用等离子淬火技术处理机床导轨
等离子体表面改性技术(报告)

等离子体表面改性技术……吴师妹整理I前沿材料表面处理技术是U前材料科学的前沿领域,利用它在一些表面性能差和价格便宜的基材表面形成合金层,取代昂贵的整体合金,节约贵金属和战略材料,从而大幅度降低成本。
科学技术和现代工业的发展,对摩擦、磨损、腐蚀和光学性能优异的先进材料的需要日益增长,这导致了整个材料表面改性技术的发展与进步,其中等离子体表面改性技术发挥了重要作用。
等离子表面处理因其性能的优势和低廉的成本已成为材料科学领域最活跃的研究方向之一。
2等离子体表面改性的原理等离子体是一种物质能量较拓的聚集状态,它的能量范用比气态、液态、固态物质都高,被称为物质的笫四态,存在具有一定能量分布的电子、离子和中性粒子,在与材料表面的撞击时会将自己的能量传递给材料表面的分子和原子,产生一系列物理和化序过程。
一些粒子还会注入到材料表面引起碰撞.散射、激发、重排、异构、缺陷、晶化及非晶化,从而改变材料的表面性能。
3等离子体表面改性技术的种类根据温度不同,等离子体可分为拓温等离子体和低温等离子体(包括热等离子体和冷等离子体)。
高温等离子体的温度高达10&K〜10吆,在太阳表面、核聚变和激光聚变中获得。
. 丘/体一般为稠离子体,冷等离子体一般为稀薄等离子体。
在材料表面改性技术中,溅射、离子镀、离子注入、等离子化学热处理丄艺应用的是在低压条件下放电产生的低压(冷)等离子体,而等离r 喷涂、等离r淬火及多元共渗相•化、等离子熔覆価冶金等工艺中应用的是低温等离子体中的稠密热等离子体,通常指压缩电弧等离子束流。
3.1低压(冷)等离子体表面处理技术近年来,低压等离子体在表面镀膜、表面改性及表面聚合方面发挥着越来越重要的作用。
3.1.1溅射和离子镀溅射镀膜是基于离子轰击靶材时的溅射效应,采用的最简单装置是直流二极溅射,其它类型的溅射设备有射频溅射磁控溅射、离子束溅射等,其中磁控溅射山于沉积速率高,是U前工业生产应用最多的一种。
MaxCUT系列数控等离子

MAXCUT是我公司为满足板材坡口切割需求的客户而开发的一款高性价比的多功能重型数控等离子/火焰切割机。该机型在船舶制造、港口机械、大型板材下料、桥梁工程、工程机械等行业得到广泛运用,主要适用于批量切割下料量大,需同时采用多割炬进行同时切割的高效率切割的下料工场。
MAXCUT最大跨距可达12000mm,纵向轨长由客户自由确定,最高空程运行速度可达16000mm/min,机器可以根据客户需求通过安装不同功能装置,实现普通等离子切割,等离子坡口切割、普通火焰切割、火焰破口切割、切割轨迹喷粉划线标记、重力冲打钻孔定位标记、高频冲打切割工件标识标记、板材切割工件标识自动喷码以及板材钻孔攻丝等功能。切割平台根据客户需要可配置抽风除尘切割工作平台、水床切割平台。
MAXCUT数控等离子/火焰切割机结构采用人性化的设计,外形风格简单大方,机体采用型钢焊接加工后经处理消高,整机刚型好,纵横向机架采用斜齿齿轮齿条传动,采用中惯量伺服电机及大扭减速机构作机床的驱动装置,使机床达到更好的运行稳定性和低噪音,机床传动斜齿条采用国内最先进的数控齿条加工设备精制而成,确保了机械运行精度和使用寿命,机器的大小车纵横导向机构采用了自行设计的获得国家专利的免维护弹性导向机构和圆导轨导向机构,是整机运行精度得到很大的提高。
MAXCUT是一款性价比非常高的大型多功能数控等离子/火焰切割机,可以实现边切割边换料,不停机;满足客户不间断连续切割,提高机床运行利用率和切割效能,降低客户使用成本,适应大型切割客户的广泛要求。
MAXCUT可配置SmartNC,SmartPlus等数控系统和Q-Panel、Z-Panel操作控制台,操作简单,界面友好,对作业人员的要求低,安全可靠。
机床直线导轨用钢的热处理工艺优化
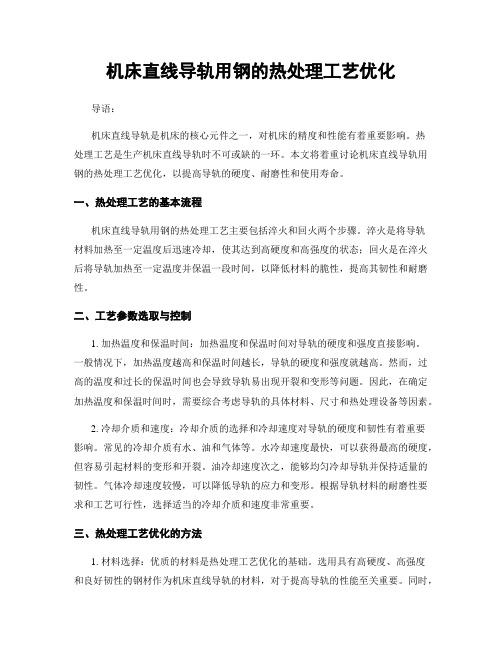
机床直线导轨用钢的热处理工艺优化导语:机床直线导轨是机床的核心元件之一,对机床的精度和性能有着重要影响。
热处理工艺是生产机床直线导轨时不可或缺的一环。
本文将着重讨论机床直线导轨用钢的热处理工艺优化,以提高导轨的硬度、耐磨性和使用寿命。
一、热处理工艺的基本流程机床直线导轨用钢的热处理工艺主要包括淬火和回火两个步骤。
淬火是将导轨材料加热至一定温度后迅速冷却,使其达到高硬度和高强度的状态;回火是在淬火后将导轨加热至一定温度并保温一段时间,以降低材料的脆性,提高其韧性和耐磨性。
二、工艺参数选取与控制1. 加热温度和保温时间:加热温度和保温时间对导轨的硬度和强度直接影响。
一般情况下,加热温度越高和保温时间越长,导轨的硬度和强度就越高。
