降低组件破片率改善计划
层压破片改善1

电池片前 后有锡珠 来料不良 电池片翘曲度大
TPT开孔时 按压电池片 层压前换片 等造成破片
叠层拎起电 池片检查 裁剪互连条 时产生震动 叠层转移电池 串使用手工
Material
1.
Method
裁减的汇流条弯曲,叠层焊接后变成弓形,再经过层压导致破片 2. TPT开孔时,手压住TPT并按在电池片上,容易破片 3. 叠层员工拎起电池串检查异物时,可能导致破片 4. 叠层员工将电池串由模板转移到叠层台时 ,使用手工拎电池串, 两端电池片受力较大,容易破片 5. 裁减互连条时产生的震动可能导致破片
Step / Time
WK 17
WK 18
1. 组织团队
2. 现状调查和分析并设定目标
3. 分析原因并确定主要原因 4. 制定对策 5. 按对策实施 6. 检查效果并回顾 7. 制定巩固措施 8. 标准化
Actual
Plan
Scheduled progress = % ; Ahead / Behind schedule = %
90.00%
80.00% 38 70.00% 60.00%
40
统计时间:
总计 不良比例
08.1.1— 08.3.31 二组件层压工序
30
50.00% 40.00%
地点:
20
17 9 6 6 6 6 3 2 2 0 5
统计人:
李战波
30.00% 20.00% 10.00% 0.00%
10
0 12 1 10 6 8 9 11 3 2 4 7
团队组长 Team Leader
团队指导员 facilitator
王益平 Wang yi ping
编号 No. 1
聚光光伏组件效率降低在生产侧的原因分析及解决方法

聚光光伏组件效率降低在生产侧的原因分析及解决方法随着太阳能光伏市场的竞争越来越激烈,太阳能光伏组件的质量成为了制约光伏产业发展的瓶颈之一。
其中,聚光光伏组件的效率降低已成为行业关注的问题之一。
本文将从生产侧的角度分析聚光光伏组件效率降低的原因,并提出相应的解决方法。
1. 光学设计方面聚光光伏组件的光学设计是关键因素之一,其直接影响其效率。
若设计不合理,则容易导致组件漏光、反射、散光等现象,导致组件效率降低。
2. 硅芯片材料质量不佳硅芯片是光伏组件的核心部件,若硅芯片质量不合格,则其效果必然不佳。
同时,硅芯片加工过程中也容易出现污染或损伤的情况,而这些都会导致组件效率降低。
3. 接线和封装不当聚光光伏组件的接线和封装也对组件效率产生直接影响。
若接线不当、接触不良,则会导致电流流失,而封装不当则容易使组件散热不良,在较高温度下工作也会导致能量损失。
解决方法加强聚光光伏组件的光学设计,提高组件的质量和效率。
通过优化反射率、透明度,减少组件的漏光,确保组件的最大光吸收。
同时,通过对传输光线的对称性、光线亮度等细节部分进行调整,更好地提升组件的利用效率。
选用优质的硅芯片材料,加工过程中确保硅芯片不受到污染和损伤,提高其转换效率。
同时,在组件的选材和生产过程中严格控制热膨胀系数,使得组件在工作中能够更好地承受温度变化和其他外力影响。
针对接线和封装过程中存在的问题,可以进行相应的优化。
在接线方面,要提高接触的精度和质量,严格保证接触不松动,避免电流流失。
在封装方面,则需要针对组件的散热问题,更好地解决组件在高温下工作时的散热问题,防止组件产生热解现象。
总之,聚光光伏组件效率降低是多方面因素造成的问题,而想要提升组件效率,需要全面进行优化和改进。
通过切实的技术改进和创新,可以更好地解决目前存在的问题,进一步推动光伏产业的发展。
太阳能组件计量tqm改善案例

太阳能组件的TQM(全面质量管理)改善案例一、背景介绍随着全球对可再生能源的需求不断增长,太阳能行业在近年来得到了快速发展。
然而,太阳能组件的制造过程中存在一些质量问题,如电池片破损、组件效率低下等,这些问题不仅影响了产品的性能,还增加了生产成本。
