锂离子电池常见性能不良的鱼骨图分析
锂离子电池基础与常见失效分析(20110805training,Ding)
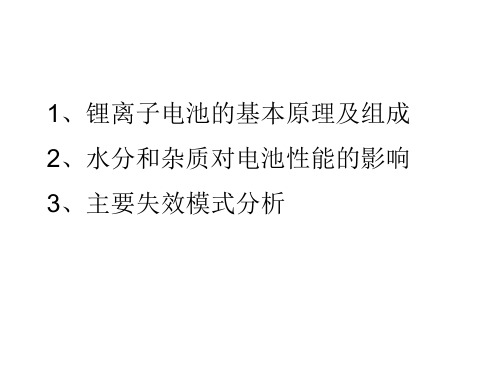
电液:锂离子电池使用的电液为无水有机电液,起到离子传导的作用,其中溶质为 LIPF6,溶剂为EC,EMC,DEC等碳酸酯,醚类和羧酸酯类,由于LIPF6的热稳定性差, 对水分非常敏感。因此,对于电池生产来说,水分和HF的控制是注液工序的关键。
电池的基本原理与组成—电解液
电液添加剂作为最为经济和有效的提升电池性能的一种手段,通常电 液添加剂的量不超过5% 其有如下几点作用: 1.在石墨负极表面参与生成SEI膜; 2.在SEI膜的形成及长期循环过程中,减少 不可逆容量的损失和气体产生; 3.提高LIPF6在有机溶剂中的热稳定性; 4.保护正极不溶解和过充电; 5.提高电液的物理性能,如离子导电率,黏 度和浸润度; 6.降低有机电液的可燃性; 7 .提供过充保护和提高过充承受能力; 8 .在滥使用的条件下,中止电池的使用
第二部分 水分和杂质对电池性能的影响
注:理解了水分和杂质的影响,就基本理解了FMEA中的失效模式 和后果之间的关系
水分对电池的影响
1、极片粘结力
2、水分对电池电压、内阻、厚度的影响
3、水分对热存储性能(85度 5小时、60度1周)影响 热膨胀率、冷膨胀率、内阻升高的比例都会随水分的增加而增大 4、水分对电池循环的影响
电池的基本原理与组成—正极材料
橄榄石结构的LiFeO4
三井物产
可以沿着c轴形成二维扩散运动,自由地脱出或嵌入。理论容量为170 mAh/g, 导电性能差;从LiFePO4变化为FePO4,体积减少6.81%,可以弥补碳负极的膨胀, 有助于提高电池的体积利用率。
电池的基本原理与组成—负极材料
• • • • •
电池的基本原理与组成—SEI
注液工序--充放电过程中有机电解液分解的电化学机理
锂电池软包裸电芯厚度不良使用鱼骨图分析案例
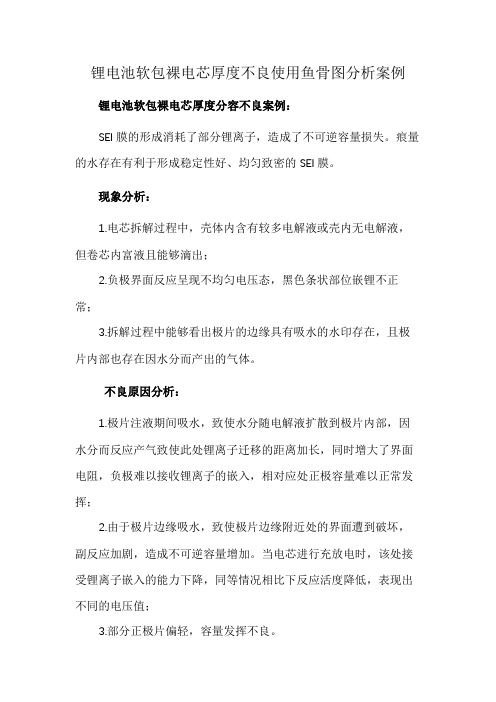
锂电池软包裸电芯厚度不良使用鱼骨图分析案例锂电池软包裸电芯厚度分容不良案例:SEI膜的形成消耗了部分锂离子,造成了不可逆容量损失。
痕量的水存在有利于形成稳定性好、均匀致密的SEI膜。
现象分析:1.电芯拆解过程中,壳体内含有较多电解液或壳内无电解液,但卷芯内富液且能够滴出;2.负极界面反应呈现不均匀电压态,黑色条状部位嵌锂不正常;3.拆解过程中能够看出极片的边缘具有吸水的水印存在,且极片内部也存在因水分而产出的气体。
不良原因分析:1.极片注液期间吸水,致使水分随电解液扩散到极片内部,因水分而反应产气致使此处锂离子迁移的距离加长,同时增大了界面电阻,负极难以接收锂离子的嵌入,相对应处正极容量难以正常发挥;2.由于极片边缘吸水,致使极片边缘附近处的界面遭到破坏,副反应加剧,造成不可逆容量增加。
当电芯进行充放电时,该处接受锂离子嵌入的能力下降,同等情况相比下反应活度降低,表现出不同的电压值;3.部分正极片偏轻,容量发挥不良。
整改建议:1.此类富电解液电芯可进行二次分容;2.针对电芯吸水,可严格管控电芯在整个制备过程中的储存保护,尤其注液至封口期间的流转,要求员工待做料不出箱,做完料即储存,不得让电芯在大环境滞留时间过长;3.严控化成后测电压,扎孔,抽真空时间及电芯储存,避免频繁开启箱体,且抽完真空的电芯做到一次性转出。