然而,过高的温度和过长的保温时间也会导致导轨易出现开裂和变形等问题。
因此,在确定加热温度和保温时间时,需要综合考虑导轨的具体材料、尺寸和热处理设备等因素。
2. 冷却介质和速度:冷却介质的选择和冷却速度对导轨的硬度和韧性有着重要影响。
常见的冷却介质有水、油和气体等。
水冷却速度最快,可以获得最高的硬度,但容易引起材料的变形和开裂。
油冷却速度次之,能够均匀冷却导轨并保持适量的韧性。
气体冷却速度较慢,可以降低导轨的应力和变形。
根据导轨材料的耐磨性要求和工艺可行性,选择适当的冷却介质和速度非常重要。
三、热处理工艺优化的方法1. 材料选择:优质的材料是热处理工艺优化的基础。
选用具有高硬度、高强度和良好韧性的钢材作为机床直线导轨的材料,对于提高导轨的性能至关重要。
同时,还需要综合考虑材料的耐磨性、耐腐蚀性和可加工性等因素,在材料选择上要进行全面权衡。
2. 工艺参数的精确控制:在热处理工艺中,控制工艺参数的精确度对于优化导轨的性能至关重要。
采用精确的温度控制设备和冷却控制方式,以确保加热温度和保温时间的准确控制,进而提高导轨的硬度和强度。
同时,还需要针对不同尺寸和形状的导轨进行针对性的优化,提高工艺的适应性和普适性。
高端数控感应淬火机床原理

高端数控感应淬火机床原理1.引言随着制造业的发展,数控机床在金属加工领域的应用日益广泛。
感应淬火机床作为一种高端数控机床,其原理与传统的淬火机床有所不同,具有更高的加工精度和效率。
本文将介绍高端数控感应淬火机床的原理及其工作过程。
2.感应淬火的基本原理感应淬火是一种利用电磁感应原理进行加热和淬火的方法。
在感应淬火机床中,通过电磁感应线圈产生高频交流电场,使工件表面产生感应加热,然后通过快速冷却来实现淬火过程。
感应淬火具有加热均匀、温度可控、淬火速度快等优点,因此在金属加工领域中得到了广泛的应用。
3.高端数控感应淬火机床的结构高端数控感应淬火机床由数控系统、感应装置、冷却系统、夹具等部分组成。
其中数控系统为感应淬火机床的核心,控制整个加工过程的参数和轨迹,具有高精度、高效率、高自动化程度等特点。
3.1数控系统数控系统是感应淬火机床的核心部件,其主要功能是控制电磁感应线圈的工作状态,调节加热功率和加热时间,实现对工件的精准加热和淬火。
数控系统通常采用PLC或CNC控制,能够实现多轴联动控制、自动化加工流程、参数设定和调整等功能。
3.2感应装置感应装置是感应淬火机床中的重要部件,通过高频交流电场对工件进行感应加热。
感应装置通常由电磁感应线圈、电源装置、冷却系统等部分组成。
电磁感应线圈根据工件的形状和尺寸设计成不同的形状和尺寸,有效地实现对工件的均匀加热。
3.3冷却系统冷却系统是感应淬火机床中的关键部件,其主要作用是对经过加热的工件进行快速冷却,实现淬火过程。
冷却系统通常采用循环水冷却或喷水冷却的方式,能够实现对工件的快速冷却和温度控制。
3.4夹具夹具是感应淬火机床中的辅助部件,用于固定和夹持工件,确保加工过程中工件的位置和姿态的稳定性。
夹具通常根据工件的形状和尺寸设计成不同的形状和尺寸,能够适应不同加工需求。
4.高端数控感应淬火机床的工作原理高端数控感应淬火机床的工作原理是将工件放置在感应装置中,通过数控系统对电磁感应线圈进行控制,实现对工件的精准加热和淬火。
热处理中的等离子体热处理技术
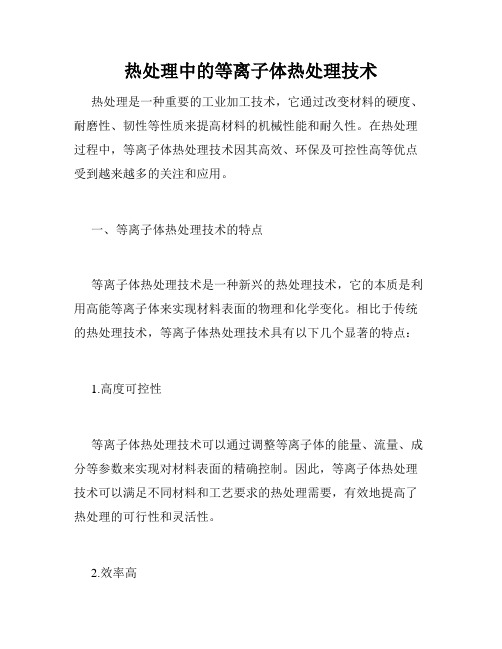
热处理中的等离子体热处理技术热处理是一种重要的工业加工技术,它通过改变材料的硬度、耐磨性、韧性等性质来提高材料的机械性能和耐久性。
在热处理过程中,等离子体热处理技术因其高效、环保及可控性高等优点受到越来越多的关注和应用。
一、等离子体热处理技术的特点等离子体热处理技术是一种新兴的热处理技术,它的本质是利用高能等离子体来实现材料表面的物理和化学变化。
相比于传统的热处理技术,等离子体热处理技术具有以下几个显著的特点:1.高度可控性等离子体热处理技术可以通过调整等离子体的能量、流量、成分等参数来实现对材料表面的精确控制。
因此,等离子体热处理技术可以满足不同材料和工艺要求的热处理需要,有效地提高了热处理的可行性和灵活性。
2.效率高等离子体热处理技术具有高热效率和快速热处理的优势,可以将材料表面的温度迅速升高至所需的温度,并在短时间内实现所需的热处理效果。
这极大地提高了材料加工效率和生产效益。
3.环保性好等离子体热处理技术不需要使用化学试剂和溶剂等化学物质,可以大大减少对环境的污染和危害。
同时,等离子体热处理技术还可以降低能源消耗和废气排放,对环境友好。
二、等离子体热处理技术的应用领域等离子体热处理技术可以广泛应用于多个领域,如金属材料、电子材料、生物材料等。
