船用管子加工通用工艺汇总
船用管子装配焊接工艺介绍
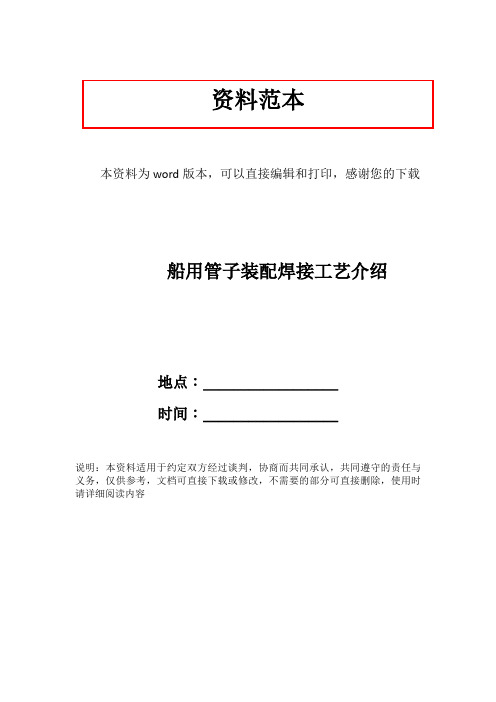
资料范本本资料为word版本,可以直接编辑和打印,感谢您的下载船用管子装配焊接工艺介绍地点:__________________时间:__________________说明:本资料适用于约定双方经过谈判,协商而共同承认,共同遵守的责任与义务,仅供参考,文档可直接下载或修改,不需要的部分可直接删除,使用时请详细阅读内容1 本工艺是管系施工工艺文件,是在考虑了本厂目前施工中的具体情况而编制的。
2 本工艺属于指导性文件,如设计图纸或专用工艺文件另有特殊规定或技术要求,则应按图纸或专用工艺文件执行。
3 本工艺不适用于主蒸汽、氧气和氮气等特殊管路及软管系统。
4 本工艺适用于内燃机动力船舶的常用管系。
范围本工艺主要规定了船用管子装配焊接通用工艺,适用于各类船舶材料满足规范要求的下列规格管子的装配焊接:外径在325mm以下的无缝钢管和合金钢管、180mm以下的铜管和铜合金管、70mm以下的铝管和铝合金管、42mm以下的双金属管和DN150mm以下的水煤气管。
对于其他类型或有特殊要求的管子应按设计要求另制定专门的焊接工艺。
1、管子与管子的焊接管子的焊接可以采用直接对焊、坡口对焊、衬圈对焊以及封底对焊等形式。
各种型式的技术要求见表一表一管子对焊型式及技术要求管子对接中心偏差均应≤1.0mm。
若管子对接时有壁厚差,则在较厚壁内侧削斜,其削斜长度不小于壁厚差的4倍。
管子经对接焊后,管子内外表面的焊渣和飞溅均应去除,如果采用气焊封底焊则焊缝内表面的修正可以省略。
2、法兰与管子的焊接2.1 钢管的法兰连接形式和适用范围见表22.2 法兰焊接应在支管和弯头焊接之后,以防止焊接变形。
焊接型式应严格按照所选用法兰标准的要求进行。
2.3 装焊时,法兰内壁与管子外表面最大间隙应不大于2mm,径向相对两点的间隙总和不得超过3mm;法兰与管子焊接的咬口深度应不大于0.2mm,超过此数值应予以修整。
焊接时不应使法兰密封平面碰电、损坏。
船舶管系知识第七章

视向 视向
图7.4.6 法兰螺孔转角视向规定
(-) 基准面
(+)
图7.4.7 法兰螺孔 转角"+"、"-"的表示
.
2. 直管法兰螺孔转角 选择其中一只法兰螺孔平分线与直管组成
的平面作为公共基准面,这样这只法兰螺孔的 转角为 0。另一只法兰的法兰螺孔平分线与此 基准面间的夹角即为这只法兰的螺也转角。
H(高 度); 从弯模中心到地平面之间的距离。
A(中 心 距); 从弯模中心到机体边缘之间的距离。
B(插芯长度); 从弯模中心到插芯活塞杆连接件的距离。
C(后夹长度); 从弯模中心到后夹导条端面之间的距离。 对于滚轮式后夹,则为弯模中心到后夹 第二个滚轮中心的距离
R: 弯管半径
图7.3.1 弯管参数示意图
注:D表示管子公称通径 R表示弯头弯曲半径
三、弯管机
1、弯管机的分类
机械
液压
弯管机
弯管机
数控
冷弯弯管机
弯管机
弯
电动
机械
管
弯管机
弯管机
机
火焰弯管机
热弯弯管机
中频弯管机
有芯弯管机 无芯弯管机 有芯弯管机 无芯弯管机
有芯弯管机 无芯弯管机
2、弯管机主要参数
B
LC
R
A
地平面
L(前夹长度): 从弯模中心到弯盘端面之间的距离。
项
目
标准范围 允许极限 备 注
弯管偏差 L1
θ
双向弯管偏差 L1
θ2 θ1
L3
L2
L2
△L1 △L2 △θ △L1 △L2 △L3
θ1 θ2
±3
船舶管子焊接通用工艺
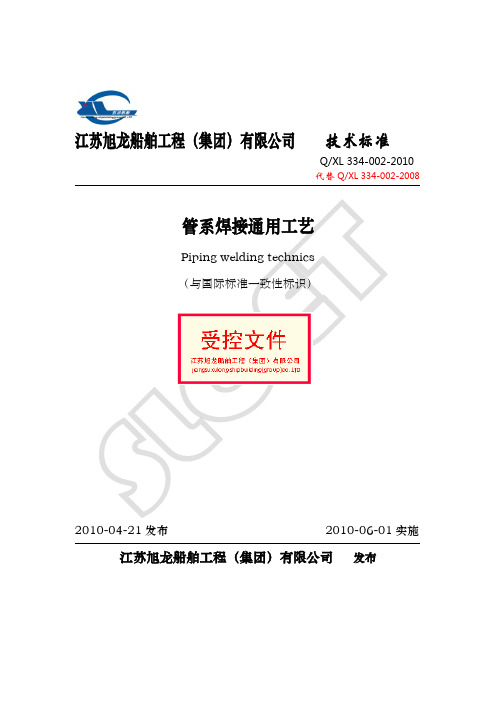
江苏旭龙船舶工程(集团)有限公司技术标准Q/XL 334-002-2010 代替 Q/XL 334-002-2008管系焊接通用工艺Piping welding technics (与国际标准一致性标识)2010-04-21 发布2010-06-01 实施 发布江苏旭龙船舶工程(集团)有限公司Q/XL 334-002-2010管系焊接通用工艺前言为确保公司承建船舶管路的焊接质量, 确保船舶使用和安全性能, 公司组织专业人员根 据造船规范和有关国家标准要求,再结合公司生产实际编制了本工艺。
