基于Minitab的响应曲面实验设计
合集下载
基于Minitab的响应曲面实验设计

-0.011125
-0.008787 -0.016813 -0.114690 -0.020865 -0.134415 0.028825 -0.043925 0.010250
0.002902
0.002902 0.002902 0.003999 0.003999 0.003999 0.004103 0.004103 0.00410111250 2 0.114690 A 0.0288250 B 0.0439250 C Y A 0.00878750 2 0.0208650 B 0.0288250 A 0.0102500 C YB Y 0.0168125 2 0.134415 C 0.0439250 A 0.0102500 B C
-3.834
-3.029 -5.794 -28.676 -5.217 -33.608 7.025 -10.705 2.498
0.006
0.019 0.001 0.000 0.001 0.000 0.000 0.000 0.041
R-Sq=99.70% R-Sq(预测)=96.26% R-Sq(调整)=99.32%
优化图
等值线图 曲面图
结论
该实验结果表明采用浓硫酸法将黑木耳多糖进行硫酸 化修饰确实可行。当反应时间和温度一定时,硫酸化多糖 的取代度随反应试剂中的浓硫酸正丁醇的比列呈现先升高 后减少的趋势,原因可能是由增加了浓硫酸的用量,使黑 木耳多糖降解。当其他条件不变,随着反应温度的升高, 样品的硫酸化取代度先升高后降低,原因可能是温度的升 高有利于反应的进行,但在酸性条件下,温度过高会使黑 木耳多糖降解。因此,在响应曲面设计的试验结果的基础 上确定黑木耳多糖硫酸化最佳条件为:浓硫酸与正丁醇的 体积比2.94:1,温度为-2.60℃,反应时间1.43h。
响应表面试验设计方法及MINITAB优化CCD_BBD ppt课件

响应表面试验设计方法及 MINITAB优化CCD_BBD
➢确信或怀疑因素对指标存在非线性影响; ➢因素个数2-7个,一般不超过4个; ➢所有因素均为计量值数据; ➢试验区域已接近最优区域; ➢基于2水平的全因子正交试验。
响应表面试验设计方法及MINITAB优化 CCD_BBD
➢中心复合试验设计 (central composite design,CCD);
➢Box-Behnken试验设计;
响应表面试验设计方法及 MINITAB优化CCD_BBD
1. 确定因素及水平,注意水平数为2,因素数一般不超 过4个,因素均为计量数据;
2. 创建“中心复合”或“Box-Behnken”设计; 3. 确定试验运行顺序(Display Design); 4. 进行试验并收集数据; 5. 分析试验数据; 6. 优化因素的设置水平。
这种设计失去了序贯性,前一次在立方点上已经做 过的试验结果,在后续的CCI设计中不能继续使用。
对于α值选取的另一个出发点也是有意义的,就是 取α=1,这意味着将轴向点设在立方体的表面上, 同时不改变原来立方体点的设置,这样的设计称为 中心复合表面设计 (central composite facecentered design,CCF)。
响应表面试验设计方法及 MINITAB优化CCD_BBD
将各试验点取在立方体棱的中点上
响应表面试验设计方法及 MINITAB优化CCD_BBD
➢ 在因素相同时,比中心复合设计的试
验次数少; ➢ 没有将所有试验因素同时安排为高水平 的试验组合,对某些有安全要求或特别需 求的试验尤为适用; ➢ 具有近似旋转性,没有序贯性。
响应表面试验设计方法及MINITAB优 化CCD_BBD
响应表面试验设计方法及MINITAB优化CCDBBD共38页文档

5
-1 -1 1 -0.6 -0.6 0.6 -1 -1 1
6
1 -1 1 0.6 -0.6 0.6 1 -1 1
7
-1 1 1 -0.6 0.6 0.6 -1 1 1
8
1 1 1 0.6 0.6 0.6 1 1 1
9 -1.68 0 0 -1 0 0 -1 0 0
10 1.68 0 0 1 0 0 1 0 0
三因子4种响应曲面设计实验点计划表
CCD
CCI
CCF
ABC ABC ABC
1
-1 -1 -1 -0.6 -0.6 -0.6 -1 -1 -1
2
1 -1 -1 0.6 -0.6 -0.6 1 -1 -1
3
-1 1 -1 -0.6 0.6 -0.6 -1 1 -1
4
1 1 -1 0.6 0.6 -0.6 1 1 -1
但由于把区组也作为一个因素来安排, 增加了分析的复杂程度。
序贯试验(顺序试验)
先后分几段完成试验,前次试验设计的点上 做过的试验结果,在后续的试验设计中继续 有用。
旋转性(rotatable)设计
旋转设计具有在设计中心等距点上预测方差 恒定的性质,这改善了预测精度。
α 的选取
在α 的选取上可以有多种出发点,旋转性是
如果要求进行CCD设计,但又希望试验水平安排不 超过立方体边界,可以将轴向点设置为+1及-1,则 计算机会自动将原CCD缩小到整个立方体内,这种 设计也称为中心复合有界设计(central composite inscribed design,CCI)。
这种设计失去了序贯性,前一次在立方点上已经做 过的试验结果,在后续的CCI设计中不能继续使用。
11
minitab实验之试验设计(DOC 64页)

步骤2:拟合选定模型
按照上图的试验计划进行试验,将结果填入上表的最后一列,则可以得到试验的结果数据(数据文件:DOE_热处理(全因)),如下:
