模具作业标准
工厂模具维修作业规范标准范本
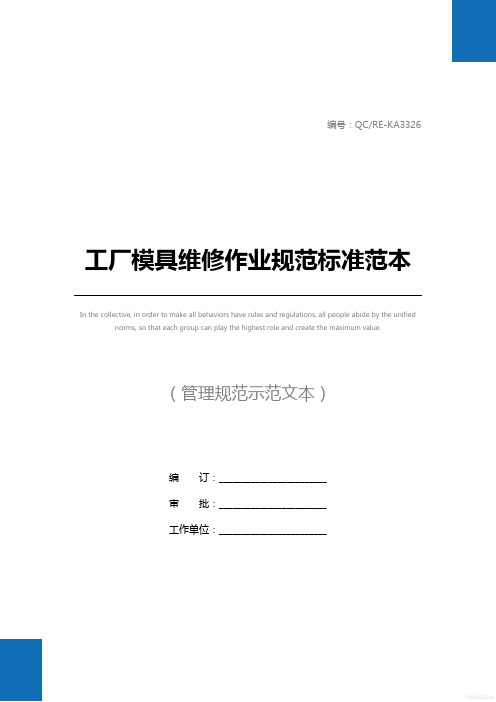
编号:QC/RE-KA3326工厂模具维修作业规范标准范本In the collective, in order to make all behaviors have rules and regulations, all people abide by the unified norms, so that each group can play the highest role and create the maximum value.(管理规范示范文本)编订:________________________审批:________________________工作单位:________________________工厂模具维修作业规范标准范本使用指南:本管理规范文件适合在集体中为使所有行为都有章可偱,所有人都共同遵守统一的规范,最终创造高效公平公开的的环境,使每个小组发挥的作用最高值与创造的价值最大化。
文件可用word 任意修改,可根据自己的情况编辑。
工厂模具维修作业规范目的:为了堤升产能及品质,提高效益,而强化模具管理。
一、各厂商提供给冲压的模具按照模具移交单冲压部指定专职人员对模具定位,脱料状况、外型、模具结构,以及冲制产品是否符合要求等项目进行严格检查。
合格进入模具仓库并随模建立模具档案,对该模具各种使用状况、生产量,维修状况记录在档案卡内。
从而作为对模具考核的重要依据来评估模具质量。
二、模具仓设专人专责管理,对仓库内存放模具都依照合格管理座标定位来摆放各机种模具,并且仓管按需要及时对相关部门提供各种模具状况信息来维护模具良好状态。
三、使用者按照工作单来模具仓领取相应之模具,并在模具档案卡上登记领取人姓名、用途及时间,待模仓管理员确认后予以领出使用。
四、生产课领出模具时应严格按要求选用合适冲床架模具,并严格按照作业指导书调整好模具并达到作业指导书之相关要求,认真做好首检制品后进行生产。
模具部线割作业标准
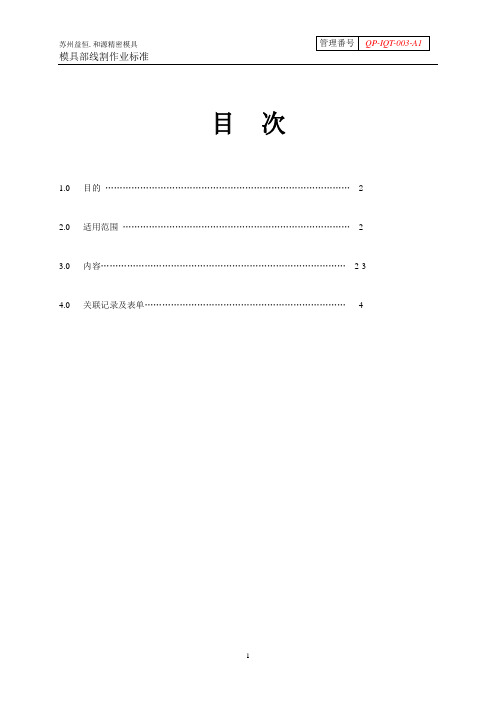
目次1.0 目的 (2)2.0 适用范围 (2)3.0 内容…………………………………………………………………………2-34.0 关联记录及表单 (4)1.0目的为加强管理,提高品质效率,降低不良率2.0适用范围模具部线割加工车间所有技术员3.0内容3.1机台的综合维护与保养3.1.1当班的作业员需保持机台外的整洁,检查上下水盖有无破损3.1.2机台垂直度需有严格保障3.1.3上下机头需定时清洗,给电板按时更换位置3.1.4定时对机台进行保养维护3.1.5机台如有异常需及时反映或上报维修3.2线割加工3.2.1线割加工前需仔细审核图纸,检查图纸与模板是否相等3.2.2线割加工前需确认模板是否平整,有无异物以及模板是否需要细孔放电3.2.3程式制作时应考虑各方面的因素,寻找最佳的线割路径,以保障品质3.2.4确认起割基准,避免线割与CNC之间的基准不同导致的加工误差,方便下一工程作业3.2.5加工过程中需严格要求品质要求,需按照图纸要求加工,应随时检测所要求的间隙3.2.6加工冲头、入块时需检测上、中、下尺寸,应及时清洗、喷防锈油以及入袋标示清楚3.2.7加工完成后,在拆除之前要确认是否有未加工到位,拆下模后应及时对模板除锈上油,应马上清洁机床,把机台所需的工具摆放整齐另请参照线割操作流程(3.4)3.3品质标准及品质要求3.3.1新模制作时应检查其模板的平面度以及直角度,要求:200mm*300mm以内的模板平面度、直角度在0.01mm-0.02mm之间300mm*500mm以上的模板平面度、直角度在0.03mm-0.05mm之间3.3.2冲头、入块加工时应要求:割一刀上中下尺寸在+0.01之内割一修一在+0.008之内割一修二在+0.005之内割一修三在+0.003之内3.3.3间隙配合要求:按现公司的五金件以及其它配件标准间隙配合要求以下为准夹板:a.导柱孔应保证导柱前端部分滑配b.冲头过孔应保证滑配,冲头在孔内不晃动脱板:a.导套孔应保证导套用手能够紧按下去不能过紧或过松b.销钉应保证用手按至模板2/3处c.冲头过孔应保证用手轻按能够很顺畅滑配,不能过紧或过松d.导引针孔应保证手能轻按下去下模板:a.导套孔应保证导套用手能够紧按下去,不能过紧或过松b.入块孔应保证入块能够用手按下去,不能过紧或过松c.销钉应保证用手按至模板2/3处其它间隙要求按图纸要求加工到位3.4线割操作流程图3.4 加工房室内温湿度要求:加工房室内温度范围: 20℃~25℃加工房室内湿度范围: 15~45%RH3.5当线割加工室温度超出要求温度△±1°.应关注设备的运行状况.对加工的产品与正常值产品尺寸进行比较.△±2°应该停止作业.防止设备主板的损害.4.0关联记录及表单《线切割机台加工点检表》《穿孔机点检表》《线割车间室温点检表》。
模具开模前检讨作业标准

6)是否存在影响产品外观面的接合线。
7)成品与成品间的装配公差是否符合模具加工工艺要求。
8)产品的分模线及倒勾的分模线客户是否已接受。
9)须前后模的包R及夹线要求的产品,不否已做夹线处理。
2.2产品注塑成形要求的确认:
2.2.1成形设备的加工参数:
2.3.6模具的倒勾处理的确认:
由于产品中存在倒勾,须进一步向客户询问或建议产品上倒勾采用何种脱模方式,
滑块或斜顶或者更改产品结构作成靠破、插破。
2.3.7模具的温控系统确认:
产品在注塑时,是对模具进行加热还是冷却,加热方式及加热温度,冷却方式
及冷却温度的范围,须在模具试模中用作参考。
2.3.8产品顶出方式及位置的确认:
注意注塑机码模的位置,以便在设计运水出入孔时及布置油缸时参考用。
2.2.4模具命寿(生产总量)的要求:
模具的生产寿命决定了模具材料及模具处理的工艺。
2.3模具设计及制作要求的确认:
2.3.1模穴数的确认:
多数由客户决定,但仍须以模具结构的可行性,产品精度及价格等为考虑因素。
2.3.2模具种类的确认:
1用途:
在模具组立图设计之前,须先与客户初步确认开模事项,藉此将问题反应出来与客户
协商沟通,便于往后模具设计及制作作业的顺利进行。
2作业内容
2.1产品原始信息的确认:
2.1.1产品的成型材料特性:
材料的特性包括:成型塑料的材料,常用缩水率,材料的颜色等.
