进料检验管理办法
工程进货检验制度

工程进货检验制度一、总则为了保证工程项目的进货物资质量,保障工程施工的顺利进行,提高工程质量和项目管理水平,特制定本工程进货检验制度。
二、检验范围1. 进口原材料和设备2. 国内及外地原材料和设备3. 临时性物资及设备三、检验规定1. 根据项目需求,合理制定检验标准和要求。
2. 对各类进货物资进行抽样检验,实行合格产品进场,不合格产品退回原厂商或者报废处理。
3. 对检验工作过程中出现的问题进行及时调查,追踪处理。
四、检验程序1. 报关及交货(1)进口原材料和设备:境外厂商在报关过程中要提供产品质量证明和相关材料,并由国内进口商按时交货。
(2)国内及外地原材料和设备:要做好货物运输保障措施,确保货物运输过程中不受损坏。
2. 仓库验收(1)质检员在货物到达仓库时对货物进行验收,根据检验标准判定货物是否合格。
(2)不合格品及时退回原厂商,并根据情况要求厂商重新提供符合标准的产品。
3. 检验抽样(1)在仓库验收后,对货物进行抽样检验,以确保所检测的产品符合标准。
(2)对于特殊物资或设备,要进行更严格的检验。
4. 检验结果处理(1)合格品可进场使用,不合格品要求原厂商处理。
(2)对于多次出现不合格情况的供应商,要进行严格处罚或停止合作。
五、技术支持1. 对于工程进货物资检验过程中出现的技术问题和争议,可邀请相关专家进行技术支持。
2. 对于检验人员的培训和考核,要及时更新技术知识,提高检验水平。
六、责任追究对于因检验不到位导致的工程质量问题,责任人要承担相应的责任,并根据情况进行处罚。
七、附则1. 本制度自颁布之日起实施。
2. 工程项目经理有权对制度进行调整和完善。
3. 对于因违反本制度而造成的损失,相关人员要承担相应的责任。
以上为工程进货检验制度的内容,希望大家能够认真遵守并执行,共同保障工程项目的顺利进行。
进料检验管理流程是什么

进料检验管理流程是什么进料检验管理是很多管理者都想要学习的内容,那么你知道进料检验应该怎么管理呢?下面为您精心推荐了进料检验管理流程,希望对您有所帮助。
进料检验管理流程1、采购部对进料依据对外下达的采购订单开具“验收单”。
2、检验员收到验收单后,依据检验标准进行检验,并将进货厂家、品名、规格、数量等,填入检验记录表内,需要抽样的检验员必须亲自抽样。
3、判定合格,即将来料加以标识“合格”,填妥检验记录表及验收单内检验情况,并通知采购部办理入库手续;判定不合格,即将来料加以标识“不合格”,填妥检验记录表及验收单内情况,并将检验情况通知采购部。
需要办理回用的,由采购部填写《不合格品回用申请单》,按程序审批并考核。
批准后检验员对该批货物标识“回用”,并于检验记录表、验收单内注明回用处理情况,通知采购部办理入库手续。
4、原材料的检验应于收到验收单后两日内验毕,紧急需用的来料优先办理。
检验合格后,仓储部见合格单方可办理入库手续,未见通知单擅自办理入库,每次对相关责任人处以50-200元处罚。
5、检验时,如无法判定合格与否,则即请技术开发部、质量管理部、采购部、使用单位等派员会同验收,判定合格与否,会同验收者亦必须在检验记录表内签字确认。
进料检验管理制度1.本公司对物料的验收及入库均依本办法作业。
2.待收料。
物料管理收料人员在接到采购部门转来已核准的“采购单”时,按供应商、物料类别及交货日期分别依序排列存档,并于交货前安排存放的库位以利收料作业。
3.收料。
(1)内购收料。
①材料进厂后,收料人员必须依“采购单”的内容,核对供应商送来的物料名称、规格、数量和送货单及发票并清点数量无误后,将到货日期及实收数量填记于“请购单”,办理收料。
②如发觉所送来的材料与“采购单”上所核准的内容不符时,应及时通知采购部门处理,并通知主管,原则上非“采购单”上所核准的材料不予接受,如采购部门要求收下该批材料时,收料人员应告知主管,并于单据上注明实际收料状况,并会签采购部门。
进料验收管理办法

进料验收管理办法进料验收管理办法一、背景介绍进料验收是生产过程中非常重要的环节,通过对原材料或零部件的验收,可以有效控制产品质量,保障生产顺利进行。
进料验收管理办法是为了规范和指导企业在进料过程中的操作,确保进料的质量符合标准要求,降低产品质量风险,提高生产效率。
二、验收的流程及责任1. 进料验收的流程主要包括:采购部门与供应商谈判确定进料要求供应商送货质检部门对进料进行验收记录验收结果不合格品处理2. 验收责任分工:采购部门负责与供应商协商确定进料要求质检部门负责进行进料验收工作生产部门根据验收结果确定后续生产计划三、验收标准1. 进料验收标准应参照国家相关标准和公司内部标准,包括外观、尺寸、化学成分等方面的要求。
