干馏热解工艺流程
干馏热解气化

煤的干馏热解气化1.干馏以往都是人们利用煤炭资源时都是采用的直接燃烧方式来获取所需的热能量,这种方式获取的可利用能量少,而且还污染环境,因此再次基础上人们对煤进行干馏获取它的产物再利用,不仅可以充分利用其中的热能量,更加比之前环保。
1.1煤干馏的定义煤干馏是指煤是指煤在隔绝空气条件下加热,使煤中的有机物受热逐渐分解,生成焦炭(或半焦)、煤焦油、粗苯、煤气等产物的过程。
按加热终温的不同,可分为三种:900~1100℃为高温干馏,即焦化;700~900℃为中温干馏;500~600℃为低温干馏(见煤低温干馏)。
1.2煤干馏的过程[1]煤干馏过程主要经历如下变化;当煤料的温度高于100度时,煤中水分蒸发出来;温度升高到200度以上时,煤中结合水释放出来;高达350度以上时,粘结性煤开始软化,并进一步形成粘稠的胶质体(泥煤、褐煤等不发生此现象);至400~500度大部分煤气和焦油都析出,称一次分解产物,在450~550度,热分解继续进行,残留物之间变稠并固化形成半焦;高于550度,半焦继续分解,析出体积缩小变硬形成多孔焦炭。
当干馏在室式干馏炉内进行时,一次热分解产物与赤热焦炭及高温炉壁相接触,发生二次热分解,形成二次热分解产物(焦炉煤气和其他炼焦化学产品)。
1.3煤干馏的产物、产率及分类[1]煤干馏的产物是煤炭、煤焦油和煤气。
煤干馏产物的产率和组成取决于原料煤质、炉结构和加工条件(主要是温度和时间)。
随着干馏终温的不同,煤干馏产品也不同。
低温干馏固体产物为结构疏松的黑色半焦,煤气产率低,焦油产率高;高温干馏固体产物则为结构致密的银灰色焦炭,煤气产率高而焦油产率低。
中温干馏产物的收率,则介于低温干馏和高温干馏之间。
按加热终温的不同,可分为三种:900~1100℃为高温干馏,即焦化;700~900℃为中温干馏;500~600℃为低温干馏。
1.4煤干馏的应用[1]低温干馏主要用褐煤和部分年轻烟煤,也可用泥炭。
低温干馏煤焦油比高温焦油含有较多烷烃,是人造石油重要来源之一。
干馏气化热解炉的工作原理
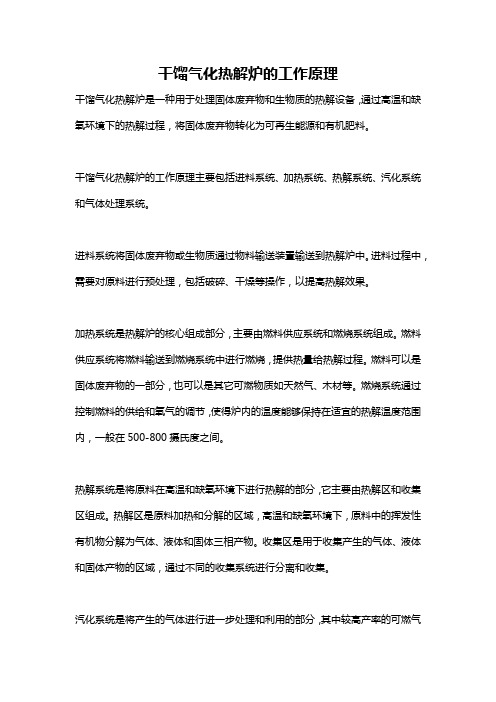
干馏气化热解炉的工作原理干馏气化热解炉是一种用于处理固体废弃物和生物质的热解设备,通过高温和缺氧环境下的热解过程,将固体废弃物转化为可再生能源和有机肥料。
干馏气化热解炉的工作原理主要包括进料系统、加热系统、热解系统、汽化系统和气体处理系统。
进料系统将固体废弃物或生物质通过物料输送装置输送到热解炉中。
进料过程中,需要对原料进行预处理,包括破碎、干燥等操作,以提高热解效果。
加热系统是热解炉的核心组成部分,主要由燃料供应系统和燃烧系统组成。
燃料供应系统将燃料输送到燃烧系统中进行燃烧,提供热量给热解过程。
燃料可以是固体废弃物的一部分,也可以是其它可燃物质如天然气、木材等。
燃烧系统通过控制燃料的供给和氧气的调节,使得炉内的温度能够保持在适宜的热解温度范围内,一般在500-800摄氏度之间。
热解系统是将原料在高温和缺氧环境下进行热解的部分,它主要由热解区和收集区组成。
热解区是原料加热和分解的区域,高温和缺氧环境下,原料中的挥发性有机物分解为气体、液体和固体三相产物。
收集区是用于收集产生的气体、液体和固体产物的区域,通过不同的收集系统进行分离和收集。
汽化系统是将产生的气体进行进一步处理和利用的部分,其中较高产率的可燃气体可以用作燃料供应系统的一部分,较低产率的气体可以用于发电、热能回收等用途。
汽化系统通常包括气体净化和气体利用两个部分,气体净化主要用于去除气体中的灰尘、有害物质和异味,气体利用主要是对气体进行能源利用。
气体处理系统是对产生的气体进行进一步处理的部分,它主要包括冷凝、脱硫、脱氯等工序,目的是提取出气体中的有价值物质,并去除有害物质,以满足环保和能源利用的要求。
总之,干馏气化热解炉的工作原理是通过高温和缺氧环境下的热解过程,将固体废弃物和生物质转化为可再生能源和有机肥料。
它包括进料系统、加热系统、热解系统、汽化系统和气体处理系统等组成部分。
通过合理的控制和处理,可以实现高效、环保和可持续利用固体废弃物和生物质资源的目标。
褐煤低温干馏(热解)加工的生产工艺介绍

一、褐煤低温干馏(热解)加工的生产工艺介绍3.1低温煤干馏(热解)加工的主要工艺煤热解工艺按照不同的工艺特征有多种分类方法。
按气氛分为惰性气氛热解(不加催化剂),加氢热解和催化加氢热解。
按热解温度分为低温热解即温和热解(500~650℃)、中温热解(650~800℃)、高温热解(900一l000℃)和超高温热解(>1200℃)。
按加热速度分为慢速(3~5℃/min)、中速(5~100℃/s)、快速(500~105℃/s)热解和闪裂僻(>106℃/s)。
