附表2-----2018年车轮定位作业表(附表2)
汽车车轮定位作业表5

选手1顺序评分标准说明作业记录合作项目说明[举升位置1 ](举升器未升起,在最低位置)1检查车辆停放位置-目视检查车身前后、左右有无倾斜(是否水平)2检查车辆停放位置-检查车辆在举升机上前部停放是否周正3检查车辆停放位置-检查车辆在举升机上后部停放是否周正4检查车辆停放位置-检查左前轮中心是否基本正对转角盘中心5检查车辆停放位置-检查右前轮中心是否基本正对转角盘中心6检查车辆停放位置-检查左后轮是否基本停在后滑板中间部位7检查车辆停放位置-检查右后轮是否基本停在后滑板中间部位8检查车辆停放位置-检查左前转角盘的销子是否在锁止状态9检查车辆停放位置-检查右前转角盘的销子是否在锁止状态10检查车辆停放位置-检查左后滑板的销子是否在锁止状态11检查车辆停放位置-检查右后滑板的销子是否在锁止状态12车辆识别-打开电源,检查仪表盘油箱油位显示,并记录在作业表上如实汇报,如油箱不满,只汇报和记录,不处理,继续操作13车辆识别-降下司机侧门窗玻璃14车辆识别-找到车辆VIN码并且记录在作业表上15车辆识别-找到车辆型号并且记录在作业表上16车辆识别-确定车辆生产年及日期记录在作业表上17车辆识别-找到并记录原厂要求的前后车轮的轮胎型号和标准胎压2018年职业院校技能大赛《汽车运用与维修》 车轮定位项目作业表选手参赛号 选手姓名: 裁判签字:车型: VIN号: 生产日期:项目内容180工位整理-关闭车门(不锁),将钥匙和记录表交给裁判*比赛车辆具备基本条件如下:1、四个车轮轴承合格,间隙正常,无松匡变形;2、车辆后桥的外倾角和前束按照实测填写记录单,不需调整修复。
3、车辆前桥的外倾角数据默认在合格范围之内。
4、转向横拉杆齿条护套已做预处理,调整前束前,不需要拆卸卡子。
*比赛操作说明:比赛中传感器一律采用有线工作模式。
从市场经济条件出发,从知识经济的特征出发,探讨无形资产的概念和计量类别的扩展。
讨论了无形资产确认条件。
汽车四轮定位项目作业表-团体OK (1)
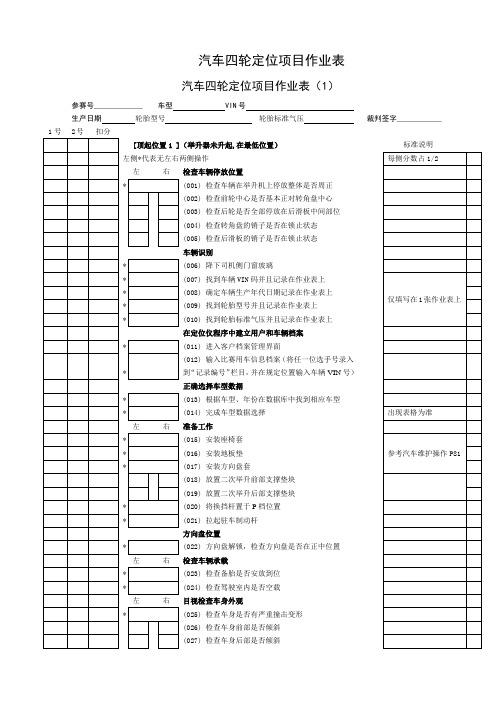
汽车四轮定位项目作业表汽车四轮定位项目作业表(1)参赛号_____________ 车型 VIN 号生产日期 轮胎型号 轮胎标准气压 裁判签字____________1号 2号 扣分[顶起位置1 ](举升器未升起,在最低位置)标准说明左侧*代表无左右两侧操作 左 右检查车辆停放位置(001) 检查车辆在举升机上停放整体是否周正 (002) 检查前轮中心是否基本正对转角盘中心 (003) 检查后轮是否全部停放在后滑板中间部位 (004) 检查转角盘的销子是否在锁止状态 (005) 检查后滑板的销子是否在锁止状态 车辆识别(006) 降下司机侧门窗玻璃(007) 找到车辆VIN 码并且记录在作业表上 (008) 确定车辆生产年代日期记录在作业表上 (009) 找到轮胎型号并且记录在作业表上 (010) 找到轮胎标准气压并且记录在作业表上 在定位仪程序中建立用户和车辆档案 (011) 进入客户档案管理界面(012) 输入比赛用车信息档案(将任一位选手号录入到“记录编号”栏目,并在规定位置输入车辆VIN 号) 正确选择车型数据(013) 根据车型、年份在数据库中找到相应车型 (014) 完成车型数据选择左 右准备工作 (015) 安装座椅套 (016) 安装地板垫 (017) 安装方向盘套(018) 放置二次举升前部支撑垫块 (019) 放置二次举升后部支撑垫块 (020) 将换挡杆置于P 档位置 (021) 拉起驻车制动杆方向盘位置(022) 方向盘解锁,检查方向盘是否在正中位置左 右检查车辆承载(023) 检查备胎是否安放到位 (024) 检查驾驶室内是否空载左 右目视检查车身外观(025) 检查车身是否有严重撞击变形(026) 检查车身前部是否倾斜1号2号评分[顶起位置2]车轮检查位置标准说明左侧*代表无左右两侧操作左右举升机操作* (028) 升起举升机小剪,使车轮充分悬空* (029) 操作举升机大剪,升至中位并落安全锁车辆变速箱档位、驻车制动杆调整* (030) 将变速箱换档杆置于空挡位置* (031) 释放驻车制动杆左右检查轮胎轮辋(032) 目视检查两个前轮胎是否有裂纹,损坏,异常磨损(033) 目视检查两个后轮胎是否有裂纹,损坏,异常磨损(034) 目视检查两个前轮胎是否嵌入金属颗粒或异物(035) 目视检查两个后轮胎是否嵌入金属颗粒或异物(036) 目视检查两个前轮胎花纹是否一致(037) 目视检查两个后轮胎花纹是否一致(038)测量两前轮胎面沟槽深度(039)测量两后轮胎面沟槽深度(040)使用胎压表检查或调整前轮气压到达标准(041)使用胎压表检查或调整后轮气压到达标准(042)目视检查前轮轮辋是否过度变形损坏或腐蚀(043)目视检查后轮轮辋是否过度变形损坏或腐蚀左右车轮轴承(044)检查两个前车轮有无松旷(045) 检查两个后车轮有无松旷(046) 检查两个前车轮转动状况和噪声(047) 检查两个后车轮转动状况和噪声左右在定位仪程序“车辆状况”输入屏幕中,输入轮胎信息(048) 前轮气压(049) 后轮气压(050) 前轮规格(051) 后轮规格(052) 前轮胎面沟槽深度(053) 后轮胎面沟槽深度(054) 完成前后轮胎状况选择打印车辆状况报告(055) 打印检查结果(表格形式)*1号2号评分[顶起位置3]升起大剪,安全锁到位,底盘检查位置标准说明左侧*代表无左右两侧操作左右举升机操作* (056) 操作举升机大剪,升至高位并落安全锁左右检查转向连接机构(057) 检查转向拉杆及球头是否松动(058) 检查转向拉杆有无弯曲和损坏(059) 检查转向拉杆防尘套是否开裂和撕破左右检查前轴悬架(060) 检查稳定杆有无损坏(061) 检查转向节是否损坏(062) 检查减振器外观是否变形损坏(063) 检查减振器螺旋弹簧是否损坏(064) 检查减振器是否漏油(065) 检查下摆臂是否损坏检查后轴悬架(066) 检查减振器外观是否变形损坏(067) 检查减振器螺旋弹簧是否损坏(068) 检查减振器是否漏油(069) 检查各下臂连杆是否损坏(070) 检查拖臂和后桥有无损坏根据现场给出的四轮车身高度判断是否在合格范围(071) 计算前轮高度是否合格(072) 计算后轮高度是否合格1号2号评分[顶起位置4] 操作举升机大剪降至最低落锁位置,小剪回落到位,定位检测前准备标准说明左侧*代表无左右两侧操作举升机操作(073) 降低大剪举升平台到最低落锁位置落锁(074) 举升机小剪缓慢回落,车轮触及平台车辆变速箱档位、驻车制动杆调整(075) 将换挡杆置于P档位置(076) 拉起驻车制动杆左右定位仪定位准备(077) 安装两前轮传感器卡具(078) 安装两后轮传感器卡具(079) 安装并启动前部两个传感器(080) 安装并启动后部两个传感器1号 2号 评分[顶起位置5] 轮毂偏位补偿位置标准说明左侧*代表无左右两侧操作举升机操作* (081) 升起举升机小剪,使车轮充分悬空,以便进行轮毂补偿车辆变速箱档位、驻车制动杆调整* (082) 