XRF 050406 late-time flattening an inverse Compton component
MORNSUN URF48_QB-200W(F H)R3 产品说明书

200W isolated DC-DC converterUltra-wideinputandregulated singleoutputPatent Protection RoHSFEATURES●Ultra-wide 4:1input voltage range ●High efficiency up to 91%●I/O isolation test voltage 2.25k VDC ●Input under-voltage protection,output short-circuit,over-current,over–voltage,over-temperature protection●Operating ambient temperature range -40℃to +85℃●Five-sided metal shielded package ●Industry standard ¼-Brick package andpin-out●EN62368approvedURF48_QB-200W(F/H)R3series are isolated 200W DC-DC products with 4:1input voltage.They feature efficiency up to 91%,2250VDC input to output isolation,operating ambient temperature of -40℃to +85℃,input under-voltage,output short circuit,over-current,over–voltage,over-temperature protection.The products meet CLASS A of CISPR32/EN55032EMI standards by adding the recommended external components and they are widely used in applications such as battery powered systems,industrial controls,electricity,instrumentation,railway,communication and intelligent robotic.Selection GuideCertificationPart No.①Input Voltage (VDC)OutputFull Load Efficiency(%)Min./Typ.Capacitive Load(µF)Max.Nominal (Range)Max.②Voltage(VDC)Current (A)(Max.)CEURF4805QB-200W(F/H)R348(18-75)8054086/886000URF4812QB-200W(F/H)R31216.789/912000URF4815QB-200W(F/H)R31513.387/892000URF4824QB-200W(F/H)R3248.489/911000URF4848QB-200W(F/H)R348 4.289/91450--URF4836QB-200W(H)R348(18-75)80365.5686/881000Note:①Use“F”suffix is for added aluminum baseplate and “H”suffix for heat sink mounting.We recommended to choose modules with a heat sink for enhanced heat dissipation and applications with extreme temperature requirements;②Exceeding the maximum input voltage may cause permanent damage.Input SpecificationsItemOperating ConditionsMin.Typ.Max.UnitInput Current (full load/no-load)Nominal input voltage 12V 、24V 、48V output--4579/1004682/200mA 15V output --4682/1004845/2005V 、36V output--4739/1004849/200Reflected Ripple Current Nominal input voltage--100--Surge Voltage (1sec.max.)-0.7--90VDC Start-up Threshold Voltage ----18Input Under-voltage Protection 1416--Input Filter Pi filterCtrl*Module on Ctrl pin open or pulled high (3.5-12VDC)Module offCtrl pin pulled low to GND (0-1.2VDC)Ctrl*Input current when off --210mAHot PlugUnavailableNote:*The Ctrl pin voltage is referenced to input GND.Output SpecificationsItemOperating ConditionsMin.Typ.Max.UnitVoltage Accuracy --±1±3%Linear Regulation Input voltage variation from low to high at full load --±0.2±0.5Load Regulation 5%-100%load--±0.5±0.75Transient Recovery Time 25%load step change --300500µs Transient Response Deviation 25%load step change 5V output --±3±7.5%Others--±3±5Temperature Coefficient Full load----±0.03%/℃Ripple &Noise*20MHz bandwidth36V output --150300mVp-p Others --150250Over-voltage Protection Input voltage range110130160%Vo Over-current Protection 110130150%Io Short-circuit ProtectionHiccup,continuous ,self-recoveryNote:The “parallel cable”method is used for ripple and noise test,please refer to DC-DC Converter Application Notes for specific information.General SpecificationsItem Operating Conditions Min.Typ.Max.UnitIsolationInput-output Electric Strength Test for 1minute with a leakage current of 5mA max2250----VDC Input-case 1500----Output-case500----Insulation Resistance Input-output resistance at 500VDC 100----M ΩIsolation Capacitance Input-output capacitance at 100KHz/0.1V 36V output --22003000pF Others --2200--Trim 36V output 100--110%Vo Others90--110Sense----105Operating Temperature -40--+85℃Storage Temperature -55--+125Over-temperature Protection Max.Case Temperature 36V output 95105115Others--115120Pin Soldering Resistance TemperatureWave-soldering,10seconds----260Soldering spot is 1.5mm away from case for 10seconds ----300Thermal resistance Free air convection (20LFM)URF48xxQB-200WR3----7.5℃/W URF48xxQB-200WFR3---- 6.3URF48xxQB-200WHR3---- 5.2Storage Humidity Non-condensing 5--95%RH VibrationIEC/EN61373train 1B categorySwitching Frequency PWM mode--250--KHz MTBFMIL-HDBK-217F@25℃500----K hours Mechanical SpecificationsCase Material Aluminum alloy case,black plastic bottom,flame-retardant and heat-resistant (UL94V-0)DimensionsURF48xxQB-200WR361.8×40.2×12.7mmDimensionsURF48xxQB-200WFR362.0×56.0×14.6mm URF48xxQB-200WHR361.8×40.2×27.7mm WeightURF48xxQB-200WR389.0g(Typ.)URF48xxQB-200WFR3109.0g(Typ.)URF48xxQB-200WHR3120.0g(Typ.)Cooling MethodFree air convection (20LFM)Electromagnetic Compatibility (EMC)EmissionsCECISPR32/EN55032CLASS A(see Fig.2for recommended circuit)RE CISPR32/EN55032CLASS A (see Fig.2for recommended circuit)ImmunityESD IEC/EN61000-4-2,EN50121-3-2Contact ±6KV Air ±8KV perf.Criteria B RS IEC/EN61000-4-3,EN50121-3-210V/mperf.Criteria A EFTIEC/EN61000-4-4,EN50121-3-2±2KV(see Fig.2for recommended circuit)perf.Criteria A Surge EN50121-3-2differential mode ±1KV,1.2/50us,source impedance 42Ω(see Fig.2for recommended circuit)perf.Criteria B CSIEC/EN61000-4-6,EN50121-3-210Vr.m.sperf.Criteria ATypical Characteristic CurvesNotes :1)Product application thermal design should be referred to the recommended PCB layout and recommended heat dissipation structure,please refer to DC-DC Converter Application Notes for specific information.Remote Sense Application1.Remote Sense Connection if not usedNotes :(1)If the sense function is not used for remote regulation the user must connect the +Sense to +Vo and -Sense to 0V at the DC-DC converter pins and will compensate for voltage drop across pins only.(2)The connections between Sense lines and their respective power lines must be kept as short as possible,otherwise they may be picking up noise,interference and/or causing unstable operation of the power module.2.Remote Sense Connection used for CompensationNotes :(1)Using remote sense with long wires may cause unstable output,please contact technical support if long wires must be used.(2)PCB-tracks or cables/wires for Remote Sense must be kept as short as possible.Twisted pair or shielded wire are suggested for remote compensation and must be kept as short as possible.(3)We recommended using adequate cross section for PCB-track layout and/or cables to connect the power supply module to the load in order to keep the voltage drop below 0.3V and to make sure the power supply's output voltage remains within the specified range.(4)Note that large wire impedance may cause oscillation of the output voltage and/or increased ripple.Consult technical support or factory for further advice of sense operation.Design Reference1.Typical application(1)We recommended using the recommended circuit shown in Fig.1during product testing and application,otherwise please ensure that at least a 220μF electrolytic capacitors is connected at the input in order to ensure adequate voltage surge suppression and protection.(2)We recommended increasing the value of Cin and pay attention to the unstable input voltage if the product input side is paralleled with motor drive circuit and/or larger energy transient circuits,to ensure the stability of input terminal and avoid repeatedly start-up problems due to input voltage lower than under-voltage protection point.(3)We recommended increasing the output capacitance with limited to the capactive load specification and/or increasing the voltage clamping circuit(such as TVS)if the output terminal is inductive device such as relay or a motor,to ensure adequate voltage surge suppression and protection.(4)Input and/or output ripple can be further reduced by appropriately increasing the input &output capacitor values Cin and Cout and/or by selecting capacitors with a low ESR (equivalent series resistance).Also make sure that the capacitance is not exceeding the specified max.capacitive load value of the product.Fig.1Note:*Please pay attention to the ambient temperature of the product when using an external capacitor,increase the electrolytic capacitor values to at least 1.5times the original parameter if the ambient temperature is low.Vout(VDC)FuseCin *Cout TVS 520A,slow blow220µF470µF SMDJ6.0A 12220µFSMDJ14A 15SMDJ17A 24100µFSMDJ28A 36SMDJ47A 48SMDJ54A2.EMC compliance circuitWe recommended using the recommended circuit shown in Fig.2during product EMC testing and application.L 1VinC1+CY2CY 4C5L 2Vin GNDDC/DC+V o0V+C2C3C4C6C7C8C9CY 3CY1Fig.2Componentsrecommended Component value C1150µF/100V electrolytic capacitor C947µF/100V electrolytic capacitor C2,C3,C4,C5,C6,C7,C82.2µF/100V ceramic capacitor L1 2.0mH,recommended to use MORNSUN P/N:FL2D-A2-202(C)L21.5µH/15A inductance CY1,CY2,CY3,CY41nF Y1safety capacitor3.Trim Function for Output Voltage Adjustment (open if unused)R 2R 1R 3V ref R TTrimVo’R 2R 1R 3V ref R TVo’Trim upTrim downTRIM resistor connection (dashed line shows internal resistor network )Calculation formula of Trim resistance:up: a=VrefVo’-Vref R 1R =T aR 2R -a 2-R 3down: a=VrefVo’-VrefR 2R =T aR 1R -a1-R 3R T =Trim Resistor value;a =self-defined parameterVo’=desired output voltage (±10%max.)Vout(VDC)R1(K Ω)R2(K Ω)R3(K Ω)Vref(V)5 3.036310 2.51211.00 2.8715 2.51514.03 2.815 2.52424.872 2.8715 2.53638.73 2.8515 2.54853.0172.913152.5Note:(1)When using the Trim down function make sure that the RT resistor value is calculated correctly.If the Trim pin is shorted with +Vo,or its value is too low,then the output voltage Vo would be lower than 0.9Vo,which may cause the product to fail;(2)URF4836QB-200W(H)R3has no down-regulation function,otherwise it may cause irreparable damage to the product.4.Reflected ripple current--test circuitDCVo0VCinDC OscilloscopeLin Note:Lin(4.7µH),Cin(220µF ,ESR <1.0Ωat 100KHz)5.The products do not support parallel connection of their output.6.We recommended the use of a converter with higher output power capability to cover applications with higher power requirements.7.For additional information please refer to application notes on URF48xxQB-200WR3Dimensions and recommended LayoutURF48xxQB-200WFR3Dimensions and recommended Layout URF48xxQB-200WHR3Dimensions and recommended LayoutNote:1.For additional information on Product Packaging please refer to .Packaging bag number:58010113(URF48xxQB-200WR3),58200069(URF48xxQB-200WFR3),58220017(URF48xxQB-200WHR3);2.The maximum capacitive load offered were tested at input voltage range and full load;3.Unless otherwise specified,data in this datasheet should be tested under the conditions of Ta=25℃,humidity<75%RH with nominal input voltage and rated load;4.All index testing methods in this datasheet are based on our company corporate standards;5.We can provide product customization service and match filter module;6.Products are related to laws and regulations:see"Features"and"EMC";7.Our products shall be classified according to ISO14001and related environmental laws and regulations,and shall be handled by qualified units.Mornsun Guangzhou Science&Tech nolo gy Co.,Ltd.Address:No.5,Kehui St.1,Kehui Development Center,Science Ave.,Guangzhou Science City,Huangpu District,Guangzhou,P.R.China Tel:86-20-38601850Fax:86-20-38601272E-mail:***************。
钢铁大侠Dixon A540系列地面接线器说明书

A540 SERIES GROUND CLAMPContentsOverview (2)Features (2)Technical Specifications (3)Installation (6)Maintenance (8)Replacement parts (8)Operation (9)Warranty (9)Sales and Service Contacts (10)OverviewThe A540 Series ground clamps are key to creating a quality temporary connection for antistatic grounding applications. The clamp features three teeth to penetrate dirt, corrosion, and road grime when in use. The teeth are constructed of stainless steel to ensure lasting operation, and isolated from the clamp handle to allow operators to establish ground and a ground-verification signal in a single clamp action. The A540 also includes a high durability cable and junction box for convenient wiring access during installation and maintenance.Common applications for the A540 series ground clamp include:•Tank truck and Rail car loading facilities•Drum and barrel filling sites•Loading of stationary tanksFeatures•Clamp tethered to cable by stainless steel strap to protects connection from strain and wear. •Pull-out resistant cord grip on junction box holds cable tighter the harder it is pulled. •Junction box creates convenient service point for hazardous location installations.•Coiled cable for compact storage.•Strong clamping force to penetrate grime and remain connected during loading process. •Can provide ground and a ground-verification signal in a single clampTechnical SpecificationsMIN MAX NOMINAL AMBIENT TEMPERATURE -40°C 90°C -JUNCTION BOXHEIGHT 10.75 in. [27.3cm] INCLUDES STRAIN RELIEFWIDTH 3.0 in. [7.62cm]DEPTH 3.0 in. [7.62cm]WEIGHT 5 lbs. (2.27 kg)INGRESS PROTECTION Weatherproof, raintight, and dust tightCONDUIT ENTRIES ONE ¾” TRADE SIZE HOLE + FACTORY INSTALLED CABLE ONBOTTOMSUITABLE FOR INSTALL IN HAZARDOUS LOCATIONS: Class I, Division 1 & 2, Groups B, C, and D hazardous locationsClass II, Division 1 & 2, Groups E, F, and G hazardous locationsClass III hazardous locationsSUITABLE FOR CONNECTION TO HAZARDOUS LOCATIONS: Class I, Division 1 & 2, Groups A, B, C, and D hazardous locationsClass I, Zone 0, 1 & 2, Groups IIC, IIB, and IIA hazardous locationsCABLELENGTH 25 ft. stretched [7.6m] (Standard; other lengths available) DIAMETER 0.4 in. [1.0cm]WEIGHT 2.5 lbs. [1.13kg]; 0.1 lbs. PER FOOT [0.15g per meter] JACKET MATERIAL Thermoplastic Elastomer, resistant to harsh environments. RESISTANCE 0.14Ω (6mΩ/foot)RECOMMENDED WIREBETWEEN CONTROLLER ANDA54018 GA Stranded copper wire (THHN)AccessoriesGround Verification Monitor:The A240 series ground verification monitors are designed to mitigate the danger of static buildup by verifying the presence of a high quality and reliable earth-ground bond. With the presence of a ground path for static to dissipate, loading and unloading of flammable or combustible liquids can be done safely. The A240 monitor verifies the bond is of sufficient quality to prevent static buildup. Internal indicators inform the operator whether the process connection is safely grounded and internal relay contacts may be used to interlock operations until a safe earth bonding has been established.Sealing Fitting:Sealing fittings are required within 18 inches of each enclosure entry used. These seal conduits from passing hazardous vapors or propagating flame. Sealing fittings are installed in-line with conduit, then filled with sealing compound once wiring has been installed and verified. Downstream junction boxes containing Intrinsically Safe circuits may be serviced without danger.¾” NPT Vertical Seal fitting with nipple; P/N: 30192ALNote: Actual color may differWiring DiagramInstallationINSTALLATION MUST BE COMPLETED BY QUALIFIED PROFESSIONALA540 Series ground clamps are suitable for installation and use in ordinary and specific hazardous locations (listed in technical specifications section) as defined by NEC NFPA70 and IECEx standard 60079. Installation to be performed by a qualified professional.MechanicalIt is recommended to wall mount the unit using stainless steel or galvanized steel hardware suitable for the monitor’s weight and wall material.ing the bolt pattern provided below, locate a sturdy area, large enough to install the junctionbox.For greatest environmental resistance it is recommended to mount the junction box in theorientation shown. Keep in mind the coiled cable will hang below the box, and the clamp must be stored in an ungrounded position. The enclosure can withstand rain and sun exposure butwill last longer when protected from the elements.2.Level the bolt pattern and drill two holes marked on the pattern.3.Have another person lift the junction box into position in front of the drilled holes.4.Insert the two anchors or bolts into the two mounting holes shown below.5.Tighten all the screws and ensure that the junction box is secure.Electrical•To be installed per NEC NFPA70 requirements for U.S. installations.•Installation in other regions must conform to local electrical codes. Instructions provided below are general guidelines and may not cover local requirements.1.Remove the lid from the A540 junction box.2.Run conduit to junction box. Ensure conduit has sealing fitting at feeder end if installation is inhazardous location.Conduit connection should be sealed from water intrusion through either rubber washers,caulking, or other sealing means.3.Pull cable from process controller into A540 junction box.4.Refer to wiring diagram above, as well as documentation for process controller to properly wirethe process controller to the A540 ground cable.5.Reinstall lid onto junction box.6.Designate an ungrounded location to store the ground clamp while not in use. It is critical thatthe ground clamp be ungrounded while not in use. Storing in a grounded state can lead tounsafe loading conditions.7.Verify proper functionality of system by testing before putting into service.MaintenanceSERVICE SHOULD BE COMPLETED ONLY BY A QUALIFIED HAZARDOUS LOCATION TECHNICIAN. REPLACE PARTS WITH GENUINE DIXON OR APPROVED EQUIVALENT PARTS; SUBSTITUTION MAY IMPAIR INTRINSIC SAFETY.The A540 has few parts that will require regular maintenance and is designed for long service periods. Unsheltered units should be serviced in dry weather to prevent rainwater from entering the enclosure and minimize moisture exposure.1.If the ground connection is becoming intermittent, it is advised to inspect the clamp and cable.2.Dulling of the clamp teeth may be a sign that the clamp has reached the end of its usable lifeand should be replaced. Contact Dixon for replacement parts.3.Checking the cable for a failing conductor can be done by clamping to a known grounded pieceof metal, then flexing the cable. If the ground controller’s indicator changes while flexing thecable, the cable has reached the end of its usable life and should be replaced. Do not attempt to repair the cable. Contact Dixon for replacement parts.a.In the event that the cable does need to be replaced, it can be removed while energized.b.Open the A540 junction box and note the wire positions for each conductor in the A540cable on the terminal block.c.Remove the wires from the terminal block.press the mesh cordgrip by pushing it toward the bottom of the junction box.e.With the cordgrip compressed, the old cable may be pulled out, and new cable installed.f.Once the new cable has been installed into the mesh cordgrip, re-wire the cable into theA540 junction box terminal strip.g.Close the A540 junction box.h.Verify proper functionality of system by testing before putting into service. Replacement partsDescription Part NumberRack Cable with clamp 30585Cord Grip 30708Sealing Fitting; ¾” Vertical 30129ALSealing Compound 30339 for 5 lbs. or 30339-002 for 1 lb.OperationWARNING - USING THE A540 IN A MANNER NOT DEFINED IN THIS MANUAL MAY IMPAIR SAFETY.1.Verify process controller is powered on and idle.2.Test the controller’s operation by clamping to a known grounded piece of metal. Verify thecontroller’s indicator changes from RED to GREEN. Remove the clamp from the test point.3.Before any other electrical connections are made, secure the A540 clamp to the processconnection that is to be loaded.4.Verify the process controller’s indicator changes from RED to GREEN.plete any other process connections.6.Once all other safety measures are active, begin the loading process.7.Once loading is complete, remove all other process connections, then the A540 last.8.Return the A540 clamp to the isolated storage facility, verifying the indicator remains red. WarrantyFor warranty claims and information regarding coverage, please contact Dixon Support at+1 (877) 582-3569Sales and Service ContactsEurope:Dixon Group Europe Ltd.Preston, EnglandPhone: +44 (0) 1772 323529Fax: +44 (0) 1772 314664Email: ************************.ukCanada:Dixon Group Canada Limited Innisfil (Barrie), OntarioPhone: 705-436-1125Fax: 705-436-6251Toll Free: 877-963-4966E-mail: ***************************USA:Dixon Bayco USAChestertown, MarylandPhone: 410-778-2000Fax: 410-778-4702Toll Free: 800-355-1991E-mail: *************************Mexico:Dixva, S. de R.L. de C.V.Monterrey, N.LPhone: 01-800-00-DIXON (34966)Fax: 01-81-8354-8197E-mail: **************************.mxAsia Pacific:Dixon (Asia Pacific) Pty Ltd Wingfield, South AustraliaPhone: +61 8 8202 6000Fax: +61 8 8202 6099E-mail: ************************.au。
INV-DS4050数字字符叠加器说明书

产品介绍1.1产品技术参数产品名称网络数字字符叠加器光电式传感器产品型号INV-DS4050楼层显示器传感器专用型电源类型DC12V±10%DC5V(由叠加器供电)功耗<4W<0.5W工作环境温度-40℃至85℃-55℃至120℃工作相对湿度<90%<90%产品尺寸长150mm×宽130mm×高38mm长70mm×宽55mm×高38mm网络接口10M/100M自适应NA报警输出1路NA1.2产品用途介绍适用于各类安装电梯监控的电梯场所,在不改变电梯原有电器线路的情况下,通过光电传感器对电梯运行状态进行采样,能在电视监视器上指示电梯所在楼层数、运行方向、停止及电梯名称。
准确知道电梯当前所在的楼层有利于用户监控的集中管理,对于出入电梯的人员进行监控,或保留录像以备日后查阅,一旦电梯故障,方便维修人员知道电梯所在楼层,从而及时处理,若有事件发生,也可方便的查阅录像中人员在活动的关键层出入情况;有利于事件的解决。
1.3产品性能介绍1、主机可提供一个电平输出作为报警信号;2、传感器在本产品上直接取电,无需再额外为传感器提供电源;3、无需在原有系统中添加交换机等其他设备;4、采用底层协议对接方式,不会对视频画面的清晰度造成任何干扰;5、可叠加电梯名称(汉字,数字,字母,符号均可);6、电梯运行状态指示:上行、下行、楼层号(楼层号显示内容可以通过设置软件任意变换,例如:将地上5层更名为会议室。
)7、安装方便,只需将该设备的光电传感器安装在电梯轿厢顶部原有传感器组的位置,主机放置在轿厢顶部;8、由于支持采用光电传感器对电梯运行状态进行采样,因而采样稳定准确,设备抗干扰性强,可靠性高;9、使用配套软件,在办公室内只需连接PC机、监视器,就能完成对叠加器参数设置;无须现场调试,方便维护;10、可根据需要设置夹层和跳层,确保显示正确,总层数最多支持到100层;1.4物品清单1、电梯字符叠加器一台2、12V电源适配器一个3、电梯专用传感器一个叠加器硬件安装2.1安装示意图下图为电梯井道剖面示意图:2.2光电传感器的安装先将光电传感器固定在电梯的传感器组上,并保证电梯平层时隔磁板能在光电传感器的“U”型口中。
REF5040资料

