PCBA相关资料
某公司PCBA资料外观检验标准
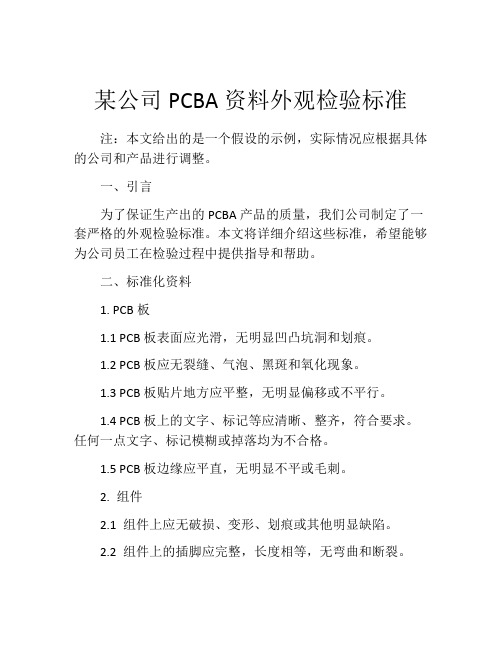
某公司PCBA资料外观检验标准注:本文给出的是一个假设的示例,实际情况应根据具体的公司和产品进行调整。
一、引言为了保证生产出的PCBA产品的质量,我们公司制定了一套严格的外观检验标准。
本文将详细介绍这些标准,希望能够为公司员工在检验过程中提供指导和帮助。
二、标准化资料1. PCB板1.1 PCB板表面应光滑,无明显凹凸坑洞和划痕。
1.2 PCB板应无裂缝、气泡、黑斑和氧化现象。
1.3 PCB板贴片地方应平整,无明显偏移或不平行。
1.4 PCB板上的文字、标记等应清晰、整齐,符合要求。
任何一点文字、标记模糊或掉落均为不合格。
1.5 PCB板边缘应平直,无明显不平或毛刺。
2. 组件2.1 组件上应无破损、变形、划痕或其他明显缺陷。
2.2 组件上的插脚应完整,长度相等,无弯曲和断裂。
2.3 组件上的焊点应均匀、无气泡、无明显渗透、无分层。
同时焊点的封度应保持良好。
2.4 组件的上表面或保护层应整齐、无泡、无皱褶、无明显瑕疵。
2.5 组件的结构应牢固、无松动、无缺损。
3. 整体功能3.1 PCBA上所有连接线路的通电和短路都应测量一次,测试设备读数正确,报警,显示一致。
3.2 PCB板上测试点的读数应符合其规格范围,且不得有异常信号,如短路、开路等。
3.3 整个PCBA可正常呼吸灯,并符合规格要求。
3.4 没有其他未列出的损坏、缺陷等。
三、检验过程1. 前检1.1 所有PCBA必须在生产前检查一遍,检查目的是发现潜在的问题。
1.2 前检应由生产人员进行,结果必须由质量控制人员审核和签字确认。
2. 初检2.1 初检应在PCBA生产完成后的第一时间进行。
2.2 初检应由一名质量控制人员进行,检查结果必须记录在检验表格上。
2.3 PCBA有任何一个不合格项,则PCBA必须送回生产部门重新制作。
3. 终检(出货前检验)3.1 终检是产品质量的最后一个把关,不得有任何疏漏。
3.2 所有产品必须经过严格的终检,通过检验后才能出货。
pcba检验标准 -回复

pcba检验标准-回复什么是PCBA检验标准?为什么需要检验标准?检验标准的应用范围是什么?如何制定有效的PCBA检验标准?这些问题将在下面的文章中进行详细讨论。
PCBA(Printed Circuit Board Assembly)检验标准是根据PCBA的工艺要求和安全性能制定的一套规范和指导原则。
PCBA是指将印刷电路板和组装件(包括元器件、插件、连接器等)进行焊接、组装和测试,形成一个完整的电子装配体的过程。
由于PCBA在电子产品的制造过程中起着非常重要的作用,因此确保其质量和可靠性对产品的最终性能和可持续发展至关重要。
PCBA检验标准的制定主要是为了实现以下几个目标。
首先,通过标准化的检验方法和程序,确保PCBA质量的一致性和稳定性,降低产品的缺陷率。
其次,通过合理的检验标准可以提高PCBA生产过程的效率,减少资源的浪费和重复劳动。
此外,检验标准还可以帮助企业改进生产工艺,优化生产流程,提高产品的可靠性和竞争力。
PCBA检验标准的应用范围非常广泛,涵盖了各个行业的电子产品制造。
无论是消费类电子产品,如手机、电视机等,还是工业设备、医疗设备等专业领域的电子产品,都需要进行PCBA检验。
此外,在军工领域,PCBA的质量和可靠性对战争装备的正常运行和作战力的发挥至关重要,因此对于军工产品更加严格的质量控制和检验要求。
制定有效的PCBA检验标准需要考虑多个因素。
首先,标准必须与PCBA的设计要求、工艺要求和使用环境相匹配。
只有确保标准的科学性和合理性,才能保证检验结果的可靠性和有效性。
其次,标准应该具备可操作性和可行性,易于实施和执行。
标准应该清晰明确地规定了检验的要点、程序和方法,以便操作人员能够正确理解和应用。
最后,标准还应该考虑到行业的最新发展和技术的进步,随时进行修订和更新,以适应不断变化的市场需求和品质要求。
总之,PCBA检验标准在电子产品制造中发挥着重要的作用。
通过制定和实施有效的检验标准,可以提高PCBA质量和可靠性,提高生产效率和生产流程的优化,并满足不同行业对于电子产品质量的要求。
PCBA性培训资料

PCBA性培训资料一、PCBA 简介PCBA 是 Printed Circuit Board Assembly 的缩写,即印刷电路板组装。
它是将电子元器件安装在印刷电路板上,并通过焊接等工艺使其成为一个具有特定功能的电子组件。
PCBA 广泛应用于各种电子设备中,如计算机、手机、家电、汽车电子等。
二、PCBA 生产流程PCBA 的生产流程大致可以分为以下几个主要步骤:1、设计原理图设计:确定电路的连接和功能。
PCB 布局设计:安排电子元器件在电路板上的位置。