本标准代替 Q/XL 334-002-2008 本标准是 Q/XL 334-002-2008 的重新修订本标准由 江苏旭龙船舶工程(集团)有限公司 提出 本标准由公司 技术部 归口本标准起草部门:工艺室 本标准主要起草人: 朱 军 本标准由总经理 周爱红 批准 本标准首次发布:2004 年 04 月 02 日zhujun2/9SLOETQ/XL 334-002-2010管系焊接通用工艺管系焊接通用工艺Q/XL 334-002-2010 1 范 围本规范规定了气体保护焊和氩弧焊用于管子焊接的焊前准备、人员要求、焊接程序、焊 接要求、和检验。
本规范适用于管子与管子、 管子与附件之间的对接和角接接头, 焊接时, 可采用纯 CO2 气体或 CO2+Ar 混合气体的 CO2 半自动或自动焊接, 也可采用钨极氩弧焊。
焊接位置为管 子水平转动位置和管子水平固定位置。
2 焊材和设备的要求2.1 焊条,焊丝和焊剂应符合有关标准的规定或验船部门认可。
2.2 焊条必须存放在干燥,通风良好的库房内,库房室温应大于5℃,相对湿度小开6℃, 严防焊条受潮变质。
焊条在使用前,需根据其万分,进行不同程度的烘干。
2.3 焊丝和焊剂应存放于干燥通风的室内。
严防焊丝生锈和焊剂受潮。
焊丝在使用前盘入焊 丝盘时,应清除螺丝上的油污,焊剂在使用前亦要进行烘干。
船用管子加工通常工艺标准
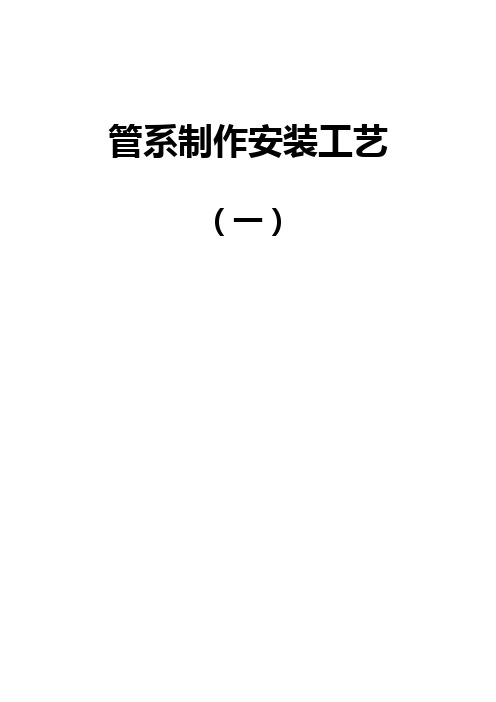
管系制作安装工艺(一)船用管子制作工艺本文件适用于各类船舶下列规格管子的加工:外径在500mm以下的无缝钢管和合金钢管、250mm以下的铜管和铜合金管(包括铜镍管)、6英寸以下的水煤气管及其它金属管。
本文件可供船舶管系施工设计时选用。
对于特殊要求的管子应按设计要求加工。
1、材料1.1 管子材料应符合我国造船规范要求和有关国家标准的规定。
出口船舶用管材须符合该船舶入级相应的船级社要求。
1.2 各种管材,必须具有制造厂的炉罐号和合格证书,如缺少证明时,应根据有关规定或订货要求补做试验,合格后方可使用。
1.3管子加工前,必须核对管子材料是否符合图纸要求。
1.4管子加工前,应对管材内外表面质量进行检查。
1.4.1无缝钢管和合金钢管,其内外表面不得有裂缝、折叠、分层、结疮、轧折、发纹等缺陷存在。
如有上述缺陷应予清除,清除部位壁厚的减薄不得超过该材料标准允许的负偏差。
1.4.2 焊接钢管内外表面不允许存在由于焊接引起的裂缝、咬口、飞溅、凹陷等缺陷。
1.4.3 有色金属管子,其表面应光滑清洁,不应有针孔、裂缝、气泡、分层、锈蚀等缺陷。
1.5碳素钢管、不锈钢管在订货时,应向制造厂提出退火处理要求。
1.6 法兰、套管、螺纹接头、异径接头、定型弯头等连接件,必须具有材质报告证件,方可使用。
2、管子弯曲加工2.1 弯管设备2.1.1 弯管机须经过设备管理部门检查验收,才能正式投入使用。
2.1.2 弯管模子、滑块或滑轮槽道和塞芯头部光洁和顺,切口处必须倒圆。
2.1.3 弯管模子和滑块的圆槽直径按表1。
2.1.4 有芯弯管机、芯棒头部的外径和长度按表2。
2.1.5 弯管机的工夹具/模具和附属设备应当定期检查和维修,以确保良好状态。
2.2 弯管技术要求2.2.1 管子的弯曲,一般采用冷弯的方法,在工厂缺少冷弯设备的情况下,允许采用热弯,但水煤气管不宜采用热弯,20号钢管不宜采用中频弯曲。
2.2.2 不锈钢管及合金钢管宜冷弯,如必须热弯时,不锈钢管加热应避免渗碳,而对淬硬倾向较大的合金钢管则不得浇水冷却。
船舶管系管子弯曲加工方法

船舶管系管子弯曲加工方法1常见加工方法1.1钢管的弯曲加工方法见表9.3.1。
表9.3.1 钢管的弯曲加工方法弯管机 数控 冷弯手工1.2铜管的弯曲加工方法见表9.3.2。
表9.3.2钢管的弯曲加工方法手工操作冷弯——弯管机 铜管的数控—— 弯曲加热弯 工方法标准弯头 虾壳弯1.3不锈钢管、铜镍铁合金管的弯曲加工方法见表9.3.3。
表9.3.3 不锈钢管、钢镍铁合金管的弯曲加工方法不锈钢管、铜冷弯——弯管机——手工操作——有芯弯管 镍铁合金管的标准弯头 加工方法虾壳弯1.4铝管的弯曲加工方法见表9.3.4。
表9.3.4 铝管的弯曲加工方法冷管——弯管机——手工操作铝管的弯曲加工方法冷热弯——弯管机——手工操作 虾壳弯2各种管子弯曲加工方法的适用场合见表9.3.5。
3弯管机3.1弯管机的分类根据冷弯和热弯两大类弯管方法,有相应的两大类弯管机,即适用于冷弯的弯管机和适用于热弯的弯管机。
按其转动部分的动力种类来分,分为液压弯管机和电动弯管机,按操作方法来分,分为机械弯管机和数控弯管机,冷弯类弯管机按是否采用芯头防皱和保证椭圆度来分,分为有芯弯管机和无芯弯管机。
有些小型弯管机,针对不同规格的管子,既可作有芯弯管机,也可作无芯弯管机。
热弯类弯管机按加热方法来分,分为中频弯管机和火焰弯管机。
还有一种三芯滚动机,是由电力驱动,适用于弯制弯曲半径大的管子。
图9.3.1 弯管参数示意图从弯盘中心到机体边缘之间的距离。
B(插芯长度);从弯盘中心到插芯活塞杆连接件的距离。
C(后夹长度);从弯盘中心到后夹导条端面之间的距离。
对于滚轮式后夹,则为弯盘中心到后夹 第二个滚轮中心的距离3.2常用弯管机简介电动、机械操作、冷弯、无芯弯管机(简称电动无芯弯管机)电动无芯弯管机是应用最早的一种弯管机,也是最基本的弯管机,其他形式的弯管机都是由它发展变化而来的。
电动无芯弯管机主要由传动部分(机内)和弯曲部分(机外)组成。
图9.3.2为电动无芯弯管机传动部分的示意图。
船用管子制作通用工艺

管系制作通用工艺船用管子制作通用工艺一、目的及范围本工艺规定了船舶管子零件的材料、切割、装配、弯曲、表面处理、等方面的工艺及其质量验收指标要求。
本工艺适用于各类船舶下列规格管子的加工:外径在500mm以下的无缝钢管、焊接钢管和不锈钢管,250mm以下的铜管和铜合金管(包括铜镍管)、6英寸以下的水煤气管及其它金属管。
本文件可供船舶管系施工设计时选用。
对于特殊要求的管子应按设计要求加工。
二、引用标准下列标准所包含的条文,通过在本工艺中引用而构成本工艺的条文。
由于标准都会被修订,使用本工艺的各部门应探讨使用下列标准最新版本的可能性。
CB/T3790-1997 船舶管子加工技术条件CB/T3365-91 管子无余量下料工艺CB/Z94-68 黑色金属磷化技术条件CB*/Z343-84 热浸锌通用工艺船舶建造质量检验(CSQS)1998版中国船级社钢质海船入级和建造规范(CCS)2001版德国劳氏船级社钢质海船入级和建造规范(GL)1992版三、管子材料要求3.1 管子材料的机械性能和化学成分应符合有关国家标准、行业标准和我国造船规范要求。
出口船舶用管材须符合该船舶入级相应的船级社要求。
3.2 各种管材,根据其设计压力和设计温度分为三级,见表1。
对于I级、II级管,必须具有船舶检验部门的合格证书及制造厂的炉罐号。
III级管应具有制造厂的合格证书,如缺少证明时,应根据有关规定或订货要求补做试验,合格后方可使用。
四、管子的切割表1 管系等级注:1.Ⅰ级栏中的设计压力和设计温度两个参数,只要其中一个符合表中规定数值的,即为Ⅰ级管;Ⅱ级栏中的设计压力和设计温度两个参数,均达到表中规定数值的,即为Ⅱ级管。
2.除Ⅰ、Ⅱ级管外,其余的是Ⅲ级管。
3.表中其他介质是指空气、水、滑油或液压油等。
4.1 管子切割前,必须核对管子材料、规格是否符合图纸要求。
4.2 管子切割前,应对管材内外表面质量进行检查。
4.2.1无缝钢管和合金钢管,其内外表面不得有裂缝、折叠、分层、结疮、轧折、发纹等缺陷存在。
最新船用管子加工通用工艺
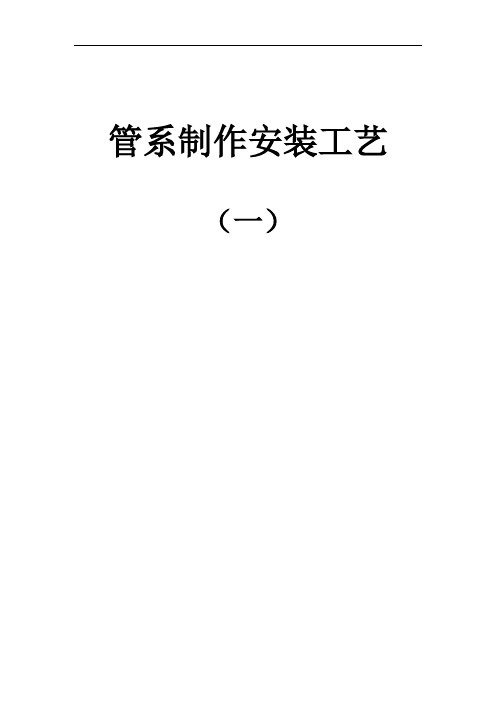
管系制作安装工艺(一)船用管子制作工艺本文件适用于各类船舶下列规格管子的加工:外径在500mm以下的无缝钢管和合金钢管、250mm以下的铜管和铜合金管(包括铜镍管)、6英寸以下的水煤气管及其它金属管。
本文件可供船舶管系施工设计时选用。
对于特殊要求的管子应按设计要求加工。
1、材料1.1 管子材料应符合我国造船规范要求和有关国家标准的规定。
出口船舶用管材须符合该船舶入级相应的船级社要求。
1.2 各种管材,必须具有制造厂的炉罐号和合格证书,如缺少证明时,应根据有关规定或订货要求补做试验,合格后方可使用。
1.3管子加工前,必须核对管子材料是否符合图纸要求。
1.4管子加工前,应对管材内外表面质量进行检查。
1.4.1无缝钢管和合金钢管,其内外表面不得有裂缝、折叠、分层、结疮、轧折、发纹等缺陷存在。
如有上述缺陷应予清除,清除部位壁厚的减薄不得超过该材料标准允许的负偏差。
1.4.2 焊接钢管内外表面不允许存在由于焊接引起的裂缝、咬口、飞溅、凹陷等缺陷。
1.4.3 有色金属管子,其表面应光滑清洁,不应有针孔、裂缝、气泡、分层、锈蚀等缺陷。
1.5碳素钢管、不锈钢管在订货时,应向制造厂提出退火处理要求。
1.6 法兰、套管、螺纹接头、异径接头、定型弯头等连接件,必须具有材质报告证件,方可使用。
2、管子弯曲加工2.1 弯管设备2.1.1 弯管机须经过设备管理部门检查验收,才能正式投入使用。
2.1.2 弯管模子、滑块或滑轮槽道和塞芯头部光洁和顺,切口处必须倒圆。
2.1.3 弯管模子和滑块的圆槽直径按表1。
表1 mm2.1.4 有芯弯管机、芯棒头部的外径和长度按表2。
表2 mm2.1.5 弯管机的工夹具/模具和附属设备应当定期检查和维修,以确保良好状态。
2.2 弯管技术要求2.2.1 管子的弯曲,一般采用冷弯的方法,在工厂缺少冷弯设备的情况下,允许采用热弯,但水煤气管不宜采用热弯,20号钢管不宜采用中频弯曲。
2.2.2 不锈钢管及合金钢管宜冷弯,如必须热弯时,不锈钢管加热应避免渗碳,而对淬硬倾向较大的合金钢管则不得浇水冷却。
船舶管子焊接通用工艺
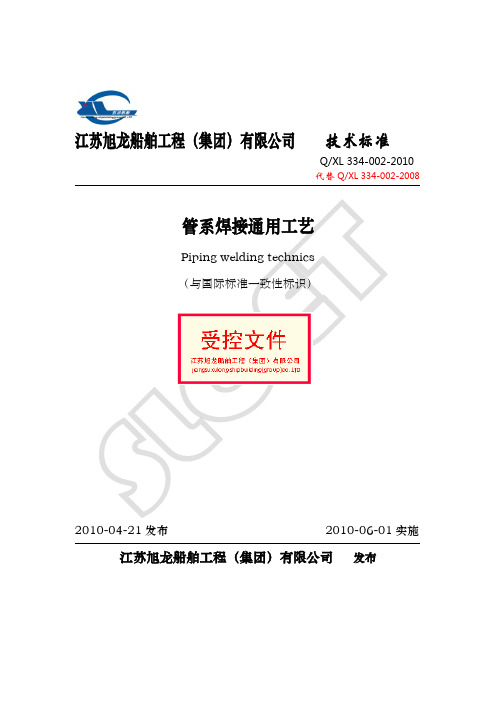
江苏旭龙船舶工程(集团)有限公司技术标准Q/XL 334-002-2010 代替 Q/XL 334-002-2008管系焊接通用工艺Piping welding technics (与国际标准一致性标识)2010-04-21 发布2010-06-01 实施 发布江苏旭龙船舶工程(集团)有限公司Q/XL 334-002-2010管系焊接通用工艺前言为确保公司承建船舶管路的焊接质量, 确保船舶使用和安全性能, 公司组织专业人员根 据造船规范和有关国家标准要求,再结合公司生产实际编制了本工艺。
本标准代替 Q/XL 334-002-2008 本标准是 Q/XL 334-002-2008 的重新修订本标准由 江苏旭龙船舶工程(集团)有限公司 提出 本标准由公司 技术部 归口本标准起草部门:工艺室 本标准主要起草人: 朱 军 本标准由总经理 周爱红 批准 本标准首次发布:2004 年 04 月 02 日zhujun2/9SLOETQ/XL 334-002-2010管系焊接通用工艺管系焊接通用工艺Q/XL 334-002-2010 1 范 围本规范规定了气体保护焊和氩弧焊用于管子焊接的焊前准备、人员要求、焊接程序、焊 接要求、和检验。
本规范适用于管子与管子、 管子与附件之间的对接和角接接头, 焊接时, 可采用纯 CO2 气体或 CO2+Ar 混合气体的 CO2 半自动或自动焊接, 也可采用钨极氩弧焊。
焊接位置为管 子水平转动位置和管子水平固定位置。
2 焊材和设备的要求2.1 焊条,焊丝和焊剂应符合有关标准的规定或验船部门认可。
2.2 焊条必须存放在干燥,通风良好的库房内,库房室温应大于5℃,相对湿度小开6℃, 严防焊条受潮变质。
焊条在使用前,需根据其万分,进行不同程度的烘干。
2.3 焊丝和焊剂应存放于干燥通风的室内。
严防焊丝生锈和焊剂受潮。
焊丝在使用前盘入焊 丝盘时,应清除螺丝上的油污,焊剂在使用前亦要进行烘干。
船舶管系加工工艺
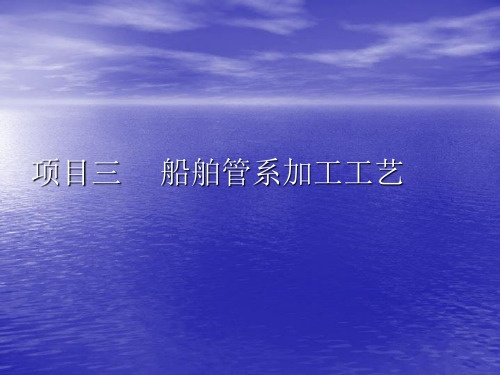
项目3.2 管子加工工艺
• • • • • • • • • • • • • • •
知识目标 1.了解管子切割的方法和使用场合; 2.了解管子焊接的方法和操作要点; 3.掌握管子弯曲的方法和操作过程; 4.了解管子弯曲时的要求; 5.了解弯管机床的类型和特点; . 6.掌握管子弯制的工艺过程; 7.掌握管子画线与校管的操作过程; 8.了解强度试验的作用和操作步骤; 9.掌握管子清理与表面处理的方法和工艺过程。 能力目标 1.能进行管子弯曲操作; 2.能编制管子弯制的工艺过程; 3.会对弯曲的管子进行校验; 4.能对管路系统进行强度试验。
• 当管子的公称通径较小时,一般用螺纹连接通舱管件(标 •
•
形管节)来代替上述的法兰连接通舱管件,螺纹连接通舱 管件一般采用碳素钢或铅黄铜制作。 碳素钢螺纹连接通舱管件适用于海水、淡水、油类、压缩 空气和温度低于400℃的蒸汽管路。 公称通径为6~25mm时,适用于公称压力低于10MPa;公 称通径32mm时,适用于公称压力低于4MPa的管路,铅黄 铜管只用于海水、淡水管路 。
电动无芯弯管机弯曲部分的示意图
弯模套在弯管机的主轴上,用键与轴配合并随着主轴一起 旋转。此外,弯管机台面上还配有电源机构;主轴控制盒,用 来控制弯模的顺转、停止和倒转等工作状态 。
(2)法兰焊接双面座板
• 用于管路穿过甲板、舱柜时,座板的两面
分别连接阀件、附件或管子。 • 双面座板与单面座板相比,多了一个凸肩 和双面安装双头螺栓。凸肩外径比相应法 兰外径大10—20mm,凸肩厚度为6— 12mm。其适用范围及其他结构尺寸基本与 单面座板相同。
• 法兰焊接双面座板如图3_4所示。其制造和
常用的如铬钼钢。对壁温超过450℃以上的 主蒸汽和过热蒸汽管,耐热钢与普通碳素 钢相比较,耐热钢具有两个特殊性能: • (1)高温强度 • (2)高温抗氧化性
船舶管件加工工艺(
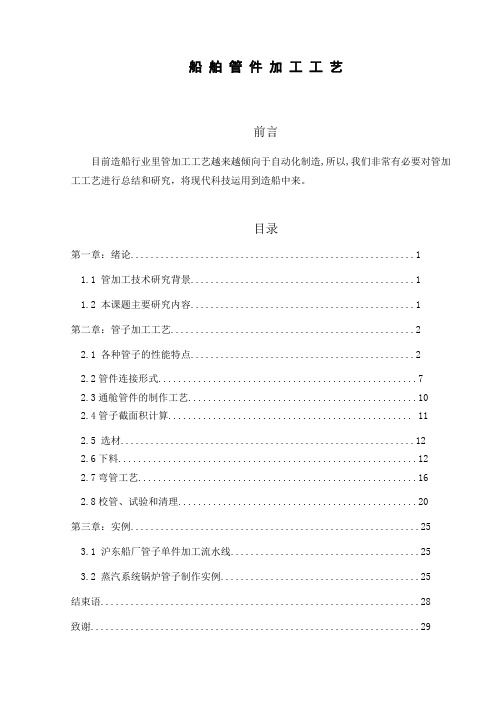
船舶管件加工工艺前言目前造船行业里管加工工艺越来越倾向于自动化制造,所以,我们非常有必要对管加工工艺进行总结和研究,将现代科技运用到造船中来。
目录第一章:绪论 (1)1.1 管加工技术研究背景 (1)1.2 本课题主要研究内容 (1)第二章:管子加工工艺 (2)2.1 各种管子的性能特点 (2)2.2管件连接形式 (7)2.3通舱管件的制作工艺 (10)2.4管子截面积计算 (11)2.5 选材 (12)2.6下料 (12)2.7弯管工艺 (16)2.8校管、试验和清理 (20)第三章:实例 (25)3.1 沪东船厂管子单件加工流水线 (25)3.2 蒸汽系统锅炉管子制作实例 (25)结束语 (28)致谢 (29)参考文献 (30)摘要随着造船科技的不断进步,管加工工艺越来越倾向于自动化制造,所以,我们有必要对管加工工艺进行总结和研究。
目前存在的问题:国内管子生产工艺仍和国外有一定的差距,加工方面,本身材料的强度和管材有关,也有后期的制造加工工艺有关,弯管的制造工艺以及支管仍然是比较难控制的。
本论文主要总结了现在各大船厂的管加工工艺,并且按照船舶管加工工艺的流程:下料——弯制——校管——焊接——泵磨——清洗,针对各种管子的性能特点,分析研究了几种管加工工艺中出现的问题和新技术,比如:弯管,焊接,切割,强度试验,弯管回弹问题的解决等等。
用了三种不同的方法确定了支管马鞍线和相贯线的方法:传统计算法,CAD作图分析法,PROE作图分析法。
基本确定了船舶管加工整个的工艺流程。
关键词:加工工艺流程管材特性新工艺方法管件连接计算放样第一章绪论1.1 管加工技术研究背景国内:武昌造船厂采取先焊后弯等新工艺,逐步建立全船关系计算机三维放样和管子加工流水线及自动化管子加工车间,减少了弯管废品率和各种消耗等。
国外:管子加工趋向于自动化流水线技术,自上世界70年代初开始,国内外船厂开始使用管子加工流水线,德国的奥斯得力公司已为世界各有关行业建造了50多条管子加工流水线,应用范围适合所有管子制造行业,其自动化程度可视客户的实际需要而定。
船用管子加工通用工艺汇总

热温度参照表4
表4
管子材料
开始弯曲温度°C
弯曲终了温度°C
碳钢
900〜1050
700
紫铜
850〜860
300
黄铜
600〜700
400
钼钢、钼铬钢
900〜1000
750
双金属
850
580
不锈钢
950〜1100
850
2211采用冷弯进行弯曲的铜和铜合金管,在弯曲后应进行退火 处理,退火温度为500〜700°C。
管系制作安装工艺
船用管子制作工艺
本文件适用于各类船舶下列规格管子的加工:外径在500mm以 下的无缝钢管和合金钢管、250mm以下的铜管和铜合金管(包括铜镍 管)、6英寸以下的水煤气管及其它金属管。
本文件可供船舶管系施工设计时选用。 对于特殊要求的管子应按设计要求加工。
1、材料
1.1管子材料应符合我国造船规范要求和有关国家标准的规定。 出口船舶用管材须符合该船舶入级相应的船级社要求。
2.2.3管子弯曲半径,一般采用2.5〜3倍管子外径,在管路布置 比较紧凑的地方,允许小于2.5倍,但不得小于2倍,较小弯曲半径 的管子,应采用定型弯头。
2.2.4弯管操作者,应熟悉弯管设备的结构、性能及其操作程度和 规则。
2.2.5有芯弯管前,管子内径与塞芯工作部分,应涂适量的润滑油
226有芯弯管时,芯棒的端头圆柱截面位置应超过与其垂直的模 具中心线,其超前值一般根据试验来决定,新安装和调试的弯管机可 参照表3选取。
3.2.2角尺支管和Y型支管应尽量少用。
3.2.3支管宜设在总管法兰近端,以便清除焊渣和毛剌。
船舶管系制作安装工艺汇总

东海船舶修造有限公司船舶管系制作安装工艺技术科编制Lenovo User2008-9-1船舶管系制作安装工艺为现代造船的发展,规范管系制作及安装,保证管系制作和安装质量,使船舶建造更加规范化、正规化所编制。
本工艺参照各种相关船舶建造标准、规范及本公司实际而编制。
管系布置、预制及安装流程原则、规则。
一.管系布置原则1.管系布置要层次分明,顺序为先大口径管,后小口径管。
管子的排列应尽可能平直,成组成束并列,整齐和美观,以最短的距离连接,达到最佳目的,避免不必要的迂回和斜交叉。
2.管系的布置间距(1) 并行管或交叉管,邻近两根管子(包括管子附件),间距应在20mm 以上。
(2) 对于需要包扎绝缘的管子,包好绝缘后,其外缘与相邻管子、管系附件或船体结构件的间距在30mm以上。
(3) 下列管子与电缆的间距应在100mm以上。
a.蒸汽管子绝缘层外表。
b.非水隔层绝缘的排气管外表。
c.工作压力9.8MPa(100kg/cm2)以上的高压空气管。
3.位置应便于安装和操作,各种管子应尽量沿准船体结构或箱柜的附近布置。
4在通道拆装维修及检查等必要的空间内,不应设置管路,对机械拆装、维修、检查等必要的空间应根据设备详图,经阅校核后再做最后决定。
5.当电缆、管子和通风管道在同一位置时,最好由上至下,按照电缆-管子-通风管的顺序布置。
6淡水管不得通过油舱,油管不得通过淡水舱,如不能避免时,应在油密隧道或套管内通过,海水管也尽量避免通过淡水舱,其它管子通过燃油舱时,管壁按规范要求加厚,且不得有可拆接头。
7.燃油舱柜的空气管、溢流管、测量管和注入管应避免通过居住舱室,如必须通过时,则通过该类舱室的管子不得有可拆接头。
8.配电板及重要仪器上方及后面不得设置蒸汽管、油管、水管、排气管、油柜和水柜。
特殊情况下必须布置时,则不得设置管接头,并采取有效的防护措施。
9.锅炉、烟道、蒸汽管、排气管及消音器的上方应避免设置油管及油柜,如无法避免时,油管不得有接头,且应装设滴油盘或其他防护设备。
- 1、下载文档前请自行甄别文档内容的完整性,平台不提供额外的编辑、内容补充、找答案等附加服务。
- 2、"仅部分预览"的文档,不可在线预览部分如存在完整性等问题,可反馈申请退款(可完整预览的文档不适用该条件!)。
- 3、如文档侵犯您的权益,请联系客服反馈,我们会尽快为您处理(人工客服工作时间:9:00-18:30)。
管系制作安装工艺(一)船用管子制作工艺本文件适用于各类船舶下列规格管子的加工:外径在500mm以下的无缝钢管和合金钢管、250mm以下的铜管和铜合金管(包括铜镍管)、6英寸以下的水煤气管及其它金属管。
本文件可供船舶管系施工设计时选用。
对于特殊要求的管子应按设计要求加工。
1、材料1.1 管子材料应符合我国造船规范要求和有关国家标准的规定。
出口船舶用管材须符合该船舶入级相应的船级社要求。
1.2 各种管材,必须具有制造厂的炉罐号和合格证书,如缺少证明时,应根据有关规定或订货要求补做试验,合格后方可使用。
1.3管子加工前,必须核对管子材料是否符合图纸要求。
1.4管子加工前,应对管材内外表面质量进行检查。
1.4.1无缝钢管和合金钢管,其内外表面不得有裂缝、折叠、分层、结疮、轧折、发纹等缺陷存在。
如有上述缺陷应予清除,清除部位壁厚的减薄不得超过该材料标准允许的负偏差。
1.4.2 焊接钢管内外表面不允许存在由于焊接引起的裂缝、咬口、飞溅、凹陷等缺陷。
1.4.3 有色金属管子,其表面应光滑清洁,不应有针孔、裂缝、气泡、分层、锈蚀等缺陷。
1.5碳素钢管、不锈钢管在订货时,应向制造厂提出退火处理要求。
1.6 法兰、套管、螺纹接头、异径接头、定型弯头等连接件,必须具有材质报告证件,方可使用。
2、管子弯曲加工2.1 弯管设备2.1.1 弯管机须经过设备管理部门检查验收,才能正式投入使用。
2.1.2 弯管模子、滑块或滑轮槽道和塞芯头部光洁和顺,切口处必须倒圆。
2.1.3 弯管模子和滑块的圆槽直径按表1。
表1 mm2.1.4 有芯弯管机、芯棒头部的外径和长度按表2。
表2 mm2.1.5 弯管机的工夹具/模具和附属设备应当定期检查和维修,以确保良好状态。
2.2 弯管技术要求2.2.1 管子的弯曲,一般采用冷弯的方法,在工厂缺少冷弯设备的情况下,允许采用热弯,但水煤气管不宜采用热弯,20号钢管不宜采用中频弯曲。
2.2.2 不锈钢管及合金钢管宜冷弯,如必须热弯时,不锈钢管加热应避免渗碳,而对淬硬倾向较大的合金钢管则不得浇水冷却。
2.2.3 管子弯曲半径,一般采用2.5~3倍管子外径,在管路布置比较紧凑的地方,允许小于2.5倍,但不得小于2倍,较小弯曲半径的管子,应采用定型弯头。
2.2.4 弯管操作者,应熟悉弯管设备的结构、性能及其操作程度和规则。
2.2.5 有芯弯管前,管子内径与塞芯工作部分,应涂适量的润滑油。
2.2.6有芯弯管时,芯棒的端头圆柱截面位置应超过与其垂直的模具中心线,其超前值一般根据试验来决定,新安装和调试的弯管机可参照表3选取。
表3注:表中D及d分别代表管子的外径和内径。
2.2.7 采用塞砂弯管时,应选用河沙,但也允许用铁砂或石英砂、河沙、石英砂的直径一般约为2~4mm,铁砂直径约为1mm。
砂子颗粒应均匀、干燥、清洁,不允许有水分和油污及可燃物等。
填砂可用抖动或敲击的方法填实,敲击时只允许用木锤,砂子填实后,用干燥木塞住管口。
2.2.8 弯曲焊接钢管和水煤气管时,应尽量将焊缝安置在因弯曲而引起弯形的最小方位上,如图1所示。
在弯立体弯头时,亦应考虑焊缝的位置。
2.2.9 弯制铜管、铝管时,必须小心地清除管子内外表面及机械设备与管子相接触部分所粘附的硬质杂物(如铁屑、砂土等)。
不允许在管子表面刻线,只许用铅笔或粉笔在管子表面划标记。
弯制时,应加少许润滑油以防止管材内外表面拉伤。
2.2.10 管子热弯时,加热应缓慢均匀和热透,且应防止过热。
加热温度参照表4。
表42.2.11 采用冷弯进行弯曲的铜和铜合金管,在弯曲后应进行退火处理,退火温度为500~700°C。
2.2.12 合金钢管和外径大于120mm碳素钢蒸气管,经弯曲后,应进行退火处理,碳素钢管加热至600~650°C,保持时间应为25mm 壁厚(或不足25mm 者)至少1小时,然后在平静空气中缓慢冷却,合金钢管的热处理根据成分决定。
2.2.13 管子热弯后,应清除表面的氧化皮.2.3 检验2.3.1 管子弯曲成型后,应根据CSQS1998《中国造船质量标准》进行检查。
2.3.2 椭圆度和收缩率的测量,采用外卡钳或游标卡尺,2.3.3 管子减薄量,允许采用超声波测厚仪进行测量。
2.3.4 检查合格后,应在管子上标以验收印记。
3、管子预制3.1 管子的切割与开孔3.1.1 有色金属管、水煤气管和外径不超过32mm的钢管,应用机械方法切割和开孔;对外径超过32mm钢管允许使用气割开孔;合金钢管切割和开孔的方法应根据材料成分决定。
3.1.2 管子上开孔和切割后,切口必须修整光顺,氧气渣和毛剌必须全部清除干净。
3.1.3 管子切割后,管端面和管子外表面的垂直度公差Δ,应符合表5所规定的要求。
表5 mm3.2 钢管焊接支管3.2.1钢管焊接支管型式一般如图2中a、b、c、d四种。
图23.2.2 角尺支管和Y型支管应尽量少用。
3.2.3 支管宜设在总管法兰近端,以便清除焊渣和毛剌。
3.2.4 支管不允许插入总管中,马鞍口应与总管很好吻合,其焊接尺寸要求见图2 的Ⅰ、Ⅱ、Ⅲ详图,当采用单面焊时L=0-1mm,双面焊L=1.5-2mm。
当支管内壁厚小于6mm时,不用开坡口。
3.2.5 总管上支管孔应同轴,其不同轴度不得大于±1mm。
3.2.6 支管高度在确保法兰连接螺丝安装方便下尽量缩短。
3.3 铜管焊接支管3.3.1 铜管焊接支管型式一般如图3中A、B两种。
3.3.2 当总管内径大于支管内径时采用图3中A型,当总管内径等于支管内径时采用图3中B型。
3.3.3 A型支管插入端不得超过领口最底点。
3.3.4 B型支管与总管交接处应相贯。
3.3.5 铜管支管也可以采用三通接头。
3.4 法兰连接3.4.1 钢管法兰连接型式和适用范围按表6。
注:(1)“不限”系指在造船规范所允许各系统管路使用的最高压力或最高温度范围内。
(2)B型法兰应用于蒸汽系统当压力大于1.6Mpa或温度大于300°C时,管子外径不得大于150mm。
sd3.4.3 装焊法兰时,法兰内壁与管子外表面之间的最大间隙在任何一点均不应超过2mm,径向相对两点的间隙总和不得超过3mm。
3.4.4 凡安装支管和弯头等配件的管子,宜将支管和弯头等配件焊完后,再装焊法兰,以防止焊接变形。
3.5 螺纹接头连接3.5.1 符合于国家标准或部标准的螺纹接头,可用于各种管子的连接,但应根据管路介质压力去选用各种型式的螺纹接头。
3.6 钢管的套管连接3.6.2 套管连接不得用于有可能发生疲劳、严重腐蚀或裂缝腐蚀之处,套管材料应与管路材料相同。
3.6.3 垂直位置的套管,如用于淡水、海水系统,应将下管端外套管内孔部位进行封底焊接,如是用于水平方向则可省略。
3.7铜管的对接3.7.1 管子对接可采用直接对焊、坡口对焊、衬圈对焊以及封底对焊等形式。
各型式的枝术要求见表9。
表9表93.7.2 异径管子的连接3.7.2.1 异径接头焊接有三种形式如图5,其接头的技术要求参照表9。
a.同心型b.异心型c.锥形图 53.7.2.2 异径法兰连接:形式如图6所示。
应严格控制工作介质流向,只许由小口径流向大口径。
图 63.7.3 管子与定型弯头连接的技术要求参照表9。
3.8 铜管的对接铜管的对接有直接对接,扩管搭接,套管搭接等形式,其结构形式和适应范围见表10。
表103.9 通舱管件3.9.1 当管子通过船舶各种水密、油密的隔舱、甲板,或船体加强梁结构时,应按表1.1各种型式通舱管件选用:表1.1注:A、B型通舱管件,仅适用于钢管。
C、D、B型舱管件可用于钢管和铜管。
3.9.2 通舱管件壁厚应大于或等于连接管子壁厚的1.25倍。
3.9.3 各通舱件的焊缝均要大于或等于管壁厚度。
3.10 虾壳式焊接弯管(斜接焊弯管)船舶管路不能采用机械冷弯及定型弯头时,可采用虾壳式焊接弯管,这种弯管一般适用于船舶的主副机大口径排气管,锅炉烟道及其他低压力管路等,其材料可用船用钢板或无缝钢管,其结构型式如图83.113.11.1 管子预制尺寸公差标准按表1.2。
表1.23.11.2 管子弯曲后,未装法兰前,须在平台上按表12第2、3、4项的角度公差进行检验,超出公差范围者须进行校正。
3.11.3 法兰、支管装配完毕,未烧焊前,按表12第1—6项的长度公差检验。
4、管子焊接4.1 焊接材料4.1.1 焊条、焊丝和焊剂应符合有关标准的规定或经验部门认可,所有材料应具有制造厂的产品合格证。
4.1.2 焊条必须存放干燥、通风良好的库房内,库房温度最好为10-35℃,相对湿度小于50%,严防焊条受潮变质,焊条在使用前,需根据其成分,进行不同温度的烘干。
4.1.3 焊丝和焊剂应存放于干燥通风的室内,严防焊丝生锈和焊剂受潮。
焊丝在使用前盘入焊丝盘时应清除螺丝上的油污,焊剂在使用前亦要进行烘干。
4.1.4 氧气、二氧化碳气瓶的灌气,应严格执行充灌技术规程,防止将空气、水分等杂质带入瓶内。
4.2 焊前准备4.2.1焊接部位要清洁干净,不能有油漆、油、锈、氧化皮或其他对焊接质量有害的附着物。
4.2.2 点焊定位的焊渣和叠焊前的焊渣都要清除干净。
4.2.3 根据管系的工作温度、压力和所载运的介质,选用焊缝型式、焊接方式和焊接材料。
所选用焊接材料的强度应不低于母材强度的下限,工作压力高于3.0 MPa的空气系统及过热蒸汽系统等管子与法兰的焊接,必须采用低氢型焊条。
4.2.4各厂按有关《焊工考试规则》,对焊工进行考试,合格者方可进行施焊。
4.2.5 在低温环境中焊接要求:4.2.5.1 一般碳素钢管焊接(含碳量0.23%以下)其环境温度不能低于-20℃。
4.2.5.2 合金钢管在低温区焊接时,应将工件进行预热,其预热温度和相应材料钢板预热温度相同。
4.2.5.3 管件应尽可能在车间焊接,避免受到雨、雪或强风的影响。
4.3 焊接技术要求4.3.1 钢管的对接接头、支管和法兰连接的接头应使用手工焊或埋弧半自动焊以及经验船部门认可的其他焊接方法。
氧-乙炔气体焊,限于管子半径不超过100mm或壁厚不超过9.5mm的钢管对接接头。
4.3.2 管子与法兰的连接应采用双面焊,焊缝尺寸应符合表6中的规定,DN≤25mm的管子经验船部门同意,允许单面焊,但焊后管端应进行扩管,使管壁紧靠法兰内孔。
4.3.3 DN≥100mm的直三通和斜三通支管应采用双面焊。
焊缝尺寸应符合图2中的规定。
对于不采用双面焊的其他支管经验船部门同意,允许采用单面焊,但必须保证焊缝质量。
4.3.4 管子的套管连接和对接的焊缝尺寸应符合表8和表9中的规定。
4.3.5滑油、燃油、液压系统及对清洁要求较高的系统的管子焊接和支管焊接时,如单面焊应采用氩弧焊作为封底焊(单面焊接双面成形);如双面焊则内圈焊缝须磨光。