按加热方式分为外热式、内热式和内外并热式热解。
根据热载体的类型分为固体热载体、气体热载体和固一气热载体热解。
根据煤料在反应器内的密集程度分为密相床和稀相床两类。
依固体物料的运行状态分为固定床、流化床、气流床,滚动床。
依反应器内压强分为常压和加压两类。
而且煤热解工艺的选择取决于对目标产品的要求,并综合考虑煤质特点、设备制造、工艺控制技术水平以及最终的经济效益。
慢速热解如煤的炼焦过程,其热解目的是获得最大产率的固体产品――焦炭;而中速、快速和闪速热解包括加氢热解的主要目的是获得最大产率的挥发产品――焦油或煤气等化工原料,从而达到通过煤的热解将煤定向转化的目的。
表3—1 目标产品与相应的工艺条件上表列出了目标产品与一般所相应采用的热解温度、加热速度、加热方式和挥发物的导出及冷却速率等工艺条件。
到目前为止,国内外研究开发出了多种各具特色的煤热解工艺方法,有的处于试验室研究阶段,有的进入中试实验阶段,也有的达到了工业化生产阶段如鲁奇~鲁尔煤气公司法、COED 法、Toscoal法等。
下面将其中的典型热解方法加以介绍。
3.1.1国外低温煤干馏的加工工艺(一)鲁奇~鲁尔煤气公司法(Lurgi Ruhrgas)1.工艺简介该法是由LurgiGmbH公司(联邦德国)和Ruhrgas AG公司(美国)开发研究的。
其工艺流程为粒度小于5mm的煤粉与焦炭热载体混合之后,在重力移动床直立反应器中进行干馏。
煤的热解过程
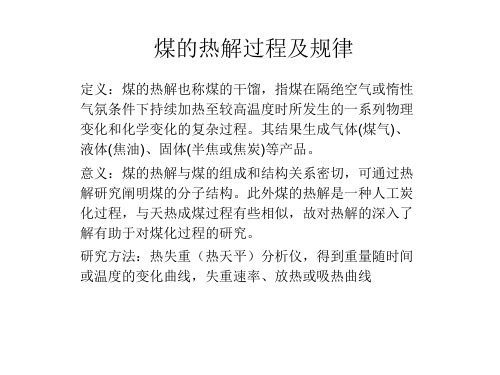
(dW/dt)%·min-1
0.0025 0.0000 -0.0025 -0.0050 -0.0075 -0.0100 -0.0125 -0.0150 -0.0175 -0.0200
0
A1 A2 A3 A4 A5
100 200 300 400 500 600 700 800 900
Temperture/℃
借用热分析技术来研究煤的热解及反应动力学,获得反应速度、反 应产物、反应控制因素、反应煤种及反应动力学常数。
煤热解常用热失重法来研究煤热解动力学。研究方法如:用程序升 温热重法,不同升温速率下的热天平研究了煤的热解及其动力学。 加热速度采用等温和程序升温两种,后者可以避免等温条件下热解 的不便,具有热解效果的可靠性,所以一般在实验中采用线性升温 的方法。
定义如下几个热解特征温度: T0—初始热解温度,℃; TP—失重速率峰值所对应的温度,℃;
Tf—热解过程的结束温度,℃。 其中:Tf=2TP- T0
典型煤种热解特征参数表
热解特征温度与Vdaf的关系
热解最大失重速率Wmax随挥发分Vdaf变化的关系
高堆密度下煤的热失重曲线
• 不同煤化度的煤样在堆密度为1.20 g·cm-1时的热失重曲线,在 100℃~120℃左右之前,煤样的失重率明显增大,随着温度,煤 样的失重率发生明显增大,700以后,失重量明显减少。
特殊煤的热解速率曲线
(1)总体变化规律基本一致,但热解失重速率变化较大;(2)最大热 解失重速率峰值向前或向后推移;(3)碱土金属不同催化作用显现; (4)二次热解明显
煤热解特征参数
由热失重实验测定煤热解转化率时,可按下式计算:
W0—试样原始质量,mg;W—试样在某一时刻的质量,mg;Wf— 试样热解到规定终点时残余质量,mg;△W—试样在某一时刻的失 重,mg;△Wf—试样在规定热解终点的失重,mg。
《煤化工工艺学》——煤的低温干馏

>600 oC
半焦开始向焦炭转化(H2 ↑,CH4 ↓, 半焦↓,焦油↓,煤气↑)
三、加热速度
1. 2. 快速
低分子产物应当多,焦油产率高
慢速
固体残渣产率高
3.
提高煤的加热速度,可使产品产率发生如下变化:
半焦↓,焦油↑ ,煤气略微↓
四、压力
1. 提高压力,可使产品产率发生如下变化:
半焦和气态产物↑,焦油↓ ,半焦强度↑
§2-4 低温干馏主要炉型
一、干馏设备的要求
效率高 加热均匀 操作方便、可靠 过程易控 原料煤类宽 粒度尺寸范围大 二次热解作用小
二、干馏供热方式
1. 外热式(由炉墙外部传入热量)
缺点:热导率小、加热不均匀、半焦质量不均、二次热 解加深、焦油产率降低
外热式供热示意图
二、干馏供热方式
原料:<6 mm粉煤; 黏结性煤:气流吹入法 加料 不黏结性煤:螺旋给料器 燃料气和空气燃烧 ② 供热 热烟气 ① ③
气体
产品
煤粉 旋风分离器
满流管 气体冷却系统
焦粉
煤气
粉尘
焦油、中油
三、气流内热式炉
2. 鲁奇三段炉(固定床)
① ② 原料:褐煤块、型煤,20~80 mm,非黏结性煤; 流程:(三段:干燥段、干馏段和冷却段)
返回
气流内热式炉干馏流程框图
返回
Toscoal法干馏非黏结性煤的工艺框图
返回
① ②
2. 3.
4.