2、制板制作 PCB 裸板:通过蚀刻、钻孔等工艺将电路图印制在基板上。
3、元器件采购根据 BOM(物料清单)采购所需的电子元器件。
4、贴片使用贴片机将表面贴装元器件(SMD)精确地安装在 PCB 板上。
5、插件手工或机器将插件元器件插入 PCB 板的相应孔位。
6、焊接采用回流焊或波峰焊等工艺将元器件焊接在 PCB 板上。
7、检测进行外观检查,确保元器件安装正确、无短路等缺陷。
功能测试,检测 PCBA 是否能正常工作。
8、清洗去除焊接过程中产生的助焊剂等残留物。
9、包装对合格的 PCBA 进行包装,以保护其在运输和存储过程中不受损坏。
三、PCBA 中的电子元器件1、电阻作用:限制电流、分压等。
常见类型:固定电阻、可变电阻。
2、电容作用:存储电荷、滤波、耦合等。
常见类型:电解电容、陶瓷电容、钽电容等。
3、电感作用:储存能量、滤波等。
常见类型:空心电感、磁芯电感。
4、二极管作用:单向导电、整流等。
常见类型:整流二极管、稳压二极管、发光二极管等。
5、三极管作用:放大信号、开关等。
常见类型:NPN 型三极管、PNP 型三极管。
6、集成电路(IC)作用:实现复杂的功能,如运算、控制等。
常见类型:微处理器、存储器、逻辑芯片等。
四、PCBA 焊接工艺1、回流焊原理:通过加热使焊膏熔化,实现元器件与 PCB 板的焊接。
优点:焊接质量高、效率高、适合表面贴装元器件。
PCBA半成品检验规范

PCBA半成品检验规范一、引言PCBA(Printed Circuit Board Assembly)是指将电子元器件焊接在印制电路板(PCB)上形成电路连接的工艺过程。
在生产过程中,对PCBA半成品的质量进行检验是至关重要的,这有助于确保最终产品的性能和可靠性。
本文将介绍PCBA半成品检验的规范和要求。
二、外观检验1. PCB外观检验PCB的外观检验包括检查表面是否平整,焊盘是否存在破损或变形等。
同时也需要检查PCB上的丝印是否清晰可辨,是否有缺陷。
2. 焊接质量检验焊接质量对于PCBA的性能至关重要。
在检验焊接质量时,需要注意以下几个方面:- 焊接质量:检查焊盘是否焊接牢固,是否存在焊虚焊接或焊接不良的情况。
- 焊剂残留:使用显微镜检查焊盘上是否有残留的焊剂,焊剂残留可能导致短路或影响信号传输。
- 焊点距离:检查焊盘上的焊点与焊盘之间的距离,确保符合设计规范。
三、功能性检验1. 电气测试通过电气测试检验PCBA半成品在工作电压下的电气性能。
常用的电气测试方法有:- 电阻测试:检查电路中的电阻值是否符合设计要求,以排除开路或短路现象。
- 绝缘测试:检查电路板之间的绝缘情况,以确保不会发生漏电或电容等问题。
- 高压测试:在一定电压下检查电路是否能正常工作,以验证其耐压能力。
2. 功能性测试根据PCBA半成品的设计要求,在实际工作环境中进行功能性测试。
测试人员需要根据产品规格书和功能说明书,进行各项功能的验证和测试,确保PCBA半成品的性能符合要求。
四、可靠性检验1. 热老化测试通过将PCBA半成品在高温条件下运行一段时间,检验其在长时期高温环境下的可靠性。
通常使用恒温箱进行热老化测试,测试样品应该在规定的温度下运行一定时间,并观察其性能和工作情况。
2. 冷热冲击试验冷热冲击试验用于检验PCBA半成品在温度变化及温度冲击下的可靠性。
将PCBA半成品暴露在高温和低温环境中交替,观察其在温度变化时是否存在问题,如焊接断裂、组件脱落等。
pcba测试检验标准
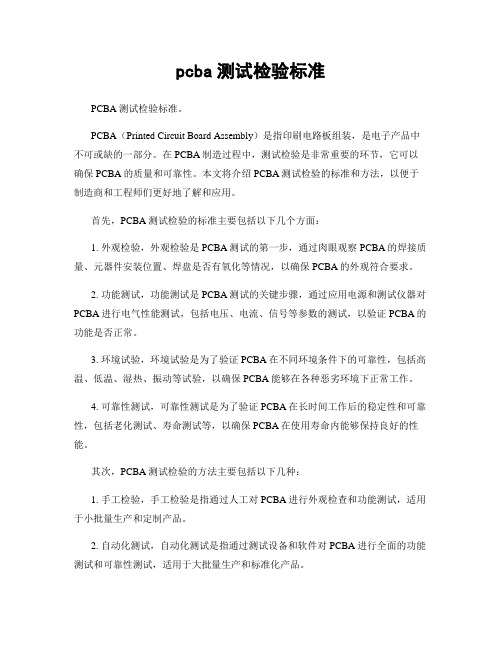
pcba测试检验标准PCBA测试检验标准。
PCBA(Printed Circuit Board Assembly)是指印刷电路板组装,是电子产品中不可或缺的一部分。
在PCBA制造过程中,测试检验是非常重要的环节,它可以确保PCBA的质量和可靠性。
本文将介绍PCBA测试检验的标准和方法,以便于制造商和工程师们更好地了解和应用。
首先,PCBA测试检验的标准主要包括以下几个方面:1. 外观检验,外观检验是PCBA测试的第一步,通过肉眼观察PCBA的焊接质量、元器件安装位置、焊盘是否有氧化等情况,以确保PCBA的外观符合要求。
2. 功能测试,功能测试是PCBA测试的关键步骤,通过应用电源和测试仪器对PCBA进行电气性能测试,包括电压、电流、信号等参数的测试,以验证PCBA的功能是否正常。
3. 环境试验,环境试验是为了验证PCBA在不同环境条件下的可靠性,包括高温、低温、湿热、振动等试验,以确保PCBA能够在各种恶劣环境下正常工作。
4. 可靠性测试,可靠性测试是为了验证PCBA在长时间工作后的稳定性和可靠性,包括老化测试、寿命测试等,以确保PCBA在使用寿命内能够保持良好的性能。
其次,PCBA测试检验的方法主要包括以下几种:1. 手工检验,手工检验是指通过人工对PCBA进行外观检查和功能测试,适用于小批量生产和定制产品。