2. 不同类型的原材料或零部件应有相应的验收标准,对关键环节的生产原料要有更为严格的验收要求。
四、验收方法1. 外观检查:检查进料外观是否完整,有无变形、损坏等情况。
2. 尺寸检查:使用相应的测量工具对进料进行尺寸测量,看是否符合要求。
3. 化学成分检测:通过化验方法对原材料进行化学成分分析,确定其质量是否达标。
五、记录与归档1. 进料验收过程中应当及时记录验收结果,包括合格、不合格品的数量和问题描述。
2. 合格的进料应当按照标准要求归档保存,不合格品要及时处理并记录处理结果。
六、不合格品处理1. 不合格品应当及时挑选出来,并做好标识,通知供应商退货或处理措施。
2. 不合格品的责任追究:供应商责任:需要供应商负责处理不合格品,或承担相应的赔偿责任。
内部责任:如果是企业内部原因导致的不合格品,应当追究相关责任人责任。
七、总结进料验收管理办法的实施能够提高产品质量,降低风险,提高生产效率。
企业要不断完善进料验收流程,加强对进料质量的管控,确保产品质量稳定可靠。
ISO9001-2015进料检验管理办法

进料检验管理办法(ISO9001:2015)1.目的为使进料产品之质量能符合本公司之要求,使有关部门及供货商有法可依,特制订此管理办法,针对IQC的作业内容、抽样计划、AQL水准、不良处理等进行明确定义。
2.范围所有提供本公司之原材料、零件、半成品的供应厂商均适用之。
3.权责工程部:负责提供标准之Sample及相关零配件或产品之工程规格及HSF标准。
资材部:负责采购之安排,材料之供应,提供新厂商及送验通知。
品保部:负责进料之检验、检验规范之制定。
4.定义4.1.严重缺点( CRITICAL DEFECT )可能导致产品对用户之安全造成伤害之缺点,亦即违反安全规定,谓之严重缺点(CR)。
4.2.主要缺点( MAJOR DEFECT )使材料功能丧失或对制程造成不易排除之影响,致该材料不堪使用,数量不符及混料者,谓之主要缺点(MA)。
4.3.次要缺点( MINOR DEFECT )与承认书、工程规格书要求有差异,但不影响材料使用功能或该缺点易于排除者、外观不良及包装不良者,其缺点谓之次要缺点(MI)。
4.4.重工(REWORK)系指所生产原材料、半成品,因有瑕疪或不良,且超出允收水平被判拒收,针对此一批退原因而做相关之处理动作,谓之重工。
4.5.拒收(REJECT)系指所生产之原材料、半成品,有瑕疪或不良,且超出允收水平被判批退。
4.6.质量异常反应供货商生产之半成品、成品在进料检验发现有重大不良时,品管应开立【质量异常单】,同时知会采购及生管,SQE提出【矫正措施报告】至厂商,并追踪改善结果。
4.7. AVL:Approved Vender List 合格厂商名册4.8. MRB:Material Review Board 物料监审委员会4.9. FAI:First Article Inspection新产品首件检验表4.10. MRS:Material Recognition Standard 零件检验标准书4.11. HSF:Hazardous Substances Free 不含有有害物质4.12. HSF左证资料:包含“ICP测试报告、MSDS、材质证明书、不使用保证书(承认用)、环境物质不使用证明书(承认用、量产用)”4.13.MSDS:Material Safety Data Sheet 物质安全数据表5.作业内容5.1.仓储单位收料后,依《仓储管理作业程序》将货物搬至待验区,再由仓库填写《收料单》,《收料单》后需附有相关产品检验报告交至IQC检验。
原材料进厂检验管理制度
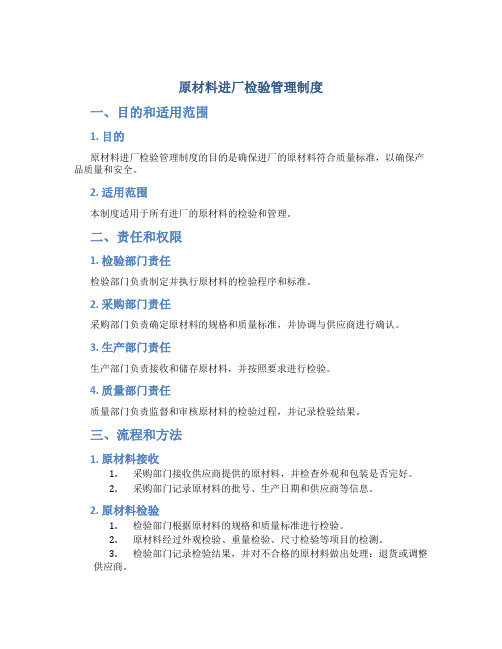
原材料进厂检验管理制度一、目的和适用范围1. 目的原材料进厂检验管理制度的目的是确保进厂的原材料符合质量标准,以确保产品质量和安全。
2. 适用范围本制度适用于所有进厂的原材料的检验和管理。
二、责任和权限1. 检验部门责任检验部门负责制定并执行原材料的检验程序和标准。
2. 采购部门责任采购部门负责确定原材料的规格和质量标准,并协调与供应商进行确认。
3. 生产部门责任生产部门负责接收和储存原材料,并按照要求进行检验。
4. 质量部门责任质量部门负责监督和审核原材料的检验过程,并记录检验结果。
三、流程和方法1. 原材料接收1.采购部门接收供应商提供的原材料,并检查外观和包装是否完好。
2.采购部门记录原材料的批号、生产日期和供应商等信息。
2. 原材料检验1.检验部门根据原材料的规格和质量标准进行检验。
2.原材料经过外观检验、重量检验、尺寸检验等项目的检测。
