乙烯的生产之深冷分离
乙烯的生产-深冷分离

目前工业上对裂解气大多采用三至五段压缩。 由于裂解炉的废热锅炉副产高压蒸汽,因此多 用蒸汽透平驱动的离心式压缩机。
(二)制冷
1、冷冻循环制冷 2、节流膨胀制冷 3、热泵
1、冷冻循环制冷
制冷原理
冷冻剂自液态汽化时,要从物料中吸收热量, 使物料温度降低。所吸收的热量,在热值上等于 它的汽化潜热。
在这个系统中,冷水向丙烯供冷,丙烯向乙烯供 冷,乙烯向甲烷供冷,甲烷向低于-100℃冷量用 户供冷。
2、节流膨胀制冷
所谓节流膨胀制冷,就是气体由较高的压 力通过一个节流阀迅速膨胀到较低的压力,由 于过程进行得非常快,来不及与外界发生热交 换,膨胀所需的热量,必须由自身供给,从而 引起温度降低。
在石油化工深冷分离中使用最广泛的是氨、丙 烯和乙烯等。对乙烯装置而言,乙烯和丙烯为本 装置产品,已有贮存设施,且乙烯和丙烯已具有 良好的热力学特性,因而均选用乙烯和丙烯作为 制冷剂。
(2)丙烯制冷系统
丙烯常压下沸点为 - 47.72 ℃,用丙烯作 冷冻剂可以得到-40℃以上温度级的冷量。
把丙烯压缩到 l.864MPa 的条件下,丙烯的 冷凝点为45℃,很容易用冷水冷却使之液化。
(4)乙烯—丙烯复迭制冷循环
(5)三元复迭制冷
用乙烯作制冷剂在正压下操作,不能获得-103℃ 以下的低温。
生产中需要-103℃以下的低温时,可采用沸点更 低的制冷剂,甲烷在常压下沸点是-161.5℃。但 是由于甲烷的临界温度是-82.5℃,若要构成冷 冻循环制冷,需用乙烯作制冷剂为其冷凝器提供 冷量,这样就构成了甲烷-乙烯-丙烯三元复迭 制冷。
C2H4 -104 -55 -39 -29 -20 -13
乙烯生产工艺流程组织—裂解气的分离流程的组织
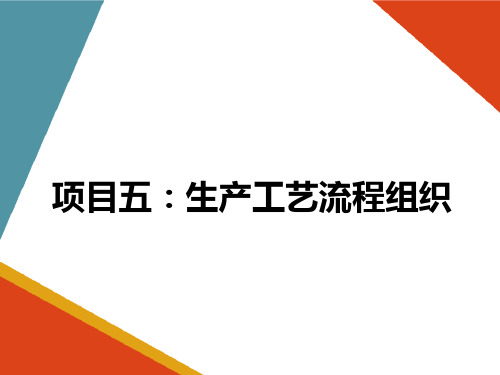
任务三 裂解气的分离流程的组织
二.前脱乙烷流程 前脱乙烷分离流程的特点是: 由于脱乙烷塔的操作压力比较高,这样势必
任务三 裂解气的分离流程的组织
任务三 裂解气的分离流程的组织
一.顺序分离流程
裂解气经过离心式压缩机一、二、三段压缩,压 力达到1MPa,送入碱洗塔,脱去H2S、CO2等酸 性气体。碱洗后的裂解气经过压缩机的四、 五段 压缩,压力达到3.7MPa. 经冷却到15℃,去干燥 器用3A分子筛脱水,使裂解气的露点温度达到70℃左右。
任务三 裂解气的分离流程的组织
一.裂解气组成
二、裂解气的净化
(一) 酸性气体的脱除
1、酸性气体的来源
• CO2,H2S和其他气态硫化物 • 气体裂解原料带入的气体硫化物和CO2 • 液体裂解原料中所含的硫化物高温氢解生成
的CO2和H2S • 结炭与水蒸气反应生成CO和CO2 • 裂解炉中有氧进入时,氧与烃类反应生成CO2
(1)催化剂 活性组分:钴(Co)、镍(Ni)、钯
(Pd) 助催化剂:铁(Fe)和银(Ag) 载体:分子筛或a-Al2O3
催化加氢脱炔的工艺方法
前加氢 利用裂解气中H2进行加氢 特点:流程简单,投资少。但操作稳定性差。
后加氢 先分离出C2、C3后,再分别加氢 特点:温度易控,不易飞温。
(5) 乙烯精馏塔 将乙烯与乙烷进行分离的塔,称乙烯精馏塔,
简称乙烯塔。 (6) 丙烯精馏塔
将丙烯与丙烷进行分离的塔,称丙烯精馏塔, 简称丙烯塔。
任务三 裂解气的分离流程的组织
三.塔的操作条件与相对挥发度
各塔中的组分的相对挥发度和分离的难易程 度见表6-1。从沸点数据可以看出,不同碳 原子数的烃类易分,同碳原子数的烃类难分。 一般先将不同碳原子数的烃类分开,再分离 同一碳原子数的烯烃和烷烃,采取先易后难 的分离顺序。
乙烯1-6第一章乙烯生产(6)

图1-30 前脱氢高压脱甲烷工艺流程(Lummus) p95
2.C2馏分的分离 P96
图1-31 前脱乙烷法C2分离流程(Linde公司) P97 • C2馏分的分离包括脱乙烷和乙烯精馏系统。 • 脱乙烷塔的目的是从裂解气中分离出C2馏分。 • 前脱乙烷流程:脱乙烷塔顶出甲烷-氢、C2馏分,去脱甲烷塔脱除甲烷
与空气的爆炸极限 (V%)
上限
下限
27.0
15.5
丙烯 -42.7 -185.25 437.94 4.61 丙烷 -42.07 -187.69 426.22 4.25
91.6 96.67
11.1
2.0
9.5
2.37
乙烯 -103.71 -169.15 482.74 5.03
乙烷 -88.63 -183.27 489.86 4.88
( 2 )典型的工艺流程
裂解气
去火炬
裂解汽油
汽 油 汽 提 塔
LS 裂解汽油 回水洗塔
CW
凝水 凝液
脱
闪
凝
酸 性 气
C =2R
蒸
液
罐
汽
提
塔
CW
CW
CW
QW
CW LS
裂解气去 分离系统
