精益生产异常项目改善调查表
精益生产--山积表

标
标准作业是企业认可的,能够
准
安全、保证质量、很少浪费、
作
合理成本、以人的动作为中心,
业
应该严格遵守的作业方法。
的
定
义
它由节拍时间、作业顺
与 作
序和标准手持三要素组 成。
用
1、明确安全地、低成本 地生产优良产品的制造
方法;
2、目视化管理的工具;
3、用作改善的工具
二
标准作业及三要素
标准作业与作业标准的区别
450*60S*80%
生产节拍(T.T) = 600件
= 36S/件
二
标准作业及三要素
练习题:
某工厂生产发动机,2月份的市场需求量为11000台,此工厂总装车 间工人一个月出勤22天,每天24小时分三班交替上班,每班休息时 间及就餐时间共35分钟。假设此总装车间可动率为90%,请问总装 车间2月份生产节拍(T.T)是多少秒?
➢不能影响操作者的正常作业 ➢必须以“作业”为开始,不可以从“等待”或“步行”开始; ➢操作者为同一人; ➢设备为相同设备; ➢机型不变; ➢需要拍摄整个场景,包括与本工序有关的零件的盛放盒,工位器具的布 置等等。
➢长时间手工作业时,需近景拍摄,保证能够看清楚操作者的手脚移动。
三
山积表编制的具体方法
第一步:工序作业要求
所选工序满足的条件:所选工序的作业人员完成的是循环往复的标准作业,使用 标准的工作方法,符合作业标准。
第二步:作业时间调查(通过现场观察及视频拍摄)
用摄像的方式拍摄3个循环的作业视频以准确测算时间
具体要求:
➢选取技能水平中等熟练的操作者; ➢3个循环的作业顺序必须一致; ➢尽量排除操作者身体异常、及拍摄过程中故意延缓或加快作业速度的情 况
改善精益生产案例

1.2工序改善的步骤
问题的发生、发现
应该改善什么
现状分析
作业是怎样进行的
发现问题的重点 改善方案的制定 实施和评价改善方案
哪些地方不经济、不均衡、 不合理
如何排除浪费、不均衡不合 理现象
是否达到目的
跟踪处理改善方案
制定标准、防止反弹
2、工序改善的步骤 —— 2.1问题的发生发现
序号 调查项目
调查重点
1、产能、效率、生产体制对策-IE应用
如图:通过滑 槽将各种设备 串联起来可以 起到降低在制 品数量、减少 搬运、停滞浪 费的作用
生产一体化,同步化;缩短生产周期;低减成本提高效率
2、装配转向节需跨一步、转身两次、弯腰一次
每次用于搬运的时间平均需2.5秒 能否不需要搬运而一步到位? 1、将工位器具向内缩40厘米,伸手即可拿到 工件,减少搬运距离; 2、改进工位器具或踏板避免弯腰动作;
4.1布置原则
⑴统一原则 ⑵最短距离原则 ⑶物流通畅原则 ⑷利用立体空间原则 ⑸安全满意原则 ⑹灵活机动原则
4.2布置的基本形式
与生产形态相对应,布置形式大致可 分为以下4种: ⑴功能式布置(以机械为中心) ⑵流程系列式布置(以流程为中心) ⑶固定式布置(以产品为中心) ⑷混合式布置
搬运案例分析:
第四篇 时间分析
1、QC研究小组和改善方法 2、时间分析 3、使用跑表法的时间分析 4、设定标准时间
1、QC研究小组和改善方法
● 专业IE工程师、生产科长、主
价值流 供应商管理 库存 分析 与评估管理 管理
可以做生产线设计的IEr
看板 设定 与管理
任
IE工程师入门
● 第一线监督者
PTS法标 可靠性 Layout分 物流系统 准时间 评估 析改善 作业标准化
质检班精益生产改善提案

质检班精益生产改善提案1作为一个生产制造企业,精益管理包含了精益设计和精益生产。
精益设计在于主要减少在生产过程中不必要的材料成本浪费和作业成本浪费。
而精益生产则是通过尽可能的优化生产流程,提高生产效率和品质,从而达到精益生产管理的目标。
2对于工厂企业来说,原材料成本一般会占了总成本中较高的份额,所以精益设计非常重要,是节约成本的关键因素。
工厂企业要做好精益设计,需要非常深厚的技术沉淀,有经验丰富的技术工程师。
如果一定要使设计完美,需要经过很长时间的反复的模拟、改善、优化的过程,而在实际生产经营活动中时间总是有限的,因此精益设计就是通过在生产中的实践,不断对产品、工艺和流程进行改善优化的过程,这就是持续改进的的过程。
工厂企业的产品生产是先有订单后安排生产,所以向用户保质保量保节点地交付产品,形成实质性的产品交易是锻造企业精益管理的目标。
精益生产的核心是识别解决生产中的瓶颈,最好是提前进行评估,找出瓶颈,直接解决或找到替代方案。
