第七章+后端工艺
第七章 离子注入原理下晶格损伤
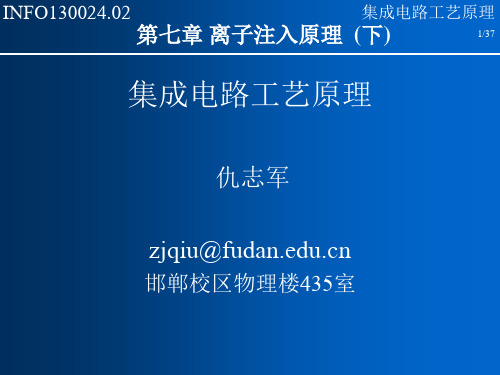
前言 晶体生长 实验室净化及硅片清洗 光刻 热氧化 热扩散 离子注入 薄膜淀积 刻蚀 后端工艺与集成 未来趋势与挑战
INFO130024.02
集成电路工艺原理
第七章 离子注入原理 (下)
上节课主要内容
3/37
1 x R 2 0.4Q p CP C x C p exp R p R 2 p
损伤的产生
• 移位原子:因碰撞而离开晶格位置的原子。 • 移位阈能Ed:使一个处于平衡位置的原子发生移位,所需 的最小能量. (对于硅原子, Ed15eV)
E<Ed 无位移原子 ������ Ed<E<2Ed 有位移原子 ������ E>2Ed 级联碰撞
• 注入离子通过碰撞把能量传给靶原子核及其电子的过程, 称为能量传递过程
INFO130024.02
集成电路ቤተ መጻሕፍቲ ባይዱ艺原理
第七章 离子注入原理 (下)
17/37
INFO130024.02
集成电路工艺原理
第七章 离子注入原理 (下)
18/37
非晶化(Amorphization)
注入离子引起的晶格损伤 有可能使晶体结构完全破 坏变为无序的非晶区。
与注入剂量的关系 – 注入剂量越大,晶格损 伤越严重。 – 临界剂量:使晶格完全 无序的剂量。 – 临界剂量和注入离子的 质量有关
INFO130024.02
集成电路工艺原理
第七章 离子注入原理 (下) 离子注入损伤估计
16/37
100KeV B离子注入损伤 初始核能量损失:30eV/nm, 硅晶面间距: 0.25nm, 每穿过一个晶面 能量损失: 30eV/nm X 0.25nm=7.5eV <Ed (15eV). 当能量降到50KeV, 穿过一个晶面能量损失为15eV, 该能量所对应的射程为: 150nm. 位 移原子数为: 150/0.25=600, 如果移位距离为: 2.5nm, 那么损伤体积: (2.5)2 X150=3X10-18cm3. 损伤密度: 2X1020 cm-3, 大约是原子密度 0.4%. 100KeV As离子注入损伤 平均核能量损失:1320eV/nm,损伤密度: 5X1021 cm-3, 大约是原子密 度10%, 该数值为达到晶格无序所需的临界剂量, 即非晶阈值.
芯片封装流程的前后端工艺环节及定义

芯片封装流程的前后端工艺环节及定义温馨提示:该文档是小主精心编写而成的,如果您对该文档有需求,可以对它进行下载,希望它能够帮助您解决您的实际问题。
文档下载后可以对它进行修改,根据您的实际需要进行调整即可。
另外,本小店还为大家提供各种类型的实用资料,比如工作总结、文案摘抄、教育随笔、日记赏析、经典美文、话题作文等等。
如果您想了解更多不同的资料格式和写法,敬请关注后续更新。
Tips: This document is carefully written by the small master, if you have the requirements for the document, you can download it, I hope it can help you solve your practical problems. After downloading the document, it can be modified and adjustedaccording to your actual needs.In addition, the store also provides you with a variety of types of practical information, such as work summary, copy excerpts, education essays, diary appreciation, classic articles, topic composition and so on. If you want to know more about the different data formats and writing methods, please pay attentionto the following updates.芯片封装流程的前后端工艺环节及定义在半导体产业中扮演着至关重要的角色,它是将芯片封装成最终产品的关键步骤。
半导体后端工艺流程

半导体后端工艺流程【摘要】半导体后端工艺流程是半导体制造过程中的重要环节,涉及多个步骤和技术。
工艺准备阶段是整个流程的第一步,包括材料准备和设备校准等工作。
接着是掩膜图形制作,通过光刻技术将芯片上的电路图案转移到光刻胶上。
然后是晶圆清洁与表面处理,保证芯片表面无尘且具有良好的附着性。
电子束光刻是一种高精度的刻蚀技术,用于制作微小且复杂的芯片结构。
最后是蚀刻与沉积,通过化学腐蚀和沉积来改变芯片表面的性质。
半导体后端工艺流程需要精密的操作和先进的设备支持,是半导体制造中至关重要的环节。
【关键词】半导体后端工艺流程,工艺准备阶段,掩膜图形制作,晶圆清洁与表面处理,电子束光刻,蚀刻与沉积,半导体后端工艺流程总结1. 引言1.1 半导体后端工艺流程概述半导体后端工艺流程是指在半导体芯片制造的最后一道工序,主要包括工艺准备、掩膜图形制作、晶圆清洁与表面处理、电子束光刻和蚀刻与沉积等步骤。
这些步骤在半导体制造过程中起着至关重要的作用,直接影响着芯片的性能和质量。
在半导体后端工艺流程中,工艺准备阶段是整个流程的第一步,包括准备所需的材料、设备和工艺参数设置。
掩膜图形制作是将设计好的电路图案转移到晶圆上的关键步骤,需要通过光刻技术来实现。
晶圆清洁与表面处理是为了去除晶圆表面的杂质和氧化层,保证后续工艺的顺利进行。
电子束光刻是一种高精度的图案转移技术,可以将微米甚至亚微米级别的图案精确地转移到晶圆表面。
蚀刻与沉积是指利用化学蚀刻和蒸发沉积等方法,在晶圆表面形成所需的结构和层。
