涂装车间技术规格及要求
喷涂车间管理规定

喷涂车间管理规定一、引言喷涂车间是一个关键的生产环节,对于保证产品质量、提高生产效率以及保障员工健康和安全至关重要。
为了规范喷涂车间的管理,确保车间运作的顺利进行,制定本管理规定。
二、车间布局与设备要求1. 车间布局:- 喷涂车间应设在通风良好的独立空间,远离易燃易爆物品和其他生产线。
- 车间应具备充足的空间,以容纳喷涂设备、原材料和成品。
- 车间内应设有明确的区域划分,包括原材料存放区、喷涂区和成品存放区。
2. 设备要求:- 喷涂设备应符合国家标准,并定期进行维护和检修,确保其正常运转。
- 车间应配备足够数量和种类的喷涂设备,以满足生产需求。
- 喷涂设备应具备防爆、防火和防静电等安全功能。
- 喷涂设备操作台应设置在合适的高度,以方便操作人员操作。
三、员工培训与安全管理1. 培训要求:- 所有从事喷涂作业的员工应接受专业培训,了解喷涂操作的基本知识和技能。
- 培训内容包括喷涂设备的使用方法、喷涂材料的选择和配比、安全操作规程等。
- 培训应定期进行,并记录培训的时间、内容和参与人员。
2. 安全管理:- 喷涂车间应配备足够数量和种类的个人防护装备,如面具、手套、防护服等。
- 员工在进行喷涂作业前应穿戴好个人防护装备,并接受安全操作指导。
- 车间内应设置明显的安全警示标识,提醒员工注意安全。
- 定期进行车间安全检查,发现问题及时整改,并记录检查结果。
四、环境保护与废物处理1. 环境保护:- 喷涂车间应配备有效的通风设备,以保证室内空气质量。
- 车间内应设立废气处理设备,将产生的废气进行过滤和净化,以减少对环境的污染。
- 喷涂车间应定期进行环境监测,确保环境指标符合相关标准。
2. 废物处理:- 废涂料和废溶剂等废物应分类收集,并采取合适的方式进行处理,以避免对环境造成污染。
- 废涂料和废溶剂的处理应符合国家相关法律法规的要求,并有相应的记录和报告。
五、质量控制与数据记录1. 质量控制:- 车间应建立完善的质量控制体系,包括对原材料、喷涂设备和成品的检查和测试。
涂装技术要求

涂装技术要求涂装技术要求一、起重机的油漆各部件颜色合同签订后由买方确定。
二、钢结构材料的表面预处量及车间底漆严格按下列要求执行:1、磨料:喷丸除锈所采用的磨料规格需符合下列标准之一:IS011124(1-4),IS011125(1-8),IS011126(1-10),IS011127(1-8)。
同时磨料必须干燥、清洁。
2、在喷砂表面处理之前,所有油、脂、水、灰、盐等用适当的方式去除。
3、喷砂处理至Sa2.5级(SIS05 5900或IS08501-1:1988)并达到Rz40-70um的表面粗糙度。
4、表面处理后立即喷涂一度15±3微米的车间底漆:7171sigmaProferral MC-7171无机硅酸锌车间底漆。
三、结构成形后的二次表面处理及油漆配套应严格按下列工艺要求执行:1、在表面处量前应去除所有的油、脂、水、灰、盐等。
2、钢结构之焊缝应光顺、无焊渣、飞溅等,焊接的咬边、气孔应补焊并打磨圆顺。
锐边、锐角应倒边、倒角,钢板(材)缺陷应采用适当的方式修复。
3、对不油漆或镀锌件处应进行适当的保护,以免喷砂破坏。
4、所有因焊接、切割、火工灼伤或机械损伤的部位、锈蚀处及钢板不进行表面预处理及喷涂车间底漆处应采用喷砂清洁处理至Sa2.5级(SIS05 5900或ISO8501-1:1988)并达到规定的表面粗糙度。
