烷基化流程简述
C4烷基化原料选择加氢技术简介
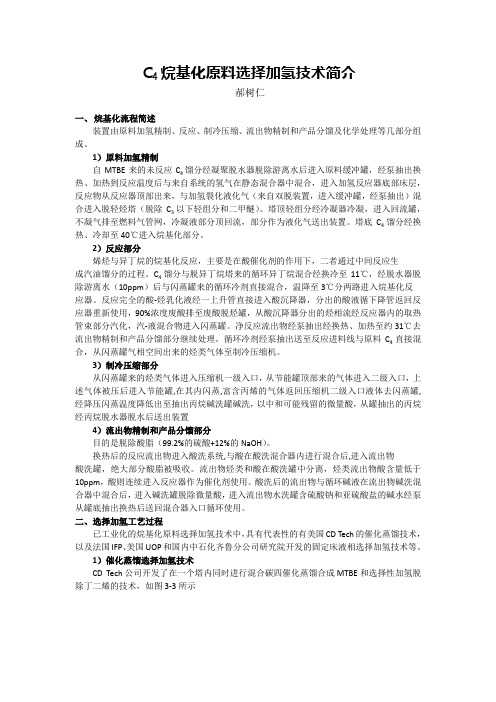
C4烷基化原料选择加氢技术简介郝树仁一、烷基化流程简述装置由原料加氢精制、反应、制冷压缩、流出物精制和产品分馏及化学处理等几部分组成。
1)原料加氢精制自MTBE来的未反应C4馏分经凝聚脱水器脱除游离水后进入原料缓冲罐,经泵抽出换热、加热到反应温度后与来自系统的氢气在静态混合器中混合,进入加氢反应器底部床层,反应物从反应器顶部出来,与加氢裂化液化气(来自双脱装置,进入缓冲罐,经泵抽出)混合进入脱轻烃塔(脱除C3以下轻组分和二甲醚)。
塔顶轻组分经冷凝器冷凝,进入回流罐,不凝气排至燃料气管网,冷凝液部分顶回流,部分作为液化气送出装置。
塔底C4馏分经换热、冷却至40℃进入烷基化部分。
2)反应部分烯烃与异丁烷的烷基化反应,主要是在酸催化剂的作用下,二者通过中间反应生成汽油馏分的过程。
C4馏分与脱异丁烷塔来的循环异丁烷混合经换冷至11℃,经脱水器脱除游离水(10ppm)后与闪蒸罐来的循环冷剂直接混合,温降至3℃分两路进入烷基化反应器。
反应完全的酸-烃乳化液经一上升管直接进入酸沉降器,分出的酸液循下降管返回反应器重新使用,90%浓度废酸排至废酸脱烃罐,从酸沉降器分出的烃相流经反应器内的取热管束部分汽化,汽-液混合物进入闪蒸罐。
净反应流出物经泵抽出经换热、加热至约31℃去流出物精制和产品分馏部分继续处理。
循环冷剂经泵抽出送至反应进料线与原料C4直接混合,从闪蒸罐气相空间出来的烃类气体至制冷压缩机。
3)制冷压缩部分从闪蒸罐来的烃类气体进入压缩机一级入口,从节能罐顶部来的气体进入二级入口,上述气体被压后进入节能罐,在其内闪蒸,富含丙烯的气体返回压缩机二级入口液体去闪蒸罐,经降压闪蒸温度降低出至抽出丙烷碱洗罐碱洗,以中和可能残留的微量酸,从罐抽出的丙烷经丙烷脱水器脱水后送出装置4)流出物精制和产品分馏部分目的是脱除酸脂(99.2%的硫酸+12%的NaOH)。
换热后的反应流出物进入酸洗系统,与酸在酸洗混合器内进行混合后,进入流出物酸洗罐,绝大部分酸脂被吸收。
烷基化过程
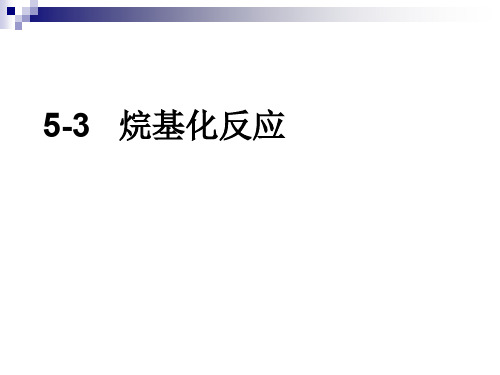
C
Cl
+ 2HCl
二氯二苯甲烷
用烯烃作烷化剂的C-烷化反应:
+ CH2=CH-CH3
CH3 CH
CH3
+ C12H24
AlCl3,HF
C12H25
2、 N-烷基化
氨基上的氢原子被烃基取代的反应叫做N烷基化反应。
烃化试剂:醇、卤代烷、酯、烯烃、醛和酮、 环氧乙烷等。
用途:(1)引入-CH2CH2OH、-CH2CH2CN极性、 非水溶性基团;
有机化合物分子中碳原子上的氢被烷基 所取代的反应叫做C-烷基化反应。
烷基化剂:烯烃;
R
卤烷(常用的烷基化)
醇、醛、酮。
HO
R
H2N
R
R
反应历程:酸催化的亲电取代反应。
如用卤烷作烷化剂的C-烷化反应:
Cl
CH2Cl +
ZnCl2 85-90oC
Cl
CH2
对氯二苯甲烷
Cl
2
+ CCl4
AlCl3 10 oC,3 h
1. 反应原理 (1)化学反应
CH3OH + (CH3)2C CH2
(CH3)3COCH3
H2
(CH3)2COCH3
Δ Ho =-36.52 KJ/mol 298K
CH3 3―C― CH2―C=CH2
CH3
CH3
(二异丁烯)
Δ Ho =69.34 KJ/mol 298K
(2) 反应机理
CH3-C=CH2 + H+ CH3
异丁烯转化率/% 97~98 99 99.9
w(残余异丁烯)/% 下游用户
2~5
烷基化
0.5~1
烷基化车间工艺流程实习总结

烷基化车间工艺流程实习总结英文回答:Internship Summary: Alkylation Process in the Workshop.During my internship in the alkylation workshop, I had the opportunity to learn and gain practical experience in the process of alkylating hydrocarbons. This internship provided me with valuable insights into the operations and workflow of the workshop.The alkylation process involves the addition of analkyl group to a molecule, typically an organic compound.It is an important step in the production of various chemicals and fuels. The workshop I worked in primarily focused on the alkylation of hydrocarbons to produce alkylated products.The workflow in the alkylation workshop can be summarized as follows:1. Feedstock Preparation: The first step involves preparing the feedstock, which is the starting material for the alkylation process. This may include the