一段
二段
三段
四段
五段
图 1-26 裂解气五段压缩工艺流程
去脱丙烷塔
• 段间设水冷器及吸入罐 ( 气液分离罐) ,裂解气凝 液在吸入罐中分层,水相返回水洗塔,油相送汽 油汽提塔或凝液汽提塔。
模万t/ 数 量
分子 温度 温度 压力 压 力
a
公斤/h 量 ℃ ℃ kPa kPa
备注
一 136339 28.4 44 二 127887 27.9 41 30 三 122677 27.4 41 四 126181 27.1 40 五 121166 26.5 41
乙烯的生产工艺介绍

乙烯的生产工艺介绍生产乙烯的重要核心过程就是分离过程,目前世界乙烯装置分离技术主要分为3大类,即顺序分离技术、前脱乙烷前加氢技术和前脱丙烷前加氢技术。
经过几十年的发展乙烯装置的分离流程,通过不断改进,已发展出几种不同的分离路线[3]。
1顺序分离技术深冷分离技术中,顺序分离技术应用的最早也最广泛。
在顺序分离技术中,是把关键组分的相对挥发度最接近1的乙烯和乙烷、丙烯和丙烷的分离放到流程的最后,首先按照从轻到重的顺序,将裂解气中的各个组分进行分离。
其典型流程主要包括:裂解气急冷、裂解气压缩、裂解气分离及制冷系统等几个主要部分[3],见图1-2。
图1-2典型的顺序分离流程示意(1)裂解气急冷重裂解汽油组分分离出来后,一部分作为急冷油塔的回流,一部分送至汽油汽提塔。
急冷油塔底部采出裂解燃料油,经燃料油汽提塔汽提,来控制闪点,并且冷却。
裂解气急冷部分还包括稀释蒸汽发生系统,它的作用是为裂解炉提供稀释蒸汽。
(2)裂解气压缩裂解气从急冷水塔中出来后进入裂解气压缩机一段吸入罐,压缩后经一段后冷器冷却进入压缩机二段吸入罐,然后分别进入压缩机三、四、五段吸入罐(3)裂解气分离裂解气经过干燥后依次经过脱乙烷塔进料、乙烯精馏塔、中间再沸器和丙烯冷剂冷却,进入脱甲烷塔,塔顶要控制乙烯损失在0.3%一下。
塔釜再沸器用丙烯冷剂回收冷量作为热源,塔釜液送进脱乙烷塔,塔釜控制乙烷含量在0.04%以下,塔顶控制丙烯含量在0.25%以下,乙炔选择加氢生成乙烯和乙烷,塔顶气相经乙烯干燥器后进乙烯精馏塔。
世界上乙烯装置采用最为广泛的一种乙烯分离技术就是顺序分离技术,随着技术进步以及节能减排的要求不断提高,各个行业也在传统的顺序流程的基础上开发了不少新的分离技术,为乙烯分离技术做了很大的改进。
2前脱乙烷分离技术图1-3前脱乙烷前加氢技术前脱乙烷技术的主要特点就是指分离流程的第一个塔为脱乙烷塔[4]。
见图1-3裂解气经急冷、压缩后预冷,首先进人脱乙烷塔系统,C2组分和C3以上组分先分开。
项目一、乙烯的生产

(一)反应原理
CO2 +2NaOH→Na2CO3 + H2O
H2S +2NaOH→Na2S+2H2O
NaOH吸收剂不可再生
(二)碱洗工艺流程
塔分三段:I段水洗塔为泡罩塔板
Ⅱ段和Ⅲ段为碱洗段填料层
碱液浓度由上而下降低:新鲜碱液含量为18%~20%,Ⅱ段循环碱液NaOH含量约为5~7%Ⅲ段循环碱液NaOH含量为2%~3%.流程图(略)
1.原料油供给和预热系统
2.裂解和高压蒸汽系统
3.急冷油和燃料油系统
4.急冷水和稀释水蒸汽系统
第二节裂解气的净化与分离技术
一、裂解气的组成与分离方法
1、组成
烃类:CH4、C2H2、C2H4、C2H6、C3H4、C3H6、C3H8、C4、C5、C6~204℃馏分
非烃类:H2、H2O、CO、CO2、H2S
所以从动力学分析得出:降低压力可增大一次反应对于二次反应的相对速度。
故无论从热力学还是动力学分析,降低裂解压力对增产乙烯的一次反应有利,可抑制二次反应,从而减轻结焦的程度。
(3).稀释剂的降压作用
如果在生产中直接采用减压操作,因为裂解是在高温下进行的,当某些管件连接不严密时,有可能漏入空气,不仅会使裂解原料和产物部分氧化而造成损失,更严重的是空气与裂解气能形成爆炸性混合物而导致爆炸。另外如果在此处采用减压操作,而对后继分离部分的裂解气压缩操作就会增加负荷,即增加了能耗。工业上常用的办法是在裂解原料气中添加稀释剂以降低烃分压,而不是降低系统总压。
另外从以上讨论,可以归纳各族烃类的热裂解反应的大致规律:
烷烃—正构烷烃最利于生成乙烯、丙烯,是生产乙烯的最理想原料。
环烷烃—在通常裂解条件下,环烷烃脱氢生成芳烃的反应优于断链(开环)生成单烯烃的反应。含环烷烃多的原料,其丁二烯、芳烃的收率较高,乙烯的收率较低。
炼厂干气中乙烯回收和利用技术进展

炼厂干气中乙烯回收和利用技术进展炼厂干气主要来自原油的二次加工,如催化裂化,热裂化,延迟焦化等,其中催化裂化的干气量最大,产率也最高[1,2]。
干气中含有氢气、氮气、甲烷、乙烯、乙烷等,其中催化裂化干气中乙烯的含量约占15%[3]。