5、对于车间底漆完好处进行清洁处理,产生锌盐的部位应采用淡水并用硬板刷刷洗干净,其余部位扫砂处量。
6、被涂覆的表面在涂装前应无尘及其它污物,并且是干燥的表面。
7、镀锌件表面:用清洗剂去除油或脂,用淡水洗去盐或污物。
8、油漆配套体系由制造方提供方案,业主确认。
四、油漆的涂装应严格按照下列要求执行:1、油漆的施工环境:(1)油漆施工不应在雨天、雪天、大雾天、大风及寒冷的天气中进行。
(2)被涂装表面温度应大于等于底材露点3度。
(3)当大气相对湿度大于85%时不应施工。
(4)除产品说明书中特别说明之外,待涂表面的钢板温度应在5℃-45℃的范围内,如超出本范围外,应采用适当的手段后方能施工。
涂装车间技术规格及要求

涂装车间技术规格及要求编制:制作日期:涂装车间技术规格及要求项目内容:1、小型结构件中途线2、大型结构件涂装线3、中大挖整机补漆线(SWE330)4、小挖整机补漆线(SWE130)5、自行葫芦输送系统(SWE330、SWE450)一、小型结构件中涂线(一)、设计依据1、生产任务:承担小型结构件中涂任务2、生产纲领:10000台/年3、生产节拍:10~25分钟/工位4、工件的尺寸以及重量:见附表一5、工作制度以及年时基数:(1)、工作制度:全年工作300天,每天两班制(2)、年时基数:工人年时基数600天,设备年时基数570天6、能源:(1)、动力电:380V 三相50HZ(2)、照明电:220V 单相50HZ7、供水:0.2~0.3MPa8、压缩空气:0.4~0.7MPa9、环境温度:-10℃~45℃10、涂装线布局:见附图11.运输方式:轨道加工艺车运输。
(二)、生产工艺流程(三)、中涂烘干室技术说明:因结构件的热容量大,烘干室温度应设计在60~120℃,为保证热效率高,运行成本低的原则,采用封闭式烘干结构,前后门为对开门,热风循环加热方式。
主要有室体、热风循环加热系统、废气处理系统以及电控系统等部分组成。
1、室体:采用钢结构骨架和彩钢保温板拼装制作,底部也需保温,材料为保温岩面,其厚度为100mm,壁板接缝处涂耐高温密封胶。
2、循环风管:采用1.5mm厚镀锌板制作,烘干室应设有废气处理和再利用装置。
3、加热系统:采用四元体燃气热风炉,带废气处理装置。
为保证循环空气的清洁度,热风循环系统中设有高温过滤装置。
燃烧机采用进口设备,保证加热设备的工作可靠性。
(四)、喷漆室技术要求:采用水旋式喷漆室结构,其结构由室体、送风系统、排风系统、水旋器装置、循环水系统以及电气控制系统组成。
1、室体:采用钢结构骨架以及EPS板拼装结构。
室体上部分为静压室,下部分为镀锌格栅板及水盆和水旋器装置。
静压室在室体顶部,有稳定气流的作用,使整个静压室到底部格栅板之间形成稳定的压差,保证漆雾最大量的被气流带走。
供应商涂装作业操作规范及质量标准
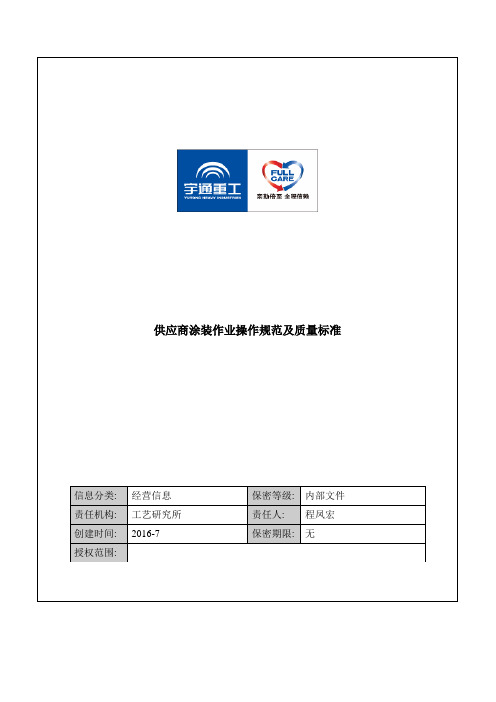
供应商涂装作业操作规范及质量标准信息分类: 经营信息保密等级: 内部文件责任机构: 工艺研究所责任人: 程凤宏创建时间: 2016-7 保密期限: 无授权范围:供应商涂装作业操作规范及质量标准一、目的指导供应商涂装操作,明确各工序质量标准。
二、使用范围为公司供应各类带涂装工件的供应商。
三、涂装操作规范及质量标准1、涂装施工条件的要求1.1、涂装前零部件要进行除锈处理,铸件及主体板厚≥5 mm厚的结构件可采用抛丸或喷砂处理;主体板厚2 mm ~4 mm的结构件进行喷砂处理;主体板厚<2 mm 的薄板件可采用酸洗或手工除锈。
