第四章 薄膜的化学气相沉积
第四章_薄膜的物理气相沉积

4.1 蒸发沉积 4.2 溅射沉积 4.3 离子束沉积 4.4 脉冲激光沉积
4.1 蒸发沉积
蒸发沉积薄膜的基本过程:
1) 原材料被加热蒸发而气化 2) 气化的原子或分子从蒸发源向基片表面输运 3)蒸发的原子或分子在基片表面被吸附、成核、 核长大,继而形成连续薄膜
4.1.1 蒸发源
缺点:需要较复杂且昂贵的高频电源
4.1.2 原材料的蒸发与输运
1.
蒸发速率 假设在原材料表面液相和气相分子处于动态平 衡,则蒸发速率
dN r Pr P0 Je Adt 2 mkT
蒸发速率与蒸发源温度的关系
dG B 1 dT 2.3 G T 2 T
4.1.3 蒸发镀膜的膜厚分布
膜厚的分布取决于蒸发源的几何形状 与蒸发特性、基片的几何形状、基片与蒸 发源的相对位置等因素。
膜厚理论计算的简化假设: 1)蒸发凝结成薄膜
4.2 溅射沉积
溅射:荷能粒子轰击固体表面,使固体原子(或 分子)逸出的现象叫溅射。 使用范围:金属、合金、半导体、氧化物、氮化 物、碳化物、超导薄膜等。 溅射率:当粒子轰击靶阴极时,平均每个粒子从 阴极上打出的原子数。 溅射阈值:当入射粒子能量高于溅射阈值时才发 生溅射。
脉冲激光沉积的优点
相比其他制膜技术,PLD具有如下特点:1) 采用紫外脉冲激光器作为等离子体的能源,它 具有高光子能量、无污染且易于控制的特点; 2)可以比较精确的控制化学计量比,实现靶 膜成分接近一致。3) 可以引入反应气体,提 供了另一种改变薄膜组分的办法;4)四个靶 材托板随意更换,可以实现多层膜、异质结的 制备,尤其适合制备量子阱结构薄膜。5)工 艺相对简单,灵活性很大,可以实现诸多不同 种类的薄膜制备;6)可以使用激光器对薄膜 进行后续处理等。
化学气相沉积法制备薄膜

W (CO)6 W 6CO
激光束
CH 4 C(碳黑) 2H 2
800 ~1000℃火焰
CH 4 C(金刚石) 2H 2
800~1000℃成工艺
化学气相沉积法合成生产工艺种类
CVD装置通常由气源控制部件 、沉积反应室、沉积温控部件、真空排气和 压强控制部件等部分组成。 任何CVD系统均包含 一个反应器、一组气体传输系统、排气系统及工艺控 制系统等。
大体上可以把不同的沉积反应装置粗分为常压化学气相沉积(APCVD)、 低压化学气相沉积(LPCVD)、等离子体增强化学气相沉积(PECVD)、有机 金属化学气相沉积(MOCVD)和激光化学气相沉积(LCVD)等。
3、等离子化学气相沉积(PECVD)
PECVD通过辉光放电形成等离子体,增强化学反应,降低沉积温度,可以在 常温至350℃条件下沉积氮化硅膜、氧化硅膜、氮氧化硅及非晶硅膜等。 在辉光放电的低温等离子体内,“电子气”的温度约比普通气体分子的平均 温度高10~100倍,即当反应气体接近环境温度时,电子的能量足以使气体分 子键断裂并导致化学活性粒子(活化分子、离子、原子等基团)的产生,使 本来需要在高温下进行的化学反应由于反应气体的电激活而在相当低的温度 下即可进行,也就是反应气体的化学键在低温下就可以被打开。所产生的活 化分子、原子集团之间的相互反应最终沉积生成薄膜。
从气相中析出的固体的形态主要有:在固体表面上生成薄膜、晶须和晶粒, 在气体中生成粒子。
4
CVD技术要求:
反应剂在室温或不太高的温度下最好是气态或有较高的蒸气压而易于挥发成 蒸汽的液态或固态物质,且有很高的纯度; 通过沉积反应易于生成所需要的材料沉积物,而其他副产物均易挥发而留在 气相排出或易于分离;
化学气相沉积

集成电路芯片工艺化学气相沉积(CVD)化学汽相淀积(CVD)化学汽相淀积是指通过气态物质的化学反应在衬底上淀积一层薄膜材料的过程。
CVD膜的结构可以是单晶、多晶或非晶态,淀积单晶硅薄膜的CVD过程通常被称为外延。
CVD技术具有淀积温度低、薄膜成分和厚度易于控制、均匀性和重复性好、台阶覆盖优良、适用范围广、设备简单等一系列优点。
利用CVD方这几乎可以淀积集成电路工艺中所需要的各种薄膜,例如掺杂或不掺杂的SiO:、多晶硅、非晶硅、氮化硅、金属(钨、钼)等。
一:化学气相沉积方法常用的CVD方法主要有三种:常压化学汽相淀积(APCVD)、低压化学汽相淀积(LPCVIi~)和等离子增强化学汽相淀积(PECVD).APCVD反应器的结构与氧化炉类似,如图1-1所示,该系统中的压强约为一个大气压,因此被称为常压CVD。
气相外延单晶硅所采用的方法就是APCVD。
图1-1APCVD反应器的结构示意图,LPCVD反应器的结构如图1-2所示,石英管采用三温区管状炉加热,气体由一端引入,另一端抽出,半导体晶片垂直插在石英舟上。
