精益生产ov讲义erview
精益生产培训讲义(ppt 197页)

5、库存的浪费(含中间在制品)
库存浪费的主要表现:
产生不必要的搬运、堆积、防护、寻找等; 使FIFO作业困难; 占用资金(损失利息)及额外的管理费用; 物品的价值衰减,变成呆料、废料; 占用空间,仓库建设投资增加; 掩盖问题、能力不足被隐藏。
39
库存隐藏的问题
庫存
廢料
機器當機 廠商散漫
過度的工程設 計
20
案例
习惯
素养 5S 6SK
整理
整顿
清扫
清洁
健康
21
第二章 认识浪费(Muda)
不同的经营思想 每天都在“烧”钱 全面生产系统(5MQS)的浪费 工厂中常见的8大浪费
22
不同的经营思想
成本中心型: 以计算或实际的成本为中心,加上预先设
定的利润,得出售价。 计算公式: 售价=成本+利润
卖方市场;消极被动; 企业类别:
高新产品 垄断产品 国内的铁路、民航等
23
不同的经营思想
售价中心型: 以售价为中心,当市场售价降低时,
利润随之减少。 计算公式:利润=售价-成本
市场好时有较高的利润;市场差时利润大 幅度降低; 企业类别:
缺乏改善意识的企业
24
不同的经营思想
利润中心型: 以利润为中心,当市场售价降低时,成本
也必须降低,以便获得的利润(目标利润)不 会减少。
与传统的大批量生产相比,精益生产只需要一 半的人员、一半的生产场地、一半的投资、一半 的生产周期、一半的产品开发时间和少得多的库 存,就能生产质量更高、品种更多的产品。
13
制造业是“服务业”
制造业
以生产企业为主导 批量生产
设法增加产量
服务业
精益生产培训讲义(PDF 68页)
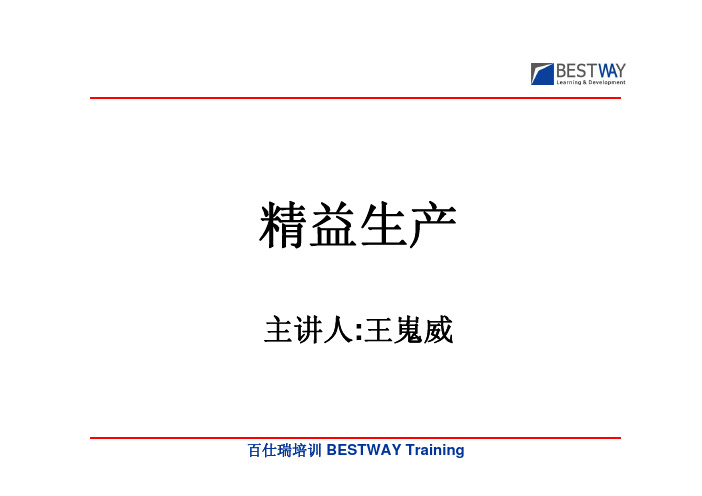
6内部用户原则来自用户 供货单位用户 供货单位
用户 供货单位
不接受 不良品
不提供 不良品
工位A
不生产不良品 工位B
物流
工位C
百仕瑞培训 BESTWAY Training
7
精益生产的来历
1. 丰田生产方式的形成及其推广 2. 美国工业的困惑 3. 美国对丰田生产方式的研究 4. 精益生产方式的兴起
百仕瑞培训 BESTWAY Training
16
5库存
特点: 在进货仓库中占据额外空间
物流停滞 更多的材料资源 出现问题的大规模返工 对客户要求反应迟缓
原因: 过程能力低下
更换品种时间长 管理决策不当 不准确的预测系统
通过库存维持生产
降低库存暴露问题
缺勤
质量
率高
低劣
计划
性差
机器 故障
销售 问题
生产不均衡
换模 时间长
缺勤
质量
率高
低劣
计划
性差
机器 故障
2
我们每天工作的工厂?…
顾客是上帝
销售
轰隆隆!轰隆隆!!