精益管理的核心在于对一个具体的产品订单,在现有资源的条件下,评估瓶颈和风险,在有限的时间节点要求内,以最快的速度最有效最经济的方法完成设计和解决瓶颈问题,打通工艺路线,保质保量保节点完成生产交付,形成实际的产品交易,取得货款回收权,在此基础上开展持续各项改进工作。
3综上所述,精益管理是现代企业的一个基础课,企业要保持稳定发展的势头,精益管理是必不可少的能力,只有每一个管理者和员工都对精益管理有深入的认识,才会在管理中真正把精益细节做到位,才能使企业从中受益。
因此为激励员工共同参与公司质量改善,以达到降低成本、提升品质、增强公司经营效益,可以通过进行开展精益改善提案活动。
精益改善提案活动是指在准时交货、生产效率、库存、生产周期、质量管理、设备管理、现场工作环境、员工整体素质、剔除浪费、管理提升等方面的方法流程前后发生可对比的改变,带来实际性正面效果的临时性变革活动。
精益改善提案项目是指一系列独特的、复杂的并相互关联的活动,这些活动有着一个明确的目标或目的,必须在特定的时间、预算、资源限定内,依据规范完成。
基于精益生产的现场改善
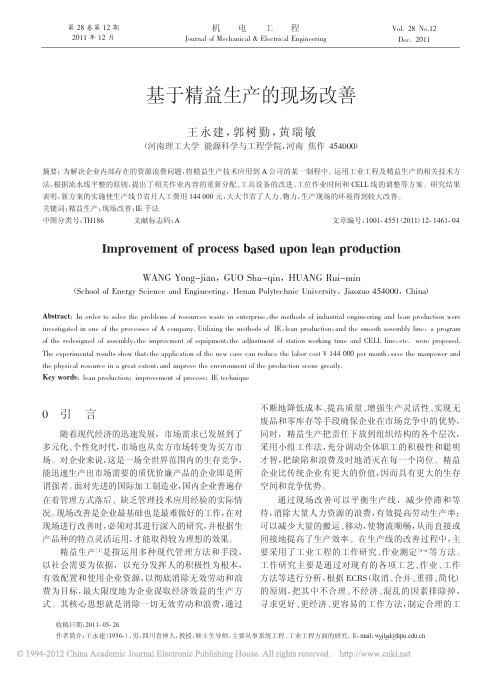
基于精益生产的现场改善王永建,郭树勤,黄瑞敏(河南理工大学能源科学与工程学院,河南焦作454000)摘要:为解决企业内部存在的资源浪费问题,将精益生产技术应用到A 公司的某一制程中。
运用工业工程及精益生产的相关技术方法,根据流水线平整的原则,提出了相关作业内容的重新分配、工具设备的改进、工位作业时间和CELL 线的调整等方案。
研究结果表明,新方案的实施使生产线节省月人工费用144000元,大大节省了人力、物力,生产现场的环境得到较大改善。
关键词:精益生产;现场改善;IE 手法中图分类号:TH186文献标志码:A文章编号:1001-4551(2011)12-1461-04Improvement of process based upon lean productionWANG Yong-jian ,GUO Shu-qin ,HUANG Rui-min(School of Energy Science and Engineering ,Henan Polytechnic University ,Jiaozuo 454000,China )Abstract :In order to solve the problems of resources waste in enterprise ,the methods of industrial engineering and lean production were investigated in one of the processes of A company.Utilizing the methods of IE ,lean production ,and the smooth assembly line ,a program of the redesigned of assembly ,the improvment of equipment ,the adjustment of station working time and CELL line ,etc.were proposed.The experimental results show that ,the application of the new case can reduce the labor cost ¥144000per month ,save the manpower and the physical resource in a great extent ,and improve the environment of the production scene greatly.Key words :lean production ;improvement of process ;IE technique收稿日期:2011-05-26作者简介:王永建(1956-),男,四川青神人,教授,硕士生导师,主要从事系统工程、工业工程方面的研究.E-mail :wyjlgd@0引言随着现代经济的迅速发展,市场需求已发展到了多元化、个性化时代,市场也从卖方市场转变为买方市场。
A03041精益生产系列现场管理和改善
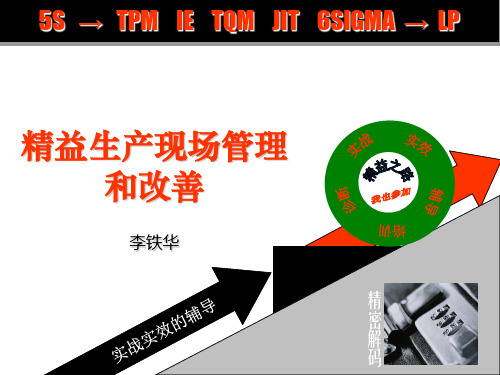
OJT——建立伙伴关系的有效途径
1. 作业说明
2.