因此,为了提高产品质量、降低生产成本,我们实施了TQM改善方案。
二、问题分析经过调查和分析,我们发现主要存在以下问题:1. 电池片破损率高:由于生产过程中的操作不当或设备故障,导致电池片容易破损。
2. 组件效率不达标:部分组件的效率低于设计要求,影响了客户的使用效果。
3. 生产成本高:由于质量问题导致的返工、报废等,增加了生产成本。
三、改善方案针对以上问题,我们制定了以下改善方案:1. 加强员工培训:提高员工的质量意识和操作技能,确保他们能够按照标准操作规程进行生产。
2. 设备维护与检查:定期对设备进行维护和检查,确保设备的正常运行,减少故障率。
3. 引入自动化生产线:通过引入自动化生产线,减少人工操作环节,降低人为因素导致的问题。
4. 质量检测与控制:加强质量检测和控制,对每个生产环节进行严格把关,确保产品符合质量要求。
5. 持续改进:根据生产数据和客户反馈,持续改进生产工艺和流程,提高产品质量和降低生产成本。
四、实施过程在实施过程中,我们采取了以下措施:1. 制定详细的实施计划:明确改善方案的目标、时间表和责任人,确保计划的顺利实施。
2. 成立专项小组:成立由各部门人员组成的专项小组,负责方案的推进和实施。
3. 数据监测与记录:对每个生产环节的数据进行监测和记录,以便对生产过程进行实时监控和调整。
4. 定期评估与反馈:定期对改善方案的实施情况进行评估和反馈,及时发现问题并采取措施解决。
5. 持续改进:根据评估结果和生产数据,持续改进生产工艺和流程,提高产品质量和降低生产成本。
五、效果评估经过一段时间的实施,我们取得了以下成果:1. 电池片破损率下降:通过加强员工培训和设备维护,电池片破损率大幅下降。
组件生产改善措施方案

组件生产改善措施方案组件生产是指在产品制造过程中,将不同的零部件组装成完整的产品的过程。
在组件生产过程中,如果能够采取一些改善措施,可以提高生产效率,降低成本,提高产品质量。
以下是一些可能的改善措施方案:1. 优化工艺流程:通过对工艺流程进行优化,可以提高生产效率和质量。
可以对每个步骤进行细致的分析,找出影响生产效率和质量的关键环节,并寻找改进方法。
2. 自动化生产:引入自动化设备和机器人,可以提高生产效率和质量。
通过自动化生产,可以减少人为错误和损失,同时提高生产的稳定性和一致性。
3. 优化物料管理:采取合理的物料管理措施,可以降低生产成本和浪费。
可以通过合理的物料采购和仓储管理,减少库存过剩和物料损耗。
4. 建立质量控制体系:建立完善的质量控制体系,可以提高产品质量并降低次品率。
可以采取各种质量控制手段,如质量检测和质量反馈机制,及时发现和解决质量问题。
5. 实施员工培训:通过对员工进行培训和教育,可以提高他们的技能水平和工作效率。
可以定期组织技术培训和操作规程培训,以提高员工的专业知识和操作能力。
6. 引进先进设备和技术:引进先进的设备和技术,可以提高生产效率和产品质量。
可以通过引进自动化设备、新工艺和新材料等方式,提高生产的技术水平和竞争力。
7. 持续改进和创新:通过持续改进和创新,可以不断提高生产效率和产品质量。
可以建立改进和创新的机制,鼓励员工提出改进建议,并及时评估和实施这些改进措施。
综上所述,通过优化工艺流程,自动化生产,优化物料管理,建立质量控制体系,实施员工培训,引进先进设备和技术,以及持续改进和创新,可以提高组件生产的效率和质量,降低成本,提高产品竞争力。
这些改善措施需要全面考虑组件生产的各个环节,并与员工、供应商等相关方紧密配合,才能取得最佳效果。
如何有效控制组件生产过程中的碎片现象

如何控制组件制造中的电池片破片与隐裂电池片作为光伏组件最重要的原材料之一,在光伏组件系统应用中起着十分重要的作用。
近年来由于硅材料的短缺及电池片厂商生产成本的逐渐降低,电池片厚度由2005年的220-270μm减薄到目前的170-190μm,其发展趋势还有可能更薄。
