制程常见问题
制作过程中的常见错误及解决方法
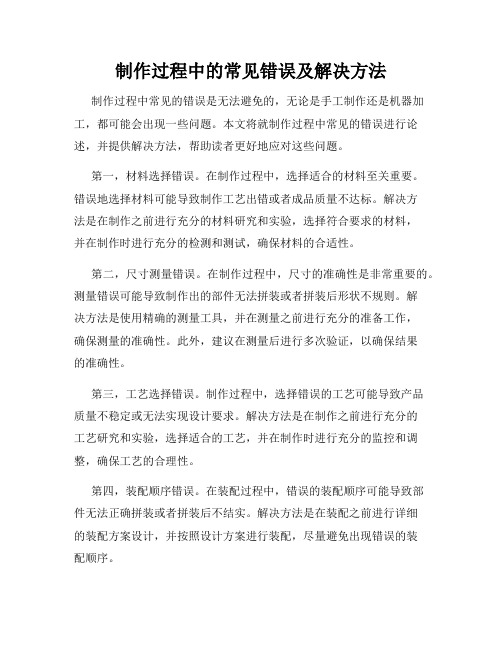
制作过程中的常见错误及解决方法制作过程中常见的错误是无法避免的,无论是手工制作还是机器加工,都可能会出现一些问题。
本文将就制作过程中常见的错误进行论述,并提供解决方法,帮助读者更好地应对这些问题。
第一,材料选择错误。
在制作过程中,选择适合的材料至关重要。
错误地选择材料可能导致制作工艺出错或者成品质量不达标。
解决方法是在制作之前进行充分的材料研究和实验,选择符合要求的材料,并在制作时进行充分的检测和测试,确保材料的合适性。
第二,尺寸测量错误。
在制作过程中,尺寸的准确性是非常重要的。
测量错误可能导致制作出的部件无法拼装或者拼装后形状不规则。
解决方法是使用精确的测量工具,并在测量之前进行充分的准备工作,确保测量的准确性。
此外,建议在测量后进行多次验证,以确保结果的准确性。
第三,工艺选择错误。
制作过程中,选择错误的工艺可能导致产品质量不稳定或无法实现设计要求。
解决方法是在制作之前进行充分的工艺研究和实验,选择适合的工艺,并在制作时进行充分的监控和调整,确保工艺的合理性。
第四,装配顺序错误。
在装配过程中,错误的装配顺序可能导致部件无法正确拼装或者拼装后不结实。
解决方法是在装配之前进行详细的装配方案设计,并按照设计方案进行装配,尽量避免出现错误的装配顺序。
第五,质量控制不严格。
在制作过程中,质量控制的不严格可能导致成品质量不稳定或无法满足设计要求。
解决方法是建立完善的质量控制流程,包括严格的质量检测和测试,并对不合格品进行严肃处理,确保制作过程的质量可控性。
第六,操作不规范。
在制作过程中,操作不规范可能导致设备损坏或者操作者安全事故。
解决方法是在操作之前进行充分的培训和指导,确保操作人员熟悉操作流程和注意事项,并建立相应的操作规范和安全制度。
第七,沟通不畅。
在制作过程中,沟通不畅可能导致信息传递不准确或者无法及时解决问题。
解决方法是建立良好的沟通渠道,确保制作过程中各个环节的沟通顺畅,并及时解决出现的问题。
胶铁制程问题点

胶铁制程问题点
(实用版)
目录
一、胶铁制程的概述
二、胶铁制程中常见的问题
三、问题点的分析与解决
四、总结
正文
一、胶铁制程的概述
胶铁制程,是一种将塑料与金属相结合的制造工艺,主要通过将塑料与金属进行粘合,形成一种结构稳定、性能优越的新型材料。
胶铁制程广泛应用于汽车、家电、建筑等领域,是现代制造业中一种重要的加工方式。
二、胶铁制程中常见的问题
在胶铁制程中,可能会出现一些问题,影响生产效率和产品质量。
常见的问题包括:
1.粘接强度不足:粘接强度不足可能会导致塑料与金属之间的粘接不牢固,容易出现脱落或损坏。
2.胶水选择不当:胶水的选择对粘接效果至关重要。
如果胶水选择不当,可能会导致粘接效果不佳,甚至出现胶水腐蚀金属等问题。
3.粘接工艺参数不合理:粘接工艺参数包括粘接温度、压力、时间等。
如果这些参数设置不合理,可能会影响粘接效果。
4.塑料与金属表面处理不当:塑料与金属表面的处理对于粘接效果至关重要。
如果表面处理不当,可能会导致粘接效果不佳。
