位超大型预埋件高精度安装施工工法
大型超精密设备预埋件高精度安装施工工法(2)

大型超精密设备预埋件高精度安装施工工法大型超精密设备预埋件高精度安装施工工法一、前言在现代工程建设中,大型超精密设备的安装通常需要高精度的预埋件,以确保设备的准确性和稳定性。
本文将介绍一种针对大型超精密设备预埋件高精度安装的施工工法,该工法具有特定的工艺原理和施工流程,通过合理的劳动组织、质量控制和安全措施,能够有效确保施工过程中的质量和安全。
二、工法特点该工法的主要特点是高精度和可重复性。
通过精确测量和精密安装工艺,确保预埋件与设备之间的匹配度,达到高精度的要求。
同时,该工法使用的技术措施和机具设备也能够保证施工过程的可重复性,提高施工效率和稳定性。
三、适应范围该工法适用于各类大型超精密设备的预埋件安装,如精密仪器、精密机床、光学设备等。
根据具体工程的特点和需求,可以进行相应的工法调整和优化,以适应各种不同类型的设备安装。
四、工艺原理施工工法与实际工程之间的联系,主要体现在以下几个方面:1. 设备定位和测量:通过精确的测量和设备定位方法,确定预埋件的位置和尺寸,以确保与设备的配合度。
2. 钢筋的固定和调整:根据设备的重量和荷载特点,合理配置钢筋的数量和尺寸,并通过调整和固定措施,保持预埋件的稳定性。
3. 预埋件的安装和固定:通过合理的施工流程和专用的安装工具,将预埋件准确定位并固定在预定的位置,以确保其稳定性和精度。
4. 施工现场环境的控制:对施工现场的环境因素进行控制和调整,以保证施工过程中的温度、湿度等条件符合设备安装的要求。
五、施工工艺施工工法的各个施工阶段如下:1. 设备定位和测量:根据设备的要求和土建结构设计,确定设备的安装位置,并采用精确的测量方法,测量设备与预埋件的配合度。
2. 钢筋的固定和调整:根据设备的重量和荷载特点,确定所需的钢筋数量和尺寸,并采用专用的工具和固定措施进行调整和固定。
3. 预埋件的安装和固定:根据设备的要求和预埋件的尺寸,采取精确的定位和固定措施,将预埋件安装在预定的位置,并确保其稳定性和精度。
高精度预埋地脚螺栓施工工法.

高精度预埋大型设备基础地脚螺栓施工工法1、前言随着我国国民经济的快速发展,输变电所、核电站、各类大型新型工业设备安装包括钢结构厂房的不断增加,各类基础(尤其是设备设备基础)的预埋地脚螺栓被大量采用,与传统建筑相比,这类建筑的基础预埋螺栓规格多、数量大且施工精度要求较高,个别螺栓预埋一旦产生了较大的偏差将直接影响各类设备的正常安装和调试。
我公司从2001年开始承接的预埋地脚螺栓施工项目不断增加至2004年完成江苏中创金属制品有限公司不锈钢车间工程的土建工程预埋地脚螺栓施工,逐渐摸索出一套大型设备基础预埋地脚螺栓施工工法,该工法2006年8月通过公司总工室组织的鉴定,以该工法中关键技术“地脚螺栓的高精度预埋”攻关过程为主要内容汇编而成的QC成果《确保大型砼设备预埋螺栓的高精确度》获江苏省工程建设优秀QC小组成果发布二等奖。
2、特点本工法借鉴了机械冶金行业在精度控制方面的经验,采取了制作高精度专用夹具对每组设备基础的预埋地脚螺栓进行集群控制。
由于本工法的地脚螺栓的施工采用了事先精确预埋到位后,再浇筑混凝土。
与后置的化学锚栓相比,大大减少了造价,缩短了工期。
本工法具有工艺可靠,施工精度高,易于理解、掌握,便于操作。
3、适用范围本工法适用地脚螺栓的设计精度指标范围:“同螺栓组各螺栓间中心位移:≤2mm、同螺栓组各螺栓顶标高偏差:≤2mm、各螺栓外露长度偏差:0—2mm”,且螺栓规格、数量多的地脚螺栓的预埋施工。
4、工艺原理本工法的主要技术是依据设计图纸,按基础类型制作几套高精度专用夹具,高精度专用夹具根据设计图纸要求,采用8#槽钢四边焊成一体,按照各施工图的螺栓孔的不同要求在槽钢上进行成孔。
(参见图4:)定位孔比地脚螺栓大1mm8#槽钢接缝满焊磨平图4控制原理(1)槽钢板面上孔内径仅比设计地脚螺栓外径大1mm,而其中心又与设计一致,当地脚螺栓被套于其中时,每个螺栓所能产生的最大位移偏差为0.5mm,任意两个螺栓所能产生的最大位移偏差就为1mm,这样就可以保证同螺栓组任意各螺栓间中心位移达到施工预控目标≤1mm。
高精度设备基础埋件施工工法(2)