3.检验部门记录检验结果,并对不合格的原材料做出处理:退货或调整供应商。
3. 原材料储存1.符合质量标准的原材料由生产部门接收并储存。
2.生产部门储存原材料时,要确保储存区域整洁、干燥,并按照规定要求进行分类和标识。
4. 检验记录1.质量部门对每次原材料检验结果进行记录。
2.记录内容包括:批号、生产日期、供应商、检验项目和结果等。
3.检验记录应保存一定时间,以备查阅。
四、培训和评估1. 培训要求1.检验部门负责对相关人员进行原材料检验的培训,包括检验标准、方法和技巧等。
2.质量部门负责定期组织培训,提升相关人员的检验技能。
2. 评估要求1.质量部门负责对原材料检验的结果进行评估和总结。
2.评估包括原材料的合格率、不合格原因分析和改进措施等。
五、问题处理1. 不合格原材料的处理1.不合格原材料由质量部门与供应商协商处理,可以退货或调整供应商。
2.质量部门应记录原材料的不合格情况和处理结果。
2. 检验程序和标准的调整1.当发现检验程序和标准有不足之处时,检验部门有权对其进行调整和改进。
关于进料加工的规章制度
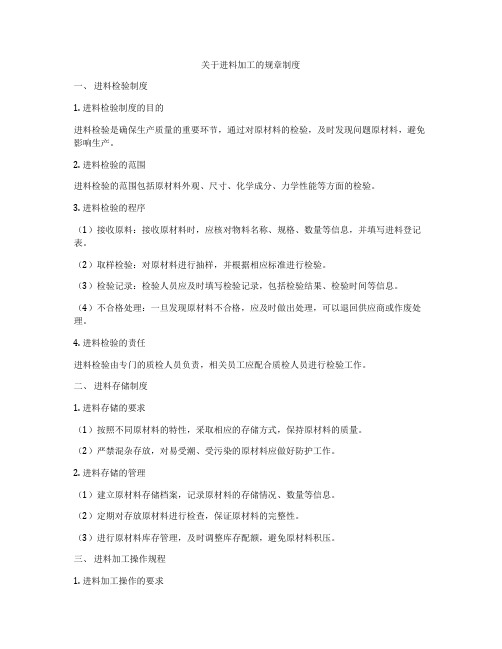
关于进料加工的规章制度一、进料检验制度1. 进料检验制度的目的进料检验是确保生产质量的重要环节,通过对原材料的检验,及时发现问题原材料,避免影响生产。
2. 进料检验的范围进料检验的范围包括原材料外观、尺寸、化学成分、力学性能等方面的检验。
3. 进料检验的程序(1)接收原料:接收原材料时,应核对物料名称、规格、数量等信息,并填写进料登记表。
(2)取样检验:对原材料进行抽样,并根据相应标准进行检验。
(3)检验记录:检验人员应及时填写检验记录,包括检验结果、检验时间等信息。
(4)不合格处理:一旦发现原材料不合格,应及时做出处理,可以退回供应商或作废处理。
4. 进料检验的责任进料检验由专门的质检人员负责,相关员工应配合质检人员进行检验工作。
二、进料存储制度1. 进料存储的要求(1)按照不同原材料的特性,采取相应的存储方式,保持原材料的质量。
(2)严禁混杂存放,对易受潮、受污染的原材料应做好防护工作。
2. 进料存储的管理(1)建立原材料存储档案,记录原材料的存储情况、数量等信息。
(2)定期对存放原材料进行检查,保证原材料的完整性。
(3)进行原材料库存管理,及时调整库存配额,避免原材料积压。
三、进料加工操作规程1. 进料加工操作的要求(1)严格按照工艺流程进行加工操作,确保产品的质量。
(2)操作人员应穿戴符合卫生要求的工作服,戴好防护用具。
2. 进料加工操作的程序(1)准备工作:包括准备所需原材料、设备、工具等。
(2)装料:将原材料按照规定比例装入设备中。
(3)加工操作:按照工艺要求进行加工操作,控制加工时间、温度等参数。
(4)复核检查:对加工后的产品进行复核检查,确保产品符合质量要求。
四、进料加工中的质量控制1. 质量控制的目的确保产品的质量稳定、可靠,提高产品的竞争力。
2. 质量控制的方法(1)设立质量控制点,对关键环节加强控制。
(2)实施巡检、抽检等方式进行产品质量的把控。
(3)建立质量档案,记录产品各项质量指标,以备查验。
来料检验管理办法及管理流程
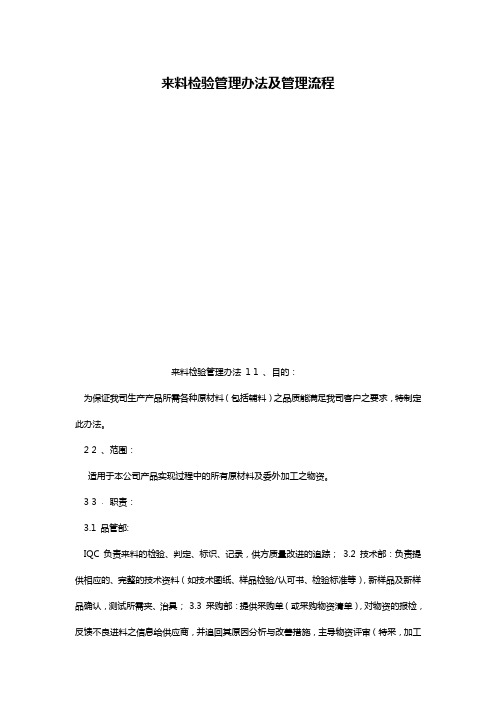
来料检验管理办法及管理流程来料检验管理办法1 1 、目的:为保证我司生产产品所需各种原材料(包括辅料)之品质能满足我司客户之要求,特制定此办法。
2 2 、范围:适用于本公司产品实现过程中的所有原材料及委外加工之物资。
3 3 ﹑职责:3.1 品管部:IQC 负责来料的检验、判定、标识、记录,供方质量改进的追踪;3.2 技术部:负责提供相应的、完整的技术资料(如技术图纸、样品检验/认可书、检验标准等),新样品及新样品确认,测试所需夹、治具;3.3 采购部:提供采购单(或采购物资清单),对物资的报检,反馈不良进料之信息给供应商,并追回其原因分析与改善措施,主导物资评审(特采,加工挑选等);向供方索要各类所需的报告3.4 销售部:负责处理与反馈客供不良物资之信息,提供客户特殊要求;3.5 仓库:负责进料的点收、送检、入库,协助采购部对不良物资的退货。
超安全存放期之物资的上线或出货前信息的反馈4 4 、各词定义:IQCIncoming Quality Control 进料品质控制AQLAcceptable Quality Level 允收品质水准MRBMaterial Review Board 物资评审委员会/小组CRI.Critical 致命缺陷(A 类):指在安装或使用过程中会对人的生命或财产安全造成明显或潜在的危害的缺陷MAJ.Major 主要缺陷(B 类):指会降低或失去产品功能或性能的缺陷或明显影响销售之外观缺陷MIN.Minor 次要缺陷(C 类):指不影响产品性能,装配,安全或销售等之外观不良,如轻微脏污、刮花、变形、披锋等。