三、问题点的分析与解决
针对上述问题,我们可以从以下几个方面进行分析和解决:
1.粘接强度不足:可以通过选择粘接强度高的胶水,或者优化粘接工艺参数,提高粘接强度。
2.胶水选择不当:可以根据实际应用需求,选择适合的胶水,并进行相关试验验证。
3.粘接工艺参数不合理:可以通过试验优化粘接工艺参数,确保粘接效果。
4.塑料与金属表面处理不当:可以加强塑料与金属表面的处理,确保粘接效果。
制程不良原因分析
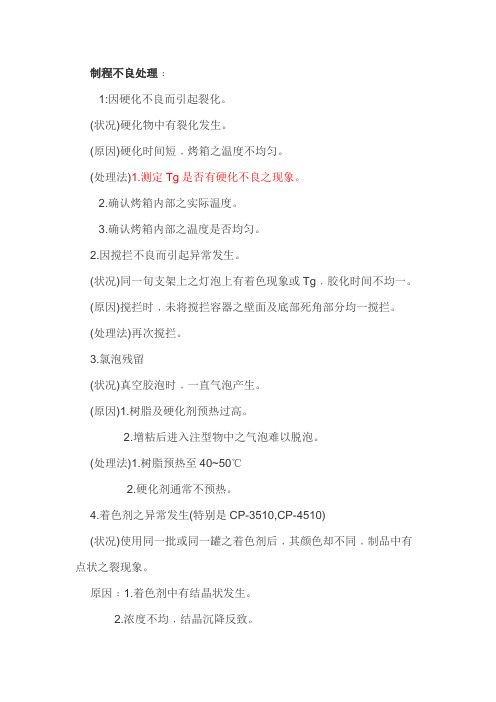
制程不良处理﹕1:因硬化不良而引起裂化。
(状况)硬化物中有裂化发生。
(原因)硬化时间短﹐烤箱之温度不均匀。
(处理法)1.测定Tg是否有硬化不良之现象。
2.确认烤箱内部之实际温度。
3.确认烤箱内部之温度是否均匀。
2.因搅拦不良而引起异常发生。
(状况)同一旬支架上之灯泡上有着色现象或Tg﹐胶化时间不均一。
(原因)搅拦时﹐未将搅拦容器之壁面及底部死角部分均一搅拦。
(处理法)再次搅拦。
3.氯泡残留(状况)真空胶泡时﹐一直气泡产生。
(原因)1.树脂及硬化剂预热过高。
2.增粘后进入注型物中之气泡难以脱泡。
(处理法)1.树脂预热至40~50℃2.硬化剂通常不预热。
4.着色剂之异常发生(特别是CP-3510,CP-4510)(状况)使用同一批或同一罐之着色剂后﹐其颜色却不同﹐制品中有点状之裂现象。
原因﹕1.着色剂中有结晶状发生。
2.浓度不均﹐结晶沉降反致。
(处理法)易结晶﹐使用前100~120 ℃加热溶解后再使用。
5.光扩散剂之异常发生。
(状况)DP-500不易分散﹐扩散剂在灯泡内沉降﹐以致有影子出现。
(原因)添加沉降防止剂变性不同分散不易。
(处理法)加强搅拦。
6.硬化剂之吸湿之异常发生。
(状况)1.有浮游或沉降之不溶解物。
2.不透明成乳白色。
(原因)1.因水酸化后成白色结晶。
2.使用后长期放置。
3.瓶盖未架锁紧。
(处理法)1.使用前确认有无水酸化现象。
2.防湿措施。
7.Disply case 中有气泡残留。
(状况)长时间脱泡后制品中仍有气泡残留。
(原因)1.增粘效果现象发生﹐不易脱泡。
2. Disply case之封胶用粘着胶带有问题。
(处理法)1.确认预热温度搅拦时间﹐真空脱泡之时间,真空度。
2.真空度不可过高。
3.树脂过当预热。
4.灌胶前case预热。
制程问题点分析

制程问题点汇总不良现象一:装配时手柄不易装入盖板内综上数据统计:新手柄与盖板配合间隙小于旧手柄与盖板配合间隙,新盖板宽度尺寸小于图纸规格不良现象二:新盖板装入底座时两边耳朵翘起不易配合到底座卡槽内5 1.7880.0486 1.7910.04271.7880.06781.8060.04791.7940.059101.8050.052111.8040.057121.8060.047131.8040.053141.8030.05615 1.8020.0561.855 1.7951.853无毛边1.836 1.6811.833无毛边1.7941.853无毛边1.853 1.7861.857无毛边1.858无毛边1.857无毛边1.859无毛边1.861 1.7551.7571.7491.7521.7651.776新盖板毛刺不良现象如下:就盖板CCD观测表面无毛刺,详细如下:综上数据统计,取样检验15PCS,发现存在毛边不良6PCS,不良率40%,新底座盖板与底座的配合间时两边耳朵翘起不易配合到底座卡槽内主因为新盖板与底座卡槽配合位置存在毛刺,详细如下:1.7621.7641.7561.7581.755纸规格导致装配时手柄不易装入盖板内。