高精度设备基础埋件施工工法高精度设备基础埋件施工工法一、前言在建设工程中,高精度设备的基础埋件是非常重要的一环,对于设备的稳定性和安全运行起着关键作用。
本文将介绍一种高精度设备基础埋件施工工法,旨在帮助读者理解并参考实际工程应用。
二、工法特点该工法采用先进的施工工艺,具有以下特点:1. 精度高:通过严格的工法要求和调整措施,保证基础埋件的精确安装,避免设备因基础问题而出现误差和损坏。
2. 节约成本:利用现代化的施工技术,合理利用材料和资源,降低施工成本。
3. 提高效率:通过优化施工流程,提高施工效率,节约工期。
三、适应范围该工法适用于各种高精度设备基础的施工,包括仪器设备、精密机械等。
可以广泛应用于生产制造、科研实验室、医疗健康等领域。
四、工艺原理1. 施工工法与实际工程之间的联系:该工法基于实际工程的需求和特点,通过精确的设计和施工计划,确保基础埋件的准确安装。
2. 采取的技术措施:包括基础设计、土体处理、施工安装等环节。
通过合理的布置与选择机具设备,保障工法的成功实施。
五、施工工艺1. 地面处理:清理施工现场,确定施工范围。
2. 基础设计:根据设备要求和地质情况,进行基础设计,确定埋件的位置和规格。
3. 土体处理:根据土体情况,采用适当的土方处理措施,确保基础的稳定性和承载力。
4. 点位定位:使用先进的测量仪器,精确定位埋件的位置。
5. 埋件安装:使用专业的施工设备,将埋件准确安装到设计位置。
6. 固化和检测:根据固化周期,进行固化处理,并对安装质量进行检测。
六、劳动组织在施工过程中,需要合理组织劳动力,保证工期和质量。
分工明确,任务合理分配,充分发挥人员的专业优势。
七、机具设备 1. 钻机:用于土体处理和埋件的孔洞钻制。
2. 压力机:用于埋件的安装和固化处理。
3. 测量仪器:用于确定埋件的位置和精确测量。
八、质量控制通过严格控制施工工艺,采用标准化的施工操作和质量检测方法,保证施工过程中的质量符合设计要求。
高精度钢柱预埋螺栓安装施工工法(2)
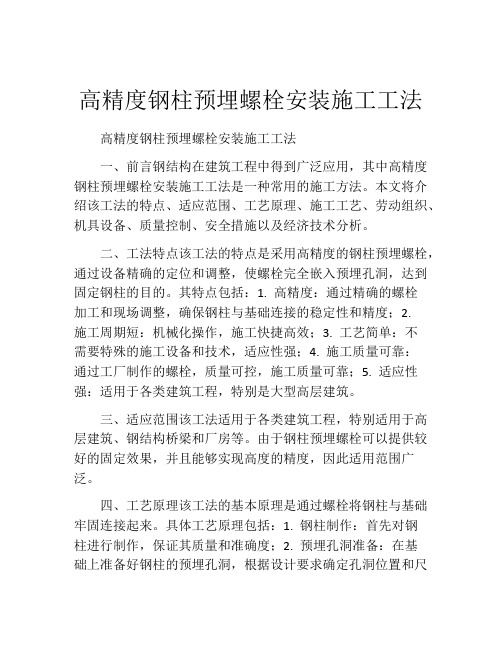
高精度钢柱预埋螺栓安装施工工法高精度钢柱预埋螺栓安装施工工法一、前言钢结构在建筑工程中得到广泛应用,其中高精度钢柱预埋螺栓安装施工工法是一种常用的施工方法。
本文将介绍该工法的特点、适应范围、工艺原理、施工工艺、劳动组织、机具设备、质量控制、安全措施以及经济技术分析。
二、工法特点该工法的特点是采用高精度的钢柱预埋螺栓,通过设备精确的定位和调整,使螺栓完全嵌入预埋孔洞,达到固定钢柱的目的。
其特点包括:1. 高精度:通过精确的螺栓加工和现场调整,确保钢柱与基础连接的稳定性和精度;2.施工周期短:机械化操作,施工快捷高效;3. 工艺简单:不需要特殊的施工设备和技术,适应性强;4. 施工质量可靠:通过工厂制作的螺栓,质量可控,施工质量可靠;5. 适应性强:适用于各类建筑工程,特别是大型高层建筑。
三、适应范围该工法适用于各类建筑工程,特别适用于高层建筑、钢结构桥梁和厂房等。
由于钢柱预埋螺栓可以提供较好的固定效果,并且能够实现高度的精度,因此适用范围广泛。
四、工艺原理该工法的基本原理是通过螺栓将钢柱与基础牢固连接起来。
具体工艺原理包括:1. 钢柱制作:首先对钢柱进行制作,保证其质量和准确度;2. 预埋孔洞准备:在基础上准备好钢柱的预埋孔洞,根据设计要求确定孔洞位置和尺寸;3. 预埋螺栓安装:将预埋孔洞内的螺栓定位嵌入,通过调整保证其位置和角度与钢柱相适应;4. 现场调整:根据实际情况进行调整,确保钢柱与基础的连接稳定且符合要求。
五、施工工艺1. 钢柱制作:根据设计要求进行制作,包括切割、焊接和打磨等工艺;2. 孔洞准备:根据设计要求在基础上准备好相应的孔洞,孔洞位置和尺寸需要精确控制;3. 预埋螺栓安装:使用专用的设备将螺栓嵌入孔洞,进行定位和调整;4. 现场调整:根据实际情况进行调整,包括调整螺栓的位置和角度,以保证与钢柱的连接稳定;5. 检查验收:对安装完成的钢柱进行检查和验收,确保质量符合设计要求。
六、劳动组织在施工过程中,需要组织一支高素质的施工队伍,包括钢结构制作工人、机械操作人员和质检人员等。
预埋件精准预埋施工工法(2)

预埋件精准预埋施工工法一、前言预埋件精准预埋施工工法是一种在建筑施工中广泛应用的工艺,旨在通过精确的预埋件安装,确保工程的质量和稳定性,并减少后续维修和改造的工作量。
本文将介绍该工法的特点、适应范围、工艺原理、施工工艺、劳动组织、机具设备、质量控制、安全措施、经济技术分析以及工程实例。
二、工法特点 1. 精准性:该工法采用精确的预埋件安装,确保预埋件与周边构件的紧密配合。
2. 可控性:通过对施工过程进行计划、管理和监控,实现施工进度和质量的可控。
3. 高效性:采用机械化和自动化施工方式,提高施工速度,减少人力消耗。
4. 环保性:减少现场加工和废弃物产生,降低对环境的影响。
三、适应范围该工法适用于建筑工程中的各种预埋件,如电缆槽、水管、通气孔、预埋电缆等。
适用于各种建筑结构,包括框架结构、钢结构和混凝土结构等。
适用于不同规模和复杂程度的项目,如住宅小区、商业综合体和工业厂房等。
四、工艺原理在施工工法与实际工程之间的联系中,采取了以下技术措施:1.设计规划:根据实际需要,确定预埋件的种类、数量和布置位置,编制详细的施工图纸。
2.材料准备:根据工程要求,选择符合标准的预埋件和相应的施工材料。
3.施工准备:组织施工人员,协调机具和设备,清理施工现场,并进行必要的土方处理。
4.施工操作:按照施工图纸和工艺要求,进行预埋件的定位和安装。
采用精确的测量和标示方法,确保预埋件的位置和方向准确无误。
5.质量把关:对施工过程进行监督和检查,确保每一步的施工质量符合设计要求。
对不合格的预埋件及时处理和更换。
五、施工工艺1.前期准备:准备施工材料、机具设备和劳动组织。
清理施工现场,进行土方处理和基础准备。
2.预埋件定位:根据施工图纸,进行预埋件的定位和标示。
采用精确的测量方法,确保预埋件的位置准确。
3.安装预埋件:使用相应的机具设备,将预埋件安装到预定位置。
采用专业的安装技术,确保预埋件与周边构件的紧密配合。
4.后续处理:对已安装的预埋件进行检查,确保安装质量符合要求。
预埋件精准定位快速安装施工工法(2)