5 5 、工作程序:5.1 进料检验管理流程见后所示;5.2 新样品确认由技术部进行,样品确认合格后封样给品管人员留样校对。
小批量(样品)试用,品管部IQC 参照采购与开发相关规定执行,必要时检验员做可追溯性标示或记录;5.3 外购或加工物资到达公司后,供方或加工方送货人员将采购物资送至仓库来料待检区,并按我司规定进行放置、防护、挂牌标示(必须包括产品或物资名称、编号、采购、销售订单号(通用件除外)、数量、送货时间及供应商或加工商名称)、采购、仓管员凭送货单与采购物资清单核对,清点无误后于供方送货单上签字暂收,然后仓库人员根据供方的送货单进行报检(外购成品由QA 检验、其它的物资由IQC 检验)若无送货单则由采购跟催或补填送货单,否则拒检;5.4IQC 检验员根据送货单、采购单(或采购物资清单),对所有物资进行先后检查(生产急用应先检,常规检测原则上在一个工作日内完成检验,需做耐久性测试的物料按品管部物料检验时间规定执行)。
进料检验管理办法

进料检验管理办法文件编号:1. 目的验证外协厂提供的产品是否满足规定的产品质量要求,确保不合格原材料和外购外协件不投入使用。
2. 适用范围本办法适用于本公司产品用原材料、外购外协件及包装箱进厂的检验控制。
(包括新产品开发、样件、小批量试制、批量生产)3. 职责3.1品管部:负责进料检验控制,进料检验员负责按检验标准对原材料、外购外协件进行检验,正确作出合格与否的符合性结论,并作好相关记录及检验状态标识;3.2工程技术中心:负责原材料标准的制订及工艺检验卡片的制订,并及时作好规范更改的传达;3.3 PMC部:负责原材料、外协件的采购,并负责不合格品的退货,对合格品及时做好相关产品标识,办理入库手续;3.4所有员工应确保和维护检验状态的标识。
4. 内容4.1原材料,外购外协件进厂应分类分批存放在仓库指定的地点,并以标识牌示“待检”;4.2检验员可采用以下一种或多种方式对进料产品进行验证;----针对外协厂提供的重要特性值的控制图和过程能力测定报告;----根据工艺检验卡片或图纸进行全数或抽样检验;----由认可的测试机构出具检验/试验报告并核对报告;----根据事先在质量协议中规定的检验项目,对外协厂所提供产品的质保书或自检报告进行确认。
4.3进料检验员接到《检验通知单》后,带上工艺检验卡片或图纸和检验工具和检验记录表到待检区;4.4进料检验员依据抽样计划对产品进行外观,尺寸,功能和包装的检查;4.5检验依急缓,特急的要在2小时内完成,急件要在4小时内完成,一般件应在8小时内检完;4.6检验员按照检验标准填写检验记录,并交给品管部主管确认,存档;4.7经检验合格之产品,检验员在产品或包装规定的位置贴上合格标签;4.8不合格原材料,外购外协件的控制依《不合格品控制程序》执行;4.9检验员将最终的检验结果,《检验通知单》返回给PMC部,PMC部进行入库或退货处理。
5. 相关程序文件5.1《检验控制程序》5.2《不合格品控制程序》6. 质量记录6.1《进货检验记录》6.2《供应商纠正与预防联络单》6.3《不合格品处置单》6.4《退货单》。
进货物资检验管理制度范文

进货物资检验管理制度范文一、概述进货物资检验是企业日常经营管理的重要环节之一,不仅关系到企业产品质量,还直接影响到企业的运营成本和客户满意度。
为了确保进货物资的质量和符合企业的要求,制定并实施进货物资检验管理制度显得尤为重要。
二、目的1. 确保进货物资的质量符合企业的技术要求和标准;2. 减少进货物资的质量问题及后续处理成本;3. 保证供应商按合同约定提供符合要求的物资;4. 提高企业产品的质量和客户满意度。
三、适用范围本管理制度适用于所有进货物资的检验,包括原材料、配件、设备等。
四、责任与权限1. 采购部门负责与供应商沟通和签订合同,并确定物资的技术要求和标准;2. 质量部门负责制定进货物资的检验方法、标准和程序,并组织实施;3. 采购人员负责监督供应商提供的物资是否符合合同和技术要求;4. 供应商负责提供符合要求的物资,并配合质量部门的检验工作;5. 生产部门负责接收质量合格的物资,并进行后续生产操作。
五、进货物资检验程序1. 采购人员在进货之前,应先与供应商进行沟通,明确物资的规格、质量要求和数量;2. 采购人员将采购合同和技术要求交给质量部门进行审核和确认;3. 质量部门根据技术要求,制定相应的检验方案,并告知供应商;4. 供应商将物资送至企业,质量部门对物资进行检验;5. 检验合格的物资,质量部门出具合格证明,并通知采购人员;6. 检验不合格的物资,质量部门通知供应商进行重新提供或处理;7. 采购人员接收合格的物资,并进行入库操作。