水分对电池的影响水分对电解液影响:电解液的溶剂结构中均存在电负性较大的羰基以及亚稳定的双键,容易与极性H2O分子作用形成络合体或反应生成相应的醇,而且温度越高,反应越快。
而且电解液的溶质锂盐也容易吸水并与水反应。
水分对SEI膜影响:Li2CO3是形成均匀致密SEI膜最主要的组分。
当水分含量过量时,会导致,过量的水会促使电解液中LiPF6的分解(发生如下反应),导致电池首次放电容量降低,形成不致密、不均匀的SEI膜。
此时,溶剂很容易嵌到石墨中造成容量损失,不可逆容量大。
分解产生的HF对电极材料有较强的腐蚀性,这也是导致容量衰减的一个原因。
锂离子电池原理、常见不良项目及成因、涂布方法汇总
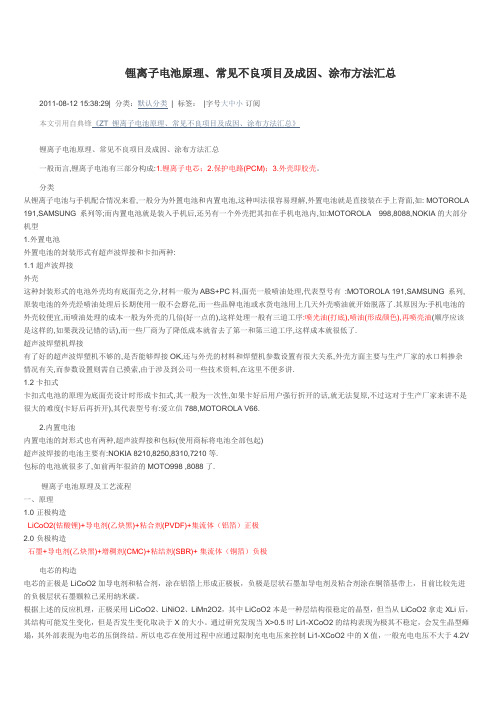
锂离子电池原理、常见不良项目及成因、涂布方法汇总2011-08-12 15:38:29| 分类:默认分类| 标签:|字号大中小订阅本文引用自典锋《ZT 锂离子电池原理、常见不良项目及成因、涂布方法汇总》锂离子电池原理、常见不良项目及成因、涂布方法汇总一般而言,锂离子电池有三部分构成:1.锂离子电芯;2.保护电路(PCM);3.外壳即胶壳。
分类从锂离子电池与手机配合情况来看,一般分为外置电池和内置电池,这种叫法很容易理解,外置电池就是直接装在手上背面,如: MOTOROLA 191,SAMSUNG 系列等;而内置电池就是装入手机后,还另有一个外壳把其扣在手机电池内,如:MOTOROLA998,8088,NOKIA的大部分机型1.外置电池外置电池的封装形式有超声波焊接和卡扣两种:1.1超声波焊接外壳这种封装形式的电池外壳均有底面壳之分,材料一般为ABS+PC料,面壳一般喷油处理,代表型号有:MOTOROLA 191,SAMSUNG 系列,原装电池的外壳经喷油处理后长期使用一般不会磨花,而一些品牌电池或水货电池用上几天外壳喷油就开始脱落了.其原因为:手机电池的外壳较便宜,而喷油处理的成本一般为外壳的几倍(好一点的),这样处理一般有三道工序:喷光油(打底),喷油(形成颜色),再喷亮油(顺序应该是这样的,如果我没记错的话),而一些厂商为了降低成本就省去了第一和第三道工序,这样成本就很低了.超声波焊塑机焊接有了好的超声波焊塑机不够的,是否能够焊接OK,还与外壳的材料和焊塑机参数设置有很大关系,外壳方面主要与生产厂家的水口料掺杂情况有关,而参数设置则需自己摸索,由于涉及到公司一些技术资料,在这里不便多讲.1.2卡扣式卡扣式电池的原理为底面壳设计时形成卡扣式,其一般为一次性,如果卡好后用户强行折开的话,就无法复原,不过这对于生产厂家来讲不是很大的难度(卡好后再折开),其代表型号有:爱立信788,MOTOROLA V66.2.内置电池内置电池的封形式也有两种,超声波焊接和包标(使用商标将电池全部包起)超声波焊接的电池主要有:NOKIA 8210,8250,8310,7210等.包标的电池就很多了,如前两年很浒的MOTO998 ,8088了.锂离子电池原理及工艺流程一、原理1.0 正极构造LiCoO2(钴酸锂)+导电剂(乙炔黑)+粘合剂(PVDF)+集流体(铝箔)正极2.0 负极构造石墨+导电剂(乙炔黑)+增稠剂(CMC)+粘结剂(SBR)+ 集流体(铜箔)负极电芯的构造电芯的正极是LiCoO2加导电剂和粘合剂,涂在铝箔上形成正极板,负极是层状石墨加导电剂及粘合剂涂在铜箔基带上,目前比较先进的负极层状石墨颗粒已采用纳米碳。