1.6810.0681.6820.0731.6910.0661.6850.081.6830.0931.6820.0731.6820.071.6830.0731.6810.0771.6820.081.6810.0831.755无毛边1.757无毛边1.749无毛边无毛边1.752无毛边1.765无毛边1.776无毛边配合间隙小于旧底座盖板与底座的配合间隙,但新底座装入底座,详细如下:1.762无毛边1.764无毛边1.756无毛边1.758无毛边1.755。
制程不良的分析报告
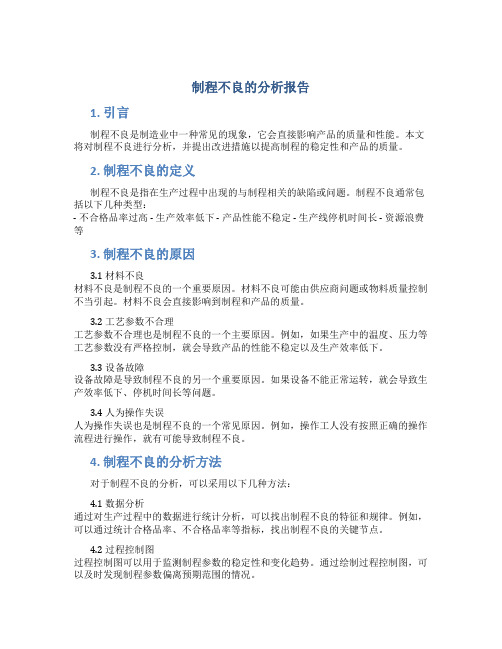
制程不良的分析报告1. 引言制程不良是制造业中一种常见的现象,它会直接影响产品的质量和性能。
本文将对制程不良进行分析,并提出改进措施以提高制程的稳定性和产品的质量。
2. 制程不良的定义制程不良是指在生产过程中出现的与制程相关的缺陷或问题。
制程不良通常包括以下几种类型:- 不合格品率过高 - 生产效率低下 - 产品性能不稳定 - 生产线停机时间长 - 资源浪费等3. 制程不良的原因3.1 材料不良材料不良是制程不良的一个重要原因。
材料不良可能由供应商问题或物料质量控制不当引起。
材料不良会直接影响到制程和产品的质量。
3.2 工艺参数不合理工艺参数不合理也是制程不良的一个主要原因。
例如,如果生产中的温度、压力等工艺参数没有严格控制,就会导致产品的性能不稳定以及生产效率低下。
3.3 设备故障设备故障是导致制程不良的另一个重要原因。
如果设备不能正常运转,就会导致生产效率低下、停机时间长等问题。
3.4 人为操作失误人为操作失误也是制程不良的一个常见原因。
例如,操作工人没有按照正确的操作流程进行操作,就有可能导致制程不良。
4. 制程不良的分析方法对于制程不良的分析,可以采用以下几种方法:4.1 数据分析通过对生产过程中的数据进行统计分析,可以找出制程不良的特征和规律。
例如,可以通过统计合格品率、不合格品率等指标,找出制程不良的关键节点。
4.2 过程控制图过程控制图可以用于监测制程参数的稳定性和变化趋势。
通过绘制过程控制图,可以及时发现制程参数偏离预期范围的情况。
4.3 原因分析对制程不良的原因进行分析,可以帮助我们找出问题的根源。
常见的原因分析方法包括5W1H法、鱼骨图、因果关系图等。
5. 制程不良的改进措施为了提高制程的稳定性和产品的质量,可以采取以下改进措施:5.1 加强材料质量控制合理选择供应商,并建立供应商质量管理体系,加强对采购材料的质量控制。
5.2 优化工艺参数通过对工艺参数的优化调整,确保制程参数在合理范围内,并加强对工艺参数的监控。
(整理)制程异常分析改善汇总.