2.1.2产品的表面工艺要求:
产品的表面要求包括:是镜面,电镀面,晒纹,喷砂面,火花纹,省光等。且每种要求
3)产品是否存在胶位薄弱处造成充填不满。
塑料模具更换安全作业规范

塑料模具更换安全作业规范塑料模具在工业生产中起着至关重要的作用,然而,模具的更换工作却是一项具有一定风险的操作。
为了确保操作人员的人身安全,提高工作效率,保证生产的顺利进行,特制定本塑料模具更换安全作业规范。
一、作业前准备1、技术资料准备在进行模具更换前,操作人员应仔细查阅相关的技术资料,包括模具图纸、操作手册、维护记录等,了解模具的结构、特点、工作原理以及注意事项。
2、工具准备根据模具的类型和更换的需求,准备齐全所需的工具,如扳手、螺丝刀、吊具、千斤顶等,并确保工具的完好性和可用性。
同时,要对电动工具进行检查,确保其绝缘性能良好,电线无破损。
3、安全防护用品准备操作人员必须配备齐全的个人安全防护用品,如安全帽、安全鞋、手套、护目镜等。
4、现场清理在更换模具前,应对工作现场进行清理,清除杂物、油污等,保持工作区域的整洁和畅通。
5、设备停机与断电确保相关设备已停机,并切断电源,挂上“禁止合闸”的警示标志。
二、模具拆卸1、模具吊运使用合适的吊具,如钢丝绳、吊钩等,确保吊运过程中的稳定性和安全性。
在吊运前,要检查吊具的可靠性,严禁使用破损或有缺陷的吊具。
操作人员应站在安全位置,远离吊运区域。
2、拆卸连接件按照顺序,逐步拆卸模具上的连接件,如螺栓、螺母、销钉等。
在拆卸过程中,要注意防止连接件掉落伤人。
对于难以拆卸的连接件,不得强行拆卸,可采用适当的工具或方法进行处理。
3、模具分离在模具分离过程中,要小心操作,避免模具突然掉落或碰撞造成损坏和人员伤害。
如果模具较重,需要多人协同操作,要明确分工,统一指挥。
三、模具搬运1、搬运路径规划提前规划好模具的搬运路径,确保路径畅通无阻,无障碍物和斜坡。
2、搬运方式选择根据模具的重量和尺寸,选择合适的搬运方式,如人工搬运、叉车搬运或行车吊运。
在搬运过程中,要注意保持模具的平衡,避免倾斜和晃动。
3、人员配合如果是多人搬运,要密切配合,听从指挥,步伐一致。
严禁在搬运过程中嬉戏打闹。
(整理)模具尺寸配合公差标注作业标准

加工一般公差
>0~6 ±0.1
>120~350 ±0.5
>6~30 ±0.2
>350~1000 ±0.8
>30~120 ±0.3
>1000 ±1.2
2.12.2.1 在现有图框中新增孔与孔中心距公差及加工一般公差的字段
2.12.2.2 此一公差适用对象:模座加工的逃孔,如RP弹簧、S.P、小拉
杆…等,以及螺丝逃孔。
2.8.1
滑块配合面单边
0 -0.01
mm
2.8.3
镶件沉头厚度
0 -0.02
mm
2.8.5
中子沉头厚度
0 -0.02
mm
2.8.2 镶件配合面单边
0 -0.01
mm
2.8.4 中子直径采g6级配合公差
2.8.6
中子固定方向尺寸
0 -0.02
mm
精品文档
精品文档
2.9 斜顶 2.9.1斜顶 配合公差为 2.9.2斜顶 孔之公差为
mm . mm .
精品文档
精品文档 斜顶 配合公差标示
2.10 EJECTOR BLOCK (顶出块) 2.10.1 顶出块部份为 mm ◦ 2.10.2 镶件部分为 mm ◦
精品文档
精品文档
2.11 靠破
2.11.1
凡靠破面尺寸公差是
+0.01 0
mm
精品文档
精品文档
EJECTOR BLOCK 配合公差标示
精品文档 1 用途 1.1 提升制程,缩短工时 1.2 精确控制尺寸 1.3 便于装配 2 作业内容 2.1 组立图 2.1.1 型腔型芯部分±0.01mm 2.1.2 滑块压条±0.01mm
精密五金模具设计作业标准-打凸点

凸點直徑﹥Φ2.0時,沖頭應固定在夾板內
2)向上打凸點,如圖(四)
凸點沖頭直接固定在下模板內
一.目的:
推行作業標准化,降低設計失誤率﹐實現模具設計快速作業。
二.適用范圍:
光寶沖模設計課。
三.內容:
在機箱產品中,經常會遇到用凸點來定位的情況,主要分定位凸點和接觸凸點;下面我們分別介紹兩種凸點的設計方法。
1.定位凸點:
在模具設計時,通常采用沖孔的形式來作,沖頭的高度以沖下材料(0.85~0.9)T為准,防
對于凸點直徑較大,也有一定高度的凸點,為了使凸點外觀完美,
凸點沖頭可直接取產品圖中的凸點內部尺寸,模板孔則以凸點外形尺寸。
為了方便調整凸點尺寸,將凸點沖頭的實際尺寸取值比凸點內部尺寸單邊大0.1mm,模板孔的實際尺寸取值比凸點外部尺寸單邊小0.1mm。
接觸凸點也可分向上及向下兩類:
1)向下打凸點,如圖(三)
材料被沖穿;脫料裝置與抽牙脫料一致。
定位凸點可分向上及向下打凸兩種形式源自1)向上打凸點,如圖(一)
凸點沖頭直接固定在下模板內,上模采用脫料裝置保証順利脫料。
2)向下打凸點,如圖(二)
凸點沖頭固定于脫料板或夾板上,視要求合理選擇固定方式;如無法判斷,請示上級主管。
2.接觸凸點:
對一些直徑較小,高度不高的凸點,設計時可將凸點沖頭與下模孔一致,不放間隙,凸點高度由沖頭球面來控制。
精密五金模具设计作业标准-穿线孔

推行作業標准化,降低設計錯誤率﹐實現模具設計快速作業。
二.適用范圍
光寶沖模設計課。三.穿Fra bibliotek孔位置及尺寸要求
對于精度要求較高﹐考慮到需要使用線割加工的內孔﹐設計者必須參照以下原則畫出穿線孔(直徑Φ0.5mm,Φ1.0mm或Φ2.0mm,Φ3.0mm﹐圖層為該模板銑床層)。
1.異形孔大于等于6mm時﹐穿線孔直徑用Φ3.0mm。穿線孔離長邊4~~6mm(如圖A)﹐注意﹕刀口板折模孔穿線孔做在非刀口處離邊4mm,(如圖B)
5.一般圓孔設計者不需畫出穿線孔。
2.異形孔小于或等于6mm大于3mm時﹐穿線孔直徑用Φ1.0mm,穿線孔做中心
(如圖C)。
3.異形孔小于3mm﹐穿線孔直徑用Φ0.5mm(細孔放電),非刀口線割孔作外面離邊4mm或做在孔中心﹐(如圖D)﹐刀口線割孔做在孔中心(如圖C)。