通过以上步骤的顺利进行,半导体后端工艺流程可以完成芯片的制造,从而生产出高性能、高质量的半导体产品。
半导体后端工艺流程是半导体制造中不可或缺的环节,对整个半导体产业的发展起着重要的推动作用。
2. 正文2.1 工艺准备阶段工艺准备阶段是半导体后端工艺流程中至关重要的一步。
在这个阶段,工程师们需要进行各种准备工作,以确保后续的工艺步骤能够顺利进行。
化工设计概论第七章-设备的工艺设计与选型
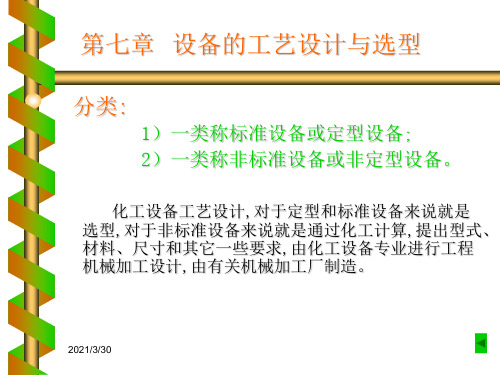
2021/3/30
51
设计与选用方法:
(1)汇总设计数据、分析设计任务根据工艺衡算和工艺物 料的要求、特性,获得物料流量、温度、压力和化学性 质、物性参数,取得有关设备的负荷、流程中的地位与 流程中其他设备的关系等数据。
• 折流板的间距不小于圆通内直径的五分之 一,且不小于50mm,最大间距不大于圆筒 内直径。
• 间距过小,不便于制造及检修,阻力增大。 过大,对传热不利。可参考表7-4。
2021/3/30
40
1.换热器设计的一般原则
• (1)基本要求 ➢ 满足工艺操作条件 ➢ 能长期运转 ➢ 安全可靠 ➢ 不泄漏 ➢ 维修清洗方便 ➢ 满足工艺要求的传热面积 ➢ 尽量有较高的传热效率 ➢ 流体阻力尽量小 ➢ 满足工艺布置的安装尺寸等要求
第七章 设备的工艺设计与选型
分类:
1)一类称标准设备或定型设备; 来自)一类称非标准设备或非定型设备。
化工设备工艺设计,对于定型和标准设备来说就是 选型,对于非标准设备来说就是通过化工计算,提出型式、 材料、尺寸和其它一些要求,由化工设备专业进行工程 机械加工设计,由有关机械加工厂制造。
2021/3/30
标准换热器型式:固定管板式,浮头式,U形管式和填料函式。 标准换热器型号的表示方法:
×××DN-P1/P2-A-LN/d-Nt/Ns Ⅰ(或Ⅱ)
×××——由三个字母组成,第一个字母表示前端管箱形式;第二个字母 代表管壳形式;第三个字母代表后端结构形式,参见图例(图7.10)。
DN——公称直径(mm)对重沸器用分数表示,分子为管箱内直径,分母为圆 筒内直径。
轴的功率。流体从泵获得的实际功率为
泵的有效功率Ne,由泵的流量和扬程求得
有效功率与轴功率的比值为离心泵的效率
集成电路工艺 接触与互连
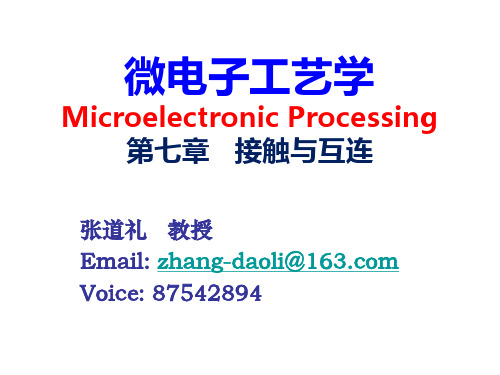
金属线 接触面积A
重掺杂硅
c
1 dJ
dV V 0
定义:零偏压附近电流密
度随电压的变化率
比接触电阻 c 的单位: Wcm2 或 m2
接触电阻:
Rc
c
A
金属-Si之间, c在10-5~10-9 Wcm2 金属-金属之间, c<10-8 Wcm2
7.2 金属化
金
半
接
整流接触
微电子工艺学
Microelectronic Processing 第七章 接触与互连
张道礼 教授 Email: zhang-daoli@ Voice: 87542894
7.1 概述
后端工艺[backend of the line technology (BEOL)]:将器件连
接成特定的电路结构:金属线及介质的制作,使得金属线在电学和 物理上均被介质隔离。
7.2 金属化
如果我们以铜导线取代传统铝导 线,并采用低介电常数的介质 (k=2.6)取代二氧化硅,将可减 低多少百分比的RC时间常数? (铝的电阻率为2.7µΩ∙cm,而 铜为1.7µΩ∙cm)。 解:
7.2 金属化
7.2 金属化
阻止电迁移的方法有 与0.5~4%铜形成合金(可以降低铝原子在晶间 的扩散系数。但同时电阻率会增加!)、以介质 将导通封闭起来、淀积时加氧。 由于铜的抗电迁移性好,铝-铜(0.5-4%)或铝 -钛(0.1-0.5%)合金结构防止电迁移,结合AlSi合金,在实际应用中人们经常使用既含有铜又 含有硅的Al-Si-Cu合金以防止合金化(即共熔) 问题和电迁移问题。
解:500℃时硅在铝中的扩散系数约 为2×10-8cm2/s,故扩散长度约为 60µm,铝与硅的密度比值约为 2.7/2.33=1.16;500℃时的S约为 0.8%。则被消耗的硅的厚度约为:
集成电路工艺原理(PPT 40页)

17
n
离子 E2
B
17 keV
e
n
P 150 keV
As, Sb >500 keV
n
INFO130024.01
集成电路工艺原理
第七章 离子注入原理 (上)
18
射程终点(EOR) 处晶格损伤大
表面处晶格 损伤较小
INFO130024.01
集成电路工艺原理
第七章 离子注入原理 (上)
19
R:射程(range) 离子 在内的总路线长度
离子注入的基本过程
将某种元素的原子或携 带该元素的分子经离化 变成带电的离子
在强电场中加速,获得 较高的动能后,射入材 料表层(靶)
以改变这种材料表层的 物理或化学性质
INFO130024.01
集成电路工艺原理
第七章 离子注入原理 (上)
6
离子注入特点
可通过精确控制掺杂剂量(1011-1018 cm-2)和能量(1-400 keV)来 达到各种杂质浓度分布与注入浓度
第七章 离子注入原理 (上)
28
注入离子的真实分布
CxCPexp12xRRpp
2
真实分布非常复杂,不服从严格的高斯分布
当轻离子硼(B)注入到硅中,会有较多的硼离子受到大 角度的散射(背散射),会引起在峰值位置与表面一侧有 较多的离子堆积;重离子散射得更深。
平面上杂质掺杂分布非常均匀(1% variation across an 8’’ wafer) 表面浓度不受固溶度限制,可做到浅结低浓度 或深结高浓度 注入元素可以非常纯,杂质单一性 可用多种材料作掩膜,如金属、光刻胶、介质;可防止玷污,自由
度大 离子注入属于低温过程(因此可以用光刻胶作为掩膜),避免了高
集成电路后端工艺
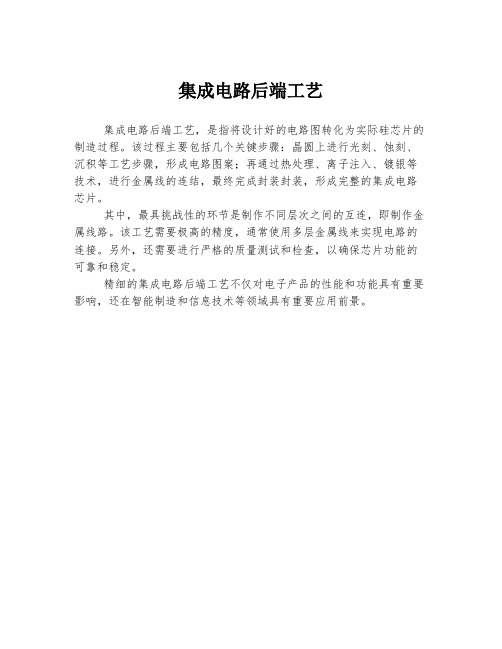
集成电路后端工艺
集成电路后端工艺,是指将设计好的电路图转化为实际硅芯片的制造过程。