YES
超时加班
额外费用
未预计的订单变化
NO 订单下达到工厂
快!119
百仕瑞培训 BESTWAY Training
3
生产方式的变革
单单件件生生产产方方式式
大大量量生生产产方方式式
精精益益生生产产方方式式
百仕瑞培训 BESTWAY Training
劳模?
13
2等待的浪费
特点: 观察机器 质量检验 等待材料 品种切换 机器故障 生产不均衡
原因: 不一致的工作方法 机器设置时间长 人员效率不高 缺乏设备资源 缺乏合适的机器
精益生产全讲义
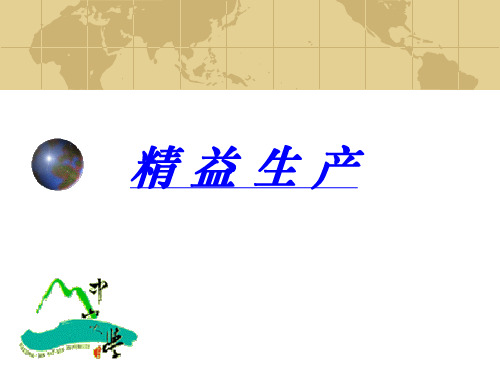
手工生产方式 完全按顾客要求 通用、灵活、便宜
粗略、丰富
懂设计制造 有较高操作技能
高 高 低 极少量需求
大批量生产方式
精益生产方式
标准化,品种单一 品种多样化、系列化
专用、高效、昂贵 柔性高、效率高
细致、简单、重复 不需要专业技能
较粗略、 多技能、丰富
待
8
管理的浪费
管理本身成为一种专 职的工作发生的浪费
事后管理的浪费
41
1、不良、修理的浪费
材料的损失; 设备、人员、工时的损失; 额外的修复、选别、追加检查; 额外的检查预防人员; 降价处理; 出货延误取消定单; 信誉下降; ……
42
2、加工的浪费
△
●
○
自动 插件
●
焊接 组装1 组装2 检测
○
◎
◎
●
包装 ●
徐小凤 ●
○
◎
○
◎
○
△
多技能员工 金 庸 ○
△
●
△
◎
◎
韦小宝 ◎
○
○
●
F4
○
◎
●
○
◎
拉登 ◎
●
△
●
○
萨达姆 △
●
◎
●
○
◎
吕不韦 ●
○
△
○
●
备注:△—计划学习,○—基本掌握,◎—完全掌握,●精通
27
案例
QC小组活动
Q C C uality ontrol ycle
多技能
高
低 高 物资缺乏、供不应 求
低 更低 更高 买方市场
精益生产培训讲义正式授课版
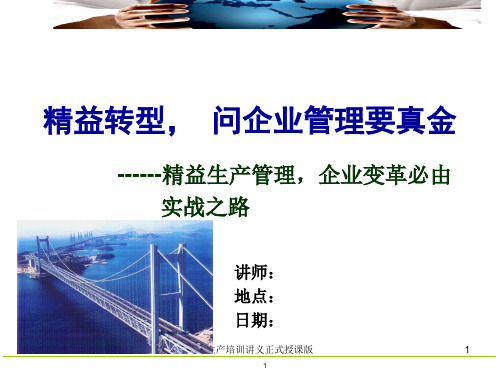
丰田生产方式 11
丰田背景
丰田佐吉 丰田喜一郎 神谷正太郎
丰田英二 大野耐一
丰田章一郎
TQM TPS
│
田神小 临公一
汽
自 ,改 农 动善思 织日想 布 式 ,即 机织不
破司九 产」三
,一 七 九年 四创
车 导 入 美
工布浪
0立
国
厂机费
年「
市
丰精
濒丰 田
场
造一
发
与九
展
导五
入0
年
代
创
精益生产培训讲义正式授课版
JIT的基本思想是:只在需要的时候、按 需要 的量、生产所需的产品,故又被称为准 时制生产、适时生产方式、广告牌生产方式。
JIT的核心是:零库存和快速应对市场变 化。
精益生产培训讲义正式授课版
26
JIT实施过程
J I T ust n ime
适品 ·适量 ·适时
适时化
生产 均衡化
生产
安定化
生产 流线化
90%
精益生产培训讲义正式授课版
24
课课程程指指引引
第四部分
JIT(Just In Time)准时化生产
1
什么叫JIT,其核心和原则是什么?
