涂装通用技术标准
涂装通用技术条件
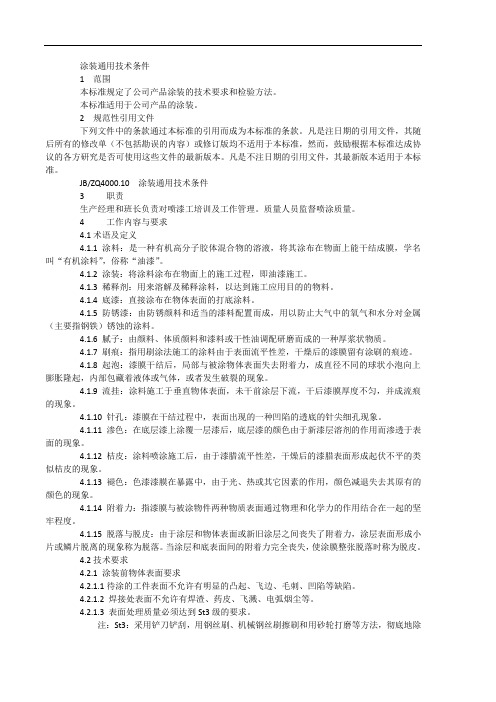
涂装通用技术条件1 范围本标准规定了公司产品涂装的技术要求和检验方法。
本标准适用于公司产品的涂装。
2 规范性引用文件下列文件中的条款通过本标准的引用而成为本标准的条款。
凡是注日期的引用文件,其随后所有的修改单(不包括勘误的内容)或修订版均不适用于本标准,然而,鼓励根据本标准达成协议的各方研究是否可使用这些文件的最新版本。
凡是不注日期的引用文件,其最新版本适用于本标准。
JB/ZQ4000.10 涂装通用技术条件3 职责生产经理和班长负责对喷漆工培训及工作管理。
质量人员监督喷涂质量。
4 工作内容与要求4.1术语及定义4.1.1 涂料:是一种有机高分子胶体混合物的溶液,将其涂布在物面上能干结成膜,学名叫“有机涂料”,俗称“油漆”。
4.1.2 涂装:将涂料涂布在物面上的施工过程,即油漆施工。
4.1.3 稀释剂:用来溶解及稀释涂料,以达到施工应用目的的物料。
4.1.4 底漆:直接涂布在物体表面的打底涂料。
4.1.5 防锈漆:由防锈颜料和适当的漆料配置而成,用以防止大气中的氧气和水分对金属(主要指钢铁)锈蚀的涂料。
4.1.6 腻子:由颜料、体质颜料和漆料或干性油调配研磨而成的一种厚浆状物质。
4.1.7 刷痕:指用刷涂法施工的涂料由于表面流平性差,干燥后的漆膜留有涂刷的痕迹。
4.1.8 起泡:漆膜干结后,局部与被涂物体表面失去附着力,成直径不同的球状小泡向上膨胀隆起,内部包藏着液体或气体,或者发生破裂的现象。
4.1.9 流挂:涂料施工于垂直物体表面,未干前涂层下流,干后漆膜厚度不匀,并成流痕的现象。
4.1.10 针孔:漆膜在干结过程中,表面出现的一种凹陷的透底的针尖细孔现象。
4.1.11 渗色:在底层漆上涂覆一层漆后,底层漆的颜色由于新漆层溶剂的作用而渗透于表面的现象。
4.1.12 桔皮:涂料喷涂施工后,由于漆腊流平性差,干燥后的漆腊表面形成起伏不平的类似桔皮的现象。
4.1.13 褪色:色漆漆膜在暴露中,由于光、热或其它因素的作用,颜色减退失去其原有的颜色的现象。
涂装通用技术条件
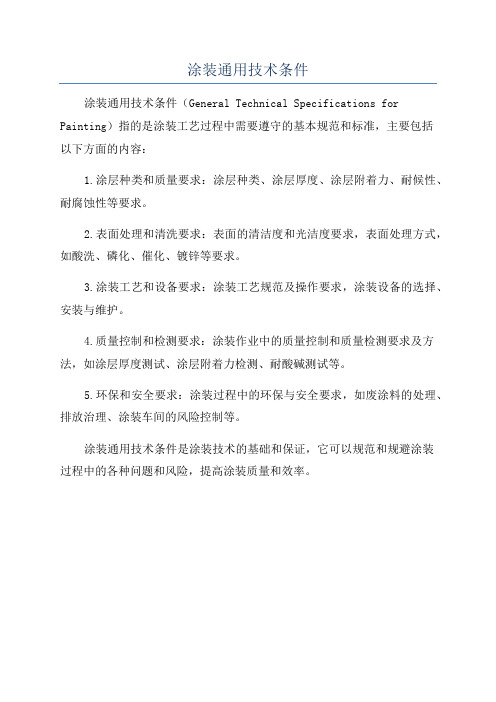
涂装通用技术条件
涂装通用技术条件(General Technical Specifications for Painting)指的是涂装工艺过程中需要遵守的基本规范和标准,主要包括
以下方面的内容:
1.涂层种类和质量要求:涂层种类、涂层厚度、涂层附着力、耐候性、耐腐蚀性等要求。
2.表面处理和清洗要求:表面的清洁度和光洁度要求,表面处理方式,如酸洗、磷化、催化、镀锌等要求。
3.涂装工艺和设备要求:涂装工艺规范及操作要求,涂装设备的选择、安装与维护。
4.质量控制和检测要求:涂装作业中的质量控制和质量检测要求及方法,如涂层厚度测试、涂层附着力检测、耐酸碱测试等。
5.环保和安全要求:涂装过程中的环保与安全要求,如废涂料的处理、排放治理、涂装车间的风险控制等。
涂装通用技术条件是涂装技术的基础和保证,它可以规范和规避涂装
过程中的各种问题和风险,提高涂装质量和效率。
涂装通用技术条件
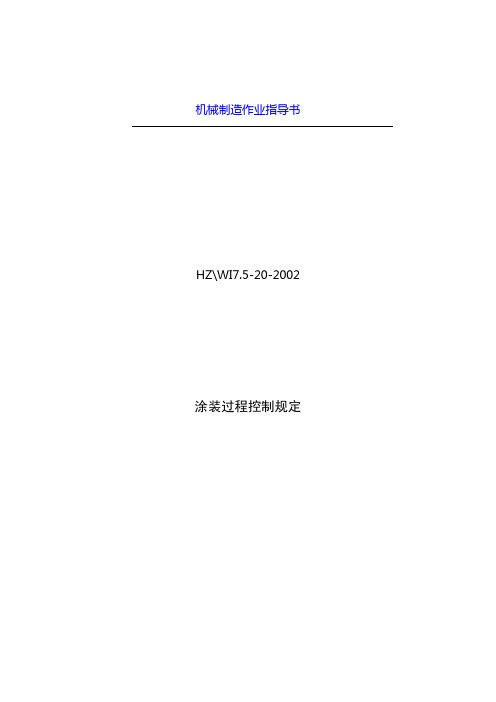
机械制造作业指导书HZ\WI7.5-20-2002涂装过程控制规定文件提出部门:编写:审核:批准:2002年9 月 2 日发布 2002年9 月 2 日实施⒈主题内容与适用范围本指导书规定了机械产品涂装的通用技术要求与检验规则。
本指导书适用于机械产品的防护和装饰性涂装。
⒉术语⒉1底漆直接涂于物体表面打底,是基层用漆。
其防锈能力强,附着力强,对金属起防锈作用。
⒉2腻子用于预先涂有底漆的表面,填平凹坑、缝隙、碰伤及划伤等缺陷;腻子应具备良好的结合力和打磨性能,经打磨后呈平整光滑的表面。
⒉3面漆用于底漆和腻子之后,保护底漆和腻子,对金属起防蚀作用。
面漆应具有良好的耐候性、化学稳定性及物理机械性能。
涂膜光亮,色彩绚丽,使产品外形光滑、整洁、美观。
⒉4稀释剂用于稀释涂料,是涂料的辅助材料之一。
⒊涂料要求⒊1涂装所用的底漆、腻子、二道底漆、面漆、稀释剂,应具有良好的配套性。
必须配套使用,具体品种按表1规定选用,图样或技术文件有特殊要求时按其要求选用。
⒊2涂料的质量必须符合化工部标准或有关标准的规定。
表1⒋涂层部位与涂层颜色⒋1产品机身外部表面的涂料颜色一般按图纸要求执行,也允许按用户要求确定。
⒋2机身上可以根据具体情况采用不同的装饰性线条或颜色。
⒋3齿轮箱体和箱盖、轴承盖、油箱的未加工内壁,以及经常浸在油中的零件未加工表面,应涂耐油涂料。
⒋4装配后不易或不能涂装的部件或表面应在装配前涂装。
⒋5需要引起注意部位的涂装,应涂鲜艳色彩的涂料。
裸露的转动零件如飞轮、皮带轮、齿轮等轮辐及转动罩壳,应涂红色涂料。
⒋6产品上各种特殊标志,如厂名、商标、指示符号、警戒标志等,应涂与该标志所在部位的颜色有明显区别、协调而醒目的颜色。
⒋7已涂装的外购件和外协件,如涂膜未被破坏且装配后不影响整机美观时,可不再涂装。
否则必须用与原色相同的涂料补涂。
⒌涂装施工涂装施工时,必须严格遵守各种涂料对温度、湿度、重涂间隔时间、调配方法、注意事项等各种规定。
涂装通用技术标准
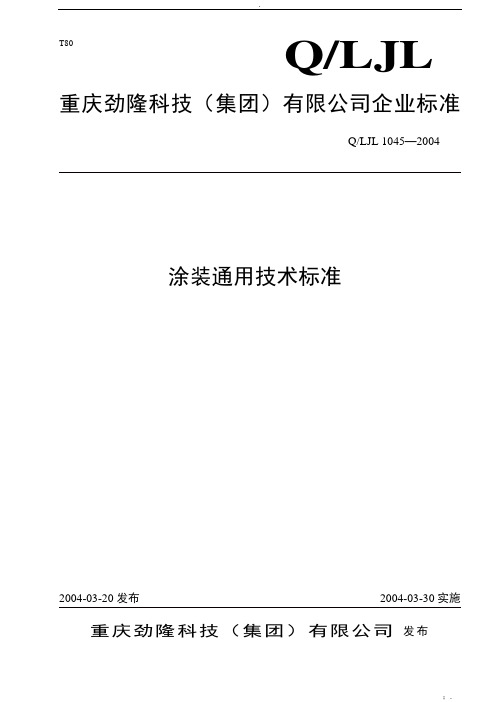
在光源不投映在被测物上的角度进行观察。
C级保护装饰面
1500mm
300Lx
15.4
在成车状态下,按显著易见度等级划分为AA,A,B,C四级。
1)AA级保护装饰面:成车状态下暴露面(特殊要求)。
2)A级保护装饰面:成车状态下站在周围50cm处能直视的范围。
3)B级保护装饰面:成车状态下站在周围50cm处不易观察的范围。
当事者协商
耐湿润性
48h无异常
加速耐候性
400h≤1级
(综合评级)
200h≤1级(综合评级)
——
400h≤1级(综合评级)
——
备注:
1)耐盐雾试验的无异常指的是单边涂层脱落宽度≤3mm,双边涂层脱落宽度≤6mm,其余区域内无脱落、变色、起泡、开裂,不得有明显的失光和软化。
2)以上要求中其余无异常指的是:涂层不得有脱落、变色、起泡、开裂,不得有明显的失光和软化。
GB/T 1720-89 漆膜附着力测定法
GB/T 1732-93 漆膜耐冲击力测定法
GB/T 1865-93 漆膜老化(人工加速 )
GB/T 1734-93 漆膜耐汽油性测定法
GB/T 1734-93 漆膜铅笔硬度
GB/T 1743-93 漆膜光泽度测定法
GB/T 1743-93 漆膜耐候性
GB/T 1764-93 漆膜厚度测定法
表7被涂装面为铝合金系列
项目
种类的符号
A1
A2
铅笔硬度
HB以上合格
附着力
2mm网格法100/100
厚度
由当事者协商
耐汽油性
8h无异常
耐机油性
24h无异常
耐盐雾试验
48h无异常
涂装标准
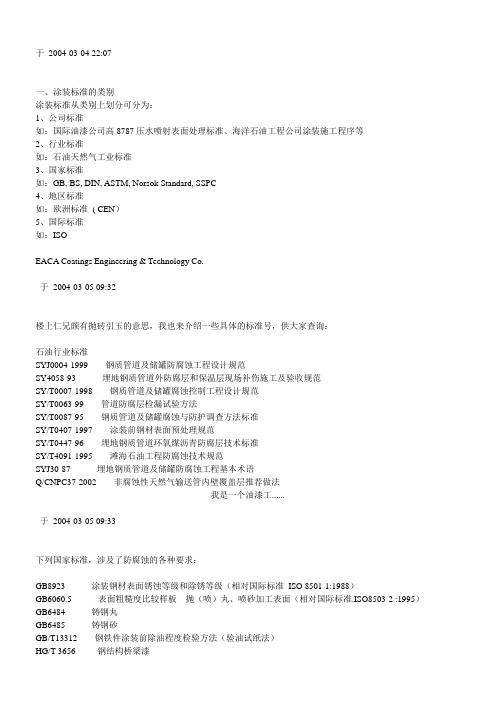
于2004-03-04 22:07________________________________________一、涂装标准的类别涂装标准从类别上划分可分为:1、公司标准如:国际油漆公司高8787压水喷射表面处理标准、海洋石油工程公司涂装施工程序等2、行业标准如:石油天然气工业标准3、国家标准如:GB, BS, DIN, ASTM, Norsok Standard, SSPC4、地区标准如:欧洲标准( CEN)5、国际标准如:ISO________________________________________EACA Coatings Engineering & Technology Co.于2004-03-05 09:32________________________________________楼上仁兄颇有抛砖引玉的意思,我也来介绍一些具体的标准号,供大家查询:石油行业标准SYJ0004-1999 钢质管道及储罐防腐蚀工程设计规范SY4058-93 埋地钢质管道外防腐层和保温层现场补伤施工及验收规范SY/T0007-1998 钢质管道及储罐腐蚀控制工程设计规范SY/T0063-99 管道防腐层检漏试验方法SY/T0087-95 钢质管道及储罐腐蚀与防护调查方法标准SY/T0407-1997 涂装前钢材表面预处理规范SY/T0447-96 埋地钢质管道环氧煤沥青防腐层技术标准SY/T4091-1995 滩海石油工程防腐蚀技术规范SYJ30-87 埋地钢质管道及储罐防腐蚀工程基本术语Q/CNPC37-2002 非腐蚀性天然气输送管内壁覆盖层推荐做法________________________________________我是一个油漆工......于2004-03-05 09:33________________________________________下列国家标准,涉及了防腐蚀的各种要求:GB8923 涂装钢材表面锈蚀等级和除锈等级(相对国际标准ISO 8501-1:1988)GB6060.5 表面粗糙度比较样板抛(喷)丸、喷砂加工表面(相对国际标准.ISO8503-2 :1995)GB6484 铸钢丸GB6485 铸钢砂GB/T13312 钢铁件涂装前除油程度检验方法(验油试纸法)HG/T 3656 钢结构桥梁漆JB/Z350 高压无气喷涂典型工艺GB1764 漆膜厚度测定法GB/T 5210 涂层附着力的测定法,拉开法GB/T 1771 色漆和清漆耐中性盐雾性能的测定(相对国际标准ISO 7253:1984)GB/T 1865 色漆和清漆人工气候老化和人工辐射曝露(相对国际标准ISO 11341:1994)GB/T1740 漆膜耐湿热测定法GB7692 涂装作业安全规程涂漆前处理工艺安全GB6514 涂装作业安全规程涂漆工艺安全GB/T15957-1995 大气环境腐蚀性分类________________________________________我是一个油漆工......epoxy编辑积分: 531发帖: 311来自: 广州于2004-03-05 09:34________________________________________附着力测试标准ISO 2409:1972 色漆和清漆-划格法测试ISO 4624:1978 色漆和清漆-附着力拉开法测试ASTM D 3359-87 胶带纸附着力标准测试法________________________________________我是一个油漆工......epoxy编辑积分: 531发帖: 311来自: 广州于2004-03-05 09:34________________________________________ASTM D 5162-01 标准操作规程-金属底材上不传导型保护用涂料的不连续性(漏涂)测试NACE RP 0188-99 标准测试规程-保护用涂料的不连续性(漏涂)测试法无机富锌漆的MEK测试ASTM D 4752-87 无机硅酸富锌漆的耐MEK溶剂擦拭标准测试法________________________________________我是一个油漆工......