钣金冷冲压检验作业指导书样本
钣金车间冲压作业指导书

钣金车间冲压作业指导书1.目的和适用范围为了保障操作人员的人身安全和设备安全,保证产品质量,特制订本作业指导书,以规范作业程序。
本作业指导书规定只准许经过公司培训的人才能使用冲压机械。
2.作业程序2.1 作业前的准备2.1.1 看懂图纸要加工的内容,选用正确的模具。
2.1.2 开机前,对滑轨、离合器、转动轴处进行加油润滑。
2.2 装模、试模2.2.1 装模前,要弄清楚本模具所需工作压力是否小于被装冲床的工作压力,严禁超负荷运转,以免损坏冲床,但也不能不考虑功率消耗,一般取机床额定压力的85%左右,还要清楚模具的闭合高度必须小于冲床的最大闭合高度,小于最小闭合高度时要加装垫板;其次要知道模具的模柄与冲头孔径是否相符;以上三者有不符之一的就要调换冲床。
2.2.2 用推车把模具推到工作机旁,开始清理冲床周围工作环境并清洁工作台面。
2.2.3 开启电机,让冲床空转几下,听听工作声音是否正常,并试一下离合器,操纵杆、刹车等控制部位是否运转正常。
2.2.4 关闭电机,把上下闭合的模具放到工作台面上。
2.2.5 松开连杆上的锁紧螺母和紧定螺钉,适当调整滑块高度后,再松开滑块上的上模柄锁紧螺母。
2.2.6 当上模上平面与滑块下平面贴紧无缝后锁紧模柄螺母,调整滑块螺母,让上模向上稍稍抬起,但不得使上、下模脱开,用扳手把下模向内轻打后,稍稍固定下模。
2.2.7 用撬杠或用手转动大飞轮带动滑块作几次空行程转动,目测后用纸试冲,看模具的周边间隙是否均匀,不均时调整下模,直到均匀为止。
2.2.8 调整好行程后,固定锁紧螺母和紧定螺钉。
2.2.9 再次锁紧下模,开启电机进行试冲。
2.3 冲裁2.3.1 模具试好以后,利用模板或定尺、导尺对工件进行定位。
首件符合图纸要求后,通知品检进行检查,确认合格后方能批量冲,对超过50件以上的批量,每隔10分钟要量尺寸,看定位是否跑动。
3.注意事项3.1 上、下模或调整定尺时必须关掉电源。
(完整word版)钣金件检验指导书
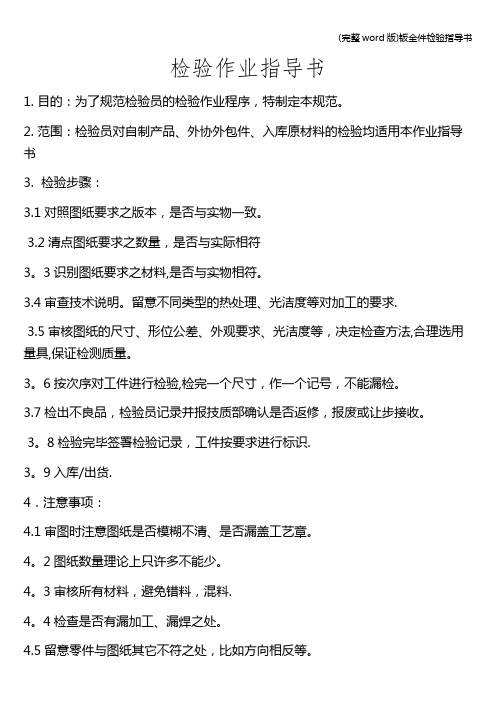
检验作业指导书1. 目的:为了规范检验员的检验作业程序,特制定本规范。
2. 范围:检验员对自制产品、外协外包件、入库原材料的检验均适用本作业指导书3. 检验步骤:3.1对照图纸要求之版本,是否与实物一致。
3.2清点图纸要求之数量,是否与实际相符3。
3识别图纸要求之材料,是否与实物相符。
3.4审查技术说明。
留意不同类型的热处理、光洁度等对加工的要求.3.5审核图纸的尺寸、形位公差、外观要求、光洁度等,决定检查方法,合理选用量具,保证检测质量。
3。
6按次序对工件进行检验,检完一个尺寸,作一个记号,不能漏检。
3.7检出不良品,检验员记录并报技质部确认是否返修,报废或让步接收。
3。
8检验完毕签署检验记录,工件按要求进行标识.3。
9入库/出货.4.注意事项:4.1审图时注意图纸是否模糊不清、是否漏盖工艺章。
4。
2图纸数量理论上只许多不能少。
4。
3审核所有材料,避免错料,混料.4。
4检查是否有漏加工、漏焊之处。
4.5留意零件与图纸其它不符之处,比如方向相反等。
4.6留意机加面油漆前是否做好防护措施。
4.7检查图纸标识需焊后加工的是否留有余量.5。
检验要求和方法5.1外观检验要求5。
1.1使用材料应符合有效版本图纸的要求,材料本身应无变形、划伤、氧化变色5。
1.2表面光滑、平整、无毛刺、变形、锈蚀、裂纹、压折、夹渣、气孔等;预埋件、铆件应牢靠、无松动,螺纹无缺损、无腐蚀等;不允许有加工遗留物;5.1。
3零件的喷漆层应均匀、连续,无缩孔、起泡、开裂、剥落、粉化、流挂、露底(局部无涂层或涂料覆盖不严)、指印等缺陷;5.1。