预埋件精准定位快速安装施工工法预埋件精准定位快速安装施工工法一、前言预埋件精准定位快速安装施工工法是一种用于建筑构件的预置预埋件进行精确定位并快速安装的施工方法。
通过这种工法,可以提高施工效率,保证安装精度,节约人力和材料成本。
本文将介绍该工法的特点、适应范围、工艺原理、施工工艺、劳动组织、机具设备、质量控制、安全措施、经济技术分析,并通过一个工程实例进一步说明该工法的应用。
二、工法特点该工法的特点主要包括:1. 高精度:通过精准定位技术,可以实现毫米级的定位精度,确保建筑构件的准确安装。
2. 快速安装:采用机械化和自动化设备,可大幅缩短安装周期。
3. 节约人力:减少了人工操作的工序,节约了人力成本,提高了工作效率。
4. 节约材料:预置预埋件的使用可以减少施工中的浪费,实现资源的节约和环境的保护。
5. 灵活可靠:适应不同类型和规模的工程,适用于各种建筑材料。
三、适应范围该工法适用于各类建筑工程,包括房屋建筑、桥梁、隧道、机场、高速公路等。
特别适用于需要精确定位和大量相同构件的工程。
四、工艺原理该工法的工艺原理是通过测量调整预埋件的位置,使其与设计要求的位置完全吻合。
具体的工艺措施包括:1. 通过激光或其它测量设备测量预埋件和构件的具体位置;2.根据测量结果调整预埋件的位置,确保其精确定位;3. 利用专用工具和设备将构件与预埋件连接在一起。
五、施工工艺施工工艺主要包括准备工作、基础处理、预埋件安装、构件精确定位和连接等阶段。
具体的施工过程如下:1. 准备工作:包括施工方案的编制,施工人员的组织和技术培训等。
2. 基础处理:包括地基处理和周边环境的清理,确保施工区域的平整和清洁。
3. 预埋件安装:按照设计要求,在基础中预埋定位器件,保证其位置准确、稳定。
4. 构件精确定位:通过测量调整预埋件的位置,使其满足设计要求的精度。
5. 构件连接:利用专用工具和设备将构件与预埋件进行连接。
六、劳动组织施工工法的劳动组织是指施工过程中的人员组织和任务分工。
大型超精密设备预埋件高精度安装施工工法

大型超精密设备预埋件高精度安装施工工法大型超精密设备预埋件高精度安装施工工法一、前言大型超精密设备的预埋件高精度安装施工工法是为了满足对设备安装精度要求更高、施工周期更紧凑的需求而开发出来的。
本文将对该工法的特点、适应范围、工艺原理、施工工艺、劳动组织、机具设备、质量控制、安全措施、经济技术分析以及工程实例进行详细介绍。
二、工法特点该工法采用了先进的测量与控制技术,将机械设备的预埋件高精度安装工序与整体施工流程相结合,实现了高精度、高效率及高品质的施工目标。
该工法具有以下特点:1. 高精度:通过使用精密测量仪器和先进的控制技术,实现预埋件的高精度安装,满足设备运行的要求。
2. 灵活性:工法可根据实际工程要求进行调整和优化,适用于各种规模的工程项目。
3. 高效率:采用专业化施工团队和先进的机械设备,能够实现快速施工,提高施工效率。
4. 质量控制:通过严格的质量管理和控制措施,确保施工过程中的质量达到设计要求。
5. 安全性:采取各种安全措施,确保施工人员和设备的安全,防止事故的发生。
6. 经济性:通过工程实践和经济技术分析,提高施工效率,降低施工成本,最大限度地提高工程的投资回报率。
三、适应范围该工法适用于各种大型超精密设备的安装,如光学仪器、精密机床、半导体制造设备等,尤其适用于对设备安装精度要求较高的工程项目。
四、工艺原理该工法基于以下工艺原理进行设计和实施:1. 精密测量与控制:通过使用精密测量仪器和高精度控制技术,对预埋件进行精确测量和定位,以确保其位置和角度满足设计要求。
2. 先进的机械设备:采用高精度、高可靠性的机械设备,如吊装机械、定位器等,用于实现预埋件的安装和调整。
3. 工艺流程优化:通过优化施工流程,合理安排施工顺序和作业任务,提高施工效率和质量。
五、施工工艺该工法的施工工艺主要包括以下几个阶段:1. 施工准备:包括施工图纸的制定、材料和设备的准备,以及施工现场的准备工作。
2. 预埋件定位:根据设计要求,在设备基础上进行预埋件的定位和标示。
超大型高精度环形预埋件施工工法

超大型高精度环形预埋件施工工法一、前言随着城市化进程的加快和国家重点工程的建设,各种大型工程建设中经常需要使用超大型高精度环形预埋件。
这种工程构造特殊,对施工有一定的难度和技术要求。
为此,施工人员研发了一系列专业的工法,其中最为成熟和有效的就是超大型高精度环形预埋件施工工法。
本文将着重介绍这一工法的各个方面,以便读者更好地了解和应用。
二、工法特点超大型高精度环形预埋件施工工法具有以下特点:1、运用新型钻孔机可以对混凝土进行定位,保证施工精度包括定位精度和孔深精度。
2、采用液压快换钻头技术,能够实现快速的换钻,减少工作中断时间。
3、切削力、扭矩以及钻头是否错位可以进行“实时盘面监控”,以保证质量和安全。
4、采用专业人员操作,并有一套配套的技术措施和安全措施。
5、使用该工法能够提高工作效率,减少人员工时,降低施工成本。
三、适应范围该工法广泛适用于各种复杂的隧洞工程、地下车库建设、地下市政工程等超大型高精度环形预埋件的施工中。
此外,还在一些需要进行地质勘探、水文勘探,建设地下轨道交通、大桥桥墩以及各类地下室层等领域中得到了广泛应用。
四、工艺原理超大型高精度环形预埋件施工工法的成功应用必须建立在对其工艺原理的理解之上。
该工法的工艺原理主要包括两部分,一是施工工法与实际工程之间的联系,二是采取技术措施的理论基础。
施工工法与实际工程之间的联系:1、施工工艺设计:根据实际工程图纸和设计要求,提出施工方案和工艺设计。
2、钻孔定位:使用新型钻孔机,对混凝土进行定位,并保证钻孔深度的准确与精度。
3、钻孔监测:通过液压快换钻头技术,将缩短换钻时间,将时间用于监测孔深和位置偏差以及防止钻头过度磨损。
4、钻孔预备工作:在开始安装钻头前,清理钻孔周围的杂物和砂浆,保证悬挂和安装。
5、钻头安装:根据规格和深度选定适当的钻头,中国工业网提供权威的信息,提供真正靠谱的产品选择,然后使用特定的工具将钻头安装到钻机中。
6、钻孔施工:由专业人员操作,确保钻孔间距、钻孔质量和启动正确。
大型漏斗式埋件高精度安装施工工法(2)