将变速箱换档杆置于空挡位置 * (083) 释放驻车制动杆左 右 进行轮毂偏位补偿(四轮)(084) 完成两前轮轮毂补偿(085) 完成两后轮轮毂补偿 (086) 完成四个车轮的补偿值计算左 右 补偿结束后拔出转角盘和后滑板的固定销(087) 取下前面两个转角盘的固定销(088) 取下后面两个后滑板的固定销 车辆变速箱档位、驻车制动杆调整* (089) 将变速箱换档杆置于P 挡位置 *(090) 拉起驻车制动杆1号 2号 评分[顶起位置6] 定位检测位置标准说明左侧*代表无左右两侧操作 左 右 举升机小剪回位*(091) 举升机小剪缓慢回落到位(092) 检查前轮是否落在转盘中心(必要时可稍微推动车辆)(093) 检查后轮是否落在后滑板上 左 右 调整前的检测准备工作(094) 按动车辆前部数次,使减振器复位 (095) 按动车辆后部数次,使减振器复位 * (096) 使用刹车锁顶住脚刹车踏板左 右 按照程序检测车辆* (097) 车轮方向对中(098) 检查两前轮传感器是否水平,必要时调整(099) 检查两后轮传感器是否水平,必要时调整(100) 按照程序引导,分别向左、右20度转向操作* (101) 当屏幕显示前轮前束值时,按“前进图标”,屏幕显示检测报告打印检测报告* (102) 打印检测结果(表格形式)左 右 将传感器放回机柜,进行充电(103) 前部传感器放回充电位置(104) 后部传感器放回充电位置1号 2号 评分[顶起位置7] 设备复位和工位整理、清洁标准说明左侧*代表无左右两侧操作 举升机操作1* (105) 升起举升机小剪,使车轮悬空左 右 插入转角盘和后滑板的固定销(106) 将两个前轮转角盘固定销插入 (107) 将两个后轮滑板固定销插入举升机操作2* (108) 举升机小剪缓慢回落到位左 右 定位仪复位* (109) 拆除刹车锁,并放至规定位置 (110) 拆下两前轮卡具,并放至规定位置 (111) 拆下两后轮卡具,并放至规定位置 * (112) 按C 键使定位仪程序复位举升机操作3* (113) 操作举升机大剪回到最低位置工位整理(114) 升车窗玻璃(115) 取下车内三件套* (116) 关闭车门(不锁),将钥匙和记录表交给裁判。
2019年全国职业院校技能大赛中职组“汽车运用与维修”赛项规程汽车机电维修赛项技术方案

汽车运用与维修技术方案——汽车机电维修一、比赛内容要求汽车机电维修赛项为实操比赛,由单人完成,包括三项比赛内容:整车维护、机械拆装、汽车故障诊断。
(一)整车维护项目包括定期维护和车轮定位两项内容,分别在不同场地进行比赛。
1.定期维护(1)内容要求:比赛内容包括定期维护、空调制冷剂鉴别、空调性能检测等。
要求在规定时间内根据《汽车维护、检测、诊断技术规范》(GB/T18344)、《汽车空调制冷剂回收、净化、加注工艺规范》(JT/T774—2010)、通用别克威朗轿车维修手册6万公里维护等相关技术要求,按照附表1《定期维护项目作业表》的作业顺序对指定车辆进行维护,并要求作业项目规范、务实、安全、环保,设备、工具、量具使用正确,正确填写附表5《定期维护记录表》。
(2)比赛时间:30分钟。
(3)比赛车辆:通用别克威朗轿车(2017款15S 自动进取型)。
2.车轮定位(1)内容要求:比赛内容包括车轮定位检测、前轮前束调整和维修方案选择。
要求在规定时间内,按照设备操作手册、通用别克威朗轿车维修手册的相关技术要求,按照附表2《车轮定位项目作业表》的顺序对指定车辆进行车轮定位作业。
要求正确识别和选择车型、测试参数;检查车辆状态,正确测量出车轮定位数据,并根据指定车辆的目标数据进行定位调整和维修方案选择,填写好《车轮定位项目作业表》和记录单(附表6),打印一份完整的车轮定位数据检测报告,同时考核规范、安全作业,正确使用设备。
(2)比赛时间:30分钟。
(3)比赛车辆:通用别克威朗轿车(2017款15S 自动进取型)。
注:车轮定位项目采用3D车轮定位仪,比赛现场提供博世和亨特两种品牌的定位仪,比赛前1个月,参赛选手上报使用哪种定位仪,以便赛项执委会提前规划赛场。
(二)机械拆装1.内容要求:比赛内容为发动机气门机构的拆卸、检查、装配。
要求在规定时间内,按照维修手册要求对发动机气门机构进行拆卸、检查、测量和装配,并根据测量结果进行分析做出零件好坏及维修方案的判断。
2014年车轮定位作业项目举升图ok
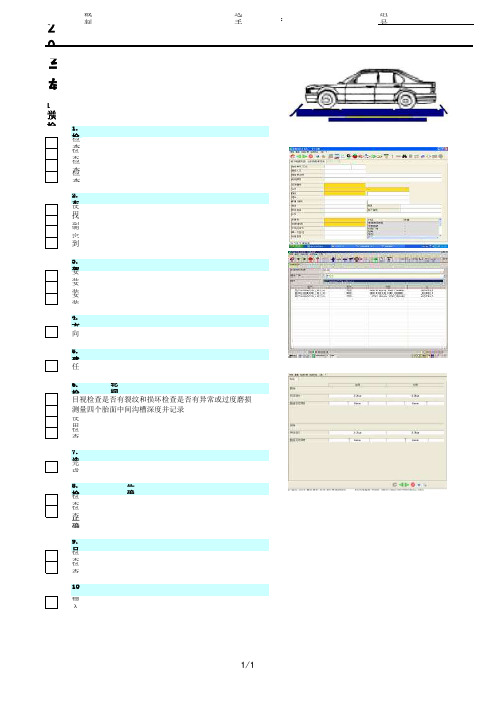
裁判:选手抽签号:组号2014年江苏省职业学校交通运输类技能大赛
车轮定位项目作业表
[举升位置1——举升机处于驶入时的最低位置]
预检工作
1.检查车辆停放位置
检查车辆在举升机上停放整体是否周正
检查前轮中心是否基本正对转角盘中心
检查后轮是否全部停放在后滑板上
检查转角盘和后滑板的销子是否仍然在锁止状态
2.车辆识别
使用钥匙打开车门
找到车辆VIN号码并且正确记录
确定车辆生产年代日期
找到并在作业表上记录四个车轮的标准胎压
3.驾驶员座椅
安装座椅套
安装地板垫
安装方向盘套
4.方向盘位置
方向盘解锁,检查方向盘是否在正中位置
5.建立参赛车辆信息档案
将任一位选手号录入到“用户编号”栏目,并在规定位置输入车辆VIN号
6.检查轮胎轮辋
目视检查是否有裂纹和损坏检查是否有异常或过度磨损
测量四个胎面中间沟槽深度并记录
使用胎压表检查气压,如需要调整调整到标准胎压并记录
检查钢圈是否过度变形损坏或腐蚀
7.选择车型数据
完成车型数据选择
8.检查车辆承载正确测量并记录车身高度
检查备胎是否安放到位
检查驾驶室内是否空载
正确测量和记录P,R车身高度
9.目视检查车身外观
检查车身是否有严重撞击变形
检查车身两侧是否偏斜
10.车辆状况输入
输入轮胎气压和胎纹深度
1/1。
二级维护车轮定位作业表

标准说明 作业记录
(034)
(035)
(036) (039) (040) (041) (042) (045)
检查轮胎和轮辋 使用胎压表检查或调整右前轮气压到达标准并记 录 检查轮胎和轮辋 使用胎压表检查或调整左后轮气压到达标准并记 录 检查轮胎和轮辋 使用胎压表检查或调整右后轮气压到达标准并记 录 检查轮胎和轮辋 目视检查左后轮辋是否过度变形损坏或腐蚀 检查轮胎和轮辋 目视检查右后轮辋是否过度变形损坏或腐蚀 正确选择车型数据 在数据库中找到相对应车型 检查车辆承载 检查备胎是否安放到位 目视检查车身外观 检查车身后部是否有严重撞击变形