于2004-03-05 09:44________________________________________国际上常用的相关标准有:1、新钢材表面锈蚀等级--- ISO 8501-1:1988 / SSPC Vis2、已有涂层表面的锈蚀等级--- ISO4628 / ASTM D6103、底材表面可溶性盐的检测--- ISO8502-64、表面处理等级--- ISO8501:1988 / SSPC SP / DIN 559285、表面粗糙度--- ISO8503 / ASTM D 4417 / RUGOTEST No.36、喷砂磨料标准--- ISO11124/ 11125/ 11126/ 111277、底材表面灰尘--- ISO8502-38、干膜厚度的测量--- SSPC PA2 / DIN 55929 / ISO28089、附着力--- ISO4624 / SIS184171 / ASTM D3359 / ISO240910、无机富锌底漆固化程度--- ASTM D475211、针孔检测--- DIN 5567012、已有涂层的评估--- ISO4628 / ASTM D714________________________________________EACA Coatings Engineering & Technology Co.于2004-03-05 09:46________________________________________表面处理相关标准除锈程度ISO8501-1/ISO8501-2/SSPC SP底材表面清洁程度ISO8502-1~9表面粗糙度ISO8503/ASTM D4417/RUGOTEST No.3喷砂磨料标准ISO11124/ISO11125/ISO11126/ISO11127________________________________________EACA Coatings Engineering & Technology Co.于2004-03-05 09:48________________________________________表面处理--- 除锈程度ISO8501-1:1988锈蚀等级(Rust Grades)A:钢表面完全被粘附的氧化皮覆盖,极少量或无可见锈B:钢表面被氧化皮和锈覆盖C:钢表面完全被锈覆盖,极少量或无可见点蚀D:钢表面完全被锈覆盖,可见点蚀除锈程度Sa : 喷砂除锈Sa1/Sa2/Sa2.5/Sa3(SSPC SP7/SP6/SP10/SP5)St : 手工或动力工具除锈St2 / St3Fl : 火焰清洁AFl/BFl/CFl/DFlISO8501-2 --- 已有涂层表面的表面处理等级P Sa : 已有涂层表面局部彻底的喷砂处理P Sa2/P Sa2.5/P Sa3P St : 已有涂层表面局部手工和动力工具处理P St2/P St3P Ma : 已有涂层表面局部机械打磨处理P Ma________________________________________EACA Coatings Engineering & Technology Co.于2004-03-11 19:26________________________________________涉及工业防腐行业,SSPC和NACE标准比较全面,内容也丰富,但这些标准在借用时应有所选择,毕竟有国情差异.我现将SSPC和NACE标准的大致内容一一介绍给大家,是英文的,讲就着看.NACE标准大致有下列几种:(一)、Recommended Practices1-1、NACE No. 1/SSPC-SP 5 White Metal Blast Cleaning1-2、NACE No. 10/SSPC-PA 6 Fiberglass-Reinforced Plastic (FRP)Linings Applied to Bottoms of Carbon Steel Aboveground Storage Tanks1-3、NACE No. 11/SSPC-PA 8 Thin-Film Organic Linings Applied in New Carbon Steel Process Vessels1-4、NACE No. 12/AWS C2.23M/SSPC-CS 23.00 Specification for the Application of Thermal Spray Coatings (Metallizing) of Aluminum, Zinc, and Their Alloys and Composites for the Corrosion Protection of Steel1-5、NACE No. 2/SSPC-SP 10 Near-White Metal Blast Cleaning1-6、NACE No. 3/SSPC-SP 6 Commercial Blast Cleaning1-7、NACE No. 4/SSPC-SP 7 Brush-Off Blast Cleaning1-8、NACE No. 5/SSPC-SP 12 Surface Preparation and Cleaning of Metals by Waterjetting Prior to Recoating1-8、NACE No. 6/SSPC-SP 13 Surface Preparation of Concrete1-9、NACE No. 8/SSPC-SP 14 Industrial Blast Cleaning1-10、NACE VIS 7/SSPC-VIS 4 Guide and Visual Reference Photographs for Steel Cleaned by Waterjetting1-11、RP0100 RP0100-2000 Cathodic Protection of Prestressed Concrete Cylinder Pipelines1-12、RP0102 RP0102-2002 In-Line Inspection of Pipelines1-13、RP0169 RP0169-2002 Control of External Corrosion on Underground or Submerged Metallic Piping Systems 1-14、RP0170 RP0170-97 Protection of Austenitic Stainless Steels and Other Austenitic Alloys from Polythionic Acid Stress Corrosion Cracking During Shutdown of Refinery Equipment1-15、RP0176 RP0176-2003 Corrosion Control of Steel Fixed Offshore Structures Associated with Petroleum Production1-16、RP0177 RP0177-2000 Mitigation of Alternating Current and Lightning Effects on Metallic Structures and Corrosion Control Systems1-17、RP0178 RP0178-2003 Fabrication Details, Surface Finish Requirements, and Proper Design Considerations for Tanks and Vessels to Be Lined for Immersion Service1-18、RP0180 RP0180-2001 Cathodic Protection of Pulp and Paper Mill Effluent Clarifiers1-19、RP0185 RP0185-96 Extruded Polyolefin Resin Coating Systems with Soft Adhesives for Underground or Submerged Pipe1-20、RP0186 RP0186-2001 Application of Cathodic Protection for External Surfaces of Steel Well Casings1-21、RP0187 RP0187-96 Design Considerations for Corrosion Control of Reinforcing Steel in Concrete1-22、RP0188 RP0188-99 Discontinuity (Holiday) Testing of New Protective Coatings on Conductive Substrates1-23、RP0189 RP0189-2002 On-Line Monitoring of Cooling Waters1-24、RP0191 RP0191-2002 The Application of Internal Plastic Coatings for Oilfield Tubular Goods and Accessories 1-25、RP0192 RP0192-98 Monitoring Corrosion in Oil and Gas Production with Iron Counts1-26、RP0193 RP0193-2001 External Cathodic Protection of On-Grade Carbon Steel Storage Tank Bottoms1-27、RP0195 RP0195-2001 Recommended Practice for Corrosion Control of Sucker Rods by Chemical Treatment 1-28、RP0196 RP0196-96 Galvanic Anode Cathodic Protection of Internal Submerged Surfaces of Steel Water Storage Tanks1-29、RP0197 RP0197-97 Standard Format for Computerized Electrochemical Polarization Curve Data Files1-30、RP0198 RP0198-98 The Control of Corrosion Under Thermal Insulation and Fireproofing Materials--A Systems Approach1-31、RP0199 RP0199-2004 Installation of Stainless Chromium-Nickel Steel and Nickel-Alloy Roll-Bonded