低阶煤无黏结性,有利于在固定床或流化床干馏炉中处理。
最佳热解温度是随煤阶降低而降低的,低阶煤开始热解温 度低。 低阶煤中挥发分含量较多,可得到较多的焦油和煤气。
热解工艺流程
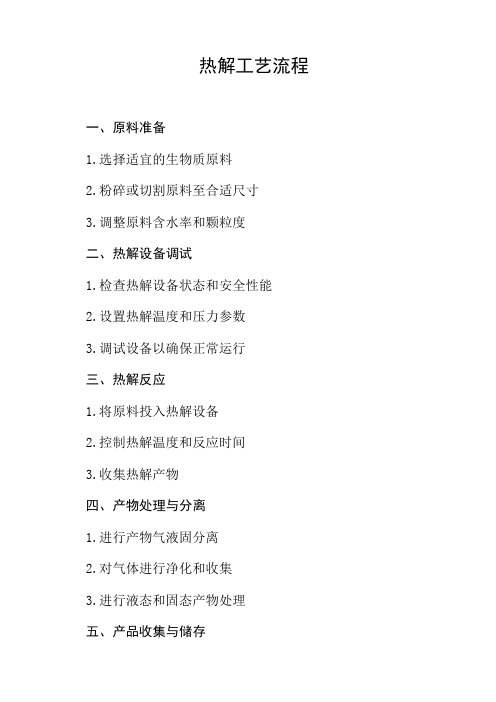
热解工艺流程
一、原料准备
1.选择适宜的生物质原料
2.粉碎或切割原料至合适尺寸
3.调整原料含水率和颗粒度
二、热解设备调试
1.检查热解设备状态和安全性能
2.设置热解温度和压力参数
3.调试设备以确保正常运行
三、热解反应
1.将原料投入热解设备
2.控制热解温度和反应时间
3.收集热解产物
四、产物处理与分离
1.进行产物气液固分离
2.对气体进行净化和收集
3.进行液态和固态产物处理
五、产品收集与储存
1.收集处理后的产品
2.进行产品质量检验
3.储存合格产品并准备出售。
干馏热解气化
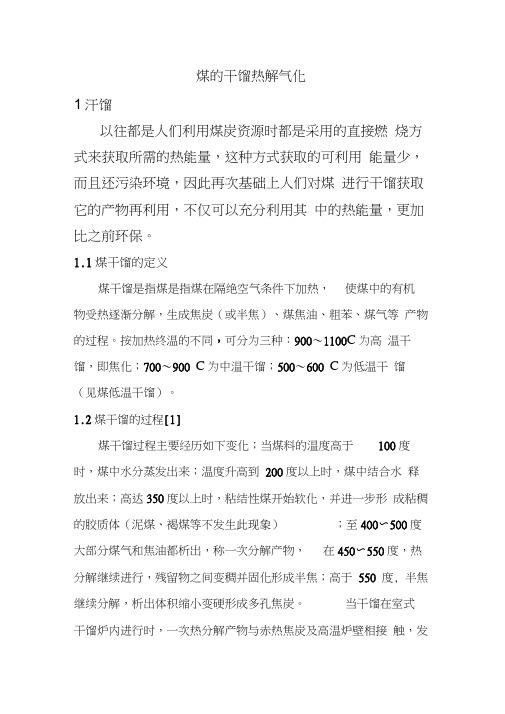
煤的干馏热解气化1汗馏以往都是人们利用煤炭资源时都是采用的直接燃烧方式来获取所需的热能量,这种方式获取的可利用能量少,而且还污染环境,因此再次基础上人们对煤进行干馏获取它的产物再利用,不仅可以充分利用其中的热能量,更加比之前环保。
1.1煤干馏的定义煤干馏是指煤是指煤在隔绝空气条件下加热,使煤中的有机物受热逐渐分解,生成焦炭(或半焦)、煤焦油、粗苯、煤气等产物的过程。
按加热终温的不同,可分为三种:900〜1100C为高温干馏,即焦化;700〜900 C为中温干馏;500〜600 C为低温干馏(见煤低温干馏)。
1.2煤干馏的过程[1]煤干馏过程主要经历如下变化;当煤料的温度高于100度时,煤中水分蒸发出来;温度升高到200度以上时,煤中结合水释放出来;高达350度以上时,粘结性煤开始软化,并进一步形成粘稠的胶质体(泥煤、褐煤等不发生此现象);至400〜500度大部分煤气和焦油都析出,称一次分解产物,在450〜550度,热分解继续进行,残留物之间变稠并固化形成半焦;高于550 度, 半焦继续分解,析出体积缩小变硬形成多孔焦炭。
当干馏在室式干馏炉内进行时,一次热分解产物与赤热焦炭及高温炉壁相接触,发生二次热分解,形成二次热分解产物(焦炉煤气和其他炼焦化学产品)。
1.3煤干馏的产物、产率及分类[1]煤干馏的产物是煤炭、煤焦油和煤气。
煤干馏产物的产率和组成取决于原料煤质、炉结构和加工条件(主要是温度和时间)。
随着干馏终温的不同,煤干馏产品也不同。
低温干馏固体产物为结构疏松的黑色半焦,煤气产率低,焦油产率高;高温干馏固体产物则为结构致密的银灰色焦炭,煤气产率高而焦油产率低。
中温干馏产物的收率,则介于低温干馏和高温干馏之间。
按加热终温的不同,可分为三种:900〜1100C为高温干馏,即焦化;700〜900C为中温干馏;500〜600C为低温干馏。
1.4煤干馏的应用[1]低温干馏主要用褐煤和部分年轻烟煤,也可用泥炭。
石油分馏煤的干馏

石油分馏煤的干馏
石油分馏煤干馏是一种重要的煤化学工艺,通过高温下将煤料加热,从而分解
出不同成分。
本文将介绍石油分馏煤的干馏过程及其应用。
1. 干馏原理
石油分馏煤的干馏是一种热解过程,煤料在缺乏空气的条件下受热分解,产生
气体、液体和固体产物。
在干馏过程中,煤料会依次经历失重、软化、膨胀、裂解和焦化等阶段。
2. 干馏产物
气体产品:主要是各种有机气体和一些杂质气体,如甲烷、乙烷、一氧化碳等。
这些气体可被用作燃料或作为化工原料。
液体产品:是由干馏过程中沥青质和焦油等组成的,其中含有许多有机烃,可用作化工原料或润滑油。
固体产品:主要是焦炭,是石油分馏煤干馏的主要产物之一。
焦炭具有高热值和高热稳定性,广泛用于冶金和工业领域。
3. 干馏应用
•燃料:石油分馏煤的干馏产生的气体和液体产品可用作燃料,为工业生产和生活提供能源。
•化工原料:干馏产生的液体产品中含有多种有机烃,可作为化工原料用于合成各种化学产品。
•冶金行业:干馏产生的焦炭在冶金行业用作还原剂,降低矿石中的氧化物,提高金属的纯度。
石油分馏煤的干馏过程将煤料中的有机物分解为不同的产物,这些产物在工业
生产中具有重要的应用价值。
通过不断的研究和改进,提高煤化学工艺的效率,将煤资源充分利用,为促进工业和经济发展做出贡献。
煤的热解
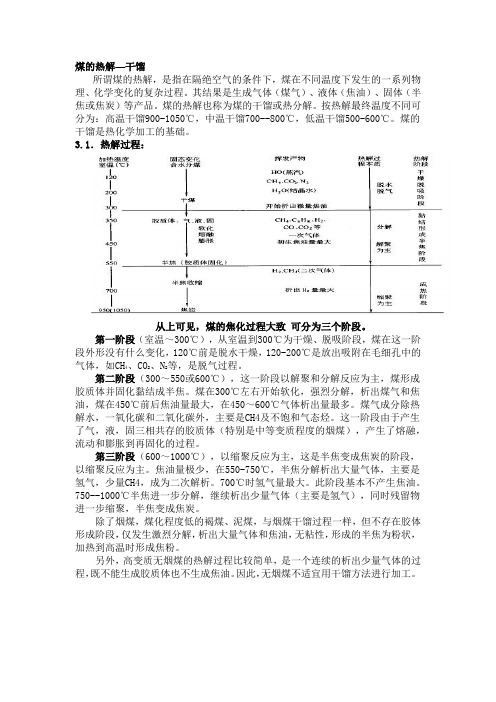
煤的热解—干馏所谓煤的热解,是指在隔绝空气的条件下,煤在不同温度下发生的一系列物理、化学变化的复杂过程。
其结果是生成气体(煤气)、液体(焦油)、固体(半焦或焦炭)等产品。