拟合选定模型的主要任务是根据整个试验的目的,选定一个数学模型。通常首先可以选定“全模型”,就是在模型中包含全部因子的主效应及全部因子的二阶交互效应。在经过细致的分析之后,如果发现某些主效应和二阶交互效应不显著,则在下次选定模型的时候,应该将不显著的主效应和二阶交互效应删除。
实验内容和步骤:
实验之一:全因子试验设计
:例:改进热处理工艺提高钢板断裂强度问题。合金钢板经热处理后将提高其断裂其抗断裂性能,但工艺参数的选择是个复杂的问题。我们希望考虑可能影响断裂强度的4个因子,确认哪些因子影响确实是显著的,进而确定出最佳工艺条件。这几个因子及其试验水平如下:
A:加热温度,低水平:820,高水平:860(摄氏度)
在实际工作中,常常要研究响应变量Y是如何依赖于自变量,进而能找到自变量的设置使得响应变量得到最佳值(望大、望小或望目)。如果自变量的个数较少(通常不超过3个),则响应曲面方法(response surface methodology,RSM)是最好的方法之一,本方法特别适合于响应变量望大或望小的情形。通常的做法是:先用2水平因子试验的数据,拟合一个线性回归方程(可以包含交叉乘积项),如果发现有弯曲的趋势,则希望拟合一个含二次项的回归方程。其一般模型是(以两个自变量为例):
进行2水平全因子设计时,全因子试验的总试验次数将随着因子个数的增加而急剧增加,例如,6个因子就需要64次试验。但是仔细分析所获得的结果可以看出,建立的6因子回归方程包括下列一些项:常数项、主效应项有6项、二阶交互作用项15项、三阶交互项20项,…,6阶交互项1项,除了常数项、主效应项和二阶交互项以外,共有42项是3阶以及3阶以上的交互作用项,而这些项实际上已无具体的意义了。部分因子试验就是在这种思想下诞生的,它可以使用在因子个数较多,但只需要分析各因子和2阶交互效应是否显著,并不需要考虑高阶的交互效应,这使得试验次数大大减少。
按照上图的试验计划进行试验,将结果填入上表的最后一列,则可以得到试验的结果数据(数据文件:DOE_热处理(全因)),如下:
拟合选定模型的主要任务是根据整个试验的目的,选定一个数学模型。通常首先可以选定“全模型”,就是在模型中包含全部因子的主效应及全部因子的二阶交互效应。在经过细致的分析之后,如果发现某些主效应和二阶交互效应不显著,则在下次选定模型的时候,应该将不显著的主效应和二阶交互效应删除。
实验内容和步骤:
实验之一:全因子试验设计
:例:改进热处理工艺提高钢板断裂强度问题。合金钢板经热处理后将提高其断裂其抗断裂性能,但工艺参数的选择是个复杂的问题。我们希望考虑可能影响断裂强度的4个因子,确认哪些因子影响确实是显著的,进而确定出最佳工艺条件。这几个因子及其试验水平如下:
A:加热温度,低水平:820,高水平:860(摄氏度)
在实际工作中,常常要研究响应变量Y是如何依赖于自变量,进而能找到自变量的设置使得响应变量得到最佳值(望大、望小或望目)。如果自变量的个数较少(通常不超过3个),则响应曲面方法(response surface methodology,RSM)是最好的方法之一,本方法特别适合于响应变量望大或望小的情形。通常的做法是:先用2水平因子试验的数据,拟合一个线性回归方程(可以包含交叉乘积项),如果发现有弯曲的趋势,则希望拟合一个含二次项的回归方程。其一般模型是(以两个自变量为例):
进行2水平全因子设计时,全因子试验的总试验次数将随着因子个数的增加而急剧增加,例如,6个因子就需要64次试验。但是仔细分析所获得的结果可以看出,建立的6因子回归方程包括下列一些项:常数项、主效应项有6项、二阶交互作用项15项、三阶交互项20项,…,6阶交互项1项,除了常数项、主效应项和二阶交互项以外,共有42项是3阶以及3阶以上的交互作用项,而这些项实际上已无具体的意义了。部分因子试验就是在这种思想下诞生的,它可以使用在因子个数较多,但只需要分析各因子和2阶交互效应是否显著,并不需要考虑高阶的交互效应,这使得试验次数大大减少。
minitab部分因子设计,响应面设计,参数设计

2.实验因子的选择
对于这批数据按全因子试验进行分析,具体操作为:选择[统计]=>[DOE]=>[因子]=>[分析因子设计],打开分析因子设计对话框。首先将全部备选项列入模型,删除在模型中包括中心点,在“图形”中的残差与变量下将压力和温度选入进去。得到的结果如下:
纯度的效应和系数的估计(已编码单位)
项效应系数系数标准误T P
从残差与各变量的图也验证了存在严重的弯曲现象。这些都表明,对响应变量单纯地拟合一阶线性方程已经不够了,需要再补充些“星号点”,构成一个完整的响应曲面设计,拟合一个含二阶项的方程就可能问题了。补充的4个星号点的实验结果见数据表:DOE_烧碱纯度(响应2)。
下面对全部11个点构成的中心复合序贯设计进行分析,拟合一个完整的响应曲面模型。分析如下:
(2)看删减后的模型是否比原来的有所改进。
全模型
变化
删减模型
R-Sq
99.35%
减小
99.34%
R-Sq(调整)
98.70%
增大
98.91%
S
0.181900
减小
0.166665
R-Sq(预测)
97.27%
增大
97.85%
PRESS
0.693677
减小
0.546550
由于模型项缺少了一项,R-Sq通常会有所降低,但关键要看调整的R-Sq(调整)是否有所提高,s值是否有所降低,预测残差平方和PRESS是否有所降低,R-Sq(预测)是否有所提高。从表中来看,均符合上述要求,表明删除了不显著的交互作用后,回归的效果更好了。
看方差分析表中的失拟现象,本例中,失拟项对应的P值为0.747,明显大于显著性水平0.05,接受原假设,认为本模型中不存在失拟现象。