该过程主要包括几个关键步骤:晶圆上进行光刻、蚀刻、沉积等工艺步骤,形成电路图案;再通过热处理、离子注入、镀银等技术,进行金属线的连结,最终完成封装封装,形成完整的集成电路芯片。
其中,最具挑战性的环节是制作不同层次之间的互连,即制作金属线路。
该工艺需要极高的精度,通常使用多层金属线来实现电路的连接。
另外,还需要进行严格的质量测试和检查,以确保芯片功能的可靠和稳定。
精细的集成电路后端工艺不仅对电子产品的性能和功能具有重要影响,还在智能制造和信息技术等领域具有重要应用前景。
芯片封装流程的前后端工艺环节

芯片封装流程的前后端工艺环节英文回答:Front-end Process.The front-end process of chip packaging involves the following steps:Wafer preparation: The silicon wafer is cleaned, patterned, and etched to create the integrated circuits (ICs).Die attach: The ICs are attached to a lead frame or substrate using a conductive adhesive.Wire bonding: Gold wires are used to connect the ICs to the lead frame or substrate.Molding: A plastic material is used to encapsulate the ICs and protect them from environmental factors.Back-end Process.The back-end process of chip packaging involves the following steps:Lead finishing: The leads are coated with a protective material such as solder or gold.Testing: The packaged chips are tested to ensure they meet electrical and functional specifications.Shipping: The packaged chips are shipped to the customer.中文回答:前端工艺。
第七章 模锻工艺
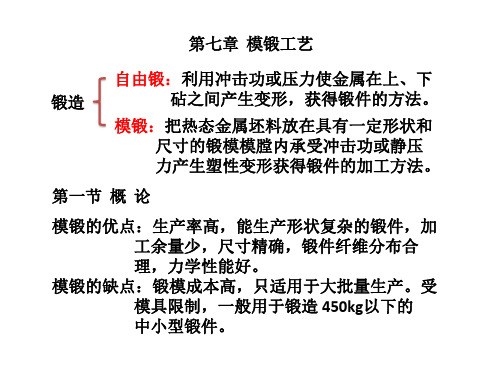
二、模锻工艺方案的选择 基本原则:保证锻件生产的技术可行性和经济合理性。 在工艺上应满足对锻件质量和数量的要求; 在经济上应使锻件生产成本低,经济效益好。
1.模锻工艺的选择 ①较大批量生产,采用模锻锤或热模锻压力机; ②中小批量生产,采用螺旋压力机或在自由锻锤上胎 模锻及固定模模锻。 工艺方案的选择: ①必须保证锻件的质量要求。 ②必须考虑工厂的具体条件,根据工厂的设备状况选 择合理的工艺方案。
二、热模锻压力机上模锻件图设计要点 热模锻压力机上模锻件图设计的原则、内容、方法 与锤上模锻基本相同。 根据热模锻压力设备特点,锻件图设计有以下要求: ①热模锻压力机有顶出装置,锻件可以顺利地从较深的 模膛内取出,分模面选择较灵活。
头部沿轴向的内孔无 法锻出,飞边体积较 多,金属浪费大。
②热模锻压力机上模锻不用顶杆时,模锻件斜度与锤 上模锻相同。若采用顶杆顶出锻件,则模锻斜度一 般比锤上模锻件小一级。外斜度为3°~7°,一般 常用5°;内斜度为7°~l0°。
锻件技术条件:锻件图无法表示的锻件质量和检验要求 的内容,均应列入技术条件中加以说明。
包括内容:
①未注明的模锻斜度和圆角半径。 ②允许错移量和残余飞边的宽度。 ③允许的表面缺陷深度。 ④锻后热处理方法及硬度要求。 ⑤表面清理方法。 ⑥需要取样进行金相组织和力学性能试验时, 应注明在锻件上的取样位置。 ⑦其他特殊要求,如直线度、平面度等。
非圆形锻件的外廓包容体重量Gb和体积Vb(图7-9)为: Vb lbh Gb lbh
表7-1锻件形状复杂程度等级 级别 Ⅰ Ⅱ Ⅲ Ⅳ 代号 S1 S2 S3 S4 形状复杂系数值 0.63~1 0.32~0.63 0.16~0.32 ≤0.16 形状复杂程度 简单 一般 比较复杂 复杂
后端工艺流程英文
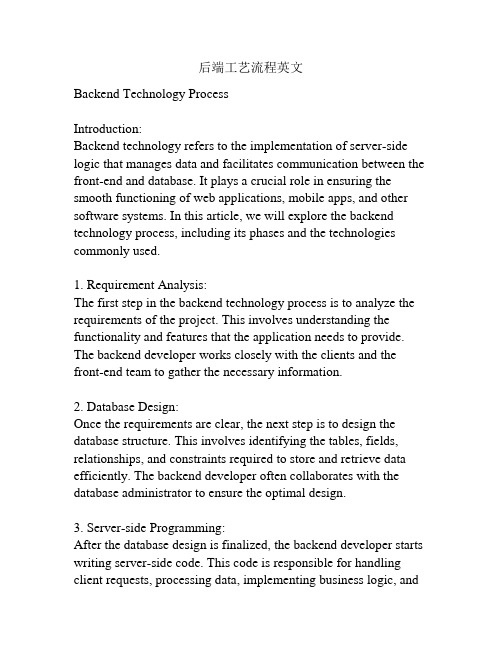
后端工艺流程英文Backend Technology ProcessIntroduction:Backend technology refers to the implementation of server-side logic that manages data and facilitates communication between the front-end and database. It plays a crucial role in ensuring the smooth functioning of web applications, mobile apps, and other software systems. In this article, we will explore the backend technology process, including its phases and the technologies commonly used.1. Requirement Analysis:The first step in the backend technology process is to analyze the requirements of the project. This involves understanding the functionality and features that