制程OQC工作流程图
OQC检验流程图
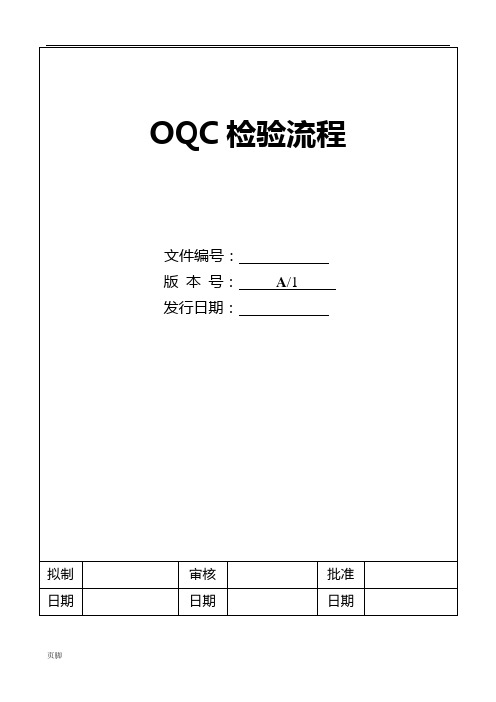
文件编号:
版本号:A/1
发行日期:
版 本 更 改 清 单
版本
更改容
更改人
日期
1.目的
规成品入库、出货检验作业流程,确保入库、出厂产品质量符合要求。
2. 适用围
本程序适用于本公司产品出货前的检验。
3.职责
OQC负责成品出货检验及出货过程的监控,并填写检验记录表和出货检验报告。
4.容
4.1 生产按包装作业指导书进行包装,即单个或最小批产品的包装,包装完成后按批次交OQC检验,需标识注明产品名称、数量、订单等信息。
5.相关文件
无
6.相关记录
《OQC质量信息反馈单》
附件:检验流程图
4.4生产依照作业指导书进行装箱。
4.5OQC装箱检验,检验容包括:产品数量、实物与清单一致性、外箱标贴,外箱是否破损、包装方式等。
4.6以上检验不合格,则:
a.对产品进行标识不合格、签字,填写检验记录,放置在指定的不合格品区后退货给产线进行挑选/返工;
b.检验NG批次填写《OQC质量信息反馈单》,并经QC主管、生产主管、班长、IPQC签名确认后连同不良品一起退货给产线,产线填写自检结果、原因分析和纠正改善措施,挑选/返工完成后将产品、《OQC质量信息反馈单》一起提交OQC复检,QQC跟踪其纠正改善效果并填写复检状况。
4.7装箱检验OK后封箱,封口需贴OQC签名或盖章的封条,否则OQC不在外箱单签名(或盖检验员章)确认,并填写检验记录。
4.8对OQC检验合格产品,品质主管需随机进行抽取检验,依据OQC准备的检容包括:外观、结构、尺寸、性能、试验、试装、包装、外包装、装箱、入库、发货等全部信息,抽检确认不合格,则按OQC流程返还生产进行返工。
OQC出货检验流程图

OQC出货检验流程图
作成日期: 批准 审核
作成
备货至出货区 OK 仓库 追溯同类不良 OQC
贴不良标识
OQC
出货报验
品质异常报告
ห้องสมุดไป่ตู้
OQC NG OQC 出货检验
置不合格物料区
仓库
不良原因分析 OK 制造 返工 OQC 重新检验 顾客特采 OQC 特采标识 业务 反馈给顾客 各相关部门 提出纠正预防措施 制造部 纠正预防措施实施 品管部 措施效果确认 项目部 特许出货 名词注解:1、 IQC 进料检验 2、 IPQC 制程检验 3、 PQC 半成品检验 4、 FQC 成品检验 5、 OQC 出货检验 效果标准化 出 货 仓库 报废 开具《出货检 验报告》
品质控制流程图【2024版】
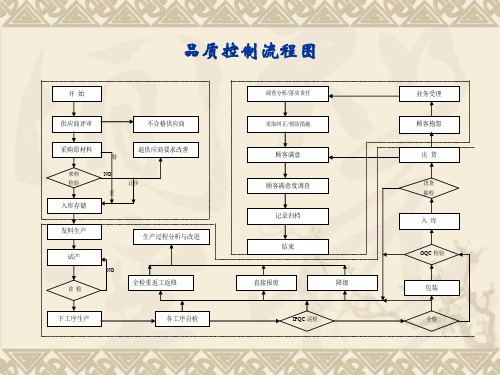
开始
供应商评审
不合格供应商
采购原材料
特
退供应商要求改善
来料 检验
入库存储
NO 让步
采
发料生产
生产过程分析与改进
获试产
首检
NO
全检重返工返修
下工序生产
各工序自检
调查分析/落实责任 采取纠正/预防措施
顾客满意 顾客满意度调查
记录归档 结束
直接报废
降级
IPQC 巡检
业务受理 顾客抱怨
出货
出货 抽检
潜在不符合识别
分析不符合原因
提出预防措施
对策否可行 NO
YES 执行预防措施
验证预防措施 NG
OK 标准化
相关记录存档
1.11 监视和测量装置控制流程
计测量器申购、验收
是否合格YES
计测量登记
是否校准 YES
执行內﹑外校准
校准判定 PASS
校准标识、记录
NO NO FAIL
使用﹑保管﹑维护
临时校准
入库
OQC 检验
包装
全检
目录
1.1进料检验流程 1.2 来料品质异常处理流程 1.3 首件检验流程 1.4 制程异常处理流程 1.5 不良品修理流程 1.6 出货检验流程 1.7 客戶投诉处理流程 1.8 不合格品處理流程 1.9 纠正措施实施流程 1.10 预防措施实施流程 1.11 监视和测量装置控制流程 1.12 产品标识流程 1.13 內部质量体系审核流程
3.修理员须在修理板上标识上自 已的标识
1.6 出货检验流程
生产部将产品 送检OQC
OQC清点数量及 确认状态标识
依成品检验标准及 抽样计划实施检验
IQC--IPQC--FQC--OQC检验控制流程图
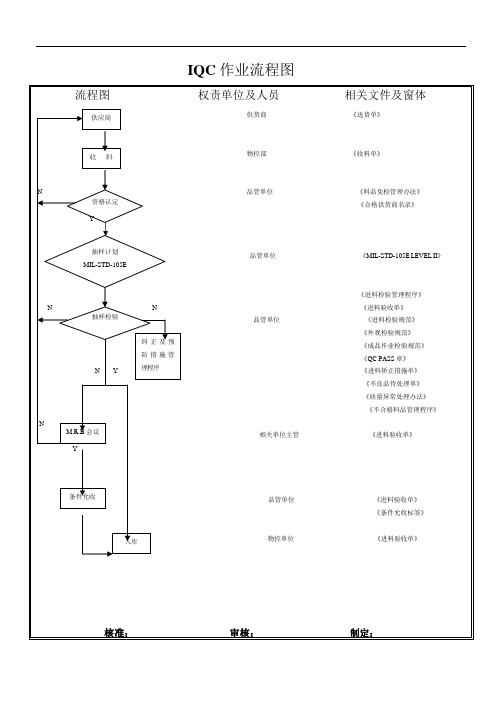
纠 正 及 预防 措 施 管
理程序
IQC 作业流程图
流程图
权责单位及人员
相关文件及窗体
供货商
《送货单》
物控部
《收料单》
N
品管单位
《料品免检管理办法》 资格认定