2. 自动化测试,自动化测试是指通过测试设备和软件对PCBA进行全面的功能测试和可靠性测试,适用于大批量生产和标准化产品。
3. 抽样检验,抽样检验是指通过对PCBA进行抽样检测,以代表整个批次的质量水平,适用于中等规模生产和一般产品。
4. 定期检验,定期检验是指对PCBA进行定期的环境试验和可靠性测试,以确保PCBA的长期稳定性和可靠性,适用于长周期生产和高可靠性产品。
总之,PCBA测试检验是确保PCBA质量和可靠性的重要环节,制造商和工程师们应该根据标准和方法对PCBA进行全面的测试检验,以确保产品质量和客户满意度。
外发_PCBA稽核资料

0
重工過程中使用的MSD元件是否根據它們的潮濕敏感等級進行儲存和使用?
2.15 Is there evidence to demonstrate that the control process in use for MSDs is effective and complies with J-STD-0033A?
1.2 Is the rework process and equipment used appropriate to meet established industry standards ? 是否採用適當的重工流程和設備使得它符合工業標準要求?
1.3 Is there a tracking system in place to monitor and limit the number of Reworks conducted on any given unique board serial number? 是否有追蹤系統監控和限制給定序列號板子的重工次數?
Score Obtained 0
Score Percentage
Pass Percentage 80%
Outcome
Not Audited
23 16 70% 80%
FAIL
63 #REF! #REF! 63
63
0
0
0
0
0
80% 80% 80% 80% 80%
Not
Not
Not
Not
Not
Audited Audited Audited Audited Audited
0
是否有證據表明MSD元件的制程管控是有效的並且符合J-STD-0033A要求?
2.16 Is there evidence that a board must be slow baked prior to MSD removal for when an MSD component is needed for failure analysis?
pcba生产工作内容

pcba生产工作内容一、物料清点1.1 对照物料清单,对所有物料进行清点,确保物料数量和种类与清单相符。
1.2 对物料进行外观检查,确保无破损、老化、潮湿等问题。
1.3 如有异常,及时上报并处理。
二、SMT贴片2.1 根据生产计划,准备相应的PCBA板卡和元器件。
2.2 使用SMT贴片机进行贴片操作,确保元器件正确、稳定地粘贴在PCBA板上。
2.3 对贴片后的PCBA板进行外观检查,确保无缺件、错件、虚焊等问题。
三、光学检测3.1 使用光学检测设备对PCBA板进行外观检测,包括元器件位置、极性、焊点质量等。
3.2 对检测出的缺陷进行记录和分析,及时采取相应措施进行处理。
四、ICT检测4.1 根据产品要求,使用ICT测试设备对PCBA板进行功能性检测。
4.2 对检测出的故障进行记录和分析,及时采取相应措施进行处理。
五、DIP插件5.1 根据生产计划,准备相应的插件元器件。
5.2 进行DIP插件操作,确保元器件正确、稳定地插装在PCBA板上。
5.3 对插装后的PCBA板进行外观检查,确保无缺件、错件等问题。
六、波峰焊6.1 使用波峰焊设备对PCBA板进行焊接处理,确保焊点质量和连接性良好。
6.2 对焊接后的PCBA板进行外观检查,确保无虚焊、短路等问题。
七、人工目测7.1 使用显微镜对PCBA板进行人工目检,确保无微小缺陷和潜在问题。
7.2 对目检出的缺陷进行记录和分析,及时采取相应措施进行处理。
八、通断检测8.1 使用万用表对PCBA板进行通断检测,确保线路连接正常,无断路或短路问题。
8.2 对检测出的故障进行记录和分析,及时采取相应措施进行处理。
pcba检验标准

pcba检验标准PCBA检验标准。
PCBA(Printed Circuit Board Assembly)是指印刷电路板组装,是电子产品制造过程中的一个重要环节。
为了确保PCBA产品的质量和稳定性,需要进行严格的检验。
本文将介绍PCBA检验的标准及相关内容。
首先,PCBA检验标准包括外观检验和功能性检验两部分。
外观检验主要是对PCBA产品的外观进行检查,包括焊接质量、元件安装位置、焊盘状态等。