and Explosion-Bonded Clad Plate in Air Pollution Control Equipment1-32、RP0200 RP0200-2000 Steel-Cased Pipeline Practices1-33、RP0273 RP0273-2001 Handling and Proper Usage of Inhibited Oilfield Acids1-34、RP0274 RP0274-98 High-V oltage Electrical Inspection of Pipeline Coatings1-35、RP0281 RP0281-98 Method for Conducting Coating (Paint) Panel Evaluation Testing in Atmospheric Exposures1-36、RP0285 RP0285-2002 Corrosion Control of Underground Storage Tank Systems by Cathodic Protection1-37、RP0286 RP0286-2002 Electrical Isolation of Cathodically Protected Pipelines1-38、RP0287 RP0287-2002 Field Measurement of Surface Profile of Abrasive Blast-Cleaned Steel Surfaces Using a Replica Tape1-39、RP0290 RP0290-2000 Impressed Current Cathodic Protection of Reinforcing Steel in Atmospherically Exposed Concrete Structures1-40、RP0291 RP0291-96 Care, Handling, and Installation of Internally Plastic-Coated Oilfield Tubular Goods and Accessories1-41、RP0292 RP0292-2003 Installation of Thin Metallic Wallpaper Lining in Air Pollution Control and Other Process Equipment1-42、RP0295 RP0295-2003 Application of a Coating System to Interior Surfaces of New and Used Rail Tank Cars 1-43、RP0296 RP0296-2000 Guidelines for Detection, Repair, and Mitigation of Cracking of Existing Petroleum Refinery Pressure Vessels in Wet H2S Environments1-44、RP0297 RP0297-97 Maintenance Painting of Electrical Substation Apparatus Including Flow Coating of Transformer Radiators1-45、RP0298 RP0298-98 Sheet Rubber Linings for Abrasion and Corrosion Service1-46、RP0300 RP0300-2003 Pilot Scale Evaluation of Corrosion and Fouling Control Additives for Open Recirculating Cooling Water Systems1-47、RP0302 RP0302-2002 Selection and Application of a Coating System to Interior Surfaces of New and Used Rail Tank Cars in Molten Sulfur Service1-48、RP0303 RP0303-2003 Field-Applied Heat-Shrinkable Sleeves for Pipelines: Application, Performance, and Quality Control1-49、RP0375 RP0375-99 Wax Coating Systems for Underground Piping Systems1-50、RP0386 RP0386-2003 Application of a Coating System to Interior Surfaces of Covered Steel Hopper Rail Cars in Plastic, Food, and Chemical Service1-51、RP0387 RP0387-99 Metallurgical and Inspection Requirements for Cast Galvanic Anodes for Offshore Applications1-52、RP0388 RP0388-2001 Impressed Current Cathodic Protection of Internal Submerged Surfaces of Carbon Steel Water Storage Tanks1-53、RP0390 RP0390-98 Maintenance and Rehabilitation Considerations for Corrosion Control of Atmospherically Exposed Existing Steel-Reinforced Concrete Structures1-54、RP0391 RP0391-2001 Materials for the Handling and Storage of Commercial Concentrated (90 to 100%) Sulfuric Acid at Ambient Temperatures1-55、RP0392 RP0392-2001 Recovery and Repassivation After Low pH Excursions in Open Recirculating Cooling Water Systems1-56、RP0394 RP0394-2002 Application, Performance, and Quality Control of Plant-Applied, Fusion-Bonded Epoxy External Pipe Coating1-57、RP0395 RP0395-99 Fusion-Bonded Epoxy Coating of Steel Reinforcing Bars1-58、RP0398 RP0398-98 Recommendations for Training and Qualifying Personnel as Railcar Coating and Lining Inspectors1-59、RP0399 RP0399-99 Plant-Applied, External Coal Tar Enamel Pipe Coating Systems: Application, Performance, and Quality Control1-60、RP0402 RP0402-2002 Field-Applied Fusion-Bonded Epoxy (FBE) Pipe Coating Systems for Girth Weld Joints: Application, Performance, and Quality Control1-61、RP0403 RP0403-2003 Avoiding Caustic Stress Corrosion Cracking of Carbon Steel Refinery Equipment and Piping1-62、RP0472 RP0472-2000 Methods and Controls to Prevent In-Service Environmental Cracking of Carbon Steel Weldments in Corrosive Petroleum Refining Environments1-63、RP0475 RP0475-98 Selection of Metallic Materials to Be Used in All Phases of Water Handling for Injection into Oil-Bearing Formations1-64、RP0487 RP0487-2000 Considerations in the Selection and Evaluation of Rust Preventives and Vapor Corrosion Inhibitors for Interim (Temporary) Corrosion Protection1-65、RP0490 RP0490-2001 Holiday Detection of Fusion-Bonded Epoxy External Pipeline Coatings of 250 to 760 µm (10 to 30 mils)1-66、RP0491 RP0491-2003 Worksheet for the Selection of Oilfield Nonmetallic Seal Systems1-67、RP0492 RP0492-99 Metallurgical and Inspection Requirements for Offshore Pipeline Bracelet Anodes1-68、RP0495 RP0495-2003 Guidelines for Qualifying Personnel as Abrasive Blasters and Coating and Lining Applicators in the Rail Industries1-69、RP0497 RP0497-97 Field Corrosion Evaluation Using Metallic Test Specimens1-70、RP0502 RP0502-2002 Pipeline External Corrosion Direct Assessment Methodology1-71、RP0572 RP0572-2001 Design, Installation, Operation, and Maintenance of Impressed Current Deep Groundbeds1-72、RP0575 