purification and pre-treatment of the hydrocarbons to remove impurities and improve their quality.2. Catalyst Preparation: In the next step, the catalyst is prepared. The catalyst is a substance that facilitates the alkylation reaction. It is usually a strong acid, such as sulfuric acid or hydrofluoric acid. The catalyst is carefully handled and stored to ensure its effectiveness.3. Reaction Setup: Once the feedstock and catalyst are prepared, the reaction setup is done. This includes the design and arrangement of the equipment required for the alkylation process. The setup may vary depending on the scale of the operation and the specific requirements of the reaction.4. Alkylation Reaction: The actual alkylation reaction takes place in this step. The feedstock is mixed with thecatalyst in the reactor under controlled conditions. The reaction is typically carried out at high temperatures and pressures to enhance the reaction rate and yield.5. Product Separation: After the alkylation reaction, the mixture is subjected to separation processes to isolate the desired alkylated products from the unreacted feedstock and other by-products. This may involve distillation, extraction, or other separation techniques.6. Product Treatment: The separated alkylated products are further treated to remove any remaining impurities or unwanted components. This may include purification steps such as filtration, drying, or chemical treatment.7. Final Product Storage: The purified alkylated products are then stored in appropriate containers or tanks for further use or distribution. Proper labeling and documentation are essential to ensure traceability and quality control.Throughout my internship, I actively participated invarious stages of the alkylation process, including feedstock preparation, reaction setup, and product separation. I also gained hands-on experience in operating and maintaining the equipment used in the workshop.Overall, this internship was a valuable learning experience that allowed me to understand the practical aspects of the alkylation process. I developed skills in process optimization, problem-solving, and teamwork. I am confident that the knowledge and experience gained during this internship will be beneficial for my future career in the chemical industry.中文回答:实习总结,烷基化车间工艺流程。
烷基化装置工艺流程说明

