硅锰冶炼中影响电耗的原因及如何合理降低吨产品电耗措施
冶炼企业的节电降损措施及实施

、 、
线员工
,
防止 了 大 马 拉小 车 等现 象 的发 生
“ ”
.
。
的收入 与产 品 的产量 质量 电耗 直 接 挂 钩 促 使 生
调 控 用 电负荷 降低 电能 损 耗
产
一
线 员 工 在 工 作 中 提 高 节 电 工 作 积 极 性 和 自觉
收 稿 日 期 :2 0 0 8 0 7 0 2
— —
文 章 编 号 :1 0 0 9
—
1 8 3 1 ( 2 0 0 8 )0 5
—
005 8
—
02
隅 炼 芷 业的 节 电 隆 损措 旋 及实 旋
卢绍成
(1 广 西 河 池 供 电局 广 西 河 池
.
,
梁
哲
。
,
2 547000 ;
.
广 西 河 池 市 南方 冶 炼 有限 公 司 广 西 河 池
,
547000
一
、
节 电技
用 电负荷 7 M W 平 均 负荷 6 M W 主 要 产 品 电解 铅
金 属锑
.
能 促 进 安 全 生 产 节 能工 作进
2 -2
步开 展
。
采 用 先进 的生产
工
艺流程
,
年 产 电解 铅 约 8 万
t
,
t
.
2 号金属锑约 1 万
19 9 5
,
t
,
白银 约 2 0 0
,
硫酸约 4 万
一
1
企业概况
某 冶炼 有 限 责任公 司 是 其 所 在 市 范 围 内有 色 金
性 千 方 百 计 地 在 保证 安 全 生 产 提高产 品产量 和保
矿热炉冶炼硅铁的节能思路

矿热炉冶炼的节能思路“原料是基础,设备是条件,操作是关键,治理是保障”。
原料是基础:硅石;一个企业,要节约本钱,必需从入厂原料抓起。
如FeSi 冶炼生产需要的SiO2含Si量是不是大于或等于98%,若是小于98%,那么冶炼生产中的电耗就会依照每低于一个百分点增加135Kwh/T,sio2的密度和抗暴性、抗压强度(1000-1400Kg力/厘米2)。
一样简易的判定方式是手拿一块sio2石料,在水泥地上大约在1米以上高让其自由下落,以不碎裂为合格。
不是所有的sio2都能用来生产FeSi,因为他们的类型是不同的,乃至成份相同时,它们在加热进程和高温还原进程中的表现也不相同,这是因为sio2形成进程的不同,故其特性、杂质含量、结构、晶体等也不相同,从而表现也不一样。
一样AI2O3含量高于0.4%,Fe2O3>%,MgO>%的硅石属杂质较多的原料,在1575°C时,它的还原速度比低杂质的快,在1715°C时那么相反:在1757°C时,其结构急剧破坏,有效表面积迅速增加,从而有利于还原反映的进行,故还原速度专门大.当硅石变成液态以后,其挥发度和还原度都迅速增加,在这种情形下,硅石的成份起了重要作用,硅石含有大量的成渣杂质,炉渣形成后,还原速度下降.工业性实验说明,含有以上杂质超标的硅石冶炼时技术指标不行.硅石的粒度对还原速度有专门大阻碍.正常硅石的还原速度随粒度的增大而急速下降,而含杂质较大的硅石大体不变.这是由硅石的矿物组成和微观结构决定的,在确信炉料硅石的粒度时应当考虑这些问题.确信炉料中硅石的粒度时,必需考虑硅石的结构.国外某公司用不同粒度(50,50-100和100mm)的硅石冶炼75%硅铁时,其电耗别离为8550、8380和8960Kwh,这说明选择适合的硅石粒度是很重要的。
不是所有的硅石都能用来生产硅铁,因为它们的类型是不同的。
乃至成份相同时,它们在加热进程中和高温还原进程中的表现也不相同。
冶炼中的能耗管理与节约措施

加强技术创新和研发,推 广节能减排新技术
建议一
建议二
建议三
THANKS
感谢观看
严格控制工艺参数
在冶炼过程中,严格控制各项工艺参数,确保工艺稳定,减少能 源浪费。
减少不必要的操作
优化生产流程,减少不必要的操作和环节,降低能源消耗。
能源分质利用
根据能源品质的不同,合理分配使用,避免低品质能源的浪费。
新能源与技术的应用
开发利用新能源
积极开发利用太阳能、风能等新能源,替代传统化石能源,降低碳 排放。
能源回收与再利用
1 2 3
余热回收
利用冶炼过程中产生的余热进行回收和再利用, 如发电、供热等,提高能源利用效率。
废气处理与利用
对冶炼过程中产生的废气进行净化处理,提取有 价值的成分进行再利用,如回收有价金属、制备 化工原料等。
废水处理与回用
对冶炼过程中产生的废水进行处理,使其达到回 用标准,用于冷却、洗涤等环节,减少新水的消 耗和废水的排放。
政策鼓励使用清洁能源,促进冶炼 行业向低碳、环保方向转型。
技术创新推动
鼓励冶炼企业进行技术创新,研发 更高效、环保的冶炼技术和设备。
03
CATALOGUE
冶炼中的能耗管理措施
优化工艺流程
减少不必要的工艺步骤
01
通过技术改进和流程优化,消除或减少不必要的工艺步骤,降
低能源消耗。
优化温度控制
02
精确控制冶炼过程中的温度,避免过高的温度和长时间的加热
增加能源供应稳定
性
合理的能耗管理可以优化能源结 构,提高能源供应的稳定性,降 低能源短缺的风险。
提高企业竞争力
实施有效的能耗管理和节约措施 可以使企业在市场上更具竞争力 ,赢得更多商机。
金属冶炼中的能源利用与节能措施

随着环保要求的提高,部分金 属冶炼企业开始尝试使用清洁 能源,如电力、天然气等。
不同金属冶炼工艺所需的能源 类型和消耗量存在差异,如钢 铁冶炼以煤炭为主,铝冶炼则 大量使用电能。
能源利用效率分析
当前金属冶炼的能源利用效率普遍偏 低,大部分企业的能源利用效率低于 国际先进水平。
提高能源利用效率有助于降低生产成 本、减少环境污染和应对能源危机。
THANKS
感谢观看
节能技术介绍
01
02
03
