;globular 球形的;carbide碳化物;quenching淬火,骤冷;removal 除去,放出。
powder metallurgy 粉末冶金;sintering 烧结;refractory metals 难熔金属; tantalum 钽; molybdenum 钼; modulus of elasticity 弹性模量;chemical catalysts化学催化剂; precipitate沉淀物;deflection 挠曲; cemented carbides 烧结碳化物;damping qualities阻尼特性; tungsten carbide碳化钨; cobalt 钴;cratering 缩孔; shock loading振动载荷; Reduction还原;synthetic合成的, 人造的;plasticizer可塑剂;polymer聚合体;celluloid赛璐珞;bakelite酚醛塑料, 胶木, 电木;thermoplastics 热塑性塑料;thermosetting plastics 热固性塑料;polyethylene (PE) 聚乙烯;polypropylene (PP)聚丙烯;polystyrene (PS) 聚苯乙烯;poly-tetra-fluoro-ethylene (PTFE)聚四氟乙烯;polyvinyl chloride (PVC)聚氯乙烯;moulding 模塑,成型;extruding 挤出;vacuum forming 吸塑;blow moulding 吹塑;the geometrical form of polymer molecule 聚合物分子的几何形状;ram injection moulding machine柱塞式注射成型机; screw extrusion machines螺杆式挤出成型机;the heating chamber 加热室a screw preplasticiser unit 螺杆预热装置;curing 固化,硬化; epoxide环氧化物;phenol苯酚,石碳酸;silicone(聚)硅酮, 硅有机树脂;asbestos石棉;melamine [`meləmi(:)n]三聚氰胺;polyester[.pɔli`estə] n. 聚酯纤维, 涤纶;polymerization [.pɔlimərai`zeiʃən]聚合;epoxy resin环氧树脂;lend itself to 有助于; Know-how〈口〉实际知识,技术秘诀,诀窍;idle reture stroke 空回程;the marked creep effects 明显的蠕变效应。
材料成型及控制工程专业英语词汇表
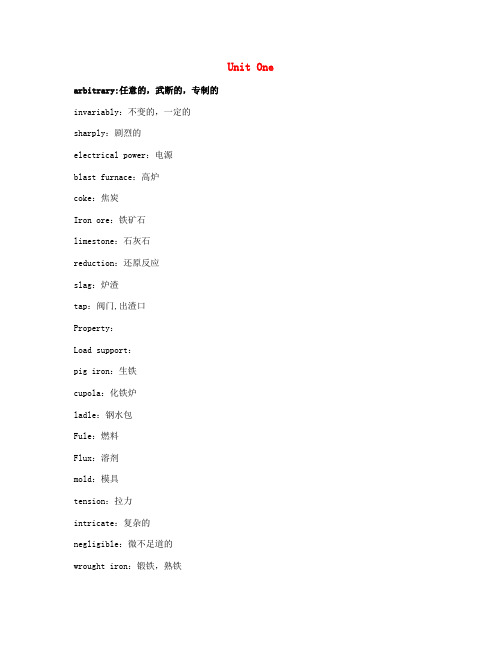
Unit One arbitrary:任意的,武断的,专制的invariably:不变的,一定的sharply:剧烈的electrical power:电源blast furnace:高炉coke:焦炭Iron ore:铁矿石limestone:石灰石reduction:还原反应slag:炉渣tap:阀门,出渣口Property:Load support:pig iron:生铁cupola:化铁炉ladle:钢水包Fule:燃料Flux:溶剂mold:模具tension:拉力intricate:复杂的negligible:微不足道的wrought iron:锻铁,熟铁Free graphite:自由石墨flack graphite:片状的石墨mild steel:低碳钢ferrous alloy:铁合金moderately priced:价格适中ductile:延展Elastic:弹性durable:耐用的non-ferrous:eminently practical:非常实用ball bearings:滚珠轴承metal sheet:金属板AISI:code designation:规定牌号plain steel:碳素钢approximate:近似的high strength low alloy steel:高强度低合金钢proprietary:专卖的specified:规定的,详细说明的optimal:最佳的,最理想的hot rolling:热轧elevated:提高的stress relief:应力消除justification:理由,superalloy:超耐热高应力耐蚀合金turbine blade:涡轮叶片rust:生锈chromium:铬austenite:奥氏体nickel:镍ferritic stainless steel:铁素体不锈钢serviceable:可以使用的quench:淬火body centered tetragonal crystal structure:体心四方晶体结构yield high strength:产生高强度cutlery:刀具,餐具spring:弹簧precipitation hardening:沉淀硬化essentially:本质上dislocation motion:位错运动corrosion resistance structural members:耐腐蚀结构件tungsten:钨molybdenum:钼chromium:铬dual:双重的heat resistance:耐热的cobalt:钴oxidation:氧化justifying:证明,,,有理severe:严峻的turbojet:涡轮喷气飞机carbide formation kinetics:碳化物形成动力学viscosities:粘性surface flim:表面膜shrinkage:收缩solidifacation:凝固inferior:差的uniform:统一的,均衡的porosity:有孔的forge:锻造simple shape:简单断面型钢white iron:白口铸铁crystalline fracture surface:结晶断面gray iron:灰口铸铁significant:有效的,有意义的precipitation:沉淀flakes:片状的magnesium:镁spheroidal:球状的ductile iron:球墨铸铁by a factor of 20:是原来的20倍malleable iron:可锻铸铁nodular graphite:球形石墨equivalent:等价的Welding:焊接Consult:查阅Scientific literature:科学文献Symbol:符号Topic:话题Corresponding author:通讯作者Keywords:关键词Abstract:摘要Classification number:中图分类号Reference:参考文献Retrieval word:检索词Background:研究背景Correlation:相关性,关联Unit threeLesson one Manufacturing:v.生存、制造;n.制造业;Shapeless:不成型的、不定型的;Accuracy:精度;Tolerance:公差;Classification:类别;Assemble:装配;Metallurgy:A simplifide manner:简化的方式;Melt extrusion:熔融挤出;Die casting:模具铸造,压力铸造、拉模铸造;Pressing of metal powder:金属粉末压制;Rolling:轧制;Extrusion:挤压;Formulation:Cold and hot forging:冷锻/自由锻和热锻;Deep drawing:拉深(深冲压);Sawing:锯切;Plastic deformation:Turning:车削;Milling:铣削;Broaching:拉削、绞孔、扩孔;Removing metal:Blacksmith:铁匠;Locksmith:Grind/graind:磨;Metal treatment processes:金属处理工艺;Heat treating:Anodizing:阳极氧化处理;Surface hardening:表面硬化;Essentially:本质上;Joining processes:连接;Metallurgical joining:冶金连接;Welding:焊接;Diffusion bonding:扩散接合;Riveting:铆接;Mechanical:Shrink fitting:预紧(过盈)装配;Production rates:生产率;Capable:有能力的;Recrystallization temperature:Extraordinary cost:额外成本;Die set:模座;Varible:可变因素,变量;Dimensional:空间的,尺寸的;Specified:规定的,详细说明的;Dimensional tolerance:尺寸公差;Surface finish:表面光洁度;Quality:质量;Sophisticated:复杂的;Variation:变化;Means of new development:新开发的手段;Lost wax vacuum casting:失蜡真空铸造;Tighter tolerance:更严格的公差;Brake drum:刹车鼓;Vibration:震动;Interchangeability:可替换性;Defective:有缺陷的;Modern mass production:现代大规模生产;Indicate:表明,指出;Gross national product:国民生产总值;Manufacturing industries:制造业;Manufacturing productivity:制造业的生存率;Discrete parts:分立零件;Ingredient:原料,要素,组成部分;Human and managerial resource:人力及管理资源;Plant:工厂,车间;Interface:相互作用;Physiological:生理学的;Psychological:心理学的;Precede:领先,在。
材料成型专业英语

2. The introduction of our department
2. Introduction of our department
2. The introduction of our department (1)
Material Processing and Control Engineering is an engineering major integrated machinery and materials disciplines, with the method of forming, taking the materials processing as a target, and employing the process control for quality assurance measures to manufacture products. The two main majors are sheet metal stamping and plastic injection molding. The key is development of material forming mold.
Professional English
of
Material Processing and Control Engineering
for Graduate Student
Outline
1. The content of this course 2. The introduction of our department 3. The Properties of English for Science and Technology
For industrial purposes,materials are divided into engineering materials or nonengineering materials. 从工业用途来讲,材料可以划分为工程材料和非工 程材料两大类。
材料成型专业英语 Heat Treatment
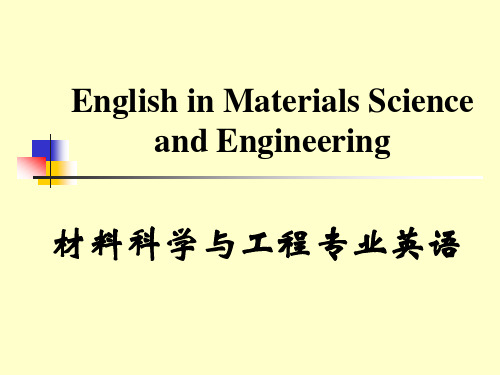
English in Materials Science and Engineering
The presence of undissolved particles increases the value of G, since these particles serve as additional nuclei. The value of G diminishes with increasing size of austenitic grains. Crystallization nuclei appear mainly on grain boundaries, therefore, the conditions for nucleation are worse in coarse grained steel where the extent of grain boundaries is smaller.