烷基化装置工艺流程说明本装置由原料加氢精制、反应、致冷压缩、流出物精制和产品分馏及化学处理等几部分组成,现分别简述如下:1.原料加氢精制自MTBE 装置来的未反应碳四馏分经凝聚脱水器(104-D-105)脱除游离水后进入碳四原料缓冲罐(104-D-101),碳四馏分由加氢反应器进料泵(104-P-101)抽出经碳四-反应器进料换热器(104-E-104)换热后,再经反应器进料加热器(104-E-101)加热到反应温度后与来自系统的氢气在静态混合器(104-M-101)中混合,混合后的碳四馏分从加氢反应器(104-R-101)底部进入反应器床层。
加氢反应是放热反应。
随混合碳四带入的硫化物是使催化剂失活的有害杂质。
催化剂失活后可用热氢气吹扫使其活化。
反应后的碳四馏分从加氢反应器顶部出来与加氢裂化液化气混合。
自液化气双脱装置过来的加氢裂化液化气进入加氢液化气缓冲罐(104-D-102),加氢裂化液化气由脱轻烃塔进料泵(104-P-102)抽出与反应器(104-R-101)顶部出来的碳四馏分混合后进入脱轻烃塔(104-C-101)。
脱轻烃塔(104-C-101)的任务是脱去碳四馏分中的碳三以下的轻组分,同时将二甲醚脱除。
脱轻烃塔是精密分馏的板式塔,塔顶压力控制在1.7MPa(g)。
塔顶排出的轻组分经脱轻烃塔顶冷凝器(104-E-103A/B)冷凝冷却后,进入脱轻烃塔回流罐(104-D-103)。
不凝气经罐顶压控阀(PIC-10401)后进入全厂燃料气管网。
冷凝液由脱轻烃塔回流泵(104-P-103)抽出,一部分做为(104-C-101)顶回流,另一部分作为液化气送出装置。
塔底抽出的碳四馏分经(104-E-104)与原料换热后再经碳四馏分冷却器(104-E-105)冷至40℃进入烷基化部分。
塔底重沸器(104-E-102)采用0.45MPa 蒸汽加热,反应器(104-R-101)进料加热器使用1.0MPa 蒸汽加热,凝结水都送至凝结水回收罐(104-D-304)回收。
烷化工艺流程

烷化工艺流程
《烷化工艺流程》
烷化是一种在化学工业中广泛运用的重要工艺流程,用于生产烷烃类化合物,如乙烷、丙烷等。
烷化过程通常包括烷烃与烷基化试剂进行反应,生成较长链的烷基化合物。
该过程通常应用于原油精炼和烷烃类化合物的工业生产中。
烷化工艺流程的主要步骤包括原料准备、催化剂选择、反应条件控制等。
首先,需要准备好烷烃原料和烷基化试剂,其中烷烃原料通常来自于天然气或石油提炼,而烷基化试剂则是用于引发烷化反应的重要物质。
在催化剂选择上,通常选择具有高活性和烷烃选择性的固体酸性催化剂,如氧化铝、硅铝酸等。
此外,还需要合理控制反应条件,包括温度、压力和反应物比例等参数,以确保反应的高效进行。
在实际操作中,烷化工艺流程通常采用连续式反应器进行进行,将烷烃和烷基化试剂通过反应器进行充分混合反应,产生烷基化合物。
此外,还需要对反应产物进行分离和纯化,以得到高纯度的烷基化合物。
在实际工业生产中,烷化工艺流程已经在燃料生产、润滑油生产和化学原料生产等领域得到广泛应用。
总之,《烷化工艺流程》是一项重要的化工工艺技术,对于烷烃类化合物的生产具有重要意义。
随着化工技术的不断发展和进步,相信烷化工艺流程将会在未来得到更加广泛的应用和推广。
烷基化操作规程-(1)
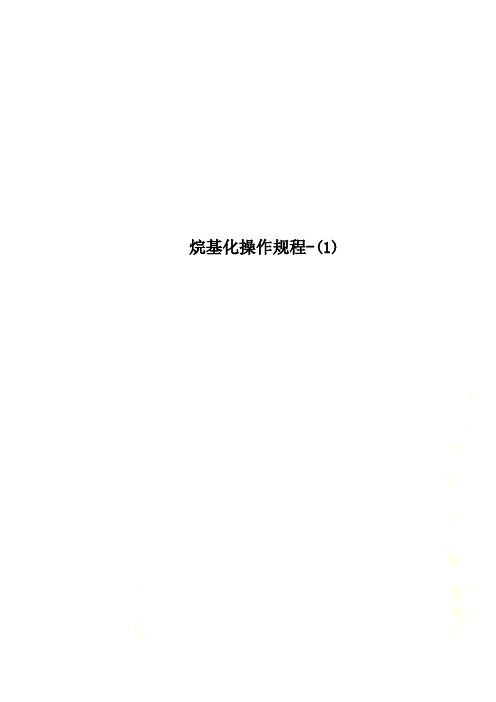
烷基化操作规程-(1)烷基化操作规程流出物制冷硫酸法烷基化装置操作手册目录第一章、工艺简介第二章、工艺原理第三章、操作原理第四章、开停工指南第五章、硫酸安全使用手册第六章、化验分析手册第七章、故障及分析第一章工艺简介本章内容主要介绍烷基化过程中的基本化学原理,讨论对产品质量有较大影响的操作变量。
烷基化反应实在强酸存在的条件下轻烯烃(C3、C4、C5)和异丁烷的化学反应。
虽然烷基化反应在没有催化剂存在时在高温下也可以发生,但是目前投入工业运行的主要的低温烷基化装置仅以硫酸或者氢氟酸做催化剂。
一些公司正在继续致力于固体酸催化剂烷基化装置的工业化。
烷基化过程发生的反应较为复杂,产品沸点范围较宽。
选择合适的操作条件,大多数产品的馏程能够达到所期望的汽油馏程,马达法辛烷值范围88~95,研究法辛烷值范围93~98。
STRATCO流出物制冷硫酸法烷基化工艺极其专利反应设备(STRATCO接触式反应器)的设计可促进烷基化反应、抑制副反应如聚合反应的发生。
副反应提高了酸消耗量,并造成产品干点升高、辛烷值降低。
本章的其余部分将对影响烷基化产品质量的烷基化反应化学原理及其工艺变量进行讨论。
A.化学原理在STRATCO烷基化工艺中,烯烃与异丁烷在硫酸催化剂存在的情况下发生反应,形成烷基化物——一种汽油调和组分。
进料中存在的正构烷烃不参加烷基化反应,但会在反应区域内起到稀释剂的作用。
下列化学式即可表示理想的C3、C4、C5烯烃的烷基化反应:乳化液进行,在乳化液中烯烃与异丁烷接触。
酸/烃乳化液通过在STRATCO的专利设备——接触式反应器中对酸烯烃混合物剧烈搅拌得到。
STRATCO烷基化反应工艺使用硫酸作为催化剂。
根据定义,催化剂可以加快化学反应,但自身不发生变化。
然而,在硫酸烷基化工艺中,必须连续的向系统中加入硫酸。
由于副反应及进料中的污染物造成酸浓度下降,所以需要向系统中补充酸。
聚合反应是一种与烷基化反应竞争的副反应。
烷基化装置工艺流程说明

烷基化装置工艺流程说明本装置由原料加氢精制、反应、致冷压缩、流出物精制和产品分馏及化学处理等几部分组成,现分别简述如下:1.原料加氢精制自MTBE 装置来的未反应碳四馏分经凝聚脱水器(104-D-105)脱除游离水后进入碳四原料缓冲罐(104-D-101),碳四馏分由加氢反应器进料泵(104-P-101)抽出经碳四-反应器进料换热器(104-E-104)换热后,再经反应器进料加热器(104-E-101)加热到反应温度后与来自系统的氢气在静态混合器(104-M-101)中混合,混合后的碳四馏分从加氢反应器(104-R-101)底部进入反应器床层。