对于这批数据按全因子试验进行分析,具体操作为:选择[统计]=>[DOE]=>[因子]=>[分析因子设计],打开分析因子设计对话框。首先将全部备选项列入模型,删除在模型中包括中心点,在“图形”中的残差与变量下将压力和温度选入进去。得到的结果如下:
纯度的效应和系数的估计(已编码单位)
项效应系数系数标准误T P
从残差与各变量的图也验证了存在严重的弯曲现象。这些都表明,对响应变量单纯地拟合一阶线性方程已经不够了,需要再补充些“星号点”,构成一个完整的响应曲面设计,拟合一个含二阶项的方程就可能问题了。补充的4个星号点的实验结果见数据表:DOE_烧碱纯度(响应2)。
下面对全部11个点构成的中心复合序贯设计进行分析,拟合一个完整的响应曲面模型。分析如下:
(2)看删减后的模型是否比原来的有所改进。
全模型
变化
删减模型
R-Sq
99.35%
减小
99.34%
R-Sq(调整)
98.70%
增大
98.91%
S
0.181900
减小
0.166665
R-Sq(预测)
97.27%
增大
97.85%
PRESS
0.693677
减小
0.546550
由于模型项缺少了一项,R-Sq通常会有所降低,但关键要看调整的R-Sq(调整)是否有所提高,s值是否有所降低,预测残差平方和PRESS是否有所降低,R-Sq(预测)是否有所提高。从表中来看,均符合上述要求,表明删除了不显著的交互作用后,回归的效果更好了。
看方差分析表中的失拟现象,本例中,失拟项对应的P值为0.747,明显大于显著性水平0.05,接受原假设,认为本模型中不存在失拟现象。
响应面法和实验设计软件Minitab 及 Design-Expert介绍

2. 创建“中心复合”或“Box-Behnken”设计; 3. 确定试验运行顺序(Display Design); 4. 进行试验并收集数据; 5. 分析试验数据; 6. 优化因素的设置水平。
2 中心复合试验设计
基本概念
立方点 轴向点 中心点 区组 序贯试验 旋转性
立方点(cube point)
响应面优化法的不足
• 响应面优化的前提是:设计的实验点应包括最佳的实
验条件,如果实验点的选取不当,使用响应面优化法 是不能得到很好的优化结果的。因而,在使用响应面 优化法之前,应当确立合理的实验的各因素与水平。
响应面法的适用范围
确信或怀疑因素对指标存在非线性影响; 因素个数2-7个,一般不超过4个; 所有因素均为计量值数据; 试验区域已接近最优区域; 基于2水平的全因子正交试验。
11
0 -1.68 0 0 -1 0 0 -1 0
12
0 1.68 0 0 1 0 0 1 0
13
0 0 -1.68 0 0 -1 0 0 -1
14
0 0 1.68 0 0 1 0 0 1
15
0 0 0 0 0 00 0 0
16
0 0 0 0 0 00 0 0
17
0 0 0 0 0 00 0 0
18
Box-Behnken Design
Box-Behnken Design,简称BBD,也是响应 面优化法常用的实验设计方法,其设计表安排 以三因素为例(三因素用A、B、C表示),见下 页表,其中 0 是中心点,+, -分别是相应的高 值和低值。
响应面法的实验设计一般步骤
1. 确定因素及水平,注意水平数为2,因素数一般不超 过4个,因素均为计量数据;
2 中心复合试验设计
基本概念
立方点 轴向点 中心点 区组 序贯试验 旋转性
立方点(cube point)
响应面优化法的不足
• 响应面优化的前提是:设计的实验点应包括最佳的实
验条件,如果实验点的选取不当,使用响应面优化法 是不能得到很好的优化结果的。因而,在使用响应面 优化法之前,应当确立合理的实验的各因素与水平。
响应面法的适用范围
确信或怀疑因素对指标存在非线性影响; 因素个数2-7个,一般不超过4个; 所有因素均为计量值数据; 试验区域已接近最优区域; 基于2水平的全因子正交试验。
11
0 -1.68 0 0 -1 0 0 -1 0
12
0 1.68 0 0 1 0 0 1 0
13
0 0 -1.68 0 0 -1 0 0 -1
14
0 0 1.68 0 0 1 0 0 1
15
0 0 0 0 0 00 0 0
16
0 0 0 0 0 00 0 0
17
0 0 0 0 0 00 0 0
18
Box-Behnken Design
Box-Behnken Design,简称BBD,也是响应 面优化法常用的实验设计方法,其设计表安排 以三因素为例(三因素用A、B、C表示),见下 页表,其中 0 是中心点,+, -分别是相应的高 值和低值。
响应面法的实验设计一般步骤
1. 确定因素及水平,注意水平数为2,因素数一般不超 过4个,因素均为计量数据;
响应面法和实验设计软件Minitab及DesignExpert简介

中心点,亦即设计中心,表示在图上,坐标 皆为0。
三因素下的立方点、轴向点和中心点
区组(block)
也叫块。设计包含正交模块,正交模块 可以允许独立评估模型中的各项及模块 影响,并使误差最小化。
但由于把区组也作为一个因素来安排, 增加了分析的复杂程度。
序贯试验(顺序试验)
先后分几段完成试验,前次试验设计的点上 做过的试验结果,在后续的试验设计中继续 有用。
响应面法的分类
中心复合试验设计 (central composite design,CCD);
Box-Behnken试验设计;
中心复合试验设计
中心复合试验设计也称为星点设计。其设 计表是在两水平析因设计的基础上加上极值点 和中心点构成的,通常实验表是以代码的形式 编排的, 实验时再转化为实际操作值,(一般 水平取值为 0, ±1, ±α , 其中 0 为中 值, α 为极值, α =F*(1/ 4 )
按上述公式选定的α 值来安排中心复合试