2012-5-26 合肥工大材料学院 何顺荣制作 8
English in Materials Science and Engineering
In hypoeutectoid * steels, the transformation of austenite begins with the formation of ferrite and the saturation of the remaining solution with carbon, and in hypereutectoid steels, with the precipitation of cementite and depletion* of the austenite of carbon. [2]
材料成型级控制工程专业英语阅读
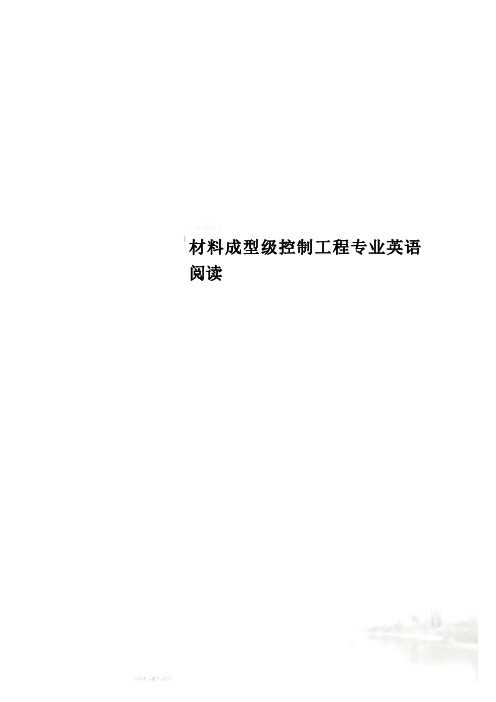
材料成型级控制工程专业英语阅读材料成型级控制工程专业英语阅读1.2.1 Plain Carbon Steel 普通碳钢Hot-rolled steel delivered (供给)by steelmaking works as rolled sections(bars, beams,sheets.tubes,etc) is the most wildly used material for manufacture of various machines,machine tools, building structures,consumer goods,etc.Delivered steel should have the properties as specified by State Standards(国家标准).钢铁制造车间供给的热轧钢主要为棒材、柱材、板材、管材等,热轧钢是制造各种机械、机器工具、建筑结构和消费品中应用最广泛的材料。
所供给的钢应具有国家标准规定的各种性能。
In the RSSU.Plain carbon steels are classified into three groups:A, B and C,depending on their application.在RSSU中,普通碳钢根据其用途分为A、B、C三类。
A: If a steel is to be used for making products without hot working (welding, Forging.Etc.). Its structure and properties in the final product will be the same as delivered from the rolling mill.In that case the user requests for a steel of warranted(保证)mechanical properties,while the chemical composition is not guaranteed(保证、担保).A:如果钢在制造产品的过程中没有进行热加工(焊接、锻造等),则最终产品的组织和性能将与轧厂提供的相同。
材料成型及控制工程专业英语版介绍-完整版-狂砍幸福
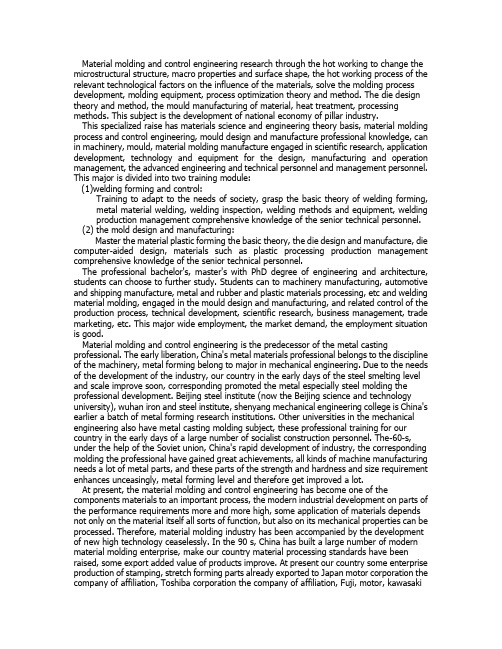
Material molding and control engineering research through the hot working to change the microstructural structure, macro properties and surface shape, the hot working process of the relevant technological factors on the influence of the materials, solve the molding process development, molding equipment, process optimization theory and method. The die design theory and method, the mould manufacturing of material, heat treatment, processing methods. This subject is the development of national economy of pillar industry.This specialized raise has materials science and engineering theory basis, material molding process and control engineering, mould design and manufacture professional knowledge, can in machinery, mould, material molding manufacture engaged in scientific research, application development, technology and equipment for the design, manufacturing and operation management, the advanced engineering and technical personnel and management personnel. This major is divided into two training module:(1)welding forming and control:Training to adapt to the needs of society, grasp the basic theory of welding forming, metal material welding, welding inspection, welding methods and equipment, welding production management comprehensive knowledge of the senior technical personnel.(2) the mold design and manufacturing:Master the material plastic forming the basic theory, the die design and manufacture, die computer-aided design, materials such as plastic processing production management comprehensive knowledge of the senior technical personnel.The professional bachelor's, master's with PhD degree of engineering and architecture, students can choose to further study. Students can to machinery manufacturing, automotive and shipping manufacture, metal and rubber and plastic materials processing, etc and welding material molding, engaged in the mould design and manufacturing, and related control of the production process, technical development, scientific research, business management, trade marketing, etc. This major wide employment, the market demand, the employment situation is good.Material molding and control engineering is the predecessor of the metal casting professional. The early liberation, China's metal materials professional belongs to the discipline of the machinery, metal forming belong to major in mechanical engineering. Due to the needs of the development of the industry, our country in the early days of the steel smelting level and scale improve soon, corresponding promoted the metal especially steel molding the professional development. Beijing steel institute (now the Beijing science and technology university), wuhan iron and steel institute, shenyang mechanical engineering college is China's earlier a batch of metal forming research institutions. Other universities in the mechanical engineering also have metal casting molding subject, these professional training for our country in the early days of a large number of socialist construction personnel. The-60-s, under the help of the Soviet union, China's rapid development of industry, the corresponding molding the professional have gained great achievements, all kinds of machine manufacturing needs a lot of metal parts, and these parts of the strength and hardness and size requirement enhances unceasingly, metal forming level and therefore get improved a lot.At present, the material molding and control engineering has become one of the components materials to an important process, the modern industrial development on parts of the performance requirements more and more high, some application of materials depends not only on the material itself all sorts of function, but also on its mechanical properties can be processed. Therefore, material molding industry has been accompanied by the development of new high technology ceaselessly. In the 90 s, China has built a large number of modern material molding enterprise, make our country material processing standards have been raised, some export added value of products improve. At present our country some enterprise production of stamping, stretch forming parts already exported to Japan motor corporation the company of affiliation, Toshiba corporation the company of affiliation, Fuji, motor, kawasakiheavy industries, wu mountain instrument corporation and other enterprise. By cold forming, hot extrusion process of copper pipe production has been exported to the United States, Germany and Australia and other countries.Our country material molding and control technology is still needs further development, computer control forming technology in our country at present is still in the initial stage, and in this industry the technology level of our country in the world still is backward, and our country to this domain product demand is big rise, thereby material molding field would be in the next few years for considerable development. 21 century information industry, material industry, the energy industry will be the national production of the three pillar industries, and material molding and control technology material industry is one of the important parts, it would involve all fields of national production.。
材料成形及控制工程-专业英语阅读

CHAPTER I MA TERIALS AND THEIR PROPERTIES1. 1 Metals and Non-metalsAmong numerous properties possessed by materials, their mechanical properties, in the majority of cases, are the most essential and therefore, they will be given much consideration in the book. All critical parts and elements, of which a high reliability is required, are made of metals, rather than of glass, plastics or stone. As has been given in Sec 1-l, metals are characterized by the metallic bond; where positive ions occupy the sites of the crystal lattice and are surrounded by electron gas .All non-metals have an ionic or a covalent bond. These types of bond are rigid and are due to electrostatic attraction of two ions of unlike charges. Because of the metallic bond, metals are capable of plastic deformation and self-strengthening upon plastic deformation. Therefore, if there is a defect in a material or if the shape of an element is such that there are stress concentrators, the stresses in these points may attain a great value and even cause cracking. But since the plasticity of the material is high, the metal is deformed plastically in that point, say, at the tip of a crack, undergoes strengthening, and the process of fracture comes to an arrest. This does not occur in non-metals. They are uncapable of plastic deformation and self-strengthening; therefore, fracture will occur as soon as the stresses at the tip of a defect exceed a definite value. These facts explain why metals are reliable structural materials and can not be excelled by non-metallic materials.Words and Terms:mechanical property 机械(力学)性能critical part and element 关键零部件covalent bond 共价键metalic bond crystal lattice 金属键晶格electrostatic attraction 静电吸引plastic deformation 塑性变形self-strengthening 自强化stress oncentrator 应力集中点the tip of a crack 裂纹尖端Questions: 1) What are the differences in properties between metals and non-metals?2) Why are metals capable of plastic deformation and self-strengthening?1. 