而功能性检验则是对PCBA产品的功能进行测试,包括电气性能、信号传输、温度稳定性等。
在进行外观检验时,需要注意焊接质量是否良好,焊盘是否出现虚焊、短路等情况,元件安装位置是否准确,元件是否倒装、漏装等。
同时,还需要检查PCBA产品的外观是否完整,有无划痕、变形等情况。
而在进行功能性检验时,需要根据PCBA产品的设计要求,进行相应的测试。
例如,对于电源板,需要测试电压、电流是否稳定;对于通信板,需要测试信号传输是否正常;对于控制板,需要测试程序运行是否正常等。
除了以上提到的检验内容外,还需要根据PCBA产品的具体要求,进行特定的检验。
例如,对于在恶劣环境下使用的PCBA产品,还需要进行耐高温、耐低温、耐湿热等环境测试。
在进行PCBA检验时,需要严格按照相关的标准进行操作,以确保检验结果的准确性和可靠性。
同时,还需要使用专业的检验设备和工具,以提高检验效率和准确性。
总之,PCBA检验是确保产品质量的重要环节,需要严格按照标准进行操作,同时结合实际情况,进行全面的检验。
只有通过严格的检验,才能保证PCBA产品的质量和稳定性,满足客户的需求和期望。
PCBA检查标准

PCBA检查标准引言PCBA〔Printed Circuit Board Assembly〕是指印刷电路板组装,也就是将元器件、芯片等组装到印刷电路板上,形成一个完整的电路板。
为了确保PCBA的质量,我们需要进行检查和测试。
本文将介绍PCBA检查的标准和方法,以确保PCBA的质量符合要求。
检查内容PCBA检查主要包括外观检查、焊接质量检查和电气性能检查。
下面将逐一介绍这些检查内容。
外观检查外观检查是检查PCBA外观是否到达要求的步骤。
具体的外观检查内容包括: - 印刷电路板上是否有划痕、破损等物理损伤; - 元器件的位置是否正确; - 元器件与电路板之间的焊接是否牢固; - 元器件是否有漏焊、多焊、错位等问题; - PCB上的标识、文字等是否清晰可辨。
焊接质量检查焊接质量检查主要是检查PCBA焊接工艺是否符合要求。
具体的检查内容包括: - 元器件焊接是否均匀、光滑; - 焊盘与元器件引脚之间是否有间隙; - 焊盘上是否有锡丝、锡球等异物; - 是否有焊接过程中产生的焊渣; - 焊盘上的焊盘量是否符合要求。
电气性能检查电气性能检查是检查PCBA的电性能是否符合要求。
具体的电气性能检查内容包括: - 使用万用表或测试仪器对PCBA进行电阻、电流等根本参数的测试; - 使用示波器对PCBA进行波形测试,检查信号质量;- 使用逻辑分析仪对PCBA进行逻辑测试,检查信号时序等。
检查方法PCBA检查可以采用目视检查和仪器检测相结合的方法。
下面将介绍具体的检查方法。
目视检查目视检查是最根本的检查方法,可以通过肉眼观察PCBA的外观、焊接质量等情况。
目视检查时,需要注意以下几点: - 在光线明亮的环境下进行检查,以确保观察结果准确; - 观察时要仔细观察每个元器件的位置、焊接质量等情况,确保没有遗漏; - 可以使用放大镜来进行细致观察,以发现微小的问题。
仪器检测仪器检测是通过使用测试仪器对PCBA的各项电性能进行检测。
pcba板检验标准
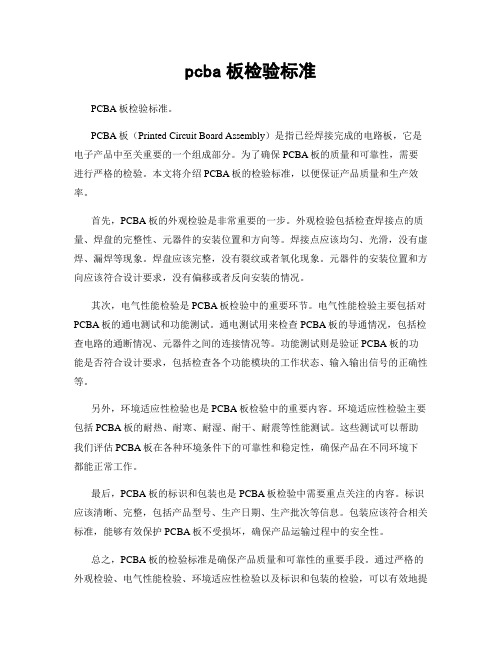
pcba板检验标准PCBA板检验标准。
PCBA板(Printed Circuit Board Assembly)是指已经焊接完成的电路板,它是电子产品中至关重要的一个组成部分。
为了确保PCBA板的质量和可靠性,需要进行严格的检验。
本文将介绍PCBA板的检验标准,以便保证产品质量和生产效率。
首先,PCBA板的外观检验是非常重要的一步。
外观检验包括检查焊接点的质量、焊盘的完整性、元器件的安装位置和方向等。
焊接点应该均匀、光滑,没有虚焊、漏焊等现象。
焊盘应该完整,没有裂纹或者氧化现象。
元器件的安装位置和方向应该符合设计要求,没有偏移或者反向安装的情况。
其次,电气性能检验是PCBA板检验中的重要环节。
电气性能检验主要包括对PCBA板的通电测试和功能测试。
通电测试用来检查PCBA板的导通情况,包括检查电路的通断情况、元器件之间的连接情况等。
功能测试则是验证PCBA板的功能是否符合设计要求,包括检查各个功能模块的工作状态、输入输出信号的正确性等。
另外,环境适应性检验也是PCBA板检验中的重要内容。
环境适应性检验主要包括PCBA板的耐热、耐寒、耐湿、耐干、耐震等性能测试。
这些测试可以帮助我们评估PCBA板在各种环境条件下的可靠性和稳定性,确保产品在不同环境下都能正常工作。
最后,PCBA板的标识和包装也是PCBA板检验中需要重点关注的内容。
标识应该清晰、完整,包括产品型号、生产日期、生产批次等信息。
包装应该符合相关标准,能够有效保护PCBA板不受损坏,确保产品运输过程中的安全性。
总之,PCBA板的检验标准是确保产品质量和可靠性的重要手段。