4表面处理后,零件表面允许有不可避免的轻微夹具印痕和轻微的水印;在不影响装配的情况下,边、棱角处允许有轻微的粗糙;非重要表面允许有轻微的水纹或个别的斑点;5.1.5去毛刺要求:用手沿零件加工边角的任何位置及方向触摸均无刮卡现象。
5。
2尺寸检验方法和要求5.2.1标注公差尺寸检验方法及标准:用游标卡尺,高度尺,角度尺,百分表,平台,投影仪,高度测量仪或检测夹具等进行检验.标准:实测尺寸偏差应符合图纸公差要求。
钣金件检验指导书

钣金件检验指导书钣金件检验指导书1-简介1-1 目的1-2 适用范围1-3 定义和缩写词解释2-质量标准2-1 钣金件质量标准的选择2-2 相关质量标准及要求的说明3-物料检验3-1 材料选择和接收检验3-2 材料外观检验3-3 尺寸和几何要求检验3-4 化学成分和物理性能检验4-制程检验4-1 冲压工艺参数检验4-2 冲压设备的检验要求4-3 冲压件的外观检验4-4 冲压件尺寸和几何要求检验5-表面处理检验5-1 表面处理工艺要求和检验5-2 涂装和喷涂工艺的质量检验5-3 电镀工艺的质量检验5-4 镀膜工艺的质量检验6-钣金件组装检验6-1 组件检验顺序和方法6-2 钣金件组装尺寸和几何要求检验 6-3 焊接工艺的质量检验6-4 紧固件使用和拧紧力矩的检验7-最终产品检验7-1 最终产品外观检验7-2 最终产品尺寸和几何要求检验 7-3 功能性能和可靠性测试7-4 安全性能和环境要求的检验8-检验记录和报告8-1 检验记录的要求和形式8-2 检验报告的编写和发布9-附件附件1:相关质量标准附件2:检验记录表格范本本文涉及附件:附件1:相关质量标准附件2:检验记录表格范本本文所涉及的法律名词及注释:1-质量标准:指钣金件应满足的相关技术规范和要求。
2-冲压:指将金属片通过模具加工成特定形状的工艺过程。
3-表面处理:指对钣金件的表面进行除锈、涂装、电镀等处理的工艺过程。
4-焊接:指将两个或更多金属材料通过加热或压力连接起来的工艺过程。
钣金作业指导书

1 .目的:本作业指导书用于指导装配组的生产作业过程。
确保该过程受控,安全、准确、有效。
2.范围:装配工加工区3.职责:此作业指导书由装配工主管负责编写,装配车间及相关人员共同执行。
4.定义:4.1.首件:各工序在同一生产条件下,进行批量生产的第一件。
4.2.生产工作单:生产工作单为指导零件加工过程的主要依据,主要包气括:零件图号、需求数量、工程号及工程名称、零件材料、加工工序、生产完成数量、报废数量、生产操作者签名、检验员签名(如果是自检则和操作者一样)生产日期等内容。
4.3.材料型号:材料型号由以下内容组成SM**-AABBBCCCSM:----材料代号固定的前两位代码。
**:----材料类型♦AS:铝板♦CS:铜板♦AZ:敷铝锌板♦HG:热镀锌板♦MS: A3钢板♦SS:不锈钢板AA:---板材厚度,为实际厚度乘以10,如2MM为“20”1.5MM为“15”BBB:--板材宽度,为实际宽度数值的前三位。
如1500MM为“150”如1250MM为“125”。
CCC:--板材长度,为实际长度数值的前三位。
如2250MM为“225”如2440MM为“244”。
典型的材料代号如:SMAZ-20125225,表示厚度为2MM,长度为2250MM宽度为1250MM的敷铝锌板5.装配作业流程:5.1.零件编程:装配组接到生产任务,由装配工计划员(目前由主管或装配班长代替)将工作单交给编程员,编程员在接到任务后,根据工作单及图纸等技术文件,编写零件的装配作业程序,并打印出清单,附在工作单上,交装配组生产。
3. 编程人员在编程时应该把零件号编入零件的加工程序中去具体编法如下:例:图号8K2.151.010 零件编号:8K21510105.2. 冲压作业:5.2.1操作者每天开机后生产前,进行点检及安全检查,若发现问题则记录在工作交接单上并及时处理其问题,若无法解决,则报告领班或主管。