1.金属材料在金属材料的表面热处理中,等离子体热处理技术可以实现对金属表面的硬化、氮化、氧化、硅化等多种功能的改善。
这可以提高金属材料的耐磨性、耐腐蚀性和韧性等机械性能,满足各种工业材料的需求。
2.电子材料在电子材料中,等离子体热处理技术可以实现对半导体材料和电子器件表面的清洁、刻蚀、抛光、氧化等等多种功能的改善。
这可以提高电子材料的电学性能、稳定性和可靠性,为电子领域的发展做出贡献。
3.生物材料在生物材料中,等离子体热处理技术可以实现对生物材料表面的功能性改善和生物相容性的提高。
这可以增强生物材料的可用性和生物标准,促进生物医学的发展。
三、等离子体热处理技术的优势等离子体热处理技术不仅具有高度的可控性和环保性,还有以下几个优势:1.改善材料表面性能:等离子体热处理技术可以对材料表面的物理和化学性质进行改善,从而提高材料的表面硬度、耐磨性、腐蚀性等性能。
龙门式数控等离子火焰切割机参数要求
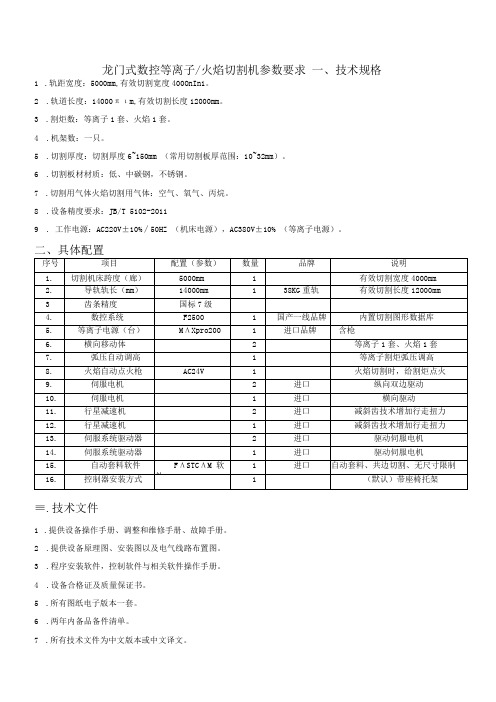
龙门式数控等离子/火焰切割机参数要求一、技术规格1.轨距宽度:5000mm,有效切割宽度400OnIn1。
2.轨道长度:14000πιm,有效切割长度12000mm。
3.割炬数:等离子1套、火焰1套。
4.机架数:一只。
5.切割厚度:切割厚度6~150mm (常用切割板厚范围:10~32mm)。
6.切割板材材质:低、中碳钢,不锈钢。
7.切割用气体火焰切割用气体:空气、氧气、丙烷。
8.设备精度要求:JB/T 5102-2011
9. 工作电源:AC220V±10%∕50HZ (机床电源),AC380V±10% (等离子电源)。
≡.技术文件
1.提供设备操作手册、调整和维修手册、故障手册。
2.提供设备原理图、安装图以及电气线路布置图。
3.程序安装软件,控制软件与相关软件操作手册。
4.设备合格证及质量保证书。
5.所有图纸电子版本一套。
6.两年内备品备件清单。
7.所有技术文件为中文版本或中文译文。
等离子淬火技术在数控机床导轨上的应用

连 为 民 , 思 沧 , 小琦 刘 唐
( 中科技 大学 机 械学 院 湖北 武汉 华 摘 40 7 ) 3 04
要: 分析 介绍 了等离 子体 的 基本概 念 及 其加 热 原 理 。通 过 对 等 离子 淬 火 技术 的研 究 , 并结 合 机 床 导 轨 的 实 际情 况 , 到 了一种 可 以替 代传统 导 轨加工 工 艺 的新途 径 。实践 证 明 , 找 利用等 离 子技术 处 理机 床 导轨 , 有工 作性 具
等 离 子发 生 器 ( 离 子 距 ) 对 机 床 导 轨 进 行 表 面 淬 等 ,
热 区 迅 速 冷却 , 成 细 密 的 白 口或 隐 针 马 氏体 类 的 高 形
硬 度 组 织 , 高 表 面 的 硬 度 和 耐 磨 性 , 且 处 理 工 件 提 而
的变 形 小 、 效率 高 。 一 般 的 机 床 导 轨 , 等 离 子 淬 火 经 后 , 硬 化 层 硬 度 可 达 HV 0 其 80~9 0 深 度 可 达 0 1 0, .0~
能稳 定 , 工作 效 率 高 , 备 投资 小 , 设 处理 成本 低 等优 点 。
关键 词 - 面淬 火 ; 表 等离 子 ; 轨 ; 控机 床 导 数
中 图 分 类 号 :G 5 T 16 文献标 识码 : B 文 章 编 号 :0 74 1 (02 0 .0 90 10 .44 20 )30 2 —1
用 等 离 子 淬 火 技 术 处 理 机 床 导轨 , 用 的是 常 压 采 下 的低 温等 离 子 束 , 质 气 体 为 A 气 。 其 工 作 过 程 介 r 是 : 床 导 轨 固定 在 工 作 台 上 静 止 不 动 , 用 数 控 机 机 利 床 进 行 三 坐标 联 动 , 确 地 控 制 安 装 在 机床 主 轴 上 的 精
数控等离子操作方法步骤是

数控等离子操作方法步骤是
数控等离子操作的步骤一般包括以下几个:
1. 准备工作:根据工艺要求选择合适的等离子电极和喷嘴,检查设备运行状态,清洁工作区域。
2. 设定程序:通过数控系统输入相关参数,包括等离子功率、气体流量、切割速度等。
3. 加气与预热:将气体(通常是氧气、氮气或空气)引入等离子喷嘴,产生等离子电弧。
在切割前对工件进行预热,使其达到适宜的温度。
4. 开始切割:将工件放置在切割台上,并通过数控系统控制切割头的移动,精确定位切割起始点。
等离子电弧与工件接触后,切割头沿着预设的路径进行运动,同时喷射气体将熔化的金属吹散。