加氢反应是放热反应。
随混合碳四带入的硫化物是使催化剂失活的有害杂质。
催化剂失活后可用热氢气吹扫使其活化。
反应后的碳四馏分从加氢反应器顶部出来与加氢裂化液化气混合。
自液化气双脱装置过来的加氢裂化液化气进入加氢液化气缓冲罐(104-D-102),加氢裂化液化气由脱轻烃塔进料泵(104-P-102)抽出与反应器(104-R-101)顶部出来的碳四馏分混合后进入脱轻烃塔(104-C-101)。
脱轻烃塔(104-C-101)的任务是脱去碳四馏分中的碳三以下的轻组分,同时将二甲醚脱除。
脱轻烃塔是精密分馏的板式塔,塔顶压力控制在1.7MPa(g)。
塔顶排出的轻组分经脱轻烃塔顶冷凝器(104-E-103A/B)冷凝冷却后,进入脱轻烃塔回流罐(104-D-103)。
不凝气经罐顶压控阀(PIC-10401)后进入全厂燃料气管网。
冷凝液由脱轻烃塔回流泵(104-P-103)抽出,一部分做为(104-C-101)顶回流,另一部分作为液化气送出装置。
塔底抽出的碳四馏分经(104-E-104)与原料换热后再经碳四馏分冷却器(104-E-105)冷至40℃进入烷基化部分。
塔底重沸器(104-E-102)采用0.45MPa 蒸汽加热,反应器(104-R-101)进料加热器使用1.0MPa 蒸汽加热,凝结水都送至凝结水回收罐(104-D-304)回收。
烷基化装置工艺流程概述
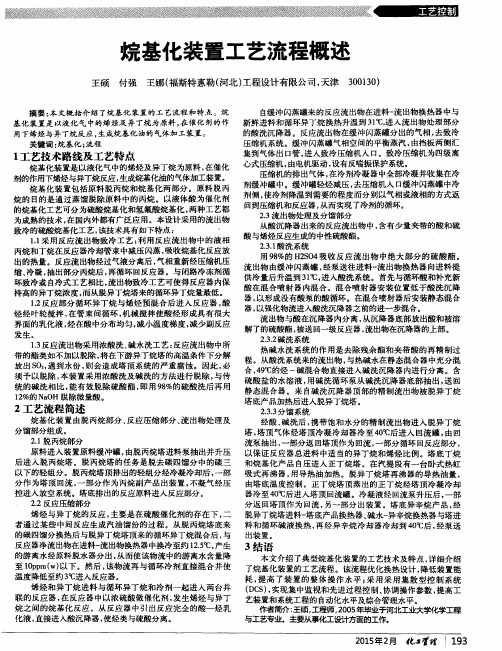
烷基化装置工艺流程概述
王硕 付强 王娜( 福斯特惠勒 ( 河北) 工程设计有限公司, 天津 3 0 0 1 3 0 )
摘要: 本 文概 括介 绍 了烷 基化装 置的 工艺流程 和特 点。烷 自 缓 冲 闪蒸罐来 的反应 流 出物 在进料一 流 出物 换热 器中与 1 ℃, 进 入 流出物 处理 部分 基化 装置是 以液化 气 中的烯烃及 异 丁烷 为原料 , 在 催化 剂的作 新鲜 进料 和循 环异 丁烷换 热升 温到 3 的酸 洗沉 降器 。反 应流 出物在缓 冲 闪蒸 罐分 出的气相 , 去 致冷 用下烯烃与异 丁烷 反应 , 生成烷基化 油的 气体加 工装置 。 压缩 机系统 。缓 冲闪蒸 罐气相 空间的平 衡蒸 汽 , 由挡板 两侧汇 关键词 : 烷基化 ; 流程 集 到气体 出 口管 , 进 入致冷 压缩机 入 口。致冷压缩 机为 四级离 1 工艺技术路线及工艺特点 心式 压缩机 , 由电机 驱动 , 设 有反喘振 保护系统 。 烷基 化装 置是 以液化 气 中的烯烃 及异丁烷 为原 料 , 在催化 压缩机 的排 出气体 , 在冷剂冷 凝器 中全部 冷凝并 收集在 冷 剂的作用 下烯烃 与异丁烷反应 , 生成烷基化 油的气体加 工装 置。 剂 缓冲罐 中 。缓 冲罐轻 烃减压 , 去 压缩机 入 口 缓 冲 闪蒸罐 中冷 烷 基化 装置 包括 原料 脱 丙烷 和烷 基化两 部 分 。原料 脱 丙 剂侧 , 使冷 剂降温 到需要 的程 度而分 别以气相 或液相 的方式 返 烷 的 目的是通 过蒸 馏 脱除原 料 中的 丙烷 。以 液体 酸为 催化 剂 回到压缩机和 反应器 , 从而实 现 了冷剂 的循 环 。 的烷基化 工艺 可分为 硫酸烷 基化和 氢氟酸烷 基化 , 两 种工艺都 2 . 3流 出物处 理及分馏部 分 为成 熟的技 术 , 在 国内外都有广 泛应 用。本设 计采用 的流 出物 从酸 沉 降器 出来 的反应 流 出物 中, 含有 少量夹 带的酸 和硫 致冷的硫 酸烷基化 工艺 , 该技术具有如 下特点 : ’ 酸与烯烃 反应生成 的中性硫酸酯 。 1 . 1 采用 反应 流 出物致 冷 工艺 : 利 用反 应流 出物 中的液 相 2 _ 3 . 1 酸洗 系统 丙烷 和丁烷 在反应 器冷却 管束 中减压 闪蒸 , 吸收烷 基化反 应放 用9 8 %的 H 2 S 0 4 吸收反应流出物中绝大部分的硫酸酯。 出的 热量 。反应流 出物经 过气液 分离后 , 气相重新 经压缩 机压 流 出物 由缓 冲闪 蒸罐 , 经泵送 往进 料一 流 出物 换 热 器向进 料提 缩、 冷凝, 抽 出部 分丙烷 后 , 再循环 回反应 器 。与 闭路冷 冻剂循 供冷 量后升 温到 3 1 ℃, 进入酸 洗 系统 。首先 与循 环酸和补 充新 环致 冷或 自冷式 工艺相 比 , 流出物致 冷工 艺可使 得反应 器内保 酸在 混 合喷 射器 内混 合 。混 合喷射 器安 装位 置低 于 酸洗 沉 降 持高 的异丁烷浓 度 , 而 从脱异丁烷 塔来的循环 异丁烷量最低 。 器, 以形成没有酸泵的酸循环。在混合喷射器后安装静态混合 1 . 2 反应 部 分循 环 异丁烷 与 烯烃 预混 合 后进 入 反应 器 , 酸 器, 以 强化物流进入 酸洗沉降 器之前的进一 步混合 。 烃 经 叶轮搅 拌 , 在 管束 间循 环 , 机 械搅拌 使 酸烃 形成 具有 很大 流 出物 与酸在 沉降 器内分 离 , 从 沉 降器底部 放出酸 和被溶 界 面的乳 化液 , 烃 在酸 中分 布均 匀 , 减 小温 度梯度 , 减 少副反应 解了的硫酸酯 , 被送 回一级反 应器 , 流出物在沉 降器的上部 。 发生 。 2 . 3 . 2 碱 洗系统 1 - 3 反应 流 出物 采用 浓酸洗 、 碱 水洗 工艺 : 反应 流 出物 中所 热碱 水 洗系 统的 作用 是去 除 残余 酯和 夹带 酸 的再精 制过 带的酯 类如 不加 以 脱除 , 将在下 游异丁 烷塔 的高温条 件下分 解 程 。