高铁轨道板场建场方案
CRTSⅢ型先张轨道板预制场拟建方案

CRTSⅢ型轨道板场建场方案一.编制依据(1)国家相关法律、法规和铁道部相关规章制度;(2)《铁路大型临时工程和过渡工程设计暂行规定》(铁建设【2008】189号)。
(3)《铁路工程施工组织设计指南》(铁建设[2009]226号)(4)现场实地调查情况。
(5)现有的科学技术成果、工法成果、机械设备装备情况、施工技术与管理水平。
(6)业主三年工期指导性施工组织设计。
二.工程概况砀山轨道板场位置安徽省宿州市砀山县砀山经济开发区,场址位于线路相对里程:DK255+600 ,占地面积145亩。
场址紧邻国道G310,交通方便、场址周围水源、电源方便为我场生产和生活提供较便利的条件。
砀山轨道板场承担新建郑徐客运专线DK197+892-DK279+366共计81.47公里,轨道板数量:30000块。
施组工期:30000/(每天96块*每月25天)=13个月。
详见附图1:“郑徐客专线路平纵示意图”三.建场方案根据郑西公司下达施工工期2015年4月1日开始铺设轨道的工期,我场配备12个台座,96套模型。
假设30000块的总产量,生产时间1年,每月生产25天,每个台座每天生产8块,需要台座数量:N=∑÷Y÷M÷T÷n=30000÷1÷12÷25÷8=12.5个∑--板场承担任务量,假设3万块Y--生产年数,取1年M--每年生产月数,取12个月T---每月生产天数,取25天n--每个台座每天生产数量,取8块从以上计算可以看出,最佳台座数量为12个台座。
轨道板生产车间长度为300米,宽度为48米。
生产车间外部采用保温彩钢板,内部采用钢结构。
轨道板预制场共设置9个区域:板场由窖池生产区、侧板拆组区、钢筋加工区、混凝土制备区、材料存放区、养护区、轨道板存放区、辅助生产区、办公生活区九个部分组成。
详见附图2:“轨道板预制场总平面图”3.1 施工及生活用水轨道板场采用接通当地居民自来水供应生活用水,管路选用D95无缝钢管,按枝状排布,供应全场生产及生活用水。
高铁无碴轨道板预制、铺设施工方案

高铁无碴轨道板预制、铺设施工方案1、轨道板预制1.1轨道板预制厂轨道板在工厂内集中预制,采用专用预制模具,进行工厂化流水作业。
轨道板预制厂主要分为生产区、存板区和生活区,生产区主要包括轨道板预制车间、钢筋加工车间、搅拌站等,参见图1.1-1所示。
图1.1-1 轨道板预制场平面布臵示意图如图所示,预制车间设3条预制生产线,各设2台16m跨度10t桁吊,用于拆模、翻板、二次养生、钢筋骨架入模及混凝土浇筑等工作;钢筋加工车间设1条钢筋加工生产线,配备2台30m跨度5t桁吊,用于原材料和半成品等倒运,绑扎好的钢筋骨架采用专用小车横向移运至预制车间。
轨道板生产所需的混凝土由设在预制厂内的专用搅拌站供应,采用料斗接料,专用混凝土运输车运送至预制车间内。
搅拌站按15天用量考虑原材料储备。
轨道板采用自动温控设备配合2台2t/h的锅炉进行高温促进养护,达到强度拆模预施应力并检查后放入养生池进行二次养护。