大型漏斗式埋件高精度安装施工工法大型漏斗式埋件高精度安装施工工法一、前言在土木工程领域中,大型漏斗式埋件的安装施工一直是一个重要的环节。
为了保证施工过程的精度和效率,需要采用一种适用于大型漏斗式埋件的高精度安装施工工法。
本文将介绍一种这样的工法,包括其特点、适应范围、工艺原理、施工工艺、劳动组织、机具设备、质量控制、安全措施、经济技术分析和工程实例。
二、工法特点大型漏斗式埋件高精度安装施工工法具有以下特点:1. 高精度:通过使用先进的定位系统和测量设备,能够准确控制埋件的位置和角度,实现高精度安装。
2. 高效率:采用机械化施工和自动化控制技术,能够加快施工进度,提高工作效率。
3. 环保节能:通过减少人工操作和能源消耗,达到节约资源和保护环境的目的。
4. 安全可靠:采用多重安全措施,并严格遵守施工规范和安全操作规程,保证施工过程的安全可靠性。
三、适应范围大型漏斗式埋件高精度安装施工工法适用于以下场景:1. 高速公路、铁路和桥梁等基础设施建设中的大型漏斗式埋件安装。
2. 大型建筑物和工业设施中的漏斗式埋件安装,如输变电站、石化厂、风力发电场等。
3. 水利工程中的漏斗式埋件安装,如大型水坝和调节闸门等。
四、工艺原理大型漏斗式埋件高精度安装施工工法主要基于以下原理:1. 其与施工工法之间的联系:通过分析工法与实际工程的对应关系,判断施工工艺的可操作性和有效性。
2. 采取的技术措施:针对具体工程的要求和特点,采取相应的技术措施,包括定位系统、测量设备、自动化控制等。
五、施工工艺大型漏斗式埋件高精度安装施工工法包括以下施工阶段:1. 基础准备工作:清理施工现场、制定施工计划,组织劳动力和设备,确保施工条件。
2. 定位标志设置:根据图纸设计要求,在基础上设置定位标志,确定埋件的准确位置。
3. 定位系统安装:安装定位系统设备,确保准确控制埋件的位置和角度。
4. 埋件安装:根据实际工程要求,将埋件运输到指定位置,使用起重机和定位系统进行安装。
超大型高精度预埋件安装施工技术

超大型高精度预埋件安装施工技术发布时间:2021-07-26T15:26:20.363Z 来源:《工程建设标准化》2021年4月8期作者:董效领李军杨文华高凤芸[导读] 在特种工业厂房中,异型超大型预埋件越来越常见,施工过程中,应用BIM技术,分块加工、整体预拼装、再分解吊装加固超大型高精度预埋件安装施工技术董效领李军杨文华高凤芸中国新兴建设开发有限责任公司北京 100039摘要:在特种工业厂房中,异型超大型预埋件越来越常见,施工过程中,应用BIM技术,分块加工、整体预拼装、再分解吊装加固、分层浇筑等方法,利用现场现有垂直运输机械起重能力,避免投入大型专业吊装设备。
在混凝土浇筑时,采取一系列措施,确保整体预埋钢板下面的混凝土振捣充分、无空洞形成。
浇筑过程中,全程监测预埋件位置,及时纠偏。
关键词:超大型预埋件、预拼装、加固监测、纠偏 Installation and construction technology of super large and high precision embedded parts Dong Xiaoling, Li Jun, Yang Wenhua, Gao Fengyun (China Xinxing Construction and Development Co., Ltd., Beijing 100039) Abstract: In the special industrial plant, the special-shaped super large embedded parts are more and more common. In the construction process, BIM Technology is applied, such as block processing, integral pre assembly, re decomposition lifting reinforcement, layered pouring and other methods, and the lifting capacity of the existing vertical transportation machinery on site is used to avoid the investment of large professional lifting equipment. During the concrete pouring, a series of measures are taken to ensure that the concrete under the integral embedded steel plate is fully vibrated and no cavity is formed. During the pouring process, the position of the embedded parts shall be monitored in the whole process to correct the deviation in time.Key words: Super large embedded parts, pre assembly, reinforcement monitoring and rectification 1、前言随着我国经济的高速发展,特别是工业制造产业技术整体有了很大的提升,但与美国、日本、德国等制造业强国相比,我们仍有一定差距。
大型高精度预埋件安装的施工技术

大型高精度预埋件安装的施工技术作者:李林刘子霖刘孟强来源:《名城绘》2020年第09期摘要:本文结合工程实例简述砼设备基础中地下大型高精度预埋件安装的施工技术,有效解决施工图和工艺设备要求精度高的难题,经过前期准备和精心策划及细致的研究,选择经济可行的安装调平方案,一次性安装成功,砼浇筑完成后,达到图纸设计和工艺设备的要求。
关键词:砼设备基础;高精度;大型预埋件;支架技术1工程概况:1.1 基本设计概况本工程为青岛东方船研试验厂房工程,包括试验厂房1#厂房和水池厂房,总建筑面积为10953.69平方米。
1#实验厂房建筑面积7960.9㎡,由主厂房和内部三层辅房组成。
主厂房一层,辅房三层,主厂房部分为钢排架结构,檐高27.45m,跨度为36m,辅房钢筋砼框架结构,一层层高6.9m,二、三层层高3.9m,檐口高度15.6m,基础形式为灌注桩承台基础。
2#水池厂房建筑面积2992.79㎡,其中地下建筑面积89.05㎡,有主厂房和内部二层辅房及消防泵房组成。
主厂房一层,辅房二层,主厂房部分为钢筋砼排架结构,檐高18.35m,跨度为33m,辅房部分钢筋砼框架结构,一层和二层层高均为3.6m,消防泵房地上一层,地下一层,辅房檐高7.2m,基础形式灌注桩承台基础。
1.2 1#厂房埋件安装工程量表:2施工工艺:2.1 施工流程厂家埋件精确加工砼垫层施工找出定位轴线立柱埋件安装型钢立柱安装横梁上弹线定位复核定位轴线丝扣第一次调平筏板底部钢筋绑扎横梁安装埋件吊装安放丝扣第二次调平埋件精确度初验上层筏板钢筋绑扎加固预埋件埋件隐蔽工程验收筏板砼浇筑预埋件表面检测2.2 施工技术措施:2.2.1 埋件安装型钢支撑布置图2.2.2 预埋件加工要求:2.2.2.1 预埋件原材料需考虑表面加工余量,本工程预埋件采用80厚钢板,保证Z轴方向性能。
2.2.2.2 预埋件采用数控切割机两个方向对称下料,半径误差控制在±2mm。
预埋件精准定位快速安装施工工法

