第七讲:QCC要因确定
QCC-要因分析(步鄹4)

繞線時線未拉直
線穿CORE 線穿 時打結
勾線未直進直出
鑷子未泡凡立水
夾具太緊
鑷子
夾具磨破漆包線
方法
鑷子不光滑
設備
未包膠布
4
真因驗証<一 真因驗証 一> 耐壓不良
不良發生查檢表 鐵心COATING對比實 鐵心COATING對比實 COATING
7.20%
8.00%
站別 繞線時線未拉直 抽線時未理平 勾線未直進直出 預焊時PULSE未遮擋 未遮擋 預焊時 繞線 繞線 繞線 預焊
1
1. 彙集整理特性與要因之關系 首先要找出可能影響特性的要因.集合直接與工作相關的人員,以及有關單位 的人員,進行腦力激湯,收集多的意見,經充分思考、討論特性與要因之關系后,加 以整理,並予以系統表示,準備完成特性要因圖或關連圖特等.此時,特性宜以不良 情況表示,例如「鳳梨缸頭甜度偏低」、「文件取出費時等」 2.使用QC手法分析特性與要因之關系 調查分析特性要因圖上,被認為重要的要因當中,那些是真正的要因,其與特性 之間又具有何種關系.此處重要的是正確地了解事實,而不是只用推測,因此,可 使用QC 手法分析下列各種數據 a.過去和數據. b.已經會別過的日常數據. c.在工作現場進行實驗所得到的新數據. 進行分析進,主要的調查項目包括: a.觀察會間的差異 就有關4M(材料、機械設備、人員、方法)進行會別,並繪制已層別過的推移 圖、直方圖、散布圖、管制圖等,調查層間是否有差異. b,觀察時間性的變化 使用推移圖、查檢表或管制圖,調查特性與要因是否有進時間性的變化. c.觀察相關關系 繪制散布圖,調查要因與特性、要因與要因、特性與特性的2組數據之間,是否 有相關關系存在. 2 d.觀現場與現物
相關要因 理線腳冷焊 勾針繞線拉斷單線
QCC各步骤ppt课件

45.6 36
32
4
2
5
变碰印刮其 形凸凹伤它
100
75
累 计 50 百 分 25 比
0
改善后
N=10 日期:18/3 作成:黄理源
下降 87.3%
10 3 5
2
1
0
4 100 50
0
0
刮印碰变其
伤凹凸形它
效果确认《案例》
与现状把握时比较
250 225 200 175 150
片 / 125 H 100
吸盘拉起时此处先翘起。
9.效果确认
重点:
以图表比较说明是否达成目标。
活动内容:
◎使用和现状把握相同图表做改善前、后比较。 ◎进行和目标值比较。 ◎改善效益如何。
效果确认案例
与现状把握时比较
70
钣 60 修 50 数 / 40 项 30 目 20
10
0
N=79 日期:6/2 作成:黄理源
86.1 91.1 93.7
5.右前翼各工程钣修率层别
50
40
30
钣
修 20 率 10
0
数据来源:03年2月6日冲压日报表
生产1253件
钣修79件
39
16
11
9
4
PB工程 PC工程 PD工程 PE工程 PF工程
现状把握《案例》
6.右前翼PE工程钣修项目层别
80
钣
修
70
数 60
/ 50
项
40
目
30
20
10
0
N=79
日期:6/2
◎框虚线区为本期活动工站
现状把握《案例》
品管圈QCC介绍如何运用QCCppt

⑵无形成果:较不容易以数据表示的成果。
三、品管圈活动的组织及职责
要有效地实施品管圈活动,必先成立品管 圈活动的相关组织,并明确制定有关章程。
品管圈活动推行的一般组织结构:
总经理 部、课 班、组
品管圈推行委员会 主任委员
作业员
委员 委员 委员
执委会
⑾实施品管圈活动时,必须全体圈员共同参与、 共同讨论,才能产生集思广益的效果,因此圈长 的任务之一就是组织全体圈员都能参与,全员发 言。
二、品管圈活动的目标及成果
1.品管圈活动的特点 ⑴创造愉悦的工作 ⑵发挥员工的脑力,将大脑“联网” ⑶改善企业运作
2.品管圈活动的目标
通过实施品管圈活动可达成下列目标:
⑶品管圈活动最重要、也最难做到的一点 就是圈员们的自发精神,如果圈员们缺乏 主动精神或迫于上层的压力被动工作,会 影响品管圈活动的效果。
⑷企业要获利,永续经营,则必须实施品 质管理,因此现场员工要讨论的事项必须 以品质为中心,应关乎到Q(品质)、C (成本)、D(交期)、M(士气)、S (安全)、T(技术)等。
课题是一种期待达成的目标,为能实现课 题目标,需先针对此课题进行充分探讨, 继而提出最适合的方案,创造出新的方法, 此方法适用于突破性的较大改善,已逐渐 在QCC中推广使用。
两类改善方式的改善流程如下图所示:
课题达成型 活动计划制订
问题解决型 活动计划制订
课题确定、目标设定
现状把握、目标设定