FEATURESDESCRIPTION APPLICATIONSInput Signal 0V to 4V12348765DNC(1)NC(2)TRIMDNC(1)V INTEMPGNDV OUTREF50xxSO-8, MSOP-8(3)(1) DNC = Do not connect.(2) NC = No internal connection.(3) MSOP-8 package available Q3, 2007.NOTES:REF5020,,REF5025REF5030,REF5040 REF5045,REF5050SBOS410–JUNE2007 Low-Noise,Very Low Drift,PrecisionVOLTAGE REFERENCE•LOW TEMPERATURE DRIFT:–High-Grade:3ppm/°C(max)The REF50xx is a family of low-noise,low-drift,veryhigh precision voltage references.These references –Standard-Grade:8ppm/°C(max)are capable of both sinking and sourcing,and are •HIGH ACCURACY:very robust with regard to line and load changes.–High-Grade:0.05%(max)Excellent temperature drift(3ppm/°C)and high –Standard-Grade:0.1%(max)accuracy(0.05%)are achieved using proprietary •LOW NOISE:3μV PP/V design techniques.These features,combined withvery-low noise make the REF50xx family ideal for use •HIGH OUTPUT CURRENT:±10mAin high-precision data acquisition systems.•TEMPERATURE RANGE:–40°C to+125°CEach reference voltage is available in both standard-and high-grade versions.They are offered in MSOP-8(available Q3,2007)and SO-8packages,and are •16-BIT DATA ACQUISITION SYSTEMSspecified from–40°C to+125°C.•ATE EQUIPMENT•INDUSTRIAL PROCESS CONTROL REF50xx Family•MEDICAL INSTRUMENTATION MODEL OUTPUT VOLTAGE •OPTICAL CONTROL SYSTEMS REF5020 2.048V •PRECISION INSTRUMENTATION REF5025 2.5VREF5030 3.0VREF5040 4.096VREF5045 4.5VREF5050 5.0VPlease be aware that an important notice concerning availability,standard warranty,and use in critical applications ofTexas Instruments semiconductor products and disclaimers thereto appears at the end of this data sheet.All trademarks are the property of their respective owners.ABSOLUTE MAXIMUM RATINGS (1)REF5020,,REF5025REF5030,REF5040REF5045,REF5050SBOS410–JUNE 2007This integrated circuit can be damaged by ESD.Texas Instruments recommends that all integrated circuits be handled with appropriate precautions.Failure to observe proper handling and installation procedures can cause damage.ESD damage can range from subtle performance degradation to complete device failure.Precision integrated circuits may be more susceptible to damage because very small parametric changes could cause the device not to meet its published specifications.PACKAGE/ORDERING INFORMATION (1)(1)For the most current package and ordering information see the Package Option Addendum at the end of this document,or see the TI web site at .(2)MSOP-8(DGK)package available Q3,2007.PARAMETER REF50xx UNIT Input Voltage +18V Output Short-Circuit30mA Operating Temperature Range –55to +125°C Storage Temperature Range –55to +150°C Junction Temperature (T J max)+150°C Human Body Model (HBM)3000V ESD Rating Charged Device Model (CDM)1000V(1)Stresses above these ratings may cause permanent damage.Exposure to absolute maximum conditions for extended periods may degrade device reliability.These are stress ratings only,and functional operation of the device at these or any other conditions beyond those specified is not implied.ELECTRICAL CHARACTERISTICS:PER DEVICE REF5020,,REF5025 REF5030,REF5040 REF5045,REF5050SBOS410–JUNE2007Boldface limits apply over the specified temperature range,T A=–40°C to+125°C.At T A=+25°C,I LOAD=0,C L=1μF,and V IN=(V OUT+0.2V)to18V,unless otherwise noted.PER DEVICE PARAMETER CONDITIONS MIN TYP MAX UNITREF5020(V OUT=2.048V)(1)OUTPUT VOLTAGEOutput Voltage V OUT 2.7V<V IN<18V 2.048V Initial Accuracy:High-Grade–0.050.05% Standard-Grade–0.10.1% NOISEOutput Voltage Noise f=0.1Hz to10Hz6μV PPREF5025(V OUT=2.5V)OUTPUT VOLTAGEOutput Voltage V OUT 2.5V Initial Accuracy:High-Grade–0.050.05% Standard-Grade–0.10.1% NOISEOutput Voltage Noise f=0.1Hz to10Hz7.5μV PPREF5030(V OUT=3.0V)OUTPUT VOLTAGEOutput Voltage V OUT 3.0V Initial Accuracy:High-Grade–0.050.05% Standard-Grade–0.10.1% NOISEOutput Voltage Noise f=0.1Hz to10Hz9μV PPREF5040(V OUT=4.096V)OUTPUT VOLTAGEOutput Voltage V OUT 4.096V Initial Accuracy:High-Grade–0.050.05% Standard-Grade–0.10.1% NOISEOutput Voltage Noise f=0.1Hz to10Hz12μV PPREF5045(V OUT=4.5V)OUTPUT VOLTAGEOutput Voltage V OUT 4.5V Initial Accuracy:High-Grade–0.050.05% Standard-Grade–0.10.1% NOISEOutput Voltage Noise f=0.1Hz to10Hz13.5μV PPREF5050(V OUT=5.0V)OUTPUT VOLTAGEOutput Voltage V OUT 5.0V Initial Accuracy:High-Grade–0.050.05% Standard-Grade–0.10.1% NOISEOutput Voltage Noise f=0.1Hz to10Hz15μV PP (1)For V OUT≤2.5V,the minimum supply voltage is2.7V.ELECTRICAL CHARACTERISTICS:ALL DEVICESREF5020,,REF5025REF5030,REF5040REF5045,REF5050SBOS410–JUNE 2007Boldface limits apply over the specified temperature range,T A =–40°C to +125°C.At T A =+25°C,I LOAD =0,C L =1μF,and V IN =(V OUT +0.2V)to 18V,unless otherwise noted.REF50xxPARAMETERCONDITIONSMIN TYP MAX UNITOUTPUT VOLTAGE TEMPERATURE DRIFT Output Voltage Temperature Drift dV OUT /dTHigh-Grade 2.53ppm/°C Standard-Grade 38ppm/°CLINE REGULATION Line Regulation dV OUT /dV INREF5020(1)Only V IN =2.7V to 18V0.11ppm/V All Other Devices 0.11ppm/V Over Temperature 0.21ppm/V LOAD REGULATION Load Regulation dV OUT /d ILOAD–10mA <I LOAD <+10mA,V IN =V OUT +0.75V2030ppm/mA Over Temperature 50ppm/mA SHORT-CIRCUIT CURRENT Short-Circuit Current I SC V OUT =025mA TEMP PIN Voltage OutputAt T A =+25°C575mV Temperature Sensitivity 2.64mV/°C TURN-ON SETTLING TIME Turn-On Settling Time To 0.1%with C L =1μF200μsPOWER SUPPLY Supply Voltage V SSee Note(1)V OUT +0.2(1)18V Quiescent Current 0.81mA Over Temperature 1.2mATEMPERATURE RANGE Specified Range –40+125°C Operating Range –55+125°CThermal Resistance θJAMSOP-8150°C/W SO-8150°C/W(1)For V OUT ≤2.5V,the minimal supply voltage is 2.7V.TYPICAL CHARACTERISTICS0.20.50.71.01.21.51.72.02.22.52.73.03.23.53.74.04.24.54.75.0Drift (ppm/C)°P o p u l a t i o n (%)0.51.01.52.02.53.03.54.04.55.05.56.06.57.07.58.0Drift (ppm/C)°P o p u l a t i o n (%)-50-25T emperature (C)°0.050.040.030.020.010-0.01-0.02-0.03-0.04-0.05O u t p u tV o l t a g e A c c u r a c y (%)125255075100-0.0-0.0-0.0-0.0-0.00.00.00.00.00.0Drift (ppm/C)°P o p u l a t i o n (%)10Frequency (Hz)160140120100806040200P S R R (d B )100k1001k10k-15-10-5Load Current (mA)0.80.70.60.50.40.30.20.10D r o p o u t V o l t a g e (V )150510+125C°+25C °-°40CREF5020,,REF5025REF5030,REF5040REF5045,REF5050SBOS410–JUNE 2007At T A =+25°C,I LOAD =0,and V S =V OUT +0.2V,unless otherwise noted.For V OUT ≤2.5V,the minimum supply voltage is 2.7V.TEMPERATURE DRIFTTEMPERATURE DRIFT (0°C to +85°C)(–40°C to +125°C)Figure 1.Figure 2.OUTPUT VOLTAGE OUTPUT VOLTAGE ACCURACYINITIAL ACCURACYvs TEMPERATUREFigure 3.Figure 4.POWER-SUPPLY REJECTION RATIOvs FREQUENCYDROPOUT VOLTAGE vs LOAD CURRENTFigure 5.Figure 6.-10-5Load Current (mA)2.501252.501002.500752.500502.500252.500002.499752.499502.499252.499002.49875O u t p u t V o l t a g e (V )105+125C°+25C°-°40C -50-25T emperature (C)°0.90.80.70.60.50.40.3T E M P P i n O u t p u t V o l t a g e (V )125255075100-50-25T emperature (C)°10501000950900850800750700650600Q u i e s c e n t C u r r e n t (m A )125255075100-50-25T emperature (C)°0.50.40.30.20.10-0.1-0.2-0.3-0.4-0.5L i n e R e g u l a t i o n (p p m /V )1252550751001s/div1V /d i vm -50-25T emperature (C)°35302520151050S h o r t -C i r c u i t C u r r e n t (m A )125255075100REF5020,,REF5025REF5030,REF5040REF5045,REF5050SBOS410–JUNE 2007TYPICAL CHARACTERISTICS (continued)At T A =+25°C,I LOAD =0,and V S =V OUT +0.2V,unless otherwise noted.For V OUT ≤2.5V,the minimum supply voltage is 2.7V.REF5025OUTPUT VOLTAGETEMP PIN OUTPUT VOLTAGEvs LOAD CURRENTvs TEMPERATUREFigure 7.Figure 8.QUIESCENT CURRENT LINE REGULATION vs TEMPERATUREvs TEMPERATUREFigure 9.Figure 10.SHORT-CIRCUIT CURRENTvs TEMPERATURENOISEFigure 11.Figure 12.40s/div m 2V/div1V/divV OUTV IN400s/divm 5V/div1V/divV OUTV IN20s/div m -1mA-1mA+1mAI LOADV OUT5mV/div1mA/div20s/divm -10mA+10mA+10mAI LOAD V OUT2mV/div10mA/div100s/div m -1mA-1mA+1mAI LOAD V OUT5mV/div1mA/div100s/divm -10mA-10mA+10mAI LOAD V OUT2mV/div10mA/divREF5020,,REF5025REF5030,REF5040REF5045,REF5050SBOS410–JUNE 2007TYPICAL CHARACTERISTICS (continued)At T A =+25°C,I LOAD =0,and V S =V OUT +0.2V,unless otherwise noted.For V OUT ≤2.5V,the minimum supply voltage is 2.7V.STARTUPSTARTUP(REF5025,C =1μF)(REF5025,C =10μF)Figure 13.Figure 14.LOAD TRANSIENT LOAD TRANSIENT (C L =1μF,I OUT =1mA)(C L =1μF,I OUT =10mA)Figure 15.Figure 16.LOAD TRANSIENT LOAD TRANSIENT (C L =10μF,I OUT =1mA)(C L =10μF,I OUT =10mA)Figure 17.Figure 18.20m s/div V OUTV IN5mV/div500mV/div100s/divm V OUTV IN5mV/div500mV/divREF5020,,REF5025REF5030,REF5040REF5045,REF5050SBOS410–JUNE 2007TYPICAL CHARACTERISTICS (continued)At T A =+25°C,I LOAD =0,and V S =V OUT +0.2V,unless otherwise noted.For V OUT ≤2.5V,the minimum supply voltage is 2.7V.LINE TRANSIENTLINE TRANSIENT (C L =1μF)(C L =10μF)Figure 19.Figure 20.APPLICATION INFORMATIONSUPPLY VOLTAGEOUTPUT ADJUSTMENT (TRIM Pin)BASIC CONNECTIONSTEMPERATURE DRIFTDrift +ǒVOUTMAX*V OUTMINV OUT Temp RangeǓ106(ppm)(1)REF5020,,REF5025REF5030,REF5040REF5045,REF5050SBOS410–JUNE 2007The REF50xx is family of low-noise,precision bandgap voltage references that are specifically designed for excellent initial voltage accuracy and The REF50xx family of voltage references features drift.Figure 21shows a simplified block diagram of extremely low dropout voltage.With the exception of the REF50xx.the REF5020,which has a minimum supply requirement of 2.7V,these references can be operated with a supply of 200mV above the output voltage in an unloaded condition.For loaded conditions,a typical dropout voltage versus load plot is shown in Figure 6of the Typical Characteristics.The REF50xx provides a very accurate voltage output.However,V OUT can be adjusted from the nominal value for the purpose of trimming system errors by configuring the TRIM pin (pin 5).The TRIM pin provides for adjustment of the voltage at V OUT over a ±15mV range.Figure 23shows a typical circuit using the TRIM pin to adjust V OUT .When using this technique,the temperature coefficients of the resistors can degrade the temperature drift at the output.Figure 21.REF50xx Simplified Block DiagramFigure 22shows the typical connections for the REF50xx.A supply bypass capacitor ranging between 1μF to 10μF is recommended.A 1μF to 50μF,low-ESR output capacitor (C L )must be connected to V OUT .Figure 23.V OUT Adjustment Using the TRIM PinThe REF50xx is designed for minimal drift error,which is defined as the change in output voltage over temperature.The drift is calculated using the box method,as described by the following equation:Figure 22.Basic ConnectionsThe REF50xx features a maximum drift coefficient of 3ppm/°C for the high-grade version,and 8ppm/°C for the standard-grade.TEMPERATURE MONITORINGPOWER DISSIPATIONNOISE PERFORMANCEREF5020,,REF5025REF5030,REF5040REF5045,REF5050SBOS410–JUNE 2007The temperature output terminal (TEMP,pin 3)The REF50xx family is specified to deliver current provides a temperature-dependent voltage output loads of ±10mA over the specified input voltage with approximately 60k Ωsource impedance.As seen range.The temperature of the device increases in Figure 8,the output voltage follows the nominal according to the equation:relationship:T J =T A +P D ×θJAV TEMPPIN=509mV +2.64×T(°C)Where:T J =Junction temperature (°C)This pin indicates general chip temperature,accurate to approximately ±15°C.Although it is not generally T A =Ambient temperature (°C)suitable for accurate temperature measurements,it P D =Power dissipated (W)can be used to indicate temperature changes or for θJA =Junction-to-ambient thermal resistance temperature compensation of analog circuitry.A (°C/W)temperature change of 30°C corresponds to an approximate 79mV change in voltage at the TEMP The REF50xx junction temperature must not exceed pin.the absolute maximum rating of +150°C.The TEMP pin has high output impedance (see Figure 21).Loading this pin with a low-impedance circuit induces a measurement error;however,it does Typical 0.1Hz to 10Hz voltage noise for each member not have any effect on V OUT accuracy.To avoid of the REF50xx family is specified in the Electrical errors caused by low-impedance loading,buffer the Characteristics:Per Device table.The noise voltage TEMP pin output with a suitable low-temperature drift increases with output voltage and operating op amp,such as the OPA333,OPA335,or OPA376,temperature.Additional filtering can be used to as shown in Figure 24.improve output noise levels,although care should be taken to ensure the output impedance does not degrade performance.Figure 24.Buffering the TEMP Pin OutputAPPLICATION CIRCUITSDATA ACQUISITIONNEGATIVE REFERENCE VOLTAGEREF5020,,REF5025REF5030,REF5040REF5045,REF5050SBOS410–JUNE 2007Data acquisition systems often require stable voltage For applications requiring a negative and positive references to maintain accuracy.The REF50xx family reference voltage,the REF50xx and OPA735can be features low noise,very low drift,and high initial used to provide a dual-supply reference from a 5V accuracy for high-performance data converters.supply.Figure 25shows the REF5025used to Figure 26shows the REF5040in a basic data provide a 2.5V supply reference voltage.The low drift acquisition system.performance of the REF50xx complements the low offset voltage and zero drift of the OPA735to provide an accurate solution for split-supply applications.Care must be taken to match the temperature coefficients of R 1and R 2.Figure 26.Basic Data Acquisition SystemFigure 25.The REF5025and OPA735Create Positive and Negative Reference VoltagesPACKAGING INFORMATIONOrderableDevice Status (1)Package Type Package DrawingPins Package Qty Eco Plan (2)Lead/Ball Finish MSL Peak Temp (3)REF5020AID ACTIVE SOIC D 875Green (RoHS &no Sb/Br)CU NIPDAU Level-2-260C-1YEAR REF5020AIDG4ACTIVE SOIC D 875Green (RoHS &no Sb/Br)CU NIPDAU Level-2-260C-1YEAR REF5020AIDR ACTIVE SOIC D 82500Green (RoHS &no Sb/Br)Call TI Level-2-260C-1YEAR REF5020AIDRG4ACTIVE SOIC D 82500Green (RoHS &no Sb/Br)Call TI Level-2-260C-1YEAR REF5020ID ACTIVE SOIC D 875Green (RoHS &no Sb/Br)CU NIPDAU Level-2-260C-1YEAR REF5020IDG4ACTIVE SOIC D 875Green (RoHS &no Sb/Br)CU NIPDAU Level-2-260C-1YEAR REF5020IDR ACTIVE SOIC D 82500Green (RoHS &no Sb/Br)CU NIPDAU Level-2-260C-1YEAR REF5020IDRG4ACTIVE SOIC D 82500Green (RoHS &no Sb/Br)CU NIPDAU Level-2-260C-1YEAR REF5025AID ACTIVE SOIC D 875Green (RoHS &no Sb/Br)CU NIPDAU Level-2-260C-1YEAR REF5025AIDG4ACTIVE SOIC D 875Green (RoHS &no Sb/Br)CU NIPDAU Level-2-260C-1YEAR REF5025AIDR ACTIVE SOIC D 82500Green (RoHS &no Sb/Br)Call TI Level-2-260C-1YEAR REF5025AIDRG4ACTIVE SOIC D 82500Green (RoHS &no Sb/Br)Call TI Level-2-260C-1YEAR REF5025ID ACTIVE SOIC D 875Green (RoHS &no Sb/Br)CU NIPDAU Level-2-260C-1YEAR REF5025IDG4ACTIVE SOIC D 875Green (RoHS &no Sb/Br)CU NIPDAU Level-2-260C-1YEAR REF5025IDR ACTIVE SOIC D 82500Green (RoHS &no Sb/Br)CU NIPDAU Level-2-260C-1YEAR REF5025IDRG4ACTIVE SOIC D 82500Green (RoHS &no Sb/Br)CU NIPDAU Level-2-260C-1YEAR REF5030AID ACTIVE SOIC D 875Green (RoHS &no Sb/Br)CU NIPDAU Level-2-260C-1YEAR REF5030AIDG4ACTIVE SOIC D 875Green (RoHS &no Sb/Br)CU NIPDAU Level-2-260C-1YEAR REF5030AIDR ACTIVE SOIC D 82500Green (RoHS &no Sb/Br)Call TI Level-2-260C-1YEAR REF5030AIDRG4ACTIVE SOIC D 82500Green (RoHS &no Sb/Br)Call TI Level-2-260C-1YEAR REF5030ID ACTIVE SOIC D 875Green (RoHS &no Sb/Br)CU NIPDAU Level-2-260C-1YEAR REF5030IDG4ACTIVE SOIC D 875Green (RoHS &no Sb/Br)CU NIPDAU Level-2-260C-1YEAR REF5030IDR ACTIVE SOIC D 82500Green (RoHS &no Sb/Br)CU NIPDAU Level-2-260C-1YEAR REF5030IDRG4ACTIVE SOIC D 82500Green (RoHS &no Sb/Br)CU NIPDAU Level-2-260C-1YEAR REF5040AIDACTIVESOICD875Green (RoHS &no Sb/Br)CU NIPDAULevel-2-260C-1YEAR12-Oct-2007Orderable Device Status (1)Package Type Package DrawingPins Package Qty Eco Plan (2)Lead/Ball Finish MSL Peak Temp (3)REF5040AIDG4ACTIVE SOIC D 875Green (RoHS &no Sb/Br)CU NIPDAU Level-2-260C-1YEAR REF5040AIDR ACTIVE SOIC D 82500Green (RoHS &no Sb/Br)Call TI Level-2-260C-1YEAR REF5040AIDRG4ACTIVE SOIC D 82500Green (RoHS &no Sb/Br)Call TI Level-2-260C-1YEAR REF5040ID ACTIVE SOIC D 875Green (RoHS &no Sb/Br)CU NIPDAU Level-2-260C-1YEAR REF5040IDG4ACTIVE SOIC D 875Green (RoHS &no Sb/Br)CU NIPDAU Level-2-260C-1YEAR REF5040IDR ACTIVE SOIC D 82500Green (RoHS &no Sb/Br)CU NIPDAU Level-2-260C-1YEAR REF5040IDRG4ACTIVE SOIC D 82500Green (RoHS &no Sb/Br)CU NIPDAU Level-2-260C-1YEAR REF5045AID ACTIVE SOIC D 875Green (RoHS &no Sb/Br)CU NIPDAU Level-2-260C-1YEAR REF5045AIDG4ACTIVE SOIC D 875Green (RoHS &no Sb/Br)CU NIPDAU Level-2-260C-1YEAR REF5045AIDR ACTIVE SOIC D 82500Green (RoHS &no Sb/Br)Call TI Level-2-260C-1YEAR REF5045AIDRG4ACTIVE SOIC D 82500Green (RoHS &no Sb/Br)Call TI Level-2-260C-1YEAR REF5045ID ACTIVE SOIC D 875Green (RoHS &no Sb/Br)CU NIPDAU Level-2-260C-1YEAR REF5045IDG4ACTIVE SOIC D 875Green (RoHS &no Sb/Br)CU NIPDAU Level-2-260C-1YEAR REF5045IDR ACTIVE SOIC D 82500Green (RoHS &no Sb/Br)CU NIPDAU Level-2-260C-1YEAR REF5045IDRG4ACTIVE SOIC D 82500Green (RoHS &no Sb/Br)CU NIPDAU Level-2-260C-1YEAR REF5050AID ACTIVE SOIC D 875Green (RoHS &no Sb/Br)CU NIPDAU Level-2-260C-1YEAR REF5050AIDG4ACTIVE SOIC D 875Green (RoHS &no Sb/Br)CU NIPDAU Level-2-260C-1YEAR REF5050AIDR ACTIVE SOIC D 82500Green (RoHS &no Sb/Br)Call TI Level-2-260C-1YEAR REF5050AIDRG4ACTIVE SOIC D 82500Green (RoHS &no Sb/Br)Call TI Level-2-260C-1YEAR REF5050ID ACTIVE SOIC D 875Green (RoHS &no Sb/Br)CU NIPDAU Level-2-260C-1YEAR REF5050IDG4ACTIVE SOIC D 875Green (RoHS &no Sb/Br)CU NIPDAU Level-2-260C-1YEAR REF5050IDR ACTIVE SOIC D 82500Green (RoHS &no Sb/Br)CU NIPDAU Level-2-260C-1YEAR REF5050IDRG4ACTIVESOICD82500Green (RoHS &no Sb/Br)CU NIPDAULevel-2-260C-1YEAR(1)The marketing status values are defined as follows:ACTIVE:Product device recommended for new designs.LIFEBUY:TI has announced that the device will be discontinued,and a lifetime-buy period is in effect.NRND:Not recommended for new designs.Device is in production to support existing customers,but TI does not recommend using this part in a new design.PREVIEW:Device has been announced but is not in production.Samples may or may not be available.12-Oct-2007OBSOLETE:TI has discontinued the production of the device.(2)Eco Plan -The planned eco-friendly classification:Pb-Free (RoHS),Pb-Free (RoHS Exempt),or Green (RoHS &no Sb/Br)-please check /productcontent for the latest availability information and additional product content details.TBD:The Pb-Free/Green conversion plan has not been defined.Pb-Free (RoHS):TI's terms "Lead-Free"or "Pb-Free"mean semiconductor products that are compatible with the current RoHS requirements for all 6substances,including the requirement that lead not exceed 0.1%by weight in homogeneous materials.Where designed to be soldered at high temperatures,TI Pb-Free products are suitable for use in specified lead-free processes.Pb-Free (RoHS Exempt):This component has a RoHS exemption for either 1)lead-based flip-chip solder bumps used between the die and package,or 2)lead-based die adhesive used between the die and leadframe.The component is otherwise considered Pb-Free (RoHS compatible)as defined above.Green (RoHS &no Sb/Br):TI defines "Green"to mean Pb-Free (RoHS compatible),and free of Bromine (Br)and Antimony (Sb)based flame retardants (Br or Sb do not exceed 0.1%by weight in homogeneous material)(3)MSL,Peak Temp.--The Moisture Sensitivity Level rating according to the JEDEC industry standard classifications,and peak solder temperature.Important Information and Disclaimer:The information provided on this page represents TI's knowledge and belief as of the date that it is provided.TI bases its knowledge and belief on information provided by third parties,and makes no representation or warranty as to the accuracy of such information.Efforts are underway to better integrate information from third parties.TI has taken and continues to take reasonable steps to provide representative and accurate information but may not have conducted destructive testing or chemical analysis on incoming materials and chemicals.TI and TI suppliers consider certain information to be proprietary,and thus CAS numbers and other limited information may not be available for release.In no event shall TI's liability arising out of such information exceed the total purchase price of the TI part(s)at issue in this document sold by TI to Customer on an annualbasis.12-Oct-2007TAPE AND REEL BOXINFORMATIONDevicePackage Pins SiteReel Diameter (mm)Reel Width (mm)A0(mm)B0(mm)K0(mm)P1(mm)W (mm)Pin1Quadrant REF5020AIDR D 8SITE 4133012 6.4 5.2 2.1812Q1REF5020IDR D 8SITE 4133012 6.4 5.2 2.1812Q1REF5025AIDR D 8SITE 4133012 6.4 5.2 2.1812Q1REF5025IDR D 8SITE 4133012 6.4 5.2 2.1812Q1REF5030AIDR D 8SITE 4133012 6.4 5.2 2.1812Q1REF5030IDR D 8SITE 4133012 6.4 5.2 2.1812Q1REF5040AIDR D 8SITE 4133012 6.4 5.2 2.1812Q1REF5040IDR D 8SITE 4133012 6.4 5.2 2.1812Q1REF5045AIDR D 8SITE 4133012 6.4 5.2 2.1812Q1REF5045IDR D 8SITE 4133012 6.4 5.2 2.1812Q1REF5050AIDR D 8SITE 4133012 6.4 5.2 2.1812Q1REF5050IDRD8SITE 41330126.45.22.1812Q17-Nov-2007DevicePackagePins Site Length (mm)Width (mm)Height (mm)REF5020AIDR D 8SITE 41346.0346.029.0REF5020IDR D 8SITE 41346.0346.029.0REF5025AIDR D 8SITE 41346.0346.029.0REF5025IDR D 8SITE 41346.0346.029.0REF5030AIDR D 8SITE 41346.0346.029.0REF5030IDR D 8SITE 41346.0346.029.0REF5040AIDR D 8SITE 41346.0346.029.0REF5040IDR D 8SITE 41346.0346.029.0REF5045AIDR D 8SITE 41346.0346.029.0REF5045IDR D 8SITE 41346.0346.029.0REF5050AIDR D 8SITE 41346.0346.029.0REF5050IDRD8SITE 41346.0346.029.07-Nov-2007IMPORTANT NOTICETexas Instruments Incorporated and its subsidiaries(TI)reserve the right to make corrections,modifications,enhancements, improvements,and other changes to its products and services at any time and to discontinue any product or service without notice. Customers should obtain the latest relevant information before placing orders and should verify that such information is current and complete.All products are sold subject to TI’s terms and conditions of sale supplied at the time of order acknowledgment.TI warrants performance of its hardware products to the specifications applicable at the time of sale in accordance with TI’s standard warranty.Testing and other quality control techniques are used to the extent TI deems necessary to support this warranty.Except where mandated by government requirements,testing of all parameters of each product is not necessarily performed.TI assumes no liability for applications assistance or customer product design.Customers are responsible for their products and applications using TI components.To minimize the risks associated with customer products and applications,customers should provide adequate design and operating safeguards.TI does not warrant or represent that any license,either express or implied,is granted under any TI patent right,copyright,mask work right,or other TI intellectual property right relating to any combination,machine,or process in which TI products or services are rmation published by TI regarding third-party products or services does not constitute a license from TI to use such products or services or a warranty or endorsement e of such information may require a license from a third party under the patents or other intellectual property of the third party,or a license from TI under the patents or other intellectual property of TI. Reproduction of TI information in TI data books or data sheets is permissible only if reproduction is without alteration and is accompanied by all associated warranties,conditions,limitations,and notices.Reproduction of this information with alteration is an unfair and deceptive business practice.TI is not responsible or liable for such altered rmation of third parties may be subject to additional restrictions.Resale of TI products or services with statements different from or beyond the parameters stated by TI for that product or service voids all express and any implied warranties for the associated TI product or service and is an unfair and deceptive business practice.TI is not responsible or liable for any such statements.TI products are not authorized for use in safety-critical applications(such as life support)where a failure of the TI product would reasonably be expected to cause severe personal injury or death,unless officers of the parties have executed an agreement specifically governing such use.Buyers represent that they have all necessary expertise in the safety and regulatory ramifications of their applications,and acknowledge and agree that they are solely responsible for all legal,regulatory and safety-related requirements concerning their products and any use of TI products in such safety-critical applications,notwithstanding any applications-related information or support that may be provided by TI.Further,Buyers must fully indemnify TI and its representatives against any damages arising out of the use of TI products in such safety-critical applications.TI products are neither designed nor intended for use in military/aerospace applications or environments unless the TI products are specifically designated by TI as military-grade or"enhanced plastic."Only products designated by TI as military-grade meet military specifications.Buyers acknowledge and agree that any such use of TI products which TI has not designated as military-grade is solely at the Buyer's risk,and that they are solely responsible for compliance with all legal and regulatory requirements in connection with such use.TI products are neither designed nor intended for use in automotive applications or environments unless the specific TI products are designated by TI as compliant with ISO/TS16949requirements.Buyers acknowledge and agree that,if they use anynon-designated products in automotive applications,TI will not be responsible for any failure to meet such requirements. Following are URLs where you can obtain information on other Texas Instruments products and application solutions:Products ApplicationsAmplifiers Audio /audioData Converters Automotive /automotiveDSP Broadband /broadbandInterface Digital Control /digitalcontrolLogic Military /militaryPower Mgmt Optical Networking /opticalnetworkMicrocontrollers Security /securityRFID Telephony /telephonyLow Power /lpw Video&Imaging /videoWirelessWireless /wirelessMailing Address:Texas Instruments,Post Office Box655303,Dallas,Texas75265Copyright©2007,Texas Instruments Incorporated。
GSM无线参数简介