因此,如何应对电池片破片及隐裂所带来的制造成本的增加,如何有效控制各道工序破片、隐裂片的产生是当前最值得组件制造厂商思索的问题。
本文从组件制造过程中易产生破片及隐裂的工序对电池片的破片与隐裂的产生及预防措施进行分析讲解。
一、分选工序分选工序是第一道接触电池片的工序,其中的每个细小环节都对电池片产生直接的影响。
1、开箱后的拆包从库房领取电池片后需对电池片进行拆包,拆包时要注意刀片划开封装膜的方向与位置,不可划到电池片的侧面,在保护垫的上方划开相对安全,不容易造成电池片破碎或受伤(如图1)。
图1 图22、电性能测试拆包后的电池片在进行电性能测试时(如图2所示)容易产生破片与隐裂,测试仪测试平台上需保持干净无异物,当探针下降的过程中不会因为电池片下面有异物而压碎电池片,另外要定期对测试仪探针的灵活程度进行检查,部分探针上下收缩不灵活时直接压在电池片上会使栅线位置出现隐裂,严重的直接导致电池片沿栅线位置破碎。
在放取电池片时不可撞到四周的测试挡块,撞击挡块易造成电池片崩边、缺角。
3、周转盒保护措施分选完的电池片需要放到指定的周转盒中流到下道工序,周转盒四周的保护措施(如图3所示)显得相对重要,可以对电池片起到缓冲保护的作用,避免直接与周转盒接触造成崩边、缺角等现象。
图3 图44、周转车周转电池片在用周转车转运到单焊工序时,周转车的轮子的减震是关键,效果好的减震可以避免电池片在周转车中颠簸而造成电池片碎片及隐裂。
(如图4所示)二、焊接工序焊接工序是整个组件制造中的较为关键的工序,焊接质量的优、劣直接决定组件质量的优、劣,同时焊接工序也是最容易产生电池片的破片与隐裂的工序。
组件调节工作实施方案

组件调节工作实施方案一、背景介绍。
随着科技的发展和社会的进步,各种设备和机械的组件调节工作变得日益重要。
组件调节工作是指对机械设备中的各种组件进行调整和优化,以确保设备的正常运行和性能的稳定。
在现代工业生产中,各种设备和机械的组件调节工作不仅关乎设备的稳定性和效率,更关乎生产线的顺畅运行和产品质量的稳定性。
因此,制定一套科学合理的组件调节工作实施方案对于提高生产效率和保障产品质量具有重要意义。
二、目标和意义。
1. 目标,制定一套科学合理的组件调节工作实施方案,以确保设备的正常运行和性能的稳定。
2. 意义,组件调节工作实施方案的制定对于提高生产效率、保障产品质量、降低生产成本具有重要意义,同时也有利于提高设备的使用寿命和降低维护成本。
三、实施步骤。
1. 调研分析,首先需要对设备的各个组件进行全面的调研分析,了解各个组件的结构和性能特点,找出存在的问题和改进的空间。
2. 制定方案,根据调研分析的结果,制定针对性的组件调节工作实施方案,明确调节的目标和方法,确保调节工作的科学性和有效性。
3. 实施调节,按照制定的方案,对设备的各个组件进行调节和优化,确保调节工作的顺利进行和效果的达到。
4. 测试验证,在调节工作完成后,需要对设备进行全面的测试验证,确保设备的性能和稳定性达到预期目标。
5. 完善改进,根据测试验证的结果,对调节工作进行完善改进,确保设备的性能和稳定性达到最佳状态。
四、注意事项。
1. 安全第一,在进行组件调节工作时,必须严格遵守相关的安全操作规程,确保人员和设备的安全。
2. 专业人员,组件调节工作需要由具有相关专业知识和经验的人员进行,确保调节工作的科学性和有效性。
3. 设备保养,组件调节工作完成后,需要加强设备的日常保养和维护工作,确保设备的稳定性和使用寿命。
五、总结。
制定一套科学合理的组件调节工作实施方案对于提高生产效率和保障产品质量具有重要意义。
只有通过科学合理的调节工作,才能确保设备的正常运行和性能的稳定,提高生产效率和降低生产成本。
组件产线不良及改善措施分析报告
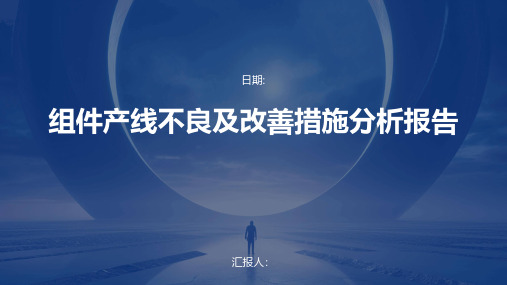