通过严格的外观检验、电气性能检验、环境适应性检验以及标识和包装的检验,可以有效地提高PCBA板的质量,确保产品的可靠性和稳定性。
希望本文所介绍的PCBA板检验标准能够对相关行业提供一定的参考和帮助,促进产品质量的提升和行业的发展。
PCBA加工流程资料

PCBA加工流程资料PCB设计规范1. 目的为了规范产品的可靠性、最低成本性、符号PCB工艺设计,规定PCB工艺设计的相关参数,使得PCB的设计满足可生产性、可测试性、安规、EMC、EMI等的技术多标准要求,在产品设计过程中构建产品的工艺、技术、质量、成本优势。
2.适用范围本规范适用于所有电子产品的PCB工艺设计,运用于但不限于PCB的设计、PCB投板工艺审查、单板工艺审查等活动。
3.定义3.1导通孔(via):一种用于内层连接的金属化孔,但其中并不用于插入元件引线或其它增强材料。
3.2盲孔(Blind via):从印制板内仅延展到一个表层的导通孔。
3.3埋孔(Buried via):未延伸到印刷板表面的一种导通孔。
3.4过孔(Through via):从印制板的一个表层延展到另一个表层的导通孔。
3.5元件孔(Component hole):用于元件端子固定于印制板及导电图形电气联接的孔。
3.6 Stand off:表面贴器件的本体底部到引脚底部的垂直距离。
4. 规范内容4.1产品设备的工艺设计4.1.1PCB工艺边:在SMT、AI生产过程中以及在插件过波峰焊的过程中,PCB应留出一定的边缘便于设备夹持。
这个夹持的范围应≥5mm,在此范围内不允许放置元器件和设置焊盘。
如图1图14.1.2 PCB板缺槽:PCB板的一些边缘区域内不能有缺槽,以避免印制板定位或传感器检测时出现错觉,具体位置因为不同设备而变化。
4.1.3 拼板设计要求:SMT中,大多数的表面贴装PCB板的面积比较小,为了充分的利用板材、高效率的制造生产、测试、组装、往往将一种产品的几种或数种拼在一起,对PCB的拼板有以下几点要求:a、板的尺寸不可以太大,也不可以太小,以生产、测试、装配工程中便于生产设备的加工和不产生较大的变形为宜。
现在生产使用的PCB大部分都使用纸质和复合环氧树脂基板在拼板过大的情况下很容易产生变形,所以要充份考虑拼板的大小问题。
PCBA外观检验培训资料

一、IPC-A-610基础知识
1.4、PCB
(1),PCB:印刷电路板未打上元件的板;
(2),PCBA: 印刷电路板组装已打上元件);
江苏艾索新能源股份有限公司 EverSolar © All rights reserved by EverSolar, even and especially in cases of proprietary rights applications. We also retain sole power of disposal, including all rights relating to copying, transmission and dissemination.
江苏艾索新能源股份有限公司 EverSolar © All rights reserved by EverSolar, even and especially in cases of proprietary rights applications. We also retain sole power of disposal, including all rights relating to copying, transmission and dissemination.
三、元器件安装
3.2、元器件安装---方向---水平
目标-1,2,3 级 元器件位于焊盘中间(对称中心)。 元器件标识可见。 非极性元器件同方向放置,因此可 用同一方法(从左到右或从上到下) 识读其标识。 可接受-1,2,3 级 极性元器件及多引线元器件方向摆 放正确。 手工成型与手工插件时,极性符号 可见。 元器件都按规定正确放在相应焊盘 上。 非极性元器件没有按照同一方向放置。
PCBA规范资料

项目元件种类标准要求参考图片三极管1.三极管的移位引脚水平移位不能超出焊盘区域.2.垂直移位其引脚应有2/3以上的长度在焊接区.MAMAMAMAMAMAMAMA 1.侧面偏移时,最小链接宽度(C)不得小于元件焊端宽度(W)或焊盘宽度(P)的1/2;按P与W的较小者计算。
1.末端偏移时,最大偏移宽度(B)不得超过元件焊端宽度(W)或焊盘宽度(P)的1/2.按P与W的较小者计算。
侧面(水平)移位宽度(A)不得大于其元件直径(W)或焊盘宽度(P)的1/4.按P与W的较小者计算。
末端偏移宽度(B)不大于元件焊端宽度(A)的1/2。