4.共用板(零)件線孔一般做在對產品尺寸無直接影響的板(零)件上﹐例復合模公母模共用時做在公模上。
注塑机模具上下模作业指导书【标准版】
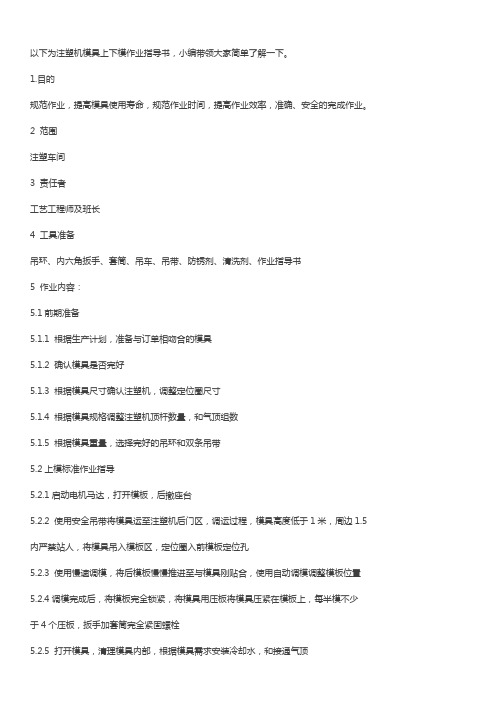
以下为注塑机模具上下模作业指导书,小编带领大家简单了解一下。
1.目的规范作业,提高模具使用寿命,规范作业时间,提高作业效率,准确、安全的完成作业。
2 范围注塑车间3 责任者工艺工程师及班长4 工具准备吊环、内六角扳手、套筒、吊车、吊带、防锈剂、清洗剂、作业指导书5 作业内容:5.1前期准备5.1.1 根据生产计划,准备与订单相吻合的模具5.1.2 确认模具是否完好5.1.3 根据模具尺寸确认注塑机,调整定位圈尺寸5.1.4 根据模具规格调整注塑机顶杆数量,和气顶组数5.1.5 根据模具重量,选择完好的吊环和双条吊带5.2上模标准作业指导5.2.1启动电机马达,打开模板,后撤座台5.2.2 使用安全吊带将模具运至注塑机后门区,调运过程,模具高度低于1米,周边1.5 内严禁站人,将模具吊入模板区,定位圈入前模板定位孔5.2.3 使用慢速调模,将后模板慢慢推进至与模具刚贴合,使用自动调模调整模板位置5.2.4调模完成后,将模板完全锁紧,将模具用压板将模具压紧在模板上,每半模不少于4个压板,扳手加套筒完全紧固螺栓5.2.5 打开模具,清理模具内部,根据模具需求安装冷却水,和接通气顶5.2.6 将工具放回指定位置,准备相应的物料和辅料,调整工艺,开机生产5.3下模标准作业指导书5.3.1 根据订单需求,确认订单已经完成5.3.2 准备相应的吊装、拆卸工具5.3.3 将座台后撤,将料筒物料排空,如生产含腐蚀性材料,使用PP料清洁料筒、螺杆5.3.4 将模具冷却水管拆除,用气将冷却水管道清洁,拆掉气顶管道,清洁模具表面,喷洒防锈剂5.3.5 用低速合模将模具移动至低压锁模区,准备吊车,安装吊环、吊带,慢速上升至吊带绷紧5.3.6 使用专用拆卸工具,拆卸螺栓,取下压板5.3.7 慢速开模,将模具慢速吊出锁模区,低空将模具运至模具存放区,放到指定位置,卸下吊带、吊环,清洁模具表面5.3.8 清理现场工具及卫生,根据生产需求计划调整模具6 记录6.1 根据模具生产实际情况认真填写《上下模记录》、《模具保养清单》、《模具维修申请》扩展资料:上模的步骤:上模全部需要手工进行,下面所有的机械操作应在手动或调模状态下进行,手工操作前应关闭油泵电动机,以确保操作人员的安全。
模具抛光作业标准

模具抛光作业标准1.总则:1.1、抛光表面质量要符合顾客对制品的要求或项目部长的要求。
1.2、抛光作业不得破坏模具表面形状(如棱角、圆角、平面、直线、相切、止口等),型腔口角要保持锋利。
1.3、抛光前检查形状是否加工到位,圆角过渡是否顺滑,表面是否有明显台阶,所有上述形状特征需要钳工负责人修整完毕后才能开始抛光作业,抛光作业人员不得擅自改变零件形状。
1.4、抛光过程中一旦发现模具表面有点蚀、裂痕、焊疤、麻点等问题应立即停止作业,并向生产部和项目部长报告。
1.5、抛光作业现场要保持清洁,精抛工序应在无尘环境进行。
2.注意事项:2.1、用砂纸抛光需要用软的木棒或竹棒,当产品表面呈圆角、圆弧或球面形状时,使用的软木棒的头部形状应该与模具表面形状吻合。
2.2、当换用不同型号的砂纸或油石条时,抛光方向应变换45°~90°,以确保前道磨痕彻底去除。
2.3、在换用不同型号的砂纸前,必须用100%纯棉花沾取酒精一类的清洁液对抛光表面仔细擦拭;从砂纸抛光换成研磨膏抛光时,必须把颗粒和煤油清洁干净才可继续下一道工序抛光。
2.4、使用研磨膏时,双手、手袖必须清洁。
2.5、每道打磨抛光应从困难部位(边、角等部位)开始。
2.6、每道抛光应争取在最短的时间内完成,抛光的力度亦随着表面光洁度增加而减轻。
2.7、最后一道抛光应在产品脱模方向进行。
2.8、清洗表面的研磨剂和润滑剂,喷上防锈剂,粘上保护膜。
3、作业指导:3.1抛光基本流程3.1.1、粗抛,去除刀痕、电火花层,然后采用条状油石加煤油研磨。
3.1.2、半精抛,使用砂纸和煤油。
3.1.3、精抛,用抛光布轮混合钻石研磨膏进行研磨,之后用粘毡和研磨膏手工抛光。
3.2、各级别表面的抛光要求3.2.1、A0级抛光,油石使用顺序为180#-320#-400#-600#;砂纸号数依次为400#-600#-800#-1000#-(1500#);钻石研磨膏依次采用W7、W3.5、W1.5。
注塑模具钳工作业标准
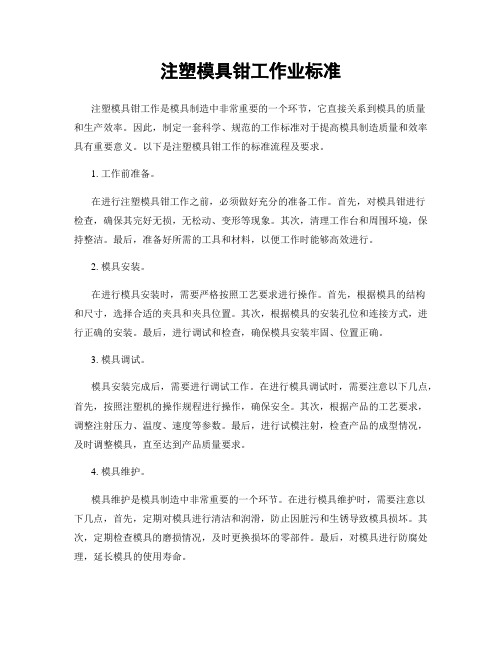
注塑模具钳工作业标准注塑模具钳工作是模具制造中非常重要的一个环节,它直接关系到模具的质量和生产效率。
因此,制定一套科学、规范的工作标准对于提高模具制造质量和效率具有重要意义。
以下是注塑模具钳工作的标准流程及要求。
1. 工作前准备。
在进行注塑模具钳工作之前,必须做好充分的准备工作。
首先,对模具钳进行检查,确保其完好无损,无松动、变形等现象。
其次,清理工作台和周围环境,保持整洁。
最后,准备好所需的工具和材料,以便工作时能够高效进行。
2. 模具安装。
在进行模具安装时,需要严格按照工艺要求进行操作。
首先,根据模具的结构和尺寸,选择合适的夹具和夹具位置。
其次,根据模具的安装孔位和连接方式,进行正确的安装。
最后,进行调试和检查,确保模具安装牢固、位置正确。
3. 模具调试。
模具安装完成后,需要进行调试工作。
在进行模具调试时,需要注意以下几点,首先,按照注塑机的操作规程进行操作,确保安全。
其次,根据产品的工艺要求,调整注射压力、温度、速度等参数。
最后,进行试模注射,检查产品的成型情况,及时调整模具,直至达到产品质量要求。
4. 模具维护。
模具维护是模具制造中非常重要的一个环节。
在进行模具维护时,需要注意以下几点,首先,定期对模具进行清洁和润滑,防止因脏污和生锈导致模具损坏。
其次,定期检查模具的磨损情况,及时更换损坏的零部件。