2 Ferrous AlloysMore than 90 % by weight of the metallic materials used by human beings are ferrous alloys. This represents an immense family of engineering materials with a wide range of microstructures and related properties. The majority of engineering designs that require structural load support or power transmission involve ferrous alloys. As a practical matter, these alloys fall into two broad categories based on the carbon in the alloy composition. Steel generally contains between 0. 05 and 2.0 wt % carbon. The cast irons generally contain between 2.0 and 4.5 wt % carbon. Within the steel category,we shall distinguish whether or not a significant amount of alloying elements other than carbon is used . A composition of 5 wt % total non-carbon additions will serve as an arbitrary boundary between low alloy and high alloy steels. These alloy additions are chosen carefully because they invariably bring with them sharply increased materials costs. They are justified only by essential improvements in properties such as higher strength or improved corrosion resistance.Words and Terms:ferrous 铁的;含铁的corrosion resistance 耐腐蚀;抗蚀力arbitrary 特定的;武断的Questions:l) What is the difference in composition between steel and cast iron?2) How can you distinguish low alloy steels from high alloy steels?CHAPTER 2 HEA T TREA TMENT OF STEEL2. 1 Principle of Heat Treatment of SteelThe role of heat treatment in modern mechanical engineering cannot be overestimated. The changes in the properties of metals due to heat treatment are of extremely great significance.2. 1. 1 Temperature and TimeThe purpose of any heat treating process is to produce the desired changes in the structure of metal by heating to a specified temperature and by subsequent cooling.Therefore , the main factors acting in heat treatment are temperature and time , so that any processof heat treatment can be represented in temperature-time ( t-τ) coordinates .Heat treatment conditions are characterized by the following parameters: heating temperature t , i.e. the maximum temperature to which an alloy metal is heated; time of holding at the maxheating temperatureτh; heating rate νh and cooling rateνc.If heating (or cooling) is made at a constant rate, the temperature-time relationship will be described by a straight line with a respective angle of incline.With a varing heating (or cooling) rate , the actual rate should be attributed to the given temperature , more strictly , to an infinite change of temperature and time : that is the first derivative of temperature in time : νact = dt/dτ.Heat treatment may be a complex process , including multiple heating stages , interrupted or stepwise heating (cooling) , cooling to subzero temperatures , etc . Any process of heat treatment can be described by a diagram in temperature-time coordinates.Words and Terms:coordinates 坐标系heating rate 加热速度straight line 直线heating temperature 加热温度cooling rate 冷却速度first derivative 一阶导数Questions:1) What are the two main factors acting in heat treatment?2) How many stages may usually be inc luded in the heat treatment of steel?2. 1. 2 Formation of AusteniteThe transformation of pearlite into austenite can only take place at the equilibrium critical point on a very slow heating as follows from the Fe-C constitutional diagram. Under common conditions, the transformation is retarded and results in overheating, i.e. occurs at temperatures slightly higher than those indicated in the Fe-C diagram.When overheated above the critical point, pearlite transforms into austenite, the rate of transformation being dependent on the degree of overheating.The time of transformation at various temperatures (depending on the degree of overheating) shows that the transformation takes place faster (in a shorter time) at a higher temperature and occurs at a higher temperature on a quicker heating. For instance , on quick heating and holding at 780 ℃,the pearlite to austenite transformation is completed in 2 minutes and on holding at 740 ℃,in 8 minutes .The end of the transformation is characterized by the formation of austenite and the disappearance of pearlite (ferrite + cementite). This austenite is however inhomogeneous even in the volume of a single grain. In places earlier occupied by lamellae (or grains) of a pearlitic cementite , the content of carbon is greater than in places of ferritic lamellae . This is why the austenite just formed is inhomogeneous .In order to obtain homogeneous austenite , it is essential on heating not only to pass through the point of the end of pearlite to austenite transformation , but also to overheat the steel above that point and to allow a holding time to complete the diffusion processes in austenitc grains.The rate of homogenization of austenite appreciably depends on the original structure of the steel, in particular on the dispersion and particle shape of cementite. The transformations described occur more quickly when cementite particles are fine and, c therefore, have a large total surface area.Words and Terms : pearlite 珠光体constitutional diagrm 状态图inhomogeneous 不均匀的lamellae 层片critical point 临界温度overheat 过热grain 晶粒diffuse扩散Questions:1) Is there no diffusion process in the transformation from pearlite to austenite?2) Is it true that the higher the temperature, the faster the transformation from pearlite into austenite?3) How to obtain homogeneous austenite?CHAPTER 3 PRINCIPLES OF PLASTIC FORMING3. 1 Physical Metallurgy of Hot WorkingThe principles of the physical metallurgy of hot working are now well recognized. During the deformation process itself, e.g. a rolling pass, work hardening takes place but is balanced by the dynamic softening processes of recovery and recrystallization. These processes, which are thermally activated, lead to a flow stress that depends on strain rate and temperature as well as on strain. The structural changes taking place within the material result in an increase in dislocation density with strain until in austenitic steels and nickel- and copper-base alloys a critical strain (εc)is reached when the stored energy is sufficiently high to cause dynamic recrystallization . With further strain, dynamic recrystallization takes place repeatedly as the new recrystallized grains are themselves work-hardened to the critical level of stored energy. These dynamic structural changes leave the metal in an unstable state and provide the driving force for static recovery and static recrystallization to take place after the deformation pass. Static recrystallization may be followed by grain growth if the temperature is sufficiently high. In order to be able to apply these principles to commercial working processes, we require answers to two main questions: (a) how long does recrystallization take place after a deformation pass; and (b) what grain size is produced by recrystallization and grain growth? The answers determine the structure of the material entering the next and subsequent passes and hence influence the flow stress of the material and the working forces required. Eventually they determine the structure and properties of the hot worked products.Words and Terms : physical metallurgy 物理冶金work hardening 加工硬化static recovery静态回复thermally activated 热激活的hot working 热加工dynamic softening 动态软化recrystallization 再结晶dislocation density 位错密度critical strain 临界应变Questions:l) When does dynamic recrystallization take place within the material work hardened?2) What do the answers to the two questions determine?3. 1. 1 Dynamic Structural ChangeDuring the deformation of austenite at hot-working temperatures and constant strain rate, the characteristic form of stress-strain curve observed is illustrated in Fig. 3. 