方案拟定
三、QCC活动计划及实施进度
QCC活动计划及实施进度表
课题选定 把握和分析现状 对策1 效果确认 对策2
巩固措施 检讨和今后的方针
计划
QCC培训课件

QCC起源于日本,最初是由日本品管大师石川馨博士于1962年所创。后来,QCC逐渐在亚洲和世界各地得到推 广和应用。
QCC目标与原则
互相学习,共同提高
QCC成员之间要互相学习、互相帮助,共 同提高。
目标
QCC的主要目标是提高产品质量、降低生 产成本、提高生产效率、增强员工参与感 和归属感等。
原则
强化质量意识
通过宣传、教育等方式,提高团队成员的质量意识,确保 QCC活动的成果符合质量标准。
建立学习型组织
推动团队成员不断学习新知识、新技能,提高个人素质和 能力水平,为QCC活动提供有力支持。
THANKS
感谢观看
提出改进建议
针对存在的问题,提出具体的改进建议,包括改 进措施、实施计划和预期效果等。
制定改进方案
根据改进建议,制定具体的改进方案,明确责任 人、时间节点和所需资源等。
持续改进并推广优秀经验
持续改进
01
不断关注实施过程中的问题和反馈,及时调整和改进方案,确
保持续改进的效果。
推广优秀经验
02
将成功的经验和做法进行提炼和整理来自通过培训、交流等方式QCC以员工自愿参加为基础,实行 自主管理,自我教育,互相启发, 共同提高。
广泛的群众性
QCC是吸引广大职工群众积极参与 质量管理的有效形式,具有广泛的群 众性。
高度的民主性
QCC组长可以轮流担任,人人都有 发挥才智和锻炼成长的机会。
严密的科学性
QCC在活动过程中遵循规定的工作 程序,采用科学的统计技术和工具 来分析和解决问题。
03
问题识别与原因分析
识别生产过程中存在问题
01
02
03
观察生产过程
QCC 基本知识讲解

是否达到目标
Action
9、制订巩固措施 10、总结和下一步打算
二、创新型QC小组标准流程
1、选择课题
2、设定目标
Plan
3、提出各种方案 并确定最佳方案
4、制订对策
Do
5、实施对策
6、检查效果
否
Check
是否达到目标
Action
7、制订巩固措施 8、总结和下一步打算
图解QC履历1
图解QC履历2
2、提高生产力: 4、增加利润;
(二)、对管理阶层的效益 1、使工作容易推行; 2、减轻管理工作;
(三)、对同仁的效益 1、提高个人能力水平:2、增加个人知识: 3、满足个人成就感: 4、增加个人所得: 5、环境美化,现场有朝气: 6、扩大生活圈,提高生活乐趣: 7、有参与经营被重视的感觉:
请用一笔划的4条直线 连接下面的9点
(脑力激荡、活跃发言)
会议总结 (议而有果、确认任务)
会议追踪 (确认记录、整理FLW)
三、 QC小组组建程序与注册登记
QC小组组建程序 1. 自上而下的组建程序 2. 自下而上的组建程序 3. 上下结合的组建程序
QC小组的人数 一般3~10人之间为宜。
QC小组的注册登记
四、 QC小组活动的基本条件
制图人:张庆洲 日期:2003.4.03
1、2003年1-3月份硅胶损失率 平均损失率37%
实验条件投: 入数量:1000g
投入日期:3月21日~3月30日
损失构 成项目
(1)称量散热硅胶损失固体并分
类统计
损失实物 286g
胶管挂壁 184.2g
胶瓶残留 39.8g
2、通过实验得出损失构成
QCC课题-原因要因分析

镀膜线故障次数分布推移图
35 30 25 20 15 10
5 0
1月 2月 3月 4月 5月 6月 7月 8月 9月 10月 11月 12月
镀膜线故障总次数 A线故障次数 B线故障次数 电气故障次数 机械故障次数 电气传动次数 机械传动次数 阴极次数 工艺电源次数 其他次数 真空泵次数 水系统次数 清洗机次数
0 1月 2月 3月 4月 5月 6月 7月 8月 9月 10月 11月 12月
镀膜线故 障总时间
A线故障 时间
B线故障 时间
电气故障 时间
机械故障 时间
镀膜线故障类别时间分布推移图
1000
800 600
400 200
0 1月 2月 3月 4月 5月 6月 7月 8月 9月 10月 11月 12月
电气传动时间 机械传动时间 阴极时间 工艺电源时间 其他时间 真空泵时间 水系统时间 清洗机时间
2021/9/28
原因分析实例
2010年1-6月份故障分析数据
分类 镀膜线故障总时间 镀膜线故障总次数
A线故障时间 B线故障时间 A线故障次数 B线故障次数 电气故障时间 机械故障时间 电气故障次数 机械故障次数 电气传动时间 机械传动时间
1月
2月
3月
4月
5月