由于石英管壁靠近炉管,温度很高,因此也称它为热壁CVD装置,这与利用射频加热的冷壁反应器如卧式外延炉不同.这种反应器的最大特点就是薄膜厚度的均匀性非常好、装片量大,一炉可以加工几百片,但淀积速度较慢.它与APCVD的最大区别是压强由原来的1X10SPa降低到1X102Pa左右。
图1-2LPCVD反应器的结构示意图图1-3平行板型PECVD反应器的结构示意图PECVD是一种能量增强的CVD方法,这是因为在通常CVD系统中热能的基础上又增加了等离子体的能量.图1-3给出了平行板型等离子体增强CVD反应器,反应室由两块平行的金属电极板组成,射频电压施加在上电极上,下电极接地。
射频电压使平板电极之间的气体发生等离子放电。
工作气体由位于下电极附近的进气口进入,并流过放电区。
半导体片放在下电极上,并被加热到100—400;C左右.这种反应器的最大优点是淀积温度低。
第四章CVD工艺

早期CVD 技术以开管系统为主, 即Atmosphere Pressure
CVD (APCVD)。
近年来,CVD技术令人注目的新发展是低压CVD技术,
即Low Pressure CVD(LPCVD)。
LPCVD原理与APCVD基本相同,主要差别是:
低压下气体扩散系数增大,使气态反应物和副产物的
三、CVD方法简介
☞封闭式(闭管沉积系统)CVD
闭管法的优点:污染的机会少,不必连续抽气保持
反应器内的真空,可以沉积蒸气压高的物质。
闭管法的缺点:材料生长速率慢,不适合大批量生长,
一次性反应器,生长成本高;管内压力检测困难等。
闭管法的关键环节:反应器材料选择、装料压力计算、
温度选择和控制等。
四、低压化学气相沉积(LPCVD)
学气相沉积。用来制备化合物薄膜、非晶薄膜、外
延薄膜、超导薄膜等,特别是IC技术中的表面钝化
和多层布线。
五、等离子增强化学气相沉积(PECVD)
☞等离子化学气相沉积
Plasma CVD
Plasma Associated CVD
Plasma Enhanced CVD
这里称PECVD
PECVD是指利用辉光放电的物理作用来激活化学
一、化学气相沉积的基本原理
☞化学气相沉积的基本原理
➢ CVD的(化学反应)动力学
热分解反应(吸热反应)
(2)金属有机化合物
M-C键能小于C-C键,广泛用于沉积金属和氧化物薄膜。
金属有机化合物的分解温度非常低,扩大了基片选
择范围以及避免了基片变形问题。
(3)氢化物和金属有机化合物系统
广泛用于制备化合
气相沉积反应的CVD技术。广泛应用于微电子学、
化学气相沉积法ppt课件

优点:可以在热敏感的基体上进行沉积;
缺点:沉积速率低,晶体缺陷密度高,膜中杂质 多。
原料输送要求:把欲沉积膜层的一种或几种组分 以金属烷基化合物的形式输送到反应区,其他 的组分可以氢化物的形式输送。
精选ppt
(A)CVD的原理
CVD的机理是复杂的,那是由于反应气体中不同 化学物质之间的化学反应和向基片的析出是同 时发生的缘故。
基本过程:通过赋予原料气体以不同的能量使其 产生各种化学反应,在基片上析出非挥发性的 反应产物。
图3.14表示从TiCl4+CH4+H2的混合气体析出 TiC过程的模式图。如图所示,在CVD中的析出 过程可以理解如下:
精选ppt
7
⑥绕镀性好:可在复杂形状的基体上及颗粒材 料上沉积。
⑦气流条件:层流,在基体表面形成厚的边界 层。
⑧沉积层结构:柱状晶,不耐弯曲。通过各种 技术对化学反应进行气相扰动,可以得到细晶 粒的等轴沉积层。
⑨应用广泛:可以形成多种金属、合金、陶瓷和 化合物沉积层
精选ppt
8
(2)CVD的方法
LCVD技术的优点:沉积过程中不直接加热整块 基板,可按需要进行沉积,空间选择性好,甚 至可使薄膜生成限制在基板的任意微区内;避 免杂质的迁移和来自基板的自掺杂;沉积速度
比2
(D)超声波化学气相沉积(UWCVD)
定义:是利用超声波作为CVD过程中能源的一种 新工艺。
①常压CVD法; ②低压CVD法; ③热CVD法; ④等离子CVD法; ⑤间隙CVD法; ⑥激光CVD法; ⑦超声CVD法等。
精选ppt
14
(C)CVD的流程与装置
化学气相沉积解读
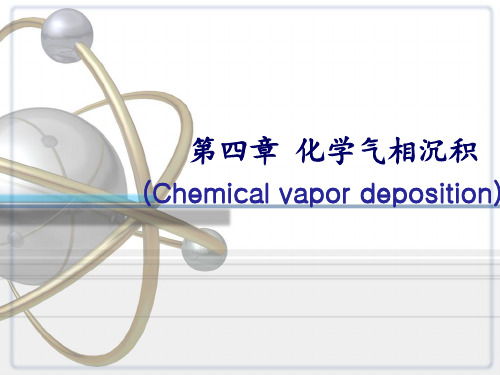
由上图分析可知: 高温:扩散控制 低温:表面反应控制 反应导致的沉积速率为:
其中 N0 为表面原子密度。 沉积速率随温度的变化规律取决于Ks,D,δ 等随温度的变化情况。 因此,一般而言,化学反应或化学气相沉积的速度将随温度的升 高而加快。 但有时并非如此,化学气相沉积的速率随温度的升高 出现先升高后降低的情况。 这是什么原因呢?
