2018年度人力资源与社会保障专题培训过程失效模式与后果分析PFMEA.doc
过程失效模式跟后果分析(PFMEA)(ppt61)中英文(2)

PFMEA is an output of the "Process Design and Development" phase of APQP
PFMEA是APQP中“过程设计和开发”阶段的 产物
2018/9/24
PFMEA
When do we do a PFMEA? 何时进行PFMEA?
It is derived from a DFMEA 在DFMEA之后进行
A PFMEA done solely to fill out a form and meet “requirements” is just an exercise 为了满足QS9000要求而填写PFMEA表格, 仅是练习而已
2018/9/24
PFMEA
When do we do a PFMEA? 何时进行PFMEA?
2018/9/24
PFMEA
Process FMEA 过程FMEA
PFMEA is focussed on the Product PFMEA 关注对产品的影响
P F M E A i s fo c u s s e d o n th e P R O D U C T . N a m e l y , h o w th e P R O CE S S c a n c a u s e fl a w s o r v a r i a t i o n i n th e P R O D U C T .
2018/9/24
PFMEA
When do we do a PFMEA? 何时进行PFMEA?
Do a PFMEA (or at least review the old one) if: 以下情况需进行PFMEA(或至少评审过去的PFMEA) : the process is new
pfmea过程失效模式与后果分析报告

通过深入分析,我们确定了导致这些失效的潜在原因,包 括设备老化、操作规程不完善、员工培训不足、原材料质 量控制不严格以及工艺参数设置不合理等。
对未来工作的建议和展望
改进措施建议
持续改进计划
未来研究方向
基于PFMEA的结果,我们提出了一系 列改进措施,包括更新设备、优化操 作规程、加强员工培训、严格控制原 材料质量以及调整工艺参数等。这些 措施旨在减少失效发生的风险,提高 生产过程的可靠性和稳定性。
为了确保改进措施的有效实施,我们 制定了持续改进计划。该计划包括定 期评估改进效果、监测潜在问题的出 现以及调整改进措施等。通过持续改 进,我们期望能够不断优化生产过程 ,提高产品质量和客户满意度。
在报告的最后,我们提出了一些未来 可能的研究方向。这些方向包括进一 步探索失效模式与潜在原因之间的关 系、研究新的失效分析方法以及开发 更加智能化的失效预测模型等。通过 深入研究,我们期望能够为企业的持 续改进提供更有力的支持。
失效模式
汽车发动机性能下降
后果
影响汽车动力性能,可能导致油耗增加、排放超标
潜在原因
制造过程中材料、工艺、设备等方面的问题
风险评估
高风险,需采取措施进行改进
案例二:电子产品制造过程的PFMEA分析
失效模式
电子元件短路
潜在原因
制造过程中元件组装、焊 接等环节出现问题
后果
产品功能失效,可能引发 安全事故
提前发现和预防问
题
PFMEA是一种预防性的质量工具 ,它通过提前发现和预防潜在的 问题,减少后期修改和返工的成 本。
优化设计和过程
PFMEA分析结果可以为设计和过 程的改进提供指导,帮助企业优 化产品和过程的性能、可靠性和 安全性。
过程失效模式及后果分析PFMEA中英文

PFMEA
How do we do a PFMEA?
A Summary 怎样进行PFMEA?提要
Assess, 评估 the severity of the effect (S) 后果的严重程度
PFMEA
何谓PFMEA 何时作PFMEA 何人作PFMEA
如何作PFMEA
16步工作步骤
Process FMEA 过程FMEA
PFMEA
How do we do a PFMEA?
A Summary 怎样进行PFMEA?提要
Assemble the cross-functional PFMEA team 组建跨部门PFMEA小组
PFMEA
Process Failure Mode and Effects Analysis
过程失效模式及后果分析(PFMEA)
PFMEA PFMEA
陶国
PFMEA Proprietary Information 专有信息
Your FMEA (Control Plan, Process Capability, etc.) may be considered proprietary and should not be shared with anyone outside the division without first consulting your management. FMEA (控制计划、过程能力等) 可视为专有信息,在未事先 征 得管理部门同意之前,不得向部门以外的任何人透露。 this includes the sharing of information with your customer 也不得向顾客透露有关信息。
PFMEA过程失效模式及后果分析