Y
《合格供货商名录》
抽样计划 MIL-STD-105E
品管单位 《MIL-STD-105E LEVEL II 》
《进料检验管理程序》
N
N
《进料验收单》 抽样检验
品管单位
《进料检验规范》 《外观检验规范》 《成品作业检验规范》 《QC PASS 章》 N
Y
《进料矫正措施单》 《不良品待处理单》 《质量异常处理办法》 《不合格料品管理程序》
N
相关单位主管
《进料验收单》
Y
品管单位
《进料验收单》 《条件允收标签》
物控单位 《进料验收单》
核准: 审核: 制定:
供应商
收
料
入库
M.R.B 会议 条件允收
核准:审核:制定:。
oqc工作流程

oqc工作流程一、概述。
oqc(Outgoing Quality Control)是产品出货前的最后一道质量控制环节,其主要任务是确保产品质量符合客户要求和标准,保证产品出货质量稳定可靠。
oqc工作流程是一个系统性的质量控制过程,包括抽样检验、测试、评定和记录等环节。
二、抽样检验。
1. 抽样计划制定。
在oqc工作流程中,首先需要制定抽样计划,确定每个批次产品的抽样数量和抽样标准。
抽样计划应根据产品类型、生产批次、客户要求等因素进行合理确定,确保抽样的代表性和可靠性。
2. 抽样方法选择。
根据抽样计划确定的抽样数量和标准,oqc工作流程中需要选择合适的抽样方法进行抽样。
常用的抽样方法包括随机抽样、分层抽样、整批抽样等,根据具体情况选择合适的抽样方法。
三、测试评定。
1. 外观检查。
在oqc工作流程中,对产品外观进行检查是必不可少的环节。
通过外观检查可以评定产品的表面质量,包括有无划痕、变色、变形等情况,确保产品外观符合客户要求和标准。
2. 功能测试。
除了外观检查,oqc工作流程中还需要进行功能测试,验证产品的性能和功能是否符合要求。
通过功能测试可以检测产品的工作状态、性能参数等,确保产品的功能稳定可靠。
3. 物理性能测试。
针对一些特殊产品,oqc工作流程中还需要进行物理性能测试,包括抗拉强度、耐磨性、耐腐蚀性等方面的测试,确保产品的物理性能符合标准要求。
四、记录和处理。
1. 检验记录。
oqc工作流程中需要对抽样检验和测试评定的结果进行记录,包括抽样数量、抽样方法、检查结果、测试数据等内容。
检验记录是质量控制的重要依据,可以为产品质量的稳定提供数据支持。
2. 不合格品处理。
在oqc工作流程中,如果发现产品不合格,需要及时进行处理。
不合格品处理包括分类、标识、隔离、返工、报废等环节,确保不合格产品不会流入市场,最大限度地保护客户利益和公司声誉。
五、总结。
oqc工作流程是产品质量控制的重要环节,通过抽样检验、测试评定、记录和处理等环节,可以有效保证产品质量的稳定可靠。
德森克IQC-IPQC-OQC品质作业管控流程图
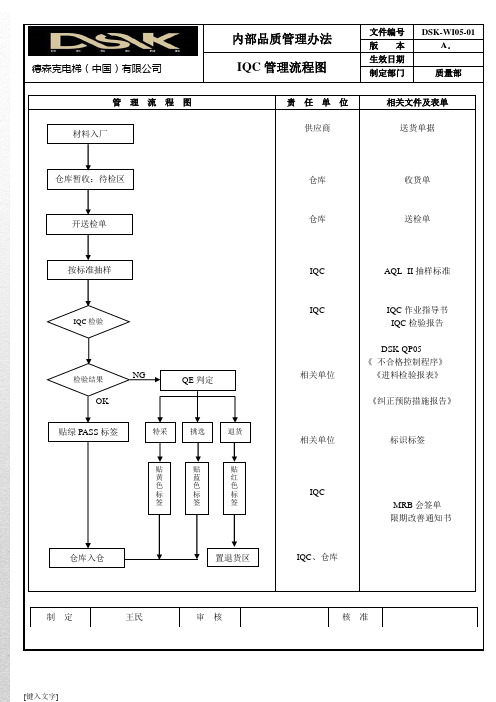
德森克电梯(中国)有限公司内部品质管理办法文件编号 DSK-WI05-01版 本 A . IQC 管理流程图生效日期 制定部门质量部管 理 流 程 图责 任 单 位相关文件及表单NGOK供应商仓库 仓库IQCIQC相关单位相关单位IQCIQC 、仓库送货单据收货单 送检单AQL- II 抽样标准IQC 作业指导书 IQC 检验报告DSK-QP05《 不合格控制程序》 《进料检验报表》《纠正预防措施报告》标识标签MRB 会签单 限期改善通知书制 定 王民 审 核 核 准材料入厂仓库暂收:待检区开送检单按标准抽样贴绿PASS 标签IQC 检验QE 判定特采挑选退货仓库入仓置退货区贴黄色标签 贴蓝色标签 贴红色标签检验结果德森克电梯(中国)有限公司内部品质管理办法文件编号 DSK-WI05-01版 本 A0 供应商品质控制管理流程图生效日期 制定部门质量部管 理 流 程 图责 任 单 位 相关文件及表单N NGOKNGOKIQC IPQCQE/IQC 工程师供应商IQC 工程师IQC 工程师IQC 工程师IQC 工程师来料检验规范书 IQC 来料不良检测报告 IPQC 巡拉作业指导书试验报告品质异常联络单改善处理报告品质异常联络单制 定 王民 审 核 核 准品质异常联络单IQC 检验中发现的来料异常 生产中发现的来料异常 组装试验中发现的来料异常跟进回复结果跟进改善结果结案提出处理对策采购部继续跟进供 应商回复德森克电梯(中国)有限公司内部品质管理办法文件编号 DSK-WI05-01版 本 A0 制程控制(IPQC )管理流程图生效日期 制定部门质量部管 理 流 程 图责 任 单 位 相关文件及表单NGOKOKNGNGOKNGOKOKNG NG OKOK生产部生产部IPQC 生产部 FQC相关责任部门相关责任部门质量部(IPQC )IPQC 、生产部、工程部生产部、工程部 质量部领料单 《 生产计划表、》 《作业指导书》IPQC 巡检报告/BOM《改善措施报告》QC 日报表纠正/预防措施通知单IPQC 巡拉检查报告纠正/预防措施报告首件检验报告制 定 王民 审 核 核 准生产领料生产投产生产、工程分析原因批量生产不良率较低改善IPQC 核对物料 FQC 检测确认责任部门写纠正/预防措施送首件确认IPQC 检验 结 案效果确认不良率较高德森克电梯(中国)有限公司内部品质管理办法文件编号 DSK-WI05-01版 本 A .0 品质保证(OQC)管理流程图生效日期 制定部门质量部管 理 流 程 图责 任 单 位相关文件及表单OKNGOKNGOK生产部生产部生产部 OQCOQC相关单位相关单位质量部生产部、仓库、质量部成品送检单AQL- II 抽样标准QA 检验报告返工报告《纠正/预防措施报告》《纠正/预防措施报告》成品入库单制 定 王民 审 核 核 准成品包装OK送成品待检区开送检单按标准抽样盖OQC PASS 印品质判定返工送仓库验收入库 写纠正/预防措施结 案 OQC 检验验证措施德森克电梯(中国)有限公司内部品质管理办法文件编号 DSK-WI05-01版 本 A .0 品质投诉处理管理流程图生效日期 制定部门质量部管 理 流 程 图责 任 单 位相关文件及表单则 否 是NG OK相关部门质量部质量部、生产工程或技术部相关部门相关部门责任单位 质量部质量部投诉报告投诉处理单投诉处理单会议记录《纠正/预防措施报告》再《纠正/预防措施报告》《纠正/预防措施报告》制 定 王民 审 核 核 准投诉内容/项目原因分析确定责任单位查核内容属实会议检讨写纠正/预防措施 验证措施 结 案德森克电梯(中国)有限公司品质工程控制(QE )管理流程图①生效日期 制定部门质量部管 理 流 程 图责 任 单 位 相关文件及表单 NGOKIQC技术部/工程部QE 相关部门相关部门IQC 仓库试验申请单试验报告MRB 会议MRB 会签单 限期改善通知书标识贴纸MRB 会签单制 定 王民 审 核 核 准相关试验相关部门决定让步接收 仓库入仓贴黄色标签 贴绿色标签 贴红色标签需做试验的产品 技术工程试验产品试验结果生产下单加工使用 退货置退货区德森克电梯(中国)有限公司品质工程控制(QE )管理流程图②生效日期 制定部门质量部管 理 流 程 图责 任 单 位 相关文件及表单 OK NGOK工程部、技术部QE QE质量部生产部、仓储部样品报告样品报告首件/样品检验报告试验报告样品评审单 首件/样品检验报告生产计划表制 定 王民 审 核 核 准相关试验设计样品 制作样品 试验结果通知相关部门生产量产。
OQC作业流程图
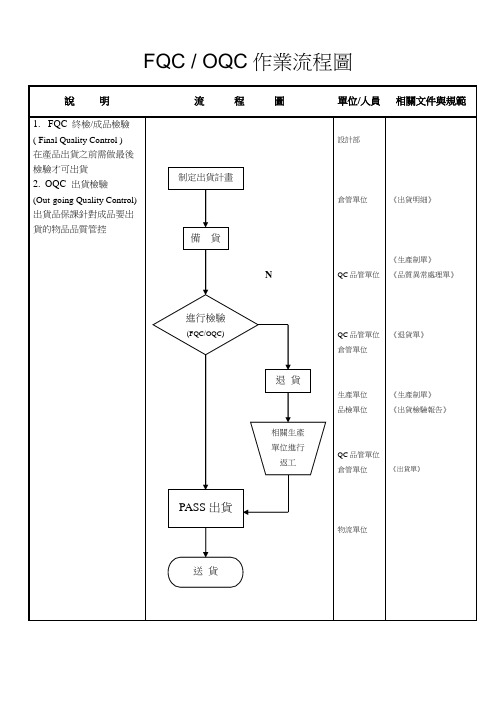
FQC / OQC作業流程圖製程巡檢作業辦法目的:落實品質意識在現場作業人員于制程過程中,實施檢驗或試驗以查證制程之合格性。
三〃範圍:凡本公司產品之各制程。
四、職責:生產部門:負責自製品自檢、送檢、重工、維修及入庫。
品保部門:負責自製品檢驗及記錄、標示。
五、內容:1、首件(產前樣/批版)、自主、巡迴檢驗:(1)品保部門IPQC人員在以下時段需做首件檢驗。
(1)每台機開始生產前開機需做首件檢驗。
(2)設計規格變更時需做首件檢驗。
(3)人員或材料更換時需做首件檢驗。
(2)生產部門作業人員應隨時注意生產產品品質狀況,並按照規定做好自主檢驗。
(3)品保部門IPQC人員應到現場做巡迴檢驗並做好記錄。
(4)品保部門檢驗管制程式,應按照規範和作業指導書之要求訂制(QC工程圖)。
(5)生產部門相關人員在制程中,發現不合格又無法矯正時,應及時停機報告主管,並通知品保部門,而品保部門應按照相關程式處理。
(6)品保部門IPQC人員按照實際檢驗情況記錄不合格品,並對制程式不良品作統計分析把結果回饋於相關部門,作糾正預防對策之依據。
(7)不合格品處理與標示(紅豆標&件投標):(1)、經判定為不合格品時,應在該批半成品貼上紅色圓點貼紙(故障貼紙)又稱紅豆,並加以區分,隨後將不合格批移至返工區或報廢區進行處理。