5. 路径控制:数控系统通过移动切割头的速度和方向来控制切割路径,通常使用直线或曲线路径。
6. 程序监控:操作人员通过监控数控系统的界面,实时监测切割过程中的参数,如切割速度、气体流量等,以及检查切割质量。
7. 切割后处理:切割完成后,对切割件进行清理,包括去除残留的熔渣和金属粉尘,进行表面处理等。
8. 关闭设备:切割作业结束后,关闭等离子切割系统的电源和气源,并进行设备的维护和保养工作。
需要注意的是,具体的数控等离子操作步骤可能会因不同的设备和工艺要求而有所差异,上述步骤仅为一般情况下的操作流程。
数控火焰等离子切割机操作指导书

数控火焰(等离子)切割机操作指导书(ISO9001-2015/ISO45001-2018)一、工作前的准备工作:1、操作者应熟悉该机性能、技术参数,经培训考试合格后,定人定机操作。
2、各气管、阀门,不允许有泄漏,检查安全装置是否有效,检查所提供气体压力(应符合规定),空压机、油水分离器等内积水和杂质。
检查消耗品及割炬防撞碰装置,设备附近禁止存放易燃易爆物品,必须设立灭火器以及其它消防器材。
3、检查所有电气箱是否处于密闭状态。
不允许电气箱处于开启状态进行切割工作。
4、严禁在切割机导轨、工作面放置物品。
不得在上面敲打、校直和修整工件。
5、开机前应检查导轨、齿条及床身。
按照说明书的要求对各个润滑点进行润滑保养。
二、工作中的注意事项:1、开机:主电源开关合上,操作屏面下部拧开钥匙,进入程序界面,5秒钟后,按任意键进行进入菜单,按照菜单的提示进行操作,切记,根据板厚和材质,选择适当割咀和切割方式(即火焰切割或等离子切割机。
重新设定内存中的切割速度和预热时间,通过键盘设定火焰切割预热氧、切割氧合理压力、等离子弧焊电源电流、引弧气气压及流量、切割气气压及流量、涡流气气压及流量、涡流气气压及流量:以及引弧时间:切割速度、割缝补偿、手动调节引弧高度和弧压等参数的设定。
2、调整被切割的钢板尽量与轨道保持平行。
3、根据自己切割的图形在操作屏内的图形管理进行选择,设定,图形管理中没有的图形,可通过CAD绘图通过程序转化程*TXT文本文档,通过U盘(无病毒)的方式导入。
并进行设定。
新工件程序输入后,应先试运行,确认无误后再投入运行。
4、检查加热火焰以及切割射流,如发现割咀弄脏或损坏,应及时更换、清理。
割咀应用随机专用工具清理。
5、切割过程中发生回火现象,应及时切断电源,停机关闭气体阀门,回火阀片如被烧化,应停止使用,等待专业维修人员进行更换。
6、操作人员上机时,要时刻注意设备运行状况,如发现有异常情况,应按动紧停开关,及时退出工作位,严禁开机脱离现场。
数控等离子淬火机床

冷 气 壁 温 度 低 , 离 度很 低 几 乎 不 能 通 过 电 流 , 使 电 弧 电 电 迫
流往 电离度 高的 中心部位 流过 , 即电弧 向 中心部 位 压缩 , 从 而形成所 谓 的 “ 收缩 ” 由于 喷 嘴孔 径本 身很 小 , 加 上 热 。 再 等离子 弧弧柱 周 围的 冷 气壁 依 附 在 喷 嘴孔 道 壁 面上 , 弧 使
密 的 高 硬 度 组 织 , 而 不 需 要 贴 塑 就 可 以 达 到 工 艺 要 从
度 组 织 , 高 表 面 的 硬 度 和 耐 磨 性 , 且 处 理 工 件 的 变 提 而 形小 、 率 高 。一般 的机 床 导轨 , 等离 子 淬火 后 , 效 经 其
硬 化 层 硬 度 可 达 8 0 ~9 0 0 0 H ̄ , 度 可 达 0.0 ~ 深 1 0.0 2 mm, 织 为 细 小 的 隐 针 深 度 范 围 内 , 硬 度 变 化 不 明 显 , 全 能 够 达 到 使 其 完
立式数控淬火机床操作说明

立式数控淬火机床操作说明1. 介绍立式数控淬火机床是一种先进的金属热处理设备,用于对金属工件进行淬火处理。
本文档将详细介绍立式数控淬火机床的操作步骤和注意事项,以确保安全、高效地进行淬火处理。
2. 操作步骤步骤1:开机准备在进行任何操作之前,请确保机床的电源已经连接,并检查电源开关和控制系统是否正常工作。
同时,检查冷却系统的工作状态,并确保冷却液和润滑油的供应充足。
步骤2:加载工件将待处理的工件放置在机床的工作台上,并使用夹具固定,以确保工件在淬火过程中的稳定性。
步骤3:设置淬火参数根据工件的具体要求,设置淬火的温度和时间参数。
这些参数可以通过机床的控制系统进行调整,确保淬火过程的准确控制。
步骤4:开始淬火确认设置参数后,按下启动按钮,机床开始进行淬火处理。
此时,机床会自动将工件加热至设定温度,并在温度达到后保持一段时间。
步骤5:冷却处理在保持工件温度一段时间后,机床会自动进行冷却处理。