RP0575-2001 Internal Cathodic Protection Systems in Oil-Treating Vessels1-73、RP0590 RP0590-96 Recommended Practice for Prevention, Detection, and Correction of Deaerator Cracking 1-74、RP0592 RP0592-2001 Application of a Coating System to Interior Surfaces of New and Used Rail Tank Cars in Concentrated (90 to 98%) Sulfuric Acid Service1-75、RP0602 RP0602-2002 Field-Applied Coal Tar Enamel Pipe Coating Systems: Application, Performance, and Quality Control1-76、RP0690 RP0690-98 Standard Format for Collection and Compilation of Data for Computerized Material Corrosion Resistance Database Input1-77、RP0692 RP0692-2003 Application of a Coating System to Exterior Surfaces of Steel Rail Cars1-78、RP0775 RP0775-99 Preparation, Installation, Analysis, and Interpretation of Corrosion Coupons in OilfieldOperations1-79、RP0892 RP0892-2001 Coatings and Linings Over Concrete for Chemical Immersion and Containment Service 1-80、SSPC-VIS 2 Standard Method of Evaluating Degree of Rusting on Painted Steel Surfaces(二)、Material Requirements2-1、MR0103 MR0103-2003 Materials Resistant to Sulfide Stress Cracking in Corrosive Petroleum Refining Environments2-2、MR0174 MR0174-2001 Recommendations for Selecting Inhibitors for Use as Sucker-Rod Thread Lubricants 2-3、MR0176 MR0176-2000 Metallic Materials for Sucker-Rod Pumps for Corrosive Oilfield Environments2-4、NACE MR0175/ISO 15156 Petroleum and natural gas industries—Materials for use in H2S-containing environments in oil and gas production(三)、Test Method3-1、TM0101 TM0101-2001Measurement Techniques Related to Criteria for Cathodic Protection on Underground or Submerged Metallic Tank Systems3-2、TM0102 TM0102-2002 Measurement of Protective Coating Electrical Conductance on Underground Pipelines 3-3、TM0103 TM0103-2003 Laboratory Test Procedures for Evaluation of SOHIC Resistance of Plate Steels Used in Wet H2S Service3-4、TM0169 TM0169-2000 Laboratory Corrosion Testing of Metals3-5、TM0172 TM0172-2001 Determining Corrosive Properties of Cargoes in Petroleum Product Pipelines3-6、TM0173 TM0173-99 Methods for Determining Quality of Subsurface Injection Water Using Membrane Filters 3-7、TM0174 TM0174-2002 Laboratory Methods for the Evaluation of Protective Coatings and Lining Materials on Metallic Substrates in Immersion Service3-8、TM0177 TM0177-96 Laboratory Testing of Metals for Resistance to Sulfide Stress Cracking and Stress Corrosion Cracking in H2S Environments3-9、TM0183 TM0183-2000 Evaluation of Internal Plastic Coatings for Corrosion Control of Tubular Goods in an Aqueous Flowing Environment3-10、TM0185 TM0185-2000 Evaluation of Internal Plastic Coatings for Corrosion Control of Tubular Goods by Autoclave Testing3-11、TM0186 TM0186-2002 Holiday Detection of Internal Tubular Coatings of 250 to 760 µm (10 to 30 mils) Dry-Film Thickness3-12、TM0187 TM0187-2003 Evaluating Elastomeric Materials in Sour Gas Environments3-13、TM0190 TM0190-98 Impressed Current Laboratory Testing of Aluminum Alloy Anodes3-14、TM0192 TM0192-2003 Evaluating Elastomeric Materials in Carbon Dioxide Decompression Environments3-15、TM0193 TM0193-2000 Laboratory Corrosion Testing of Metals in Static Chemical Cleaning Solutions at Temperatures Below 93°C (200°F)3-16、TM0194 TM0194-94 Field Monitoring of Bacterial Growth in Oilfield Systems3-17、TM0196 TM0196-96 Chemical Resistance of Polymeric3-18、TM0197 TM0197-2002 Laboratory Screening Test to Determine the Ability of Scale Inhibitors to Prevent the Precipitation of Barium Sulfate and/or Strontium Sulfate from Solution (for Oil & Gas Prod. Systems)3-19、TM0198 TM0198-98 Slow Strain Rate Test Method for Screening Corrosion-Resistant Alloys (CRAs) for Stress Corrosion Cracking in Sour Oilfield Service3-20、TM0199 TM0199-99 Standard Test Method for Measuring Deposit Mass Loading (Deposit Weight Density) Values for Boiler Tubes by the Glass-Bead-Blasting Technique3-21、TM0284 TM0284-2003 Evaluation of Pipeline and Pressure Vessel Steels for Resistance to Hydrogen-Induced Cracking3-22、TM0286 TM0286-2001 Cooling Water Test Unit Incorporating Heat Transfer Surfaces3-23、TM0294 TM0294-2001 Testing of Embeddable Impressed Current Anodes for Use in Cathodic Protection of Atmospherically Exposed Steel-Reinforced Concrete3-24、TM0296 TM0296-2002 Evaluating Elastomeric Materials in Sour Liquid Environments3-25、TM0297 TM0297-2002 Effects of High-Temperature, High-Pressure Carbon Dioxide Decompression on Elastomeric Materials3-26、TM0298 TM0298-2003 Evaluating the Compatibility of FRP Pipe and Tubulars with Oilfield Environments3-27、TM0299 TM0299-99 Corrosion Control and Monitoring in Seawater Injection Systems3-28、TM0374 TM0374-2001 Laboratory Screening Tests to Determine the Ability of Scale Inhibitors to Prevent the Precipitation of