1.2、涂装施工应在清洁、干燥、空气流通、光线充足的地方进行。
环境温度应保持在10 ℃~30 ℃,环境温度比钢材露点温度至少高3 ℃,相对湿度不大于75%,如在大于该湿度施工时,应采取防潮措施。
1.3、应保持涂装用具(喷枪、漆刷、气绳、盛漆桶等)的清洁。
1.4、喷涂用压缩空气应保持清洁干燥,在喷漆设备的管路中,应装有储气罐和油水分离器。
喷漆工在使用过程中,注意经常放水。
1.5、零部件前处理经检查合格后,方可进行底漆的喷涂。
2、前处理工序(抛丸、喷丸等)2.1、转涂装车间工件的要求2.1.1、铸件、锻件的需涂漆表面应平整,没有明显的突起、毛刺、锐边、砂眼。
2.1.2、焊接结构件转油漆时,其表面不允许有焊渣、飞溅、药皮、焊瘤及机械加工残存的飞边、毛刺、铁屑等。
2.2、工装保护在喷丸或抛丸前,要对工件部分部位进行保护,避免造成损伤,影响装配。
2.2.1 、工装保护部位主要有螺纹孔、镗孔、精加工面及设计要求需保护的部位。
2.2.2 、一般对于加工面、镗孔及通孔粗糙度小于等于12.5,喷丸(喷砂)前需保护,保护的目的是:防止将螺纹、镗面和其它需保护的加工面打坏,同时避免丸粒(砂粒)进入不易清理的部位。
保护工装主要使用:螺栓、螺母、橡胶皮子及部分特制保护工装,对于较长的螺纹孔,应从两边同时上螺栓或橡胶塞子。
部件涂装生产线技术要求(涂装)
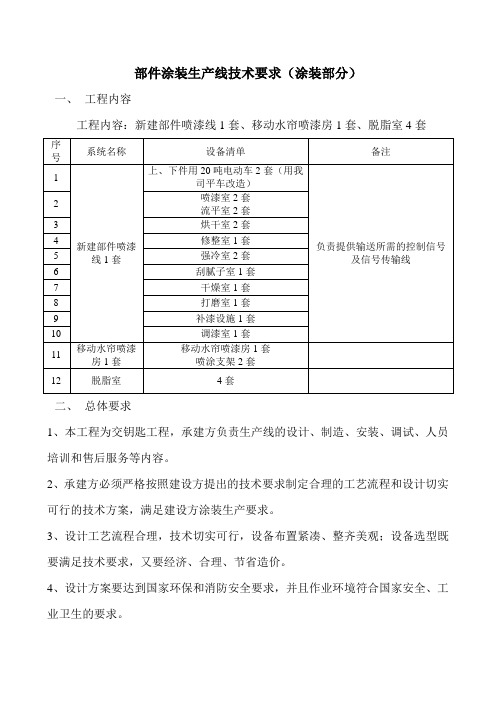
部件涂装生产线技术要求(涂装部分)一、工程内容工程内容:新建部件喷漆线1套、移动水帘喷漆房1套、脱脂室4套二、总体要求1、本工程为交钥匙工程,承建方负责生产线的设计、制造、安装、调试、人员培训和售后服务等内容。
2、承建方必须严格按照建设方提出的技术要求制定合理的工艺流程和设计切实可行的技术方案,满足建设方涂装生产要求。
3、设计工艺流程合理,技术切实可行,设备布置紧凑、整齐美观;设备选型既要满足技术要求,又要经济、合理、节省造价。
4、设计方案要达到国家环保和消防安全要求,并且作业环境符合国家安全、工业卫生的要求。
5、设计应充分考虑设备维修、维护的方便快捷。
6、电气系统采用集中控制,尽量靠近供电系统,自动化程度较高。
7、设计应考虑物料存储区域、转运方式。
8、设计及制造所选用的材料均不得含有硅酮成分。
三、涂装生产线基本生产纲领1、生产纲领:年产量:1200台∕年,40挂∕台2、产品基本参数:最大工件外形尺寸:L×W×H:4500×1800×1700㎜最大工件重量:6000㎏3、工作制度和年时基数:全年工作日:250天工作班制:两班制班工作时制:10小时设备开动率:90%以上4、厂房条件:L×W:60×24m,下弦9.0m5、能源条件及要求:车间电源:380V∕220V,50Hz加热采用电加热(能源为电能)气源、水源要求,乙方在设计图中明确提出。
四、工艺说明1、工艺流程2、输送方式:自行葫芦输送生产节拍:6.5min∕挂3、工艺参数:五、设备说明:品目一、上、下件用20吨电动车(数量:2套)设备说明:由我司废弃平车改造制作。
利用我司20吨平车由乙方改造成20吨电动平车,具体要求如下:品目二、喷漆、流平室(数量:各2套)1、工艺目的:为喷涂作业提供一个良好的涂覆场所和舒适的作业环境,提高涂层质量。
2、工艺设备:2.1喷漆室为水旋式喷漆室,由室体、三维小车、送风装置、地板格栅、排风装置、照明装置、漆雾处理装置、水槽、管路、远程可视系统等部分组成。