从 酸洗 系统来的 流 出物 , 与热碱水 在静态 混合 器中充分 混 放出s ( ) 2 , 遇 到水份 , 则会 造成 塔顶 系统 的严 重腐蚀 。因此 , 必 合, 4 9  ̄ C 的烃 一碱混 合物 直接 进入碱 洗沉 降器 内进行分 离 。含 须予 以脱 除 , 本 装 置采用 浓酸 洗及 碱洗 的方 法进 行 脱除 , 与 传 硫酸盐的水溶液 , 用碱洗循环泵从碱洗沉降器底部抽出, 送回 统 的碱 洗相 比 , 能 有效 脱除 硫酸 酯 , 即用 9 8 %的硫 酸洗 后再 用 静态 混 合器 。来 自碱洗 沉 降器 顶部 的精 制流 出物 被脱 异丁 烷 1 2 %的 N a O H脱除 微量酸 。 塔底产 品加 热后进入 脱异丁烷塔 。 2 工艺流程简述 2 - 3 - 3 分馏 系统 烷 基化 装 置 由脱丙烷 部 分 、 反 应压 缩部分 、 流 出物 处理 及 经酸、 碱 洗后 , 携 带 饱和 水分 的精 制流 出物 进 入脱 异丁 烷 分馏部分 组成 。 塔, 塔顶气体经塔顶冷凝冷却器冷至4 0  ̄ C 后进入 回流罐 , 由回 2 . 1 脱 丙烷 部分 流泵 抽 出, 一部 分返 回塔顶作为 回流 , 一部 分循 环 回反应 部分 , 原料 进入 装 置原 料缓 冲罐 , 由脱 丙烷塔 进料泵 抽 出并 升压 以保 证 反应 器总 进料 中适 当的 异丁烷 和 烯烃 比例 。塔 底丁 烷 后 进入 脱丙 烷塔 。脱 丙烷 塔 的任务 是 脱去碳 四馏 分 中的 碳三 和烷 基化 产 品 自压进 入正 丁烷 塔 。在汽 提 段有一 台 卧式 热虹 以 下的轻组 分 。脱丙烷塔 顶排 出的轻组分 经冷 凝冷却后 , 一部 吸式 再 沸器 , 用 导热 油加 热 。脱异 丁烷 塔再 沸 器的导 热 油量 , 分 作为 塔顶 回流 , 一部 分作 为丙烷 副 产品 出装 置 , 不凝 气 经压 由塔 底温 度 控制 。正 丁烷 塔顶 蒸 出的正 丁烷 经塔 顶冷 凝 冷却 控进 入放空 系统 。塔底排 出的反应原料 进入反应部分 。 器冷 至 4 0 q C 后进入塔 顶 回流罐 。冷凝液 经 回流 泵升压 后 , 一部 2 . 2 反 应压缩部分 分返 回塔 顶 作为 回流 , 另一 部分 出装 置 。塔 底 异辛烷 产 品 , 经 烯烃 与异 丁烷 的反 应 , 主 要是 在硫 酸催 化剂 的 存在 下 , 二 脱异 丁烷塔进 料一 塔 底产 品换 热器 、 碱水 一 异辛烷 换热 器与塔进 者通 过 某些 中间反应 生成 汽 油馏份 的过 程 。从脱 丙烷 塔 底来 料和 循 环碱 液换 热 , 再 经异 辛烷 冷 却器 冷却到 4 0 ℃后 , 经 泵送 的碳 四馏分 换热后 与脱异 丁烷塔 顶来 的循 环异 丁烷混 合后 , 与 出装 置。 反应 器净流 出物 在进料一 流出物换热 器中换冷 至约 1 2 . 5  ̄ C , 产生 3结语 的游 离水 经原料 脱水器分 出 , 从而使 该物流 中的游 离水含 量降 本文介 绍了典 型烷基 化装 置的工艺 技术及 特点 , 详细 介绍 至1 0 p p m( w) 以下 。然 后 , 该 物流 再 与循 环冷 剂直 接混 合 并使 了烷 基化 装置的 工艺流程 。该 流程优 化换热设 计 , 降低 装置能 温度 降低至 约 3 ℃进 入反应器 。 耗, 提 高 了装 置 的 整 体操 作水 平 ; 采 用 采 用 集 散 型控 制 系统 烯烃 和异 丁烷 进料 与循 环 异丁 烷和 冷剂 一起 进 入两 台并 ( D C S ) , 实现 集 中监 视和 先进 过程控 制 、 协调 操作 参数 , 提 高 工 联 的反 应 器 , 在 反应 器中 以浓硫 酸做 催化 剂 , 发 生烯 烃与 异丁 艺装 置和 系统 工程的 自 动化 水平及综合 管理水平 。 烷 之 间的烷 基化 反应 。从 反应 器 中 引出反应 完 全的 酸一 烃乳 作者 简介 : 王硕 , 工程 师 , 2 0 0 5 年 毕业于 河 北工 业大 学化 学工 程 化液, 直接 进入酸沉 降器 , 使烃类与硫酸 分离 。 与工 艺 专业 。主要 从事 化 工设 计方 面的 工作 。
烷基化流程简述
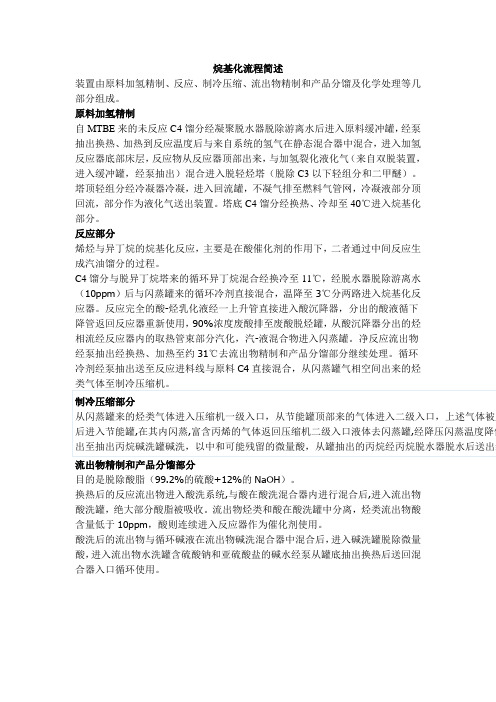
烷基化流程简述装置由原料加氢精制、反应、制冷压缩、流出物精制和产品分馏及化学处理等几部分组成。
原料加氢精制自MTBE来的未反应C4馏分经凝聚脱水器脱除游离水后进入原料缓冲罐,经泵抽出换热、加热到反应温度后与来自系统的氢气在静态混合器中混合,进入加氢反应器底部床层,反应物从反应器顶部出来,与加氢裂化液化气(来自双脱装置,进入缓冲罐,经泵抽出)混合进入脱轻烃塔(脱除C3以下轻组分和二甲醚)。
塔顶轻组分经冷凝器冷凝,进入回流罐,不凝气排至燃料气管网,冷凝液部分顶回流,部分作为液化气送出装置。
塔底C4馏分经换热、冷却至40℃进入烷基化部分。
反应部分烯烃与异丁烷的烷基化反应,主要是在酸催化剂的作用下,二者通过中间反应生成汽油馏分的过程。
C4馏分与脱异丁烷塔来的循环异丁烷混合经换冷至11℃,经脱水器脱除游离水(10ppm)后与闪蒸罐来的循环冷剂直接混合,温降至3℃分两路进入烷基化反应器。
反应完全的酸-烃乳化液经一上升管直接进入酸沉降器,分出的酸液循下降管返回反应器重新使用,90%浓度废酸排至废酸脱烃罐,从酸沉降器分出的烃相流经反应器内的取热管束部分汽化,汽-液混合物进入闪蒸罐。