1. These curves are for low-alloy steels, tested in torsion, but are similar to those obtained for other steels in the austenitic condition tested in torsion, tension, or compression. After initial rapid work- hardening the curves go through a maximum associated with the occurrence of dynamic recrystallization. The peak in flow stress occurs after some low fraction of recrystallization has taken place so the strain to the peak(εp) is always greater than the critical strain for dynamic recystallization (εc ) . The relationship between the two strains is complex , but it has been suggested thatεc=αεp( where αis a constant ) is a reasonable approximation for conditions of deformation of interest in hot working. however , the proposed values of αdiffer , being 0.83 , 0.86 , and 0.67 . It can be seen from Fig.3.1 that εp increases systematically with Zener-Hollomon parameter ( Z ) , independent of the particular combination of stain rate (ε)and temperature ( T / K ) in the relationship : Z=εexp Q def/RTWhere the activation energy Q def for this alloy steel is 314 kJ/mol. A similar value of 312kJ/mol is appropriate for a range of C-Mn steels but lower values of 270 and 286 kJ/mol have also been observed.Asεc marks a change in microstructure from one of somewhat poorly developed subgrains , produced by the action of work hardening and dynamic recovery,to one which also contains recrystallization nuclei , it is also a critical strain in terms of the static structural changes that take place after deformation . The dependence of εp,and hence of εc,on Z is shown for the low-alloy steel and a number of C-Mn steels in Fig. 3.2. It can be seen that, indicated by the Fig.3.2 ,εp generally increases with increasing Z although the curve for the data of Sakui et al. passes through a minimum at Z = 3 x 10s-1,( corrected to Q def = 312 kcal / mol ) . The curves for the data of Nakamura and Ueki, Cook, Rossard and Blain, and Hughes, and also the data of Suzuki et al. for a number of C-Mn steels were obtained from tests on material reheated to the same temperature as the testing temperature.These all show a trend for higher values of εp at higher testing temperatures.In contrast, the curves for the data of Le Bon et al. , Barraclough , and Morrision refer to tests carried out at lower temperature than the reheating temperature and these show no effect of test temperature 0n εp.In the former group of results, higher reheating/test temperatures will give larger initial grain sizes. As shown by Sah et al., Sakui et al., and Roberts et al. , increase in grain size ( d0)leads to an increase inεp and their data indicate a relationship of the form εp∝d0^ 1/2 Words and TermsStress-strain curve 应力应变曲线torsion 扭转;转矩activation energy 激活能initial grain size 原始晶粒尺寸Questions:l ) What doεc andεp mark ?2 ) What is the relationship between εc andεp ?3. 1. 2 Static Recrystallization RateAfter deformation, softening by static recovery and recrystallization take place with time at rates which depend on the prior deformation conditions and the holding temperature. These processes may be followed by studying the changes in yield or flow stress during a second deformation given after different holding times to obtain a restoration index, or recrystallization may be measured directly by metallographic examination of quenched specimens. An example of the form of recrystallization curves obtained by the latter method for low-alloy steel is shown inFig 3.3. The curves generally follow an A vrami equation of the formwhere X v is the fraction recrystallized in time t ; t F is the time for some specified fraction of recrystallization ( say 0.5 ) ; k is a constant ; and C=-In ( 1-F ) . For the Curves shown k = 2 , which is consistent with the value observed for other steels deformed to strains <εc.With this relationship t0.05=0 . 27t0.5 and t0.95 = 2.08 t0.5 , i.e. recrystallization proceeds over about one order of magnitude in time.The dependence on strain of the characteristic time t0.5, measured by either metallographic or restoration method, is shown for several steels in Fig. 3.4. All the curves show a steep dependence on strain for strains up to ~0. 8εp,which fits a relationship t0.5∝ε-m , where the mean value of m = 4 . This value is also given by observations on ferritic metals. The lower limit of strain to which this relationship is applicable is uncertain as the critical strain for static recrystallization has not received systematic study. The data of Norrison indicate that it is < 0.05 for low-carbon steel at 950℃whereas the observations of Djaic and Jonas indicate a value of > 0.055 for high-carbon steel at 780 ℃.It is clear whether this difference arises from thedifference in temperature or composition as the simple dependence on Z suggested by the broken line in Fig. 3.2 may be unrealistic. This deserves further study as low strains my be applied in the final passes of plate rolling and , as shown previously , these could have significant effects on the final grain size if they exceed the critical strain for static recrystallization.In the strain range of steep dependence of t0.5 on ε,Morrison observed that there was no effect of strain rate over the two orders of magnitude studied . This is somewhat surprising as interesting strain rate (or Z) increases the flow stress at any particular strain. Increasing flow stress would be expected to increase the random dislocation density and decrease the subgrain size and hence increase the stored energy.The subgrain boundaries provide the largest contribution to the stored energy and as their misorientation increases with strain, the driving force for recrystallization will increase. However, this increase would be expected to be about linear with strain so the much greater dependence of t0.5on strain must also arise from an increase in density of nucleation sites and in nucleation rate. The lack of influence of strain rate may thus reflect compensating effects on stored energy and substructure development at any strain. This contrasts with the strain rate effect observed for stainless steel.The observations of Djaic and Jonas indicate that an abrupt change takes place from strain dependence to independence at a strain ~0.8εp,as illustrated in Fig . 3. 4. This corresponds reasonably with the strain expected forεc and arises because preexisting recrystallization nuclei are always present in the deformed structure at strains greater thanεc.Static recrystallization under these conditions has been referred to as ‟metadynamic‟ to distinguish it from the 'classical ' recrystallization after lower strains when the nuclei must be formed after deformation . The restoration measurements indicate that the recrystallization kinetics may have a complex form after strains betweenεc and the onset of steady state , and direct metallographic observations of static recrystallization after stains well into steady state show that the exponent k in the A vrami equation drops to a value of ~1 . This means that t0.05 = 0.074 t0.5 and t0.95 = 4.33 t0..5, i. e. static recrystallization proceeds over about two orders of magnitude in time after strains which give dynamically recrystallized structures during deformation 。
材料成型及控制工程专业英语及翻译

最新消息1-2the benefits of civilization which we enjoy today are essentiallydue to the improved quality of products available to us .文明的好处我们享受今天本质上是由于改进质量的产品提供给我们。
the improvement in the quality of goods can be achieved with proper design that takes into consideration the functional requirement as well as its manufacturing aspects. 提高商品的质量可以达到与适当的设计,考虑了功能要求以及其制造方面。
The design process that would take proper care of the manufacturing process as well would be the ideal one. This would ensure a better product being made available at an economical cost.设计过程中,将采取适当的照顾的生产过程将是理想的一个。
这将确保更好的产品被使可得到一个经济成本。
Manufacturing is involved in turning raw materials to finished products to be used for some purpose. 制造业是参与将原材料到成品用于某些目的。
In the present age there have been increasing demands on the product performance by way of desirable exotic properties such as resistance to high temperatures, higher speeds and extra loads.在现在的时代已经有越来越多的产品性能要求的理想的异国情调的性能如耐高温,更高的速度和额外的负载These in turn would require a variety of new materials and its associated processing.这些反过来需要各种新材料及其相关的处理Also, exacting working conditions that are desired in the modern industrial operations make large demands on the manufacturing industry.这些反过来需要各种新材料及其相关的处理。
材料成型及控制专业英语考点