存板区的轨道板吊装采用1台25t的汽车式起重机完成。
1.2轨道板预制工艺1.2.1模板制作安装轨道板模板制作精度要求高,应联合有能力的厂家定制具有足够的强度、刚度及稳定性的钢模,确保轨道板各部位结构尺寸的正确及预埋件位臵的准确,同时定做专用检测工具。
模板应通过专用可调节桁架安装在台座上,以保证模板的平整度。
模板首次拼装完成后进行检查,其制造精度为轨道板成品精度要求的1/2,允许偏差执行标准如表1.2.1-1所示。
表1.2.1-1 模板制造允许偏差模板应实行日常检查和定期检查,检查结果应记录在模板检查表中。
日常检查应在每一循环作业前进行,内容为模板外观;定期检查每月进行1次,内容包括高度和平整度。
1.2.2钢筋和预埋件制安使用前首先目视检查钢筋表面洁净、损伤、油渍、锈蚀等状态,并检查钢筋原材料试验报告及产品质量证明书。
钢筋的加工、装配以及检测方法报监理工程师审批后准予施工,钢筋应在常温下按设计图加工,弯曲须一次成形,不得进行回复操作。
2023年京沪高铁某特大桥轨道板铺设施工方案

2023年京沪高铁某特大桥轨道板铺设施工方案特大桥是京沪高铁的一项重要工程,轨道板铺设是特大桥施工中的关键环节。
本文将就2023年京沪高铁某特大桥轨道板铺设施工方案进行详细介绍。
1. 施工前准备工作在施工前,需要认真研究特大桥的结构和设计要求,确保施工方案符合相关标准和规范。
同时,还需进行现场勘测,了解施工现场的地质条件、土质情况等,为后续施工提供可靠的数据支持。
2. 材料准备轨道板是铺设在特大桥上的关键构件,因此材料的选择和准备十分重要。
应选用优质的钢材作为轨道板的基材,并进行加工处理,以确保其质量和牢固性。
3. 施工方案确定根据特大桥的具体情况,制定轨道板铺设的施工方案。
首先确定轨道板的铺设位置和数量,然后确定合适的铺设方法和顺序。
在施工方案中,还需考虑到施工期间的安全措施和操作细节,以确保施工的顺利进行。
4. 施工机械准备为了提高施工效率和质量,应选用适当的施工机械。
施工机械的选择应根据特大桥的情况确定,同时还需考虑到施工现场的环境和条件。
例如,可选用铺轨机、起重机等机械设备,以提高轨道板的铺设效率和准确性。
5. 施工过程控制在轨道板铺设的施工过程中,应进行严格的施工过程控制。
首先,根据施工方案确定好每个环节的施工时间和顺序,合理安排施工人员的工作任务。
其次,在施工过程中,要加强对施工现场的管控,确保施工的安全和有序进行。
最后,在施工结束后,应及时对施工质量进行检查和验收,确保铺设的轨道板符合相关要求。
6. 施工安全措施在特大桥的轨道板铺设施工中,施工安全是十分重要的。
施工前,应组织施工人员进行安全培训,提高他们的安全意识和操作技能。
施工过程中,要建立健全的安全管理制度,加强对施工现场的巡查和检查,及时排除安全隐患。
同时,要配备必要的安全设施和防护措施,确保施工人员的人身安全。
综上所述,2023年京沪高铁某特大桥轨道板铺设施工方案包括施工前准备工作、材料准备、施工方案确定、施工机械准备、施工过程控制和施工安全措施。
京沪高铁某特大桥轨道板铺设施工方案
