工艺风险评估验证及状态维护
工艺风险评估验证及状态维护资料

工艺风险评估验证及状态维护资料
1、工艺风险评估
工艺风险评估是一种风险管理技术,它指的是用最有效的、最科学的方法,识别、分析以及控制其中一产品的设计、生产、安装和使用过程中所涉及到的工艺风险,通过识别和控制风险措施,提高产品的安全性,从而实现最终的工艺安全。
2、工艺风险验证
工艺风险验证是将工艺风险评估中分析出的可能存在的工艺风险进行验证,根据所得数据分析结果与工艺安全标准对比,是否满足工艺安全标准,如果不满足,那么形成的数据应作为有效的对策措施,按照规定来进行风险控制。
3、工艺风险状态维护
工艺风险状态维护指的是在工艺风险评估和验证的基础上,按照规定的定期维护措施对工艺安全状况进行定期检测、跟踪,并根据需要不断调整控制预防措施,以保障工艺的安全性。
3-工艺风险评估-HACCP

2/93
返回目录
课程目录
一、HACCP定义 二、法规指南要求 三、HACCP概述
四、HACCP工作准备
五、HACCP工作流程 六、HACCP报告
3/93
返回目录
一、HACCP定义
4/93
en/2008_02_12_gmp_annex20_en.pdf GMP第20附录质量风险管理
返回目录
WHO TRS
WHO技术报告系列No.908附录7 《危害分析和关键控制点》
11/93
http://www.who.int/medicines/library/qsm/trs908/trs908-7.pdf 技术报告系列No. 908,2003,附录7
返回目录
PIC/S
2010年1月4日 PIC/S发布了实施质量风险管理
示例
12/93
/publication.php?id=4 质量风险管理
返回目录
ISPE
返回目录
文件编制要求
按照业主确认的格式进行文件的编制,经过业主QA批 准后方可执行。
工艺风险评估-HACCP SOP (如适用)
报告模板
报告编号:RA-XXX-00 即:RA-产品编号-版本号
29/93
返回目录
纯蒸汽 发生器
压缩空气
35/93
返回目录
危害分析
在产品的生产过程中从人、机、料、法、环方面找出可能 发生危害的因素。 在危害分析阶段,评估团队将审核产品的物料,活动,设 备,储存,分发和预计用途。每一步骤将写出可能引入、 增加或控制的潜在的危害(生物、化学和物理)的清单。
原料药工艺风险评估

原料药工艺风险评估标准化管理处编码[BBX968T-XBB8968-NNJ668-MM9N]XXXXX原料药工艺风险评估(样本)一、风险等级评估风险等级严重性可能性可检测性对关键质量属性有影响操作范围接近设计空间或注风险发生及有高必须严格控制才能保证册范围或参数范围较窄,参发生趋势时可以质量参数偏离范围为关数本身较难控制,正常情况立即被发现。
键性偏差。
下可能会偏离范围。
对关键质量属性可能有操作范围接近设计空间或注发现发生后稍中影响,不严格控制会出册范围或参数范围较宽,参后才能被发现现质量大的偏差数本身容易控制,异常情况下才会偏离范围。
对关键质量属性影响很操作范围远比设计空间或注发现发生后很低小,参数偏离范围为小册范围窄或参数范围比较宽,久后才能被发现偏差或微偏差紧急情况下才会偏离设计空间二、风险评估矩阵1、风险等级矩阵2、内在关键性矩阵高高高高严高潜在关键关键严中低中高重中非关键潜在关键重低低低中性低非关键非关键潜在性低低中高低中高可能性可能性3、可检测性和内在关键性矩阵 4、评估相关性报告文件最终关键性序名称描述可高非关键非关键关键号1 产品属性评估表影响工艺步骤评估检中非关键关键关键2 产品质量属性评估表影响工艺参数评估3 产品质量属性评估表工艺参数关键性评估测低非关键关键关键4 产品质量属性评估表工艺参数关键性评估性非关键潜在关键(采取控制措施后)内在关键性三:产品工艺风险评估1、风险评估小组确定评估小组负责人,成员有研发专家、技术转移人员、生产操作人员、工程人员、项目人员、验证人员、QA、QC、供应商(如必要);2、寻找产品质量属性(CQA)和关键工艺参数(CPP)的必要前提条件:1)文件资源:A 保证评估前已具备所有必要的文件;B 详细的文件资料能有效支持CQA和CPP风险评估的执行,有资料需求单。
2)良好培训A GMP知识培训;B 质量风险管理(ICHQ9);C 公司质量风险管理规程;D 产品工艺知识;E 产品质量属性和关键工艺参数评估程序;F 产品质量属性和关键工艺参数风险评估模板。
XX片剂工艺验证风险评估模板

质量风险评估工艺参数关键性评估报告编号:STP-SJ-品名:XXX片生产阶段:研发阶段口中试阶段口批量生产阶段口评估日期:20XX年X月X日1、质量风险评估的目的运用风险管理的工具,全面评估现执行的XXX片生产工艺,通过质量风险管理方法评估后确定生产工艺的关键步骤和关键工艺参数;通过加强员工培训教育、完善工艺规程及标准操作规程等管理和控制措施,提高质量风险控制的能力,以确保持续稳定的生产出符合预定用途和注册要求的药品。
2、评估流程五步法评估关键工艺参数1)筛选产品与工艺相关的关键质量属性2)筛选影响产品关键质量属性的工艺步骤3)筛选影响关键质量属性的工艺参数4)结合工艺参数进行风险评估确定工艺参数的关键性5)采取管理和控制措施进行风险控制,重新评估工艺参数的关键性3、风险等级与风险矩阵3.1风险等级3.2严重性和可能性矩阵(风险等级、内在关键性)风险等级内在关键性低中高 可能性3.3可检测性和内在关键性矩阵(最终关键性) 最终关键性内在关键性4、评估报告相关文件可 检 测 性重 性高 中 低非关键潜在关键关键产品质量属性评估表1—影响工艺步骤评估产品质量属性评估表2—影响工艺参数评估产品风险评估表3—工艺参数关键性评估产品风险评估表4—工艺参数关键性评估(采取管理或控制措施后)说明:1、产品质量属性:根据产品质量指标填写,如:外观、溶解度、鉴别、含量、杂质、水分等。
2、工艺步骤:该栏填写工艺步骤编号和相应的工艺步骤名称。
3、对质量属性有无影响填写“有”或“无” ;人机物法环任何一项或以上对质量属性有影响,结论栏中填写“有” ;均无影响,结论栏中填写“无” 。
4、质量指标(关键质量属性):该栏填写对应的工艺参数发生偏差时可能产生的影响,分高、中、低、无四个等级。
高:影响啊很大,主要决定因素;中:异常时有影响,影响一般;低:有影响但很小;无:无影响。
5、影响:按照该参数对各个关键质量属性各项中最严重程度来确定该参数的最终影响产品质量的程度。
设备确认与风险评估
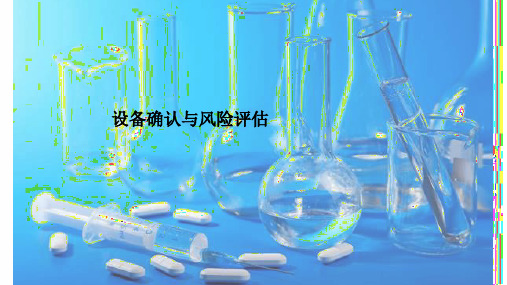
21:30:42
设备确认与风险评估
系统影响性评估(SIA)
系统影响性评估:评估系统的运行、控制、报警和故障状况对产品质量的影响的过程。 系统影响性评估将系统分为三类:直接影响系统、间接影响系统、无影响系统。
设备确认与风险评估
系统及设备验证关键性评估
在完成对系统/设备的影响性评估之后,应对直接影响系统和间接影响系统的进行验证关键性评估,验证关键性 评估包括三个步骤: ——确定关键质量属性(CQA) ——确定关键工艺参数(CPP) ——对关键工艺参数进行风险评估 验证关键性评系指通过对直接影响系统或间接影响系统的关键组件进行风险评估,确定其在整个系统中的风险 程度,并建议控制措施降低风险。
组件关键性评估系指通过对直接影响系统的组件进行风险评估,确定其在整个系统中的风险程度。 通过评估,将组件归类为关键和非关键两种。 关键组件:系统的某个组件,其运行、接触、数据、控制、报警或故障会对产品的质量参数(功效、特性、安 全、纯度、质量)有直接影响。 非关键组件:系统的某个组件,其运行、接触、数据、控制、报警或故障会对产品的质量参数(功效、特性、 安全、纯度、质量)有间接影响或没有影响。
21:30:42
设备确认与风险评估
组件关键性影响性评估CCA
序号
关键组件关键性评估问题
1
组件是否用于证明符合所注册的工艺的规定?