第四章 化学气相沉积
(Chemical vapor deposition)
•
•
4.4 薄膜生长动力学 4.5 化学气相沉积装置
4.4 薄膜生长动力学
在CVD过程中,薄膜生长过程取决于气体与衬底间界面
的相互作用,具体过程如下: 1. 反应气体扩散通过界面 层 2. 气体分子在薄膜或衬底 表面的吸附 3. 原子表面的扩散、反应 和溶入薄膜晶格之中 4. 反应产物扩散离开衬底 表面并通过界面层
此式表明:Si的沉积速度将随着距离的增加呈指数 趋势下降,即反应物将随着距离的增加逐渐贫化。
•
轴向生长速率的均匀性:
•
扩散速度小于气流速度
•
沉积速率随距离的增加呈指数下降! 倾斜基片使薄膜生长的均匀性得以改善 ;
提高气体流速v和装置的尺寸b 调整装置内温度分布,影响扩散系数D的分布
因此,提高沉积均匀性可以采取如下措施:
我们用CVD方法共同的典型式子来说明: 设这一反应正向进行时为放热反应,则
aA( g ) bB( g ) cC (s) dD( g )
ΔH<0, U0<U
上式描述的正向和逆向反应速率如下页图a所示,均随 温度上升而提高。同时,正向反应的激活能低于逆向反应 的激活能。而净反应速率应是正反向反应速率之差,而他 随温度升高时会出现一个最大值。因此温度持续升高将会 导致逆反应速度超过正向的,薄膜的沉积过程变为薄膜的 刻蚀过程。
第四章化学气相沉积

设在生长中的薄膜表面形成了界面层,其厚度为,cg和cs分别为 反应物的原始浓度和其在衬底表面的浓度,则
扩散至衬底表面的反应物的通量为: 衬底表面消耗的反应物通量与Cs成正比
平衡时两个通量相等,得
F1 hg (Cg Cs )
F2 ksCs
F1 F2
Cs
Cg 1 ks
hg
hg为气相质量输运系数,Ks为表面化学反应速率常数
4. 氧化反应 利用氧气作为氧化剂促进反应:
SiH4(g) + O2 = SiO2(s) + H2O(g) (450℃) Si(C2H5O)4 + 8O2 = SiO2 + 10H2O + 8CO2
(Si(C2H5O)4是正硅酸乙酯 简称TEOS)
SiCl4 + O2 = SiO2 + 2Cl2 GeCl4 + O2 = GeO2 + 2Cl2
1) 反应物的
质量传输 气体传送
2) 薄膜先驱 物反应
3) 气体分 子扩散
4) 先驱物 的吸附
CVD 反应室
副产物
7) 副产物的解吸附作用
8) 副产物去除
排气
5) 先驱物扩散 到衬底中
6) 表面反应
连续膜
衬底
第四章 化学气相沉积----4.2 化学气相沉积
二、CVD动力学分析 1、CVD模型(Grove模型)
薄膜的生长过程取决于气体与衬底间界面的相互作用, 可能涉及以下几个步骤: (1)反应气体从入口区域流动到衬底表面的淀积区域 (2)气相反应导致膜先驱物(组成膜最初的原子或分
子)和副产物的形成 (3)膜先驱物附着在衬底表面
第四章 化学气相沉积----4.2 化学气相沉积
薄膜气相沉积

薄膜气相沉积薄膜气相沉积(Chemical Vapor Deposition,简称CVD)是一种常用的薄膜制备技术,广泛应用于材料科学、电子工程、光学、能源等领域。
本文将介绍薄膜气相沉积的原理、类型、应用以及未来发展方向。
一、原理薄膜气相沉积是通过在气相中控制化学反应,使气态前驱物分解并沉积在基底表面上形成薄膜的一种技术。
其基本原理是在高温下,将含有金属或非金属元素的化合物(称为前驱物)通过气体输送至基底表面,并在表面发生化学反应,生成所需的薄膜材料。
二、类型常见的薄膜气相沉积技术包括化学气相沉积(Chemical Vapor Deposition,CVD)、物理气相沉积(Physical Vapor Deposition,PVD)和分子束外延(Molecular Beam Epitaxy,MBE)等。
其中,CVD是最常用的一种技术,可以进一步分为热CVD、低压CVD和等离子体增强CVD等多种形式。
1. 热CVD:在高温下,将前驱物分解并沉积在基底表面上,常用于制备金属薄膜或非晶态材料薄膜。
2. 低压CVD:在较低的气压下进行沉积,常用于制备高质量的晶体薄膜,如多晶硅薄膜、氮化硅薄膜等。
3. 等离子体增强CVD:通过在气相中产生等离子体,使前驱物更容易分解并沉积在基底表面上,常用于制备氮化物、碳化物等复杂材料薄膜。
三、应用薄膜气相沉积技术在多个领域具有重要应用价值。
1. 电子工程:薄膜气相沉积技术可以制备金属、半导体和绝缘体薄膜,用于制造集成电路、光电器件和显示器件等。
2. 光学:薄膜气相沉积技术可以制备具有特定光学性质的薄膜,用于制造反射镜、透镜、光纤等光学元件。