04
回收余热
利用金属冶炼过程中产生的效燃烧技术
采用高效燃烧器、空气预热等 技术,降低燃料消耗,提高燃
烧效率。
回收烟气余热
利用金属冶炼过程中产生的烟 气余热进行热回收,用于预热
助燃空气或生产热水等。
能源管理技术
采用先进的能源管理系统,对 金属冶炼过程中的能源利用进
05
案例分析:某钢铁企业的能源利 用与节能实践
企业概况与能源利用现状
企业规模
某钢铁企业是国内大型钢铁企业 之一,拥有完善的生产线和庞大
的员工队伍。
能源消耗
该企业在金属冶炼过程中需要大量 能源,主要包括煤炭、焦炭、电力 等。
排放与污染
传统冶炼工艺会产生大量废气、废 水和固体废弃物,对环境造成一定 影响。
设备老旧、技术落后和管理不善是导 致能源利用效率低下的主要原因。
能源利用中的问题与挑战
金属冶炼过程中产生大量的废气 、废水和固体废弃物,对环境造
成严重污染。
传统能源资源的日益枯竭和价格 上涨给金属冶炼行业带来巨大压
力。
应对气候变化和环保政策的压力 促使金属冶炼行业加快转型和升
级。
02
节能措施在金属冶炼中的应用
金属冶炼的能源节约措施
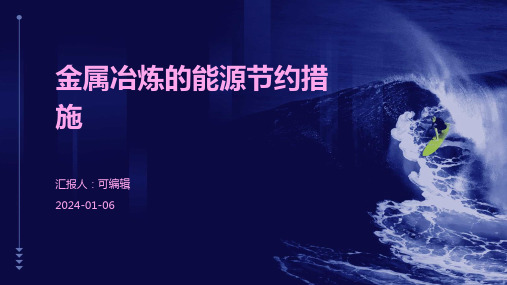
研发和应用环保技术,减少冶炼过 程中的污染物排放,实现绿色生产 。
04
政策支持与监管
政府出台相关政策支持能源节约措施
政府可以出台一系列政策,鼓励金属 冶炼企业采取能源节约措施,例如提 供财政补贴、税收减免等优惠政策, 激发企业节能降耗的积极性。
政府还可以设立专项资金,支持企业 开展节能技术研发和设备过程中需要大量 的冷却水,对当地水资源 造成压力。
02
能源节约的重要性
降低生产成本
减少能源消耗
通过改进工艺和设备,降低金属冶炼 过程中的能源消耗,从而降低生产成 本。
提高能源利用效率
采用先进的能源管理技术和系统,优 化能源利用,提高能源利用效率,降 低生产成本。
减少环境污染
减少排放
利用太阳能为冶炼设备提供辅助能源 ,减少对传统能源的依赖。
利用生物质能为冶炼设备提供热源或 进行生物质发电。
风能利用
将风能转化为机械能或电能,为冶炼 设备提供动力。
加强技术创新与研发
新技术研发
投入研发力量,开发新的冶炼技 术和工艺,提高能源利用效率。
智能化技术应用
引入智能化技术,实现设备的远程 监控和自动化控制,降低能耗。
开展环境影响评价
企业应对新建、改建或扩建项目进行环境影响评价,评估项目对环 境的影响,并提出相应的环保措施。
加强环保宣传与教育
1 2 3
提高员工环保意识
企业应定期开展环保宣传和教育活动,提高员工 对环保的认识和意识,培养员工的环保行为习惯 。
开展环保培训
企业应对新员工进行环保培训,使他们了解企业 的环保要求和规章制度,同时对在职员工进行定 期的环保培训。
金属冶炼的能源节约措 施
金属冶炼中的能耗优化与节能减排措施
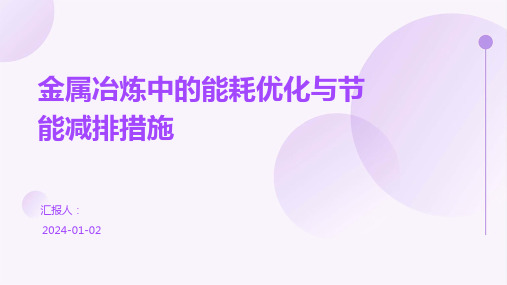
土壤污染
金属冶炼过程中产生的废 渣、废液等固体废弃物处 理不当,对土壤造成严重 污染。
02
能耗优化技术
高效冶炼技术
总结词
高效冶炼技术是金属冶炼中的重要能耗优化技术,通过提高冶炼效率,降低能 耗和减少污染物排放。
详细描述
高效冶炼技术包括采用先进的冶炼设备和工艺,如熔融还原、直接炼钢、连铸 连轧等,提高金属的回收率和冶炼效率,从而降低单位产品的能耗和污染物排 放。
放。
国际经验借鉴
日本钢铁企业
日本钢铁企业在节能减排方面具有先进经验,通过采用先进的生产技术和设备,提高能源利用效率, 减少污染物排放。同时,加强生产过程中的能源管理和环保监管,确保节能减排措施的有效实施。
欧洲钢铁企业
欧洲钢铁企业注重环保和可持续发展,在金属冶炼过程中采取了一系列节能减排措施,如使用低碳能 源、开发新型冶炼技术等。这些措施不仅有助于企业降低能耗和排放,还有助于提高企业的市场竞争 力。
04
案例分析与实践
先进企业实践
宝钢集团
宝钢集团在金属冶炼过程中采用了先进的节能技术,如余热回收、高效连铸和连轧等, 有效降低了能耗和排放。同时,通过优化生产流程和工艺参数,进一步提高能源利用效
率和减排效果。
鞍钢集团
鞍钢集团注重技术创新,在金属冶炼过程中推广应用了新型耐火材料、节能型熔炼炉和 烟气除尘技术等。这些技术的应用不仅提高了生产效率,还显著降低了能耗和污染物排
加强与其他行业的合 作,共同推进绿色制 造技术的发展和应用 。
探索更环保的冶炼工 艺,减少污染物排放 ,降低对环境的影响 。
对企业的建议
企业应积极采用先进的节能技术和设 备,提高能源利用效率,降低生产成 本。
与科研机构和高校合作,共同开展节 能减排技术研究和应用,提升企业竞 争力。
金属冶炼中的能源利用与节约措施

节约能源对环境保护的意义
减少温室气体排放:节约能源可以减少化石燃料的使用,从而减少温室气体的排放,减缓全球变 暖的速度。
保护自然资源:节约能源可以减少对自然资源的消耗,保护地球上的森林、矿产等资源。
减少环境污染:节约能源可以减少废气、废水、废渣等污染物的排放,降低对环境的污染程度。
促进可持续发展:节约能源可以促进经济的可持续发展,提高能源利用效率,降低能源成本,提 高企业的竞争力。
发展绿色冶炼技术 :采用绿色冶炼技 术,减少环境污染 ,提高能源利用效 率
未来能源结构调整对金属冶炼的影响
清洁能源:使用太阳能、风能等可再生能源,减少对传统能源的依赖 节能技术:采用高效节能技术,降低能源消耗,提高能源利用效率 循环利用:实现能源的循环利用,减少能源浪费,降低环境污染 智能化:利用智能化技术,实现能源的精细化管理和优化配置,提高能源利用效率