2
JIT实施过程、什么叫一件流
3
均衡化实施步骤与技巧
4
后拉式广告牌作业原则优点及要求条件
精益生产培训讲义正式授课版
25
JIT
J I T ust n ime
适品 ·适量 ·适时
即LeanProduction。
经过4年研究 1996年着出。“国际汽车计划”(IMVP)第二阶 《精益思想》 段研究结果 弥补了前一研究成果并没有对怎样能学习精益生产
精益生产基础培训讲义

與大量生產思想觀念的變革
四.精益生產的精髓
2.“瘦”,豐田式“瘦型”生產方式 “減肥”運動,剔除多余的機構,富余的人力, 把無效益的事情都砍掉.
四.精益生產的精髓
3.在制品是萬惡之源,提倡在制品向零挑戰.
大量生產把一定量的在制品當作 均衡生產的必要條件
严格把控质量关,让生产更加有保障 。2020 年11月 下午8时 21分20 .11.252 0:21No vember 25, 2020
重规矩,严要求,少危险。2020年11 月25日 星期三8 时21分 55秒20 :21:552 5 November 2020
好的事情马上就会到来,一切都是最 好的安 排。下 午8时21 分55秒 下午8 时21分2 0:21:55 20.11.2 5
(4)不重要也不緊急
馬上辦理
輕
好好規劃
重
馬上辦但只花一點時間
或找人代辦 緩
有空再辦
急
c.工作的時段管理
(1)早上八點至十點: 精力顛峰,適合作規劃 (2)早上十點至十二點:注意力及短暫記憶力最強,
適合腦力激蕩會議,訓練等. (3)下午一點至二點:昏昏欲睡,適合互動溝通工作. (4)下午二點至四點:開始清醒,長期記憶力最淺,適
例:
某日一機臺投入24Hour,其中保養1Hour,機故維修
0.5Hour,待料2Hour.則當日:
24-1-0.5-2
稼動率=
×100%=85%
24
可動率=
24-1-0.5 22
×100%=94%
4.平衡率:
各工序平均工時
平衡率 =
×100%
精益生产讲义
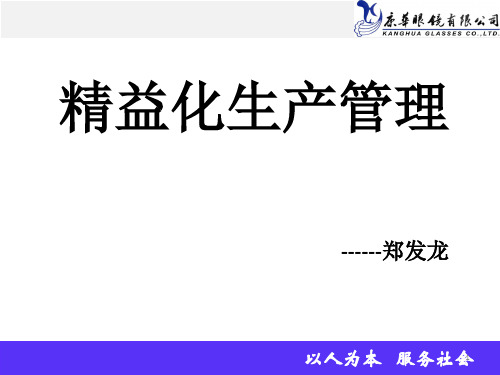
• 操作员熟练度 • 操作员习惯性 • 操作员有没有依照操作标准作业 • 操作员之体力与情绪 • 操作员的工作场所及使用工具
以人为本 服务社会8
品质管理实务:人员管理
• 人员技术水平 • 人员技能纯熟度 • 人员工作士气 • 人员工作方法
员工的效能=能力X意愿 以人为本 服务社会9
以人为本 服务社会36
举例
型号 项目
钻孔 回刀
ABCD 4486 5148
先后排序 ① ④ ③ ②
4
10
9
18
24
18
22
25
以人为本 服务社会37
企业经营
交期 成本 品质
安全 库存 品质 效率 体系 体系 体系 体系 人 设备 原料 方法
以人为本 服务社会38
我们要:
以人为本 服务社会39
OJT管理:不教而杀谓之虐!