涂装生产线的技术要求
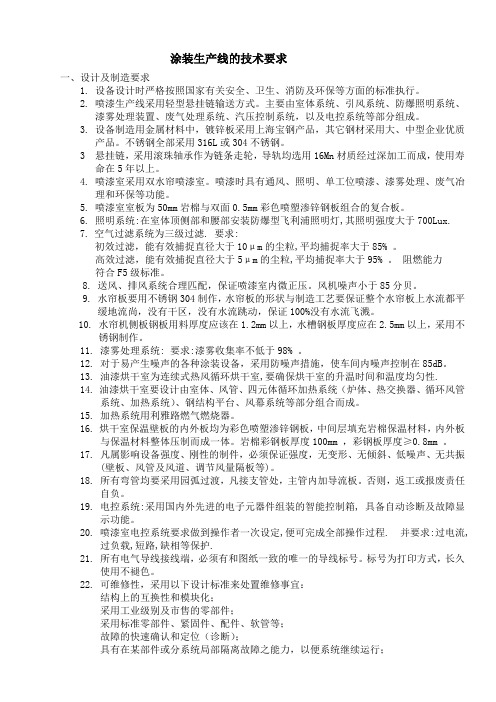
涂装生产线的技术要求一、设计及制造要求1. 设备设计时严格按照国家有关安全、卫生、消防及环保等方面的标准执行。
2. 喷漆生产线采用轻型悬挂链输送方式。
主要由室体系统、引风系统、防爆照明系统、漆雾处理装置、废气处理系统、汽压控制系统,以及电控系统等部分组成。
3. 设备制造用金属材料中,镀锌板采用上海宝钢产品,其它钢材采用大、中型企业优质产品。
不锈钢全部采用316L或304不锈钢。
3 悬挂链,采用滚珠轴承作为链条走轮,导轨均选用16Mn材质经过深加工而成,使用寿命在5年以上。
4. 喷漆室采用双水帘喷漆室。
喷漆时具有通风、照明、单工位喷漆、漆雾处理、废气冶理和环保等功能。
5. 喷漆室室板为50mm岩棉与双面0.5mm彩色喷塑渗锌钢板组合的复合板。
6. 照明系统:在室体顶侧部和腰部安装防爆型飞利浦照明灯,其照明强度大于700Lux.7.空气过滤系统为三级过滤. 要求:初效过滤,能有效捕捉直径大于10μm的尘粒,平均捕捉率大于85% 。
高效过滤,能有效捕捉直径大于5μm的尘粒,平均捕捉率大于95% 。
阻燃能力符合F5级标准。
8. 送风、排风系统合理匹配,保证喷漆室内微正压。
风机噪声小于85分贝。
9. 水帘板要用不锈钢304制作,水帘板的形状与制造工艺要保证整个水帘板上水流都平缓地流尚,没有干区,没有水流跳动,保证100%没有水流飞溅。
10. 水帘机侧板钢板用料厚度应该在1.2mm以上,水槽钢板厚度应在2.5mm以上,采用不锈钢制作。
11. 漆雾处理系统: 要求:漆雾收集率不低于98% 。
12. 对于易产生噪声的各种涂装设备,采用防噪声措施,使车间内噪声控制在85dB。
13. 油漆烘干室为连续式热风循环烘干室,要确保烘干室的升温时间和温度均匀性.14.油漆烘干室要设计由室体、风管、四元体循环加热系统(炉体、热交换器、循环风管系统、加热系统)、钢结构平台、风幕系统等部分组合而成。
15. 加热系统用利雅路燃气燃烧器。
涂装线技术说明书

安徽东宝汽车制造有限公司汽车涂装生产线技术说明书涂装设备有限公司二零零三年七月文件内容:一:涂装车间的主要参数-------------------------------- 3 二:设计原则----------------------------------------------- 7 三:工艺过程----------------------------------------------- 9 四:技术说明----------------------------------------------- 14 五:涂装车间的主要设备明细-------------------- ----- 29 六:附:工艺设备平面布置图一份-------------------- 31一:涂装车间主要参数1.年生产纲领:面包车1万辆/ 年2.年工作日下:251 天2.2工作制度:单班制2.3.年总工时:1970小时(根据部标JBJ/T2-2000,单班年总工时为1970小时;双班年总工时为3820小时;三班年总工时为5250小时)2.4.设备工作时间:按1970小时计算2.5.日均产量:40辆/ 天(小时产量为5台/小时)2.6.生产节拍:约,12分钟/ 台设备利用率:0.85 %返修率15 %等于0.75台/小时,通过修补线3.产品外形尺寸:3765×1575×1780毫米4.