2
功能/组件是否用于控制一个关键工艺参数?
3
功能/组件的正常操作或控制对产品质量或功效是否具有直接的影响?
工艺安全风险评估方法

工艺安全风险评估方法
工艺安全风险评估方法是一种系统性的方法,用于评估工艺过程中可能存在的安全风险。
以下是一些常用的工艺安全风险评估方法:
1. PHE(可能性、危害、严重程度)矩阵法:这种方法基于一个矩阵,将可能性和危害的严重程度进行评估,并依据评估结果确定相应的安全风险等级。
2. 事件树分析法(ETA):这种方法基于事件树理论,对工艺过程中可能发生的事件进行分类和分析,包括事件发生的可能性、危害、严重程度等因素,以及对应的控制措施和应急响应计划。
3. 风险矩阵法:这种方法将可能的风险事件进行分类,然后通过评估风险事件发生的可能性和危害的严重程度等因素,确定相应的风险等级。
4. 故障模式与影响分析法(FMEA):这种方法通过对工艺过程中可能出现的故障模式进行分析,评估故障的严重程度和可能性,并制定相应的预防和纠正措施。
5. 危险与可操作性研究(HAZOP):这种方法通过对工艺过程中可能存在的危险情况进行分析,评估危险的严重程度和可能性,并制定相应的控制措施和管理措施。
以上是一些常用的工艺安全风险评估方法,具体使用哪种方法
可以根据实际情况和需求来确定。
同时,评估的结果需要综合考虑各种因素,包括可能性、危害、严重程度、控制措施的可行性和效果等,以制定相应的安全措施和管理策略。
工艺验证质量风险评价
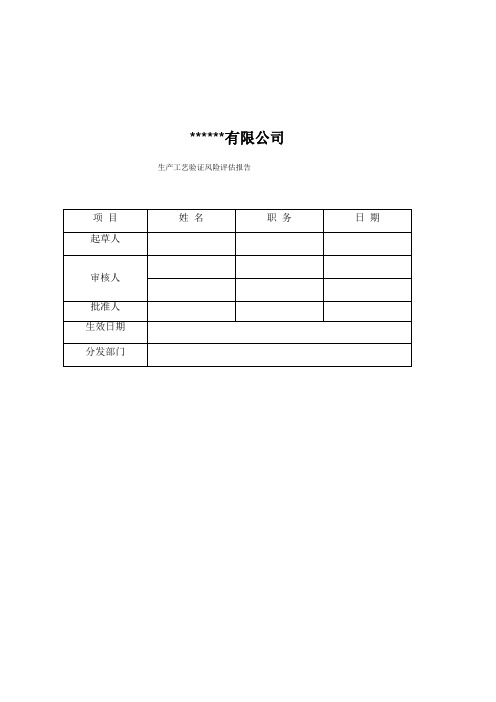
******有限公司生产工艺验证风险评估报告目录1概述2目的3适用范围4依据文件5质量风险管理小组职责6风险评估6.1风险评估过程6.2风险评估(失败模式影响分析)6.3安全性特征问题清单及可能危害分析6.4危害判断及风险控制措施6.5实施结论1、概述工艺验证应当证明一个生产工艺按照规定的工艺参数能够持续生产出符合预定用途和质量要求的产品。
验证的范围和程度应当经过风险评估来确定。
本报告拟对中药饮片工艺流程进行风险评估,以期对其工艺操作过程和关键参数的控制能正确认识并采取降低安全风险预见的控制措施,使生产质量的风险降低到可以接受的水平。
2、目的本文是对公司产品的净制、切制、炒制、炙制、煅制、蒸制等工序的操作和关键参数的控制风险评估。
对于每种风险可能产生损害的严重度(S)和危害的发生概率(P)进行估计。
在某一风险水平不可接受时,提出降低风险预见的控制措施,以期将剩余风险降低到可以接受的水平。
3、适用范围本报告适用于普通饮片生产车间、毒性饮片生产车间、直接口服饮片车间的产品生产的净制、切制、炒制、炙制、煅制、蒸制、煮制、发芽、发酵等工序。
4、依据文件药品生产质量管理规范(2010年修订)质量风险管理规程(SMP-QA-00-005)各岗位的操作规程相关产品的工艺规程5、质量风险管理小组职责6、风险评估6.1风险评估过程:项目质量风险管理提出——风险识别一一风险评估一一风险控制一一风险交流和通报一一风险评估一一风险管理活动评价6.2风险评估(失败模式影响分析)6.2.1严重性、可能性、检测性的定性•严重性(失败的结果)极高:预示对质量造成严重影响(产品不符合质量标准、没有可能的专家声明)高:预示对质量有显著影响(不符合质量标准、没有稳定性数据、可能的专家声明)中等:预示对质量有较小影响(没有满足质量标准、可得到稳定性数据)低:预示对产品质量没有/较小影响(质量在标准内)•可能性经常的失败:预料经常发生重复的失败:预料以一个低频次发生偶尔的失败:预料不经常发生不太可能的失败:不太可能发生•检测性一般不被检测到:很可能不被注意到的失败,因此未被检测到(没有技术上的解决,没有人工控制)可能不被检测到:可能被省略的失败(人工控制、现场检查)经常被检出:一般将被检出(人工控制、有统计控制的日常工作)总被检出:在任何情况下失败都能且将被检出(监控、可用的技术解决方式)6.2.2严重性、可能性、检测性的定量将不同水平以数值区间区分开,并将不同水平等级数值化。
制药设备验证风险评估报告

制药设备验证风险评估报告一、引言制药设备在药品生产中起到关键作用,对药品的质量和安全性有着重要影响。
为了确保制药设备运行的安全性和有效性,本报告对制药设备的验证风险进行评估,并提供相应措施和建议。
二、方法本次评估采用了风险评估的常用方法,包括风险识别、风险分析和风险评估。
通过对制药设备工作流程和设备本身的特点进行分析,识别可能存在的风险,并对这些风险进行定性和定量的评估。
三、风险识别根据制药设备的特性和工作流程,我们对以下几个方面进行了风险识别:1.设备故障:设备在运行过程中可能发生故障,导致药物生产的中断或质量问题。
2.操作不当:操作员对设备操作不熟悉或操作不规范,可能引发设备故障或操作失误。
3.设备设计缺陷:设备设计方面存在缺陷,可能引发安全隐患或操作困难。
4.清洁不当:设备清洗不彻底或不符合规范要求,可能污染产品或影响药品质量。