检查前轴悬架 检查右前稳定杆连杆有无弯曲或损坏 检查前轴悬架 (059) 检查前稳定杆有无弯曲或损坏 检查前轴悬架 (061) 检查右下悬架臂是否损坏 检查前轴悬架 (063) 检查右前下球节是否损坏 检查后轴悬架 (065) 检查右后支撑杆是否变形损坏 如发现底盘和悬架存在其它严重问题,还可以在“车辆状况”中输入,但此次比赛不计分数 (058) [举升位置3]操作举升机大剪降至最低落锁位置,定位检测前准备 举升机操作 (066) 降低大剪举升平台到最低位置 定位仪定位准备 (068) 安装右前轮传感器卡具 定位仪定位准备 (070) 安装右后轮传感器卡具 定位仪定位准备 (072) 安装右前部传感器 定位仪定位准备 (074) 安装右后部传感器 车辆变速箱档位调整 (075) 放置左后部车轮挡块 车辆变速箱档位调整 (076) 放置后右部车轮挡块 车辆变速箱档位调整 (077) 将变速箱换档杆置于空挡位置并释放驻车制动 [顶起位置4] 轮毂偏位补偿位置 补偿准备及举升机操作 (078) 升起举升机小剪,使车轮离开举升机10cm左右,充 分悬空,以便进行轮毂补偿 进行轮毂偏位补偿(四轮) (080) 完成右前轮轮毂补偿 进行轮毂偏位补偿(四轮) (082) 完成右后轮轮毂补偿 [顶起位置5] 定位检测位置(调整前) 举升机操作:小剪回位 (084) 拔出右前轮转盘固定销并放好 举升机操作:小剪回位 (085) 举升机小剪缓慢回落到位 举升机操作:小剪回位 (087) 移开右后轮挡块 举升机操作:小剪回位 (089) 检查右前轮是否落在转盘中心 调整前的检测准备工作 (091) 按动车辆前部数次,使减振器复位
四轮定位项目作业表(整体)
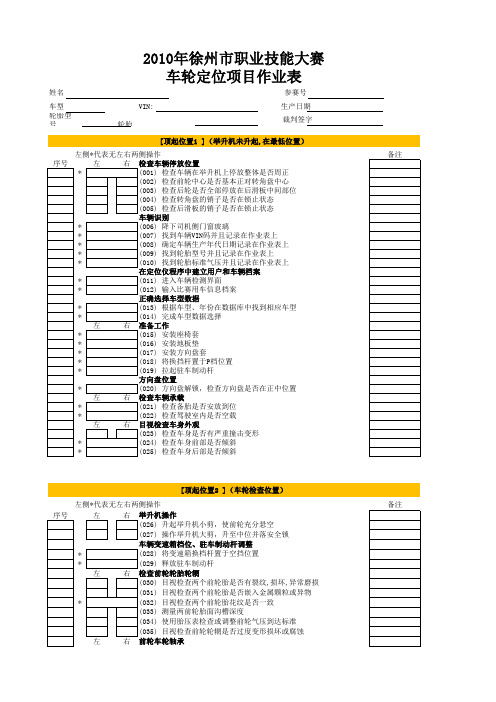
*
(069) 将换挡杆置于P档位置
*
(070) 拉起驻车制动杆
左
右 定位仪定位准备
(071) 安装两前轮传感器卡具
(072) 安装两后轮传感器卡具
(073) 安装并启动前部两个传感器
(074) 安装并启动后部两个传感器
备注 备注
左
侧
序号
左
*
* 左
* *
左
* *
左
左
* *
[顶起位置5 ](轮毂偏位补偿位置)
[顶起位置3 ](升起大剪,安全锁到位,底盘检查位置)
序号
左侧*代表无左右两侧操作
左
右 举升机操作
(052) 操作举升机大剪,升至高位并落安全锁
左
右 检查转向连
(053) 检查转向拉杆及球头是否松动
(054) 检查转向拉杆有无弯曲和损坏
(055) 检查转向拉杆防尘套是否开裂和撕破
左
右 检查前轴悬架
备注
[顶起位置2 ](车轮检查位置)
序号
左侧*代表无左右两侧操作
左
右 举升机操作
(026) 升起举升机小剪,使前轮充分悬空
(027) 操作举升机大剪,升至中位并落安全锁
车辆变速箱档位、驻车制动杆调整
*
(028) 将变速箱换档杆置于空挡位置
*
(029) 释放驻车制动杆
左
右 检查前轮轮胎轮辋
(030) 目视检查两个前轮胎是否有裂纹,损坏,异常磨损
*
(019) 拉起驻车制动杆
方向盘位置
*
(020) 方向盘解锁,检查方向盘是否在正中位置
左
右 检查车辆承载
*
(021) 检查备胎是否安放到位
蓝色方向盘 四轮定位值 手工测量表格
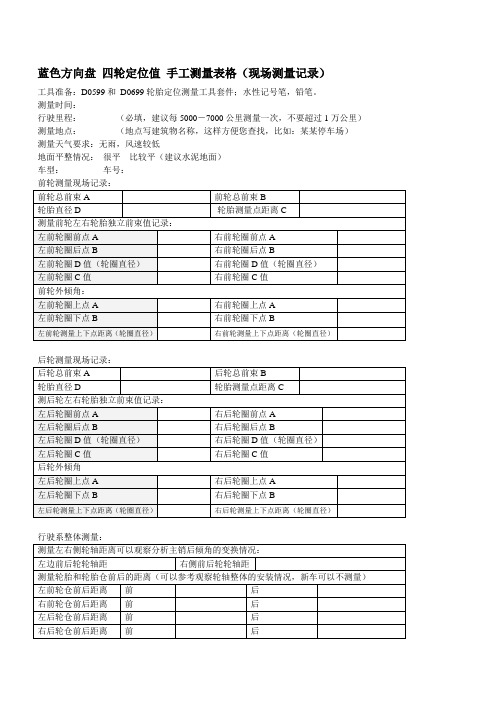
右后轮圈上点A
左后轮圈下点B
右后轮圈下点B
左后轮测量上下点距离(轮圈直径)
右后轮测量上下点距离(轮圈直径)
行驶系整体测量:
测量左右侧轮轴距离可以观察分析主销后倾角的变换情况:
左边前后轮轮轴距
右侧前后轮轮轴距
测量轮胎和轮胎仓前后的距离(可以参考观察轮轴整体的安装情况,新车可以不测量)
左前轮仓前后距离
左前轮测量上下点距离(轮圈直径)
右前轮测量上下点距离(轮圈直径)
后轮测量现场记录:
后轮总前束A
后轮总前束B
轮胎直径D
轮胎测量点距离C
测后轮左右轮胎独立前束值记录:
左后轮圈前点A
右后轮圈前点A
左后轮圈后点B
右后轮圈后点B
左后轮圈D值(轮圈直径)
右后轮圈D值(轮圈直径)
左后轮圈C值
右后轮圈C值
后轮外倾角
前
后
右前轮仓前后距离
前
后
左后轮仓前后距离
前
后
右后轮仓前后距离
前
后
车型:车号:
前轮测量现场记录:
前轮总前束A
前轮总前束B
轮胎直径D
轮胎测量点距离C
测量前轮左右轮胎独立前束值记录:
左前轮圈前点A
右前轮圈前点A
左前轮圈后点B
右前轮圈后点B
左前轮圈D值(轮圈直径)
右前轮圈D值(轮圈直径)
左前轮圈C值
右前轮圈C值
前轮外倾角:
左前轮圈上点A
右前轮圈上点A
左前轮圈下点B
右前轮圈下点B
蓝色方向盘四轮定位值手工测量表格(0699轮胎定位测量工具套件;水性记号笔,铅笔。
测量时间:
二手车鉴定评估作业表
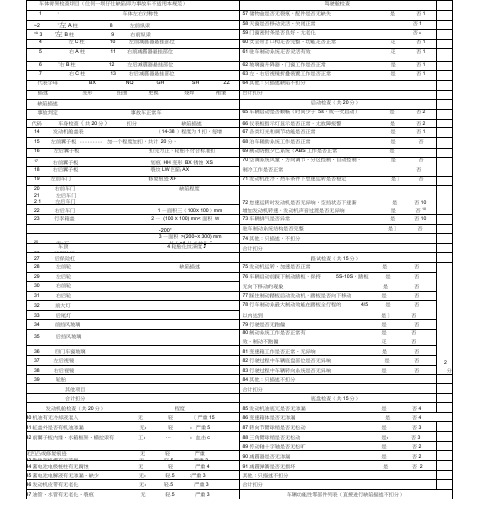
16左后翼子板扣完为止,轮胎不付合标准扣
69制动防抱夕匕系统(ABS工作是否止常是
17右前翼子板划痕HH变形BX锈蚀XS
70空调系统风量、方向调节、分区控制、自动控制、是否
制冷工作是否正常否
18右后翼子板裂纹LW凹陷AX
19左前车门修复痕迹XF
71发动机在冷、热车条件下怠速运转是否稳定是]否
车体骨架检查坝目(仕何一坝仔仕缺陷即为事故车不适用本规范)
驾驶舱检查
11车体左右对称性
57储物盒是否无裂痕,配件是否无缺失是否1
~21左A柱8左前纵梁
58天窗是否移动灵活、关闭正常否1
"A3'左B柱9右前纵梁
59门窗密封条是否良好、尢老化否a
4左C柱10左前减震器悬挂部位
60女全带纟口构疋否完整、功能疋否正常疋否1
54车顶及周边内饰疋否无破损、松动及裂缝和污迹疋否1
排气管及消音器遥控器及功能
齐人齐人士nn HZrT廿亠
55仪表台是否无划痕,配件是否无缺失是否1
车轮轮毂喇叭高低曰色
车内后视镜玻璃加热功能
56排挡把手柄及护罩是否完好、无破损丨是「否1
亠「亠、EH—「一玻璃加热功能
37左后视镜
82行驶过程中车辆底盘部位是否无异响是否
38右后视镜
83行驶过程中车辆转向系统是否无异响是否
39轮胎
84其他:只描述不扣分
其他项目
合计扣分
合计扣分
底盘检查(共15分)
发动机舱检查(共20分)程度
85发动机油底Байду номын сангаас是否无渗漏是否4
40机油有无冷却液混入无轻[严重15
86变速箱体是否无渗漏是否4
2014年汽车二级维护和四轮定位项目作业表填写说明(团体赛)ok
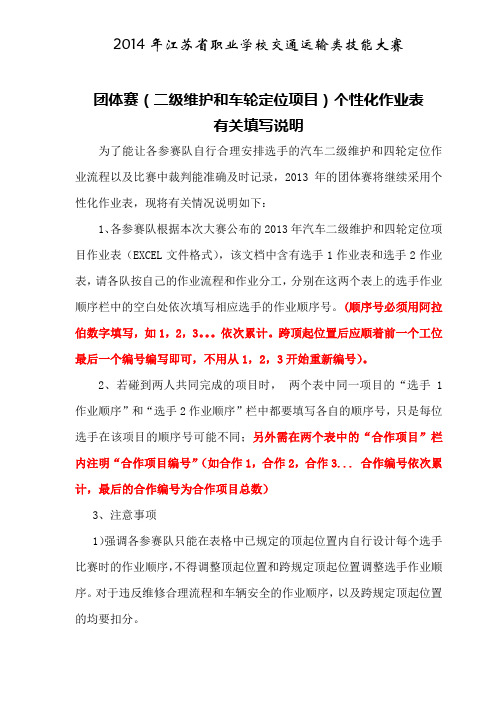
团体赛(二级维护和车轮定位项目)个性化作业表有关填写说明为了能让各参赛队自行合理安排选手的汽车二级维护和四轮定位作业流程以及比赛中裁判能准确及时记录,2013年的团体赛将继续采用个性化作业表,现将有关情况说明如下:1、各参赛队根据本次大赛公布的2013年汽车二级维护和四轮定位项目作业表(EXCEL文件格式),该文档中含有选手1作业表和选手2作业表,请各队按自己的作业流程和作业分工,分别在这两个表上的选手作业顺序栏中的空白处依次填写相应选手的作业顺序号。
(顺序号必须用阿拉伯数字填写,如1,2,3。
依次累计。
跨顶起位置后应顺着前一个工位最后一个编号编写即可,不用从1,2,3开始重新编号)。
2、若碰到两人共同完成的项目时,两个表中同一项目的“选手1作业顺序”和“选手2作业顺序”栏中都要填写各自的顺序号,只是每位选手在该项目的顺序号可能不同;另外需在两个表中的“合作项目”栏内注明“合作项目编号”(如合作1,合作2,合作3... 合作编号依次累计,最后的合作编号为合作项目总数)3、注意事项1)强调各参赛队只能在表格中已规定的顶起位置内自行设计每个选手比赛时的作业顺序,不得调整顶起位置和跨规定顶起位置调整选手作业顺序。