PFMEA过程失效模式及后果分析PFMEA(Process Failure Mode and Effects Analysis)过程失效模式及后果分析是一种常用的质量管理工具,用于评估和改进产品制造过程中的潜在问题和风险。
它旨在预测和预防可能导致产品失效的过程步骤。
1.确定过程步骤:首先,识别和定义产品制造过程中的每个关键步骤,包括原材料采购、加工、装配、测试等。
2.确定失效模式:对于每个过程步骤,识别可能导致失效的模式。
失效模式可以是设备故障、人为错误、材料质量问题等。
3.评估失效后果:对于每个失效模式,评估其可能导致的后果和影响。
后果可以涉及到产品质量问题、安全风险、客户满意度等。
4.定义风险优先级:根据失效模式的严重性、发生频率和检测能力,为每个失效模式分配一个风险优先级。
这可以帮助制定合理的风险控制策略。
5.制定改进计划:对于评估出的高优先级失效模式,制定相应的改进计划和控制措施。
这可能包括优化生产工艺、提供培训和教育、改进设备维护等。
6.实施和监控措施:执行改进计划,并监控其有效性。
定期对PFMEA进行更新,以反映过程改进和新的风险评估。
通过实施PFMEA,可以有效地识别和消除潜在的制造过程问题,并降低产品质量问题的风险。
下面以汽车制造业为例,具体分析PFMEA的应用。
在汽车制造过程中,每个制造步骤都可能存在潜在的失效模式。
例如,原材料采购环节可能存在材料质量问题的风险,加工环节可能存在操作错误或设备故障的风险,装配环节可能存在组装错误或安装不良的风险,测试环节可能存在测试不准确或设备故障的风险。
针对这些潜在问题,可以使用PFMEA来识别并评估其风险。
例如,在加工环节,识别可能的失效模式可能包括不正确的参数设置、设备故障、操作错误等。
然后,评估这些失效模式可能导致的后果和影响,如产品偏差、生产延误、设备故障等。
根据评估结果,确定失效模式的风险优先级,以便制定相应的改进计划和控制措施。
例如,对于评估为高风险的加工失效模式,可以采取以下改进措施:加强对操作员的培训和教育,确保他们正确操作设备和设置参数;增加设备维护和保养频率,以减少设备故障的风险;实施过程监控和自动化控制,以确保稳定的生产环境。
过程失效模式及后果分析管理办法

过程失效模式及后果分析管理办法过程失效模式及后果分析(Process Failure Modes and Effects Analysis,简称PFMEA),是一种常用于管理过程风险和改进的工具。
PFMEA通过对过程中可能发生的失效模式及其后果进行分析,提前识别出潜在问题,并采取相应措施降低风险。
下面将介绍PFMEA的管理办法。
一、PFMEA的管理目标PFMEA的管理目标是识别和分析过程中的失效模式及其潜在后果,评估失效发生的概率和影响程度,并制定相应的预防控制措施,降低风险。
二、PFMEA的管理步骤1.选择适当的团队成员:PFMEA的分析需要跨越多个职能领域,因此需要选择适当的团队成员,包括具有相关专业知识和经验的人员。
2.确定过程:明确要分析的过程范围和目标,包括过程流程、输入和输出等。
3.识别失效模式:团队成员通过头脑风暴和过程分析,识别可能导致过程失效的因素。
失效模式可以是物理性的、功能性的、行为性的等。
4.评估失效影响程度:对每个失效模式,评估其对过程和最终产品或服务的影响程度,包括安全性、质量、交付时间、成本等方面。
5.确定失效发生的概率:评估每个失效模式发生的概率,包括概率的频率、可能性等。
6.评估现有控制措施:评估当前过程中已存在的控制措施,对失效模式的控制程度,包括检验、测试等。
7.制定改进措施:根据评估结果,确定需要改进的控制措施,包括预防措施和检测措施,以降低失效发生的概率和影响程度。
8.实施改进措施:制定实施改进措施的计划,并跟踪监控改进效果。
9.更新PFMEA:根据实施改进措施的结果,修订和更新PFMEA,并确保团队成员了解改进措施的目标和具体要求。
三、PFMEA的管理原则1.整体团队参与:PFMEA需要全员参与,涉及到的问题通常跨越多个职能领域,需要充分调动团队的智慧和经验。
2.系统性分析:PFMEA需要从系统层面进行分析,识别可能的失效模式和其后果,并考虑多种因素对失效的影响。
过程失效模式及后果分析-教程
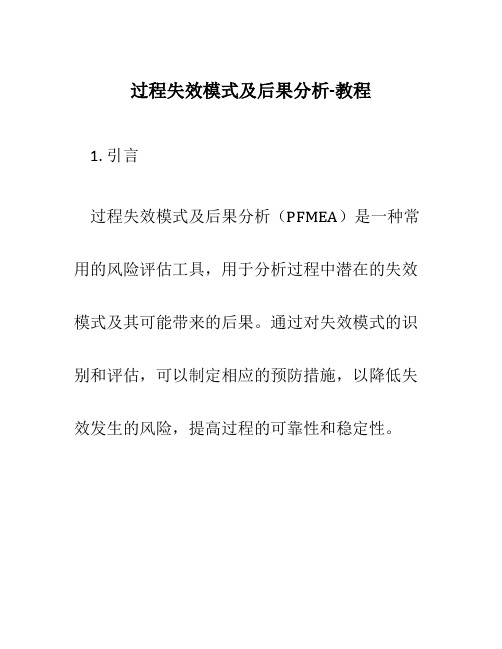
过程失效模式及后果分析-教程1. 引言过程失效模式及后果分析(PFMEA)是一种常用的风险评估工具,用于分析过程中潜在的失效模式及其可能带来的后果。
通过对失效模式的识别和评估,可以制定相应的预防措施,以降低失效发生的风险,提高过程的可靠性和稳定性。
本教程将介绍PFMEA的基本概念、步骤和应用方法,帮助读者了解如何进行过程失效模式及后果分析。
2. PFMEA的基本概念2.1 过程失效模式过程失效模式是指发生在特定过程中的潜在失效形式。
它可以是机械故障、工艺不稳定、材料质量问题等各种各样的问题,可能导致产品或服务无法达到预期的功能要求。
2.2 后果分析后果分析是对失效模式引起的后果进行评估和分析。
它包括两个方面的内容:失效后果的严重性评估和失效后果的概率评估。
严重性评估用于判断失效对产品或服务的影响程度,概率评估用于评估失效产生的频率或概率。
3. PFMEA的步骤PFMEA主要包括以下步骤:3.1 选择分析对象选择需要进行PFMEA分析的过程或系统,确定所要分析的范围和目标。
