通用汽车APQP先期产品质量策划
精编【PPAP管理】五大手册简介APQPPPAPMSAFMEASPC简介

【PPAP管理】五大手册简介APQPPPAPMSAFMEASPC简介xxxx年xx月xx日xxxxxxxx集团企业有限公司Please enter your company's name and contentvISO/TS 16949:2009 参考手册的应用和案例目录前言一、产品质量先期策划和控制计划(APQP) 11.产品质量先期策划的由来 12.产品质量策划责任矩阵图 13.产品品质规划的基本原则 14.产品质量策划的基本步骤 25.A P Q P的主要内容4案例:先期产品质量策划控制程序13二、生产性零组件核准程序(PPAP) 161.范围、定义和目的162.何时要求提交163.生产件核准的要求174.提交等级175.过程要求196.记录和原型样品的保存207.零组件提交状态20案例:生产件核准程序21三、失效模式和效应分析(FMEA) 221.F M E A简介2 22.实施重点233.设计的D F M E A(D e s i g n F M E A) 2 34.分析方式(A n a l y s i s A p p r o a c h) 2 45.F M E A程序(F M E A P r o c e s s) 2 46.F M E A表格内容说明2 5案例:F M E A制作办法30附件:FMEA软件30四、测量系统分析(M S A—M e a s u r e m e n t S y s t e m s A n a l y s i s)3 11.测量系统变差的类型312.测量系统分析33附件:MSA软件46五、统计过程控制(SPC—Statistic Process Control) 471.控制图47案例—R控制图应用案例58 案例P控制图(不合格品率控制图) 58 案例缺陷数控制图(C图) 61 案例工序能力指数计算68 案例:SPC控制程序68附件:SPC系统实施步骤69前言ISO/TSl6949:2009且未指定其核心工具的具体内容,故组织在推行ISO/TSl6949:2009时,对核心工具的选择有较大的自由度。
APQP

目录
一、 APQP的基础知识介绍 二、 APQP的第一阶段 三、 APQP的第二阶段 四、 APQP的第三阶段 五、 APQP的第四阶段 六、 APQP的第五阶段
一、APQP基础介绍
(什么是APQP)
产品质量先期策划 ( Advanced Product Quality Planning )
2.6 工程图纸(包括数学数据)
顾客设计不排除策划小组以如下方式评审工程图纸的职责。工程图样可 以包括必须在控制计划上显示的特殊(政府法规和安全性)特性。当顾 客工程图纸不存在的时候,小组应当对受控制图纸进行评审,来确定哪 些特性影响了配合,功能,耐久性,以及政府法规和安全要求。
应当对工程图纸进行评审,确定是具有足够的信息以表明单个零件的尺 寸布置。应当清楚地标识控制或基准面/定位面,以便能为当前的控制 设计适当的功能量具和设备。应当对尺寸进行评估,从而保证可行性, 以及工业制造和测量标准相互一致性。适当时,小组应保证数学数据和 顾客的系统兼容,便于进行有效的双向交流。
2.7工程规范
项目小组应详细评审工程规范,识别功能、耐久性和外观要 求;
2.8 材料规格
除了图纸和性能规格,还应对材料规格进行,关于物理特性, 性能,环境,处理和贮储要求的特殊特性评审。这些特性也 应当被包括在控制计划内。
2.9 图纸和规格的变更
当要求对图纸和规格进行变更时,小组必须确保所变更能立即 通知到所有受影响的领域,并适当的书面记录。
造要求,以及任何可能对项目构成风险影响的因素 使用失效模式与影响分析(FMA) 开发初始工程要求
1.13 管理者支持
产品质量先期策划能够成功的关键之一,就是来自管理者的兴 趣,承诺与支持。管理层对产品质量策划会议的参与对确保项 目的成功是十分重要的。管理者支持应当在每个产品质量策划 阶段的结束时进行更新,来加强他们的承诺与支持。在需要时, 这些更新和/或帮助会经常发生。产品质量先期策划的一个主 要目标就是通过展示所有的策划要求都已满足,关注问题都记 录在案并安排有解决方案,包括项目进度和支持所需产能的资 源和人员配备,来保持管理者的支持。
五大手册具体如下

五大手册具体如下:1、FMEA:失效模式和效果分析2、MSA:测量系统分析3、APQP:先期质量策划4、PPAP:生产件批准程序5、SPC:统计过程控制TS16949:国际标准化组织(ISO)于2002年3月公布了一项行业性的质量体系要求,它的全名是“质量管理体系—汽车行业生产件与相关服务件的组织实施ISO9001:2000的特殊要求”,英文为TS16949。
我们从实践角度出发,在背景、目标与意义、内容三方面,对该质量管理体系要求作简要介绍。
1.TS16949的背景和动态为了协调国际汽车质量系统规范,由世界上主要的汽车制造商及协会于1996年成立了一个专门机构,称为国际汽车工作组International Automotive Task Force (IATF) 。
IATF的成员包括了国际标准化组织质量管理与质量保证技术委员会(ISO/TC176),意大利汽车工业协会(ANFIA),法国汽车制造商委员会(CCFA)和汽车装备工业联盟(FIEV),德国汽车工业协会(VDA),汽车制造商如宝马(BMW),克莱斯勒(Daimler Chrysler),菲亚特(Fiat),福特(Ford),通用(General Motors),雷诺(Renault)和大众(Voldswagen)等。
IATF对3个欧洲规范VDA6.1(德国),VSQ(意大利),EAQF(法国)和QS9000(北美)进行了协调,在ISO9001:2000版标准结合的基础上,在ISO/TC176的的认可下,制定出了TS16949 :2002 这个规范。
2002年3月1日,ISO与IATF公布了国际汽车质量的技术规范TS16949:2002,这项技术规范适用于整个汽车产业生产零部件与服务件的供应链,包括整车厂,2002年版的TS16949已经生效,并展开认证工作。
在2002年4月24号,福特,通用和克莱斯勒三大汽车制造商在美国密歇根州底特律市召开了新闻发布会,宣布对供应厂商要采取的统一的一个质量体系规范,这个规范就是TS16949。
上海通用常用术语
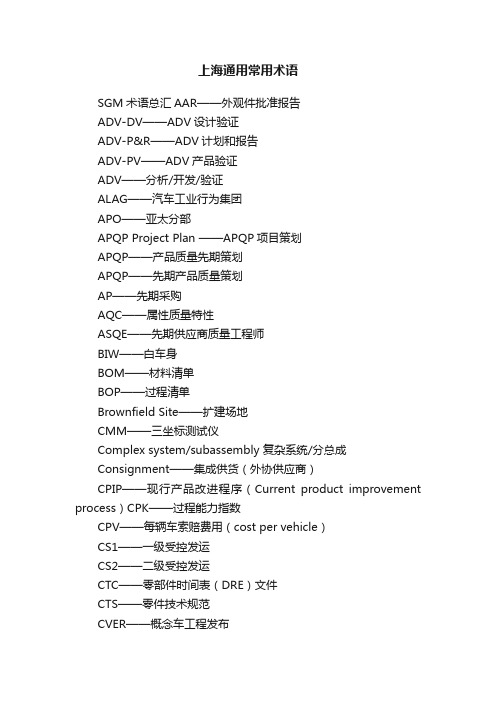