3. 能源:薄膜气相沉积技术可以制备太阳能电池、燃料电池、光催化材料等,用于能源转换和储存。
4. 材料科学:薄膜气相沉积技术可以制备高温超导材料、磁性材料、涂层材料等,用于研究材料性质和开发新型材料。
四、发展方向薄膜气相沉积技术在过去几十年取得了巨大的发展,但仍存在一些挑战和改进空间。
材料合成与制备 第4章 CVD合成

沉积温度对氧化锌纳米材料形貌的影响
纳米氧化锌是重要的紫外发光材料,其在紫、蓝、绿光发光二极管 和激光器以及紫外探测器等方面显示了巨大的应用潜力,对于提高 光记录密度和光信息的存取速度将起到非常重要的作用。以氧化锌 粉为原料,采用化学气相沉积方法,在无需使用催化剂的情况下, 通过调控沉积温度分别得到了棒状、线状和螺旋状等形状各异的氧 化锌纳米材料。
化学气相沉积法制备GaN薄膜
GaN微纳米材料,由于其具有热产生率低、抗辐射、击穿电压高、电 子饱和漂移速度大和介电常数小的优点,已被广泛应用在高频、高温、高压 电子器件领域、发光二级管(LED) 、半导体激光器(LD)和太阳能电池等方面。
硅基底的CVD扩磷工艺
单晶硅的主要用途是用作半导体材料、利用太阳能光伏发电和供热等。 掺杂后的单晶硅可用于薄膜衬底材料、超大规模集成电路及太阳能电池。
Si基底CVD扩磷工艺如下: (1)向高温炉中通入氩气,当高温炉中的气压与外界气压相同时,气 体将高温炉门顶开,关闭气体。 (2)将清洗好的硅基底放在瓷舟上,该位置为高温炉第1温区。将红 磷装满2个瓷舟,关闭炉门。 (3)用氩气清洗气路和高温炉腔体3遍,关闭氩气,打开机器泵开始 抽真空。 (4)抽真空30 min后,打开升温系统开始升温,升温时间为2 h。 (5)当温度升到扩磷温度(1050/1150℃)时,通过高温热扩散运动向 硅基底扩磷。 (6)当达到实验时间后,通入氩气,当高温炉内温度降到室温后将样 品取出待检测。
第四章 化学气相沉积
一、化学气相沉积法的概念
化学气相沉积(中文版)2016

CVD 源材料
• 硅烷 (SiH4) • 四乙氧基硅烷 (tetra-ethyl-oxy-silane, TEOS ,Si(OC2H5)4)
CVD 源材料: 硅烷
• 自燃性的 (自己会燃烧), 易爆的, 以及有毒的 • 打开没有彻底吹除净化的硅烷气体管路, 可能引起火灾或是小爆炸,并形成微细的 二H
• 室温下为液态 • 化学性能不活泼 • 安全
H H H H C H H C H H H O
C C O Si O C C H
H H H O C H H H H C H H
CVD 源材料吸附:四乙氧基硅烷 (TEOS)
• 四乙氧基硅烷 (tetra-ethyl-oxy-silane, TEOS ,Si(OC2H5)4),也称正硅酸四乙酯 • 大型有机分子 • TEOS分子不是完整对称的 • 可以与表面形成氢键并物理吸附在基片表面 • 表面迁移率高 • 好的阶梯覆盖、保形性与间隙填充 • 广泛使用在氧化物的沉积上
–通常是 400 °C
• 等离子体增强-四乙氧基硅烷, 臭氧-四 乙氧基硅烷 和 高密度等离子体
CVD氮化硅的特性与沉积方法
• 很适合于作钝化层,因为 • 它有非常强的抗扩散能力,尤其是钠和水 汽在氮化硅中的扩散系数很小; •另外,还可以作PSG 或 BPSG的扩散阻挡层
CVD氧化硅与CVD氮化硅的特性
• Si(OC2H5)4+O2→SiO2+4C2H4+2H2O
成膜质量好,但如果铝层已沉积,这个温度是不允许的
PE-TEOS 对O3-TEOS
等离子体增强-TEOS 臭氧-TEOS
阶梯覆盖率: 50% 保形性: 87.5%
阶梯覆盖率: 90% 保形性: 100%
第四章--薄膜的化学气相沉积

压力梯度驱动的扩散过程使得该组元得以不 断到达衬底表面。
降低压力(提高扩散系数Di)将有利于提高气体 的扩散通量,加快化学反应进行的速度。
低压CVD就是利用这一原理,即采用了降低沉 积室压力的办法,加快气体组分的扩散和促 进化学反应的进行。
27
(四)表面吸附及表面化学反应
气体组分在扩散至薄膜表面后,还要经 过表面吸附、表面扩散、表面反应、反 应产物脱附等多个过程,才能完成薄膜 的沉积过程。
30
对CVD过程来说,尤其是当衬底温度 很低或者衬底表面已经被吸附分子 覆盖的情况下,Sc的数值可能很小; 而在气相与固相处于平衡下,Sc=0。
31
假设从物理吸附向化学吸附的转化过程为一 个一级反应,速率为
Rr krns krns0 (4- 54), 式中,kr为相应过程的速度常;数 ns、ns0分别为表面物理吸附子分的面密度 以及吸附分子可以占位据置的面密度。
20