3.2 建立团队建立一个跨部门的团队,包括相关的设计、生产和质量控制人员。
团队成员应具备相关的知识和经验,以能够准确地分析和评估失效模式及其后果。
3.3 列出过程步骤对所选过程进行详细的步骤分解,将整个过程拆分为多个子过程或操作步骤。
3.4 识别失效模式对每个步骤识别可能存在的失效模式,包括机械失效、材料问题、环境因素等。
3.5 评估失效后果对每个失效模式评估其可能带来的后果,包括严重性和概率评估。
根据经验和数据进行评估,各团队成员提供专业意见。
3.6 优先级排序根据失效后果的严重性和概率进行排序,确定重要性较高的失效模式。
3.7 制定预防措施对于重要性较高的失效模式,制定相应的预防措施,包括改进设计、改变工艺、提高操作规范等。
3.8 实施并跟踪将制定的预防措施实施到实际生产过程中,并定期进行跟踪和评估,以确保措施的有效性和可操作性。
PFMEA过程失效模式与后果分析报告
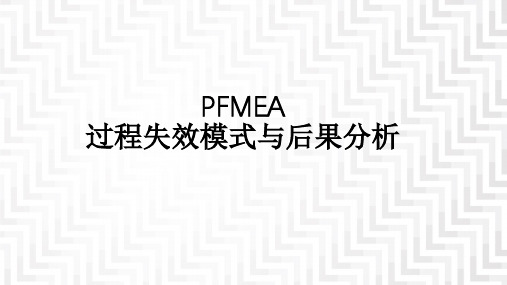
让我们共同进步
知识回顾 Knowledge Review
失效:在规定条件下(环境、操作、时间),不
关键参数
能完成既定功能或产品参数值和不能维持在规定 的上下限之间,以及在工作范围内导致零组件的
失效
规定条件无法达到要求或者规格
ห้องสมุดไป่ตู้
破裂卡死等损坏现象。 严重度(S):指一给定失效模式最严重的影响
严重度(S) 失效模式对后果的影响,越严重越需要通过设计来改善
后果的级别,是单一的FMEA范围内的相对定级 结果。严重度数值的降低只有通过设计更改或重
有些“早知道”是必需的 有些“就不会”是不允许发生的
PFEMA 是对制程中的风险点进行提前识别并预防以致风险降低到最小。 PFEMA 是QCP 的前提之一。 一般PFEMA需要在产品大批量生产前完成, 并在后期逐步更新完善。
PFEMA的用法-关键步骤
确定对象及需 求
识别潜在的失 效模式及后果
S
识别失效原因
探测度(D):指在零部件离开制造工序或装配 之前,利用第二种现行过程控制方法找出失效起 因/机理过程缺陷或后序发生的失效模式的可能性 的评价指标;或者用第三种过程控制方法找出后 序发生的失效模式的可能性的评价指标。 风险优先数(RPN):指严重度数(S)和频度
数(O)及不易探测度数(D)三项数字之乘积。
FMEA的分类
FMEA又根据产品故障可能产生的环节:设计、 制造过程、使用、承包商(供应商)以及服务可 细分为: 1.DFMEA: 设计FMEA
2.PFMFA: 过程FMEA
3.MFMEA:设备FMEA
4.SFMEA: 体系 FEMA
针对系统 及子系统
针对设备和 设备部件
2018年度人力资源与社会保障专题培训过程失效模式与后果分析PFMEA.doc

2018年度人力资源与社会保障专题培训过程失效模式与后果分析-PFMEA前言:近年来,发生过很多起汽车召回的事件,这包括美国的克莱斯勒、福特、通用三大汽车公司,日本的丰田汽车等知名企业都有召回的案例,我们国家也制定和发布了《缺陷汽车产品召回管理条例》,对缺陷汽车的召回要求更高、更规范化。
在这些召回事件中,绝大多数都是由于设计、零部件或材料上的缺陷可能导致对顾客的安全后果,这些召回对企业的经济损失是相当大的,甚至会导致企业破产,因此,IATF标准要求汽车零件制造商必须要作FMEA分析,尽可能的克服和减少缺陷的发生。
本课程将系统地讲解PFMEA的内容、要求、信息流、实施步骤和方法;包括过程流程图、PFMEA、特性矩阵表、控制计划等工具,帮助学员了解通过实施FMEA的过程,掌握产品特性内部、产品特性与过程特性、DFMEA和PFMEA、流程图和PFMEA、PFMEA和控制计划之间的相互关联,解决过程设计可能出现的问题,在产品实现过程的前期确保失效模式得到考虑并实现失效的控制和预防。
课程信息:【培训日期】2018年6月2日(周六)【培训时间】9:00—16:00(1天)【培训地点】吴江经济技术开发区人力资源服务中心(吴江经济技术开发区云梨路1028号)【培训对象】制造工程师、质量工程师、SQE、设计工程师、和其他直接负责过程开发与过程开发管理人员。
【培训费用】会员单位扣10点/人,非会单位900元/人次(包括教材、餐饮、发票等)。
【备注】报名人员因故不能参加者需提前一天告知,无故缺席者点数照扣,谢绝空降。
课程大纲:⏹FMEA 概述●FMEA的背景与历史●FMEA与可靠性、FMEA与风险分析●FMEA的定义●FMEA的种类: SFMEA, DFMEA, PFMEA●FMEA小组●DFMEA与PFMEA的关联●PFMEA开发的时机●FMEA的基本步骤:AIAG与VDA的不同描述⏹PFMEA的输入●过程流程图●特性矩阵表●过程流程图与PFMEA的关系●PFMEA的两个假设:与产品设计和供方的关系●宏观流程图与微观流程图⏹练习1PFMEA●PFMEA表格、表头解释●过程的功能与要求:条件要求、结果要求、后果要求●失效模式开发:与功能/要求的关系、失效模式的定义与标准化、失效模式的充分性●失效后果分析:与失效链的关系、与DFMEA的关系、与专业知识的关系、与相关的失效模式的关系●严重度评价:◆安全法规、基本功能和次要功能、感官功能的理解◆“对顾客的影响”“对制造的影响”的差异与使用◆质量风险、交付风险、成本风险◆AIAG、VDA、PSA不同的评价准则◆贝尔缺陷分级原则●级别:特殊特性练习2:小组发表与培训师讲评⏹PFMEA风险分析●潜在原因分析:与门/或门、与供应商质量的关系、常见的错误描述方式、原因的层次与数量、PFMEA是否存在SFMEA?