contents •引言•产线不良情况概述•原因分析•改善措施制定•实施改善措施及效果验证•总结与展望•参考文献目录分析组件产线的不良状况,找出问题所在,提出改善措施,以提高生产效率和产品质量。
背景在生产过程中,组件产线经常会出现各种不良问题,如质量问题、效率问题、设备问题等,这些问题会导致生产成本增加、交货期延误、客户满意度下降等负面影响。
因此,对组件产线进行不良分析,采取有效改善措施,对提高生产效率和产品质量具有重要意义。
目的报告的目的和背景VS范围方法报告的范围和方法总结词:严重详细描述:本月产线不良情况严重,总不良率达到20%,比上月不良率15%上升了5个百分点。
本月产线不良情况总览各工序不良情况分析总结词:分散详细描述:各工序均有不良情况,且分布较为分散,无明显集中趋势。
主要问题包括零部件质量不达标、操作人员技能不足、设备故障等。
操作人员疏忽人员疲劳或缺乏休息操作人员技能不足人员因素导致的质量问题03设备与生产需求不匹配01设备老化或故障02设备维护不当材料质量不达标01材料存储不当02材料供应不稳定03工艺流程不合理工艺参数不合适工艺方法缺乏验证01020304人员培训人员考核人员招聘人员激励设备维护设备采购设备改进设备更新材料质量把关规范材料存储方法,避免材料受潮、变质等问题。
材料存储材料运输材料替代01020403针对不良材料进行替代,提高产品质量和稳定性。
严格把关材料质量,确保进料质量符合要求。
确保材料运输安全、稳定,避免运输过程中出现损坏等问题。
工艺流程优化工艺参数调整工艺方法研究工艺纪律管理针对工艺方法因素的改善措施人员培训与考核总结词详细描述总结词详细描述设备维护与保养材料质量把控与更换总结词详细描述工艺方法优化与实施总结词详细描述301 02 03优化组装工艺流程,加强操作培训和过程监控。
完善检测手段,引入先进的检测设备和技术,提高检测效率和准确性。
仍需努力的方向与展望010*******参考文献010203。
2014年3月破片专案分析

破片分析
制程破片情况
以上图片可以看出,本月破片主要集中在ITO和BM这两道制程: BM制程破片仍然为TP2线后烘烤以及下料机裂片破片,目前针对 此破片,仍在需求更好的解决方案。 ITO制程方面的破片,从上表来看,主要来源于G3.0的破片压力。 G3.0生产订单增加,且主要都为双面ITO制程的玻璃,经过的工序较多, 来料非化强以及人工取放片等等因素导致破片明显上升,控制此类破 片将是本月重点改善项目。
法
:生产工序多,大部分都是双面
改善措施
1.对G3.0所有涉及到人工取、放片的机台周 边进行撞击防护,粘附泡棉,减缓撞击力度, 防止崩角破片。
2.针对崩角较多的线别(尤其脱膜段),由各线负责人每周进行一次周 保养;彻底检查机台内部各机构,重点查找崩角碎片,针对确认碎片 位置来重点进行改善。
改善措施
破片专案分析报告
戈亚东 2014/3/29
目录
破片现状
破片分析
改善措施 下月计划
破片现状
当月设备破片数及破片率
3月份设备共计破片417片,比2月份破片数增加一倍:其中G2.5破 片194片,G3.0破片223片。3月份破片明显上升,一方面为产能较多, 车间几乎满产;另一方面TP2线生产BM制程时后烘烤破片情况,一直 没有能得到有效控制,破片量很大。 综合上月总产能(11条线),计算机台破片率为0.54‰;
人
:人为取放片,稍有不注
意就会磕碰到机台拐角上,导致 细小崩角或暗裂。
紧,边导轮爬坡, 烤炉板顶PIN凹 痕, 破 片分析
料
:来料玻璃
本身非化强(如 79A1、78A2), 自身硬度不够,经 过机台侯易造成崩 角。
ITO结构,甚至双面Metal结构,经过的机 台多以及反复烘烤冷却,易造成玻璃裂片
组件前道降低电池片碎片率的方法

组件前道降低电池片碎片率的方法电池片的碎片率对于光伏组件的性能和寿命具有重要影响。