示范, 让他做 做看
指导方式的三阶段 之准备
3. 指导后观察
制作训练计划表 谁…… 那个作业…… 到什么程度…… 到几时……
准备所有东西 标准作业书、
治工具、材料 、零件、其它 必须品……
确认标准作业书
指导别人之前先自 己做做看……
专题 委职 业绩
OJT
培训
锻炼
辅导
• OFF-JT脱岗培训 • 在QMS中HRS有程序性安排 • 其需求来自公司整体的规划和岗位能力需求 • 如:班组长的培训需求
公
司
全面引进LP制造方式
方
强化班组建设
…
针
岗 位
职责 知识
业务 知识
程
顺序合理化
作業難易度 習熟期間 必要的知識.技能
习熟期间ILU期待化
工作等級對應 的技能基準
作业要点明确化
技能教育训练体系图
作業要件一覽表
技能歷 個人管理表
技能訓練計劃表 技能教育訓練的實施
23
人员多能化
指A导C5TS工ION→作PO的WTPE方RM式IE TQM JIT 6SIGMA行→动力L咨P询
PQCDSM
PDCA 管理方法: SDCA
现场6大管理要素: 5M1E
(人员、设备、材料、环境和测量系统)
6
3.督AC5导TSIO者N→的PO位WTPE置RM IE TQM JIT 6SIGMA行→动力L咨P询
高层管理
中层管理
改进
基层管理
维持
維
作业人员
持
與
高层管理
精益生产线评审表(案例)

4.2
1
精益化管理生产线评审表
生产线名称: 序号 考评项目 考评内容 强化质量过程控制,有详尽的操作 及检验指导书,并同工艺文件一起 在各工序放置且有效执行。 加强工艺纪律,定期对操作者工艺 纪律执行情况进行检查,对发现问 题制定整改措施并有效实施。 强化产品在线检验,现场量检具齐 全且有效;按检验指导书要求开展 首、末件检验,自检、互检、专检 、巡检等检查工作。 做好质量数据(线内不良、后工序 不良、前十位质量问题等)收集、 统计和分析,对质量数据异常波动 实时分析,提出整改方案并有效实 施。月度质量指标达到控制目标要 求,运行趋势平稳、向好。 有效实施“质量门”管理,对生产 线质量控制点及在线检测进行全面 策划,完善“质量门”;明确“质 量门”操作标准和“守门人”管理 办法;每日检查“质量门”运行情 况进行,做好运行记录,确保指标 控制在特性值要求范围。 有明确的不合格品处置流程,严格 执行不合格品剔除、隔离、标识及 记录,防止不合格转入后生产线。 有效开展QC(质量控制)小组活 动,做好记录及评价,年度确保取 得1项以上公司级QC改进成果。 基本分 考评标准 检查人: 项目得分: 检查点 (请做好详细检查记录) 评审分值
3.2
1
3.3
1
现场检查当日生产情况,时节拍 差异率上下浮动超过10%,且未有 是否有时节拍差异率(达到10%以上)影响因素的记录表,并对 原因说明的,每出现一处扣0.2分 各影响因素如实记录? 。 检查生产线各工序标准作业指导 文件,每发现一处缺失的扣0.2分 1、是否对各工序的标准作业进行规定? 。 现场检查员工序作业有未按作业 2、抽选工序,按照作业指导文件检查操作的符合性。 指导标准操作的状况,每发现一 处扣0.2 分。 抽查月度工序标准作业稽查记 录,缺失或检查内容不完整的, 扣 1 分 异常统计表记录不完整或未动态 更新,扣0.5分。 生产线异常统计表未能有效体现 停工原因,扣0.5分。 生产线可动率未达到要求目标, 扣1分 抽查生产绩效指标完成情况,未 进行分析,制定改进、优化措施 的,每发现一处扣0.5分。 1、是否有工序标准作业检查计划或者周、月度检查的要求或规 定? 2、是否按照要求进行检查和记录?