5.数据完整性:对设备运行数据的记录和保存存在不足或错误,可能导致数据完整性问题。
四、风险分析基于风险识别结果,我们对每个风险进行了分析,包括风险的原因、影响和可能性。
1.设备故障:原因可能包括设备老化、设备维护保养不当等。
影响可能包括药物生产的中断、产品质量问题等。
可能性根据设备的使用年限、维护保养情况等因素进行评估。
2.操作不当:原因可能包括人员培训不足、操作规范不明确等。
影响可能包括设备故障、操作失误等。
可能性根据人员培训情况、操作规范的明确性等因素进行评估。
3.设备设计缺陷:原因可能包括设计不合理、安全性考虑不足等。
影响可能包括设备安全隐患、操作困难等。
可能性根据设计评审的结果、已知安全问题等因素进行评估。
4.清洁不当:原因可能包括清洁程序不完善、操作不规范等。
影响可能包括产品污染、药品质量问题等。
可能性根据清洁程序的严格程度、操作规范的遵守情况等因素进行评估。
5.数据完整性:原因可能包括数据记录不完整、数据保存不安全等。
影响可能包括数据误读、数据丢失等。
可能性根据数据记录管理的规范性、数据保存的安全性等因素进行评估。
生产工艺质量风险评估
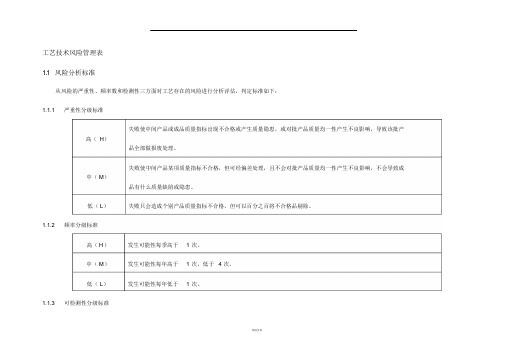
工艺技术风险管理表1.1 风险分析标准从风险的严重性、频率数和检测性三方面对工艺存在的风险进行分析评估,判定标准如下:1.1.1 严重性分级标准失败使中间产品或成品质量指标出现不合格或产生质量隐患,或对批产品质量均一性产生不良影响,导致该批产高(H)品全部做报废处理。
失败使中间产品某项质量指标不合格,但可经偏差处理,且不会对批产品质量均一性产生不良影响,不会导致成中(M)品有什么质量缺陷或隐患。
低(L)失败只会造成个别产品质量指标不合格,但可以百分之百将不合格品剔除。
1.1.2 频率分级标准高(H )发生可能性每季高于 1 次。
中(M)发生可能性每年高于 1 次,低于 4 次。
低(L)发生可能性每年低于 1 次。
1.1.3 可检测性分级标准具有反映质量均一性的质量指标,如含量均匀度、有关物质等能被仪器、设备100% 控制和检测。
中间产品质量与高(H)成品质量指标均对同一质量项目进行控制和检测。
涉及水分、装量等能被仪器、人员进行离线检测,但如不对过程进行有效控制,产品质量均一性无法确认,检测中(M)结果应被怀疑的质量指标。
无法对影响产品质量的控制指标的真实性进行有效监控,因此可能会影响到产品质量均一性,也可能会造成整批低(L)产品报废,可通过产品质量间接反映出问题。
1.2 风险分析列表项目可能的失败模可能的失败影风险评价控制措施风险再评价验证活动式领料领料发料错误产品整批报废H M H M核。
H L H L 确认复核方式、复核内容使用了错误的粉碎筛网过筛物料细度与工艺要求不一致,影响后续工艺和产品溶出度H M M H筛网应有目数标识;每次使用前操作人员必需核对筛网目数;用标准筛对物料粉末进行过筛检查;H L H L确认筛网标识、筛网目数;检查粉末细度;筛网破裂异物进入产品中H M M H每次使用前、后对筛网的完好性进行检查H M H L 确认筛网的完好性;响严重性可能性可检测风险级严重性可能性可检测风险级S O 性D 别S O 性D别按生产指令、批生产记录进行复风险评价风险再评价严可可风严可可风可能的失败模可能的失败影重能检险重能检险项目控制措施验证活动式响性性测级性性测级S O 性别S O 性别D D控制设备转速、粘合剂浓度与加确认设备转速、粘合剂、软材干湿度不影响湿颗粒的M M M M 量、湿混时间;M L M L 均匀制备软材外观;依据经验判定软材的干湿程度;软材影响干颗粒、成软材含量不均制备品含量的均一H M M H 控制干混时间、湿混时间;M L M M 确认干混、湿混时间匀性粘合剂配制错整批产品报废H L M M 双人单独复核粘合剂名称、浓度H L L L 确认复核方式误风险评价风险再评价严可可风严可可风可能的失败模可能的失败影重能检险重能检险项目控制措施验证活动式响性性测级性性测级S O 性别S O 性别D D颗粒粒度不符湿法整粒刀转合要求,影响后M M M M 每次使用前操作人员必需确认整M M H L 确认整粒刀转速;湿法速过低或过高粒刀转速;续生产制粒异物进入产品每次使用前、后对筛网的完好性筛网破裂H M M H H M H L 确认筛网的完好性;中进行检查使用的干燥空颗粒被微生物使用高效过滤器对空气进行过沸腾H H M H H L M M 无气不洁净污染滤,并定期维护保养、更换干燥使用的干燥空延长干燥时间,M M M M 控制风机频率,确保风量;M L M L 确认风机频率、抖袋频次;风险评价风险再评价严可可风严可可风可能的失败模可能的失败影重能检险重能检险项目控制措施验证活动式响性性测级性性测级S O 性别S O 性别D D气风量不足影响药品水分控制抖袋频次,防止堵塞;含量延长干燥时间,加热温度不足影响药品水分M M M M 控制进风温度、物料温度及干燥M L M L确认进风温度、物料温度时间;及干燥时间;含量物料平衡、收过滤袋安装前检查;干燥颗粒损耗大率不合格,成M M H M 根据干燥前中后段对风机频率调M L H L 确认风机频率品收率降低节。