锂电池生产中各种不良原因及解析总结.doc
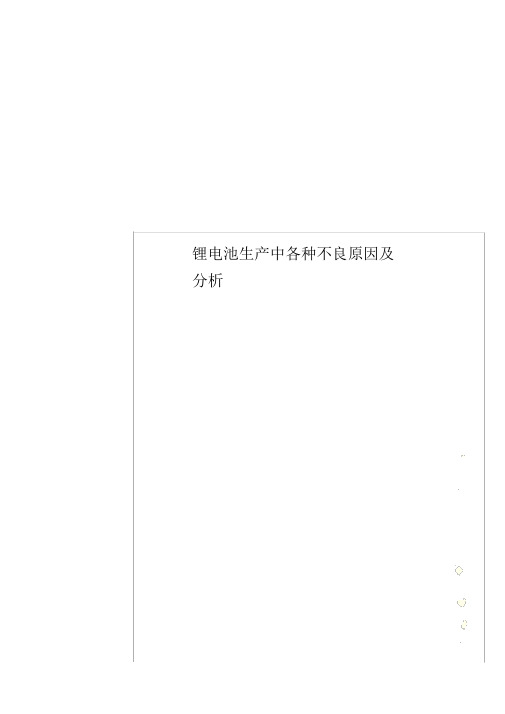
锂电池生产中各种不良原因及分析各种不良原因的造成以及原因分析20130830一、短路:1、隔膜刺穿:1)极片边尾有毛刺,卷绕后刺穿隔膜短路(分切刀口有毛刺、装配有误);2)极耳铆接孔不平刺穿隔膜(铆接机模具不平);3)极耳包胶时未包住极耳铆接孔和极片头部(裁大片时裁刀口有毛刺);4)卷绕时卷针划破隔膜(卷针两侧有毛刺);5)圧芯时气压压力太大、太快压破隔膜(气压压力太大,极片边角有锐角刺穿隔膜纸)。
2、全盖帽时极耳靠在壳闭上短路:1)高温极耳胶未包好;2)壳壁胶纸未贴到位;3)极耳过长弯曲时接触盖帽或壳壁。
3、化成时过充短路:1)化成时,正负极不明确反充而短路;2)过压时短路;3)上柜时未装好或内部电液少,充电时温度过高而短路。
4、人为将正负极短路:2)清洗时短路。
二、高内阻:1、焊接不好:极耳与极片的焊接;极耳与盖有虚焊。
2、电液偏少:注液量不准确偏少;封口时挤压力度过大,挤出电液。
3、装配结构不良:极片之间接触不紧密;各接触点面积太小。
4、材质问题:极耳及外壳的导电性能;电液的导电率;石墨与碳粉的导电率。
三、发鼓:1、电池内有水分:制造流程时间长;空气潮湿;极片未烘干;填充量过大,入壳后直接发鼓;极片反弹超厚,入壳后发鼓。
2、短路:过充或短路。
3、高温时发鼓;超过50°C 温度发鼓。
四、低容量:1、敷料不均匀,偏轻或配比不合理。
2、生产时断片、掉料。
3、电液量少。
4、压片过薄。
五、极片掉料:2、拉浆温度过高。
3、各种材料因素:如 P01、PVDF 、SBR、CMC 等性能问题。
4、敷料不均匀。
六、极片脆:1、面密度大,压片太薄。
2、烘烤温度过高。
3、材料的颗粒度,振头密度等。
各工位段不良原因的造成及违规操作一、配料:不良原因: 1)各种添加剂与P01 的配比;2 )浆料中的气泡;导致拉浆时不良率增加,以及3 )浆料中的颗粒;正负极活性物质的容量发挥和4)浆料的粘度。
极片掉料。
不良操作:1)加入添加剂时少加或多加;2)浆料搅拌时间不准确;3)浆料中添加剂或多或少。
深度剖析锂离子电池鼓胀原因

深度剖析锂离子电池鼓胀原因锂离子电池由于具有高寿命、高容量被广泛推广使用,但是随着使用时间的延长,其存在鼓胀、安全性能不理想和循环衰减加快的问题也日益严重,引起了锂电界深度的分析和抑制研究。
根据实验研发经验,笔者将锂电池鼓胀的原因分为两类,一是电池极片的厚度变化导致的鼓胀;二是由于电解液氧化分解产气导致的鼓胀。
在不同的电池体系中,电池厚度变化的主导因素不同,如在钛酸锂负极体系电池中,鼓胀的主要因素是气鼓;在石墨负极体系中,极片厚度和产气对电池的鼓胀均起到促进作用。
一、电极极片厚度变化在锂电池使用过程中,电极极片厚度会发生一定的厚度变化,尤其是石墨负极。
据现有数据,锂电池经过高温存储和循环,容易发生鼓胀,厚度增长率约6%——20%,其中正极膨胀率仅为4%,负极膨胀率在20%以上。
锂电池极片厚度变大导致的鼓胀根本原因是受石墨的本质影响,负极石墨在嵌锂时形成LiCx(LiC24、LiC12和LiC6等),晶格间距变化,导致形成微观内应力,使负极产生膨胀。