最后,对模具进行防腐处理,延长模具的使用寿命。
5. 安全操作。
在进行注塑模具钳工作时,必须严格遵守安全操作规程。
首先,必须穿戴好劳动防护用具,如手套、护目镜等。
其次,严禁在机器运行时进行维修和调试操作,确保人身安全。
最后,对操作人员进行安全培训,增强安全意识,降低事故发生的风险。
6. 质量检验。
在注塑模具钳工作完成后,需要进行产品质量检验。
质量检验的内容包括产品尺寸、外观、材料等方面。
检验过程中,需要严格按照质量标准进行操作,确保产品质量符合要求。
总结:注塑模具钳工作是模具制造中至关重要的一个环节,它直接关系到模具的质量和生产效率。
模具标准件加工作业指导书

导套二次加工(磨)
1、下料
2、齐头,内径缩小3-5mm钻孔;
3、外径粗车留1-2余量;
4、内径粗车留1.5-2mm余量;
5、内径半精车留0.6-0.8mm余量;
6、外径半精车留0.5-0.8mm余量;
7、其余尺寸车成,油槽深成,表面粗糙度3.2;
8、表面渗碳1-1.3,淬硬HRC58-62。
b.半精镗留0.2-0.3余量;
c.精镗至尺寸公差要求H7,表面粗糙度1.6;沉孔镗成,深度-0.05。
六、铸CH-1凸模、凹模镶件加工工艺
1、钳工:测量毛坯,分配余量,划四面加工尺寸线成;(基面、靠背面、两拼缝面及废料切刀面)
2、按线找正,先加工基面成,再以基面为准加工靠背面及两拼缝面或废料切刀面成,靠背面、拼缝面均留单面0.5余量;
1、导向端粗磨,留0.2-0.3余量;
2、导向端半精磨,留0.1-0.15余量;
3、导向端精磨至尺寸公差要求H7,表面粗糙度0.4;
4、固定端粗磨留0.1-0.2余量;
5、固定端精磨至尺寸公差要求r6,表面粗糙度0.8;肩抗平1.6。
四、冲孔凸模、凹模的加工工艺
冲孔凸模(车、热、磨)
冲孔凹模(车、磨)
12、热处理:表面淬硬或整体淬硬;
注:需特殊热处理要求的工艺说明(真空淬硬或表面氮化)。
13、钳:形面、形腔、刃口抛光,表面粗糙度达0.8。
八、镶块整体淬火,分组加工工艺
1、元钢下料(下料表);
2、锻坯料(下料表)
3、热量,⊥、∥。粗糙度6.3
5、磨:上下两端面及宽度一端面磨平,⊥、∥、≤0.02/200;
外径固定端粗精磨至尺寸公差要求r6,表面粗糙度0.8,;
模具调试作业规范(上)

目录一:作业流程 (3)1. 拉延模 (3)2. 切边冲孔模(侧冲吊冲) (3)3. 翻边整形模(侧翻) (3)二.作业步骤: (4)1.拉延模 (4)1.1 检查装配作业及修整基准侧。
(4)1.2组装、研配。
(4)研配导向零件。
(5)研配压边圈 (5)研配凹模 (6)1.3型面精抛光 (7)1.4 T1拉延模的调整及判定 (8)功能零件的调整。
(8)开裂及拉薄的情况 (9)起皱及压伤的情况 (10)2切边冲孔模(侧切侧冲模) (11)2.1 检查装配作业并研配基准侧。
(11)2.2 研配导向零件。
(12)2.3研配刃口(正切、侧切刃口)。
(13)2.4 对正冲、侧冲冲头。
(14)2.5 对废料切刀。
(15)2.6研配压料器。
(15)2.7模具型面抛光。
(16)2.8 T1试模检测各功能零件并打工序件。
(17)3.翻边整形模(翻边冲孔模)........................................................................ 错误!未定义书签。
3.1检查装配作业并研配基准侧。
................................................................. 错误!未定义书签。
3.2研配导向零件。
......................................................................................... 错误!未定义书签。
3.3研配翻边镶件。
......................................................................................... 错误!未定义书签。
3.4 研配压料器/浮顶器。
............................................................................... 错误!未定义书签。
模具安全操作规程
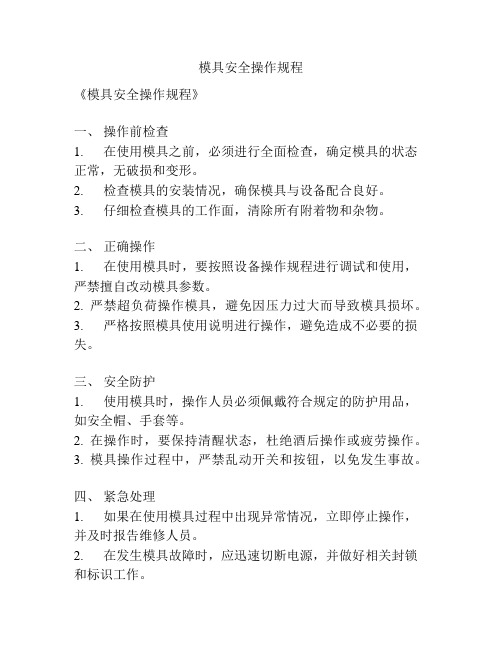
模具安全操作规程
《模具安全操作规程》
一、操作前检查
1. 在使用模具之前,必须进行全面检查,确定模具的状态正常,无破损和变形。
2. 检查模具的安装情况,确保模具与设备配合良好。
3. 仔细检查模具的工作面,清除所有附着物和杂物。
二、正确操作
1. 在使用模具时,要按照设备操作规程进行调试和使用,严禁擅自改动模具参数。
2. 严禁超负荷操作模具,避免因压力过大而导致模具损坏。
3. 严格按照模具使用说明进行操作,避免造成不必要的损失。
三、安全防护
1. 使用模具时,操作人员必须佩戴符合规定的防护用品,如安全帽、手套等。
2. 在操作时,要保持清醒状态,杜绝酒后操作或疲劳操作。
3. 模具操作过程中,严禁乱动开关和按钮,以免发生事故。
四、紧急处理
1. 如果在使用模具过程中出现异常情况,立即停止操作,并及时报告维修人员。
2. 在发生模具故障时,应迅速切断电源,并做好相关封锁和标识工作。
五、巡查维护
1. 定期对模具进行巡查和维护,保持模具的良好状态。
2. 及时清洁模具,保持模具表面整洁,避免附着物影响使用。
六、经常培训
1. 对模具操作人员进行定期培训,提升他们的安全意识和操作技能。
2. 根据实际情况,及时更新模具操作规程,使其符合最新的安全标准。
以上就是模具安全操作规程,希望大家能够牢记并严格执行,确保模具的安全操作,保护自己和他人的生命财产安全。
模具检验作业标准