无线参数简介1 无线资源各管理对象的包含关系图 (4)2 管理对象参数介绍 (4)2.1 BSC参数 (4)2.1.1 MCC 移动国家号码 (4)2.1.2 MNC 移动网号 (4)2.1.3 InterHo BSC控制小区间切换 (5)2.1.4 IntraHo 是否允许小区内切换 (5)2.1.5 OverLevel 流量控制策略 (5)2.1.6 T1 闭塞/解闭塞周期 (6)2.1.7 T3 7号瞬断的保护时间 (6)2.1.8 T4 全局复位周期 (6)2.1.9 T7 切换请求的保护周期 (7)2.1.10 T8 源BSC切换执行周期 (8)2.1.11 T10 指派周期 (9)2.1.12 T13 全局复位保护周期 (10)2.1.13 T17 流量控制第一过载周期(并入mT11) (11)2.1.14 T18 流量控制第二过载周期(并入mT12) (11)2.1.15 T19 BSS侧电路复位周期 (12)2.1.16 T20 电路群闭塞/解闭塞周期 (12)2.1.17 T9101 监督RLSD消息的接收 (13)2.1.18 T9103 (13)2.1.19 T9104 监督MSC过来的CLEAR COMMAND命令 (14)2.1.20 T9105 监督SCCP连接过程 (15)2.1.21 T9113 监视在目标小区中的外部切换 (15)2.1.22 zxgT1 信道激活保护时间 (16)2.1.23 zxgT2 源实例信道申请保护时间 (17)2.1.24 zxgT3 建链响应保护时间 (17)2.1.25 zxgT4 等待P0对HO COM或ASS COM消息确认的保护时间 (17)2.1.26 zxgT5 监督加密模式修改过程 (17)2.1.27 zxgT6 监督SAPI3建链 (18)2.1.28 zxgT7 等待P0响应指配或切换完成消息的保护时间 (18)2.1.29 zxgT8 切出时HoCmd(to Um)-ClearCmd(from P0) (19)2.1.30 zxgT9 RF Channel Release保护时间 (19)2.1.31 zxgT11 指配排队周期 (19)2.1.32 rmsTqho 切换排队周期 (19)2.1.33 zxgT12 周期性状态证实间隔 (20)2.1.34 zxgT13 监督BTS和MS的模式修改过程 (20)2.1.35 zxgT14 从目标实例发Ass/Ho Com到收到Ass/Ho Com Ack (20)2.1.36 zxgT15 强拆时目标实例等待资源可用时间 (21)2.1.37 zxgT16 定向重试等待时间 (21)2.1.38 zxgmT11 流量控制第一过载时间 (21)2.1.39 zxgmT12 流量控制第二过载时间 (21)2.1.40 Tmirco 微微切换的延时定时器 (22)2.1.41 Tbsic BSIC 解码周期 (22)2.1.42 aisT1 P0指派保护定时器 (22)2.1.43 aisT4 外部切入等待资源保护定时器 (22)2.1.44 aisT8 OutGoHoing状态保护定时器 (23)2.1.45 aisT12 Serving状态保护定时器 (23)2.1.46 BCRT 系统消息广播常规定时器 (23)2.1.47 BCPT 系统消息广播等待FUC应答保护定时器 (23)2.1.48 T3101 立即指派周期 (23)2.1.49 T3103 源小区切换周期 (24)2.1.50 T3107 指派周期 (25)2.1.51 T3109 信道释放周期 (27)2.1.52 T3111 信道去活延时 (28)2.1.53 BMRN BSC复位过程最大重复次数 (29)2.1.54 CMRN 电路复位过程最大重复次数 (29)2.1.55 ConfuMsg 混乱消息 (29)2.1.56 RIndThs 自发指示的门限值 (29)2.1.57 LoadInd 负载指示 (30)2.1.58 LVT 负载有效时间 (30)2.1.59 LIP 负载指示周期 (30)2.1.60 EDRAF 外部定向重试是否允许发送指派失败 (31)2.1.61 ACE 是否允许BSC自己分配地面电路 (31)2.1.62 LocName BSC的位置信息 (31)2.2 B TS(小区)参数 (31)2.2.1 CellType 小区类型 (31)2.2.2 LAC 位置区码 (32)2.2.3 CI 小区识别码 (32)2.2.4 NCC 网络色码 (32)2.2.5 BCC 基站色码 (32)2.2.6 GsmInd 小区的频率带 (32)2.2.7 BCCH 小区BCCH绝对载频号 (33)2.2.8 CA 小区频率集(非BCCH) (33)2.2.9 CcchCfg 公共控制信道配置 (33)2.2.10 T3212 周期性位置更新定时器 (34)2.2.11 MRLTO MS检验无线链路失败的计数器S的最大值 (34)2.2.12 BRLTO BTS检验无线链路失败的计数器S的最大值 (35)2.2.13 T3122 接入尝试的保护周期 (35)2.2.14 PlmnPmt 允许的网络色码 (35)2.2.15 CRH 小区重选滞后 (36)2.2.16 RxLAMin 允许接入的最小接收电平 (36)2.3 R ADIO C ARRIER(载频)参数 (37)2.3.1 PwrClass 对应载频的功率等级 (37)2.3.2 TxPwrRed 功率调整参数 (37)2.3.3 RcList 射频跳频频点列表 (37)2.4 C HANNEL参数 (38)2.4.1 ARFCN 信道对应的频点 (38)2.4.2 ChComb 信道组合方式 (38)2.4.3 TSC 训练序列码 (38)2.5 H ANDOVER C ONTROL参数 (39)2.5.1 HInMin 小区间切换最小间隔 (39)2.5.2 RxLevMin 最小接收强度等级 (39)2.5.3 HoMargin PBGT切换最小门限 (39)2.6 P OWER C ONTROL(功率控制)参数 (40)2.6.1 PCUL 是否上行功率控制 (40)2.6.2 PCDL 是否下行功率控制 (40)2.6.3 MTPMax MS最大功率电平 (40)2.6.4 MTPMin MS最小功率电平 (40)2.6.5 BTPMin BS最小功率电平 (41)3 问题及回答 (41)4 附录 (42)4.1 前后台参数对照表 (42)4.1.1 BSC参数 (42)4.1.2 Bts参数 (45)4.1.3 HandoverControl参数 (51)4.1.4 PowerControl参数 (56)1无线资源各管理对象的包含关系图2管理对象参数介绍2.1BSC参数2.1.1MCC 移动国家号码描述:MCC由三位十进制数组成。
IFR4905

IRF4905HEXFET ® Power MOSFETFifth Generation HEXFETs from International Rectifier utilize advanced processing techniques to achieve extremely low on-resistance per silicon area. This benefit, combined with the fast switching speed and ruggedized device design that HEXFET Power MOSFETs are well known for, provides the designer with an extremely efficient and reliable device for use in a wide variety of applications.The TO-220 package is universally preferred for all commercial-industrial applications at power dissipation levels to approximately 50 watts. The low thermal resistance and low package cost of the TO-220 contribute to its wide acceptance throughout the industry.Parameter Max.UnitsI D @ T C = 25°C Continuous Drain Current, VGS @ -10V -74I D@ T C = 100°C Continuous Drain Current, V GS @ -10V -52A I DMPulsed Drain Current -260P D @T C = 25°C Power Dissipation 200W Linear Derating Factor 1.3W/°C V GS Gate-to-Source Voltage ± 20V E A S Single Pulse Avalanche Energy 930mJ I AR Avalanche Current -38A E AR Repetitive Avalanche Energy 20mJ dv/dt Peak Diode Recovery dv/dt -5.0V/ns T J Operating Junction and -55 to + 175T STGStorage Temperature RangeSoldering Temperature, for 10 seconds 300 (1.6mm from case )°CMounting torque, 6-32 or M3 screw10 lbf in (1.1N m)Absolute Maximum RatingsParameterTyp.Max.UnitsR θJC Junction-to-Case0.75R θCS Case-to-Sink, Flat, Greased Surface 0.50 °C/WR θJAJunction-to-Ambient62Thermal Resistancel Advanced Process Technology l Ultra Low On-Resistance l Dynamic dv/dt Ratingl 175°C Operating Temperature l Fast Switching l P-ChannellFully Avalanche RatedDescription05/24/07PD - 91280DIRF4905Repetitive rating; pulse width limited bymax. junction temperature. ( See fig. 11 )I SD ≤ -38A, di/dt ≤ -270A/µs, V DD ≤ V (BR)DSS ,T J ≤ 175°CNotes:Starting T J = 25°C, L = 1.3mH R G = 25Ω, I AS = -38A. (See Figure 12)Pulse width ≤ 300µs; duty cycle ≤ 2%.Source-Drain Ratings and CharacteristicsIRF4905Fig 4. Normalized On-ResistanceVs. TemperatureFig 1. Typical Output Characteristics Fig 3. Typical Transfer Characteristics11010010000.1110100D DS-I , D r a i n -t o -S o u r c e C u r r e n t (A )-V , Drain-to-Source Voltage (V)11010010000.1110100D DS-I , D r a i n -t o -S o u r c e C u r r e n t (A )-V , Drain-to-Source Voltage (V)110100100045678910GS D -I , D r a i n -t o -S o u r c e C u r r e n t (A )-V , Gate-to-Source Voltage (V)0.00.51.01.52.0-60-40-2020406080100120140160180JT , Junction Temperature (°C)R , D ra i n -t o -S o u r c e O n R e s i s t a n c e D S (o n)(N o r m a l i z e d )Fig 2. Typical Output CharacteristicsIRF4905Fig 8. Maximum Safe Operating AreaFig 6. Typical Gate Charge Vs.Gate-to-Source VoltageFig 5. Typical Capacitance Vs.Drain-to-Source Voltage Fig 7. Typical Source-Drain Diode Forward Voltage01000200030004000500060007000110100C , C a p a c i t a n c e (p F )DS -V , Drain-to-Source Voltage (V)0481216204080120160200GGS -V , G a t e -t o -S o u r c e V o l t a ge (V )Q , Total Gate Charge (nC)11010010000.40.60.81.01.21.41.61.8SD S D -I , R e v e r s e D r a i n C u r r e n t (A )-V , Source-to-Drain Voltage (V)1101001000110100-I , D r a i n C u r r e n t (A )-V , Drain-to-Source Voltage (V)DSDIRF4905Fig 10a. Switching Time Test CircuitFig 10b. Switching Time WaveformsFig 9. Maximum Drain Current Vs.Case TemperatureV DDV VIRF4905Fig 13b. Gate Charge Test CircuitFig 13a. Basic Gate Charge Waveform Fig 12c. Maximum Avalanche EnergyVs. Drain CurrentV-10VDSCurrent Sampling ResistorsFig 12b. Unclamped Inductive WaveformsFig 12a. Unclamped Inductive Test CircuitI ASV DD05001000150020002500255075100125150175JE, S i n g l e P u l s e A v a l a n c h e E n e r g y (m J )AS Starting T , Junction Temperature (°C)IRF4905 Peak Diode Recovery dv/dt Test CircuitV DD* Reverse Polarity of D.U.T for P-ChannelV GS*** V GS = 5.0V for Logic Level and 3V Drive DevicesFig 14. For P-Channel HEXFETSQualification Standards can be found on IR’s Web site. 233 Kansas St., El Segundo, California 90245, USA Tel: (310) 252-7105TAC Fax: (310) 252-7903 Visit us at for sales contact information. 05/07Note: For the most current drawings please refer to the IR website at:/package/。
STM32F050

■ Communication interfaces – 1 x I2C interface; supporting Fast Mode Plus (1 Mbit/s) with 20 mA current sink, SMBus/PMBus, and wakeup from STOP – 1 x USART supporting master synchronous SPI and modem control; one with ISO7816 interface, LIN, IrDA capability auto baud rate detection and wakeup feature – 1 x SPI (18 Mbit/s) with 4 to 16 programmable bit frames, with I2S interface multiplexed
3.5.3 Voltage regulator . . . . . . . . . . . . . . . . . . . . . . . . . . . . . . . . . . . . . . . . . . 14
3.5.4 Low-power modes . . . . . . . . . . . . . . . . . . . . . . . . . . . . . . . . . . . . . . ly schemes . . . . . . . . . . . . . . . . . . . . . . . . . . . . . . . . . . . . . 13
3.5.2 Power supply supervisors . . . . . . . . . . . . . . . . . . . . . . . . . . . . . . . . . . . 13
IC datasheet pdf-OPA4830,pdf(Quad, Low-Power, Single-Supply, Wideband Operational Amplifier)

PRODUCTION DATA information is current as of publication date. Products conform to specifications per the terms of the Texas Instruments standard warranty. Production processing does not necessarily include testing of all parameters.
2
Submit Documentation Feedback Product Folder Link(s): OPA4830
Copyright © 2006–2008, Texas Instruments Incorporated
OPA4830
.................................................................................................................................................... SBOS350A – DECEMBER 2006 – REVISED MAY 2008
APPLICATIONS
• • • • • • SINGLE-SUPPLY ANALOG-TO-DIGITAL CONVERTER (ADC) INPUT BUFFERS SINGLE-SUPPLY VIDEO LINE DRIVERS CCD IMAGING CHANNELS ACTIVE FILTERS PLL INTEGRATORS PORTABLE CONSUMER ELECTRONICS
一种模拟的时钟恢复方法[发明专利]
![一种模拟的时钟恢复方法[发明专利]](https://img.taocdn.com/s3/m/1532b2b7ad02de80d5d8405a.png)
专利名称:一种模拟的时钟恢复方法专利类型:发明专利
发明人:迟蕾
申请号:CN201110424455.2
申请日:20111216
公开号:CN102497244A
公开日:
20120613
专利内容由知识产权出版社提供
摘要:本发明提供的一种模拟的时钟恢复方法,根据IEEE1588协议的时钟调整算法计算出来的时钟频率差和相位差,模拟时钟频率和相位的恢复,以在不具备硬件时钟恢复能力的设备上实现时钟恢复;并且通过整数计算获得本地时钟恢复后的时间,避免浮点数计算精度不高的问题,并在确定本地时钟恢复后的时间时累加执行方法所需时间,进一步提高了时间精度,进而提供一个时钟精度达到微秒级的时间通过整数计算获得本地时钟恢复后的时间,且避免浮点数计算精度不高的问题,并在确定本地时钟恢复后的时间时累加执行方法所需时间,提高了时间精度。
申请人:瑞斯康达科技发展股份有限公司
地址:100085 北京市海淀区上地六街28号院2号楼
国籍:CN
代理机构:北京德琦知识产权代理有限公司
更多信息请下载全文后查看。
雷维顿Decora壁栅式PIR人员检测自适应技术电源开关说明书

M D S 15Decora ® Wall Switch PIR Lev-Lok ® Occupancy Sensor with Self-Adaptive TechnologyBASIC OPERATIONThe Leviton Decora ® Wall Switch Passive Infrared (PIR) Lev-Lok ® Occupancy Sensor (MDS15) uses PIR detec tion technology to monitor a room for occupancy through asegmented Fresnel lens. This specialized lens divides the field-of-view into sensor zones. When a person passes into or out of a sensor zone, the sensor detects motion and switches the lights ON. The lights will remain ON as long as there is an occupant moving through the sensor zones.A delayed-OFF time adjustment prevents the lights from switching OFF when the space is occupied. In order to keep the lights ON, a person must pass through a sensor zone atleast once during the selected delayed-OFF time interval. An LED indicator blinks each time the unit detects activity in the sensor zones. When the space being monitored by the sensor isunoccupied for the length of time chosen as the delayed-OFF interval, the unit will beep 3 times. Ten seconds after the last warning beep, the unit will switch the lights OFF.LEV-LOK TECHNOLOGYLev-Lok’s innovative design streamlinesinstallation and reduces costs. In just two easy steps, the wiring device is securely attached to the wiring module.Place the wiring module over the device’s connection pins and twist clockwise tolock. Replacement is just as easy—just turn counter-clockwise to unlock and remove. The module is keyed so that it cannot be installed incorrectly. This not only saves time during the initial installation, but makes maintenance applications quicker, safer and easier as well.APPLICATIONSThe MDS15 is used to provide automatic lighting control for energy savings and convenience in a variety of commercial applications, including:• Small offices• Heavier loads • Private restrooms • Lounges • Storage areas • Classrooms• Conference roomsThe MDS15 can be used for automatic switching of incandescent lamps and low-voltage lighting with electronic and magnetic ballasts. The unit also features a manual override switch that can be used to keep lights OFF while an area is occupied, which may be desired in conference rooms and other areas during slide or film presentations. The unit installs in place of asingle-pole wall switch and fits in a standard wallbox. The unit requires a ground connection.MDS15Leviton Manufacturing Co., Inc. Global Headquarters201 North Service Road, Melville, NY 11747-3138 tech line 800-824-3005 fax 800-832-9538©2017 Leviton Manufacturing Co., Inc. All rights reserved. Subject to change without notice.PRODUCT DATA15FEATURES• Fits in standard wallbox and replaces single-pole wall switch; ground connection required. Gangable with other units• Low-profile design eliminates obtrusive“scanning-device” look. Elegant Decora wallplates compliment any interior for sleek aesthetics; uses Decora wallplates and coordinates with Leviton’s popular line of Decora wiring devices• 180° field-of-view provides approximately 2,100 square feet of coverage suitable for small offices, conference rooms, class rooms, stock rooms, lounges, private restrooms and a variety of commercial areas• Convenient pushbutton provides manual-ON/OFF light switching at any time• Two dual element PIR sensors used to widen detection range• Segmented Fresnel lens provides optimum sensitivity and performance. Designed with an extensive “minor motion” area where even slight body movements will be detected • Vandal resistant PIR lens• Lev-Lok makes installation and replacement simple with latch-and-lock system which streamlines installation and reduces costs• The Lev-Lok wiring module is keyed so that itcannot be installed incorrectly, saving time during installation and making maintenance quicker, safer and easier• Blinders—horizontal field-of-view may be adjusted between 180° and 60° of arc by using integral blinders located on either side of the lens. No masking tape required• Manual-ON/auto-OFF mode for installations where manual ON switching is required but auto-OFF switching is still desired• Red LED indicator light flashes when PIR sensor detects motion to verify detection is active• Time Delay—in adapting mode, the time delay can be configured from 30s (test mode), 5, 10 and 20 minutes. In non-adapting mode, the delay can be configured from 5, 10, 20 and 30 minutes• Light sensor adjustable Ambient Light Override ranges from approximately 2FC (20LUX) to 500+FC (5,000+LUX) to prevent lights from turning ON automatically during periods of ample natural light, increasing energy savings• Light sensor enables the load hold-OFF feature once level has been set• Self-adjusting delayed-OFF time intervalcompensates for real-time occupancy patterns, preventing unnecessary ON/OFF switching• Exclusive Walk-through feature provides increased energy savings by not leaving the lights ON for an extended period after only momentary occupancy • False detection circuitry• Presentation Mode feature for slide or filmpresentations allows pushbuttons to turn lights OFF and keep them OFF while the room is occupied • Additional manual service switch provided for installer to force lights to hold-OFF or hold-ON during installation• Beep Warn—unit beeps 3 times after delayed-OFF time expires, then waits 10 seconds before turning lights OFF• Exclusive Leviton High Inrush Stability (H.I.S.)Circuitry—specifically designed to handle today’s high inrush electronic ballast loads and offer unmatched durability and service.• Relay switches at the zero crossing point of the AC power curve to ensure maximum contact life and compatibility with electronic ballasts • No neutral design in optional for retrofit applicationsFIELD-OF-VIEWThe MDS15 provides a 180° field of view with a maximum coverage area of approximately 2,100 square feet. The maximum sensing distance in front of the sensor is 40 feet, and at each side is 30 feet. The “minor motion” zone detects relatively small body movements and allows the lights to stay ON even though a person may not be moving or walking around the room. The remainder of the field-of-view, the “major motion” zone, exhibits a lesser degree of sensitivity and requires larger movements.MDS15Field-of-View (in feet)M D S 15DIMENSIONAL DIAGRAMSBLINDERSRANGE TIMELIGHT 10203047104710Mounting YokeVandal Resistant PIR Lens LED Window & Light Sensor PushbuttonControl Panel,Cover Removed BlindersHot (Black)LoadBlackGreen GroundBlueLine120-230-277VAC,50/60 HzNeutral (White)BlackWhiteNote: Ground must be connectedMDS15 Two-Location ControlWIRING DIAGRAMSHot (Black)LoadBlackGreen GroundBlue BlueGreen GroundLine120-230-277VAC,50/60 HzNeutral (White)BlackWhiteBlackNote: Ground must be connectedMDS15 Single Location Control 4.06”(103.12mm) 3.28”(83.31mm)1.75”(44.45mm)3.81”(96.77mm)0.12”(3.05mm)0.88”(22.35mm)1.83”(46.48mm)0.46”(11.68mm)2.67”(67.82mm)LEV-LOK DIAGRAM LEV-LOK DIMENSIONS3. Turn and lock flush4. Push latch up and turn to release1. Remove protective label2. Orient and push1.58"(40.1m m )1.50"(38.1mm)0.40"(10.2mm)MSPSW-XSxLeviton Manufacturing Co., Inc. Global Headquarters201 North Service Road, Melville, NY 11747-3138 tech line 800-824-3005 fax 800-832-9538 ©2017 Leviton Manufacturing Co., Inc. All rights reserved. Subject to change without notice.PRODUCT DATAG-8709B/K17-aa REV NOV 201715INSTALLATIONThe MDS15 is preset to deliver optimumperformance in a wide variety of applicationswithout requiring any adjustments during installation. Exclusive self-adjusting operating features willautomatically compensate for real-time occupancy patterns to provide maximum convenience and energy savings. The unit may replace a single-pole wall switch mounted in a standard wallbox.The unit must be properly grounded in order to operate. The unit’s integral blinders may be used to restrict the field-of-view to prevent unwanted detection of hallway traffic. It should be positioned at least 6 feet away from HVAC registers. Theswitch located under the push-button provides three operational setting: “ON” holds the lighting load ON (motion detection not active), “OFF” disconnects the lighting load from the power for relamping purposes, and “AUTO” activates automatic motion detection. Note that whenever the unit is powered up, it will take approximately 1 minute to begin normal operation.To indicate color, add suffix to the end of the catalog number. White (-W) , Ivory (-I), and Ebony (-E).SPECIFICATIONS Leviton Manufacturing Co., Inc. Global Headquarters201 North Service Road, Melville, NY 11747-3138 tel 800-323-8920 fax 800-832-9538 tech line (8:30AM-7:00PM ET Mon-Fri) 800-824-3005Leviton Manufacturing Co., Inc. Energy Management, Controls and Automation20497 SW Teton Avenue, Tualatin, OR 97062 tel 800-736-6682 fax 503-404-5594 tech line (6:00AM-4:00PM PT Mon-Fri) 800-959-6004Visit our Website at: /sensors©2017 Leviton Manufacturing Co., Inc. All rights reserved. Subject to change without notice.。
Skyworks Solutions SKY12406-360LF 1-Bit 数字衰减器数据手册说