5.2.2操作者接到生产任务时,应确认程序,模具清单及工作单是否齐全发现不当之处应立即向班长反馈,或者上报有关人员处理。
钣金检验作业指导书

5.1.23毛丝:产品表面出现细小的尘丝。
检验项目
抽样方案
检查水平
AQL
判定数组
7.5.1
GB/T2828.1正常检验一次抽样
Ⅱ
A=0
B=0.65
C=2.0
8.1
8.2
8.3
定数抽样
n=3,B类不合格:Ac=0,Re=1
7.5.2
7.5.3
8.1.2 附着力判定标准:
序号
检验项目
缺陷内容
判定
检验方法
8.1.3
附着力测试
丝印轻微脱落(丝印內容无损)
C
3M胶纸
丝印脱落(丝印內容仍可清晰分辨)
B
丝印脱落(丝印內容残缺)
B
8.2百格试验
8.2.1 测试规范及要求:用刀片在被测样品表面割划1*1mm2的方格(伤至本体上),用3M胶纸(型号600#)
7.1.4目视时间:5~10S。
7.2检验常用单位代码对照表
项目名称
数目(个)
直径(mm)
深度(mm)
距离(mm)
长度(mm)
宽度(mm)
面积(mm2)
对应代码
N
D
H
DS
L
W
S
7.3 检验标准说明
7.3.1当非异色的缺陷的直径D<0.20mm且不连续时,可以不作为缺陷。
7.3.2以下所提到的不良缺陷的数目均指单面上的不良缺陷数目。
5.1.16鱼眼:由于溶剂挥发速度不对而在喷涂件表面出现凹痕或小坑。
5.1.17飞油:超出了规定的喷涂区域。
5.1.18剥落:产品表面出现涂层脱落的现象。
冲压作业指导书样本
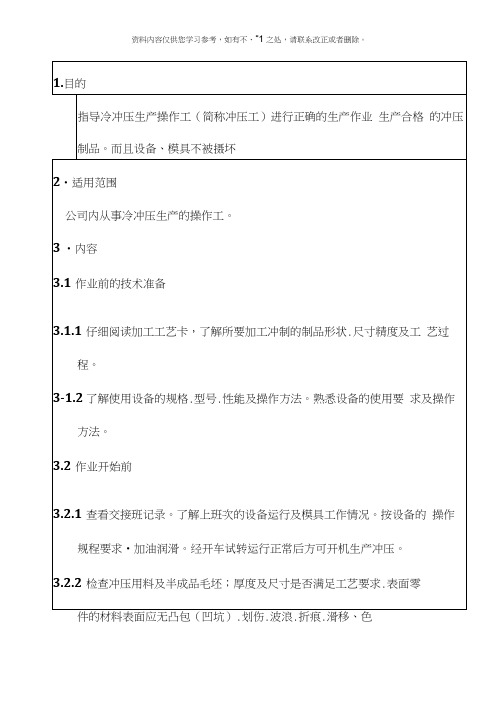
件的材料表面应无凸包(凹坑).划伤.波浪.折痕.滑移、色差等缺陷.工底间毛坯件应无变形.压痕.裂纹.皱折等。
否则,通知检验人员处理。
3.2.3检查冲模是否安装的牢固.有无松动。
模具内有无杂物。
模具存放限位器是否放在合适的位置。
按工艺要求调整设备气垫压力。
资料内容仅供您学习参考,如有不7之处.请联系改正或者删除。
3.2.4备好装放冲压件、废料的工位器具及位置。
禁止生产过程中有坯料翻倾、滑落、伤人的现象出现;操作空间不宜拥挤,留出800mm 竟人行通道,以备不时之需。
33工作过程中3.3.1 冲压工应严格按《冲压安全作业工艺补充规定》《冷冲压件润滑工艺规程》及相关设备操作规程进行操作;作业时应思想集中.谨慎操作, 准确定位。
3.3.2 每批生产时的首件要进行自检:自检合格后交检验人员检验.检验合格后才能批量生产,生产的合格零件按要求摆放到工位器具内。
自检不合格时要进行分析,必要时找调整工重新进行模具安装调试,调模后的第一件必须自检自检合格后交检验人员检验检验合格后才能批量生产。
检验不合格.程陰同上。
3.3.3 生产时要进行实时监测:随时观察模具状态.及时清理废料.保持模具区清洁,刃口无崩刃.无废屑产生等.并监测机床工艺参数' 避免生产过程中压床滑块移位造成零件成形偏差。
3.3.4 当设备、模具和其它有关装置发生故障时。
必须停车检查:33.4.1滑块停点不准,或停止后自动下滑。
33.4.2设备发生不正常声响。
33.4.3制品零件出现不允许的毛剌或影响外观质量的缺隊33.4.4制品及废料取不出来。
3.4.1作业完毕.首先要关闭电源。
将冲模内杂物清理干净,要在模具导向部位及活动部分涂上润滑油.对有气垫(缓冲器)的压力机要放出其中的压缩空气并控净压力机.清理台面上的废料、废品。
整理好自己的工作位置,保持整洁。
配合检验人员对当班产生的不合格品进行区分, 楓定置区孵独存放。
3.4.2最后要填写交班记录.将所有在工作过程中出现的正常及非正常现象写清皑以备下一班次接班者明了。
钣金检验作业指导书

塞规、卡尺