产品重量:400 kg (为设计值)5.产品涂装面积:电泳60 平方米PVC 8 平方米中涂内12平方米,外20平方米面漆内12平方米,外20平方米6.厂房:跨度18米×3跨长度132米宽度54米粱下弦净高9米另加辅跨利用于涂装车间7.能源:7.1 电力: 10,000V ±10% 联系50HZ 三相电力:(装机) 380V KW7.2 天然气: 热值10,000 kCal/kg7.3 蒸汽: 0.4 Mpa t/h7.4 压缩空气0.6 Mpa m3/h压缩空气0.3 Mpa m3/h7.5 工业水0.2±0.05 Mpa m3/h 8.工件节距:前处理电泳 5.8 m中涂面漆 5.8 m 9.输送速度:前处理电泳间歇方式8.0min /台前处理电泳烘干连续方式 1.0 m/m in 10.涂层标准10.1 前处理线1) 磷化膜为Zn/Mn/Ni成份。
涂装车间技术方案

技术方案项目单位:xx—喷涂车间涂装线喷涂车间涂装线方案描述一项目整体设计原则涂装生产线方案的设计充分考虑到技术的先进性,充分满足喷涂产品的质量、产能要求,确保工艺及各项技术参数的实现,并力求实用、安全、可靠,可以有效控制及提高产品涂装质量。
涂装生产线上凡自制设备在结构设计上,尽量采用通用件和标准件,以提高自动化程度;涂装生产线的总体布置设计,充分考虑工艺流程系统的合理性,设备布置协调、整齐、美观,便于操作、维修。
在满足各项技术要求的基础上,尽量减少一次性投资成本;并尽可能降低涂装生产线的能耗。
1.1 根据既定的车间面积,使产能最大、质量最佳化。
1。
2 设备是全新设备(包括所有零部件、元器件和各种附件)。
1。
3 工件经过抛丸处理后,表面抛丸质量为Sa2。
5级、粗糙度为Rz=25~40。
1.4 喷漆在喷漆室进行,喷漆室采用水旋式漆雾净化装置净化漆雾,喷漆室采用上送风、下抽风的气流组织形式,保证喷漆室内各处的气流成均匀层流状态,各室体内的送、排风电器带变频功能,可以用于调整室体内的气压平衡.1。
5 烘干室采用燃气四元体间接加热,烘干室采用直通式结构。
1.6 喷漆室废气通过水旋漆雾净化后直接高空排放;烘干室废气通过四元体处理后高空排放.1.7 所有室体两端设电动对开门,供工件出入;室体两侧面各开有两扇安全作业门,供操作工人出入及设备人员检修。
电动门与输送系统连锁自动开关。
1。
8 设备外观颜色,符合甲方指定颜色的要求、或在验收前涂装成甲方指定颜色。
1。
9 室体骨架与输送骨架必须使用同一骨架系统,所有骨架材料均做防锈处理,骨架之间采用焊接或螺栓连接。
二设计依据2.1. 设备用途工件的喷涂,烘干等处理.2。
3。
工件涂装前表面质量抛丸后达Sa2。
5~3.0级,粗糙度Rz=25~45 2。
4. 输送方式葫芦+地面台车2.5。
涂装材料溶剂型油漆2.6。
涂装部位工件外表面2.7. 固化条件30min/80~100℃2。
- 1、下载文档前请自行甄别文档内容的完整性,平台不提供额外的编辑、内容补充、找答案等附加服务。
- 2、"仅部分预览"的文档,不可在线预览部分如存在完整性等问题,可反馈申请退款(可完整预览的文档不适用该条件!)。
- 3、如文档侵犯您的权益,请联系客服反馈,我们会尽快为您处理(人工客服工作时间:9:00-18:30)。