Calcium Sulfate and Calcium Carbonate from Solution (for Oil & Gas Prod. Systems)3-29、TM0384 TM0384-2002 Holiday Detection of Internal Tubular Coatings of Less Than 250 µm (10 mils) Dry-Film Thickness3-30、TM0397 TM0397-2002 Screening Tests for Evaluating the Effectiveness of Gypsum Scale Removers3-31、TM0398 TM0398-98 Laboratory Corrosion Testing of Metals in Static Chemical Cleaning Solutions at Temperatures Above 100°C (212°F)3-32、TM0399 TM0399-99 Standard Test Method for Phosphonate in Brine3-33、TM0497 TM0497-2002 Measurement Techniques Related to Criteria for Cathodic Protection on Underground or Submerged Metallic Piping Systems3-34、TM0498 TM0498-2002 Standard Test Methods for Measuring the Carburization of Alloys Used for Ethylene Cracking Furnace Tubes3-35、TM0499 TM0499-99 Immersion Corrosion Testing of Ceramic Materials。
涂装技术要求

架桥机、运梁车涂装技术要求1.1涂装前表面清理1.1.1涂装前表面等级要求1.1.1.1富锌防锈防滑底漆,钢梁表面清理应达到GB/T8923-1988规定的Sa3级。
1.1.1.2涂醇酸、酚醛、聚氨脂底漆,钢梁表面清理应达到GB/T8923-1988规定的Sa2.5级。
1.1.1.3 栏杆、扶手、人行道、吊篮等附属钢结构涂装防锈底漆钢表面清理应达到GB/T8923-1988规定的Sa2级。
1.1.2.涂装前钢梁表面粗糙度要求1.1.2.1.涂装涂料涂层时,钢梁表面粗糙度规定为Rz25~60μm,即符合JB/T6060.5-1998规定。
1.1.2.2.富锌防滑底漆钢梁表面粗糙度Rz50~100μm,即符合JB/T6060.5-1998规定。
1.1.2.3.涂装涂料涂层选用最大粗糙度不超过涂装体系干膜厚度的1/3,表面粗糙度超过规定时,需加涂一道底漆。
1.1.3.钢表面清理用磨料钢表面清理磨料应符合YB/T5149-1993和YB/T5150-1993标准规定的钢丸、钢砂或应使用无盐分和无沾污的石英砂。
1.2.钢梁的涂料涂装体系(见下表)1.3.高强螺栓连接部分摩檫面涂装1.3.1.采用无机富锌防滑防锈涂料,涂层厚度为80μm。
涂层抗滑移系数不小于0.55。
1.4.涂层质量要求1.4.1.涂层表面平整均匀,不允许有剥落、其泡、裂纹、气孔。
1.4.2.金属涂层表面均匀一致,不允许有起皮、股泡、大熔滴、松散粒子、裂纹、掉块。
1.4.3.涂层附着力按GB/T9286-1998规定作划格实验,附着力不底于一级。
1.5试验方法1.5.1表面粗糙度检验1.5.1.1.表面粗糙度采用GB/T8923-1988规定的比较样块进行粗糙度目视和触觉评定。
1.5.1.2.表面粗糙度可用触针式表面轮廓仪测量。
1.5.1.3.峰谷深度可用指针式千分尺。
1.5.2.涂层表面质量检查采用目视法1.5.3涂层厚度检测方法1.5.3.1涂层干膜厚度和湿膜厚度测量,按GB/T13452.2-1992规定进行。
工程机械涂装通用技术条件
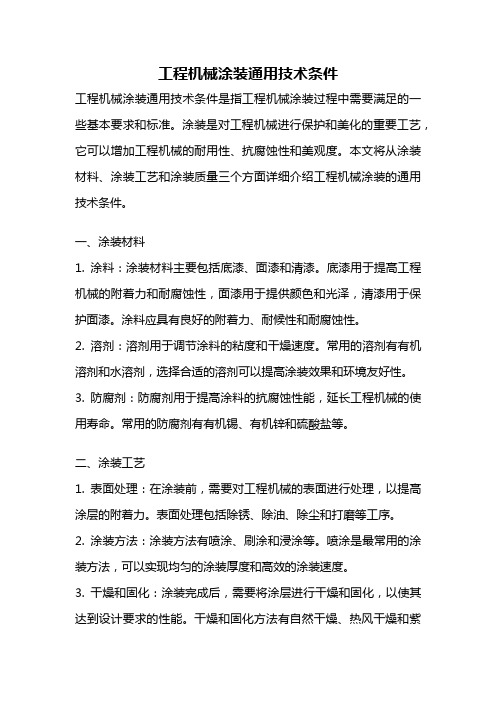
工程机械涂装通用技术条件工程机械涂装通用技术条件是指工程机械涂装过程中需要满足的一些基本要求和标准。
涂装是对工程机械进行保护和美化的重要工艺,它可以增加工程机械的耐用性、抗腐蚀性和美观度。
本文将从涂装材料、涂装工艺和涂装质量三个方面详细介绍工程机械涂装的通用技术条件。
一、涂装材料1. 涂料:涂装材料主要包括底漆、面漆和清漆。
底漆用于提高工程机械的附着力和耐腐蚀性,面漆用于提供颜色和光泽,清漆用于保护面漆。
涂料应具有良好的附着力、耐候性和耐腐蚀性。
2. 溶剂:溶剂用于调节涂料的粘度和干燥速度。
常用的溶剂有有机溶剂和水溶剂,选择合适的溶剂可以提高涂装效果和环境友好性。
3. 防腐剂:防腐剂用于提高涂料的抗腐蚀性能,延长工程机械的使用寿命。
常用的防腐剂有有机锡、有机锌和硫酸盐等。
二、涂装工艺1. 表面处理:在涂装前,需要对工程机械的表面进行处理,以提高涂层的附着力。
表面处理包括除锈、除油、除尘和打磨等工序。
2. 涂装方法:涂装方法有喷涂、刷涂和浸涂等。
喷涂是最常用的涂装方法,可以实现均匀的涂装厚度和高效的涂装速度。
3. 干燥和固化:涂装完成后,需要将涂层进行干燥和固化,以使其达到设计要求的性能。
干燥和固化方法有自然干燥、热风干燥和紫外线固化等。
三、涂装质量1. 涂装厚度:涂装厚度是涂层质量的重要指标之一。
涂装厚度过大会导致涂层开裂,涂装厚度过小会影响涂层的保护效果。
因此,涂装厚度应符合设计要求。
2. 涂装均匀性:涂装均匀性是指涂层在工程机械表面的分布是否均匀。
涂装均匀性差会导致涂层出现色差和质量问题,影响外观效果。
3. 涂层附着力:涂层附着力是指涂层与工程机械表面的粘结强度。
涂层附着力差会导致涂层脱落,影响涂层的使用寿命。
4. 涂层硬度:涂层硬度是指涂层的耐刮擦和耐磨损性能。
涂层硬度过低会影响涂层的耐久性和抗损伤性能。
5. 涂装质量检测:涂装质量检测是保证涂装质量的重要手段。
常用的涂装质量检测方法有涂层厚度测量、涂层附着力测试和涂层硬度测试等。
td298《涂装设备电气装置制造、安装及验收通用技术标准》
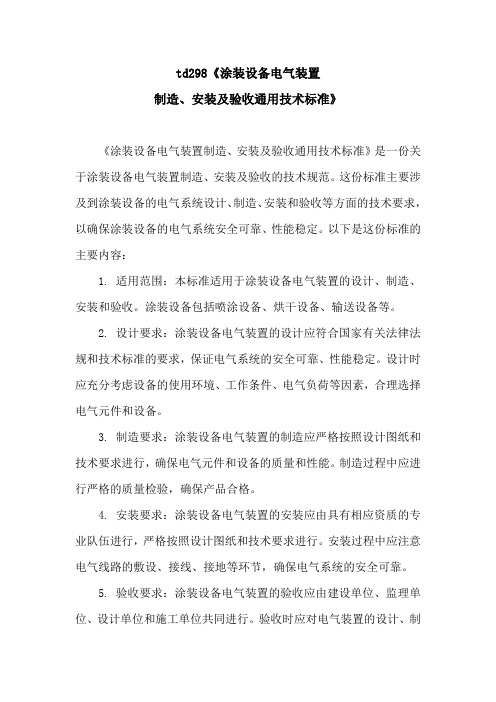
td298《涂装设备电气装置制造、安装及验收通用技术标准》《涂装设备电气装置制造、安装及验收通用技术标准》是一份关于涂装设备电气装置制造、安装及验收的技术规范。
这份标准主要涉及到涂装设备的电气系统设计、制造、安装和验收等方面的技术要求,以确保涂装设备的电气系统安全可靠、性能稳定。
以下是这份标准的主要内容:1. 适用范围:本标准适用于涂装设备电气装置的设计、制造、安装和验收。
涂装设备包括喷涂设备、烘干设备、输送设备等。
2. 设计要求:涂装设备电气装置的设计应符合国家有关法律法规和技术标准的要求,保证电气系统的安全可靠、性能稳定。
设计时应充分考虑设备的使用环境、工作条件、电气负荷等因素,合理选择电气元件和设备。
3. 制造要求:涂装设备电气装置的制造应严格按照设计图纸和技术要求进行,确保电气元件和设备的质量和性能。
制造过程中应进行严格的质量检验,确保产品合格。
4. 安装要求:涂装设备电气装置的安装应由具有相应资质的专业队伍进行,严格按照设计图纸和技术要求进行。
安装过程中应注意电气线路的敷设、接线、接地等环节,确保电气系统的安全可靠。
5. 验收要求:涂装设备电气装置的验收应由建设单位、监理单位、设计单位和施工单位共同进行。
验收时应对电气装置的设计、制造、安装等环节进行全面检查,确保各项技术要求得到满足。
6. 安全要求:涂装设备电气装置的安全要求主要包括:电气线路的绝缘性能、电气设备的防护等级、电气系统的接地保护等。
在设计和制造过程中,应充分考虑这些安全要求,确保电气系统的安全可靠。
7. 维护与保养:涂装设备电气装置的维护与保养主要包括:定期检查电气线路和设备的运行状态,及时发现并排除故障;定期对电气设备进行清洁和保养,确保设备的正常运行;定期对电气系统进行安全检查,确保电气系统的安全可靠。
8. 环保要求:涂装设备电气装置的环保要求主要包括:降低能耗、减少废弃物排放、提高资源利用率等。
在设计和制造过程中,应充分考虑这些环保要求,确保电气装置的环保性能。
涂装施工工艺标准
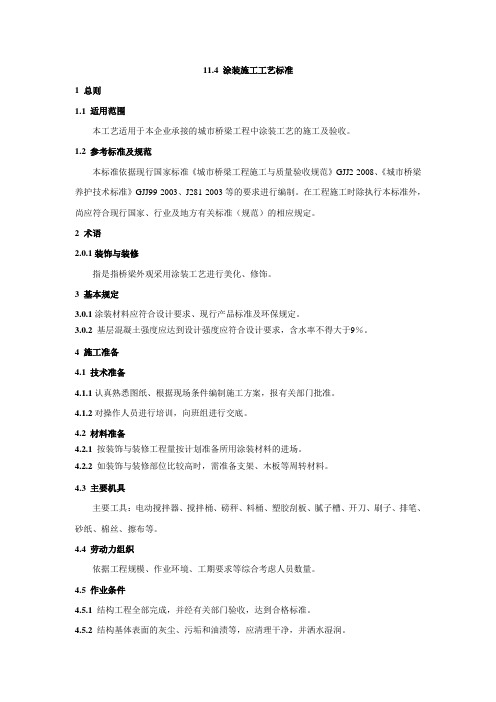
11.4 涂装施工工艺标准1 总则1.1 适用范围本工艺适用于本企业承接的城市桥梁工程中涂装工艺的施工及验收。
1.2 参考标准及规范本标准依据现行国家标准《城市桥梁工程施工与质量验收规范》GJJ2-2008、《城市桥梁养护技术标准》GJJ99-2003、J281-2003等的要求进行编制。
在工程施工时除执行本标准外,尚应符合现行国家、行业及地方有关标准(规范)的相应规定。
2 术语2.0.1装饰与装修指是指桥梁外观采用涂装工艺进行美化、修饰。
3 基本规定3.0.1涂装材料应符合设计要求、现行产品标准及环保规定。
3.0.2 基层混凝土强度应达到设计强度应符合设计要求,含水率不得大于9%。
4 施工准备4.1 技术准备4.1.1认真熟悉图纸、根据现场条件编制施工方案,报有关部门批准。
4.1.2对操作人员进行培训,向班组进行交底。
4.2 材料准备4.2.1 按装饰与装修工程量按计划准备所用涂装材料的进场。
4.2.2 如装饰与装修部位比较高时,需准备支架、木板等周转材料。
4.3 主要机具主要工具:电动搅拌器、搅拌桶、磅秤、料桶、塑胶刮板、腻子槽、开刀、刷子、排笔、砂纸、棉丝、擦布等。
4.4 劳动力组织依据工程规模、作业环境、工期要求等综合考虑人员数量。
4.5 作业条件4.5.1 结构工程全部完成,并经有关部门验收,达到合格标准。
4.5.2结构基体表面的灰尘、污垢和油渍等,应清理干净,并洒水湿润。
4.5.3抹灰前应检查基体表面的平整,以决定其抹灰厚度。
抹灰前应在大角的两面弹出抹灰层的控制线,以作为打底的依据。
4.5.4施工环境应通风良好,基面必须于燥。
4.5.5涂装施工时的环境温度不低于8℃,施工环境相对湿度不宜大于80%。
5 质量、技术要点5.1 材料要求5.1.1所用涂装材料应符合设计要求、现行产品标准及环保规定。
5.1.2涂装材料应有产品合格证、出厂日期及使用说明。
5.2 技术要求5.2.1 基面的浆皮、浮灰、油污、杂物等应彻底清除干净;基面应坚实平整粗糙,不得有积水;不得有空鼓、开裂、起砂和脱皮等缺陷。
QZSJG 7-2007摩托车和轻便摩托车涂装通用技术条件(2007[1]9)
![QZSJG 7-2007摩托车和轻便摩托车涂装通用技术条件(2007[1]9)](https://img.taocdn.com/s3/m/f4474acabe23482fb5da4c2a.png)
本标准代替历次版本发布情况Q/ZSJY 35-2003、Q/ZSJY36-2003、Q/ZSJG 7-2006、Q/ZSJG 7-2007(2007年5月30日发布)。
本标准备案号:QZSJ/0068。