净反应流出物经泵抽出经换热、加热至约31℃去流出物精制和产品分馏部分继续处理。
循环冷剂经泵抽出送至反应进料线与原料C4直接混合,从闪蒸罐气相空间出来的烃类气体至制冷压缩机。
制冷压缩部分从闪蒸罐来的烃类气体进入压缩机一级入口,从节能罐顶部来的气体进入二级入口,上述气体被压后进入节能罐,在其内闪蒸,富含丙烯的气体返回压缩机二级入口液体去闪蒸罐,经降压闪蒸温度降低出至抽出丙烷碱洗罐碱洗,以中和可能残留的微量酸,从罐抽出的丙烷经丙烷脱水器脱水后送出装流出物精制和产品分馏部分目的是脱除酸脂(99.2%的硫酸+12%的NaOH)。
换热后的反应流出物进入酸洗系统,与酸在酸洗混合器内进行混合后,进入流出物酸洗罐,绝大部分酸脂被吸收。
流出物烃类和酸在酸洗罐中分离,烃类流出物酸含量低于10ppm,酸则连续进入反应器作为催化剂使用。
烷基化流程简述
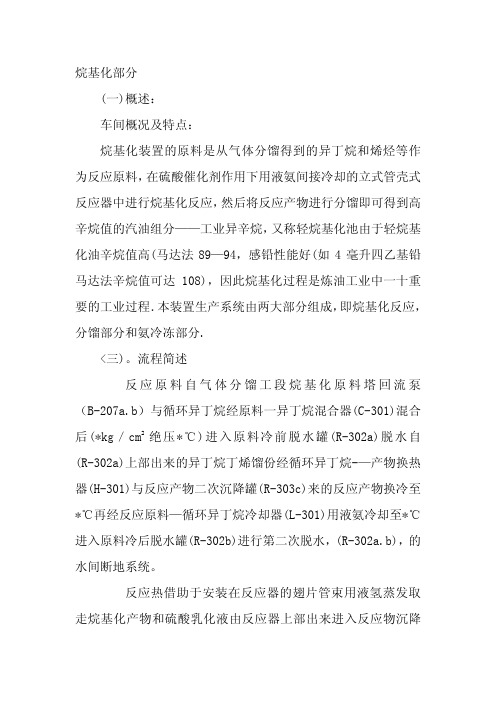
烷基化部分(一)概述:车间概况及特点:烷基化装置的原料是从气体分馏得到的异丁烷和烯烃等作为反应原料,在硫酸催化剂作用下用液氨间接冷却的立式管壳式反应器中进行烷基化反应,然后将反应产物进行分馏即可得到高辛烷值的汽油组分——工业异辛烷,又称轻烷基化池由于轻烷基化油辛烷值高(马达法89—94,感铅性能好(如4毫升四乙基铅马达法辛烷值可达108),因此烷基化过程是炼油工业中一十重要的工业过程.本装置生产系统由两大部分组成,即烷基化反应,分馏部分和氨冷冻部分.<三)。
流程简述反应原料自气体分馏工段烷基化原料塔回流泵(B-207a.b)与循环异丁烷经原料一异丁烷混合器(C-301)混合后(*kg/cm2绝压*℃)进入原料冷前脱水罐(R-302a)脱水自(R-302a)上部出来的异丁烷丁烯馏份经循环异丁烷-—产物换热器(H-301)与反应产物二次沉降罐(R-303c)来的反应产物换冷至*℃再经反应原料—循环异丁烷冷却器(L-301)用液氨冷却至*℃进入原料冷后脱水罐(R-302b)进行第二次脱水,(R-302a.b),的水间断地系统。
反应热借助于安装在反应器的翅片管束用液氢蒸发取走烷基化产物和硫酸乳化液由反应器上部出来进入反应物沉降罐(R-303a.b)沉降分离,分离出来的硫酸循环使用.反应产物由(R-303a.b)部出来进入反应物二次沉降罐(R-303c) 进行二次沉降分离,(R-303c)上部出来的反应产物经(H—301),与循环异丁烷换热后,经产物碱洗混合器.(C302)与碱液混合进入反应产物碱洗罐(R-305),自(R-305)顶出来经产物水洗混合器(C-303)与*~*℃温水混合后进入反应产物水洗罐(R-306)水洗后反应产物进入(T-301)进科缓冲罐(R-307)当*%的硫酸降至*%以下时,不再使用,由(R-302a.b)压入废酸沉降罐(R-304)沉降分离出来的废硫酸经循环硫酸泵送入废酸贮罐(R-324),用汽车槽车送往奎屯硫酸厂处理。
化工工艺学 烷基化

1. 化学反应
异丁烷与烯烃的化学反应可表述如下:
副反应有裂解、叠合、异构化、歧化和缩聚等, 生成众多的低沸点和高沸点副产物。↓副反应, 常使异丁烷大大过量。
2. 催化剂 (1) 硫酸
用作烷基化催化剂的硫酸浓度为86%~96%(w)。 硫酸浓度不能太低,以保证反应的顺利进行。硫酸
浓度太高,会促使烯烃氧化。同时,在浓酸中烷/ 烯比严重失调,副反应激烈,副产物增多。 为↑酸烃的接触面,在反应器内需使催化剂与作用 物处于良好的乳化状态,并适当↑酸烃比以↑烷基化 产物的收率和质量。
分子结合重又形成水合氢离子。
由上述机理,反应物和产物在酸膜中的扩散速 度、催化剂表面的酸浓度、反应物的浓度以及 反应温度都会对反应速度产生明显影响。动力 学试验表明,反应速度对乙烯分压是一级,而 水蒸气的分压的正面影响与乙烯相同,负面影 响是使催化剂表面酸浓度(即酸强度)↓,↓反应 速度,因此合适的水蒸气分压由实验确定。
三、乙烯水合制乙醇
1. 生产方法评述 (1) 硫酸水合法
第一步是乙烯与硫酸反应生成烷基硫酸酯 ,第 二步是烷基硫酸酯通直接蒸气加热水解蒸出醇, 硫酸浓度被稀释至50%左右。
提纯费用大,污染严重,副反应多,原料消耗 高。
(2) 直接水合法
乙烯单程转化率在5%左右,选择性94%~95%, 优点是不存在治理大量废酸问题,环境污染也比硫 酸水合法小得多。缺点是转化率低,绝大多数乙烯 需循环使用。
5-3 烷基化
利用取代反应或加成反应,在有机化合 物分子中的氮、氧、碳、硅、硫、金属 等原子上引入烷基或芳烃基的反应。
烷基化剂:烯烃、卤代烷烃、卤代芳烃、 硫酸烷酯、饱和醇
一、由异丁烷和烯烃合成烷基化汽油
烷基化
热烷基化 催化烷基化
烷基化过程
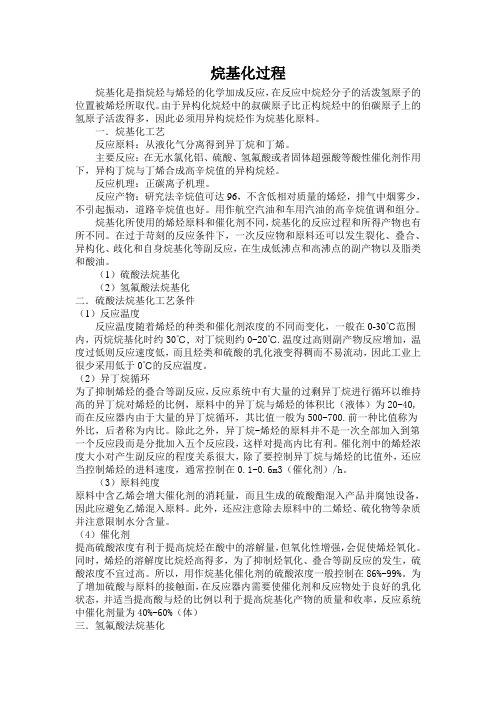
烷基化过程烷基化是指烷烃与烯烃的化学加成反应,在反应中烷烃分子的活泼氢原子的位置被烯烃所取代。
由于异构化烷烃中的叔碳原子比正构烷烃中的伯碳原子上的氢原子活泼得多,因此必须用异构烷烃作为烷基化原料。
一.烷基化工艺反应原料:从液化气分离得到异丁烷和丁烯。
主要反应:在无水氯化铝、硫酸、氢氟酸或者固体超强酸等酸性催化剂作用下,异构丁烷与丁烯合成高辛烷值的异构烷烃。
反应机理:正碳离子机理。
反应产物:研究法辛烷值可达96,不含低相对质量的烯烃,排气中烟雾少,不引起振动,道路辛烷值也好。
用作航空汽油和车用汽油的高辛烷值调和组分。
烷基化所使用的烯烃原料和催化剂不同,烷基化的反应过程和所得产物也有所不同。
在过于苛刻的反应条件下,一次反应物和原料还可以发生裂化、叠合、异构化、歧化和自身烷基化等副反应,在生成低沸点和高沸点的副产物以及脂类和酸油。