工艺风险评估验证及状态维护精品PPT课件
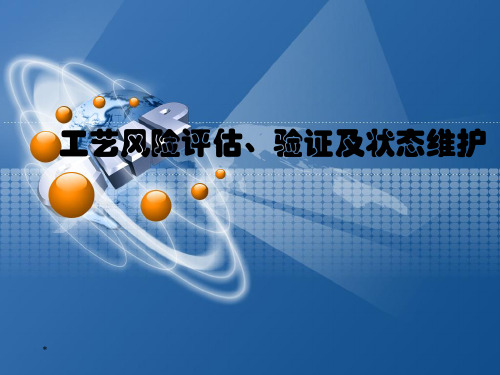
• PV验证批量应与预期商业化生产的规模和预期的产品批量 相通。同时验证批次应符合关键工艺参数(CPP)和前处 理标准(CFP)的要求,同时符合工艺规程(PFD)中描述 的其他控制参数以及相关范围要求。
*
工艺参数的确定
• 弄清原始数据的定义:反映最初观察或 实施结果的任何记录、图表、工作表、 备忘录、笔记等。原始数据可以是纸张
形式或电子形式的。进行观察的人必须 是填写原始数据的人,不要撕毁任何原 始记录!修改之处划一条线,签名及日 期,划线之处能够辨认文字。
*
工艺参数的确定
*
工艺过程风险评估示例
• 关键工艺FMEA风险评估表 • 冻干粉针剂轧盖风险评估示例
*
工艺验证与工艺优选
• 工艺验证—证明工艺在预期参数范围内 运行时,能有效地、重复地生产出符合 预定质量标准和质量属性的产品的有文 件记录的一系列活动。
• 工艺优选—工艺开发的一个阶段,对工 艺条件的优化过程。
*
*
FDA工艺验证指南
• FDA2011年1月颁布工艺验证:一般原则 和规范。
• 第一阶段:工艺设计 • 第二阶段:工艺确认 • 第三阶段:持续的工艺核实
*
最差条件与挑战性试验
• 最差条件—在SOP范围内,由工艺参数的上、 下限和相关因素组成的一个或一系列条件。与 理想条件相比时,最差条件使产品或者生产工 艺失败的几率为最大,但这类最差条件不一定 必然导致产品或工艺的不合格。
• 挑战性试验—确定某一个工艺过程或一个系统 的某一组件,如一个设备、一个设施在设定的 苛刻条件下能否确保达到预定的质量要求的试 验。
生产工艺验证风险评估报告
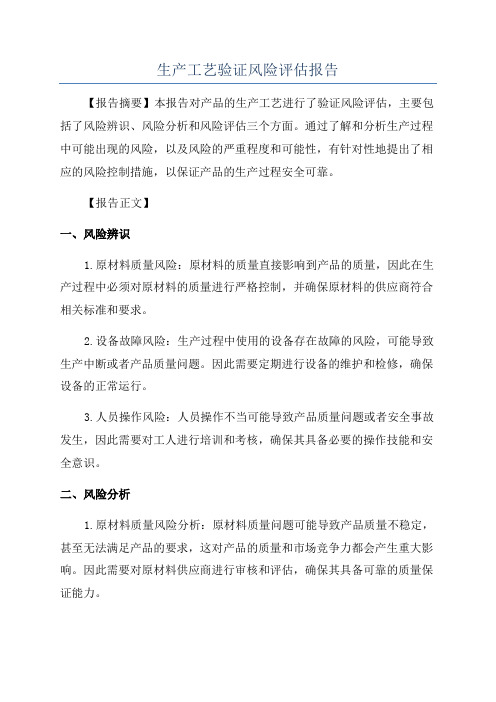
生产工艺验证风险评估报告【报告摘要】本报告对产品的生产工艺进行了验证风险评估,主要包括了风险辨识、风险分析和风险评估三个方面。
通过了解和分析生产过程中可能出现的风险,以及风险的严重程度和可能性,有针对性地提出了相应的风险控制措施,以保证产品的生产过程安全可靠。
【报告正文】一、风险辨识1.原材料质量风险:原材料的质量直接影响到产品的质量,因此在生产过程中必须对原材料的质量进行严格控制,并确保原材料的供应商符合相关标准和要求。
2.设备故障风险:生产过程中使用的设备存在故障的风险,可能导致生产中断或者产品质量问题。
因此需要定期进行设备的维护和检修,确保设备的正常运行。
3.人员操作风险:人员操作不当可能导致产品质量问题或者安全事故发生,因此需要对工人进行培训和考核,确保其具备必要的操作技能和安全意识。
二、风险分析1.原材料质量风险分析:原材料质量问题可能导致产品质量不稳定,甚至无法满足产品的要求,这对产品的质量和市场竞争力都会产生重大影响。
因此需要对原材料供应商进行审核和评估,确保其具备可靠的质量保证能力。
2.设备故障风险分析:设备故障可能导致生产中断,引起产品质量问题和生产计划延误。
因此需要对设备进行定期的检修和维护,并建立相应的备用设备,以应对可能的故障情况。
3.人员操作风险分析:人员操作不当可能导致产品质量问题或者安全事故发生,对生产和企业形象都会产生负面影响。
因此需要对工人进行培训,提高其操作技能和安全意识。
三、风险评估1.原材料质量风险评估:原材料质量风险的严重程度取决于原材料对产品质量的影响程度,以及原材料质量的稳定性。
通过对原材料的质量进行评估,确定其对产品质量的影响,以及原材料供应商的质量管理能力。
2.设备故障风险评估:设备故障可能导致生产中断,严重影响生产进度和产品质量。
通过对设备的故障概率、维修时间和备用设备的可用性进行评估,确定设备故障风险的可能性和严重程度。
3.人员操作风险评估:人员操作不当可能导致产品质量问题和安全事故发生。
工艺验证工艺风险评估
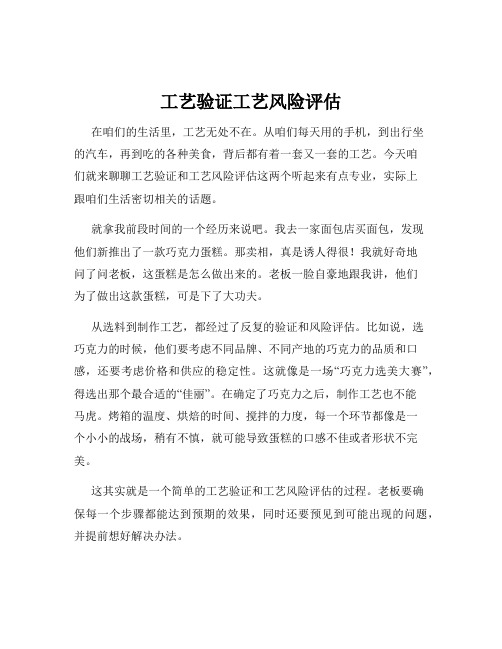
工艺验证工艺风险评估在咱们的生活里,工艺无处不在。
从咱们每天用的手机,到出行坐的汽车,再到吃的各种美食,背后都有着一套又一套的工艺。
今天咱们就来聊聊工艺验证和工艺风险评估这两个听起来有点专业,实际上跟咱们生活密切相关的话题。
就拿我前段时间的一个经历来说吧。
我去一家面包店买面包,发现他们新推出了一款巧克力蛋糕。
那卖相,真是诱人得很!我就好奇地问了问老板,这蛋糕是怎么做出来的。
老板一脸自豪地跟我讲,他们为了做出这款蛋糕,可是下了大功夫。
从选料到制作工艺,都经过了反复的验证和风险评估。
比如说,选巧克力的时候,他们要考虑不同品牌、不同产地的巧克力的品质和口感,还要考虑价格和供应的稳定性。