<0.15mm(以平面度、直线度、平行度等指标考核);变形引起的错位,常用手摸处≤0.15mm,不影响装配。
C
塞规、卡尺
7.5.5
材质
材质与样品不一致
B
见 样 品
8.1 附着力测试:
8.1.1测试规范及要求:用3M胶纸(型号:600#)贴于样品丝印表面并按紧,使胶带均匀粘附于样品表面,提起胶带一边沿45°角迅速拉起,拉起胶带后丝印无脱落现象,每单位测试样品以五次试验后结果为准。
7.5.4
7.5.5
定数抽样
n=10,B类不合格:Ac=0,Re=1
n=10,C类不合格:Ac=1,Re=2
6、抽样方案:
7、检验.1.1 光源:物件距光源0.65~1.0m的40W日光灯下。
7.1.2目视距离:30-40cm。
7.1.3目视角度:检测面与人眼方向成45°~90°。
0
1
2
1.0<L<2.0,W<0.3,DS>40
0
0
1
3
软划痕
L<4,W<0.2,DS>30
0
2
3
4<L<8,0.2<W<0.3,DS>40
0
1
2
8<L<10,W<0.3,DS>40
0
0
1
4
堆漆/积油
不允许
6
飞油
L<0.3或参照限度样品。
7
剥落
不允许
8
色差
ΔE<1.0或参照限度样品
10
手印(不能擦除)
8.1.2 附着力判定标准:
钣金作业指导书

钣金作业指导书一、任务描述本文档旨在提供钣金作业的详细指导,包括作业前准备、操作流程、注意事项等内容,以确保钣金作业的顺利进行。
二、作业前准备1. 确定作业范围:根据客户需求或者车辆损坏情况,确定需要进行钣金修复的部位。
2. 准备工具和材料:根据作业范围准备相应的工具和材料,如钣金锤、钳子、焊接设备、钢板等。
3. 安全措施:确保作业区域通风良好,佩戴个人防护装备,如手套、护目镜等。
三、操作流程1. 清洁作业区域:使用清洁剂清洗作业区域,确保表面干净无尘。
2. 检查损坏程度:子细检查损坏部位,确定是否需要修复或者更换钣金件。
3. 钣金修复:根据损坏情况选择相应的修复方法,如钣金拉伸、钣金修补、钣金更换等。
4. 焊接处理:如有需要,进行焊接处理,确保焊接点坚固可靠。
5. 打磨和涂装:修复完成后,进行打磨和涂装,使修复部位与周围车身颜色一致。
6. 质量检验:对修复部位进行质量检验,确保修复效果符合要求。
四、注意事项1. 安全第一:在作业过程中,务必注意个人安全,避免发生意外伤害。
2. 子细检查:在进行钣金修复前,子细检查损坏部位,确保修复方案的准确性。
3. 熟练操作:钣金作业需要一定的技术和经验,操作人员应具备相应的专业知识和技能。
4. 精细处理:在进行钣金修复时,应尽量保持细致和精细,确保修复效果符合要求。
5. 质量控制:修复完成后,进行质量检验,确保修复部位的质量达到标准要求。
五、总结本文档提供了钣金作业的详细指导,包括作业前准备、操作流程、注意事项等内容。
在进行钣金作业时,务必严格按照操作流程进行,注意个人安全和修复质量。
通过遵循本指导书,可以有效提高钣金作业的效率和质量,满足客户的需求。
钣金件检验指导书

钣金件检验指导书一、介绍钣金件是制造业中常见的一种金属件。
它们广泛应用于汽车、电子设备、建筑等行业中,具有重要的功能和作用。
为了保证钣金件的质量,确保其能够满足设计需求和使用要求,进行钣金件的检验是至关重要的。
二、目的本指导书的目的是为钣金件的检验提供一套标准化的流程和要求,帮助相关人员进行高效的检验工作,确保钣金件的质量符合标准。
三、检验准备1. 检验环境:检验钣金件的场所应干燥、明亮,有足够的空间布置检验设备和样品。
同时,应保持整洁,避免杂物和灰尘对检验的干扰。
2. 检验设备:根据不同的钣金件特性,选择合适的检验设备,如测量工具、显微镜、硬度计等。
确保这些设备处于良好的工作状态,准备充足的备用工具和耗材。
3. 检验流程:制定合理的检验流程,包括检验前的准备工作、具体的检验方法和步骤,以及结果记录和评估。