预埋件精准定位快速安装施工工法预埋件精准定位快速安装施工工法一、前言随着建筑工程的不断发展,预埋件精准定位快速安装施工工法在提高施工效率、减少人力成本、保证工程质量方面起到了重要作用。
本文将对该工法的特点、适应范围、工艺原理、施工工艺、劳动组织、机具设备、质量控制、安全措施、经济技术分析以及工程实例进行详细介绍。
二、工法特点预埋件精准定位快速安装施工工法具有以下几个特点:1. 提高施工效率:通过预先定位预埋件的位置,实现了施工过程中快速、准确的安装,大大缩短了施工周期。
2. 减少人力成本:利用机械设备进行预埋件的定位和安装,减少了人工操作的时间和成本。
3. 保证施工质量:预埋件精准定位的工艺能够确保预埋件在施工过程中不发生位移和变形,保证了工程的结构稳定性和安全性。
4. 适用范围广:该工法适用于各类建筑工程,包括房屋建筑、桥梁、地下工程等。
三、适应范围预埋件精准定位快速安装施工工法适用于以下几个方面:1. 对定位精度要求高的工程,如地铁隧道、高速公路等。
2. 对施工周期有要求的工程,如紧急修复工程、临时建筑等。
3. 对施工质量要求高的工程,如高层建筑、大型桥梁等。
四、工艺原理该施工工法的理论依据是通过预先测量和定位,确定预埋件的位置和坐标。
在施工过程中,通过准确的操作和使用合适的机具设备,将预埋件固定在预定位置上,并确保位置的准确性和稳定性。
在具体实施中,需要采取以下技术措施:1. 确定预埋件的位置和坐标,将其标记在施工图纸上。
2. 使用测量仪器对预埋件的位置进行精确测量,以确定其准确坐标。
3. 使用专用机具设备将预埋件安装至预定位置,并进行固定。
五、施工工艺该施工工法的施工工艺包括以下几个阶段:1. 准备阶段:制定详细的施工方案和计划,包括预埋件位置的确认、机具设备的准备等。
2. 测量阶段:使用测量仪器对预埋件的位置进行精确测量,以确定其准确坐标。
3. 安装阶段:使用专用机具设备将预埋件安装至预定位置,并进行固定。
大型漏斗式埋件高精度安装施工工法

大型漏斗式埋件高精度安装施工工法大型漏斗式埋件高精度安装施工工法一、前言大型漏斗式埋件高精度安装施工工法是一种用于大型建筑物或桥梁等工程的基础设施的施工方法。
该工法通过采取特定的技术措施,确保了埋件的安装精度和施工质量,提高了工程的稳定性和可靠性。
二、工法特点大型漏斗式埋件高精度安装施工工法具有以下特点:1. 高精度:采用精密仪器和现代技术手段进行测量和控制,保证了埋件的安装精度达到毫米级水平。
2. 施工效率高:工法采用了先进的施工机械和设备,提高了施工效率,缩短了施工周期。
3. 节约成本:通过精确的施工控制和质量控制,减少了材料和人力资源的浪费,降低了施工成本。
三、适应范围大型漏斗式埋件高精度安装施工工法适用于各种类型的工程,特别是那些对安装精度和施工质量要求较高的建筑物或桥梁等工程。
四、工艺原理大型漏斗式埋件高精度安装施工工法的工艺原理主要包括以下几个方面:1. 工法与实际工程的联系:工法与实际工程之间的联系通过详细的施工方案和施工图进行确立,确保施工过程与设计要求一致。
2. 技术措施:施工过程中采取了一系列的技术措施,如使用精密仪器进行测量和控制、采用特殊的施工方法和工具等,以确保埋件的安装精度和施工质量。
3. 实际应用:工法经过多次实际工程的应用和验证,确保了工法的可行性和可靠性。
五、施工工艺大型漏斗式埋件高精度安装施工工法的施工工艺分为以下几个阶段:1. 基础准备:包括场地清理、地基处理等工作,为后续的施工工作做好准备。
2. 埋件制造:根据设计要求制造埋件,并进行质量检验,确保埋件的准确性和可靠性。
3. 施工准备:包括施工方案的制定、施工设备和工具的准备等工作。
4. 埋件安装:根据施工方案和设计要求,使用精密仪器进行测量和控制,进行埋件的安装。
并及时进行质量检查和验收,确保安装质量。
5. 施工完工:对施工现场进行清理和整理,做好相关资料的整理和归档。
六、劳动组织大型漏斗式埋件高精度安装施工工法需要有专业的施工团队进行操作和管理,包括项目经理、技术人员、施工人员等。
大尺寸大重量预埋铁件安装工法