涂装车间技术规格及要求编制:制作日期:涂装车间技术规格及要求项目内容:1、小型结构件中途线2、大型结构件涂装线3、中大挖整机补漆线(SWE330)4、小挖整机补漆线(SWE130)5、自行葫芦输送系统(SWE330、SWE450)一、小型结构件中涂线(一)、设计依据1、生产任务:承担小型结构件中涂任务2、生产纲领:10000台/年3、生产节拍:10~25分钟/工位4、工件的尺寸以及重量:见附表一5、工作制度以及年时基数:(1)、工作制度:全年工作300天,每天两班制(2)、年时基数:工人年时基数600天,设备年时基数570天6、能源:(1)、动力电:380V 三相 50HZ(2)、照明电:220V 单相 50HZ7、供水:~8、压缩空气:~9、环境温度:-10℃~45℃10、涂装线布局:见附图11.运输方式:轨道加工艺车运输。
(二)、生产工艺流程(三)、中涂烘干室技术说明:因结构件的热容量大,烘干室温度应设计在60~120℃,为保证热效率高,运行成本低的原则,采用封闭式烘干结构,前后门为对开门,热风循环加热方式。
主要有室体、热风循环加热系统、废气处理系统以及电控系统等部分组成。
1、室体:采用钢结构骨架和彩钢保温板拼装制作,底部也需保温,材料为保温岩面,其厚度为100mm,壁板接缝处涂耐高温密封胶。
2、循环风管:采用1.5mm厚镀锌板制作,烘干室应设有废气处理和再利用装置。
3、加热系统:采用四元体燃气热风炉,带废气处理装置。
为保证循环空气的清洁度,热风循环系统中设有高温过滤装置。
燃烧机采用进口设备,保证加热设备的工作可靠性。
(四)、喷漆室技术要求:采用水旋式喷漆室结构,其结构由室体、送风系统、排风系统、水旋器装置、循环水系统以及电气控制系统组成。
1、室体:采用钢结构骨架以及EPS板拼装结构。
室体上部分为静压室,下部分为镀锌格栅板及水盆和水旋器装置。
静压室在室体顶部,有稳定气流的作用,使整个静压室到底部格栅板之间形成稳定的压差,保证漆雾最大量的被气流带走。
喷漆室内设计成微负压状态,喷漆室两侧有采光玻璃和照明灯箱以及供人进出的检修门,其中检修门为外开结构,玻璃采用钢化玻璃,室内的光照强度不小于500Lux,照明灯箱设计为组控制方式,采用挂壁式日光灯箱,灯具采用飞利浦产品。
2、送风系统:该系统是向喷漆室提供符合工艺要求的新鲜空气的设备,每个喷漆室两台送风机组,机组的功能段包括进风段、初效过滤段、风机段、均流段、出风段等。
空调机组壁板采用插接式结构,过滤、风机段应设有检修门,正压段的检修门为内开,负压段的检修门为外开,壁板接缝处涂密封胶,确保机组漏风率不大于%。
送风机组采用双吸风外转子低噪音空调专用风机。
送风管道全采用杜锌版咬口制作,机组出风口设置手动风量调节阀,进气采用车间外新鲜空气,送风机组的风量应满足~0.5m/s的要求。
3、排风装置:排风装置由离心风机、电动防火阀、水气分离器、排风管道等部分组成。
风机排风量应满足喷漆室内水旋器的风速与室内微负压得要求。
排风管道采用1.2mm镀锌板制作,分管法兰与螺栓要镀锌处理。
排风管总高不小于15m,且要高出厂房屋顶2m。
4、水循环系统:由循环水泵、循环管路、补水装置、漆渣过滤装置、液位控制系统以及排污系统等部分组成。
循环水泵采用直连式卧式泵,效率高,运行可靠,稳定性好。
漆渣过滤网、挡水板、水旋器等安装在水中的部件,采用不锈钢材料制作,防止锈蚀。
液位控制器以及排污系统是为了控制水位,防止水泵空吸。
当水位低于设定水位时,水泵自动保护,通知补水。
5、漆雾吸收装置:该部分由水盆、水旋器等组成。