精益生产:公司生产效率提升改善项目报告

制作夹具,简化工艺 普通焊机改为储能式焊接机,减少后工序作业
人员 手动大螺丝改为自动打螺丝
月份
6月 6月 6月 6月 6月 6月 6月 6月
10
19系列天花灯固定器改善
螺丝加固定器改为半牙螺丝,取消固定器
6月
4.过程亮点展示
4.1、98,143系列压线扣工艺改善
1.压线扣单价0.03元 ,预计每年省1万元
54229.5
线外人员出勤
3298 457 488 1528 3595.5 9366.5
UPPH 151.98 35.15 39.78 76.96
2.70 345.67
数据分析 基准值 129.30 29.97 35.21 66.33
2.30
提升比率 17.54% 17.28% 12.98% 16.02% 17.56%
确认
2
953A 670 17 498 11 477 11 6 10.07%
3
9225N 650 19 535 13 483 13 6 8.52%
4
923N 650 19 535 13 479 13 6 7.63%
组装
5
9825 530 23 424 16 402 16 7 9.21%
6
983
530 23 424 16 419 16 7 11.02%
生物颗粒
优
高效,熔炼,安全 方便,灵活,节能 低碳,环保,恒温
4.过程亮点展示
4.7、异形插件机方案拟定
改善前视频
改善后方案视频
4.过程亮点展示
4.8、筒灯自动化生产线方案确认
筒灯自动化线视频
4.过程亮点展示
【改善提案案例大全】生产车间改善提案案例

【改善提案案例大全】生产车间改善提案案例提案改善报告书(案例1)精益生产项目提案改善报告书项目名称提案人改善参与人员 ******** (照片、图表反应问题点):**** 倒线工装提案类别品质效率申报部门成本设备工装****** 工具环境安全提案编号 5S 其他完成日期******申报日期******(照片、图表反应改善后状况):改进前问题点图片改进后图片改进前的问题点现状改善实施方法、过程(文字重点描述改善前的做法及存在的问题): 生产中出现质量不合格产品时需从线盘上倒下,由于没有倒盘工装、设备,只能人工一点点的取下,每线盘废线用 20-30 分钟,费时、费力,效率很低,工作强度较大。
(1 重点描述自我的想法;2 改善所用工具、物料,具体改善哪些内容、怎么做的。
) 为提升倒线效率,降低工作强度,故提出制作方便、适用的、能提升倒线效率、降低工作强度的简易工装用于倒线。
方法措施:采用圆钢制作支撑底脚、一轴承座、一根线盘轴,在支撑底脚上安装轴承座、轴承,线盘轴装在轴承上,工装形成。
倒线时将线盘套在轴上,转动线盘,线因为自重自动落地。
{经济效益、能感受到、看到、摸到的(效益/年)}:(对品质、效率、安全、士气的影响):员工倒转线盘,铜线因为自重落地盘好。
用 2 分钟,提升效率 10 倍。
每倒一盘线节约工时 18 分钟。
有型效果取得成效无形效果计算根据(计算式):提升效率=改进前 20 分钟/改进后 2 分钟=10 倍。
每盘线节约工时=20 分钟 -2 分钟=18 分钟。
改善提案--范本提案改善报告提案改善报告提出日期:20xx 年 4 月 13 日班別工号姓名分机 0447 谢夫文 820 提案名稱增加导轨铣斜面治具 1.改善前哪里有缺点?哪一点不好?为什么不好?现在做法:铣床加工蒂森导轨侧边斜面8°时每次铣 1 根,加工需要工时较长,平均每根 25 分钟(如图)编号(NO):本提案类型:□维持及提高品质■增加生产量□确保安全保存單位保存年限□降低成本□6S 类□其他2.改善计划说明制作治具,使上下两根导轨错位 0.68mm 可每次铣 2 根角度均为8°(治具如图)之前治具每次铣1根专用治具增加台阶面,可铣 2 根专用治具每次铣2根3.改善后改善了什么?有什么好处?(可附表说明)节约工时:现在每次加工 1 根为 25 分钟,改善后每次加工 2 根同样 25 分钟由原来 4 根/H 改为 8 根/H,工时可节约一半,每天产能提高一倍4.直接主管会签意见判定提案的可行性及会签部门(由直属主管协助评估):5.使用单位主管会签意见使用效果确认:□ 不适用□ 尚可□ 佳□ 其他使用单位主管签字: 6.执行主管会签意见日期:责任分类:负责 1.主要責任单位:由 2.需其他部门协助处理:□技术部□计划部■质量部□销售部 3.处理期限需求:请于□一周內□两周內□一个月內□两个月內■ 总(副)经理签字:日期:□行政部222提案改善关于smt工段的提案改善意见1. 改善背景2. 现状分析3. 改善建议4. 改善汇总改善背景我司smt工段作业中存在的废时耗力情况,其中清尾补料和换单作业用时较长。
精益-DM阶段

RH在站周期长,过程存在浪费,缩短RH精炼周期,势在必行!