冷却过程可以通过控制系统进行调整,以确保工件达到所需的硬度和强度。
步骤6:卸载工件待淬火处理完成后,将工件从机床上卸载,并进行必要的后续处理,如淬火工件表面的清洁、抛光等。
3. 注意事项•在操作机床之前,请确保穿戴好个人防护装备,如手套、护目镜等。
•严禁在机床运行时触摸工件或机床的移动部件。
•在操作机床时,请保持注意力集中,严禁分心或玩弄手机等物品。
•在设置淬火参数时,请确保参数的准确性和合理性,以避免损坏工件或机床。
•在进行冷却处理时,要确保冷却液和润滑油的供应充足,并注意冷却液的安全使用。
•在卸载工件时,要格外小心,并使用必要的工具和夹具以确保安全。
4. 结论本文档介绍了立式数控淬火机床的操作步骤和注意事项。
通过遵循正确的操作流程和注意事项,可以确保安全地进行淬火处理,提高工件的硬度和强度。
在操作过程中,请始终保持注意力集中,并妥善保养机床,以确保其正常和高效的工作。
机床导轨淬火硬度标准

机床导轨淬火硬度标准
机床导轨一般采用淬火工艺进行硬化处理,以提高其耐磨、抗压和抗腐蚀性能。
淬火硬度标准一般根据具体的材料和使用要求而定,常见的标准有以下几种:
1. HRC标准:HRC是硬度测试中的一个单位,通常用于测量材料的硬度。
机床导轨一般要求在50-60 HRC左右,以保证其具备足够的硬度和耐磨性。
2. HV标准:HV也是硬度测试中的一个单位,常用于测量金属材料的硬度。
机床导轨的淬火硬度标准一般要求在450-550 HV之间,取决于导轨材料和使用要求。
3. Rockwell C标准:Rockwell C硬度测试是一种常用的金属硬度测试方法。
机床导轨的淬火硬度标准一般要求在50-60 Rockwell C之间,以确保导轨具备足够的硬度和耐磨性。
需要注意的是,硬度标准通常是根据具体的要求和性能来确定的,不同的机床导轨可能有不同的硬度要求。
因此,在具体的应用中,可以根据所选用的材料、导轨的尺寸和要求等因素确定合适的淬火硬度标准。
等离子激光切割机防护罩导轨防护罩滑道风琴保护罩

等离子激光切割机防护罩导轨防护罩滑道风琴保护罩等离子激光切割机防护罩导轨防护罩滑道风琴保护罩柔性风琴防护罩用尼龙革、塑料织物或合成橡胶折叠、缝制或热压而成,风琴防护套内有PVC板材支撑,可耐热、耐油、耐冷却液、瞬间接触温度可达2000℃,采用绝缘支撑板。
行程速度可达100m/min,根据用户要求、风琴防护套除生产平面风箱式上可带不锈钢片,也可生产圆形、六角形、八角形等。
风琴防护罩优势:● 此类护罩硬物冲撞不变形、寿命长、密封好和运行轻便等特点,该产品使用专用的材料,耐冷却剂,防油、铁屑,护罩具行程长和压缩小的优点。
● 柔性风琴防护罩内没有任何金属零件,不用担心导轨防护罩工作时会出现零件松动而给机器造成严重的破坏。
耐正负压圆形防护罩,里外钢丝圈圆形防尘罩,油缸气缸防护罩防尘罩:防尘、防水、防油、耐腐蚀、抗老化、直径大小可与按照要求制作、护罩一般比值:10:1、材质说明:防水布、防火布、耐高温、阻燃布、塑胶布、尼龙复合布、石棉布、橡胶布、尼龙革、人造革、三防布、五防布、增强尼龙布等,客户订货时需要对使用环境来选择材质。
(1). 防护罩防漏可任意弯曲伸缩管的直径和长度不受限制均可按客户要求制(2) 连接方式:一两端颈口卡箍连接,二两端法兰用螺丝连接,三一端颈口卡箍连接一端法兰螺丝连接(3)材料专用布内衬钢丝, 三防布内衬钢丝,塑胶布内衬钢丝,石棉布内衬钢丝耐高温布内衬钢丝,阻燃布内衬钢丝,防火布内衬钢丝,防油防水布内衬钢丝。
(4) 定货要求:客户必须提供一.拉伸后的长度二.收缩后的厚度三.保护件的直径四.护罩的外径要求连接方式五.使用环境及材料要求(5). 技术说明一般护罩拉伸后的长度与收缩后的厚度比值为一米比十厘米也可按客户要求加工制作比值更大或更小的伸缩护套产品。
分开式防护罩(拉链式)、采用缝纫设备制作成型。
性能:拉链式防护罩给机床厂家解决了不用拆卸设备的麻烦,拉链式防护罩,中间有一条长长的拉链,拉开以后直接套在油缸上,在拉上拉链这样就可以使用了,客户订货时需要对使用环境来选择材质。
导轨的选材及热处理工艺
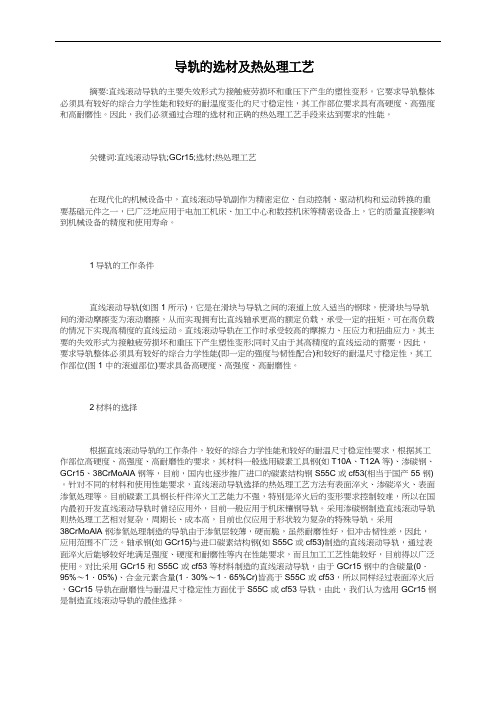
导轨的选材及热处理工艺摘要:直线滚动导轨的主要失效形式为接触疲劳损坏和重压下产生的塑性变形。
它要求导轨整体必须具有较好的综合力学性能和较好的耐温度变化的尺寸稳定性,其工作部位要求具有高硬度、高强度和高耐磨性。
因此,我们必须通过合理的选材和正确的热处理工艺手段来达到要求的性能。
关键词:直线滚动导轨;GCr15;选材;热处理工艺在现代化的机械设备中,直线滚动导轨副作为精密定位、自动控制、驱动机构和运动转换的重要基础元件之一,已广泛地应用于电加工机床、加工中心和数控机床等精密设备上,它的质量直接影响到机械设备的精度和使用寿命。