六、进货物资检验方法1. 外观检验:根据物资的外观要求,对物资进行外观检查,如有问题,及时沟通和处理;2. 尺寸检验:对物资的尺寸进行测量和检查,确保其符合技术要求;3. 材料检验:对物资的材料成分进行化学分析和性能测试,确保材料质量符合要求;4. 功能检验:对物资的功能进行测试,确保其满足使用要求;5. 包装检验:对物资的包装进行检查,确保包装完好无损;6. 其他特殊检验:根据具体物资的特殊要求,进行相应的特殊检验。
进料检验管理办法
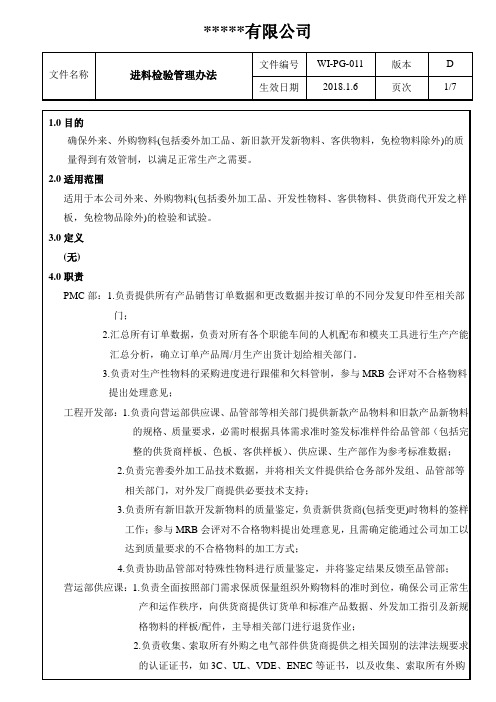
品管部:1.负责所有外来、外购物料(除免检物料外)的检验和试验,并保证在规定时间内完成物料检验,必需时向营运部供应课提供相关物料安规标准样板;
2.负责检验核对和保留所有外购之电气部件供货商提供之相关国别的法律法规要求的认证证书,如3C、UL、VDE、ENEC等证书,以及所有外购物料的环保报告,如出口欧洲国家的产品需提供符合欧盟RoHS指令的环保测试报告、出口美国的产品需提供符合美国联邦条例(US)要求的总铅含量报告;
5.3批量采购之质量检验
5.3.1仓务部根据供货商的《送货单》结合供应课的《采购单》,核对来料名称、型号、规格,并点清数量。
5.3.1.1核对结果正确时,将物料放置“待检区”或挂上“待检验”标示牌,在ERP系统内将《IQC检验报告》相关项目录入并反馈IQC进行检验和试验(新旧款开发新物料和免检物品除外),免检物品详见《免检物料一览表》);
2.负责完善委外加工品技术数据,并将相关文件提供给仓务部外发组、品管部等相关部门,对外发厂商提供必要技术支持;
3.负责所有新旧款开发新物料的质量鉴定,负责新供货商(包括变更)时物料的签样工作;参与MRB会评对不合格物料提出处理意见,且需确定能通过公司加工以达到质量要求的不合格物料的加工方式;
4.负责协助品管部对特殊性物料进行质量鉴定,并将鉴定结果反馈至品管部;
2.汇总所有订单数据,负责对所有各个职能车间的人机配布和模夹工具进行生产产能汇总分析,确立订单产品周/月生产出货计划给相关部门。
3.负责对生产性物料的采购进度进行跟催和欠料管制,参与MRB会评对不合格物料提出处理意见;
工程开发部:1.负责向营运部供应课、品管部等相关部门提供新款产品物料和旧款产品新物料的规格、质量要求,必需时根据具体需求准时签发标准样件给品管部(包括完整的供货商样板、色板、客供样板)、供应课、生产部作为参考标准数据;
金属材料检验规范

制订单位
核准
审核人
起草人
2011年2月14日修订
程序文件
标
题
金属类进料检验管理办法
页次
1 OF 3
编号
A-WI00-017
版次
第B版
▲钢板或钢带厚度的允许偏差单位:mm
公称厚度mm
在下列宽度时的厚度允许偏差
600-750
750-1000
1000-1500
1500-2000
2000-2300
3.3.2因次要缺点被判不接收,无致命缺点、重要缺点,且不影响整机产品性能的材料。
3.3.3因不合格品所占本次送检总数的比例大于10%被判不接收,有条件逐个检测剔除不良品的。
3.3.4有条件返工、维修,且重新通过检验的被判不接受品。
3.4判定接收材料,须在材料上贴“检验合格”标签或印章,判定不接收材料要贴“不接收”标签。
注:表中规定的不平度只适用于屈服点下限值不超过460N/mm²的钢板,屈服点超过的以及进行调质的钢板,其不平度的最大值为表内规定的1.5倍。
2.3.4.化学成分分析及机械性能实验:需要时可进行材质分析和性能试验。
2.4型钢
2.4.1验证要求:型钢报检时必须提交该批型钢符合标准要求及订货合同的质量证明书。
0.9
1.1
>9-10
1.0
0.2
0.3
0.4
0.6
0.9
1.2
>10-11
1.1
0.3
0.4
0.6
0.7
1.0
1.3
>11-12
1.2
0.4
0.5
0.7
0.8
1.1
1.4
材料进场检验及储存管理制度模版
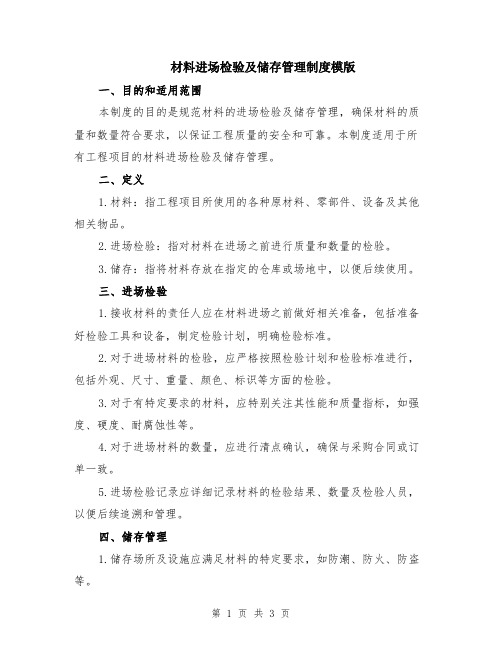
材料进场检验及储存管理制度模版一、目的和适用范围本制度的目的是规范材料的进场检验及储存管理,确保材料的质量和数量符合要求,以保证工程质量的安全和可靠。
本制度适用于所有工程项目的材料进场检验及储存管理。
二、定义1.材料:指工程项目所使用的各种原材料、零部件、设备及其他相关物品。
2.进场检验:指对材料在进场之前进行质量和数量的检验。