6月
956
453
795
1065
1399
1572
30
255
83
128
132
3
3
8
15
8
7
1
1
3
2
1
2
2
2
1
0
1
3
8
4
1
QCC定义ppt课件

品管圈的意义
对公司 1. 改善产品和服务的质量 2. 提高生产力,降低成本 3. 激励员工士气 4. 增加公司与员工的沟通 对管理 1. 鼓励员工自己解决问题,减轻工作负担 2. 确保工作的高效开展 对成员 1. 获得自身发展的训练机会,增加知识,增强创造性 2. 获得参与机会,改善合作关系 3. 获得物质奖励,自我发展机会
5
品管圈活动的基本概念
品管圈的精神
尊重人性,建立 轻松愉快的现场
发挥员工潜在能力, 开发无限的脑力资源
提高企业竞争力
工作现场
品管圈的作法
自动自发 自我启发 全员参与 全员发言 相互启发
品管圈的目标 现
提
提
提提
提场
高高ຫໍສະໝຸດ 高高高成现
现
品问
改为
场
场
质题
善品
水
士
意意
意管
准
气
识识
识中
心
6
QC小组分类:
(1)"现场型"QC小组 (2)"攻关型"QC小组 (3)"管理型"QC小组 (4)"服务型"QC小组
2
QCC宣传资料的张贴 吴兆文/
品管部
3
QCC宣传手册的制作 李松/品
管部
4
QCC定义培训
李松/品
管部
5 QCC活动九大步骤培训 吴兆文
/品管部
6 自我、人际与团队培训 吴兆文 /品管部
7 QCC的成立与原则培训 李松/品
管部
8
QC手法培训
李松/品
管部
9 QCC小组成立与活动开展 各部门
10
QCC成果发布
品管圈(QCC)培训讲义

——如何运用QCC
讲师:曾严征
什么是QCC?
QCC英文全称QUALITY CONTROL CYCLE,中文 译作“品管圈”。
同一工作现场、工作性质相似的基层人员自发地 进行品质管理的活动时组成的小组称为品管圈。
这个小组做为全面品质管理的一个环节,在自我 启发和相互启发下,灵活运用各种QC手法,全员 参加,对自己的工作现场不断地进行维持与改善 的活动,称为品管圈活动。
⑴提高现场班组长的管理能力及领导能力,进而 提高部门绩效。
⑵提高最基层员工的品质意识、问题意识及改善 意识,并能将此气氛渗透至现场每一个角落。
⑶使现场成为品质保证的核心,使各部门管理稳 定并持续进步,公司方针目标之达成度得发提高 。
⑷提高员工对上班工作的喜悦和成就感,并提高 员工向心力及士气,进而提高效率。
管理改善活动,当新圈组成后,为使QCC活动切 实有效,并使圈员有一种归属感,应向自己公 司QCC推行部门办理登记。
六、改善步骤
1.问题解决型 现在流程发生了问题,必须调查其中不良 原因,再将过去的做法做全部或部分改变 ,从而解决问题所采取的改善方法,该办 法很早就被QCC所使用,效果很好。
2.课题达成型
⑻如没有工具,或不懂得利用工具,是无法做好 事情的。
⑼品管圈并不是为了解决某一问题而组织的临时 机构,而是常设机构,因为现场的问题有无限多 ,因此必须将问题一个一个、不断地、持续地解 决与改善。
⑽品管圈活动所要发现及解决的问题是以自己的 工作现场为主,即以自我检讨、自主管理为重点 ,如问题与其他部门有关连,当然可通过沟通、 协调或建议的方式共同解决。
三、QCC活动计划及实施进度
QCC活动计划及实施进度表
课题选定 把握和分析现状 对策1 效果确认 对策2
QCC基本知识

QCC基本知识 QCC基本知识
决定主题(第三圈会) ■ 决定主题(第三圈会)
经过上一步,圈员们应定出解决问题的 经过上一步, 先后顺序,达成共识,并决定第一次挑战 先后顺序,达成共识, 的主题。 的主题。 圈长应提醒圈员们考虑本圈是否有能力 解决所提出的主题。 解决所提出的主题。
QCC基本知识 QCC基本知识
◎有些圈员好高骛远,一开始就提出超 有些圈员好高骛远, 过解决能力的主题下手,最后遭到失败与 过解决能力的主题下手, 挫折,从而失掉信心和斗志。这个时候我 挫折,从而失掉信心和斗志。 们的圈长应怎么做呢? 们的圈长应怎么做呢? 万一失败,圈长要负起维系军心的作用。 万一失败,圈长要负起维系军心的作用。 管理上有一句名言:失败不能光是后悔,因 管理上有一句名言:失败不能光是后悔, 为你已经交了学费,更何况经验的取得来自 为你已经交了学费, 于每一场硬仗。 于每一场硬仗。
QCC基本知识 QCC基本知识
■ 掌握改善主题的重点
对于改善主题,使用层别法将需要的资 料加以集计,并使用柏拉图法将造成的状 况和原因加以分析,找出重要的关键项目, 改善的工作应从重要的项目下手.