组件前道的质量控制和处理是降低电池片碎片率的有效手段。
以下是10条关于组件前道降低电池片碎片率的方法:1. 挑选较为均匀的硅片:电池片的碎片率与硅片质量、厚度、表面性质有关。
挑选硅片时需要选择表面平整度好、厚度均匀的硅片,并控制硅片厚度偏差在±20um以内。
2. 设计合理的切割工艺:切割过程可能会导致电池片断裂或受损,因此需要设计合理的切割工艺,确保硅片不会产生裂纹或割伤。
3. 控制切割时的力度:控制切割时的力度能够减少电池片的碎片率。
在切割幅度和频率相同的情况下,降低切割压力可使碎片率降低。
4. 防止硅片表面受污染:硅片表面的污染会对电池片性能产生影响,导致碎片率提高。
因此需要在组件前道时防止硅片表面受到污染。
5. 切割前清洁硅片表面:清洁硅片表面可以有效降低电池片碎片率。
使用合适的清洗工艺可以去除硅片表面的污染和松散物,确保切割时硅片不受损害。
6. 优化加工工艺:优化加工工艺可以提高组件前道的生产效率和稳定性。
采用合适的加工工艺,能够减少电池片的碎片率并保证组件性能。
7. 精细化管理生产环节:严格管理每个生产环节,确保每个加工工艺都符合要求,可有效降低电池片的碎片率和组件的缺陷率。
8. 采用高精度设备:采用高精度设备可以提高生产效率和稳定性,同时可以减少碎片率和缺陷率。
比如使用高精度的切割机、光刻机等设备。
9. 加强人员培训:组件前道操作人员的技能和经验对于电池片碎片率和组件性能具有重要影响。
加强人员培训,提高操作技能,能够减少电池片的碎片率和缺陷率。
10. 引进先进技术:引进先进的技术可以提高生产效率和组件性能,同时可以减少电池片的碎片率。
比如使用高效的太阳能电池切割机、晶圆清洗机、显微镜等。
以上是关于组件前道降低电池片碎片率的10条方法。
对于每一个方法,都需要详细地制定操作流程和质量标准,严格按照标准执行,以降低电池片的碎片率和组件的缺陷率。
组件生产改善措施方案

组件生产改善措施方案1. 提高工人培训水平:组织定期的培训课程,提升工人的技术水平和操作能力。
培训内容可包括组件生产流程、工艺要求、质量控制等方面的知识和技能培养。
2. 引进先进的设备和技术:定期考察市场并引进先进的组件生产设备和技术,提高生产效率和产品质量。
同时,对现有设备进行维护保养,确保其正常运行。
3. 设立质量监控岗位:专门设置质量监控岗位,对组件生产过程进行全程监控,确保每个环节的质量符合标准要求。
如果发现质量问题,及时采取纠正措施,防止次品产生。
4. 建立完善的质量管理体系:建立质量管理文件和流程,明确每个环节的责任和要求。
设置质量指标,进行定期的质量评估和数据分析,及时发现问题和改进方案。
5. 强化供应商管理:建立供应商评估机制,对供应商的产品质量和交货周期进行评估和监控。
与供应商建立长期合作关系,并进行技术交流和合作,提高整体供应链的质量水平。
6. 提升工艺流程和效率:优化组件生产的工艺流程,减少不必要的环节和中间环节,提高生产效率。
同时,进行生产线布局的优化,减少物料搬运时间和人工操作时间。
7. 加强质量意识培养:组织员工参与质量改进活动,激发员工对质量的责任感和主动性。
定期开展质量分享会议,宣传质量管理的重要性,培养全员参与质量管理的意识。
8. 建立追溯体系:建立组件生产的追溯体系,确保能够对每一批次的产品进行追踪。
当出现质量问题时,能够准确定位问题原因,采取相应的改进措施。
9. 加强与客户沟通:与客户保持及时的沟通和反馈,了解其需求和反馈意见。
根据客户的反馈,及时调整和改进组件生产的方案,提供更好的产品和服务。
10. 不断优化改进:持续监控和评估组件生产过程的质量和效率,及时发现问题并采取改进措施。
通过不断优化改进,提升组件生产的质量水平和竞争力。
有效降低实验电气设备及元件损坏率的措施和方法
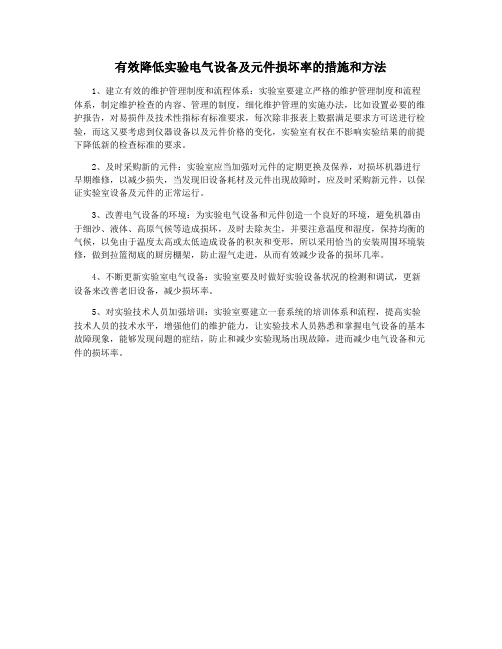