四、检验项目1. 外观检验:钣金件的外观是直接可见的,应该检查是否有表面缺陷、凹陷、划痕等问题。
还应注意外观的光洁度和涂层的附着力。
2. 尺寸检验:根据钣金件的设计图纸,测量实际零件的尺寸,检查是否符合要求。
可采用测量工具进行测量,如卡尺、游标卡尺等。
3. 安装可靠性检验:对于需要安装的钣金件,应进行安装可靠性检验,即检查安装是否牢固、精确。
可采用拧紧扭矩、振动等测试方法。
4. 材料成分检验:对于大型钣金件制造商,有必要进行材料成分的检验,确保所使用的材料符合相应的标准和要求。
可采用光谱分析等测试方法。
5. 表面处理检验:如果钣金件经过了表面处理,如电镀、喷涂等,需要进行表面质量的检验,以确保表面光滑、耐腐蚀和耐磨损。
六、记录和评估在进行钣金件检验的过程中,应及时记录检验结果和相关数据。
根据检验结果,对钣金件的质量进行评估,判断是否合格。
对于不合格的钣金件,需要进行问题分析并采取相应的纠正措施,以确保下一批次的钣金件质量。
七、安全注意事项在进行钣金件检验的过程中,需要注意以下安全问题:1. 检验设备的使用和维护应符合相关的安全操作规程。
钣金件通用检验作业指导书
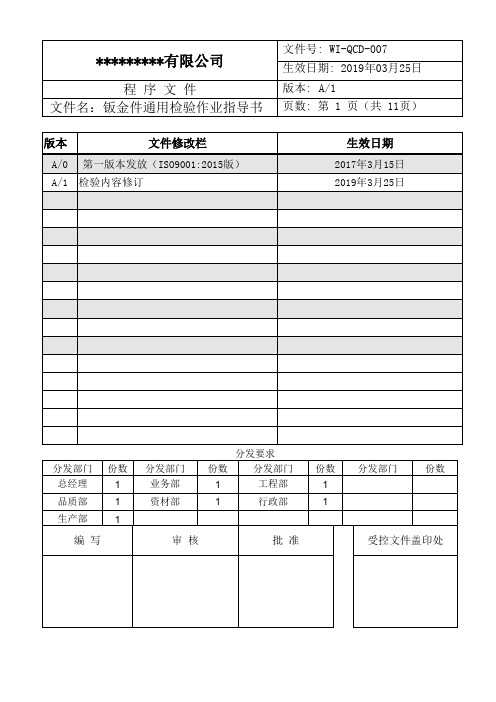
1、目的规范钣金检验作业,制定了钣金制造各工序检验的方法和要求。
确保在生产过程中产品品质的稳定,使各过程的产品质量得以控制。
2、适用范围适用于公司内钣金制造加工的质量检验工作。
●当产品有特殊要求涵盖本指导书或有技术变更的,依据特殊要求执行。
●当产品有客户指定要求的,依据客户指定要求执行。
3、职责3.1 生产部操作工负责对所加工零部件进行自检和互检。
3.2 质量部负责所加工零部件的检验和不良品处理。
3.3 工程部负责产品技术支持。
4、定义:4.1:自检:操作员在生产操作过程中,对自已操作加工好的部件或半成品按照《作业指导书》《检验规范》检查,合格品后转入下工序,不合格品挑出来返工或由检验员判定。
4.2互检:是指操作员对上工序流入本工序加工的半成品按照《作业指导书》与IPQC的要求进行检查,合格品继续加工,不合格品退回上道工序返工。
操作工在操作前,要对上道工序加工零件或原材料进行外观和形状检验,如果发现不良品,操作工可以拒收并通知检验员或工程师处理该不良品。
4.3首检:每次更换型号或材料时,检验员应对生产的产品依相关资料(如生产任务单、图纸、样品等)进行核对,并根据相关检验/测试标准对样品进行检验.4.4 巡检:现场QC应定时不间断的对生产过程进行巡视,对各人负责的工序至少每隔1小时进行抽样检验,检验产品是否符合要求,操作是否得当。
检验频率 1h/次,检验数量 2pcs/次。
5、检验方法及要求5.1剪切作业检验标准5.1.1尺寸要求:a)尺寸裁切依据图纸公差要求。
b)图纸未标注的公差板材单边测量尺寸≤1mm为合格,对角线≤2mm 为合格。
c)剪切后的板四周边缘不允许有蜷曲和变形,卷曲高度≤0.5mm 的为合格,超过0.5mm为不合格。
d)冲裁后毛刺高L≤5%t(t为板厚)。
e)图纸中未明确标明之尖角(除特别注明外)均为R1.5。
f)对有可能造成伤害的尖角、棱边、要做去除毛刺处理。
5.1.2表面要求:a)长度超过5毫米的深划痕(有手感的),特别是正中很明显的位置,不允许有。
钣金冷冲压检验作业指导书

钣金冷冲压检验作业指导书编制:审核:批准:生效日期:受控标识处:分发号:发布日期:2012年6月28日实施日期:2012年6月28日1.0 目的对钣金冷冲压件加工过程的监督及成品检验的要求。
2.0 适用范围本标准适用于公司及其外协加工的钣金冷冲压件。