3.储存:指将材料存放在指定的仓库或场地中,以便后续使用。
三、进场检验1.接收材料的责任人应在材料进场之前做好相关准备,包括准备好检验工具和设备,制定检验计划,明确检验标准。
2.对于进场材料的检验,应严格按照检验计划和检验标准进行,包括外观、尺寸、重量、颜色、标识等方面的检验。
3.对于有特定要求的材料,应特别关注其性能和质量指标,如强度、硬度、耐腐蚀性等。
4.对于进场材料的数量,应进行清点确认,确保与采购合同或订单一致。
5.进场检验记录应详细记录材料的检验结果、数量及检验人员,以便后续追溯和管理。
四、储存管理1.储存场所及设施应满足材料的特定要求,如防潮、防火、防盗等。
2.材料应按照种类、规格、质量等进行分类管理,并做好标识,以便于查找和使用。
3.储存的材料应定期检查并做好记录,包括数量、质量和储存状态等。
4.对于易损、易腐蚀的材料,应采取相应的防护措施,确保其不受损害。
5.不符合要求的材料,应及时做好退换处理,并制定相关流程和记录。
6.材料的领用应按照工程进度和需要进行,做好记录,并确保领用数量和使用情况一致。
五、责任和考核1.进场检验的责任人负责制定检验计划、执行检验工作,并做好相关记录。
2.储存管理的责任人负责监督材料的储存,保证其安全和整洁。
3.对于材料进场检验不符合要求的,应追究相关责任人的责任,并进行相应的处理。
4.对于材料储存管理不到位的责任人,应进行相应的考核和惩罚。
六、附则1.本制度的解释权归工程项目管理部门所有。
2.本制度的修改和补充应经过相关部门的审批和批准。
HS-71-01进料检验管理办法

6.4.8检查批的标识入库:检验合格的物料,检验员在货箱上贴上相关的检验合格标签或盖IQC检验合格章(附件3),检验不合格的物料,检验员在货箱上贴上不合格标签或盖IQC检验不合格章(附件3),IQC检查员在送货单上填写相关质量结果签名后交文员入电脑MRP系统,同时将送货单送交相关仓管员,合格批由仓管员把物料从待检区移到合格区入库,不合格由仓管员把物料从待检区转移到不合格品放置区。
6.4.4紧急物料的放行:当公司收到采购物料,因生产急需来不及检验,由相应部门申请,质量管理部负责人批准,予以放行,IQC人员对该批物料做好产品主动性标识,记录、通知仓库人员发料且做好记录,同时IQC检查员对该批物料继续抽样检查。由PQE人员进行跟踪,如生产过程中发现不合格或IQC抽样发生不合格时,停止生产,并撤回该批物料。
8.2物料不良问题/不合格发生通知书跟进表(HS-71-01-02)
8.3 CKD SKD套料检验报告(HS-71-01-03)
8.4 IQC来料检验报告(HS-71-01-04)
8.5不合格发生通报书(HS-71-01-05)
8.6原材料年度试验计划(HS-71-01-06)
检查员有对于实施了管理检查的供应商计划进行访问/调查的权利,供应商的品质管理经考评不合格时质量管理部总经理承认后取消管理检查。
3.9免检:本厂无法作进料检验,但可由制程中检验判定其质量之好坏之原物料及质量稳定之原物料和不影响产品质量之五金工具、文具用品、包装材料等一般辅料进厂不作进料检验,对关键辅料或其它根据品质情况及技术情报,认为品质特性良好的物品。
IQC进料检验管理办法-1

5.2.3将异常现象记录在<进料履历表>上﹐为下次检验时检验的重点,防止检验漏失,并做为改善检验方法,提升不良检出能力之依据。
5.3仓库内原料﹑油漆油墨﹑辅材如有超出有效期时﹐仓库人员通知IQC人员对其重新确认。
6.参考文件
517客供物料于进料检验制程中发现规格数量质量等不符时email请客户及相关部门裁决如客户与相关部门意见一致则依裁决作业如不一致则召开会议依会议决议作业
文件编号:QS-SAD-003
翼晖盛科技(深圳)有限公司
IQC进料检验管理办法
编制:_________日期:2013-01-20
审核: _________日期:2013-01-20
《MIL-STD-105E》抽样计划表
7.表单
<进料验收单>
<环境/品质异常处理报告>
<进料履历表>
5.1.6.1 IQC将检验结果记录于<进料验收单>﹑<进料履历表>上。
5.1.6.2依IQC<进料验收单>及相关资料作出相应之日、周、月报表。
5.1.6.3表单的审核权限﹕
1) <。
2) <进料检验报告>﹕由检验员填写﹐组长审核后再由课长核准
5.1.6.4所有的数据进行保存依<质量记录管制程序>进行管控。
5.1.7客供物料于进料检验、制程中发现规格、数量、质量等不符时,e-mail请客户及相关部门裁决,如客户与相关部门意见一致则依裁决作业,如不一致则召开会议依会议决议作业。
5.2制程材料异常之处理:
5.2.1若制程出现材料异常时,IQC人员应立即至现场进行确认,如属来料不良,则根据当时的物料状况,物料不良的比率及严重性,作出有效的处理对策,并汇报到部门主管处。
材料进场检验及储存管理制度范本

材料进场检验及储存管理制度范本第一章总则第一条为规范材料进场检验及储存管理,确保材料质量和安全,提高施工质量,制定本制度。
第二条本制度适用于本单位所有材料的进场检验及储存管理,包括但不限于建筑材料、设备材料等。
第三条材料进场检验及储存管理应遵循“安全第一、质量第一、合理使用、节约为主”的原则。
第二章进场检验第四条进场检验的目的是确保材料的质量和数量符合规定,达到使用要求。
第五条进场检验应严格按照有关标准和规定进行,不得随意放行。
第六条进场检验应包括外观检查、尺寸检测、性能测试等项目,具体检验内容根据不同的材料确定。
第七条进场检验应由专业人员进行,必要时可委托第三方检验机构进行抽样检测。
第八条进场检验不合格的材料,应及时办理退货手续,并对退货原因进行分析,以便采取措施避免类似情况再次发生。
第九条进场检验合格的材料,应及时标识并妥善保管,防止混用和损失。
第十条进场检验记录应详细、准确,包括材料的名称、规格、批号、生产日期等信息,并保存备查。
第三章储存管理第十一条储存管理的目的是保证材料的质量和数量不受损失,便于使用和管理。
第十二条储存场所应选择坚固、干燥、通风良好的地方,防潮、防尘、防火措施必须到位。
第十三条不同种类的材料应分别存放,防止混淆和交叉污染。
第十四条储存材料应按照先进先出原则,合理组织摆放和堆垛,确保易腐、易损材料得到及时使用。
第十五条储存材料应定期检查和清理,防止变质、腐蚀等情况发生。
第十六条储存材料应标识明确,包括材料的名称、规格、批号等信息。
第四章监督检查第十七条监督检查的目的是确保材料进场检验及储存管理制度的实施效果。
第十八条监督检查应随机抽查材料的进场检验记录和储存情况,对不合格情况及时处理。
第十九条监督检查应由专业人员进行,结果应及时通报相关责任人,监督整改措施的落实。
第五章处罚措施第二十条对于严重违反材料进场检验及储存管理制度的行为,将给予相应的处罚。
第二十一条处罚措施包括但不限于警告、罚款、停工整顿、追究责任等,根据实际情况确定。
原材料进厂检验管理制度[五篇材料]
![原材料进厂检验管理制度[五篇材料]](https://img.taocdn.com/s3/m/3e72086b2f3f5727a5e9856a561252d380eb203a.png)
原材料进厂检验管理制度[五篇材料]第一篇:原材料进厂检验管理制度原材料进厂检验管理制度第1章总则第1条:目的为检查生产用原材料、辅料的质量是否符合企业的采购要求提供准则,确保来料质量合乎标准,严格控制不合格品流程,特制定本制度。
第2条:适用范围适用于所有进厂用于生产的原、辅材料的检验和试验。
第3条:定义来料检验又称进料检验,是工厂制止不合格物料进入生产环节的首要控制点。
来料检验由品管部来料检验员具体执行。
第4条:职责(1)品管部负责进货的检验和试验工作。
(2)库房负责验收原材料的数量(重量)并检查包装情况。
(3)品管部制定《来料检验控制作业标准》。
第2章来料检验的规划第5条:明确来料检测要项(1)来料检验员对来料进行检验之前,首先要清楚该批货物的质量检测要项,不明之处要向来料检验主管咨询,直到清楚明了为止。
(2)对于新来料,在明确该料的检测标准和方法之后,将之加入《来料检验控制作业标准》。
第6条:影响来料检验方式、方法的因素(1)来料对产品质量的影响程度。
(2)供应商质量控制能力及以往的信誉。
(3)该类货物以往经常出现的质量异常。
(4)来料对公司运营成本的影响。
(5)客户的要求。
第7条:确定来料检验的项目及方法(1)外观检测。
用目视、手感、嗅觉、口尝、限度样品进行验证。
(2)尺寸检测。
用卡尺、千分尺等量具验证。
(3)结构检测。
用拉力器、扭力器、压力器验证。
(4)特性检测。
如物理的、化学的、生物的、机械的特性,一般采用检测仪器和特定方法来验证。
第8条:来料检验方式的选择(见抽检方案)(1)全检。
适用于来料数量少、价值高、不允许有不合格品物料或工厂指定进行全检的物料。
(2)抽检。
适用于平均数量较多,经常性使用的物料。
(抽检比例≥3%)第3章来料检验的程序第9条:品管部制定《来料检验控制标准及规范程序》,由品管部经理批准后发放至检验人员执行。
检验和试验的规范包括材料名称、检验项目、标准、方法、记录要求。
- 1、下载文档前请自行甄别文档内容的完整性,平台不提供额外的编辑、内容补充、找答案等附加服务。