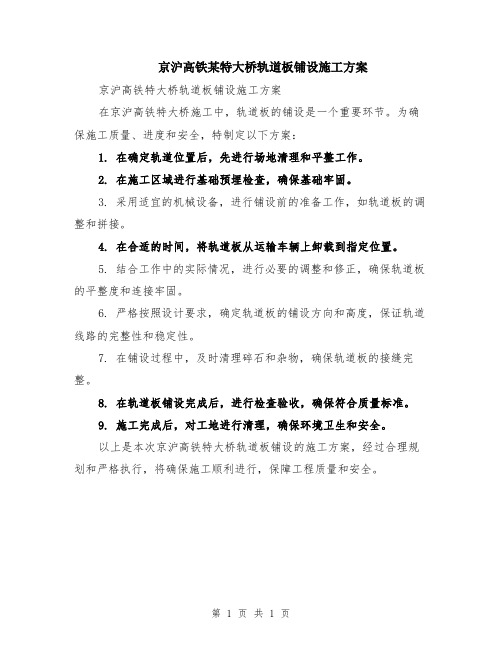
京沪高铁某特大桥轨道板铺设施工方案京沪高铁特大桥轨道板铺设施工方案
在京沪高铁特大桥施工中,轨道板的铺设是一个重要环节。
为确保施工质量、进度和安全,特制定以下方案:
1. 在确定轨道位置后,先进行场地清理和平整工作。
2. 在施工区域进行基础预埋检查,确保基础牢固。
3. 采用适宜的机械设备,进行铺设前的准备工作,如轨道板的调整和拼接。
4. 在合适的时间,将轨道板从运输车辆上卸载到指定位置。
5. 结合工作中的实际情况,进行必要的调整和修正,确保轨道板的平整度和连接牢固。
6. 严格按照设计要求,确定轨道板的铺设方向和高度,保证轨道线路的完整性和稳定性。
7. 在铺设过程中,及时清理碎石和杂物,确保轨道板的接缝完整。
8. 在轨道板铺设完成后,进行检查验收,确保符合质量标准。
9. 施工完成后,对工地进行清理,确保环境卫生和安全。
以上是本次京沪高铁特大桥轨道板铺设的施工方案,经过合理规划和严格执行,将确保施工顺利进行,保障工程质量和安全。
第 1 页共 1 页。
【精品】轨道板场建场总体设计

一、概述石武铁路客运专线(河北段)北起河北省省会石家庄市,南至河北与河南省界,沿线经过石家庄市、邢台市、邯郸市,线路全长202。
683km。
石武客运专线是京广客运专线的组成部分,并与京石、武广客运专线贯通形成北京至广州客运专线,连接了华北、华中、华南等广大地区,区位优势明显、辐射范围广阔,是纵贯我国中部的南北大动脉。
石武铁路客运专线(河北段)SZ-3设计无砟轨道为单线138。
51 km,铺设轨道板21331块。
我部为中铁四局SZ-3项目经理部下设的轨道板场分部,负责我局管段内的所有CRTSⅡ型标准轨道板预制生产。
轨道板制造采用易于保证产品质量的工厂化生产管理模式,配置机械化、自动化程度高的成套装备.轨道板预制主要由毛坯板生产和承轨面磨削组成,毛坯板生产采用先张法长线台座生产工艺,承轨面磨削引入机械加工理念,采用专用高精度数控磨床。
二、建厂设计内容1、根据总体要求和工程特点确定厂址;2、根据工程工期确定生产能力;3、根据原材料及轨道板总体运输规划进行物流设计;4、根据工艺原理,科学、经济地实现生产工艺;5、根据工艺要求,合理配置装备及相关设施;6、各功能区设计。
三、轨道板场总体设计3。
1厂址选择轨道板场建场具有占地量大、交通条件要求高等特点。
因此板场成立后立即着手开展板场选址工作.通过深入调查了解,初步选定位于成安县商城镇开发园区临近S315省道北侧的一片商业用地。
该地块位于新建石武铁路DK460处,东西长529m,南北宽约328m,紧邻315省道、京珠高速公路、京广铁路、邯济铁路及建设中的石武铁路,园区内配套交通完善,较适合作为轨道板场建场用地.因此选定该地块为建厂用地。
1、交通运输条件铁路:既有京广铁路与本线走向大致平行,可作为施工运输的铁路主干道。
另有多条铁路与既有京广铁路相连,构成了利用铁路运输工程材料和设备的运输网络,可作为远距离运输的主要方式。