事先不予以教化,不告之行为的规则,待事 后犯了事先未告知的规则时,按事先未告
知的规则进行处罚,是虐政。
以人为本 服务社会15
品质不良的来源-----变异
变异来源之五 管理因素
• 紧急订单比较多 • 机种更换频繁 • 人员流动频繁 • 设计不妥当
以人为本 服务社会16
戴明PDCA循环 图解
或=待料停产总工时数÷当期生产总工时数
以人为本 服务社会29
100
90
C
70
B
A类存货:项目占约占10% 价值约占70%
B类存货:项目约占25% 价值约占20%
50
C类存货:项目约占65% 价值约占10%
20
10 A
25
65
项目百分比
10
精益生产课程讲义

LEAN MANUFACTURING
制造系统的演化
• 手工生产:低产量,个性化,质量波动。 • 大规模生产:大批量少品种,工序式生产,设
备大、难组合。 • 同步生产:消除浪费,不断改进,员工参与。 • 精益生产组织:在同步生产基础上强调缩短周
期,提高资源利用率,需求驱动。 • 敏捷生产组织:改善整个价值链,节点上边着
谢谢大家!
•
弄虚作假要不得,踏实肯干第一名。0 2:35:17 02:35:1 702:35 12/9/20 20 2:35:17 AM
•
安全象只弓,不拉它就松,要想保安 全,常 把弓弦 绷。20. 12.902:35:1702 :35Dec -209-D ec-20
•
重于泰山,轻于鸿毛。02:35:1702:35:1 702:35 Wedne sday , December 09, 2020
质量、成本和交付期
• 不同系统中的成本
成本 大规模生产 成本 精益生产
•
销售价格
销售价格
•
产量
产量
质量、成本和交付期
❖消除浪费,降低成本 浪费的种类 • 返工、过量生产、搬运、多余动作、
等待、库存、过程不当
质量、成本和交付期
❖缩短交付周期 • 交付周期和制造周期 • 制造中的时间 • 成批和流动 • 缩短周期:关注流程
精益链
• 精益生产发展的方向和目标是精益链, 即在整个供应链上链接着很多精益工厂, 使整个供应链的成本降低、反应速度加 快,以满足消费者不断发展的需求及市 场竞争。
精益工厂模拟
直接人工 固定费用 材料 库存 总费用 产量 均摊费用 交付周期 利润
1
2
3
4
讲义二精益生产第一讲、第二讲

(一)什么是精益生产?
精益生产的基本概念
精益生产是为了适应市场多元化的需要,在多品种小批量的市场需 求制约下诞生的一种全新生产方式;
“只是在需要的时候,按需要的量,生产所需的产品”,它强 调按销售定单进行生产、按市场需求进行生产,也就是适时、 适量生产,这种生产方式的核心是追求一种无库存的生产系统 或使库存达到最小的生产系统,从而以此消除企业生产各个方 面的浪费。
2)福特解决了互换性, 1914发明了流水线;
3)大量生产、销售标准化产品;
4)1920~1979年代:大量生产(Ford)
特点:批量大,成本低,价格便宜,工人都
能买得起汽车(最低290$)
顾客要求:便宜就行,只要有“黑色的T型车”就满足了
大批量生产
(一)什么是精益生产?
3、精益生产方式——现代
背景: 1)丰田汽车的大野耐一有“及时”的生产概念 2)丰田对JIT的尝试,市场需求的多样性 3) 1970年代:精益生产为丰田度过能源危机
1、 手工生产方式——工业革命—二十世纪初
背景:工业处于初级阶段,靠工人的高超手艺制造产品 特点:效率低下,成本高,价格昂贵 顾客要求:很多产品只是富人的奢侈品,
普通百姓没有选择,如汽车。
2、大批量生产方式——二十世纪初—七十年代
手工生产
背景:
1)泰勒在工业工程的发展,时间与动作研究,作业进行标准化;
特点:生产系统灵活、按需生产,低成本、高质量、交货
大野耐一
顾客要求:既便宜、质量要好、同时要符合自己的偏好(多样性)
所以,精益是在顺应顾客的需求下产生的
(一)什么是精益生产?