文件名称模具检验作业标准模具检验作业标准1.目的:通过规定模具检验标准,维护模具使用质量及分辨模具磨损情况,提高产品品质。
2适用范围:本公司的模具检验3.各部门的职责仓管部门:负责模具入库前的品质检查,并针对模具的状态决定相应维修方案,进行返厂或报废处理。
生产部门:负责使用中的模具的品质,根据产品的质量状况对模具进行初步判断,是否缺损,能否继续进行生产,确保产品的质量。
4.模具管理标准工作方法4.1入仓前检查模具长宽高以及尺寸和模深4.2外表是否有缺角,崩裂情形,以及模具表面光洁度。
4.3配模前需测量,每组模具高度,公差在0.05m/m以内。
4.4模具表面缺角、凹陷需更换、重新放电修整。
4.5入仓时要擦拭干净,上防锈油。
5.入仓模具合金厚度等级划分5.1针对现有模具合金厚度不等的情况。
上冲钨钢不等厚,性能标差离散性大,下冲钨钢不等厚,成型脱磁不稳定。
特提出合金厚度等级划分5.2 以JFC140为例子,JFC140的磨损大,更换周期短,更换频繁,在模具紧缺的情况下,为弥补破损模具的漏洞,会将等高的模具出仓使用,合金厚度高矮不一,换下来的140模具首要的进行模具合金厚度等级的划分。
5.3现将JFC140的合金分成ABCD四个等级,对于进仓的模具,首先观察模具合金的厚度,A等级模具合金厚度为新制合金厚度,就是未经过放电处理的合金厚度,B等级的模具合金厚度比A等级的合金厚度矮一点,A等级的模具轻微磨损后放电处理后,厚度变化不大。
C等级合金厚度比B等级合金厚度薄,A等级合金中度磨损后放电处理后应划分为C等级厚度。
D等级合金厚度最低,经过两次放电处理后的合金厚度,或者A 等级合金重度磨损后的厚度,同时模具的反复使用后经过等高处理,合金的高度临近最低冲模高度,应划分成D等级。
合金厚度过低会造成不退磁而发生粘模情况,产品无法正常与模具分离会发生重模也就是二次压制,导致冲模肿大,严重导致冲模破裂,严重影响正常生产。
塑料模具更换安全作业规范
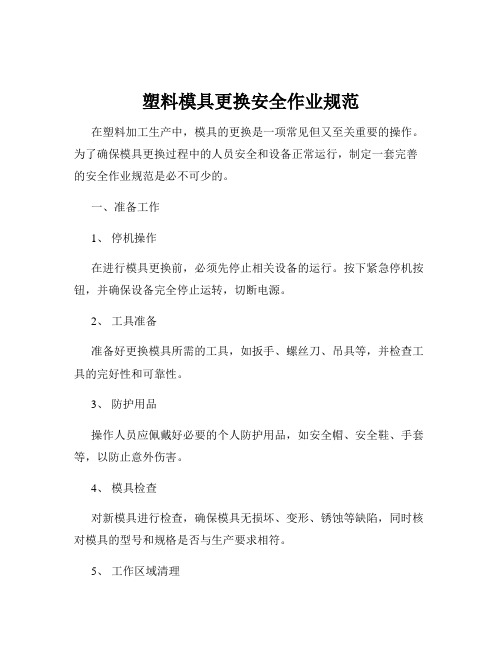
塑料模具更换安全作业规范在塑料加工生产中,模具的更换是一项常见但又至关重要的操作。
为了确保模具更换过程中的人员安全和设备正常运行,制定一套完善的安全作业规范是必不可少的。
一、准备工作1、停机操作在进行模具更换前,必须先停止相关设备的运行。
按下紧急停机按钮,并确保设备完全停止运转,切断电源。
2、工具准备准备好更换模具所需的工具,如扳手、螺丝刀、吊具等,并检查工具的完好性和可靠性。
3、防护用品操作人员应佩戴好必要的个人防护用品,如安全帽、安全鞋、手套等,以防止意外伤害。
4、模具检查对新模具进行检查,确保模具无损坏、变形、锈蚀等缺陷,同时核对模具的型号和规格是否与生产要求相符。
5、工作区域清理清理工作区域内的杂物和障碍物,确保有足够的操作空间。
二、模具拆卸1、拆除连接部件使用合适的工具,小心地拆除模具与设备之间的连接部件,如螺栓、水管、气管等。
在拆卸过程中,应注意防止部件掉落伤人。
2、吊运模具如果模具较重,需要使用吊运设备进行吊运。
在吊运前,要检查吊具的安全性,确保吊具能够承受模具的重量。
操作人员应远离吊运区域,由专人指挥吊运操作。
3、标记和记录在拆卸过程中,对模具的各个部件进行标记和记录,以便在安装时能够正确组装。
三、模具安装1、模具定位将新模具准确地放置在设备的安装位置上,确保模具与设备的安装孔对齐。
2、连接部件安装按照拆卸时的相反顺序,安装模具与设备之间的连接部件。
在紧固螺栓时,要采用对角紧固的方法,确保受力均匀。
3、调试和检查安装完成后,进行模具的调试和检查。
检查模具的开合是否顺畅,各部件之间的配合是否紧密,以及水管、气管等连接是否正常。
四、开机试生产1、人员撤离在开机试生产前,确保所有操作人员都已撤离到安全区域。
2、缓慢启动设备启动时应缓慢进行,观察模具的运行情况,如有异常应立即停机检查。
3、试生产进行试生产,检查产品的质量是否符合要求。
在试生产过程中,要密切关注设备和模具的运行状态,如有问题及时停机处理。
模具管理办法:作业规范与安全防护

模具管理办法:作业规范与安全防护1. 引言模具是工业生产中重要的工具,用于制造各种产品。
为了确保模具的正常使用和维护,提高生产效率,保障员工的安全,制定模具管理办法是必要的。
本文将重点介绍模具管理中的作业规范和安全防护措施。
2. 作业规范2.1 模具存放与保管模具应当有专门的存放区域,并按照标识分类、编号,并定期进行盘点;存放区域应保持干燥、通风和整洁,防止模具受潮、变形或损坏;模具存放时应采取防尘措施,避免灰尘对模具造成损坏。
2.2 模具使用使用模具时,应按照作业指导书和操作规程进行操作,不得随意更改模具的设计或尺寸;在操作过程中,应注意保持模具清洁,避免附着异物或油污;禁止重锤或其他金属工具直接敲击模具,以免造成损坏;使用模具时应避免过度施力或使用不当的工艺,以保证模具的寿命。
2.3 模具修理与维护定期检查模具的使用状态,发现问题及时整理或维修;修理和维护模具应由专业人员进行,并记录维修情况和细节;维修后的模具应经过专门测试和检查,确保其正常使用。
2.4 模具交接与归还模具的交接应由相关人员进行,必须清楚记录交接时间和责任人;使用完毕的模具应及时归还到指定的存放区,并进行盘点。
3. 安全防护3.1 个人防护用品在操作模具时,操作者应佩戴合适的个人防护用品,包括手套、护目镜、耳塞等;根据具体工作环境,可能需要佩戴防护服、防滑鞋等个人保护装备。
3.2 防护设施工作区域应设有明显的警示标识,提醒人们注意模具的存在;应根据模具的大小和重量,配备合适的吊装设备;在模具周围设置防护栏杆或围栏,确保人员不会无意识进入工作区域。
3.3 应急预案制定模具使用过程中的应急预案,包括火灾、漏水、事故等情况;模具使用过程中发生紧急情况时,及时报警并采取相应的救援措施。
4. 总结模具管理办法的制定对于提高生产效率和保障员工安全至关重要。
