出货检验作业规范-
QA出货检验作业规范
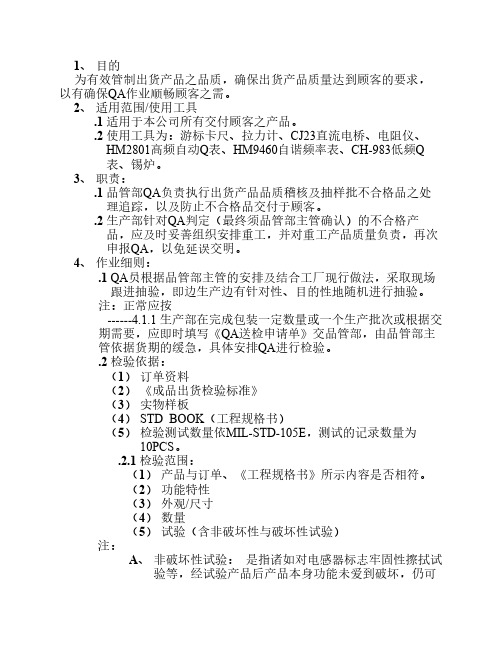
1、目的为有效管制出货产品之品质,确保出货产品质量达到顾客的要求,以有确保QA作业顺畅顾客之需。
2、适用范围/使用工具.1 适用于本公司所有交付顾客之产品。
.2 使用工具为:游标卡尺、拉力计、CJ23直流电桥、电阻仪、HM2801高频自动Q表、HM9460自谐频率表、CH-983低频Q表、锡炉。
3、职责:.1 品管部QA负责执行出货产品品质稽核及抽样批不合格品之处理追踪,以及防止不合格品交付于顾客。
.2 生产部针对QA判定(最终须品管部主管确认)的不合格产品,应及时妥善组织安排重工,并对重工产品质量负责,再次申报QA,以免延误交明。
4、作业细则:.1 QA员根据品管部主管的安排及结合工厂现行做法,采取现场跟进抽验,即边生产边有针对性、目的性地随机进行抽验。
注:正常应按------4.1.1 生产部在完成包装一定数量或一个生产批次或根据交期需要,应即时填写《QA送检申请单》交品管部,由品管部主管依据货期的缓急,具体安排QA进行检验。
.2 检验依据:(1)订单资料(2)《成品出货检验标准》(3)实物样板(4)STD BOOK(工程规格书)(5)检验测试数量依MIL-STD-105E,测试的记录数量为10PCS。
.2.1 检验范围:(1)产品与订单、《工程规格书》所示内容是否相符。
(2)功能特性(3)外观/尺寸(4)数量(5)试验(含非破坏性与破坏性试验)注:A、非破坏性试验:是指诸如对电感器标志牢固性擦拭试验等,经试验产品后产品本身功能未爱到破坏,仍可使用。
此种试验叫非破坏性试验;B、破坏性试验;是指诸如电感器引线强度拉力试验等,经试验后,产品本身结构或功能受到破坏,不可使用(或产品寿命经试验的已完全不能达到预期的使用期限),此种试验则叫破坏性试验。
拟制审核批准..2.2 抽样计划:(1) MIL-STD-105E单次正常抽样。
(2) AQL值Max(B)类=0.1 Min(C类)=0.65.3 判定及处理:.3.1 (1)QA将抽样合格成品移到“QA PASS区”并在《产品标识卡》标签上加盖自己的检验代号印章。
OQC出货检验规范及方法

DC外露尺寸
规格见《DC
JACK技术
资料》
包装数量
包装方式错误,短装,混装,多装
纸箱外观
受潮,撞伤,变形,拆痕,麦头错,
净,毛重错,数量错
以下空白
注:底盖美国客户用TCBF,欧洲客户用TCBR,英国,澳大利亚,马来西亚用TCBF3
所有安规产品须做高压测试,其标准请参照具体测试标准,其AQC值为0.
核准:审核:制作
MI
性能测试不可
超出《车充成品
测试标准》范围
无电压;空载/负载电压高,低
测试项中任何
一项或多项不
符合为一缺失
灯不亮;短路
灯亮;无电压;短路电流高,低
7。2外观检测
表面无起粒粗糙,无脏污,无灰尘,无变形
无破烂,压伤
线材
铜头弹性
铜头不可无弹性,下陷或被胶水粘死
弹片
不可变形,不可无弹性
塑壳
无花斑、破损,流纹,色差,毛边
螺丝
上下盖无松脱现象,螺丝未打紧,打花,漏打
塑壳
无花斑、破损,刮伤,胶水外露,合缝
不可超过0.3MM
贴纸
漏贴,贴错,倒贴,歪斜
LED
灯下陷不可低于塑壳平面,不可破损,
歪斜
DA/DC
DA:PIN针下陷,PIN针错位,卡钩装
反,卡钩无弹性,漏打螺丝,上下盖主
体破损,合缝大,刮伤,PIN氧化.