摩托车和轻便摩托车
涂装通用技术条件
1范围
本标准规定了摩托车和轻便摩托车涂装的要求、试验方法、检验规则、包装、运输及贮存。
GB/T 6739-2006漆膜硬度铅笔测定法
GB/T 6807-2001钢铁工件涂装前磷化处理技术条件
GB/T 9276-1996漆层自然气候曝露试验方法
GB/T 9286-1998色漆和清漆漆膜的划格试验
GB/T 9754-1988色漆和清漆不含金属颜料的色漆漆膜元20°、60°和85°镜面光泽的测定
——调整、细化了各类零部件涂装的性能指标;
——细化了种类、底材及质量等级分类;
——补充了相应的试验方法;
——补充了检验规则、包装、运输及贮存等章节。
本标准由宗申产业集团有限公司技术中心会提出。
本标准由宗申产业集团有限公司技术中心归口管理。
本标准由宗申产业集团有限公司技术中心主任 吴建批准。
本标准由重庆宗申机车工业制造有限公司、重庆宗申技术开发研究有限公司负责起草。
GB/T 1743-1979漆膜光泽测定法
GB/T 1763-1979漆膜耐化学试剂性测定法
GB/T 1764-1979漆膜厚度测定法
GB/T 1771-1991色漆和清漆耐中性盐雾性能的测定
GB/T 1865-1997色漆和清漆人工气候老化和人工辐射暴露
GB/T 6458-1986金属覆盖层中性盐雾试验(NSS试验)
3.4桔皮
涂装设备通用技术条件 第1部分:钣金件

涂装设备通用技术条件第1部分:钣金件下载提示:该文档是本店铺精心编制而成的,希望大家下载后,能够帮助大家解决实际问题。
文档下载后可定制修改,请根据实际需要进行调整和使用,谢谢!本店铺为大家提供各种类型的实用资料,如教育随笔、日记赏析、句子摘抄、古诗大全、经典美文、话题作文、工作总结、词语解析、文案摘录、其他资料等等,想了解不同资料格式和写法,敬请关注!Download tips: This document is carefully compiled by this editor. I hope that after you download it, it can help you solve practical problems. The document can be customized and modified after downloading, please adjust and use it according to actual needs, thank you! In addition, this shop provides you with various types of practical materials, such as educational essays, diary appreciation, sentence excerpts, ancient poems, classic articles, topic composition, work summary, word parsing, copy excerpts, other materials and so on, want to know different data formats and writing methods, please pay attention!1. 引言在涂装行业中,钣金件是至关重要的组成部分。
涂装通用技术条件
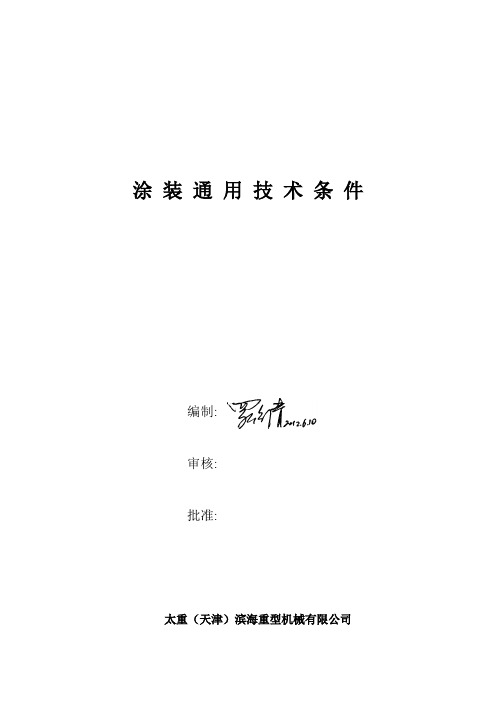
涂装通用技术条件编制:审核:批准:太重(天津)滨海重型机械有限公司目录1 适用范围 12 相关标准 13 术语和定义 14 涂装前的表面处理 25 涂层设计 36 涂装施工要求 47 涂装质量控制与检测 68 已涂覆过的钢材表面局部清除和涂装99 完工报告101涂装通用技术条件1 适用范围本标准规定了公司生产的机械产品及其零部件的涂装技术要求及检测要求。
主要适用于钢铁产品的表面涂装。
合同文件中有特殊要求的,除满足合同要求外还需满足本标准的规定。
2 相关标准JB/T 5000.12-2007 重型机械通用技术条件第12部分:涂装GB/T 5206.1 色漆和清漆词汇第一部分通用术语GB/T 5206.2-1986 色漆和清漆词汇第二部分树脂术语GB/T 5206.3-1986 色漆和清漆词汇第三部分颜料术语GB/T 8264-1987 涂装技术术语GB/T 5210-2006 色漆和清漆拉开法附着力试验GB/9286-1998 色漆和清漆漆膜的划格试验GB/T 8923-1988 涂装前钢材表面锈蚀等级和除锈等级GB/T 8923.2-2008 涂覆涂料前钢材表面处理表面清洁度的目视评定第2部分:已涂覆过的钢材表面局部清除原有涂层后的处理等级GB/T 8923.3-2009 涂敷涂料前钢材表面处理表面清洁度的目视评定第3部分:焊缝、边缘和其他区域的表面缺陷的处理等级3 术语和定义采用GB/T 5206、GB/T 8264中规定的术语.4 涂装前的表面处理所有用于设备制造的钢铁原材料,涂漆前均需进行表面除锈处理。
所有需要进行涂装的钢铁原材料或制件表面,在涂漆前必须将铁锈、氧化皮、油脂、灰尘、泥土、污物等清除干净。
4.1 除锈前,应先用有机溶剂、碱液、乳化剂、蒸汽等除去原材料或制件表面的油脂、污垢。
4.2 钢铁表面的除锈方法、除锈等级及适用范围见表1。
表1中Sa及St各等级的除锈要求及评定方法按GB/T 8923的规定。
涂装通用技术条件
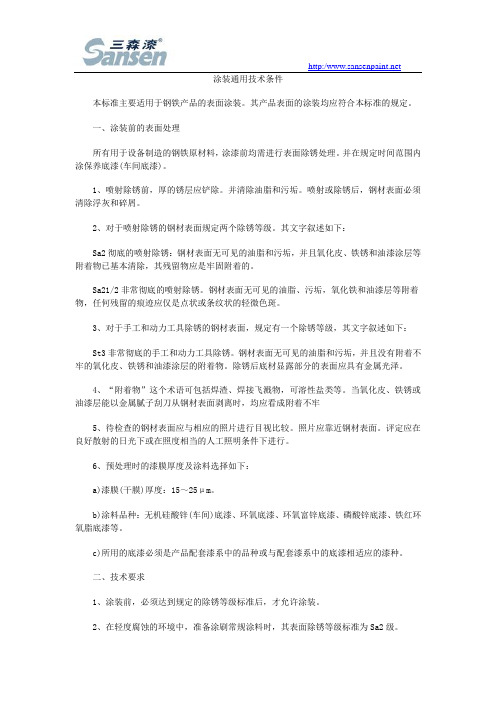
涂装通用技术条件本标准主要适用于钢铁产品的表面涂装。
其产品表面的涂装均应符合本标准的规定。
一、涂装前的表面处理所有用于设备制造的钢铁原材料,涂漆前均需进行表面除锈处理。
并在规定时间范围内涂保养底漆(车间底漆)。
1、喷射除锈前,厚的锈层应铲除。
并清除油脂和污垢。
喷射或除锈后,钢材表面必须清除浮灰和碎屑。
2、对于喷射除锈的钢材表面规定两个除锈等级。
其文字叙述如下:Sa2彻底的喷射除锈:钢材表面无可见的油脂和污垢,并且氧化皮、铁锈和油漆涂层等附着物已基本清除,其残留物应是牢固附着的。
Sa21/2非常彻底的喷射除锈。
钢材表面无可见的油脂、污垢,氧化铁和油漆层等附着物,任何残留的痕迹应仅是点状或条纹状的轻微色斑。
3、对于手工和动力工具除锈的钢材表面,规定有一个除锈等级,其文字叙述如下:St3非常彻底的手工和动力工具除锈。
钢材表面无可见的油脂和污垢,并且没有附着不牢的氧化皮、铁锈和油漆涂层的附着物。
除锈后底材显露部分的表面应具有金属光泽。
4、“附着物”这个术语可包括焊渣、焊接飞溅物,可溶性盐类等。
当氧化皮、铁锈或油漆层能以金属腻子刮刀从钢材表面剥离时,均应看成附着不牢5、待检查的钢材表面应与相应的照片进行目视比较。
照片应靠近钢材表面。
评定应在良好散射的日光下或在照度相当的人工照明条件下进行。
6、预处理时的漆膜厚度及涂料选择如下:a)漆膜(干膜)厚度:15~25μm。
b)涂料品种:无机硅酸锌(车间)底漆、环氧底漆、环氧富锌底漆、磷酸锌底漆、铁红环氧脂底漆等。
c)所用的底漆必须是产品配套漆系中的品种或与配套漆系中的底漆相适应的漆种。
二、技术要求1、涂装前,必须达到规定的除锈等级标准后,才允许涂装。
2、在轻度腐蚀的环境中,准备涂刷常规涂料时,其表面除锈等级标准为Sa2级。
3、受化工大气腐蚀、海水侵蚀、高温氧化以及无机富锌涂料为底漆时,表面除锈等级标准为Sa21/2级。
4、涂漆前钢材表面粗糙度必须控制,除了控制喷射磨料的角度和速度外,循环使用的磨料其丸粒的直径不得大于1.2mm。
qj813a-1996涂装通用技术条件
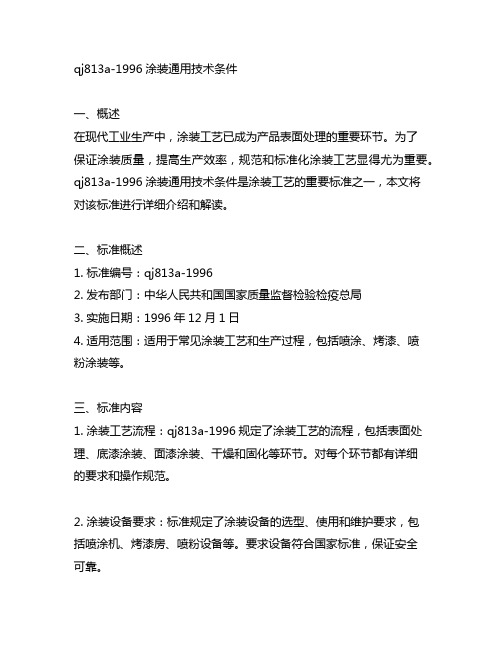
qj813a-1996涂装通用技术条件一、概述在现代工业生产中,涂装工艺已成为产品表面处理的重要环节。
为了保证涂装质量,提高生产效率,规范和标准化涂装工艺显得尤为重要。
qj813a-1996涂装通用技术条件是涂装工艺的重要标准之一,本文将对该标准进行详细介绍和解读。
二、标准概述1. 标准编号:qj813a-19962. 发布部门:中华人民共和国国家质量监督检验检疫总局3. 实施日期:1996年12月1日4. 适用范围:适用于常见涂装工艺和生产过程,包括喷涂、烤漆、喷粉涂装等。
三、标准内容1. 涂装工艺流程:qj813a-1996规定了涂装工艺的流程,包括表面处理、底漆涂装、面漆涂装、干燥和固化等环节。
对每个环节都有详细的要求和操作规范。
2. 涂装设备要求:标准规定了涂装设备的选型、使用和维护要求,包括喷涂机、烤漆房、喷粉设备等。
要求设备符合国家标准,保证安全可靠。
3. 涂料选用:标准中对涂料的选用有详细的规定,包括涂料的品种、质量要求、储存和使用等。
要求严格控制涂料质量,确保涂装效果和产品质量。
4. 涂装质量检测:qj813a-1996规定了涂装质量的检测方法和标准,包括检测设备的选择、检测指标和标准要求。
要求对涂装效果进行全面、客观的检测,确保产品达到标准要求。
5. 环境保护要求:标准中还包括了涂装过程中的环境保护要求,要求符合国家环保标准,节约能源和减少污染。
6. 安全生产要求:标准明确了涂装过程中的安全生产要求,包括防火、防爆、用电安全等方面,确保生产过程安全可靠。
四、标准意义1. 提高涂装质量:qj813a-1996为涂装工艺提供了标准化的操作规范和质量要求,有利于提高涂装质量,确保产品表面光洁、耐腐蚀。
2. 降低生产成本:标准要求严格控制涂料、设备和能源的消耗,有利于降低涂装生产成本,提高经济效益。
3. 保护环境:标准中包括了涂装过程中的环境保护要求,有利于减少污染排放,保护生态环境。
汽车涂装中的涂装工艺规范和标准
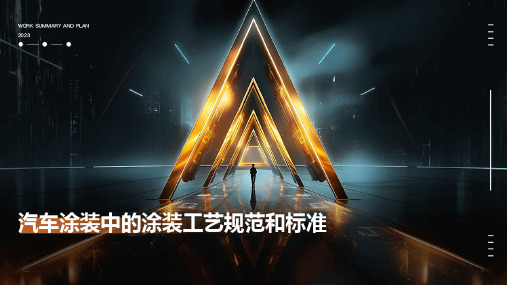
涂装废弃物处理
涂装废弃物应按照国家相关法 律法规进行分类、收集和处理 。
涂装废弃物中含有的有害物质 应进行无害化处理,避免对环 境和人体健康造成危害。
涂装企业应建立废弃物管理制 度,加强废弃物处理和监管, 确保废弃物得到妥善处理。
环保标准与合规性
01
汽车涂装中的涂装工艺应符合国家和地方的环保标准及法规要 求。
汽车涂装中的涂装工艺规范和标准
目录 CONTENTS
• 涂装工艺规范 • 涂装标准 • 质量控制与检验 • 安全与环保 • 培训与提升
01
涂装工艺规范
涂装前处理
表面处理
去除表面的油污、锈迹、氧化皮 等杂质,确保表面清洁干燥,以 便涂料能够均匀附着。
预涂装处理
对表面进行预涂装处理,如打底 、填充等,以提高涂料的附着力 和覆盖力。
。
涂料储存与管理
确保涂料储存环境干燥、阴凉 ,避免混放和污染。
工艺参数控制
严格控制涂料的调配比例、喷 涂压力、喷涂距离等工艺参数
。
涂装后的质量检验
外观检查
检查涂膜表面是否光滑 、平整、无气泡、无杂
质。
色差控制
对比涂膜颜色与标准色 板,确保色差在允许范
围内。
厚度测量
使用测厚仪检测涂膜厚 度,确保符合工艺要求
考核与认证
建立完善的考核和认证体系,确保 涂装工人的技能水平符合要求。
新工艺与新技术的推广
引入先进的涂装工艺和技术