有效降低实验电气设备及元件损坏率的措施和方法
1、建立有效的维护管理制度和流程体系:实验室要建立严格的维护管理制度和流程体系,制定维护检查的内容、管理的制度,细化维护管理的实施办法,比如设置必要的维护报告,对易损件及技术性指标有标准要求,每次除非报表上数据满足要求方可送进行检验,而这又要考虑到仪器设备以及元件价格的变化,实验室有权在不影响实验结果的前提下降低新的检查标准的要求。
2、及时采购新的元件:实验室应当加强对元件的定期更换及保养,对损坏机器进行早期维修,以减少损失,当发现旧设备耗材及元件出现故障时,应及时采购新元件,以保证实验室设备及元件的正常运行。
3、改善电气设备的环境:为实验电气设备和元件创造一个良好的环境,避免机器由于细沙、液体、高原气候等造成损坏,及时去除灰尘,并要注意温度和湿度,保持均衡的气候,以免由于温度太高或太低造成设备的积灰和变形,所以采用恰当的安装周围环境装修,做到拉篮彻底的厨房棚架,防止湿气走进,从而有效减少设备的损坏几率。
4、不断更新实验室电气设备:实验室要及时做好实验设备状况的检测和调试,更新设备来改善老旧设备,减少损坏率。
5、对实验技术人员加强培训:实验室要建立一套系统的培训体系和流程,提高实验技术人员的技术水平,增强他们的维护能力,让实验技术人员熟悉和掌握电气设备的基本故障现象,能够发现问题的症结,防止和减少实验现场出现故障,进而减少电气设备和元件的损坏率。
层压简介
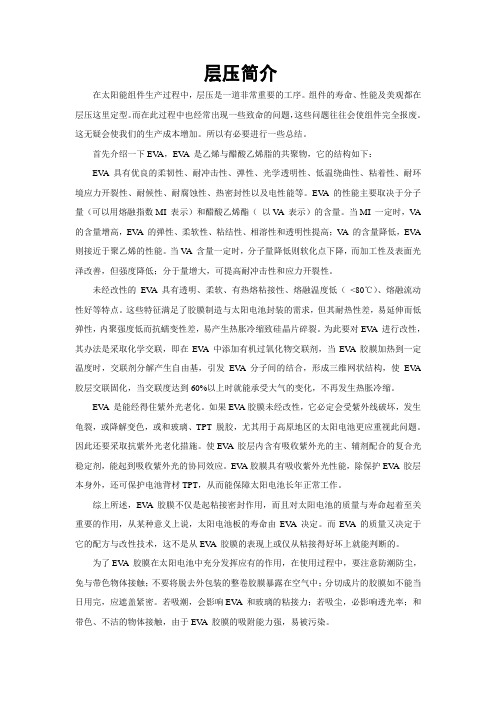
层压简介在太阳能组件生产过程中,层压是一道非常重要的工序。
组件的寿命、性能及美观都在层压这里定型。
而在此过程中也经常出现一些致命的问题,这些问题往往会使组件完全报废。
这无疑会使我们的生产成本增加。
所以有必要进行一些总结。
首先介绍一下EV A,EV A 是乙烯与醋酸乙烯脂的共聚物,它的结构如下:EV A 具有优良的柔韧性、耐冲击性、弹性、光学透明性、低温绕曲性、粘着性、耐环境应力开裂性、耐候性、耐腐蚀性、热密封性以及电性能等。
EV A 的性能主要取决于分子量(可以用熔融指数MI 表示)和醋酸乙烯酯(以V A 表示)的含量。
当MI 一定时,V A 的含量增高,EV A 的弹性、柔软性、粘结性、相溶性和透明性提高;V A 的含量降低,EV A 则接近于聚乙烯的性能。
当V A 含量一定时,分子量降低则软化点下降,而加工性及表面光泽改善,但强度降低;分于量增大,可提高耐冲击性和应力开裂性。
未经改性的EV A 具有透明、柔软、有热熔粘接性、熔融温度低(<80℃)、熔融流动性好等特点。
这些特征满足了胶膜制造与太阳电池封装的需求,但其耐热性差,易延伸而低弹性,内聚强度低而抗蠕变性差,易产生热胀冷缩致硅晶片碎裂。
为此要对EV A 进行改性,其办法是采取化学交联,即在EV A 中添加有机过氧化物交联剂,当EV A 胶膜加热到一定温度时,交联剂分解产生自由基,引发EV A 分子间的结合,形成三维网状结构,使EV A 胶层交联固化,当交联度达到60%以上时就能承受大气的变化,不再发生热胀冷缩。
EV A 是能经得住紫外光老化。
如果EV A胶膜未经改性,它必定会受紫外线破坏,发生龟裂,或降解变色,或和玻璃、TPT 脱胶,尤其用于高原地区的太阳电池更应重视此问题。
因此还要采取抗紫外光老化措施。
使EV A 胶层内含有吸收紫外光的主、辅剂配合的复合光稳定剂,能起到吸收紫外光的协同效应。
EV A胶膜具有吸收紫外光性能,除保护EV A 胶层本身外,还可保护电池背材TPT,从而能保障太阳电池长年正常工作。
降低组件破片率改善计划PPT课件

3. 检验手法 (光电/组件)
员工数片/检 验手法是否规
范统一?
检验人员是否 均考核合格?
2. 运输方式
打包托盘的层 数规定是否符
合要求?
托盘上下车卸 货是否符合要
求?
4.检验漏失
厂内检验漏失 率过高?