防焊前五项制程问题分析: 一、防焊空泡:造成原因:1、前处理不良。
(H2SO4浓度、水质、吹干段角度及风量,吸水海棉清洁度、烘干温度)。
2、磨刷后放置时间过长,室内湿度偏低。
3、印刷台面沾有油墨及其它有机溶剂,反沾板面,油墨搅拌不均。
4、预烤不足。
5、曝光能量太低或太高。
6、显影侧蚀太多。
7、HAL浸助焊剂时间太长,锡槽温度太高,浸锡时间太长。
预防措施:1、前处理作业必须按SOP要求生产。
2、磨刷后放置时间不得超过2H ,室内湿度控制在50-60%之间。
3、印刷台面保持清洁,印第一面时台面上垫一张白纸,以保证板面清洁度。
4、预烤温度保持70±2℃,烤后之板保证不粘棕片。
5、曝光能量保持在9-13格。
6、显影点控制在50-60%,避免过多侧蚀。
7、后烤通风保持良好,塞孔板必须分段烘烤。
8、HAL作业须完全按照SOP操作,不可有违规作为。
二、L/Q内圈阴影:原因分析:1、油墨过期。
2、预烤时间过长,温度过高。
3、挡点印刷时,孔环处积墨过多,印刷房湿度不够。
4、曝光前,静置时间过长。
5、显影速度过快,压力过小。
6、棕片遮光度不够。
7、曝光时吸真空压力未能达到要求。
改善对策:1、油墨按照先进先出的方式使用,保证在油墨保质期内使用。
2、预烤时间和温度按SOP要求作业,且烤好后及时取出防止冷烤。
3、印刷房湿度保持在50-60%之间,挡点印刷保持连贯,且印一PNL刮一次网版。
4、预烤后板静置时间不能眼过12H,最连贯4H以内对位完。
5、显影点保持在50-60%之间。
6、选用遮光度及质量较好之棕片生产。
7、吸真空不得低于600㎜Hg,且须保持导气良好。
三、卡锡珠:原因分析:1、印刷塞孔不满(量产板)。
2、退洗板导通孔内油墨未剥除干净。
3、油墨本身质量问题。
4、HAL贴胶未贴好,某些孔呈半覆盖状态。
5、HAL浸助焊剂及浸锡时间过短。
改善对策:1、从印刷各条件去改善塞孔程度。
(刮刀压力、角度、确度、速度、网目T数量)2、选用适合的退洗液,尽可能洗净导通孔内油墨,保证塞孔效果。
生产制程问题改善措施

生产制程问题改善措施引言在制造业中,生产制程问题是不可避免的。
这些问题可能会导致生产效率低下、产品质量下降和成本增加。
因此,对生产制程问题进行改善是非常重要的。
本文将讨论一些常见的生产制程问题,并提出改善措施。
问题一:生产效率低下低生产效率是制造业中经常面临的问题。
主要原因可能包括设备故障、工艺不合理和操作不当等。
下面是一些建议来改善生产效率:•定期维护和保养设备,以确保设备正常运行并减少故障的发生。
•优化生产工艺,通过分析数据和流程改进来减少生产时间。
•提供员工培训,确保操作规范和高效。
问题二:产品质量下降产品质量下降是另一个常见的生产制程问题。
有几个因素可能导致产品质量下降,如原材料质量不合格、错误的工艺参数和人为错误。
以下是改善产品质量的一些建议:•建立严格的原材料供应链管理,确保原材料质量符合要求。
•控制工艺参数,确保每一步工艺都按照规范执行。
•培训员工,提高操作技能和质量意识。
问题三:成本增加成本增加是制造业中一直受到关注的问题。
高成本可能是由于原材料价格的上涨、废品率的增加和设备维修费用的增加等问题引起的。
以下是降低成本的一些建议:•寻找替代的原材料来源,以降低原材料成本。
•优化工艺流程,减少废品率,并提高产品质量。