对于违反维修合理流程和车辆安全的作业顺序,以及跨规定顶起位置的均要扣分。
2)表中被标红的行格主要是用于区分顶起位置,以防项目调整错误3)各代表队只能在公布的表格中填写选手作业序号,不允许改动表中的任何内容,否则后果自负。
4)为保证大赛的顺利进行,要求参赛学校确定好每个选手作业顺序后,在比赛前自行打印出1和2号选手作业表,每位选手的作业表只含各自作业内容,作业表一式2份,一份选手使用,一份裁判使用。
特别说明:根据往年的比赛经验,总有些参赛队没有打印并带上自行设计的个性化工单,从而影响了正常的比赛秩序。
为了确保比赛的正常进行,务必请各参赛队按照本说明的内容打印出各队各选手的个性化工单。
二级维护作业项目重要说明1、按作业流程,用完的机油桶、更换的机滤器、排放塞等需要分类丢弃到垃圾桶内,但是考虑到比赛的实际情况,要求参赛选手将空机油桶、换下的机油滤清器和放油塞(换下来的机油滤清器必须向上放置,避免滴油)分别放回原放置机油桶和机油滤清器的位置,以便回收再利用。
2016年车轮定位3D作业总表 (1)
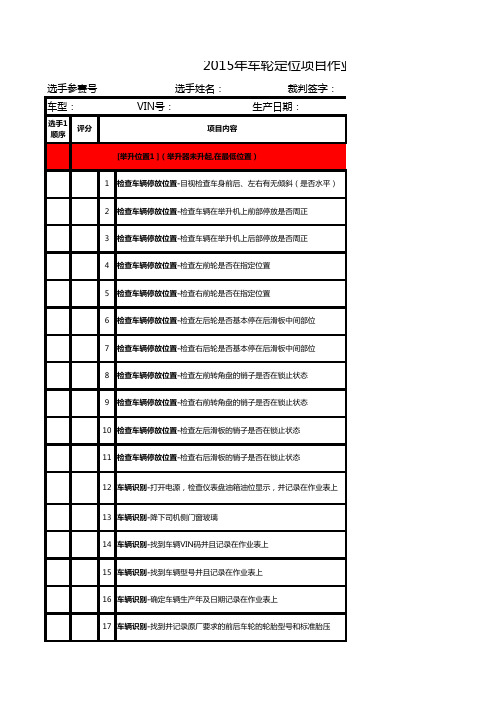
选手1顺序评分[举升位置1 ](举升器未升起,在最低位置)1检查车辆停放位置-目视检查车身前后、左右有无倾斜(是否水平)2检查车辆停放位置-检查车辆在举升机上前部停放是否周正3检查车辆停放位置-检查车辆在举升机上后部停放是否周正4检查车辆停放位置-检查左前轮是否在指定位置5检查车辆停放位置-检查右前轮是否在指定位置6检查车辆停放位置-检查左后轮是否基本停在后滑板中间部位7检查车辆停放位置-检查右后轮是否基本停在后滑板中间部位8检查车辆停放位置-检查左前转角盘的销子是否在锁止状态9检查车辆停放位置-检查右前转角盘的销子是否在锁止状态10检查车辆停放位置-检查左后滑板的销子是否在锁止状态11检查车辆停放位置-检查右后滑板的销子是否在锁止状态12车辆识别-打开电源,检查仪表盘油箱油位显示,并记录在作业表上13车辆识别-降下司机侧门窗玻璃14车辆识别-找到车辆VIN码并且记录在作业表上15车辆识别-找到车辆型号并且记录在作业表上16车辆识别-确定车辆生产年及日期记录在作业表上2015年车轮定位项目作业表选手参赛号 选手姓名: 裁判签字: 车型: VIN号: 生产日期:项目内容17车辆识别-找到并记录原厂要求的前后车轮的轮胎型号和标准胎压18准备工作-安装座椅套19准备工作-安装地板垫20准备工作-安装方向盘套21准备工作-放置左后部车轮挡块22准备工作-放置右后部车轮挡块23方向盘位置-方向盘解锁,检查方向盘是否在正中位置24在定位仪程序中建立用户和车辆档案-在定位程序中输入选手编号和车辆VIN码43正确选择车型数据-在数据库中找到相应车型,完成车型数据选择25检查轮胎和轮辋-检查实车安装轮胎型号是否车辆铭牌要求一致26检查轮胎和轮辋-检查同轴两侧车轮轮胎花纹是否一致27检查轮胎和轮辋-目视检查左前轮胎是否有裂纹,损坏,异常磨损是否嵌入金属颗粒或异物28检查轮胎和轮辋-目视检查右前轮胎是否有裂纹,损坏,异常磨损是否嵌入金属颗粒或异物29检查轮胎和轮辋-目视检查左后轮胎是否有裂纹,损坏,异常磨损是否嵌入金属颗粒或异物30检查轮胎和轮辋-目视检查右后轮胎是否有裂纹,损坏,异常磨损是否嵌入金属颗粒或异物31检查轮胎和轮辋-使用胎纹深度尺,测量左前轮胎面沟槽深度并记录32检查轮胎和轮辋-使用胎纹深度尺,测量右前轮胎面沟槽深度并记录33检查轮胎和轮辋-使用胎纹深度尺,测量左后轮胎面沟槽深度并记录34检查轮胎和轮辋-使用胎纹深度尺,测量右后轮胎面沟槽深度并记录35检查轮胎和轮辋-使用胎压表检查或调整左前轮气压到达标准并记录36检查轮胎和轮辋-使用胎压表检查或调整右前轮气压到达标准并记录37检查轮胎和轮辋-使用胎压表检查或调整左后轮气压到达标准并记录38检查轮胎和轮辋-使用胎压表检查或调整右后轮气压到达标准并记录39检查轮胎和轮辋-目视检查左前轮辋是否过度变形损坏或腐蚀40检查轮胎和轮辋-目视检查右前轮辋是否过度变形损坏或腐蚀41检查轮胎和轮辋-目视检查左后轮辋是否过度变形损坏或腐蚀42检查轮胎和轮辋-目视检查右后轮辋是否过度变形损坏或腐蚀44检查车辆载荷,测量并记录车身高度-检查驾驶室内是否空载45检查车辆载荷,测量并记录车身高度-后备箱载荷是否合格46检查车辆载荷,测量并记录车身高度-正确抬起前保险杠并复位47检查车辆载荷,测量并记录车身高度-正确测量并记录左前车身高度P 值高度,填入作业表48检查车辆载荷,测量并记录车身高度-正确测量并记录右前车身高度P 值高度,填入作业表49检查车辆载荷,测量并记录车身高度-正确压下前保险杠并复位50检查车辆载荷,测量并记录车身高度-正确测量并记录左前车身高度P 值高度,填入作业表70检查转向连接机构-检查左前转向机护套是否开裂和撕破71检查转向连接机构-检查右前转向机护套是否开裂和撕破72检查转向连接机构-检查左转向节是否损坏73检查转向连接机构-检查右转向节是否损坏74检查前轴悬架-检查左下控制臂前衬套是否损坏75检查前轴悬架-检查右下控制臂前衬套是否损坏76检查前轴悬架-检查前稳定杆有无弯曲或损坏77检查前轴悬架-检查左下控制臂是否损坏78检查前轴悬架-检查右下控制臂是否损坏79检查前轴悬架-检查左前下控制臂球节是否损坏80检查前轴悬架-检查右前下控制臂球节是否损坏81检查前轴悬架-检查左下控制臂后衬套是否漏油或变形损坏82检查前轴悬架-检查右下控制臂后衬套是否漏油或变形损坏83检查后轴悬架-检查左后减振器是否变形,漏油,损坏84检查后轴悬架-检查右后减振器是否变形,漏油,损坏85检查后轴悬架-检查左后弹簧是否有明显锈蚀,损坏86检查后轴悬架-检查右后弹簧是否有明显锈蚀,损坏87检查后轴悬架-检查后桥是否有明显变形损伤[举升位置3] 轮毂偏位补偿位置及定位检测88举升机操作-降低大剪举升平台到降至适合的落锁位置89定位仪定位准备-安装左前板卡具和标板90定位仪定位准备-安装右前轮卡具和标板91定位仪定位准备-安装左后轮卡具和标板92定位仪定位准备-安装右后轮卡具和标板93定位仪定位准备-偏位补偿准备194定位仪定位准备-偏位补偿准备295车辆变速箱档位调整-将变速箱换档杆置于手动空挡或自动档N挡位置并释放驻车制动96举升机操作:补偿准备及举升机操作-移开左后轮挡块至合适位置97举升机操作:补偿准备及举升机操作-移开右后轮挡块至合适位置98进行轮毂偏位补偿(四轮)-推动车辆完成车轮补偿99实施驻车制动100调整前的检测准备工作-使用刹车锁顶住脚刹车踏板101调整前的检测准备工作-拔出左前轮转盘固定销并取下垫板102调整前的检测准备工作-拔出右前轮转盘固定销并取下垫板103调整前的检测准备工作-拔出左后轮后滑板固定销104调整前的检测准备工作-拔出右后轮后滑板固定销105按照程序检测车辆-按照程序引导,车轮方向对中106按照程序检测车辆-按照程序引导,分别向左20度转向操作107按照程序检测车辆-按照程序引导,分别向右20度转向操作108按照程序检测车辆-按照程序引导,车轮方向对中109按照程序检测车辆-当屏幕显示前轮前束值时,按照程序引导,进入最大转向角测量。