下图是石墨负极极片在放置、充放电过程中的结构变化示意图。
石墨负极的膨胀主要是嵌锂后产生不可恢复膨胀导致的。
这部分膨胀主要与颗粒尺寸、粘接剂剂及极片的结构有关。
负极的膨胀造成卷芯变形,使电极与隔膜间形成空洞,负极颗粒形成微裂纹,固体电解质相界面(SEI)膜发生破裂与重组,消耗电解液,使循环性能变差。
影响负极极片变厚的因素有很多,粘接剂的性质和极片的结构参数是最重要的两个。
石墨负极常用的粘接剂是SBR,不同的粘接剂弹性模量、机械强度不同,对极片的厚度影响也不同。
极片涂布完成后的轧制力也影响负极极片在电池使用中的厚度。
在相同的应力下,粘接剂弹性模量越大,极片物理搁置反弹越小;充电时,由于Li+嵌入,使石墨晶格膨胀;同时,因负极颗粒及SBR的形变,内应力完全释放,使负极膨胀率急剧升高,SBR处于塑性变形阶段。
这部分膨胀率与SBR的弹性模量和断裂强度有关,导致SBR的弹性模量和断裂强度越大,造成不可逆的膨胀越小。
曲线不良和EL测试图片分析
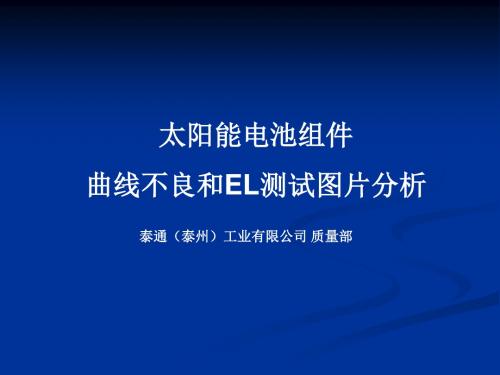
图(一)
图(二)
一、电池漏电流过大
例 一
原因:电池片有害的杂质和缺陷 造成。 影响:组件整体电压减小,I-V曲线表现在下降处有拱起。
例 二——电池漏电流过大
二、裂片
例 一
分析:电池片来料隐裂或人为因素造成电池片破裂。 影响:该片电流减小, I-V曲线电流有台阶。
例 二 —— 裂片
ห้องสมุดไป่ตู้
例 三 —— 裂片
五、短路
例 一
原因:电池片本身问题。 影响:I-V曲线弯曲,整体功率降低。
例 二 —— 短路
六、材料缺陷
例 一
原因:电池片本身问题。 影响:电流电压减小,整体功率降低。
el泰通泰州工业有限公司质量部正常的太阳能电池组件的iv曲线平滑所测试的el图片亮度一致无阴影如图一二在实际生产中出现一些组件iv曲线弯曲对于这些曲线不良经el测试后发现电池片存在不良的现象具体为
太阳能电池组件 曲线不良和EL测试图片分析
泰通(泰州)工业有限公司 质量部
正常的太阳能电池组件的I-V曲线平滑,所测试的EL 图片亮度一致、无阴影(如图一、二),在实际生产中 出现一些组件I-V曲线弯曲,对于这些曲线不良经EL测试 后,发现电池片存在不良的现象,具体为:
例 四 —— 裂片
三、低效片
例 一
分析:电池片自身问题,效率比其它电池片偏低。 影响:该片电流小, I-V曲线电流有台阶。
例 二 —— 低效片
例 三 —— 低效片
例 四—— 低效片
例 五 —— 低效片
例 六 —— 低效片
四、分档不均
例 一
原因:比其它电池片效率高。 影响:I-V曲线有起伏,对组件质量影响不大。
03 解释锂离子电池行业重大隐患图例 2023年

物理隔离图例
水
浸泡在水
物料盒装电池
货架
中的电池
实体墙
图 11 浸泡水中的电池
图 12 实体墙隔离存放的电池
图 13 防爆柜中的电池
集装箱 图 15 集装箱中的电池
物料盒装电池 铁皮柜 图 14 铁皮柜中的电池
防火卷帘
图 16 防火卷帘中的电池
2.本项是指存在下列情形的: (1)锂离子电池储存仓库存放故障电池时,未对故障电池采取物理隔离措施。
故障电池图例
胀气的电池
图 1 故障电池图例-胀气电池 短路 电池, 有高 温碳 化痕 迹