过去因为没有合适的分离回收和综合利用技术,大多数干气当作为燃料气使用或放火炬烧掉,造成了极大的资源浪费和环境污染[4]。
据统计,随着炼油企业的发展,国内催化裂化装置能力已经达到93Mt/a,每年生产的干气产量约为4.14Mt,其中含有乙烯730Kt左右[5]。
若炼厂干气回收轻烃技术能全面推广,每年可以节约用于生产乙烯的轻质油4.15Mt,创造效益上百亿元[6]。
因此,回收利用炼厂干气已经成为炼油企业降低乙烯生产成本和实现资源有效利用的重要手段。
目前,炼厂干气中乙烯回收利用技术分为两大类:一是通过对干气的精制,然后对干气中的乙烯进行浓缩,最后通过分离回收得到聚合级的乙烯;二是用干气作为原料,利用其中的稀乙烯,直接生产乙苯、环氧乙烷、丙醛等。
本文重点对国内外回收利用干气技术进行了综述。
1 炼厂干气中乙烯分离回收技术从炼厂干气中提取乙烯的技术主要有深冷分离法、吸收分离法、水合物分离法、吸附分离法和膜分离法等。
其中水合物分离法是新出现的分离方法,膜分离法正处于实验室阶段或工业试验阶段,而深冷分离法,吸收分离法和吸附分离法已经成熟并实现工业化[7]。
下面分别做以介绍。
1.1深冷分离法深冷分离法是一种已经相当成熟的技术。
早在20世纪50年代,人们就开发了常规深冷分离技术[8,9,10]。
该方法是一种低温的分离工艺,利用原料中各个组分的相对挥发度的不同,通过气体透平膨胀制冷,在低温下将干气中各个组分按工艺要求冷凝下来,然后利用精馏法将其中的各类烃按照蒸发温度的不同逐一进行分离。
但由于常规深冷分离工艺能耗大,人们不断对其进行改进,最突出的是利用分凝分馏器进行分离。
分凝分馏器是美国空气产品公司的设计专利;九十年代初,美国Stone&Webster 公司将其应用于烃气分离工艺中,形成了以分凝分馏器为核心的第一代ARS (Advanced Recovery System)技术[11]。
深冷 分离

◎生产系统设施布置要解决的主要问题是: ◉是根据企业的经营目标和生产纲领,在已确定的空间场所内,按照从
原材料的接收、零件和产品的制造,到成品的包装、发运的全过程,将 人员、设备、物料所需要的空间做最适当的分配和最有效的组合,以便 获得最大的生产经济效益。
流,在办公室布置中尤其重要。
7
◎设施布置≈工厂设计≈ 工厂总体布置+车间布置。 ◎工厂总体布置设计 ◉生产车间、辅助生产车间、仓库、动力站、办公室、露天
作业场地等各种作业单位和运输线路、管线、绿化和美化设 施的相互位置
◉物料的流向和流程、厂内外运输的联接及运输方式。
◎车间布置设计 ◉各生产工段(工作站)、辅助服务部门、储存设施等作业
因素变化可能带来的布置变更,以便于以后的扩展和调 整。
◎安全原则。应考虑使作业人员有安全感,方便、舒适。
13
6.1.3流动模式与空间需求
◎在生产与物流系统设计中, 流动模式和空间需求
是两项重要的前提。 生产系统设施规划要考虑产品、 工艺和计划, 这些内容基本确定后, 机器设备、 物料与人员就大致确定下来了, 这时候就可以确定 相应的空间需求。
◎容量和空间要求。只有先确定了人员、机器和设备的要求
后,才能进行布置,为每一作业单位分配合理的空间,并考 虑通道、洗手间、餐厅、楼梯等附属设施的要求。
◎环境和美学。布置决策也要求确定窗户、分隔高度、室内
植物等环境因素,以降低噪音、改善空气流通和提供隐密性 等。
◎信息流。通信交流对公司都是很重要的,布置必须方便交
工作地 工作地 工作地
宏观--微观的多次轮回
乙烯装置操作工乙烯深冷分离精馏试卷(练习题库)

乙烯装置操作工乙烯深冷分离精微试卷(练习题库)1、冷箱是由许多O组成的。
2、冷箱一般是由O板翅式换热器串联或并联而成。
3、冷箱内部所装珠光砂的作用是()。
4、外部管道与冷箱的联接一般采用()。
5、冷箱内部所有受压部件采用O相连。
6、冷箱壳体充氮气是为了防止O进入。
7、冷箱系统热交换物流达十余种,物流的流向形式有()。
8、冷箱系统所用的冷剂有()。
9、O运用的不是焦耳一汤姆逊效应。
10、冷箱系统氢气开工线是指()。
11、冷箱系统控制的主要指标为()。
12、控制粗氢中乙烯含量的目的是()。
13、深冷顺序分离流程中,氢气经冷箱回收冷量后送往()。
14、粗氢中乙烯含量主要通过O来保证的。
15、冷箱系统分离出来的氢气纯度主要取决于()。
16、深冷顺序分离流程中,脱甲烷塔第三进料分离罐顶部气相物料氢气含量大约为()。
18、与传统的顺序分离法相比较,KTI与布朗路特公司合作开发的KTI/AET 先进乙烯工艺,其主要的优点在于19、同传统乙烯装置深冷分离与脱甲烷系统相比较,采用先进的分凝分离器技术的脱甲烷系统的优点有()。
20、ARS技术的核心是采用了高效、节能的()。
21、关于分凝分离器的分离过程叙述正确的是()。