1 导轨的工作条件直线滚动导轨(如图1 所示),它是在滑块与导轨之间的滚道上放入适当的钢球,使滑块与导轨间的滑动摩擦变为滚动磨擦,从而实现拥有比直线轴承更高的额定负载,承受一定的扭矩,可在高负载的情况下实现高精度的直线运动。
直线滚动导轨在工作时承受较高的摩擦力、压应力和扭曲应力,其主要的失效形式为接触疲劳损坏和重压下产生塑性变形;同时又由于其高精度的直线运动的需要,因此,要求导轨整体必须具有较好的综合力学性能(即一定的强度与韧性配合)和较好的耐温尺寸稳定性,其工作部位(图1 中的滚道部位)要求具备高硬度、高强度、高耐磨性。
2 材料的选择根据直线滚动导轨的工作条件,较好的综合力学性能和较好的耐温尺寸稳定性要求,根据其工作部位高硬度、高强度、高耐磨性的要求,其材料一般选用碳素工具钢(如T10A、T12A 等)、渗碳钢、GCr15、38CrMoAlA 钢等,目前,国内也逐步推广进口的碳素结构钢S55C 或cf53(相当于国产55 钢) 。
针对不同的材料和使用性能要求,直线滚动导轨选择的热处理工艺方法有表面淬火、渗碳淬火、表面渗氮处理等。
目前碳素工具钢长杆件淬火工艺能力不强,特别是淬火后的变形要求控制较难,所以在国内最初开发直线滚动导轨时曾经应用外,目前一般应用于机床镶钢导轨。
采用渗碳钢制造直线滚动导轨则热处理工艺相对复杂,周期长、成本高,目前也仅应用于形状较为复杂的特殊导轨。
车床导轨修复技术及工艺

车床导轨修复技术及工艺胡刚【摘要】车床占通用机床使用量50%.车床使用多年后,其他部分如床头箱、走刀箱、溜板箱、尾座等,都可以通过更换齿轮、轴承、其他零件得以更新,唯独导轨或床鞍燕尾(直线移动部分)因有局部磨损而影响加工精度.导轨的修复是一个难题,通常一是将床身部分拆解开运到大修厂(磨削)导轨,二是人工借助工具、量具修磨刮研方法.然而,前者要拆解车床,后者工期较长.本文通过专用的、可移动的小型磨床和一套完整的工艺,将旧车床导轨修复或改造成数控车床.【期刊名称】《现代制造技术与装备》【年(卷),期】2017(000)004【总页数】4页(P123-126)【关键词】车床;导轨;修复【作者】胡刚【作者单位】青岛东田智能科技有限公司,青岛 266101【正文语种】中文车床主导轨有两付,一付是床鞍导轨,一付是尾座导轨。
尾座的V型导轨前端位于床鞍下面,永远不会磨损;后端位于床尾,磨损微乎其微。
本文提出的方法根据维修师傅多年经验,自制一种小型移动式车床导轨修复专用磨床,核心技术是以尾座导轨为主要定位基准,加以调整然后修复。
此外,还有相应的配套工艺,具有移动方便、现场维修、定位快捷、不需要对待修车床进行拆解的特点,大大提高了人工铲刮的效率和质量。
(1)先做一个直径大于Φ50长300mm左右圆柱体,用千分尺或百分尺分段测量圆度误差和椭圆度误差,以便与修复后作对比。
(2)检验主轴跳动:用千分表或百分表检查车床主轴径向及轴向跳动,按标准在0.01~0.02mm以内;用检验棒(插入主轴锥孔)检验,近端0.01mm,远端(300mm)0.02mm。
如果差别过大,原因可能是:主轴前端轴承锁紧螺母松动;轴承老化;主轴变形。
根据实测进行修调并记录实测值,然后转入下一工序。
检验棒——量具(同轴度0.002mm)。
(3)调整水平:用检验棒插入主轴锥孔,将机床水平重新调整(有些机床长时间工作不调整,振动使得水平偏移)。
此时,应以床身后床身平面未磨损面及检验棒为基准。
铸铁导轨高频淬火硬度

铸铁导轨高频淬火硬度
铸铁导轨作为一种常见的机械零部件,在使用过程中需要具备较高的硬度和耐磨性能。
因此,通过高频淬火技术对铸铁导轨进行处理,可以大幅提升其硬度和耐磨性能。
高频淬火是一种传热速度极快的热处理方法,通过对铸铁导轨进行高频电流加热,使其表面迅速达到高温状态,然后通过快速冷却的方式使其表面形成坚硬的马氏体组织。
这种处理方式不仅硬度高,而且表面的残余应力也较小,不易引起裂纹和变形。
在实际应用中,铸铁导轨的高频淬火硬度可以通过Rockwell硬度测试机进行测试。
一般来说,淬火后的硬度可以达到HRC50-60左右,比无处理的铸铁导轨提高了近倍。
同时,高频淬火处理还可以提升铸铁导轨的耐磨性能和疲劳寿命,从而延长其使用寿命。
总之,铸铁导轨的高频淬火处理是一种有效提升其硬度和耐磨性能的方法,可以满足机械设备的高要求。
- 1 -。
等离子火焰切割机安全操作规程

数控等离子火焰切割机安全操作规程一、工作前必须穿戴好劳动防护用品,操作时必须戴好防护眼镜。