the application needs to provide. The backend developer works closely with the clients and the front-end team to gather the necessary information.2. Database Design:Once the requirements are clear, the next step is to design the database structure. This involves identifying the tables, fields, relationships, and constraints required to store and retrieve data efficiently. The backend developer often collaborates with the database administrator to ensure the optimal design.3. Server-side Programming:After the database design is finalized, the backend developer starts writing server-side code. This code is responsible for handling client requests, processing data, implementing business logic, andinteracting with the database. Popular programming languages for backend development include Java, Python, Ruby, and Node.js. 4. API Development:In many cases, the backend serves as an API (Application Programming Interface) that allows the front-end to communicate with the server. The backend developer designs and implements APIs that define the methods and endpoints through which the front-end can send requests and receive responses. API development requires careful consideration of security, scalability, and performance.5. Integration Testing:Once the server-side code and APIs are developed, it is necessary to test their integration with the front-end. Integration testing ensures that the communication between the client-side and server-side components works as expected. Various techniques, such as unit testing and mocking, are employed to simulate different scenarios and identify bugs or issues.6. Performance Optimization:In real-world scenarios, web applications often face heavy traffic and large data volumes. Therefore, it is crucial to optimize the backend performance to ensure fast and responsive user experience. Techniques like caching, load balancing, and using efficient algorithms are employed to achieve the desired level of performance.7. Security Implementation:Data security is a top priority in backend development. Thebackend developer needs to implement security measures, such as encryption, authentication, and authorization, to protect sensitive information and prevent unauthorized access. Regular vulnerability assessments and code reviews are performed to identify and fix security loopholes.8. Deployment and Maintenance:Once the backend technology is developed, it is deployed to production servers. Continuous integration and deployment(CI/CD) processes automate the deployment and ensure a smooth