二级反应 A+B=C+D (4-42) A、B两组元参加的正反应过程反应速率等于
R
knAnB
k
pApB (kT)2
(443)
式中, pA、pB为气体组A元 、B的分压; nA、nB为组元体密度
同样,两个组元A的分子参与的过程也属于二 级反应,这时,反应速率为
RknA2k(kp2A T )2 (4-44)
21
反应速度常数
k
k0e
E
RT,其
中K0系
数,
E为 反 应 过 程 的 激 活 能
图4.10示意性地画 出了化学反应从状 态1至状态2的自由 能变化曲线
22
反应总速率应正比于
Rk0n1e-RG*T-k0-n2e-G*RTG (4-47) G*和G*+G相 当 于 正 向 和 逆的向激反活应能 k0、k0-分 别 是 正 反 方 向速反度应常的数 的 系
第4章薄膜的化学气相沉积
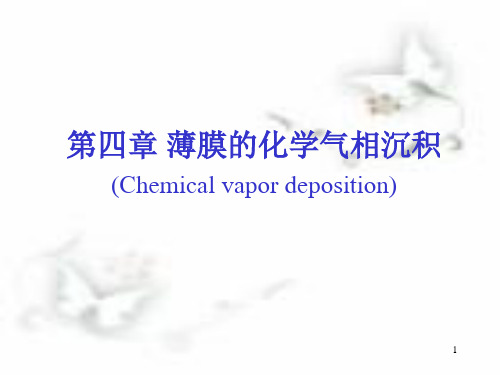
一、化学反应的自由能变化
1、化学反应的自由能判定式 对于一个化学反应总可以表达为: aA+bB=cC 自由能变化:△G=cGc-aGA-bGB 其中a、b、c分别为反应物和产物的mol数 Gi—是每mol i物质的自由能。 i=A,B, C 0 对于每种反应物:Gi Gi RT ln ai
①+② ×3,得到 总反应为:
1 CO 2 ( g ) CO( g ) O 2 ( g ) 2
②
△G0 =195.5kJ/mol
2YCl3 ( g ) 3CO2 ( g ) Y2O3 (s) 3CO( g ) 3Cl2 ( g )
此时, G0 195.5 3 248.7 337.8KJ / mol
27
这一自由能变化决定了反应将过于趋向于向左进行。 d)再用YBr3代替YCl3
2YBr3 g 3CO2 g Y2O3 s 3CO g 3Br2 g
此时:△G 0 = -450.8+337.8= -113 kJ/mol
•与此相对应的平衡条件要求:当系统的总压力为 0.2MPa时,YBr3的分压为1 kPa。
24
二、化学反应路线与自由能变化
1、单晶与多晶的生长条件
根据晶体的形核生长理论:要满足晶体的生长 条件,就需要新相形成自由能△G<0。
对于单晶:引入一个生长核心(△ G <0),同时要抑制其它的
晶核形成,确保单晶生长条件,就要△ G在数值上接近 于0 。显然在满足这一条件的情况下,应有相当数量的 反应物与反应产物处于一种平衡共存的状态 。
(450℃)
另外,还可以利用
SiCl 4( g ) 2H 2( g ) O 2( g ) SiO 2(s) 4HCl ( g ) (1500℃)
化学气相沉积法的原理CVD技术的反应原理

•
化学气相沉积的古老原始形态可以追朔到古人类在取 暖或烧烤时熏在岩洞壁或岩石上的黑色碳层。 作为现代 CVD技术发展的开始阶段在 20 世纪 50 年代主 要着重于刀具涂层的应用。 从 20 世纪 60 ~ 70 年代以来由于半导体和集成电路技术
•
•
发展和生产的需要,CVD 技术得到了更迅速和更广泛
•
•
•
随着激光的广泛应用,激光在气相沉积上也都得到利 用,激光气相沉积(LCVD)通常分为热解LCVD和光解L CVD两类,主要用于激光光刻、大规模集成电路掩膜 的修正以及激光蒸发-沉积。 在向真空方向发展方面在向真空方向发展方面,出现 了超高真空/化学气相沉(UHV/CVD)法。
•
这是一种制造器件的半导体材料的系统,生长温度低 (425~600℃),但真空度要求小于1.33×10Pa,系统的 设计制造比分子束外延 (MBE) 容易,其主要优点是能 实现多片生长。
•
此外,化学气相沉积制膜技术还有射频加热化学气相
沉积(RF/CVD)、紫外光能量辅助化学气相沉积(UV/CV
D)等其它新技术不断涌现。
•
•
•
4.2.1化学气相沉积法的概念 化学气相沉积乃是通过化学反应的方式,利用加热、等 离子激励或光辐射等各种能源,在反应器内使气态或蒸 汽状态的化学物质在气相或气固界面上经化学反应形成 固态沉积物的技术。 简单来说就是:两种或两种以上的气态原材料导入到一 个反应室内,然后他们相互之间发生化学反应,形成一种 新的材料,沉积到基片表面上。 从气相中析出的固体的形态主要有下列几种:在固体表 面上生成薄膜、晶须和晶粒,在气体中生成粒子。
第4章 化学气相沉积
第四章 化学气相沉积讲解

设在生长中的薄膜表面形成了界面层,其厚度为,cg和cs分别为 反应物的原始浓度和其在衬底表面的浓度,则
扩散至衬底表面的反应物的通量为: 衬底表面消耗的反应物通量与Cs成正比
平衡时两个通量相等,得
F1 hg (Cg Cs )
F2 ksCs
F1 F2