验设计(CCD)是最典型的情形,它可以实 现试验的序贯性,这种CCD设计特称中心 复合序贯设计(central composite circumscribed design,CCC),它是CCD中 最常用的一种。
如果要求进行CCD设计,但又希望试验水平安排不 超过立方体边界,可以将轴向点设置为+1及-1,则 计算机会自动将原CCD缩小到整个立方体内,这种 设计也称为中心复合有界设计(central composite inscribed design,CCI)。
响应面法和实验设计软件 Minitab、Design-Expert简介
1.响应面法 2.实验设计软件 Minitab 3.实验设计软件 Design-Expert
三因素下的立方点、轴向点和中心点
区组(block)
也叫块。设计包含正交模块,正交模块 可以允许独立评估模型中的各项及模块 影响,并使误差最小化。
但由于把区组也作为一个因素来安排, 增加了分析的复杂程度。
序贯试验(顺序试验)
先后分几段完成试验,前次试验设计的点上 做过的试验结果,在后续的试验设计中继续 有用。
响应面法的分类
中心复合试验设计 (central composite design,CCD);
Box-Behnken试验设计;
中心复合试验设计
中心复合试验设计也称为星点设计。其设 计表是在两水平析因设计的基础上加上极值点 和中心点构成的,通常实验表是以代码的形式 编排的, 实验时再转化为实际操作值,(一般 水平取值为 0, ±1, ±α , 其中 0 为中 值, α 为极值, α =F*(1/ 4 )
按上述公式选定的α 值来安排中心复合试
验设计(CCD)是最典型的情形,它可以实 现试验的序贯性,这种CCD设计特称中心 复合序贯设计(central composite circumscribed design,CCC),它是CCD中 最常用的一种。
如果要求进行CCD设计,但又希望试验水平安排不 超过立方体边界,可以将轴向点设置为+1及-1,则 计算机会自动将原CCD缩小到整个立方体内,这种 设计也称为中心复合有界设计(central composite inscribed design,CCI)。
响应面法和实验设计软件 Minitab、Design-Expert简介
1.响应面法 2.实验设计软件 Minitab 3.实验设计软件 Design-Expert
响应表面试验设计及MINITAB优化

但由于把区组也作为一个因素来安排, 增加了分析的复杂程度。
序贯试验(顺序试验)
先后分几段完成试验,前次试验设计的点上 做过的试验结果,在后续的试验设计中继续 有用。
旋转性(rotatable)设计
旋转设计具有在设计中心等距点上预测方差 恒定的性质,这改善了预测精度。
α的选取
在α的选取上可以有多种出发点,旋转性是
适用范围
➢确信或怀疑因素对指标存在非线性影响; ➢因素个数2-7个,一般不超过4个; ➢所有因素均为计量值数据; ➢试验区域已接近最优区域; ➢基于2水平的全因子正交试验。
方法分类
➢中心复合试验设计 (central composite design,CCD); ➢Box-Behnken试验设计;
除一个坐标为+α或-α外,其余坐标皆为0。
在k个因素的情况下,共有2k个轴向点。
中心点(center point)
中心点,亦即设计中心,表示在图上,坐标 皆为0。
三因素下的立方点、轴向点和中心点
区组(block)
也叫块。设计包含正交模块,正交模块 可以允许独立评估模型中的各项及模块 影响,并使误差最小化。
三因子4种响应曲面设计实验点计划表
CCD
CCI
CCF
ABC ABC ABC
1
-1 -1 -1 -0.6 -0.6 -0.6 -1 -1 -1
2
1 -1 -1 0.6 -0.6 -0.6 1 -1 -1
3
-1 1 -1 -0.6 0.6 -0.6 -1 1 -1
4
1 1 -1 0.6 0.6 -0.6 1 1 -1
总之,当时间和资源条件都允许时,应尽 可能按推荐的Nc个数去安排试验,设计结 果和推测出的最佳点都比较可信。实在需 要减少试验次数时,中心点至少也要2-5 次。
序贯试验(顺序试验)
先后分几段完成试验,前次试验设计的点上 做过的试验结果,在后续的试验设计中继续 有用。
旋转性(rotatable)设计
旋转设计具有在设计中心等距点上预测方差 恒定的性质,这改善了预测精度。
α的选取
在α的选取上可以有多种出发点,旋转性是
适用范围
➢确信或怀疑因素对指标存在非线性影响; ➢因素个数2-7个,一般不超过4个; ➢所有因素均为计量值数据; ➢试验区域已接近最优区域; ➢基于2水平的全因子正交试验。
方法分类
➢中心复合试验设计 (central composite design,CCD); ➢Box-Behnken试验设计;
除一个坐标为+α或-α外,其余坐标皆为0。
在k个因素的情况下,共有2k个轴向点。
中心点(center point)
中心点,亦即设计中心,表示在图上,坐标 皆为0。
三因素下的立方点、轴向点和中心点
区组(block)
也叫块。设计包含正交模块,正交模块 可以允许独立评估模型中的各项及模块 影响,并使误差最小化。
三因子4种响应曲面设计实验点计划表
CCD
CCI
CCF
ABC ABC ABC
1
-1 -1 -1 -0.6 -0.6 -0.6 -1 -1 -1
2
1 -1 -1 0.6 -0.6 -0.6 1 -1 -1
3
-1 1 -1 -0.6 0.6 -0.6 -1 1 -1
4
1 1 -1 0.6 0.6 -0.6 1 1 -1
总之,当时间和资源条件都允许时,应尽 可能按推荐的Nc个数去安排试验,设计结 果和推测出的最佳点都比较可信。实在需 要减少试验次数时,中心点至少也要2-5 次。