QCC基本知识 QCC基本知识
■ 探讨原因
我们使用鱼骨图法,全体圈子员用脑 力激荡术,在圈会时做动脑会议,将可能 之原因一一找出,最后再决定几个主要 最后再决定几个主要 原因(可应用排列图).
QCC基本知识讲义 QCC基本知识讲义
课程简介
QCC的定义 ■QCC的定义 QCC的起源 ■QCC的起源 QCC的解读 ■QCC的解读 QCC的推动步骤 ■QCC的推动步骤 QCC的意义与启示 ■QCC的意义与启示
QCC基本知识 QCC基本知识
QCC的定义 QCC的定义
第七讲:QCC要因确定.

现场确 认
孙小凤
制表人:韦东方
制表时间:2010年4月24日
P
要因验证(一)
验证时间:10/4/27 人 员:邓继男 方 法 :现场调查
末因一:人员视力差异
说明:公司招聘基本要求:人员辨色正常,裸视在1.0 (含)以上。
例如:轧刚厂轧制钢板,弯曲率达到30%,末端原因之一是“压下量大”, 对工艺规定的压下量25MM是否过大呢? 就需要安排现场的试验、验证,于是安排了试验计划,在其他因素不变的 情况下,把压下量改为20MM,试轧一批钢板,结果弯曲率为8%,有明显 好转,从而判定“压下量大”是主要原因。
一、如何确定主要原因
关的作业手顺要求,若作业手顺不当很容易造成端子部破损。
A:左手推入式
B:双手推入式
C:右手单放式
D:左手单放式
现场验证:经现场统计P检点灯作业手顺共有以上A、B、C、D四种方式。
报废率(PPM)
60 58 56 54 52 50 48
57 55 55 53
要因
55
光头圈
合计
A 左手推入 B 双手推入 C 右手单放 D 左手单放 式 式 式 式
投入数 27089 23678 27833 25907 30535 31173
报废率 1 1 1 1 1 2
报废率 37 42 36 39 33 64 42
80 60 40 20 0
平均
166215 7 报废率(PPM)
要因
光头圈
42
64
37
42
36
39
QCC活动培训教材

详细描述
头脑风暴法是一种通过集体讨论、自由发言 的方式激发创意和思考的方法。在QCC活动 中,头脑风暴法常用于集思广益,鼓励团队 成员提出新的观点和想法,以寻找最佳的问 题解决方案。
水平对比法
总结词
一种比较事物之间差异的方法
详细描述
水平对比法是一种通过比较不同事物 之间的差异来发现问题的方法。在 QCC活动中,水平对比法常用于比较 类似产品、服务或过程之间的优缺点, 以便找出改进的方向。
流程图法
要点一
总结词
一种表示事物发展过程的方法
要点二
详细描述
流程图法是一种通过图形化方式表示事物发展过程的方法 。在QCC活动中,流程图法常用于分析问题的发生、发展 过程,帮助团队成员理解问题所在,并寻找解决问题的最 佳时机。
矩阵图法
总结词
一种展示事物之间关系的表格图形化方法
详细描述
矩阵图法是一种通过表格图形化方式展示事物之间关系 的方法。在QCC活动中,矩阵图法常用于分析问题的影 响因素,以及它们之间的关系,以便制定有效的解决方 案。
原因分析
总结词:分析原因
VS
详细描述:原因分析是QCC活动中非 常关键的一步,它涉及到对问题产生 的根本原因进行深入探究。通过分析, 团队可以找出影响问题解决的主要因 素,为制定对策提供依据。在这一步 中,团队需要运用科学的方法和工具 进行全面、客观的分析。
制定对策
总结词:制定方案
详细描述:在找出问题的原因后,团队需要 制定相应的对策和解决方案。这些对策应该 具有针对性和可操作性,能够有效地解决现 有问题并实现设定的目标。在制定对策时, 团队需要考虑各种资源和条件的限制,以确
特点
QCC活动具有群众性、自下而上性、科学性和循序渐进性。它以团队为基础, 以员工为主体,通过激发员工的积极性和创造性,实现企业目标。
QCC之主题选定
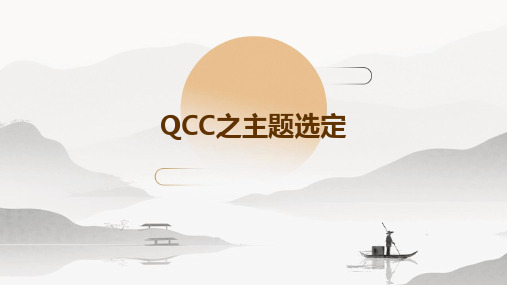
提高团队凝聚力
一个共同的主题能够将团队成员紧密地联系在一起,使他们有共同的目标和愿景。在解决问题的过程中,团队成员需要共同 协作、互相支持,这有助于提高团队的凝聚力和合作精神。
通过共同的主题,团队成员可以更好地了解彼此的工作和角色,加强相互之间的沟通和协作,从而提高整个团队的效率和工 作质量。
改进点。
优化工作流程设计,减少 冗余和重复环节。
详细描述