3.0 引用标准GB/T 13916-2002 冲压件形状和位臵未注公差GB/T 1804-2000 一般公差未注公差的线性和角度尺寸的公差GB/T 13914-2002 冲压件尺寸公差GB/T 13915-92 冲压件角度公差GB/T 15055-2007 冲压件未注公差尺寸极限偏差JB/T 8930-1999 冲压工艺质量控制规范JB/T 4129-1999 冲压件毛刺高度JB/T 4381-1999 冲压剪切下料件未注公差尺寸的极限偏差GB/T 2828.1-2012 计数抽样检验程序第1部分:按接收质量限(AQL)检索的逐批检验抽样计划4.0 检验内容4.1板材4.1.1板材的选择严格按图纸要求选材。
4.1.2板材允许缺陷板材允许有个别轻微的擦伤、压痕、凹面、及清理痕迹,其深度不得超过板料厚度公差带的一半。
4.1.3板材的周边质量所有切割周边均需齐平、无尖角、利边、无毛刺、无裂纹、转角处应圆滑。
4.2冲压件尺寸公差 4.2.1冲压件未注尺寸公差图纸没有要求的(非配合)尺寸偏差按GB/T 15055—2007进行检验。
该标准分为四级(f、m、c、v),采用f级,表示为GB/T 15055-f,见表1。
当冲压零件为精密冲压件和冷挤压件时,该标准不适用。
应选用GB/T 1804-m(一般未注公差的线性和角度尺寸的公差)进行检验,见本标准3.10的表6。
注:对于0.5及0.5mm以下的尺寸应标公差。
4.2.2冲压件未注公差成形尺寸的极限偏差图纸没有要求的(非配合)尺寸偏差按GB/T 15055—2007 进行检验。
该标准分为四级(f、m、c、v),采用f级,表示为GB/T 15055-f,见表2。
钣金作业指导书

钣金作业指导书一、任务背景钣金作业是一项重要的创造工艺,用于创造各种金属制品,如汽车车身、电子设备外壳等。
为了确保钣金作业的质量和效率,制定一份详细的钣金作业指导书是必要的。
二、作业流程1. 材料准备- 根据设计要求,准备所需的钣金材料,如冷轧钢板、铝合金板等。
- 检查材料质量,确保无明显损伤、变形或者腐蚀。
2. 设计与加工- 根据产品设计图纸,确定钣金件的形状、尺寸和加工工艺。
- 使用CAD软件绘制钣金件的展开图,并进行材料利用率计算。
- 根据展开图,制定钣金件的切割、折弯和冲压工艺。
- 使用数控折弯机、冲床等设备进行加工,确保尺寸和形状的精确度。
3. 表面处理- 根据产品要求,进行表面处理,如喷涂、电镀、抛光等。
- 检查表面处理质量,确保无划痕、氧化或者脱落现象。
4. 装配与焊接- 根据产品要求,对钣金件进行装配,如螺栓连接、焊接等。
- 使用适当的焊接设备和焊接材料,确保焊缝的质量和强度。
- 进行焊接后的表面处理,如打磨、喷涂等。
5. 检验与质量控制- 对成品进行外观检查,确保无明显缺陷或者损伤。
- 进行尺寸测量,与设计要求进行比对。
- 进行功能性测试,确保产品的性能符合要求。
- 记录检验结果,进行质量控制和追溯。
三、安全注意事项1. 操作人员应穿戴好个人防护装备,如手套、护目镜等。
2. 在操作过程中,应注意机器设备的安全操作规程,避免意外事故的发生。
3. 使用化学药品时,应注意防护措施,避免对人体和环境造成伤害。
4. 遵守工作场所的安全规定,保持工作区域的整洁和有序。
四、常见问题及解决方法1. 钣金件加工过程中浮现尺寸偏差- 检查设备的精度和稳定性,确保设备正常运行。
- 检查加工工艺和刀具的选择,调整加工参数。
2. 钣金件表面浮现划痕或者氧化- 检查表面处理工艺和材料的选择,调整处理参数。
- 使用适当的保护措施,避免表面受到外界损伤。
3. 钣金件装配后浮现松动或者不匹配- 检查装配工艺和零件的尺寸,调整装配参数。
钣金冲压件进料检验作业指导书

德信诚培训网钣金冲压件进料检验作业指导书
1.0目的
为了规范我司进料检验作业程序以及更好的保证原物料的质量,提高公司产品质。
2.0适用范围
本指导书适用于我司所有的进料检验。
3.0作业步骤