transition from development to production. Regular maintenance and monitoring are carried out to ensure system stability, scalability, and uptime.Conclusion:The backend technology process involves various phases, including requirement analysis, database design, server-side programming, API development, integration testing, performance optimization, security implementation, and deployment. It requires a combination of technical skills, architectural understanding, and attention to detail. By following a systematic approach, backend developers deliver robust and efficient solutions that power modern software systems.。
半导体后端工艺:传统封装方法组装工艺的八个步骤

一、背景介绍半导体是现代电子行业的核心材料,其应用范围广泛,涉及到各种电子设备和系统。
半导体芯片的制作过程包括前端工艺(制作芯片)和后端工艺(封装芯片)。
后端工艺封装芯片是保护芯片、连接外部电路和提高功率传输效率的重要环节。
传统的封装方法组装工艺是后端工艺的关键部分,其包括多个步骤,需要严谨的操作和精密的设备。
二、后端工艺封装的意义半导体芯片在制造完成后需要进行封装,主要是为了保护芯片,连接外部电路和提高功率传输效率。
传统的封装方法组装工艺是后端工艺封装芯片的重要环节,对最终产品的性能和可靠性起到至关重要的作用。
三、传统封装方法组装工艺的八个步骤1. 原材料准备:准备封装芯片所需要的原材料,包括芯片、封装材料、连接线、塑料封装体等。
2. 芯片粘接:将芯片固定在封装底座或引线架上,使用导电胶水或金线等材料进行粘接。
3. 封装体注塑:将上述粘接好的芯片放入封装模具中,通过注塑工艺将封装材料注入模具,形成封装体。
4. 引线焊接:在封装体上焊接连接线,连接线的焊接需要高精度的自动化焊接设备。
5. 封装测试:对封装完成的芯片进行测试,检查连接线是否焊接良好,芯片功能是否正常。
6. 封装涂覆:对封装体进行表面处理,包括防潮、防尘、绝缘涂层等。
7. 功能测试:对封装完成的芯片进行功能测试,验证其性能和可靠性。
8. 包装:将封装完成的芯片进行包装,包括标识、说明书、静电防护包装等。
四、传统封装方法组装工艺的挑战和发展方向传统封装方法组装工艺存在着一些挑战,包括制程复杂、工艺精度要求高、生产效率低等问题。
随着半导体技术的发展,新型封装技术如3D封装、MEMS封装等逐渐成熟,为解决传统封装方法组装工艺的挑战提供了新的思路。
未来,随着智能手机、物联网、人工智能等应用领域的不断扩大,半导体芯片的封装工艺也将不断创新,以满足市场对芯片性能和功能的需求。
传统封装方法组装工艺在半导体后端工艺中扮演着重要的角色,其具体的步骤和发展方向对于半导体行业的发展具有重要意义。
后端工艺的N型欧姆接触

后端工艺的N型欧姆接触徐海铭;秦征峰;寇春梅;黄蕴【摘要】文章首先从原理上较为全面地阐述了欧姆接触形成的必要条件和广泛应用,其次主要针对工艺生产过程中产生的多种n+欧姆接触不良情况进行了汇总分析并提供了相应解决方案。
提出了等离子损伤对欧姆接触电阻有较大影响并对此进行实验对比验证。
伴随着现代工艺的不断发展进步,欧姆接触电阻将会在电路设计应用中越来越受到重视并发挥重大作用。
%This paper introduces the necessary conditions of the ohmic contact formation.Secondly,a variety of bad n+ ohmic contact is analyzed and provided appropriate solutions in process.At the same time plasma damage has a great influence in the ohmic contact that is proposed and verified.【期刊名称】《电子与封装》【年(卷),期】2012(012)003【总页数】4页(P33-35,40)【关键词】欧姆接触;PLASMA;台阶覆盖【作者】徐海铭;秦征峰;寇春梅;黄蕴【作者单位】中国电子科技集团公司第58研究所,江苏无锡214035;中国电子科技集团公司第58研究所,江苏无锡214035;中国电子科技集团公司第58研究所,江苏无锡214035;中国电子科技集团公司第58研究所,江苏无锡214035【正文语种】中文【中图分类】TN451 引言随着半导体技术不断发展,人们对欧姆接触的低阻性能要求也越来越高。
欧姆接触是金属与半导体界面的一种重要接触形式,它会对器件的效率、增益和开关速度等性能指标有直接影响,还可以用于一切器件和电路信号的输入、输出以及各元件间的相互连接。
集成电路工艺原理 ppt课件

6/43
不足之处: 可靠性低、噪声大、放大率低等缺点
7/43
1948年 W. Shockley 提出结型晶体管概念
1950年 第一只NPN结型晶体管
8/43
Ti 公司的Kilby 12个器件,Ge 晶体
9/43
(Fairchild Semi.)
Si IC
J. Kilby-TI 2000诺贝尔物理奖
16/43
Physical gate length in nm
We are here.