这就像是一场“巧克力选美大赛”,得选出那个最合适的“佳丽”。
在确定了巧克力之后,制作工艺也不能马虎。
烤箱的温度、烘焙的时间、搅拌的力度,每一个环节都像是一个小小的战场,稍有不慎,就可能导致蛋糕的口感不佳或者形状不完美。
这其实就是一个简单的工艺验证和工艺风险评估的过程。
老板要确保每一个步骤都能达到预期的效果,同时还要预见到可能出现的问题,并提前想好解决办法。
再比如说,咱们穿的衣服。
一件衣服从布料变成咱们身上漂亮的时装,这中间也经历了无数的工艺环节。
服装厂要验证裁剪的方式是否合理,缝纫的线是否结实,染色是否均匀,而且还要评估在生产过程中会不会出现布料浪费、工人操作失误等风险。
工艺验证,简单来说,就是检查咱们的工艺是不是真的能做出咱们想要的东西,而且每次做出来的质量都差不多。
就像做数学题,咱们得保证用同样的方法,每次都能算出正确的答案。
这可不是一件容易的事儿!得有严格的标准,得有精确的测量,还得有认真负责的态度。
比如说,一家生产玩具的工厂,他们要生产一款会说话的娃娃。
那在生产之前,就得先验证一下,设计的电路能不能让娃娃清晰地说话,外壳的材质够不够结实,颜色够不够鲜艳。
这每一个环节都得仔仔细细地检查,不能有一点儿马虎。
工艺风险评估呢,则是在工艺验证之前,先想想可能会出现哪些问题。
生产工艺验证风险评估报告
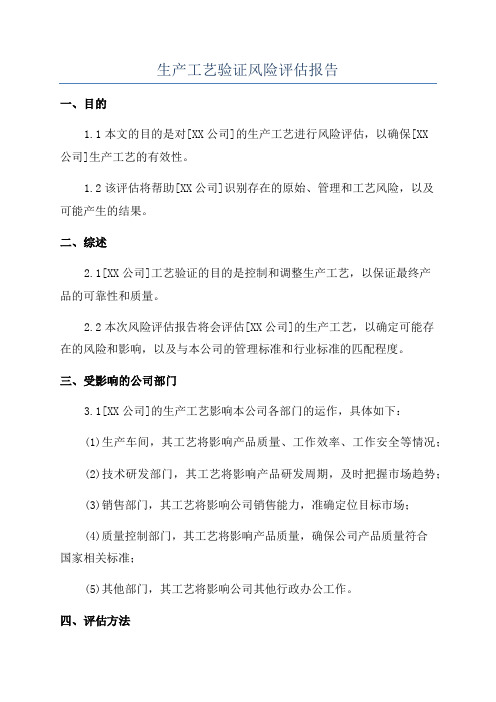
生产工艺验证风险评估报告
一、目的
1.1本文的目的是对[XX公司]的生产工艺进行风险评估,以确保[XX
公司]生产工艺的有效性。
1.2该评估将帮助[XX公司]识别存在的原始、管理和工艺风险,以及
可能产生的结果。
二、综述
2.1[XX公司]工艺验证的目的是控制和调整生产工艺,以保证最终产
品的可靠性和质量。
2.2本次风险评估报告将会评估[XX公司]的生产工艺,以确定可能存
在的风险和影响,以及与本公司的管理标准和行业标准的匹配程度。
三、受影响的公司部门
3.1[XX公司]的生产工艺影响本公司各部门的运作,具体如下:
(1)生产车间,其工艺将影响产品质量、工作效率、工作安全等情况;
(2)技术研发部门,其工艺将影响产品研发周期,及时把握市场趋势;
(3)销售部门,其工艺将影响公司销售能力,准确定位目标市场;
(4)质量控制部门,其工艺将影响产品质量,确保公司产品质量符合
国家相关标准;
(5)其他部门,其工艺将影响公司其他行政办公工作。
四、评估方法
4.1本次评估主要采用FMEA(失效模式影响分析),结合实际运行情况,分别从原始、管理和工艺风险等三方面,进行评估。
工艺验证报告总结
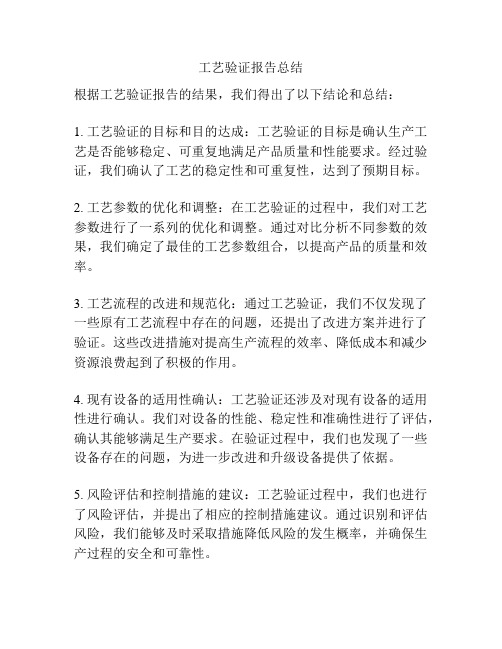
工艺验证报告总结
根据工艺验证报告的结果,我们得出了以下结论和总结:
1. 工艺验证的目标和目的达成:工艺验证的目标是确认生产工艺是否能够稳定、可重复地满足产品质量和性能要求。
经过验证,我们确认了工艺的稳定性和可重复性,达到了预期目标。
2. 工艺参数的优化和调整:在工艺验证的过程中,我们对工艺参数进行了一系列的优化和调整。
通过对比分析不同参数的效果,我们确定了最佳的工艺参数组合,以提高产品的质量和效率。
3. 工艺流程的改进和规范化:通过工艺验证,我们不仅发现了一些原有工艺流程中存在的问题,还提出了改进方案并进行了验证。
这些改进措施对提高生产流程的效率、降低成本和减少资源浪费起到了积极的作用。
4. 现有设备的适用性确认:工艺验证还涉及对现有设备的适用性进行确认。
我们对设备的性能、稳定性和准确性进行了评估,确认其能够满足生产要求。
在验证过程中,我们也发现了一些设备存在的问题,为进一步改进和升级设备提供了依据。
5. 风险评估和控制措施的建议:工艺验证过程中,我们也进行了风险评估,并提出了相应的控制措施建议。
通过识别和评估风险,我们能够及时采取措施降低风险的发生概率,并确保生产过程的安全和可靠性。
综上所述,通过工艺验证报告的分析和总结,我们确认生产工艺的稳定性和可重复性,并对工艺参数、流程和设备进行了优化和改进。
这些结果将为生产过程的持续改进和提高产品质量提供参考。
同时,我们也建议根据风险评估提出的控制措施进行有效的风险管理。
无菌工艺模拟风险评估关键点
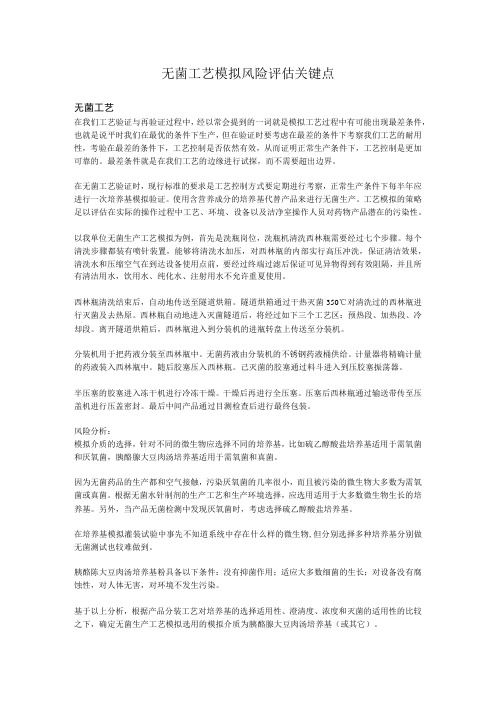
无菌工艺模拟风险评估关键点无菌工艺在我们工艺验证与再验证过程中,经以常会提到的一词就是模拟工艺过程中有可能出现最差条件,也就是说平时我们在最优的条件下生产,但在验证时要考虑在最差的条件下考察我们工艺的耐用性,考验在最差的条件下,工艺控制是否依然有效,从而证明正常生产条件下,工艺控制是更加可靠的。
最差条件就是在我们工艺的边缘进行试探,而不需要超出边界。
在无菌工艺验证时,现行标准的要求是工艺控制方式要定期进行考察,正常生产条件下每半年应进行一次培养基模拟验证。
使用含营养成分的培养基代替产品来进行无菌生产。