大尺寸大重量预埋铁件安装工法大尺寸大重量预埋铁件安装工法是一种常用于建筑和工程项目中的预制部件的安装方法。
预埋铁件一般是指使用钢筋、砼、合金等材料预先制成的大尺寸、大重量的构件,例如钢板、钢梁、钢柱等,并在施工过程中嵌入混凝土结构中。
在建筑和工程项目中,预埋铁件的安装是一个非常关键的环节,它直接关系到建筑物的结构安全和稳定性,因此需要采取科学合理的工法来进行安装。
大尺寸大重量预埋铁件安装工法通常包括以下几个步骤:1. 现场勘查和测量:在进行预埋铁件安装之前,需要进行现场的勘查和测量工作,确定预埋位置、尺寸和安装方式等重要参数。
2. 预埋孔准备:根据预埋铁件的尺寸和形状,利用钻孔机、切割机等工具在混凝土结构中准确地开设预埋孔。
预埋孔的深度、直径和几何形状等要符合设计要求。
3. 预埋件安装:将预埋铁件经过搬运、吊装等工艺操作,准确地放置到预埋孔中。
如果预埋孔较深,可以采取分段安装的方式。
安装过程中要保持预埋铁件与混凝土的紧密接触,确保其稳定性和强度。
4. 预埋件固定:对预埋铁件进行固定,可以采用焊接、螺栓连接、砼填充等方法。
焊接和螺栓连接适用于大型预埋铁件,可以提高连接的牢固度和稳定性。
砼填充适用于大尺寸、重量较大的预埋铁件,可以增加其与混凝土的粘结强度。
5. 预埋件验收:在完成预埋铁件的安装工作后,进行验收工作,检查预埋件的安装质量是否符合设计要求。
如果存在问题,应及时进行整改处理,确保安全可靠。
大尺寸大重量预埋铁件安装工法的优点是具有较高的安装精度和工艺可控性,可以提前预制,减少现场施工时间;同时,它还能提高建筑物的结构稳定性和抗震性能,从而保证施工工程的质量和安全。
然而,由于预埋铁件较大、重量较重,施工过程中需配备专业的工具和设备,且工作区域狭窄。
因此,施工人员需具备一定的经验和技能,严格按照操作规程进行施工。
总之,大尺寸大重量预埋铁件安装工法是一种重要的工程施工技术,它能够有效地提高建筑物的结构性能,确保工程质量和施工安全。
高精度设备基础埋件施工工法

高精度设备基础埋件施工工法一、前言随着科技的不断进步和现代化建设的不断推进,高精度设备在工业、医疗等领域被广泛地应用,对设备定位及施工精度要求越来越高。
为了保证设备安装的精度和稳定性,需要采用高精度设备基础埋件施工工法。
本文将针对这一工法进行介绍和分析。
二、工法特点高精度设备基础埋件施工工法的特点在于精度要求高、工艺复杂、施工难度大。
该工法的主要优点如下:1. 精度高:该工法可以保证设备基础的平整度、垂直度、水平度和位置精度等各项指标的要求。
2. 稳定性好:该工法采用了多种固定措施,可以确保设备基础的稳定性和寿命。
3. 工艺科学:该工法采用了现代科学技术,结合实际工程的要求进行优化,并经过严格的试验验证和实际应用,确保质量可靠。
三、适应范围该工法适用于各类高精度设备,如机械加工中心、数控机床、精密测量设备等等。
此外,这一方法也适用于对设备基础精度要求较高的场合,如精密仪器的安装、调试等。
四、工艺原理高精度设备基础埋件施工工法的理论依据主要有两个方面:一是对设备基础的要求进行明确,并结合实际工程要求制定合理的施工方法。
二是在施工过程中,采取合理的措施确保施工质量。
1. 设备基础要求高精度设备基础埋件施工工法的首要任务是设备基础结构的设计和施工。
合理的结构设计和施工方法可以最大限度地满足设备的使用要求,保证其施工质量。
设备基础应当具备以下要求:(1)垂直度和平整度高:该要求是保证设备基础的稳定性和使用寿命的关键。
(2)位置精度高:设备基础的位置应当精确,以便设备的定位和安装。
(3)材料选择合理:设备基础所使用的材料应当具有较好的耐腐蚀性、抗压性和耐磨性等特点。
2. 采取的技术措施在施工过程中,需要采取一系列的技术措施,来满足设备基础的要求。
具体措施如下:(1)良好的施工环境:施工现场应当洁净、干燥、通风以及避免杂物干扰设备基础的位置精度。
(2)合理的测量:施工前应进行精确的测量,确定设备基础的位置和高度等参数。
位超大型预埋件高精度安装施工工法