图 3 故障电池图例-短路电池
破损的电池,有泄露电解液污渍和气味 图 2 故障电池图例-破损电池 过充电电池,电压≥4.7V, 通常胀气
解释锂离子电池行业重大隐患图例 2023 年
(应急部令【2023】10 号)
(七)锂离子电池储存仓库未对故障电池采取有效物理隔离措施的; 【解读】 1. 名词解释
故障电池是指单体电池电压超 3 伏特,存在胀气、短路、破损、过充电安全缺陷的电 池,不包括持续浸泡在水中的电池。 物理隔离措施指通过实体墙、防爆柜或铁皮柜、单独集装箱、防火卷帘等方式,将故障 电池与非故障电池有效隔离。
锂电池极片缺陷图谱(一)
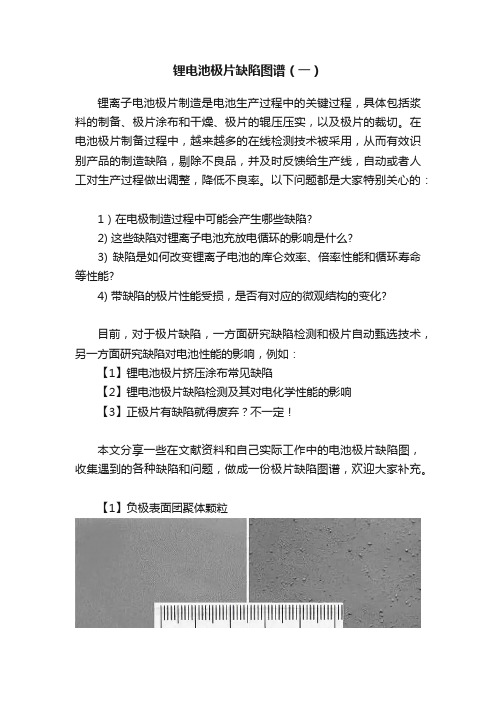
锂电池极片缺陷图谱(一)锂离子电池极片制造是电池生产过程中的关键过程,具体包括浆料的制备、极片涂布和干燥、极片的辊压压实,以及极片的裁切。
在电池极片制备过程中,越来越多的在线检测技术被采用,从而有效识别产品的制造缺陷,剔除不良品,并及时反馈给生产线,自动或者人工对生产过程做出调整,降低不良率。
以下问题都是大家特别关心的:1)在电极制造过程中可能会产生哪些缺陷?2) 这些缺陷对锂离子电池充放电循环的影响是什么?3) 缺陷是如何改变锂离子电池的库仑效率、倍率性能和循环寿命等性能?4) 带缺陷的极片性能受损,是否有对应的微观结构的变化?目前,对于极片缺陷,一方面研究缺陷检测和极片自动甄选技术,另一方面研究缺陷对电池性能的影响,例如:【1】锂电池极片挤压涂布常见缺陷【2】锂电池极片缺陷检测及其对电化学性能的影响【3】正极片有缺陷就得废弃?不一定!本文分享一些在文献资料和自己实际工作中的电池极片缺陷图,收集遇到的各种缺陷和问题,做成一份极片缺陷图谱,欢迎大家补充。
【1】负极表面团聚体颗粒配方:球形石墨+SUPER C65+CMC+蒸馏水两种不同搅拌工艺的极片宏观形貌:表面光滑(左)和表面存在大量小颗粒(右)配方:球形石墨+SUPER C65+CMC/SBR+蒸馏水极片表面小颗粒放大形貌(a和b):导电剂的团聚体,没有完全分散表面光滑极片的放大形貌:导电剂充分分散,均匀分布【Bitsch B,Willenbacher N, Wenzel V, et al. Impact of Mechanical Process Engineering onthe Fabrication Process of Electrodes for Lithium Ion Batteries[J]. ChemieIngenieur Technik. 2015, 87(4): 466-474.】【2】正极表面团聚体颗粒配方:NCA+乙炔黑+PVDF+NMP搅拌过程中,环境湿度太高,导致浆料成果冻状态,导电剂没有完全分散好,极片辊压后表面存在大量的颗粒。
SMT常见不良鱼骨图分析ppt模板

刮刀變形
爐中運行速度
零件過於 爐樘內 預熱時 軌道 冷卻
印刷 刮刀不 參數設 印刷厚 位移 水平 定不當 度不均
錫膏機
錫膏量少 刮刀變形
刮刀角
開口與
鋼板 鋼板開 度不佳
PAD不符 不潔 口尺寸
印刷速 度過快
碑
舊錫膏管制不當
靠近板邊
程序坐標修改
不正確關閉 mark點
刮刀 水平
排風 不通
刮刀 角度
溫度設 預熱 抽
膏
下錫 印刷 印刷 脫 模 印刷有機
不良 太厚 短路
錫尖
鋼板 鋼板 開口 鋼板