上海通用常用术语SGM术语总汇AAR——外观件批准报告ADV-DV——ADV设计验证ADV-P&R——ADV计划和报告ADV-PV——ADV产品验证ADV——分析/开发/验证ALAG——汽车工业行为集团APO——亚太分部APQP Project Plan ——APQP项目策划APQP——产品质量先期策划APQP——先期产品质量策划AP——先期采购AQC——属性质量特性ASQE——先期供应商质量工程师BIW——白车身BOM——材料清单BOP——过程清单Brownfield Site——扩建场地CMM——三坐标测试仪Complex system/subassembly 复杂系统/分总成Consignment——集成供货(外协供应商)CPIP——现行产品改进程序(Current product improvement process)CPK——过程能力指数CPV——每辆车索赔费用(cost per vehicle)CS1——一级受控发运CS2——二级受控发运CTC——零部件时间表(DRE)文件CTS——零件技术规范CVER——概念车工程发布CVIS——整车检验标准(complete vehicle inspection standard)DC——设计完成Defect outflow detection——缺陷检测DFM/DFA——可制造/可装配性涉及DFM/EA——设计失效模式分析DPV——每辆车缺陷数DR——DR特性DRE——设计释放工程师DRL——一次生产通过率损失DR——生产质量综合指数(Direct Run)DV——设计验证E&APSP——工程&先期采购定点程序EP——电子采购流程Error Occurrence Prevention——防错EWO——工程更改(engineering work order)EWO——工程更改指令FE1,2,3——1,2,3功能评估FMEA——失效模式和后果分析(DFMEA设计;PFMEA生产,MFMEA设备维护)FTQ——一次通过质量FTQ——一次质量合格率(First Time Quality)GA——总装GCA——全球顾客评审规范(Global customer audit)GD&T——几何公差&尺寸GDS——全球交付审查(Global delivery survey)GM1411—— PPAP临时批准GMAP——通用汽车亚太、GME——通用汽车欧洲GMNA——通用汽车欧洲GM——通用汽车公司、GP-10——实验室认可GP-10——试验室认可程序GP-11——样件批转GP-11——样件批准GP-12——早期生产遏制GP-12——早期生产遏制GP-4——生产件批准程序GP-5——供应商质量过程和测量GP-5——供应商质量过程和测量(问题回复及解决)GP-8——持续改进GP-8——持续改进GP-9——按节拍生产GP-9——按节拍生产GPDS——全球产品描述系统GPSC——全球采购及供应链GPS——全球采购系统GP——通用程序GQTS——全球质量跟踪系统GR&R——量具的重复性与在再现性Greenfield Site——新建工厂GVDP——全球整车开发流程IPTV——每千辆车缺陷数IPTV——千辆车故障率(incidents per thousand vehicles)IVEP——集成车工程发布IV——OTSJIS——作业指导书(Job instruction sheets)KCC——关键控制特性KCDS——关键特性指示系统Kick-off Meeting——启动会议(第一次APQP供应商项目评审)KPC——关键产品特性LAAM——(通用汽车)拉丁美洲、非洲及中东LAO——拉丁美洲分部Layered Process Audit 分层审核Layered Process Audit——分层审核LCR——正常生产能力MC1——FE2MC2——FE3MCB——FE1MCR——最大生产能力MC——匹配MOP——制造/采购MPCE——欧洲物料生产控制MPC——物料生产控制MRD——物料需求日期(首次正式交样)MSA——测量系统分析MVBns(原NS)——非销售车制造验证MVBs(原S)——销售车制造验证N.O.D——决议通知NAO——北美分部NBH——停止新业务OEM——主机客户OTS——外购国产化零部件和/或系统工程认可程序PAA——生产行动授权(Production action authorization)PAD——生产装配文件PC&L——生产控制&物流PCR——问题交流报告(Problem Communication Report)PDI——发运前检查(pre-delivery inspection)、PDT——产品开发小组PFMEA——过程失效模式和后果分析PPAP——生产件批准程序PPAP——生产件审批PPK——过程能力指数PPM——1)项目经理;2)每白万件的产品缺陷数PPV——产品及过程验证PQC——产品质量特性PR/R——问题报告及解决Pre-Production——预生产PRR——问题报告和解决(problem report and resolution PRR——问题交流与解决程序(Problem resolution report)PSA——潜在供应商评审PTR——零部件试生产PTR——生产试运行(Production trial run)PVV——TrgoutQSA——质量体系评审QSB——质量体系基础、QTC——工装报价能力R&R——按节拍生产RASIC——负责,批准,支持,通知,讨论RFQ——报价要求RPN reduction plan——降低RPN值计划RPN——风险顺序数S&R——车辆行驶时摩擦、振动噪音,泛指异响(Squeak&Rattle)S.T.E.P——采购定点小组评估过程SDE——供应商开发工程师SFMEA——系统失效模式分析SIL——单一问题清单(Single issues list)SMT——系统管理小组SOA——加速开始SOR——(供应商质量)要求声明SORP——正式生产SOS——标准作业单(Standardized operation sheets)SPA——发运前检查(Shipping priority aduit)SPC——统计过程控制SPO——(通用汽车)零件与服务分部SQE——供应商质量工程师SQIP——供应商质量改进过程SQ——供应商质量SSF——系统填充开始SSTS——分系统技术规范Sub contactor——分供方Sub-Assembly/Sub-SystemSVER——结构车工程车SVE——子系统验证工程师Team feasibility commitment——小组可行性承诺TKO——模具启动会议UG——UG工程绘图造型系统VAP——每辆车开发过程VLE——车辆平台负责人VTC——验证试验完成WDPV——平均每辆车不符合项与权重乘积的综合(平均每辆车扣分值)weighted discrepancies per vehicle WO——工程工作质量WWP——全球采购。
APQP产品质量先期策划