●练习3:原因分析●预防性控制措施开发:与发生率(频度)评价的关联、“现行”的含义、与制造设计规范的关联、常见的过程控制措施(防错、DOE……)●探测性控制措施开发:探测对象(失效模式还是原因)、检验与防错●频度分析:经验数据域频度的关系、准则的理解,“1”的理解●探测度分析:检验的时机与手段、准则的理解、“1”的理解练习4:控制措施、频度、探测度分析、RPN⏹PFMEA风险控制/改进●风险控制原则●多方位风险分析●改进措施与SOD评价●动态管理●练习5:继续完成改进措施,或者在给出的PFMEA中找错。
过程失效模式及后果分析
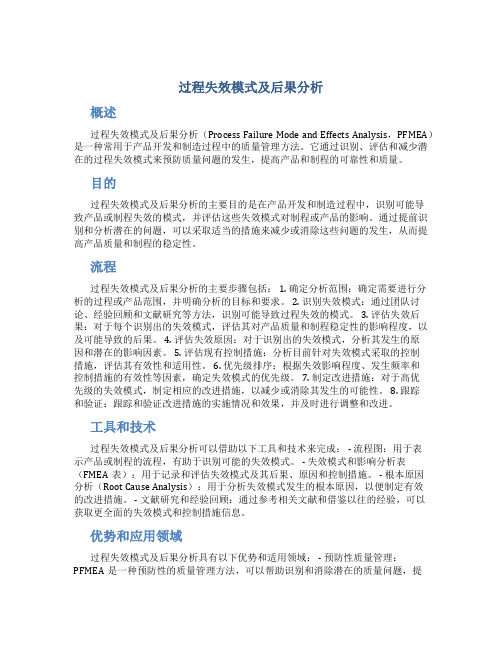
过程失效模式及后果分析概述过程失效模式及后果分析(Process Failure Mode and Effects Analysis,PFMEA)是一种常用于产品开发和制造过程中的质量管理方法。
它通过识别、评估和减少潜在的过程失效模式来预防质量问题的发生,提高产品和制程的可靠性和质量。
目的过程失效模式及后果分析的主要目的是在产品开发和制造过程中,识别可能导致产品或制程失效的模式,并评估这些失效模式对制程或产品的影响。
通过提前识别和分析潜在的问题,可以采取适当的措施来减少或消除这些问题的发生,从而提高产品质量和制程的稳定性。
流程过程失效模式及后果分析的主要步骤包括: 1. 确定分析范围:确定需要进行分析的过程或产品范围,并明确分析的目标和要求。
2. 识别失效模式:通过团队讨论、经验回顾和文献研究等方法,识别可能导致过程失效的模式。
3. 评估失效后果:对于每个识别出的失效模式,评估其对产品质量和制程稳定性的影响程度,以及可能导致的后果。
4. 评估失效原因:对于识别出的失效模式,分析其发生的原因和潜在的影响因素。
5. 评估现有控制措施:分析目前针对失效模式采取的控制措施,评估其有效性和适用性。
6. 优先级排序:根据失效影响程度、发生频率和控制措施的有效性等因素,确定失效模式的优先级。
7. 制定改进措施:对于高优先级的失效模式,制定相应的改进措施,以减少或消除其发生的可能性。
8. 跟踪和验证:跟踪和验证改进措施的实施情况和效果,并及时进行调整和改进。
工具和技术过程失效模式及后果分析可以借助以下工具和技术来完成: - 流程图:用于表示产品或制程的流程,有助于识别可能的失效模式。
- 失效模式和影响分析表(FMEA表):用于记录和评估失效模式及其后果、原因和控制措施。
- 根本原因分析(Root Cause Analysis):用于分析失效模式发生的根本原因,以便制定有效的改进措施。
- 文献研究和经验回顾:通过参考相关文献和借鉴以往的经验,可以获取更全面的失效模式和控制措施信息。
过程失效模式及后果分析(PFMEA)
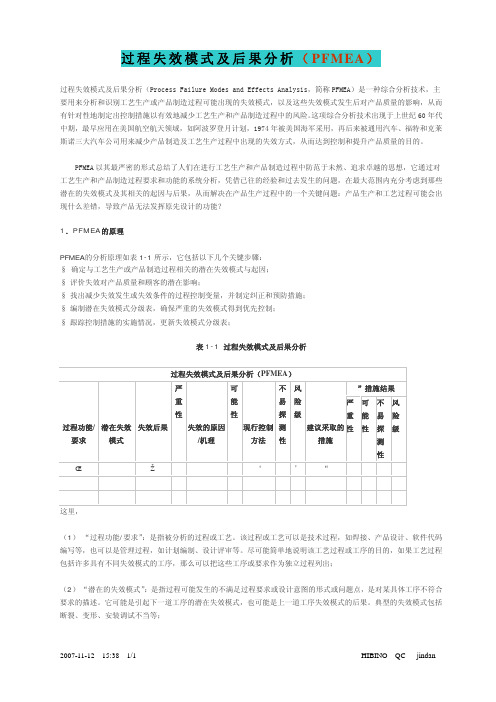
过程失效模式及后果分析(PFMEA)过程失效模式及后果分析(Process Failure Modes and Effects Analysis,简称PFMEA)是一种综合分析技术,主要用来分析和识别工艺生产或产品制造过程可能出现的失效模式,以及这些失效模式发生后对产品质量的影响,从而有针对性地制定出控制措施以有效地减少工艺生产和产品制造过程中的风险。
这项综合分析技术出现于上世纪60年代中期,最早应用在美国航空航天领域,如阿波罗登月计划,1974年被美国海军采用,再后来被通用汽车、福特和克莱斯诺三大汽车公司用来减少产品制造及工艺生产过程中出现的失效方式,从而达到控制和提升产品质量的目的。
PFMEA以其最严密的形式总结了人们在进行工艺生产和产品制造过程中防范于未然、追求卓越的思想,它通过对工艺生产和产品制造过程要求和功能的系统分析,凭借已往的经验和过去发生的问题,在最大范围内充分考虑到那些潜在的失效模式及其相关的起因与后果,从而解决在产品生产过程中的一个关键问题:产品生产和工艺过程可能会出现什么差错,导致产品无法发挥原先设计的功能?1.PFMEA的原理PFMEA的分析原理如表1-1所示,它包括以下几个关键步骤:§确定与工艺生产或产品制造过程相关的潜在失效模式与起因;§评价失效对产品质量和顾客的潜在影响;§找出减少失效发生或失效条件的过程控制变量,并制定纠正和预防措施;§编制潜在失效模式分级表,确保严重的失效模式得到优先控制;§跟踪控制措施的实施情况,更新失效模式分级表;表1-1 过程失效模式及后果分析过程失效模式及后果分析(PFMEA)”措施结果过程功能/要求潜在失效模式失效后果严重性失效的原因/机理可能性现行控制方法不易探测性风险级建议采取的措施严重性可能性不易探测性风险级ŒŽ‘ ’“这里,(1)“过程功能/要求”:是指被分析的过程或工艺。
该过程或工艺可以是技术过程,如焊接、产品设计、软件代码编写等,也可以是管理过程,如计划编制、设计评审等。
过程失效模式及后果分析中英文
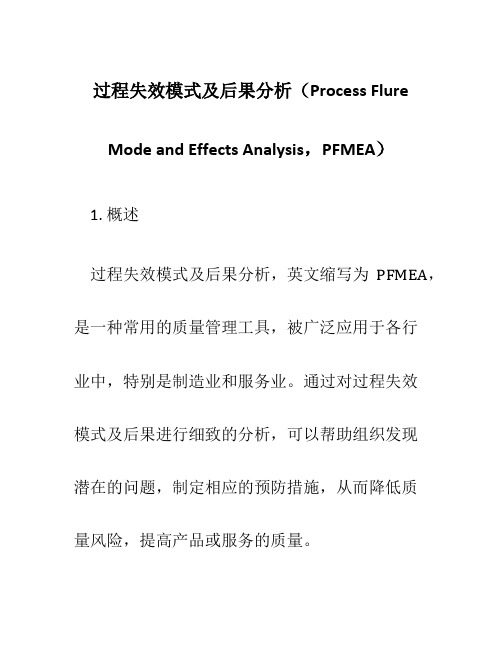
过程失效模式及后果分析(Process FlureMode and Effects Analysis,PFMEA)1. 概述过程失效模式及后果分析,英文缩写为PFMEA,是一种常用的质量管理工具,被广泛应用于各行业中,特别是制造业和服务业。