DC:缩水,不饱模,毛边,流纹,水
刮伤,缩水,胶水外露,合缝不可超过
0.3MM
贴纸
漏贴,贴错,倒贴,歪斜
LED
灯下陷不可低于塑壳平面,不可破损,
歪斜
DA/DC
DA:PIN针下陷,PIN针错位,卡钩装
OQC出货检验规范
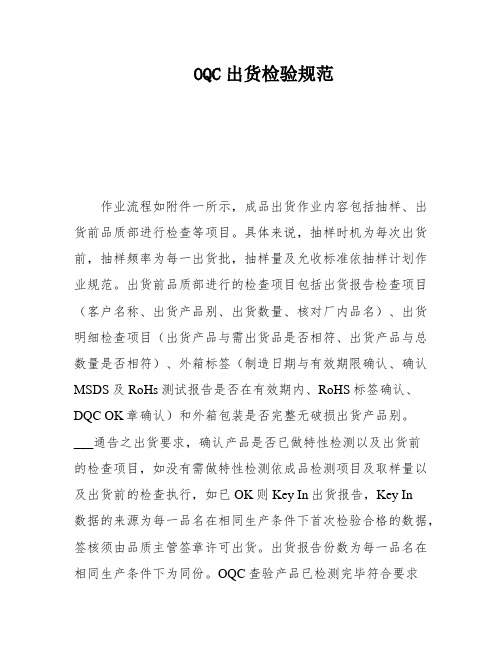
OQC出货检验规范
作业流程如附件一所示,成品出货作业内容包括抽样、出货前品质部进行检查等项目。
具体来说,抽样时机为每次出货前,抽样频率为每一出货批,抽样量及允收标准依抽样计划作业规范。
出货前品质部进行的检查项目包括出货报告检查项目(客户名称、出货产品别、出货数量、核对厂内品名)、出货明细检查项目(出货产品与需出货品是否相符、出货产品与总数量是否相符)、外箱标签(制造日期与有效期限确认、确认MSDS及RoHs测试报告是否在有效期内、RoHS标签确认、DQC OK章确认)和外箱包装是否完整无破损出货产品别。
___通告之出货要求,确认产品是否已做特性检测以及出货前
的检查项目,如没有需做特性检测依成品检测项目及取样量以及出货前的检查执行,如已OK则Key In出货报告,Key In
数据的来源为每一品名在相同生产条件下首次检验合格的数据,签核须由品质主管签章许可出货。
出货报告份数为每一品名在相同生产条件下为同份。
OQC查验产品已检测完毕符合要求
时,因客户紧急需求,但出货报告未制作完成时,有品质主管确认方可出货报告后补给营业,由营业自行传真给客户。
针对成品超过保存期限尚有出货需求者,需要进行成品过期再检出货。
QA成品出货检验作业规范
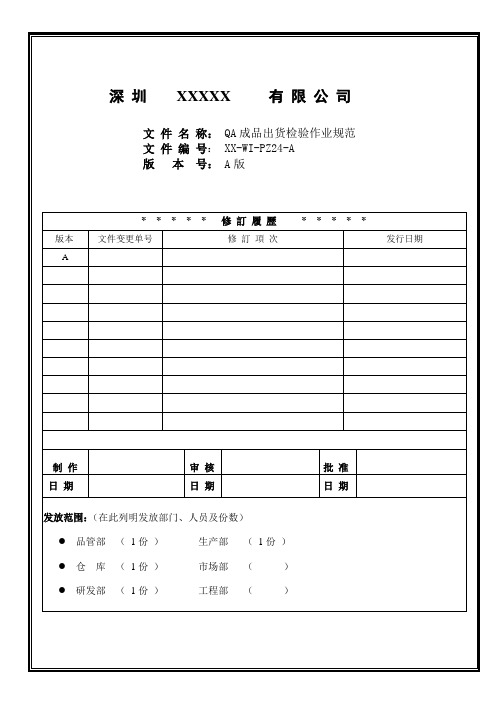
QA成品出货检验作业规范文件类型三阶文件
第 1 页共 4 页
一.目的
明确QA成品出货检验流程及品质判定标准,保证产品出货质量,确保客户满意。
二.范围
适用于本公司各类型产成品之成品出货检验作业,若本标准与客户标准相抵触时,则依双方约定为准。
三.参考文件:
《QA成品品质检验项目及判定标准》、《产品条形码编码规则》、《系统软硬件配置表》、产品资料及调试说明、《技术更改通知》、《特采作业办法》、《产品流程单》等。
四.承认样品
对于文字难以叙述清楚或不易判定合格与否的外观缺点,则以样品、图纸及说明图片作为检验时判定的依据。
五.作业程序
1.仓库送检
1.1成品每批次出货前财务部仓库必需开出《出库单》连同该批产品对应之《产品流程单》和
产品一起报送品管部QA检验。
1.2对于急需出货的物料,仓库必须在送检单上标注“急用”字样,并标明出货具体时间。
2.QA抽样检验
2.1 QA接到送检单后,按送检单所述到生产部抽取检验样本至检验台实施检验。
2.2抽样前先确认所抽物料规格型号要与送检单一致,对不符合送检单描述的产品QA可拒绝
检验,并即时反馈仓管确认处理。
2.3抽样计划:(见下表所示)
送检总量正常抽样数量加严抽样数量
5个以下 1 2
5-10 2 4
11-100 4 8
101以上 5 10
当出现以下情况时也可采用加严或全检作业:
技术变更后首次交付;
屡次发生质量问题。
2.4 检验项目:
2.4.1一般包括产品外观、标识、烧录软件、包装及配件的几项或更多内容。
出货检验规范
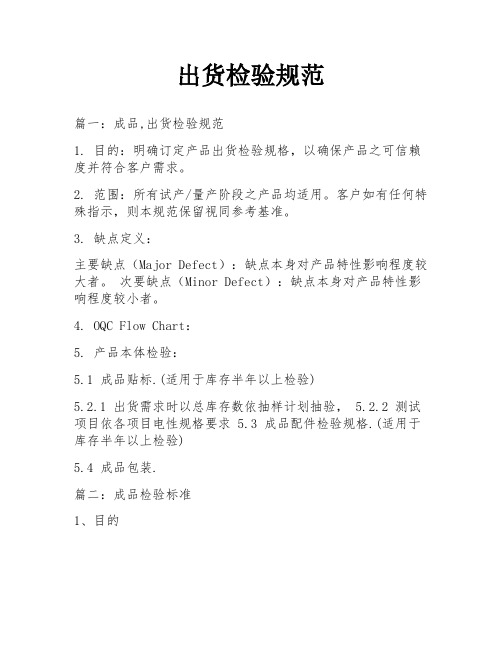
出货检验规范篇一:成品,出货检验规范1. 目的:明确订定产品出货检验规格,以确保产品之可信赖度并符合客户需求。
2. 范围:所有试产/量产阶段之产品均适用。
客户如有任何特殊指示,则本规范保留视同参考基准。
3. 缺点定义:主要缺点(Major Defect):缺点本身对产品特性影响程度较大者。
次要缺点(Minor Defect):缺点本身对产品特性影响程度较小者。
4. OQC Flow Chart:5. 产品本体检验:5.1 成品贴标.(适用于库存半年以上检验)5.2.1 出货需求时以总库存数依抽样计划抽验, 5.2.2 测试项目依各项目电性规格要求 5.3 成品配件检验规格.(适用于库存半年以上检验)5.4 成品包装.篇二:成品检验标准1、目的规范成品入库及出货检验流程,确保出货产品满足客户的需求,不断的提升品质,提高客户的满意度,模拟客户对产品的验证。
2、适用范围适用于所有LED 灯具产品入库及出货检验。
3、定义3.2 检验面的定义A 面:直接看到的区域如:玻璃面,铝基板,LED,透镜面。
B 面:不在直视范围,但暴露在外的面,如:灯具两侧面、散热片、铝型材、外壳,电源等。
C 面:正常使用时看不到的面。
须拆卸的面。
3.3 缺陷代码定义4、检验条件4.1 检验光源:普通日光灯灯源500lux.4.2 检验角度:如图一所示,产品与水平视线成30°,并在检验时±15°旋转产品。