Cs
Cg 1 ks
hg
hg为气相质量输运系数,Ks为表面化学反应速率常数
第四章 化学气相沉积----4.2 化学气相沉积
1. 歧化反应
大多数歧化反应,源区只有在高温下才能生成可进行歧化反 应的中间产物,源区的反应器壁也要处于高温下,以避免在 反应器上进行沉积,如生成SiI2中间产物需要1150℃:
Si(s) + 2I2(g) → SiI4 (g) SiI4 (g) + Si(s) → 2SiI2 (g) 衬底区生成硅外延层的歧化反应只需900℃:
第四章 化学气相沉积----4.2 化学气相沉积
3. 热解反应 某些元素的氢化物和金属有机化合物高温下不稳
定,发生分解,产物可沉积为薄膜,反应是不可逆的。 如:
SiH4(g) = Si(s) + 2H2(g) Ni(CO)4(g) = Ni(s) + 4CO(g)
TiI(g) = Ti(s) + 2I 多晶硅沉积的生长温度可低至600℃;单晶硅则需850。 当需要低温工艺时,硅烷可作为理想的硅源来使用。
4. 氧化反应 利用氧气作为氧化剂促进反应:
SiH4(g) + O2 = SiO2(s) + H2O(g) (450℃) Si(C2H5O)4 + 8O2 = SiO2 + 10H2O + 8CO2
(Si(C2H5O)4是正硅酸乙酯 简称TEOS)
化学气相沉积技术

produce the desired deposit. Frequently, volatile by-products are also
produced, which are removed by gas flow through the reaction chamber.
速加热晶圆。只对基底加热,而不是气体或腔壁。可以减少不必要的气
相反应,以免产生不必要的粒子。
气相外延 (Vapor phase epitaxy, VPE)
……
34
化学气相沉积的特点
优点:
1)既可制作金属薄膜,又可制作多组分合金薄膜,且成分控制准确;
2)可在复杂形状基片上沉积薄膜,绕射性能好;
3)一些反应可在常压或低真空进行,不需要昂贵的真空设备;
超高真空CVD (Ultrahigh vacuum CVD, UHVCVD):
在非常低压环境下的CVD。大多低于10-6 Pa (约为10-8 torr)。大部
分现今的CVD制程都是使用LPCVD或UHVCVD。
30
化学气相沉积的种类
以气相的特性分类:
气溶胶辅助CVD (Aerosol assisted CVD, AACVD):
层位于最初表面以上。
8
SiO2薄膜的热氧化法制备
Oxidation technology
大多数热氧化在加热炉中进行,温
度800到1200℃。将基片放在石英
支架(石英舟)里,一个加热炉同
时可以处理一批基片。
水平炉和垂直炉
化学气相沉积过程
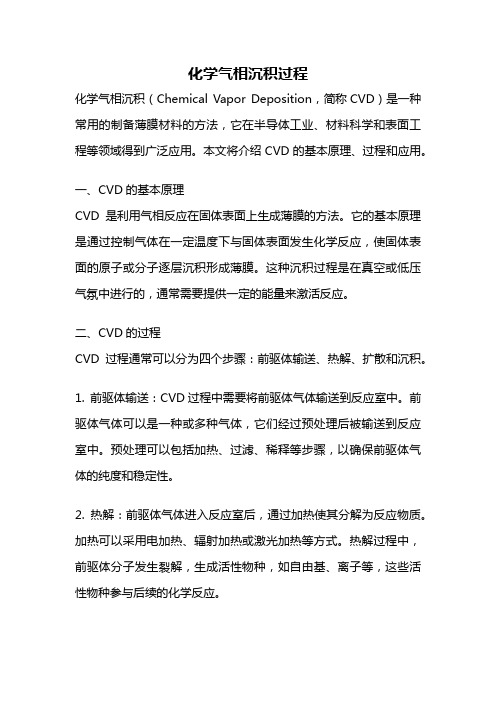
化学气相沉积过程化学气相沉积(Chemical Vapor Deposition,简称CVD)是一种常用的制备薄膜材料的方法,它在半导体工业、材料科学和表面工程等领域得到广泛应用。
本文将介绍CVD的基本原理、过程和应用。
一、CVD的基本原理CVD是利用气相反应在固体表面上生成薄膜的方法。
它的基本原理是通过控制气体在一定温度下与固体表面发生化学反应,使固体表面的原子或分子逐层沉积形成薄膜。
这种沉积过程是在真空或低压气氛中进行的,通常需要提供一定的能量来激活反应。
二、CVD的过程CVD过程通常可以分为四个步骤:前驱体输送、热解、扩散和沉积。
1. 前驱体输送:CVD过程中需要将前驱体气体输送到反应室中。
前驱体气体可以是一种或多种气体,它们经过预处理后被输送到反应室中。
预处理可以包括加热、过滤、稀释等步骤,以确保前驱体气体的纯度和稳定性。
2. 热解:前驱体气体进入反应室后,通过加热使其分解为反应物质。
加热可以采用电加热、辐射加热或激光加热等方式。
热解过程中,前驱体分子发生裂解,生成活性物种,如自由基、离子等,这些活性物种参与后续的化学反应。
3. 扩散:热解后的活性物种在反应室中扩散到固体表面。
扩散过程受到温度、压力、气流速度等因素的影响。
扩散过程中,活性物种与固体表面发生反应,形成沉积物质。
4. 沉积:活性物种与固体表面反应后,会形成沉积物质。
沉积物质的生成速率取决于活性物种的浓度、反应速率等因素。
沉积物质以层状结构逐渐沉积在固体表面上,形成所需的薄膜。
三、CVD的应用CVD广泛应用于半导体工业、材料科学和表面工程等领域。
具体应用包括:1. 半导体器件制备:CVD可用于制备半导体材料的薄膜,如硅、氮化硅、氮化镓等。