(2)、發生不合格品時,品保部門IPQC人員應填寫《IPQC服裝(巡廠)驗貨報告》加以記錄,並按照相關程序處理,並通知相關部門處理。
六〃使用表單:1、首件(制前樣/批版)吊卡2、特采申請單3、IPQC服裝(巡廠)驗貨報告4、返工\返修單5、報廢單6、制程異常備忘錄不合格品處理作業辦法一、目的:按照品質計畫及管制措施找出不合格品,採取各項管理及處理措施,並對不合格品進行分析,以防誤用。
二、範圍:供方之原材料、主輔料;廠內制程中之半成品、成品和庫存品;顧客之退貨品。
三、職責:生產、資材部門:負責不合格品標示、隔離及處理,必要時參與評審。
OQC作业流程图

流程
作業依據
作業內容
應用表單及標示
NG
無
1:OQC點數,放置OQC待檢區
2:OQC根據包裝核對
OQC交接卡
成品出貨檢驗規范出貨檢驗基准書
成品外觀檢驗標准
抽樣檢驗作業指導生產作業指導書
測試規格書
SPEC
包裝檢ቤተ መጻሕፍቲ ባይዱ標准
1:OQC¨依據批量取樣﹐先進行外觀:AQL:0.40﹔
2:尺寸量測AQL:0.40﹔
4:電氣檢測AQL:0.40﹔(電氣檢測之樣品需全數進行外觀檢驗)
5.包裝作業(所有產品需真空包裝,每小箱放兩袋干燥劑)﹐在封箱前產品應與外包裝進行核對OK后才入箱封箱。
6:封箱后﹐在外裝處蓋上PASS章及檢測印章及檢驗員代號,放入待入庫區。
OQC檢驗記錄表
出貨檢驗報告表
1.待入庫產品,由MRP人員依完成產品狀況輸入MRP并列印記錄與完成品送倉庫與倉庫負責人交接入庫。
(過AIR曲線圖﹑保証書﹑出貨測試報告表有客戶要求才附)
2.業務依客戶訂單列印出貨申請單通知出貨
生產成品入庫單
出貨申請單
出貨申請單
出貨注意事項
1.倉庫與OQC收到<出貨申請單>則准備出貨產品﹐OQC進行查核(對產品型號﹑數量﹑標識查核和核對)及填<出貨檢驗報告>資料﹐經主管審核后附貼在產品箱內。
2:<出貨查檢表>經主管審核后﹐將產品放行。
出貨檢驗報告表
出貨查檢表
质检过程流程图 (2)

IQC 控制流程图库房库房对送货的原资料进行报检IQC 依据《原资料查验规程》进行查验合格IQC判断入库放入合格地区库房表单: 1、进货查验记录单2、进料异样投诉单文件:《原资料查验规程》不合格IQC质检主管采买库房质检主管填写《进料异样投诉单》,并实时反应主管由质检部主管组织评审,依据实质状况,给出结果(特采、精选、退货)将质检开出的《进料异样投诉单》反应给供给商,要求改良对入库的不合格原资料隔绝,放入不合格地区跟进供给商对《进料异样投诉单》反应,并要求IQC 考证其改良成效(连续 3 批质量状况);PQC控制流程图操作者对自检合格的产品,填好流转卡依据《半成品查验规程》PQC进行查验,并做好记录合格PQC 在流转卡上署名、盖印;判断合格操作者将合格的产品齐整摆放在拟订地区填写《不合格点评审单》,并不合格实时反应主管;同时做好不合格表记PQC由质检部主管组织评审,要求责任部门进行原由剖析、纠正质检主管举措以及给出评审结果将质检判断不合格的产品放操作者置不合格地区PQC关于判断返工 / 返修的产品进行追踪复检,并做好记录文件:《半成品查验规程》表单: 1、不合格点评审单对《不合格点评审单》责任部质检主管门的原由剖析、纠正举措进行跟催;并要求 PQC对举措的有效性进行考证;2、半成品查验记录单表记:红色不合格表记(临时没有表记)流转卡只有同轴车间、数据车间在用;OQC控制流程图依据《成品查验规程》进OQC行查验,并做好记录合格将合格的产品齐整摆放在生产车间拟订地区不合格OQC质检主管生产车间OQC质检主管填写《不合格点评审单》,并实时反应主管;同时做好不合格表记由质检部主管组织评审,要求责任部门进行原由剖析、纠正举措以及给出评审结果将质检判断不合格的产品搁置不合格地区关于判断返工 / 返修的产品进行追踪复检,并做好记录对《不合格点评审单》责任部门的原由剖析、纠正举措进行跟催;并要求OQC 对举措的有效性进行考证;文件:《成品查验规程》表单: 1、不合格点评审单2、成品查验记录单。
QC工作流程图、生产流程图
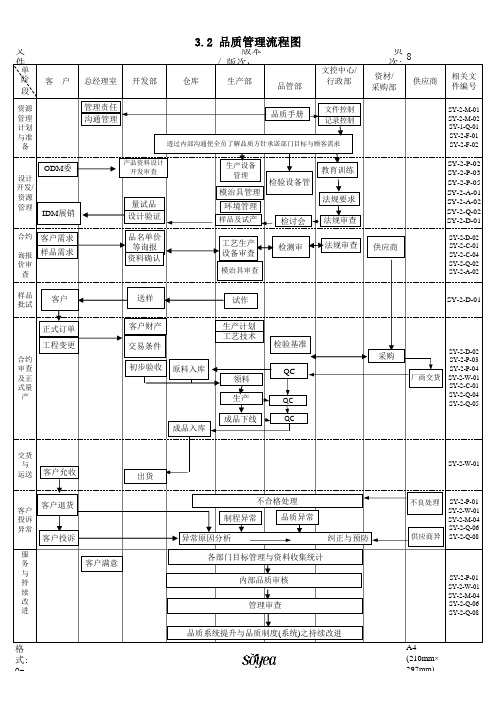
文件编号: SY-1-Q-01
单 阶 位 段
资源 管理 计划 与准 备
版本/ 版次:A/0
开发部 仓库 生产部 品管部 品质手册 文控中心/ 行政部
文件控制 记录控制
页
次:
资材/ 采购部
8
供应商 相关文 件编号
SY-2-M-01 SY-2-M-02 SY-1-Q-01 SY-2-F-01 SY-2-F-02