智能化技术在能源管理中的应用与展望
智能化技术:大数据、云计算、人工智能等
应用领域:能源管理、设备监控、生产调度等
应用效果:提高能源利用效率、降低能耗、减少污染等 展望:智能化技术在金属冶炼中的广泛应用,实现能源利用的智能化、 精细化管理。
THANK YOU
汇报人:
法规监督:政府对节能减排进 行监督,确保法规执行
法规激励:政府对节能减排企 业给予奖励和补贴,鼓励企业 采取节能减排措施
企业节能减排的社会责任与担当
政策法规:政府出台相关政策法规,鼓励企业节能减排 社会责任:企业应承担社会责任,积极参与节能减排 技术研发:企业应加大技术研发投入,提高能源利用效率 环保意识:企业应提高员工环保意识,加强环保教育
采用先进的冶 炼工艺,如连 续铸造、连续 轧制等,提高 生产效率,降
锰硅合金生产节能措施

锰硅合金生产节能措施锰硅合金生产节能措施随着世界各国对能源消耗的关注,节能降耗已经成为锰硅合金行业的重要环节,也是企业生存的关键。
锰硅合金的生产有电炉法和高炉法两种,我国主要使用电炉法生产,降低电耗可以从以下方面入手。
1、提高炉料电阻节约电能的根本思想是提高电弧电阻炉的有功功率。
根据功率公式(P=I2R),提高R料,从而提高有功功率。
2、调整焦炭配入量和粒度级配焦炭层过厚,电极上抬,熔池温度低,熔体从炉内排出不畅;焦炭层过薄,电极插入过深,易翻渣,恶化炉况,影响电耗。
两种情况都会导致渣比增大,增加电耗。
因此控制合适的焦炭厚度至关重要,通过调整粒度可以达到这一目的。
3、降低渣比降低渣比可以减少热损失,提高锰回收率,有效地降低电耗。
主要措施有提高Mn、Si的还原率和适当提高炉温。
4、合理渣型炉渣成分决定着合适的冶炼温度、碱度、粘度、电性等因素,并影响元素在合金与炉渣中的分配。
锰硅合金生产的理想炉渣成分为:MnO8%~10%,CaO12%~15%,MgO4%~5%,SiO232%~36%,Al2O334%~43%。
5、提高入炉含锰物料品位对于锰硅合金冶炼,提高入炉锰品位,可以提高锰回收率,降低电耗。
锰矿品位低,则渣量大,还原剂、熔剂消耗增多,导致电量增加。
实验表明,入炉锰矿品位每降低1%,就将多消耗64kWh/t的电。
6、选取合理的冶炼周期矿热炉冶炼锰硅合金的周期,是由炉内熔池反应区容积大小和渣中元素Mn、Si的还原程度决定的,实际生产中常根据炉内不发生“翻渣”现象为界。
适当延长冶炼时间,从而达到锰硅合金矿热炉实施低渣比冶炼操作。
由于入炉有功功率的提高,保证了炉内焦炭层反应区的高温条件,使Mn、Si的还原率大幅度提高,节省了电能。
但冶炼时间不能过长,否则出铁温度过高将造成合金中锰的挥发损失,降低Mn的回收率。
此外,MnO含量已接近还原平衡的“乏渣”,留在炉内,会使冶炼电耗增加。
因而,根据具体的操作条件,通过实践决定合理的冶炼时间。
电炉降低冶炼电耗的研究与实践

电炉降低冶炼电耗的研究与实践电炉降低冶炼电耗的研究与实践炼钢车间⼀、前⾔机制公司炼钢车间现有正常运转的⼀座30t电炉和⼀座30t钢包精炼炉,属于短流程炼钢。
2009年冶炼平均电耗为450kwh/t,为此炼钢车间攻关⼩组展开技术攻关,摸索出⼀条降低冶炼电耗的途径。
2010年电耗稳步下降到421kwh/t,降幅达6.4%。
电弧炉炼钢是以宝贵的电能作为主要能源。
⽬前国外已采⽤的短流程具有很⼤潜⼒,吨钢电耗已可达180 kW h左右,甚⾄更低。
据资料表明,整个电炉炼钢过程能量平衡基本分布如下表:机制公司的炼钢电耗相⽐之下较⾼,很有必要⼤⼒推进技术进步,实现节能降耗,发挥短流程⼯艺的⽣命⼒。
⼆、冶炼电耗搞的原因1、原料对电耗的影响2009年由于废钢质量不稳定、轻薄料多、夹杂严重、⼏何尺⼨超长、单块超重造成装料不密实,每炉钢进料次数平均达2.5次,多的达4~5次。
根据监测,每多进⼀次料,需要延长冶炼时间25 min,增加电耗50 kWh / t。
由于个别废钢太长造成炉盖盖不严,⼤量热⽓、⽕焰冒出损失了热能,导电不良的渣钢及⼤块废钢装料位置不正确,冶炼时搭桥塌料⽽打断电极,增加了电极消耗和冶炼时间。
2、⼯艺执⾏不到位有的配电操作⼯没有按合理的供电曲线配电,炼⼀炉钢始终⽤⼀个电压档位以及⼤电流冶炼。
铁⽔供应不⾜导致炼钢⼯艺⽐较散乱,炼钢过程中等待时间(换炉盖、换炉体、等铁⽔)较长。
出钢温度普遍较⾼;有的超出出钢温度40多度,根据计算钢⽔温度每提⾼10 ℃,冶炼电耗上升4 kWh / t。
三、降低电耗的措施1、加强废料管理,优化配料⽅案废钢质量是影响电耗的客观因素,⽽原料管理是影响电耗的主观因素。
⾸先应对废钢进⾏处理,过长的废钢应割断,使其不超过0 .5 m,⼤块废钢不得超过500 kg。
对特殊轻薄料须进⾏打包处理,废钢原料应按⼤、中、⼩分别放开堆放。
装料要讲究科学合理,⼤、中、⼩料的合理配⽐为:⼩料15%~25% ,中料45% ~50% ,⼤料35%~45%。
金属冶炼中的能源利用和节约措施
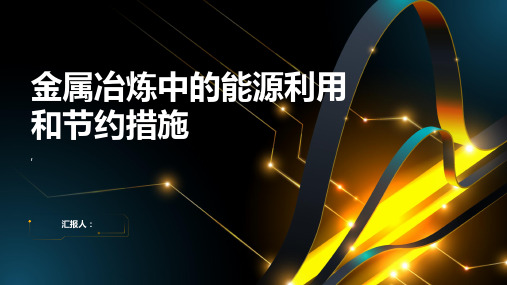
推广可再生能源:如太阳能、 风能等,减少对传统能源的依 赖
Part Four
金属冶炼中的新能 源利用
新能源在金属冶炼中的应用现状
太阳能:用于金属冶炼过程中的加热和冷却 风能:用于金属冶炼过程中的动力和通风 水能:用于金属冶炼过程中的冷却和清洗 生物质能:用于金属冶炼过程中的加热和动力 地热能:用于金属冶炼过程中的加热和冷却 核能:用于金属冶炼过程中的加热和动力
推广清洁能源:推广使用清洁能源, 减少对传统能源的依赖,降低环境 污染。
添加标题
添加标题
添加标题
添加标题