公路:本工程所经地区公路基础设施比较完善,近年来公路的发展尤其迅猛。
轨道板预制场施工组织设计

一、轨道板预制场建设1、轨道板预制场建场原则根据混凝土轨道板轨道的生产工艺特性,产品及原材料的储存、运输要求。
确定无碴轨道混凝土轨道板的供应范围不宜超过60公里(双线),合120公里单线。
120公里单线需要混凝土轨道板约24000块左右,轨道板生产工期计划为14个月,产量1块/天·模,日生产70块,模型投入量70套左右。
在60km中间地段适宜位置建立轨道板预制场,尽量利用永久征地。
轨道板预制场提前生产储存轨道板,再用汽车运输到施工作业面。
预制场主要承担轨道板的生产、运输任务。
2、轨道板场建设及生产工期安排⑴建场计划:预制场从基础建设、到设备安装正常运行约需6个月,可正式投入生产。
⑵生产计划:轨道板生产工期共14个月,铺设工期6个月,预制场先生产10个月,铺设阶段同步生产4个月,以保证轨道板供应的连续性。
3、轨道板预制场平面布置图预制场占地总面积约116亩,长485m,宽160m,划分为生产区、生活区两大区域,两个区均实行封闭管理。
生产区按施工工艺流程划分八个区,原材料存放区、钢筋加工区、钢筋绑扎区、组装灌注蒸养区、混凝土拌合区、临时存放区、预应力施加区、成品检查存放区。
各工序的物流衔接采用龙门吊、专用运输车、汽车吊等机械完成,各工区根据自身特点配备专用的生产加工机具。
根据生产办公室、锅炉房、配电室、物资仓库、试验室等。
生活区按其功能,设置住宿区、食堂、职工活动中心及卫生所等。
根据预应力轨道板的形式特点(后张双向预应力)及各类轨道板的共性(扣件预埋套管位置相同),采用台座法生产,利于预应力轨道板及普通轨道板模型的部分共用。
生产线布置重点考虑各作业区的独立作业及相互配合,物流畅通,工序衔接合理,施工干扰小的原则布设。
根据轨道板的外形特点、生产工艺、质量要求,模型采用高精度、高刚度钢模型,框架式轨道板与预应力轨道板底模共用,局部进行修改,内模设计为伸缩式内模。
生产线划分为八个区,原材料存放区、钢筋加工区、钢筋绑扎区、组装灌注蒸养区、混凝土拌合区、临时存放区、预应力施加区、成品检查存放区。
高速铁路轨道板场施工组织设计
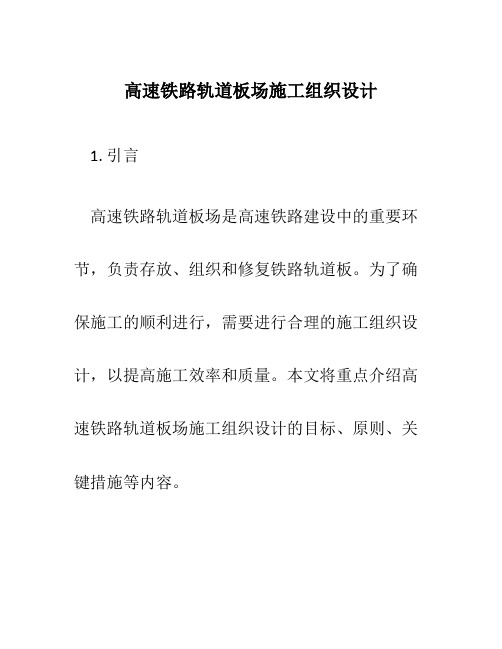
高速铁路轨道板场施工组织设计1. 引言高速铁路轨道板场是高速铁路建设中的重要环节,负责存放、组织和修复铁路轨道板。
为了确保施工的顺利进行,需要进行合理的施工组织设计,以提高施工效率和质量。
本文将重点介绍高速铁路轨道板场施工组织设计的目标、原则、关键措施等内容。
2. 目标高速铁路轨道板场施工组织设计的目标是确保轨道板的安全、高效、优质施工。
具体目标包括:•提高施工效率:通过合理的工程流程和组织方式,提高施工速度,缩短施工周期。
•保证施工质量:严格按照技术规范和施工标准进行施工,确保轨道板的质量符合要求。
•保障施工安全:制定安全操作规程,培训操作人员,确保施工过程中没有安全事故发生。