工艺模拟的策略足以评估在实际的操作过程中工艺、环境、设备以及洁净室操作人员对药物产品潜在的污染性。
以我单位无菌生产工艺模拟为例,首先是洗瓶岗位,洗瓶机清洗西林瓶需要经过七个步骤。
每个清洗步骤都装有喷针装置,能够将清洗水加压,对西林瓶的内部实行高压冲洗,保证清洁效果,清洗水和压缩空气在到达设备使用点前,要经过终端过滤后保证可见异物得到有效阻隔,并且所有清洁用水,饮用水、纯化水、注射用水不允许重夏使用。
西林瓶清洗结束后,自动地传送至隧道烘箱。
隧道烘箱通过干热灭菌350℃对清洗过的西林瓶进行灭菌及去热原。
西林瓶自动地进入灭菌隧道后,将经过如下三个工艺区:预热段、加热段、冷却段。
离开隧道烘箱后,西林瓶进入到分装机的进瓶转盘上传送至分装机。
分装机用于把药液分装至西林瓶中。
无菌药液由分装机的不锈钢药液桶供给。
计量器将精确计量的药液装入西林瓶中。
随后胶塞压入西林瓶。
己灭菌的胶塞通过料斗进入到压胶塞振荡器。
半压塞的胶塞进入冻干机进行冷冻干燥。
干燥后再进行全压塞。
压塞后西林瓶通过输送带传至压盖机进行压盖密封。
最后中间产品通过目测检查后进行最终包装。
风险分析:模拟介质的选择,针对不同的微生物应选择不同的培养基,比如硫乙醇酸盐培养基适用于需氧菌和厌氧菌,胰酪腺大豆肉汤培养基适用于需氧菌和真菌。
因为无菌药品的生产都和空气接触,污染厌氧菌的几率很小,而且被污染的微生物大多数为需氧菌或真菌。
确认、验证、风险评估
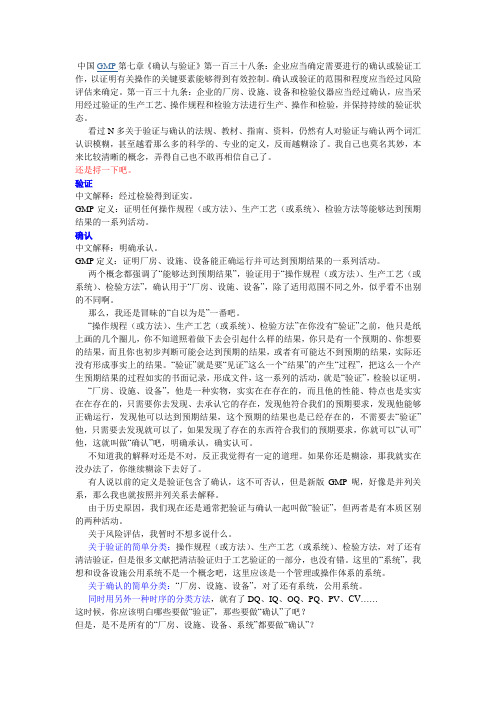
中国GMP第七章《确认与验证》第一百三十八条:企业应当确定需要进行的确认或验证工作,以证明有关操作的关键要素能够得到有效控制。
确认或验证的范围和程度应当经过风险评估来确定。
第一百三十九条:企业的厂房、设施、设备和检验仪器应当经过确认,应当采用经过验证的生产工艺、操作规程和检验方法进行生产、操作和检验,并保持持续的验证状态。
看过N多关于验证与确认的法规、教材、指南、资料,仍然有人对验证与确认两个词汇认识模糊,甚至越看那么多的科学的、专业的定义,反而越糊涂了。
我自己也莫名其妙,本来比较清晰的概念,弄得自己也不敢再相信自己了。
还是捋一下吧。
验证中文解释:经过检验得到证实。
GMP定义:证明任何操作规程(或方法)、生产工艺(或系统)、检验方法等能够达到预期结果的一系列活动。
确认中文解释:明确承认。
GMP定义:证明厂房、设施、设备能正确运行并可达到预期结果的一系列活动。
两个概念都强调了“能够达到预期结果”,验证用于“操作规程(或方法)、生产工艺(或系统)、检验方法”,确认用于“厂房、设施、设备”,除了适用范围不同之外,似乎看不出别的不同啊。
那么,我还是冒昧的“自以为是”一番吧。
“操作规程(或方法)、生产工艺(或系统)、检验方法”在你没有“验证”之前,他只是纸上画的几个圈儿,你不知道照着做下去会引起什么样的结果,你只是有一个预期的、你想要的结果,而且你也初步判断可能会达到预期的结果,或者有可能达不到预期的结果,实际还没有形成事实上的结果。
“验证”就是要“见证”这么一个“结果”的产生“过程”,把这么一个产生预期结果的过程如实的书面记录,形成文件,这一系列的活动,就是“验证”,检验以证明。
“厂房、设施、设备”,他是一种实物,实实在在存在的,而且他的性能、特点也是实实在在存在的,只需要你去发现、去承认它的存在,发现他符合我们的预期要求,发现他能够正确运行,发现他可以达到预期结果,这个预期的结果也是已经存在的,不需要去“验证”他,只需要去发现就可以了,如果发现了存在的东西符合我们的预期要求,你就可以“认可”他,这就叫做“确认”吧,明确承认,确实认可。
如何做好一个工艺验证

如何做好工艺验证工作呢?一个人或者说一个部门能不能做好验证工作?在论坛经常会看到一个验证主管去完成公司全部的验证文件(方案及报告),这样的验证能否做好待下去大家讨论!验证是一项跨部门的工作,与多个部门有关,需要相关部门的密切合作。
故此对于验证工作大家一定要有团队概念,这是做好验证工作的必要条件(注:对于全公司验证交个一个人或者一个部门来完成的,自己在尽力去做的同时,要和你的领导沟通让更多的相关人员参与进来)。
要做好验证这点很重要。
下面我从几个方面来阐述我对做好工艺验证的认识:1.首先做好验证计划这个计划是从下到上来做的,也就是说每个车间要每年将本单位要做的工艺验证按照生产计划及车间具体情况列出自己的计划,交质量部验证主管统一平衡,起草出公司的工艺验证总计划,这里注意时间节点及可能出现的变更,尽可能列出切实可行的年度总计划,交生产及质量负责人批准下发至各有关部门,质量部负责验证跟踪的人员按总计划列出每月需要完成的项目,及时的跟踪完成情况,做好各方面的沟通协调(注意,质量部验证主管不是起草方案和报告的人员,是审核和协调);2. 关于职责分配虽然在验证管理或者验证主计划内会有规定,但是那些一般对于具体的验证实施不会具体到参与验证的人员,在起草验证方案和审核时要注意,涉及具体工作一定要落实到具体的人,并且还要培训到位,让每一份验证方案涉及到的相关人员明确自己职责,提前做好准备工作,以便验证顺利进行。