1、路径介绍及示例
1.4 问题陈述的示例2 提高1580分厂轧机作业率
2013年迁钢二热轧的作业率为74%; 2013年京唐1580分厂的作业率为70%,有待进一步提高。
1、 路径介绍及示例
1.1 客户需求分析的解释——是一种了解客户需求的、确定产品市场定位的工具。
本次调查共发放 质量异议处理调 查表213份,由 客服处六名人员 分别打电话催办, 共计打出电话3 73个,发出传 真245份。调查 表第一阶段回收 28份,第二阶段 回收34份,第 三阶段回收21 份,合计回收8 3份,有效调查 表77份。
1、 路径介绍及示例
1.4 客户需求分析的案例
客户期望异议 处理周期为12. 7天
1、 路径介绍及示例
1.1 项目范围的解释——包括项目的最终产品或者服务,以及实现该产品或者服
务所需要执行的全部工作。
1.2 项目范围的作用——项目范围的确定异常重要,项目范围明确规定了那些是
本项目重点研究的范围,那些是与本项目不关联的,项目团队必须在项目范
围锁定上取得共识。如果项目范围过大,可能无力完成。如果范围过小,又 会浪费项目资源,牺牲效率,降低项目的价值。
、密集图、帕累托图、箱线图、点图、直方图等。
1、路径介绍及示例
1.4 问题陈述的示例1
京唐公司RH在站周期与其他先进企业的比较
钢厂 RH周期 京唐 45min 宝钢 35min 日本 34min
上表显示,京唐公司RH在站周期比先进钢企要长;说明我们在 RH工 序的利用率上存在差距。众所周知,在站周期长导致我们过程温度需求量 大,从而能源消耗量大;同时真空槽需要长期热态才能保证生产的稳定与 顺行,在站周期长就会对热态真空槽产生较大影响,存在过程的能源浪费。
精益TnPM项目推进计划评分表
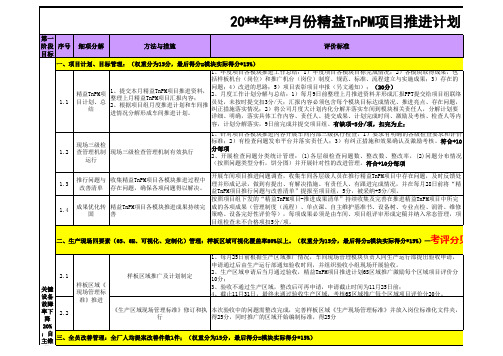
件数
接班、运行中、大班、小班、开机前、停产。记录表中出现异常的需要记录到异常故障登录表
1 件; 样板
4.2
机台/岗位目 标回顾分析
组织员工对机台/岗位的指标目标进行 分析
中,异常故障登录表中常规手段无缝解决的问题需转移到问题卡中,不按要求的扣5分/台;(20 分) 2、每月需汇总各机台/岗位的异常故障登录表,组织员工对其进行分析,并回顾是否达成目标。
20**年**月份精益TnPM项目推进计划
第一 阶段 序号 细项分解 目标
方法与措施
评价标准
一、项目计划、目标管理:(权重分为15分,最后得分=模块实际得分*15%)
1、年度项目各模块推进工作总结:1)年度项目各模块目标完成情况;2)各模块取得成果,包
括样板机台(岗位)和推广机台(岗位)制度、规范、标准、流程建立与实施成果;3)存在的
1、严格按照项目组下发的表格对11月份设备异常和故障进行规范统计,用帕雷多图对故障开展
三高一长分类统计(必要时回顾2015年设备问题),并针对排名前两位的设备问题;用why-why
分析法和(或)鱼翅图开展故障分析,找出要因并制定改进措施,跟踪验证措施有效性,并及时
5.3
设备故障管 理
按公司故障管理要求开展设备异常和 故障管理
1.3
推行问题与 改善清单
收集精益TnPM项目各模块推进过程中 存在问题,确保各项问题得以解决。
开展车间项目推进问题调查,收集车间各层级人员在推行精益TnPM项目中存在问题,及时反馈处 理并形成记录,做到有提出、有解决措施、有责任人、有跟进完成情况,并在每月28日前将“精 益TnPM项目推行问题与改善清单”提报至项目组,5分,被采纳+5分/项。
精益改善项目案例:生产效率提升(

1、”三天不变”刚性计划; 2、当天作业实物配套率提升;
(重点为恰时供货物料改善) 3、作业尾数快速补货流程; 4、自制件在制品库存降低;
工作 思路
月度意向计划准确率提升; 规范各类订单下周频率、周期; 紧急订单关键资源评审机制;
月意向计划准确率 月度订单下达次数 月度订单接单率
➢建立长物料储备订单完成率监控 ➢长线物料当天作业配套率提升; ➢总装物料异常损失时间降低 ➢供方异常停产追溯;
1. 仓储区域规划; 2. 配送器具“轮子