SKY12406-360LF: GaAs IC 1-Bit Digital Attenuator 12 dB LSB 50 MHz–600 MHzdata sheetFeatureslP ositive voltage control (0/+3 V)l H igh bit accuracy l L ow loss l A bsorptive in 50 W systems l P ackaged lead (Pb)-free, RoHS-compliant and Green™Functional DiagramV CTL2V CTL1RF In/OutDescriptionThe SKY12406-360LF is a pHEMT GaAs FET IC single bit attenu-ator packaged in an 2 x 2 mm 8-lead exposed pad plastic package for low-cost commercial applications. This attenuator has an LSB of 12 dB. The SKY12406-360LF is particularly suited where high attenuation accuracy, low insertion loss, and low intermodulation products are required. Typical applications include cellular radio, wireless data, and wireless local loop gain level control circuits.Electrical SpecificationsV CTL = 0 V/3 V, T = 25 °C, P INPUT = 0 dBm, Z o = 50 W, unless otherwise notedParameterFrequency Min.typ.Max.Unit Insertion Loss 50 MHz–600 MHz 0.30.4dB Attenuation 50 MHz–600 MHz 11.61212.4dB Return Loss50 MHz–600 MHz1520dBSkyworks Green™ products are RoHS (Restriction of Hazardous Substances)-compliant, conform to the EIA/EICTA/JEITA Joint Industry Guide (JIG) Level A guidelines, are halogen free according to IEC-61249-2-21, and contain <1,000 ppm antimony trioxide in polymeric materials.Data Sheet • SKY12406-360LFty pical Insertion Loss-1-0.9-0.8-0.7-0.6-0.5-0.4-0.3-0.2-0.1000.10.20.30.40.50.60.70.80.9 1.0Frequency (GHz)d B0.10.20.30.40.50.60.70.80.9 1.0Frequency (GHz)Input Return Los sty pical Return Loss (Insertion Loss State)-50-45-40-35-30-25-20-15-10-50d Btypical attenuation0.10.20.30.40.50.60.70.80.9 1.0Frequency (GHz)dB-13.0-12.8-12.6-12.4-12.2-12.0-11.8-11.6-11.4-11.2-11.0ty pical Return Loss (attenuation State)-50-45-40-35-30-25-20-15-10-50d B0.10.20.30.40.50.60.70.80.9 1.0Frequency (GHz)sOutput Return LossTypical Performance DataV CTL = 3 V, T = 25 °C, P INPUT = 0 dBm, Z o = 50 W , C BLK = 560 pF, C BP = 560 pF, unless otherwise notedoperating CharacteristicsV= 0 V/3 V, T = 25 °C, P = 0 dBm, Z = 50 W , unless otherwise notedData Sheet • SKY12406-360LFSkyworksSolutions,Inc.•Phone[781]376-3000•Fax[781]376-3100•*********************•Bottom ViewPin 1Pin 8Pin outAbsolute Maximum RatingsPerformance is guaranteed only under the conditions listed in the specifications table and is not guaranteed under the full range(s) described by the Absolute Maximum specifications.Exceeding any of the absolute maximum/minimum specifications may result in permanent damage to the device and will void the warranty.CAUTION: A lthough this device is designed to be as robust aspossible, ESD (Electrostatic Discharge) can damage this device. This device must be protected at all times from ESD. Static charges may easily produce potentials of several kilovolts on the human body or equipment, which can discharge without detection. Industry-standard ESD precautions must be employed at all times.CharacteristicValue RF input power @ 3 V 24 dBm at 50 MHz 27 dBm at 600 MHz Operating temperature-40 °C to +85 °C Storage temperature-65 °C to +150 °CTruth Table1 = 3 V.0 = 0 V.Any state other than described in the truth table will put the attenuator in an undefined state.If a non-described state occurs, no damage to the attenuator will occur.DC blocks are required on RF1 and RF2. C BLK = 560 pF for 50 MHz operation.C BP = 560 pF for 50 MHz operation.V CtL1V CtL2RF1–RF210Insertion loss 01AttenuationPin DescriptionsPin NumberPin Name description1RF1RF port 2GND Ground3V CTL1DC control voltage4C BP RF GND, must be AC coupled to ground 5GND Ground6V CTL2DC control voltage 7GND Ground 8RF2RF portExposed PaddlePaddleMust be connected to RF groundRecommended Solder Reflow ProfilesRefer to the “Recommended Solder Reflow Profile” Application Note.Tape and Reel InformationRefer to the “Discrete Devices and IC Switch/Attenuators Tape and Reel Package Orientation” Application Note.Data Sheet • SKY12406-360LF0.20 Ref.Seating PlaneC BLK = 560 pF (0402 size) 4 places C = 560 pF (0402 size) 1 placesV CTL1CTL2QFN 8L 2 x 2 mm PackageEvaluation BoardSuggested Land Pattern (Top View)Data Sheet • SKY12406-360LFSkyworksSolutions,Inc.•Phone[781]376-3000•Fax[781]376-3100•*********************•Copyright © 2008, Skyworks Solutions, Inc. All Rights Reserved.Information in this document is provided in connection with Skyworks Solutions, Inc. (“Skyworks”) products or services. These materials, including the information contained herein, are provided by Skyworks as a service to its customers and may be used for informational purposes only by the customer. Skyworks assumes no responsibility for errors or omissions in these materials or the information contained herein. Skyworks may change its documentation, products, services, specifications or product descriptions at any time, without notice. Skyworks makes no commitment to update the materials or information and shall have no responsibility whatsoever for conflicts, incompatibilities, or other difficulties arising from any future changes.No license, whether express, implied, by estoppel or otherwise, is granted to any intellectual property rights by this document. Skyworks assumes no liability for any materials, products or information provided hereunder, including the sale, distribution, reproduction or use of Skyworks products, information or materials, except as may be provided in Skyworks Terms and Conditions of Sale.THE MATERIALS, PRODUCTS AND INFORMATION ARE PROVIDED “AS IS” WITHOUT WARRANTY OF ANY KIND, WHETHER EXPRESS, IMPLIED, STATUTORY, OR OTHERWISE, INCLUDING FITNESS FOR A PARTICULAR PURPOSE OR USE, MERCHANTABILITY, PERFORMANCE, QUALITY OR NON-INFRINGEMENT OF ANY INTELLECTUAL PROPERTY RIGHT; ALL SUCH WARRANTIES ARE HEREBY EXPRESSLY DISCLAIMED. SKYWORKS DOES NOT WARRANT THE ACCURACY OR COMPLETENESS OF THE INFORMATION, TEXT, GRAPHICS OR OTHER ITEMS CONTAINED WITHIN THESE MATERIALS. SKYWORKS SHALL NOT BE LIABLE FOR ANY DAMAGES, INCLUDING BUT NOT LIMITED TO ANY SPECIAL, INDIRECT, INCIDENTAL, STATUTORY, OR CONSEQUENTIAL DAMAGES, INCLUDING WITHOUT LIMITATION, LOST REVENUES OR LOST PROFITS THAT MAY RESULT FROM THE USE OF THE MATERIALS OR INFORMATION, WHETHER OR NOT THE RECIPIENT OF MATERIALS HAS BEEN ADVISED OF THE POSSIBILITY OF SUCH DAMAGE.Skyworks products are not intended for use in medical, lifesaving or life-sustaining applications, or other equipment in which the failure of the Skyworks products could lead to personal injury, death, physical or environmental damage. Skyworks customers using or selling Skyworks products for use in such applications do so at their own risk and agree to fully indemnify Skyworks for any damages resulting from such improper use or sale.Customers are responsible for their products and applications using Skyworks products, which may deviate from published specifications as a result of design defects, errors, or operation ofproducts outside of published parameters or design specifications. Customers should include design and operating safeguards to minimize these and other risks. Skyworks assumes no liability for applications assistance, customer product design, or damage to any equipment resulting from the use of Skyworks products outside of stated published specifications or parameters. Skyworks, the Skyworks symbol, and “Breakthrough Simplicity” are trademarks or registered trademarks of Skyworks Solutions, Inc., in the United States and other countries. Third-party brands and names are for identification purposes only, and are the property of their respective owners. Additional information, including relevant terms and conditions, posted at , are incorporated by reference.。
Fujitsu F50单栈媒体 货币发放器说明书

Currency Handling SolutionsEconomical, Compact, and Reliable Bill Dispensing UnitF50 Combines Compact Design with High Reliability Cash DispensingEnhanced Features• Double pick detection ensures proper media handling andaccurate media counts.• Media can be presented using front or side delivery tray for maximuminstallation and integration flexibility• On-board predictive diagnostics through sensors can detect a problembefore an actual hard failure• Adjustable storage area can support domestic and most internationalcurrencies• Pick mechanism can reliably dispense mixed new and used currency andmixed paper and polymer currency.Benefits• Simple design allows complete access to cash path therebylowering down time and 2ndline calls.• Bill low sensor provides notice when media replenishment is duepromoting higher uptime, lower overall costs and greater surcharge revenue.• Divert tray ensures only fit bills are presented to increasing end-customersatisfaction.• Solid, industrial-grade tooled steel provides greater strength andreliability in the harshest conditions. All at an entry level price.• Flexible design protects OEM investment by providing maximum numberof application possibilities.IntDimensions (W x D x H )278mm x 152mm x 329mm Weight 7kgMaximum Capacity1,200 new notes (approx.) 150mmMaximum Dispense99 notes per transactionService AreaFront and side service accessOut of note sensorOptional Reject Area Capacity20 notesAcceptable Media RangeMax. (mm) 82mm x 165 mm Mín. (mm) 65mm x 130 mmF50 Solution OverviewWith over 30-years’ experience in designing andbuilding media dispensing devices of legendary quality, Fujitsu has expanded the family of products available to its OEM sales channel to meet the needs of a greater number of applications.The Fujitsu model F50 media dispenser offers important features at a very low price point – all without any sacrifice of quality or reliability. Compact in size, but packed with functionality, the F50 will drive down your production costs and decrease the total cost ofownership for your customers through higher reliability and reduced maintenance.The F50 offer many features usually found only on more expensive units. For example double-pick detection ensures proper media dispensing, and advancedonboard and remote diagnostics provide the ability to detect sensor problems before actual failure. Most importantly, the F50 is a solid, rugged industrial-grade unit that will continue to run and run with limited manual intervention or maintenance.F50 Single Denomination Bill DispenserThe F50 also provides you with maximum flexibility in final product design. It can be installed in either a wide-and-shallow or a narrow-and-deep profile using the available front side delivery tray. This design enables servicing and replenishment from the front or side.The adjustable storage bin can be used for a variety of media sizes enabling you to use the same dispenser for domestic or international currency. The F50 is capable of dispensing over 50 of the world’s most popular currency . With the F50’s small footprint, high-end features, reliability and low maintenance – now you have the opportunity to get an advanced, flexible media dispenser at an entry-level price and better satisfy the cost-of-ownership requirements of your customers.So whether your applications include low-end ATMs, bill breakers or media dispensers, you should look at the F50 from Fujitsu.Thickness (mm)0.07 ~ 0.15 Processing Speed1.5 notes per secondInterface Specifications RS232CElectrical RequirementsDC +24V +/- 10% Avg. 2A Peak4ATemperatureOperation: 0°C - 40°C Stop State:-5°C - 50°CRelative HumidityOperation: 10% - 85% Stop State: 8% - 95%RoHS Compliant Yes UL ComplianceFujitsu Frontech North América, Inc., reserves the right to change specifications without noticeFormoreinformation,call(877)******************************.comorvisitusat:F ujitsu F r on t e c h North America, Inc. www .fujitsuf ron t e c 27121 T owne Centre Drive, Suite 100, F oo thill Ranch, C A . 92610©2014 Copyright F ujitsu F r on t e c h North America Inc. All rights reserved. F ujitsu and the F ujitsu logo are registered trademarks. All other trademarksare the property of their respective owners. S t a t ements herein are based on normal operating conditions and are not intended to c rea t e any implied warranty of merchantability or fitness for a particular purpose. Fujitsu Frontech North America, Inc. reserves the right to modify, at any time without notice, these statements, our services, products, and their warranty and performance specifications . .Fujitsu Frontech North AmericaYes F50 Product SpecificationsF50_DS_071614。
手机射频校准错误代码表
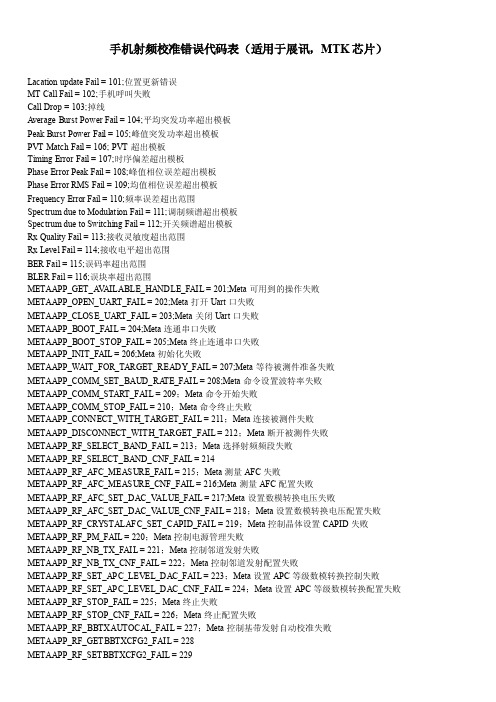
手机射频校准错误代码表(适用于展讯,MTK芯片)Lacation update Fail = 101;位置更新错误MT Call Fail = 102;手机呼叫失败Call Drop = 103;掉线A verage Burst Power Fail = 104;平均突发功率超出模板Peak Burst Power Fail = 105;峰值突发功率超出模板PVT Match Fail = 106; PVT超出模板Timing Error Fail = 107;时序偏差超出模板Phase Error Peak Fail = 108;峰值相位误差超出模板Phase Error RMS Fail = 109;均值相位误差超出模板Frequency Error Fail = 110;频率误差超出范围Spectrum due to Modulation Fail = 111;调制频谱超出模板Spectrum due to Switching Fail = 112;开关频谱超出模板Rx Quality Fail = 113;接收灵敏度超出范围Rx Level Fail = 114;接收电平超出范围BER Fail = 115;误码率超出范围BLER Fail = 116;误块率超出范围METAAPP_GET_A V AILABLE_HANDLE_FAIL = 201;Meta可用到的操作失败METAAPP_OPEN_UART_FAIL = 202;Meta打开Uart口失败METAAPP_CLOSE_UART_FAIL = 203;Meta关闭Uart口失败METAAPP_BOOT_FAIL = 204;Meta连通串口失败METAAPP_BOOT_STOP_FAIL = 205;Meta终止连通串口失败METAAPP_INIT_FAIL = 206;Meta初始化失败METAAPP_WAIT_FOR_TARGET_READY_FAIL = 207;Meta等待被测件准备失败METAAPP_COMM_SET_BAUD_RA TE_FAIL = 208;Meta命令设置波特率失败METAAPP_COMM_START_FAIL = 209;Meta命令开始失败METAAPP_COMM_STOP_FAIL = 210;Meta命令终止失败METAAPP_CONNECT_WITH_TARGET_FAIL = 211;Meta连接被测件失败METAAPP_DISCONNECT_WITH_TARGET_FAIL = 212;Meta断开被测件失败METAAPP_RF_SELECT_BAND_FAIL = 213;Meta选择射频频段失败METAAPP_RF_SELECT_BAND_CNF_FAIL = 214METAAPP_RF_AFC_MEASURE_FAIL = 215;Meta测量AFC失败METAAPP_RF_AFC_MEASURE_CNF_FAIL = 216;Meta测量AFC配置失败METAAPP_RF_AFC_SET_DAC_V ALUE_FAIL = 217;Meta设置数模转换电压失败METAAPP_RF_AFC_SET_DAC_V ALUE_CNF_FAIL = 218;Meta设置数模转换电压配置失败METAAPP_RF_CRYSTALAFC_SET_CAPID_FAIL = 219;Meta控制晶体设置CAPID失败METAAPP_RF_PM_FAIL = 220;Meta控制电源管理失败METAAPP_RF_NB_TX_FAIL = 221;Meta控制邻道发射失败METAAPP_RF_NB_TX_CNF_FAIL = 222;Meta控制邻道发射配置失败METAAPP_RF_SET_APC_LEVEL_DAC_FAIL = 223;Meta设置APC等级数模转换控制失败METAAPP_RF_SET_APC_LEVEL_DAC_CNF_FAIL = 224;Meta设置APC等级数模转换配置失败METAAPP_RF_STOP_FAIL = 225;Meta终止失败METAAPP_RF_STOP_CNF_FAIL = 226;Meta终止配置失败METAAPP_RF_BBTXAUTOCAL_FAIL = 227;Meta控制基带发射自动校准失败METAAPP_RF_GETBBTXCFG2_FAIL = 228METAAPP_RF_SETBBTXCFG2_FAIL = 229METAAPP_RF_SETAFCSINEWA VEDETECT_FAIL = 230METAAPP_RF_SET_MT6140CW2_TO_REG_FAIL = 231METAAPP_RF_GET_MT6140ACODE_FROM_REG_FAIL = 232 METAAPP_RF_GET_RFID_FAIL = 233METAAPP_RF_GET_IMMEIDA TE_BSI_FAIL = 234METAAPP_RF_SET_IMMEIDA TE_BSI_FAIL = 235METAAPP_RF_MULTISLOT_TX_FAIL = 236;Meta控制多时隙发射失败METAAPP_RF_EPSK_SET_APC_LEVEL_DAC_FAIL = 237METAAPP_NVRAM_INIT_FAIL = 238;Meta控制NVRAM初始化失败METAAPP_NVRAM_AFC_SLOPE_INV ALID_FAIL = 239METAAPP_NVRAM_AGC_PA THLOSS_LEN_FAIL = 240METAAPP_NVRAM_GET_REC_LEN_FAIL = 241METAAPP_NVRAM_GET_RAMPTABLE_LEN_FAIL = 242METAAPP_NVRAM_COMPOSE_AGC_PA THLOSS_FAIL = 243 METAAPP_NVRAM_DECOMPOSE_AGC_PA THLOSS_FAIL = 244 METAAPP_NVRAM_COMPOSE_RAMPTABLE_FAIL = 245 METAAPP_NVRAM_DECOMPOSE_RAMPTABLE_FAIL = 246 METAAPP_NVRAM_SET_REC_FIELD_V ALUE_FAIL = 247 METAAPP_NVRAM_GET_REC_FIELD_V ALUE_FAIL = 248 METAAPP_NVRAM_COMPOSE_ADC_CAL_TABLE_FAIL = 249 METAAPP_NVRAM_DECOMPOSE_ADC_CAL_TABLE_FAIL = 250 METAAPP_NVRAM_COMPOSE_BARCODE_FAIL = 251METAAPP_NVRAM_DECOMPOSE_BARCODE_FAIL = 252 METAAPP_NVRAM_COMPOSE_IMEI_FAIL = 253METAAPP_NVRAM_DECOMPOSE_IMEI_FAIL = 254METAAPP_NVRAM_COMPOSE_IP2_FAIL = 255METAAPP_NVRAM_DECOMPOSE_IP2_FAIL = 256METAAPP_NVRAM_WRITE_FAIL = 257METAAPP_NVRAM_WRITE_CNF_FAIL = 258METAAPP_NVRAM_READ_FAIL = 259METAAPP_NVRAM_READ_CNF_FAIL = 260METAAPP_NVRAM_COMPOSE_SECURITY_FAIL = 261METAAPP_NVRAM_DECOMPOSE_SECURITY_FAIL = 262 METAAPP_NVRAM_GET_TXIQ_LEN_FAIL = 263METAAPP_NVRAM_COMPOSE_TXIQ_FAIL = 264METAAPP_NVRAM_DECOMPOSE_TXIQ_FAIL = 265METAAPP_NVRAM_COMPOSE_SETTINGBAND_FAIL = 266 METAAPP_NVRAM_DECOMPOSE_SETTINGBAND_FAIL = 267 METAAPP_NVRAM_COMPOSE_CUST_ACOUSTIC_FAIL = 268 METAAPP_NVRAM_DECOMPOSE_CUST_ACOUSTIC_FAIL = 269 METAAPP_NVRAM_LOCK_FAIL = 270METAAPP_FILE_READ_FAIL = 271METAAPP_FILE_WRITE_FAIL = 272METAAPP_IMEI_CALCULA TE_CD_FAIL = 273METAAPP_ADC_READ_FROM_NVRAM_CNF_FAIL = 274 METAAPP_ADC_MEASURE_FAIL = 275METAAPP_ADC_MEASURE_CNF_FAIL = 276METAAPP_GET_VERSION_INFO_FAIL = 277METAAPP_GET_VERSION_INFO_CNF_FAIL = 278METAAPP_FA T_OPEN_FAIL = 279METAAPP_FA T_CLOSE_FAIL = 280METAAPP_FA T_GET_FILE_SIZE_FAIL = 281METAAPP_FA T_READ_TO_FILE_FAIL = 282METAAPP_FA T_WRITE_BY_FILE_FAIL = 283METAAPP_FA T_DELETE_FAIL = 284METAAPP_FA T_FIND_START_FAIL = 285METAAPP_FA T_FIND_HEAD_FAIL = 286METAAPP_FA T_FIND_PREV_FAIL = 287METAAPP_FA T_FIND_NEXT_FAIL = 288METAAPP_FA T_FIND_GET_DISK_INFO_FAIL = 289METAAPP_FA T_GET_DISK_INFO_FAIL = 290METAAPP_QUERY_TWO_APC_DC_OFFSET_SUPPORT_FAIL = 291METAAPP_BT_ADDRESS_FORMA T_FAIL = 292;Meta控制蓝牙地址格式化失败METAAPP_WIFI_SET_REGDOMAIN_FAIL = 293;Meta控制WIFI设置注册表失败METAAPP_WIFI_SET_TXPOWER_FAIL = 294;Meta控制WIFI设置发射功率失败METAAPP_WIFI_CONTTX_FAIL = 295;Meta控制WIFI连续发射失败METAAPP_WIFI_CSM_FAIL = 296METAAPP_WIFI_CONTPKTTX_FAIL = 297METAAPP_WIFI_QUERY_TX_STA TUS_FAIL = 298;Meta查询发射状态失败METAAPP_WIFI_CONTPKTRX_FAIL = 299;METAAPP_WIFI_QUERY_RX_STA TUS_FAIL = 300;Meta查询接收状态失败METAAPP_WIFI_QUERY_RX_COUNTER_FAIL = 301;Meta查询WIFI接收计数器失败METAAPP_WIFI_QUERY_CHIPCAP_FAIL = 302;Meta查询WIFI芯片上面容值失败METAAPP_WIFI_QUERY_CHANNELLIST_FAIL = 303;Meta查询WIFI通道清单失败METAAPP_WIFI_STOP_FAIL = 304;Meta停止Wifi失败METAAPP_TIMEOUT_FAIL = 305;Meta延时失败BARCODE_LIMIT_FAIL = 306;条形码极限超出范围AFC Calibration Fail = 501;AFC校准失败1顶针与RF头是否接触良好,是否因没有接触好而导致损耗大了。
86105