Source silicide urce
Drain
Year
No complete technological solution available !!!
gate oxide channel
1/43
集成电路工艺原理
2/43
大纲(1)
教科书:
1. 王蔚,田丽,任明远,“集成电路制造技术-原理与工艺” 2. J.D. Plummer, M.D. Deal, P.B. Griffin, “硅超大规模集成电路工艺
技术-理论、实践与模型”
参考书:
• C.Y. Chang, S.M. Sze, “ULSI Technology” • 王阳元 等,“集成电路工艺原理” • M. Quirk, J. Serda, “半导体制造技术”
12/43
• SSI (小型集成电路),晶体管数 10~100,门数<10 • MSI (中型集成电路),晶体管数 100~1,000,10<门数<100 • LSI (大规模集成电路),晶体管数 1,000~100,000,门数>100 • VLSI (超大规模集成电路),晶体管数 100,000~ 1,000,000 • ULSI (特大规模集成电路) ,晶体管数>1,000,000 • GSI (极大规模集成电路) ,晶体管数>109 • SoC--system-on-a-chip/SIP--system in packaging
第七章 集装单元化设备

第七章 集装单元化设备
第二节 集装箱
二、集装箱的种类
1.通用干货集装箱 1.通用干货集装箱 通常为封闭式,在一端或侧面设有箱门。一般用来 装运文化用品、化工用品、电子机械、工艺品、医 药、日用品、纺织品及仪器零件等。 通用干货集装箱也称为杂 货集装箱,用来运输无需 控制温度的件杂货。
第七章 集装单元化设备
第二节 集装箱
二、集装箱的种类
5.敞顶集装箱 5.敞顶集装箱 敞顶集装箱是一种没有刚性箱顶的集装箱,但有可折叠 式或可折式顶梁支撑的帆布、塑料布或涂塑布制成的顶 篷,其他构件与通用集装箱类似。这种集装箱适于装载 大型货物或重货,如钢铁、木材,特别是像玻璃板等易 碎的重货,利用吊车从顶部吊入箱内不易损坏,而且也 便于在箱内固定。
第二节 集装箱
二、集装箱的种类
2.保温集装箱 2.保温集装箱 保温集装箱是为了运输需要冷藏或保温的货物。所 有箱壁都采用导热率低的材料隔热。
保温集装箱种类: 保温集装箱种类:
1)冷藏集装箱 2)隔热集装箱 3)通风集装箱
第七章 集装单元化设备
第二节 集装箱
二、集装箱的种类
3.罐式集装箱 3.罐式集装箱 罐式集装箱专用以装运酒类、油类、液体食品以及化 学品等液体货物的集装箱,还可以装运其他危险液体 货物。 这种集装箱有单罐和 多罐数种,罐体四角 由支柱、撑杆构成整 体框架。
四、集装单元化的基本原则
(1)通用化 (2)标准化 (3)系统化
系统化指集装单元化技术中 系统化 的每一个问题都必须置于物 流系统中来考虑,否则就难 以付诸实现或难以获得成效。
通用化即集装化要与物流全过程的 通用化 设备与工艺相适应,不同形式的集 装化方法之间、同一种集装化方法 的不同规格的集装之间相协调,以 便在物流全过程中畅通无阻。 标准化指从集装化术语的使用,集 标准化 装工具的尺寸、规格、强度、外形 和重量,集装工具材质、性能、实 验方法,装卸搬运加固规则一直到 编号、标志、操作规范和管理办法 等等,都必须要标准化,以便进行 全社会和国际间的流通和交换。
半导体前端工艺与后端工艺

半导体前端工艺与后端工艺这半导体啊,在如今这科技日新月异的时代,那可是顶重要的物件儿。
您就瞧瞧身边那些个五花八门的电子产品,啥手机啦、电脑啦,哪一个离得开半导体哟!而半导体的制造过程,那就像是一场精心编排的大戏,前端工艺和后端工艺,那就是这出戏里的两个重头角色。
先说这前端工艺,那可是半导体诞生的摇篮。
就好比盖房子打地基,这地基要是不扎实,后面的房子能结实吗?这前端工艺啊,主要就是在那晶圆片上搞事情。
晶圆片您知道吧?就是一块儿圆圆、薄薄、亮晶晶的硅片。
工程师们在这上头一层一层地加料、刻蚀、掺杂,就跟绣花似的,精细着呢!比如说光刻这一步,那可真是个技术活。
得用专门的光刻机,把设计好的电路图案,像盖章一样印到晶圆片上。
这要求精度高得吓人,差一丝一毫都不行。
就好比您纳鞋底,针脚歪了一点儿,这鞋就不舒坦。
再说说掺杂,这也是前端工艺里的关键一招。
就像是给这晶圆片加点“佐料”,让它具备特定的电学性能。
这“佐料”加得好不好,直接影响着半导体的性能。
您想想,要是这“佐料”加错了或者加少了,那不就成了一锅夹生饭嘛!说完前端工艺,咱再瞅瞅后端工艺。
这后端工艺啊,就像是给新生儿打扮梳妆,让它能漂漂亮亮地出门见人。
经过前端工艺制造出来的晶圆片,上面有成千上万个小小的芯片,这后端工艺就得把这些芯片一个一个地切割、封装、测试。
切割这事儿,您可别小瞧。
得小心翼翼地,不能把芯片给弄伤了。
封装呢,就像是给芯片穿上一层防护服,保护它不受外界的干扰和损伤。
而且这封装的形式也有好多,有塑料封装、陶瓷封装,各有各的用处。