引入先进的流程管理工具 和方法,如BPM(业务流
程管理)系统。
加强跨部门协作和沟通, 确保流程顺畅运行。
04
主题选定常见问题与对策
问题一:主题过大或过小
总结词
主题选定过大或过小会导致小组在实施过程 中难以把握和操作,影响活动效果。
详细描述
如果主题选定过大,涉及面过广,小组在实 施时难以全面深入地研究和讨论;而主题选 定过小,则可能使活动过于局限,缺乏广泛
01
分析现有生产流程,识别瓶颈和低效环节 。
03
02
详细描述
04
引入自动化设备和智能制造技术,提高设 备利用率和工作效率。
优化生产计划和调度,减少等待和闲置时 间。
05
06
加强员工培训和技能提升,提高生产操作 水平。
案例二:降低不良率
总结词:通过严格控制产品质
量和改进生产工艺,降低不良
率。
01
详细描述
总结词
以目标为导向选定主题
详细描述
根据组织或团队设定的目标,选定与之相关的主题,确保活动与整体目标保持一致,促 进目标的实现。
创新主题选择
QCC基础专业知识讲座课件
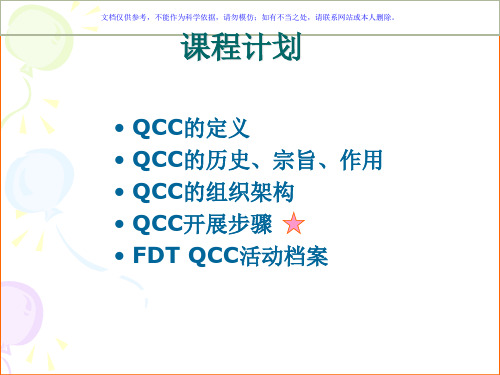
1960
全面质量管理 TQM
1962
日本首创QC小组
中国第一个QC小组 北京内燃机总厂
1978
试点阶段(78-79年) 仅2005年一年, 全国共注册131万
推广阶段(80-85年) 个QC小组, 发展阶段(86年至今) 创经济效益362亿
元。
文档仅供参考,不能作为科学依据,请勿模仿;如有不当之处,请联系网站或本人删除。
1.选择课题
2.现状调查 3.设定目标 4.分析原因 5. 要因确认 6.制订对策 7.对策实施 8.检查效果
否 达到目标
是 9.标准化 10.总结和下一步打算
1.选择课题
2.设定目标
P
3.可行性分析
4.分析原因
5. 要因确认
6.制订对策
D
7.对策实施
8.检查效果
C
否
达到目标
是
9.标准化 A
10.总结和下一步打算
6.对策制定
• 针对找到的要因制定对策和措施,对策要 具体、可行。
– 结合技术、经验、和创造性思维提出想法; – 对提出的所有对策进行有效性、经济性、可
实施性、难易程度等确定实施的对策; – 避免采用临时性的应急对策,不仅要治标,
更要治本。
文档仅供参考,不能作为科学依据,请勿模仿;如有不当之处,请联系网站或本人删除。
• 个人成长方面:
– 有利于开发智力资源,发挥人的潜能,提高人的素质; – 有利于改善人与人之间的关系,增强员工的团结协作
精神; – 有助于提高员工的科学思维能力、组织协调能力、分
析与解决问题的能力;
文档仅供参考,不能作为科学依据,请勿模仿;如有不当之处,请联系网站或本人删除。
QCC(品管圈)之第七步:标准化与维持管理
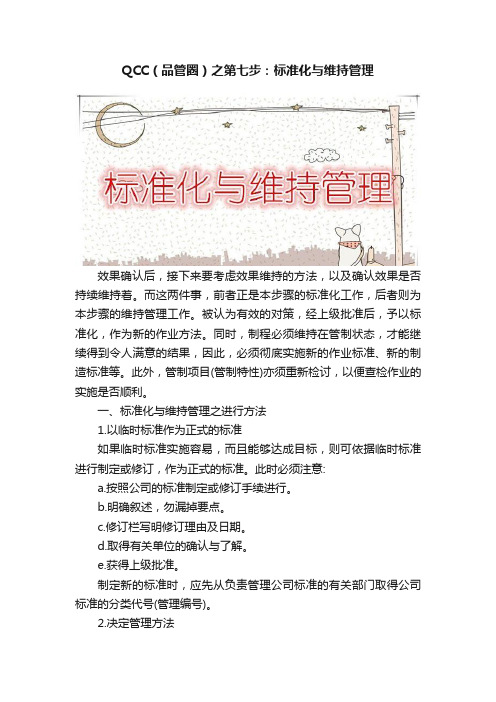
QCC(品管圈)之第七步:标准化与维持管理效果确认后,接下来要考虑效果维持的方法,以及确认效果是否持续维持着。
而这两件事,前者正是本步骤的标准化工作,后者则为本步骤的维持管理工作。
被认为有效的对策,经上级批准后,予以标准化,作为新的作业方法。
同时,制程必须维持在管制状态,才能继续得到令人满意的结果,因此,必须彻底实施新的作业标准、新的制造标准等。
此外,管制项目(管制特性)亦须重新检讨,以便查检作业的实施是否顺利。
一、标准化与维持管理之进行方法1.以临时标准作为正式的标准如果临时标准实施容易,而且能够达成目标,则可依据临时标准进行制定或修订,作为正式的标准。
此时必须注意:a.按照公司的标准制定或修订手续进行。
b.明确叙述,勿漏掉要点。
c.修订栏写明修订理由及日期。
d.取得有关单位的确认与了解。
e.获得上级批准。
制定新的标准时,应先从负责管理公司标准的有关部门取得公司标准的分类代号(管理编号)。
2.决定管理方法改善的效果必须维持,否则可能又会恢复原状。
因此,决定「管制项目(control point)」与「查检项目(check point)」及其管制方法势在必行;同时要制定或修订QC工程图、制程异常对策表等管理标准,以便进行管制相关的特性值及确实地抑制不良要因,使效果能够维持在良好的状态。
3.让所有相关人员了解新管理方法并彻底实施召开会议,或利用朝会等各种集会,向有关人员说明新管理方法,让大家都了解,并彻底实施。