试作 生产计划 工艺技术
SY-2-D-01
正式订单
工程变更
合约 审查 及正 式量 产
检验基准 采购 QC QC
SY-2-D-02 SY-2-P-03 SY-2-P-04 SY-2-W-01 SY-2-C-01 SY-2-Q-04 SY-2-Q-05
成品下线 成品入库
交货 与 运送
SY-2-W-01
客户允收
出货
不合格处理
不良处理
SY-2-P-01 SY-2-W-01 SY-2-M-04 SY-2-Q-06 SY-2-Q-08
客户 投诉 异常 服 务 与 持 续 改 进
客户退货
制程异常 客户投诉
客户满意
品质异常 纠正与预防
供应商异
异常原因分析 各部门目标管理与资料收集统计 内部品质审核 管理审查
q00101法规要求教育训练品质手册客户承认正式订单客户允收客户退货试作不合格处理品质异常异常原因分析纠正与预防措施客户投诉客户需求检测审查法规审查检验基准qc工艺技术领料供应商管理管理审查品质系统提升与品质制度系统之持续改进记录控制文件控制检验设备管理工艺生产设备审查厂商交货内部品质审核标达成管理责任沟通管理样品需求品名单价承认工程变更客户满意客户财产交易条件审初步验收原料入库成品入库生产设备管理模治具审查环境管理生产计划生产成品下线qcqc采购不良处理供应商异常透过内部沟通使全员了解品质方针承诺部门目标与顾客需求模治具管理制程异常各部门目标管理与资料收集统计标达成出货odm委托资料确认产品资料设计开发审查idm展销与odm设计验证样品及试产检讨会法规审查ngngok车手把大扶手等前轮座后轮座等扶手轮子等车手把车手管大扶手前脚管前轮座后轮座轮轴扶手组装贴贴纸贴纸后脚管轮子组装轮轴等车手管前脚管后脚管等靠背太阳罩等车手贴纸说明书等领料平车车缝平车车缝搭dy平车缝制半成品上拉链各部位压明线成品包边锁眼打四合扣塑胶原材料外加五金件外加铝管外加缝制品外加印刷品外加包装纸箱外加检查仓库投入生产车手部分组装大扶手部分组装前轮座后轮座部分组装车手部分组装共它部分组装检查领料在线组装仓库检查包装仓库检查出货物料抽检首件确认各单位按单取料包装组合车架qc检查车架组合软件部分擦拭车台成品qc包装搬运车台不良品处理报废退回仓库合格不合格合格附表qc检验流程图生产二科检验标准的建立供应商交货仓库点收通知检验免检iqc检验标识入库完成品检验判定包装入库出货检验判定出货出货标识不合格原材料不良退货选用投入生产制成qc检验判定合格巡查日记不合格成品不合格在制品报废返工选用报废返工选用完成检验日记半成品
品质部职责和工作流程(组织架构图)
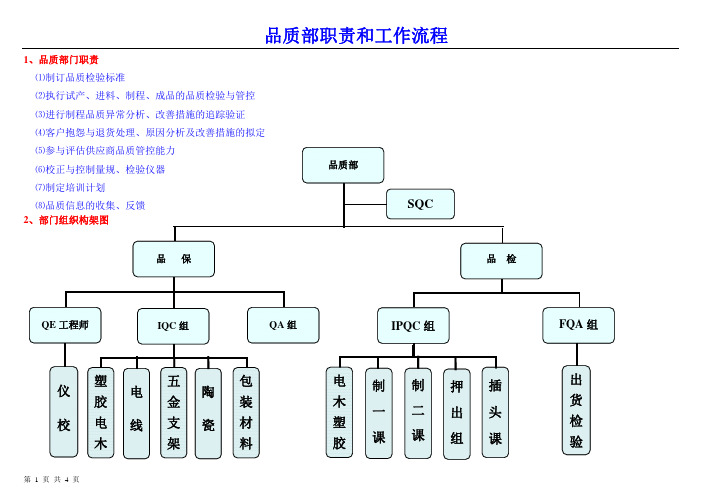
1、品质部门职责⑴制订品质检验标准⑵执行试产、进料、制程、成品的品质检验与管控⑶进行制程品质异常分析、改善措施的追踪验证⑷客户抱怨与退货处理、原因分析及改善措施的拟定⑸参与评估供应商品质管控能力⑹校正与控制量规、检验仪器⑺制定培训计划⑻品质信息的收集、反馈2、部门组织构架图仪校塑胶电木电线五金支架陶瓷包装材料品质部SQC品保QE工程师IQC组QA组品检FQA组出货检验IPQC组电木塑胶制一课制二课插头课押出组3.工作职责及能力要求职务工作范围、内容所需具备的能力备注品质主管1、对所属人员的教育培训2、执行状况的稽核3、协助制造部门建立不良产品的纠正和预防措施.中专以上学历,至少3年以上品质管理工作经验,熟悉品质管理运作程序。
熟练电脑操作. 对本公司产品有一定的了解。
有较强的识图能力,了解ISO体系。
IQC 1、免检供货商申请。
2、供应商异常回复追踪验证。
3、进料检验18周岁以上,高中以上文化程度,无色盲,会简单的量具使用及保养,具有一定的沟通、协调能力.有一年以上的工作经验,会使用.对本公司产品有一定的了解.有一定的识图能力.熟知进料检验的流程. 会电脑知识IPQC 1、现场首末件检验确认,巡检。
2、问题点的反馈,品质异常改善对策的追踪确认。
3、各工序半成品的检验。
18周岁以上,初中以上文化程度,会简单的量具使用及保养,熟悉抽检方法及对制程不良的处理.对本公司产品有一定的了解.有一定的识图能力,熟知制程检验的流程.OQC 出货产品的检验及填写检验报告18周岁以上,高中以上文化程度,会使用简单的量具,熟悉所有出货产品的品质要求. 对本公司产品有一定的了解有一定的识图能力.QA 1、出货稽查2、协助QE工作3、所有量具的使用及点检、保养、校正。