加强能源管理:建立健全能源管理 体系,加强能源管理,降低能源消 耗。
加强技术创新:加强技术创新,研 发新的冶炼技术和设备,提高能源 利用效率。
Part Six
政策与法规对能源 利用的影响
国内外相关政策与法规的制定和实施情况
Part Five
企业实践案例分析
成功实现能源节约的金属冶炼企业案例
节能措施:采用高效节能设 备,优化生产工艺,提高能 源利用效率
效果:每年节约能源成本数 百万元,减少碳排放量
案例企业:某大型钢铁企业
启示:企业应重视能源节约, 采用先进技术和管理手段, 实现可持续发展
能源利用和节约的实践经验总结
金属冶炼中的能源利用 和节约措施
,
汇报人:
目录
01 添 加 目 录 项 标 题 03 节 约 能 源 的 必 要 性 及 措 施 05 企 业 实 践 案 例 分 析 07 未 来 展 望 与 研 究 方 向
02 金 属 冶 炼 中 的 能 源 利 用 现 状
04 金 属 冶 炼 中 的 新 能 源 利 用 06 政 策 与 法 规 对 能 源 利 用 的
关于工业硅冶炼高产,低耗,高质个人总结

关于工业硅冶炼高产,低耗,高质个人总结关于工业硅冶炼高产,低耗,高质个人总结关于工业硅冶炼高产、低耗、高质个人总结要达到大煤大焦工业硅冶炼高产、低耗、高质的冶炼效果,个人认为是受多方面因素影响的,如设备自身参数及生产工艺操作对高产、低耗有着决定性的作用,原材料性质(主要化学成分)对工业硅高质起着源头控制作用。
现我从从设备自身参数和冶炼操作工艺两个大的方面做一个分析总结。
一、设备自身参数炉台设备自身参数会影响炉台生产消耗,搭配合理的设备参数有利于生产发挥到极致。
工业硅冶炼是高能耗冶炼作业,主要的能量来源是电能。
通过变压器输出电能,经过短网,导电夹,三相电极对炉底炉料引弧放电,再利用高温电弧提供热量还原SiO2,完成工业硅冶炼。
1、变压器变压器自身的额定功率,直接制约着炉台生产负荷的配送,如我公司变压器额定功率9000KVA工业硅炉,正常操作的每小时可配送9000Kwh,但是从以往生产数据来看,我公司炉台炉膛和电极参数设定是按超额定负荷设定的,为此要从生产体现出变压器的性能,必须摸索一个合理的配电制度,保证变压器工作达到最佳状态,从而提高产量,降低消耗。
第-1-页共6页2、短网物理尺寸短网是传输电能主要的设备,短网铜管的质量优劣直接影响电能传输质量,如我公司短网横截面直径在60mm,那么按9000KVA负荷,则通过的电流密度是非常大的,若短网质量差,短网上电能线损将会更多,所以如何保证短网的物理直径和质量对增产降耗有着很实际的现实意义,只有合理的短网参数才能够有效的降低炉台生产消耗,提高生产产量。
3、炉膛参数及极心圆炉膛参数包括炉膛直径和炉膛深度,由于炉台生产时间长,设备均出现移位现象,导致原来设定参数变化等,比如我公司3#炉年度一周期极心圆过大,导致中心三角区不化料,特别生产时间的延续,坩埚逐渐缩小,直致三角区形成死料,阻碍三相电极坩埚连通。
所以新开炉应复核炉膛参数,主要是极心圆大小,确保开炉后炉台正常运行,提高产量,降低消耗。
硅锰冶炼中影响电耗的原因及如何合理降低吨产品电耗措施

硅锰冶炼中影响电耗的原因及如何合理降低吨产品电耗措施2020.1.9一、影响产品冶炼电耗的主要因素1、原料对吨产品冶炼电耗的影响冶炼锰硅合金的主要原料有锰系原料、焦炭等。
焦炭由于成分不稳定等因素,往往导致冶炼炉况波动,使吨产品冶炼电耗高低不一;锰系原料由于进口锰矿价格居高不下以及国内贫矿杂质含量高等因素的制约.导致原料入炉锰频繁上下调整,同时冶炼生产中必将有部分热量和焦炭来还原多余的杂质,使吨产品冶炼电耗难以保持稳定。
表1 原料入炉锰与吨产品冶炼电耗对比表由表1 可以看出。
锰硅合金吨产品冶炼电耗明显受原料入炉锰品位的影响,实际每升高或降低l%,相应冶炼电耗也降低或升高63kwh/t 。
2、生产工艺及操作管理对吨产品冶炼电耗的影响由于操作人员对实际生产工艺要求的认识及操作水平高低不一,炉况频繁受偏加料、供电功率波动、三相电极做功不均衡、超负荷运行等因素的影响.使吨产品冶炼电耗升高。
3、设备装备及运行状况对吨产品冶炼电耗的影响目前.行业内大部分在线矿热炉普遍设备装备差、劳动强度高、机械化程度低。
由于设备逐步老化、原有设计存在一定缺陷,加之电网供电质量不稳定,致使矿热炉有效作业率不足,热停次数和时间增加,直接造成锰硅合金吨产品冶炼电耗升高。
二、降低吨产品冶炼电耗的主要措施1、科学合理供电(1)提高输入炉内的电压有效功率锰硅合金冶炼中用于维持熔池反应区的的高温和热量主要由消耗电能满足。
因为电功率值与电压、电流和功率因数成正比,理论上要求电压波动不超过±5%,主要是一次电压必须稳定,并保持在上限范围内,这样最大限度提高输入炉内的电压有效功率,冶炼才具备取得好的技术经济指标的基础。
(2)适当选用二次电压在炉容和冶炼产品规格相同的情况下,应根据“ 电炉总效率=电效率×热效率”的原则取得最佳效益,即:提高炉温,使Si 利用率提高、渣中跑Mn下降、吨产品冶炼电耗降低。
在保证电极下插适当深度、炉口热损失较小的情况下适当地选用较高一级的二次电压,当输入功率稳定时,二次电流相对较小,这样有利于提高功率因数和电效率;但当二次电压过高、电弧过长,必然需要上抬电极,热损失增加。
降低电耗的几点途径
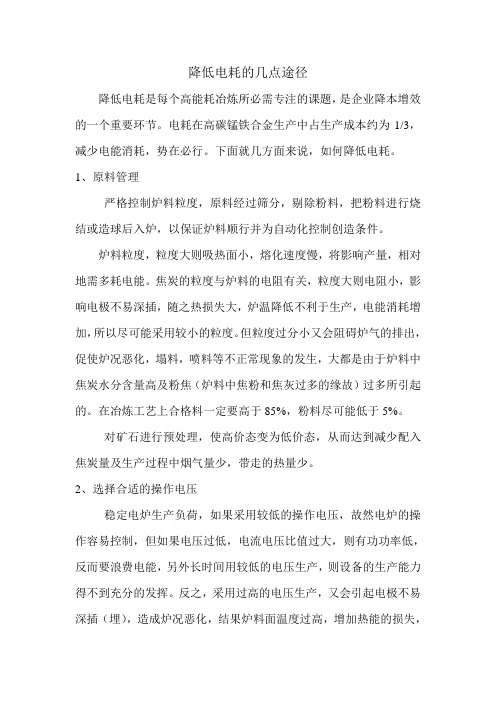
降低电耗的几点途径降低电耗是每个高能耗冶炼所必需专注的课题,是企业降本增效的一个重要环节。
电耗在高碳锰铁合金生产中占生产成本约为1/3,减少电能消耗,势在必行。
下面就几方面来说,如何降低电耗。