这里列出QSR中直接写出“应采用产品质量先期策划和控制计划参考手册”的段落:4.2.3.1 产品质量先期策划4.2.3.3 可行性评审4.2.3.7 控制计划
■
4.9.1
过程监视和作业指导书
■
4.9.2
维持过程控制
■
4.9.3
修改的过程控制要求
■
4.20.3
统计工具的选择
9 APQP与防错整个APQP的过程是采取防错措施,降低产品/服务发送到顾客时产生问题的风险,这是APQP的核心.
会计学
1
APQP产品质量先期策划
目录
一、概述1.什么是APQP的益处的基础4.常用的分析技术进度图6.产品质量策划循环7.产品质量策划责任矩阵图与QSR与防错
目录
二、APQP的五个过程1.计划和定义项目2.产品设计与开发3.过程设计与开发4.产品和过程确认5.反馈、评定和纠正措施三、控制计划1.概述2.过程的分析和控制方法3.控制计划栏目说明
APQP的五个过程(续)
图示
1
R(t)F(t)
APQP的五个过程(续)
什么是可靠度?
可靠度R(t)=
t 时刻仍然完好的产品数量
被观测产品的总数可靠性:产品在规定的时间内,在规定的条件下,完成规定功能的能力。可靠度是用完成规定功能的概率来表示。置信区间:当被观测的产品数量有限时,所计算得到的R(t)有一定误差,因此要给出其置信区间:例如:某产品置信为90%的可靠度置信区间是:。详见有关 参考书。1.6 顾客输入——后续顾客能够提供与他们的需要和期望有关的有价值的信息;
APQP的五个过程(续)
1.3 产品/过程标竿资料——使用标竿法(Benchmarking)为了制定产品/过程的性能目标提供输入。——R&D也提供标竿和概念——成功的标竿法如下:识别适宜的标竿;搞清本企业现有状况和标竿之间差距的原因;制定差距、赶上杆竿或超过标竿的计划。
APQP资料-通用汽车

本参考手册是通用汽车全球小组集体努力的结晶,该小组致力于建立通用汽车共同的APQP的过程。
在此之前,通用汽车的每一个供应商质量组织采用各部门和地区特定的方法,推动APQP的实施。
全球小组对APQP的过程进行了协调和标准化,从而建立了此通用汽车APQP手册(通用APQP手册GM1927)。
此手册定义了通用汽车共同的全球产品质量策划需求,它们对于建立和实施产品或服务的APQP过程必不可少。
它旨在作为一种标准,以向SQE以及供应商提供一种通用的格式,以推进APQP 的各个步骤的实施。
本文是初次发行稿的第2次修订版,并且已加以更新,以反映通用汽车为所有全球供应商所确定的最新要求。
此修订本的批准如下:全球采购部拉美业务部供应商质量供应商质量M.WOLF M。
MORRETRI动力总成亚太业务部供应商质量供应商质量T.NEJMAN M。
ALDEA北美卡车业务部欧洲业务部供应商质量供应商质量W.KRAATZ M。
SCHOENLEBER注:本APQP中文版由上海通用汽车采购部供应商质量和开发组织翻译,根据中国实际情况进行了修订。
本程序的解释权归供应商开发小组所有。
主要的更改和变化1.强调了GM APQP在全球范围内的统一性和严密性。
2.对APQP各阶段工作明确定义为17项任务,对各项任务的责任人、时间、任务输入输出、实施方法、SQE责任、供应商责任、参考资料等明确定义,以规范项目的开展。
3.在RFQ中增加供应商质量SOR,明确质量要求、体系要求、使用程序、质量策划、分供方要求等。
对PT零件供应商,还对KPC过程能力、PFMEA风险顺序等明确要求。
4.供应商报价时应同时提交初始DFMEA、PFMEA、控制计划、过程流程图等质量文件,并在定点时作为评审内容之一。
5.供应商报价时应同时提交“要求的质量信息”和相应的质量计划。
6.定点前要召开定点策略会议,评审RFQ、潜在供应商的资格、SOR、项目进度要求等。
7.定点前采购员、SQE等要进行技术评审,以评审供应商的报价文件,确认供应商有能力满足GM的进度、设计、制造能力、包装等要求。
上海通用供应商质量管理16步程序
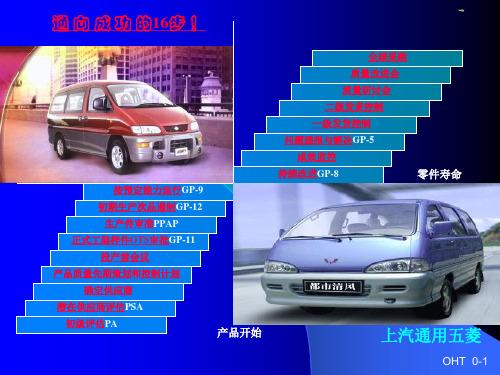
初级评估(PA / TA)
定义:在潜在供应商评估之前,对新的潜在供应商作一个初步评估,或
让供应商自我评估以确定其是否具备基本的质量体系、合适的技
术能力和良好的管理水平。
目的:通过半天的评估以确认新的潜在供应商是否有资格进行潜在供应
商评估。
范围:适用于所有被认作是潜在来源的新的供应商。
程序:A 采购员、经理或工程师进行现场评估
范围: 适用于需提供新样件的所有供应商。
程序:-由客户提供对样件的检验清单
-供应商得到有关提供样件要求的通知
-供应商得到GP-11中提出的要求
-供应商提交样件和按客户要求等级提供文件
-供应商会得到提交样件审理结果的通知:
―批准用于样车制造
―可用于样车制造
―不可用于样车制造
样件审批或工装样品(OTS)认可(GP—11)
按预定能力运行(GP—9)
定义:实地验证供应商生产工序是否有能力按照预定生产能力制造
符合质量及数量要求的产品。
目的: 通过事先进行生产的“按预定能力运行”来降低正式投产和加
速生产时失败的风险。
范围:除非由采购部门供应商质量及采购总监授权豁免以外,所有新
的零件都必须执行“按预定能力运行”。
程序:进行风险评估
OHT3-2
质量研讨会
定义:在供应商现场进行质量研讨,解决具体质量问题。
目的:尽快解决问题,使产品质量迅速提高,并建立一个具备控制和
持续改进质量的系统。
范围:可在供应商质量改进过程中任何时候进行。当某产品批量生产
不合格品PPM较高,或有反复PR/R,或受发货控制,或查访及
风险评估期间被特别指出时。
成效监控
持续改进GP-8
TS16949简介及PPAP学习

蒋大维