煤的热解也称为煤的干馏或热分解。
按热解最终温度不同可分为:高温干馏900-1050℃,中温干馏700--800℃,低温干馏500-600℃。
煤的干馏是热化学加工的基础。
3.1.热解过程:从上可见,煤的焦化过程大致可分为三个阶段。
第一阶段(室温~300℃),从室温到300℃为干燥、脱吸阶段,煤在这一阶段外形没有什么变化,120℃前是脱水干燥,120-200℃是放出吸附在毛细孔中的气体,如CH4、CO2、N2等,是脱气过程。
第二阶段(300~550或600℃),这一阶段以解聚和分解反应为主,煤形成胶质体并固化黏结成半焦。
煤在300℃左右开始软化,强烈分解,析出煤气和焦油,煤在450℃前后焦油量最大,在450~600℃气体析出量最多。
煤气成分除热解水,一氧化碳和二氧化碳外,主要是CH4及不饱和气态烃。
这一阶段由于产生了气,液,固三相共存的胶质体(特别是中等变质程度的烟煤),产生了熔融,流动和膨胀到再固化的过程。
第三阶段(600~1000℃),以缩聚反应为主,这是半焦变成焦炭的阶段,以缩聚反应为主。
焦油量极少,在550-750℃,半焦分解析出大量气体,主要是氢气,少量CH4,成为二次解析。
700℃时氢气量最大。
此阶段基本不产生焦油。
750--1000℃半焦进一步分解,继续析出少量气体(主要是氢气),同时残留物进一步缩聚,半焦变成焦炭。
除了烟煤,煤化程度低的褐煤、泥煤,与烟煤干馏过程一样,但不存在胶体形成阶段,仅发生激烈分解,析出大量气体和焦油,无粘性,形成的半焦为粉状,加热到高温时形成焦粉。
另外,高变质无烟煤的热解过程比较简单,是一个连续的析出少量气体的过程,既不能生成胶质体也不生成焦油。
因此,无烟煤不适宜用干馏方法进行加工。
干馏热解工艺流程
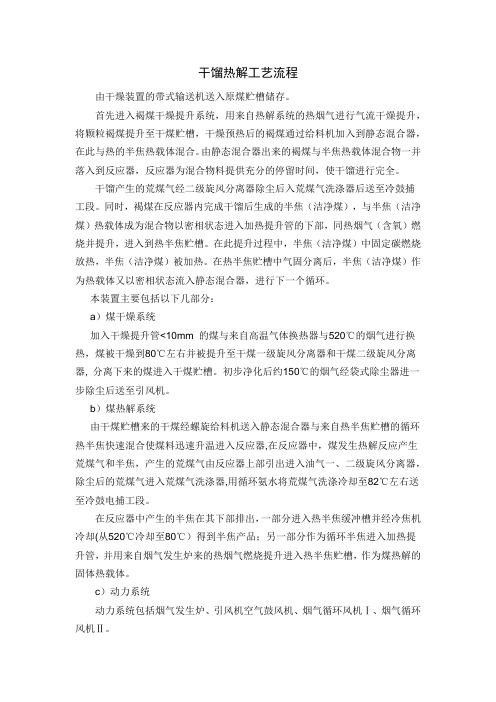
干馏热解工艺流程由干燥装置的带式输送机送入原煤贮槽储存。
首先进入褐煤干燥提升系统,用来自热解系统的热烟气进行气流干燥提升,将颗粒褐煤提升至干煤贮槽,干燥预热后的褐煤通过给料机加入到静态混合器,在此与热的半焦热载体混合。
由静态混合器出来的褐煤与半焦热载体混合物一并落入到反应器,反应器为混合物料提供充分的停留时间,使干馏进行完全。
干馏产生的荒煤气经二级旋风分离器除尘后入荒煤气洗涤器后送至冷鼓捕工段。
同时,褐煤在反应器内完成干馏后生成的半焦(洁净煤),与半焦(洁净煤)热载体成为混合物以密相状态进入加热提升管的下部,同热烟气(含氧)燃烧并提升,进入到热半焦贮槽。
在此提升过程中,半焦(洁净煤)中固定碳燃烧放热,半焦(洁净煤)被加热。
在热半焦贮槽中气固分离后,半焦(洁净煤)作为热载体又以密相状态流入静态混合器,进行下一个循环。
本装置主要包括以下几部分:a)煤干燥系统加入干燥提升管<10mm 的煤与来自高温气体换热器与520℃的烟气进行换热,煤被干燥到80℃左右并被提升至干煤一级旋风分离器和干煤二级旋风分离器, 分离下来的煤进入干煤贮槽。
初步净化后约150℃的烟气经袋式除尘器进一步除尘后送至引风机。
b)煤热解系统由干煤贮槽来的干煤经螺旋给料机送入静态混合器与来自热半焦贮槽的循环热半焦快速混合使煤料迅速升温进入反应器,在反应器中,煤发生热解反应产生荒煤气和半焦,产生的荒煤气由反应器上部引出进入油气一、二级旋风分离器,除尘后的荒煤气进入荒煤气洗涤器,用循环氨水将荒煤气洗涤冷却至82℃左右送至冷鼓电捕工段。
在反应器中产生的半焦在其下部排出,一部分进入热半焦缓冲槽并经冷焦机冷却(从520℃冷却至80℃)得到半焦产品;另一部分作为循环半焦进入加热提升管,并用来自烟气发生炉来的热烟气燃烧提升进入热半焦贮槽,作为煤热解的固体热载体。
c)动力系统动力系统包括烟气发生炉、引风机空气鼓风机、烟气循环风机Ⅰ、烟气循环风机Ⅱ。
褐煤低温干馏(热解)加工的生产工艺介绍

一、褐煤低温干馏(热解)加工的生产工艺介绍3.1低温煤干馏(热解)加工的主要工艺煤热解工艺按照不同的工艺特征有多种分类方法。
按气氛分为惰性气氛热解(不加催化剂),加氢热解和催化加氢热解。
按热解温度分为低温热解即温和热解(500~650℃)、中温热解(650~800℃)、高温热解(900一l000℃)和超高温热解(>1200℃)。
按加热速度分为慢速(3~5℃/min)、中速(5~100℃/s)、快速(500~105℃/s)热解和闪裂僻(>106℃/s)。
按加热方式分为外热式、内热式和内外并热式热解。
根据热载体的类型分为固体热载体、气体热载体和固一气热载体热解。
根据煤料在反应器内的密集程度分为密相床和稀相床两类。