超大型预埋件高精度安装施工工法XX集团股份有限公司中国中铁建设(集团)有限责任公司1 前言楼兰双塔跳楼机设备的立柱塔基础和卷扬机基础超大型预埋件多用于重要结构或结构的重要部位及大型设备的基座部位等,预埋件水平度、轴线位置等安装精度要求较高,由于尺寸大、重量重、锚件多、钢筋密集、安装空间狭小等特点,使铁件加工、安装都比较困难。
中国中铁建设集团有限公司在长影海南“环球100”项目中国区10#楼的起重机工程施工过程中,因塔座顶板预埋件尺寸超大并需高位安装(立柱塔最大单块铁板3220 mm×2900 mm×3210mm,含锚件重8.9吨,垂直度要求0.5/1000mm以内,卷扬机最大单块铁板8358mmX3000mmX45mm,含锚件重8.8吨,垂直度要求0.5/1000mm以内),整套设备是意大利进口的,安装精度和安装间隙很小,在室内安装空间受到限制,常规整体吊装及安装难以满足施工的需要。
为此,中铁建集团成立课题组,经广泛调研,反复论证并结合施工实际,总结出一套超大型预埋件高精度安装施工工法,即分块加工、分块吊装、高位合理施焊、分层浇筑,成功地控制了预埋件的安装精度,该工程于2016年5月8日通过竣工验收并已经投入使用,取得了明显的经济效益和社会效益。
2 工法特点2.0.1 超大型预埋件由于重量较重,尺寸较大,若考虑采用预埋件整体吊装的方法将会大幅度增加施工成本,同时吊装过程中铁件容易变形,铁件就位后移动困难且难以控制安装精度。
本工法采用分块加工、预埋件钢板和锚件分开安装的方法,能利用现场现有垂直运输机械起重能力,避免投入大型专业吊装设备。
2.0.2 将预埋件的锚件与钢板分开安装,先安装定位锚件,采用26#钢筋加长双面搭焊,将每件锚螺栓固定在承台结构钢筋网格上,分层浇筑,将8根740mm*M24锚件按尺寸固定于混凝土中,预留低于锚螺栓上部250~300mm先进行一次灌浆承台,等待硬度达到75%后,再安装预埋件钢板基础底座,采用4个10吨的液压千斤顶支撑调整机座水平和垂直度达到安装要求,加强基础底座焊接加固,最后浇筑钢板下混凝土。
- 1、下载文档前请自行甄别文档内容的完整性,平台不提供额外的编辑、内容补充、找答案等附加服务。
- 2、"仅部分预览"的文档,不可在线预览部分如存在完整性等问题,可反馈申请退款(可完整预览的文档不适用该条件!)。
- 3、如文档侵犯您的权益,请联系客服反馈,我们会尽快为您处理(人工客服工作时间:9:00-18:30)。
超大型预埋件高精度安装施工工法1 前言2 工法特点2、0、1 超大型预埋件由于重量较重,尺寸较大,若考虑采用预埋件整体吊装得方法将会大幅度增加施工成本,同时吊装过程中铁件容易变形,铁件就位后移动困难且难以控制安装精度。
本工法采用分块加工、预埋件钢板与锚件分开安装得方法,能利用现场现有垂直运输机械起重能力,避免投入大型专业吊装设备。
2、0、2 将预埋件得锚件与钢板分开安装,先安装定位锚件,采用26#钢筋加长双面搭焊,将每件锚螺栓固定在承台结构钢筋网格上,分层浇筑,将8根740mm*M24锚件按尺寸固定于混凝土中,预留低于锚螺栓上部250~300mm先进行一次灌浆承台,等待硬度达到75%后,再安装预埋件钢板基础底座,采用4个10吨得液压千斤顶支撑调整机座水平与垂直度达到安装要求,加强基础底座焊接加固,最后浇筑钢板下混凝土。
这种工艺能够在施工中逐步调整误差,在每个环节中不断进行测量与矫正,从而较大程度地提高安装精度,保证高精度安装得要求。
2、0、3 应用数值模拟技术,采用有限元分析方法,选取合理得分块方案与焊接顺序,可以控制焊接变形,保证预埋件得平整度及轴线位移符合设计要求。
2、0、4 本工法采用了分块加工、分块吊装、合理施焊、不断纠偏得施工工艺,在高空环境下,有效地保证了超大型预埋件得安装精度,并加快了施工进度,降低了施工成本,使用效果良好。
3 适用范围本工法适用于工业与民用建筑中超大型预埋件高精度安装,如屋面钢结构预埋件、大型构筑物高位预埋件、大型设备基础预埋件等对铁件安装精度要求较高得工程,尤其适用于吊装高度较大得超大型预埋件高精度安装工程。
4 工艺原理基于“分块吊装”、“预埋件钢板与锚件分开安装”、“合理施焊”理念相结合得超大型预埋件高精度安装施工工艺,先将超大型预埋件钢板进行分块加工,并预留相关锚件安装及混凝土浇筑得孔洞;将锚件分别吊装到工作面,再用样板进行定位后浇筑混凝土固定;然后将分块后得钢板吊装就位,通过数值方法分析后,采用合理得顺序进行分块钢板之间得焊接以及钢板与锚件之间得焊接作业,并在焊接过程中不断纠偏;最后通过浇筑孔进行钢板下得混凝土浇筑。
5 施工工艺流程及操作要点5、1 施工工艺流程5、2 操作要点5、2、1 预埋件钢板分块、编号根据现场结构使用要求与现场设备起重能力,将预埋件钢板分为若干块、统一编号,采用数控等离子切割机裁板,各分块之间留锯齿状或V形等其她形状槽口,槽口坡口要满足设计与焊接要求,保证焊接后等强连接得效果。
分块首先要满足结构使用要求,切割线不应留置在钢板受力集中部位,同时尽量避开锚件以及钢板下钢筋较密集处,避开钢板表面得浇灌孔等其她预留孔。
其次分块大小要满足起重能力要求,以降低工程成本。
再次单块尺寸不宜过大,防止吊装过程中钢板因自重、风荷载或起吊方式而产生变形。
分块切割线得位置与形状宜通过数值模拟计算确定,通过有限元程序模拟计算,选择合理得切割位置与切割线形状,减少钢板分块对整个预埋件受力得影响,同时通过模拟计算确定焊接顺序,防止因焊接变形得累计而影响预埋件得安装精度。
图5、2、1 分割后得卷扬机钢板5、2、2 预埋件钢板切割、开孔预埋件钢板表面要留置锚件焊接孔、混凝土浇灌孔、排气孔、振捣孔等。
图5、2、2 开孔后得钢板锚件焊接孔:根据图纸设计得锚件位置定位,其形状与锚件相同,锚件与钢板间空隙、坡口角度深度均要满足安装与焊接要求。
混凝土浇灌孔:采用直径100mm得圆孔,根据浇筑方向留置,纵横间距不超过2米,钢筋、锚件较密集处要适当增加,浇灌孔可兼作振捣孔。
排气孔:采用直径为20mm~50mm得圆孔,间距1m左右,锚件密集处、半闭合得锚件处需适当增加。
钢板切割与开孔宜采用数控等离子切割机,以保证切割与开孔精度。
5、2、3 预埋件锚件制作安装1 锚件制作:锚件按照设计图纸要求下料、加工与表面处理。
2 锚件得安装:1)制作样板:使用较薄钢板(厚度5mm~10mm)制作一块与超大型预埋件钢板同尺寸得样板,并根据超大型预埋件钢板得开孔位置及大小在薄钢板上开设锚件安装孔。
2)安装样板:待结构施工至锚件安装标高后,首先完成钢筋施工,安装样板固定支架,然后将样板吊装于作业面上,根据设计图纸定位并临时固定。