TS16949五大工具简介: 1)、APQP(先期产品质量策划):意在在产品未进行生产之前把所有的 问题解决掉,所以它是个复杂的过程,也是需要几 个来回反复才会成为最后策划的结果。) 2)、 FEMA(失效模式及后果分析): FMEA则是在APQP的二三阶段时进行 的失效模式分析,包括产品和过程。包含DFMEA, PFMEA,这些工作的导 入事件多为APQP的初期或中、早期。它们主要正对的产品的设计、生产工 艺或过程而言的。属于预防性的计划。 3)、SPC (统计过程控制):管制住某几个重要参数,监督它们生产的 稳定性。若发现有较大的波动,则立即采取措施,纠正工艺或生产流程。 4)、MSA (测量系统分析):校对量、检具 5)、PPAP (生产件批准程序)
(3) “失效后果”:是指失效模式对产品质量和顾客可能引发的不良影响, 根据顾客可能注意到或经历的情况 来描述失效后果,对最终使用者来说,失 效的后果应一律用产品或系统的性能来阐述,如产生高压、准确度变差等; (4) “严重性”: 是潜在失效模式对顾客影响后果的严重程度,为了准确 定义失效模式的不良影响,通常需 要对每种失效模式的潜在影响进行评价并 赋予分值,用 1-10 分表示,分值愈高则影响愈严重。 “可能性”: 是 指具体的失效起因发生的概率,可能性的分级数着重在其 含义而不是数值,通常也用 1—10 分来评估可能性的大 小,分值愈高则出 现机会愈大。 “不易探测度”: 是指在零部件离开制造工序或装备工位之前,发现失效起 因 过程缺陷的难易程度,评价指标也分为 1—10 级,得分愈高则愈难以被 发现和检查出;
-8-
四、PPAP程序要求
-9-
五、PPAP三大件
一、过程流程图 PFD 二、潜在失效模式 DFMEA PFMEA 三、控制计划 Control Plan
APQP产品质量策划及质量控制
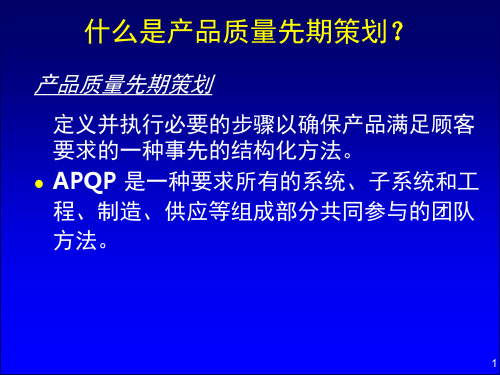
福特汽车公司APQP 23 个要素
STA
车辆运营的12个 焦点要素
动力系
5
一般 APQP 时间表
概念提出
/批准
项目批准
样件
试生产
投产
策划 产.品设计和开发
P过程设计和开发 D产品和过程验证/确认
反馈、评定和纠正措施
C
下一个项目策划
A 生产
6
FPDS APQP 要求
FPDS S5 项目
SI SC PH PA ST PR CP CC LR LS J1 FS
10
APQP 23个要素
1 资源决定 2 顾客输入要求 (2a 工艺技术) 3 设计失效模式后果分析 4 设计评审 5 设计验证计划 6 分承包方 APQP 状态 7 设施、工具和量具 8 样件制造计划 9 样件制造 10 图纸和规范 11 小组可行性承诺
12 制造过程流程图 13 过程失效模式后果分析 14 测量系统评价 15 试生产控制计划 16 操作工过程指导书 17 包装规范 18 产品试生产 19 生产控制计划 20 初始过程能力研究 21 生产确认试验 22 生产件批准 (PSW) 23 在IPD交付PSW零件
DFMEA中推荐的措施在<PR> 得到100%实施
SI
SC PH PA ST
PR
CP
CC LR LS
J1
FS
CFMEA
50 41
36 33.5
25.5
14.5
8
4.5 3.5
0
-6
25
4 – 设计评审
定义:
定期安排会议验证设计,并与管理层监控 计划进度
SI 50 41
SC PH PA ST 36 33.5 30 25.5
上海通用汽车APQP讲解-经典资料

SPC(Statistical Process Control)
总结词
SPC是一种利用统计技术对制造过程进行 监控和控制的工具。
VS
详细描述
SPC通过收集和分析过程数据,识别过程 的异常波动,找出原因并采取措施,以保 持过程的稳定和一致性。它有助于提高产 品质量、减少浪费和降低成本。
MSA(Measurement System Analysis)
APQP需要关注全球供应链的协同和整合,确保供应商、制造商和客户之 间的有效沟通和协作。
APQP在全球供应链中的重要性体现在提高供应链的可靠性和敏捷性,降 低风险和成本,提升整体竞争力。
06
如何提高APQP的实施效 果
如何提高APQP的实施效果
• 请输入您的内容
谢谢观看
总结词
创新思维,技术引领
详细描述
上海通用汽车在某零件的APQP实施过程中,充分发挥 创新思维,采用先进的技术手段,提高了生产效率和产 品质量。同时,通过技术引领,推动了整个行业的进步 和发展。
05
APQP的未来发展趋势和 挑战
APQP与数字化转型的结合
数字化转型为APQP带来新的机遇和挑战,通过引入先进的信息技术,实现APQP过程的数字化、智能 化和网络化。
总结词
MSA是一种评估测量系统准确性和可靠性 的工具。
详细描述
MSA通过分析测量系统的重复性、再现性 和线性等特性,确保测量系统的准确性和可 靠性。它有助于减少测量误差、提高产品质 量和生产效率。
PPAP(Production Part Approval Process)
总结词
PPAP是一种用于确保供应商在生产批量产品之前满足客户工程和产品质量要求的过程。
通用汽车APQP培训资料

背景
推 动 全 球 通 用 APQP 程 序 的 更 新
• 部 门 和 区 域 对 AIAG APQP 程 序 的 “ 调 整 ” • 不同的供应商所作的结果不同
– 不同的项目更新报告格式 – 不同的项目节点进度表 – 在 产 品 开 发 循 环 中 的 不 同 时 间, 要 求 不 同 的 细 节 • 当 SQE 进 一 步 “调 整 ” 要 求 和 制 定 唯 一 表 格 或 进 度 表 时 ,发生额外的变化
16
全 球 APQP 的 发 展
适 用 GM 全 球 的 全 球 通 用 APQP 程 序