依固体物料的运行状态分为固定床、流化床、气流床,滚动床。
依反应器内压强分为常压和加压两类。
而且煤热解工艺的选择取决于对目标产品的要求,并综合考虑煤质特点、设备制造、工艺控制技术水平以及最终的经济效益。
慢速热解如煤的炼焦过程,其热解目的是获得最大产率的固体产品――焦炭;而中速、快速和闪速热解包括加氢热解的主要目的是获得最大产率的挥发产品――焦油或煤气等化工原料,从而达到通过煤的热解将煤定向转化的目的。
表3—1 目标产品与相应的工艺条件上表列出了目标产品与一般所相应采用的热解温度、加热速度、加热方式和挥发物的导出及冷却速率等工艺条件。
到目前为止,国内外研究开发出了多种各具特色的煤热解工艺方法,有的处于试验室研究阶段,有的进入中试实验阶段,也有的达到了工业化生产阶段如鲁奇~鲁尔煤气公司法、COED 法、Toscoal法等。
下面将其中的典型热解方法加以介绍。
3.1.1国外低温煤干馏的加工工艺(一)鲁奇~鲁尔煤气公司法(Lurgi Ruhrgas)1.工艺简介该法是由LurgiGmbH公司(联邦德国)和Ruhrgas AG公司(美国)开发研究的。
其工艺流程为粒度小于5mm的煤粉与焦炭热载体混合之后,在重力移动床直立反应器中进行干馏。
煤的干馏和石油分馏

煤的干馏和石油分馏
煤是一种重要的矿物资源,被广泛用于能源生产和化工工业。
其中,煤的干馏
和石油的分馏是两种常见的提取高值化合物的方法。
本文将分别介绍煤的干馏和石油的分馏过程。
煤的干馏
煤的干馏是一种通过高温加热煤来释放挥发性物质的过程。
这些挥发性物质包
括煤焦油、煤气和焦炭。
干馏过程通常在缺乏氧气的环境中进行,以避免煤燃烧而产生灰烬。
干馏的工艺流程
1.加热煤岩:将煤岩置于封闭的反应器中,通过加热使其达到高温。
2.挥发性物质的释放:在高温下,煤岩中的挥发性物质会逐渐释放出
来,形成煤焦油和煤气。
3.收集产品:通过冷凝器收集煤焦油和煤气,进一步提炼和加工。
4.生成焦炭:残留的固体部分被称为焦炭,可以在高炉中用作冶炼原
料。
石油的分馏
石油分馏是一种将石油中的不同碳链长度的烃类分离的过程,通过这种方法可
以获得不同用途的石油产品,例如汽油、柴油和煤油等。
分馏的工艺流程
1.蒸馏塔:将原油加热至一定温度后,将其输入到蒸馏塔中。
2.分馏:在蒸馏塔中,石油中的烃类按照碳链长度由短到长依次分馏,
生成不同沸点的馏分。
3.收集产品:收集不同沸点范围内的馏分,用于制备不同用途的石油
产品。
4.降温冷凝:通过冷却管道使馏分冷却凝结,形成液体产品。
煤的干馏和石油的分馏是两种常见的化工分离技术,通过这些过程可以提取出
各种高值化合物,为能源和化工行业提供了重要的原料来源。
第二章木材热解过程及其影响因素

有特有的化学活性,为 涂料、合成樟脑、松油 醇、合成香料、医药、 合成树脂、有机化工等 方面化工原料。
【木材干馏液体产物来源】
序 号
产物类别
主要来源
1 醋酸
源自木材组分中所含有的乙酰基和低聚糠的热分解; 甲醇的二次分解。
2
醛类(甲醛、乙 醛、糠醛等)
木材中的纤维素、半纤维素及木质素热分解时都能生 成醛类,也可通过二次反应生成。如甲醛主要来自木 材中所含有的甲氧基。
二、木材干馏产物
◆固态产物:木炭,275 ℃以上生成,得率 33%—38%(1/3);
◆液态产物:粗木醋液(可凝性气体冷却产 物),分层情况因原料而异,得率45%— 50%(1/2);
粗木醋液
材种 阔叶材
针叶材
层次 上层 下层 上层 中层 下层
液体成分 澄清木醋液 沉淀木焦油 粗松节油 澄清木醋液 沉淀木焦油
◆从物质迁移、能量传递的角度对其进行分析 ,在生物质热解过程中,热量首先传递到颗粒 表面,再由表面传到颗粒内部。热解过程由外 至内逐层进行,生物质颗粒被加热的成分迅速 裂解成相应的产物。
※热解工艺类型
根据工艺操作条件,生物质热解工艺主要可分 为慢速和快速热解。
◆慢速热解(又称干馏工艺、传统热解)工艺 具有几千年的历史,是一种以生成木炭为目的 的炭化过程。将木材放在窑内,在隔绝空气的 情况下加热,可以得到占原料质量30%~35%的 木炭产量。
图 木材热解温度、时间与产物的关系
◆液体产物: 1. 在0.5 h-1.5 h,产物主要为水分; 2. 在2-4 h反应剧烈,大量有机物; 3. 在 4 h后,反应平缓,有少量产物。
◆气体产物:
1. 在2 h前,排出釜内空气; 2. 在 2-4 h,大量气体产物
干馏式炭化炉
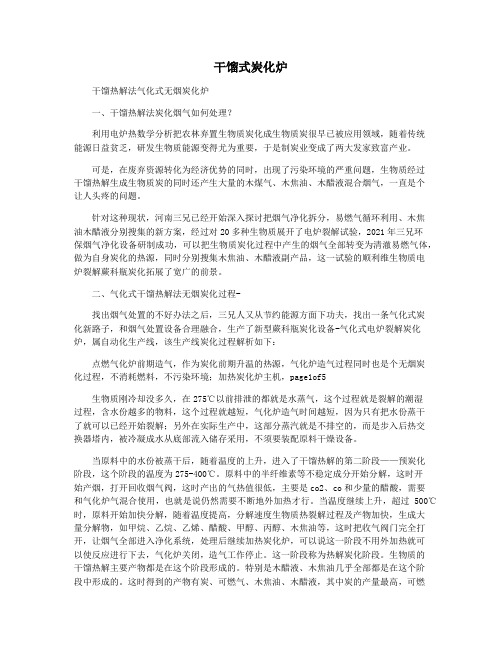