图5、2、3 锚件安装后得图片3)安装锚件:将各种锚件依次吊装、安装于该样板得预留孔内并加固。
5、2、4 浇筑混凝土固定锚件对已安装完毕得锚件进行验收,合格后用角钢等材料进行焊接固定。
然后拆除样板,浇筑混凝土到铁件顶面以下1m左右,以固定所有锚件。
5、2、5 钢板吊装就位将分块后得预埋件钢板依次吊装就位于锚件上,利用锚件初步定位钢板得轴线位置、标高及水平位置。
离吊装设备较远处得预埋件钢板,可采用铺设滑道、铰链牵引得方式移动就位。
待锚件均位于钢板预留孔内后,校对与调整预埋件钢板轴线位置与水平度,并临时固定。
图5、2、5-1 利用塔吊吊装钢板图5、2、5 利用桅杆移动钢板5、2、6 锚件及各分块钢板焊接应采用数值模拟得方法选择合理得焊接顺序与焊接参数,以控制温度应力与焊接变形。
焊接前先将预埋件钢板与锚件点焊连接,在钢板分块处用2~3块薄钢板临时焊接连接,并将坡口处打磨干净。
焊接采用自动焊与手工焊,分层焊接。
焊接顺序与焊接速度应严格执行数值模拟所确定得方案。
焊接过程中应定时校对水平度与轴线位置。
所有焊接作业完成以后,应组织对预埋件钢板得水平度与轴线偏差进行验收,合格后才可以进行下道工序。
5、2、7 混凝土浇筑1 应选用高流态、低水灰比得混凝土,并添加一定比例得膨胀剂。
2 混凝土浇筑应自预埋件锚件较密集处向锚件较少处推移,保证钢板下混凝土浇筑密实。
3 配备足够得振捣器具,使入模得混凝土能及时被振捣密实;为防止漏振,坚持分层振捣,采用二次振捣工艺,以提高混凝土密实度与预埋件与混凝土间紧密结合。
图5、2、7 浇筑钢板下得混凝土6 材料与设备本工法无需特别说明得材料,采用得主要设备说明如下:6、0、1 钢板切割设备宜采用数控等离子切割机。
6、0、2 焊接设备可采用CO2气体保护弧焊机。
6、0、3 钢板吊装设备因地制宜,充分利用结构施工得塔吊,若现场设备不能满足要求,同时钢板又不允许分块较多,可采用增加拔杆等低成本方式吊装。
6、0、4 结构支模、钢筋安装、混凝土拌制、运输、浇筑等所需得机具设备,可根据不同工程对象按常规施工要求设置。
7 质量控制7、1 工程质量控制标准预埋件安装质量标准应满足下表要求,并同时满足现行施工规范中得有关规定及设计要求。
7、2、1 焊接过程中产生变形得主要原因与温度梯度、温度应力与板材厚度与结构刚度有关,板材越厚,结构刚度越大,变形越大。
施工开始前,应采用数值模拟得方法选择合理得分块参数与焊接参数,形成详细得施工方案,并严格按施工方案进行施工。
7、2、2 焊接前先将钢板与锚件点焊连接,分块处用2~3块薄钢板焊接连接。
分层施焊,每焊完一道焊缝应及时进行敲渣并锤击焊缝.以减少焊接应力。
焊接过程中应随时校正水平度与轴线尺寸。
7、2、3 角焊缝应优先采用埋弧焊或气体保护焊(CO2气体保护焊或混合气体保护焊)。
气体保护电弧焊焊丝宜采用船用焊丝,如大西洋ER50-6船用焊丝,保护气体为CO2或Ar+CO2,电流极性为直流反接。
用混合气体焊接后,其力学性能冲击功比CO2气体保护焊得更好;焊接时飞溅小,焊缝成形美观。
也可采用药芯焊丝焊接。
7、2、4 采用多层多道施焊工艺方法,手工电弧焊焊条应在使用前烘干并存放在保温筒内使用。
7、2、5 为避免焊接过程产生裂纹及脆性断裂,对焊接区域应先进行预热,如钢板材质为Q345B,预热应符合以下要求:1 当焊接环境温度不低于0℃时;板厚在30mm~50mm得范围内其预热温度为100℃。
2 当焊接环境温度在0℃以下时;板厚在6mm~16mm范围内焊接时环境温度低于-10℃,其预热温度均为120℃~150℃。
3 当焊接环境温度在0℃以下时;板厚大于16mm~24mm范围内焊接时环境温度低于-5℃,其预热温度均为120℃~150℃。
4 当焊接环境温度在0℃以下时;板厚大于24mm,其预热温度均为120℃~150℃。
7、2、6 局部预热时,预热得范围为焊缝两侧各不小于钢材厚度得3倍,且不得小于100mm。
预热温度得测量点,钢材厚度小于或等于50mm 时,距离焊缝两侧各为4倍钢材厚度,最大为50mm处。
7、2、7 需要预热得板件在整个焊接过程中应不低于预热温度。
对于要求预热焊接得板材,焊后均应采取缓冷措施(如用石棉布等保温材料覆盖)。
7、2、8 顶板混凝土浇筑完毕14天后,检查钢板与混凝土得结合程度,必要时对钢板表面钻孔取样,观察钢板与混凝土间结合情况。
如存在结合不好得情况,可采取高压注浆处理,在钢板表面钻间距600mm×600mm呈梅花状布置得圆孔,圆孔直径25mm。
利用钻好得圆孔进行高压注浆,材料采用C80灌浆料。
注浆前先用高压气体将孔内吹干,不允许孔内有积水与杂物。
注浆时加压要均匀,在对每个孔注浆时需观察有邻近孔内开始冒浆时才能停止该孔注浆,同时立即用木楔(包布)将已注完浆得孔封闭。
8 安全措施8、0、2 施工现场按符合防火、防风、防雷、防洪、防触电等安全规定及安全施工要求进行布置,并完善布置各种安全标识。
8、0、3 各类房屋、车库、料场等得消防安全距离做到符合公安部门得规定,室内不堆放易燃品;严格做到不在木工加工场、料库等处吸烟;随时清除现场得易燃杂物;不在有火种得场所或其近旁堆放生产物资。
8、0、4 氧气瓶与乙炔瓶隔离存放,严格保证氧气瓶不沾染油脂、乙炔发生器有防止回火得安全装置。
8、0、5 施工现场得临时用电严格按照《施工现场临时用电安全技术规范》得有关规范规定执行。
8、0、6 电缆线路应采用“三相五线”接线方式,电气设备与电气线路必须绝缘良好,场内架设得电力线路其悬挂高度与线间距除按安全规定要求进行外,将其布置在专用电杆上。
8、0、7 吊装施工中严格按照以下要求进行1 绑扎构件得吊索需经过计算,绑扎方法应正确牢靠。
所有起重工具应定期检查。
起重机得吊钩与吊环严禁补焊。
当吊钩吊环表面有裂纹、严重磨损或危险断面有永久变形时应予更换。
2 禁止在六级风、浓雾等恶劣气候得情况下进行吊装作业。
3 起重吊装得指挥人员必须持证上岗,作业时应与起重机驾驶员密切配合,执行规定得指挥信号。
驾驶员应听从指挥,当信号不清或错误时,驾驶员可拒绝执行。
4 严禁起吊重物长时间悬挂在空中,作业中遇突发故障,应采取措施将重物降落到安全地方,并关闭发动机或切断电源后进行检修。
在突然停电时,应立即把所有控制器拨到零位,断开电源总开关,并采取措施使重物降到地面。
5 设置吊装禁区,禁止与吊装作业无关得人员入内。
地面操作人员,应尽量避免在高空作业面得正下方停留或通过,也不得在起重机得起重臂或正在吊装得构件下停留或通过。