3.1相关环节送检,品管根据《外来物品送检单》准备相应的检验工具
和检验资料。
3.2检验(检验步骤)
3.2.1对《外来物品送检单》的完整性进行确认,根据《外来物品送
检单》中的物料种类索要应的《材质证明》和《SGS报告》以及相应
供应商的检验记录;
3.2.2对物品进行检验,根据来料数量确定其抽样比例。
;
3.2.3根据工程资料和国家标准对原材料进行检验,首确认产品的材
质和料厚是否正确;
3.2.4对物品外观进行相应的检验,确定产品外观是否可满足要求;
3.2.5对产品的尺寸进行检验,确定产品尺寸是否符合图面要求;
3.2.6做好相应的检验记录,严格按照《进料检验/试验管理规定》做更多免费资料下载请进:好好学习社区。
钣金件检验作业指导书

钣金件检验作业指导书文件编号编制:刘桂强审核:批准:Xxxxxxxxxxxxxxx有限公司发放范围:车间、生产部、技术部、档案室各一份一、目的规范钣金结构件的检验标准,以使各过程的产品质量得以控制,保证本公司的产品质量,从而使我公司的产品让顾客满意。
二、适用范围本标准适用于各种钣金结构件的检验,图纸和技术文件并同使用。
当有冲突时,以技术规范和客户要求为准。
三、引用标准本标准的尺寸未注单位皆为mm,未注公差按以下国标IT13级执行GB/T1800.3-1998 极限与配合标准公差和基本偏差数值表GB/T1800.4 -1998 极限与配合标准公差等级和孔、轴的极限偏差表GB/1804-2000 一般公差未注公差的线性和角度尺寸的公差未注形位公差按GB/T1184 –1996 形状和位置公差未注公差值执行。
四、原材料检验标准1.金属材料1.1钣材厚度及质量应符合国标,采用的钣材需出示性能测试报告及厂商明。
1.2材料外观:平整无锈迹,无开裂与变形。
1.3 尺寸:按图纸或技术要求执行,本司未有的按现行国标执行。
2.塑粉2.1塑粉整批来料一致性良好,有出厂证明与检验报告,包含粉号、色号以及各项检验参数。
2.2试用后符合产品要求(包括颜色、光泽、流平性、附着力等)。
3通用五金件、紧固件3.1外观:表面无绣迹、无毛刺批锋,整批来料外观一致性良好。
3.2尺寸:按图纸与国标要求,重要尺寸零缺陷。
3.3性能:试装配与使用性能符合产品要求。
五、工序质量检验标准1.冲裁检验标准1.1对有可能造成伤害的尖角、棱边、粗糙要做去除毛刺处理。
1.2图纸中未明确标明之尖角(除特别注明外)均为R1.5。
1.3冲压加工所产生的毛刺,对于门板、面板等外露可见面应无明显凸起、凹陷、粗糙不平、划伤、锈蚀等缺陷。
1.4毛刺:冲裁后毛刺高L≤5%t(t为板厚)。
1.5划伤、刀痕:以用手触摸不刮手为合格,应≤0.1。
1.6平面公差度要求见表一。
钣金件检验指导书

钣金件检验指导书钣金件检验指导书1、钣金件检验目的:钣金件检验的目的是确保产品的质量符合预定的技术要求,以及系统化地记录产品在生产过程中的一致性和可追溯性。
2、检验前准备:2.1 检验设备和工具准备:- 钣金件检测设备(例如千斤顶、测量工具、表面检测工具等)- 钣金件检测工具(例如量规、卡尺、千分尺等)- 光源和显微镜(用于表面检验)- 实验室耗材(例如溶剂、清洁剂等)- 相关文件和标准2.2 检验人员准备:- 熟悉相关质量要求和检验方法的技术人员- 掌握钣金件检验工艺和流程的操作人员3、钣金件检验步骤:3.1 外观检验:- 检查钣金件的表面是否平整、无划痕、无擦痕等,确保外观符合要求- 使用光源和显微镜检查钣金件的表面是否存在凸起、凹陷或其他缺陷- 对钣金件进行视觉检查,确保涂层的均匀性和无起泡、脱落等问题3.2 尺寸检验:- 使用量规、卡尺、千分尺等工具测量钣金件的尺寸是否符合要求- 检查钣金件的平直度、垂直度、并进行相应的调整和修正- 对钣金件的孔洞和定位孔进行测量和校准,确保其位置和尺寸准确3.3 材质检验:- 使用化学分析仪器测试钣金件的材质成分是否符合要求- 进行金相显微镜观察,确保钣金件的晶粒结构符合要求- 进行硬度测量,确保钣金件的硬度值处于指定的范围内3.4 表面处理检验:- 对钣金件的表面处理进行视觉检查,确保处理效果符合要求- 使用表面粗糙度测试仪器对钣金件的表面进行粗糙度测试- 进行耐腐蚀性测试,确保钣金件的表面处理能够满足相应的要求4、检验记录和结果:在钣金件检验过程中,应记录检验日期、检验人员、检验步骤和结果等信息,以确保检验结果的可追溯性。