化” ; 3. 配送模式变革; 4. 减少无效配送;
7
Y1-生产组织模式变革
“生产组织模式变革”改善路径图
订单计划体系优化
供应保障体系改善
制造模式变革
推进 方向
1、订单评审机制建议; 2、订单下达规范性提升; 3、月度意向计划准确性改善;
1、长线物料储备机制; 2、长线物料当天配套率改善; 3、物料异常停产时间改善;
8
9
工作内容 长线计划营销系统录入 “长线计划引入ERP”请求提交 机型压缩机型号及数量匹配 机型模块型号及数量匹配 长线计划生产码转换 “长线物料计划分解”请求提交 供货比例导入
“长线物料计划分解”请求再提交
长线物料计划确认相应供应商及数量
三月 滚动 计划
序号 1 2 3 4 5 6
7
8
工作内容 长线计划营销系统录入 “长线计划引入ERP”请求提交 机型压缩机型号及数量匹配 机型模块型号及数量匹配 长线计划生产码转换 “长线物料计划分解”请求提交
产品了解美的品牌的较多
T HREATS
产品利润率较低,格力同类产 品售价高于我们1-2百元
原材料成本上升,铜等大宗材 料行情波动大,成本压力大
精益生产系列课程---品质8字改善法

倾向管理 不良预知和事前对策 不发生不良的条件管理
正常生产 零不良的实现与维持
什么是“品质改善8字法”
品质改善 8字形展开
设定不会造成不良的条件 严守不会造成不良的条件
以“零不良”为目标 维持管理的4步骤+改善的3步骤 成“8”字型无限的滚动推进
品质改善8字法实施步骤
现状应有状态的 确认与分析 现状把握
将所得到的事实整理到QM矩阵中,并作为修订基准和标准的依据
针对不方便遵守的项目进行省时、省力化改善
修订各部门的点检表,进行培训,并基于基准实施检查 实施检查结果的倾向管理,提前检讨预先对策机制
步骤一:把握现状
1-①:调查品质状况(并提出改善目标)
装配不良记录表
设定改善目标
不良 减少
现状
目标
步骤一:把握现状
0.05mm以 0.07 X
品质不良
找出品质特性与 4M1E的相关性 不会发生不良的条件设定
4M要因
培养快速发现异常能力 和快速解决问题的能力
品质部门点检 项目
检验 基准书
检验 记录表
保养部门点检 项目
定期点检整备 基准
定期保养日程 表
生产部门点 检项目
自主保养基 准书
自主保养日 程表
作业基准书
换模换线改 善
换模换线基 准书
建立条件管 理体制的教
1-①:调查品质状况
首先,对当前的制程不良和客诉进行把握, 使用“柏拉图”选定当前优先改善的课题
92%
100%
80%
65%
A
B
C
D
将不良层别到“不可分割缺陷的现象” (层别的技术要基于制造工艺的状态来分析)
精益生产系列现场管理和改善PPT
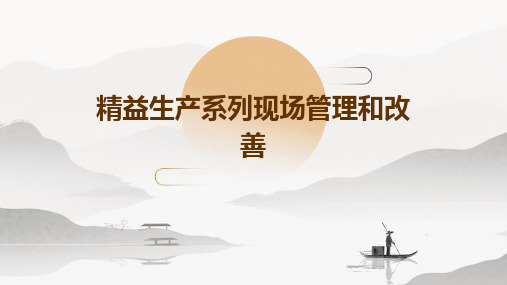
目视化管理
01
视觉识别
利用颜色、图形、文字等视觉元素, 使信息传递更加直观。
异常预警
通过红、黄、绿等颜色标识,及时 发现异常情况并进行处理。
03
02
标准化操作流程
通过可视化的方式展示操作步骤和 要点,提高工作效率。
目视化沟通
促进员工之间的信息交流和协作, 提高整体工作效率。
生产布局优化
• 总结词:通过合理规划生产布局,降低物料搬运成本和时间。
• 详细描述:生产布局是指生产设备和人员在工作场所的布局方式。合理的生产布局可以降低物料搬运成本和时间,提高 生产效率。在传统生产模式下,设备和人员布局可能存在不合理之处,导致物料搬运距离过长、时间浪费等问题。通过 优化生产布局,企业可以将设备和人员集中在一起,减少物料搬运距离和时间。这不仅可以降低生产成本,还可以提高 产品质量和客户满意度。为了实现生产布局优化,企业需要对工作场所进行重新规划和设计,并加强员工培训和标准化 操作。
跨部门协作与沟通
加强部门间的沟通和协作, 共同推进持续改进工作。
培训与知识分享
开展相关培训和知识分享 活动,提高员工的质量意 识和持续改进能力。
05
员工参与与多技能培养
员工建议系统
鼓励员工提出改进意见
建立一个平台或渠道,让员工可以随时提出对生产流程、设备、 工作环境等方面的改进意见。
定期评审与实施
持续学习与发展