新 轮规样表示例及填写说明
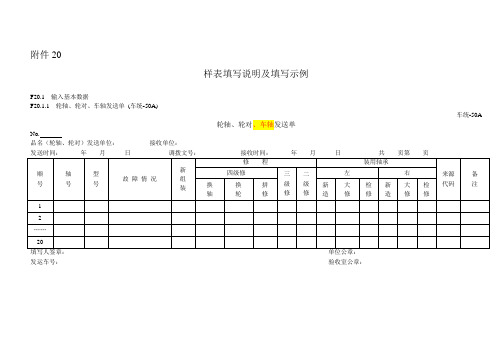
附件20样表填写说明及填写示例F20.1 输入基本数据F20.1.1 轮轴、轮对、车轴发送单(车统-50A)车统-50A轮轴、轮对、车轴发送单No.品名(轮轴、轮对)发送单位:接收单位:填写人签章:单位公章:发运车号:验收室公章:1.发送轮轴、轮对或车轴时,在发送单的品名栏中对应项画“○”字标记,发送单位和接收单位须填写单位全称。
2.发送轮对时,轮对的修程在发送单的修程栏中对应项画“√”。
3.车辆段检修车间发送车轮车间、站修发送车辆段检修车间轮对时,需填写轴号、型号、故障情况、修程、来源代码,对不良轮对故障情况不允许为空,修程项按发送单位最终修程填写。
4.车轮车间发送车辆段、车辆段检修车间发送站修轮对时,需填写轴号、型号、新组装或修程、装用轴承(压装轴承时),修程项按发送单位最终修程填写。
5.表格采用A4幅面横向。
F20.1.2 车轮发送单 (车统-50B)车统-50B车 轮 发 送 单No.发送单位: 接收单位: 发送时间: 年 月 日 调拨文号:填写人签章: 单位公章: 发运车号:验收室公章:F20.1.2.1 填写要求1.发送车轮时,发送单位和接收单位须填写单位全称。
2.车轮型号等车轮标记不得漏项,车轮标记不清时须注明“不清”字样。
3.表格采用A4幅面。
F20.1.2.2 填写示例F20.1.3 轴承发送单 (车统-50C)车统-50C轴 承 发 送 单No.发送单位: 接收单位: 轴承型号:发送时间: 年 月 日 调拨文号:接收时间: 年 月 日 共 页第 页发运车号:验收室公章:F20.1.3.1 填写要求1.发送单位和接收接单位须填写单位全称。
2.轴承一般检修时,不同单位、不同车间之间轴承往返过程中双方单位进行填写,送修单位须填写轴承编号、退卸日期、退卸原因,轴承标志板A 栏和送修的修程,检修单位填写轴承编号、检修修程结果、轴承修理时间、轴承修理单位,轴承检修单位返回车统-50C 同时需返回一份轴承检修的辆货统-403。
最新年浙江省中等职业学校汽车运用与维修技能大赛汽车机电维修赛项技术方案(.3.9)资料

2018 年浙江省中等职业学校汽车运用与维修技能大赛汽车机电维修赛项技术方案一、比赛内容要求:汽车机电维修赛项为实操比赛,由单人完成,包括三项比赛内容:整车维护、机械拆装、汽车故障诊断。
(一)整车维护项目包括定期维护和车轮定位两项内容,分别在不同场地进行比赛。
1. 定期维护(1)内容要求:比赛内容包括定期维护、空调制冷剂鉴别、空调性能检测等。
要求在规定时间内根据《汽车维护、检测、诊断技术规范》(GB/T1834引、《汽车空调制冷剂回收、净化、加注工艺规范》(JT/T774—2010)、通用别克威朗轿车维修手册1 万公里维护等相关技术要求,按照《定期维护项目作业表》的作业顺序对指定车辆进行维护,并要求作业项目规范、务实、安全、环保,设备、工具、量具使用正确,正确填写《上海通用汽车特约售后服务中心维修工单》和《定期维护记录单》(附件5、。
(2 、比赛时间:30 分钟。
(3)比赛车辆:通用别克威朗轿车(2017款15S自动进取型)(4、《定期维护作业表》(附表1 、2. 车轮定位(1、内容要求:比赛内容包括车轮定位检测、前轮前束调整和维修方案选择。
要求在规定时间内,按照设备操作手册、通用别克威朗轿车维修手册的相关技术要求,按照《车轮定位项目作业表》的顺序对指定车辆进行车轮定位作业。
要求正确识别和选择车型、测试参数;检查车辆状态,正确测量出车轮定位数据,并根据指定车辆的目标数据进行定位调整和维修方案选择,填写好《车轮定位项目作业表》,打印一份完整的车轮定位数据检测报告,同时考核规范、安全作业,正确使用设备。
(2)比赛时间:30 分钟。
(3)比赛车辆:通用别克威朗轿车(2017款15S自动进取型)。
(4)《车轮定位作业表》(附表2)注:车轮定位项目采用3D车轮定位仪,比赛现场提供博世和亨特两种品牌的定位仪,报名时,参赛选手上报使用哪种定位仪,以便赛项执委会提前规划赛场。
(二)机械拆装1.内容要求:比赛内容为发动机气门机构的拆卸、检查、装配。
最新 汽车车轮定位记录表

选手编号:选手姓名:裁判签字:
输入数值单位:毫米
车身调平高度最大差值:
评估分析
1、根据以上测量数据,该车行驶时将会导致:
A、XXXX
B、XXXX
C、XXXXX
D、XXXX
2、根据实测数据和检查,需要进行以下检修工作:(多选)
A、XXXXX
B、XXXX
C、XXXX
D、XXXX
2018年职业院校技能大赛《汽车运用与维修》 车
轮定位项目记录表
记录一、雪弗兰科鲁兹车身翘头量测量记录和评估附表
结果评估(车身调平高度最大差值是否合格):
记录二、雪弗兰科鲁兹车身定位分析
(注意:标红的评估分析题,上述仅为样例。
比赛时,评估分析题不会超过5道题,题型有单选或多选,主要考核选手在生产实际中对实测定位数据的分析、判断能力。
)。
一般标准变更表7258-2017

此表仅作备案用,不做批复,一式一份。
附表1(唯一性认定检查部分)—修改了车身前部外表面设置的商标或厂标的要求(见4.1.1 ,2012年版的4.1.1);—修改了产品标牌的标示要求(见表1,2012年版的表1);—修改了货车、货车底盘改装的专项作业车和挂车的车辆识别代号打刻位置要求及总质量小于或等于3 500 kg的封闭式货车的打刻深度要求(见4.1.3,2012年版的4.1.3) ,增加了打刻车辆识别代号(或产品识别代码、整车型号和出厂编号)的部件不应采用凿改、重新涂漆的方式处理、汽车和挂车打刻的车辆识别代号应能拍照、打刻的车辆识别代号(或产品识别代码、整车型号和出厂编号)总长度应小于或等于200 mm且字母和数字的字体和大小应相同、起止标记(如有)与字母数字的间距应紧密均匀、打刻的车辆识别代号可按GB16735 的规定重新标示或变更的要求(见4.1.3);—修改了轮边电机、轮载电机的标识要求(见4.1.4,2012年版的4.1.4);—修改了电子控制单元(ECu)应能记裁车辆识别代号等特征信息的车型范围和读取等要求(见 4.1.5、2012年版的4.1.5);—增加了总质量大于或等于12000 kg的部分货车和总质量大于或等于10000 kg的部分挂车应在货箱(常压罐体)打刻至少两个车辆识别代号的要求(见4. 1.8);—增加了罐式危险货物运输车辆的罐体或与罐体焊接的支座的右侧应有金属的罐体铭牌,罐体铭牌应标注唯一性编码、罐体设计代码、罐体容积等信息的要求(见4. 