1、原料管理严格控制炉料粒度,原料经过筛分,剔除粉料,把粉料进行烧结或造球后入炉,以保证炉料顺行并为自动化控制创造条件。
炉料粒度,粒度大则吸热面小,熔化速度慢,将影响产量,相对地需多耗电能。
焦炭的粒度与炉料的电阻有关,粒度大则电阻小,影响电极不易深插,随之热损失大,炉温降低不利于生产,电能消耗增加,所以尽可能采用较小的粒度。
但粒度过分小又会阻碍炉气的排出,促使炉况恶化,塌料,喷料等不正常现象的发生,大都是由于炉料中焦炭水分含量高及粉焦(炉料中焦粉和焦灰过多的缘故)过多所引起的。
在冶炼工艺上合格料一定要高于85%,粉料尽可能低于5%。
对矿石进行预处理,使高价态变为低价态,从而达到减少配入焦炭量及生产过程中烟气量少,带走的热量少。
2、选择合适的操作电压稳定电炉生产负荷,如果采用较低的操作电压,故然电炉的操作容易控制,但如果电压过低,电流电压比值过大,则有功功率低,反而要浪费电能,另外长时间用较低的电压生产,则设备的生产能力得不到充分的发挥。
反之,采用过高的电压生产,又会引起电极不易深插(埋),造成炉况恶化,结果炉料面温度过高,增加热能的损失,电耗增高。
在冶炼工艺上必须选择一个最佳的电气参数。
选择适当的操作电压,维持较高的生产负荷是节能的重要因素之一。
现采取低压高负荷操作,选用三档,140A的一次侧电流。
4#炉2011年1月25日统计有功功率电量及无功功率电量如下:从表中可以看出二次侧功率因数偏低。
3、提高电炉的动转率提高电炉的动转率,减少小停电次数,长时间停炉。
长时间停炉致使炉温大幅度下降,在次启动电炉时,势必又要消耗更多的电能来恢复炉温,每停一次电总要浪费一些电能。
建议恢复电极自动压放装置,减少电炉热停炉次数,也可延长操作机械的使用年限。
锰硅合金生产节能措施
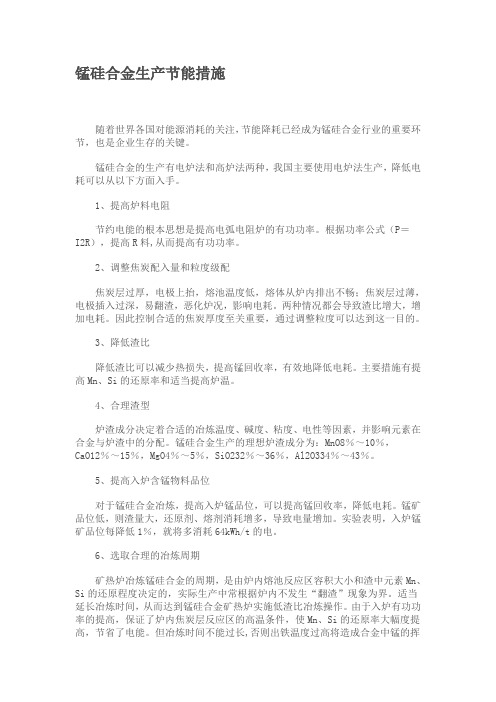
锰硅合金生产节能措施随着世界各国对能源消耗的关注,节能降耗已经成为锰硅合金行业的重要环节,也是企业生存的关键。
锰硅合金的生产有电炉法和高炉法两种,我国主要使用电炉法生产,降低电耗可以从以下方面入手。
1、提高炉料电阻节约电能的根本思想是提高电弧电阻炉的有功功率。
根据功率公式(P=I2R),提高R料,从而提高有功功率。
2、调整焦炭配入量和粒度级配焦炭层过厚,电极上抬,熔池温度低,熔体从炉内排出不畅;焦炭层过薄,电极插入过深,易翻渣,恶化炉况,影响电耗。
两种情况都会导致渣比增大,增加电耗。
因此控制合适的焦炭厚度至关重要,通过调整粒度可以达到这一目的。
3、降低渣比降低渣比可以减少热损失,提高锰回收率,有效地降低电耗。
主要措施有提高Mn、Si的还原率和适当提高炉温。
4、合理渣型炉渣成分决定着合适的冶炼温度、碱度、粘度、电性等因素,并影响元素在合金与炉渣中的分配。
锰硅合金生产的理想炉渣成分为:MnO8%~10%,CaO12%~15%,MgO4%~5%,SiO232%~36%,Al2O334%~43%。
5、提高入炉含锰物料品位对于锰硅合金冶炼,提高入炉锰品位,可以提高锰回收率,降低电耗。
锰矿品位低,则渣量大,还原剂、熔剂消耗增多,导致电量增加。
实验表明,入炉锰矿品位每降低1%,就将多消耗64kWh/t的电。
6、选取合理的冶炼周期矿热炉冶炼锰硅合金的周期,是由炉内熔池反应区容积大小和渣中元素Mn、Si的还原程度决定的,实际生产中常根据炉内不发生“翻渣”现象为界。
适当延长冶炼时间,从而达到锰硅合金矿热炉实施低渣比冶炼操作。
由于入炉有功功率的提高,保证了炉内焦炭层反应区的高温条件,使Mn、Si的还原率大幅度提高,节省了电能。
但冶炼时间不能过长,否则出铁温度过高将造成合金中锰的挥发损失,降低Mn的回收率。
此外,MnO含量已接近还原平衡的“乏渣”,留在炉内,会使冶炼电耗增加。
因而,根据具体的操作条件,通过实践决定合理的冶炼时间。
冶炼电耗超标整改措施(一)

冶炼电耗超标整改措施(一)冶炼电耗超标整改措施背景介绍冶炼过程中,电耗超标是常见的问题之一,不仅造成能源浪费,也增加了生产成本。
为解决这一问题,下面列举了一些有效的整改措施,以降低冶炼电耗,提高能源利用效率。
措施一:设备优化•升级电炉:采用能耗更低、效率更高的电炉设备,提高冶炼效率,降低电耗。
•定期维护:对设备进行定期检修和保养,确保设备工作正常、高效。
措施二:工艺调整•调整炉温:根据实际情况,优化炉温设定,避免过高或过低的炉温对电耗的影响。
•优化炉料配比:合理选择炉料比例,确保炉料燃烧效率,减少能源浪费。
措施三:能量回收利用•废热回收利用:利用余热发电或供暖,将废热转化为可再生能源,提高能源利用效率。
•废气处理:采用先进的废气处理装置,将排放的废气进行处理,减少环境污染。
措施四:管理优化•提高员工意识:加强员工培训,提高他们对节能环保的重要性的认识,培养他们的节能意识。
•监测与分析:建立电耗监测系统,对电耗进行实时监测和分析,及时发现问题,采取措施予以解决。
结论通过设备优化、工艺调整、能量回收利用和管理优化等一系列措施的实施,可以有效降低冶炼电耗,提高能源利用效率。
这不仅有助于减少资源浪费,改善环境质量,还可以为企业节约成本,提高经济效益。
我们应该不断探索创新,共同推动冶炼行业的可持续发展。
行动计划为了全面落实上述整改措施,以下是一份简要的行动计划,以指导冶炼企业在冶炼电耗超标整改方面的工作:1.确定目标:设定减少电耗的具体目标,例如降低10%的电耗。
2.组建专业团队:成立由技术人员、工程师和管理人员组成的团队,负责整改工作的规划和实施。
3.设备优化:评估现有设备的性能和效率,鉴定需要升级或更换的设备,并制定改造计划。