精益生产课程培训讲义
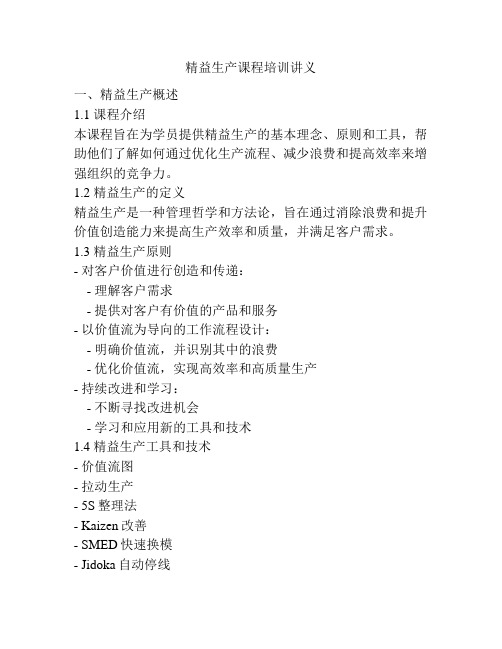
精益生产课程培训讲义一、精益生产概述1.1 课程介绍本课程旨在为学员提供精益生产的基本理念、原则和工具,帮助他们了解如何通过优化生产流程、减少浪费和提高效率来增强组织的竞争力。
1.2 精益生产的定义精益生产是一种管理哲学和方法论,旨在通过消除浪费和提升价值创造能力来提高生产效率和质量,并满足客户需求。
1.3 精益生产原则- 对客户价值进行创造和传递:- 理解客户需求- 提供对客户有价值的产品和服务- 以价值流为导向的工作流程设计:- 明确价值流,并识别其中的浪费- 优化价值流,实现高效率和高质量生产- 持续改进和学习:- 不断寻找改进机会- 学习和应用新的工具和技术1.4 精益生产工具和技术- 价值流图- 拉动生产- 5S整理法- Kaizen改善- SMED快速换模- Jidoka自动停线- 库房管理- TPM全员维护二、精益生产工具的使用2.1 价值流图- 价值流图的定义和作用- 如何绘制价值流图- 分析价值流图,识别浪费,制定改进计划2.2 拉动生产- 拉动生产的原理和好处- 瓶颈理论和平衡生产- 如何实施拉动生产2.3 5S整理法- 5S整理法的目的和原理- 5S五个步骤的具体操作- 维持5S的方法和建议2.4 Kaizen改善- Kaizen改善的概念和原则- PDCA循环的具体步骤- 如何开展改善活动2.5 SMED快速换模- SMED快速换模的意义和原理- SMED步骤的具体操作- 实现快速换模的关键要点2.6 Jidoka自动停线- Jidoka自动停线的目的和原理- 如何实施Jidoka- Jidoka在质量管理中的应用2.7 库房管理- 库房管理的重要性和挑战- 5S在库房管理中的应用- JIT库存管理的原理和实践2.8 TPM全员维护- TPM全员维护的意义和目标- TPM的五大支柱- 如何推动和实施TPM三、精益生产的案例分析3.1 汽车制造业中的精益生产- 丰田生产方式的介绍- 丰田生产系统的成功经验3.2 制造业以外的精益生产应用- 精益服务的原则和案例- 精益医疗的理念和实践- 精益建筑的方法和效果四、精益生产的挑战和解决方案4.1 精益生产的挑战- 文化转变和员工参与- 可持续改进的问题- 管理者的角色和责任4.2 精益生产的解决方案- 培训和教育的重要性- 建立改进文化和激励机制- 在全员参与和持续改进上下功夫五、结语精益生产是一种持续追求卓越的经营理念,其原则和工具可以应用于各个行业和领域。