一、词组(英译汉、汉译英)mechanical property 机械(力学)性能metallic bond 金属键critical part and element 关键零部件electrostatic attraction 静电吸引plastic deformation 塑性变形self-strengthening 自强化deoxidation脱氧stress concentrator 应力集中点corrosion resistance 耐腐蚀plain carbon steel 普通碳钢hot-rolled steel 热轧钢alloying element 合金元素harmful impurity 有害杂质low alloy steel 低合金钢stress relief 应力松驰austenitic 奥氏体ferritic 铁素体martensite马氏体dislocation 位错viscosity 粘性shrinkage 收缩slip system 滑移系thermosetting 热固性的thermoplastic 热塑性的heating rate 加热速度constitutional diagram 状态图inhomogeneous 不均匀的inherent 内在的,本质的free energy 自由能center of crystallization 结晶核心sorbite索氏体troostite屈氏体isothermal decomposition 等温分解annealing 退火work hardening 加工硬化thermomechanical treatment 形变热处理normalizing 正火critical strain 临界应变stress-strain curve 应力应变曲线hardening 淬火holding temperature 保温温度activation energy 激活能tempering 回火holding time 保温时间yield or flow stress 屈服或流动应力nucleation rate 成核率driving force 驱动力two phase region 两相区linear dependence 线性关系defect 缺陷superplastic formability 超塑性成形forging 锻件,锻造drop stamping 锤上模锻difficult-to-machine alloy 难切削合金vapor cushioning 蒸汽垫final forging 终锻closed impression die 闭式压锻模rotary bending 旋转模弯曲fine blanking 精密冲裁cutting punch 冲裁凸模shearing zone 剪切区burr 毛刺confined chamber 闭式模锻wire drawing 拔丝stretch forming 拉伸成形hydrostatic extrusion 静液挤压tensile strength 拉应力stretch draw forming 拉深成形cold rolled sheet 冷轧板strain hardening 应变强化teach and playback 示教和重现explosive forming 爆炸成形strain gradient 应变梯度ejection 脱模,出坯,挤出magnetic forming 磁力成形injection mold 注射模compression mold 压模,压铸模plastics-processing 塑性加工multicavity mold 多型腔注射模milling 研磨,铣削grinding 磨削,研磨three-plate mold 三板式注射模polishing 磨光,抛光二、句子翻译1.Among numerous properties possessed by materials, their mechanical properties, in the majority of cases, are the most essential and there fore, they will be given much consideration in the book.在一些主要的应用场合,力学性能是材料的各种性能中最重要的性能,因此本书中将重点讨论。
材料成型及控制工程 英语
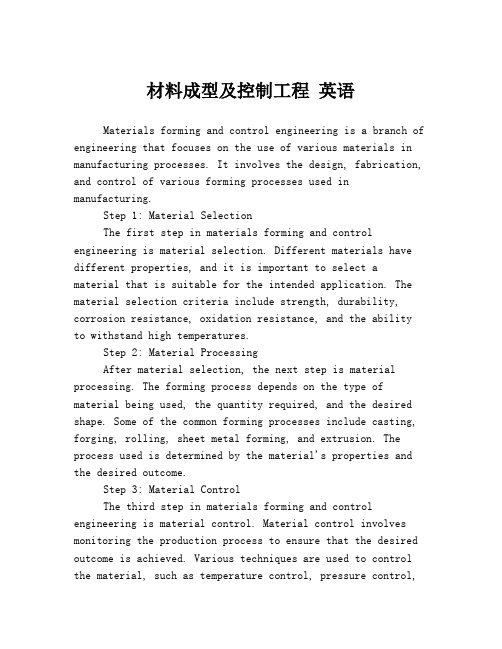
材料成型及控制工程英语Materials forming and control engineering is a branch of engineering that focuses on the use of various materials in manufacturing processes. It involves the design, fabrication, and control of various forming processes used in manufacturing.Step 1: Material SelectionThe first step in materials forming and control engineering is material selection. Different materials have different properties, and it is important to select amaterial that is suitable for the intended application. The material selection criteria include strength, durability, corrosion resistance, oxidation resistance, and the abilityto withstand high temperatures.Step 2: Material ProcessingAfter material selection, the next step is material processing. The forming process depends on the type of material being used, the quantity required, and the desired shape. Some of the common forming processes include casting, forging, rolling, sheet metal forming, and extrusion. The process used is determined by the material's properties and the desired outcome.Step 3: Material ControlThe third step in materials forming and control engineering is material control. Material control involves monitoring the production process to ensure that the desired outcome is achieved. Various techniques are used to control the material, such as temperature control, pressure control,and humidity control.Step 4: Quality ControlQuality control is essential in materials forming and control engineering. It ensures that the materials produced meet the desired standards. This involves inspecting the materials to ensure they meet the required specifications and performing tests to determine if the materials are fit for use.Step 5: Material RecyclingFinally, recycling is an essential aspect of materials forming and control engineering. Recycling materials reduces the need for raw materials, reduces waste, and conserves energy. Materials that can be recycled include metals, plastics, glass, and paper.In conclusion, materials forming and control engineering is a vital component in the manufacturing industry. Itinvolves selecting the appropriate materials, processing them through various forming processes, controlling the process, and ensuring the materials meet the desired quality standards. Recycling the materials is also an essential aspect of the process, as it conserves energy, reduces waste, and minimizes the need for raw materials. The production of high-quality materials is essential in ensuring the success of the manufacturing industry.。
材料成型及控制工程专业英语翻译(部分)
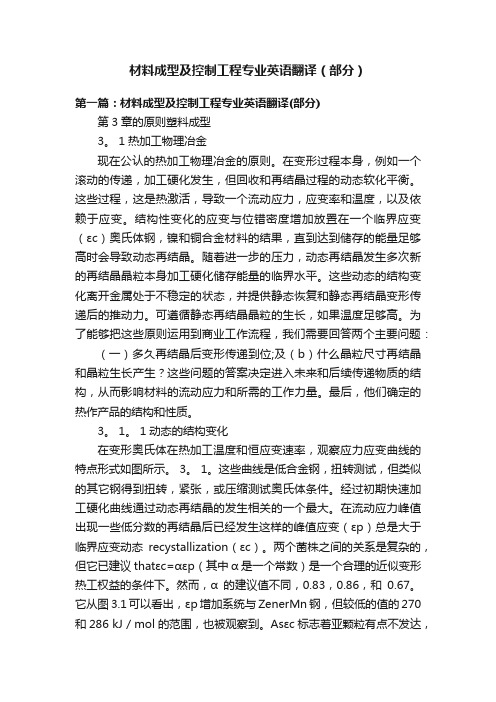
材料成型及控制工程专业英语翻译(部分)第一篇:材料成型及控制工程专业英语翻译(部分)第3章的原则塑料成型3。
1热加工物理冶金现在公认的热加工物理冶金的原则。
在变形过程本身,例如一个滚动的传递,加工硬化发生,但回收和再结晶过程的动态软化平衡。
这些过程,这是热激活,导致一个流动应力,应变率和温度,以及依赖于应变。
结构性变化的应变与位错密度增加放置在一个临界应变(εc)奥氏体钢,镍和铜合金材料的结果,直到达到储存的能量足够高时会导致动态再结晶。
随着进一步的压力,动态再结晶发生多次新的再结晶晶粒本身加工硬化储存能量的临界水平。
这些动态的结构变化离开金属处于不稳定的状态,并提供静态恢复和静态再结晶变形传递后的推动力。
可遵循静态再结晶晶粒的生长,如果温度足够高。
为了能够把这些原则运用到商业工作流程,我们需要回答两个主要问题:(一)多久再结晶后变形传递到位;及(b)什么晶粒尺寸再结晶和晶粒生长产生?这些问题的答案决定进入未来和后续传递物质的结构,从而影响材料的流动应力和所需的工作力量。
最后,他们确定的热作产品的结构和性质。
3。
1。
1动态的结构变化在变形奥氏体在热加工温度和恒应变速率,观察应力应变曲线的特点形式如图所示。
3。
1。
这些曲线是低合金钢,扭转测试,但类似的其它钢得到扭转,紧张,或压缩测试奥氏体条件。
经过初期快速加工硬化曲线通过动态再结晶的发生相关的一个最大。
在流动应力峰值出现一些低分数的再结晶后已经发生这样的峰值应变(εp)总是大于临界应变动态recystallization(εc)。
两个菌株之间的关系是复杂的,但它已建议thatεc=αεp(其中α是一个常数)是一个合理的近似变形热工权益的条件下。
然而,α的建议值不同,0.83,0.86,和0.67。
它从图3.1可以看出,εp增加系统与ZenerMn钢,但较低的值的270和286 kJ / mol的范围,也被观察到。
Asεc标志着亚颗粒有点不发达,加工硬化和动态恢复行动,其中也包含了再结晶核的变化,在微观结构,它也是一个静态后发生的结构性变化的临界应变变形。
材料成型及控制工程专业英语--2.-HEAT-TREATMENT-OF-STEEL

材料成型及控制⼯程专业英语--2.-HEAT-TREATMENT-OF-STEELThe role of heat treatment in modern mechanical engineering can not be overestimated.The changes in the properties of metals due to heat treatment are of extremely great significance.热处理在现代机械⼯程中的作⽤不可能评价的过⾼。
由热处理⽽产⽣的性能改变是特别重要的。
2.1.1 temperature and time 温度和时间The purpose of any heat treating process is to produce the desired changes in the structure of metal by heating to a specified temperature and by subsequent cooling.任何热处理的⽬的都是(通过)将⾦属加热到⼀定的温度并(随后)冷却,以使⾦属组织产⽣所需变化。
2.1.1温度和时间Therefore, the main factors acting in heat treatment aretemperature and time, so that any process of heattreatment can be represented in temperature-time ( t-r ) coordinates.因此,热处理的主要因素是温度和时间,所以任何热处理⼯艺都以⽤温度-时间为坐标轴进⾏表⽰。
热处理⼯艺主要有以下⼏个参数:加热温度t max ,既合⾦加热的最⾼温度;在加热温度下的保温时间;加热速率和冷却速率。
Heat treatment conditions are characterized by thefollowing parameters: heating temperature t max , i.e.the maximum temperature to which an alloy metal is heated; time of holding at the heating temperature ; heating rate and cooling rate .如果以不变速率加热或冷却,则温度和时间的关系可以具有不同倾斜⾓的直线。
材料成型专业英语单词

1.material science and engineering 材料科学与工程2.material processing and controlengineering 材料成型及控制工程3.graphite n. 石墨graphitization n.石墨化graphitic adj.石墨化的4.malleable adj. 有延展性的,可锻性的,韧性的~ iron 可锻铸铁5.magnesium n.镁6.nodule n.球,结节,石墨球nodular adj. 球状的~cast iron 球墨铸铁7.pearlite 珠光体ferrite 铁素体8.matrix n. 基体9.anneal v. 使退火10.n ormalize v. 正火11.c hromium 铬12.m etallurgy n. 冶金(学、术)13.u ndercooling n. 过冷14.n ucleus 核15.a ustenite n. 奥氏体~steel 奥氏体钢16.a ustenize v. 奥氏体化17.a ustenitize v. 使奥氏体化18.a gitation n. 搅拌,鼓动19.c arbide n. 碳化物20.h omogeneous adj. 同类的,同族的,相似的,均匀的,同质的,均一的21.a luminium n. 铝22.l ever n.杠杆23.r adius n. 半径,半径距离;辐射光线,径向射线24.d eoxidant n. 脱氧剂25.a dverse adj. 逆的,相反的,敌对的;不利的,有害的26.s egregation n. 分离,分开,隔离;偏析27.d uctile adj.可延展的,有延(弹)性的,可塑的,可锻的,柔性的~iron球墨铸铁28.e lectrode n. 电极29.c erium n.铈30.c alcium 钙31.e utectic adj.共晶的;n.共晶体32.i nsulate v.使绝缘,隔离33.i nsulation n. 绝缘体,绝热,保温34.i nsulator n.绝缘体,绝热体35.r efractory adj. 耐熔的,n. 耐火材料36.a ntimony n.锑37.u ltrasonic adj. 超声波的,超音的n.超声波38.p arameter n. 参数,参量39.H ERF high energy rate forming 高能快速成型40.f use v. 熔化,熔合,熔接41.t in n. 锡42.c opper n.铜43.b ronze n. 青铜,古铜44.n ickel n. 镍45.E MPA, SEM,TEM46.b ainite n. 贝氏体47.m artensite n. 马氏体48.t emper n. 回火49.i ntermetallic a. 金属间(化合)的50.m echanism n. 机械,机构,机制,作用原理51.e mbrittle v. 使变脆,脆化52.e mbrittlement n. 脆性,脆裂53.f riction n.摩擦力54.v iscous adj. 粘(性,滞,稠)的55.s have v. 剃(齿),刮(平,面)削,刨,修整56.s having n. 刮片,削片,剃片57.p eel v. 剥片,脱壳,剥落~off58.b illet n. 钢坯,棒料,短棒59.d iameter n. 直径60.c omponent n. 组分,元件零件,组件61.m anganese n.锰62.s ulphide n.硫化(物)63.j oint n. vt. 焊缝,结合处,分型面64.c ementite n. 渗碳体65.c entrifugal adj.离心的,利用离心力的66.i nsoluble adj. 不溶的,难以溶解的67.d endrite n. 树枝晶68.g lobule n.小球,滴69.j olt v.n. 振(击,动,实),颠簸,摇动70.h orizon n. 地平线,水平线,水平面71.j oint n. v. 焊缝,结合处,分型面72.c entrifugal adj. 离心的,利用离心力的73.i nsoluble adj.不溶的,难以溶解的;不能解决的,不能解释的74.o xide n. 氧化物75.p uncture n. 刺,穿刺;刺痕,刺穿;vt.刺,刺穿,刺破;揭穿,使无用,削弱vi. 被刺穿,被戳穿76.p rimary adj. 最初的,原始的,原有的,原本的,基本的,基层的,初级的,初等的,首要的,主要的n. 居首位的事务,原色,基色,初选77.s pherical adj. 球的,球形的,球面的,球面图形的,天体的78.m ould cavity 型腔79.p ouring temperature 浇注温度80.t he primary austenite 初生奥氏体81.h eat-affected zone 热影响区82.m olecular adj. 分子的,摩尔的83.o xidation n.氧化(作用)84.e utectoid n.adj. 共析(的),共析体(的)85.s pheroidization 球化处理86.m etallic matrix composite 金属基复合物87.n ucleation 形核88.a short-range order 近程有序89.a long-range order 远程有序90.e mbryo n. 胚,胚胎91.c luster n.(同类事务或人的)一串,一束,一簇;建筑群,房屋群92.a ntimony n.锑93.r unning system=gating system 浇注系统94.s lag n.熔渣,炉渣95.z inc 锌96.m etallographic structure 金相组织97.d ross n. 浮渣,废物,杂质98.h ydraulic press 水压机99.e xtrusion die 冲压模100.arsenic 砷,三氧化二砷101.boron 硼102.phosphorus 磷103.phosphorous 亚磷的,含磷的104.dioxide 二氧化碳105.argon 氩106.piston n.活塞107.pneumatically adv 空气地,压缩空气推动的108.the volume free energy 体积自由能109.molten puddle 熔池110.porous adj. 多孔的,有孔的111.nitrogen n. 氮气112.gas-shielded arc welding 气体保护电弧焊113.fume n. 烟雾,气味114.transparent adj. 透明的,清澈的115.finishing 修整,精加工116.plastic forming process 塑形成形工艺117.。