水和空气按一定比例同时进入水旋器,风速达到20~30m/s,由于水和空气的速度相差很大,水在空气中很好的雾化,与空气中的漆雾充分接触、凝聚,然后以25~30m/s的速度冲向洗涤板,水和漆雾的分子进一步的接触、凝聚。
空气冲击冲击板后突然转向,漆雾被留在水中,从而实现捕捉漆雾的目的。
废渣清除是在水旋喷漆室的循环水槽中进行的,应设有专门的废渣沉淀池。
(五)、流平室流平室由室体、送风系统等部分组成。
1、室体:采用钢结构骨架和EPS板拼装结构,两侧采用钢化玻璃,室体为敞开式。
2、送风系统:该系统是向流平室内提供符合工艺要求的新鲜空气,风速范围在~0.5m/s,出风管根据现场情况合理布置,保证出风洁净度为以上的颗粒去除率达到95%以上。
(六)、腻子打磨室主要由室体、送排风系统、除尘装置、照明系统合电气控制系统等部分组成。
1、室体:采用板框式结构,两侧中部采用钢化玻璃,前后做手推门,壁板采用厚度100mm的夹心板制作,照明灯箱采用外挂防暴结构,灯具采用飞利浦产品,照明度不小于500Lux。
照明采用分组控制,室内地板采用镀锌板格栅,室体外观要求结构先进、美观大方。
2、送风系统:送风系统布置在室体顶部,自然进风,有过滤系统。
3、排风系统:排风系统要求排风管采用厚度不小于1.5mm的镀锌板制作,排风管总高不小于15m,且要求高出厂房屋顶2m。
4、除尘装置:除尘彻底,易于清理,须带反吹装置。
5、简易水循环系统。
(室内开地沟加小循环水池,水泵作为动力。
)(七)、控制系统该中涂线采用分散控制方式,各设备均为独立控制,电源材料选用国内优质品牌,各部分店控设备应有报警装置,且安全、可靠、稳定。
1、喷漆室控制:松排风连锁控制,先送风后排风,启动方式为软启动,循环水泵采用直接启动方式,水泵应设有水位控制保护装置且有过载保护,照明灯箱采用分组控制方式。
送排风机采用变频控制电路,其电机采用普通防爆电机,控制部分为变频电路,变频范围0~10HZ2、烘干室控制:采用天然气加热方式,燃烧机和循环风机采用互相连锁的控制方式,开机时先开风机后开加热器,关机时先关加热器后关风机。
温度自动控制,燃烧机火焰采用位式调节方式,烘干室的循环风机采用软启动方式。
3、控制柜以及外线系统:系统控制柜采用标准GGD柜体结构产品,外表面为静电喷塑形,并配有照明,维修插座及冷却风扇,密封良好,门开关方便。
柜内交流、直流、弱电、强电等布线按图标分色进行,喷漆送风装置内要有照明系统,电压AC36V,柜内控制电压为AC220V,动力电电压为AC380V,动力电缆,照明线及电器元件均采用符合国家标准要求的优质产品。
(八)、涂装设备配置二、大型结构件涂装线(一)、设计依据:1、生产任务:承担中大挖结构件的涂装生产任务2、生产纲领:2500-3000台/年3、生产节拍:8台/天每天两班制4、工件尺寸及重量:见附表一5、工作制度及年时基数:(1)、工作制度:全年工作300天,每天两班制(2)、年时基数:工人年时基数4800小时设备年时基数4560小时6、能源:(1)、动力电: 380V 三相 50HZ(2)、照明电: 220V 单向 50HZ7、压缩空气:~8、环境温度:-10℃~45℃9、涂装线布置:见附图10:运输方式:自行葫芦输送系统、轨道加工艺车运输。
(二)、生产工艺流程(三)、喷砂室主要由室体、回砂系统、除尘系统、电气控制系统等。
1、室体采用钢结构和夹芯板拼装而成,室体下部分为镀锌板格栅。
室体外观要求美观大方。
整个室体要求确保密封,室外无灰尘污染。
2、采用高效沙尘分离器,将砂料及粉尘分离出来,提高喷砂效率减小除尘器负荷,沙尘分离器上设有调节装置,可调节分离出的沙粒的大小,这样可以满足不同磨料进行作业。