minitab实验之试验设计(2)解读
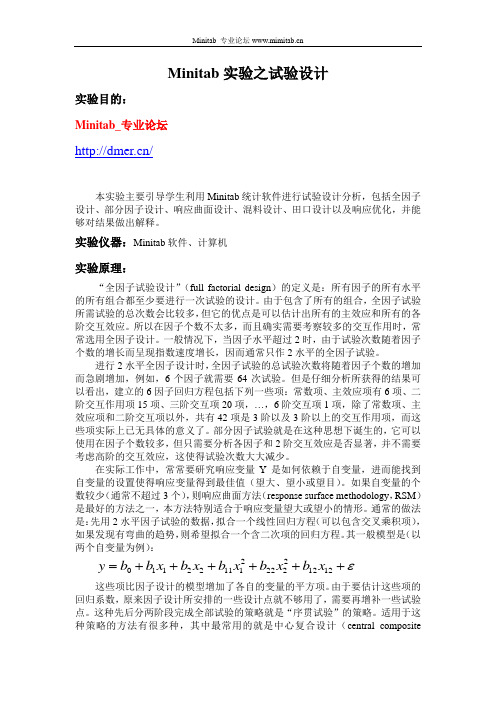
(2)对于预测结果的整体估计。计算结果显示R-Sq和R-Sq(预测)分别为92.49%和53.68%,二者差距比较大;残差误差的SSE为288.14,PRESS为1778.45,两者差距也比较大;说明在本例中,如果使用现在的模型,则有较多的点与模型差距较大,模型应该进一步改进。
分析要点三:分析评估各项效应的显著性。计算结果显示,4个主效应中,加热温度、加热时间和保温时间是显著的,只有转换时间不显著;6个2因子水平交互效应中,只有加热时间*保温时间是显著的。说明本例中还有不显著的自变量和2因子交互作用,改进模型时应该将这些主效应和交互作用删除。
加热温度*保温时间3.062 1.531 1.500 1.02 0.337
加热时间*转换时间1.263 0.631 1.500 0.42 0.685
加热时间*保温时间7.113 3.556 1.500 2.37 0.045
转换时间*保温时间0.837 0.419 1.500 0.28 0.787
S = 6.00146 PRESS = 1778.45
稳健参数设计(robust parameter design)(也称健壮设计、鲁棒设计,简称参数设计)是工程实际问题中很有价值的统计方法。它通过选择可控因子的水平组合来减少一个系统对噪声变化的敏感性,从而达到减小此系统性能波动的目的。过程的输入变量有两类:可控因子和参数因子。可控因子是指一旦选定就保持不变的变量,它包括产品或生产过程设计中的设计参数,而噪声因子是在正常条件下难以控制的变量。在做参数设计时,就是把可控因子的设计当做研究的主要对象,与此同时让噪声因子按照设定的计划从而系统改变其水平的方法来表示正常条件下的变化,最终按照我们预定的望大、望小或望目地目标选出最佳设置。田口玄一博士在参数设计方法方面贡献非常突出,他在设计中引进信噪比的概念,并以此作为评价参数组合优劣的一种测度,因此很多文献和软件都把稳健参数设计方法称为田口方法(Taguchi design)。
分析要点三:分析评估各项效应的显著性。计算结果显示,4个主效应中,加热温度、加热时间和保温时间是显著的,只有转换时间不显著;6个2因子水平交互效应中,只有加热时间*保温时间是显著的。说明本例中还有不显著的自变量和2因子交互作用,改进模型时应该将这些主效应和交互作用删除。
加热温度*保温时间3.062 1.531 1.500 1.02 0.337
加热时间*转换时间1.263 0.631 1.500 0.42 0.685
加热时间*保温时间7.113 3.556 1.500 2.37 0.045
转换时间*保温时间0.837 0.419 1.500 0.28 0.787
S = 6.00146 PRESS = 1778.45
稳健参数设计(robust parameter design)(也称健壮设计、鲁棒设计,简称参数设计)是工程实际问题中很有价值的统计方法。它通过选择可控因子的水平组合来减少一个系统对噪声变化的敏感性,从而达到减小此系统性能波动的目的。过程的输入变量有两类:可控因子和参数因子。可控因子是指一旦选定就保持不变的变量,它包括产品或生产过程设计中的设计参数,而噪声因子是在正常条件下难以控制的变量。在做参数设计时,就是把可控因子的设计当做研究的主要对象,与此同时让噪声因子按照设定的计划从而系统改变其水平的方法来表示正常条件下的变化,最终按照我们预定的望大、望小或望目地目标选出最佳设置。田口玄一博士在参数设计方法方面贡献非常突出,他在设计中引进信噪比的概念,并以此作为评价参数组合优劣的一种测度,因此很多文献和软件都把稳健参数设计方法称为田口方法(Taguchi design)。
响应表面试验设计方法及MINITAB优化(CCD_BBD)

2 中心复合试验设计 基本概念
立方点 轴向点 中心点 区组 序贯试验 旋转性
立方点(cube point) 立方点(cube
立方点,也称立方体点、角点,即2水平对 应的“-1”和“+1”点。各点坐标皆为+1或-1。 在k个因素的情况下,共有2k个立方点
轴向点(axial point) 轴向点(axial
三因子4种响应曲面设计实验点计划表 三因子 种响应曲面设计实验点计划表 CCI CCF C A B C A B C -1 -0.6 -0.6 -0.6 -1 -1 -1 -1 0.6 -0.6 -0.6 1 -1 -1 -1 -0.6 0.6 -0.6 -1 1 -1 -1 0.6 0.6 -0.6 1 1 -1 1 -0.6 -0.6 0.6 -1 -1 1 1 0.6 -0.6 0.6 1 -1 1 1 -0.6 0.6 0.6 -1 1 1 1 0.6 0.6 0.6 1 1 1 0 -1 0 0 -1 0 0 0 1 0 0 1 0 0 0 0 -1 0 0 -1 0 0 0 1 0 0 1 0 -1.68 0 0 -1 0 0 -1 1.68 0 0 1 0 0 1 0 0 0 0 0 0 0 0 0 0 0 0 0 0 0 0 0 0 0 0 0 0 0 0 0 0 0 0 0 0 0 0 0 0 0 0 0 0 0 0 0 0
方法分类
中心复合试验设计 design,CCD); (central composite design,CCD); Box-Behnken试验设计; Box-Behnken试验设计; 试验设计
一般步骤