4.3 外观检验距离:未点亮距眼睛30cm±10cm,与眼睛成一条直线,点亮后距离100cm±10cm.4.4 外观检验时间:10s/每个面。
4.5 测试设备:见测试项目内仪器。
5、引用标准5.1 GB/T 2828.1-2003 Ⅱ级按接受质量限(AQL)检索的逐批检验抽样计划。
5.2 AQL 允收质量水平:MIN=1.5 MAJ=0.65 CRI=0(抽样方案主要以0.65 抽取数量)。
出货检验规范[模板]
![出货检验规范[模板]](https://img.taocdn.com/s3/m/35ca6c83b84ae45c3a358ccf.png)
出货检验规范1. 目的通过对生产完成之成品或直接出货之半成品的特性进行检验和测试,以确保产品要求得到满足,防止不良品流出。
2. 概述本规范描述了出货检验抽样要求、检验要求、环境要求、异常处理等内容。
3. 术语4. 内容4.1 抽样计划及允收标准依照【品管抽样检验计划作业规范】执行(客户有明确要求的按客户要求)。
4.2 检验前要求:生产单位将送检之成品整齐放置于“待验区”并填写好《OQC出货检验报告》表头之相关内容,交由OQC人员检验。
4.3 检验作业要求:4.3.1OQC人员依对应的SIP或《通用可靠性作业规范》及【环保检测标准】要求进行半成品或成品检验,逐项检查对每一项检查项目是否与产品标准要求相符合。
a、OQC人员在检验时需核对客户、品名、料号、订单编号、物料编号、材质、送检人、日期、送检批量、抽检批量及检查物料是否有HSF标识,b、检查是否有HSF送检,送检是否合格;产品测试标准参数所要求之检验项目列入OQC检验项目进行检验。
4.3.2所有的检验内容和结果均应记录在《OQC出货检验报告》上,注明不良项目及状况,检验合格则在“检验结果”栏填写“OK”或合格。
4.3.3每天验收成品的品质状况应记录在《OQC检验日报表》上,以便品质追踪统计。
4.3.4检验判定后的处理A、检验结果判定合格,则按原样包装好,并在该批成品的外包装“现品票”上加盖“OQC PASS”印章。
B、“现品票”标签由生产单位填写办理入库手续。
C、检验结果判定为拒收,则在该批成品的外包装箱上贴红票,并开出《品质异常退货通知单》,将不合格品移至“退货区”,通知生产领班/不良品隔离,填写一份《异常处理单》【注:当不良率≥5%,OQC及时填写《OQC出货检验报告》并开出《品质异常处理单》,通知相关部门进行处理,并加以改善,所有经产线返工处理后产品再送检OQC,重新检验合格后方可入库。
】,连同不良样品经品质课长核准后,通知责任单位重新返工处理。
出货检验(OQC) 作业指导书,流程
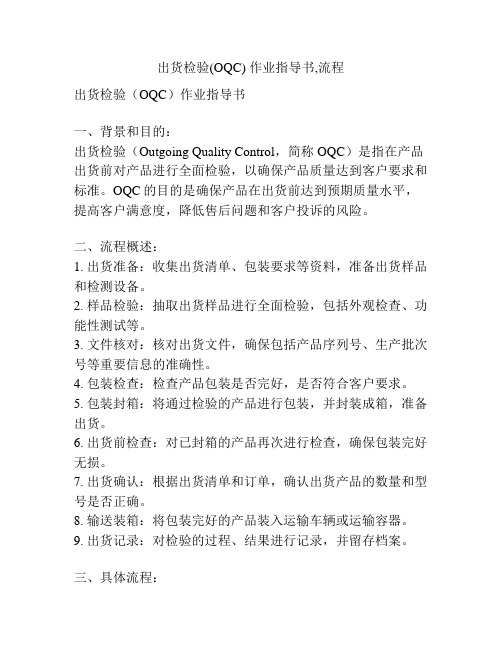
出货检验(OQC) 作业指导书,流程出货检验(OQC)作业指导书一、背景和目的:出货检验(Outgoing Quality Control,简称OQC)是指在产品出货前对产品进行全面检验,以确保产品质量达到客户要求和标准。
OQC的目的是确保产品在出货前达到预期质量水平,提高客户满意度,降低售后问题和客户投诉的风险。
二、流程概述:1. 出货准备:收集出货清单、包装要求等资料,准备出货样品和检测设备。
2. 样品检验:抽取出货样品进行全面检验,包括外观检查、功能性测试等。
3. 文件核对:核对出货文件,确保包括产品序列号、生产批次号等重要信息的准确性。
4. 包装检查:检查产品包装是否完好,是否符合客户要求。
5. 包装封箱:将通过检验的产品进行包装,并封装成箱,准备出货。
6. 出货前检查:对已封箱的产品再次进行检查,确保包装完好无损。
7. 出货确认:根据出货清单和订单,确认出货产品的数量和型号是否正确。
8. 输送装箱:将包装完好的产品装入运输车辆或运输容器。
9. 出货记录:对检验的过程、结果进行记录,并留存档案。
三、具体流程:1. 出货准备:a. 收集出货清单、包装要求等资料,并确认所需检测设备的可用性。
b. 准备出货样品,根据产品类型和规模,确定样品数量。
c. 准备检测设备和工具,确保能满足全面检验的要求。
2. 样品检验:a. 根据抽样标准,从待出货产品中抽取样品。
b. 进行外观检查,包括外包装完好性、产品外观是否无破损等。
c. 进行功能性测试,根据产品特性和标准,测试产品性能和功能是否符合要求。
3. 文件核对:a. 核对产品序列号、生产批次号等信息,确保准确无误。
b. 核对出货文件,包括合格证、检验报告等,确保文件齐全。
4. 包装检查:a. 检查产品包装是否完好,是否符合客户要求。
b. 检查包装材料是否符合防潮、防震、防尘等要求。
5. 包装封箱:a. 将通过检验的产品进行包装,确保包装方式正确无误。
b. 封装成箱,贴上标签,做好箱子标识。
出货检验作业指导书(含表格)
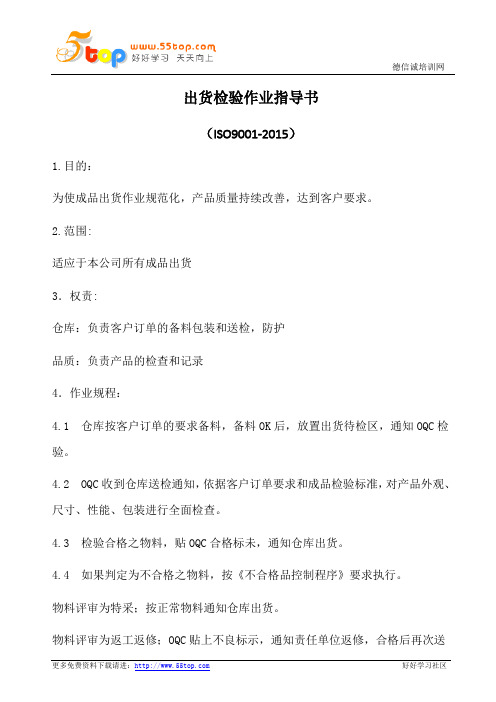