通过对过程失效模式及后果进行细致的分析,可以帮助组织发现潜在的问题,制定相应的预防措施,从而降低质量风险,提高产品或服务的质量。
2. 过程失效模式及后果分析的流程过程失效模式及后果分析通常包括以下几个步骤:2.1 确定分析范围在进行过程失效模式及后果分析之前,首先需要明确分析范围。
确定要分析的具体过程或工作流程,并明确分析的目的和依据。
2.2 制定团队选择一支多学科的团队,包括工程师、技术专家、质量专员等相关人员。
团队成员的经验和专业知识对于分析的质量起到关键作用。
2.3 识别失效模式团队成员集体讨论,识别出可能会发生的过程失效模式。
失效模式可以是过程中的错误、故障、缺陷等。
根据每个失效模式,评估其可能导致的后果。
后果可以是质量问题、安全问题、环境问题等。
2.5 评估失效严重性根据失效后果的严重程度,对每个失效模式进行评估。
一般采用定性或定量的方法来评估失效严重性,如风险矩阵法、风险优先数法等。
对每个失效模式,识别出其可能的原因。
原因可以是人、机、料、法、环的问题。
2.7 评估失效频率根据失效原因的发生频率,对每个失效模式进行评估。
评估失效频率有助于确定应对措施的优先级。
2.8 制定预防措施通过分析失效模式、后果、严重性、原因和频率,制定相应的预防措施。
预防措施可以是人员培训、工艺改进、设备维护等。
2.9 实施和跟踪将预防措施落实到实际操作中,并对其进行跟踪和监控,确保其有效性。
3. 过程失效模式及后果分析的优点过程失效模式及后果分析具有以下几个优点:3.1 早期发现问题通过对过程失效模式及后果进行分析,可以在产品或服务开发的早期阶段发现潜在的问题,从而避免问题进一步扩大和影响产品或服务质量。
PFMEA过程失效模式及后果分析
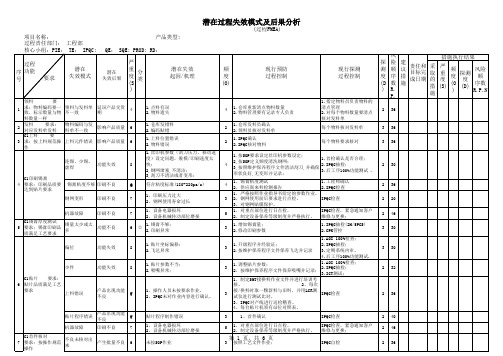
第 1 页,共 6 页
3 按照工艺文件作业;
IPQC检查,紧急通知客户 维修与更换;
IPQC自检
风
措施执行结果
探 测 度 (D )
险 顺 序 数 R. P.
建 议 措 施
责任和 采 目标完 取 成日期 的
措 施
严 重 度 (S)
频 度 (O )
探测 度 (D)
风险 顺 序数 R.P.N
2 36
3 36 3 36
领料
要
1
求:物料编码要一 领料与发料单 致,标示数量与物 不一致
延误产品交货 期
4
料数量一样
2
发料 要求: 对应发料单发料
物料编码与发 料单不一致
影响产品质量
6
C1上料 要
3 求:按上料规范操 上料元件错误 影响产品质量 6
作
连锡、少锡、 虚焊
功能失效
8
C1印刷锡膏
4 要求:印刷品质要 锡膏粘度不够 印刷不良
钢网变形
印刷不良
7
使用前未点检
1.接插件未防护; 2.作业操作失误;
1.摆放不按要求 2.重叠
1.上料位置错误 2.物料错误 1.丝印机参数(刮刀压力,移动速 度)设定问题,脱模/印刷速度太 快; 2,钢网堵塞,不清洁; 3,刮刀不清洁或者变形; 符合粘度标准(180-220pa/s)
1、印刷压力过大 2、钢网使用寿命过长
炉温设定错误
板未放到位 1、板与板叠放产生撞件 2、取放板时板跌落地面引起 3、PCB摆放错误 现场管理不到位 1、现场“5S”未做好 2.物品未标示 未执行工艺要求。 不良位置没有标识。
现场管理不到位 修理技术欠孰练 不按作业规范操作
PFMEA过程失效模式及后果分析
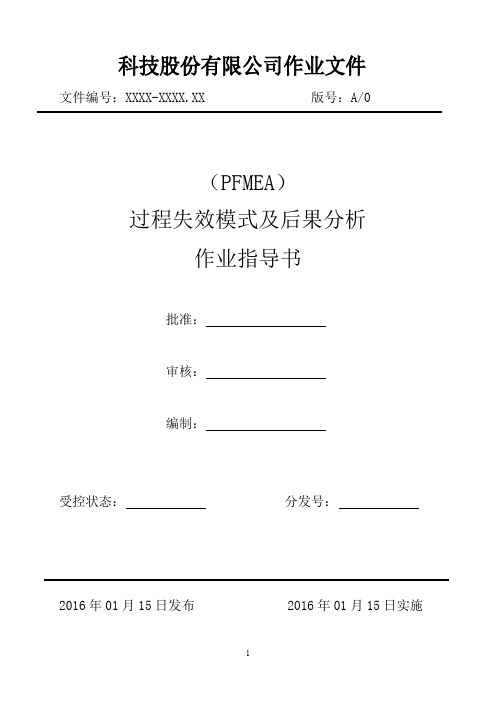
科技股份有限公司作业文件文件编号:XXXX-XXXX.XX 版号:A/0(PFMEA)过程失效模式及后果分析作业指导书批准:审核:编制:受控状态:分发号:2016年01月15日发布2016年01月15日实施过程潜在失效模式及后果分析作业指导书(PFMEA)XXXX-XXXX.XX1目的过程潜在失效模式及后果分析,简称PFMEA。
是一种信赖度分析的工具,可以描述为一组系统化的活动,是对确定产品/过程必须做哪些事情才能使顾客满意这一过程的补充。
其目的是:(a)并评价产品/过程中的潜在失效以及该失效的后果;(b)确定能够消除或减少潜在失效发生机会的措施;(c)将全部过程形成文件。
2范围:适用于公司用于零组件的所有新产品/过程的样品试制和批量生产。
适用于过程设计的风险性及后果的分析;适用于过程重复,周期性永不间断的改进分析。
3术语和定义:1)PFMEA:指Process Failure Mode and Effects Analysis(过程失效模式及后果分析)的英文简称。
由负责制造/装配的工程师/小组主要采用的一种分析技术,用以最大限度地保证各种潜在的失效模式及其相关的起因/机理已得到充分的考虑和论述。
2)失效:在规定条件下(环境、操作、时间),不能完成既定功能或产品参数值和不能维持在规定的上下限之间,以及在工作范围内导致零组件的破裂卡死等损坏现象。
3)严重度(S):指一给定失效模式最严重的影响后果的级别,是单一的PFMEA范围内的相对定级结果。
严重度数值的降低只有通过设计更改或重新设计才能够实现。
4)频度(O):指某一特定的起因/机理发生的可能发生,描述出现的可能性的级别数具有相对意义,但不是绝对的。