1. 确定因素及水平,注意水平数为2,因素数一般不超 过4个,因素均为计量数据; 2. 创建“中心复合”或“Box-Behnken”设计; 3. 确定试验运行顺序(Display Design); 4. 进行试验并收集数据; 5. 分析试验数据; 6. 优化因素的设置水平。
minitab正交分析报告、响应分析报告

步骤2:拟合选定模型
按照上图的试验计划进展试验,将结果填入上表的最后一列,如此可以得到试验的结果数据〔数据文件:DOE_热处理〔全因〕〕,如下:
拟合选定模型的主要任务是根据整个试验的目的,选定一个数学模型。通常首先可以选定“全模型〞,就是在模型中包含全部因子的主效应与全部因子的二阶交互效应。在经过细致的分析之后,如果发现某些主效应和二阶交互效应不显著,如此在下次选定模型的时候,应该将不显著的主效应和二阶交互效应删除。
〔2〕看方差分析表中的失拟现象。方差分析表中,失拟项的P值为0.709,无法拒绝原假设,认为回归方程并没有因为漏掉高阶交互作用项而产生失拟现象。
〔3〕看方差分析表中的弯曲项。方差分析表中,弯曲项对应的概率P值0.633,明确无法拒绝原假设,说明本模型中没有弯曲现象。
分析要点二:分析评估回归的总效果
〔1〕两个确定系数R-Sq与R-Sq〔调整〕,计算结果显示,这两个值分别为92.49%和83.11%,二者的差距比拟大,说明模型还有待改良的余地。
〔4〕观察残差对于以各自变量为横轴的散点图,重点观察此散点图中是否有弯曲趋势。
从上面这些图可以看到,这些图形都显示残差是正常的。
步骤4:判断模型是否需要改良
这一步需要综合前面的分析:包括残差诊断和显著性分析。从上面的分析我们得知,在模型中包含不显著项,应该予以删除,所以需要建立新的模型。
选择[统计]=>[DOE]=>[因子]=>[分析因子设计],打开分析因子设计对话框。主要是修改“项〞选项中的设置,在选取的项中将加热温度、加热时间和保温时间保存,其他项皆删去,操作中的其余各项都保持不变。单节确定。
Minitab实验之试验设计
实验目的:
本实验主要引导学生利用Minitab统计软件进展试验设计分析,包括全因子设计、局部因子设计、响应曲面设计、混料设计、田口设计以与响应优化,并能够对结果做出解释。
按照上图的试验计划进展试验,将结果填入上表的最后一列,如此可以得到试验的结果数据〔数据文件:DOE_热处理〔全因〕〕,如下:
拟合选定模型的主要任务是根据整个试验的目的,选定一个数学模型。通常首先可以选定“全模型〞,就是在模型中包含全部因子的主效应与全部因子的二阶交互效应。在经过细致的分析之后,如果发现某些主效应和二阶交互效应不显著,如此在下次选定模型的时候,应该将不显著的主效应和二阶交互效应删除。
〔2〕看方差分析表中的失拟现象。方差分析表中,失拟项的P值为0.709,无法拒绝原假设,认为回归方程并没有因为漏掉高阶交互作用项而产生失拟现象。
〔3〕看方差分析表中的弯曲项。方差分析表中,弯曲项对应的概率P值0.633,明确无法拒绝原假设,说明本模型中没有弯曲现象。
分析要点二:分析评估回归的总效果
〔1〕两个确定系数R-Sq与R-Sq〔调整〕,计算结果显示,这两个值分别为92.49%和83.11%,二者的差距比拟大,说明模型还有待改良的余地。
〔4〕观察残差对于以各自变量为横轴的散点图,重点观察此散点图中是否有弯曲趋势。
从上面这些图可以看到,这些图形都显示残差是正常的。
步骤4:判断模型是否需要改良
这一步需要综合前面的分析:包括残差诊断和显著性分析。从上面的分析我们得知,在模型中包含不显著项,应该予以删除,所以需要建立新的模型。
选择[统计]=>[DOE]=>[因子]=>[分析因子设计],打开分析因子设计对话框。主要是修改“项〞选项中的设置,在选取的项中将加热温度、加热时间和保温时间保存,其他项皆删去,操作中的其余各项都保持不变。单节确定。
Minitab实验之试验设计
实验目的:
本实验主要引导学生利用Minitab统计软件进展试验设计分析,包括全因子设计、局部因子设计、响应曲面设计、混料设计、田口设计以与响应优化,并能够对结果做出解释。
响应面法和实验设计软件Minitab 及 DesignExpert简介

中心点,亦即设计中心,表示在图上,坐标 皆为0。
三因素下的立方点、轴向点和中心点
区组(block)
也叫块。设计包含正交模块,正交模块 可以允许独立评估模型中的各项及模块 影响,并使误差最小化。
但由于把区组也作为一个因素来安排, 增加了分析的复杂程度。
序贯试验(顺序试验)
先后分几段完成试验,前次试验设计的点上 做过的试验结果,在后续的试验设计中继续 有用。
立方点,也称立方体点、角点,即2水平对 应的“-1”和“+1”点。各点坐标皆为+1或-1。 在k个因素的情况下,共有2k个立方点
轴向点(axial point)
轴向点,又称始点、星号点,分布在轴向上。
除一个坐标为+α或-α外,其余坐标皆为0。
在k个因素的情况下,共有2k个轴向点。
中心点(center point)
这样做,每个因素的取值水平只有3个(-1,0,1),而 一般的CCD设计,因素的水平是5个(-α,-1,0,1,α), 这在更换水平较困难的情况下是有意义的。
这种设计失去了旋转性。但
保留了序贯性,即前一次在 立方点上已经做过的试验结 果,在后续的CCF设计中可 以继续使用,可以在二阶回
归中采用。
中心点的个数选择
旋转性(rotatable)设计
旋转设计具有在设计中心等距点上预测方差 恒定的性质,这改善了预测精度。
α的选取
在α的选取上可以有多种出发点,旋转性是
个很有意义的考虑。在k个因素的情况下,应 取
α = 2 k/4
当k=2, α =1.414;当k=3, α =1.682; 当k=4, α =2.000;当k=5, α =2.378