养成习惯,形成流程,可以使验证按计划有效性的执行。
3.工艺验证实施前需要完成的项目:这个在你的公司文件中会有明确的规定。
⑴关键质量属性和关键工艺参数已确定;与验证相关文件要确认是否现行版本(包括工艺规程、各工序SOP,所有记录(批生产记录,批检验记录、清洁记录,设备运行记录等)、质量标准,检验操作规程);⑵厂房设施、系统和设备的验证或确认(包括计量器具的校准或检定,检验仪器的确认及产品分析方法验证或确认)已完成;⑶参与工艺验证执行的所有人员的培训已经完成(无菌制剂要完成人员进入无菌区的更衣确认),验证负责人负责组织工艺验证的培训,起草人负责对方案进行培训;⑷工艺验证中所用物料,包装材检验合格并放行(如:操作间和设备及现场环境满足工艺要求;公用系统满足工艺要求(工艺用水,空气、氮气及净化系统检测结果合格)4.工艺验证的方案(报告)的起草工艺验证方案起草人要对产品工艺有足够的认识,研发转移至生产的产品的工艺验证由研发工艺开发人员及生产单位工艺员共同起草(涉及变更的也有双方共同起草);日常生产产品的工艺验证由生产生产单位工艺负责人起草;5.验证的实施工艺验证按批准的验证方案逐项落实,生产车间负责人做好工作计划的人员分配,工艺员及QA做好验证过程数据收集的记录整理分析,跟踪中间体控制情况,做好验证过程的变更及偏差处理。
原料药工艺风险评估

原料药工艺风险评估This model paper was revised by the Standardization Office on December 10, 2020XXXXX原料药工艺风险评估(样本)一、风险等级评估风险等级严重性可能性可检测性对关键质量属性有影响操作范围接近设计空间或注风险发生及有高必须严格控制才能保证册范围或参数范围较窄,参发生趋势时可以质量参数偏离范围为关数本身较难控制,正常情况立即被发现。
键性偏差。
下可能会偏离范围。
对关键质量属性可能有操作范围接近设计空间或注发现发生后稍中影响,不严格控制会出册范围或参数范围较宽,参后才能被发现现质量大的偏差数本身容易控制,异常情况下才会偏离范围。
对关键质量属性影响很操作范围远比设计空间或注发现发生后很低小,参数偏离范围为小册范围窄或参数范围比较宽,久后才能被发现偏差或微偏差紧急情况下才会偏离设计空间二、风险评估矩阵1、风险等级矩阵2、内在关键性矩阵高高高高严高潜在关键关键严中低中高重中非关键潜在关键重低低低中性低非关键非关键潜在性低低中高低中高可能性可能性3、可检测性和内在关键性矩阵 4、评估相关性报告文件最终关键性序名称描述可高非关键非关键关键号1 产品属性评估表影响工艺步骤评估检中非关键关键关键2 产品质量属性评估表影响工艺参数评估3 产品质量属性评估表工艺参数关键性评估测低非关键关键关键4 产品质量属性评估表工艺参数关键性评估性非关键潜在关键(采取控制措施后)内在关键性三:产品工艺风险评估1、风险评估小组确定评估小组负责人,成员有研发专家、技术转移人员、生产操作人员、工程人员、项目人员、验证人员、QA、QC、供应商(如必要);2、寻找产品质量属性(CQA)和关键工艺参数(CPP)的必要前提条件:1)文件资源:A 保证评估前已具备所有必要的文件;B 详细的文件资料能有效支持CQA和CPP风险评估的执行,有资料需求单。
2)良好培训A GMP知识培训;B 质量风险管理(ICHQ9);C 公司质量风险管理规程;D 产品工艺知识;E 产品质量属性和关键工艺参数评估程序;F 产品质量属性和关键工艺参数风险评估模板。
- 1、下载文档前请自行甄别文档内容的完整性,平台不提供额外的编辑、内容补充、找答案等附加服务。
- 2、"仅部分预览"的文档,不可在线预览部分如存在完整性等问题,可反馈申请退款(可完整预览的文档不适用该条件!)。
- 3、如文档侵犯您的权益,请联系客服反馈,我们会尽快为您处理(人工客服工作时间:9:00-18:30)。
22:28:19
工艺验证的批次和批量
• 所有验证批次生产完成之前,可以对每个独立的批次进行 放行。然而,所有早于独立批次的验证批次生产的组合数 据都应记录在过渡报告中,并且在每批产品放行之前由质 量部门对数据进行审批。同步验证中,最后一批产品的过 渡期报告应包括所有验证批次的数据,并将其作为最终报 告进行管理。
22:28:19
工艺验证批次
• 领航批:1批,用于数理统计。 • 中试批:3批,比正常批量小。研发批次
的放大确认。 • 商业化生产批:3批,标准批量。规模化
生产确认。
22:28:19
工艺验证的报告
• PV方案至少包括:⑴工艺描述和PFD参考资料;⑵该项目 工艺验证研究的预期目标;⑶所有设备和设施的清单; ⑷所有分析方法的清单;⑸CPP和CFP,⑹需要实施的分 析检测;⑺可接受标准(包括产品的质量标准和可接受 标准、在线控制和验证的可接受标准,以及附加检测的 可接受标准;⑻取样计划和样品处理规程;⑼结果记录 和评估方法;⑽验证小组的角色和职责;(11)包含或参 考时间。