出货检验作业指导书(ISO9001-2015)1.目的:为使成品出货作业规范化,产品质量持续改善,达到客户要求。
2.范围:适应于本公司所有成品出货3.权责:仓库:负责客户订单的备料包装和送检,防护品质:负责产品的检查和记录4.作业规程:4.1 仓库按客户订单的要求备料,备料OK后,放置出货待检区,通知OQC检验。
4.2 OQC收到仓库送检通知,依据客户订单要求和成品检验标准,对产品外观、尺寸、性能、包装进行全面检查。
4.3 检验合格之物料,贴OQC合格标未,通知仓库出货。
4.4 如果判定为不合格之物料,按《不合格品控制程序》要求执行。
物料评审为特采;按正常物料通知仓库出货。
物料评审为返工返修;OQC贴上不良标示,通知责任单位返修,合格后再次送检,最终OK后方可出货。
物料评审为报废,OQC贴上不良标示,由责任单位填写报废申请单,申请报废。
4.5 OQC检验人员将检验结果填写《出货检验报告单》,检验和记录由检验人员按规定期限及方法保存。
4.6 客户要求ROSH环保之物料4.6.1环保物料出货时,OQC需在包装箱上贴环保标示;4.6.2品质部需随货附上客户要求的附带资料,并自留底一份,以备查验;4.6.3当有不符合环保要求的货已交客户时,由业务与客户协商解决,并由品质部会同相关部门,追溯不良原因和提出相应改善对策,并向相关单位及供应商水平展开。
4.6.4环保物料按《环境物质管制程序》执行管制。
5.相关文件:《不合格品控制程序》《环境物质管制程序》6.相关表单:《出货检验报告单》出货检验日报表.xls不合格品处理单不合格品处置单.xls。
出货检验规范

出货检验规范Company Document number:WTUT-WT88Y-W8BBGB-BWYTT-199981、目的:规范出货成品检验,防止不合格产品被出货。
2、范围:适用于本公司所有成品出货前的检验作业。
3、职责生产部/市场部:成品出货前的检验通知。
品管部:成品出货前的检验执行。
物流部/生产车间:成品出货检验工作的配合。
4、作业细则生产部/市场部根据成品出货日期,提前三天通知品管部/物流部/生产车间。
品管部正式验货前1小时,通知成品库/生产车间进行验货准备。
物流部根据通知内容,开据《待验单》将待验成品准备好并挂“待验”标志牌。
品管部针对待验成品,准备相应的资料及样板。
品管部根据制单或客户订单,确定抽样计划,对出货成品品质进行检验。
5、检验内容外观检查:检查产品是否刮花、伤痕、污渍、变形、受损及包装是否美观。
规格检查:检查是否符合制单或订单要求。
特性验证:检验产品的理化及卫生指标是否发生变化。
产品包装和标识检查。
检查产品的包装方式、包装数量、包装材料的使用、单箱数量是否符合要求。
贴纸的粘贴位置、书写内容、外箱填写是否规范正确。
6、不合格的判定品管部QA根据“产品质量检验标准”判定抽检中出现的不合格品数量,若QA无法判定结果,可交品管部主管判定,提出不合格品的处理意见。
7、验货结果的判定与标识品管部QA根据不合格品的确认结果,判定该批产品是否允收。
对允收批产品,通知货仓部入库出货。
对拒收批产品,则挂“待处理”牌,物流部不得擅自移动该批产品。
8、产品的补数和返工、报废QA根据检验结果,确定抽检批产品的允收情况,并书面通知生产部进行补数和返工。
补数:是确认该批产品允收,但生产需按查验出来的不合格数量进行补数。
返工:经确认的不合格品率已超过品质允收(AQL)时,品管部通知生产部安排返工,返工过程的品质控制由生产车间和QC负责,返工完成后,生产车间须通知QA到场重检,直到合格为止。
报废:QA对存在的严重不合格产品确认报废,由品管部填写报废单,注明报废原因,交生产部审批,生产部负责查清报废原因。
出货检验作业规范

版本
更改类型
生效日期
更改内容
会签部门:
品质:工程:
采购:业务:
研发: DCC:
生产 :PMC:
行政:财务:
制作:
审核:
批准:
1、目的
成品出前,检验管制成品质量/HSF物质减免)可符合顾客及法规的要求。
2、适用范围
2.1凡是由本公司制程上所生产之产品均属之。
2.2所有交货至有HSF(无有害物质或有害物质减免)要求之客户的材料均适用。
3、定义
3.1严重缺点:对使用、维修或依赖该产品之个人有发生危险或不安全结果之缺点。
3.2主要缺点:系指严重缺点以外之缺点,其结果或许会导致故障,或实质上减低产品单位之使用性能以致不能达成期望之目标。
3.3次要缺点:系指产品单位之使用性,也许实质上不致减低其期望目的之缺点或虽与已设定之标准有所差异,但在产品单位之使用与操作效用上,并无多大影响。
6、以《检验规范》及《产品承认书》为标准执行产品外观及功能检验,超出标准要求的产品外观异常参照AQL允收水平,功能性异常执行O收1退作业。