4.工艺调整:分析现有工艺过程,发现潜在的优化点,并根据实际情况进行合理调整。
5.能量回收利用:调查现有废热和废气的排放情况,寻找回收利用的机会,并进行投资估算。
6.管理优化:加强员工培训,提高节能意识,建立电耗监测系统,进行定期的数据分析和评估。
硅锰合金电耗

硅锰合金电耗嘿,咱今儿就来好好聊聊硅锰合金电耗这档子事儿!你说这硅锰合金电耗,就像咱过日子得算计柴米油盐一样重要。
电耗要是高了,那成本不就蹭蹭往上涨啦,就好像你本来打算买个自行车,结果这花费都够买小汽车啦!咱先得明白,硅锰合金生产就跟盖房子似的,每个环节都得精心对待。
从原料的选择开始,那可不能马虎,就跟你挑菜一样,得挑新鲜水灵的呀。
要是原料不好,那后面电耗能不高嘛!然后呢,这工艺就像是做菜的火候,得掌握好咯。
温度高了低了都不行,得恰到好处。
你想想,火大了菜糊了,火小了半天不熟,这不就浪费能源嘛!就好比那电,用多了心疼,用少了又怕质量不行。
还有啊,设备也很关键呀!这就好比战士手里的武器,你拿着把钝刀能打胜仗吗?好的设备就像是一把锋利的宝剑,能让咱在硅锰合金生产的战场上披荆斩棘,还能省不少电呢!咱再说说操作工人,他们就像是厨师,手艺好才能做出美味佳肴。
操作熟练的工人,那就能把电耗控制得稳稳的,就像老司机开车,又稳又省油。
要是碰到个新手,那可就没准咯,说不定电就哗哗地流走啦!咱平时也得注意保养维护这些设备呀,就跟咱爱护自己身体一样。
你不保养,身体能好吗?设备不维护,能高效工作吗?那电耗能不上去吗?咱举个例子哈,有个工厂,之前那电耗高得吓人,老板愁得头发都白了几根。
后来呢,他们仔细研究了各个环节,换了好原料,改进了工艺,给设备做了个大保健,还培训了工人。
嘿,你猜怎么着,电耗一下子就降下来了,那成本也跟着下来了,老板笑得嘴都合不拢啦!所以说呀,这硅锰合金电耗可不是小事,咱得重视起来。
从每个细节入手,就像蚂蚁搬家一样,一点一点把电耗降下来。
咱不能只盯着眼前的利益,得长远考虑呀。
你说是不是这个理儿?总之呢,要想把硅锰合金电耗控制好,就得像个勤劳的小蜜蜂,精心照料每一个环节。
只有这样,咱才能在这个行业里站稳脚跟,才能让咱的工厂像棵大树一样茁壮成长!可别小瞧了这电耗,它可关系着咱的钱包和未来呢!。
基于节能条件的硅锰合金生产技术分析

基于节能条件的硅锰合金生产技术分析摘要:硅锰合金生产中普通存在渣铁分离不好、翻渣、电流送不上、产量低、电耗高等问题,在很大程度上导致了能耗较高、污染难以控制。
论文分析了传统的硅锰生产污染控制方式及不足,分析了硅锰合金生产节能技术及应用,旨在为硅锰合金生产企业提供一些参考和简介,实现节能环保。
关键词:硅锰合金;生产;节能技术锰硅合金是炼钢常用的复合脱氧剂,也是低碳锰铁和电硅热法生产金属锰的还原剂。
随着我国钢铁工业的快速发展和需求的扩大,铁合金工业得到了长足的发展与进步。
2018年,我国的硅锰产量达到了 945万吨,占铁合金产量的比重达到30.3%,相比2017年增长了1.43倍。
硅锰产能逐渐向宁夏、广西、内蒙古、贵州等地转移,是增产的主要省份,在建产能也主要集中在云南、内蒙古、宁夏、贵州、重庆等地。
宁夏晟晏、乌兰察布旭峰新创和惠义铁合金等公司,是硅锰企业产量排名靠前的企业。
在倡导环保节能的背景下,硅锰合金在生产过程需要合理运用各种控制措施,才能实现节能降耗目标。
因为硅锰合金企业在生产过程中,会向外部排放大量的烟尘、粉尘、二氧化硫等有害气体,对大气造成污染;产生挥发酚、氰化物、氨氮等对水体污染的物质,以及尘泥、废渣等固体污染物。
硅锰铁合金生产给环境带来的污染,要求企业要重视节能生产、清洁生产,更好地保护环境。
一、传统的硅锰生产污染控制方式及不足传统的硅锰生产污染控制,理念上采取末端控制的思路,即在污染产生之后,针对大气污染、水污染或固体污染采取针对性的措施。
这种控制理念,在硅锰合金生产早期的污染控制中,发挥了重要的作用,然而伴随硅锰合金企业生产效率的提升、工业化进程的加快,这种理念的不足越来越多,例如投资成本越来越大、经济效益越来越低、污染控制效果越来越差等。
从工艺方面来看,传统的硅锰生产污染控制主要通过计算机和留渣法进行控制,例如空心电极设备的运用,改进了矿热炉自身的用电,起到了节能降耗效果;此外还有一些直流矿热炉、低压补偿、低频供电等技术也运用到了硅锰合金生产中,对保护环境、控制污染起到了较好作用。
冶炼电流、电压的调节对高效冶炼硅锰的影响

冶炼电流、电压的调节对高效冶炼硅锰的影响摘要本文论述了调节电流、电压对提高电炉产量、节能的可行性和必要性,介绍了硅锰冶炼中电流电压的调整原理及计算确定方法,关键词电流;最佳控制;电压;调节;硅锰;熔炼1.硅锰合金组成结构和冶炼方式简介硅锰合金的冶炼有别于一般高炉和中频炉等的冶炼,高炉是热风炉,通过热风热对矿石进行熔炼高温还原。
中频炉通过电磁加热进行冶炼。
而铁合金硅锰合金的冶炼是通过,三个导电电极【内充满烧成结晶状态的自培电极糊(由固体碳素材料和粘结剂组成)】深插于由锰矿石、焦炭、硅石、莹石等原料中加热。
通过电炉特种变压器—短网—电极通电产生电弧,电流热进行熔炼,矿石经过高温充分熔解,生成硅酸盐后通过碳C还原成硅锰合金产品。
入炉冶炼电功率方式是大电流、低电压。
6300KVA~12500KVA电炉,二次电压165V以下。
12500KVA以上,冶炼二次电压在165~250V之间。
而冶炼的二次电流则几万到十几万、甚至几十万安培不等,不同的电炉参数不同。
功率越大的电炉则冶炼二次电压越高,冶炼二次电压取决于硅锰电炉的三个电极生成的圆周直径,以及电炉对产弧弧光的要求。