通过严格的作业规范,可以确保模具的正常使用和维护;安全防护措施可以有效地降低事故的发生概率。
模具装卸维修安全作业操作规程(3篇)
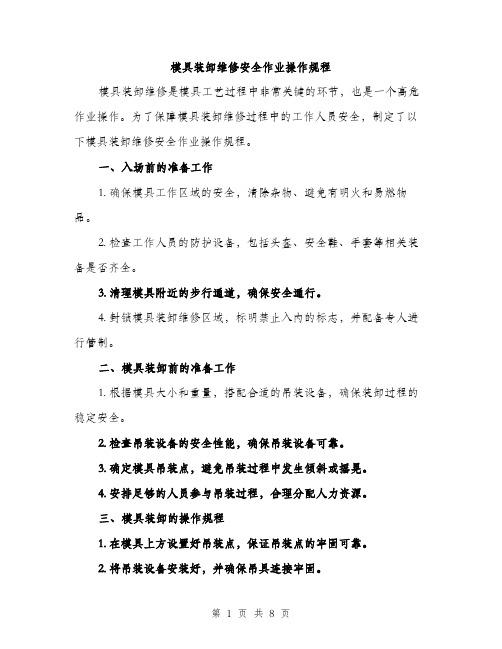
模具装卸维修安全作业操作规程模具装卸维修是模具工艺过程中非常关键的环节,也是一个高危作业操作。
为了保障模具装卸维修过程中的工作人员安全,制定了以下模具装卸维修安全作业操作规程。
一、入场前的准备工作1. 确保模具工作区域的安全,清除杂物、避免有明火和易燃物品。
2. 检查工作人员的防护设备,包括头盔、安全鞋、手套等相关装备是否齐全。
3. 清理模具附近的步行通道,确保安全通行。
4. 封锁模具装卸维修区域,标明禁止入内的标志,并配备专人进行管制。
二、模具装卸前的准备工作1. 根据模具大小和重量,搭配合适的吊装设备,确保装卸过程的稳定安全。
2. 检查吊装设备的安全性能,确保吊装设备可靠。
3. 确定模具吊装点,避免吊装过程中发生倾斜或摇晃。
4. 安排足够的人员参与吊装过程,合理分配人力资源。
三、模具装卸的操作规程1. 在模具上方设置好吊装点,保证吊装点的牢固可靠。
2. 将吊装设备安装好,并确保吊具连接牢固。
3. 操作人员进行吊装前,必须按照规定的操作程序穿戴好防护装备,并确保身体健康。
4. 根据模具的重量和大小,进行合适的吊装设备的选择,并确保吊装设备的额定工作范围内。
四、模具维修的操作规程1. 在进行模具维修前,必须将其全部部件拆卸,清洗并清理干净,确保不会缺失任何零部件。
2. 进行模具维修的人员必须经过专业的培训,并持有相应的操作证书。
3. 进行模具维修时,必须操作规范,避免造成附件或本体的损坏。
4. 维修作业时,必须使用合适的工具和设备来进行拆装。
五、模具装配及测试的操作规程1. 在进行模具装配之前,必须对模具的维修情况进行检查,并进行相应的调整和修复。
2. 进行模具装配时,必须按照规定的顺序进行,确保装配的准确性。
3. 模具装配完成后,进行测试,确保模具的正常工作状态。
4. 模具测试时,必须按照规定的操作程序,确保测试过程的安全性。
六、模具维修后的设备保养规程1. 在模具维修完成后,必须对模具进行彻底的清洁,确保模具表面光洁。
模具装卸维修安全作业操作规程
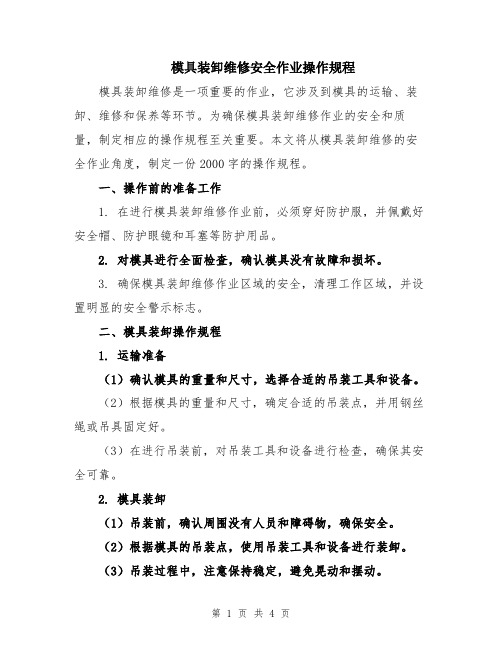
模具装卸维修安全作业操作规程模具装卸维修是一项重要的作业,它涉及到模具的运输、装卸、维修和保养等环节。
为确保模具装卸维修作业的安全和质量,制定相应的操作规程至关重要。
本文将从模具装卸维修的安全作业角度,制定一份2000字的操作规程。
一、操作前的准备工作1. 在进行模具装卸维修作业前,必须穿好防护服,并佩戴好安全帽、防护眼镜和耳塞等防护用品。
2. 对模具进行全面检查,确认模具没有故障和损坏。
3. 确保模具装卸维修作业区域的安全,清理工作区域,并设置明显的安全警示标志。
二、模具装卸操作规程1. 运输准备(1)确认模具的重量和尺寸,选择合适的吊装工具和设备。
(2)根据模具的重量和尺寸,确定合适的吊装点,并用钢丝绳或吊具固定好。
(3)在进行吊装前,对吊装工具和设备进行检查,确保其安全可靠。
2. 模具装卸(1)吊装前,确认周围没有人员和障碍物,确保安全。
(2)根据模具的吊装点,使用吊装工具和设备进行装卸。
(3)吊装过程中,注意保持稳定,避免晃动和摆动。
3. 模具安装(1)在安装前,清理模具和安装面,确保其干净平整。
(2)将模具按照要求插入到设备中,并进行固定。
(3)安装完成后,进行调试和检查,确保模具的安装质量和稳定性。
三、模具维修操作规程1. 维修准备(1)确定维修内容和需要的工具和材料。
(2)确认维修作业区域的安全,并设置明显的安全警示标志。
(3)穿戴好防护用品,包括防护服、安全帽、防护眼镜和耳塞等。
2. 模具维修(1)在进行维修前,尽量将模具放在平稳的工作台上,确保安全和稳定。
(2)根据维修内容,使用合适的工具和材料进行维修。
(3)维修过程中,保持工作台和周围环境的整洁,避免杂物的堆积。
3. 维修完成后的工作(1)将维修好的模具进行清洁和整理,确保其干净和正常。
(2)及时将维修用的工具和材料进行归库和整理,防止遗失和污染。
(3)记录维修的详细情况,包括维修时间、维修内容和使用的工具和材料等。
四、模具保养操作规程1. 保养前的检查工作(1)检查模具的状况,确认是否需要进行保养。
作业标准-模具发包[1]
![作业标准-模具发包[1]](https://img.taocdn.com/s3/m/683334a833687e21ae45a969.png)
12.模 具 施 工 與 驗 收 時 , 如 附 圖 所 示 。
製表
備
同喬模具款
註
應收
模具款
整理ppt
RDQR-044 B 版
模具發包作業辦法
• 附件二:
年
月
日
同喬實業股份有限公司 台照
模具估價單
新 開
廠商:
修 理
T E L :(
N o. )
品名
機種 編號
TCV-
保證 模數
估價 金額 $
實付 金額 $
手 動
刻
字
是
否 試模 是
否
OZ
1. 工 作 天 _______天 ,試 模 _______天 , 共 計 _______天 完 成 。
廠 商 簽 章 (請 蓋 公 司 及 負 責 人 印 章 )
2. 模 穴 、 模 心 材 質 。
說 3. 模具若有問題貴所須負責至完整。
專員
4. 若 模 具 延 七 天 以 上 , 每 天 罰 總 額 3/1000
5.2若為新產品設變之模具修改,則由原廠商製作 為原則,進行估價、議價之工作,若原廠商無法配合 可另尋其它替代廠商修改。
5.2.1已量產模具設變與委外修理之模具進出廠 手續,由技術單位主辦,開發協辦。
5.3模具發包需經開發部主管核定後呈總經理審核 後發包。
5.4模具之製作方式依整『理pp模t 具仕樣書』及『模具訂 製合約表』上的內容執行。
mm
※ 模 具 表 面 處 理 □ 拋 光 □ 磨 光 □ 噴 砂 □ 咬 花 J P.L面 寬 度 :