22、下列情况中不适合应用分凝分离器技术的是()。
23、冷箱系统的冷量来源是()。
24、冷箱系统操作要求()。
25、为使冷箱尾气中乙烯损失量减小,应该使操作压力和操作温度向()的方向变化。
26、冷箱系统的操作压力正常情况下是通过O来控制的。
27、冷箱系统压力波动会造成()。
28、对于冷箱系统压差过大的处理方法,下列选项不正确的是()。
29、冷箱系统压差过大、温度分布异常,处理方法不正确的是()。
30、正常操作时,关于冷箱温度的控制,下列选项不正确的是()。
31、冷箱系统压差过大、温度分布异常可能的原因有()。
32、冷箱系统压差过大、温度分布异常的可能原因是()。
33、冷箱系统压力、温度波动,下列说法不正确的是()。
乙烯的生产之深冷分离共74页

35、不要以为自己成功一次就可以了 ,也不 要以为 过去的 光荣可 以被永 远肯定 。
66、节制使快乐增加并使享受加强。 ——德 谟克利 特 67、今天应做的事没有做,明天再早也 是耽误 了。——裴斯 泰洛齐 68、决定一个人的一生,以及整个命运 的,只 是一瞬 之间。 ——歌 德 69、懒人无法享受休息之乐。——拉布 克 70生产之深冷分离
31、别人笑我太疯癫,我笑他人看不 穿。(名 言网) 32、我不想听失意者的哭泣,抱怨者 的牢骚 ,这是 羊群中 的瘟疫 ,我不 能被它 传染。 我要尽 量避免 绝望, 辛勤耕 耘,忍 受苦楚 。我一 试再试 ,争取 每天的 成功, 避免以 失败收 常在别 人停滞 不前时 ,我继 续拼搏 。
乙烯的生产—裂解气的分离流程的组织

炔<1μg/g,产品回收率达98%。
项目二 乙烯的生产 石油化工产品生产技术
流裂 任程解 务的气 五组分
织离
知识点3:裂解气的压缩
1.压缩的原因
需要大量冷量和耐低温设备 常压下,冷凝精馏分离温度低
裂解气常压下沸点很低
常压下沸点
解决办法
1.压缩的原因
为什么要多段压缩? 压缩后的气体温度必须要限制
✓ 原因:裂解气压缩是绝热过程,压力升高,温度升高。 ✓避免压缩过程温升过大造成裂解气中双烯烃尤其是 丁二烯之类的二烯烃在较高的温度下发生大量的聚 合,以至形成聚合物堵塞叶轮流道和密封件。 ✓生产上通过裂解气的多段压缩和段间冷却结合的方 法实现。(压缩机出口温度一般不超过100 ℃,各段 入口温度一般为38 ~40 ℃。)
有水生成
影响加氢效果
水分带入低温 系统造成冻堵
二、脱水
危害
低温下,水冻结成冰,而且与轻质烃形成白色结晶水合物(高 压低温下稳定) ,如CH4·6H20、C2H6·7H20、C3H8·7H20等。 这些固体附着在管壁上,既增加动能消耗,又堵塞管道。
脱水方法
固体吸附法(分子筛、硅胶、活性氧化铝),目前广泛采用 效果较好的是分子筛吸附剂。
顺利进行。
四、脱炔
乙炔的脱除方法主要有溶剂吸收法和催化加氢法。
催化加氢脱炔
特点:不会带入任何新杂质;工艺操作简单;将炔烃变成产品烯烃
1、原理:
主反应: 副反应:
CH≡CH十H2→CH2=CH2 CH≡CH十2H2→CH3—CH3 CH2=CH2十H2→CH3—CH3
mC2H2+nH2→低聚物(绿油)
乙烯装置分离工段------丙烯精馏工序工艺设计

乙烯装置分离工段------丙烯精馏工序工艺设计摘要乙烯是石油化学工业中最重要基础有机原料之一。
由乙烯装置生产的乙烯、丙烯、丁二烯、苯、甲苯、二甲苯,即“三烯三苯”是生产各种有机化工原料和合成树脂、合成纤维、合成橡胶三大合成材料的基础原料,涉及到国民生活的各个方面。
所以,乙烯生产能力的大小直接影响着乙烯及其他衍生物的供应。
其产能是衡量一国乙烯竞争力的重要标准,也是衡量一个国家石油化工产业的重要标志。
乙烯装置是石油化工行业的龙头装置,对应乙烯装置,石油烃裂解制乙烯技术研究始于20世纪30年代,经过近70年的发展,裂解技术日臻完善,目前该技术所生产的乙烯已经占到世界乙烯总产量的98%以上。
本次设计参考了**乙烯厂的部分资料,以生产实践为基础,理论联系实际,针对乙烯装置分离工段进行重点设计。
设计生产能力为年生产10万吨。
本设计内容主要对丙烯精馏塔进行了物料衡算、热量衡算、塔型设计、尺寸计算与选型。
其中包括塔径计算、塔板布置、流体力学计算,附件的计算与选型,其中包括塔冷凝器的选择、再沸器的选取、接管及除沫器的计算、塔高的计算等内容。
设计过程中查阅了大量的文献资料,并以**乙烯厂装置为参考,设计基本达到了合理程度,绘制了工艺流程图和填料装配图。