• GM-1927 取 代 所 有 区 域 的 和 部 门 的 APQP 参 考 手 册 • GM-1927 统 一 并 标 准 化 了 多 区 域 和 部 门 的 APQP 手 册
– 与 AIAG APQP 手 册 的 5 步 法 联 合 并 为 实 施 APQP 计 划 提 供 详 细要求
• AIAG APQP 手 册 是 7 本 手 册 之 一 , 于 1994 年 6 月 起 草 并 完 成 – 本手册为先期产品质量策划开发提供通用性指南
QS-9000 • 本手册统一了福特,克莱斯勒和通用汽车各自对质量体
系要求
– 福 特 -- Q-101 质 量 体 系 标 准 – 克莱斯勒质量保证手册 – 通 用 汽 车 -- 争 创 最 佳
背景
APQP
定义
产 品 质 量 先 期 策 划 -- APQP • 采用结构化方法确定和建立必要的步骤以确保满足顾
客对产品的要求。 • 适用于所有新零件 • 确定供应商的职责
目的和结构
• 与顾客沟通所有的要求以便开发产品质量计划 • 供 应 商 高 级 管 理 层 的 支 持 是 APQP 程 序 成 功 实 施 的 关 键 • 要求参与各方相互信任和支持
汽车公司产品质量先期策划apqp指南
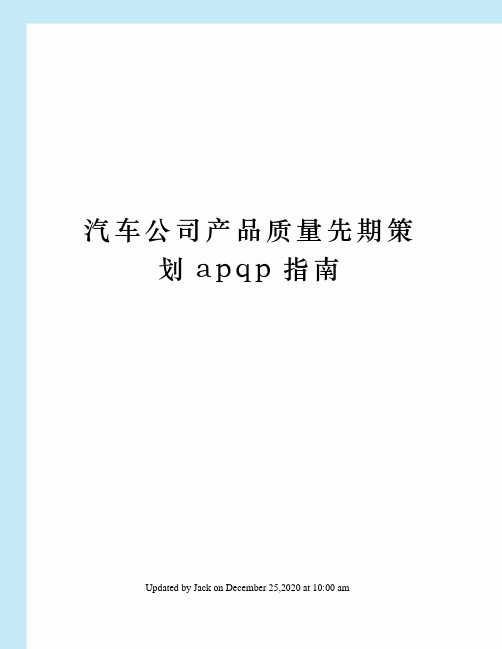
汽车公司产品质量先期策划a p q p指南Updated by Jack on December 25,2020 at 10:00 amxx汽车公司产品质量先期策划(APQP)指南前言福目录前言 (2)APQP基本原则 (5)APQP过程流程6 图………………………………………………………………………………………APQP基本原7 则…………………………………………………………………………………………APQP报告程序 (10)APQP状态报告流程11图…………………………………………………………………………………APQP状态报12告…………………………………………………………………………………………APQP状态报告表13格……………………………………………………………………………………填写状态报告表14格………………………………………………………………………………………质量事件检查15表…………………………………………………………………………………………风险评估 (15)APQP时间进度 (17)福特/供方系统“V”模式 (18)APQP通用的项目时间进度甘特19图…………………………………………………………………APQP要素和质量事件检查表……………………………………………………………………21资源决定 (22)顾客输入要求 (23)工艺技术 (24)设计失效模式后果分析25(DFMEA)…………………………………………………………………设计/制造评审 (27)设计验证计划 (28)分承包方APQP状29态…………………………………………………………………………………设施、工具和量具……………………………………………………………………………………30 样件制造控制计划……………………………………………………………………………………32 样件制造 (33)图纸和规范 (34)小组可行性承诺 (36)制造过程流程图 (38)过程失效模式后果分析40 (PFMEA)……………………………………………………………………测量系统评价 (42)试生产控制计划 (44)操作工过程指导书……………………………………………………………………………………45 包装规范 (46)产品试生产 (47)生产控制计划 (48)初始过程能力 (49)生产确认试验 (50)零件提交保证书(PSW) (51)目录(续)附录部分 (52)附录A:APQP角色和职责 (53)VO-PD APQP领导/支持职责-关系表 (54)动力系角色与职责矩阵 (55)动力系项目评估过程 (56)STA 角色与职责 (57)外部供方 (67)附录B:相关表格 (69)附录C:术语词汇表 (72)附录D:参考书目和相关网站 (79)参考书及网站 (80)APQP基本原则APQP过程流程图APQP过程基本原则产品质量先期策划(APQP)产品质量先期策划(APQP)是一种结构化的方法,用来定义和执行为确保产品满足顾客所必须的活动。
QC五大工具基本知识讲解
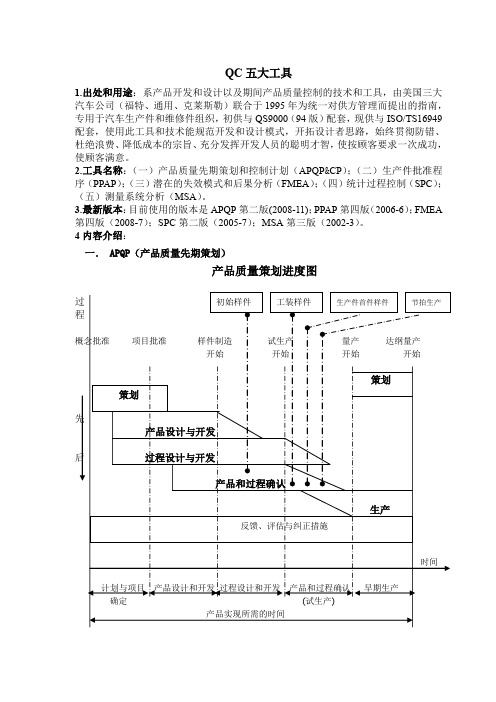
产品实现进行策划,其策划过程只需按图所表明的步骤进行即可。 该图显示了项目要进行策划的思考过程如下:
a.把产品实现所需时间,按节点分成若干个阶段。 阶段划分如表 1 所示。
施,例:指标的分解、风险分析、制订初始工程标准等,它是质
量计划的重要组成部分。
-----若提供产品设计,此时输出还需规定语言,制图标准、形 位和尺寸公差、材料牌号的标注规定、产品重要度标注、设计基
准、版号、配合尺寸等。
7 管理者支持
使 用 的 ·质量功能展开(QFD) 工具: ·产品质量策划的方法(APQP 方法) Ⅱ 输入: 第一阶段的输出
样件试验报告(如有要求)
质保部
25
设计验证
设计验证报告
项目小组
26
送样
送样记录
项目小组
27
项目小组多方论证
小组可行性承诺
项目小组
28
管理者支持
三
过程设计开发阶段
29
包装标准
顾客的包装要求
技术部
30
项目小组多方论证
包装图纸和说明
技术部
31
项目小组多方论证
▣ 凡按 ISO/TS16949 的要求建立质量管理体系的组织,在进行产品质量先期策划 时,必须按本方法来进行策划。(顾客有特殊要求者除外)。 3)使用本方法进行产品质量策划带来的好处:
▣ 用本方法为某产品开发确定和建立的步骤,因领导的重视和鼓励、各部门组成 的团队目标一致,能充分发挥设计人员的业务水平,必将瀛得顾客的满意;