7、经检验后发现重大品质异常或抽检不良批超出管制界限3%时,需立即填写《纠正预防措施报告》,交主管确认后,依照不合品控制程序处理。
8、按客户要求对出货产品进行出货抽检及填写《检验报告》,所有要求检验的项目必须在相关的表格中填写检验数据或参数,凡表单上有需要填写具体的检验数值或内容由检测人员签名,并需有组长或主管签名确认;
4、权责:
4.1品质部检验员负责所有成品检验,及依基准承认书﹑成品检验规范及管制计划判定是否合格;当判定有争议时则由品质部经理裁决。
4.2成品质量/HSF问题要求改善时由品管员提出“纠正预防措施报告”;出货品质/HSF问题要求改善时由品管员提出“纠正预防措施报告”,经品质部主管确认后,发往责任单位作对策改善。
[成品出货检验流程]成品出货检验规范
![[成品出货检验流程]成品出货检验规范](https://img.taocdn.com/s3/m/9adeeb2359fb770bf78a6529647d27284b7337c6.png)
[成品出货检验流程]成品出货检验规范1、严把产品出厂质量关,对公司产品质量和客户投诉负责。
2、严格执行《成品检验标准》、《产品包装标准》按生产批次对成品检验和试验。
3、负责客户验货时的接待工作。
4、负责客户(验货员)产品满意度调查,做好品质历史档案。
5、负责对外协采购成品的检验和试验,对外购产品品质负责,做好供方品质档案。
6、负责按《产品包装标准》的单号对每批次出货的产品不重复留样(船样),并做好留样所属业务员及客户标示记录。
7、负责与销售部协调客户验货事宜。
1、高中以上学历,1年以上的相关工作经验。
2、具有一定的沟通、协调等能力,工作细心负责。
3、具备本车间在制品检验的各种技能,熟练运用检验测量器具。
出货检验员岗位描述:根据质量要求,控制出厂产品质量,保证出厂的产品质量能达到规定的要求。
出货检验员工作权限:1、对本职工作有监督权,有对不合格产品禁止通过的权利。
2、对本部门工作有执行权和建议权。
3、对不合格产品(包括外协产品)提出返修权。
4、对不合格产品(包括外协产品)的叫停权。
出货检验员衡量标准:1、计量器具的准确性。
2、对不合格品处理的及时性。
3、客户反馈问题分析、处理的及时性。
4、成品检验的及时性和准确性。
5、品质历史记录的健全性。
总则1.1制定目的为加强产品之品质管理,确保出货品质稳定,特制定本规定。
1.2适用范围凡本公司制造完成之产品,在出货前之品质管制,悉依本规定执行。
1.3权责单位(1)品管部负责本规定制定、修改、废止之起草工作。
(2)总经理负责本规定制定、修改、废止之核准。
检验规定2.1成品入库检验成品入库前,依《最终检验规定》采取逐批检验入库之方式,每一订单之成品可以以一批或数批之方式交验入库。
2.2成品出货检验同一订单(制造命令)之成品入库完成后,在出货之前,应进行成品出货检验。
检验方式如下:(1)由客户派员或客户指定验货机构人员对产品进行出货检验。
(2)客户授权由本公司品管部派员作出检验。
成品出货检验规范

成品出货检验规范1. 0目的为控制本厂所有生产的出货成品的品质最终能完全达到客户之期望值.2.0范围:适用于本厂所有生产之出货成品.3.0 职责3.1装配负责于成品之装配包装.3.2 QA负责于成品的抽样检查.3.3仓库部负责成品之搬运、储存、装柜.4.0检验标准:4.1依据MIL-STD-105E Level II单次抽样计划,AQL值:CR:0 MAJ:1.5 MIN:4.0.4.2依据订单、包装资料以及《成品检验标准》。
5.0 作业程序5.1生产部将包装好的成品摆放于装配部成品区,挂好待检牌,同时填写好“成品入库单”,或先入仓库待检区通知品管部QA员检查。
5.2 QA员接到通知后,根据“入库单”准备齐相关“订单”、“包装资料”、“成品检验标准”于装配部成品区按照MIL-STD-105E Level II单次抽样对成品进行抽取样本检查。
5.3 QA对抽取之样本第一外箱,根据外箱跌落测试规范进行外箱跌落测试.测试之后对其该箱之内外箱及产品进行特别之功能及外观检查.检查后之良品与不良品同此批一同判定,其它物料性测试依据客户要求按相应《测试进行》或客户标准执行。
测试结果记录于“QA Test Report”中。
5.4 QA对其抽成品检查后,合格品按要求正常之装回原箱,不合格品通知装配负责人一同对其进行核对,确认.5.5 QA抽查后,统计其不合格总数,据“AQL允收之标准”对该批成品进行判定;不合格数量不超过“AQL允收标准”时,此批为合格,QA在成品标识单上盖〝 QA PASS〞章,然后QA填写好“成品检验报告”交于主管核实,并于“入库单”上签名,同时与“成品检验报告”复写件交于仓库,通知入库或转移至成品区。