关键词:乙烯;装置;丙烯;精馏ABSTRACT目录引言 (1)第一章、文献综述 (2)1.1设计概述 (2)1.2国内外乙烯工业的现状和发展前景 (2)1.3乙烯的主要生产方法 (3)1.3.1 烃类热裂解法生产乙烯 (3)1.3.2 乙烯的主要分离技术 (4)1.3.3 乙烯生产的其他方法 (5)第二章、乙烯等主要产品的性质和工艺流程的确定 (6)2.1乙烯等主要产品和主要副产品的性质、用途和质量规格 (6)2.1.1 聚合级乙烯 (6)2.1.2 聚合级丙烯 (6)2.1.3 主要副产品的性质、用途和质量规格 (7)2.2乙烯生产工艺技术简介 (9)2.2.1 装置简介 (9)2.2.2 基本原理 (9)2.2.3工艺流程 (10)2.2.4工艺条件控制指标 (17)第三章、乙烯装置的物料衡算 (19)3.1物料衡算 (19)3.1.1 裂解装置的物料衡算 (19)3.1.2 丙烯精馏塔物料衡算 (20)3.2热量衡算 (23)3.2.1 丙烯精馏塔热流示意图 (23)3.2.2 热量衡算 (23)3.3设备尺寸衡算与选型 (25)3.3.1 丙烯精馏塔的设备尺寸计算与选型 (25)3.3.2 丙烯精馏塔附属设备及主要附件选型与计算 (30)第四章、设计结果汇总 (36)引言乙烯是石油化工的基础原料。
乙烯生产-深冷分离

(1)氨蒸汽压缩制冷 (2)丙烯制冷系统 (3)乙烯制冷系统 (4)乙烯—丙烯复迭制冷 (5)三元复迭制冷
(1)氨蒸汽压缩制冷
(1)蒸发 (2)压缩 (3)冷凝 (4)节流膨胀
冷冻剂
冷冻剂本身物理化学性质决定了制冷温度的范 围。如液氨降压到0.098MPa时进行蒸发,其蒸发 温度为-33.4℃。 要满足深冷分离,获得-100℃的低温,必须用 沸点更低的气体作为冷冻剂。
在这个系统中,冷水向丙烯供冷,丙烯向乙烯供 冷,乙烯向甲烷供冷,甲烷向低于-100℃冷量用 户供冷。
2、节流膨胀制冷
所谓节流膨胀制冷,就是气体由较高的压 力通过一个节流阀迅速膨胀到较低的压力,由 于过程进行得非常快,来不及与外界发生热交 换,膨胀所需的热量,必须由自身供给,从而 引起温度降低。
0.76
0.18 0.09
4.36
原料来源
石脑油裂解 轻柴油裂解
14.09 0.32 26.78 0.41 26.10 5.78 0.48 10.30 0.34 4.85 1.04 4.53 4.98
13.18 0.27 21.24 0.37 29.34 7.58 0.54 11.42 0.36 5.21 0.51 4.58 5.40
但不能任意加压,若压力增高: 对设备材料强度要求增高; 动力消耗增大; 使低温分离系统精馏塔釜温升高,易引起一些
不饱和烃的聚合 使烃类相对挥发度降低,增加了分离的困难。
因此,在深冷分离中要采用经济上合理而技 术上可行的压力,一般为3.54~3.95MPa。
2.多段压缩
(1)裂解气经压缩后,不仅压力升高,而且温度也会升 高,某些烃类尤其是丁二烯之类的二烯烃,容易在较高 的温度下发生聚合和结焦。这些聚合物和结焦物会堵塞 压缩机阀片和磨损气缸,或沉积在叶轮上。
乙烯生产技术和工艺流程介绍
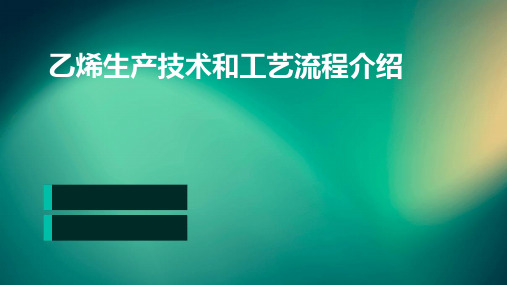
乙烯具有可燃性和麻醉性,常温下易 于聚合,因此需要避免长时间暴露于 空气中。
乙烯生产工艺简介
裂解工艺
01
通过高温裂解石油烃类或天然气等原料,生成含有乙烯的裂解
气。
分离工艺
02
裂解气经过急冷、压缩、深冷分离等步骤,将乙烯从其他气体
中分离出来。
精制工艺
03
对分离得到的乙烯进行进一步精制,以去除杂质和提高纯度。
安全联锁保护
定期安全检查
对关键设备和阀门设置安全联锁保护,避 免误操作导致的事故发生。
定期对装置进行安全检查和维护,确保各项 安全防护措施的有效性。
环保法规遵循及污染治理
废气治理
对裂解炉废气和压缩机尾气进行治理,采用干法 或湿法脱硫、脱硝技术,降低废气中的污染物排 放。
固体废弃物处理
对废催化剂、废保温材料等固体废弃物进行分类 收集和处理,避免对环境造成污染。
往复式压缩机
适用于高压比、小流量的场合,但易损件较多,维护成本较高。
螺杆式压缩机
运转平稳、可靠性高,适用于中等流量和压力范围,但制造成本 较高。
制冷原理及设备配置方案
制冷原理
设备配置方案
通过压缩机将制冷剂压缩成高温高压气体, 然后通过冷凝器将其冷却成高压液体,再通 过节流装置降压降温后进入蒸发器吸收热量, 实现制冷效果。
产品纯度提升措施
优化精馏塔操作条件
调整回流比、塔顶温度等参数,提高产品纯 度。
采用高效分离元件
如高效填料、新型塔板等,提高传质效率。
加强原料气预处理
如脱水、脱硫等,减少杂质对分离效果的影 响。
定期检测和维护设备
确保设备处于良好状态,减少因设备问题导 致的产品纯度下降。
乙烯、丙烯安全生产要点
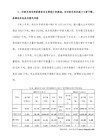
3安全要点
3.1裂解炉