4.对作业员实施有关新作业方法的教育训练如果只是把新的作业标准书交给作业员,就期待作业员能做出标准作业,这的确有困难。
作业员不一定都会好好地阅读,而即使读过,好会有人对内容产生误解。
因此,主管人员应对部属充分实施有关作业标准的教育训练。
5.确认改善效果是否持续维持效果维持,一般使用查检表、推移图、直方图或管制图等QC手法加以确认。
制程异常通常由以下几种情况可以发现:a.有关管制特性的管制图呈现异常状态。
QCC品管圈基础知识

QCC品管圈基础知识QCC活动的主要内容二、活动主题选定,制定活动计划1、每期品管圈活动,必须围绕一个明确的活动主题进行,结合部门工作目标,从品质、成本、效率、交期、安全、服务、管理等方面,每人提出2~3个问题点,并列出问题点一览表。
2、以民主投票方式产生活动主题,主题的选定以品管圈活动在3个月左右能解决为原则。
3、提出选取理由,讨论并定案。
4、制定活动计划及进度表,并决定适合每一个圈员的职责和工作分工。
5、主题决定后要呈报部门直接主管/经理审核,批准后方能成为正式的品管圈活动主题。
6、活动计划表交QCC推行委员会备案存档。
7、本阶段推荐使用脑力激荡法和甘特图。
QCC活动的主要内容三、目标设定1、明确目标值并和主题一致,目标值尽量要量化。
2、不要设定太多的目标值,最好是一个,最多不超过两个。
3、目标值应从实际出发,不能太高也不能太低,既有挑战性,又有可行性。
4、对目标进行可行性分析。
QCC活动的主要内容四、现状调查,数据收集1、根据上次的特性要因图(或围绕选定的主题,通过圈会),设计适合本圈现场需要的、易于数据收集、整理的查检表。
2、决定收集数据的周期、收集时间、收集方式、记录方式及责任人。
3、圈会结束后,各责任人员即应依照圈会所决定的方式,开始收集数据。
4、数据一定要真实,不得经过人为修饰和造假。
5、本阶段使用查检表。
QCC活动的主要内容五、数据收集整理1、对上次圈会后收集数据过程中所发生的困难点,全员检讨,并提出解决方法。
2、检讨上次圈会后设计的查检表,如需要,加以补充或修改,使数据更能顺利收集,重新收集数据。
3、如无前两点困难,则圈长落实责任人及时收集数据,使用QC手法,从各个角度去层别,作成柏拉图形式直观反映,找出影响问题点的关键项目。
4、本阶段可根据需要使用适当之QC手法,如柏拉图、直方图等。
QCC活动的主要内容六、原因分析1、在圈会上确认每一关键项目。
2、针对选定的每一关键项目,运用脑力激荡法展开特性要因分析。
- 1、下载文档前请自行甄别文档内容的完整性,平台不提供额外的编辑、内容补充、找答案等附加服务。
- 2、"仅部分预览"的文档,不可在线预览部分如存在完整性等问题,可反馈申请退款(可完整预览的文档不适用该条件!)。
- 3、如文档侵犯您的权益,请联系客服反馈,我们会尽快为您处理(人工客服工作时间:9:00-18:30)。
P
序 号 1 2 3 4 5 6 7 8 9
要因验证
通过要因验证表汇总末端因素如下:
末端因素 人员视力差异 治具导电胶压力过 大 治具G/S侧倒角过小 点灯治具卡槽不平 整 机种差异 P检环境照度太暗 搬运不当 作业手顺不统一 TARY盘未交叉 确认内容 人员视力对破片率的影响 程度 治具导电胶的压力程度 确认方 法 调查分 析 现场调 查分析 确认地 点 现场 现场 现场 现场 现场 现场 现场 现场 现场 标准 视力标准1.0 标准压力 负责人 邓继男 肖芳坤 肖芳坤 肖芳坤 邓继男 韦东方 韦东方 郑 琳 完成时间 4月27日 4月29日 5月1日 5月7日 5月8日 5月9日 5月12日 5月13日 5月14日
抱短边
抱长边
抽取5个人观察3天,发现同时抱两批的比例为100% ,抱长边的比例为 29% ,抱短边的比例为 71%。
制表人:韦东方 制表时间:2010年5月12日
P
末因八:搬运不当
日期 5/6 5/7 5/8 5/9 5/10 5/11
要因验证(八)
验证时间:10/5/12人 员:韦东方 方 法 :现场调查
本小组运用脑力激荡法从人、机、料、环、法几个方面进行原因 分析:
人
端 子 部 破 损 机 料 环 法
制表人:韦东方
人员视力差异
治具造成破片
治具G/S侧倒角过小 治具卡槽S侧凹槽太深
机种差异
P检站在帷幕内作业
P检环境照度太暗 搬运不当
作业手法不正确
作业员作业手顺不当 TARY盘未交叉