•定期维护设备,减少维修费用,并延长设备使用寿命。
结论生产制程问题对制造业的影响非常大,可以导致低生产效率、产品质量下降和成本增加。
然而,通过采取一系列改善措施,可以有效地解决这些问题。
定期维护设备、优化工艺流程和培训员工等措施可以提高生产效率和产品质量,并降低成本。
制造业应该重视生产制程问题,并积极寻找解决方案,以提高竞争力和可持续发展。
SMT制程不良原因及改善对策

SMT制程不良原因及改善对策SMT制程(Surface Mount Technology)是一种常用的电子组装技术,广泛应用于电子产品的制造过程中。
然而,由于各种原因所引起的不良现象在SMT制程中时有发生。
本文将讨论SMT制程不良原因以及改善对策。
1.焊接不良:焊接不良可以导致焊点虚焊、焊接断裂等问题。
常见的原因包括焊接温度不够、焊接时间不足、焊接设备不稳定等。
改善对策包括提高焊接设备的质量和稳定性、增加焊接温度和时间的控制精度等。
2.贴装不良:贴装不良可以导致元件偏移、元件漏贴等问题。
常见的原因包括贴装位置错误、贴装头磨损、胶垫损坏等。
改善对策包括提高贴装机的精度和稳定性、定期更换贴装头和胶垫等。
3.元件损坏:元件在SMT制程中容易受到机械损伤、电静电等因素的影响而受损。
改善对策包括提供合适的防护措施,如使用防静电设备、增加元件存储和运输的保护等。
4.焊盘不良:焊盘不良可以导致焊点接触不良、导致电路连通性问题。
常见的原因包括锡膏质量不佳、焊盘形状不准确等。
改善对策包括使用高质量的锡膏、提高焊盘生产过程的精度等。
5.引脚弯曲:引脚弯曲会导致元件无法正确插入或连接。
常见的原因包括元件存储和运输过程中引脚受到碰撞、搬运过程中的不当操作等。
改善对策包括提供合适的存储和运输保护措施、培训操作人员正确操作等。
改善SMT制程不良有很多对策,下面列举了其中一些常见的:1.提高设备的质量和稳定性:定期对设备进行维护和保养,确保其正常运行和精度稳定。
采用高质量的设备和工具,可大大降低不良率。
2.优化工艺参数:根据产品要求和设备特性,合理的调整焊接温度、焊接时间等工艺参数,以确保焊接效果和质量。
3.加强员工培训:提供必要的培训和指导,使操作人员熟悉SMT制程的原理和操作技巧,减少人为失误和操作不当导致的不良。
4.严格品质管理:建立完善的品质管理体系,包括设备校验、材料检测、过程控制等环节,确保产品质量稳定。
5.提供合适的存储和运输保护:对元件进行正确的存储和运输保护,避免机械损伤、静电损伤等因素导致的元件损坏。
- 1、下载文档前请自行甄别文档内容的完整性,平台不提供额外的编辑、内容补充、找答案等附加服务。
- 2、"仅部分预览"的文档,不可在线预览部分如存在完整性等问题,可反馈申请退款(可完整预览的文档不适用该条件!)。
- 3、如文档侵犯您的权益,请联系客服反馈,我们会尽快为您处理(人工客服工作时间:9:00-18:30)。
SMT常见工艺问题简述 SMT常见工艺问题概述(一)锡膏制程(一)普通锡膏(63/37)普通锡膏于制程中常见的工艺问题主要为以下几种:元件竖立,短路,冷焊,偏移,锡珠1.元件竖立元件竖立又叫“曼哈顿效应“。
主要是由于元件两端焊锡浸润不均匀,因此,熔融焊料的不够均衡的表面张力拉力就施加在元件的两端上,引发此类不良的原因较多,但主要有三大类。