mm
※ 刻 字 型 式 □ 雕刻 □ 放電 □ 打印 □ 其他
K導梢中心:
- 1、下载文档前请自行甄别文档内容的完整性,平台不提供额外的编辑、内容补充、找答案等附加服务。
- 2、"仅部分预览"的文档,不可在线预览部分如存在完整性等问题,可反馈申请退款(可完整预览的文档不适用该条件!)。
- 3、如文档侵犯您的权益,请联系客服反馈,我们会尽快为您处理(人工客服工作时间:9:00-18:30)。
模具作业标准1、凸模1.1形状与尺寸应符合图纸或提供样件的要求。
完成刀口形状确认后按DR引伸件研合凸模(用板件合模):钳工仕上时应以凸模为基准,注意清角,避免研合时碰伤棱线,试按DR/TR之板件研配凸模。
棱线、搭接线应没有凹凸、扭曲的现象,R角应光滑圆顺且没有凹凸及尖角。
1.2凸模或凹模的研合率:管理面80%以上,准管理面70%以上。
1.3因特殊要求,铸件易磨损部位(或堆焊刀口),应该用合金钢焊条(7号钢)填补,堆焊部位的深度、宽度应在10×10mm以上,或者用合金钢块镶嵌在易磨损部位。
1.4表面粗糙度:主要部位0.4,次要部位0.8。
1.5如凸模是分块的,则各镶块间接合面间隙应小于0.1mm。
1.6镶块与窝座(或挡块)及键的配合应无间隙。
1.7材料及淬火硬度:一般使用合金铸铁GM241、GM246或ICD5,火焰的谇火硬度为HRC50以上。
1.8刀口应无裂纹、崩刃现象。
1.9刀口垂直度应不大于0.01mm,不允许有倒锥。
1.10刀口表面粗糙度,主要部位0.8,次要部位1.6.1.11刀口镶块接合面缝隙,料厚大于0.8mm的间隙不大于0.15mm,料厚小于0.8mm的间隙应小于0.05mm。
1.12多孔冲及异型面冲载,其凸模的位置、相对高度应准确可靠,应保证刀口的切入两基本一致,使切口顺利完成,若切口顺利完成,若大面积冲切厚板件,刀口应采用阶梯形(有高低差)。
1.13凸模材料为合金钢,淬火硬度为HRC56~62.1.14销孔的表面粗糙度为1.6,精度为H7.2、凹模2.1形状与尺寸应符合凸模的要求,棱线、搭接线应没有凹凸,扭曲的现象,R角应光滑圆顺且没有凹凸及尖角。
2.2工作部位表面粗糙度:主要部位低于0.8,次要部位1.6,凹模口圆角处粗糙度不低于0.4。
2.3因特殊要求,铸件易磨损部位(或堆焊刀口),应该用合金钢焊条填补,堆焊部位的深度、宽度应在10×10mm以上,或者用合金钢块镶嵌在易磨损部位。
2.4与凸模间隙:直线和圆角部位应扣料厚,曲线弯角部位适当减小。
2.5如凹模是分块的,则各镶块间接合面间隙应小于0.1mm。
2.6镶块于窝座(或挡块)及键的配合应无间隙。
2.7刀口应无裂纹、崩刃现象。
2.8刀口垂直度应不大于0.01mm,部允许有倒锥现象;2.9刀口镶块接合面缝隙,料厚大于0.8mm的间隙不大于0.15mm,料厚小于0.8mm的间隙小于0.05mm。
2.10销孔的表面粗糙度为1.6,精度为H7。
2.11内刀口高度应以留料3片为准,但内刀口高度应不小于6mm。
2.12材料及淬火硬度:一般使用合金铸铁或合金钢,火焰的淬火硬度为HRC50以上。
3、压边圈3.1压边圈与凸模的型面研合率为70%以上;3.2压边圈的表面粗糙度为0.8;3.3压边圈的淬火硬度HRC50以上;3.4拉延筋的分布合理,高度应合适;3.5采用正拉延(一般在双动压力机上)结构的模具,其压边圈应安装限位螺栓。
4、推、压料机构及定位4.1退、压料板表面粗糙度,主要部位及大平面为1.6;4.2退、压料板与凸凹模间隙在0.05~0.2mm之间(可调整);4.3以产品形状定位的板类定位面与圧料板研合率应在70%以上;4.4退压料板顶出后要高于凸凹模,但一般不能超出料厚,料厚0.5mm以下时,要与凸凹模平齐。
4.5退圧料弹簧应统一标准,直径和长度同一规格允许公差为±0.5,所有弹簧其簧压应一致,弹簧窝座深度也应一致,误差在±0.2mm以内。
4.6复合模要保证弹簧压缩量大于拉深或成形的尺寸。
4.7退圧料限位螺钉、限位衬套应可靠。
螺钉或衬套高度尺寸应一致,误差为H8,上压料板的外侧应安装侧保险销。
4.8废料刀设置合理、安全、可靠。
4.9定位销、块、板应定位准确、可靠、合理,放取方便且不划伤工件,销的拔出力在15~20公斤。
4.10出料孔位置与角度合理,漏料顺畅。
5、取、放料及定位机构5.1定位销、块、板设置要合理,定位要牢靠,对工件的放取应无阻碍,无划伤现象。
销的拔出力为15~20公斤以上。
5.2对工件不易取出的模具需增加顶料装置。
特大型的工件放取应有滚轮等装置。
外观件还需要安装防碰、防划伤等结构。
6、导向机构6.1各导板、滑块、斜锲面(包括平面导板)应采用耐磨板(含油),其倒角为R5~10,且应圆滑过度。
6.2各导板与滑配面工作表面粗糙度为0.4(包括斜锲面),极限时,两导板接触面不少于30mm。
6.3表面硬度应在RHC55以上。
6.4反侧、导板、滑块与窝座固定应无间隙,安全可靠。
强制退回机构应可靠,表面硬度为HRC55以上。
6.5导板与滑块及斜锲面、凸轮面之间的研合率应在85%以上,上下滑块的垂直度为0.02/100两者的间隙在0.03mm~0.05mm,压边圈的导板间隙为0.05mm~0.2mm。
6.6导柱导套规格应标准化、系统化,大型模具导柱导套直径有限选用¢50、¢60、¢80、¢100,小型模具导柱导套直径也应优先化。
导柱导套应设置合理可靠及防错装。
6.7导柱导套的配合间隙为h5/h6,或h6/h7,工作表面粗糙度为0.4,导柱应更高一级为0.2,研合后周边应有均匀斑点。
6.8导柱压入底板后垂直度为0.02/1000,导柱压入量应是导柱直径的1.5倍以上。
6.9表面硬度为HRV55以上。
7、外观及安装尺寸7.1铸件表面清干净,去除毛刺及浇口,不允有裂纹及砂眼气孔。
7.2上、下模板及其他铸件应有足够的强度。
中小型模具的加强筋应在35mm-40mm以上,下模板厚度应为70mm以上。