Ⅲ 输入: 第二阶段的输出
b)APQP_CP先期质量策划(第二版)

2020/11/16
陈瑞泉
28
产品质量策划的基本原则
与进度图表有关的计划: 任何项目的成功都有赖于价有所值,以满足顾客的需
要和期望。下面所示 《产品质量策划进度图表》以及前 面已描述的《产品质量策划循环》要求策划小组尽全力预 防缺陷,缺陷预防通过设计技术和制造技术来同步推进。 策划小组应准备修改产品质量计划以满足顾客的期望。产 品质量策划小组有责任确保其进度符合或超过顾客进度计 划。
—输入与输出
·包装标准 ·产品/过程质量体系评审 ·过程流程图 ·场地平面布置图 ·特性矩阵图 ·过程失效模式及后果分析 ·试生产控制计划 ·过程指导书 ·测量系统分析计划 ·初始过程能力研究计划 ·包装规范 ·管理者支持
2020/11/16
·试生产 ·测量系统分析 ·初始过程能力研究 ·生产件批准 ·生产确认试验 ·包装评价 ·生产控制计划 ·质量策划认定和管理者支 持
陈瑞泉
27
产品质量策划的基本原则
控制计划: 控制计划是零件和过程系统控制的书面描述,单独的
控制计划包括三个独立的阶段: ☆样件—— 在样件制造过程中,对尺寸测量和材料
与性能试验的描述; ☆试生产—— 在样件试制之后,全面生产之前所进
行的尺寸测量和材料与性能试验的描述; ☆生产—— 在大批量生产中,将提供产品/过程特性
将产品质量策划过程看成一个不断循环的过程,表明持 续改进是无止境的。这种持续改进通常是将一个项目中 取得的经验、获得的知识应用于下一个项目的开发。
2020/11/16
陈瑞泉
5
2020/11/16
陈瑞泉
6
什么是质量先期策划?
a)它是一种满足并超越顾客要求的工具; b)它不仅仅是关于质量的策划,它是将质量控制手段 与 管理功能全面结合的 一种活动; c)它是一种项目管理的方法; d)它是一个有效的防错工具。 如果把TS16949管理体系比做一个系统,那么APQP 则是一个子系统;而FMEA、SPC、MSA则是子子系统, 它们是支持APQP的。
通用汽车APQP

11
项目计划概览
APQP 17 个 任 务 / 可 交 付 的 内 容
-关键利益各方会议 -技术评审 -风险评估/定点 -供应商项目评审 -时间进度表/未关闭问题 -量具/工装/设备审核 - GP-11 - 过 程 FMEA -控制计划 - GP-12
-可行性/制造评估函
-流程图 - 设 计 FMEA
17
全 球 APQP - 风 险 评 估 和 定 点 任务号:3
DFMEA (1 – Supplier Design Responsible, 2 – GM Design Responsible) 9 Design Review (1 – Supplier Design Responsible, 2 – GM Design Responsible) 10 Gage, Tool and Equipment Review 11 GP-11 12 PFMEA Development 13 Control Plan 14 GP-12 15 PPAP 16 Run @ Rate (GP-9) 17 Lessons Learned
6
项目计划概览
APQP 项目计划 APQP Project Plan
4 Phase GM Phase 0 Pre-sourcing Plan and Define Phase 1 Phase 2 Phase 3 AIAG Product Design and Development Process Design and Development Product and Process Validation Feedback, Assessment and Corrective Action Presourcing Alpha
先期产品质量策划与控制计划apqp第二版(完整版)
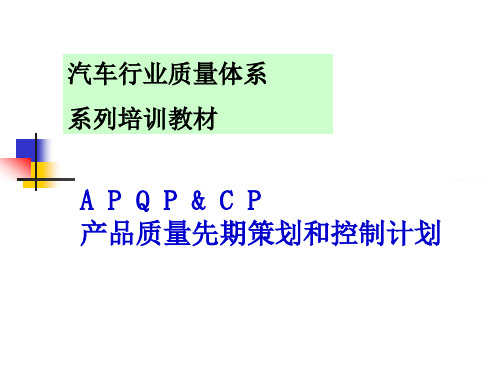
进度计划应采用甘特图的形式,通常使用 excel或 project制作,参见附件APQP进度计 划范例。
10
培训
产品质量策划的成功依赖于有效的培训方案,它传授 所有满足顾客需要和期望的要求及开发技能。
顾客和供方的参与
主要顾客可与其供方共同进行质量策划。但供方
有义务建立横向职能小组来管理产品质量策划过程。
供方应同样要求其分承包方。
11
顾客和供方的参与
一级顾客可与其供方共同进行质量策划。但供 方有义务建立横向职能小组来管理产品质量策 划过程。供方应同样要求其分承包方。
遇到困难,建议使用多方论证的解决方法。 可行时,应使用附录B中的分析技术。
15
产品质量的进度计划
产品质量策划小组在完成组织活动后的第一項工作是 制定进度计划。
在选择需作计划并绘制成图的进度要素时,应考虑产 品的类型、复杂性和顾客的期望。
所有的小组成员都应在每一事项、措施和进度上取得 一致意见。
7
XX汽车配件有限公司 产品质量先期策划(APQP)小组名单
编号:2009-0001
项目/产品名称
主要用户
序
姓名
号1
李一
2
王二
3
张三
4
李四
5
6
7
8
910ຫໍສະໝຸດ C-195/*******汽车有限公司
小组成员名单
部门及职务 技术部部长 营销部副部长
1.组织、协调工AP作QP内小容组的工作
2.负责技术部的工作管理 负责与用户保持联系,协调APQP小
样件-在制造过程中,对尺寸测量、材料与 性能试验的描述;
汽车APQP

汽车工程师们,你们真的懂APQP?体系固然重要,而且各家整车厂、零部件厂都有,也基本比较完善。