即:A.元件不良:元件两端电极氧化或附有异物,导致焊锡时上锡不良;基板材料导热性差,基板的厚度均匀性差;焊盘的热容量差异较大,焊盘的可焊性差异较大;锡膏中助焊剂的均匀性差或活性差。
B.设计缺失:焊盘铜箔大小不一或一端连接有接地等较大的铜箔,造成回流时焊盘两端受热不均匀。
C.制程缺失:制程缺失的因素很多。
如两个焊盘上的锡膏厚度差异较大,锡膏太厚,印刷精度差,错位严重;预热温度太低;贴装精度差,元件偏移严重等。
以上三种成因中第一项就不用赘述了。
只要严把进料和储存两关就好了。
下面简述一下二,三两项成因的控制方法。
——对于设计上的缺失,长期办法当然是修改设计方案。
短期办法或没法修改方案的情况下,就需要从二个方面入手。
一是通过更改钢网的开口设计来达到控制的目的。
即将铜箔较小的一端焊盘网孔局部加大,使之与大铜箔大小比例为1:1。
从而降低焊盘两端锡膏回流时的时间差;二是修改炉温曲线,即延长升温区(回流前)的时间,降低升温速率,使整块PCB上各点的温度尽量保持平衡。
从而避免因回流时的温度不平衡而导致元件受力竖起。
——制程缺失产生的原因就更多了。
一个公司制程品质的好坏不在于有多么先进的设备,关键在于制程控制的方法和管理的力度上。
好的控制方法应该从原材料的采购,进料的检验,储存环境和储存条件的设定等做起,每一环节都切实履行自己的职责,再到原物料的使用(包括使用环境,使用条件等工艺参数的设定)和设备的维护保养,校正以及参数设定,操作人员的培训和管理等,需要一个贯穿始终,环环相扣,职责分工明确又相互关联的控制系统。
在各个职能部门和相关工作人员的通力协作下才能臻至理想状态。
这一点,每个公司有每个公司的做法和不同的控制体系。
具体的操作就是仁者见仁,智者见智了。
2.短路短路这种不良现象多发于细间距IC的引脚之间,所以又叫“桥接“。
当然也有CHIP件之间发生短路现象的,那是极少数。
下面就细间距IC引脚间的桥接问题浅谈它的诚因及解决方法。
桥接现象多发于0.5mm及以下间距的IC引脚间,因其间距较小,故模板设计不当或印刷稍有疏漏就极易产生。
A.模板依据IPC-7525钢网设计指南要求,为保证锡膏能顺畅地从网板开孔中释放到PCB焊盘上,在网板的开孔方面,主要依赖于三个因素:1、)面积比/宽厚比>0.662、)网孔孔壁光滑。
制作过程中要求供应商作电抛光处理。
3、)以印刷面为上面,网孔下开口应比上开口宽0.01mm或0.02mm,即开口成倒锥形,便于焊膏有效释放,同时可减少网板清洁次数。
具体的说也就是对于间距为0.5mm及以下的IC,由于其PITCH小,容易产生桥接,钢网开口方式长度方向不变,开口宽度为0.5~0.75焊盘宽度。
厚度为0.12~0.15mm,最好使用激光切割并进行抛光处理,以保证开口形状为倒梯形和内壁光滑,以利印刷时下锡和成型良好。
B.锡膏锡膏的正确选择对于解决桥接问题也有很大关系。
0.5mm及以下间距的IC使用锡膏时应选择粒度在20~45um,黏度在800~1200pa.s左右的,锡膏的活性可根据PCB表面清洁程度来决定,一般采用RMA级。
C.印刷印刷也是非常重要的一环。
(1)刮刀的类型:刮刀有塑胶刮刀和钢刮刀两种,对于PITCH≤0.5mm的IC,印刷时应选用钢刮刀,以利于印刷后的锡膏成型。
(2)刮刀的调整:刮刀的运行角度以45°的方向进行印刷可明显改善锡膏不同模板开口走向上的失衡现象,同时还可以减少对细间距的模板开口的损坏;刮刀压力一般为30N/mm²。