干馏式炭化炉干馏热解法气化式无烟炭化炉一、干馏热解法炭化烟气如何处理?利用电炉热数学分析把农林弃置生物质炭化成生物质炭很早已被应用领域,随着传统能源日益贫乏,研发生物质能源变得尤为重要,于是制炭业变成了两大发家致富产业。
可是,在废弃资源转化为经济优势的同时,出现了污染环境的严重问题,生物质经过干馏热解生成生物质炭的同时还产生大量的木煤气、木焦油、木醋液混合烟气,一直是个让人头疼的问题。
针对这种现状,河南三兄已经开始深入探讨把烟气净化拆分,易燃气循环利用、木焦油木醋液分别搜集的新方案,经过对20多种生物质展开了电炉裂解试验,2021年三兄环保烟气净化设备研制成功,可以把生物质炭化过程中产生的烟气全部转变为清澈易燃气体,做为自身炭化的热源,同时分别搜集木焦油、木醋液副产品,这一试验的顺利维生物质电炉裂解蕨科瓶炭化拓展了宽广的前景。
二、气化式干馏热解法无烟炭化过程-找出烟气处置的不好办法之后,三兄人又从节约能源方面下功夫,找出一条气化式炭化新路子,和烟气处置设备合理融合,生产了新型蕨科瓶炭化设备-气化式电炉裂解炭化炉,属自动化生产线,该生产线炭化过程解析如下:点燃气化炉前期造气,作为炭化前期升温的热源,气化炉造气过程同时也是个无烟炭化过程,不消耗燃料,不污染环境;加热炭化炉主机,page1of5生物质刚冷却没多久,在275℃以前排泄的都就是水蒸气,这个过程就是裂解的潮湿过程,含水份越多的物料,这个过程就越短,气化炉造气时间越短,因为只有把水份蒸干了就可以已经开始裂解;另外在实际生产中,这部分蒸汽就是不排空的,而是步入后热交换器塔内,被冷凝成水从底部流入储存采用,不须要装配原料干燥设备。
当原料中的水份被蒸干后,随着温度的上升,进入了干馏热解的第二阶段——预炭化阶段,这个阶段的温度为275-400℃。
原料中的半纤维素等不稳定成分开始分解,这时开始产烟,打开回收烟气阀,这时产出的气热值很低,主要是co2、co和少量的醋酸,需要和气化炉气混合使用,也就是说仍然需要不断地外加热才行。
煤的干馏,石油的分馏方法
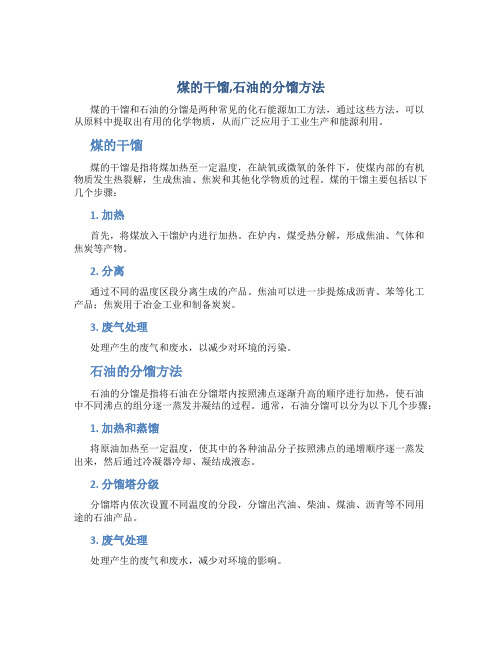
煤的干馏,石油的分馏方法
煤的干馏和石油的分馏是两种常见的化石能源加工方法,通过这些方法,可以
从原料中提取出有用的化学物质,从而广泛应用于工业生产和能源利用。
煤的干馏
煤的干馏是指将煤加热至一定温度,在缺氧或微氧的条件下,使煤内部的有机
物质发生热裂解,生成焦油、焦炭和其他化学物质的过程。
煤的干馏主要包括以下几个步骤:
1. 加热
首先,将煤放入干馏炉内进行加热。
在炉内,煤受热分解,形成焦油、气体和
焦炭等产物。
2. 分离
通过不同的温度区段分离生成的产品。
焦油可以进一步提炼成沥青、苯等化工
产品;焦炭用于冶金工业和制备炭炭。
3. 废气处理
处理产生的废气和废水,以减少对环境的污染。
石油的分馏方法
石油的分馏是指将石油在分馏塔内按照沸点逐渐升高的顺序进行加热,使石油
中不同沸点的组分逐一蒸发并凝结的过程。
通常,石油分馏可以分为以下几个步骤:
1. 加热和蒸馏
将原油加热至一定温度,使其中的各种油品分子按照沸点的递增顺序逐一蒸发
出来,然后通过冷凝器冷却、凝结成液态。
2. 分馏塔分级
分馏塔内依次设置不同温度的分段,分馏出汽油、柴油、煤油、沥青等不同用
途的石油产品。
3. 废气处理
处理产生的废气和废水,减少对环境的影响。
总的来说,煤的干馏和石油的分馏是两种不同的化石燃料加工方法,它们在生产实践中具有重要的应用价值,不仅可以提高能源利用效率,还可以获得各种化工产品,满足不同领域的需求。
煤的干馏 热解过程(煤化学课件)

低温干馏(500-600℃)-以液体产物为目标 中温干馏(700-800℃)-制取燃料煤气 高温干馏(950-1050℃)-炼焦
★典型(粘结性)烟煤热解过程
②胶质体的生成和固化阶段 (300~550℃)
③半焦转化为焦炭的阶段 (550 ~1000 ℃)
①干燥脱吸阶段 (室温~300℃)
煤化程度高的非粘结性煤(贫煤、无烟煤)
热解过程简单,以裂解为主,仅有少量热解气体放出。 区别:不产生胶质体,也不产生焦油。
煤热解是煤转化的关键步骤, 煤气化、液化、焦化和燃烧都要经过和发生热解过程。
对炼焦来说,可正确地选 择原料煤,寻求扩大原料 煤的途径确定合适的工艺 条件和提高产品(焦炭、 煤气、焦油等)质量和数 量。
炼焦
液化 气化
对液化和气化而言,可以 在比较温和的条件下得到 优质的焦油和煤气,为其 工艺条件的选取提供数据。
课程小结
黏结性烟煤受热时发生的变化
思考题:煤的热解过程中两次脱气阶段脱除的气体一样吗?