3.1.1在点火前,要检查风门是否打开。炉膛内有机物要进行置换并分析合格。所有联锁均应挂上。若初次点火,应分析燃料气氧含量是否合格(小于3%),并严禁夹带液体。停车期间,燃料管线要立即加上盲板,以防伐门内漏,燃料在炉膛内积聚而发生事故。
冬季开工要检查燃料气的保温和排凝。凝液往往是碳五等烃类,不能就地排放。凝液若带进炉内,会造成炉膛正压回火,使裂解炉联锁停车,火从看火孔外冒,易烧坏炉周围的仪表、电气设备。带液严重的回火,会造成炉膛内发生爆燃,易损坏裂解炉。
3.1.4生产中要经常通过视镜注意观察裂解炉内火焰分布是否均匀,有无偏烧及炉管变形情况,异常变化要及时处理。要定期对炉管的变形、腐蚀情况和管壁测厚情况进行分析、判断,防止生产中炉管烧穿、焊口开裂发生事故。
3.1.5炉子烧焦时要注意检查原料和裂解气去急冷系统的阀门是否切死并加堵盲板,用蒸汽置换合格后方可通入空气烧焦。
3 .4.5各油罐设立的取样口、检测口,除采样和检测时打开外,其它时间必须关闭。发现阀门关不严时,应采取加接阀的办法防止泄漏。
3 .4.6绝对禁止在装置区和贮罐区装油品或液化石油气。
(4)冷箱的设备、管道、仪表管线必须干燥,并检查裂解气露点的控制是否低于-65℃。若水含量高,会使冷箱管线及塔盘冻堵,严重时会造成停车。
3.2.1.1.3检查压缩机油泵压力、轴位移、温度等联锁系统是否处于正常使用和完好状态,防止压缩机因联锁停车而导致全装置的停车。
深冷分离流程

此塔的关键组分CH4和C2H4,可以看成二元系统,在 裂解气组成—定的情况下,温度和压力的确定取决 于系统的气—液相平衡性质。
相同压力相温度下,乙烯在塔顶尾气中的含量,随 H2与CH4之比的增加而增加。
2、脱甲烷法
4)顺序分离流程采用后加氢脱除炔烃的方法。
① 顺序分离流程及其特点
简而言之
√ 技术比较成熟,对裂解原料适应性强技术比较 成熟,对裂解原料适应性强 × 流程长流程长 × 裂解气全部进入深冷分离,冷量需求大裂解气 全部进入深冷分离,冷量需求大
② 前脱乙烷流程及其特点
前脱乙烷分离流程是以脱乙烷塔为界限。将物 料分成两部分。一部分是轻馏分,即甲烷、氢、乙 烷和乙烯等组分;另一部分是重组分,即丙烯、丙 烷、丁烯、丁烷以及碳五以上的烃类。然后再将这 两部分各自进行分离,分别获得所需的烃类。
适合于分离含适合于分离含C4 组分多的重裂 解气。
二、脱甲烷塔及操作条件
1、脱甲烷塔的任务 2、脱甲烷法
① 高压法 ② 低压法
深冷分离系统冷量消耗分配
脱乙烷塔
其余塔
乙烯塔
36%
52%
脱甲烷塔
1、脱甲烷塔的任务
将裂解气中比乙烯轻的组分(如H2、CH4)从塔顶分 出.把比乙烯重的组分(C2H6、C3+ C4+)烃分出。
乙Байду номын сангаас装置
丙烯精馏塔
液体烃球型罐
① 高压法 高压法的脱甲烷塔顶温度为-96℃左右,压力为3.1-3.8MPa; 节约制冷的能量消耗:提高压力比降低温度消耗的能量 少,压力高,分离温度高,这样制冷系统可采用乙烯冷剂, 不必采用CH4和H2冷剂; 当脱甲烷塔顶尾气压力高时,可借助高压尾气的自身 膨胀获得额外的降温,比用CH4、H2冷冻机要简单经济。 压力高可增加气体的密度,缩小脱甲烷塔的塔径和容 积,消耗的耐低温材料少。
- 1、下载文档前请自行甄别文档内容的完整性,平台不提供额外的编辑、内容补充、找答案等附加服务。
- 2、"仅部分预览"的文档,不可在线预览部分如存在完整性等问题,可反馈申请退款(可完整预览的文档不适用该条件!)。
- 3、如文档侵犯您的权益,请联系客服反馈,我们会尽快为您处理(人工客服工作时间:9:00-18:30)。
(5)三元复迭制冷
用乙烯作制冷剂在正压下操作,不能获得-103℃ 以下的低温。 生产中需要-103℃以下的低温时,可采用沸点更 低的制冷剂,甲烷在常压下沸点是-161.5℃。但 是由于甲烷的临界温度是-82.5℃,若要构成冷 冻循环制冷,需用乙烯作制冷剂为其冷凝器提供 冷量,这样就构成了甲烷-乙烯-丙烯三元复迭 制冷。 在这个系统中,冷水向丙烯供冷,丙烯向乙烯供 冷,乙烯向甲烷供冷,甲烷向低于-100℃冷量用 户供冷。
二、裂解气分离方法简介
裂解气的提浓、提纯工作,是以精馏方法 精馏 完成的。 精馏方法要求将组分冷凝为液态。氢气常 压沸点为-263 ℃、甲烷-161.5℃,很难液化, 碳二以上的馏分相对地比较容易液化(乙烯沸点 -103.68 ℃ )。因此,裂解气在除去甲烷、氢 气以后,其它组分的分离就比较容易。 主要矛盾 所以分离过程的主要矛盾是如何将裂解气 中的甲烷和氢气先行分离。 甲烷和氢气 工业生产上采用的裂解气分离方法,主要 有深冷分离和油吸收精馏分离两种。