电炉功率越大极心圆直径越大,那么电压就会越高,但一般不高于280V,主要是考虑电炉的绝缘条件承受能力。
生产过程根据炉况不断的调节电压电流,以达到最大和最佳的冶炼功率,减少损耗、热量流失,提高产能。
而怎样把电炉冶炼电流、电压做到最合理的匹配,是我们要探讨的目的。
1.治炼电流的控制那么硅锰生产冶过程中,是不是电流越大来冶炼、效率就越高、产量就越高、效果越好呢,答案是否定的。
每个电弧炉都有其固定设计的参数,电炉在设计好之后,某些参数就会定死(多大容量的电炉以KVA为准,那么参数就有一个标准,比如短网尺寸,极圆心、电极筒直径等已然确定)。
所以我们要讨论的是一定容量下电炉的最佳冶炼效果。
因为铁合金电炉变基本都需要超负载运行,所以从电效率的角度出发的,冶炼电流是由短网的参数和特性决定的,也就是说冶炼电流的大小由短网(一般为紫铜材料做成)来决定,必须在短网的承受能力之内,找到最佳的电流进行冶炼。
冶炼用电量

冶炼用电量冶炼用电量是指在冶炼过程中所需的电力能源消耗量。
随着工业的发展和技术的进步,冶炼用电量在金属冶炼、有色金属冶炼、钢铁冶炼等行业中扮演着重要的角色。
本文将从冶炼用电量的概念、影响因素、节约措施等方面进行探讨。
一、冶炼用电量的概念冶炼用电量是指在冶炼过程中所消耗的电力能源。
冶炼过程通常包括矿石的破碎、磨矿、选矿、熔炼等环节,而这些环节都需要大量的电力供应。
因此,冶炼用电量成为衡量冶炼工艺和设备能耗的重要指标。
1. 冶炼工艺:不同的冶炼工艺对电力的需求量有所不同。
例如,电炉熔炼相对于传统的燃气熔炼更加节能,能够有效降低冶炼用电量。
2. 设备能效:冶炼过程中使用的设备能效直接影响电力的消耗量。
高效的设备能够将电能转化为热能或机械能的效率提高,从而减少能源的浪费。
3. 原材料质量:原材料的质量直接影响到冶炼过程中的能耗。
优质的原材料能够提高冶炼的效率,减少能源的消耗。
4. 工艺控制:合理的工艺控制能够减少能源的浪费。
通过优化冶炼过程中的温度、压力等参数,可以实现能耗的最小化。
三、节约冶炼用电量的措施1. 优化冶炼工艺:选择高效的冶炼工艺,如电炉熔炼等,能够有效降低冶炼用电量。
2. 更新设备:使用节能高效的设备替代老化的设备,能够提高设备的能效,并减少能源的消耗。
3. 提高原材料利用率:通过优化原材料的质量和配比,提高冶炼过程中的原材料利用率,从而降低能源的消耗。
4. 强化工艺控制:通过监测和控制冶炼过程中的温度、压力等参数,实现能耗的最小化。
5. 发展清洁能源:积极发展和利用清洁能源,如风能、太阳能等,减少对传统能源的依赖,从而降低冶炼用电量。
总结:冶炼用电量是冶炼过程中所需的电力能源消耗量,其大小受到冶炼工艺、设备能效、原材料质量和工艺控制等多个因素的影响。
为了节约冶炼用电量,可以采取优化工艺、更新设备、提高原材料利用率、强化工艺控制和发展清洁能源等措施。
通过这些措施的实施,可以实现冶炼过程中能源的有效利用,减少资源的浪费,进而促进工业的可持续发展。
- 1、下载文档前请自行甄别文档内容的完整性,平台不提供额外的编辑、内容补充、找答案等附加服务。
- 2、"仅部分预览"的文档,不可在线预览部分如存在完整性等问题,可反馈申请退款(可完整预览的文档不适用该条件!)。
- 3、如文档侵犯您的权益,请联系客服反馈,我们会尽快为您处理(人工客服工作时间:9:00-18:30)。
硅锰冶炼中影响电耗的原因
及如何合理降低吨产品电耗措施
2020.1.9
一、影响产品冶炼电耗的主要因素
1、原料对吨产品冶炼电耗的影响
冶炼锰硅合金的主要原料有锰系原料、焦炭等。
焦炭由于成分不稳定等因素,往往导致冶炼炉况波动,使吨产品冶炼电耗高低不一;锰系原料由于进口锰矿价格居高不下以及国内贫矿杂质含量高等因素的制约.导致原料入炉锰频繁上下调整,同时冶炼生产中必将有部分热量和焦炭来还原多余的杂质,使吨产品冶炼电耗难以保持稳定。
表1 原料入炉锰与吨产品冶炼电耗对比表由表1可以看出。
锰硅合金吨产品冶炼电耗明显受原料入炉锰品位的影响,实际每升高或降低l%,相应冶炼电耗也降低或升高63kwh/t。
2、生产工艺及操作管理对吨产品冶炼电耗的影响
由于操作人员对实际生产工艺要求的认识及操作水平高低不一,炉况频繁受偏加料、供电功率波动、三相电极做功不均衡、超负荷运行等因素的影响.使吨产品冶炼
电耗升高。
3、设备装备及运行状况对吨产品冶炼电耗的影响
目前.行业内大部分在线矿热炉普遍设备装备差、劳
动强度高、机械化程度低。
由于设备逐步老化、原有设计
存在一定缺陷,加之电网供电质量不稳定,致使矿热炉有
效作业率不足,热停次数和时间增加,直接造成锰硅合金
吨产品冶炼电耗升高。
二、降低吨产品冶炼电耗的主要措施
1、科学合理供电
(1)提高输入炉内的电压有效功率
锰硅合金冶炼中用于维持熔池反应区的的高温和热
量主要由消耗电能满足。
因为电功率值与电压、电流和功
率因数成正比,理论上要求电压波动不超过±5%,主要是
一次电压必须稳定,并保持在上限范围内,这样最大限度
提高输入炉内的电压有效功率,冶炼才具备取得好的技术
经济指标的基础。
(2)适当选用二次电压
在炉容和冶炼产品规格相同的情况下,应根据“电炉
总效率=电效率×热效率”的原则取得最佳效益,即:提
高炉温,使Si利用率提高、渣中跑Mn下降、吨产品冶炼
电耗降低。
在保证电极下插适当深度、炉口热损失较小的情况下。
适当地选用较高一级的二次电压,当输入功率稳定时,二次电流相对较小,这样有利于提高功率因数和电效率;但当二次电压过高、电弧过长,必然需要上抬电极,热损失增加。
2、优化经济配料
(1)提高原料入炉锰品位
由表1可以看出。
在容量25000kvA矿热炉正常生产情况下。