550~750℃
半焦分解析出大量的气体,主要是H2和少量 的CH4,成为热解的二次气体。半焦分解释 出大量气体后,体积收缩产生裂纹。在此阶 段基本上不产生焦油。
非粘结性烟煤的热解过程
低煤 化度
高煤 化度
煤化程度低的非粘结性煤(褐煤、长焰煤)
相同点:同样有分解、解聚和缩聚反应发生,生成大量气体和焦油。 不同点:没有胶质体生成,不产生熔融、膨胀等现象。热解后煤粒仍 成分离状态,不会粘结成块。
生成和排出大量挥发物。
为热解的一次脱气阶段。
气体
03
CH4及同系物,还有H2、CO、
CO2及不饱和烃
析出量
02 焦油在450℃时析出的量最大;
油页岩干馏工艺流程描述
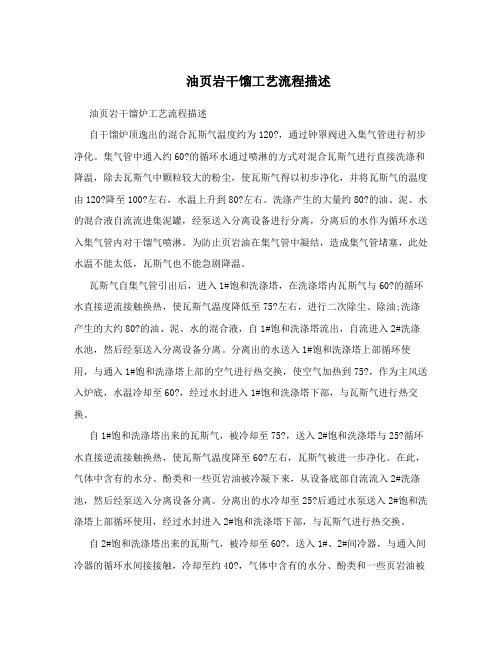
油页岩干馏工艺流程描述油页岩干馏炉工艺流程描述自干馏炉顶逸出的混合瓦斯气温度约为120?,通过钟罩阀进入集气管进行初步净化。
集气管中通入约60?的循环水通过喷淋的方式对混合瓦斯气进行直接洗涤和降温,除去瓦斯气中颗粒较大的粉尘,使瓦斯气得以初步净化,并将瓦斯气的温度由120?降至100?左右,水温上升到80?左右。
洗涤产生的大量约80?的油、泥、水的混合液自流流进集泥罐,经泵送入分离设备进行分离,分离后的水作为循环水送入集气管内对干馏气喷淋。
为防止页岩油在集气管中凝结,造成集气管堵塞,此处水温不能太低,瓦斯气也不能急剧降温。
瓦斯气自集气管引出后,进入1#饱和洗涤塔,在洗涤塔内瓦斯气与60?的循环水直接逆流接触换热,使瓦斯气温度降低至75?左右,进行二次除尘、除油;洗涤产生的大约80?的油、泥、水的混合液,自1#饱和洗涤塔流出,自流进入2#洗涤水池,然后经泵送入分离设备分离。
分离出的水送入1#饱和洗涤塔上部循环使用,与通入1#饱和洗涤塔上部的空气进行热交换,使空气加热到75?,作为主风送入炉底,水温冷却至60?,经过水封进入1#饱和洗涤塔下部,与瓦斯气进行热交换。
自1#饱和洗涤塔出来的瓦斯气,被冷却至75?,送入2#饱和洗涤塔与25?循环水直接逆流接触换热,使瓦斯气温度降至60?左右,瓦斯气被进一步净化。
在此,气体中含有的水分、酚类和一些页岩油被冷凝下来,从设备底部自流流入2#洗涤池,然后经泵送入分离设备分离。
分离出的水冷却至25?后通过水泵送入2#饱和洗涤塔上部循环使用,经过水封进入2#饱和洗涤塔下部,与瓦斯气进行热交换。
自2#饱和洗涤塔出来的瓦斯气,被冷却至60?,送入1#、2#间冷器,与通入间冷器的循环水间接接触,冷却至约40?,气体中含有的水分、酚类和一些页岩油被冷凝下来,从设备底部自流流入3#洗涤池,然后经泵送入分离设备分离。
通入间冷器的循环水自间冷器上部流出,进入循环水池,冷却降温,由水泵送入玻璃钢冷却塔进一步冷却至常温流入循环水池,经水泵送入1#、2#间冷器,循环使用。
固体热载体干馏工艺.

LR工艺
气流床
内热式
小瓷球、 沙子、半 焦
半焦 瓷球
500~850
快速
Garrett工艺 TOSCOAL工 艺
气流床 卧式转鼓 (回转窑)
内热式 内热式
280(压力为 344KPa)
快速 快速
10
500~600
托斯考(Toscoal)工艺
TOSCOAL 工艺是由美国油页岩公司开发的用陶瓷球作为 热载体的煤炭低温热解方法。将6 mm 以下的粉煤加入提升管中 ,利用热烟气将其预热到260~ 320℃,预热后的煤进入旋转滚 筒与被加热的高温瓷球混合。热解温度保持在427~ 510℃ 。煤 气与焦油蒸气由分离器的顶部排出。进入气液分离器进一步分 离,热球与半焦通过分离器内的转鼓分离,细的焦渣落入筛下 ,瓷球通过斗式提升机送入球加热器循环使用。该工艺于70 年 代建成处理量为25 t / d 的中试装置。但试验中发现由于瓷球被 反复加热到600℃以上循环使用, 在磨损性上存在问题。此外, 粘结性煤在热解过程中会粘附在瓷球上,因此仅有非粘结性煤 和弱粘结性煤可用于该工艺。
TOSCOAL工 艺
0~13
表2-3煤炭热解技术原理比较
热解工艺 DG工艺 BJY工艺 BT工艺
原理 直立式循环 流化床 移动床循环 流化床 下行床循环 流化床
加热方 式 内热式 内热式 内热式
热载体 半焦 半焦、循 环灰 热灰
热解温度 /℃ 470~600 600~900 570~660
热解速度 快速 快速 快速
国内
国外
8
2.6.3.2不同工艺比较:
热解工艺
表2-2 煤炭热解技术原料产品分析比较
经验煤种
进料 粒度 /mm
中药炮制技术—干馏技术(中药炮制技术课件)

用武火炒制备油状物,如蛋黄油。温度在 在280℃左右。
02
实操举例
实操举例
蛋黄油
始载于《备急千金要方》,《中国药典》 (2015年版)未载该药。
实操举例
炮制方法
鸡蛋煮熟,取蛋黄,置锅内,文火加热, 待除尽水分后,改用武火280度熬制,至 蛋黄油出尽为止,滤尽蛋黄油装瓶
干 馏 技 术
干馏技术
1 干馏技术概述 2 实操举例
01
干馏技术概述
干馏技术
将药物置于容器内,以火
烤灼,使产生汁液的方法称为干
定
馏技术。
义
操作工艺
制备有别于原药材的干馏物, 以适合临床需要。大多产生抗过
目
敏、抗菌消炎作用。
的
1.上部收集-收集冷凝液 多以砂浴加热,在干馏器上部收集冷凝
的液状物。如黑豆馏油。温度在400℃~ 450℃。 2.下部收集-收集液状物