铸件应人工时效,消除应力。
7.3上、下模板、压边圈周边应倒角或倒R。
7.4模具闭合高度要满足机床条件,在同一机床适用的模具,封闭高度应尽可能统一,同时适用多付模具,其封闭高度一致,应首先满足成形模的要求。
7.5装配后模具,上下模座平行度为300mm内不大于0.06,双动拉延模上下模座平行度不大于0.2-0.25/300。
7.6拉延模内腔应有样件并涂油,其他滑动面应涂黄油或防锈油。
7.7安装孔、安装槽、顶杆孔其中心距允差为±0.5mm,模具具有快速安装定位结构,模柄安全可靠,无松动、转动现象。
7.8(小型模具)模柄规格应满足工艺设备条件,并与压力中心基本保持一致,包括与设备工作中心保持一致。
7.9(小型模具)模柄转配后,与上模座的上表面垂直度在±0.01/100以内,模柄安全可靠,无松动、转动现象。
7.10顶杆要等长,长度误差不大于±0.1,直径误差不大于±0.2,标记要清晰。
7.11起重棒、孔(吊耳)要设置合理、起吊方便、可靠,零件重量超过25工斤时应设置起吊螺孔。
7.12模具应设有平横块及限位块且必须等高限位块偏差为0.05mm。
7.13模具安装中心,前后左右应打标记,模具正面应有“F”向标记。
7.14上模板正面或侧面应有标记牌,标明模具名称、图号、工序号、重量、制造单位即日期,标记牌固定可靠。
上下模板上应铸出产品图号、工序号。
7.15模具外表面应涂防锈漆的颜色。
8、模具调整时检查的项目及技术要求8.1制件8.1.1制件形状与尺寸应符合检具要求或装配要求8.1.2制件应无明显毛刺(允许有小于0.2mm高的毛刺,A级模具所冲工件允许有小于0.1mm高的毛刺)及拉痕。
不允许有划伤、皱纹、裂纹等现象。
8.1.3废料流动应安全可靠,取出方便。
废料刀设置合理,废料最长不超过450mm。
周边废料应落在模具外,冲孔的废料应引导落在模具外或废料箱内。
8.1.4工件不易取出的模具需增加顶料装置。
特大型的工件放取应有滚轮等装置。
外观件还需安装防碰、防划伤等结构。
8.2凸模及凹模8.2.1调整各部位配合间隙要合适。
8.2.2调整后的表面粗糙度应符合规定要求。
8.2.3调整后的凸凹模硬度应符合规定要求。
8.2.4各工作表面及R部位应抛光。
8.2.5调整后各部位刃口高度、垂直度应符合规定要求。
8.2.6调整时,落料类应调整凸模、冲孔类应调整凹模。
8.3定位及退料8.3.1定位要稳定、可靠、准确。
8.3.2退料板要灵活、力量可靠、放取工件方便。
8.3.3导板及滑动机构工作要平稳,斜锲、凸轮强制退回机构工作平稳可靠。
8.3.4导板与滑块的工作表面接触良好、间隙合理,但应防止圧料板被上模带上。
8.3.5废料顺利通过废料孔或不飞溅。
8.4安装与外观8.4.1模具各部位按规定的颜色涂漆。
8.4.2标牌内容正确、大小合适、字迹清晰。
8.4.3联合安装时,各模具的闭合高度要保持一致。
8.4.4模柄与安装槽、孔装夹要合适。
冲压加工工序名称中英文对照表序号工艺名称英文全称略写1 落料Blank BL2 切割Cut CUT3 冲孔Piercing PI/PRC4 剪边Trimming TR5 分割Separating SEP6 修边Shaving SHV7 引伸Draw DR8 再引伸Redraw RDR9 成形Form FO10 整形Restricting RST11 压印Emboss EMB12 弯边/翻边Flange FL13 翻孔Burring BUR14 卷边Curling CRL15 弯曲Bend BE16 侧冲边/ CAMPI/CAMPRC17 包边Hemming HEM18 弯曲整形Flange AND Restricting FL RST19 落料、冲孔Bland AND Piercing BL+PRC20 剪边、冲孔Trimming AND Piercing TR+PRC板件模初学入门简易指导书拉延模平横块的制作尺寸要求:1.连带料厚加平衡块高度尺寸减0.5mm,再用钢片或铜片,0.3壹片、0.1壹片、0.05贰片垫上。
2.模具于精研完成及扣料厚完成:(一)测量平衡块尺寸并作记录;(二)平衡块及平衡块基座须打钢印编号及刻所测得数据;(三)将测得所需数量及规格单送予加工单位并填上需要日期3.平衡块的功能和作用(一)是为了便于模具在拉延生产中,易于控制料的流动性和稳定性。
4.垫钢片作用(一)便于试模时平衡块过高要再加延搁试模和浪费工时,故换取各种不同规格的垫片,以便于控制各部位间隙。
模具钳工作业流程参考表一、引伸模(拉延模)1.上下模组立和研配导板。
2.下型模:(1)打磨雕刻痕;(2)清各处R角;(3)魔石推磨,由粗转细;(4)砂纸推磨,由粗转细;(5)自检各部位是否平顺光滑—送检;(6)各处凸花淬火;(7)淬火后生锈处砂纸磨顺抛光、亮;(8)自检、送检。
3.圧料圈(活塞面)同上作业。
4.上型模:(1)打磨雕刻痕;(2)清各处R角;(3)备平垫块;(4)凹模置下面凸模放上、合上、下模;(5)上机台研配上模;(6)研配导板及检验导板间隙;(7)将合模机、主机压力调至最小,然后下至上下模接触点;(8)将四点平垫块调降至上下模接触点;(9)模具上升擦红丹;(10)备保险丝于模具有凹凸花较小地方,位置于前、后、左、右,模具下降压至保险丝成扁形,然后查看凹凸花前、后、左、右是否均匀,(如过0.2以上必须上报处理),处理方式,移导板位置;(11)研配;(12)扣料厚;(13)精研配几次至自检达到要求层次;(14)送检;(15)拆模具;(16)拆模推磨石;(17)推砂纸抛光;(18)上下模内部上油后台并带试模(并通知上报安排试模日期);(19)试模;(20)试模情况各种记录填写;(21)试模OK,自检;(22)送检板件;(23)送检NG,整修再试,试至送检合格为止;(24)合格拆模;(25)凹凸花拉延筋淬火;(26)推砂纸抛光;(27)再送检;(28)OK后上油漆(依规定的各种颜色);注:任何一套模具,该倒R角的必须依规定倒R角。