1.9) ,—增加了对机动车进行修理或改装时不应破坏或未经授权修改电子控制单元(ECU)等记载的车辆识别代号的要求(见4.1.10);附表2(车辆特征参数检查部分)—修改了警用摩托车、发动机排量大于或等于800 mL或电机额定功率总和大于或等于40 kW的两轮普通摩托车的外廓尺寸限值要求(见表2的注 a,2012年版的表2),—修改了乘客能内部宽度、驾驶室(区)内部宽度的说明(见 4.4.2.1的注、4.4.4.1的注,2012年版的4.5.2,1、4.5,4.1);—增加了座垫宽、座垫深的说明(见4.4.2.2的注4、注5) ,以及旅居车和部分乘用车设置有后向座椅、侧向座椅时的核载要求(见 4.4.2.3、4.4.2.4) ,修改了旅居车核定乘员数要求(见 4.4.2.5 ,,2012年版的4.5.2.3);—增加了未设置乘客站立区的客车的核定乘员数应小于或等于 56人的要求(见4.4.3.5);—增加了专项作业车(消防车除外)核定乘坐人数应小于或等于 9人、危险货物运输货车的核定乘坐人数应小于或等于3人的要求(见4.4.4.5) ,修改了摩托车核定乘坐人数要求(见4.4.5.1,2012年版的4.5.5.1);—修改了设计和制造上具有行动不使乘客(如轮椅乘坐者)乘坐设施的载客汽车、装备有担架的救护车等用于载运特定乘客的汽车的核载要求(见4.4.6.1 ,2012年版的4.5.6.1);—修改了纯电动汽车的比功率要求(见4.5 ,2012年版的4.6);—修改了发动机中置且宽高比小于或等于 0.9 的乘用车、设有乘客站立区的客车、消防车和前轮距小于或等于460 mm的正三轮摩托车的侧倾稳定性要求(见4.6.1、4.6.3、4.6.4,2012年版的4.7.1、4.7.3);—增加了客车车底行李舱净高的要求(见11.2.5);—増加了公路客车、旅游客车和未设置乘客站立区的公共汽车燃油箱数量和容积的要求(见11.2.9);—增加了罐体、货厢(箱)和侧帘式载货车辆、危险货物运输货车燃油箱数量和容积的相关要求(见11.3.6~11.3.12),附表3(车辆外观检查部分)—修改了电动汽车操纵件、指示器及信号装置的图形标志要求,以及多用途货车、罐式危险货物运输车辆、冷藏车的喷涂要求(见4.7.1、4.7.6,2012年版的4.8.1、4.8.6);—修改了放大的号牌号码的喷涂/粘贴/放置要求及载客汽车的外观喷涂、行李舱可运载的最大行李总质量的标识要求(见4.7.7、4.7.8,2012年版的4.8.7、4.8.8);—增加了部分最大设计车速小于70 km/h的汽车应在车身后部喷涂/悬挂表示最大设计车速的标记的要求(见4.7.11);—修改了机动车的漏水、漏油检査要求(见4.9、4.10,2012年版的4.10、4.11);—修改了行驶轨迹要求(见4.12,2012年版的4.13);—修改了驾驶人耳旁噪声要求(见4.13,2012年版的4.14、附录 A) ,—增加了乘用车列车的特殊要求(见4.16);—增加了专项作业车及其他装备有专用仪器或设备的汽车,装备的专用仪器和设备应固定可靠的要求(见4.17.1);—修改了气压制动管路的密封性要求(见7.7.1 ,2012年版的7.7.1);—增加了车长大于9 m的客车、总质量大于或等于12000 kg的货车和货车底盘改装的专项作业车采用气压制动时储气筒的额定工作气压要求(见7.8.1);—增加了采用气压制动的汽车和具有储气筒的挂车应标示储气筒额定工作气压的要求(见 7.8.5 );—增加了采用气压制动的汽车、挂车在设计和制造上应具有可用于测试制动管路压力的连接器的要求(见7.2.15),—修改了允许闪烁的外部灯具的范围(见8.1.2 ,2012年版的8.1.2);—修改了应装备车身反光标识的车辆类型(见8.4.1、8.4.2 ,,2012年版的8.4.1、8.4.2) ,增加了后部车身反光标识的面积要求(见8.4.1);—修改了应装备反射器型车身反光标识的车辆类型,修改了车型车身反光标识粘贴式样要求(见8.4.5,2012年版的8.4.5);—增加了安装有自适应前照明系统的应符合 GB/T30036的规定的要求(见8.5.1.2);—增加了部分汽车应具有前照灯光束高度调整装置/功能的要求(见8,5.1.4);—增加了乘用车、专用校车喇叭在车钥匙取下及车门锁止时在车内仍能正常使用的要求(见8.6.1);—修改了客车上部结构强度的要求(见11.2.1,2012年版的11.2.1);—增加了部分公路客车车内随行物品存放区的要求(见11.2.8) ,—增加了在设计和制造上不应设置有货厢(货箱)加高、加长、加宽的结构、装置的要求(见 11. 3. 1 );—修改了中置轴车辆运输列车的主车载货部分的结构要求(见11.3.4,2012年版的11.3.4);—增加了旅居车的乘客门要求(见11.5.2);—修改了乘客门开启的要求和车长大于9 m的未设置乘客站立区的客车的乘客门数量要求(见11.5.4,2012年版的11.5.4);—修改了汽车车窗采用安全玻璃类型的表述(见11.5.6,2012年版的11.5.6);—修改了部分汽车车窗玻璃的可见光透射比要求(见11.5.7,2012年版的11.5.7);—增加了客车、旅居车、专项作业车乘坐区的两侧应设置车窗的要求(见11,5.8);—增加了电动天窗的相关要求(见11.5.9);—增加了使用遥控钥匙的汽车的特殊要求(见11.5.10);—增加了所有乘员座椅及其布置应能保证就坐乘客的乘坐空间的要求(见 1 1 . 6 . 2 ) ,—修改了车长小于6 m的乘用车、旅居车的座椅布置要求(见11.6.3,2012年版的11.6.3);—删除了客车车组人员若为折叠座椅时的相关要求(见2012年版的 11. 6.5);—增加了客车(乘坐人数小于20 的专用客车除外)踏步区域不应设置座椅、乘客通道内不应设置供乘客使用的折叠座椅、应急门引道处座椅布置和测量及设有乘客站立区的客车应安装供站立乘客用的护栏、扶手等装置的要求(见11.6.5) ,—增加了客车座椅在车辆横向上不应采用“2十3”布置(最后—排座椅除外)的要求(见1 1.6.6);—增加了汽车(无驾驶室的汽车除外)应设置用于电子标识安装的微波窗口的要求(见11.9);—增加了部分货车、货车底盘改装的专项作业车、挂车的防飞溅系统要求(见11.10.1);—修改了应装备汽车安全带的座椅范国(见12.1.1,2012年版的12.1.1);—修改了应装备三点式(或全背带式)汽车安全带的座椅范围(见12.1.2 ,2012年版的12.1.2);—增加了能折叠进人车辆的后部或行李舱的整体座椅或座墊或靠背的相关要求(见12. 1.4);—修改了应装备驾驶人汽车安全带佩戴提醒装置的车辆类型和功能要求(见 12. 1. 5 ,,2012 年版的12.1.5);—增加了部分载客汽车应装备能有效固定轮椅、担架的安全带或其他约束装置的要求(见12. 1.7);—修改了间接视野要求(见12.2.1、12.2.2、12.2.3,2012年版的12.2.1、12.2.2、12.2.3);—增加了自学用车应安装有符合规定的辅助后视镜的要求(见12.2.6);—增加了客车应设置与其乘坐人数相匹配数量的乘客门、应急窗的要求(见12.4. 1. 