关注行业发展趋势,及时引入新的涂装工艺和技术,提高生产效 率和涂装质量。
培训与指导
对新工艺和技术进行培训和指导,确保涂装工人能够熟练掌握和应 用。
评估与优化
对新工艺和技术的实际效果进行评估和优化,不断完善和提高生产 水平。
钢结构防护涂装通用技术条件

钢结构防护涂装通用技术条件钢结构在建筑、桥梁、船舶等领域中广泛应用,但在使用过程中,由于氧化、腐蚀等原因,建筑物或设备的安全性和可靠性会受到影响。
为了提高钢结构的耐久性和保护性能,通常需要进行涂装防护。
下面提供一份钢结构防护涂装通用技术条件,以供参考:1、涂料选材及性能要求涂料应为合格产品,符合国家相关标准和规定。
其基础材料及添加剂应有一定的体系,保证工程质量和涂层的各项性能。
涂料应具有良好的耐化学腐蚀性、耐紫外线性、耐磨性和耐水性等,在极端环境下不会脱落、开裂和脆化。
2、基础材料表面处理将钢结构表面浸入酸性清洗剂,实现表面脱脂、脱漆和铁锈的去除。
此外,还可以进行喷砂、喷丸、铲除工艺等,使钢表面粗糙,便于涂料附着,提高涂层的附着力。
3、涂装工艺喷涂工艺是常用的涂装方式之一。
在涂装过程中,要确保喷涂机的压力、温度、喷嘴大小等因素合理,以保证涂膜的平整度和稳定性。
在涂装过程中还应做好涂轮,防止漏涂、漏栓和喷雾。
另外,钢结构的尺寸和形状繁多,涂层厚度、涂装顺序也需要根据实际情况来确定。
4、涂料的质量控制涂料的质量控制包括涂层密度、干燥时间、涂装质量检测等。
涂层密度的控制包括干涂厚度和涂料用量的计算;干燥时间的控制包括调节湿度和温度;涂装质量的检测包括涂膜厚度、外观质量、耐腐蚀性等。
在实际生产过程中,还应定期对涂层质量进行检查和测试。
5、安全环保设计施工过程中,应充分考虑防护人员的安全性、施工环境的卫生性,并减少对环境的损害。
使用的材料应符合国家环保要求。
对于有害气体、粉尘和噪音等应及时加强通风、防护和扬尘控制。
总之,钢结构防护涂装技术是重要的建筑、桥梁等基础结构的保养必经之路。
优秀的防护涂装技术,不仅能改变基础结构的外观,也能提高整体耐久性,延长使用寿命,为我们的生活和工作提供更有保障、更可靠的保护。
涂装通用技术条件

涂装通用技术条件1目的和范围:本标准规定了涂装质量检验活动的验收标准,保证产品符合单位工艺,质量要求。
本标准适用于单位自制与采购的外购件/外协件涂装检验。
2要求及检验标准:2.1 涂料使用要求:2.1.1:涂料在使用时,一定要严格按照各种规定涂料的配套稀释剂配制。
2.1.2:各个部位选用的漆种、颜色应按设计要求的执行。
各外协件单位与本单位配套外协产品严格要求使用的统一厂家(批号,批次)品牌涂料。
2.1.3:涂料的质量必须符合本单位的标准或有关工艺规定。
2.1.4 :凡标牌不清、品质不明、包装破损或储存过期的涂料,必须检验符合标准规定后方可使用。
(使用前详细阅读产品使用说明书及操作要求)2.1.5:涂料种类和颜色不得随意混用、代用或错用。
如需代用时需经技术部门的批准。
2.2 工件表面级别分类:2.2.1:A级表面:为零部件的主要表面。
主要以在距离1m的水平范围内环视,部件最显眼的正面来进行确定。
2.2.2:B级表面:为零部件的次表面。
2.1.2:B级表面主要以站在四周或驾驶室内环视,能一眼看到的部件表面(除A级表面外)来进行确定。
2.2.3 :C级表面:为零部件一般表面。
主要以封闭在整机内但在使用和检修时可以看到的地方,以及装成整机后看不到的地方来进行确定。
2.3 前处理2.3.1:所有部件表面在涂漆前应根据相应工艺或具体情况采用手工打磨、喷丸、除油、酸洗、磷化电泳等处理方法把影响涂漆质量的油污、铁锈、氧化皮、型砂、焊渣飞溅、锐边和灰尘等清除干净。
2.3.2:经喷丸处理的零部件,工件表面应达到Sa2.5级,即表面上所有的油脂、污垢、氧化皮锈、腐蚀物、旧漆和其它杂质被清除,允许存在由于清理不彻底而出现的阴影或色差,但至少要有95%的表面一致呈灰白色。
A和B级表面不得有残存氧化皮、型砂、锈迹、焊渣飞溅、锐边等,表面应呈金属本色;C级表面允许残留有不超过表面面积的10%的氧化皮和锈的痕迹,允许残留有少量的不松动的焊渣飞溅,但不得影响装配。
涂装工艺及验收技术标准
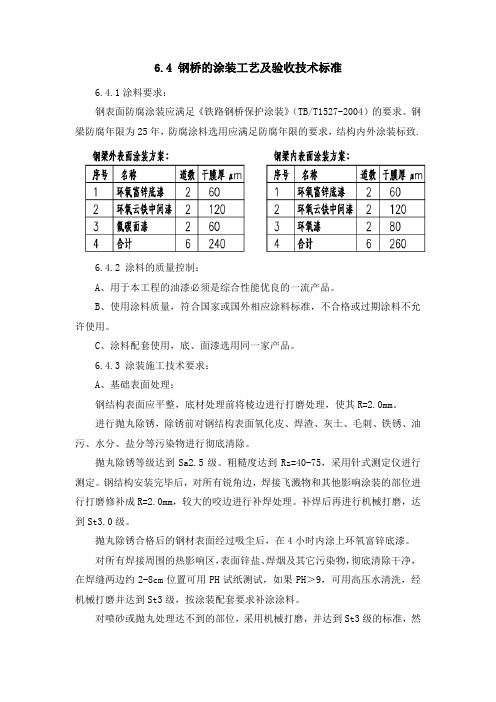
6.4 钢桥的涂装工艺及验收技术标准6.4.1涂料要求:钢表面防腐涂装应满足《铁路钢桥保护涂装》(TB/T1527-2004)的要求。
钢梁防腐年限为25年,防腐涂料选用应满足防腐年限的要求,结构内外涂装标致.6.4.2 涂料的质量控制:A、用于本工程的油漆必须是综合性能优良的一流产品。
B、使用涂料质量,符合国家或国外相应涂料标准,不合格或过期涂料不允许使用。
C、涂料配套使用,底、面漆选用同一家产品。
6.4.3 涂装施工技术要求:A、基础表面处理:钢结构表面应平整,底材处理前将棱边进行打磨处理,使其R=2.0mm。
进行抛丸除锈,除锈前对钢结构表面氧化皮、焊渣、灰土、毛刺、铁锈、油污、水分、盐分等污染物进行彻底清除。
抛丸除锈等级达到Sa2.5级。
粗糙度达到Rz=40-75,采用针式测定仪进行测定。
钢结构安装完毕后,对所有锐角边,焊接飞溅物和其他影响涂装的部位进行打磨修补成R=2.0mm,较大的咬边进行补焊处理。
补焊后再进行机械打磨,达到St3.0级。
抛丸除锈合格后的钢材表面经过吸尘后,在4小时内涂上环氧富锌底漆。
对所有焊接周围的热影响区,表面锌盐、焊烟及其它污染物,彻底清除干净,在焊缝两边约2-8cm位置可用PH试纸测试,如果PH>9,可用高压水清洗,经机械打磨并达到St3级,按涂装配套要求补涂涂料。
对喷砂或抛丸处理达不到的部位,采用机械打磨,并达到St3级的标准,然后按涂装配套要求补涂涂料。
B、涂装工艺:涂装方法:本工程制作安装采取刷涂、滚涂、有气喷涂及高压无气喷涂的多种方法涂装。
每道漆涂装时,先用板刷将边角、缝隙等处涂刷一遍,再采用滚涂或喷涂进行大面积涂撞。
常温下每道漆的涂装间隔时间为24小时。
如果因某些原因没按规定时间涂覆下道漆,并且间隔时间较长时,进行拉毛处理后再进行下道漆涂装。
再进行下道漆前要测定前道漆得干膜厚度,如达不到要求,需要进行补涂。
在整个涂装过程中,所用的各种涂料必须严格按规定的配制比例配漆,使用各自配套的专用稀释剂,配好后的涂料必须在规定时间内用完,否则失效。
常用涂装技术标准
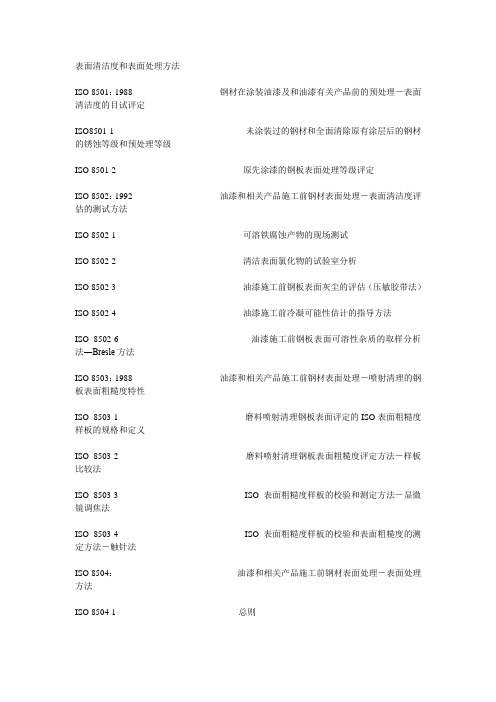
表面清洁度和表面处理方法ISO 8501:1988 钢材在涂装油漆及和油漆有关产品前的预处理-表面清洁度的目试评定ISO8501-1 未涂装过的钢材和全面清除原有涂层后的钢材的锈蚀等级和预处理等级ISO 8501-2 原先涂漆的钢板表面处理等级评定ISO 8502:1992 油漆和相关产品施工前钢材表面处理-表面清洁度评估的测试方法ISO 8502-1 可溶铁腐蚀产物的现场测试ISO 8502-2 清洁表面氯化物的试验室分析ISO 8502-3 油漆施工前钢板表面灰尘的评估(压敏胶带法)ISO 8502-4 油漆施工前冷凝可能性估计的指导方法ISO 8502-6 油漆施工前钢板表面可溶性杂质的取样分析法―Bresle方法ISO 8503:1988 油漆和相关产品施工前钢材表面处理-喷射清理的钢板表面粗糙度特性ISO 8503-1 磨料喷射清理钢板表面评定的ISO表面粗糙度样板的规格和定义ISO 8503-2 磨料喷射清理钢板表面粗糙度评定方法-样板比较法ISO 8503-3 ISO表面粗糙度样板的校验和测定方法-显微镜调焦法ISO 8503-4 ISO表面粗糙度样板的校验和表面粗糙度的测定方法-触针法ISO 8504:油漆和相关产品施工前钢材表面处理-表面处理方法ISO 8504-1 总则ISO 8504-2 磨料喷射清理ISO 8504-3 手工和动力工具清理SSPC SP1-82 溶剂除油SSPC SP2-95 手工除锈SSPC SP3-95 动力工具除锈SSPC SP4-95 火焰除锈SSPC SP5/Nace No.1-2000 出白级喷射SSPC SP6/Nace No.3-2000 工业级喷射SSPC SP7 Nace No.4-2000 清扫级喷射SSPC SP8-82 酸洗法SSPC SP10 Nace No.2-2000 近白级喷射SSPC SP11-87 动力工具打磨到裸露金属SSPC-SP12/NACE NO.5-2002 钢铁和其它硬质材料重涂前的高压和超高压水喷射清理法SSPC-SP13/NACE NO.6-97 混凝土表面处理磨料ISO 11124:1993 油漆和相关产品施工前钢材表面处理-喷射清理金属磨料的规定ISO 11125:1993 油漆和相关产品施工前钢材表面处理-喷射清理金属磨料的测试方法ISO 11126:1993 油漆和相关产品施工前钢材表面处理-喷射清理非金属磨料的规定ISO 11127:1993 油漆和相关产品施工前钢材表面处理-喷射清理非金属磨料的测试方法SSPC SP AB1 Abrasive specification No.1 Mineral and Slag abrasive 磨料规范No.1:矿物磨料和矿渣磨料漆膜厚度ISO 2808:1974 色漆和清漆-漆膜厚度的测定SSPC PA2-96 磁性测厚仪干膜厚度测量法附着力ISO 2409:1972 色漆和清漆-划格法测试ISO 4624:1978 色漆和清漆-附着力拉开法测试ASTM D 3359-87 胶带纸附着力标准测试法漏涂测试ASTM D 5162-01 标准操作规程-金属底材上不传导型保护用涂料的不连续性(漏涂)测试NACE RP 0188-99 标准测试规程-保护用涂料的不连续性(漏涂)测试法无机富锌漆的MEK测试ASTM D 4752-87 无机硅酸富锌漆的耐MEK溶剂擦拭标准测试法涂层的缺陷评定ISO 4628:1982 色漆和清漆-涂层的常见缺陷程度、数量和大小的劣化评定法ISO 4628-1 概要和等级图示ISO 4628-2 起泡程度评定ISO 4628-3 锈蚀程度评定ISO 4628-4 开裂程度评定ISO 4628-5 剥落程度评定ISO 4628-6 粉化程度评定ASTM D610--68 被涂钢板表面的锈蚀程度评定ASTM D659-74 外用涂料的粉化程度评定ASTM D660-44 外用涂料的细裂程度评定ASTM D661-44 外用涂料的开裂程度评定ASTM D662-44 外用涂料的腐蚀程度评定ASTM D714-56 涂料的起泡程度评定ASTM D772-47 外用涂料的剥落程度评定涂装施工SSPC PA3 Guide to Safety and Painting ApplicationSSPC PA1 Shop, Field and Maintenance Painting 车间、现场和维护涂装钢结构的防腐蚀涂料系统保护ISO 12944:1998 色漆和清漆-钢结构防腐蚀涂料系统保护NORSOK M501:1999 表面处理和保护涂层BS5493 Code of practice for protective coating of