制表时间:2010年4月22日
报废率(PPM )
76 84 74 79 76 71
5/4
5/5 5/6 5/7 平均
27980
28330 27089 23678 158503
2
2 2 2 12
71
71 74 84 76
要因
光头圈
5/
5/4
5/5
5/6
结论:连续观察6天因此因素造成的报废数据,其报废率为76PPM,占总端子部报废率
例如:轧刚厂轧制钢板,弯曲率达到30%,末端原因之一是“压下量大”, 对工艺规定的压下量25MM是否过大呢? 就需要安排现场的试验、验证,于是安排了试验计划,在其他因素不变的 情况下,把压下量改为20MM,试轧一批钢板,结果弯曲率为8%,有明显 好转,从而判定“压下量大”是主要原因。
一、如何确定主要原因
结论:连续观察6天四种作业手顺点灯的状况,有35次面板与治具碰撞,将碰撞面
板进行外观检查,其中有8PC造成报废,其报废率为55PPM,占端子部报废的19%.
制表人:韦东方 制表时间:2010年5月13日
P 要因验证(十) 末因十: TARY盘未交叉 验证时间:10/5/14
说明:
。
人 员:孙小凤
方 法 :现场调查
P检点灯 为暗室
非要因
帷幕外381LUX 帷幕内29.7LUX
光头圈
环境照度 35LUX以下
1.通过实测P检帷幕内比帷幕外环境照度低351.3(LUX) 2.中小尺寸面板点灯检查作业规范
结论:TSN:TL03-05-000中小尺寸面板点灯检查作业规范要求P检点灯环境照度需管控在35LUX以
下,故P检环境照度不能做改善,因此此因素排除。
关的作业手顺要求,若作业手顺不当很容易造成端子部破损。
A:左手推入式
B:双手推入式
C:右手单放式
D:左手单放式
现场验证:经现场统计P检点灯作业手顺共有以上A、B、C、D四种方式。
报废率(PPM)
60 58 56 54 52 50 48
57 55 55 53
要因
55
光头圈
合计
A 左手推入 B 双手推入 C 右手单放 D 左手单放 式 式 式 式
若TARY盘未交叉TARY盘与TARY盘之间紧密贴合没有空间,面板被TARY盘挤压容易造成破损
未 交 叉
有 交 叉
有交叉数
300 300 300 300 300 300
5.5CM
现场验证:取同样数量的TARY叠放在一起,有交叉高度为“ 5.5CM ”,未交叉 高度为“ 5CM ”。
日期
5/3 5/4 5/5 5/6 5/7 5/8
二、确定主要原因实例
实例:P检面板报废率高,现分析出报废高的 症结在于“端子部破损”,于是针对“端子部 破损”进行原因分析,得到9个末端因素。针 对这9个末端因素逐条进行验证。为使要因确 认严密有序,更好的利用组员的力量来完成, 可制定要因确认计划表,如下例。
P
原因分析
9项末端因素
治具导胶压力大
例如:铸模强度低的末端因素是“砂子含泥量大”,确认时,就要到现场 抽取砂子的样本,测定含泥量为3%,与标准要求含泥量不大于1%不符, 说明砂子含泥量已失控,就能判定它是主要原因。
一、如何确定主要原因
2)、现场试验 有些末端因素是不能直接测量、测试得到的,而要通过试验才能得到作为 证据的数据,这时就要到现场安排试验验证,取得数据,以便作出更科学 的判定。
治具G/S侧导胶过小与面板 是否产生碰撞
点灯治具卡槽卡片对破片 率的影响 机种差异是否照成破片 P检环境照度太暗破片率影 响程度 搬运动作 作业员点灯作业手顺是否 统一 TARY是否交叉
现场调 查分析
现场调 查 现场确 认 现场确 认 调查分 析 现场调 查分析
治具G/S侧倒角处与 面板碰撞率为“0%”
符合 标准 不符合 标准
不是 要因
是 要因
一、如何确定主要原因
4、要因确认通常有以下几种方法:
1)、现场测量、测试 有许多原因,需要到现场测量、测试取得数据,并与标准(要求)进行比 对,如果取得的数据在标准范围内,就可以判定它不是主要影响因素,如 果取得的数据与标准要求有明显的差距,就可以判定它确实是影响问题的 主要原因,以此作为判定依据。
报废率(P P M )
120 100 80 60 40 20 0 4/26 4/27 4/28 4/29 4/30 5/1 平均
71 69 65 72 101 90
78
结论:连续观察6天因此因素的点灯状况,其报废率高达78PPM,占端子部报废率 的27%.