(3)印刷速度:锡膏在刮刀的推动下会在模板上向前滚动。
印刷速度快有利于模板的回弹,但同时会阻碍锡膏漏印;而速度过慢,锡膏在模板上将不会滚动,引起焊盘上所印的锡膏分辨率不良,通常对于细间距的印刷速度范围为10~20mm/s(4)印刷方式:目前最普遍的印刷方式分为“接触式印刷”和“非接触式印刷”。
模板与PCB之间存在间隙的印刷方式为“非接触式印刷”。
一般间隙值为0.5~1.0mm,其优点是适合不同黏度锡膏。
锡膏是被刮刀推入模板开孔与PCB焊盘接触,在刮刀慢慢移开之后,模板即会与PCB自动分离,这样可以减少由于真空漏气而造成模板污染的困扰。
模板与PCB之间没有间隙的印刷方式称之为“接触式印刷”。
它要求整体结构的稳定性,适用于印刷高精度的锡膏,模板与PCB保持非常平坦的接触,在印刷完后才与PCB脱离,因而该方式达到的印刷精度较高,尤适用于细间距、超细间距的锡膏印刷。
贴装的精度是首先必须保证的,其次是贴D.贴装装的高度,对于PITCH≤0.5mm的IC在贴装时应采用0距离或者0~-0.1mm的贴装高度,以避免因贴装高度过低而使锡膏成型塌落,造成回流时产生短路。
E.回流1、升温速度太快2、加热温度过高3、锡膏受热速度比电路板更快4、焊剂润湿速度太快。
3.冷焊冷焊是指在元件电极或引脚与电路板焊点之间没有形成焊接点。
一般来说,这可归因于以下四方面的原因:1、焊锡熔敷不足 2、引脚共面性差 3、润湿不够4、焊锡损耗,这是由镀锡板上锡膏塌落,引脚的芯吸作用或焊点附近的通孔引起的引脚的芯吸作用可以通过减慢加热速度以及让底面比顶面受热更多来加以解决,此外,使用润湿速度较慢的焊剂,较高的活化温度也能最大限度地减少芯吸作用.用焊锡掩膜来覆盖连接路径也能防止由附近的通孔引起的芯吸作用。
4.偏移偏移是指元件两端或IC引脚在回流后超出焊盘范围或歪斜。
产生的原因主要是(1)贴装精度不够造成元件偏移(2)贴装压力太大破坏了锡膏的完整性(3)元件太轻,锡膏太厚解决的办法是调整贴装精度;调整贴装高度,使元件贴装完成后是轻放在锡膏上面,而不是陷入锡膏中破坏其完整性,这样在回流时通过锡膏熔融时产生的拉力使元件自动校正完成焊接。
5.锡珠锡珠就是指锡膏在回流后产生的一个个焊锡球.它们形成在具有极低的托脚的元件如高电容的周围。
锡珠是由焊剂排气而引起,在预热阶段这种排气作用超过了锡膏的内聚力,排气促进了锡膏在低间隙元件下形成孤立的颗粒,在熔融时,熔化了的孤立锡膏再次从元件下冒出来,并聚结起形成锡珠。
锡珠的成因包括: 1、焊点和元件重叠太多 2、在元件下涂了过多的锡膏 3、贴装元件的压力太大,使锡膏被挤出元件电极两端4、预热时温度上升速度太快 5、预热温度太高 6、湿气从元件和阻焊料中释放出来 7、焊剂的活性太高 8、所用的粉料太细 9、金属负荷太低 10、印刷成型不好,锡膏塌落太多 11、锡粉氧化物太多 12、锡膏回温不足,吸收了空气中的水分 13、PCB吸潮 14、PCB焊盘上有阻焊物,造成回流时上锡不良。
解决锡珠可从以下几方面如手:(1)模板:改变传统的开口方法,将开口设计成半圆、凹形或菱形,以减少锡膏印刷量及贴装时挤压溢出的可能性。
(2)调节回流温度,使预热温度缓慢上升和加长预热时间。
(3)充分保证锡膏满足回温时间。