这些薄膜可以用于制作晶体管、光电二极管等器件。
2. 表面涂层:CVD可用于在材料表面形成保护性涂层,提高材料的耐磨性、耐腐蚀性和耐高温性能。
常用的涂层材料包括金属氮化物、碳化物等。
3. 光学薄膜制备:CVD可用于制备透明、反射或吸收特定波长的光学薄膜。
- 1、下载文档前请自行甄别文档内容的完整性,平台不提供额外的编辑、内容补充、找答案等附加服务。
- 2、"仅部分预览"的文档,不可在线预览部分如存在完整性等问题,可反馈申请退款(可完整预览的文档不适用该条件!)。
- 3、如文档侵犯您的权益,请联系客服反馈,我们会尽快为您处理(人工客服工作时间:9:00-18:30)。
Es RT
ns 为表面吸附分子的面密 度;k s 0为常数。 扩散现象可被视为一个 一级反应。
34
按照扩散统计理论,表面单位长度
上分子、原子的扩散通量为
dns J s Ds dx 式中,D s 为表面扩散系数, D s=D s0 e
Es RT
;
35
D s0 为常数
由此计算在一定时间间隔内,表面吸附分子、 原子的平均扩散距离为
结论: (1)沉积速率沿气体流动方向指数下降(反应物贫化引 起) (2)提高气体流速V和装置尺寸b有助于提高均匀性。 (3)调整温度分布,影响扩散系数D,进而调控沉积的 均匀性。
44
2c0 M si D R e bM g r
2 Dx
4vb 2
(4 - 78)
三、化学气相沉积装置
1. CVD系统的基本组成
扩散通量一般表达为
dni J i Di (4 - 50) dx
24
扩散过程的推动力是浓度梯度引起的组分
自由能梯度。如果dni/dx=0,则没有扩散 发生。 气相中组分的扩散系数Di应与气体的温度T
和总压力P有关。
p0 T n Di ( ) Di 0 p T0 (4 - 51)
Di 0为i组分在参考温度T0,参考压力p 0时的 扩散系数,它根据气体 的组分不同而有所改变 。
化学镀可以沉积一些金属膜,(Ni,Co,Pd, Au);也可用于制备氧化物膜(PdO2,TiO2, SnO2等)
特点:不需要高温,设备简单,经济实惠,
可大面积沉积
63
六、LB技术
利用分子的活性在气液界面上形成凝结膜,将 该膜逐次叠积在基片上形成分子层(或称膜) 的技术,称为Langmuir-Blodgett技术(LB技 术)。 LB技术是由Katharine Blodgett和Irving Langmuir 在1933年发现的。 利用LB技术,可以生长高质量、有序单原子层 或多原子层,其介电强度较高。
第四章 薄膜的化学气相沉积
化学气相沉积(CVD,chemical
vapor
deposition)
1
2
CVD模型
3
4
5
6
一、化学气相沉积热力学
要想得到单晶生长条件,基本做法是只引入一 个生长核心,同时抑制其他生长核心的形成。
根据晶体形核理论,要使晶体生长,需要新相 形成过程的自由能变化△G<0。 但是,要抑制多晶核的形成,确保单晶生长, 需要△G要尽量接近于零。也就是说,反应物 与产物近似于平衡状态。 如果△G为负且绝对值很大,会导致大量新晶 核同时形成,生成多晶。
65
LB技术的原理: (1)两性成膜材料溶解到有机溶剂中,
- G RT
(4 - 48)
K 为相应反应的平衡常数 ,与式4 - 18b比较后, 得到k 0=k 0-,即正反方向反应的速 度 常数的系数相等。
23
(三)气体组分的扩散
在CVD过程中,衬底表面附近存在着流动 性很差,厚度为δ的气相边界层。气相里
的各种组分只有经过扩散过程通过边界层,
才能参与薄膜表面的沉积过程。
量,即Sc≈1;
30
对CVD过程来说,尤其是当衬底温度 很低或者衬底表面已经被吸附分子 覆盖的情况下,Sc的数值可能很小;
而在气相与固相处于平衡下,Sc=0。
31
假设从物理吸附向化学吸附的转化过程为一
个一级反应,速率为
R r k r n s k r n s 0 (4 - 54), 式中,k r为相应过程的速度常数; n s、n s 0分别为表面物理吸附分子的面密度 以及吸附分子可以占据位置的面密度。 既是所有可能被占据的表面吸附位置中 已经被物理吸附分子所占据的比例。
64Leabharlann LB膜可以应用到电子仪器和太阳能转换 系统上。
LB膜研究领域如今已有长足发展,大量 材料如脂肪酸或其他长链脂肪族材料,用 很短的脂肪链替代的芳香族等都可形成高 质量的LB膜。 LB技术中,待沉积的分子一定要平衡亲 水性区和不亲水性区。分子链的一端是亲 水性的(如COOH),另一端为不亲水性 的(如CH3)。
45
46
47
48
49
2. 常见的CVD装置