鼓励员工持续学习和提升,提供进一步培训和认证的机会,促进 个人职业发展。
员工激励措施
薪酬激励
提供具有竞争力的薪酬待遇,激励员工努力工作。
晋升机会
为员工提供明确的晋升通道和机会,激发员工的 积极性和工作动力。
精益生产现场管理和改善
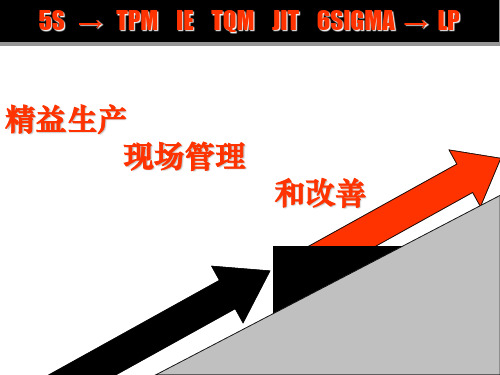
围绕品质、成本、货期、安全和士气等班组业务目标, 有效管理人员、设备、材料、方法、环境和测量6大要素, 运用PDCA管理循环推动业绩改善,确保各项目标的实现
3.督导者的位置
改进分为革新和改善
維 持 與 改 善
高层管理
中层管理
基层管理
作业人员
改进
维持
高层管理
中层管理
督导人员
作业人员
日本式 工 作 机 能
案例:某集团精益现场管理模式
1 . 现场管理者的任务
「最大限度地活用人‧物‧设备,彻底在工程中做出质量,追求效率化」.
现场的任务
现场管理者的工作
精益 公司基本方针
业务目标
PQCDSM
PDCA 管理方法: SDCA
现场6大管理要素: 5M1E 〔人员、设备、材料、环境和测量系统
不管原因
5会做、肯做、敢做而又多做
标准化做得越彻底, 改善点就越容易被发现出来!
没有标准作业的地方就没有改善可言 !
改善
标准作业 彻底执行
发现问题追查要因
实际的生产活动中,将标准作业使全员彻底执行。 仔细观察作业,针对没有遵守作业标准的人确实实施指导和训导。 如果有无法遵守作业标准之因素,应立即寻找真正的原因并立项对策。 如果作业条件有所变更,或找出更好的作业方式时,应适时修订现状之作业标准。
指导工作的方式
OJT——建立伙伴关系的有效途径
1. 作业说明
2. 示范,让他做做看
3. 指导后观察
指导方式的三阶段 之准备
制作训练计划表 谁…… 那个作业…… 到什么程度…… 到几时…… 确认标准作业书 指导别人之前先自己做做看…… 步骤好吗…… 抓到重点吗…… 调查技能程度 技能…… 知识……
精益改善报告完整版

4630211操作负荷表
时间:秒u
150
节拍:180
18 16 14 2 12 10 8 6 10 4 2 0 下料 飞料 铣长度 工序4 工序5 工序6 5 2 12 12 9 8 2 15 6 3 8
9 设备运转时间 人工操作时间
100
50
0 1 2
改善前生产一个产品所需的 时间为1233秒
– – 1.现场时间的观测 2.确定了存在的浪费
3.小批量产品生产布局 (U形生产线) 4.小批量生产线日常管理看板的制作
– – 5.工作台的制作 6.5S检点表及作业指导书的改进
珠海市俊凯机械有限公司
改善前 改善后
557559员工负荷表
500 450 400 350 300 250 200 150 100 50 0 CNC2 工人总时间 406 61
162
珠海市俊凯机械有限公司
改善前的生产现场 改善后的生产现场
设备上随处可见的油污和垃圾
设备焕然一新
珠海市俊凯机械有限公司
改善前生产现场 改善后生产现场
传统的一类设备直线分区摆放
建立的U型生产线
珠海市俊凯机械有限公司
改善前工具柜里的物品摆放 改善后工作台的物品摆放
工具摆放混乱,没有标示,经常用工 具时需要到处寻找工具浪费时间
558880 生产力(每100人工/小时)
557526 生产力(每100人工/小时) 531759 生产力(每100人工/小时)
26.2%
7.14% 78.9%
珠海市俊凯机械有限公司
俊凯快速换模工作站改善
活动背景:
美塞斯产品种类多(大至35种),单种数量少,最多的月需量 300PCS,最少的月需量45PCS
- 1、下载文档前请自行甄别文档内容的完整性,平台不提供额外的编辑、内容补充、找答案等附加服务。
- 2、"仅部分预览"的文档,不可在线预览部分如存在完整性等问题,可反馈申请退款(可完整预览的文档不适用该条件!)。
- 3、如文档侵犯您的权益,请联系客服反馈,我们会尽快为您处理(人工客服工作时间:9:00-18:30)。
改善 项目 原 因 分 析
问题点 生产线上的可回 收和不可回收边 料混乱
1WHY(可能产生的原因?)