Agilent 86100CWide-Bandwidth Oscilloscope Mainframe and ModulesTechnical Specifi cationsDCA-J• Accurate compliancetesting of optical transceivers • Automated jitter and amplitude interference decomposition• Internally generated pattern trigger• Modular platform for testing waveforms to 40 Gb/s and beyond• Broadest coverage of data rates with optical reference receivers, electrical channels, and clock recovery • Built-in S-parameters with TDR measurements • Compatible with Agilent 86100A/B-series, 83480A-series,and 54750-series modules • < 100 fs intrinsic jitter• Open operating system – Windows ® XP ProFour instruments in oneA digital communications analyzer,a full featured wide-bandwidth oscilloscope, a time-domain refl ectometer, and a jitter analyzerTable of ContentsOverviewFeatures3 Eye-diagram/mask test4 Jitter analysis5 Equalization and amplitude analysis6 Jitter spectrum/PLL bandwidth7 TDR/TDT/S-parameters7 Measurements8 Additional capabilities9 Clock recovery10 Specifi cationsMainframe & triggering(includes precision time base moduleand precision waveform analyzer module) 13 Computer system & storage16 ModulesOverview 17 Module selection table 18 Specifi cationsMultimode/single-mode 19 Single-mode 21 Dual electrical 23 TDR 25 Clock recovery 27 Ordering Information29Overview of Infi niium DCA-J FeaturesFour instruments in oneThe 86100C Infi niium DCA-J can be viewed as fourhigh-powered instruments in one:• A general-purpose wide-bandwidth sampling oscilloscope. PatternLock triggering signifi cantly enhances the usability as a general purpose scope.• A digital communications analyzer• A time domain refl ectometer• A precision jitter and amplitude interference analyzer Just select the desired instrument mode and start making measurements.Confi gurable to meet your needsThe 86100C supports a wide range of modules for testing both optical and electrical signals. Select modules to get the specifi c bandwidth, fi ltering, and sensitivity you need. Digital communications analysisAccurate eye-diagram analysis is essential for characterizing the quality of transmitters usedfrom 100 Mb/s to 40 Gb/s. The 86100C is designedspecifi cally for the complex task of analyzing digital communications waveforms. Compliance mask and parametric testing no longer require a complicated sequence of setups and confi gurations. If you can pressa button, you can perform a complete compliance test. The important measurements you need are right at your fi ngertips, including:• i ndustry standard mask testing with built-inmargin analysis• e xtinction ratio measurements with accuracy andrepeatability• e ye measurements: crossing %, eye height and width,‘1’ and ‘0’ levels, jitter, rise or fall times and moreThe key to accurate measurements of lightwave communications waveforms is the optical receiver. The 86100C has a broad range of precision receivers integrated within the instrument.• B uilt-in photodiodes, with fl at frequency responses, yield the highest waveform fi delity. This provideshigh accuracy for extinction ratio measurements.• S tandards-based transmitter compliance measurements require fi ltered responses. The 86100C offers a broad range of fi lter combinations. Filters can be automatically and repeatably switched in or out of the measurement channel remotely over GPIB or with a front panel button. The frequency response of the entire measurement path is calibrated, and will maintainits performance over long-term usage.• T he integrated optical receiver provides a calibrated optical channel. With the accurate optical receiver built into the module, optical signals are accurately measured and displayed in optical power units.• S witches or couplers are not required for an average power measurement. Signal routing is simplifi ed and signal strength is maintained.Windows is a U.S. registered trademark of Microsoft Corporation.Eye diagram mask testingThe 86100C provides effi cient, high-throughput waveform compliance testing with a suite of standards based eye-diagram masks. The test process has been streamlined into a minimum number of keystrokes for testing at industry standard data rates.Standard formatsRate (Mb/s)1X Gigabit Ethernet 12502X Gigabit Ethernet 250010 Gigabit Ethernet 9953.2810 Gigabit Ethernet 10312.510 Gigabit Ethernet FEC 11095.710 Gigabit Ethernet LX4 3125Fibre Channel 1062.52X Fibre Channel 21254X Fibre Channel 42508x Fibre Channel 850010X Fibre Channel 10518.7510X Fibre Channel FEC 11317Infi niband 2500STM0/OC1 51.84STM1/OC3 155.52STM4/OC12 622.08STM16/OC48 2488.3STM16/OC48 FEC 2666STM64/OC192 9953.28STM64/OC192 FEC 10664.2STM64/OC192 FEC 10709STM64/OC192 Super FEC 12500STM256/OC768 39813STS1 EYE 51.84STS3 EYE 155.52Other eye-diagram masks are easily created through scaling those listed above. In addition, mask editing allows for new masks either by editing existing masks,or creating new masks from scratch. A new mask can also be created or modifi ed on an external PC usinga text editor such as Notepad, then can be transferredto the instrument’s hard drive using LAN or Flash drive. Perform these mask conformance tests with convenient user-defi nable measurement conditions, such as mask margins for guardband testing, number of waveforms tested, and stop/limit actions. Mask margin can be determined automatically to a user defi nable hit/error ratio. Transmitter waveform dispersion penalty (TWDP) tests can be performed directly in the 86100C. Exporting the waveform for external post processing is not required. (Option 201 and MATLAB® required. Dispersion penalty script for specifi c test standards must be loaded intothe 86100C.)Eyeline ModeEyeline Mode is available in the 86100C and provides insight into the effects of specifi c bit transitions within a data pattern. The unique view assists diagnosis of device or system failures due to specifi c transitions or sets of transitions within a pattern. When combined with mask limit tests, Eyeline Mode can quickly isolate the specifi c bit that caused a mask violation.Traditional triggering methods on an equivalent time sampling scope are quite effective at generating eye diagrams. However, these eye diagrams are made up of samples whose timing relationship to the data patternis effectively random, so a given eye will be made upof samples from many different bits in the patterntaken with no specifi c timing order. The result is that amplitude versus time trajectories of specifi c bits inthe pattern are not visible. Also, averaging of the eye diagram is not valid, as the randomly related samples will effectively average to the “middle” of the eye. Eyeline Mode uses PatternLock triggering (Option 001 required) to build up an eye diagram from samples taken sequentially through the data pattern. This maintainsa specifi c timing relationship between samples and allows Eyeline Mode to draw the eye based on specifi c bit trajectories. Effects of specifi c bit transitions can be investigated, and averaging can be used with the eye diagram.MATLAB® is a registered trademark of The MathWorks, Inc.PatternLock Triggering advances the capabilities of the sampling oscilloscopeThe Enhanced Trigger option (Option 001) on the 86100C provides a fundamental capability never availablebefore in an equivalent time sampling oscilloscope.This new triggering mechanism enables the DCA-J to generate a trigger at the repetition of the input data pattern – a pattern trigger. Historically, this required the pattern source to provide this type of trigger to the scope. With the press of a button, PatternLock automatically detects the pattern length, data rate and clock rate making the complex triggering process transparent to the user.PatternLock enables the 86100C to behave more like a real-time oscilloscope in terms of user experience. Observation of specifi c bits within the data pattern is greatly simplifi ed. Users that are familiar with real-time oscilloscopes, but perhaps less so with equivalent time sampling scopes will be able to ramp up quickly. PatternLock adds another new dimension to pattern triggering by enabling the mainframe software to take samples at specifi c locations in the data pattern with outstanding timebase accuracy. This capability is a building block for many of the new capabilities available in the 86100C described later.Jitter analysis (Option 200)The “J” in DCA-J represents the ability to performjitter analysis. The 86100C is a Digital Communications Analyzer with jitter analysis capability. The 86100C adds a fourth mode of operation – Jitter Mode. Extremelywide bandwidth, low intrinsic jitter, and advanced analysis algorithms yield the highest accuracy in jitter measurements.As data rates increase in both electrical and optical applications, jitter is an ever increasing measurement challenge. Decomposition of jitter into its constituent components is becoming more critical. It providescritical insight for jitter budgeting and performance optimization in device and system designs. Many communications standards require jitter decomposition for compliance. Traditionally, techniques for separation of jitter have been complex and often diffi cult to confi gure, and availability of instruments for separation of jitter becomes limited as data rates increase.The DCA-J provides simple, one button setup and execution of jitter analysis. Jitter Mode decomposesjitter into its constituent components and presentsjitter data in various insightful displays. Jitter Mode operates at all data rates the 86100C supports, removing the traditional data rate limitations from complex jitter analysis. The 86100C provides several key attributes to jitter analysis:• Very low intrinsic jitter (both random and deterministic) translates to a very low jitter noisefl oor which provides unmatched jitter measurementsensitivity.• Wide bandwidth measurement channels deliver very low intrinsic data dependent jitter and allow analysis of jitter on all data rates to 40 Gb/s and beyond.• PatternLock triggering technology provides sampling effi ciency that makes jitter measurements very fast.• Firmware revision 8.0 allows for accurate jitter measurements on signals with large RJ/PJ components (up to 0.7 UI).Jitter analysis functionality is available through the Option 200 software package. Option 200 includes:• Decomposition of jitter into Total Jitter (TJ), Random Jitter (RJ), Deterministic Jitter (DJ), Periodic Jitter (PJ), Data Dependent Jitter (DDJ), Duty Cycle Distortion (DCD), and Jitter induced by IntersymbolInterference (ISI).• Various graphical and tabular displays of jitter data • Export of jitter data to convenient delimited textformat• Save / recall of jitter database• Jitter frequency spectrum• Isolation and analysis of Sub-Rate Jitter (SRJ), that is, periodic jitter that is at an integer sub-rate of the bitrate.• Bathtub curve display in both Q and logBER scale• Adjustable total jitter probabilityEqualization and advanced waveform analysis (Option 201)As bit rates increase, channel effects cause signifi cant eye closure. Many new devices and systems are employing equalization and pre/de-emphasis to compensate for channel effects. Option 201 Advanced Waveform Analysis will provide key tools to enable design, test, and modeling of devices and systems that must deal with diffi cult channel effects:• C apture of long single valued waveforms. PatternLock triggering and the waveform append capability of Option 201 enable very accurate pulse train data sets up to 256 megasamples long, similar to a very deep memory real-time oscilloscope acquisition.• E qualization. The DCA-J can take a long single valued waveform and route it through a linear equalizer algorithm (default or user defi ned) and display the resultant equalized waveform in real time. The user can simultaneously view the input (distorted) and output (equalized) waveforms.• Interface to MATLAB® analysis capability. User candefi ne a measurement with a MATLAB® script. Result can be reported on oscilloscope results display.• A utomatic dispersion penalty analysis (such as transmitter waveform dispersion penalty or TWDP). User-entered MATLAB® scripts used to automatically process waveforms and determine penalty values.Advanced amplitude analysis/RIN/Q-factor (Option 300)In addition to jitter, signal quality can also be impacted by impairments in the amplitude domain. Similar tothe many types of jitter that exist, noise, inter-symbol interference, and periodic fl uctuation can cause eye closure in the amplitude domain. Option 300 can be added to an 86100C mainframe (Option 200 mustalso be installed) to provide in-depth analysis of the quality of both the zero and one levels of NRZ digital communications signals. Amplitude analysis is performed at a single button press as part of the jitter mode measurement process.• M easurement results are analogous to those provided for jitter and include Total Interference (TI), Deterministic Interference (dual-Dirac model, DI), Random Noise (RN), Periodic Interference (PI), and Inter-symbol Interference (ISI)• T ablular and graphical results for both one andzero levels• Export of interference data to delimited text format • Save/recall of interference database• Interference frequency spectrum• Bathtub curve display• Q-factor (isolated from deterministic interference)• Adjustable probability for total interference estimation Relative Intensity Noise (RIN)Relative Intensity Noise (RIN) describes the effects of laser intensity fl uctuations on the recovered electrical signal. Like amplitude interference, excessive RIN can close the eye diagram vertically, and therefore affect the power budget or system performance. The DCA-J can measure RIN on square wave as well as industry-standard PRBS and other patterns. In order to avoid having the measurement infl uenced by inter-symbol interference, the instrument searches the pattern for sequences of consecutive bits (for example, fi ve zeroes or fi ve ones) and measures the random noise and the power levels in the center of this sequence. When a reference receiver fi lter is turned on RIN is normalized to a 1 Hz bandwidth. The user can also choose between RIN based on the one level or on the optical modulation amplitude (RIN OMA according to IEEE 802.3ae). RIN measurements require Options 001, 200, and 300.Phase noise/jitter spectrum analysisAnalysis of jitter in the frequency domain can provide valuable insight into jitter properties and the root causes behind them. The phase locked-loop of the 83496B clock recovery module or 86108A precision waveform analyzer module can effectively be used as a jitter demodulator. Internally monitoring the loop error signal and transforming it into the frequency domain allows the jitter spectrum of a signal to be observed. Throughself-calibration, effects of the loop response are removed from the observed signal, allowing accurate jitter spectral analysis over a 300 Hz to 20 MHz span.This technique provides measurements not available with other test solutions:• J itter spectrum/phase noise for both clock or datasignals• D isplay in seconds or dBc/Hz• H igh sensitivity: for input signals > 0.5 Vpp,< –100 dBc/Hz at 10 kHz offset for 5 Gb/s, –106 dBc/Hz for 2.5 Gb/s, –140 dBc/Hz at 20 MHz offset (integrated spectrum of the instrument jitter from 10 kHz to 20 MHz is less than 100 fs)• H igh dynamic range: can lock onto and display signals with > 0.5% pp frequency deviation such asspread spectrum clocks and data• Data rates from 50 Mb/s to 13.5 Gb/s• Clock rates from 25 MHz to 6.75 GHzSpectral results can be integrated to provide an estimate of combined jitter over a user-defi ned span. As both clocks and data signals can be observed, the ratio ofdata-to-clock jitter can be observed. The displayed jitter spectrum can also be altered through a user-defi ned transfer function, such as a specifi c PLL frequency response.Phase noise analysis is achieved via an external spreadsheet application run on a personal computer communicating to the 83496B/86108A through the 86100C mainframe (typically using a USB-GPIB connection). An 83496A clock recovery module mustbe upgraded to a “B” version to function in the phase noise system.PLL bandwidth/jitter transferThe on-board phase detector of the 83496B and 86108A allows for a precision measurement of phase-locked loop (PLL) bandwidth, sometimes referred to as jitter transfer. The external software application discussed above for phase noise/jitter spectrum controls several jitter sources including the Agilent N4903 JBERT, 81150A function generator, N5182A MXG, or pattern generators/ sources with delay line or phase modulation inputs (modulated with a 33250A function generator) to provide a modulated stimulus to the device under test (DUT). The application will monitor the internal phase detector of the 83496B or 86108A to measure the stimulus as well as the DUT response. By sweeping the frequency of the jitter stimulus, the ratio of the output jitter to the input jitter provides the PLL bandwidth. The measurement systemis extremely fl exible and can test input/outputs from 50 Mb/s to 13.5 Gb/s (data signals) and/or 25 MHz to 6.75 GHz (clock signals). Thus several classes of DUTs can be measured including clock extraction circuits, multiplier/ dividers, and PLLs. Similar to a phase noise analysis, this capability is achieved via an external application runon a PC.S-parameters and time domain refl ectometery/ time domain transmission (TDR/TDT)High-speed design starts with the physical structure.The transmission and refl ection properties of electrical channels and components must be characterized to ensure suffi cient signal integrity, so refl ections andsignal distortions must be kept at a minimum. Use TDR and TDT to optimize microstrip lines, backplanes, PC board traces, SMA edge launchers and coaxial cables. Analyze return loss, attenuation, crosstalk, and otherS-parameters (including magnitude and group delay) with one button push using the 86100C Option 202 Enhanced Impedance and S-parameter software, either in single-ended or mixed-mode signals.Calibration techniques, unique to the 86100C, provide highest precision by removing cabling and fi xturing effects from the measurement results. Translation of TDR data to complete single-ended, differential, and mixed mode S-parameters (including magnitude and group delay) are available through Option 202 and the N1930A Physical Layer Test System software. Higher two-event resolution and ultra high-speed impedance measurements are facilitated through TDR pulse enhancers from Picosecond Pulse Labs1.N1024 TDR calibration kitThe N1024A TDR calibration kit contains precision standard devices based on SOLT (Short-Open-Load-Through) technology to calibrate the measurement path.1. Picosecond Pulse Labs 4020 Source Enchancement Module ()MeasurementsThe following measurements are available from thetool bar, as well as the pull down menus. The available measurements depend on the DCA-J operating mode. Oscilloscope modeTimeRise Time, Fall Time, Jitter RMS, Jitter p-p, Period, Frequency, + Pulse Width, - Pulse Width, Duty Cycle, Delta Time, [Tmax, Tmin, Tedge—remote commands only] AmplitudeOvershoot, Average Power, V amptd, V p-p, V rms,V top, V base, V max, V min, V avg, OMA (OpticalModulation Amplitude)Eye/mask modeNRZ eye measurementsExtinction Ratio, Jitter RMS, Jitter p-p, Average Power, Crossing Percentage, Rise Time, Fall Time, One Level, Zero Level, Eye Height, Eye Width, Signal to Noise, Duty Cycle Distortion, Bit Rate, Eye AmplitudeRZ Eye MeasurementsExtinction Ratio, Jitter RMS, Jitter p-p, Average Power, Rise Time, Fall Time, One Level, Zero Level, Eye Height, Eye Amplitude, Opening Factor, Eye Width, Pulse Width, Signal to Noise, Duty Cycle, Bit Rate, Contrast Ratio Mask TestOpen Mask, Start Mask Test, Exit Mask Test, Filter, Mask Test Margins, Mask Test Scaling, Create NRZ Mask Advanced measurement optionsThe 86100C has four software options that allow advanced analysis. Options 200, 201, and 300 require mainframe Option 001. Option 202 does not require Option 86100-001.Option 200: Enhanced jitter analysis softwareOption 201: Advanced waveform analysisOption 202: Enhanced impedance and S-parameters Option 300: Amplitude analysis/RIN/Q-factor Measurements (Option 200 jitter analysis)Total Jitter (TJ), Random Jitter (RJ), Deterministic Jitter (DJ), Periodic Jitter (PJ), Data Dependent Jitter (DDJ), Duty Cycle Distortion (DCD), Intersymbol Interference (ISI), Sub-Rate Jitter (SRJ), Asynchronous periodic jitter frequencies, Subratejitter components.Data Displays (Option 200 jitter analysis)TJ histogram, RJ/PJ histogram, DDJ histogram, Composite histogram, DDJ versus Bit position, Bathtub curve (log or Q scale)Measurements (Option 201 advancedwaveform analysis)Deep memory pattern waveform, user-defi ned measurements through MATLAB® interface, Transmitter Waveform Dispersion Penalty (TWDP) Data Displays (Option 201 advancedwaveform analysis)Equalized waveformMeasurements (Option 300 advancedamplitude analysis/RIN/Q-factor, requiresOption 200)Total Interference (TI), Deterministic Interference (Dual-Dirac model, DI), Random Noise (RN), Periodic Interference (PI), and Inter-symbol Interference (ISI), RIN (dBm or dB/Hz), Q-factor Data Displays (Option 300 advancedamplitude analysis/RIN/Q-factor, requiresOption 200) TI histogram, RN/PI histogram,ISI histogramTDR/TDT Mode (requires TDR module)Quick TDR, TDR/TDT Setup, Normalize, Response, Rise Time, Fall Time, Δ Time, Minimum Impedance, Maximum Impedance, Average Impedance,(Single-ended and Mixed-mode S-parameters withOption 202)Additional capabilitiesStandard functionsStandard functions are available through pull down menus and soft keys, and some functions are also accessible through the front panel knobs.MarkersTwo vertical and two horizontal (user selectable)TDR markersHorizontal — seconds or meterVertical — Volts, Ohms or Percent Refl ection Propagation — Dielectric Constant or VelocityLimit testsAcquisition limitsLimit Test “Run Until” Conditions — Off, # of Waveforms, # of SamplesReport Action on Completion — Save waveform to memory, Save screen imageMeasurement limit testSpecify Number of Failures to Stop Limit TestWhen to Fail Selected Measurement — Inside Limits, Outside Limits, Always Fail, Never FailReport Action on Failure - Save waveform to memory, Save screen image, Save summaryMask limit testSpecify Number of Failed Mask Test SamplesReport Action on Failure — Save waveform to memory, Save screen image, Save summaryConfi gure measurementsThresholds10%, 50%, 90% or 20%, 50%, 80% or CustomEye BoundariesDefi ne boundaries for eye measurmentsDefi ne boundaries for alignmentFormat Units forDuty Cycle Distortion — Time or Percentage Extinction/Contrast Ratio — Ratio, Decibelor PercentageEye Height — Amplitude or Decibel (dB)Eye Width — Time or RatioAverage Power — Watts or Decibels (dBm)Top Base Defi nitionAutomatic or CustomΔ Time Defi nitionFirst Edge Number, Edge Direction, Threshold Second Edge Number, Edge Direction, Threshold Jitter ModeUnits (time or unit interval, watts, volts, or unitamplitude)Signal type (data or clock)Measure based on edges (all, rising only, falling only) Graph layout ( single, split, quad)Quick measure confi guration4 User Selectable Measurements for Each Mode,Eye-mask, TDR etc.)Default Settings(Eye/Mask Mode)Extinction Ratio, Jitter RMS, Average Power,Crossing PercentageDefault Settings(Oscilloscope Mode)Rise Time, Fall Time, Period,V amptdHistogramsConfi gureHistogram scale (1 to 8 divisions)Histogram axis (vertical or horizontal)Histogram window (adjustable Window viamarker knobs)Math measurements4 User-defi nable functions Operator — magnify, invert, subtract, versus, min, maxSource — channel, function, memory, constant,response (TDR)CalibrateAll calibrationsModule (amplitude)Horizontal (time base)Extinction ratioProbeOptical channelFront panel calibration output levelUser selectable –2V to 2VUtilitiesSet time and dateRemote interfaceSet GPIB interfaceTouch screen confi guration/calibrationCalibrationDisable/enable touch screenUpgrade softwareUpgrade mainframeUpgrade moduleBuilt-in information systemThe 86100C has a context-sensitive on-linemanual providing immediate answers to your questions about using the instrument. Links onthe measurement screen take you directly to the information you need including algorithms for all of the measurements. The on-line manual includes technical specifi cations of the mainframe and plug-in modules. It also provides useful information such as the mainframe serial number, module serial numbers, fi rmware revision and date, and hard disk free space. There is no need for a large paper manual consuming your shelf space.File sharing and storageUse the internal 40 GB hard drive to store instrument setups, waveforms, or screen images. A 256 MB USB memory stick is included with the mainframe. Combined with the USB port on the front panel this provides for quick and easy fi le transfer. Images can be stored in formats easily imported into various programs for documentation and further analysis. LAN interface is also available for network fi le management and printing. An external USB DVD/CD-RW drive is available as an option to the mainframe. This enables easy installation of software applications as well as storage of large amounts of data.File securityFor users requiring security of their data, 86100C Option 090 offers a removable hard drive. This also enables removal of the mainframe from secure environments for calibration and repair.Powerful display modesUse gray scale and color graded trace displays to gain insight into device behavior. Waveform densities are mapped to color or easy-to-interpret gray shades. These are infi nite persistence modes where shading differentiates the number of times data in any individual screen pixel has been acquired.Direct triggering through clock recoveryTypically an external timing reference is used to synchronize the oscilloscope to the test signal. In cases where a trigger signal is not available, clock recovery modules are available to derive a timing reference directly from the waveform to be measured. The Agilent 83496A/B series of clock recovery modules are available for electrical, multimode optical, and single-mode optical input signals. 83496A/B modules have excellent jitter performance to ensure accurate measurements. Each clock recovery module is designed to synchronize to a variety of common transmission rates. The 83496A/Bcan derive triggering from optical and electrical signalsat any rate from 50 Mb/s to 13.5 Gb/s.The 86108A module incorporates the clock recovery capabilities of the 83496B into a module that also has sampling channels. Since the clock recovery system is integrated with the samplers, measurements are achieved with a single instrument connection.Clock recovery loop bandwidthThe Agilent clock recovery modules have adjustable loop bandwidth settings. Loop bandwidth is very importantin determining the accuracy of your waveform when measuring jitter, as well as testing for compliance. When using recovered clocks for triggering, the amount ofjitter observed will depend on the loop bandwidth. Asthe loop bandwidth increases, more jitter is “tracked out”by the clock recovery resulting in less observed jitter.• N arrow loop bandwidth provides a “jitter free” system clock to observe a wide jitter spectrum• Wide loop bandwidth in some applications is specifi ed by standards for compliance testing. Wide loop bandwidth settings mimic the performance of communicationssystem receiversThe 83496A/B and 86108A have a continuously adjustable loop bandwidth from as low as 15 kHz to as high as 10 MHz, and can be confi gured as a golden PLL for standardscompliance testing.。
均流器