5)探测度(D):指在零部件离开制造工序或装配之前,利用第二种现行过程控制方法找出失效起因/机理过程缺陷或后序发生的失效模式的可能性的评价指标;或者用第三种过程控制方法找出后序发生的失效模式的可能性的评价指标。
2018.6.14潜在失效模式及后果分析(PFMEA)

模式及后果分析
FMEA号码: 联系电话: 最新修改日期:
称:
寇卫平
建议的措施
负责人/部门/ 计划完成日期
采取的措施
S
O
D
RPN
无 无 无 无 每年不定期抽样进行第三方检测 无 无 定人进行领料,领料时双方100%核对 生产部 按烘料作业指导书设定烘料时间和温 生产部 度 无 1以生产样件工艺参数为准,更 1锁定生产样件成型工艺参数,2操作 技术部/生产部/ 新工艺参数表,且锁定。2操作 员100%检查,3巡检每2H一次进行抽查 品质部 员100%检查,3巡检每2H一次进 行抽查 1以生产样件工艺参数为准,更 1锁定生产样件成型工艺参数,2操作 技术部/生产部/ 新工艺参数表,且锁定。2操作 员100%检查,3巡检每2H一次进行抽查 品质部 员100%检查,3巡检每2H一次进 行抽查 1以生产样件工艺参数为准,更 1锁定生产样件成型工艺参数,2操作 技术部/生产部/ 新工艺参数表,且锁定。2操作 员100%检查,3巡检每2H一次进行抽查 品质部 员100%检查,3巡检每2H一次进 行抽查 定人进行领料,领料时双方 100%核对 实施烘料记录 2 6 1 1 2 3 4 18 质量部 每年不定期抽样进行第三方检测 7 2 2 28
胶口设计不合理 冷却时间不够 浇口设计不合理 顶出受力不平衡 胶口设计不合理 注射压力偏小 顶出受力不平衡 注塑压力过大 保压压力过大 C 注射时间过长 C 注射时间不足 检验标准认识不足 未检验 检验标准认识不足 未检验 B 成型工艺参数未调试好 C 成型工艺参数未调试好 B 操作工漏装
4
对模具做模流分析,选择合适位置、形状、大小 的胶口
6
2
3
30
仓库实行严格先进先出管理 做限高标识限高 必须持证上岗 制定新的库位标识 更换新的库位标识 无 增加检验人员 无 增加检验人员 无 生产部
过程失效模式及后果分析模板(PFMEA)

潜在失效模式
严
潜在失效后果
重 度
级 别
S
潜在失效原因机理
频 度 O
现行控制
探 测 度 D
R P N
建议采取的措施
责任人 完成日期
措施结果 验证 S O D RPN
长度超出上限 下限 报废
4
员工计算失误
4
员工计算失误
6 首件检验 2 首件检验
板材开裂
2
折弯
外型扭曲
报废 报废
4
周转/搬运碰到
XXX 2019/3/2 XXX 2019/3/2 XXX 2019/3/2 XXX 2019/3/2 XXX 2019/3/6 XXX 2019/3/6 XXX 2019/3/6 XXX 2019/3/6 XXX 2019/3/6 XXX 2019/3/7 XXX 2019/3/7 XXX 2019/3/9 XXX 2019/3/9 XXX 2019/3/9
4
周转/搬运碰到
4 巡检 1次/2hr 2 巡检 1次/2hr
孔径规格不符 影响装配
8
钻孔设备精度不够 2 巡检 1次/2hr
3
钻孔 尺寸超差
影响装配
7
钻头定位不准
2 首件检验
位置不对中心 影响装配
7
钻头定位不准
2 首件检验
焊渣飞溅
影响外观
设备调试不良
3 巡检 1次/2hr
3
毛刺未及时磨掉
4 巡检 1次/2hr
过程失效模式及后果分析(PFMEA)
Process Failure Modes and Effects Analysis
产品名称: XXXXXXXXXXXXXXX 小组成员: XXX(开发)、XXX(生产)、XX(品质)、XXX(技术)…
PFMEA 过程失效和结果分析

13
PFMEA 表格模版举例 表格模版举例
14
过程失效的潜在原因
• 漏操作 • 误加工 • 错误的安装 • 遗失零备件 • 备件错用 • 错误的处理半成品 • 错误的操作 • 错误的调整 •设备润滑不当 设备润滑不当 •使用错误的工具
• 差的控制程序 • 不正确的设备维护 • 错误的配方 • 老化 • 缺乏安全 • 错误的机器设置 • 执行错误的程序 • 环境 • 连接错误 差的FMEA系统 • 差的 系统
6
PFMEA 流程
实施行动计划降低 4 RPN
3 确定 S/O/D 的分级表
CI
D
5 检查并促进行
计算RPN并制
定优先计划
动计划的实施
只要一个流程没有从生产 线上退出, 线上退出,PFMEA 将永远 不会结束 6 执行可控的
C
2 绘制流程
图
1
标准程序
组队
7 改进后再次评
P
估 RPNs
A
识别失效模式: 识别失效模式 产品未能符合设计的意图或过程的要求 识别潜在要因 : 应按失效为何发生的迹象来确定,按照可纠正或可控制的情形来描述 识别潜在后果: 识别潜在后果:如果失效模式没有预防或纠正而导致顾客察觉的失效模式后果来定义
19
PFMEA 是 ISO9001 的一部分
Process Failure Mode and Effects Analysis
Statistical Process Control Quality System Analysis
Measurement System Analysis
ISO-9001 QS-9000
•操作步骤是否重复还是无顺序? •这些步骤是否频繁产生失误? •是否有循环的返工?