难点其实在于从上至下的执行,这点上单靠工程师们是远远不够的!无论是SQE还是采购对于供应商开发项目都是非常关心的,在汽车行业或者其他的制造行业我们通用的项目开发流程就是APQP,也就是先期产品质量策划(Advanced Product Quality Planning),这个工具大家都不陌生,但也并不是都非常精通吧?今天我们一起捋一捋APQP的细节,本文不仅仅面向SQE和采购哦,项目工程师,前期项目质量工程师,项目工艺工程师等都可以来读一读的哦~在开始APQP之旅前一起来熟悉几个大家经常挂在嘴边的概念:过程:一组将输入转化为输出的相互关联或相互作用的活动。
产品:过程的结果。
质量:一组固有特性满足要求的程度。
规范:判断一特定的特性是否可接受的工程技术要求。
变差:过程的单个输出之间不可避免的差别。
防错:为了防止不合格产品的制造而进行的产品和制造过程的设计和开发。
设计评审:为确定设计达到规定目标的适宜性,充分性和有效性所进行的活动。
设计验证:通过提供客观证据对规定要求已得到满足的认定。
设计确认:通过提供客观证据对特定的预期用途或应用要求已得到满足的认定。
1.项目的策划和定义阶段(1)本阶段工作目的及任务a)进行总体策划,包括人员,资源及项目时间进度安排b)确定顾客的需要和期望,提供比竞争者更好的产品c)确定设计目标和设计要求(2)本阶段的输入及形成的文件a)本阶段的输入为:顾客要求、以往的经验、企业确定的产品目标及要求、市场调研结果。
b)输入形成文件:立项可行性报告,包括:①市场调研结果②保证记录和质量信息③小组经验④业务计划/营销策略⑤产品/过程指标⑥产品/过程设想⑦产品可靠性研究⑧顾客输入(3)根据输入,完成下列工作,并形成相应文件。
a)成立跨部门的横向协调小组,并明确组长及相关职责人员,输出“小组名单”。
- 1、下载文档前请自行甄别文档内容的完整性,平台不提供额外的编辑、内容补充、找答案等附加服务。
- 2、"仅部分预览"的文档,不可在线预览部分如存在完整性等问题,可反馈申请退款(可完整预览的文档不适用该条件!)。
- 3、如文档侵犯您的权益,请联系客服反馈,我们会尽快为您处理(人工客服工作时间:9:00-18:30)。
方法:
z 在采购项目计划中明确产品定点策略会议日期 z 采购员向关键方发出会议邀请 z 采购员举行会议(典型的日程安排 GM1927-18) z 关键方讨论和评审项目信息和进度 z 相关人员讨论有关要求: --技术文件中工程要求评审 --供应商质量要求声明 --售后和 IPTV(每千辆车缺陷数)要求 ● 评审潜在投标人清单,以保证只向符合 GM 标准的供应商发出询价要求(RFQ),并确定需要进行潜在供应
M 对于复杂系统/分总成供应商的特定文件
GM1927----23M 直接采购检查清单 GM1927----24M 供应商项目评审 GM1927----25M 分供方项目状态表 GM1927----26M 分供方详细状态 GM1927----27 检具设计表 GM1927----28 PEMEA 风险评估表
必需的输入:
输入源:
技术文件
产品工程师
(BOM—材料清单、SOR—要求声明、SSTS/CTS—分系统/零件技术规范等)
ADV—(分析/开发/验证)程序任务和交付内容
产品工程师
投标人清单(量化质量指标)
采购员
以前项目的经验教训
采购员/SQE/工程师
项目相关信息
关键方(参照 GM1927-18)
资源:
采购、供应商质量、工程
划 E. 项目评审#2 4
更新过程流程图 7 、PFMEA 12 和 控制计划 13 检具、工装与设备概念 10 可行性承诺#2 6 更新的进度表 5 与问题清单 5
第四步:
过程设计与发展
A. SQE 参加设计评审 9 并提出经验教 训 17
B. SQE 评审检具与工装设计 10 C. SQE 指导过程流程图 7 、PFMEA 12
附件
附件包含所有 GM 特定的 APQP 表和文件,它们将在实施 APQP 的整个过程中使用 APQP,任务定义 1 至 17 中指导每一个表或文件的特定应用。
文件采购
GM 全球 APQP 本文件中包括在此 GM 全球 APQP 手册(GM1927)中所参照的所有具体的 GM APQP 表和文件,可以加 以拷贝使用。也可以通过 网址上 GM 的 SupplyPower 而获得此手册和所有的文 件。
上海盖普企业管理咨询有限公司 提供
附件
附件 2—复杂系统/分总成供应商 APQP 管理策划………………………………………………36
附
件
3—
术
语……………………………………….………………………………………………39
附件----GM1927 文件
GM1927----1 APQP 项目计划 GM1927----2 APQP 进度表 GM1927----3 供应商质量要求声明(SOR) GM1927----4 要求的质量信息 GM1927----5 APQP 问题清单 GM1927----6 关键方会议检查清单 GM1927----7 早期风险评估 GM1927----10 经验教训程序 GM1927----13 技术评审检查清单 GM1927----14 APQP 启动会议检查清单 GM1927----15 APQP 启动会议介绍 GM1927----16 过程控制计划审核工作表 GM1927----17 GM&供应商项目联系人清单 GM1927----18 主要相关方会议日程安排 GM1927----19 制造可行性分析信 GM1927----20 持续过程能力 GM1927----21 风险顺序数总结
APQP 活动
1 关键方会议 2 技术评审 3 风险评估与采购 4 供应商项目评审 5 进度表/问题清单 6 可行性分析与制造承诺 7 过程流程图 8 DFMEA
9 设计评审
10 量具、工装与设备评审 11 GP-11 12 PFMEA 13 控制计划 14 GP-12 15 PPAP 16 节拍生产(GP-9) 17 经验教训