锰硅合金的吨产品冶炼电耗明显受原料入炉锰综合品位的影响。
随着所用锰矿原料中Mn充分被回收,渣铁比由1.2~1.3降低至0.9一1.0,从而有效增加了Mn 金属回收量,在均衡耗电的前提下.入炉锰品位每升高或降低1%,相应冶炼电耗也降低或升高≤100kwh/t。
(2)选用物化性能适宜的锰系原料
由于锰矿的性能受其矿物组成影响,锰系原料实际采购中除重点要求选择高Mn/Fe外,比电阻大、熔点高和粉末率低也是采购锰矿需要注意的方面。
①比电阻
比电阻大的锰矿容易使电极深插。
热能利用率高,使吨产品冶炼电耗降低。
②熔点
熔点高的锰矿成渣较晚,炉料能保持良好的透气性和较高的炉温,有利于充分进行相关化学反应,减少渣量,
使吨产品冶炼电耗降低。
③粉末率
粉末率低的锰矿能保证入炉原料透气性相对较好,同时也可以减少炉内冶炼塌料次数,避免炉况异常波动,使吨产品冶炼电耗降低。
3、合理控制炉渣碱度
实际生产中,炉渣碱度大、流动性差,必然导致排渣不畅.不利于MnO的还原和Mn回收率的提高。
因此,要重点做好焦炭的足量配比和炉况的稳定顺行工作,改善炉渣流动性,提高SiO2还原率,使渣中SiO2由33%一36%降低至28%~31%,确保炉渣碱度稳定在0.6~0.75之间,从而实现低渣比冶炼、减少原料溶剂的配入量和降低吨产品冶炼电耗的目的。
4、加强炉前操作管理
①均匀混合炉料,勤加薄盖布料
在原燃料配比准确情况下.均匀混合炉料、勤加薄盖布料能使炉料充分预热、料面保持良好的透气性。
这也就是小炉子采用人工加料、大中型炉子要在设备和流程上保证混料布料均匀(原料不落地入炉),并取得良好技术经济指标的重要原因。
当输入功率一定、炉料电阻较大时,通过炉内支路电流减小、电弧电流增加,使熔池功率增大、坩埚区域扩大,热效率随之提高,加上炉料良好的透气性,
单位时间还原出来的Mn自然增多。
②合理压放电极,保持炉况稳定
冶炼操作过程中,电炉功率的调整是通过改变电极位置来实现的。
在选择好工作电压后,保持“深电极、满负荷、低料面”作业,实际操作中,要保持三相电极平衡及电极工作端长度1600—1800mm(其中埋入炉料1500mm左右),确保炉料的正常焖烧,力求减少热损失。
有时三相电流差异较大,应从均匀布料、料面高度、电极插入深度等方面找原因平衡。
特别是出铁后期,电极操作要格外精心,此时较容易过流跳闸。
并导致坩埚上部未完全还原的炉料混入铁水中,使出铁不完全,不仅影响当炉产量,对后续冶炼生产也会造成一定影响。
主要做法:
(1)提前15分钟接班,正常情况下保证正点出铁;
(2)杜绝空烧和刺火;
(3)加强人工拉渣。
③适当延长冶炼时间,减少出铁次数
实际生产中,在避免翻渣的情况下。
可以适当延长冶炼时间,达到减少热量损失和提高炉膛温度的目的,比如将出铁炉次由10炉/天减少到8炉/天。
由于入炉功率的提高,从而保证了炉内焦炭层反应区的高温条件,使Mn 还原率大幅提高,同时也降低吨产品冶炼电耗和人员劳动
强度。
5、保持良好设备运行状态
①维护电极,减少热停炉
维护好电极、避免热停事故.是生产组织的关键,一般短期热停炉。
每热停一小时需要两个小时恢复炉况,能耗损失较大。
常见的电极事故有:漏糊、硬断和软断,均在电极压放中时常发生。
电极直径越大,频繁停送电,都容易导致电极事故.因此多根据电极消耗、时间间隔、热量吸收等综合因素,采用电脑定量压放电极的方式实现自动压放。
具体要求:
(1)电极糊的理化成分应符合国标要求.同时适合该炉型的使用要求;
(2)电极糊的堆放、破碎、转运必须保持洁净,防止灰尘和杂物落入;
(3)糊柱高度要适合,一般来说25000kvA的糊柱高度应控制在4~4.3m之间:
(4)避免每班电极的下放量过长或过短,每次下放量不应超过3cm。
②定期维护出铁口
出铁口定期维护是也冶炼生产的关键.因跑眼、炉壁烧穿等事故都会造成较大的能耗损失,而且严重影响炉衬
寿命,这就要求开眼时应多捅少烧。
特别是少吹氧气、定
期轮换使用出铁口并及时修补维护。
③加强定检修,做好各类机械、电气设备的维护工作
设备的良好运转时保证作业率的关键,也是节能降耗
的重要方面。
很多机械、电气设备都是在“高温、高负荷、
高粉尘”条件下运行的,因此做好“降温、除尘、润滑”等Et常定期检查维护保养工作是十分重要的。
同时采用
化学的方法除去循环冷却水中的Ca、Mg离子,减少结垢,
可以有效提高设备的可靠性和作业率。
重点是炉用变压器,要定期进行巡视检查、油样分析。
6、革新技术,实施技术改造
XXX集团XXX铁合金公司目前两台电炉(25000kvA电炉)生产锰硅合金,从生产实践来看,尽管在生产过程中
各项技术经济指标较硅铁、高碳铬铁表现较为优秀,但当
期炉体冶炼安全是生产顺行的关键.为更好地调节处理炉况,仍需进行局部技改。
电炉的关键设备是变压器和短网(含电极部分),变压
器应选择新型节能变压器(过载能力大、功率因数高,必
要时进行电容补偿),短网材质精良和安装合理,电器参
数与炉体参数匹配得当,这样的炉体设备才能实现高效节
能的目的。
比如:采用高效长寿的电炉构件提高作业率;采用二
次电压补偿技术;采用单相有载调压变压器和水冷铜管与水冷电缆组合式短网母线,来降低短网温度,同时降低电压和损耗。
总结
节能降耗在铁合金生产过程中是一个永恒的主题,降低锰硅合金吨产品冶炼电耗更是一个需要长期实践、探究和逐步实现的过程。
在抓好原料、设备及操作基础条件的同时,更要做到优化经济用料、合理安全用电、标准化操作、精心维护炉况。
在科学管理、技术攻关与节能改造相结合的同时,才能对降低锰硅合金吨产品冶炼电耗起到满意的效果,真正确保电耗指标逐年进步。