4350fbTypical applicaTionFeaTuresDescripTionLoad Share ControllerThe L TC ®4350 is a load share controller that allows sys-tems to equally load multiple power supplies connected in parallel. The output voltage of each supply is adjusted using the SENSE + input until all currents match the share bus. The L TC4350 also isolates supply failures by turning off the series pass transistors and identifying the failed supply. The failed supply can then be removed and replaced with a new unit without turning off the system power . The L TC4350 is available in a 16-pin narrow SSOP package.L , L T , L TC, L TM, Linear Technology and the Linear logo are registered trademarks and Hot Swap and ThinSOT are trademarks of Linear Technology Corporation. All other trademarks are the property of their respective owners.5V Load Share (5A per Module)applicaTionsnBuild N + 1 Redundant Supply n Hot Swap™ Power Suppliesn Isolates Supply Failures from Output n Eliminates ORing DiodesnIdentifies and Localizes Output Low, Output High and Open-Circuit Faultsn Output Voltages from 1.5V to 12V n 16-Lead Narrow SSOP PackagenServers and Network Equipment n Telecom and Base Station Equipment n Distributed Power Systems4350fbpin conFiguraTionabsoluTe MaxiMuM raTingsSupply Voltage (V CC ) ................................................17V Input VoltageTIMER ...................................................–0.3V to 1.2V R +, R – (Note 2) ......................................–0.3V to 17V FB .........................................................–0.3V to 5.3V OV, UV .......................................................–0.3V to 17V Output VoltageCOMP1 ....................................................–0.3V to 6V COMP2 ....................................................–0.3V to 3V GAIN, SB ...............................................–0.3V to 5.6V GATE (Note 3) ............................................–0.3V to 20V I OUT , STATUS .............................................–0.3V to 17V R SET .............................................................–0.3V to 1V Operating Temperature RangeLTC4350C ................................................0°C to 70°C LTC4350I .............................................–40°C to 85°C Storage Temperature Range ..................–65°C to 150°C Lead Temperature (Soldering, 10 sec)...................300°C(Note 1)orDer inForMaTionLEAD FREE FINISH TAPE AND REEL PART MARKING PACKAGE DESCRIPTION TEMPERATURE RANGE L TC4350CGN#PBF L TC4350CGN#TRPBF 435016-Lead Plastic SSOP 0°C to 70°C L TC4350IGN#PBFL TC4350IGN#TRPBF4350I16-Lead Plastic SSOP–40°C to 85°CConsult L TC Marketing for parts specified with wider operating temperature ranges. Consult L TC Marketing for information on non-standard lead based finish parts.For more information on lead free part marking, go to: http://www.linear .com/leadfree/For more information on tape and reel specifications, go to: http://www.linear .com/tapeandreel/elecTrical characTerisTicsSYMBOL PARAMETER CONDITIONS MINTYP MAX UNITS DC CharacteristicsI CC V CC Supply CurrentUV = V CCl 1.0 1.6 2.0mA V LKOH V CC Undervoltage Lockout High l 2.36 2.45 2.52V V LKOL V CC Undervoltage Lockout Low l2.24 2.34 2.44V V FB FB Pin Voltage 0°C to 85°C (L TC4350I) or 0°C to 70°C (L TC4350C) –40°C to 85°C (L TC4350I) 1.208 1.1961.220 1.220 1.236 1.244V V V FBLIR FB Line Regulation V CC = 3.3V to 12V , COMP1 = 1.240V 0.020.05%/V V FBLORFB Load RegulationCOMP1 = 2V COMP1 = 0.64Vl l–0.0008 0.003–0.1 0.1% %The l denotes the specifications which apply over the full operating temperature range, otherwise specifications are at T A = 25°C. V CC = 5V unless otherwise noted.4350fbelecTrical characTerisTics Note 1: Stresses beyond those listed under Absolute Maximum Ratings may cause permanent damage to the device. Exposure to any Absolute Maximum Rating condition for extended periods may affect device reliability and lifetime.The l denotes the specifications which apply over the full operatingtemperature range, otherwise specifications are at T A = 25°C. V CC = 5V unless otherwise noted.SYMBOL PARAMETER CONDITIONS MIN TYP MAX UNITSDC CharacteristicsV UVTH UV Pin Threshold High Going Threshold Low Going Threshold l l 1.215 1.205 1.244 1.220 1.258 1.237V V V OVTH OV Pin Threshold High Going Threshold Low Going Thresholdl l 1.203 1.180 1.220 1.205 1.250 1.229V V V TM TIMER Pin Threshold l 1.18 1.22 1.26V I TM TIMER Pin Current TIMER On, V TIMER = 0VTIMER On, V TIMER = 0V , V OV > V OVTH l l –1.75 –5.30–2 –6–2.3 –6.7µA µA V G GAIN Pin Voltage R GAIN = 25k, (V R + – V R –) = 100mV l 2.3 2.5 2.7V V GO GAIN Pin Offset R GAIN = 25k, (V R + – V R –) = 0mVl00.020.20V V SB(MIN)SB Pin Minimum Voltage 28mV V SB(MAX)SB Pin Maximum Voltage V CC = 3.3V V CC = 12V l l 2.4 5.6 2.7 7.8 2.9 10.5V V I SB(MAX)SB Pin Maximum Current V SB = 0Vl –8–33–41mA R SB SB Pin Resistor Value l 142033kΩV E/A2OFFE/A2 OffsetV SB – V GAINl 82550mV V RSET(MAX)R SET Pin Maximum Voltage V CC = 3.3V , R SET = 100ΩV CC = 12V , R SET = 100Ωl l 0.94 0.941 1 1.03 1.03V V V RSET(MIN)R SET Pin Minimum Voltage V CC = 5V , R SET = 1000Ω V CC = 5V , R SET = 100Ωl l 0.001 0.0010.5 0.5V V I RSET(MAX)R SET Pin Maximum Current R SET = 50Ω, V IOUT = 1.1V l 182021mA V RCTH Reverse Current Threshold V R + – V R +l 103040mV ∆V GATE External N-Channel Gate Drive V GATE – V CC l 10.81212.7V I GATE GATE Pin Current Gate On, V GATE = 0V l –8–10–12µA V SOLSTATUS Pin Output LowI OUT = 3mA l0.10.31.2VNote 2: R + and R – could be at 17V while V CC = 0V .Note 3: An internal clamp limits the GATE pin to a minimum of 10.8V above V CC . Driving this pin to voltages beyond the clamp may damage the part.4350fbTypical perForMance characTerisTicsUV Threshold vs TemperatureOV Threshold vs V CCOV Threshold vs TemperatureFB vs V CCFB vs TemperatureGain PIn Voltage vs V CCI CC vs V CCI CC vs TemperatureUV Threshold vs V CCV CC (V)021.0I C C (m A )2.03.548104350 G011.53.02.561214TEMPERATURE (°C)–501.661.641.621.601.581.561.5425754350 G02–25I C C (m A )V CC (V)02U V T H R E S H O L D (V )1.2501.2451.2401.2351.2301.2251.2201.21548104350 G0361214TEMPERATURE (°C)U V T H R E S H O L D (V )1.2551.2501.2451.2401.2351.2301.2251.2201.2154350 G04V CC (V)2O V T HR E S H O L D (V )1.2221.2201.2181.2161.2141.2121.2101.2081.2061.2041.2024104350 G05612TEMPERATURE (°C)O V T H R E S H O L D (V )1.2251.2201.2151.2101.2051.2004350 G06V CC (V)1.210F B (V )1.2304350 G071.2151.2251.220TEMPERATURE (°C)1.210F B (V )1.2151.2201.2251.230–254350 G08V CC (V)2.2G A I N (V )2.42.74350 G092.32.62.5124350fbTypical perForMance characTerisTicsGain Pin Voltage vs Temperature∆V GATE vs V CC∆V GATE vs Temperaturepin FuncTionsUV (Pin 1): Undervoltage Pin. The threshold is set at 1.244V with a 24mV hysteresis. When the UV pin is pulled high, the charge pump ramps the GATE pin. When the UV pin is pulled low, the GATE pin will be pulled low.OV (Pin 2): Overvoltage Pin. The threshold is set at 1.220V with a 15mV hysteresis. When the OV pin is pulled high, the GATE pin is pulled low. After a timer cycle, the STATUS pin is pulled low until the OV pin is pulled low.TIMER (Pin 3): Analog System Timing Generator Pin. This pin is used to set the delay before the load sharing turns on after the UV pin goes high. The other use for the TIMER pin is to delay the indication of a fault on the STATUS pin.When the timer is off, an internal N-channel shorts the TIMER pin to ground. When the timer is turned on, a 2µA or 6µA timer current (I TIMER ) from V CC is connected to the TIMER pin and the voltage starts to ramp up with a slope given by: dV/dt = I TIMER /C T . When the voltage reaches the trip point (1.220V), the timer will be reset by pulling the TIMER pin back to ground. The timer period is given by: (1.220V • C T )/I TIMER .GAIN (Pin 4): Analog Output Pin. The voltage across the R + and R – pins is divided by a 1k resistor and sourced asa current from the GAIN pin. An external resistor on the GAIN pin determines the voltage gain from the current sense resistor to the GAIN pin.COMP2 (Pin 5): Analog Output Pin. This pin is the output of the share bus error amplifier E/A2. (A compensation capacitor between this pin and ground sets the crossover frequency for the power supply adjustment loop.) In most cases, this pin operates between 0.5V to 1.5V and repre-sents a diode voltage up from the voltage at the R SET pin. It is clamped at 3V . During start-up, this pin is clamped to ground. After a timer cycle (and if the GATE pin is high), the COMP2 pin is released.COMP1 (Pin 6): Analog Output Pin. This pin is the output of the voltage regulating error amplifier E/A1. A com-pensation capacitor between this pin and ground sets the crossover frequency of the share bus loop. This pin operates a diode voltage up from the voltage at the SB pin and is clamped at 8.4V .SB (Pin 7): Analog Output Pin. This pin drives the share bus used to communicate the value of shared load current between several power supplies. There is an amplifier that drives this pin a diode below the COMP1 pin using an internal NPN as a pull-up and a 20k resistor as a pull-down.TEMPERATURE (°C)2.2G A I N (V )2.32.42.52.62.7–254350 G10V CC (V)1011134350 G11987612∆V G A T E(V )TEMPERATURE (°C)11.0∆V G A T E (V )11.512.012.513.0–254350 G12pin FuncTionsGND (Pin 8): Chip Ground.FB (Pin 9): Analog Error Amplifier Input (E/A1). This pin is used to monitor the output supply voltage with an external resistive divider. The FB pin voltage is compared to 1.220V reference. The difference between the FB pin voltage and the reference is amplified and output on the COMP1 pin. R SET(Pin 10):Analog Output Pin. The I OUT amplifier converts the voltage at the COMP2 pin (down a diode voltage) to the R SET pin. Therefore, the current through the external resistor (R SET) placed between the R SET pin and ground is (COMP2 – V DIODE)/R SET. This current is used to adjust the output voltage.I OUT (Pin 11): Analog Output Pin. The current flowing into the I OUT pin is equal to the current flowing out of the R SET pin that was set by the external resistor R SET. This current is used to adjust the output supply voltage by modifying the voltage sensed by the power supply’s internal voltage feedback circuitry.R– (Pin 12): Analog Input Pin. With a sense resistor placed in the supply path between the R+ and R– pins, the power supply current is measured as a voltage drop between R+ and R–. This voltage is measured by the I SENSE block and multiplied at the GAIN pin.R+ (Pin 13): Analog Input Pin. With a sense resistor placed in the supply path between the R+ and R– pins, the power supply current is measured as a voltage drop between R+ and R–. This voltage is measured by the I SENSE block and multiplied at the GAIN pin.GATE (Pin14): The high side gate drive for the external N-Channel power FET. An internal charge pump provides the gate drive necessary to drive the FETs. The slope of the voltage rise or fall at the GATE is set by an external capacitor connected between GATE and GND, and the 10µA charge pump output current. When the undervoltage lockout circuit monitoring V CC trips, the OV pin is pulled high or the UV pin is pulled low, the GATE pin is immedi-ately pulled to GND.STATUS (Pin 15): Open-Drain Digital Output. The STATUS pin has an open-drain output to GND. This pin is pulled low to indicate a fault has occurred in the system. There are three types of faults. The first is a undervoltage lockout on V CC or the UV pin is low while the output voltage is active. The second is when the COMP2 pin is above 1.5V or below 0.5V and the voltage on the GAIN pin is greater than 100mV. The final failure is when the OV pin is high. The three faults will activate the pull-down on the STATUS pin after a timing cycle.V CC (Pin 16): The Positive Supply Input, Ranging from 3.3V to 12V for Normal Operation. I CC is typically 1.6mA. An undervoltage lockout circuit disables the chip until the voltage at V CC is greater than 2.47V. A 0.1µF bypass capacitor is required on the V CC pin. If the V CC pin is tied to the same power supply output that is being adjusted, then a 51Ω decoupling resistor is needed to hold up the supply during a short to ground on the supply output. V CC must be greater than or equal to the supply that is connected to the R+ and R– pins.4350fbblock DiagraM4350fb4350fbapplicaTions inForMaTionINTRODUCTIONMany system designers find it economically feasible to parallel power supplies to achieve redundancy. The second trend is providing some load sharing between the many supplies. In some cases, a failure in any one supply will trigger a sequence that disconnects the faulty supply and sends a flag to the system. Then, a service technician will swap in a good supply. For systems that are continuously powered, there is Hot Swap circuitry to prevent glitches on the power buses when power cards are swapped. A block diagram of this system is shown in Figure 1.By combining the features of a load share and a Hot Swap controller into one IC, the L TC4350 simplifies the design of redundant power supplies. A complete redundant power supply is a combination of a power module and the L TC4350 as shown in Figure 2. Note that the power module musthave accessible feedback network or a remote sensing pin (SENSE +) to interface to the L TC4350.The L TC4350 provides a means for paralleling power supplies. It also provides for load sharing, fault isolation and power supply hot insertion and removal. The power supply current is accurately measured and then compared to a share bus signal. The power supply’s output voltage is adjusted until the load current matches the share bus, which results in load sharing. There are two optional power FETs in series with the load that provide a quick disconnect between a load and a failed power supply. These same power FETs allow a power supply to be connected into a powered backplane in a controlled manner or removed without disruption.CURRENT SHARINGThe current sharing components will now be discussed. Figure 3 shows a simplified block diagram of these compo-nents. The I SENSE block measures the power supply current by amplifying the voltage drop across the sense resistor . An external resistor on the GAIN pin determines the gain of the I SENSE block. The voltage drop across the sense resistor is divided by a precision 1k resistor to produce a current at the GAIN pin. For example, a 10mV sense volt-age translates to a 10µA current. If a 10k resistor is on the GAIN pin, then the voltage gain is 10k/1k or 10.The voltage at the GAIN pin is compared to the current share bus using the E/A2 block. The output of E/A2 is used to adjust the output voltage of the power supply using the I OUT block. The objective of the E/A2 block is forcing the GAIN pin voltage to equal the SB pin voltage. When the GAIN pin voltages of all the L TC4350s in the system equal the SB pin voltage, the load current is shared.VOL TAGE MONITORUnique to the L TC4350 is tight output voltage regulation. This is handled by the L TC4350’s error amplifier and reference and not the power supply’s error amplifier and reference. The E/A1 amplifier monitors the output voltage via the feedback divider connected to the FB pin. The FB pin is compared to the internal reference of the L TC4350. If the FB pin is at or below the reference, then the output of E/A1 drives theBUS BUS BUSINPUT BUS OUTPUT BUSSHARE BUSFigure 1. Redundant Power Card SystemFigure 2. Redundant Power Supply4350fbapplicaTions inForMaTionSB pin (or share bus). If the FB pin is above the reference, the COMP1 pin is grounded and the SB pin is disconnected from the COMP1 pin using the series diode.The L TC4350 with the highest reference will drive the SB pin and the 20k loads connected to the SB pin. All of the other L TC4350’s COMP1 pins are pulled low because their FB pins are at a higher voltage than their references. The series diode between the COMP1 pin and the SB pin is actually a low impedance buffer amplifier with a diode in the output stage. Therefore, the master L TC4350’s E/A1 drives the share bus to the proper value that keeps the output voltage tightly regulated. The buffer amplifier is capable of driving at least fifty 20k loads (each 20k load represents an L TC4350). OUTPUT VOL TAGE ADjUSTMENTThe L TC4350 is designed to work with supplies featuring remote sense. The output voltage of each power supply needs to be adjusted below the final output voltage at thecommon load. For example, a 5V system would require the power supply output be set to 4.90V or some value below 5V . This is normally done using the trim pin of the module. The power supply output is then increased by artificially reducing the positive sense voltage by a small amount. The L TC4350 would then adjust the output voltage to 5V , an increase of 2%. The maximum range of adjustment can be set from 2% to 5% to compensate for voltage drops in the wiring, but no more than 300mV .In most power supplies, the voltage sense is tied directly to the output voltage. If a small valued resistor , R OUT , is placed in series with the power supply sense line, a voltage drop across R OUT appears as a lower sensed voltage. This requires the power supply to increase its output voltage to compensate. Thus, the L TC4350 exercises complete control of the final output voltage.The I OUT block converts the E/A2 output (COMP2 pin) to a current that flows through R OUT (see Figure 3). As the voltage at COMP2 increases, the current in R OUTFigure 3. Simplified Block DiagramADJ +). ITincreases. The output voltage will then increase by an amount equal to the voltage drop across R OUT. The external resistor, R SET, sets the voltage to current relationship in the I OUT block. The current in R OUT is defined as I ADJ = (V COMP2 – 0.58V)/R SET.The maximum voltage that can be applied across R SET is 1V. The range of the output voltage adjustment is set to be V MAXADJ = R OUT/R SET. This sets the worst-case output voltage if the share bus is accidentally shorted to V CC. As mentioned previously, this range is set to be 2% to 10% in value.The compensation elements, C CP1 and C CP2, are used to set the crossover frequencies of the two error ampli-fiers E/A1 and E/A2. In the Design Example section, the calculations for choosing all of the components will be discussed.Output Adjust Soft-StartIn the L TC4350, there is soft-start circuitry that holds the COMP2 pin at ground until both the GATE pin is 4V above the V CC pin and a timer cycle is completed following the UV pin becoming active.Upon power-up, most of the circuitry is active including the circuits that monitor and adjust the output voltage. The external power FETs are initially open circuit when power is applied. It takes about 10ms to 100ms for the FETs to transition from the off to the fully on state (as discussed in the following Hot Swapping section). During this time the FB pin is near ground which forces the SB to the positive rail. The COMP2 pin is then forced to the positive rail, which forces the R SET pin to 1V. The volt-age at the output of the power supply is now adjusted to its maximum adjusted value, which can be 10% above nominal. Once the power FETs are turned on, the load will see this adjusted output voltage. This appears to be a voltage overshoot at the load that exists until the loop can correct itself. The dominant pole in the loop exists on the COMP2 pin. Therefore, the overshoot duration is determined by the discharge time of the COMP2 pin. In order to eliminate this overshoot, the COMP2 pin is clamped at ground until the GATE pin is 4V above the V CC pin (power FETs are turned on). Now, the COMP2 pin will begin to charge up until the FB pin regulates at 1.220V.In cases where the power FETs are turned on but the power supply is still ramping up, the load voltage may overshoot. For these cases, the COMP2 pin is clamped to ground during one timing cycle. If the UV pin is greater than 1.244V, the chip begins the timer cycle. The timer cycle uses a 2µA current source into an external capacitor on the TIMER pin. As soon as the voltage at the TIMER pin exceeds 1.220V, the timer cycle is over. The time-out is defined as t = C T • 1.220V/2µA. At the end of the timer cycle, the power supply ramping should be complete. FaultsThere are several types of power supply output faults. Shorts from the output to ground or to a positive voltage greater than the normal output voltage are considered “hard faults.” These faults require the bad power supply to be immediately disconnected from the load in order to prevent disruption of the system. “Soft faults” include power supply failed open-circuit or load current sharing failure where the output voltage is normal but load sharing between several supplies is not equal. The L TC4350 can isolate soft and hard faults and signal a system controller using the STATUS pin.HARD FAUL TSThe L TC4350 can identify faults in the power supply and isolate them from the load if optional external power FETs are included between the power supply and the load. In the case of a power supply output short to ground, the reverse current block will sense that the voltage across the current sense resistor has changed directions and has exceeded 30mV for more than 5µs. The gate of the external power FETs is immediately pulled low disconnecting the short from the load. The gate is allowed to ramp-up and turn-on the power FETs as soon as the reverse voltage across the sense resistor is less than 30mV.The condition where a power supply output shorts to a high voltage is referred to as an overvoltage fault. In this case, the gate of the power FETs is pulled low disconnect-ing the overvoltage from the load. This feature uses the OV pin to monitor the power supply output voltage. Once the voltage on the OV pin exceeds the 1.220V threshold, the gate of the external power FETs is pulled low.applicaTions inForMaTion04350fbapplicaTions inForMaTionA timer is started as soon as the OV pin exceeds 1.220V. The timer consists of a 6µA current source into an external capacitor on the TIMER pin. As soon as the voltage on the TIMER pin exceeds 1.220V, the STATUS pin is pulled low. There are two external power FETs in Figure 3. The FET with its drain on the power supply side (left) and its source on the load side (right) is used to block high voltage faults from the load. If overvoltage protection is not needed, this FET is omitted. Likewise, the FET with its drain on the load side (right) can be eliminated if protection from a ground short is not needed. The other use for the power FETs is to allow hot swapping of the power supply. Hot swapping will be discussed in a later section.SOFT FAUL TSThe existence of a share bus that forces tight regulation of the system output voltage allows the system to detect if the load current is not sharing properly. As mentioned previously, the output of E/A2 will adjust until the measured current equals the share bus value. If the power supply output fails to share properly, the E/A2 output will hit the plus or minus supply. The L TC4350 uses the over/under current block to monitor the E/A2 output. This block signals the logic that a soft fault has occurred if the E/A2 output goes out of the normal 0.5V to 1.5V range where the I OUT block is active. After a timer cycle, the STATUS pin indicates a soft fault. The timer consists of a 2µA current source into an external capacitor on the TIMER pin. As soon as the voltage on the TIMER pin exceeds 1.220V, the STATUS pin is pulled low.The fault indication at the STATUS pin is disabled under one condition. The E/A2 output can be less than 0.5V when the load currents are low. In this case, it is desired to disable the soft fault indication until the current is higher. Higher current is defined as when the GAIN pin is greater than 100mV.The most common situations for soft faults are a discon-nected power supply and the share bus shorts to V CC or ground.HOT SwAPPINGThe L TC4350 controls external power FETs to allow power supplies to be hot swapped in and out of the powered system without disturbing the power buses. The gate of the power FETs are slowly ramped up. This slowly charges the power supply input and output capacitors, preventing the large inrush currents associated with capacitors being hot plugged into power buses.When power is first applied to the V CC pin, the gate of the power FET is pulled low. As soon as V CC rises above the undervoltage lockout threshold, the chip’s UV pin is functional. A 0.1µF bypass capacitor is required on the V CC pin. If the V CC pin is tied to the same power supply output that is being adjusted, then a 51Ω decoupling resistor is needed to hold up the supply during a short to ground on the supply output.If the UV pin is greater than 1.244V, the gate of the external FETs is charged with a 10µA current source. The voltage at the GATE pin begins to rise with a slope equal to 10µA/C G (Figure 4), where C G is the external capacitor connected between the GATE pin and GND. This slow charging al-lows the power supply output to begin load sharing in a nondisruptive manner.Figure 4. Supply Turn-OnV CC + 10VV CC4350 F04t1t2GATEV OUTSLOPE = 10µA/C G4350fb4350fbFigure 5. 5V Load Share (20A per Module)When the power supply is disconnected, the UV pin will drop below 1.220V if the supply is loaded. The L TC4350 then discharges the gate of the power FET isolating the load from the power supply.DESIGN EXAMPLE Load Share ComponentsThis section demonstrates the calculations involved in selecting the component values. The design example in Figure 5 is a 5V output. This design can be extended to each of the parallel sections.The first step is to determine the final output voltage and the amount of adjustment on the output voltage. The power supply voltage before the load sharing needs to be lower than the final output voltage. If the load is expecting to see a 5V output, then all of the shared power supplies need to be trimmed to 4.90V or lower . This allows 2% variation in component and reference tolerances so that the output always starts below 5V .Now that the output voltage is preset below the desired output, the L TC4350 will be responsible for increasing the output utilizing the SENSE + input to the power supply. Ifa SENSE + line is not available, then the feedback divider at the module’s error amplifier can be used. The next step is to determine the maximum positive adjustment needed for each power supply. This adjustment includes any I • R drops across sense resistors, power FETs, wiring and connectors in the supply path between the power supply and the load. For example, if the maximum current is 10A and the parasitic resistance between the power supply and load is 0.01Ω, then the positive adjustment range for I • R drops is 0.1V . Since the starting voltage is 4.9V ±0.1V , then the lowest starting voltage can be 4.8V . This voltage is 0.2V below the target. The total adjustment range that the L TC4350 will need for this example is 0.1V + 0.2V = 0.3V . Note that the lowest starting voltage should not be lower than 300mV below the target voltage.The I • R drops should be designed to be low to elimi-nate the need for additional bulk capacitance at the load. In most cases the bulk capacitance exists at the power supply output before the I • R drops. If a 0.002Ω sense resistor is used and the FET resistance is below 0.003Ω, then a total 0.005Ω series resistance is acceptable for loads to 20A. Obviously, the FB pin compensates for the DC output impedance, but the AC output impedance is the I • R drops plus the ESR of the capacitors.5V SHARE applicaTions inForMaTion。
7ZPNA4635JFC-800 JFC-810 颜色回声测 depth 快速参考指南说明书

17ZPNA4635JFC-800/JFC-810 COLOR ECHO SOUNDER Quick ReferencePress Power on.Keep pressing forPower off.BRILL 】*The navigation data such as GPS is necessary.Preset the destination / Preset the image ([EVENT] key) PressDepending on the [EVENT key set], the function differs. In case of [Store image]:Store the destination.Store the image of echo sounder.Press(4)Alarm Set Status Press Press Press Rotate Press *[GAIN (HF) Knob] key can adjust high frequency.Press Press Rotate Press *By continuously pressing the [F1]/[F2] key, a function assigned to each key can be selected.PressPressPress Rotate Press PressSelect the display menu ([DISP] key)Press Rotate Press Press*Every time when pressing the [Brill] key,the item is alternately Rotate Rotate Press Press Press Display the menu ([MENU] key)Press *The menu closes Press or Rotate (5)Status of [F1]/[F2] key assignment In case of [Store pos]:*Select by *Select by performing L:6.0 H:6.0 R:M 12.0V(1)(2) (3) (4) (5) (7)(8)Schools of fishDepth scaleBottomDepthOscillating line(6)Adjust D.range Display1 Image speed IRSpeed5 Strong27ZPNA4635Open the menu Select the menu name Select the set item Change the set content 1st time: The menu returns to the set item.2nd time: The menu returns to the menu name.The selection and the change of set content can be performed Function of Adjust Set Menu Close the menu Registration of the range can be easily changed with following operation. Preset the set value suitable for you purpose.PressPressRotate PressPressPressRotatePress*Select by performing either operation.*Select by performing either operation.PressZoom range Zoom start。
安徽福州绿色智能科技有限公司 LVCN-51 比例控制器说明书
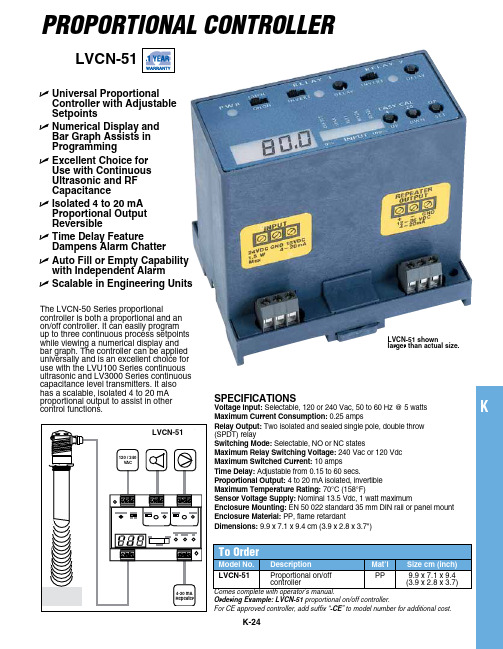
LVCN-51KK-24U U niversal Proportional Controller with Adjustable SetpointsU N umerical Display and Bar Graph Assists in ProgrammingU E xcellent Choice for Use with Continuous Ultrasonic and RF CapacitanceU I solated 4 to 20 mA Proportional Output ReversibleU T ime Delay Feature Dampens Alarm ChatterU A uto Fill or Empty Capability with Independent AlarmU S calable in Engineering UnitsProPortional ControllerSPECIFICATIONS Voltage Input: Selectable, 120 or 240 Vac, 50 to 60 Hz @ 5 watts Maximum Current Consumption: 0.25 amps Relay Output: Two isolated and sealed single pole, double throw (SPDT) relay Switching Mode: Selectable, NO or NC states Maximum Relay Switching Voltage: 240 Vac or 120 Vdc Maximum Switched Current: 10 ampsTime Delay: Adjustable from 0.15 to 60 secs.Proportional Output: 4 to 20 mA isolated, invertibleMaximum Temperature Rating: 70°C (158°F)Sensor Voltage Supply: Nominal 13.5 Vdc, 1 watt maximumEnclosure Mounting: EN 50 022 standard 35 mm DIN rail or panel mountEnclosure Material: PP, flame retardantDimensions: 9.9 x 7.1 x 9.4 cm (3.9 x 2.8 x 3.7")Ordering Example: LVCN-51 proportional on/off controller.For CE approved controller, add suffix “-CE ” to model number for additional cost.LVCN-51 shown larger than actual size.The LVCN-50 Series proportional controller is both a proportional and an on/off controller. It can easily program up to three continuous process setpoints while viewing a numerical display and bar graph. The controller can be applied universally and is an excellent choice for use with the LVU100 Series continuous ultrasonic and LV3000 Series continuous capacitance level transmitters. It also has a scalable, isolated 4 to 20 mA proportional output to assist in other control functions.。
AR3AR4