(1)硫酸法烷基化(2)氢氟酸法烷基化二.硫酸法烷基化工艺条件(1)反应温度反应温度随着烯烃的种类和催化剂浓度的不同而变化,一般在0-30℃范围内,丙烷烷基化时约30℃,对丁烷则约0-20℃.温度过高则副产物反应增加,温度过低则反应速度低,而且烃类和硫酸的乳化液变得稠而不易流动,因此工业上很少采用低于0℃的反应温度。
(2)异丁烷循环为了抑制烯烃的叠合等副反应,反应系统中有大量的过剩异丁烷进行循环以维持高的异丁烷对烯烃的比例,原料中的异丁烷与烯烃的体积比(液体)为20-40,而在反应器内由于大量的异丁烷循环,其比值一般为500-700.前一种比值称为外比,后者称为内比。
除此之外,异丁烷-烯烃的原料并不是一次全部加入到第一个反应段而是分批加入五个反应段,这样对提高内比有利。
催化剂中的烯烃浓度大小对产生副反应的程度关系很大,除了要控制异丁烷与烯烃的比值外,还应当控制烯烃的进料速度,通常控制在0.1-0.6m3(催化剂)/h。
(3)原料纯度原料中含乙烯会增大催化剂的消耗量,而且生成的硫酸酯混入产品并腐蚀设备,因此应避免乙烯混入原料。
烷基化操作规程
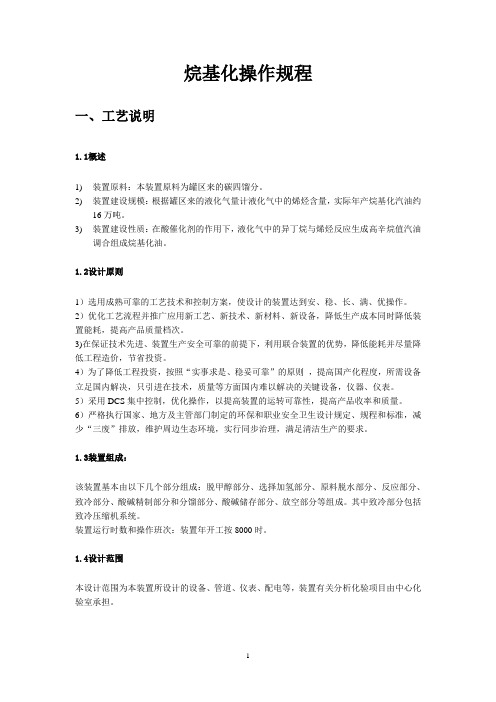
烷基化操作规程一、工艺说明1.1概述1)装置原料:本装置原料为罐区来的碳四馏分。
2)装置建设规模:根据罐区来的液化气量计液化气中的烯烃含量,实际年产烷基化汽油约16万吨。
3)装置建设性质:在酸催化剂的作用下,液化气中的异丁烷与烯烃反应生成高辛烷值汽油调合组成烷基化油。
1.2设计原则1)选用成熟可靠的工艺技术和控制方案,使设计的装置达到安、稳、长、满、优操作。
2)优化工艺流程并推广应用新工艺、新技术、新材料、新设备,降低生产成本同时降低装置能耗,提高产品质量档次。
3)在保证技术先进、装置生产安全可靠的前提下,利用联合装置的优势,降低能耗并尽量降低工程造价,节省投资。
4)为了降低工程投资,按照“实事求是、稳妥可靠”的原则,提高国产化程度,所需设备立足国内解决,只引进在技术,质量等方面国内难以解决的关键设备,仪器、仪表。
5)采用DCS集中控制,优化操作,以提高装置的运转可靠性,提高产品收率和质量。
6)严格执行国家、地方及主管部门制定的环保和职业安全卫生设计规定、规程和标准,减少“三废”排放,维护周边生态环境,实行同步治理,满足清洁生产的要求。
1.3装置组成:该装置基本由以下几个部分组成:脱甲醇部分、选择加氢部分、原料脱水部分、反应部分、致冷部分、酸碱精制部分和分馏部分、酸碱储存部分、放空部分等组成。
其中致冷部分包括致冷压缩机系统。
装置运行时数和操作班次:装置年开工按8000时。
1.4设计范围本设计范围为本装置所设计的设备、管道、仪表、配电等,装置有关分析化验项目由中心化验室承担。
1.5工艺设计技术方案烷基化装置是以液化气中的烯烃及异丁烷为原料,在催化剂的作用下烯烃与异丁烷反应,生成烷基化油的气体加工装置。
本装置包括原料加氢精制和烷基化两部分。
原料加氢精制的目的是通过加氢脱除原料中的丁二烯。
因为丁二烯是烷基化反应中主要的有害杂质,在烷基化反应过程中,丁二烯会生成多支链的聚合物,使烷基化油干点升高,酸耗加大。
烷基化操作规程
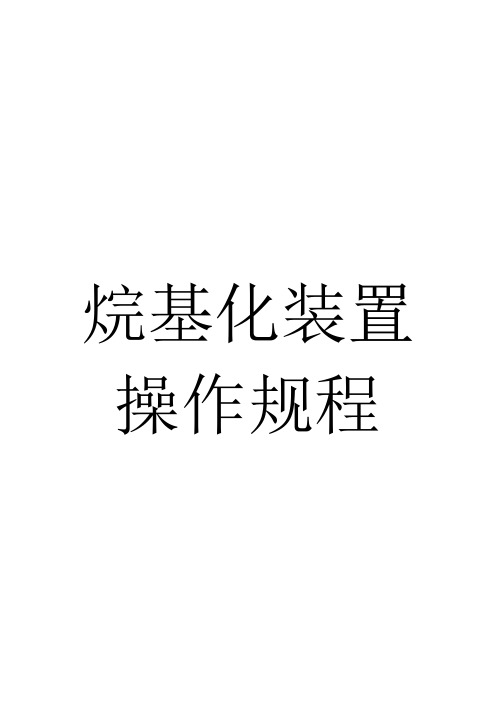
烷基化装置操作规程目录第一章 (4)第二章 (4)2.1 工艺原理 (4)2.2 工艺说明 (5)2.3 原料规格 (11)2.4 产品规格 (14)2.5 界区条件 (15)2.6 公用工程要求 (15)2.7 开车对工艺化学品的要求 (18)2.8 排放物和副产品 (19)2.9 设计考虑 (21)第三章 (22)3.1 烃类原料污染物的影响 (22)3.2 装置进料成分敏感度: (22)3.3 正操操作和控制 (22)第四章 (33)4.1 推荐的样品分析方法 (33)4.2 分析仪一览表 (34)4.3 取样一览表 (34)第五章 (37)5.1 安全淋浴器和洗眼器 (37)5.2 防火系统 (38)5.3 化学品处理和循环 (38)5.4 压力排放系统 (39)第六章 (40)6.0 开车步骤 (40)6.1 公用工程系统 (40)236.2 单机试车(预试车)和准备 (42)6.3 CDAIky装置钝化工艺 (44)6.4 正常开车 (46)第七章 (53)7.0 停车步骤 (53)7.1 从正常操作到全面停车程序 (54)7.2 短期停车 (60)7.3 长期停车 (62)7.4 事故停车步骤: (64)第八章 (65)8.1 反应危害 (65)第一章序言本手册含有烷基化工艺方面包括操作条件和生产能力在内的保密信息。
这些信息不能泄露给未经授权的人员。
本手册还提供了装置系统方和操作程序方面的信息,该手册的目的主要是为操作人员在进行装置详细操作手册准备和编制。
第二章工艺原理2.1 工艺简述该工艺涉及的反应是烯烃同异丁烷的烷基化反应。
同时副反应中有副产品产出。
烷基化初级烷基化反应涉及异丁烷同烯烃、如丁烯的反应,使用硫酸作为催化剂生成高辛烷值的三甲基戊烷异构物。
通常三甲基戊烷异构物被称之为烷基化油。
i-C4+C4H8→2,2,4-三甲基戊烷类似的反应也在异丁烷和其他烯烃如丙烯和戊烷之间发生,分别生成庚烷和壬烷异构物,但是就低选择性生产高辛烷值产品而言,选择丁烯进料更适宜。
傅克烷基化工艺的四个步骤和流程
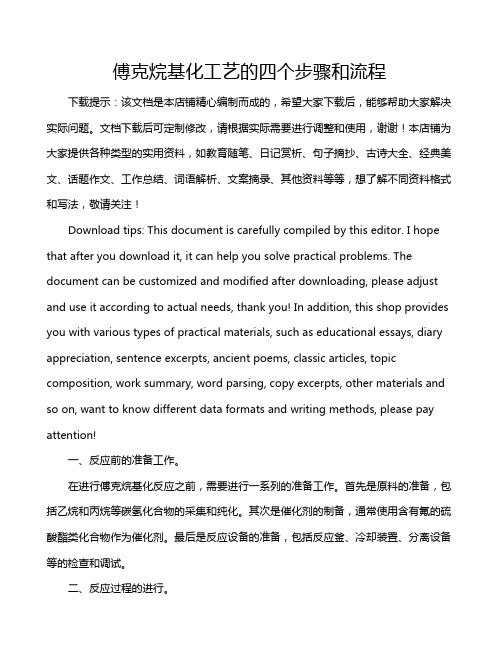
傅克烷基化工艺的四个步骤和流程下载提示:该文档是本店铺精心编制而成的,希望大家下载后,能够帮助大家解决实际问题。