顾客监控
APQP
供应商
GM
NA S NA R R R R
R(1) S(2) R(1) S(2)
R R R R R R R R
R R R A A A A A
S(2) R(1)
A A A A A A A I
R 负责(GM 或供应商) A 批准--GM 批准交付内容 S 支持交付内容的完成(GM 或供应商) I 通知—SQE 决定是否需要评审交付内容 C 咨询 NA 不适用
对供应商的说明: 此手册意在成为一份综合性和“包罗一切”的文件,然而,在某种情况下可能会出现问题。若您对本手 册的任务部分有任何问题,请与您相应的 SQE 联系。
上海盖普企业管理咨询有限公司 提供
顾客与供应商监控 APQP
以下矩阵描述了顾客或供应商监控的 APQP 之间的责任差异。供应商负责实施在矩阵中供应商一栏 中所示的所有“R”活动,而无论其零件的 APQP 是否为顾客或供应商监控。若零件指定为由顾客监控的 APQP,GM 的代表可以监控和批准 APQP 活动。
关键方对过程内容、进度与采购定点策略达成一致。
供应商研讨会指南和预期(技术设计问题/进度、小组成员、调查表等)。
技术评审的目标日期。
沟通策略—关键方信息交流的程序。
APQP 问题清单(GM1925-5)。
交付内容接受方: 采购*、工程*、供应商质量*、市场、PC&L 及其他相关人员
*关键方会议必须出席者
制订和理解采购定点过程、内容、进度和策略,保证 RFQ(报价要求)包含报价所需的所有信
息。所有产品定点前都应举行此会议。关键方在会上审核关键项目信息和“典型日程安排”
(GM1927)中涉及的进度。
交付内容: 一般的功能性要求应列入工程 SOR(要求声明)之中。
确定关键及非关键产品,如 SOR 要求,供应商准备 ADVP&R 表并得到 GM 批准。
B. SQE 对 PPAP 进行评审和状态确定 15 C. 进行按节拍生产 16 (GP-9) D. 进行项目评审#4 4
PPAP 15 和按节拍生产 16 状 可行性承诺#4 6 更新的进度表 5 与问题清单 5
产品质量先期策划(APQP)
第二步: 计划与定义项目
A. SQE 策划进行 APQP 启动会议 4 B. SQE 主持 APQP 启动会议 4 C. 供应商提供进度表 5 、问题清单 5 、
GM 通用程序(GP) 可以通过与 Boise Cascade 公司办公室产品科联系,而获得所参照的所有的 GM 通用程序(GP),电话号 码为 1-888-216-0371,传真:1-888-216-0603
AIAG 文件 所参照的所有 AIAG 特定文件可以通过与汽车工业行动组织(AIAG)联系而获得,其电话号码为: 01-248-358-3003。也可以通过访问网址 来订购文件。在欧洲,请与 CARWIN 有限公司 联系,电话:44-1708-861333。
、控制计划 13 的更新 D. SQE 评审防错&RPN 降低计划 12 E. 批准 GP-11 样件、模块与系统 11 F. SQE 更新风险评估 3 G. 进行项目评审#3 4
经更新的过程流程图 7 、PFMEA 12 、控制计划 13 、 进度图表 5 、未解决的问题清单 5 完成量具与工装设计 10 可行性承诺#3 6 GP-12 计划 14
上海盖普企业管理咨询有限公司 提供
通用汽车公司
通用汽车 全球
先期产品 质量策划
2002 年 10 月 第2版
上海盖普企业管理咨询有限公司 提供
APQP 任务定义 任务 1:产品定点策略会议…………………………………………………………………...1 任务 2:技术评审……………………………………………………………………….……..3 任务 3:APQP 风险评估与定点…………………………………………………….…..…….5 任务 4:供应商项目评审………………………………………………………………..…….7 任务 5:进度表/问题清单…………………………………………………………….………11 任务 6:可行性分析可制造性承诺………………………………………………….….……12 任务 7:流程图……………………………………………………………………….……….14 任务 8:DFMEA..…………………………………………………………………….……….16 任务 9:设计评审………………………………………………………………….………….18 任务 10:量具、工装与设备评估………………………………………………...………….20 任务 11:GP—11 预样件与样件材料…………………………………………….………….22 任务 12:PFMEA 开发……………………………………………………………..…………24 任务 13:控制计划………………………………………………………………...………….26 任务 14:GP—12 早期生产遏制…………………………………………………..…………28 任务 15:PPAP….…………………………………………………………………..…………30 任务 16:节拍生产(GP—9)……………………………………………………….………32 任务 17:经验教训……….……………………………………………………………………34
可追溯性 更新 WWP APQP 评估 3
上海盖普企业管理咨询有限公司 提供
任务编号:
1
产品质量先期策划(APQP) 全球程序
1
任务名称:
产品定点策略会议
任务责任人: 采购员、SQE 参加会议
任务时间安排: 采购定点前
任务描述:
产品定点策略会议的目的是要让所有 GM 的关键方参与选定产品项目的先期采购过程,以
C. 总结经验教训,并更新 DFMEA/ PFMEA 17
D. 完成 APQP
13
更新控制计划