厂内缺角返工 率过高? 7
对策及实施的策划一
序Hale Waihona Puke 项目对策实施方案负责人
副组长
组内分工
负责组织/策划本次改善活动,并监督各 组员工作进度 负责整个项目的开展并协调组件相关事 宜
副组长
负责制造相关对策的开展与监督执行
副组长
组员 组员 组员 组员
负责技术支持与协助 负责品管相关对策的开展执行与其他部 门改善对策的实施追踪 负责制造相关对策的制定与实施 负责与客户端相应沟通协调事宜
品管 销售
2012.01
4
检验漏失率的 降低
成立内部专案改善
/
品管 销售
2012.01
5
缺角/隐裂返工 率的降低
成立内部专案改善
/
制造 品管
2012.01
硅片原材料的
6 改善(如氧碳含 成立内部改善专案
/
量改善)
工艺 品管
20192.01
10
0.30% 0.28% 0.25% 0.25% 0.23% 0.20% 0.20% 0.18% 0.15% 0.15% 0.15% 0.12%
P
选定主题
设定目标
现状分析
原因分析
D
提出对策
对策实施
C
效果验证
A
标准化
计划进度:
聚光光伏组件效率降低在生产侧的原因分析及解决方法

聚光光伏组件效率降低在生产侧的原因分析及解决方法1. 设计不合理聚光光伏组件的设计不合理是导致效率降低的主要原因之一。
在设计过程中如果未能充分考虑到光学、材料、结构等方面的综合性能,就会导致组件的光学特性、热管理、传热设计等方面存在问题,从而影响到组件的发电效率。
2. 材料选择不当聚光光伏组件中使用的材料对于其性能和效率有着至关重要的影响。
如果材料的选择不当,比如光学膜材料的透过率不够、电池片材料的光电转换效率较低等,都会直接影响到组件的效率表现。
3. 制造工艺不精湛制造工艺不精湛是导致聚光光伏组件效率降低的另一个重要原因。
如果在生产过程中存在工艺控制不善、技术水平不高、生产设备精度不够等问题,都会影响到组件的质量和性能。
4. 环境因素生产环境的温度、湿度和尘埃等因素也可能会直接影响到聚光光伏组件的效率。
特别是在一些恶劣的环境条件下,组件的散热不良、污染积聚等问题会加剧组件效率的降低。
5. 维护保养不当在生产侧,对于聚光光伏组件的维护保养情况也会对效率产生影响。
如果在使用过程中未能及时清洁、及时检查维护,就会导致组件的污染积聚、损坏等问题,从而影响到组件的正常发电效率。
二、聚光光伏组件效率降低的解决方法1. 加强设计与研发为了提高聚光光伏组件的效率,首先需要加强设计与研发工作。
在设计阶段就需要对光学特性、材料性能、结构特点等方面进行充分的考虑,确保组件在设计上就能够具备较高的效率表现。
还要持续开展研发工作,不断引入新的材料、新的工艺、新的技术,提高组件的性能。
材料选择关乎到组件的整体性能,在生产过程中需要对材料进行严格的筛选和测试,确保在光学特性、热传导特性、光电转换效率等方面都能够满足组件的需求。
还要积极引入新的材料,不断优化组件的性能。
制造工艺的水平直接关系到组件的质量和性能,在生产侧需要加强对制造工艺的把控,提高工艺的精湛程度。
要引进先进的生产设备,加强工艺上的创新,确保组件的质量和性能在制造过程中得到保障。
- 1、下载文档前请自行甄别文档内容的完整性,平台不提供额外的编辑、内容补充、找答案等附加服务。
- 2、"仅部分预览"的文档,不可在线预览部分如存在完整性等问题,可反馈申请退款(可完整预览的文档不适用该条件!)。
- 3、如文档侵犯您的权益,请联系客服反馈,我们会尽快为您处理(人工客服工作时间:9:00-18:30)。
效果验证 标准化
6
不良影响因素
纸箱循环使用 次数无定义?
打包托盘的层 数规定是否符 合要求?
2. 运输方式
1.包装材料
中空板不同规 格混用?
内衬回收无检验 和次数规定?
托盘上下车卸 货是否符合要 求?
员工数片/检 验手法是否规 范统一?
厂内检验漏失 率过高?
3. 检验手法 (光电/组 件)
检验人员是否 均考核合格?