張力 材質 規格 厚度
鋼
板 鋼板底 開口 表面 鋼板 損壞 貼紙多 不良 粗糙 不平
新舊錫膏混用
機器的保養 未依SOP操作
定不當 不足 風 軌道流板不暢撞板 手放零件方法不當
軌道有雜物 置件 Table 高度 松動
印刷速 度過快
印刷缺 錫少錫
錫膏機
行程
印刷 偏移
鋼板下 有異物
錫膏粘 刮刀
鋼板 阻塞
刮刀 變形
運輸
坐標修改失誤
撞件零 件位移
轉移料站mark未考慮
PCB設計 零件旁邊有
角度修 改故障 Skip mark
溫區不 穩定
抽風 過大
排風 不通
其它
印刷短路後用刀片撥錫 錫膏類型不合適
錯件
小孔漏錫
作業
機器振動太大
塞鋼板開口
PCB
撿板不及時爐內撞板
通風不暢
人為pass 手推撞板 生產模式被改動(pass,idle)
印刷後PCB板停留時間延長
锂离子电池组的故障模式影响及危害性分析

1 锂离子电池组的故障模式、影响及危害性分析1.1 电池组系统定义1.1.1 约定层次的划分锂离子电池组系统分为:航行推进动力单元、电子设备动力单元、应急电源、电池组检测板和模块监测板,其中应急电源由锂/亚硫酰氯单体电池组成。
航行推进动力单元由6个51F301模块串联组成,电子设备动力单元由2个51F302模块并联组成,应急电源由1个5103模块组成。
51F3功能层次关系的对应关系见图5-1和结构层次关系见图5-2。
依据锂离子电池组系统结构层次关系图,锂离子电池组约定层次的划分见表5-1。
表5-1 电池组约定层次的划分1.1.2 约定层次的任务功能和工作方式初始约定层锂离子电池组的任务功能是给推进系统提供能源,使主载体完成预定的各项任务。
航行推进动力单元通过放电的方式给推进系统提供33.2kWh的功率容量,电子设备单元通过放电的方式给控制和导航系统提供4.74kWh的功率容量。
电池组检测板完成检测航行推进动力单元、电子设备动力单元的总电压和总电流、过流保护的功能,模块监测板完成对单体电池的电压、温度的检测。
第二约定层次51F301模块、51F302模块、5103模块的任务功能是输出能源,通过放电的方式完成初始约定层次对其要求的输出功率容量。
51F301模块需要输出5.54KWh,51F302模块需要输出2.37KWh,5103模块需要输出630Wh。
最低约定层次单体电池任务功能是输出能源,通过放电的方式完成第二约定层次对其要求的输出功率容量,单体电池需要输出0.369KWh。
最低约定层次串联二极管任务功能是单向导通和反向截止作用;最低约定层次焊点任务功能是焊接和导电。
最低约定层次传感器任务功能是测量各个单体电池的温度、电压及其支路的总电压、总电流。
1.1.3 环境剖面和工作时间锂离子电池组的环境剖面分析和对其环境条件预计,必须基于电池组的寿命剖面分析和任务剖面分析。
电池组的寿命剖面见图5-3。
勤务保障阶段图5-3 锂电池组的寿命剖面时间锂电池组的任务剖面见图5-4。
锂离子二次电池性能不良及相关原因
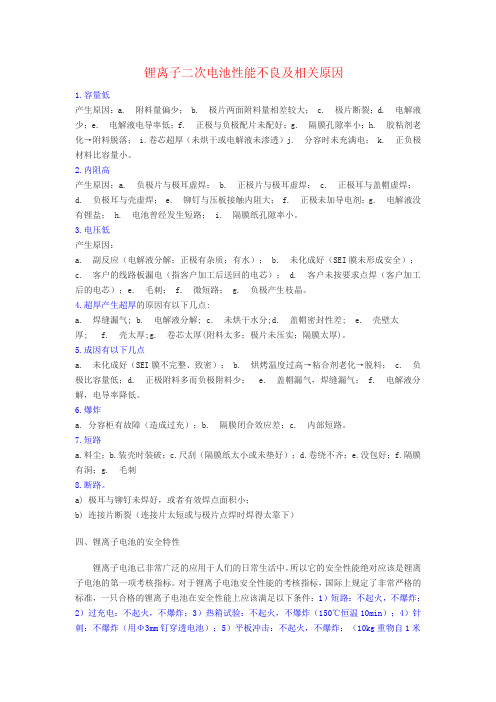
锂离子二次电池性能不良及相关原因1.容量低产生原因:a. 附料量偏少; b. 极片两面附料量相差较大; c. 极片断裂;d. 电解液少;e. 电解液电导率低;f. 正极与负极配片未配好;g. 隔膜孔隙率小;h. 胶粘剂老化→附料脱落;i.卷芯超厚(未烘干或电解液未渗透)j. 分容时未充满电;k. 正负极材料比容量小。