iron & steel structure.GB8923 涂装钢材表面锈蚀等级和除锈等级(相对国际标准ISO 8501-1:1988)GB6060.5 表面粗糙度比较样板抛(喷)丸、喷砂加工表面(相对国际标准.ISO8503-2 :1995)GB6484 铸钢丸GB6485 铸钢砂GB/T13312 钢铁件涂装前除油程度检验方法(验油试纸法)HG/T 3656 钢结构桥梁漆JB/Z350 高压无气喷涂典型工艺GB1764 漆膜厚度测定法GB/T 5210 涂层附着力的测定法,拉开法GB/T 1771 色漆和清漆耐中性盐雾性能的测定(相对国际标准ISO 7253:1984)GB/T 1865 色漆和清漆人工气候老化和人工辐射曝露(相对国际标准ISO 11341:1994)GB/T1740 漆膜耐湿热测定法GB7692 涂装作业安全规程涂漆前处理工艺安全GB6514 涂装作业安全规程涂漆工艺安全GB/T15957-1995 大气环境腐蚀性分类SYJ0004-1999 钢质管道及储罐防腐蚀工程设计规范SY4058-93 埋地钢质管道外防腐层和保温层现场补伤施工及验收规范SY/T0007-1998 钢质管道及储罐腐蚀控制工程设计规范SY/T0063-99 管道防腐层检漏试验方法SY/T0087-95 钢质管道及储罐腐蚀与防护调查方法标准SY/T0407-1997 涂装前钢材表面预处理规范SY/T0447-96 埋地钢质管道环氧煤沥青防腐层技术标准SY/T4091-1995 滩海石油工程防腐蚀技术规范SYJ30-87 埋地钢质管道及储罐防腐蚀工程基本术语Q/CNPC37-2002 非腐蚀性天然气输送管内壁覆盖层推荐做法GB6950-2001 《石油罐导静电涂料技术指标》GB/T16906-1997 《石油罐导静电涂料电阻率测定法》。
- 1、下载文档前请自行甄别文档内容的完整性,平台不提供额外的编辑、内容补充、找答案等附加服务。
- 2、"仅部分预览"的文档,不可在线预览部分如存在完整性等问题,可反馈申请退款(可完整预览的文档不适用该条件!)。
- 3、如文档侵犯您的权益,请联系客服反馈,我们会尽快为您处理(人工客服工作时间:9:00-18:30)。
精品资料T80涂装通用技术标准重庆劲隆科技(集团)有限公司 发布Q/LJL目次前言............................................................................................................................ I I1 范围 (1)2 规范性引用文件 (1)3 定义 (1)4 涂层的种类 (2)5 检验规则 (2)6 涂层外观质量要求 (3)7 除外观外的品质要求 (4)8 试验方法 (5)9 标志、包装、运输、贮存 (6)前言本标准根据YAMAHA技术规程《涂装》及相关国家标准的有关技术内容编制而成,主要技术内容与其等效。
本标准只规定了摩托车涂装件的主要特性及试验方法,本标准未作规定的其他要求按有关行业标准执行。
与YAMAHA技术规程《涂装》相比,差异如下:1. 加速耐候性试验时间要求稍低,为400小时。
2. 盐雾试验和湿润试验的试验时间要求稍低,为48小时。
3. 因试验手段的因素,本标准只引用了YAMAHA技术规程《涂装》中铅笔硬度、附着力、厚度、镜面光泽度、冲击强度、耐汽油性、耐机油性、盐雾试验、湿润试验、加速耐候性、耐制动液性等项目,其余项目未引用。
本标准由重庆劲隆科技集团提出。
本标准起草单位:重庆劲隆科技集团技术中心。
本标准主要起草人: 郎春波段贵清.本标准从2004年3月20日首次发布。
本标准批准人: 黄昆涂装通用技术标准1 范围本标准对以防腐蚀或装饰为目的,而实施涂装的零部件的涂层的定义,涂层的种类,检验规则、,涂层外观质量要求,除外观外的品质要求,试验方法,标志、包装、运输、贮存。
本标准适用于重庆劲隆科技集团有限公司制造的所有摩托车车型。
本标准不适用于耐热涂料的要求。
2 规范性引用文件下列文件中的条款通过本标准的引用而成为本标准的条款。
凡是注日期的引用文件,其随后所有的修改单(不包括勘误的内容)或修订版均不适用于本标准,然而,鼓励根据本标准达成协议的各方研究是否可使用这些文件的最新版本。
凡是不注日期的引用文件,其最新版本适用于本标准。
YGK-8-501 YAMAHA技术规程《涂装》GB/T 1720-89 漆膜附着力测定法GB/T 1732-93 漆膜耐冲击力测定法GB/T 1865-93 漆膜老化(人工加速)GB/T 1734-93 漆膜耐汽油性测定法GB/T 1734-93 漆膜铅笔硬度GB/T 1743-93 漆膜光泽度测定法GB/T 1743-93 漆膜耐候性GB/T 1764-93 漆膜厚度测定法GB/T 1771-93 漆膜耐盐雾测定法GB/T 1764-93 钢铁工件涂漆前磷化处理条件3 定义本标准中使用的主要用语的定义如下:1)涂层涂上的涂料,由于溶剂的挥发、蒸发及涂层形成要素的氧化、聚合、缩合反应而形成的固体被膜。
2)外装从周围及使用状态下,能够直接看到的零件。
3)内装从周围及使用状态下,不能够直接看到的零件。
4)露底漏涂或未能完全覆盖前道涂层而显材料色泽的现象。
5)起泡涂层表面呈现鼓包的现象。
6)脱落涂层从涂面呈现片状脱离现象。
7)锈痕涂层中产生锈点或接缝处呈现锈斑的现象。
8)裂纹涂层表面呈现不规则,深浅不同的断裂纹的现象。
9)麻点涂层表面因水、油等异物影响致使涂料不能均匀附着,产生抽缩形式的泡疤而呈凹坑的现象。
10)流痕喷涂在垂直面上的涂料向下流动,使漆面产生条痕的现象,严重时称为流挂。
11)颗粒涂层附着颗粒状物质的现象。
12)起皱涂层表面呈现凹凸不平且无规则折皱的现象。
13)桔皮涂层表面呈现桔皮状纹路的现象。
14)针孔涂层表面呈现针孔小孔或毛孔的现象。
4 涂层的种类4.1 涂层的种类按涂装面的材质及用途,分为铁系列、铝系列(包括锌、镁)、塑料系列,见表1、表2和表3的规定。
表1 被涂面为铁系列表2 被涂面为铝系列表3 被涂面为塑料材料系列4.2 表示符号涂层的表示符号,参见下例:示例JL125侧盖的涂装要求为P1。
5 检验规则5.1 判定部门及人员5.1.1 判定部门为公司品质部。
5.1.2 检验人员必须满足下列条件,具有正常识别颜色能力,两眼视力在0.7以上。
5.2 判定场所环境:使用荧光灯的照度必须在300Lx以上,判定色调时,原则上采用扩散昼光。
5.3 判定方法外观的判定原则是在成车状态下进行判定时,应按表4的规定。
表4 外观判定的原则在成车状态下,按显著易见度等级划分为AA,A,B,C四级。
1)AA级保护装饰面:成车状态下暴露面(特殊要求)。
2)A级保护装饰面:成车状态下站在周围50cm处能直视的范围。
3)B级保护装饰面:成车状态下站在周围50cm处不易观察的范围。
4)C级保护装饰面:成车状态下不可视面。
5.5 摩托车涂装件所用涂料应按技术文件规定的品牌、型号、名称执行,漆膜颜色应符合劲隆公司确认的上、下限色板要求。
6 涂层外观质量要求AA级、A级、B级保护装饰面要求外观平整光滑,光泽鲜艳一致。
C级保护装饰面以防锈为主,不要求修饰的表面。
具体要求见表定5的规定。
表5 外观检验标准7 除外观外的品质要求涂层除外观外的品质按照表8的规定项进行试验时,必须满足表6、表7的规格,如必须的品质要求在此项中没有规定,由当事者协商决定。
表6 被涂面为铁系列1)耐盐雾试验的无异常指的是单边涂层脱落宽度≤3mm,双边涂层脱落宽度≤6mm,其余区域内无脱落、变色、起泡、开裂,不得有明显的失光和软化。
2)以上要求中其余无异常指的是:涂层不得有脱落、变色、起泡、开裂,不得有明显的失光和软化。
表7 被涂装面为铝合金系列1)盐雾试验的无异常指的是单边涂层脱落宽度≤3mm,双边涂层脱落宽度≤6mm,其余区域内无脱落、变色、起泡、开裂,不得有明显的失光和软化。
2)以上要求中其余无异常指的是:涂层不得有脱落、变色、起泡、开裂,不得有明显的失光和软化。
表8 被涂面为塑料材料系列8 试验方法8.1 涂层颜色用涂装件与上、下限色板对比目测。
将标准板的1/4重叠于部件,在天然散射光线下检查,眼与样板距离30—45cm,呈120—140度角。
8.2 涂层外观以目测或触感,目测时实验人员应定于被测部位0.5m处。
8.3 涂层附着力按GB/T 1720规定网格法进行。
先在涂层上划11道相互平行的,间距可为1mm(单层漆)和2mm (多层漆)切痕,然后再垂直切割与前者切割道数及间距相同的切痕。
切割时,单刃刀尾刃口与涂面呈30度夹角,用力均匀,速度平稳无颤动。
刃口切割正好能穿透涂层触及底材。
然后在其上粘贴宽24mm,粘附力每10mm大于2.94N的透明胶,粘贴长度约50mm.用橡皮查擦使胶带完全粘贴在涂层上半分钟后,手持胶带一端与涂面垂直迅速将胶带撕下。
检查方格内涂层或前一道涂层的分离情况。
8.4 涂层硬度用中华牌高级绘图铅笔测试,采用HB铅笔刻划漆层,漆膜上不得有凹痕。
,要求铅笔笔心直径1.8mm以上,露出长度3mm左右,笔尖圆平。
检验时用手握住铅笔,铅笔与被检涂层表面保持45度角,推进速度1mm/s。
推力要保持均匀,用力以不折断铅芯为限。
推进方向按图1。
在被检部位刻划出5条平行线后,用橡皮将铅笔灰擦去,以目测检验漆膜划痕的深浅及明显程度,若涂层表面有凹痕,则涂层硬度不合格。
图1 涂层硬度测试示意图8.5 涂层厚度按GB/T 1764-89漆膜厚度测定法检验。
8.6 涂层光泽度按GB/T 1743-93漆膜光泽度测定法检验,角度按60º检验。
8.7 冲击强度按GB/T1732-93冲击强度测定法检验。
8.8 耐汽油性检验将试验件浸入90#汽油中,在20±2℃条件下放置8小时,取出,室温放置1小时,观察外观的变化。
8.9 耐机油性将试验件浸入发动机用机油中,在20±2℃条件下放置2小时,取出,室温放置1小时,观察外观的变化。
8.10 耐盐雾试验性漆膜进行耐盐雾试验时,将试验件从离有效面的焊接部、孔部、端部5mm以上的地方,用刀片交叉切,刻痕至底材,放入盐雾试验箱中,保持温度在35±1℃,喷雾收集液的PH值保持在6.5~7.5,试验时间为48小时。
试验结束后,用流动水清洗,室温放置2小时。
将宽24mm的粘胶带完全粘在交叉切纹上,立即将胶带的一端从垂直于涂装面的方向瞬间剥离,测量沿交叉纹路脱落的涂层宽度。
8.11 耐湿润性漆膜进行耐湿润试验时,将试验件放入湿润试验箱中,保持温度在50±2℃,保持湿度在98±2%,试验时间为48小时。
试验结束后,用流动水清洗,室温放置2小时。
8.12 加速耐候性漆膜进行耐候性试验时,将试验件放入光老化试验箱中,试验时间按表6、表7和表8的要求。
试验结束后,室温放置2小时。
9 标志、包装、运输、贮存9.1 标志每批产品标明制造厂名、产品名称、产品规格或型号、检验员章。
9.2 包装产品可用纸箱或塑料袋包装,或按用户要求包装。
9.3 运输和贮存在运输和贮存时严禁烟火,防止雨、雪、水。
贮存应放在干燥通风处,不宜露天长期暴晒,远离热源,不能与化学品接触。