® U.S. Registered Trademark Copyright © 1999 Honeywell Inc.All Rights ReservedExcel 10 W7752D,E,F,G,J FAN COIL UNITCONTROLLERSLNS PLUG-INSUSER GUIDECONTENTSIntroduction (1)Description of Devices (1)Products Covered (2)Organization of Manual (2)Applicable Literature (2)Product Names (2)Control Application (3)Control Provided (3)Setpoints (4)Bypass (5)LED/LCD (5)Energy-Saving Features (5)Occupancy Status (6)Safety-Features (6)Operating Modes (7)Agency Listings (8)Construction (8)Controllers (8)Controller Performance Specifications (10)Configurations (11)General (11)Fan Type (11)Type of Heating and Cooling Equipment (12)Reheat Output (13)Digital Input (13)Excel 10 Wall Module Options (14)Abbreviations and Definitions (15)Application Steps (16)Overview (16)Step 1. Plan The System (16)Step 2. Determine Other Bus Devices Required (16)Step 3. Lay Out Communications and Power Wiring (17)LonWorks Layout (17)Power Wiring (18)Step 4. Prepare Wiring Diagrams (18)General Considerations (18)W7752 Controller (20)LonWorks Termination Module (21)Step 5. Order Equipment (22)Step 6. Plug-Ins Configuration Screens (23)General (23)Output (24)Input (25)Equipment Control (26)Fan (26)Switching Levels (27)Zone Options (27)Miscellaneous (27)PID (28)EXCEL 10 FAN COIL UNIT CONTROLLER LNS PLUG-INS USER GUIDE74-3330Commissioning (28)ID Number (28)Step 7. Troubleshooting (29)Troubleshooting Excel 10 FCU Controllers and Wall Modules (29)Alarms (29)Broadcasting the Service Message (31)Manual Mode (31)Appendix A: Using A LNS tool toCommission a Fan Coil Unit (32)Temperature Sensor Calibration (32)Procedure (32)Appendix B: Configuring forMaster/Slave Operation (33)Output Configuration Options (33)Input Configuration Options (33)Equipment Control Options (33)Zone Control Options (33)Network Variable Binding (33)Appendix C: LON Interface (35)EXCEL 10 FAN COIL UNIT CONTROLLER LNS PLUG-INS USER GUIDE174-3330INTRODUCTIONDescription of DevicesThe W7752D,E,F,G and J Controllers are five Fan Coil Unit Controllers in the Excel 10 family product line. FCU systems control the space temperature in a given room by regulating the heating and/or cooling equipment which control the temperature of the air delivered to that space and the fan which controls air flow. Reheat coils are often included at the fan coil unit. The W7752 Controllers are capable of stand-alone operation; however, optimum functional benefits are achieved when the network communication capabilities are used.A family of direct wired wall modules with a temperature sensor for space temperature measurement, setpoint adjustment, bypass push-button, status LED, and LCDdisplay can be used in conjunction with W7752 Controllers.The Wall Modules are available in a variety of modelsincorporating various combinatinos of the following options:• Setpoint adjustment• Bypass pushbutton and LED • Fan Switching• See table 8 for a complete list of Wall Modules options The Excel 10 W7752 connect to a LonWorks network and interoperate with 3.rd party nodes.Fig. 1. Typical System overviewEXCEL 10 FAN COIL UNIT CONTROLLER LNS PLUG-INS USER GUIDE74-33302Products CoveredThis System Engineering Guide describes how to apply the Excel 10 Fan Coil Unit Controller and the accessories to typical FCU applications. The specific devices covered include:• W7752D,E,F,G and J FCU Controllers.• T7460 Wall Modules.• T7560 Wall Modules.Organization of ManualThe Introduction and Application Steps 1 through 5 provide the information needed to make accurate ordering decisions.Application Step 6 and the Appendices include configuration engineering that can be started using a LNS tool after the devices and accessories are ordered. Application Step 7 is troubleshooting. Information provided in support of the use of third-party LonWorks communication packages to configure FCU Controllers is found in the Appendices.The organization of the manual assumes a project is being engineered from start to finish. If you are adding to, or changing an existing system, the Table of Contents can guide you to the relevant information.Applicable LiteratureThe following is a list of documents that contains information related to the Excel 10 FCU Controller.Form No.Title74-2959Excel 10 W7752D,E,F,G,J Fan Coil Unit Controller Specification Data95-7519Excel 10 W7752D,E,F,G,J Fan Coil Unit Controller Installation Instructions74-3083Excel 10 T7460 Wall Modules Specification Data95-7610Excel 10 T7460 Wall Modules Installation Instructions74-3097Excel 10 T7560 Wall Modules Specification Data95-7620Excel 10 T7560 Wall Modules Installation Instructions95-7554Excel 10 FTT/LPT 209541B Termination Module Installation InstructionsProduct NamesThe W7752 Controller is available in five models:• W7752D FCU Controller with 230 Vac power input and with reheat relay.• W7752E FCU Controller with 230 Vac power input without reheat relay.• W7752F FCU Controller with 115 Vac power input with reheat relay.• W7752G FCU Controller with 115 Vac power input without reheat relay.• W7752J FCU Controller with 100 Vac power input without reheat relay.The 2000-series FCU controllers can use any of the following Excel 10 wall modules:• T7460A with temperature sensor.• T7460B with temperature sensor and setpoint adjustment.• T7460C with temperature sensor, setpoint adjustment,and bypass button and LED.• T7460D with temperature sensor, setpoint adjustment and 5-position fan switch.• T7460E with temperature sensor, setpoint adjustment,bypass button and LED, and 3-position fan switch.• T7460F with temperature sensor, setpoint adjustment,bypass button and LED, and 5-position fan switch.• T7560A with temperature sensor, unit enable button,setpoint adjustment, bypass button, LCD display and configurable fan override with up to five settings.Other products:• C7608A Return Air SensorRefer to the Table 12 (see Application Steps, Step 5. Order Equipment) for complete listing of all available part numbers.EXCEL 10 FAN COIL UNIT CONTROLLER LNS PLUG-INS USER GUIDE374-3330Control ApplicationFan coil unit systems in commercial buildings control room temperature through the control of heat and/or cold water valves and fan speed. Electric reheat coils may also be used in the system. The FCU Controller is located in the FCU and is typically connected to an Excel 10 wall module whichincorporates a temperature sensor, setpoint and fan speed controls, and a bypass or override button. Fig. 2 shows a typical FCU control application.Fig. 2. Typical W7752 Fan Coil Unit control application.Control ProvidedThe W7752 Fan Coil Unit Controllers provide roomtemperature control for two- and four-pipe fan coil units with optional electric heating coil. The basic control sequence is shown in Fig. 3. As space temperature falls below theheating setpoint, the heating output is increased. As space temperature increases above the cooling setpoint, the cooling output is modulated to 100%. Switching levels for staged heating/cooling and fan speeds are configurable. The fan may still be configured to run continuously during the zero energy band in the occupied mode. Additionalconfigurable fan control features include fan minimum on and off times, run-up and overrun times.W7752 Controllers use a PID control algorithm where each of the three parameters can be configured. There are additional configurable boost parameters (HeatBoost and CoolBoost)which specify a range outside of which the heating or cooling outputs are turned on fully for faster response (for thermal actuators this specifies the control hysteresis). Thecontrollers are delivered with factory defaults for each of theparameters.Fig. 3. Control sequence diagram.EXCEL 10 FAN COIL UNIT CONTROLLER LNS PLUG-INS USER GUIDE74-33304SetpointsSetpoint KnobW7752 Controllers may have an Excel 10 wall module with setpoint potentiometer connected to them. When configured setpoint knob , the value from the setpoint knob is used to calculate the cooling or heating Occupied setpoint. There are two options that determine how the setpoint to be used by the control algorithm is calculated: Relative (or Offset) andAbsolute Middle. When configured for Relative, the Excel 10wall module setpoint knob represents a number from -9° to +9 DDF(-5° to +5 K) which is added to the configured Occupied and Standby setpoints for the heat and the cool modes (Cooling Occupied Setpoint and Heating Occupied Setpoint). When SptKnob is set to Absolute Middle, the setpoint knob becomes the center of the Zero Energy Band (ZEB) between the cooling and heating Occupied or Standby setpoints. The range of the ZEB is found by taking the difference between the configured heating and cooling Occupied or Standby setpoints; therefore for Absolute Middle, the actual setpoints are found as follows:for Occupied:nvoActiveSetPt (in cooling mode) =nvoSensor.remote_set_point + (Cooling Occupied Setpoint - Heating Occupied Setpoint) / 2nvoActiveSetPt (in heating mode) =nvoSensor.remote_set_point - (Cooling Occupied Setpoint - Heating Occupied Setpoint) / 2for Standby:nvoActiveSetPt (in cooling mode) =nvoSensor.remote_set_point + (Cooling Standby Setpoint - Heating Standby Setpoint) / 2nvoActiveSetPt (in heating mode) =nvoSensor.remote_set_point - (Cooling Standby Setpoint - Heating Standby Setpoint) / 2During Unoccupied modes, the remote setpoint knob is ignored, and the configured setpoints for those modes are used instead.Setpoint LimitsSetpoints are limited to the range of 50 to 95°F (10 to 35°C).The value of the setpoint knob is limited to the range of provided by the configuration parameters Maximum Limit Setpoint pot and Minimum Limit Setpoint pot. For absolute Occupied and Standby setpoints, the setpoint knob stillrepresents the middle of the ZEB, even when set to either of these limits. The actual setpoints are given by the equations shown above. When the setpoint knob is configured to be Relative, the lowest actual Occupied setpoint allowed isequal to Heating Occupied Setpoint - Minimum Limit Setpoint pot, and the highest allowed is equal to Cooling Occupied Setpoint + Maximum Limit Setpoint pot. The lowest and highest Standby setpoints are found in a similar way.Setpoint from NetworkWhen not configured to use a wall module, nviSetPoint must be bound to another node that provides a setpoint. When bound and a valid update is received, nviSetPoint is used with the appropriate ZEB:ZEBoccupied = Cooling Occupied Septoint - Heating Occupied SetpointZEBstandby = Cooling Standby Setpoint - Heating Standby Setpoint The Unoccupied setpoint does not depend on nviSetPoint at all.Setpoint OffsetThird party nodes may be bound to nviSetPtOffset to shift the setpoint in the range of -18 to 18 DDF (-10 K to 10 K).Table 1. Example setpoint values based upon default configuration - Absolute Middle setpoint knob (°C).Occupancy Mode Configured Cooling Spt.Configured Heating Spt.ZEB SetpointKnob 1EffectiveCooling Spt.2,3EffectiveHeating Spt.2,4Occupied 23212212220Standby25196212418Unoccupied 281612X 2816NOTES:1.Sample value shown. Limited by default configuration settings to the range of 12 to 30°C.2.Limited to the range of 10 to 35°C.3.= Setpoint Knob + (ZEB/2)4.= Setpoint Knob – (ZEB/2)Table 2. Example setpoint values based upon default configuration - Relative setpoint knob (°C).Occupancy Mode Configured Cooling Spt.Configured Heating Spt.ZEB SetpointKnob 1EffectiveCooling Spt.2,3EffectiveHeating Spt.2,4Occupied 23212-22119Standby25196-22317Unoccupied 281612X 2816NOTES:1.Sample value shown. Limited by default configuration settings to the range of -5 to 5°C.2.Limited to the range of 10 to 35°C.3.= Configured Cooling Setpoint + Setpoint Knob4.= Configured Heating Setpoint + Setpoint KnobEXCEL 10 FAN COIL UNIT CONTROLLER LNS PLUG-INS USER GUIDE574-3330BypassBypass ModeDuring unoccupied periods, the bypass push-button on the Excel 10 wall module may be used to cause the occupied setpoints to be used by the control algorithm. The mode may also be initiated by setting nviManOccCmd to OC_BYPASS via the network. The controller remains in bypass mode until:1.The bypass timer has timed out, or2.The user again presses the Excel 10 wall module push-button to cancel bypass mode, or3.The occupancy schedule (nviTodEvent network input)switches the mode to occupied.4.The network input nviManOccCmd is set to OC_NUL.The Excel 10 wall module indicates the current bypass mode status (see Excel 10 wall module literature for further information).Bypass TimerWhen the bypass mode has been activated, the bypass timer is set to BypTime (default of 180 minutes), at the end of which the mode reverts to the original occupancy state (see Excel 10 wall module literature for further information).Continuous Unoccupied ModeThis mode is entered when an Excel 10 wall module is configured to allow it and:• T7460 and T7770: The bypass button is pressed for four to seven seconds (until the LED blinks),• T7560: The bypass button is pressed for more than five seconds (until flashing moon appears).This mode can also be entered via a network command (nviManOccCmd set to OC_UNOCCUPIED). The controller uses the Unoccupied setpoints. The controller remains in this mode indefinitely, or until the bypass button is pressed to exit the mode or a network command is sent to clear the mode.Bypass Push-ButtonW7752 Controllers may have an Excel 10 wall module with bypass push-button connected to them. There are three ways to configure the bypass push-button (see Table 14 for further information):NONEBYPASS_UNOCCUPIED BYPASS_ONLYOverride PriorityThe W7752 Fan Coil Unit Controller can be configured to arbitrate overrides coming from the bypass push-button and the network. There are two possible states which have the following meanings:LAST_WINS specifies that the last command received from either the wall module or nviManOccCmd determines the effective override state.NETWORK_WINS specifies that when nviManOccCmd is not OC_NUL, then the effective occupancy is given by nviManOccCmd regardless of the wall module override state.LED/LCDLED OverrideThe wall module’s LED shows the override from the bypass button or from the network.• LED on Override Bypass• One flash per second Override Unoccupied• Two flashes per second Override Standby or Occupied • LED off No Override• Four flashes per second Controller answers networkmanagement wink command.LED OccupancyThe wall module’s LED shows the effective occupancy mode.• LED on Effective Occupied or Bypass • One flash per second Effective Standby • LED off Effective Unoccupied• Four flashes per second Controller answers networkmanagement wink command.LCD DisplayThis mode is only used for T7560 Wall Modules. Theoccupancy mode is represented by the following symbols: Effective Occupied or Bypass Effective Standby Effective Unoccupied Controller is offand Controller is off, frost protection is enabled.Flashing symbols represent the Override mode:Override Occupied or BypassOverride Standby Override UnoccupiedController answers the network management winkcommand.Energy-Saving FeaturesStandby ModeThe digital input for an occupancy sensor (usually a motion detector) provides the controller with a means to enter an energy-saving standby mode whenever there are no people in the room. Standby mode occurs when the scheduled occupancy is occupied and the occupancy sensor indicates no people currently in the room. If no occupancy sensor is connected directly to the controller, an occupancy sensor from another node may be bound to the network input nviSensorOcc. The controller can also be put in standby mode by setting nviManOccCmd to OC_STANDBY via the network. When in standby mode, the Fan Coil Unit Controller uses the standby cooling or heating setpoint (SptCoolStby or SptHeatStby).Window SensorThe digital input for a window contact provides the algorithm with a means to disable its temperature control activities if someone has opened a window or door in the room. If no window sensor is connected to the controller, the sensor from another node may be used by binding it to nviWindow. Frost protection remains active. Normal temperature control resumes when the window closes.EXCEL 10 FAN COIL UNIT CONTROLLER LNS PLUG-INS USER GUIDE74-33306Demand Limit ControlWhen a high-electrical-demand signal is received from an energy management system via the LonWorks network (nviDlcShed), the controller uses Demand Limit Control Bump to shift the current setpoint (down for heating and up for cooling) by the configured value to save energy.Fig. 4. Optimum start - heating.Optimum Start GradientsThere are two parameters, Cool Rec Rampand Heat Rec Ramp, that can be configured to cause the cooling and heating setpoints respectively to ramp up to their occupied settings from their unoccupied or standby settings prior to scheduled occupancy. The Fan Coil Unit Controller uses the configured rates to determine the optimum time to startincreasing the heating or cooling demand. See the following figures. The configuration parameters are in K/hour.Fig. 5. Optimum start - cooling.Occupancy StatusThe occupancy status is determined based upon the following table. Manual override may come from the network input nviManOccCmd or from the bypass push-button.Table 3. Effective Occupancy Mode ArbitrationScheduled occupancy mode Occupancy sensor status Manual override status Effective operating mode Occupied Occupied Not assigned OC_OCCUPIED Occupied Not occupied Not assigned OC_STANDBY X X Occupied OC_OCCUPIED X X Unoccupied OC_UNOCCUPIED XX Standby OC_STANDBY Occupied X BypassOC_OCCUPIED Standby X Not assigned OC_STANDBY Standby X BypassOC_OCCUPIED Unoccupied X Not assigned OC_UNOCCUPIED Unoccupied XBypassOC_BYPASSX=Don't careSafety-FeaturesFrost ProtectionIf the room temperature falls below 46.4°F (8°C), thecontroller enables the heating circuit as frost protection and an alarm is issued. When the temperature rises above 48.2°F (9°C) again, the heating circuit is turned off again.Smoke ControlThe W7752 Controller will respond to network Emergency commands by switching of heating/cooling outputs andswitching off the fan (depressurize) or switching on the fan at its highest speed (pressurize). An alarm is issued for any emergency commandsFan Failure ProtectionWhen configured with an airflow detector, the Fan Coil Unit Controller protects equipment by switching offheating/cooling outputs and issuing an alarm when the fan fails.Fan InterlocksThe Fan Coil Unit Controller can be configured such that heating and/or cooling outputs are never on without the fan running. A fan run-up time can be configured to turn on the fan prior to the heating/cooling outputs being switched on,and a fan overrun time can be configured to keep the fan running for a period of time after the heating/cooling outputs are switched off.EXCEL 10 FAN COIL UNIT CONTROLLER LNS PLUG-INS USER GUIDE774-3330Operating ModesThe possible modes of operation are listed in Table 4.Table 4. Modes of Operation for Excel 10 FCU Controller.ModeDescriptionEvents Causing a Controller to Switch to This ModeOperational Modes (NV Reference)START-UP AND WAITControl algorithms are disabled.Outputs stay in their initial positions.Physical inputs are periodically read and digital filtering of analog inputs is turned off to speed up settling work input variables are received and output variables are sent periodically.This is the first mode after an application restart.FLOATINGOUTPUTS SYNCHThe Fan Coil Unit Controller drives the floating control valves to theirinitial positions and then transitions to one of the control modes.When the effective occupancy changes to unoccupied or standby, after start-up, after 24 hours have elapsed since the last positioning, or after each positioning to 0%, the Fan Coil Unit Controller transitions to this mode.COOLINGThe Fan Coil Unit Controller is controlling in the Cooling work input (nviApplicMode) has a value of HVAC_COOL or HVAC_AUTO and the space temperature is above the cooling setpoint.HEATINGThe Fan Coil Unit Controller is controlling in the Heating mode.Network input (nviApplicMode) has the value of HVAC_HEAT or HVAC_AUTO and the space temperature is below the heating setpoint..MANUAL MODEThe control algorithms stay active and outputs are controlledautomatically until set individually to test positions using the network input nviTest.Network input (nviManualMode) has value of MODE_MANUAL.FACTORY TEST Control algorithm is disabled; a special factory test program runs.This mode is for factory testing only.DISABLEDControl algorithms are terminated,outputs are turned off (turn-off sequences and interlocks are active).Frost protection is disabled.Network input (nviManualMode) has a value of MODE_DISABLED.PRESSURIZEHeating/cooling outputs are switched off, and the fan is switched on at its highest speed.Network input (nviEmerg) containing smoke control signal from C-Bus has the value of EMERG_PRESSURIZE.DEPRESSURIZEHeating, cooling and fan outputs are switched off.Network input (nviEmerg) containing smoke control signal from C-Bus has the value of EMERG_DEPRESSURIZE.EXCEL 10 FAN COIL UNIT CONTROLLER LNS PLUG-INS USER GUIDE74-33308Agency ListingsTable 5 provides information on agency listings for Excel 10 FCU Controller products.Table 5. Agency listings.DeviceAgency Comments W7752D to JFan Coil Unit ControllerCE General Immunity per European Consortium standards EN50081-1 (CISPR 22Class B) and EN 50082-1:1992 (based on Residential, Commercial, and Light Industrial).EN 61000-4-2IEC 1000-4-2 (IEC 801-2) Electromagnetic Discharge.EN 50140, EN 50204IEC 1000-4-3 (IEC 801-3) Radiated Electromagnetic Field.EN 61000-4-4IEC 1000-4-4 (IEC 801-4) Electrical Fast Transient (Burst).Radiated Emissions and Conducted Emissions.EN 55022:1987 Class B.CISPR-22: 1985.W7752D to JFan Coil Unit Controller FCC Complies with requirements in FCC Part 15 rules for a Class B Computing Device.W7752D to GFan Coil Unit Controller UL Tested and listed under UL 916 (file number E87744).Ambient Temperature Rating: 32 to 122 degrees F (0 to 50 degrees C).W7752D to GFan Coil Unit ControllercULTested and listed under UL 916 (file number E87744).Ambient Temperature Rating: 32 to 122 degrees F (0 to 50 degrees C).ConstructionControllersThe Excel 10 W7752 Fan Coil Unit Controller is available in five basic models. All of the controllers are mains-powered,and two models are equipped with an additional high power relay for applications with electric reheat. Table 6 shows the differences between models.Table 6. FCU Controller models.OS number Power input Reheat relayW7752D2007230 Vac XW7752E2004230 Vac W7752F2002115 Vac XW7752G2000115 Vac W7752J2003100 VacAll wiring connections to the controllers are made at screw terminal blocks accessible beneath a plastic safety cover.Mounting dimensions are shown in Fig. 6.CAUTIONIf W7752 Controllers are mounted vertically andthermal actuators are used, the transformer must not be located below the electronics due to heating effects.Electrical Shock Hazard.Mains power at terminal block can cause personal injury or death. W7752 FCU Controllers must be mounted inside their fan coil unit boxes to prevent access by unauthorized personnel.To reduce the risk of fire or electric shock, install in a controlled environment relatively free of contaminants.Fig. 6. W7752 construction in inches (mm).Controller Performance SpecificationsPower:W7752D and W7752E230 Vac +10%, -15%, 50/60 Hz.W7752F and W7752G115 Vac +10%, -15%, 50/60 Hz.W7752J100 Vac ±6%, 50/60 Hz.Operating Temperature:32° to 122°F (0° to 50°C).Shipping/Storage Temperature:-40° to 158°F (-40° to 70°C).Relative Humidity:5% to 95% noncondensingInputs:Temperature Sensor:20k ohm NTCSetpoint Potentiometer:10k ohmDigital Input:Closed ≤ 400 ohmsOpen ≥ 10 K ohmsOutputs:Triac voltage range:24 Vac ± 20%.Triac maximum current ratings:250 mA continuous650 mA surge for 30 sec.IMPORTANT:When any device is energized by a Triac, the devicemust be able to sink a minimum of 15 mA. If non-Honeywell motors, actuators, or transducers are tobe used with Excel 10 FCU Controllers, compatibilitymust be verified.Fan relays voltage range:20 to 253 VacFan relays maximum current rating:3 AElectric reheat relay voltage range:20 to 253 VacElectric reheat relay maximum current rating:10 A6 A (UL916)InteroperabilityThe W7752 Controllers use the Echelon Bus LonTalk protocol. They support the L ON M ARK Functional Profile # 8020 “Fan Coil Unit Controller”, version 2.0. Fig. 7 shows the implementation used.Fig. 7. L ON M ARK FCU object profile.ConfigurationsGeneralThe following sections provide an overview of the Excel 10 FCU Controller options related to inputs and outputs. See Application Step 6. Plug-Ins Configuration Screens for complete list of configuration options and defaults.Table 7. Hardware options summary. Option Possible ConfigurationsFan type no fanone-speedtwo-speedthree-speedFan interlock enableddisabledFCU system type two-pipefour-pipeOutput 1 actuator type floatingfloating mid (one for heat/cool)1one-stagetwo-stagethree-stagePWMthermalOutput 2 actuator type floatingfloating mid (one for heat/cool)1one-stagetwo-stagethree-stagePWMthermalValve direction directreverseReheat nonereheat (W7752D and F only)free use (W7752D and F only) Digital input not usedwindow closedoccupied sensorair flow detectorcool changeoverwindow openunoccupied sensorno air flowheat changeovermovementno movementWall module option localsharedTemperature sensor type noneNTC nonlinearized1The floating-mid option is only for changeover applications and uses only one of the two outputs.Fan TypeEach fan coil unit that is controlled by a W7752 can have a fan with up to three different speeds or no fan at all. Multi-speed fans are switched at the same switching levels as multi-staged heating control points (see Fig. 8). For example, a three-speed fan will switch on its first speed at the same control level as the first stage of heating or cooling up until the second stage of heating or cooling where the second fan speed will switch on. A two stage fan will switch with the first two stages of a 3-stage heating or cooling system. Likewise, a single speed fan will turn on at the first stage of any multi-staged system. Conversely, a multi-speed fan may follow multiple switching levels even for single-staged, floating, PWM, or thermal actuator-based systems.HysteresisThe hysteresis for fan speed extends to the next lower switching level (or a control level of 0) as is shown in Fig. 8. For example, the second fan speed will remain on until the control level falls below the switching point for the first fan speed. Minimum on and off times can be configured and will apply to all fan switching points.InterlockA fan interlock can be configured which prevents heating or cooling outputs from being turned on in the event of a fan failure (where an air flow detector is installed to detect fan failure). When fan interlock is configured, run-up and overrun times can be configured to delay switching on the heating or cooling equipment after switching on the fan and delay switching off the fan after the heating or cooling equipment is switched off.The fan can be configured to run continuously during the zero energy band during occupied periods.。
Innova EF40, EF50, EF60 INSTALLATION, INSTRUCTION
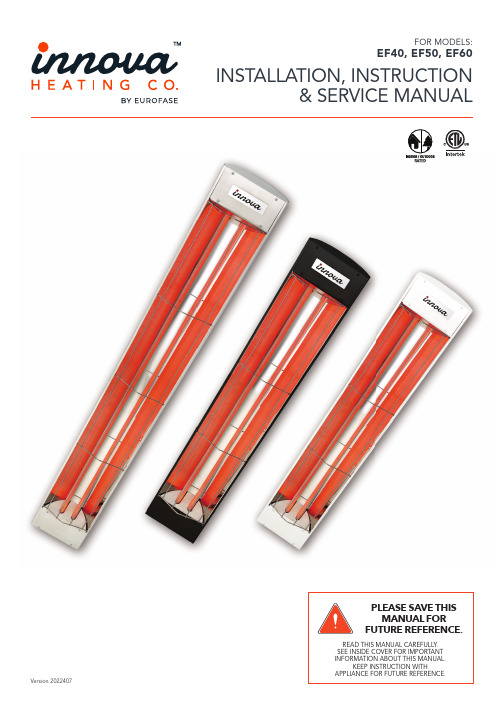
Version 2022407FOR MODELS:EF40, EF50, EF60INSTALLATION, INSTRUCTION& SERVICE MANUAL2T hank you for choosing Innova Heating Co. tomeet your heating needs. This manual is designedfor our EF40, EF50, and EF60 series of heaters.In order to ensure your heater provides efficient,safe and comfortable heat, please take the timeto review this manual.Before installing your heater, review the safetyinformation found on page 4, page 5 and page 9.Strict adherence to these guidelines is necessaryto prevent personal injury or property damage.Pages 9 through 16 reviews essential installationand assembly instructions, containing placementand orientation guidelines that are extremelyimportant to a safe and efficient installation.Please keep this manual in a safe place for futurereference and urgent needs.Note: Innova Heating Co. reserves the right to make changes to specifications, parts, components and equipment without prior notification.This Installation, operation and service manual may not be reproduced in any form without prior written consent from Innova Heating.Head Office:33 West Beaver Creek Road, Richmond Hill, ON L4B 1L8 CanadaTel: 1.800.660.5391Pat. /patentsContentsWARNINGS ........................................................................................Page 4OVERVIEW .........................................................................................Page 6IMPORTANT NOTES ..........................................................................Page 7APPLICABLE CODES & STANDARDS .................................................Page 8TECHNICAL SPECIFICATIONS ...........................................................Page 8ELECTRICAL INSTALLATIONS ............................................................Page 9MOUNTING HEIGHT / CLEARANCES ................................................Page 10CEILING MOUNT ...............................................................................Page 11WALL MOUNT ...................................................................................Page 12FLUSH MOUNT ..................................................................................Page 13INSTALLING QUARTZ ELEMENT ........................................................Page 14MAINTENANCE INSTRUCTIONS .......................................................Page 15TECHNICAL SERVICE .........................................................................Page 15REPLACEMENT PARTS.......................................................................Page 16GENERAL NOTES ..............................................................................Page 16MANUFACTURER WARRANTY...........................................................Page 173PLEASE READ ALL INSTRUCTIONS PRIORTO INSTALLING OR USING HEATER.This unit may cause a shock or possible ignition if serviceis attempted without first disconnecting its power source.Keep electrical cords, drapery, furnishings and other combustiblematerials at least 3.3ft (1m) from the heater’s front fascia and keep themaway from the two sides and rear.A LICENSED ELECTRICIAN ISREQUIRED TO INSTALL THIS PRODUCT.What’s in the box?Please inspect that all parts are included in the package.Instruction Manual (x1)The contents of this document and the specificationsof this product are subject to change without notice.Innova Heating Co. reserves the right to makechanges to the specifications and materials containedherein without notice.Please contact our customer service department orvisit our website at https:// forthe latest instruction manual.7Installation of this heater shall be in accordance with local codes, or in the absence of local codes, the National Electrical Code, NFPA 70, or the Canadian Electrical Code, Part 1, C22.1.Innova Heaters are designed and manufactured for residential / commercial heating applications for indoor and outdoor use, in accordance with the Standard for Fixed and Location-Dedicated Electric Room Heaters, UL 2021, and the Canadian Standard for Electric Air Heaters, CSA C22.2 No. 46.9101. The minimum installation height from the floor to the heater shall be:6ft (183 cm) American Standard, 8ft (244 cm) Canadian Standard2. The minimum clearances from the ceiling, walls and other objects are shown in the pictures below.4. Building materials with low heat tolerance (i.e. plastics, vinyl siding, canvas, tri-ply, etc.) may be subject to degradation at lower temperatures. It is the installer’s responsibility to ensure that adjacent materials are protected from deterioration.1113EF61FMPFS - 61” FLUSH MOUNT FRAME*65 5/8” x 12”EF39FMPFS - 39” FLUSH MOUNT FRAME*43 3/4" x 12”MINIMUM5/8” TYPE X DRY WALLONE HOUR FIRE-RATEDWHIPBeamType X 5/8”Drywall Accessible Junction BoxCeilingWhipPlease reference Flush Mount Instruction Manual for Flush Mount applications.* SOLD SEPARATELY151. It is important that these heating units are regularly cleaned to ensure long and efficient operating life.2. To clean, use a soft damp cloth and then dry thoroughly.3. Make sure all parts are dry before powering the heater.4. These heating units should be cleaned and inspected every three months.5. Avoid the use of harsh detergents, solvents, and abrasive or aerosol cleaners as they may damage surfaces.6. When cleaning the heater, always inspect the back of the heater for build-up of insects, bird droppings, dust, salt build-up, etc. and clean back thoroughly.1. If the heater is removed from mounting brackets, it should be stored in an undercover dry location.2. Always inspect the heater after high winds, earthquake, vandalism or any other unusual event that may have affected the heater. Ensure all parts are dry before powering the heater.3. Any maintenance service, excluding cleaning, must be carried out by an authorized manufacturer representative.4. If you have any question about your appliance, call the local authorized distributor.16• Innova Heaters are furnished with wall/ceiling mount swivel brackets. If the heater is hung with chains, special bracketing, or installing with a frame, these brackets can be discarded.• For pricing and a full list of models with descriptions and voltages, please see product brochures.• Wiring our Duplex/Stack Switches with our Dual Element Heaters gives users the ability to operate each elementindependently, providing half power and full power capabilities.• For optimal comfort, it is best to heat from two sides rather than from just one. However, this may not be practical in some cases.• Coverage areas vary in size, depending on personal comfort level and weather conditions.•The performance of heaters in extreme cold/windy environments may be reduced.General NotesOur heater is designed to provide you and your family with great outdoor experiences for years to come. To register, pleasefill in the Model and Serial number as well as the date of purchase in the areas below. For future reference, please savethis information. Your electric heater’s owner’s manual should be carefully read before use. Please make sure that all family members are aware of the proper way to operate the heater and how to prevent serious injury.Innova Heating warrants that this electric heater is designed and manufactured to be free from defects in materials and workmanship for a period of three years from the original date of purchase.THREE YEAR LIMITED WARRANTYTH IS WARRANTY IS APPLICABLE TO TH E ORIGINAL OWNER ONLY in accordance with the warranty terms and conditions specified below.Innova Heating Co. (warrantor) will furnish the original owner replacement parts for any component part which fails before three years of use from date of original purchase. At our option, Innova Heating Co. may offer to rebuild or replace the heater within the limited warranty period. Installation, use and maintenance must be in accordance with instructions contained in the Installation Instructions.THE WARRANTY DOES NOT COVER:• Service and labor costs incurred for diagnosing, removing or reinstallation of the heater(s) or parts(s) thereof.• Shipping and delivery charges.• Damage or repairs due to faulty installation, misapplication, negligence, thermal shock, earthquake, flood, fire, and purposeful damage to the heater.• Failure to operate due to electrical service issues including voltage conditions, blown fuses or circuit breakers.• Damage due to the inadequacy or interruption of electrical service.• Normal product wear (oxidation, scratches, heating element replacement, etc.)GENERAL CONDITIONS PERTAINING TO WARRANTYThe warranty shall be null and void if the heater is not installed by a licensed heating contractor and/or licensed electrician or if the heater is not installed according to the Installation Instructions, normal industry practices and/or if the heater is not maintained and repaired according to the instructions.Written permission is required for the return of any parts or equipment and any such return must be made on the basis of transportation charges prepaid. Shipment may be refused unless prior written permission is obtained and good returned prepaid. LIMITATION ON IMPLIED WARRANTIESImplied warranties, including any warranty of merchantability imposed on the sale of this heater under provincial or State law are limited to three year duration. Some states do not allow limitations on how long an implied warranty lasts.CLAIMS PROCEDUREAny claim under this warranty should be initiated with the dealer who sold the heater, or with any dealer handling the warrantor’s products. If this is not practical, the owner of the heater should contact Innova Heating Co. toll free at 1-800-660-5390 (hours of operation8-5MF)**********************************.1719************************ 1-800-660-5391T. 905.695.2055 F. 905.695.205633 West Beaver Creek, Richmond Hill, ON L4B 1L8。
HEF4046