文档下载后可定制修改,请根据实际需要进行调整和使用,谢谢!本店铺为大家提供各种类型的实用资料,如教育随笔、日记赏析、句子摘抄、古诗大全、经典美文、话题作文、工作总结、词语解析、文案摘录、其他资料等等,想了解不同资料格式和写法,敬请关注!Download tips: This document is carefully compiled by this editor. I hope that after you download it, it can help you solve practical problems. The document can be customized and modified after downloading, please adjust and use it according to actual needs, thank you! In addition, this shop provides you with various types of practical materials, such as educational essays, diary appreciation, sentence excerpts, ancient poems, classic articles, topic composition, work summary, word parsing, copy excerpts, other materials and so on, want to know different data formats and writing methods, please pay attention!一、反应前的准备工作。
在进行傅克烷基化反应之前,需要进行一系列的准备工作。
- 1、下载文档前请自行甄别文档内容的完整性,平台不提供额外的编辑、内容补充、找答案等附加服务。
- 2、"仅部分预览"的文档,不可在线预览部分如存在完整性等问题,可反馈申请退款(可完整预览的文档不适用该条件!)。
- 3、如文档侵犯您的权益,请联系客服反馈,我们会尽快为您处理(人工客服工作时间:9:00-18:30)。
烷基化部分
(一)概述:
车间概况及特点:
烷基化装置的原料是从气体分馏得到的异丁烷和烯烃等作为反应原料,在硫酸催化剂作用下用液氨间接冷却的立式管壳式反应器中进行烷基化反应,然后将反应产物进行分馏即可得到高辛烷值的汽油组分——工业异辛烷,又称轻烷基化池由于轻烷基化油辛烷值高(马达法89—94,感铅性能好(如4毫升四乙基铅马达法辛烷值可达108),因此烷基化过程是炼油工业中一十重要的工业过程.本装置生产系统由两大部分组成,即烷基化反应,分馏部分和氨冷冻部分.
<三)。
流程简述
反应原料自气体分馏工段烷基化原料塔回流泵(B-207a.b)与循环异丁烷经原料一异丁烷混合器(C-301)混合后(*kg/cm2绝压*℃)进入原料冷前脱水罐(R-302a)脱水自(R-302a)上部出来的异丁烷丁烯馏份经循环异丁烷-—产物换热器(H-301)与反应产物二次沉降罐(R-303c)来的反应产物换冷至*℃再经反应原料—循环异丁烷冷却器(L-301)用液氨冷却至*℃进入原料冷后脱水罐(R-302b)进行第二次脱水,(R-302a.b),的水间断地系统。
反应热借助于安装在反应器的翅片管束用液氢蒸发取走烷基化产物和硫酸乳化液由反应器上部出来进入反应物沉降
罐(R-303a.b)沉降分离,分离出来的硫酸循环使用.反应产物由(R-303a.b)部出来进入反应物二次沉降罐(R-303c) 进行二次沉降分离,(R-303c)上部出来的反应产物经(H—301),与循环异丁烷换热后,经产物碱洗混合器.(C302)与碱液混合进入反应产物碱洗罐(R-305),自(R-305)顶出来经产物水洗混合器(C-303)与*~*℃温水混合后进入反应产物水洗罐(R-306)水洗后反应产物进入(T-301)进科缓冲罐(R-307)当*%的硫酸降至*%以下时,不再使用,由(R-302a.b)压入废酸沉降罐(R-304)沉降分离出来的废硫酸经循环硫酸泵送入废酸贮罐(R-324),用汽车槽车送往奎屯硫酸厂处理。
经过碱洗,水洗的反应产物自(R-307)用((T-301)进料泵(B-302a.b)打入脱异丁烷塔(T301),罐顶维持*个绝压,+*℃士*℃,异丁烷馏分经脱异丁烷塔顶空冷器(L-302)冷凝冷却后进入回流罐(R-308),由回流泵(B-303 a.b)一部分打入反应器,一部分作回流,多余的出装置,塔底烷基化油经重沸器(H-302)蒸汽加热,维持*个绝压,*±5℃,并压至脱正丁烷塔(T-302),塔顶维持*kg/cm2绝压,*℃±3℃,顶部正丁烷馏份经塔顶冷凝器(L-302)冷凝冷却后进回流罐(R-309),由回流泵(B-304 a.b)一部分作回流,一部分出装置至高压罐区.塔底烷基化油经重沸器(H-303),蒸汽加热维持*kg/cm2绝压,*℃±5℃并压至再蒸馏塔(T-303),塔顶维持*kg/cm2绝压,*0℃±5℃,顶部轻烷基化油经(T-303)顶空冷器(L-304)冷凝冷却后,进入回流罐(R-310),
由回流泵(B-305 a.b)一部分作回流,一部分经轻烷基化油碱洗混合器与碱液混合(C-304),进入轻烷基化油碱洗罐(R-313),产品经分析合格后,再用轻烷基化油泵(B-309)送至全厂成品罐区,塔底重烷基化油经重沸器(H-304)蒸汽加热,维持*kg/cm2绝压,*℃±5℃,重烷基化油经过塔底冷却器(L-305)冷却后进入中间罐(R-312)用重烷基化油泵(B-306)送出装置。