20周岁以上,中专以上文化程度,会使用现有所有量具仪器及其点检、保养、校验,会电脑知识. 对本公司产品有一定的了解。
有较强的识图能力.SQC 1、品质记录的统计(包括周统计、月统计、年统计的品质状况)2、品质所需物品的请购、领用、发放3、技术文件及管理文件的整理、索引保存4、文件及表单的打印及收发18周岁以上,高中以上文化程度,电脑操作熟练,日常报表及统计图的制作.对QC七大手法有相当的了解.QE 1、新产品开发阶段的品质策划、检验标准的制定 .2、客诉及退货的处理。
手机工厂制造实用QC工艺流程图

下载线
1
条码扫描器
1
19 IMEI号检查
• 检查手机里的IMEI与标贴是否一致 • 检查软件版本号
30
1
20 外观检查2
• 外观检查 • 贴3C标贴
3C标贴
镊子
1
30
1
21 FQC检查
• 外观检查 • 功能检查
60
2
包装工艺流程 (1)
项目
工位名称
作业内容
所需材料
充电检查
1
投入吸塑盒
2
扫描条码
3
检查充电器、电池外观及配套充电性能
全检 全检
SMT QC
机器程式、生 产报表
AOI检查不良 记录表
本工序返工
本工序返工 及信息反馈
测温器
抽检
SMT/ IPQC
生产报表
焊点质量、元件
20
炉后AOI 检查焊接效果 有无多件、少件、 作业指导书 AOI
错件
21
分板
将联片分为单片
避免撞件及线路 损伤
作业指导书
分板治具、尖 嘴钳
全检
QC
AOI检查不良 记录表
果检查
膏塌陷等印刷不
作业指导书 AOI
良现象
全检
SMT
锡膏印刷作业 记录表
对不良品进 行清洗并反 馈至印刷工 序
7
备料 上料至机器
规格、位置、方 向、状态、数量
作业指导书
电容表、万 用表
抽检 SMT 换料记录表
.退料、特采 或挑选使用
SMT生产工艺流程 (2)
流程图 工序名
作业方案
管理专案
使用文件
检修
抽检 IPQC
检验和试验控制程序(含流程图)
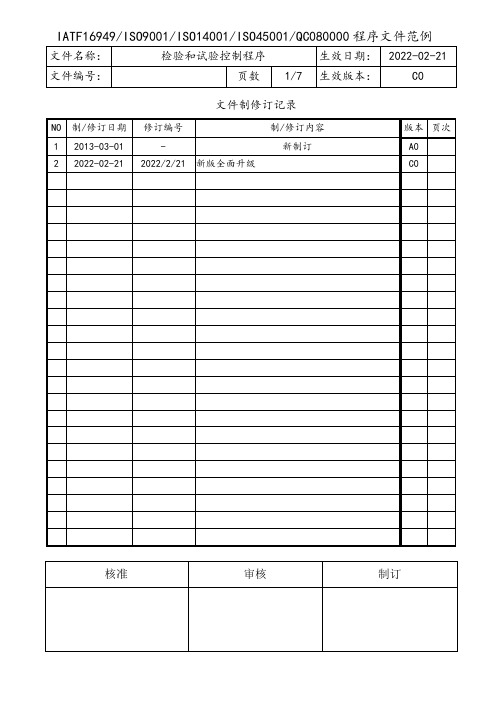
文件制修订记录1.0目的建立一个适合于对公司生产的所有产品(包括半成品与成品)及用于公司生产的所有原物料、辅料、零配件的检验与试验程序,规范公司的检验与试验作业,确保公司生产的产品质量/HSF达到客户所需的要求。
2.0范围:2.1适用于公司产品实现过程中所有物料包括原材料、半成品、成品的检验与试验。
2.2适用于公司制程管理值的验证作业。
3.0定义:3.1 IQC:Incoming Quality Control 指进料质量控制,即进料检验。
3.2 IPQC:In-process Quality Control 指生产过程中的质量控制,即制程检验,包含对产品以及生产过程中质量控制状态的检查与监视。
3.3 FQC:Final Quality Control制造过程最终检查验证,本公司指入库前的检验过程。
3.4 OQC:Outgoing Quality Control 指产品出货前由品质检验员对其进行的检验。
3.5 SQE:Supplier Quality Engineer 供应商质量工程师。
3.6 QE: Quality Engineer 质量工程师。
3.7自主检验:由操作员对本岗位材料、半成品、成品的检查,发现问题自己及时向直接上司汇报并作相应处理;同时也必须对过程质量(包括参数设定及是否按作业指导书要求作业等)的监控。
3.8首件检查:指生产者和技术员对生产调试阶段生产出来的产品(成品或半成品)进行确认并由品质检验员对其进行检验。
3.9巡检:指由品质检验员即IPQC人员对生产过程中的产品随机抽样检验或对制程过程状态(包括参数设置及是否按作业指导书要求作业等)的检查。
3.10抽检:指品质人员定期或定量对过程或项目进行抽样检查。
3.11半成品:指本公司还需要经下工序加工或装配后才能出货给客户的零组件。
3.12成品:指本公司可直接出货给客户的产品,对客户而言可能是半成品。
3.13原材料:指用于生产/加工成品的原料如塑胶粒、钢材等和组装产品用的零配件如螺丝、螺母、贴纸、辅料等,也包括包装产品用的包装材料如气泡袋、珍珠棉、PE袋、纸箱等。
塑胶五金件生产流程图 QC工程图

品保部(QA)
制程序》处理 储
存
2
储存
(store)
3
发料(store issue)
仓库 (warehouse )
射出
成型
4
射出成型(injection)
射出部(MFG)
毛边 处理
PIN 折弯 成型
电 镀
全检
5
毛边处理