材料成型及控制工程专业外文翻译--基本挤压冶炼和铸造的根源
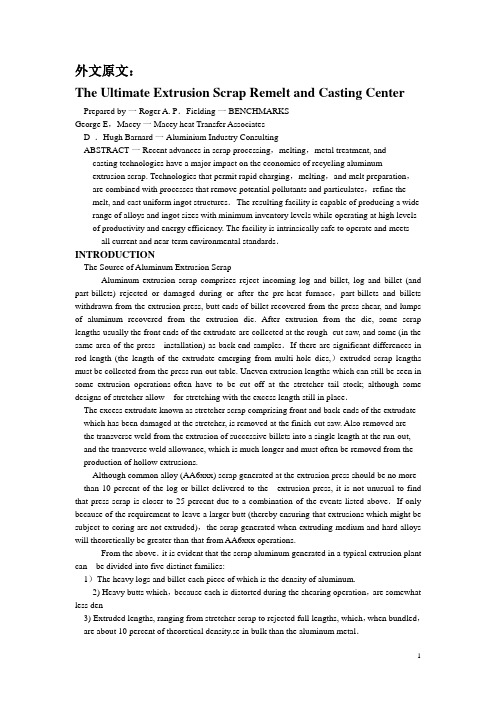
外文原文:The Ultimate Extrusion Scrap Remelt and Casting CenterPrepared by一Roger A. P.Fielding一BENCHMARKSGeorge E,Macey一Macey heat Transfer AssociatesD .Hugh Barnard一Aluminium Industry ConsultingABSTRACT一Recent advances in scrap processing,melting,metal treatment, andcasting technologies have a major impact on the economics of recycling aluminumextrusion scrap. Technologies that permit rapid charging,melting,and melt preparation,are combined with processes that remove potential pollutants and particulates,refine themelt, and cast uniform ingot structures.The resulting facility is capable of producing a wide range of alloys and ingot sizes with minimum inventory levels while operating at high levels of productivity and energy efficiency. The facility is intrinsically safe to operate and meetsall current and near-term environmental standards.INTRODUCTIONThe Source of Aluminum Extrusion ScrapAluminum extrusion scrap comprises reject incoming log and billet, log and billet (and part-billets) rejected or damaged during or after the pre-heat furnace,part-billets and billets withdrawn from the extrusion press, butt ends of billet recovered from the press shear, and lumps of aluminum recovered from the extrusion die. After extrusion from the die, some scrap lengths-usually the front ends of the extrudate-are collected at the rough- cut saw, and some (in the same area of the press installation) as back-end samples.If there are significant differences in rod-length (the length of the extrudate emerging from multi-hole dies,)extruded scrap lengths must be collected from the press run-out table. Uneven extrusion lengths-which can still be seen in some extrusion operations-often have to be cut off at the stretcher tail stock; although some designs of stretcher allow for stretching with the excess length still in place.The excess extrudate known as stretcher scrap comprising front and back-ends of the extrudate which has been damaged at the stretcher, is removed at the finish-cut saw. Also removed arethe transverse weld from the extrusion of successive billets into a single length at the run-out, and the transverse weld allowance, which is much longer and must often be removed from the production of hollow extrusions.Although common alloy (AA6xxx) scrap generated at the extrusion press should be no more than 10 percent of the log or billet delivered to the extrusion press, it is not unusual to find that press scrap is closer to 25 percent due to a combination of the events listed above.If only because of the requirement to leave a larger butt (thereby ensuring that extrusions which might be subject to coring are not extruded),the scrap generated when extruding medium and hard alloys will theoretically be greater than that from AA6xxx operations.From the above.it is evident that the scrap aluminum generated in a typical extrusion plant can be divided into five distinct families:1)The heavy logs and billet-each piece of which is the density of aluminum.2) Heavy butts which,because each is distorted during the shearing operation,are somewhat less den3) Extruded lengths, ranging from stretcher scrap to rejected full lengths, which,when bundled,are about 10 percent of theoretical density.se in bulk than the aluminum metal.4) Assorted pieces of extrusions, usually transported in boxes which,depending on where they are generated, can have a density of more than 10 percent.5) The saw chips-either loose or compressed into bricks of various sizes-which must be collected before the extrusion press at the log saw(s), or after the extrusion press at the rough-cut saw, where chips are deposited along the press run-out, at the finish-cut saw, and at any downstream cut-to-length or fabricating operationsThe Conversion of Aluminum Extrusion Scrap Into Prime IngotAluminum extrusion scrap is converted into prime ingot by melting,treating (cleaning), casting into logs,and homogenizing.The process itself generates additional scrap in the form of aluminum oxides (dross), liquid metal spills, metal trapped in filters, head and butt scrap, scrap logs, and saw chips.The cost of the conversion process is made up of the cost of the capital employed in the remelt and casting plant, the cost of metal lost (oxidized) during melting,the cost of the energy required in the melting process,the cost of alloy materials, the cost of all labor employed in the plant, the cost of the maintenance of furnaces and other production equipment, the cost of effluent treatment facilities (including the cost and treatment of water required in the casting process),and the additional costs (over and above labor) of handling the aluminum and alloying materials in all their forms.Incomplete understanding of the remelt and casting process as it is applied to the scrap from aluminum extrusion operations,and the impact of the process equipment-and its operation on the cost of converting scrap to prime billet, results in an extraordinary range of conversion costs for what is actually a relatively simple operation.But it is not only conversion costs that suffer from lack of understanding of the processes and technologies involved.The quality of billet produced varies significantly between remelt and casting operations ostensibly designed to do the same job. And the environmental impact of the processes used range from the benign to the unacceptable.Establishing GoalsThe goal of the ultimate aluminum extrusion scrap remelt and casting center is to convert all forms of aluminum extrusion scrap to billet equivalent quality and prime (smelter) material at minimal total cost, with minimal impact on the environment.The Quality of Prime (Smelter) Billet. At the risk of stating the obvious: not all smelter-billet is created equal.Aluminum log cast from smelter metal contains impurities that affect the performance of the extruded product. The casting processes-which vary from smelter to smelter- can result in the production of cast structures which vary sufficiently such that they can be detected at the extrusion press.And,homogenizing facilities (and their operation),although ostensibly the same, also vary from smelter to smelter, again producing variations that can be detected at the extrusion press.Recycled aluminum scrap, or for that matter re-melted ingot originating at a smelter, can be processed in the ultimate remelt and casting center. This can be achieved at conversion costs that are lower than the traditional smelter premium to produce extrusion log and billet indistinguishable from prime-provided that alloy composition is maintained.Obviously, sorting and segregation of the incoming scrap feed-stock is essential if the quality of the remelted and cast product is to be maintained.Defining The IssuesThe issues affecting the efficient operation of an aluminum extrusion scrap remelt and casting center can be clearly stated as follows:1)Segregating mixed scrap2) Processing contaminated scrap3)Maximizing the recovery of metal units4) Maximizing energy (fuel) efficiency5) Maximizing product mix: alloy, compositiorand diameter6)Maximizing utilization of equipment7) Maximizing labor productivity8) Maintaining control of quality.Each of the issues can be aaaressea1)Separately as follows:1) Segregating Mixed Scrap. Scrap arisingthe remelt and casting center, which is limitedmetal recovered from dross, the occasionalog, the tops and tails of logs, saw chips anoff-composition material, is segregated and recvcled as appropriate.Scrap from extrusion plant "customers" is routinely segregated at the extrusion press and the finish-cut saw, as is the scrap arising in finishing and fabricating operations.Other aluminum scrap, which is priced lower than the mill scrap listed above because or its condition and dubious origin, must be sorted. Obviously, the purchase price will have retlectea the costs involved in sorting this scrap. Whatever can be recovered is added to those alloys havinghigher tolerance to compositional variation._.’balance must be downgraded,and rejected ror secondary uses.2)Processing Contaminated Scrap.Aluminum extrusion scrap can be contaminated with water and with oil,which is mixed with saw chips and is used to