5、附件:本文档涉及的附件包括:- 钣金件检验记录表- 相关标准和规范文件- 实验室测试报告样本6、法律名词及注释:- 质量要求:产品制造商或客户对产品质量相关方面提出的要求,通常包括尺寸、材质、表面处理等。
- 检验方法:用于对钣金件进行质量检验的具体步骤和操作方式。
- 1、下载文档前请自行甄别文档内容的完整性,平台不提供额外的编辑、内容补充、找答案等附加服务。
- 2、"仅部分预览"的文档,不可在线预览部分如存在完整性等问题,可反馈申请退款(可完整预览的文档不适用该条件!)。
- 3、如文档侵犯您的权益,请联系客服反馈,我们会尽快为您处理(人工客服工作时间:9:00-18:30)。
钣金冷冲压检验作业指导书
发行版本:V1.0
发行日期:2010.12.1
实施日期:2010.12.1
归口治理部门:品质部
起草:审核:批准:
钣金冷冲压检验作业指导书
1、目的:
对钣金冷冲压件加工过程的监督及成品检验的要求。
2、适用范围:
本标准适用于恒鹏公司及其外协加工的钣金冷冲压件。
3、引用标准
GB/T 13916-2002 冲压件形状和位置未注公差
GB/T 1804-2000 一般公差_未注公差的线性和角度尺寸的公差
GB/T 13914-2002 冲压件尺寸公差
GB/T 13915-92 冲压件角度公差
GB/T 15055-2007 冲压件未注公差尺寸极限偏差
JB/T 8930-1999 冲压工艺质量操纵规范
JB/T 4129-1999 冲压件毛刺高度
JB/T 4381-1999 冲压剪切下料件未注公差尺寸的极限偏差
GB 2828—87 逐批检查计数抽样程序及抽样表(适用于连续批的检验)
4、检验内容
4.1板材
4.1.1板材的选择
严格按图纸要求选材。
4.1.2板材同意缺陷
板材同意有个不轻微的擦伤、压痕、凹面、及清理痕迹,其深度不得超过板料厚度公差带的一半。
4.1.3板材的周边质量
所有切割周边均需齐平、无尖角、利边、无毛刺、无裂纹、转角处应圆滑。
4.2冲压件尺寸公差
4.2.1冲压件未注尺寸公差
图纸没有要求的(非配合)尺寸偏差按GB/T 15055—2007进行检验。
该标准分为四级(f、m、c、v),采纳f级,表示为GB/T 15055—f,见表
1。
当冲压零件为周密冲压件和冷挤压件时,该标准不适用。
应选用GB/T 1804—m(一般未注公差的线性和角度尺寸的公差)进行检验,见本标准3.10的表6。
表1 冲裁件未注尺寸公差 mm
注:关于0.5及0.5mm以下的尺寸应标公差。
4.2.2冲压件未注公差成形尺寸的极限偏差
图纸没有要求的(非配合)尺寸偏差按GB/T 15055—2007 进行检验。
该标准分为四级(f、m、c、v),采纳f级,表示为GB/T 15055—f,见表2。
当冲压零件为周密冲压件和冷挤压件时,该标准不适用。
应选用GB/T 1804—m进行检验,见本标准3.10的表6
4.3孔距的偏差
图纸上有孔距公差要求的按图纸检验,没标注孔距公差的,孔距尺寸偏差按GB/T 1804—m进行,见本标准3.10中表6。
注:标注孔距偏差不是按线性尺寸偏差标注的,也不是按GB/T 1804执行的。
那个地点只有在未标注公差检验时才用到。
表2 冲压成形未注尺寸公差 mm。