(De-flash)
6
PIN折彎成型
Shaping pin
7 依《检验与测试
电镀 Plating
管理程序》&
《不合格品控制
程序》处理
8
全检100%
( inspection)
射出部(MFG)
冲压(MFG)
电镀厂(Electroplate Factory)
外观全检组 (100% inspect Dept.)
PIN
切脚
9
PIN切脚 (Cutting pin)
冲压(MFG)
塑胶五金件生产流程图
Process follow chart
品名:
制程責任:
页数:
1
料号: 跨功能小组成员 :
发行日期:
编制:
FMEA(REV)
1
工工序序名称(process name)
责任部门
进料
依《检验与测
检验
试管理程序》 & 《不合格品控
1
进料检验(incoming
material inspeciton)
装管
入库
检查
装管入库检查
包装部/仓库
10 (Packing and ship to
(Packiing /warehouse )
制程OQC工作流程图

每批次送检 每批次送检 每批P系统(http://10.0.0.6/nss10/) /OQA成品检验报告
OQA成品检验报告
OQA
1pcs/每批次送检
OQA成品检验报告
OK
检验 过程
NG
静电环或静电手套、手指 套、数显卡尺,厚薄规、 进行 检验 适配主机、电源线、 不合 过程 GPS101、直流电源、车 载多媒体、耳机、T卡、 格品 SIM卡、车充、无尘布、 管制, 去渍油、电脑、USB线. 要求
第1頁
每批次送检
OQA成品检验报告
OQA日常工作流程指引
流程
整改 NG 检验结
DATE:2012/03/11
VER:1.0
拟制
审核
批准
名称
工具
控制点
报表记录抽检箱号及重量
标准
频率
记录
OQA成品检验报告 OQA成品检验报告
检验 封箱机 结束
最终检验管理规范 包装操作规范/订单确认书/成品 检验结果再次确认、机器数量 检验规范/BOM/订单确认书 外箱状态卡上标示检验结果 AQL允许水准 机台送回暂放区 6S管理规范 通知产线领班检验结果 机型、工单、OQA检验结果 状态标示卡/OQA成品检验报告 确认 包装操作规范/订单确认书/成品 产品摆放栈板方式确认 检验规范 入库数量确认 成品入库单 状态标示卡/OQA成品检验报告/ 外观检验规范 签核成品入库单 品管签名处签名 记录产品入库履历表 产品入库明细记录表 BOM/包装操作规范/订单确认书/ 异常现象确认 成品检验规范 实际不良率确认 实际抽检不良数/总抽检数 通知生产管理人员现场确认不良 不良品批退单据签核 并签名,需会签至生产课长级以 由IPQC转单至QE进行主导处 上 由QE进行主导原因分析及长短期 理 对策制定,并判定责任部门 半小时内必须有可执行的短期对 跟进短期对策执行效果 策,无有效对策须向上反馈 确认返工数量、返工结果是否与 跟进返工结果 单据描述一致 同类异常是否二次发生,包括延 跟进长期对策时效性 伸机种 产品标签、OQA PASS标签
品控部工作流程图

知相关人员;
相关记录人员
重新发货:重新按要求发货;
《产品检验报告》 《送货单》 所有文件记录
出货:产品检验报告交予仓库部, 出货;
存档:把相关文件存档以备查。
不合格品控制流程
流程
不合格采购品
不合格半成品ຫໍສະໝຸດ 拒收不合格标识和隔离 信息反馈
不合格品评审 处置方式
返工
制定纠正预防措施
不合格成品 报废
叙述
负责人
通知有关人员:品管主管和生产主管决定不合 格半成品返工还是报废;
报废:对有问题的成品进行销毁,并对该次事 件提出合理的整改建议;
整改意见:相关人员对该次事件进行原因分 析,提出整改意见;
现场 QC 现场 QC 现场 QC 品管主管
品管主管/生产主 管
品管主管/生产主 管
生产部
《车间卫生检查记录》、 《车间巡检记录》《工器 具破损检查记录》等
抽检
知会采购部
合格 入仓 存档
品控部:生产过程质量控制工作流程表
流程
原料投 产
巡检
通知有关 人员
继续下一道 工序
成品
返工
报废
整改报告
检验 入仓
存档
叙述
负责人
记录/参考
原料投产:原料投入生产;
生产部
《原料投产单》
- 1、下载文档前请自行甄别文档内容的完整性,平台不提供额外的编辑、内容补充、找答案等附加服务。
- 2、"仅部分预览"的文档,不可在线预览部分如存在完整性等问题,可反馈申请退款(可完整预览的文档不适用该条件!)。