22:28:19
工艺验证(PV)
• 证明工艺在已确定的参数范围内运转时,能够有效运行, 并能够重复生产出符合预定标准和质量属性的中间产品、 API或成品。
• 前验证是首选的验证方法。特殊情况下无法进行前验证的 可以采用实质上是前验证的验证方案对工艺进行验证,但 个别批次可以在所有验证批次生产完成前予以放行,这就 是同步验证。对于不经常生产的现有产品,可以采用同步 验证的方式进行再验证。
• PV验证批次设计时,应考虑工艺的复杂程度、验证设计的 复杂程度、以及工艺变更的重要性等内容,一般建议至少 进行连续三批的验证。
• PV验证批量应与预期商业化生产的规模和预期的产品批量 相通。同时验证批次应符合关键工艺参数(CPP)和前处 理标准(CFP)的要求,同时符合工艺规程(PFD)中描述 的其他控制参数以及相关范围要求。
22:28:19
工艺过程风险评估示例
• 关键工艺FMEA风险评估表 • 冻干粉针剂轧盖风险评估示例
22:28:19
工艺验证与工艺优选
• 工艺验证—证明工艺在预期参数范围内 运行时,能有效地、重复地生产出符合 预定质量标准和质量属性的产品的有文 件记录的一系列活动。
• 工艺优选—工艺开发的一个阶段,对工 艺条件的优化过程。
22:28:19
FDA工艺验证指南
• FDA2011年1月颁布工艺验证:一般原则 和规范。
• 第一阶段:工艺设计 • 第二阶段:工艺确认 • 第三阶段:持续的工艺核实
22:28:19
最差条件与挑战性试验
• 最差条件—在SOP范围内,由工艺参数的上、 下限和相关因素组成的一个或一系列条件。与 理想条件相比时,最差条件使产品或者生产工 艺失败的几率为最大,但这类最差条件不一定 必然导致产品或工艺的不合格。
22:28:19
工艺质量风险管理的流程
• 工艺风险评估应建立在系统/设备风险评估的基础上,尤其是关键 质量属性和关键工艺参数的确定。
• 1.剂型、产品说明 • 2.列出剂型、产品的预定用途和注册要求。 • 3.列出剂型或产品的工艺流程图,确定工艺步骤 • 4.列出各工艺步骤需控制的关键质量属性 • 5.列出各工序步骤详细的过程图,确定工艺子步骤 • 6.列出工艺参数,确定关键工艺参数 • 7.输入关键参数故障事件 • 8.描述事件造成的最差影响 • 9.描述当前控制措施 • 10.通过选项确定严重性、可能性和可检测性。 • 11.计算风险优先等级 • 12.判定风险是否可以接受 • 13.不可接受的风险的控制措施 • 14.剩余风险的评估
22:28:19
关键质量属性的判定
• 关键质量属性(CQA)系指为了保证产品质量、产品效力、患者 安全性、数据完整性而需要控制(直接或间接)的物理、化学、 生物性质或特性。在确定关键质量属性时,请根据关键质量属性 评估的3个问题进行评估。对任何工艺的质量属性,3个问题中问 题1与问题2的答案是“是”,问题3的答案是“否”,就将该质量 属性确定为关键质量属性,否则,应确定为一般质量属性。关键 质量属性需要进行验证。
序号 关键质量属性评估问题
结果
1
若工艺控制失效是否会影响到某类质量属性? 是□ 否□
该质量属性是什么?
CQA
2
该工艺步骤能否将工艺失效发生的显著危害的 可能性消除或降至可接受水平吗?
是□
否□
3
后一工艺步骤能消除已辨明的危害,或将发生 危害的可能性降低到可以接受的水平吗?
是□
否□
22:28:19
关键质量控制点识别
子步骤 Q1 Q2 Q3 Q4 Q5 CCP/CP 做此判断的
和危害
CQP/QP 理由
22:8:19
关键工艺参数
• 关键工艺参数(CPP)系指发生改变之后 会影响到某项质量属性因而需要进行控 制以保证工艺能够达到所需质量的工艺 参数。针对系统/设备的过程图以及组件 的关键质量属性列出列出工艺参数,确 定关键工艺参数。关键工艺参数需要进 行验证。
关键质量控 制点识别
控制失效是否会影响到某类质量属 性?
• 是,关键质量控制点(CQP) • 否,控制点(CP)
• 注意关键质量控制点(CQP)和关键控制点(CCP)的区别。
• 注意治疗性指标和安全性指标的区别,某种风险程度上安全性指标 高于治疗性指标。
22:28:19
关键控制点的判定
• 关键控制点判定树形图 • 关键控制点确认表
22:28:19
工艺参数的确定
• 弄清原始数据的定义:反映最初观察或 实施结果的任何记录、图表、工作表、 备忘录、笔记等。原始数据可以是纸张
工艺风险评估、验证及状态维护
22:28:19
法规要求
• 企业应当确定需要进行的验证工作,以证明有关操作的 关键要素能够得到有效控制。确认或验证的范围和程度 应当经过风险评估来确定。
• 企业应当采用经过验证的生产工艺、操作规程和检验方 法进行生产、操作和检验,并保持持续的验证状态。
• 企业应当建立工艺验证和分析方法验证的文件和记录, 并能以文件和记录证明达到预定的目标。