二、通电开机前应检查机器周围附近,导轨两侧是否有杂物,10米以内不准有易燃物品(包括有易燃易爆气体产生的气皿管线),所用的气源、水源、电源是否处于正常的工作状态。
检查与机床相关的接地有无松动,各个电缆接头插座是否完好无损。
检查气瓶与橡胶软管的接头,阀门及紧固件均应紧固牢靠,不准有松动、破损和漏气现象,检查导轨齿条和床身。
检查消耗品及割炬防撞碰装置。
三、机床开动后身体和四肢不准接触机器运动部位,以免发生伤害,维护保养设备时应断电停车进行。
四、禁止使用带有油污的工具,手套等接触氧气瓶及其附件、阀门、橡胶胶管。
禁止使用易产生火花的工具开启氧气瓶或乙炔气阀门。
五、如果发生意外停电,应及时关闭主电源开关。
六、气瓶或汇流排管道冻结时,严禁用火烤或用工具敲击,氧气阀或管道可用40℃的水温融化,气瓶应有防止阳光直射措施。
七、开机后应手动低速x,y方向开动机床,检查确认有无异常情况。
八、手动升降割炬,检查动作有无异常。
九、启动等离子发生器,根据材料厚度调整电流。
十、机器运行中,操作工应坚守岗位,随时注意机器运行状况,如遇紧急情况应立即处理,保证安全运行。
严禁超性能使用切割机。
十一、禁止带电拆卸自动点火控制装置,防止高压触电。
经常检查等离子电缆有无裸露破损,更换电缆时应关闭电源。
十二、对新的工件程序输入后,应先试运行,并检查其运行情况,确认无误后再投入运行。
十三、在运行中发生报警和其他意外故障时,应使用暂停键停止运行,然后作相应的操作处理。
应尽量避免使用紧急停止按钮。
十四、吊运工件时应与行车工密切配合,注意避免吊物与设备碰撞,在上下料时应遵守“起重、搬运工”安全操作规程。
十五、下班关机前,应将系统退回操作主菜单,将割炬上升到最高位置,各个控制开关应复位。
先关闭系统电源,再关闭总电源,关闭气源、水源,检查各控制手柄是否在关闭位置,确认无误后方可离开。
- 1、下载文档前请自行甄别文档内容的完整性,平台不提供额外的编辑、内容补充、找答案等附加服务。
- 2、"仅部分预览"的文档,不可在线预览部分如存在完整性等问题,可反馈申请退款(可完整预览的文档不适用该条件!)。
- 3、如文档侵犯您的权益,请联系客服反馈,我们会尽快为您处理(人工客服工作时间:9:00-18:30)。
用等离子淬火技术处理机床导轨
连为民 刘恩沧 唐小琦
华中科技大学机械学院,湖北武汉 430074
1 序言
机床导轨主要的失效形式是磨损。
导轨的使用寿命直接影响到机床的使用寿命、工作效率及加工精度。
因此世界上各机床厂家及研究部门都对提高机床导轨硬度的技术研究十分重视。
目前,大多数厂家是采用镀铬处理机床导轨,但其工艺复杂,成本高,且排出的废液容易造成环境污染。
因此,需要一种新的机床导轨表面热处理的技术来取代这一传统的表面淬火工艺。
等离子束数控机床导轨表面硬化处理技术是利用高能量、高密度的等离子束,结合高效率、高精度的数控系统,对已经经过初步磨削加工的机床导轨,进行超高速的加热熔凝淬火,形成细密的高硬度组织,从而不需要镀铬处理就可以达到工艺要求的硬度和耐磨性。
等离子淬火技术是取代传统的镀铬处理工艺的必然途径。
2 原理和应用
用等离子淬火技术处理机床导轨,采用的是常压下的低温等离子束,介质气体为Ar气。
其工作过程是:机床导轨固定在工作台上静止不动,利用数控机床进行三坐标联动,精确地控制安装在机床主轴上的等离子发生器(等离子距),对机床导轨进行表面淬火,使其表面硬度达到工作要求。
在这套系统中,等离子发生器是主要的工作器具,数控机床是对其实行精确控制的载体。
等离子发生器的工作原理是:在阴极和水冷紫铜喷嘴之间,或阴极和工件之间,使气体介质Ar电离形成电弧。
此电弧通过孔径较小的喷嘴孔道,弧柱的直径受到限制,使弧柱受到强行压缩。
这种电弧通常叫压缩电弧。
由于紫铜喷嘴具有良好的导电性和导热性,受到水冷后,孔道壁面的温度很低。
当气体连续地流过孔道时,在靠近壁面的气流受到冷却,形成很薄的冷气流层(冷气壁)。
由于这一冷气壁温度低,电离度很低几乎不能通过电流,迫使电弧电流往电离度高的中心部位流过,即电弧向中心部位压缩,从而形成所谓的“热收缩”。
因为喷嘴孔径本身很小,再加上等离子弧弧柱周围的冷气壁依附在喷嘴孔道壁面上,使弧柱进一步被压缩,形成“机械压缩”效应;此外,弧柱相当于一束电流方向相同的平行导体,每根通电导体都在它周围产生磁场,在磁场作用下,据左手定则,每根导体受到的电磁力都是指向这一束导体的中心。
这种自身磁场产生的电磁力作用的结果,使弧柱受到一个指向弧柱轴心的压缩力,从而使电弧受到压缩,形成所谓的“磁压缩”。
在上述三种压缩作用下,弧柱被压缩到很细的范围内,并且由柔性变为刚性,能量密度高度集中,心部温度高达10000~50000℃左右,称为等离子束。