3、除尘系统:采用脉冲反吹除尘方式,使得沙尘分离,此方式过滤精度高,过滤阻力小,粉尘排放量小。
4、电控系统采用德国西门子公司的可编程器作控制核心单元,其他电气均采用施耐德等国际知名品牌,提高控制系统的可靠性,在电路设计上充分考虑安全、可靠。
5、室体内部装有飞利浦灯具,确保光照强度400Lux以上。
6、室体内部设有4个工位(四)、清砂室该清砂室主要由室体、回砂系统、除尘系统、吸收式清砂机、照明系统等部分组成。
另设有人工喷砂系统,一罐带两枪。
1、室体:采用发泡塑料夹心板制作喷砂室室体,应有外形美观、保温隔热、密闭消音、防水等特点。
室体下部分为镀锌板格栅。
室体外观要求美观大方。
整个室体要求确保密封,室外无灰尘污染。
2、回砂系统:通过室体底部的回砂装置将砂粒回收,再利用。
3、除尘系统:采用脉冲反吹除尘方式,使得沙尘分离,此方式过滤精度高,过滤阻力小,粉尘排放量小。
4、电控系统采用德国西门子公司的可编程器作控制核心单元,其他电气均采用施耐德等国际知名品牌,提高控制系统的可靠性,在电路设计上充分考虑安全、可靠。
5、室体内部装有飞利浦灯具,确保光照强度400Lux以上。
6、喷砂形式为人工喷砂,工位为4个。
(五)、喷漆室:设备配置要求按小挖中涂线喷漆室要求配置。
(六)、烘干室:设备配置要求按小挖中涂线烘干室要求配置。
(七)、打磨室:主要由室体、送排风系统、除尘装置、电气控制系统等各装置的技术要求可参照小型结构件中涂线中的打磨室配置要求配置,室内除尘达到涂装标准的要求,整个室体要求确保密封良好,室外无灰尘污染。
(八)、流平室:设备配置要求按小挖中涂线烘干室要求配置。
(九)、涂装设备配置三、中大挖整机补漆线(一)、设计依据:1、生产任务:承担中大挖整机的涂装生产任务2、生产纲领:生产总量的15%3、生产节拍:4、工件尺寸:见附表一5、工作制度及年时基数:(1)、工作制度:全年工作300天,每天两班制(2)、年时基数:工人年时基数4800小时设备年时基数4560小时6、能源:(1)、动力电: 380V 三相 50HZ(2)、照明电: 220V 单向 50HZ7、供水:~8、压缩空气:~9、环境温度:-10℃~45℃10、涂装线布置:见附图(二)、生产工艺流程(三)、具体补漆操作以及室体要求1、整机进入待检工位,确定需要修补的位置和修补量后进入整机补漆室体,在同一室体内完成刮灰、打磨、喷漆、烘干的工序。
2、室体要求:(1)、待检工位要求有照明系统,光照强度要求在500Lux以上。
(2)、整机补漆工位室体要求用干式喷漆系统,烘干采用局部烤灯进行局部烘干,有局部抽风系统,照明电控系统。
(七)、中大挖整机补漆线设备配置四、小挖整机补漆线(一)、设计依据:1、生产任务:承担中小挖整机的涂装生产任务2、生产纲领:生产总量的15%3、生产节拍:4、工件尺寸:见附表一5、工作制度及年时基数:(1)、工作制度:全年工作300天,每天两班制(2)、年时基数:工人年时基数4800小时设备年时基数4560小时6、能源:(1)、动力电: 380V 三相 50HZ(2)、照明电: 220V 单向 50HZ7、供水:~8、压缩空气:~9、环境温度:-10℃~45℃10、涂装线布置:见附图(二)、生产工艺流程(三)、具体补漆操作以及室体要求1、整机进入待检工位,确定需要修补的位置和修补量后进入整机补漆室体,在同一室体内完成刮灰、打磨、喷漆、烘干的工序。