HEF4046B MSI
Fig.1 Functional diagram.
FAMILY DATA HEF4046BP(N): HEF4046BD(F): HEF4046BT(D): 16-lead DIL; plastic (SOT38-1) 16-lead DIL; ceramic (cerdip) (SOT74) 16-lead SO; plastic (SOT109-1) ( ): Package Designator North America IDD LIMITS category MSI See further on in this data. See Family Specifications
factor to obtain the maximum lock range. The average output voltage of the phase comparator is equal to 1⁄2 VDD when there is no signal or noise at the signal input. The average voltage to the VCO input is supplied by the low-pass filter connected to the output of phase comparator 1. This also causes the VCO to oscillate at the centre frequency (fo). The frequency capture range (2 fc) is defined as the frequency range of input signals on which the PLL will lock if it was initially out of lock. The frequency lock range (2 fL) is defined as the frequency range of input signals on which the loop will stay locked if it was initially in lock. The capture range is smaller or equal to the lock range. With phase comparator 1, the range of frequencies over which the PLL can acquire lock (capture range) depends on the low-pass filter characteristics and this range can be made as large as the lock range. Phase comparator 1 enables the PLL system to remain in lock in spite of high amounts of noise in the input signal. A typical behaviour of this type of phase comparator is that it may lock onto input frequencies that are close to harmonics of the VCO centre frequency. Another typical behaviour is, that the phase angle between the signal and comparator input varies between 0° and 180° and is 90° at the centre frequency. Figure 3 shows the typical phase-to-output response characteristic.
- 1、下载文档前请自行甄别文档内容的完整性,平台不提供额外的编辑、内容补充、找答案等附加服务。
- 2、"仅部分预览"的文档,不可在线预览部分如存在完整性等问题,可反馈申请退款(可完整预览的文档不适用该条件!)。
- 3、如文档侵犯您的权益,请联系客服反馈,我们会尽快为您处理(人工客服工作时间:9:00-18:30)。
a r X i v :a s t r o -p h /0604158v 3 8 J a n 2007Astronomy &Astrophysics manuscript no.Corsi cESO 2008February 5,2008XRF 050406late-time flattening:an inverse Compton component?A.Corsi 1,2,3and L.Piro 11IASF-Roma /INAF,Via Fosso del Cavaliere 100,00133Roma,Italy.2Universit`a degli studi di Roma “La Sapienza”,Piazzale Aldo Moro 5,00185Roma,Italy.3INFN -Sezione di Roma c /o Dip.di Fisica -Universit`a degli studi di Roma “La Sapienza”,Piazzale Aldo Moro 5,00185Roma,Italy.ABSTRACTAims.We investigate for possible evidence of inverse Compton (IC)emission in the X-ray afterglow of XRF 050406.Methods.In the framework of the standard fireball model,we show how the late-time flattening observed in the X-ray light curve between ∼104s and ∼106s can be explained in a synchrotron-plus-IC scenario when the IC peak frequency crosses the X-ray band.Results.We thus conclude that the appearance of an IC component above the synchrotron one at late times successfully accounts for these X-ray observations.Key words.Gamma rays:bursts –X-rays:Individuals (XRF 050406)–X-rays:bursts –radiation mechanisms:non-thermal1.IntroductionThe “Burst Alert Telescope”(BAT;Barthelmy et al.2005)on board Swift (Gehrels et al.2004)was triggered by GRB 050406on April 6,2005,at 15:58:48.40UT (Parsons et al.2005).The BAT located the burst at RA =02h 17m 53s and Dec =−50◦10′52′′(J2000),with an uncertainty of 3arcmin (Krimm et al.2005).The photon index of the 15−350keV time-averaged spectrum was Γ=2.38±0.34(Krimm et al.2005).Because of the spec-tral softness,this burst was classified as an X-ray flash (XRF;Heise et al.2001).The 15−350keV fluence was(1.0+1.13−0.36)×10−7ergs cm −2(Romano et al.2006).Assuming a redshift of z =2.44(Schady et al.2006),the isotropic energy release was ∼1.4×1051ergs.The “X-Ray Telescope”(XRT;Burrows et al.2005a)im-aged the BAT field starting from 84s after the trigger,and the X-ray counterpart of XRF 050406was found during the on-ground analysis (Cusomano et al.2005;Capalbi et al.2005).The “Ultra-Violet /Optical Telescope”(UVOT;Roming et al.2005)also started imaging about 88s after the trigger.The optical afterglow was not detected on-board (Landsman et al.2005),but subsequent on-ground analysis revealed a source within the XRT error circle (Rol et al.2005).Late-time ob-servations (∼7.8hr after the burst)performed by the Magellan /Clay Telescope revealed a single faint source (R =22.0±0.09)located at RA =02h 17m 52s .3and Dec =−50◦11′15′′(J2000;Berger et al.2005a,b).2 A.Corsi and L.Piro:XRF050406:an IC component?Table1.Closure relationships between the X-ray afterglow spectral and temporal indices(β=1.1±0.3,α1=1.58±0.17)of XRF050406in the standard synchrotronfireball model for a wind or ISM environment.In parenthesis:relationships in an ISM modified for the effect of IC cooling.The(u)marks those relationships that are not affected by IC emission.ISM environment Wind environmenta)νc<νX<νm2α−β=0(u)2.1±0.42α+β−1=03.3±0.5c)νm<νX<νc2α−3β=0(u)−0.14±0.962α−3β−1=0−1.1±1.02(2−β)=0)0.86±0.96(0.48±0.31)2α−3β+1=00.86±0.96f(2.5)(1+z)1/2ǫ1/2B,−2ǫ2e,0.5E1/252t−3/2dHz(1)is the injection frequency,with f(p)= p−2ǫe /ǫB in the fast-cooling regime and x∼√1These expressions for x are valid if x2>>1(Sari&Esin2001).A.Corsi and L.Piro:XRF050406:an IC component?3 x does not depend on time,thus the temporal decay index atfrequencies aboveνc does not change(cases a)and b)).On the basis of the closure relationships,scenarios b),c),and d)are compatiblewith the observations in both an ISMand a wind environment(Chevalier&Li1999).Hereafter,wewill limit our discussion to the ISM case.We have seen in Sect.2that the optical-to-X-ray spectralindex before theflare is ratherflat.In a standard synchrotronscenario,such aflat value cannot be explained unless the syn-chrotron peak frequency is between the optical and the X-rayband.In Fig.1we show that settingνc(100s)∼0.03keV(peak frequency between the optical and the X-ray band)andνm(100s)∼0.2keV(case b)in Table1),marginal consistencywith the data can be obtained.However,under these conditions,νm crosses the V-band around2×103s;until that time,the lightcurve(Fig.1)features a rise,while XFR050406was no longervisible at∼600s above the background(Schady et al.2006),suggesting a progressive fading of the optical afterglow(the V-band upper-limits adopted here are standard3σupper-limits,thus the corresponding limitingfluxes are3times higher thanthe1σupper-limits reported by Schady et al.2006).Note alsothat in a synchrotron scenario,β 0.5at frequencies above thepeak one.Sinceνc(100s)∼0.03keV andνm(100s)∼0.2keVimplyβ=0.5forνc≤ν≤νm=0.2keV,in Fig.1we areminimizing the peak-flux value required tofit the optical andX-ray data at100s,thus minimizing the rise in the opticalfluxobserved until the peak frequency is above the optical band.To account for a decreasing optical emission,the syn-chrotron peak frequency should be below the optical band.Inthis case,tofit the early X-ray afterglow while overestimatingas little as possible the opticalflux around∼100s,the bestchoice is to setνc(100s)≤1014Hz andνm(100s)∼0.2keV(case b)in Table1).In fact,thenβopt−X=0.5,which is theflat-test value allowed in a standard synchrotron scenario when thepeak frequency is below the optical band(and p>2).Underthese assumptions,normalizing to the observed X-rayflux at100s,the predicted V-bandflux is overestimated for a factorof∼ 5.In the R-band,the predicted light curve will decreaseas t−1/4until the time at whichνm crosses the band(∼2300s)and as t−34up to the time of the Magellan/Clay obser-vation(t∼3×104s).Since in this case the measured X-ray spectral and temporal indices imply p =2.5±0.3,thent−34=t−1.375,and we expect the predicted R-bandflux tobe around a factor of∼2above the Magellan/Clay data point.Requiring additional extinction in the GRB host galaxy or acontribution to the early X-rayflux coming from the rising partof theflare(or a combination of these two effects)helps ac-count for the broad-band observations,as we see in the follow-ing section.3.2.IC componentTo model the observed early-time emission within the syn-chrotronfireball model we choose scenario b)of Table1withνc(100s)≤1014Hz andνm(100s)∼0.2keV.We thus setp=2.5.Fig.1.0.2−10keV(upper panel,solid line),V-band(lowerpanel,dotted line),and R-band(lower panel,dashed line)lightcurves in a standard synchrotronfireball model withǫB=0.19,ǫe=6.3×10−2,E52=0.5,n=0.1,p=2.5,so as tofitthe observed optical and X-rayfluxes at100s,i.e.to satisfythe conditionsνm(100s)∼0.2keV,νc(100s)∼0.03keV(seetext).The0.2−10keV data points(upper panel,crosses),theV-band data points(lower panel,triangles),and the the R-banddata point(lower panel,box)are taken from Romano et al.(2006),Schady et al.(2006),and Berger et al.(2005a),respec-tively.The R-band light curve and data point have been shifteddown by a factor of10for clarity.To model theflattening observed in the X-ray afterglowat late times,we add the contribution of an IC component.Following the prescriptions given by Sari&Esin(2001),theIC spectrum is modeled as a power-law spectrum similar tothe synchrotron one,plus logarithmic corrections when rele-vant in the considered regime.In the power-law approxima-tion,the IC spectrum is normalized to a peak-flux value off IC max=2×10−7f max n(R/1018),where f max is the peakfluxof the synchrotron component and R is thefireball radius in cm(Sari&Esin2001).To constrain the values of E52,n,ǫe,ǫB that reliably cir-cumscribe the portion of parameter space compatible with thescenario we are testing,we set the following conditions:0.1keV νm(100s) 0.3keV,(3)4 A.Corsi and L.Piro:XRF050406:an IC component?Fig.2.The shadowed regions are the parts of theǫB-ǫe plane where the conditions expressed by Eq.(3)(dotted lines),Eq.(4) (dashed line),Eq.(5)(solid lines),Eq.(6)(dash-dotted lines),Eqs.(7)and(8)(dash-dot-dot-dotted lines)are simultaneously satisfied,for E52=5and n=100(upper-left panel),E52=5and n=150(upper-right panel),E52=5and n=200(lower-left panel),and E52=10and n=100(lower-right panel).The long-dashed line marks the portion of theǫB-ǫe plane where x= ǫeǫB 1/2 106s2(4−p)>10if t IC0<106,so as to assure that x>1up to106s,which is necessary for the consistency of our formulation(Sari&Esin2001).νc(100s) 1014Hz,(4)50×10−3mJy f syn0.2keV(100s) 70×10−3mJy,(5)where f syn0.2keV (100s)=f synmax 0.2keVνc(100s) −0.50.2keVA.Corsi and L.Piro:XRF050406:an IC component?5Fig.3.Synchrotron-plus-IC model predictions for the0.2−10keV light curve withǫB=1.9×10−4,ǫe=0.25,E52=5,n=100, p=2.5.The dash-dotted line represents the synchrotron component,while the dash-dot-dot-dotted line the IC one.The solid line is the resulting totalflux.The model predictions are compared with the0.2−10keV data points(crosses)by Romano et al. (2006).no local extinction is added,the predicted V-and R-bandfluxesare overestimated of a factor of∼5and∼2.4,respectively.In a“Small Magellanic Clouds”(SMC)-like environment(Pei1992),an intrinsic extinction of A(V int)∼0.32mag in theGRB site(at z=2.44)allows consistency to be recoveredwith the optical data(Fig.4,upper panel);this implies an ab-sorption column density of N H∼0.32×1.6×1022cm−2.Insuch an environment,due to the lower metallicity,the upper-limit of9×1020cm−2set by the XRT analysis should beincreased by a factor of∼7(Stratta et al.2004),and thusthe required N H should be compared with this increased limit.The numerical test that guided us infinding this solution wasrepeated for E52=0.5,1,2,3,5,10,combined withn=10,50,100,150,200,250,300,350,400.Solutionsare found for E52=3,5,10(Fig.5,right-to-left)and forn=100,150,200.If before the X-rayflare(say t 300s)there is some con-tribution from the rising part of theflare itself(as one may ex-pect in a late internal shock scenario),we can relax the normal-ization condition to some extent.Settingνm(300s)∼0.2keV(so as to reproduce the observed X-ray spectral and tempo-ral indices after theflare for p=2.5)and normalizing thesynchrotron spectrum tofit the observed X-rayflux level at∼300s,the0.2keV light curve at t 300s will rise slowly(ast−1/4),and the0.2keVflux at100s will be lowered by a factorof(300s/100s)−1/46 A.Corsi and L.Piro:XRF 050406:an ICcomponent?Fig.4.Synchrotron-plus-IC model predictions compared with the observed data in the case ǫB =1.9×10−4,ǫe =0.25,E 52=5,n =100,p =2.5(upper panel)and ǫB =9×10−4,ǫe =0.36,E 52=1,n =350,p =2.5(lower panel).In the upper panel,the V -band (dotted line)and R -band (dashed line)light curves include a SMC-like local (z =2.44)extinction of A (V int )∼0.32mag;in the lower panel,the V -band (dotted lines)and R -band (dashed lines)light curves include an SMC-like extinction of A (V int )∼0.13mag (thick lines)or a Galactic-like A (V int )∼0.15mag (thin lines).In both panels the R -band light curve and data point have been shifted down by a factor of 10for clarity.logarithmic corrections to the IC spectrum are significant be-tween 0.2−10keV ,and they have been added to the power-law approximation.The IC spectrum has beennormalized to apeak-flux value of f ICmax =14/45×f max σT n R (Sari &Esin 2001),where σT is the Thompson cross section.In the optical band (Fig.4,lower panel),the addition of a Galactic-like extinction term (Cardelli et al.1989,with R V =3.1),with A (V int )∼0.15mag in the GRB site (z =2.44),allows us to explain both the R -and V -band observations.A SMC-like environment with A (V int )∼0.13mag could also be an alternative solution.The implied values of the local N H are ∼0.15×1.79×1021cm −2and ∼0.13×1.6×1022cm −2,both fully compatible with the upper-limit from the X-ray analysis.(For an SMC-like environment,as already noted,this upper-limit should be increased by a factor of ∼7.)Fig.5.Numerical test results showing for which values of ǫB and ǫe the conditions expressed by Eqs.(3)to (8)are simul-taneously satisfied (and x >10up to 106s).We repeated this search for E 52=0.5,1,2,3,5,10combined with n =10,50,100,150,200,250,300,350,400.Solutions are found for E 52=3and n =100,150,200(shadowed re-gion on the right);E 52=5and n =100,150,200(shadowed region in the center);E 52=10and n =100,150,200(shad-owed region on the left).The three regions represent,for each value of E 52,the superposition of regions similar to those rep-resented in Fig.2,each corresponding to one value of n among the ones allowed for the considered value of E 52.For exam-ple,the central region is the superposition of the three regions shown in the upper-left,upper-right,and lower-left panels of Fig.2.We can finally focus on the spectral predictions of the model we are proposing to explain the XRF 050406late-time flattening.In a synchrotron-plus-IC scenario,since the lightcurve flattening is associated with νICm crossing the X-ray band,the spectral index should vary between the values of −1/3(fort 105s the X-ray band is below νICc)and ∼(p −1)/2for the first solution proposed here (Fig.3)and between 0.5(for2×104s t 2×105s the X-ray band is between νICc and νICm )and p /2(plus logarithmic term corrections)for the second solution (Fig.7).The predicted mean spectral indices between 2.0×104s and 106s are <β>∼0.4and <β>∼0.8for the first and second solutions,paring those val-ues with the mean spectral index of β=1.1±0.3,measured before the flattening (Romano et al.2006),it is evident that a hardening should be observed at late times.For XRF 050406,about 60source counts were collected between ∼2.0×104s and ∼106s,so that a detailed spec-tral analysis cannot be performed.A ratio of 1.8±0.5between hard (H :0.2−1.0keV)and soft (S :1.0−10keV)pho-tons in the whole interval time is the only information that one can get from this faint source (private communication by P.Romano,2006).Comparing this with 0.5 H /S 1.0ob-tained by Romano et al.(2006)after the flare (see the lowest panel in Fig.3of Romano et al.2006),the spectrum during the late-time flattening seems to be harder,but no firm con-A.Corsi and L.Piro:XRF050406:an IC component?7Fig.6.The shadowed regions are the parts of theǫB-ǫe planewhere the required conditions(see text)are simultaneouslysatisfied(and x>10up to106s).Solutions are found forE52=0.5and n=350,400(upper-left panel),E52=1andn=200,250,300,350,400(upper-right panel),E52=2andn=150,200,250,300,350(lower-left panel),and E52=3and n=150,200(lower-right panel).clusion can be reached due to the large errors.Since hard-ening is a natural expectation in a synchrotron-plus-IC sce-nario,we then investigated on the compatibility of our pre-dictions with the observed H/ing the XRT PC response2(Grade0-12,on-axis counts,infinite extraction region),assum-ing N H=2.8×1020cm−2,and normalizing the spectrum so asto have about60counts in total,we computed a rough estimateof the expected H/S ratio for a spectrum with<β>∼0.4and<β>∼0.8,obtaining H/S=2.4±0.7and H/S=1.5±0.4for the two spectra3;those values of H/S are both compatiblewith the observed value of1.8±0.5within the errors.Althougha conclusive statement is not allowed,encouraging indicationsin favor of the present model as a mechanism for the late-timeflattening arise globally.We thus conclude that future observations of brightersources,possibly allowing performance of time-resolved spec-troscopy during the late-timeflattening,will be a key to con-firming or rejecting the scenario we are suggesting and its po-tential extension as a general explanation for this kind of late-time behavior in GRB X-ray light curves.8 A.Corsi and L.Piro:XRF050406:an ICcomponent?Fig.7.Synchrotron plus IC model predictions for the0.2−10keV light curve withǫB=9×10−4,ǫe=0.36,E52=1,n=350, p=2.5,compared with the observed data(crosses).The dash-dotted line is the contribution from the synchrotron component while the dash-dot-dot-dotted line the one from IC emission.The solid line is the resulting totalflux.Landsman,W.,Hunsberger,S.,Breeveld,A.,et al.2005,GRBCoordinates Network,3182Nousek,J.A.,Kouvelioutou,C.,Grupe,D.,et al.2006,ApJ,642,389Panaitescu,A.&Kumar,P.2000,ApJ,543,66Parsons,A.,Barthelmy,S.,Cummings,J.,et al.2005,GRBCoordinates Network,3180Pei,Y.C.1992,ApJ,395,130Piro,L.,De Pasquale,M.,Soffitta,P.,et al.2005,ApJ,623,314Rol, E.,Schady,P.,Hunsberger,S.,et al.2005,GRBCoordinates Network,3186Romano,P.,Moretti,A.,Banat,P.L.,et al.2006,A&A,450,59Roming,P.W.A.,Kennedy,T.E.,Mason,K.O.,et al.2005,Space Sci.Rev.,120,95Sari,R.&Esin,A.A.2001,ApJ,548,787Sari,R.,Piran,T.,&Narayan,R.1998,ApJ,497,L17Schady,P.,Mason,K.O.,Osborne,J.P.,et al.2006,ApJ,643,276Schlegel,D.J.,Finkbeiner,D.P.,&Davis,M.1998,ApJ,500,525Stratta,G.,Fiore,F.,Antonelli,L.A.,et al.2004,ApJ,608,846Tagliaferri,G.,Goad,M.,Chincarini,G.,et al.2005,Nature,436,985Wei,D.M.&Lu,T.1998,ApJ,505,252Wei,D.M.&Lu,T.2000,A&A,360,L13Wu,X.F.,Dai,Z.G.,Wang,X.Y.,et al.2005,ApJ,submittedto,astro-ph/0512555List of Objects‘XRF050406’on page1‘XRF050406’on page1‘XRF050406’on page1‘GRB050406’on page1‘XRF050406’on page1‘XRF050406’on page1‘XRF050406’on page1‘XRF050406’on page2‘XRF050406’on page2‘XRF050406’on page2‘XFR050406’on page3‘XRF050406’on page4A.Corsi and L.Piro:XRF050406:an IC component?9‘XRF050406’on page6‘XRF050406’on page7。