2. 创建“中心复合”或“Box-Behnken”设计; 3. 确定试验运行顺序(Display Design); 4. 进行试验并收集数据; 5. 分析试验数据; 6. 优化因素的设置水平。
三因素下的立方点、轴向点和中心点
区组(block)
也叫块。设计包含正交模块,正交模块 可以允许独立评估模型中的各项及模块 影响,并使误差最小化。
但由于把区组也作为一个因素来安排, 增加了分析的复杂程度。
序贯试验(顺序试验)
先后分几段完成试验,前次试验设计的点上 做过的试验结果,在后续的试验设计中继续 有用。
立方点,也称立方体点、角点,即2水平对 应的“-1”和“+1”点。各点坐标皆为+1或-1。 在k个因素的情况下,共有2k个立方点
轴向点(axial point)
轴向点,又称始点、星号点,分布在轴向上。
除一个坐标为+α或-α外,其余坐标皆为0。
在k个因素的情况下,共有2k个轴向点。
中心点(center point)
这样做,每个因素的取值水平只有3个(-1,0,1),而 一般的CCD设计,因素的水平是5个(-α,-1,0,1,α), 这在更换水平较困难的情况下是有意义的。
这种设计失去了旋转性。但
保留了序贯性,即前一次在 立方点上已经做过的试验结 果,在后续的CCF设计中可 以继续使用,可以在二阶回
归中采用。
中心点的个数选择
旋转性(rotatable)设计
旋转设计具有在设计中心等距点上预测方差 恒定的性质,这改善了预测精度。
α的选取
在α的选取上可以有多种出发点,旋转性是
个很有意义的考虑。在k个因素的情况下,应 取
α = 2 k/4
当k=2, α =1.414;当k=3, α =1.682; 当k=4, α =2.000;当k=5, α =2.378
2. 创建“中心复合”或“Box-Behnken”设计; 3. 确定试验运行顺序(Display Design); 4. 进行试验并收集数据; 5. 分析试验数据; 6. 优化因素的设置水平。
minitab响应曲面设计步骤

minitab响应曲面设计步骤
使用Minitab进行响应曲面设计通常包括以下步骤:
1. 收集数据:根据实验计划,收集实验所需的响应变量和处理变量的数据。
2. 导入数据:在Minitab中导入数据,确保数据格式正确,并进行必要的数据清理。
3. 建立模型:选择适当的响应曲面模型类型,例如线性模型、二次模型或响应曲面模型,并建立模型。
可以使用Minitab的回归分析功能进行模型建立。
4. 调整模型:根据需要,根据统计指标(如p-value)和实际意义,调整模型的显著性与拟合程度。
5. 进行设计:使用Minitab的设计功能,生成响应曲面设计的试验计划。
6. 进行实验:按照设计的试验计划进行实验,并记录响应变量和处理变量的数据。
7. 分析实验数据:使用Minitab进行实验数据的分析,包括模型拟合度分析、主效应和交互效应的显著性检验等。
8. 优化响应变量:利用建立的模型,寻找优化响应变量的最佳处理条件。
9. 验证结果:在实际生产中验证最佳处理条件的效果,并与预测结果进行比较,评估模型的准确性。
注意,以上步骤仅为一般流程,实际应用中可能存在差异,具体步骤也可以根据实际情况进行调整和修改。
- 1、下载文档前请自行甄别文档内容的完整性,平台不提供额外的编辑、内容补充、找答案等附加服务。
- 2、"仅部分预览"的文档,不可在线预览部分如存在完整性等问题,可反馈申请退款(可完整预览的文档不适用该条件!)。
- 3、如文档侵犯您的权益,请联系客服反馈,我们会尽快为您处理(人工客服工作时间:9:00-18:30)。
优化图
等值线图 曲面图
结论
该实验结果表明采用浓硫酸法将黑木耳多糖进行硫酸 化修饰确实可行。当反应时间和温度一定时,硫酸化多糖 的取代度随反应试剂中的浓硫酸正丁醇的比列呈现先升高 后减少的趋势,原因可能是由增加了浓硫酸的用量,使黑 木耳多糖降解。当其他条件不变,随着反应温度的升高, 样品的硫酸化取代度先升高后降低,原因可能是温度的升 高有利于反应的进行,但在酸性条件下,温度过高会使黑 木耳多糖降解。因此,在响应曲面设计的试验结果的基础 上确定黑木耳多糖硫酸化最佳条件为:浓硫酸与正丁醇的 体积比2.94:1,温度为-2.60℃,反应时间1.43h。
项
系数
常量
0.537380
反应时间/h
-0.011125
反应温度/℃
-0.008787
浓硫酸;正丁醇配比
-0.016813
反应时间/h*反应时间/h
-0.114690
反应温度/℃*反应温度/℃
-0.020865
浓硫酸;正丁醇配比*浓硫酸;正丁醇配比,
-0.134415
反应时间/h*反应温度/℃
0.028825
将因素水平规范化
规范变量为:
AA01.5
1
1
BB04
2
24
CC03
3
1
因素水平表
水平
因素
反应时间(A0)//h 反应温度(B0)//℃
浓硫酸:正丁醇 (C0)
-1
0.5
-20
2:1
0
1.5
4
3:1
1
2.5
28
4:1
响应曲面实验设计
分析响应曲面设计
取代度的估计回归系数
系数 0.537380 -0.0111250 -0.00878750 -0.0168125 -0.114690 -0.0208650 -0.134415 0.0288250 -0.0439250 0.0102500
回归方程
Y0.5373 0.08101A 12 0.050087B 80.7 05 10 6C 81 0.114A2 69 0.0020B 82 60.5 10 34C4 2 15 0.028A 82 B0.50043A 92 C 05 .0010B 25 C00
解得
A 0.071293812
B
0.274900323
C 0.061372150