末端连接宽度(C)大于元件直径(W),或焊盘宽度(P)中的1/2.线圈偏出焊盘的距离(D)≦0.5mm.片式元件倾斜超出焊接部分不得大于料身(W)宽度的1/3.片式元件侧面偏位(水平)片式元件末端偏移(垂直)圆柱状元件(侧面偏移)圆柱状元件(末端偏移)圆柱状元件末端链接宽度判定移位旋转偏位线圈片式元件MAMAMAMAMAMAMAMAMA1.焊锡宽度(W)需大于PCB焊盘宽度(P)的2/32.锡面须光滑,焊接轮廓宽度L≥1/2D,锡面高度T≥1/4D元件本体浮起与PCB的间隙不得大于0.1mm。
线圈类元件不允许旋转偏位.三极管旋转偏位时每个脚都必须有脚长的2/3以上的长度在焊盘区.且有1/2以上的焊接长度.不允许正反面标示的元件有翻贴现象.(即:丝印面向下)片式电阻常见不允许焊接元件有斜立或直立现象(元件一端脱离焊盘焊锡而翘起)最小爬锡高度(F)应大于城堡高度(H)的1/3.不接受焊盘无锡的组装不良.旋转偏位后其横向偏出焊盘部分不得大于元件直径的1/4.所有元件三极管元件翻贴片式元件无引脚元件所有元件片式/圆柱状元件焊锡高度空焊少锡浮高旋转偏位反贴/反白立碑圆柱状元件线圈插件堵孔PCBA不接受锡膏残留于插件孔、螺丝孔的不良现象,避免造成DIP组装困难MA露铜PCB1.不允许PCB线路有露铜的、焊接造成铜箔翘起的现象2.不影响引线的露铜面积不得大于∮1mm.MA多件所有物料不允许有空位焊盘贴装元件MA连锡/短路所有元件 1.不允许线路不同的引脚之间有连锡、碰脚等现象形成短路。
电路板(pcba)外协加工要求【最新资料】
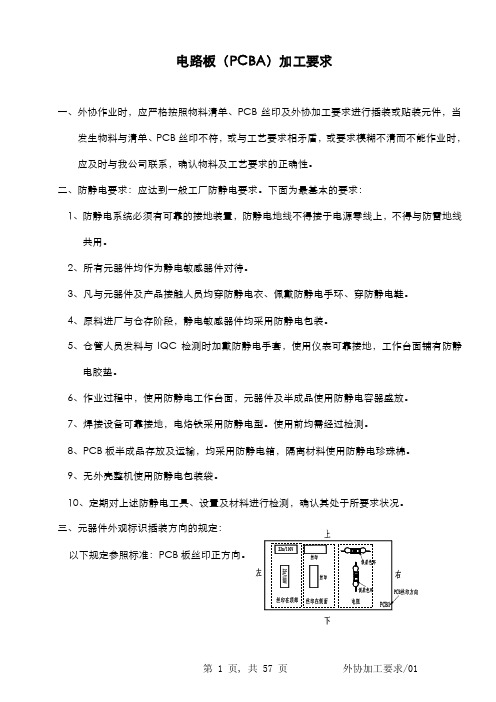
电路板(PCBA)加工要求一、外协作业时,应严格按照物料清单、PCB丝印及外协加工要求进行插装或贴装元件,当发生物料与清单、PCB丝印不符,或与工艺要求相矛盾,或要求模糊不清而不能作业时,应及时与我公司联系,确认物料及工艺要求的正确性。
二、防静电要求:应达到一般工厂防静电要求。
下面为最基本的要求:1、防静电系统必须有可靠的接地装臵,防静电地线不得接于电源零线上,不得与防雷地线共用。
2、所有元器件均作为静电敏感器件对待。
3、凡与元器件及产品接触人员均穿防静电衣、佩戴防静电手环、穿防静电鞋。
4、原料进厂与仓存阶段,静电敏感器件均采用防静电包装。
5、仓管人员发料与IQC检测时加戴防静电手套,使用仪表可靠接地,工作台面铺有防静电胶垫。
6、作业过程中,使用防静电工作台面,元器件及半成品使用防静电容器盛放。
7、焊接设备可靠接地,电烙铁采用防静电型。
使用前均需经过检测。
8、PCB板半成品存放及运输,均采用防静电箱,隔离材料使用防静电珍珠棉。
9、无外壳整机使用防静电包装袋。
10以下规定参照标准:PCB1、极性元器件按极性插装。
2、丝印在侧面的元器件(如高压陶瓷电容)竖向插装时,丝印朝右;横向插装时,丝印朝下。
丝印在顶部的元器件(不包括贴片电阻)横向插装时,字体方向同PCB板丝印方向;竖向插装时,字体上方朝右。
3、电阻卧式横向插装时,误差色环朝右;卧式竖向插装时,误差色环朝下;电阻立式插装时,误差色环朝向板面。
四、焊点:贴片焊点《贴片元件》一节中描述,此处指插装元件焊点。
1、插装元件在焊接面引脚高度1.5~2.0mm。
2、焊点高度:焊锡爬附引脚高度单面板不小于1mm,双面板不小于0.5mm且需透锡。
3、焊点形状:呈圆锥状且布满整个焊盘。
4、焊点表面:光滑、明亮,无黑斑、助焊剂等杂物,无尖刺、凹坑、气孔、露铜等缺陷。
5、焊点强度:与焊盘及引脚充分润湿,无虚焊、假焊。
6、焊点截面:元件剪脚尽可能不剪到焊锡部分,在引脚与焊锡的接触面上无裂锡现象。
- 1、下载文档前请自行甄别文档内容的完整性,平台不提供额外的编辑、内容补充、找答案等附加服务。
- 2、"仅部分预览"的文档,不可在线预览部分如存在完整性等问题,可反馈申请退款(可完整预览的文档不适用该条件!)。
- 3、如文档侵犯您的权益,请联系客服反馈,我们会尽快为您处理(人工客服工作时间:9:00-18:30)。
PCBAPCBA是英文Printed Circuit Board +Assembly 的简称,也就是说PCB空板经过SMT上件,再经过DIP插件的整个制程,简称PCBA .印刷电路板,又称印制电路板,印刷线路板,常使用英文缩写PCB(Printed ci rcuit board),是重要的电子部件,是电子元件的支撑体,是电子元器件线路连接的提供者。
由于它是采用电子印刷技术制作的,故被称为“印刷”电路板。
在印制电路板出现之前,电子元件之间的互连都是依靠电线直接连接而组成完整的线路。
现在,电路面包板只是作为有效的实验工具而存在,而印刷电路板在电子工业中已经成了占据了绝对统治的地位。
20世纪初,人们为了简化电子机器的制作,减少电子零件间的配线,降低制作成本等优点,于是开始钻研以印刷的方式取代配线的方法。
三十年间,不断有工程师提出在绝缘的基板上加以金属导体作配线。
而最成功的是1925年,美国的Charles Du cas 在绝缘的基板上印刷出线路图案,再以电镀的方式,成功建立导体作配线。