5.6如统计其不合格总数超过其“AQL允收标准”,QA员填写好“成品检验报告”并同不合格样板交品管部主管最终确认.如确认为不合格,QA员填写“品质异常报告书”与不合格样板一同交生产部主管,并在成品标识单上盖“QA Reject”章由生产部对不合格品进行纠正及返工改善,QA对其进行追踪,及对该批纠正之后的产品进行重检并把检验结果记录于“成品检验报告”上。
出货检验规范

出货检验规范出货检验规范建立出货检查控制程序,为确保产品出厂前进行最终检验和测试,判定产品品质符合顾客要求,防止不合格品流出。
一、职责1)品质部负责产品出货前检验的执行与结果记录,负责所有技术要求的相关检验记录。
2)研发工程部负责检验项目及参数值的确定。
3)营销部负责产品出货前的检验通知。
4)仓库负责产品出货检验工作的配合。
5)生产部负责对不合格产品进行返工返修及按需要执行纠正措施。
二、检验控制流程1)产品入库前/出货检验实施:①生产部装配车间完成装配后首先进行内部自检、互检、复检,确认合格后填写《内部报检单》向品质部报检。
(报检单内容应清楚反映:机型、名称、报检数量、装配员工自检签名、复检人员签名、具体报检时间)②品质部接到生产部装配车间《内部报检单》后,首先确认报检的机型、数量与销售部出货通知单相符。
③品质部确定了生产部报检信息与出货信息一致后对出货产品进行检验。
④品质部应重点对机器的结构、功能、系统等按照标准文件设定参数进行测试。
⑤在检验过程中发现不良问题较多而且超过3个低级问题时,检验员无须再检验可以直接向生产部车间主管提出拒检,同时做好不良标识待处理。
⑥品质部拒绝检验已作好不良标识后要及时向生产主管反馈不良信息,由生产部装配主管或生产工艺人员找到异常问题机器的装配者要求立即返工并对机器重新检验,直到自检合检后再次向品质报检。
⑦品质部接到生产部装配车间二次报检后,应重点对返工的部位进行检验,同时按照系统出厂参数设定值进行调试确保合格,最后将检验结果记录于《产品检验报告》中。
⑧二次检验合格下架后,品质部还要根据客户远近评估包装方式并对包装要求进行监控,一定要满足在运输过程中对机器造成损坏因素的预防效果。
⑨最后检查包装所使用的包装是否符合规格要求,是否有破损,出货标贴或警示标识是否醒目等,所有工作完成后方可出货。
⑩最后品质部还得跟装车过程,监督在装车过程中防止造成损坏。
2)库存品出货检验实施:①仓库接到销售部出货通知后通知生产部,要求安排员工将要出货的产品重新提交待检验区,挂上“待检”牌待检,同时并向品质部报检。
出货检验(OQC)-作业指导书-流程
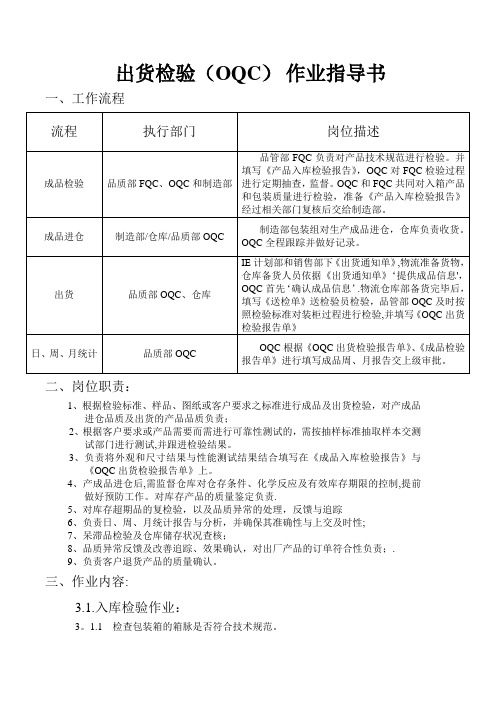
出货检验(OQC)作业指导书一、工作流程二、岗位职责:1、根据检验标准、样品、图纸或客户要求之标准进行成品及出货检验,对产成品进仓品质及出货的产品品质负责;2、根据客户要求或产品需要而需进行可靠性测试的,需按抽样标准抽取样本交测试部门进行测试,并跟进检验结果。
3、负责将外观和尺寸结果与性能测试结果结合填写在《成品入库检验报告》与《OQC出货检验报告单》上。
4、产成品进仓后,需监督仓库对仓存条件、化学反应及有效库存期限的控制,提前做好预防工作。
对库存产品的质量鉴定负责.5、对库存超期品的复检验,以及品质异常的处理,反馈与追踪6、负责日、周、月统计报告与分析,并确保其准确性与上交及时性;7、呆滞品检验及仓库储存状况查核;8、品质异常反馈及改善追踪、效果确认,对出厂产品的订单符合性负责;.9、负责客户退货产品的质量确认。
三、作业内容:3.1.入库检验作业:3。
1.1 检查包装箱的箱脉是否符合技术规范。
3.1.2 检查包装箱及包装质量是否符合技术标准。
3。
1.3 准备并复核《产品入库检验报告》,经过相关部门复核后交给制造部. 3。
1。
4 将检验结果记录于《OQC入库检验记录表》上.3.1。
5 产品检验合格后,在外箱包装箱的箱脉标签旁盖上蓝色“PASS”章。
3。
1。
6 产品经检验为不合格,应先开出《品質异常联络单》,经由各個相关单位确认后,需要重工产品开出产品《重工单》,通知相关单位进行重工处理,不合格品依照《不合格品控制程序》执行.3。
1。
7 制造部包装组对生产成品进仓,仓库负责收货.OQC全程跟踪并做好记录.3。
1。
8 将产品每日的入库数量,入库质量状况交给质量部统计员进行统计。
3.2。
出货检验作业:3。
2。
1根据IE计划部和销售部下达的《出货通知单》,仓库备货人员依据《出货通知单》‘提供成品信息’,OQC首先‘确认成品信息’。
内容如下:A 出货单编号。
B 出厂企业(客户名称)。
C 出厂的箱数。
D 出厂的总panel数量,总功率。
成品出货检验规范

4.1.2對於小批量入庫之產品,先按MIL-STD-105E(II)確定需檢驗之箱數,再於檢驗箱內分散檢驗批抽樣數
4.1.3如客戶有特殊要求者,按客戶要求的方法執行抽樣檢驗.