1.作业现场的物料箱标识不清淅; 2.调机或异常故障后的调机品未及清走; 1.机台漏油; 2.机械手定位部件磨损,精准度下降; 3.取产品的机械手吸具选型不当或破损; 4.模具浇口断点差,常有堵浇口或注不满现象。
车间 废料 率的 下降
产品的超单生 产现象严重
部份产品包装方式尾数箱不合理
机台射嘴漏胶
2.射咀和模具R不符 3.射咀R角度磨损或破裂 1.质量问题不确定
机台射座与安装模具的定位环 中心点存在错位 外协加工模具 热流道模具 模具浇口被撞击,变小 不确定产品未采用分开装箱 个人能力问题 安排不合理 要及时的进行批评教育 员工对操作方法不熟练 印刷颜色、印刷位置与标准品 对比调试 烫印位置与标准品对比调试
下机后未留样提出修模
标准产量的恢复
模具堵腔太多
人员的合理安排
人工的浪费
电镀及特殊产品外观要求高 维修时间长 模具维修、保养不到位 生产计划安排不合理。 工作安排不合理。 工作时间做与工作无关的事情
材料采购时间长 难以实现一人多机。 缺乏管理专业知识的培训。
装模工装模时孔位 中心未校准 模具设计标准不一致 座进压力过大或速度太快 班组管理问题 通过技术改进来解放劳动力 临时增加人手 注意力不集中 印刷换版、换单的调试 烫金机换版、异常调机 换单、换型号的调机 烫金及丝印机实际温度与设计温度的偏差 设备日常点检、维护不力
机台射座与安装模具的定位环中心点 存在错位
操作方法过于粗暴
缺少书面一点教材
员工随意丢产品
2、超出装箱员的能力 3、假忙不过来 4、操作方法不当
后加工机台调试 产品的改善
后加工调机产品尽量采用成型的不良品
组装产品的调试 设备运行的不稳定
夹具或固定螺丝松动重新固定的调试
设备运行的不稳定 设备的润滑保养不到位 1、成型周期长
改进作业流程
工艺设定不合理。 优化包装方式,减少人工,实 现1人多机 部分连线产品受场地限制 缺乏自动设备 模具有堵腔
3WHO
员工无法正确识别可放置区域; 未及时更换补充 技工未按生产清线管理规定的要求持行工作; 设备日常点检、维护不力 横入速度过快或缓冲位置设定不合理 技术人员欠缺事物分析能力 模具设计历史问题 技术人员的技能水平与工作经验不足 操作人员成本意识淡薄与 作业方法未撑握; 根据实际情况,决定开机前是否冲机。由当班班 长检讨当班此类冲机是否必要,班长1抽查。 待确认产品未及时跟进 实验过程过长
4WH
未能形成标准作业要求。 培训、教育工作未到位。 维修人员处理不及时 专职培训太少 专岗、专业培训欠缺 日常转色流程未形成书面的作 业规范标准;
5WH
培训、引导工作未完善;
Hale Waihona Puke 配件采购周期长机台产品掉到机 台下面后污染严 重无法回收利用
1、换色清洗螺杆时冲机用料与方法未控制,来回 冲机次数过度频繁。 冲机作业不规范
及异常报警处理 时过度冲机
专职培训、教导工作欠缺;
2、异常报警处理时过度冲机 3.计划员排单时未按同色或相近颜色分类排单
返工产品处理不 及时,导致生产 完单后返工后的 废品不能回收利
1、现场返工过多,超出班组处理能力 2、检测结果滞后 1.标签打印错误 2、生产系数太大 3、未按订单量生产 4、现场返工过多,对质量缺乏信心,怕返工造成 后续补单 1.射嘴孔与模具浇口杯的孔位不在同一条直线上
2WHY
现场5S持行力差; 部分在使用中损坏 清线工作不撤底; 油封或油管磨损、破裂 机械手横入终点限位垫破损 选择吸具未做评估和检查 加工过程尺寸未到位 工艺设定不合理 深颜色难冲机时还在一味用 原料洗机 预防滞料长时间受热发生变化 订单量小、换单、换色频繁 安排不合理 实验结果未及时入系统 人为失误 与配套部门沟通不够 尾数箱按整箱生产
生产工艺缺少检查、优化
技术人员对自我检查的 意识不强
工 时 产 量 的 提 升
2、产品排箱过于浪费人力 3、连线作业程度低 4、手工作业过多
产品有质量问题,为了交货暂堵掉生产。 中夜班生产过程中堵腔未留样 质量标准不一致 加工配件时间长 维修员、保养员责任心不强 腔数少的模具和可散装产品的机台相隔太远。 班组长精益管理水平差异。 工作标准制定不合理