[1] 直至1936年,奥地利人保罗·爱斯勒(Paul Eisler)在英国发表了箔膜技术[1],他在一个收音机装置内采用了印刷电路板;而在日本,宫本喜之助以喷附配线法“メタリコン法吹着配线方法(特许119384号)”成功申请专利。
[2]而两者中Paul Eisl er 的方法与现今的印刷电路板最为相似,这类做法称为减去法,是把不需要的金属除去;而Charles Ducas、宫本喜之助的做法是只加上所需的配线,称为加成法。
虽然如此,但因为当时的电子零件发热量大,两者的基板也难以配合使用[1],以致未有正式的实用作,不过也使印刷电路技术更进一步。
1941年,美国在滑石上漆上铜膏作配线,以制作近接信管。
1943年,美国人将该技术大量使用于军用收音机内。
1947年,环氧树脂开始用作制造基板。
同时NBS开始研究以印刷电路技术形成线圈、电容器、电阻器等制造技术。
1948年,美国正式认可这个发明用于商业用途。
自20世纪50年代起,发热量较低的晶体管大量取代了真空管的地位,印刷电路版技术才开始被广泛采用。
而当时以蚀刻箔膜技术为主流[1]。
1950年,日本使用玻璃基板上以银漆作配线;和以酚醛树脂制的纸质酚醛基板(C CL)上以铜箔作配线。
[1]1951年,聚酰亚胺的出现,便树脂的耐热性再进一步,也制造了聚亚酰胺基板。
[1]1953年,Motorola开发出电镀贯穿孔法的双面板。
这方法也应用到后期的多层电路板上。
[1]印刷电路板广泛被使用10年后的60年代,其技术也日益成熟。
而自从Motorol a的双面板面世,多层印刷电路板开始出现,使配线与基板面积之比更为提高。
1960年,V. Dahlgreen以印有电路的金属箔膜贴在热可塑性的塑胶中,造出软性印刷电路板。
[1]1961年,美国的Hazeltine Corporation参考了电镀贯穿孔法,制作出多层板。
[1]1967年,发表了增层法之一的“Plated-up technology”。
[1][3]1969年,FD-R以聚酰亚胺制造了软性印刷电路板。
[1]1979年,Pactel发表了增层法之一的“Pactel法”。
[1]1984年,NTT开发了薄膜回路的“Copper Polyimide法”。
[1]1988年,西门子公司开发了Microwiring Substrate的增层印刷电路板。
[1] 1990年,IBM开发了“表面增层线路”(Surface Laminar Circuit,SLC)的增层印刷电路板。
[1]1995年,松下电器开发了ALIVH的增层印刷电路板。
[1]1996年,东芝开发了B2it的增层印刷电路板。
[1]就在众多的增层印刷电路板方案被提出的1990年代末期,增层印刷电路板也正式大量地被实用化,直至现在。
为大型、高密度的印刷电路板装配(PCBA, printed circuit board assembly)发展一个稳健的测试策略是重要的,以保证与设计的符合与功能。
除了这些复杂装配的建立与测试之外,单单投入在电子零件中的金钱可能是很高的 - 当一个单元到最后测试时可能达到25,000美元。
由于这样的高成本,查找与修理装配的问题现在比其过去甚至是更为重要的步骤。
今天更复杂的装配大约18平方英寸,18层;在顶面和底面有2900多个元件;含有6000个电路节点;有超过20000个焊接点需要测试。
在朗讯加速的制造工厂(N. Andover, MA),制造和测试艺术级的PCBA和完整的传送系统。
超过5000节点数的装配对我们是一个关注,因为它们已经接近我们现有的在线测试(ICT, in circuit test)设备的资源极限(图一)。
我们现在制造大约800种不同的PCBA或“节点”。
在这800种节点中,大约20种在5000~6000个节点范围。
可是,这个数迅速增长。
新的开发项目要求更加复杂、更大的PCBA和更紧密的包装。
这些要求挑战我们建造和测试这些单元的能力。
更进一步,具有更小元件和更高节点数的更大电路板可能将会继续。
例如,现在正在画电路板图的一个设计,有大约116000个节点、超过5 100个元件和超过37800个要求测试或确认的焊接点。
这个单元还有BGA在顶面与底面,BGA是紧接着的。
使用传统的针床测试这个尺寸和复杂性的板,ICT一种方法是不可能的。
在制造工艺,特别是在测试中,不断增加的PCBA复杂性和密度不是一个新的问题。
意识到的增加ICT测试夹具内的测试针数量不是要走的方向,我们开始观察可代替的电路确认方法。
看到每百万探针不接触的数量,我们发现在5000个节点时,许多发现的错误(少于31)可能是由于探针接触问题而不是实际制造的缺陷(表一)。
因此,我们着手将测试针的数量减少,而不是上升。
尽管如此,我们制造工艺的品质还是评估到整个PCBA。