(4)吸潮的PCB应先预烤4~6小时,温度为80~110℃(二)高温锡膏高温锡膏制程中常见的工艺问题主要为:元件竖立空焊偏移1.元件竖立元件竖立在高温锡膏制程中为发生率最高的不良项目,这是因为高温锡膏的熔融温度很高(245℃),一般的电子元件两端电极在高温下均会出现不同程度的氧化现象,若有元件的电极在达到熔融温度之前氧化,则回流时就会产生上锡不良而被锡膏的熔融拉力拉起造成竖立。
另外,在高温锡膏制程中若PCB焊盘设计不当(大小不对称),则产生竖件的可能性将会比普通锡膏高。
要有效防止元件竖立的发生,除应该注意普通锡膏制程中的关键点外,还应该在回流曲线上有所改进。
即使PCB从常温升至175℃的时间保持在80~95S之间,从175℃~245℃的时间保持在45~60S之间,245℃以上的时间保持在30S左右。
这样,将会最大限度的减少竖立的发生。
2.空焊高温制程中的空焊问题是仅次于元件竖立的又一大难关。
其形成的原因除普通制程中的焊锡熔敷不足、引脚共面性差、润湿不够、焊锡损耗外,还有一种就是由于高温制程中回流的温度很高,造成锡膏中的活性剂挥发过多,而高温锡膏的流变性本来就较普通锡膏差,故此锡膏在回流时产生了一层氧化膜而阻碍了焊点的形成。
解决的办法是降低预热区温度,使预热区温度缓慢上升(1.5~2℃/S);延长预热时间(由90S 左右延长至120S左右)。
3.偏移因高温锡膏的流变性较差,故防止偏移的最好办法是保证贴装的精确度。
电子元件产生虚焊的原因与规律对于电子设备来说,特别是使用时间较长的电站设备来说,内部的元件出现虚焊造成接触不良现象是常见的故障之一,也是比较难于超找的故障。
1、元件产生虚焊的常见原因(1)焊锡熔点比较低,强度不大由于焊锡熔点低,而元件引脚和固定元件的板子材料不同,其热膨胀系数不同,日久后,伴随着元件工作温度的变化,在热胀冷缩的作用下,就会产生虚焊现象。
(2)元件引脚存在的应力现象如果元件安装不到位,或者元件比较重,或者固定元件的线路板存在变形,都会使得元件引脚对其焊点产生应力作用,在这个应力作用的长期作用下,就会产生虚焊现象。
(3)焊接时用锡量太少在安装或维修过程中,焊接元件时用锡量太少,时间长后就比较容易产生虚焊现象。
(4)元件产生的高温引起其固定点焊锡变质有的元件会产生较高的温度,在长期的高温作用下,固定点的焊锡重者会发生脱焊,轻者出现虚焊故障。
(5)元件引脚安装时没有处理好在元件安装时或者在维修过程中,没有处理很好地对元件的引脚进行去脂去氧气层处理,或镀锡不好,这也是产生虚焊的常见(6)焊锡本身质量不良如果同时有很多点都出现了虚焊的故障,多数原因是因为焊锡本身质量不好引起的。
(7)线路板敷铜面质量不好焊接之前线路板敷铜没有很好地进行去脂去氧化层和加涂敷、助焊处理,造成吃锡效果为好,日久后出现了虚焊现象。
2、虚焊点容易发生的部位(1)体积和重量比较大的元件因为元件本身的重量比较大,在安装或搬运的过程中容易产生应力。
久后元件引脚就会逐渐与线路板分离,产生虚焊。
(2)经常会受到外力作用的元件在电子设备中,为了与其他设备连接方便,设置了插接件,还有如各种微动开关之类器件。
若这些经常受到外力作用或者使用不当会使这些元件产生松动,久而久之产生虚焊。
(3)工作温度比较高的元件在电子设备中,不可避免地存在着一些工作温度比较高的元件,比如大功率电阻,大功率开关管和散热器周围元件等,这些元件由于本身的温度比较高,在热胀冷缩作用下其引脚很容易产生虚焊现象。