protect bright finishes;scrap can also be contaminated with paints and lacquers,thermal break materials, other plastics, rubber, and,in the case of fabricated components,with rivets and other fasteners made from many different materials. All these materials must be removed and/or separated from the aluminum before it is melted.Manv attempts have been made to process this contaminated material in the melting furnace, combining the processes of de-contamination, separation and melting.They have not been successful.The solutions include placing the contaminated material on an extended furnace hearth and allowing the contaminants to burn-off prior to charging.Another solution is to use dual or multi-chamber furnaces that contain,and attempt to re-circulate,the burning effluents to recover some of the energy released,adding it to that required to melt the scrap charge.While the capital cost of these solutions is high,the energy efficiency of each is relatively low. All require extensive effluent treatment facilities if they are to meet even the least stringent environmental regulations. This is because the large volumes of combustion products (and unburnt volatile materials), released at the instant the charge enters the furnace,are rapidly carried from the furnace towards the effluent treatment systems. Incinerators, coolers and bag-houses must be sized to accommodate the maximum flow rates.There is a better wayl Contaminated scrap can be treated continuously, before it is charged into the furnace,at instantaneous rates that are a fraction of the common charge rates. For example,an efficient furnace-charging system might be designed to load ten tons into the furnace in a matter of seconds: a rate of (say) 20 tons per minute. On the other hand,a system for continuouslytreating contaminated scrap for the same furnace will be required to treat scrap at a rate of (about) 200 pounds(100kg) per minute.3)Maximizing the Recovery of Metal Units. Clean,segregated scrap should be rapidly charged into the melting furnace, and the furnace should be completely closed. The melt should not be disturbed.However, if the dross formation is considered excessive, the furnace should be skimmed,and the skim immediately transferred to a closed chamber and covered with inert gas.When the melt reaches the correct temperature,it should be transferred (in a transfer system that eliminates turbulence) to the holding or casting furnace. Most remelt operations appear to ignore these simple rules.Operators are allowed to stir the melt. Metal is allowed to cascade from melting furnace to holding furnace, often creating mountains of dross where it enters the holder.4)Maximizing Energy (Fuel) Efficiency. Scrap aluminum, much of which will have been pre- heated when it was de-contaminated,together with pre-heated pig and some cold scrap,is rapidly charged into a hot furnace. As stated above, efficient scrap melting is done in a closed (sealed might be a better word) furnace. The combustion air, which must be pre-heated,must be rigorously controlled. Recuperation of heat from the furnace gases must not affect the combustion process.The holding furnace, and homogenizing furnaces, must likewise be designed and operated to maximize energy efficiency.5)Maximizing Product Mix:Alloy, Composition and Diameter. An efficient remelt and casting center will serve many customers,combining pig and available scrap,and recycling their scrap back to the customer's preferred composition(s), required log and billet dimensions.The product of the number of alloy compositions and the log diameters is the measure of product mix. Depending on the number of customers and their require, alloy-diameter variants can run into hundreds.To accommodate these variations, furnace campaigns must be planned to start melting and casting the pure aluminum alloys, then the common AAA6xxx alloys, followed by the hard alloys.6) Maximhefng Utiilzation of Equipment In an aluminum scrap remelt and casting center, the melting fumace(s)must inevitably be the production bottlenecks. All other equipment and operations must be designed, installed, and operated to ensure that the furnaces reach their full potential.This means that furnaces must be available at an rimes. Pumwe and utilization measured agakVt.standard of 24 X 7 X 52 i.e. 8736 annual hours. Maintenance time must therefore be minimized. This is accomplished by engineering all the equipment and operations (including the furnaces) to minimize the possibility of damage, and to maximize the life under normal operating conditions.Traditional aluminum scrap remelt and casting operations have been designed to accept a wide range of materials-smelter pig and ingot, customer scrap, reject log, billet and butts, extrusion scrap-often bundled or compressed-but also in mill lengths up to 21 feet (7m), and saw chips-loose and compressed into briquettes. This is usually loaded into rectangular furnaces through large doors, or if contaminated, into rectangular open wells. The loading (charging) operation is done using fork trucks or custom designed charging machines. The furnace doors, charging wells and roofs are inevitably damaged. The faster the charging operation, the greater is the resulting damage.7)Maximizing Labor bor productivity as measured in thousands of tons per person-year, is maximized when the plant throughput is maximized and the total number of people employed is at a minimum.8) Maintaining control of quality. Rigorous segregation of scrap, control of alloy additions and composition, together with the control of all processes-temperatures and times-including control of the dimensions of the product, ensure that the resulting homogenized log or billet meets quality The Ultimate Remelt and Casting Center.standards equivalent to prime smelter metal.Technology is available to deliver all the objectives listed above while meeting or exceeding all current and perceived future environmental regulations. All of the technologies are employed in aluminum scrap remelt and casting operations but, to the writer’s knowledge,to one installation combines all the technologies required to maximize the performance and financial returns. The technologies:1 Breaking bundles (bales), fabrications, and shearing long extrusions into short lengths, thereby maximizing the density of the extrusion scrap prior to charging into the melting furnace.2 Breaking bundles (bales), fabrications and shearing long extrusions into short lengths, thereby minimizing the possibility of damage to furnace walls and roof when the scrap is charged into the melting furnace.3 Continuously de-coating the short lengths of extrusion scrap, small pieces or fabricated aluminum, and saw chips to minimize the equipment required to eliminate effluents and meet all current environmental standards.4 Utilizing the energy released by the coatings, associated plastics:rubbers, and oils to preheat the scrap aluminum.5 Storing the heated aluminum to retain the energy.6 RaDidlv changing the heated aluminum scrap into the melting fumace.7 Employing circular top-charging melting fumace(s) equipped with a charging system that eliminates the possibility of damage to furnace floor, walls and roof.8 Employing circular top-charging melting furnace(s) with small sealed doors to ensure control of combustion.9 Using stack recuperators to pre-heat the combustion air.10 Employing circular top-charging melting fumace(s) constructed to extend the life between major repairs from months to years.Tilting the melting furnace(s) and thenoiaing turnace(s) to ensure that transfer ofmetal between the furnaces is turbulent-ree throughout the transfer of metal.Employing straight launder systems for all metal transfer and castinq,minimizing bothturoulence and the resulting wear. Engineering the holding furnace to enable complete access to the surface of the molten aluminum.Using stack recuperators to pre-heat the combustion air. Using in-line continuous addition of grain refiner rod.Using in-line degassing systems.Using in-line filtering systems.Using internally guided hydraulic casting machine to eliminate the potentially high maintenance external guide systems.Employing off-line set up station for the casting table.Using hot-top and Air-Slip casting technology.Using batch-homogenizing systems designed to ensure that the load is uniformly processed from end-to-end and side-to-side.Using continuous homogenizing systems designed to ensure that all logs are