50
51
52
53
电容耦合PECVD
阴极和衬底鞘层电位-污染
直流:导电薄膜 射频:导电或绝缘薄膜
不足: (1)电极表面高鞘层电 位,离子轰击阴极,产生 溅射污染。
(2)等离子密度很高时,
产生弧光放电,限制高功 率使用。
54
电容感耦合PECVD
当ks>>D/δ时,衬底表面的反应物浓度为零,反 应物的扩散过程较慢,在衬底附近反应物发生 贫化,这个过程为扩散控制的沉积过程;
相反,当 ks<<D/δ时,ns=ng,反应过程由较慢 的表面反应过程所控制,称为表面反应控制的 沉积过程。
41
反应导致的沉积速率为 ksngD Js R N 0 N 0 (D k s ) N 0为表面原子密度。 沉积速率随温度的变化 规律 取决于k s、D、等随温度的变化。
吸附、反应、脱附过程的快慢也可能会 成为薄膜沉积过程的控制性环节 。
28
29
气相组分向衬底表面的扩散通量为J;到 达衬底后被衬底表面俘获得几率为δ;被
反射离开衬底表面的几率为1- δ;
化学吸附几率为ζ;凝聚系数为Sc;Sc决
定了薄膜的生长速率
在各种物理气相沉积过程中,薄膜的沉
积速率只取决于蒸发、溅射来的物质通
32
(五)表面扩散
薄膜表面吸附的分子或原子也具有一定的扩 散能力,这也是薄膜结构与性能会产生巨大 差异的原因。
在薄膜表面,被吸附的分子和原子一般应处
于能量较低的势阱中。因此,吸附分子、原
子的扩散也需要克服相应的能垒Es。
33
单位表面上吸附分子、原子发生扩散的 速率为
Rs ns k s 0 e
D J g (n g n s ) (4 - 67) 其中,D是气相组元的扩散系数 。
同时,与衬底表面消耗的反应物对应的 反应物通量正比于ns,即
J s k sns
(4 - 68);
k s 是反应速度常数 达到平衡时,两个通量 相等
40
ng ns k s 1 D
(4 - 69)
22
反应总速率应正比于 R k 0 n1e -k 0-n 2e
G* RT G * G RT
(4 - 47)
G * 和G *+G相当于正向和逆向反应 的激活能, k 0 、k 0-分别是正反方向反应的 速度常数的系数
当化学反应达到平衡时 , R 0.这时, n 1 1 k 0 e n 2 K k 0
Dt e
Es 2 RT
上式表明,表面吸附分子、原子的扩散能力 随着温度的上升呈指数形式增加。 表面分子、原子的平均扩散距离随温度的变 化具体如何?
36
划分为沉积机制为主温度区间和脱附机
制为主的温度区间
37
(六)温度对CVD过程中薄膜沉积速 率的影响
温度是化学气相沉积过程中最重要的参数之
一。
假设在薄膜沉积过程中,薄膜的表面附近形
成了化学成分的界面层厚度为δ;ng 和 ns 分
别为反应物在远离表面处的浓度和其在衬底
表面的浓度。
温度对CVD过程影响如何?
38
低温:反应物充足、反应速度常数随温度升高指数增加。
高温:反应速度很快导致反应物不足,扩散限制沉积。 39
由此,扩散至衬底表面的反应物通量为
(2)表面吸附、表面反应的阶段。
第一阶段主要涉及了气体的宏观流动、气体分 子的扩散以及气相内的化学反应等三个基本过 程; 第二阶段涉及了气体分子大的 表面吸附与脱附、 表面扩散以及表面化学反应并形成薄膜微观结 构等三个微观过程。
10
(一)气体的输运
在CVD系统中,气体的流动处于黏滞流状 态。 气体在CVD系统中发生两种宏观流动:
研究表明:D和δ随温度变化较小。Ks随温度变化较大
42
(七)CVD薄膜沉积速率的均匀性
考虑Si在衬底上沉积生长时的CVD过程。
43
第一个边界条件假设了在衬底表面处,反应进行得很彻底, 没有残余的反应物存在; 第二个条件假设了在装置的上界面y=b处,物质的扩散项等于 零; 第三个条件假设了输入气体的初始浓度为c0。 经过推导得出薄膜沉积速度为:
正号表明相应的反应是可逆化学反应中
的正反应。
20
二级反应 A+B=C+D (4-42) A、B两组元参加的正反应过程反应速率等于
p Ap B R k n An B k (4 43) 2 (kT) 式中,p A、p B为气体组元A、B的分压; n A、n B为组元体密度
26
压力梯度驱动的扩散过程使得该组元得以不
断到达衬底表面。
降低压力(提高扩散系数Di)将有利于提高气体
的扩散通量,加快化学反应进行的速度。
低压CVD就是利用这一原理,即采用了降低沉
积室压力的办法,加快气体组分的扩散和促
进化学反应的进行。
27
(四)表面吸附及表面化学反应
气体组分在扩散至薄膜表面后,还要经 过表面吸附、表面扩散、表面反应、反 应产物脱附等多个过程,才能完成薄膜 的沉积过程。
7