4.1.4送檢之成品外包裝箱標識需全檢確認(料號、標識、客戶之相關特殊要求及備注標記)
4.4.1.2IPQC依据业务开立的富弘进料验收单,填写好相对应之报表(制程及初件制程检验记录,成品线LOT管理单),交由制造组长,制造课长及其品保课长会签合格后,交由FQC,报表一式两份,一份交由富弘IQC,一份自留底。
4.4.1.3FQC将收集齐的报表与业务开立的进料验收单,备品(针对注塑类产品每次出货须提供5PCS备品,针对wire harness每次出货须提供10PCS备品,针对一端沾锡类产品须提供15PCS样品,其中5PCS为我司沾锡合格之成品,另外5PCS为未沾锡之成品)一起装入PE袋在出货之前交由送货员,由送货员交于富弘IQC。
4.3.6检验完后在《OQC成品检验履历表》上登记OK后,将入库单交由制造组长。
4.3.7制造在确认成品检验合格按入库单上的数量入库。
4.4 出货
4.4.1针对富弘出货之成品:
4.4.1.1业务提前一天开立富弘进料验收单,制造助理打印成品标签,交由制造组长,制造组长将标签交于FQC全检合格后,交由制造组长张贴,FQC依据进料验收单上的规格及数量打印合格标签及免检标签张贴于标签处,并填写相对应之出货检验报告(入库验收单,产品检验记录表,环境物质管控表),交由制造组长,制造课长及其品保课长会签合格,报表一式两份,一份交由富弘IQC,一份自留底。
4.2.1.2主要缺陷(MA):指影響產品效用之缺陷.
出货检验标准规范
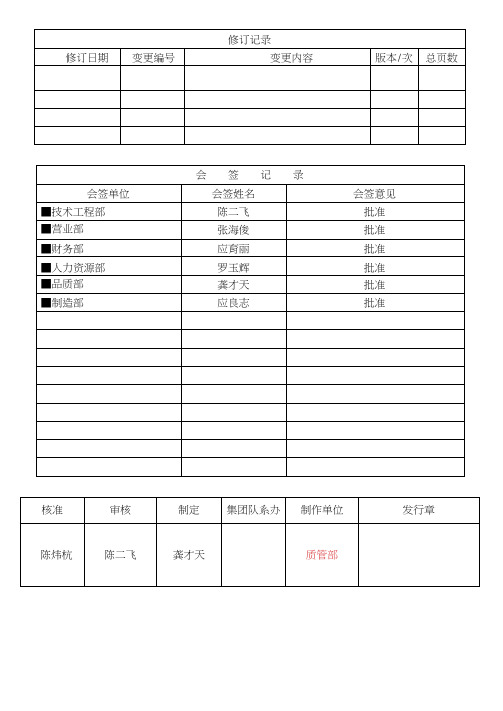
5. 4. 6钢板类检査原那么:
5. 4. 7铝板类检査原那么:
5・5出货检査流程如下:
5. 5.1业务开出?发货告知单?,需提前分发有关单位,仓库依?发货告知单?备货。
OQC 依5. 4项规定进行检査。
5. 5.2当发现异常时,OQC开出?品质异常解决单?,MRB流程作出最后鉴定成果后,OQC将有
关异常状况记录于?品质异常解决单?中发给贵任单位进行解决及改良.不合格品依MRB流程最后鉴定成果,按?不合格品控制程序?进行特采或挑选、重工解决。
由OQC每月对各类别产品进行抽样送实验室进行检测,并
5. 5. 3对环境管制物质测试工
程,对检测成果进行保存.
六.有关文献:
6.1?检査与实验控制程序? HLSG2-Q00020
6. 2?不合格品控制程序?