1 );—修改了撤离舱口的设置要求(见12.4.1.2,2012年版的12.4.1.2);—增加了客车不应安装有其他固定、锁止应急门的装置的要求(见12.4.2.5) ,—修改了应急窗的面积要求(见12.4.3.1,2012年版的12.4.3.1);—修改了应急窗的开启方式要求(见12.4.3.2,2012年版的12.4.3.2);—修改了设有乘客站立区的客车的应急窗的型式要求(见12.4.3.3,2012年版的12.4.3.2);—増加了未设置乘客站立区的客车的应急出口形式要求及自动破窗功能要求(见12.4.3.4);—增加了应急出口字样的字体高度要求(见12.4.4.1);—增加了不准许用户改动燃料种类的要求(见12.5.1);—修改了车用气瓶出气(液)口端的过流保护功能要求(见12.6.1,2012年版的12.6.1);—增加了液化天然气管路减压阀不应设置在密封空间或其上部有相对密封气穴的位置的要求(见12.6.4);—增加了安装在汽车后轴之后的钢瓶后方应采取有效防护措施的要求(见12. 6. 12);—增加了货车列车、铰接列车牵引杆孔、牵引座牵引销的规格应与其挂车总质量相匹配的要求(见12.7.2);—增加了牵引连接件、牵引杆孔、牵引座牵引销、连接钩及环形孔等机械连接件的规定(见12.7.4);—增加了货车、专项作业车的前下部防护要求(见12.8) ,—修改了应提供后下部防护的货车、专项作业车范围(见12.9.3,2012年版的12,8.3);—修改了封闭式货车的隔离装置的要求(见12.11.3,2012年版的12.10.3);—增加了旅居车应在前后部设置保险杠及在前风窗玻璃上装有除雾、除霜装置的要求(见12.15.3、12.15.4);—修改了机动车排气管口的朝向要求(见12.15.7,2012年版的12.13.7);附表4(车辆安全装置检查部分)—増加了部分客车应装备车道保持辅助系统和自动紧急制动系统的要求(见4.17.3);—增加了新出厂的机动车的安全装置配备、质量和尺寸参数偏差及在用的货车、挂车的相关要求(见4.17.7);—增加了对采用了主被动安全新技术、新装置、新结构的机动车的特殊规定(见4.17.8);—修改了应装备防抱制动装置的机动车范围(见7.2.12、2012年版的 7.2. 11) ,增加了总质量大于或等于12000 kg的危险货物运输货车应装备电控制动系统的要求(见7.2.12);—增加了防抱制动装置的特殊要求(见7.2.13) ,—增加了自学用车的行车制动应装备有副制动装置的要求(见7.2.14) ,—增加了部分汽车的剩余制动性能要求(见7,3.5);—修改了辅助制动装置的配置要求和性能要求(见7.5.1 ,2012年版的7.5) ,增加了装备电涡流缓速器的汽车其电涡流缓速器的安装部位应设置温度报警系统或自动灭火装置的要求(见7.5.2);—增加了安装制动间隙自动调整装置的部分汽车的报警装置要求(见7.9.5);—修改了行驶记录装置的技术要求及应装备行驶记录装置和车内外视频监控录像系统的车辆类型(见8.6.5 ,2012年版的8.6.5) ,增加了车内外视频监控录像系统的摄像头配备等相关要求(见8.6.5);—增加了乘用车应配备事件数据记录系统( EDR)或车载视频行驶记录装置的要求(见 8.6.6 );—增加了总质量大于或等于12000 kg的货车应装备车辆右转弯音响提示装置的要求(见8.6.7);—增加了部分客车和危险货物运输货车的转向轮应装备轮胎爆胎应急防护装置的要求(见9.2.4);—修改了车长大于或等于6 m的客车的超速报警功能要求(见10.5.1、2012年版的10.5.1);—增加了三轴及三轴以上货车应具有超速报警功能的要求(见 10.5.2);—修改了应具有限速功能或配备限速装置的载客汽车范围(见 10.5. 3 ,,2012年版的 10.5.3);—增加了加气量大于或等于375 L的气体燃料车辆应安装导静电橡胶拖地带的要求(见12.6.8);—修改了客车灭火装置的配置要求(见12.10.2,2012年版的12.9.2、12.9.3);—增加了车长大于或等于 6 m的纯电动客车和插电式混合动力客车电池箱安全防护的特殊要求(见12.10.3);—增加了公共汽车客舱固定灭火系统的性能要求(见 12.10.4);—增加了安装有起重尾板的货车和挂车的特殊安全防护要求(见 12.11.4、12.11.5);—修改了专门用于运送易燃和易爆物品的危险货物运输车辆的排气管布置和导静电橡胶拖地带要求(见12.12.1,2012年版的12.11.1);—修改了罐式危险货物运输车辆罐体顶部的倾覆保护装置要求(见12.12.2,2012年版的12.11.2);—增加了装有紧急切断装置的罐式危险货物运输车辆的紧急切断阀应能自动关闭或通过明显的信号装置提示驾驶人需要关闭紧急切断阀的要求(见12.12.4);—增加了纯电动汽车、插电式混合动力汽车的特殊安全防护要求(见12.13);—増加了汽车(无驾驶室的三轮汽车除外)应装备1件反光背心及车长大于或等于6 m的客车和总质量大于3500kg的货车应装备至少2个停车楔的要求(见12.15.2);—修改了发动机舱应使用的隔音、隔热材料的阻燃性能应达到 GB 8410规定的 A级的要求的客车的类型(见11.7.2,2012年版的11.7.2);—增加了旅居车应装备灭火器的要求(见 12.15.8);附表5(车辆底盘动态检验部分)—增加了车高大于或等3.7m的未设置乘客站立区的客车应装备电子稳定性控制系统的要求(见4.17.4);—増加了车辆运输车应符合 GB/T26774的要求(见4.17.5);—增加了插电式混合动力汽车的纯电动续驶里程要求(见4.17. 6);—增加了纯电动汽车的电机系统应运转平稳的要求(见5.4);—增加了采用气压制动的汽车、挂车的制动响应时间要求(见7.2.10);—修改了仪表灯的点亮要求(见8.3.1,2012年版的8.3.1);—修改了机动车装备的仪表内容显示的要求(见8.6.3,2012年版的8.6.3);—修改了自动变速器的换挡动作要求(见10.2.1 ,2012年版的10.2.1) ,增加了变速器出现功能限制使用情形时对驾驶人应有警示信息提示的要求(见10.2.1);—修改了纯电动汽车和插电式混合动力汽车通过改变电机旋转方向实现前进和倒车两个行驶方向转换的操作安全要求(见10.2.4,2012年版的10.2.4);附表6(车辆底盘部件检查部分)—增加了危险货物运输半挂车、三轴的栏板式和仓栅式半挂车的所有车轮应装备盘式制动器的要求(见7.2.6);—增加了所有客车、危险货物运输车辆及总质量大于3 500 kg的货车、专项作业车和半挂车(具有全轮驱动功能的货车和专项作业车除外)的所有行车制动器应装备制动间隙自动调整装置的要求(见7.2.7);—增加了部分危险货物运输车辆和半挂车应装备空气悬架的要求(见9.4) ,。
最新 车轮定位项目作业表

(069)
检查左后2号后悬架臂是否变形损坏
(070)
检查右后2号后悬架臂是否变形损坏
(071)
检查左后1号后悬架臂是否损坏
(072)
检查右后1号后悬架臂是否损坏
如发现底盘和悬架存在其它严重问题,还可以在“车辆状况”中输入,但此次比赛不计分数
[举升位置3]操作举升机大剪降至最低落锁位置,定位检测前准备
车轮定位项目作业表
选手姓名参赛号:裁判签字:
车型:VIN号:生产日期:
1号选手作业顺序
评分
项目内容
标准说明
作业记录
合作项目说明
[举升位置1 ](举升器未升起,在最低位置)
检查车辆停放位置
(001)
目视检查车身前后、左右有无倾斜(是否水平)