制表人:韦东方 制表时间:2010年5月1日
P
要因验证(四)
验证时间:10/5/7 人 员:肖芳坤 方 法 :现场试验
末因四:点灯治具S侧凹槽太深
说明:点灯治具S侧凹槽太深,在点灯过程中面板端子部S侧易卡在凹槽里,造成面板S侧线路破损。
凹槽太深
碎片残留在治具内
治具数 12
投入数 28800
卡片次数 1250
卡片率 4.34%
经统计P检S侧凹槽太深治具共有12台,每台一天投入2400PC, 一天共投入28800pc,共计卡片1250次,卡片率4.34%. 日期 5/2 5/3 投入数 25270 26156 报废数 2 2 报废率 79 76
非要因
光头圈 20
结论:从上图可以看出,机种与面板报废率之间无相关,为“非要因”
。
制表人:韦东方 制表时间:2010年5月8日
P
要因验证(六)
验证时间:10/5/9 人 员:韦东方 方 法 :现场测量
末因六:P检环境照度太暗
说明:P检为帷幕内作业环境照度比帷幕外暗,上制程后流至P检面板端子部裂纹经P检点灯震动容 易造成裂纹延伸报废。
制表人:韦东方 制表时间:2010年5月9日
P
末因七:搬运不当
面板报废。
要因验证(七)
验证时间:10/5/12 人 员:韦东方 方 法 :现场调查
说明:如果在搬运过程中搬运不当会导致面板滑落及面板左右晃动撞击在TARY盘上造成
现场验证:经现场调查发现同仁在抱面板时均同
抱两批体力 不支
时抱两批,以节省搬运时间,由于P检作业人员多数 为女同仁,在抱面板时存在体力不支导致TAYR盘倾 斜造成面板滑落及面板左右晃动,同时发现他们抱 面板方式也不统一,有的抱长边有的抱短边。
投入数 27089 23678 27833 25907 30535 31173
报废率 1 1 1 1 1 2
报废率 37 42 36 39 33 64 42
80 60 40 20 0
平均
166215 7 报废率(PPM)
要因
光头圈
42
64
37
42
36
39
33
5/6
5/7
5/8
5/9
5/10
5/11
平均
点灯治具卡槽平整 光滑 机种对破片率影响 为0 P检环境照度对破片 率影响为0 标准搬运方式 作业手顺统一一致 TARY100%做交叉
现场确 认
孙小凤
制表人:韦东方
制表时间:2010年4月24日
P
要因验证(一)
验证时间:10/4/27 人 员:邓继男 方 法 :现场调查
末因一:人员视力差异
说明:公司招聘基本要求:人员辨色正常,裸视在1.0 (含)以上。
胶压在面板端子部上导通线路确认品位。如果治具导胶压力过大,易将面板端子部压破。
导胶点灯现象
端子部
端子部
导胶位置
非要因
光头圈
结论:经现场调查,工程调机均使用原材报废面板,如果压力过大时,工程 会及时进行调整,直到调到标准压力可正常点灯为止。因此此因素排除.
制表人:韦东方 制表时间:2010年4月29日
3)、现场调查 有些末端因素是属于人的原因类别,不能直接从现场产测量或现场试验得 到数据,但可以从现场调查中,得到数据加以确认。 例如:对“操作者未及时修整砂轮”这一原因,就可以通过对现场操作进 行随机抽查的方式进行调查确认。 工艺规定每磨10个工件必须重新修整砂轮,在三天的时间内随机抽查10人 次(包含不同班次的操作者)。 调查结果:磨10个工件修整一次砂轮的2人次, 磨15个工件修整一次砂轮的2人次, 磨20个工件修整一次砂轮的5人次, 磨25个工件修整一次砂轮的1人次, 工艺执行率仅为20%,因此,判定“操作者未及时修整砂轮”为主要原因。