processed in the same manner.Using sawing systems that maximize the recovery of billet from each sawn log.CONCLUSIONBy selecting a number of available technologies and combining them into a state-of-the-art aluminum extrusion scrap remelt and casting center, the recycling industrty can produce billet wquialent to prime while minimizing its concersion cosrs and meeting all current encironmental saandsrds.REFERENCESArticles and papers relecant to the recycling of aluminum extrusion scrap prepared by the associates of BENCHMARKS and The Virtual Company Inc.,which have appeared since May 1996:1 .Fielding, Roger A. P.,D. Hugh Barnard, and George. E. Macey, "The Role of Modeling in the Design and Operation of Remelt and Casting Facilities," Sixth International Extrusion Technology Seminar, V ol. I,Chicago, Illinois, May 1996, 437-442.2. Fielding,Roger A. P. and Carol F. Kavanaugh,"The Role of Grain Refining, Degassing,and Filtration in the Production of Quality Ingot Products," Light Metal Age, Vol.54,Nos. 9, 10 October 1996,46-59. (Contribution by Carol Kavanaugh on Effective and Efficient Measurement: The Design of Experiments.)3. Fielding, Roger A. P., "The Aluminum Association Standard Test Procedure for Aluminum Alloy Grain Refiners 1990: TP-1,A Case Study in Cooperative Development," Light Metal Age, Vol.55, Nos. 5,6, June 1997, 66-80.4. Fielding, Roger A. P.,"Recycling Secondary Aluminum Scrap at Roth Bros, Syracuse, N.Y.," Light Metal Age, Vol. 56, Nos.1,2, February 1998,99=101.5. Fielding, Roger A. P., "The Economy of Extrusion Scrap Recycling.The Metallurgical, Minerals and Metals Conference, TMS San Antonio TX, March 1998,”Light Metals, 1998,1137-1142.6 .Bryant, A. J.,and Roger A. P. Fielding,"The Impact of Recent Developments in Billet and Extrusion Metallurgy on the Development of Equipment Technology," Light Metal Age, V ol. 56, Nos. 3,4, April 1998, 6-34.7. Bryant, A. J., and R. A. P. Fielding, "The Evaluation of Extrusion Billet from the Cast house 一Part I,,’Light Metal Age, V ol.57, Nos. 1,2, February 1999, 80-86.8. Bryant, A. J. and R. A. P. Fielding, "The Evaluation of Extrusion Billet from the Cast house 一Part II,,,Light Metal Age, V ol. 57, Nos. 3,4, April 1999, 78-82.9. Bryant, A. J.,W. Dixon, R. A. P. Fielding,and G. E. Macey, "Defects in Medium and High Strength Extrusion Alloys," Light Metal Age, V ol. 57,Nos. 5,6,June 1999,30-54.10. Bryant, A. J. and R. A. P. Fielding, "Recent Developments in Grain Refining,Degassing, and Filtration for the Production of Quality Ingot Products," Unpublished Report, August 2000. 11.Barnard,Hugh,"Evaluating Melting Furnace Combustion Systems," Light Metal Age, V ol.59, Nos.9, 10, October 2001,16, 17.12. Bryant, A. J., G. E. Macey, and R. A. P. Fielding, "Homogenization of Aluminum Alloy Extrusion Billet, Part I,,”Light Metal Age, Vol. 60, Nos. 3, 4, April 2002, 6-15.13. Bryant, A. J., G. E. Macey, and R. A. P. Fielding,"Homogenization of Aluminum Alloy Extrusion Billet, Part I.,"Light Metal Age, V ol 60,Nos. 5,6,June 2002,18-27.中文译文:基本挤压冶炼和铸造的根源编写——罗杰托维奇菲尔丁——基准乔治英, Macey——Macey传热协会D 。
材料成型专业英语
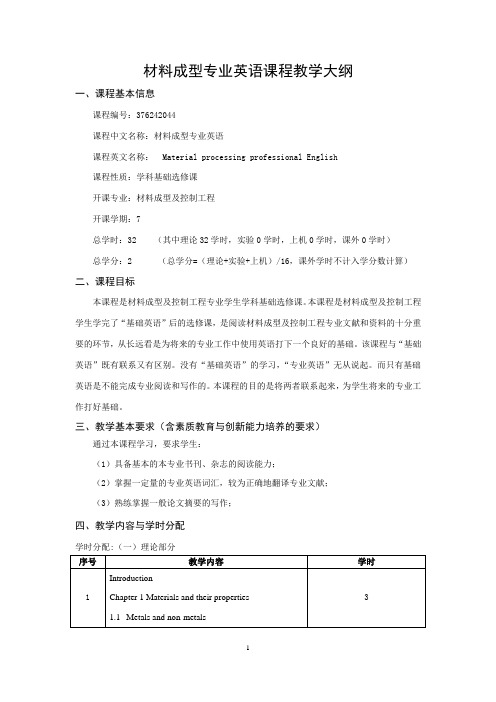
材料成型专业英语课程教学大纲一、课程基本信息课程编号:376242044课程中文名称:材料成型专业英语课程英文名称:Material processing professional English课程性质:学科基础选修课开课专业:材料成型及控制工程开课学期:7总学时:32 (其中理论32学时,实验0学时,上机0学时,课外0学时)总学分:2 (总学分=(理论+实验+上机)/16,课外学时不计入学分数计算)二、课程目标本课程是材料成型及控制工程专业学生学科基础选修课。
本课程是材料成型及控制工程学生学完了“基础英语”后的选修课,是阅读材料成型及控制工程专业文献和资料的十分重要的环节,从长远看是为将来的专业工作中使用英语打下一个良好的基础。
该课程与“基础英语”既有联系又有区别。
没有“基础英语”的学习,“专业英语”无从说起。
而只有基础英语是不能完成专业阅读和写作的。
本课程的目的是将两者联系起来,为学生将来的专业工作打好基础。
三、教学基本要求(含素质教育与创新能力培养的要求)通过本课程学习,要求学生:(1)具备基本的本专业书刊、杂志的阅读能力;(2)掌握一定量的专业英语词汇,较为正确地翻译专业文献;(3)熟练掌握一般论文摘要的写作;四、教学内容与学时分配学时分配:(一)理论部分五、教学方法及手段(含现代化教学手段及研究性教学方法)多媒体设备并结合板书教学,期间利用网络资源为教学服务。
六、实验(或)上机内容无七、前续课程、后续课程前续课程:大学英语;后续课程:焊接技术与工程科技创新实践活动、焊接技术与工程专业生产实习、焊接技术与工程专业毕业设计/论文。
八、推荐教材、参考书[1]胡礼木,王卫卫.材料成型及控制工程专业英语阅读(第一版). 北京:机械工业出版社, 2004.[2]张军.材料专业英语听说教程(第一版). 北京:机械工业出版社,2001.九、考核方式。
- 1、下载文档前请自行甄别文档内容的完整性,平台不提供额外的编辑、内容补充、找答案等附加服务。
- 2、"仅部分预览"的文档,不可在线预览部分如存在完整性等问题,可反馈申请退款(可完整预览的文档不适用该条件!)。
- 3、如文档侵犯您的权益,请联系客服反馈,我们会尽快为您处理(人工客服工作时间:9:00-18:30)。
▪The role of heat treatment in modern mechanical engineering can not be overestimated.▪The changes in the properties of metals due to heat treatment are of extremely great significance.热处理在现代机械工程中的作用不可能评价的过高。
由热处理而产生的性能改变是特别重要的。
☐2.1.1 temperature and time 温度和时间The purpose of any heat treating process is to produce the desired changes in the structure of metal by heating to a specified temperature and by subsequent cooling.▪任何热处理的目的都是(通过)将金属加热到一定的温度并(随后)冷却,以使金属组织产生所需变化。
☐2.1.1温度和时间Therefore, the main factors acting in heat treatment aretemperature and time, so that any process of heattreatment can be represented in temperature-time ( t- r ) coordinates.▪因此,热处理的主要因素是温度和时间,所以任何热处理工艺都以用温度-时间为坐标轴进行表示。
▪Heat treatment conditions are characterized by the following parameters: heating temperature t max, i.e. the maximum temperature to which an alloy metal is heated; time of holding at the heating temperature ; heating rate and cooling rate .▪☐热处理工艺主要有以下几个参数:加热温度t max ,既合金加热的最高温度;在加热温度下的保温时间;加热速率和冷却速率。
☐如果以不变速率加热或冷却,则温度和时间的关系可以具有不同倾斜角的直线。
▪If heating (or cooling) is made at a constant rate, the temperature-time relationship will be described by a straight line with a respective angle of incline .▪Respective 分别的, 各自的☐如果加热速率(或冷却速率)变化,则实际速率由给定温度确定,更严格的说,是温度对时间的无穷变化:即温度对时间的一阶导数。
▪With a varying heating ( or cooling) rate. the actual rateshould be attributed to the given temperature ,more strictly, to an infinite change of temperature and time: that is the first derivative of temperature in time .▪Infinite 无限的东西(如空间、时间), [数]无穷大☐加热可以是复杂的过程,可以包括几个加热阶段、间断式或阶梯式的加热/冷却,冷却到0℃以下等。
任何热处理过程都可以描述成为以温度和时间为坐标轴的曲线。
▪Heat treatment may be a complex process, including multiple heating stages . interrupted or stepwise heating ( cooling) , cooling to subzero temperatures , etc . Any process of heat treatment can he described by a diagram intemperature-time coordinates .▪interrupt -中断stepwise -楼梯式的, 逐步的subzero- 零度以下的(温度)2.1.2 formation of austenite▪The transformation of pearlite into austenite can only take place at the equilibrium critical point on a very slow heating as follows from the Fe-C constitutional diagram. Under common conditions, the transformation is retarded and results in overheating, i. e. occurs at temperatures slightly higher than those indicated in the Fe-C diagram.▪Constitutional diagram相图(构成的, 增强体质的, 宪法的)pearlite-珠光体 retard延迟, 使减速, 阻止, 妨碍, 阻碍根据Fe-C相图,在平衡临界点缓慢加热,珠光体转变为奥氏体。
一般条件下,转变会延迟导致guore,即转变温度略高于Fe-C相图中的指定温度。
▪When overheated above the critical point, pearlite transform into austenite,the rate of transformation being dependent on the degree of overheating .☐当加热温度高于临界点时,珠光体转变为奥氏体,转变速率依赖于过热的程度。
(过热、过冷的概念)☐各温度下的转变时间(依赖于过热度)表明在较高的温度下相变产生较快(时间短);加热速度快时,相变在较高温度产生。
▪The time of transformation at various temperatures (depending on the degree of overeating) shows that the transformation takes place faster (in a shorter time) at a higher temperature and occurs at a highertemperature on a quicker heating .▪For instance, on quick heating and holding at 780℃,the pearlite to austenite transformation is completed in 2 minutes and on holding at 740°C, in 8 minutes .▪℃——centigrade☐例如,780℃加热速度较快时,珠光体完全转变为奥氏体需要2分钟,740℃时则需要8分钟。
▪The end of the transformation is characterized by formation of austenite and the disappearance of pearlite ( ferrite +cementite) . This austenite is however inhomogeneous even in the volume of a single grain.▪转变结束是以奥氏体形成和珠光体(F+渗碳体)消失为标记的。
然而,即使在单个晶粒中奥氏体的也不均匀。
▪In places earlier occupied by lamellae (or grains) of a pearlitic cementite, the content of carbon is greater than in places of ferritic lamellae . This is why the austenite just formed is inhomogeneous .▪早期形成的片状(或li状)珠光体渗碳体,其含碳量高于片状铁素体,这就是奥氏体(成分)不均匀的原因。
▪lamellae薄片状的, 薄层状的☐为了获得均匀的奥氏体,加热温度不仅要超过珠光体转变为奥氏体的终点温度,而且要高于这一温度,并保温一段时间,使奥氏体晶粒内发生完全扩散。
▪In order to obtain homogeneous austenite, it isessential on heating not only to pass through the point of the end of pearlite to austenite transformation, but also to overheat the steel above that point and to allow a holding time to complete the diffusion processes inaustenitic grains2.1.2 formation of austenite▪The rate of homogenization of austenite appreciably depends on the original structure of the steel, in particular on the dispersion and particle shape of cementite . The transformations described occur more quickly when cementite particles are fine and, therefore ,have a large total surface area .▪奥氏体均匀化的速度主要依赖与钢的原始组织,特别是渗碳体的分布及晶粒形状。