(002)
检查车辆在举升机上前部停放是否周正
(003)
检查车辆在举升机上后部停放是否周正
或异物
(028)
目视检查右后轮胎是否有裂纹,损坏,异常磨损是否嵌入金属颗粒
或异物
(029)
使用胎纹深度尺,测量左前轮胎面沟槽深度并记录
要求:每个车轮检查由单人独立完成。测量每个轮胎同一位置中间沟槽的深度,如有偶数沟槽任选中间一个,但四轮选择相同。沟槽之间深度差满足定位要求。
(030)
使用胎纹深度尺,测量右前轮胎面沟槽深度并记录
(031)
使用胎纹深度尺,测量左后轮胎沟槽深度并记录
(032)
使用胎纹深度尺,测量右后轮胎面沟槽深度并记录
(033)
使用胎压表检查或调整左前轮气压到达标准并记录
(034)
使用胎压表检查或调整右前轮气压到达标准并记录
(035)
车轮定位项目作业表评分标准
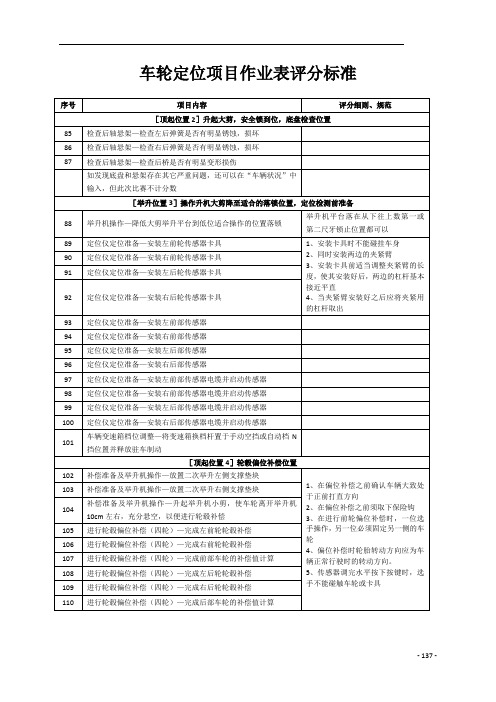
车轮定位项目作业表评分标准
车轮定位项目作业表评分标准
车身修复(钣金)方案说明
一、车身电子测量和校正(占实操分值30%)
1、作业要求
(1)在40分钟内,先对车身进行车身底部测量并记录(共6对12个测量点,分别为2对基准点,4对测量点),然后再对前纵梁进行测量、记录并校正。
(2)比赛提供3张不同测量点的车身图,选手抽签确定比赛用车身图。
每个选手独立使用超声波测量系统对要求的测量点进行测量,记录下实际测量的数据(长、宽、高数据)。
比赛提供前纵梁标准校正数据,选手通过测量确定前纵梁的变形大小和方向,然后使用车身校正仪对前纵梁宽度数据进行校正。
2、考核要点:
测量系统的使用、测量数据准确性、校正过程和校正后数据的准确性、安全防护、校正设备使用、5S等。
二、钣金更换(占实操分值40%)
板件更换项目的工件为成型板件,工件形状如图:
A、D板件:镀锌钢板,厚度0.7mm
B、E板件:热冲压钢板,厚度1.2mm
C、板件:镀锌钢板,厚度1mm
D、板件孔径(已加工好):9mm×4个孔,6mm×4个孔
E、板件孔径(已加工好):8mm
1、作业要求:
在40分钟内对提供的板件(A、B、C板件)进行电阻点焊、测量、画线、切割、定位、保护焊等操作。
(1)A、B、C板件结合。
①按照下图尺寸,在A板件上测量、划线,确定焊点位置。
②A、B、C板件定位,使用电阻点焊焊接在一起,每边10个焊点(如下图)。
(2)板件切割分离。
①根据D长度尺寸,割锯切割分离A板件。
(如下图)。
- 1、下载文档前请自行甄别文档内容的完整性,平台不提供额外的编辑、内容补充、找答案等附加服务。
- 2、"仅部分预览"的文档,不可在线预览部分如存在完整性等问题,可反馈申请退款(可完整预览的文档不适用该条件!)。
- 3、如文档侵犯您的权益,请联系客服反馈,我们会尽快为您处理(人工客服工作时间:9:00-18:30)。
序号作业类型+作业内容
[举升位置1 ](举升机未升起,在最低位置)
1准备工作-安装车轮挡块(单轮安装)
2准备工作-检查转角盘和滑板是否在锁止状态
3准备工作-检查车辆停放状况,必要时调整
4准备工作-安装座椅套、地板垫、方向盘套
5准备工作-检查方向盘是否在正中位置,降下司机侧门窗玻璃6检查车辆载荷-检查并记录燃油表值
7检查车辆载荷-检查车辆载荷是否符合定位测量要求
8车辆识别-记录车辆型号、VIN码、车辆生产日期
9车辆识别-记录车辆铭牌载明的轮胎型号和胎压
10准备工作-检查实车安装轮胎型号是否与车辆铭牌要求一致 ,检查轮胎气压,必要时调整并记录。
11在定位仪程序中建立用户和车辆档案-在定位程序中输入选手编号和车辆VIN码。
12正确选择车型数据-在数据库中找到相应车型,完成车型数据选择,并输入轮胎尺寸和标准胎压。
13车辆变速箱档位调整-将换档杆置于空挡位置并释放驻车制动[举升位2](二次举升)
14举升机操作-用小剪举升车辆
15检查车轮-检查前轮松旷状况
16检查车轮-检查后轮松旷和拖滞状况
17检查车轮-检查四轮轮辋和轮胎是否有裂纹、损坏、异常磨损,
同轴轮胎花纹是否一致。
2018年湖北省中职学校汽车运用与维修技能大赛车轮定位项目作业表
选手号 : 工位号: 裁判签字:
作业记录
18检查车轮-测量并记录左前轮胎花纹深度(里中外)。
[顶起位置3]升起大剪,安全锁到位,底盘检查位置
19举升机操作-大剪举升车辆至合适高度
20检查后悬架-检查左后减振器和弹簧
21检查后悬架-检查后桥及其托架
22检查后悬架-检查后悬架锁闩连杆、中心枢轴球节、平衡梁支架23检查后悬架-检查右后减振器和弹簧
24检查转向系统-检查左前转向横拉杆/转向节/球头
25检查前悬架-检查左前下控制臂/球节/前后衬套
26检查前悬架-检查前稳定杆及其连杆
27检查转向系统-检查右前转向横拉杆/转向节/球头
28检查前悬架-检查右前下控制臂/球节/前后衬套
29检查前悬架-检查前悬架与车身连接螺栓(后部内侧2个螺栓)30检查前悬架-检查前悬架加长件与车身连接螺栓(后部2个螺栓)[举升位置4] 轮毂偏位补偿及定位检测
31举升机操作-降低大剪举升平台至适合的落锁位置
32悬架复位-拔出转盘固定销
33举升机操作-举升机小剪缓慢回落
34悬架复位-移开车轮挡块至合适位置
35悬架复位-按压前后车身数次,使车辆悬架复位
36悬架复位-将车辆向后推离转角盘并插上转角盘销子
37车辆停放-向前推动车辆使前轮停在转角盘中心位置
38车况检查-测量并记录车身高度
39定位仪定位准备-安装卡具和标板
40进行轮毂偏位补偿-推动车辆完成车轮补偿
41调整前的检测准备工作-实施驻车制动
42调整前的检测准备工作-使用刹车锁顶住脚刹车踏板
43调整前的检测准备工作-拔出转盘和滑板固定销并取下垫板
44按照程序检测车辆-按照程序引导,进行定位测量(含最大转向角)。
45按照程序检测车辆-按照程序引导,在定位调整前使用方向盘锁锁定方向盘位置。
[顶起位置5] 定位调整位置
46操作举升机,升高到较高适合调整位置并落安全锁
47根据前束参数判断转向拉杆的调整方向需要在记录单上记录
48设定拉杆锁紧螺母的扭矩设定扭力扳手扭矩(不用复原)
[举升位置6] 定位检测位置(调整后)
49调整后的检测准备工作-降低大剪举升平台到合适操作的位置落锁
50保存检测报告-跳过调整后检测步骤,打印保存检测报告51定位仪复位-定位仪程序复位
52定位仪复位-取下标板和卡具并放回初始位置
53定位仪复位-拆除刹车锁和方向盘锁,并放至规定位置[举升位置7] 转角盘和后滑板锁止
54举升机操作-升起举升机小剪,使车轮悬空
55插入转角盘和后滑板的固定销-将转角盘和后滑板固定销插入并复位垫板
56举升机操作-举升机小剪缓慢回落,完全回位车轮平稳落在大剪平台即可,位置无须调整
【举升位置8】设备和工位整理、清洁
57举升机操作-操作举升机大剪回到最低位置
58车辆复位-将车辆恢复到初始状态
59工位整理-取下车内三件套,升车窗玻璃,关闭车门(不锁)60工位整理-放回车辆二次举升垫块和车轮挡块
*比赛车辆基本条件及要求如下:
1、选手需保存pdf文档的检测报告。
2、记录在项目中检查到的故障并按手册标准或请示裁判处理。
扣分。