PFMEA过程失效模式及后果分析

PFMEA过程失效模式及后果分析PFMEA(Process Failure Mode and Effects Analysis)是一种通过系统地识别和评估潜在的失效模式及其后果来预防产品和过程问题的方法。
它有助于组织在设计和开发阶段就发现并解决潜在的问题,从而提高产品质量和生产效率。
在这篇文章中,我们将重点讨论PFMEA过程中的失效模式及其后果分析。
失效模式是指导致产品或过程失效的特定原因或机制。
它可以是由于设计缺陷、材料问题、加工误差、操作失误等引起的。
失效模式常常以不同的方式出现,在不同的环境下可能会有不同的后果。
在进行PFMEA过程中,首先需要识别潜在的失效模式。
这可能涉及到对产品、过程和相关文档的仔细研究,以了解可能存在的问题。
接下来,需要对每个失效模式的影响进行评估,这也就是后果分析。
后果分析可以帮助确定失效对产品质量、生产效率和安全性等方面造成的影响,从而决定需要采取的预防措施。
在进行PFMEA过程失效模式及后果分析时,以下是一些常见的失效模式和其可能的后果:1.设计缺陷:-可能的后果:产品性能不达标、产品寿命缩短、安全隐患、产品被召回等-预防措施:加强设计评审、使用可靠的设计工具、进行模拟测试等2.材料问题:-可能的后果:产品强度不足、耐腐蚀性差、产品寿命缩短等-预防措施:严格选择、测试和审查材料供应商、加强入库检查等3.加工误差:-可能的后果:产品尺寸偏差、表面质量不良、装配困难等-预防措施:加强生产工艺控制、使用先进的制造设备、严格执行质量标准等4.操作失误:-可能的后果:生产过程中出现错误、设备损坏、人员伤亡等-预防措施:提供员工培训、实施作业规程、设立安全警示标志等除了上述提到的失效模式和后果,还有许多其他可能的情况需要被考虑和分析。
在进行PFMEA过程中,团队成员需要全面了解产品和过程,积极参与讨论和决策,以确保有效识别和评估潜在的问题。
此外,通过对失效模式及后果进行分析,团队还可以确定应对措施的优先级和实施计划。
过程潜在失效模式及后果分析--PFMEA教材
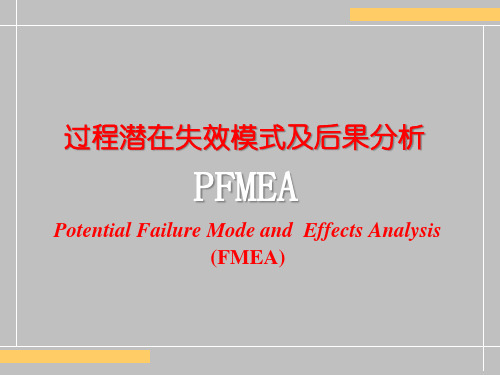
摘要/练习
1.请制定各工序流程图 2.组成小组并确定其成员 3.总结PFMEA的好处
过程FMEA的開發
典型的PFMEA?
过程 潜在 功能 失效 要求 模式
清除
板面
粉尘/ 板
污迹, 防止
面
粉尘 氧
造成 电测
化
短路
潜在
失效 后果 分析
严 重 度
级 别
潜在的 频 失效原因 度
现行过程/ 探 风险 建议 责任
措施结果
预防控制 测 顺序 的措 及完
度 数 施 成日 采取 严 频 探 风险
期
的措 施
重 度
度
测 顺序 度数
4
影 响 外 观
烘干温度 低
3 烘干温度 6 控制在 80-90℃
传速度太快
传送速度 2 控制在2.0- 3
3.5m/min
水洗缸受
水洗缸
污染
3
更换:1 4
次/班
过程潜在失效模式及后果分析
核心小组: 蔡应明、文钊、汤越宁、余胜华、王利波、杨奎、单秀真、周平、何志毅、杨日权、宫岱岳、魏轲
項目
功能
潛在的 失效模式
潛在的 失效后果
嚴 重級 度別 S
潛在失效的 起因/機理
成型
尺寸不良
将烘好的料,通过
注塑设备、模具,
在一定的工艺参
数下转化成有一
定形状的塑件
功能不良,影响 8 装配
成型压力过大/小
过程潜在失效模式及后果分析
PFMEA
Potential Failure Mode and Effects Analysis (FMEA)
课程目的
学习 FMEA 的好处 让你的组织用 FMEA 方法共享利益 能够应用 FMEA 分析 开始你自己的工作分析潜在失效模式和后 果分析
- 1、下载文档前请自行甄别文档内容的完整性,平台不提供额外的编辑、内容补充、找答案等附加服务。
- 2、"仅部分预览"的文档,不可在线预览部分如存在完整性等问题,可反馈申请退款(可完整预览的文档不适用该条件!)。
- 3、如文档侵犯您的权益,请联系客服反馈,我们会尽快为您处理(人工客服工作时间:9:00-18:30)。
2018年度人力资源与社会保障专题培训
过程失效模式与后果分析-PFMEA
前言:
近年来,发生过很多起汽车召回的事件,这包括美国的克莱斯勒、福特、通用三大汽车公司,日本的丰田汽车等知名企业都有召回的案例,我们国家也制定和发布了《缺陷汽车产品召回管理条例》,对缺陷汽车的召回要求更高、更规范化。
在这些召回事件中,绝大多数都是由于设计、零部件或材料上的缺陷可能导致对顾客的安全后果,这些召回对企业的经济损失是相当大的,甚至会导致企业破产,因此,IATF标准要求汽车零件制造商必须要作FMEA分析,尽可能的克服和减少缺陷的发生。
本课程将系统地讲解PFMEA的内容、要求、信息流、实施步骤和方法;包括过程流程图、PFMEA、特性矩阵表、控制计划等工具,帮助学员了解通过实施FMEA的过程,掌握产品特性内部、产品特性与过程特性、DFMEA和PFMEA、流程图和PFMEA、PFMEA和控制计划之间的相互关联,解决过程设计可能出现的问题,在产品实现过程的前期确保失效模式得到考虑并实现失效的控制和预防。