测试这一步,那更是重中之重。
得把每个芯片都好好检查一遍,看看性能是不是达标,有没有啥毛病。
这就好比菜市场挑菜,得把好的留下,坏的扔掉。
只有经过了这层层筛选和考验的芯片,才能被送到市场上,装到各种电子产品里,为咱们的生活服务。
您瞧瞧,这半导体的前端工艺和后端工艺,哪一个都不简单,哪一个都容不得马虎。
少了哪一步,这半导体都没法发挥它的大作用。
- 1、下载文档前请自行甄别文档内容的完整性,平台不提供额外的编辑、内容补充、找答案等附加服务。
- 2、"仅部分预览"的文档,不可在线预览部分如存在完整性等问题,可反馈申请退款(可完整预览的文档不适用该条件!)。
- 3、如文档侵犯您的权益,请联系客服反馈,我们会尽快为您处理(人工客服工作时间:9:00-18:30)。
7.4 铜互连工艺
7.4.1 阻挡层和铜仔晶层 7.4.2电镀 7.4.3 CMP
Zhao
铜互连带来的挑战-铜扩散阻挡层
1)铜在SiO2中极易扩散,造成对硅器件的沾污: 增加SiO2的漏电流 增加结漏电流 降低了击穿电压
2)铜极容易氧化和被腐蚀; 3)铜与low-k间的粘附性很差。 要实现铜互连必须找到一种扩散阻挡层,将铜约束在互连结构中 ,同时实现防止铜的氧化或腐蚀、改善与介质的粘附性。
铜/Low-K可以满足器件小型化的要求
从90纳米技术代开始,铜/low-k的材料组合成为必须。 采用铜/low-k互连可大幅减小互连pitch,从而减少互连金属层数。
内容:
7.1 绪论 7.2 摩尔定律对互连材料的要求
7.2.1 电导率和铜互连 7.2.2 电迁移 7.2.3 线间电容和low-k材料
旋涂有机聚合物 旋涂含硅聚合物: hydrogen silsesquioxane (HSQ) 和 methylsilsesquioxane (MSQ).
Black Diamond(I,II,III):
CVD沉积 SiCO matrix + organic species (ATRP= alpha-terpinene) Plasma, 260C
铜的电迁移比铝材料小很多:铜的晶格扩散的激活能为2.2eV, 晶界扩散结合能在0.7到1.2eV之间;而铝分别为1.4eV和0.4-0.8eV.
电迁移:电迁移为什么重要?
电子在导电过程中会撞击导体中的离子,将动量转移给离子从而 推动离子发生缓慢移动。该现象称为电迁移。
在导电过程中,电迁移不断积累,并最 终在导体中产生分散的缺陷。这些缺陷 随后集合成大的空洞,造成断路。 因此,电迁移直接影响电路的可靠性。
7.3 铜互连带来的技术挑战
7.3.1 铜扩散阻挡层 7.3.2 大马士革工艺
7.4 铜互连工艺
7.4.1 阻挡层和铜仔晶层 7.4.2电镀 7.4.3 CMP
Zhao
大马士革结构的填充采用电镀完成
阴极
阳极
连续化学液循环
Zhao
大马士革结构的填充采用电镀完成
以导电扩散阻挡层为电极无法实现完美填充。因此,需要淀积 一层铜籽晶层作为电镀阴极。 铜籽晶层目前仍采用PVD淀积。 电镀可实现完美填充。 电镀工艺与low-k介质有很好的工艺兼容性。 电镀通常可形成(111)方向的织构,因此有利于获得好的电 导率。 电镀有所谓“自退火(self-annealing)效应,可形成大的铜晶体 颗粒,有利于降低材料电阻率。
Thin initial interfacial layer to promote adhesion
Broadband UV radiation, 400C:
由CVD形成两项混合聚合物 紫外光照射使致孔剂挥发, 形成多孔材料。
• Porogen removal pores • Cross-linking • Enhancement of mechanical strength
7.4 铜互连工艺
7.4.1 阻挡层和铜仔晶层 7.4.2电镀 7.4.3 CMP
Zhao
铝互连工艺流程
铝互连由干法刻蚀实现图形化
Zhao
铝互连与铜互连的比较
由于铜无法用干法刻蚀实现图形化,铜互连采用镶嵌工艺, 也称为大马士革工艺(Damascene). Zhao
第一层铜互连工艺流程(metal-1): 单大马士革工艺(single damascene)
国际半导体技术路线图 2002年-互连
Zhao 90纳米之前采用铝互连,90纳米(~1998年)引入铜互连。
内容:
7.1 绪论 7.2 摩尔定律对互连材料的要求
7.2.1 电导率和铜互连 7.2.2 电迁移 7.2.3 线间电容和low-k材料
7.5 铜互连发展状和趋势
7.5.1 22纳米以下的新挑战 深宽比不断增加 阻挡层厚度极限 PVD的局限性 7.5.2 正在进行中的研发 PVD 工艺优化 新型阻挡层 籽晶修复层 自对准阻挡层 7.5.3 铜/钨混合接触和铜接触 7.5.4 结语
3nm layer 4nm layer 1E-16
D D 0 exp(Q / kT )
D (cm /s)
2
1E-17
Q=2.21eV=213 (KJ/mole) D =6.3X10 (cm /sec)
1E-18 13.5