01
பைடு நூலகம்
成品性状
油状液体,具青黄色荧 光,味极苦,黏稠
02
03
炮制作用
具有清热解毒作用。用于烧伤、湿疹、 耳脓、疮疡已溃等。
煤石油分馏干馏初中
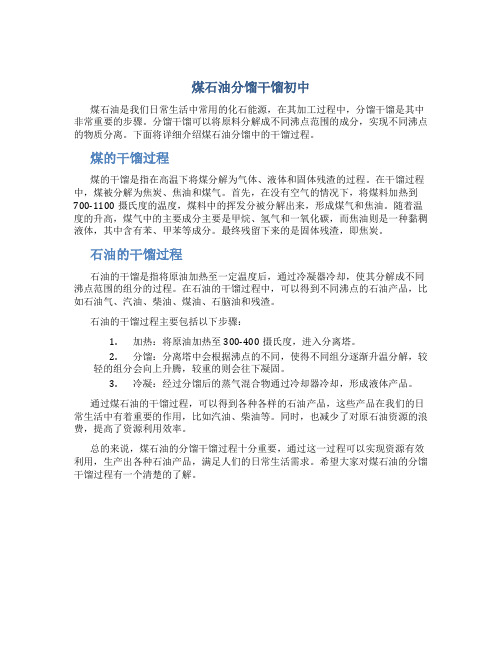
煤石油分馏干馏初中煤石油是我们日常生活中常用的化石能源,在其加工过程中,分馏干馏是其中非常重要的步骤。
分馏干馏可以将原料分解成不同沸点范围的成分,实现不同沸点的物质分离。
下面将详细介绍煤石油分馏中的干馏过程。
煤的干馏过程煤的干馏是指在高温下将煤分解为气体、液体和固体残渣的过程。
在干馏过程中,煤被分解为焦炭、焦油和煤气。
首先,在没有空气的情况下,将煤料加热到700-1100摄氏度的温度,煤料中的挥发分被分解出来,形成煤气和焦油。
随着温度的升高,煤气中的主要成分主要是甲烷、氢气和一氧化碳,而焦油则是一种黏稠液体,其中含有苯、甲苯等成分。
最终残留下来的是固体残渣,即焦炭。
石油的干馏过程石油的干馏是指将原油加热至一定温度后,通过冷凝器冷却,使其分解成不同沸点范围的组分的过程。
在石油的干馏过程中,可以得到不同沸点的石油产品,比如石油气、汽油、柴油、煤油、石脑油和残渣。
石油的干馏过程主要包括以下步骤:1.加热:将原油加热至300-400摄氏度,进入分离塔。
2.分馏:分离塔中会根据沸点的不同,使得不同组分逐渐升温分解,较轻的组分会向上升腾,较重的则会往下凝固。
3.冷凝:经过分馏后的蒸气混合物通过冷却器冷却,形成液体产品。
通过煤石油的干馏过程,可以得到各种各样的石油产品,这些产品在我们的日常生活中有着重要的作用,比如汽油、柴油等。
同时,也减少了对原石油资源的浪费,提高了资源利用效率。
总的来说,煤石油的分馏干馏过程十分重要,通过这一过程可以实现资源有效利用,生产出各种石油产品,满足人们的日常生活需求。
希望大家对煤石油的分馏干馏过程有一个清楚的了解。
- 1、下载文档前请自行甄别文档内容的完整性,平台不提供额外的编辑、内容补充、找答案等附加服务。
- 2、"仅部分预览"的文档,不可在线预览部分如存在完整性等问题,可反馈申请退款(可完整预览的文档不适用该条件!)。
- 3、如文档侵犯您的权益,请联系客服反馈,我们会尽快为您处理(人工客服工作时间:9:00-18:30)。
干馏热解工艺流程
由干燥装置的带式输送机送入原煤贮槽储存。
首先进入褐煤干燥提升系统,用来自热解系统的热烟气进行气流干燥提升,将颗粒褐煤提升至干煤贮槽,干燥预热后的褐煤通过给料机加入到静态混合器,在此与热的半焦热载体混合。
由静态混合器出来的褐煤与半焦热载体混合物一并落入到反应器,反应器为混合物料提供充分的停留时间,使干馏进行完全。
干馏产生的荒煤气经二级旋风分离器除尘后入荒煤气洗涤器后送至冷鼓捕工段。
同时,褐煤在反应器内完成干馏后生成的半焦(洁净煤),与半焦(洁净煤)热载体成为混合物以密相状态进入加热提升管的下部,同热烟气(含氧)燃烧并提升,进入到热半焦贮槽。
在此提升过程中,半焦(洁净煤)中固定碳燃烧放热,半焦(洁净煤)被加热。
在热半焦贮槽中气固分离后,半焦(洁净煤)作为热载体又以密相状态流入静态混合器,进行下一个循环。
本装置主要包括以下几部分:
a)煤干燥系统
加入干燥提升管<10mm 的煤与来自高温气体换热器与520℃的烟气进行换热,煤被干燥到80℃左右并被提升至干煤一级旋风分离器和干煤二级旋风分离器, 分离下来的煤进入干煤贮槽。
初步净化后约150℃的烟气经袋式除尘器进一步除尘后送至引风机。
b)煤热解系统
由干煤贮槽来的干煤经螺旋给料机送入静态混合器与来自热半焦贮槽的循环热半焦快速混合使煤料迅速升温进入反应器,在反应器中,煤发生热解反应产生荒煤气和半焦,产生的荒煤气由反应器上部引出进入油气一、二级旋风分离器,除尘后的荒煤气进入荒煤气洗涤器,用循环氨水将荒煤气洗涤冷却至82℃左右送至冷鼓电捕工段。
在反应器中产生的半焦在其下部排出,一部分进入热半焦缓冲槽并经冷焦机冷却(从520℃冷却至80℃)得到半焦产品;另一部分作为循环半焦进入加热提升管,并用来自烟气发生炉来的热烟气燃烧提升进入热半焦贮槽,作为煤热解的固体热载体。
c)动力系统
动力系统包括烟气发生炉、引风机空气鼓风机、烟气循环风机Ⅰ、烟气循环风机Ⅱ。
新鲜空气经空气鼓风机加压至50kPa(G)大部分送入高温气体换热器加热
至360℃与来自烟气循环风机Ⅰ的循环烟气一同进入烟气发生炉,在此被加热并与煤气加压站来的煤气燃烧得到的烟气混合,将混合气体温度升至500℃后进入加热提升管,作为气力提升载体将半焦提升至热半焦贮槽并同时提供半焦部分燃烧加热半焦需要的氧气。
燃烧后的高温烟气经热半焦贮槽进入热烟气旋风分离器,除尘后的高温烟气进入高温气体换热器,在这里,高温烟气与煤气、保温烟气和空气换热后进入干燥提升管,在这里将原料煤中的水分干燥至2℅以下并提升至
干煤一级旋风分离器。
d)过程热回收系统
该过程的热回收系统包括热半焦余热回收和热烟气余热回收两部分,热半焦(520℃)的余热回收在冷焦机中完成。
冷却至80℃的半焦去成品半焦库。
温度约800℃的热烟气余热回收在高温气体换热器中完成。
来自热烟气旋风分离器的高温烟气与来自煤气加压站的煤气、烟气循环风机Ⅱ来的循环烟气和空气鼓风机来的冷空气分别换热后,温度降至520℃左右进入干燥提升管。