深冷分离——在 -100℃左右的低温下,将裂 解气中除了氢和甲烷以外的其它烃类全部冷凝下 来。然后利用裂解气中各种烃类的相对挥发度不 同,在合适的温度和压力下,以精馏的方法将各 组分分离开来。
分离要求
要得到高纯度的单一的烃,如重要的基本有机原料 乙烯、丙烯等,就需要将它们与其它烃类和杂质等 分离开来,并根据工业上的需要,使之达到一定的 纯度,这一操作过程,称为裂解气的分离。 各种有机产品的合成,对于原料纯度的要求是不同的。 所以分离的程度可根据后续产品合成的要求来确定。
一、 裂解气的组成及分离方法
(一)裂解气的组成
组分
H2 CO+CO2+H2S CH4 C2H2 C2H4 C2H6 C3H4 C3H6 C3H8 C4 C5 ≥C6 H2O
乙烷裂解
34.0 0.19 4.39 0.19 31.51 24.35
0.76
原料来源 石脑油裂解 轻柴油裂解
14.09 0.32 26.78 0.41 26.10 5.78 0.48 10.30 0.34 4.85 1.04 4.53 4.98 13.18 0.27 21.24 0.37 29.34 7.58 0.54 11.42 0.36 5.21 0.51 4.58 5.40
(3)乙烯制冷系统
常压下乙烯的沸点为- 104℃,即用乙烯作制冷 剂可以获-100℃的低温。 乙烯的临界温度为9.9℃,临界压力为5.15MPa, 在此温度之上,不论压力多大,也不能使其液化, 所以不能用普通冷水使之液化。为此,乙烯循环 制冷中的冷凝器需要使用制冷剂冷却。 工业生产中常采用丙烯作制冷剂来冷却乙烯,这 样丙烯的冷冻循环和乙烯冷冻循环制冷组合在一 起,构成乙烯-丙烯复迭制冷。
2.多段压缩
(1)裂解气经压缩后,不仅压力升高,而且温度也会升 高,某些烃类尤其是丁二烯之类的二烯烃,容易在较高 的温度下发生聚合和结焦。这些聚合物和结焦物会堵塞 压缩机阀片和磨损气缸,或沉积在叶轮上。 同时温度升高,还会使压缩机润滑油粘度下降,从而 使压缩机运转不能正常进行。
因此,裂解气压缩后的温度必须要限制,当裂解气中 含有碳四、碳五等重组分时,压缩机出口温度一般不能 超过100℃。 在生产上主要是通过裂解气的多段压缩和冷却相结合 的方法来实现。裂解气段间采用水冷,各段入口38~ 40℃。
在裂解气分离装置中,用丙烯作冷冻剂可以得 到-40℃以上温度级的冷量。 -47.72℃ 因为丙烯常压下沸点为-47.72 ℃,用丙烯作 制冷剂构成的冷冻循环制冷过程,把丙烯压缩 l.864MPa 45℃ 到l.864MPa的条件下,丙烯的冷凝点为45℃, 很容易用冷水冷却使之液化,但是在维持压力 不低于常压的条件下,其蒸发温度受丙烯沸点 -47℃ 的限制,只能达到-47℃左右的低温条件,即 在正压操作下,用丙烯作制冷剂,也不能获得 -100℃的低温条件。 -100℃
0.18 0.09
4.36
(二)裂解气分离方法
不同压力下某些组分的沸点℃
压力 组分 H2 CH4 C2H4 C2H6 C3H6 1.103 10.13 15.19 20.26 25.23 30.39 ×105Pa ×105Pa ×105Pa ×105Pa ×105Pa ×105Pa -263 -162 -104 -86 -47.7 -244 -129 -55 -33 9 -239 -114 -39 -18 29 -238 -107 -29 -7 37 -237 -101 -20 3 44 -235 -95 -13 11 47
二、制冷
深冷分离裂解气需要把温度降到-100℃以 下。为此,需向裂解气提供低于环境温度 的冷剂。 获得冷量的过程称为制冷。 深冷分离中常用的制冷方法有两种:冷冻 循环制冷和节流膨胀制冷。
(二)制冷
1、冷冻循环制冷 2、节流膨胀制冷 3、热泵
1、冷冻循环制冷
制冷原理
将物料冷却到低于环境温度的冷冻过程称为冷冻
(1)氨蒸汽压缩制冷
(1)蒸发
(2)压缩 (3)冷凝 (4)节流膨胀
冷冻剂
冷冻剂本身物理化学性质决定了制冷温度的范围。如液
氨降压到0.098MPa时进行蒸发,其蒸发温度为-33.4℃。 如果降压到0.011MPa,其蒸发温度为-40℃。 要满足深冷分离,获得-100℃的低温,必须用沸点更低 的气体作为冷冻剂。
(4)乙烯—丙烯复迭制冷循环
4、乙烯—丙烯复迭制冷循环
在乙烯—丙烯复迭制冷循环中, 冷水在换热器(2)中向丙烯供冷,带走丙烯冷凝时 放出的热量,丙烯被冷凝为液体,然后,经节流 膨胀降温,在复迭换热器中汽化,此时向乙烯气 供冷,带走乙烯冷凝时放出的热量,乙烯气变为 液态乙烯,液态乙烯经膨胀阀降压到换热器(1)中 汽化,向被冷物料供冷,可使被冷物料冷却到 -100℃左右。 在图中可以看出,复迭换热器既是丙烯的蒸发器 (向乙烯供冷),又是乙烯的冷凝器(向丙烯供热)。 当然,在复迭换热器中一定要有温差存在,即丙 烯的蒸发温度一定要比乙烯的冷凝温度低,才能 组成复迭制冷循环。