- 3、如文档侵犯您的权益,请联系客服反馈,我们会尽快为您处理(人工客服工作时间:9:00-18:30)。
流程 名称 工具 控制点
生产日期 送检线别 工单号/订单号 机型/颜色 客户 工单总批量 送检批量 检验资料 对应送检批次数量AQL确认 制程首件确认 工治具性能确认 工作台面6S 直流电源参数 丝印LOGO要求 外观
DATE:2012/03/11
VER:1.0
拟制
审核
批准
标准
每批次送检 每批次送检 每批次送检 每批次送检 每批次送检 每批次送检
ERP系统(http://10.0.0.6/nss10/) /OQA成品检验报告
OQA成品检验报告
OQA
1pcs/每批次送检
OQA成品检验报告
OK
检验 过程
NG
静电环或静电手套、手指 套、数显卡尺,厚薄规、 进行 检验 适配主机、电源线、 不合 过程 GPS101、直流电源、车 载多媒体、耳机、T卡、 格品 SIM卡、车充、无尘布、 管制, 去渍油、电脑、USB线. 要求
检验 首件 制作
NG
BOM/订单确认书/成品检验规范 GB/T2828-2003Ⅱ箭头向下 IPQC首件履历表 SIP 6S管理规范 SIP 成品检验规范/订单确认书 外观检验规范 包装操作规范/订单确认书/成品 包装方式确认 检验规范 包装操作规范/订单确认书/成品 包装标签确认 检验规范 附件核对 BOM/订单确认书/成品检验规范 BOM/订单确认书 开机LOGO确认 软件版本确认 BOM/订单确认书 基本功能确认 成品检验规范 收星值确认/雷达灵敏度确认成品检验规范 抽取样本箱数、机台数 丝印LOGO 成品外观要求、颜色 外观 GB/T2828-2003Ⅱ箭头向下 成品检验规范/订单确认书
每批次送检
外箱状态卡
OK
OK NG 入库 确认
入库 确认
每批次入库
产品入库明细记录表
OQA
异常 提报
异常 提报
每批次送检
OQA成品批退单
第2頁
责任 部门 即时 整改
OK
订单确认书 外观检验规范 包装操作规范/订单确认书/成品 包装方式确认 检验规范 包装操作规范/订单确认书/成品 包装标签确认 检验规范 附件核对 BOM/订单确认书/成品检验规范 BOM/订单确认书 开机LOGO确认 软件版本确认 BOM/订单确认书 基本功能确认 成品检验规范 收星值确认/雷达灵敏度确认成品检验规范/ECN/订单确认书
频率
记录
制造 部送
制造 部送 检
订单确认书/生产计划
每批次送检
送检单(编号:PD-007/B)
检验 前准 备
静电环或静电手套、手指 套、数显卡尺,厚薄规、 检验 适配主机、电源线、 前准 GPS101、直流电源、车 备 载多媒体、耳机、T卡、 SIM卡、车充、无尘布、 去渍油、电脑、USB线、 开箱刀片. 静电环或静电手套、手指 套、数显卡尺,厚薄规、 检验 适配主机、电源线、 首件 GPS101、直流电源、车 制作 载多媒体、耳机、T卡、 SIM卡、车充、无尘布、 去渍油、电脑、USB线.
第1頁
每批次送检
OQA成品检验报告
OQA日常工作流程指引
流程
整改 NG 检验结
DATE:2012/03/11
VER:1.0
拟制
审核
批准
名称
工具
控制点
报表记录抽检箱号及重量OQA成品检验报告 OQA成品检验报告
检验 封箱机 结束
最终检验管理规范 包装操作规范/订单确认书/成品 检验结果再次确认、机器数量 检验规范/BOM/订单确认书 外箱状态卡上标示检验结果 AQL允许水准 机台送回暂放区 6S管理规范 通知产线领班检验结果 机型、工单、OQA检验结果 状态标示卡/OQA成品检验报告 确认 包装操作规范/订单确认书/成品 产品摆放栈板方式确认 检验规范 入库数量确认 成品入库单 状态标示卡/OQA成品检验报告/ 外观检验规范 签核成品入库单 品管签名处签名 记录产品入库履历表 产品入库明细记录表 BOM/包装操作规范/订单确认书/ 异常现象确认 成品检验规范 实际不良率确认 实际抽检不良数/总抽检数 通知生产管理人员现场确认不良 不良品批退单据签核 并签名,需会签至生产课长级以 由IPQC转单至QE进行主导处 上 由QE进行主导原因分析及长短期 理 对策制定,并判定责任部门 半小时内必须有可执行的短期对 跟进短期对策执行效果 策,无有效对策须向上反馈 确认返工数量、返工结果是否与 跟进返工结果 单据描述一致 同类异常是否二次发生,包括延 跟进长期对策时效性 伸机种 产品标签、OQA PASS标签