课程信息:
【培训日期】2018年6月2日(周六)
【培训时间】9:00—16:00(1天)
【培训地点】吴江经济技术开发区人力资源服务中心(吴江经济技术开发区云梨路1028号)【培训对象】制造工程师、质量工程师、SQE、设计工程师、和其他直接负责过程开发与过程开发管理人员。
【培训费用】会员单位扣10点/人,非会单位900元/人次(包括教材、餐饮、发票等)。
【备注】报名人员因故不能参加者需提前一天告知,无故缺席者点数照扣,谢绝空降。
课程大纲:
⏹FMEA 概述
●FMEA的背景与历史
●FMEA与可靠性、FMEA与风险分析
●FMEA的定义
●FMEA的种类: SFMEA, DFMEA, PFMEA
●FMEA小组
●DFMEA与PFMEA的关联
●PFMEA开发的时机
●FMEA的基本步骤:AIAG与VDA的不同描述
⏹PFMEA的输入
●过程流程图
●特性矩阵表
●过程流程图与PFMEA的关系
●PFMEA的两个假设:与产品设计和供方的关系
●宏观流程图与微观流程图
⏹练习1PFMEA
●PFMEA表格、表头解释
●过程的功能与要求:条件要求、结果要求、后果要求
●失效模式开发:
与功能/要求的关系、失效模式的定义与标准化、失效模式的充分性
●失效后果分析:
与失效链的关系、与DFMEA的关系、与专业知识的关系、与相关的失效模式的关系
●严重度评价:
◆安全法规、基本功能和次要功能、感官功能的理解
◆“对顾客的影响”“对制造的影响”的差异与使用
◆质量风险、交付风险、成本风险
◆AIAG、VDA、PSA不同的评价准则
◆贝尔缺陷分级原则
●级别:特殊特性
练习2:小组发表与培训师讲评
⏹PFMEA风险分析
●潜在原因分析:与门/或门、与供应商质量的关系、常见的错误描述方式、原因的层次与
数量、PFMEA是否存在SFMEA?
●练习3:
原因分析
●预防性控制措施开发:与发生率(频度)评价的关联、“现行”的含义、与制造设计规
范的关联、常见的过程控制措施(防错、DOE……)
●探测性控制措施开发:探测对象(失效模式还是原因)、检验与防错
●频度分析:经验数据域频度的关系、准则的理解,“1”的理解
●探测度分析:检验的时机与手段、准则的理解、“1”的理解
练习4:控制措施、频度、探测度分析、RPN
⏹PFMEA风险控制/改进
●风险控制原则
●多方位风险分析
●改进措施与SOD评价
●动态管理
●练习5:
继续完成改进措施,或者在给出的PFMEA中找错。
⏹控制计划
●控制计划的基本概念
●过程流程图、控制计划与PFMEA的关联
●控制计划的编制要求
●PFMEA变更与控制计划变更的关联
答疑与控制计划找错练习
授课讲师:何建军
●教育背景
南京林业大学机电工程学院
机械工程专业与计算机专业,双专业本科
●专业资格
ISO9001、ISO14001、OHSAS18001咨询师
IATF16949审核员
●当前专长
何建军先生擅长IATF16949标准;质量策划、控制和改进流程,如APQP。
何建军先生在汽车行业和设备制造业有多年实施和管理工作经验,在欧美著名的制造业集团公司和相关质量管理和生产力改进咨询和辅导的丰富经验超过14年,工作领域涉及生产现场的质量策划、控制、分析、改进以及整个公司质量管理体系的策划、建立、运行维护及持续改进。
何建军先生是中国质量协会6sigma黑带。
QFD、6sigma, 8D,QC小组;以及相关的质量
工具应用,如:新/老QC七大手法、SPC、MSA、DOE、统计抽样,假设检验,回归分析、FMEA 等。
何建军先生尤其擅长统计技术在质量管理方面的运用,曾编著《统计技术理论与运用》。
曾授课企业:
博世汽车部件(越南)全英文DOE授课、博世汽车部件(马来西亚)全英文DOE授课、博世汽车部件(长沙)有限公司 (Bosch Automotive Products Changsha)、
博世电动工具(中国)有限公司 (Bosch Power Tools Hangzhou)、上海宝钢有限公司、一汽轿车(长春)、VOLVO建筑设备(中国)、大陆汽车系统 (Continental Automotive Systems)、天合汽车部件技术 (上海) (TRW Shanghai)、艾默生环境优化技术(苏州)(Emerson Climate Technologies Suzhou)、ABB高压电机 (ABB HV Electrical Motor)、ABB厦门 (ABB Xiamen Company)、德尔福汽车门系统 (Delphi Automotive Door System Shanghai)、霍尼韦尔(Honeywell)、PPG航空材料 (PPG Aviation Material Suzhou)、SKF斯凯孚轴承(上海) (SKF Bearings Shanghai)等。
联系方式:
吴江经济技术开发区人力资源服务中心
培训发展中心
●电话:
●邮件:
●详细信息登陆网站:
培训报名信息。