o -3 2
Ta
14.0
14.5
15.0 1/kT (1/eV)
15.5
16.0
16.5
C. Zhao et. al. Microelectronic Engineering 84 (2007) 2669–2674
实验表明Cu在金属Ta和TaN薄膜中的扩散激活能很高,完全 满足扩散阻挡层的要求。 Zhao
内容:
7.1 绪论 7.2 摩尔定律对互连材料的要求
7.2.1 电导率和铜互连 7.2.2 电迁移 7.2.3 线间电容和low-k材料
Zhao
双大马士革工艺(Dual damascene)
Zhao
Zhao
Zhao
金属1 通孔1 金属1 通孔1 金属1 通孔1 金属1 通孔1 金属1 通孔1 金属1 通孔1 金属1 通孔1 金属1 通孔1 金属1 接触
Zhao
内容:
7.1 绪论 7.2 摩尔定律对互连材料的要求
7.2.1 电导率和铜互连 7.2.2 电迁移 7.2.3 线间电容和low-k材料
7.3 铜互连带来的技术挑战
7.3.1 铜扩散阻挡层 7.3.2 大马士革工艺
7.4 铜互连工艺
7.4.1 阻挡层和铜仔晶层 7.4.2电镀 7.4.3 CMP
Zhao
寄生电阻和寄生电容造成的延迟
寄生电阻
RC delay
寄生电容
Rvia 1 Rmetal 1
Cmetal
Zhao
Why Cu?电阻优势
内容:
7.1 绪论 7.2 摩尔定律对互连材料的要求
7.2.1 电导率和铜互连 7.2.2 电迁移 7.2.3 线间电容和low-k材料
7.5 铜互连发展现状和趋势
7.5.1 22纳米以下的新挑战 深宽比不断增加 阻挡层厚度极限 PVD的局限性 7.5.2 正在进行中的研发 PVD 工艺优化 新型阻挡层 籽晶修复层 自对准阻挡层 7.5.3 铜/钨混合接触和铜接触 7.5.4 结语
7.5 铜互连发展现状和趋势
7.5.1 22纳米以下的新挑战 深宽比不断增加 阻挡层厚度极限 PVD的局限性 7.5.2 正在进行中的研发 PVD 工艺优化 新型阻挡层 籽晶修复层 自对准阻挡层 7.5.3 铜/钨混合接触和铜接触 7.5.4 结语
7.3 铜互连带来的技术挑战
7.3.1 铜扩散阻挡层 7.3.2 大马士革工艺
7.4 铜互连工艺
7.4.1 阻挡层和铜仔晶层 7.4.2电镀 7.4.3 CMP
Zhao
CMOS 工艺制程中的互连制程
金属1 通孔1 金属1 通孔1 金属1 通孔1 金属1 通孔1 金属1 通孔1 金属1 通孔1 金属1 通孔1 金属1 通孔1 金属1 接触
集成电路工艺中对光刻要 求最高的是Metal1. 通常metal1的pitch为一 个技术代的CD的两倍。 出于对CMOS电路寄生电 阻控制的考虑,需要采用高 电导率材料。 出于对CMOS电路寄生电 容的考虑,互连线之间的介 电材料需采用低介电常数材 料。 出于提高可靠性的考虑, 需控制互连线的电迁移。 90nm前为铝互连,之后 Zhao 为铜/low-k互连。
7.4 铜互连工艺
7.4.1 阻挡层和铜仔晶层 7.4.2电镀 7.4.3 CMP
Zhao
PVD Ta/TaN 扩散阻挡层和铜籽晶层
PVD Cu 籽晶层(seed) PVD Ta/TaN Cu seed Ta TaN 介质 扩散阻挡层通常采用Ta和TaN双层结构: Ta靠近铜以获得大晶粒的铜仔晶层, TaN靠近介质材料以改善与介质的粘合力。
7.5 铜互连发展现状和趋势
7.5.1 22纳米以下的新挑战 深宽比不断增加 阻挡层厚度极限 PVD的局限性 7.5.2 正在进行中的研发 PVD 工艺优化 新型阻挡层 籽晶修复层 自对准阻挡层 7.5.3 铜/钨混合接触和铜接触 7.5.4 结语
7.3 铜互连带来的技术挑战
7.3.1 铜扩散阻挡层 7.3.2 大马士革工艺
PVD Ta/TaN 扩散阻挡层和铜籽晶层 组合设备
例如: 应用材料 Endura 包含一系列 不同腔室: Degas Preclean Ta/TaN barrier Cu seed 等。
原子层沉积(ALD) TaN 扩散阻挡层
PVD 扩散阻挡层 的保型性差。易 造成电镀中形成 孔洞。
ALD TaN做为扩散阻挡层具有保型性高的优点。但ALD TaN Zhao 有电阻率过高的缺点。因此,提高PVD的保型性仍是研发重点。
7.3 铜互连带来的技术挑战
7.3.1 铜扩散阻挡层 7.3.2 大马士革工艺
7.4 铜互连工艺
7.4.1 阻挡层和铜仔晶层 7.4.2电镀 7.4.3 CMP
Zhao
内容:
7.1 绪论 7.2 摩尔定律对互连材料的要求
7.2.1 电导率和铜互连 7.2.2 电迁移 7.2.3 线间电容和low-k材料
7.5 铜互连发展现状和趋势
7.5.1 22纳米以下的新挑战 深宽比不断增加 阻挡层厚度极限 PVD的局限性 7.5.2 正在进行中的研发 PVD 工艺优化 新型阻挡层 籽晶修复层 自对准阻挡层 7.5.3 铜/钨混合接触和铜接触 7.5.4 结语
7.3 铜互连带来的技术挑战
7.3.1 铜扩散阻挡层 7.3.2 大马士革工艺