2.内阻高产生原因:a. 负极片与极耳虚焊; b. 正极片与极耳虚焊; c. 正极耳与盖帽虚焊;d. 负极耳与壳虚焊; e. 铆钉与压板接触内阻大; f. 正极未加导电剂;g. 电解液没有锂盐;h. 电池曾经发生短路; i. 隔膜纸孔隙率小。
3.电压低产生原因:a. 副反应(电解液分解;正极有杂质;有水);b. 未化成好(SEI膜未形成安全);c. 客户的线路板漏电(指客户加工后送回的电芯);d. 客户未按要求点焊(客户加工后的电芯);e. 毛刺;f. 微短路;g. 负极产生枝晶。
4.超厚产生超厚的原因有以下几点:a. 焊缝漏气;b. 电解液分解;c. 未烘干水分;d. 盖帽密封性差;e. 壳壁太厚;f. 壳太厚;g. 卷芯太厚(附料太多;极片未压实;隔膜太厚)。
5.成因有以下几点a. 未化成好(SEI膜不完整、致密);b. 烘烤温度过高→粘合剂老化→脱料;c. 负极比容量低;d. 正极附料多而负极附料少;e. 盖帽漏气,焊缝漏气;f. 电解液分解,电导率降低。
6.爆炸a. 分容柜有故障(造成过充);b. 隔膜闭合效应差;c. 内部短路。
7.短路a.料尘;b.装壳时装破;c.尺刮(隔膜纸太小或未垫好);d.卷绕不齐;e.没包好;f.隔膜有洞;g. 毛刺8.断路。
a) 极耳与铆钉未焊好,或者有效焊点面积小;b) 连接片断裂(连接片太短或与极片点焊时焊得太靠下)四、锂离子电池的安全特性锂离子电池已非常广泛的应用于人们的日常生活中,所以它的安全性能绝对应该是锂离子电池的第一项考核指标。
对于锂离子电池安全性能的考核指标,国际上规定了非常严格的标准,一只合格的锂离子电池在安全性能上应该满足以下条件:1)短路:不起火,不爆炸;2)过充电:不起火,不爆炸;3)热箱试验:不起火,不爆炸(150℃恒温10min);4)针刺:不爆炸(用Φ3mm钉穿透电池);5)平板冲击:不起火,不爆炸;(10kg重物自1米高处砸向电池);6)焚烧:不爆炸(煤气火焰烧考电池)。
锂离子电池负极极板花斑的刨析.
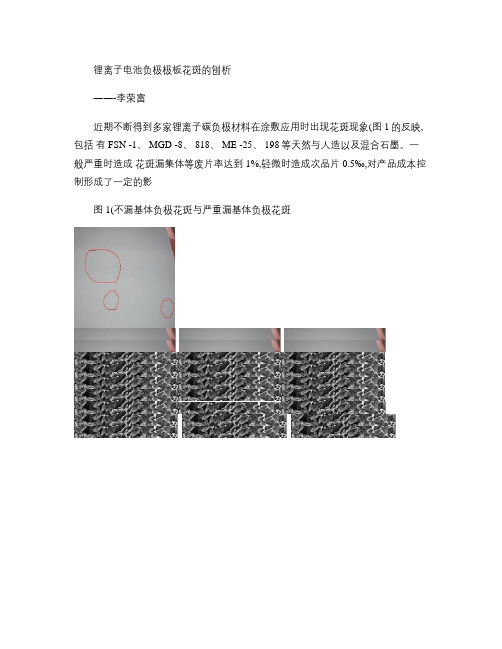
锂离子电池负极极板花斑的刨析――-李荣富近期不断得到多家锂离子碳负极材料在涂敷应用时出现花斑现象(图 1的反映,包括有 FSN -1、 MGD -8、 818、 ME -25、 198等天然与人造以及混合石墨。
一般严重时造成花斑漏集体等废片率达到 1%,轻微时造成次品片0.5‰,对产品成本控制形成了一定的影图 1(不漏基体负极花斑与严重漏基体负极花斑图 2花斑中心处 (漏基体花斑边缘正常处二、能谱扫描分析由于花斑经过扫描电镜分析 , 未在材料方面发现原因 , 我们对同一块样品又进行了 X 射线能谱分析 (EDS 分析元素组成及其相对含量 , 判定是否是由于粘合剂没有打开而造成花斑,花斑中心处 (漏基体位置能谱扫描 , 扫描出来有铜离子 8.92%重量比外 , 其他全部是碳, 没有发现有其他元素谱峰出现。
其他两个能谱扫描位置 , 由于负极材料覆盖的比较致密 , 扫描谱线中未发现铜离子出现, 同样也未发现其他元素峰出现。
虽然采用能谱进行元素定量分析误差较大, 但我们应该在图谱上观察到其他元素杂峰。
三个图谱均未发现除铜以外的其他元素。
因此判定与粘合剂未分散均匀或者粘合剂在浆料中团聚无关。