用上述等离子束加热工件表面,可以形成很大的温度梯度,可使工件表面薄层内迅速升温至熔点或相变温度以上,束柱移走后依靠工件自身的热传导,加热区迅速冷却,形成细密的白口或隐针马氏体类的高硬度组织,提高表面的硬度和耐磨性,而且处理工件的变形小、效率高。
一般的机床导轨,经等离子淬火后,其硬化层硬度可达800~900Hv,深度可达0.10~0.20mm,组织为细小的隐针马氏体。
而且在0.15mm 淬火深度范围内,其硬度变化不明显,完全能够达到使用要求。
在等离子淬火工艺中,电流大小与硬化层深度近乎正比例关系。
即电流愈大,硬化深度亦愈深。
因为硬化深度与弧柱压降U p成正比,而弧柱压降U p又与弧柱的温度和气体的电离势有关。
由弧柱压降U p 公式可知:
U p=IR p=I
ρp l p
F p
=ρp l p i p
式中 ρp———弧柱电阻系数(Ψ·cm);
F p———弧柱截面积(cm2);
l p———弧柱长,很接近弧长(cm);
i p———流过弧柱的电流密度(A/cm2)。
上式表明,弧柱压降U p,取决于弧柱电流密度i p、弧柱电阻系数ρp和弧柱长度l p这三个因素。
弧柱的电阻系数ρp主要取决于气体的电离度,而电离度又主要取决于弧柱的温度和气体的电离势。
电离势对于固定气体来说是个常数,因而弧柱的电阻系数主要取决于弧柱温度。
弧柱温度又是受弧柱电流密度的影响。
随着电流密度的增加,弧柱温度升高,弧柱电阻系
76
组合机床与自动化加工技术
空间面的加工
杨玉华
大连机床集团公司工艺所,辽宁大连 116022
我厂生产的组合机床中有一个零件:
垫板结构及图1 垫板结构及尺寸
尺寸见图1所示:
此件的C 面相对于A 面是一个空间角度平面,要
加工此面,首先要计算E 、F 、G 三点相对D 点的高度,及C 面与A 面的夹角,计算过程如下,如图示位置可以看出D 点是最高点厚度为45。
E 点的高度为;45-460×tg1.85°=30.142G 点的高度为:45-250×tg6.23°=17.709
F 点的高度为:30.142-(250cos6.23°
)2-2502=2.85
在DF 直线方向上,C 面与A 面的夹角为
arctg =(45-2.85)
4602+250
2
=4.603° 各点高度及C 面与A 面夹角确定后,我们利用组合夹具来确定C 面与A 面夹角的方法加工,首先高度最低的F 点应垫起的高度最高。
垫起的原则是加工
余量多少应垫起多高,具体工艺过程如下:
1.刨45厚两面为46。
2.磨45厚两平面共留0.55~0.65。
3.铣周边,Ra 1.6各面各留0.2~0.3。
4.磨45厚两平面共留0.3~0.4及B 面。
磨460长左端Ra 1.6面。
5.划:粗加工线(将工件放在组合夹具上划)。
6.刨:粗刨C 面留3mm (由于此件加工量不均匀,最大处的加工余量为42.15,因此需粗加工后再放到组合夹具上精加工)。
7.刨:在组合夹具上精刨C 面留0.3-0.4(工件与组合夹具整体不拆卸,转到磨床工序)。
8.磨:C 面。
9.钳:倒棱、去毛刺。
需要说明的是夹紧点在加工时会妨碍刀具的运动。
需及时变换夹紧位置。
收稿日期:2002-03-10
(编辑 何 钢)
数就要下降,但当弧柱电流密度达到一定数值时,弧柱温度已经很高,气体电离度已很高,弧电流再继续增加,弧柱电阻系数ρp 受温度的影响就小,对弧压的影响不大。
因而弧压的变化主要取决于电流密度的变化U p ,随着弧柱电流密度的增加而近于线性上升。
当然,并不是说电流越大越好。
因为电流太大时,输出功率增大,等离子束的能量密度及束柱中心温度大大升高,这时工件位于束柱中心的部位便开始熔化,冷却后便形成熔凝硬化,同时在表面上留下肉眼可见的麻坑。
因此,必须使电流位于正常范围内。
实践证明,电流密度在40~90A 范围内,能取得最佳的工作效果。
3 结束语
实践证明,利用等离子技术处理机床导轨,具有工作性能稳定、工作效率高、设备投资小(约为激光的1/3)、处理成本低、对环境无特殊要求、设备维护简单等优点,其经济效益是非常可观的。
[参考文献]
[1]崔洪芝.气缸套等离子束淬火的研究及应用.中国表面工
程,1999,12(4)
[2]崔洪芝,徐克宝,尹华跃.等离子束淬火技术及其专用发生
器的研究.制造技术与机床,2001(3)
[3]耿红军,梁玉海.等离子淬火技术在抽油泵衬套中的应用.
石油矿场机械,2001(1)收稿日期:2001-11-30
作者简介:连为民(1965-),山西长治人,华中科技大学机械学院机械电子工程专业研究生。
(编辑 江 复)
77
2002年第7期 。