HLSG2-Q00017
七.有关表单:
7.1?出货检查报告? HLSGQ-QOOOU
7.2?OQC日报表? HLSGQ-Q00006
附件:出货检査流程图如下:。
出货检验管理规范(含表格)
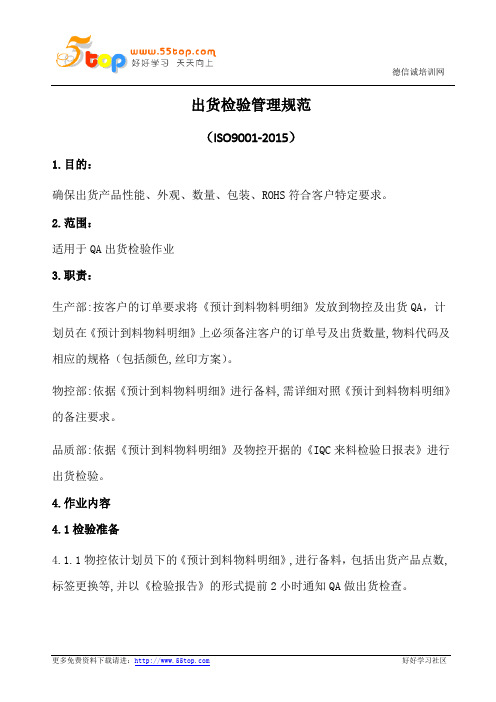
出货检验管理规范(ISO9001-2015)1.目的:确保出货产品性能、外观、数量、包装、ROHS符合客户特定要求。
2.范围:适用于QA出货检验作业3.职责:生产部:按客户的订单要求将《预计到料物料明细》发放到物控及出货QA,计划员在《预计到料物料明细》上必须备注客户的订单号及出货数量,物料代码及相应的规格(包括颜色,丝印方案)。
物控部:依据《预计到料物料明细》进行备料,需详细对照《预计到料物料明细》的备注要求。
品质部:依据《预计到料物料明细》及物控开据的《IQC来料检验日报表》进行出货检验。
4.作业内容4.1检验准备4.1.1物控依计划员下的《预计到料物料明细》,进行备料,包括出货产品点数,标签更换等,并以《检验报告》的形式提前2小时通知QA做出货检查。
4.1.2品质部QA依照物控发放的《出货通知单》、《检验报告》准备检查工作,调出《检查作业指导书》,标准样板/限度样板,规定的检查工具及检验记录表单(如《成品出货检验报告》);4.2检验过程4.2.1QA对照《预计到料物料明细》,依据《AQL抽样标准》《检验作业指导书》《工程图纸》及标准样板/限度样板首先对产品性能、整机适配、尺寸及外观进行检验。
4.2.2QA依据《包装作业指导书》及《预计到料物料明细》对其数量进行抽检,对包装、标示进行全检核对。
4.2.3如果是生产线直接出货的,由生产按照入库通知单,直接送检品质QA,QA检验OK后,加贴合格标签并签名作为生产办理入库和物控出货的依据;4.2.4如果是库存出货,库存时间超过一星期的成品一定按照常规填写《IQC来料检验日报表》送QA重新检验判定,规定期限内的只需进行标签和物品一致性的核对确认检查,无误后通知物控出货。
4.3检验记录任何形式的出货,均需经过QA检验,检验和测试结果记录在相应的《成品出货检验报告》和《可靠性试验检测报告》上,并作为出货检验结果的证据。
4.4检验结果处理4.4.1QA进行产品性能、尺寸及外观检验合格后,对抽检产品进行封箱,并在封口位贴绿色合格票;在外箱标签下方贴绿色合格票和ROHS票,绿色合格票上必须填写QA姓名及日期才可出货;对于工程变更后生产的产品,需在出货外箱上加贴变更标识,标识方法如“变更后”、“改模后”等,若客户有特殊要求时,依客户要求执行。
- 1、下载文档前请自行甄别文档内容的完整性,平台不提供额外的编辑、内容补充、找答案等附加服务。
- 2、"仅部分预览"的文档,不可在线预览部分如存在完整性等问题,可反馈申请退款(可完整预览的文档不适用该条件!)。
- 3、如文档侵犯您的权益,请联系客服反馈,我们会尽快为您处理(人工客服工作时间:9:00-18:30)。
5.1有外观要求的物料,必须进行外观包装,合格后才能发货。
5.2对发利旧库存物料,利旧更改物料进行外观尺寸的全检,必要时进行试装,试装合格后才能进行发货。
5.3有要求试装的产品要进行试装,合格后才能发货。
5.4 有要求进行性能、功能测试的,必须进行测试,合格后才能发货。
6检验记录
6.1将每个站点检验结果记录于《出货检验日报表》及其他报表。
4.2.2铁甲房(包括内置、外置架空、P型、H型)
4.2.3砼夹层机房
4.2.4美化天线、美化树、通信杆塔
4.2.5户外机柜(包括钣金、型材)
4.3检验数量及范围
4.3.1检验范围
QC对所往每个站点的物料进行确认,主要确认物料的规格型号、外观、数量;
4.3.2检验数量
通用件采取抽检方式;检验比例:
批量(件)
文件编号
版本
2.0
制作部门
品质部
生效日期
2014-1-22
出货检验作业规范
编制
审核
审批
是否需要会签:□ 需会签□不需会签
会签部门
会签人
文件发放范围
分发部门
品质部
分发份数
2
文件变更记录
版本
主要变更内容
编写人/修订人
修订日期
1.目的
对发货前检验工作进行指导,明确检验标准与方法,防止不良品流入工程安装现场。
1
2
3
4
5
6
6.1
6.2
6.3
2-8
9-15
16-25
26-50
51-90
91-150
151-280
281-500
样本(件)
2
3
5813ຫໍສະໝຸດ 203250
1
2
3
4
4.1
4.2
4.3
4.3.1
4.3.2
4.3.2.1专用零件 、隔热板、预制板(配重块)采取全检方式;
4.3.2.2标准件、附件(如螺栓、铆钉、密封胶等)只对物料类型、外观进行抽检,数量由物控及工程领料人员共同核对,QC不作为检验项目;
6.2将出货发现的品质异常记录于《品质异常处理单》,由QC组长负责跟踪及效果验证。
7相关文件
a)HN-QP-8.3-01《不合格品控制程序》
b)HN-QP-8.2-04《制程及最终检验控制程序》
c)相关技术清单图纸
8表格
a)《出货检验日报表》
b)《品质异常处理单》
C)《户外柜出货报告》
d) 其他相关报告
4.4作业流程
4.4.1由物控部备料人员将当天发货的物料放置于指定区域,QC接到通知后对物
进行外观、尺寸确认。
4.4.2QC人员根据图纸清单及产品检验规范对物料进行检验确认,检验合格在产品标牌上贴合格标签,通知物控发货人员准予装车出货。
4.4.3检验不合格,用不合格标签进行标识并第一时间上报,如是备料错误通知物控备料人员重新备料并复检,合格后准予出货,记录在出货日报表上;如是生产、设计或其它不合格问题按《不合格品控制程序》执行。
2.范围
适用于公司发往工程安装现场的所有基站物料、半成品的检验。
3.检验量具
卡尺、卷尺、钢直尺
4.作业细则
1
2
3
4
4.1作业准备工作
每天下午根据计调部门制定的《发货、进场站点信息统计表》,将第二天所需要用到的相应站点图纸、清单、检验规范、客户技术要求等资料进行准备。
4.2产品类型
4.2.1简易机房(包括标准、分段、美化、架空)