- 2、"仅部分预览"的文档,不可在线预览部分如存在完整性等问题,可反馈申请退款(可完整预览的文档不适用该条件!)。
- 3、如文档侵犯您的权益,请联系客服反馈,我们会尽快为您处理(人工客服工作时间:9:00-18:30)。
供应商管理办法
进料检验管理办法
为确保进料品质,能及适时供应生产现场所需物料、半成品,以使制程顺畅提高生产力,降低成本,特制定本标准,以为遵循。
二、适用范围:
凡本厂生产所需之物料,半成品均适用之。
三、说明:
a)定义::无
2.1.抽样方式:
2.1.1 零件进料检验系统采用下列一项或多项方法:
(A).取得并评估统数据。
(B).进料检验后测试。
(C).在外协厂商处所执行的第二者评鉴,且记录显示可接受的品质绩效。
(D).委由认证合格实验室实施的零组件评估。
2.1.2 当客户提出要求时,应使用认证合格的实验室设备,并依照《实验室作业管理
办法》执行。
2.1.3 实施产地检验之部品,其抽样方式以当批生产总数按照正常抽验方式检验
并记录,该记录可续用至当批生产部品完全纳入本厂为止。
2.1.4 计数值数据之抽样计划其允许规范必须为零缺点。
2.1.5 抽样计划表:
(A).抽样表(一)
抽样表(二)
(B).抽样表(三)
(C).抽样表(四)
(D).抽样表(五)
2.1.6 运用方式:
(A ).批量或交货量小于抽样数或严重缺点而品质不稳定时,实施全检。
(B).抽样表(一)表(二)之减量、正常、加严等三种检验其转换时机和
程序如下:
(a ).开始检验时采用正常检验。
(b ).正常检验 加严检验:实施正常检验时连续5批进料中,有2批被
拒收时改用加严检验。
(c ).加严检验 正常检验:实施加严检验时,连续5批进料均被允许时,
改用正常检验。
(d )
.正常检验 减量检验:实施正常检验时,连续10批进料均被允许
时,改用减量检验。
(e ).减量检验 正常检验:实施减量检验时,有一批进料均被拒收时,改用正常检验。
有一批拒收 连续10批均允许
2.2.检验:品保课在接获采购课转出之进料验收单后,依照零件检验标准进行1材
质、2 外观、3 尺寸、4 性能之确认,并确认结果记录于检验记录表存查。
2.2.1 进料检验人员接到采购课转出之进料验收单,抽样时在进料篮、箱、袋数上中下平均抽检,完成检验作业后再将进料检验收单转采购课。
2.2.2 进料检验用来比对之标准样件以标准样件挂签[附件一]标示品名,品号及有效日期,并经单位主管签核后登录于标准样件储位索引表,而对于电镀之外观对样件,每半年至少更换一次。
2.2.3 在协力厂商所执行之产地检验,厂商于进料时随进料验收单附上本厂所提
供或认可这检验记录表影本,交予采购课入帐后,转品保课由品保人员依检验记录表查验无误后即判定入库。
2.2.4 若生产急须之物料,由采购课通知进料检验单位先行检验。
当零件进料检
验,未经检即须行供紧急生产之用时,可由品保课先盖上红色长方形未验放行章[附件二],以供标识及便尔后有发现不符合规格要求时,能够立即回收加以更换。
2.3.免检:品保课人员接获免检物料对照免检产品一览表后,经查验无误记录于免检产品查证记录表即判定入库存,并且将待验挂签[附件一]撕至免检位置且盖上蓝色合格章[附件二],其余参照《外协厂商品质保证管理办法》实施之。
2.4.呆滞物料:品保课人员接获信息后,依照HH/QSP.20《不合格品控制程序》实施,将检查结果记录于呆滞物料复判规范暨录表存查。
2.5.判定:
2.5.1 判定合格之物料则检验人员将待验挂签[附件一]盖上蓝色菱形合格章[附
件二]。
2.5.2 判定不合格之物料由检验人员将待验挂签[附件一]盖上红色菱形不合格间
[附件二]。
2.5.3 于每日下午3:30由品保课填写拒收会报讨论表,并召集相关单位共同检
讨,有关尺寸不良部分须研发部会认,其它题由相关单位会认即可入库。
(A).拒收会报判定验退之物料,由检验人员盖上红色菱形批退章[附件一],并打印初检退料单,转采购课执行退料。
(B).拒收会报判定待处理之物料,由品保课人员于拒收会报讨论表,注明验收原因及签章以利追踪确认,再由检验人员判定入库及盖上蓝色菱形复
判合格章[附件二]。
(C).拒收会报判定待处理之物料,由品保课人员挂上待处理挂牌[附件一],并须于三工作日内由品保人员处理完毕,如判定验收须注明验收原因及签
章以利追踪确认。
(D).拒收会报判定特采之物料,由采购课开立特采申请单,转各相关单位会签,如重复性之特采须经理以上人员签核,其于一般性特采则由部门主管
核准即可后。
将特采申请单转品保课及采购单位分别存盘。
(E).特采完成签认后,品保课将单据判定入库,并须在货品标签上加盖“特采”标识。
IQC-抽样计划表
AC=允许/RE=拒。