5
6
/
/
2012.01
2012.01 9
10
2)内衬的回收检验及使 用次数制定 包材改善的 优化方案 3)中空板的回收检验及 标用次数制定
2012.01
1
2012.01
4)托盘的改良
5)热塑膜的更改(改成 PE袋)
工艺 品管 PMC 工艺 a.更改设计,变成PE袋,减少热塑次数 品管 b.增加PE袋的来料检验管控 制造 c.热塑方式的优化(如热塑机温度,封口切割长度等) PMC
2
3
廖怀峰
肖列
副组长
副组长
4
5 6 7 8 9
黄治国
徐平芳 孙宏 任科宇 郑雪丽 组件团队
副组长
组员 组员 组员 组员
负责技术支持与协助
负责品管相关对策的开展执行与其他部 门改善对策的实施追踪 负责制造相关对策的制定与实施 负责与客户端相应沟通协调事宜 负责仓库相应对策的实施 待确认
3
组件检验不良回顾
4.检验漏失
厂内缺角返工 率过高? 7
对策及实施的策划一
序 项目 对策
1)纸箱的再次利用的标 准制定
实施方案
负责人
执行 时间
2012.01
a.定义出使用的次数(通过实验) 工艺 b.纸箱可使用及报废的标准制定 品管 c.纸箱的使用规范的定义(包括存储,运输,拿取等) 制造 d.纸箱的来料检验项目优化(增加硬度等) PMC a.定义出使用的次数(通过实验) b.可使用及报废的标准制定 c.使用规范的定义(包括存储,运输,拿取等) d.来料检验项目优化(增加硬度等) a.定义出使用的次数(通过实验) b.可使用及报废的标准制定 c.使用规范的定义(包括存储,运输,拿取等) d.来料检验项目优化(增加硬度等) e.中空板的包装方式优化 a.增加托盘的来料检验管控 b.改进托盘的质量(如更改材料等) c.出货时托盘上增加减震垫 工艺 品管 制造 PMC 工艺 品管 制造 PMC
降低组件来料破片率计划书 品管部
1
工作目录
1.改善小组成立
2.组件检验不良回顾 3.改善目标设定及分解 4.工作计划表 5.不良影响因素分解
6.相应对策及实验的策划
小组成立
成员介绍及工作分工
序号 1 姓名 孙总 组内职务 组长 组内分工 负责组织/策划本次改善活动,并监督各 组员工作进度 负责整个项目的开展并协调组件相关事 宜 负责制造相关对策的开展与监督执行
2012.01
2012.01
8
对策及实验的策划二
序 项目 对策 实施方案 负责人
工艺 品管 PMC 工艺 品管 PMC 工艺 品管 PMC 销售 品管 销售 品管 销售 制造 品管 工艺 品管 a.根据不同客户的要求或路程制定相应的 1)规定打包层数并严格执行 打包层数 b.在每板上增加打包带的加固处理 a.仓库备货时的搬运,叠层方法的标准化 2)出货前搬运,叠层,打包方 制定 运输方式优化 式的标准化 b.打包及缠绕膜的裹膜方式制定 方案 c.由QC监督整个过程的执行
(0.20%)
(0.15%)
(0.12%)
Oct:
0.15%
Feb:
0.28%
May:
0.23%
Aug:
0.18%
Nov:
0.15%
Mar:
0.25%
Jun:
0.20%
Sep:
0.15%
Dec:
0.12%
工作计划表
改善工作计划表 改善 过程 季度 月份 目标 成立小组 选定主题 设定目标 现状分析
上饶光电自6月份-11月份组件的批退裂片不良率平均为0.42%,趋势如下图:
0.60% 0.50% 0.40% 0.30% 0.20% 0.10% 0.00% 0.52% 0.44% 0.30% 0.48% 0.47% 0.30%
Jun
0.60% 0.50% 0.40% 0.30% 0.20% 0.10% 0.00%
执行 时间
2012.01
2
2012.01
3)客户端装卸货的方式标准化, 制定客户端的卸货规范,由光电协助并监 并监督执行 督执行
3 4 1)统一制定检验的手法,拿取 片的动作,包装等,并形成双 制定双方的认可规范 方认可规范(光电&组件) /
2012.01
检验手法
2012.01 2012.01
检验漏失率的 成立内部专案改善 降低 缺角/隐裂返工 成立内部专案改善 率的降低 硅片原材料的 改善(如氧碳含 成立内部改善专案 量改善)
July
Aug
0.52%
Sep
Oct
Nov
0.44% 0.30%
0.48%
0.47% 0.30%
降
Jun
July
Aug
Sep
Oct
Nov
目标设定:
Q3
Q1
Q2
0.20%
0.25%
Q4
0.12%
0.15%
目标分解:
Q1
(0.25%)
Q2
Jan:
0.30%
Q3
April
0.25%
Q4
Jul:
0.20%
D
Q1 Jan Feb Mar Apr Q2 May Jun Jul Q3 Aug Sep Oct Q4 Nov Dec 0.30% 0.28% 0.25% 0.25% 0.23% 0.20% 0.20% 0.18% 0.15% 0.15% 0.15% 0.12%
P
原因分析 提出对策 对策实施
C A 计划进度: 实际进度: