精益生产基本概念介绍
精益生产简介及六西格玛基本概念
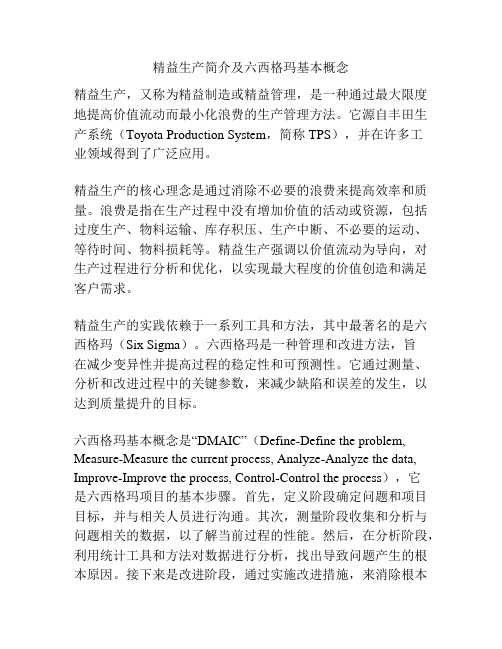
精益生产简介及六西格玛基本概念精益生产,又称为精益制造或精益管理,是一种通过最大限度地提高价值流动而最小化浪费的生产管理方法。
它源自丰田生产系统(Toyota Production System,简称TPS),并在许多工业领域得到了广泛应用。
精益生产的核心理念是通过消除不必要的浪费来提高效率和质量。
浪费是指在生产过程中没有增加价值的活动或资源,包括过度生产、物料运输、库存积压、生产中断、不必要的运动、等待时间、物料损耗等。
精益生产强调以价值流动为导向,对生产过程进行分析和优化,以实现最大程度的价值创造和满足客户需求。
精益生产的实践依赖于一系列工具和方法,其中最著名的是六西格玛(Six Sigma)。
六西格玛是一种管理和改进方法,旨在减少变异性并提高过程的稳定性和可预测性。
它通过测量、分析和改进过程中的关键参数,来减少缺陷和误差的发生,以达到质量提升的目标。
六西格玛基本概念是“DMAIC”(Define-Define the problem, Measure-Measure the current process, Analyze-Analyze the data, Improve-Improve the process, Control-Control the process),它是六西格玛项目的基本步骤。
首先,定义阶段确定问题和项目目标,并与相关人员进行沟通。
其次,测量阶段收集和分析与问题相关的数据,以了解当前过程的性能。
然后,在分析阶段,利用统计工具和方法对数据进行分析,找出导致问题产生的根本原因。
接下来是改进阶段,通过实施改进措施,来消除根本原因并改善过程表现。
最后,在控制阶段,确保改进持久化,并制定适当的监控和控制措施,以防止问题再次出现。
总之,精益生产是一种以消除浪费、提高质量和效率为目标的生产管理方法。
它借鉴了丰田生产系统的经验,并结合了六西格玛等管理工具和方法。
通过精益生产的实践,企业可以提高竞争力、满足客户需求,并实现持续的改进和创新。
精益生产基本概念介绍

精益生产基本概念介绍精益生产是一种以提高效率和降低浪费为核心的生产管理理念,旨在通过优化生产流程,满足客户需求,提高产品质量并降低成本。
精益生产最初由日本的丰田汽车公司引入并得到广泛应用。
它起源于日本的“丰田生产方式”(Toyota Production System,简称TPS),并得到了美国的“精益生产”(Lean Manufacturing)概念的发展和完善。
精益生产的核心理念是通过消除无效的活动和浪费来提高生产效率,以满足客户需求。
这种管理思想可以应用于各种生产领域,包括制造业、服务业、医疗保健等。
精益生产的基本概念包括以下几个方面:1. 价值:精益生产强调以客户价值为导向,将每个生产活动的价值与客户的需求联系起来。
只有在客户眼中具有价值的活动才是有意义的,其余的活动被视为浪费。
2. 浪费:精益生产关注浪费的问题,并试图消除它们。
七大浪费(Overproduction/超产、Waiting/等待、Transportation/运输、Overprocessing/超加工、Inventory/库存、Motion/移动、Defects/缺陷)被认为是造成资源浪费的主要原因。
3. 价值流:精益生产强调要了解和优化整个价值流程。
价值流程是指将原材料转化为最终产品的所有步骤和流程。
通过深入了解价值流,可以识别出浪费并采取相应的措施。
4. 拉动生产:精益生产提倡拉动生产,即根据客户需求进行生产,而不是根据内部生产能力。
拉动生产要求在生产单元间建立稳定的信号和流程,以确保在需要时引导和控制生产。
5. 持续改善:精益生产鼓励持续改进,通过定期检查生产流程和解决问题,以优化效率和质量。
持续改进是精益生产的核心原则之一,要求全员参与,持续提高生产效率和质量。
总之,精益生产是一种追求高效、高质量的生产管理理念。
它关注客户价值、消除浪费、优化价值流程,通过拉动生产和持续改善来实现最佳效果。
精益生产的理念和方法可以帮助企业提高竞争力,并在不断变化的市场环境中保持持续增长。
01.精益基本理念介绍
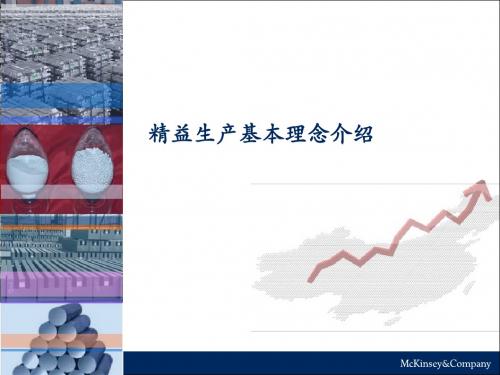
议程
▪ ▪ ▪
精益是一种系统 精益的历史 精益生产的运用
McKinsey & Company
| 1
精益的简单定义
精益是 . . .
精益不是 . . .
▪ 一整套综合原则 ▪ 响应客户需求 ▪ 持续追求完美地为客户
创造价值
▪ 仅仅是生产车间的事情 ▪ 仅限于重复装配 ▪ ▪
方式 一部改进方案 一套工具和技术
McKinsey & Company
GM
Ford
Toyota
| 8
议程
▪ ▪ ▪
精益是一种系统 精益的历史 精益生产的运用
McKinsey & Company
| 9
精益生产源于日本的丰田汽车生产系统 ……
“在丰田,生产一辆凌 志车所需要的人工数, 甚至比 (别的公司)在生 产线终端返工一辆顶级 德国豪华车所需要的人 工数还少” - (摘自 “改变了世界 的机器” The Machine that Changed the World)
McKinsey & Company
| 2
精益生产的主要好处
根本信念是四个主要目标的基础
客户满意度
安全
品质
交付
成本
▪
▪
竞争优势源自 人员 健康和安全是 所有事情中的 重中之重
▪
▪
必须对零缺陷 品质进行设计 和植入 任何缺陷都应 在产生之初即 得到发现并加 以解决
▪
▪
制定流程必须 考虑从端到端 的流程 只在需要的时 间和地点、按 照需要的数量 生产产品
| 5
但是大批量生产有许多不为人注意的陷阱
量产公司所遇到的问题: ▪ 许多公司只注意个别流程的生产率,他们采购大型、 运作迅速的机器,但这些机器不具生产弹性,且必须 批次生产 ▪ 「你可以有任何你想要的颜色,只要是黑色的都行!」 ▪ 但是市场在变 …
对精益生产的理解

对精益生产的理解精益生产是一种流程改善和效率提升的方法体系,旨在通过消除浪费、优化价值流、提升质量和降低成本,来实现企业的持续增长和竞争优势。
精益生产大体上可以分为五个基本原则:价值、价值流、流动、拉动和持续改进。
以下将对这五个基本原则进行详细解释。
价值:首先,精益生产将价值定义为符合顾客需求的产品或服务。
企业应该清楚了解顾客的需求,并将产品或服务的每个环节与顾客价值进行对比。
只有满足了顾客的需求,企业才能取得持续的成功。
价值流:其次,精益生产强调了对价值流的重视。
价值流是指产品或服务在生产过程中所经历的步骤和环节。
企业应该通过精确的价值流图,分析产品或服务的价值流,找出其中的瓶颈和浪费,以便优化生产流程。
流动:第三个原则是流动。
流动是指产品或服务在生产过程中连续无断裂地流动。
为了实现流动,企业需要根据顾客需求进行产品或服务的生产,并根据先进的生产管理技术,如精确计划、快速交付和柔性生产线等,来确保产品或服务的无缝流动。
拉动:第四个原则是拉动。
拉动是指根据顾客的需求,及时产出产品或服务,而不是根据内部的计划进行生产。
企业应该在接收到顾客订单后,根据订单的需求进行生产,以最大限度地降低库存和生产浪费,并确保及时交付顾客所需的产品或服务。
持续改进:最后一个原则是持续改进。
精益生产强调了对生产过程不断改进的重要性。
企业应该通过对生产过程的监控和分析,发现问题并采取相应的纠正措施,以提高产品或服务的质量和生产效率。
综上所述,精益生产是一种通过消除浪费、优化价值流、提升质量和降低成本的方法体系。
它通过五个基本原则——价值、价值流、流动、拉动和持续改进来指导企业改进生产过程,以达到持续增长和竞争优势的目标。
只有不断追求精益生产,企业才能在市场竞争中立于不败之地。
精益生产简介及六西格玛基本概念
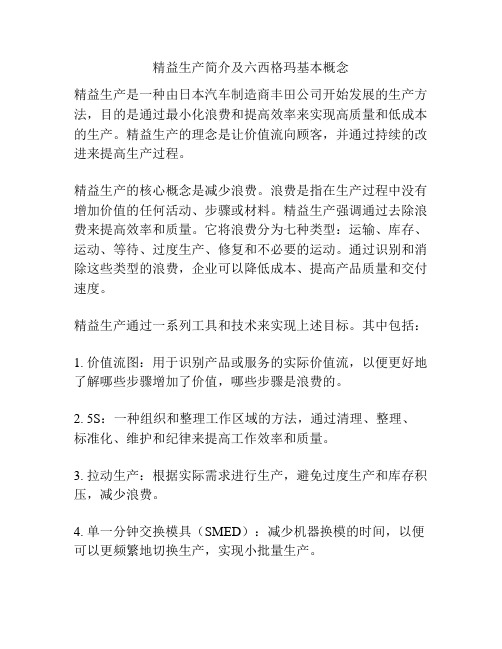
精益生产简介及六西格玛基本概念精益生产是一种由日本汽车制造商丰田公司开始发展的生产方法,目的是通过最小化浪费和提高效率来实现高质量和低成本的生产。
精益生产的理念是让价值流向顾客,并通过持续的改进来提高生产过程。
精益生产的核心概念是减少浪费。
浪费是指在生产过程中没有增加价值的任何活动、步骤或材料。
精益生产强调通过去除浪费来提高效率和质量。
它将浪费分为七种类型:运输、库存、运动、等待、过度生产、修复和不必要的运动。
通过识别和消除这些类型的浪费,企业可以降低成本、提高产品质量和交付速度。
精益生产通过一系列工具和技术来实现上述目标。
其中包括:1. 价值流图:用于识别产品或服务的实际价值流,以便更好地了解哪些步骤增加了价值,哪些步骤是浪费的。
2. 5S:一种组织和整理工作区域的方法,通过清理、整理、标准化、维护和纪律来提高工作效率和质量。
3. 拉动生产:根据实际需求进行生产,避免过度生产和库存积压,减少浪费。
4. 单一分钟交换模具(SMED):减少机器换模的时间,以便可以更频繁地切换生产,实现小批量生产。
六西格玛是另一种与精益生产相结合的管理方法。
六西格玛的目标是通过减少变异、提高质量和效率来满足客户需求。
它主要通过DMAIC(定义、测量、分析、改进和控制)的过程来实现。
1. 定义:明确项目目标和范围,确保所有团队成员对项目的目标有共同的理解。
2. 测量:收集相关数据,了解当前的业绩水平。
3. 分析:分析数据,识别潜在问题和改进机会。
4. 改进:制定和实施改进措施,以提高业绩和增加价值。
5. 控制:确保改进措施的可持续性,通过建立控制措施来监控和维持改进。
精益生产和六西格玛通常被联合应用,以实现连续改进和质量优化。
精益生产关注流程的效率和流畅性,而六西格玛则关注消除变异和提高质量。
通过结合这两种方法,企业可以实现高质量、低成本和高效率的生产。
精益生产和六西格玛是两种在管理领域中广泛应用的方法,它们提供了一个系统性的框架,帮助企业实现高质量、低成本、高效率的生产和服务。
精益生产方式思想基础
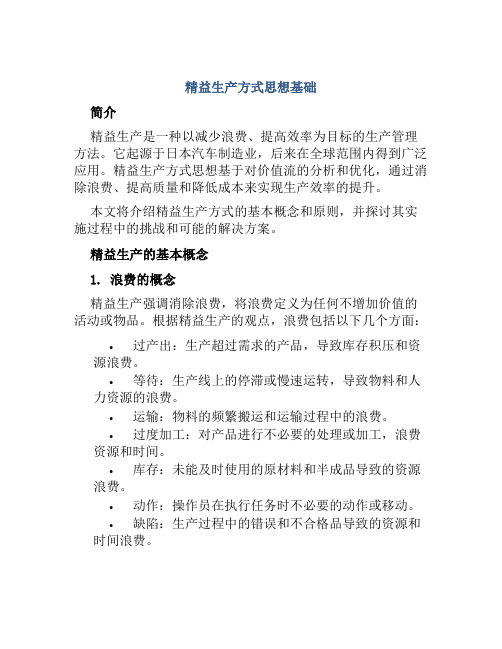
精益生产方式思想基础简介精益生产是一种以减少浪费、提高效率为目标的生产管理方法。
它起源于日本汽车制造业,后来在全球范围内得到广泛应用。
精益生产方式思想基于对价值流的分析和优化,通过消除浪费、提高质量和降低成本来实现生产效率的提升。
本文将介绍精益生产方式的基本概念和原则,并探讨其实施过程中的挑战和可能的解决方案。
精益生产的基本概念1. 浪费的概念精益生产强调消除浪费,将浪费定义为任何不增加价值的活动或物品。
根据精益生产的观点,浪费包括以下几个方面:•过产出:生产超过需求的产品,导致库存积压和资源浪费。
•等待:生产线上的停滞或慢速运转,导致物料和人力资源的浪费。
•运输:物料的频繁搬运和运输过程中的浪费。
•过度加工:对产品进行不必要的处理或加工,浪费资源和时间。
•库存:未能及时使用的原材料和半成品导致的资源浪费。
•动作:操作员在执行任务时不必要的动作或移动。
•缺陷:生产过程中的错误和不合格品导致的资源和时间浪费。
2. 价值流图精益生产使用价值流图来分析生产过程中的价值流和浪费。
价值流图是一种图形化工具,用于可视化生产过程中的各个环节和流程,并标识出其中的浪费点。
价值流图的绘制需要考虑以下几个要素:•价值流:从原材料到最终产品的所有流程。
•价值流中的价值增加环节:实际为产品添加价值的环节。
•流程时间:完成每个环节所需的时间。
•库存:每个环节中存储的物料数量。
•流程中的浪费:包括等待时间、运输时间、过度加工等。
3. 在精益生产中消除浪费的方式精益生产通过量化和深入分析浪费的根源,提出了一系列消除浪费的方式,包括:•质量管理:通过强调质量的重要性和培养质量意识,减少产品缺陷,避免浪费。
•5S方法:通过整理、整顿、清扫、清洁和纪律的执行,改善工作环境,提高工作效率。
•供应链优化:与供应商和合作伙伴合作,通过减少物料运输时间和库存,降低整体生产成本。
•作业标准化:定义明确的工作标准和流程,减少错误和重复工作。
•连续改进:通过监测和分析生产过程中的绩效指标,持续改进生产效率和质量。
精益生产的认识
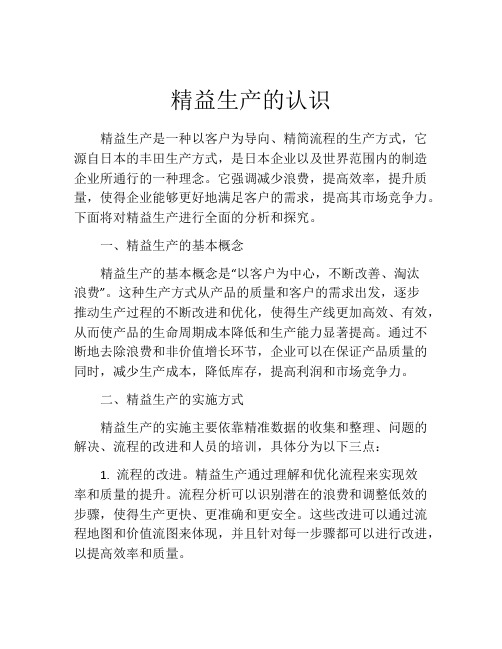
精益生产的认识精益生产是一种以客户为导向、精简流程的生产方式,它源自日本的丰田生产方式,是日本企业以及世界范围内的制造企业所通行的一种理念。
它强调减少浪费,提高效率,提升质量,使得企业能够更好地满足客户的需求,提高其市场竞争力。
下面将对精益生产进行全面的分析和探究。
一、精益生产的基本概念精益生产的基本概念是“以客户为中心,不断改善、淘汰浪费”。
这种生产方式从产品的质量和客户的需求出发,逐步推动生产过程的不断改进和优化,使得生产线更加高效、有效,从而使产品的生命周期成本降低和生产能力显著提高。
通过不断地去除浪费和非价值增长环节,企业可以在保证产品质量的同时,减少生产成本,降低库存,提高利润和市场竞争力。
二、精益生产的实施方式精益生产的实施主要依靠精准数据的收集和整理、问题的解决、流程的改进和人员的培训,具体分为以下三点:1. 流程的改进。
精益生产通过理解和优化流程来实现效率和质量的提升。
流程分析可以识别潜在的浪费和调整低效的步骤,使得生产更快、更准确和更安全。
这些改进可以通过流程地图和价值流图来体现,并且针对每一步骤都可以进行改进,以提高效率和质量。
2. 领导风险管理。
领导风险管理是指公司领导团队的参与和支持。
在实施精益生产的过程中,每个人都需要参与,领导团队可以帮助员工识别问题并为他们提供必需的资源,以便进行改进和创新。
3. 培训和参与。
教育和培训是实施精益生产的关键。
员工需要盲目地支持和协作,以确保各个部门之间的协同工作。
员工还需要具备分析和解决问题的技能,以帮助公司改进过程、降低成本、提高质量和效率。
三、精益生产的优点精益生产可谓是一个非常好的生产方式,具有诸多优点。
接下来,我们将对精益生产的优点进行简要总结。
1. 增加顾客满意度。
精益生产的目标是满足客户需求。
通过优化流程和减少浪费,提高生产效率和质量,客户将获得高质量的产品,既满足顾客需求,又提高了客户满意度。
2. 降低成本和库存。
精益生产敦促厂商最大化地利用现有的资源和员工技能,减少不必要的浪费,从而有效地提高效率,降低生产成本和库存。
精益生产的定义及基本原则
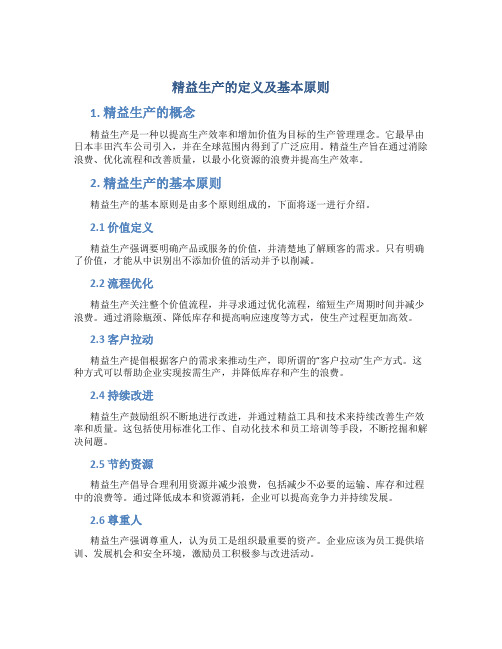
精益生产的定义及基本原则1. 精益生产的概念精益生产是一种以提高生产效率和增加价值为目标的生产管理理念。
它最早由日本丰田汽车公司引入,并在全球范围内得到了广泛应用。
精益生产旨在通过消除浪费、优化流程和改善质量,以最小化资源的浪费并提高生产效率。
2. 精益生产的基本原则精益生产的基本原则是由多个原则组成的,下面将逐一进行介绍。
2.1 价值定义精益生产强调要明确产品或服务的价值,并清楚地了解顾客的需求。
只有明确了价值,才能从中识别出不添加价值的活动并予以削减。
2.2 流程优化精益生产关注整个价值流程,并寻求通过优化流程,缩短生产周期时间并减少浪费。
通过消除瓶颈、降低库存和提高响应速度等方式,使生产过程更加高效。
2.3 客户拉动精益生产提倡根据客户的需求来推动生产,即所谓的“客户拉动”生产方式。
这种方式可以帮助企业实现按需生产,并降低库存和产生的浪费。
2.4 持续改进精益生产鼓励组织不断地进行改进,并通过精益工具和技术来持续改善生产效率和质量。
这包括使用标准化工作、自动化技术和员工培训等手段,不断挖掘和解决问题。
2.5 节约资源精益生产倡导合理利用资源并减少浪费,包括减少不必要的运输、库存和过程中的浪费等。
通过降低成本和资源消耗,企业可以提高竞争力并持续发展。
2.6 尊重人精益生产强调尊重人,认为员工是组织最重要的资产。
企业应该为员工提供培训、发展机会和安全环境,激励员工积极参与改进活动。
3. 精益生产的实施步骤实施精益生产需要经过一系列的步骤,下面将进行简要介绍。
3.1 确定目标首先,组织需要明确实施精益生产的目标,并将其与组织的战略目标进行对齐。
明确的目标可以帮助组织在实施过程中保持目标导向性。
3.2 培训和教育实施精益生产需要员工具备相应的知识和技能。
因此,组织需要为员工提供相关的培训和教育,使其了解精益生产的原理和方法。
3.3 流程改善精益生产强调流程的优化,因此,组织需要对现有的生产流程进行分析和评估,找出其中的问题和瓶颈,并采取相应的改进措施。
精益生产资料全集

精益生产资料全集精益生产是一种以提高效率、降低浪费为目标的生产管理方法。
它起源于日本汽车制造业,如今已在全球范围内得到广泛应用。
精益生产注重对生产过程进行优化,以最小的资源投入获得最大的产出,并通过消除浪费、优化价值流动、提高质量等手段来实现业务成功。
本文将介绍精益生产的基本原理和实施方法,以及相关的资料推荐,供读者参考。
一、精益生产的基本原理1.1 价值观点:精益生产强调价值链的优化,即从供应商到客户之间的整个价值流动过程。
通过深入了解客户需求,消除浪费和不必要的环节,实现高效的价值创造。
1.2 浪费的分类:精益生产将浪费分为七种不同类型,包括超生产、等待、库存、运输、过程、不合格品和不充分发挥工人创造力的浪费。
通过分析并消除每一种浪费,以提高生产效率和质量。
1.3 持续改进:精益生产强调持续改进的重要性,倡导员工参与和推动改进工作。
通过集思广益和寻找问题根本原因,实现生产过程的不断优化和创新。
二、精益生产的实施方法2.1 5S管理:5S是精益生产实施的关键步骤之一,包括整理、整顿、清扫、清洁和素养。
通过对工作区域的组织和清理、标准化和纪律化管理,提高工作效率和质量。
2.2 价值流映射:价值流映射是分析和改进价值流程的工具,通过绘制现有过程的价值流程图,找出浪费和瓶颈,并制定改进措施来优化流程。
2.3 单元化生产:单元化生产将生产过程分为小组或小单元,每个单元具有完整的生产能力。
这样可以减少传统大批量生产带来的库存和等待时间,提高生产效率和灵活性。
2.4 按需生产:精益生产倡导进行按需生产,即根据客户需求进行生产,避免超生产和过度库存的产生。
三、精益生产资料推荐3.1 《精益生产入门》:作者詹姆斯·P.沃默克(James P. Womack),这本书详细介绍了精益生产的基本概念、原则和实施方法。
3.2 《精益思维》:作者丹尼尔·T.琼斯(Daniel T. Jones),该书从思维方式的角度阐释了精益生产的精髓和核心要素。
精益生产的定义及基本原则

精益生产的定义及基本原则1. 精益生产的定义精益生产(Lean manufacturing),又称精益生产制造,是一种优化生产流程、提高生产效率和质量的管理方法。
它起源于日本的丰田汽车公司,是丰田生产方式(Toyota Production System,简称TPS)的核心理念之一。
精益生产强调通过消除浪费、提高质量和提升员工参与度来实现持续改进。
2. 精益生产的基本原则精益生产的基本原则主要包括以下几个方面:2.1. 价值流分析价值流分析是精益生产的核心工具之一,它用于评估产品价值链中的所有步骤并确定哪些步骤是不必要的或浪费的。
通过对价值流的分析,可以找出并消除各种浪费,从而提高生产效率和质量。
2.2. 浪费的削减精益生产的目标之一就是减少或消除各种浪费。
浪费是指在生产过程中没有增加价值的活动或材料。
常见的浪费包括超产、等待、运输、过度加工、库存积压、运动不必要、修补和不合格品。
通过精益生产的方法和工具,可以识别并消除这些浪费,从而提高生产效率。
2.3. 一次交付精益生产追求一次交付的原则,即在生产过程中尽可能减少不必要的中间步骤和环节,提高产品的交付速度。
通过减少等待时间和库存积压,可以降低生产成本,提高客户满意度。
2.4. 拉动生产拉动生产是精益生产的另一个核心原则,它强调根据顾客需求进行生产,而不是预测需求并进行大批量生产。
通过拉动生产,可以减少库存积压、降低生产成本,并更好地满足顾客需求。
2.5. 经过验证的改进精益生产鼓励持续改进,但改进应该是基于实证数据和验证的。
通过收集和分析数据,可以确定改进的方向和效果,并逐步优化生产过程。
2.6. 员工参与和自主决策精益生产强调员工的参与和自主决策,鼓励员工发现问题、提出改进意见,并参与到改进过程中。
通过培养员工的创新能力和团队合作精神,可以不断改进生产效率和质量。
2.7. 整体优化精益生产追求整体优化,而不是单纯追求局部的改进。
它强调各个环节之间的协调和协作,通过整体优化来提高生产效率和质量。
JIT精益生产的基本知识

JIT精益生产的基本知识一、什么是JIT精益生产?JIT(Just-in-Time)精益生产是一种生产管理方法,旨在实现以最少的库存、最小的费用和最高的效率来满足客户需求。
其核心思想是在生产的每一步都不浪费时间、劳力和资源,以实现高效的生产流程。
二、JIT精益生产的原理1.零库存原则:JIT强调减少库存量,只在需要的时候才进行生产,有效降低库存成本和过剩库存的风险。
2.及时生产:产品在需要的时候才开始生产,以减少库存积压和生产周期,提高生产效率。
3.拉动生产:JIT通过“拉动式生产”,以客户需求为导向,根据实际订单推动生产,避免过度生产和浪费。
4.持续改进:JIT倡导持续改进和优化生产流程,促进团队协作和精益生产文化的建设。
三、JIT精益生产的优势1.降低成本:减少库存和废料,提高生产效率,降低生产成本。
2.提高质量:通过减少浪费和优化生产流程,提高产品质量和客户满意度。
3.提升交付速度:JIT生产方式能够更快速地响应客户需求,提高交付速度和服务水平。
4.增强竞争力:JIT可以帮助企业提升竞争力,降低生产周期,适应市场变化,实现持续发展。
四、如何实施JIT精益生产1.建立稳定的供应链:与供应商建立稳定的合作关系,确保物料供应的稳定和及时。
2.实施流程再造:对生产流程进行优化和改进,消除浪费,提高生产效率。
3.培训员工:向员工提供JIT精益生产的培训,增强他们的生产技能和质量意识。
4.持续改进:制定并实施持续改进计划,对生产流程和产品质量进行不断改进。
五、JIT精益生产的案例分析1. 丰田汽车丰田汽车采用JIT精益生产方式,通过精细的供应链管理和及时生产,实现了高效的制造和交付,提高了产品质量和客户满意度。
2. 联想集团联想集团在生产管理中推行JIT精益生产,通过优化生产流程和降低库存,提高了生产效率和竞争力,实现了持续发展。
六、结语JIT精益生产是一种重要的生产管理方法,对企业提高效率、降低成本、提高竞争力具有重要意义。
精益生产的基本原理概述

戴尔电脑公司
精益生产在戴尔电脑公司的应用 戴尔电脑公司实施精益生产的背景 戴尔电脑公司实施精益生产的具体措施 戴尔电脑公司实施精益生产的效果与影响
其他成功应用精益生产的公司
丰田汽车:通过精益生产,提高生产效率,降低成本,成为全球最大的汽车制造商之一 戴尔电脑:采用精益生产,优化供应链管理,提高产品质量和客户满意度 苹果公司:通过精益生产,提高产品质量和生产效率,成为全球最具影响力的科技公司之一 沃尔玛:通过精益生产,优化库存管理和物流配送,提高运营效率和客户满意度
精益生产的实施步骤
明确目标
确定改进目标:明确要解决的问题和改进的目标 制定计划:制定详细的实施计划,包括时间表、责任人、所需资源等 培训员工:对员工进行精益生产理念的培训,提高员工的意识和技能 建立团队:组建专门的精益生产团队,负责实施精益生产计划 持续改进:在实施过程中不断发现问题并进行改进,实现持续优化
优势
本田汽车公司的 精益生产实践: 通过减少库存、 优化生产流程和 改善产品质量, 提高生产效率和
客户满意度
精益生产在本田 汽车公司的成功 案例:介绍一些 成功的精益生产 案例,如减少库 存、优化生产流 程和改善产品质 量等方面的成功
实践
本田汽车公司对 精益生产的贡献: 介绍本田汽车公 司对精益生产理 论的贡献和实践 经验,以及对其 他企业的启示和
局限性与挑战
• 局限性: a. 适用范围有限:精益生产主要适用于重复性生产过程,对于一次性或创新性项目可能不太适用。 b. 依赖员工技能:精益生产需要员工具备较高的技能和素质,否则难以实现预期的效果。 c. 投入成本较高: 实施精益生产需要投入大量的人力、物力和财力,对于一些小型企业可能难以承受。
精益生产定义 精益生产的 起源
精益生产基本概念介绍

精益生产基本概念介绍精益生产是一种管理方法,旨在通过降低浪费和提高价值创造活动来改善生产过程。
它起源于丰田生产系统(Toyota Production System),并已在全球范围内广泛采用。
下面将介绍精益生产的基本概念。
1. 价值创造:精益生产的核心理念是将价值创造活动最大化。
价值创造是指顾客愿意为之支付的产品或服务。
所有不增加产品或服务价值的活动都被视为浪费。
2. 浪费的分类:精益生产将浪费分为七个主要类别:过产、等待、运输、无用存储、过度加工、运动和缺陷。
通过减少或消除这些浪费,企业能够更高效地利用资源。
3. 价值流映射:精益生产使用价值流映射来识别和分析整个价值流程。
价值流映射是一种工具,通过绘制产品或服务的流程图,清楚地显示价值创造和非价值创造的步骤。
4. 拉动生产:传统的生产方式是按计划预测的需求来推动生产。
而精益生产采用拉动生产的原则,即根据实际需求进行生产,以避免过产和存货积压。
5. 连续改进:精益生产倡导持续的改进和学习文化。
通过员工参与和团队合作,不断寻找和消除浪费,达到更高的效率和质量水平。
6. 人员培训与发展:精益生产注重员工的培训和发展,以提高他们的技能和专业能力。
员工的积极参与和贡献被认为是实现精益生产的关键因素之一。
7. 全员参与:精益生产鼓励组织内全部员工参与到改进活动中来。
通过倾听和尊重员工的意见和建议,组织可以发现更多的机会来提高效率和质量。
精益生产的目标是通过不断地消除浪费和改善流程来提供更高价值的产品和服务,同时实现更高的效率和质量水平。
它不仅适用于制造业,也可以应用于服务业和其他领域。
精益生产的理念和原则可以帮助组织实现持续的改进和竞争优势。
精益生产(Lean Production)是由日本汽车制造商丰田引入并发展起来的一个管理方法和生产哲学。
它的核心概念是通过降低浪费和提高价值创造的活动来改进生产过程,以实现更高的效率、更低的成本和更好的质量。
精益生产的理念源于丰田生产系统(Toyota Production System),该系统的目标是最大限度地提高效率和质量,并在满足客户需求的同时实现成本控制。
精益生产及八大浪费

精益生产及八大浪费简介精益生产是一种高效的生产管理方法,旨在最大限度地减少浪费,提高生产效率。
八大浪费是精益生产中的核心概念之一,它指的是在生产过程中可能会发生的各种浪费现象。
本文将介绍精益生产的基本原理以及八大浪费的具体内容。
一、精益生产的基本原理精益生产的基本原理是通过不断地消除各种浪费现象,提高生产效率,实现产品和服务的快速交付。
其核心是以价值为导向的生产方式,追求高效、质量和灵活性。
在精益生产中,价值是以顾客需求为基础来定义的,任何与顾客需求不相关的活动被认为是浪费。
因此,精益生产的目标是尽可能地消除各种浪费现象,提供符合顾客需求的产品和服务。
二、八大浪费八大浪费是精益生产中的核心概念,包括以下八个方面的浪费:1. 运输浪费运输浪费是指在生产过程中因为物料、产品或人员的频繁运输而造成的资源浪费。
过多的运输会增加物料丢失和损坏的风险,并且还会占用额外的时间和空间。
减少运输浪费的方法包括优化物料存储和布局、优化生产流程等。
2. 库存浪费库存浪费是指生产过程中因为过多的存货而造成的资源浪费。
过多的库存会增加资金占用和仓储成本,并且会增加物料过期和损坏的风险。
减少库存浪费的方法包括优化生产计划、实施“小批量多次”的生产方式等。
3. 过程浪费过程浪费是指生产过程中因为生产方法不合理而造成的资源浪费。
过程浪费包括生产线不平衡、生产步骤重复、无效的工序等。
减少过程浪费的方法包括优化生产工艺、减少不必要的工序、实施自动化等。
4. 待机浪费待机浪费是指生产过程中因为生产设备空闲而造成的资源浪费。
设备的待机会占用不必要的时间和能源,增加了生产的周期和成本。
减少待机浪费的方法包括优化生产计划、提高设备利用率等。
5. 过度加工浪费过度加工浪费是指生产过程中因为进行不必要的加工或处理而造成的资源浪费。
过度加工会浪费时间、人力和能源,并且增加生产的成本。
减少过度加工浪费的方法包括优化生产流程、取消不必要的加工步骤等。
精益和六西格玛

精益和六西格玛简介精益和六西格玛是两种流程改进方法,目的都是提高组织的效率和质量。
精益以最小化资源浪费为核心,通过优化流程和流程中的价值流来实现效率提升;而六西格玛则以减少变异和缺陷为核心,通过数据驱动的方法来实现质量的提升。
本文将介绍精益和六西格玛的基本概念、应用场景以及优劣势。
精益概念精益生产(Lean Production)是由日本丰田汽车公司引入的,旨在通过消除浪费来优化生产过程和提高效率。
精益的核心理念是“为顾客创造价值,通过最小化浪费实现效率提升”。
基本原则精益生产有五大基本原则,分别是: 1. 价值定义:明确顾客对产品或服务的价值定义,只提供顾客需要的价值,减少无价值的工作。
2. 价值流映射:通过绘制价值流图,识别出影响整个价值流的活动,找出浪费的环节并进行改进。
3. 流程平衡:优化工作流程,减少瓶颈和等待时间。
4. 像流水线一样运作:通过优化生产流程和物料流动,实现高效率的生产。
5. 持续改进:建立持续改进的文化,鼓励员工参与改进和提出问题。
应用场景精益生产方法可以应用于各种组织和行业,包括制造业、服务业、医疗机构等。
精益的目标是提供高质量的产品和服务,并以尽可能低的成本实现。
优缺点精益生产方法的优点包括: - 降低成本:通过去除浪费,减少不必要的资源消耗,从而降低成本。
- 提高质量:通过优化流程,减少缺陷和错误,提高产品和服务的质量。
- 增加响应速度:精益生产方法可以缩短生产周期,提高生产效率,从而更快地满足顾客需求。
然而,精益生产方法也存在一些限制和缺点: - 对企业文化的要求较高:精益生产需要建立持续改进的文化,这对企业的领导力和员工参与度提出了要求。
- 不适用于所有行业:精益生产方法更适用于连续生产型行业,对于项目型行业可能不太适用。
- 需要长期投入:精益生产是一项长期的工作,需要持续的投入和改进。
六西格玛概念六西格玛(Six Sigma)起源于美国通用电气公司,是一种通过数据驱动的流程改进方法,旨在减少变异和缺陷,提高质量和效率。
精益生产5项基本原则
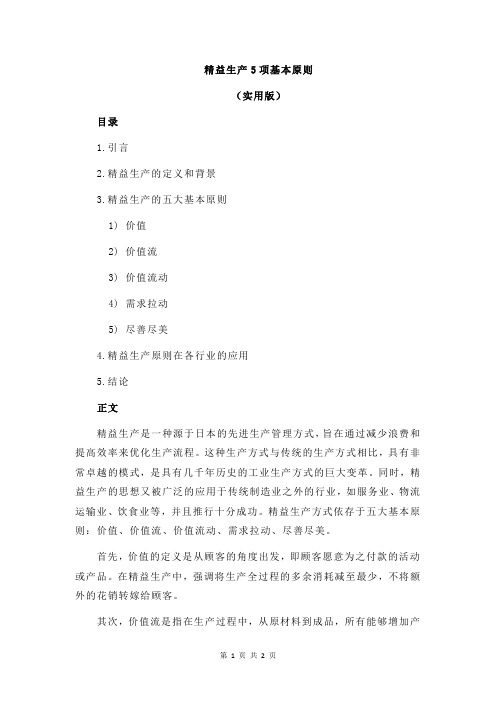
精益生产5项基本原则(实用版)目录1.引言2.精益生产的定义和背景3.精益生产的五大基本原则1) 价值2) 价值流3) 价值流动4) 需求拉动5) 尽善尽美4.精益生产原则在各行业的应用5.结论正文精益生产是一种源于日本的先进生产管理方式,旨在通过减少浪费和提高效率来优化生产流程。
这种生产方式与传统的生产方式相比,具有非常卓越的模式,是具有几千年历史的工业生产方式的巨大变革。
同时,精益生产的思想又被广泛的应用于传统制造业之外的行业,如服务业、物流运输业、饮食业等,并且推行十分成功。
精益生产方式依存于五大基本原则:价值、价值流、价值流动、需求拉动、尽善尽美。
首先,价值的定义是从顾客的角度出发,即顾客愿意为之付款的活动或产品。
在精益生产中,强调将生产全过程的多余消耗减至最少,不将额外的花销转嫁给顾客。
其次,价值流是指在生产过程中,从原材料到成品,所有能够增加产品价值的步骤。
精益生产要求识别并优化这些价值流,以提高生产效率。
第三,价值流动是指在生产过程中,让价值顺畅地流动,减少阻碍和浪费。
这意味着生产流程需要尽可能地简洁、高效,以便快速满足客户需求。
第四,需求拉动是指根据客户的需求来调整生产计划。
精益生产强调,生产计划应该根据客户的订单来制定,以确保生产的产品能够满足市场需求。
最后,尽善尽美是指精益生产要求不断改进生产过程,以追求完美。
这个原则强调,任何环节的改进都可以为整个生产流程带来益处,从而提高效率和质量。
总之,精益生产的五大基本原则为价值、价值流、价值流动、需求拉动和尽善尽美。
这些原则不仅适用于制造业,还可以广泛应用于其他行业。
精益生产基础知识|精益生产的基础是什么

精益生产管理基础知识一、精益生产的概念1、什么是精益生产?精益生产是一种以最大限度地减少运营成本为主要目标的生产方式。
(总的意思是“少的投入多的产出”。
)2、概念理解(1)精少而精,不投入多余生产要素,只在适当时间生产必要的产品。
(2)益所有经营活动有益有效,具有经济性。
(3)传统管理模式与精益生产管理模式的区别传统管理模式是在成本不变的前提下通过提高产品销售价格增加利润;精益生产管理模式是在产品销售价格不变的前提下通过降低生产成本增加利润。
二、精益生产的思想1、精益生产的思想通过消除生产所有环节上的不增值活动,来达到降低成本、缩短生产周期和改善质量的目的。
2、思想理解(1)关注流程用“尽善尽美”的思想创造流程价值。
即从营销到投产的设计流程;从定货到送货的信息流程;从原材料到产品的转换流程;全交付周期的支持和服务过程。
(2)为客户提供“尽善尽美”的价值,消除不必要的不增值的活动,最大限度实现“精益生产”的目的。
三、精益生产的目标1、精益生产的目标通过消除浪费、降低成本、提高质量、缩短制造周期,获得利润。
2、目标理解(1)两个“基本目标”一是不断取消那些不增加产品价值的工作,即“排除浪费,降低成本”;二是能快速应对市场的需求。
(2)一个“最终目标”利润最大化。
四、精益生产的核心1、精益生产的核心消除一切浪费!持续不断改善!2、核心理解(1)什么是浪费?不增加价值的活动就是浪费。
(2)尽管是增加价值的活动,所用的资源超过了“绝对最少”的界限,也是浪费。
(3)用不同的评判标准去判断一个动作、行为、方法或计划时,所得到的浪费程度都会不同。
(4)到处都存在浪费;只要存在浪费,肯定会有更好的解决方法。
(5)企业中常见的七大浪费①制造过多(生产过剩)的浪费;②搬运的浪费;③等待的浪费;④加工(不增值的工艺过程)的浪费;⑤库存的浪费;⑥动作的浪费;⑦不良(返工、修正)的浪费。
五、精益生产管理的内容及实施路线图1、精益生产管理的内容6S现场管理、成本管理、设备管理、质量管理、安全管理、流程管理等内容。
精益生产和六西格玛基本概念

精益生产和六西格玛基本概念1. 精益生产精益生产是一种管理方法,旨在通过最大限度地减少浪费和提高价值流程的效率,以实现高质量、高效率和高客户满意度。
精益生产方法起源于日本汽车制造商丰田和日产,后来被广泛应用于其他行业。
精益生产的核心原则是减少浪费,包括以下几个方面:1.1. 运输减少在物料运输过程中的不必要移动,以降低物料运输的成本和时间。
1.2. 库存尽量减少库存,以降低库存管理的成本和风险。
通过在生产过程中实施“拉动”而不是“推动”的方式,使得物料只在需要的时候才被生产和使用。
1.3. 动作优化工作流程,减少不必要的动作和动作的重复,以提高生产效率。
1.4. 等待减少生产过程中的等待时间,以提高整体生产效率。
通过合理规划和组织工作流程,确保每个环节都能够及时得到满足。
1.5. 修复优化生产过程,以减少错误和故障的修复工作。
通过实施预防性维护和质量控制,确保产品质量和生产效率。
2. 六西格玛六西格玛是一种管理方法,旨在通过降低过程的变异性和缺陷率,提高过程的表现和可靠性。
它是由著名公司摩托罗拉于20世纪80年代所开发并广泛应用的一种管理方法。
六西格玛方法主要通过以下几个步骤来实现目标:2.1. 定义阶段在这个阶段,确定项目范围、界定问题和设定目标。
通过明确问题的关键要素和关键绩效指标,为后续的分析和改进工作打下基础。
2.2. 测量阶段在这个阶段,收集数据,分析过程的当前状态和性能。
通过测量和记录关键指标,了解过程的变异性和缺陷率。
2.3. 分析阶段在这个阶段,通过统计方法和数据分析工具,找出过程中的关键影响因素,并分析其对过程性能的影响。
确定问题的根本原因,并寻找改进的机会。
2.4. 改进阶段在这个阶段,通过改进过程和消除根本原因来提高过程性能。
使用各种改进工具和方法,如流程重塑、变革管理等,确保改进措施的有效实施。
2.5. 控制阶段在这个阶段,通过制定控制计划和监控措施,确保过程改进的可持续性和稳定性。
精益生产基本知识点

精益生产基本知识问与答1、什么事精益生产?p9精益生产,又称精良生产,其中“精”表示精良、精确、精美,即少而精,更少的投入,只是在适当的时间生产必要数量的市场急需产品(或下道工序急需的产品);“益”表示利益、效率,即所有经营活动都要有益、有效,并具有经济性。
精益生产就是及时制造,消灭故障,消除一切浪费,向零缺陷、零库存进军。
2、精益生产主要特点有哪些?p9(1)一切为用户着想,产品直接面向用户,将用户纳入产品开发过程,以适应产品小批量、多元化、尽可能短的交货期生产,最大限度地满足用户需求,真正体现用户是“上帝”的精神。
(2)实施一个流,采用准时生产方式和看板管理,即只在需要的时候,按必需的量生产所需的商品,能够最大限度减少闲置时间、作业交换时间、库存、劣质品、不合格的供应商,缩短产品开发设计周期,使得导致成本提高的零部件库存减少直至接近于零,加快产品周期、减少规模效益影响;寻找、纠正和解决质量问题,提高生产率,减少浪费。
(3)以“人”为中心,部分权力下放,员工参与管理,充分发挥一线员工的积极性和创造性,从而降低产品返修率。
此外,还须满足员工学习新知识和实现自我价值的愿望,形成独特和谐的企业文化。
(4)以“精简”为手段,实现组织机构精简化,去掉一切多余的环节和人员。
强调团队工作组方式,集成各方面人才进行产品的并行设计,对产品的开发和生产具有很强的指导和集成能力。
(5)实现准时供货方式,保证最小的库存和最少的在制品数,与供货商建立良好的合作关系,相互信任、相互支持,利益共享。
(6)追求的目标是精益求精、尽善尽美、不断降低成本,做到零废品、零库存和产品品种的多样化。
3、精益思想的五大原则是什么?p121.精益思想第一大原则:价值站在客户立场上来审视企业的产品设计、制造过程、服务项目,就会发现太多的浪费,从而不满足客户需求到过多功能和多余的非增值消耗。
因此企业在制造过程中应实现增值活动,即实现增值动作和时间,如改变形状,改变性能、组装、包装等,已达到产品增值的目的,提供给用户真正需要的价值。
- 1、下载文档前请自行甄别文档内容的完整性,平台不提供额外的编辑、内容补充、找答案等附加服务。
- 2、"仅部分预览"的文档,不可在线预览部分如存在完整性等问题,可反馈申请退款(可完整预览的文档不适用该条件!)。
- 3、如文档侵犯您的权益,请联系客服反馈,我们会尽快为您处理(人工客服工作时间:9:00-18:30)。
- 找料,计算
- ARF, looking for parts, counting;
• 没有价值的行为会增加生产的成本
• Non-value added activities add cost to manufacturing.
• 要想在竞争激烈的商业环境下生存,就 必须最充分地利用资源
• To survive in this competitive business environment, there is a need to maximise utilisation of resources.
• 你的技能和领导能力的提高从而得到认 可
• Your skills and leadership development and the opportunity to be recognized.
什么是有附加值的活动?/ What are Value-Added (VA) activities ?
• 保持公司的Βιβλιοθήκη 益• Sustained profitability of the company.
对于个人
For You • 为了在旭电的安全工作
• Job security for Solectron
• 集中你的时间成就有价值的分派任务
• Focus your time and effort on valuable tasks.
Efficiency Focus
一个流 Single Piece Flow
平衡化生产 Takt Time Production
利用数据分析来解决系统的问题
Systematic Problem Solving Via Data Analysis
自动化 Stop @ Abnormality
检查缺陷 Error Proof
例如/ Examples: - 视觉检查与测试
- Visual inspection and testing
- 为了组装操作在小范围拿取工具和原料
- Small movements to reach for tools or materials for assembly etc;
什么是浪费?/ What is waste ?
• 防呆 • 扩展好的改善方法
Printer
SMT
6 Sigma 消除缺陷
• 6 Sigma 项目 • Gage R&R • DOE
立刻有效!
用眼镜看, 采取行 动
75% 缺陷
Test
Solder
PT/HHP test
Test
Test
FQA
Customer Test
用测量系统和数据分析, 再采取行动
例如 / Examples: - 贴装元件
- Mounting components on the board;
- 集成电路程序烧制
- Programme IC
- 印刷电路板放入盒子
- Secure PCB to the chassis;
- 手工插装元件
- Handload the components;
集中在质量上
Quality Focus
基础 Foundation
客户之声 Voice Of Customer; 质量体系 Quality System; 5S ; 平整化生产
Heijunka 不断地改善和提高 Gemba Kaizen (Shop Floor Continuous Improvement)
- 波峰焊操作等
- Wave solder the PCB etc
什么是可增加附加值的行为?/ What are Value–Enabled (VE) activities ?
• 不增加附加值但是必须要做的事情
• Activities which are non-value added but necessary … today
精益生产基本概念介绍
SPS 的四个主要组成部分 4 Key Elements Of The Solectron Production System
精益之屋
JIT
拉动生产 Pull Production
House of SPS
Six Sigma
零缺陷 Zero Defects
Jidoka
集中在效率上
• 停止步行/检查/查找/重做和其他一些无价 值的行为
• Stop walking, checking, searching, reworking and other non-value activities.
• 加入到工厂的成功当中
• Involved in the success of the Plant.
• 做不增加产品附加值的工作
• Work which does not increase the value of the products
例如 / Examples - 错料返修
- Rework due to the use of wrong parts;
- 补焊
- Touch-up;
- 当机器运转时,操作工等待的时间
精益给客户带来什么?
质量
LEAN Solectron Production System TM
(SPS)
竞争力
灵活性
LEAN Implementation (2004)…1 Of 3 Elements For Customer Value Proposition
消除缺陷的二个途径
现场改善 消除缺陷
• 客户愿意付钱, 并使产品发生转变或给产品增加价值的行为才是有价 值的生产活动
• Activities that transform the products, or add value to the products which the customer is willing to pay for.
25% 缺陷
基础: 现场改善可消除 75% 的缺陷
为什么要六西格码精益生产?/ Why 6-Sigma Lean ?
对于公司
For the Company • 满足客户需求
• To meet customer demands.
• 客户只会为有价值的行为买单
• Customer is willing to pay for only valueadded activities.