具体数据见下列 :能谱元素扫描数据1、花斑中心处 (漏基体2、花斑边缘3、正常处三、其他分析通过电镜图片以及能谱分析 ,花斑形成的原因应该与材料微粉、导电剂团聚以及粘合剂未打开关系不大。
为了查找问题根源 , 我们在电池制造公司的负极涂敷车间连续观察拉浆机上浆工序 ,在上浆滚与基带接触处不断有汽泡出现,出现的气泡随着移动的浆液一同涂敷, 入炉前基带表面的浆液的气泡不断破裂 (图 3标示处 ,微小的气泡没有在烘干后的极板上留下痕迹 , 但过大的气泡破裂后形成了圆形的痕迹 , 经烘干后出现了花斑(图 4标示处。
图 3 图 4表面有众多的微孔与间隙 , 由于水表面的张力 , 我们在搅拌桨料过程中 ,水受外力影响不断湿润者进入到这些微孔与间隙中 ,不断将这些部位的气泡赶出, 这就是我们采用真空搅拌浆料气泡大量减少的缘故。
- 1、下载文档前请自行甄别文档内容的完整性,平台不提供额外的编辑、内容补充、找答案等附加服务。
- 2、"仅部分预览"的文档,不可在线预览部分如存在完整性等问题,可反馈申请退款(可完整预览的文档不适用该条件!)。
- 3、如文档侵犯您的权益,请联系客服反馈,我们会尽快为您处理(人工客服工作时间:9:00-18:30)。
锂离子电池常见性能不良的鱼骨图分析
锂离子电池行业常见的性能不良的鱼骨图分析。
行业内人士都清楚,电池常见的主要性能指标包含容量、内阻及电压等。
电池生产企业都是百分之百的检验测试合格在出货给客户的。
下面就介绍这三种常见不良的鱼骨图分析,以便于伙伴们后续不良分析及改进提供参考借鉴(注:下图所列明的为涉及5M1E绝大多数主要不良因子,当然不排除还有其他因子,不限于下图的内容。
伙伴们可以结合实际自主完善)。
同时,我们知道这些不良的产生原因,可以针对性的在制造过程中去做些相应的预防及改进,以确保我们的产品质量及提高客户满意度。
有些知名的大企业就是把自己产品的常见的不良作成鱼骨图板报及教材来培训内部员工以提高质量意识。
容量
电池的容量:分额定容量和标称容量。
电池的额定容量:是指电池在环境温度为20℃±5℃条件下,以5h 率放电至终止电压时所应提供的电量,用C5表示。
电池的标称容量:是指电池在一定的放电条件下所放出的实际平均电量,主要受放电倍率和温度的影响(注:故严格来讲,电池容量应指明充放电条件)。
内阻
电池的内阻:是指电池在工作时,电流流过电池内部所受到的阻力;由欧姆内阻与极化内阻两部分组成。
其中欧姆电阻包括电极本身的电阻、电解质溶液的电阻和离子通过隔膜微孔时受到的阻力、正负极与隔膜的接触电阻等,极化电阻则为电池在充放电时由于电极极化形成的导电阻力;电池内阻值大,会导致电池放电工作电压降低,放电时间缩短。
注:一般以充电态内阻为标准。
测量电池的内阻需用专用内阻仪测量,才能确保所得到的值的精确度。
电压
开路电压:是指电池在非工作状态下即电路中无电流流过时,电池正负极之间的电势差;一般情况下,Li-ion电池充满电后开路电压为4.1—4.2V左右,放电后开路电压为3.0V左右。
通过对电池的开路电压的检测,可以判断电池的荷电状态。
工作电压:又称端电压,是指电池在工作状态下即电路中有电流流过时电池正负极之间的电势差;Li-ion电池的放电工作电压在3.6V 左右。
低电压电池指电池在一定的条件下,由于受制程各种因素影响导致电池的电压或荷电保持率低于工艺设计范围的不良电池。