我们决定使用传统的ICT与X射线分层法相结合是一个可行的解决方案。
基材基材普遍是以基板的绝缘部分作分类,常见的原料为电木板、玻璃纤维板,以及各式的塑胶板。
而PCB的制造商普遍会以一种以玻璃纤维、不织物料、以及树脂组成的绝缘部分,再以环氧树脂和铜箔压制成“黏合片”(prepreg)使用。
而常见的基材及主要成份有:FR-1 ──酚醛棉纸,这基材通称电木板(比FR-2较高经济性)FR-2 ──酚醛棉纸,FR-3 ──棉纸(Cotton paper)、环氧树脂FR-4 ──玻璃布(Woven glass)、环氧树脂FR-5 ──玻璃布、环氧树脂FR-6 ──毛面玻璃、聚酯G-10 ──玻璃布、环氧树脂CEM-1 ──棉纸、环氧树脂(阻燃)CEM-2 ──棉纸、环氧树脂(非阻燃)CEM-3 ──玻璃布、环氧树脂CEM-4 ──玻璃布、环氧树脂CEM-5 ──玻璃布、多元酯AIN ──氮化铝SIC ──碳化硅金属涂层金属涂层除了是基板上的配线外,也就是基板线路跟电子元件焊接的地方。
此外,不同的金属也有不同的价钱,不同的会直接影响生产的成本;不同的金属也有不同的可焊性、接触性,也有不同的电阻阻值,也会直接影响元件的效能。
常用的金属涂层有:铜锡厚度通常在5至15μm[4]铅锡合金(或锡铜合金)即焊料,厚度通常在5至25μm,锡含量约在63%[4]金一般只会镀在接口[4]银一般只会镀在接口,或以整体也是银的合金[编辑] 线路设计印制电路板的设计是以电子电路图为蓝本,实现电路使用者所需要的功能。
印刷电路板的设计主要指版图设计,需要内部电子元件、金属连线、通孔和外部连接的布局、电磁保护、热耗散、串音等各种因素。
优秀的线路设计可以节约生产成本,达到良好的电路性能和散热性能。
简单的版图设计可以用手工实现,但复杂的线路设计一般也需要借助计算机辅助设计(CAD)实现,而着名的设计软件有AutoCAD、OrCAD、P owerPCB、FreePCB等。
基本制作根据不同的技术可分为消除和增加两大类过程。
[编辑] 减去法减去法(Subtractive),是利用化学品或机械将空白的电路板(即铺有完整一块的金属箔的电路板)上不需要的地方除去,余下的地方便是所需要的电路。
丝网印刷:把预先设计好的电路图制成丝网遮罩,丝网上不需要的电路部分会被蜡或者不透水的物料覆盖,然后把丝网遮罩放到空白线路板上面,再在丝网上油上不会被腐蚀的保护剂,把线路板放到腐蚀液中,没有被保护剂遮住的部份便会被蚀走,最后把保护剂清理。
感光板:把预先设计好的电路图制在透光的胶片遮罩上(最简单的做法就是用打印机印出来的投影片),同理应把需要的部份印成不透明的颜色,再在空白线路板上涂上感光颜料,将预备好的胶片遮罩放在电路板上照射强光数分钟,除去遮罩后用显影剂把电路板上的图案显示出来,最后如同用丝网印刷的方法一样把电路腐蚀。
刻印:利用铣床或雷射雕刻机直接把空白线路上不需要的部份除去。
加成法加成法(Additive),现在普遍是在一块预先镀上薄铜的基板上,覆盖光阻剂(D /F),经紫外光曝光再显影,把需要的地方露出,然后利用电镀把线路板上正式线路铜厚增厚到所需要的规格,再镀上一层抗蚀刻阻剂-金属薄锡,最后除去光阻剂(这制程称为去膜),再把光阻剂下的铜箔层蚀刻掉。
积层法[1] 积层法是制作多层印刷电路板的方法之一。
是在制作内层后才包上外层,再把外层以减去法或加成法所处理。
不断重复积层法的动作,可以得到再多层的多层印刷电路板则为顺序积层法。
内层制作积层编成(即黏合不同的层数的动作)积层完成(减去法的外层含金属箔膜;加成法)钻孔减去法Panel电镀法全块PCB电镀在表面要保留的地方加上阻绝层(resist,防以被蚀刻)蚀刻去除阻绝层Pattern电镀法在表面不要保留的地方加上阻绝层电镀所需表面至一定厚度去除阻绝层蚀刻至不需要的金属箔膜消失加成法令表面粗糙化完全加成法(full-additive)在不要导体的地方加上阻绝层以无电解铜组成线路部分加成法(semi-additive)以无电解铜覆盖整块PCB在不要导体的地方加上阻绝层电解镀铜去除阻绝层蚀刻至原在阻绝层下无电解铜消失增层法增层法是制作多层印刷电路板的方法之一,顾名思义是把印刷电路板一层一层的加上。
每加上一层就处理至所需的形状。
[编辑] ALIVH[1]ALIVH(Any Layer Interstitial Via Hole,Any Layer IVA)是日本松下电器开发的增层技术。
这是使用芳香族聚酰胺(Aramid)纤维布料为基材。
把纤维布料浸在环氧树脂成为“黏合片”(prepreg)雷射钻孔钻孔中填满导电膏在外层黏上铜箔铜箔上以蚀刻的方法制作线路图案把完成第二步骤的半成品黏上在铜箔上积层编成再不停重覆第五至七的步骤,直至完成B2it[1]B2it(Buried Bump Interconnection Technology)是东芝开发的增层技术。