有的产品对原料纯度要求不高,例如用 对于聚合用的乙烯和丙烯的质量要求则很 乙烯与苯烷基化生产乙苯时,对乙烯纯 严,生产聚乙烯、聚丙烯要求乙烯、丙烯 度要求不太高,则可以分离纯度低一些, 纯度在99.9%或99.5%以上,其中有机杂质 用丙烯与苯烷基化生产异丙苯时,甚至 不允许超过5~10PPm。这就要求对裂解气 可以用丙烯-丙烷混合馏分。 进行精细的分离和提纯。
1、压缩 冷冻系统
该系统的任务是加压、降温,以保 证分离过程顺利进行。 为了排除对后继操作的干扰,提高 产品的纯度,通常设置有脱酸性气 体、脱水、脱炔和脱一氧化碳等操 作过程。 将各组分进行分离并将乙烯、丙烯产 品精制提纯,这是深冷分离的核心。
2、气体净 化系统
3、低温精 馏分离系 统
二、 压缩与制冷
冷冻循环制冷的原理是利用冷冻剂自液态汽化时, 要从物料或中间物料(又叫载冷体)吸收热量,因而使物 料温度降低的过程。液体沸腾时,汽化在整个液体中进 行,液体的温度保持不变,直至液体全部汽化。
所吸收的热量,在热值上等于它的汽化潜热。 液体的汽化温度(即沸点)是随压力的变化而改变的, 压力越低,相应的汽化温度也越低。
(一)裂解气的压缩
1.压力与温度的关系
根据物质的冷凝温度随压力增加而升高的规律,对 裂解气加压,从而使各组分的冷凝点升高,这既有利于 分离,又可节约冷冻量和低温材料。
Ñ Á /Mpa Î ¶ £ ¡ ¹ ¦ Â È ¬ æ 0.15¡ 0.3 -140 « 0.6¡ 1 « -130 3¡ 4 « -96
深冷分离
深冷分离是在-100℃左右的低温下,将裂解气中除 冷凝 了氢和甲烷以外的其它烃类全部冷凝下来。然后利用裂 解气中各种烃类的相对挥发度不同,在合适的温度和压 力下,以精馏的方法将各组分分离开来,达到分离的目 精馏 的。实际上,此法为冷凝精馏过程。 工业上把冷冻温度高于-50℃称为浅度冷冻(简称浅冷); 在-50~-l00℃之间称为中度冷冻;(简称中冷) 等于或低于-100℃称为深度冷冻(简称深冷)。 因为这种分离方法采用了-100℃以下的冷冻系统,故 称为深度冷冻分离,简称深冷分离。 深冷分离法是目前工业生产中应用最广泛的分离方 法。它的经济技术指标先进,产品纯度高,分离效果好, 但投资较大,流程复杂,动力设备较多,需要大量的耐 低温合金钢。因此,适宜于加工精度高的大工业生产。
(2)采用多段压缩可节省能量,提高效率, 减小压缩比。 (3)同时,压缩机采用多段压缩也便于在压 缩段之间进行净化与分离。
目前工业上对裂解气大多采用三至五段 压缩。
多段压缩
在多段压缩中,被压缩机吸入的气体先进行一段压缩, 压缩后压力、温度均升高,经冷却,降低气体温度并分离 出凝液,再进二段压缩,以此类推。压缩机每段气体出口 温度都不高于规定范围。 根据深冷分离法对裂解气的压力要求及裂解气压缩过 程中的特点,目前工业上对裂解气大多采用三段至五段压 缩。石油裂解气压缩的分段方法和工艺流程,通常随裂解 气组成的不同而有所差异。 同时,压缩机采用多段压缩也便于在压缩段之间进行 净化与分离,例如脱硫、干燥和脱重组分可以安排在段间 进行。 在深冷分离操作中,裂解气的压缩常采用往复式压缩 机和离心式压缩机,由于裂解炉的废热锅炉副产高压水蒸 汽,因此多用蒸气透平驱动离心式压缩机,达到能量合理 利用。现在大规模生产厂的裂解气压缩机广泛采用离心式 的。
(1)氨蒸汽压缩制冷 (2)丙烯制冷系统
(3)乙烯制冷系统
(4)乙烯—丙烯复迭制冷
(5)三元复迭制冷
1、氨蒸汽压缩制冷
在低压下液氨的沸点很低,如压力为O.12MPa 氨蒸汽压缩制冷系统可由四个基本过程组 时沸点为-30℃。液氨在此条件下,在蒸发器中 蒸发变成氨蒸气,则必须从通入液氨蒸发器的 成。 被冷物料(或载冷体)中吸取热量,产生制冷效 果,使被冷物料(或载冷体)冷却到接近-30℃。 (1)蒸发 蒸发器中所得的是低温、低压的氨蒸气。为了使 其液化,首先通过氨压缩机压缩,使氨蒸气压力 (2)压缩 升高,则冷凝点也随之升高。 (3)冷凝 高压下的氨蒸气的冷凝点是比较高的。例如把 若液氨在1.55MPa压力下汽化,由于沸点为 氨蒸气加压到1.55MPa时,其冷凝点是40℃, 40℃,不能得到低温,为此,必须把高压下的 (4)节流膨胀 此时,氨蒸气在冷凝器中变为液氨,可由普通 液氨,通过膨胀阀降压到0.12MPa,若在此压 冷水将所放出的热量带走。 力下汽化,温度可降到-30℃。由于此过程进 行的很快,汽化热量来不及从周围环境吸取, 全部取自液氨本身。节流后形成低压,低温的 汽液混合物进入蒸发器。在此液氨又重新开始 下一次低温蒸发吸热。反复进行,形成一个闭 合循环操作过程。