带入(1)(2)(3)还原为实验值
A 0 1 .43
B
0
2 .60
C
0
2 .94
即由回归方程解得的最优化条件为:
反应时间1.43h,反应温度-2.60℃, 浓硫酸:正丁醇配比2.94:1
AdjMS 0.017678 0.001290 0.000990 0.000618 0.002261 0.047925 0.055384 0.001833 0.076073 0.003820 0.003324 0.007718 0.000420 0.000067 0.000121 0.000027
F 262.48 19.15 14.70 9.17 33.57 711.57 822.32 27.22 1129.50 56.72 49.35 114.59 6.24
实验设计
选取硫酸用量、反应温度和反应时间3个因素, 以所制备的黑木耳硫酸酯的硫酸基取代度(DS)为 响应值,用Box—Behnken设计了3因素3水平试 验,根据单因素试验,3个因素的水平值区间一般 在如下范围:温度-20~28℃,反应时间0.5 ~2.5h, 反应试剂配比为2:1~4:1,同时考虑模型设计 要求值须在中心点周围对称分布,故所取因素水 平中心点为反应温度4℃,反应时间1.5h,反应试 剂 (浓硫酸:正丁醇)配比3:1,中心点和中心点 两侧的水平取值代号0、1和-1表示(表1 ),3因素3 水平共17个试验。
反应时间/h*浓硫酸;正丁醇配比
-0.043925
反应温度/℃*浓硫酸;正丁醇配比
0.010250
S=0.00820680 PRESS=0.00596523
R-Sq=99.70% R-Sq(预测)=96.26% R-Sq(调整)=99.32%
系数标准误 0.003670 0.002902 0.002902 0.002902 0.003999 0.003999 0.003999 0.004103 0.004103 0.004103
基于Minitab的响应曲面实验设计
响应曲面法优化黑木耳多糖的硫酸化工艺研究
组员: xxxx
实验介绍
响应曲面法中的Box—Behnken设计是一种寻找多因 素系统中最佳条件的数学统计方法,采用该法可建立连续 变量曲面模型,对影响因子及其交互作用进行评价,确定 最佳水平范围,由于试验组数相对较少,所以广泛应用于 各种生物优化过程中。
16
0.159577
AdjSS 0.159106 0.003869 0.000990 0.000618 0.002261 0.143775 0.055384 0.001833 0.076073 0.011461 0.003324 0.007718 0.000420 0.000471 0.000362 0.000109
T 146.417 -3.834 -3.029 -5.794 -28.676 -5.217 -33.608 7.025 -10.705 2.498
P 0.000 0.006 0.019 0.001 0.000 0.001 0.000 0.000 0.000 0.041
取代度的方差分析
来源 回归 线性 反应时间/h 反应温度/℃ 浓硫酸;正丁醇配比 平方 反应时间/h*反应时间/h 反应温度/℃*反应温度/℃ 浓硫酸;正丁醇配比*浓硫酸;正丁醇配比 交互作用 反应时间/h*反应温度/℃ 反应时间/h*浓硫酸;正丁醇配比 反应温度/℃*浓硫酸;正丁醇配比 残差误差 失拟 纯误差 合计
自由度 SeqSS
9
0.159106
3
0.003869
10.000990 Nhomakorabea1
0.000618
1
0.002261
3
0.143775
1
0.064406
1
0.003296
1
0.076073
3
0.011461
1
0.003324
1
0.007718
1
0.000420
7
0.000471
3
0.000362
4
0.000109
回归方程求极值点
求偏导得
YA 0.011 12 20.5 10 14A6 09 .00 28B 82 0.05403C 9250 YB 0.00872 80 7.05200B 86 0.05208A 82 0.05100C 250 YC 0.016 82 10.2 15 34C4 01 .05 43A 92 0.05100B 2500
实验介绍
硫酸化修饰是指通过化学的方法在多糖的结构中,引入硫 酸根基团。多糖经过硫酸化后,在分子结构引入了带有负电荷 的硫酸根基团,整个分子会显示聚阴离子特性,可以阻断病毒 与机体细胞的吸附,从而增加天然多糖的多种生物学活性。黑 木耳是药食同源真菌,属真菌类担子菌纲,主要分布在我国东 北地区的大、小兴安岭。黑木耳不仅具有很高的营养价值,还 具有多种药理功能。国内外文献报道,黑木耳具有抗氧化、降 血脂 、降血糖 、抗肿瘤和抗凝血、抗菌等活性,但多糖的水溶 性差限制了其活性更好地发挥,而化学修饰可以提高多糖在水 的溶解度,增强其生物活性。研究表明,硫酸化多糖的生物活 性与硫酸化的程度有一定的关系,通过用浓硫酸法对黑木耳多 糖进行修饰,用响应曲面法对黑木耳多糖的硫酸化修饰进行工 艺优化,以期达到提高其硫酸化程度,从而增加黑木耳多糖的 生物活性 。
P 0.000 0.001 0.006 0.019 0.001 0.000 0.000 0.001 0.000 0.000 0.000 0.000 0.041
4.42
0.093
取代度的估计回归系数
项 常量 反应时间/h 反应温度/℃ 浓硫酸;正丁醇配比 反应时间/h*反应时间/h 反应温度/℃*反应温度/℃ 浓硫酸;正丁醇配比*浓硫酸;正丁醇配比 反应时间/h*反应温度/℃ 反应时间/h*浓硫酸;正丁醇配比 反应温度/℃*浓硫酸;正丁醇配比