3. 原则高速铁路轨道板场施工组织设计应遵循以下原则:3.1 系统性原则施工组织设计需要考虑轨道板场整体的施工流程和流程之间的衔接,确保各个环节有机结合,形成一个高效、协调的施工系统。
施工组织设计应基于科学分析和评估,结合实际情况确定施工时序、资源配置和工作方式等。
设计过程中应充分考虑地质、气候、工期等因素,确保设计方案的可行性和科学性。
3.3 经济性原则施工组织设计应充分考虑资源利用效率和成本控制,实现最佳经济效益。
通过合理的施工流程和资源配置,降低施工成本,提高施工效率。
施工组织设计应确保施工人员的安全。
设计方案应考虑施工现场的安全要求,制定相应的安全操作规程,加强安全教育和培训,落实安全生产责任。
4. 关键措施为了实现高速铁路轨道板场施工组织设计的目标,需要采取一系列关键措施:4.1 工程流程设计根据施工任务和要求,确定施工流程,包括轨道板的调运、存放、组织施工和修复等环节。
为每个环节制定详细的工作方案和工序,明确各项工作的责任和时限。
4.2 人员培训和管理对轨道板场操作人员进行专业培训,提高操作技能和安全意识。
建立健全的人员管理制度,明确职责和权限,确保施工过程中的人员配备和配置。
4.3 资源配置合理配置施工所需的人力、物力和财力资源,确保施工过程中资源的充足和有效利用。
轨道板场建设方案(修改)

轨道板场建设⽅案(修改)⽬录⼀、板场概况 (1)⼆、总体施⼯设计 (2)2.1⽣产能⼒ (2)2.2 ⽣产车间 (2)2.3混凝⼟拌合站 (3)2.4主要⽣产流程设计 (3)三、场地总体规划 (8)3.1总平⾯布置 (8)3.2布局注意事项 (8)四、施⼯计划 (9)4.1总⼯期及开竣⼯⽇期 (9)4.2阶段性计划 (10)五、施⼯顺序 (10)六、施⼯⽅法 (11)6.1施⼯总平⾯布置 (11)6.1.1轨道板场场地布置原则 (11)6.1.2轨道板场布置说明 (12)6.2⼚房布置 (12)6.2.1 ⽣产车间施⼯ (13)6.2.2 打磨车间施⼯ (14)6.2.3 龙门吊基础 (14)6.2.4存板台施⼯ (14)6.2.5场内道路的布置 (14)6.2.6搅拌站施⼯ (15)6.2.7钢筋加⼯⼚房 (15)6.3其它临时设施布置 (15)6.3.1施⼯供电 (15)6.3.2施⼯通讯 (15)6.3.3施⼯供⽔ (16)6.3.4养⽣设施 (16)6.3.5⽣产、⽣活及办公⽤房 (16)6.3.6环保、卫⽣及⽂明施⼯设施 (16)6.3.7 施⼯围蔽 (17)七、⼈员配备 (17)⼋、设备需求 (18)九、重点⼯作项⽬ (19)⼗、附件 (20)⼀、板场概况本轨道板场位于⼭东省德州市齐河县⼤黄乡王邱村,与齐河制梁场毗邻,连通京沪⾼速铁路施⼯便道和316省道。
位于线路⾥程DK378+000处,采取板场与梁场结合建设的模式,板场总征地⾯积120亩,前期在梁场建设时已考虑后期板场建设的情况。
板场分成⼚房内作业的钢筋加⼯区、⽑坯板预制区、成品板打磨装配区、⼚房外的存板区、混凝⼟拌合站五⼤区,与梁场主要共⽤⽣活区、原材料存放场地、试验室、进场道路、⽔井和锅炉等六项。
具体情况见附图:齐河轨道板场平⾯布置图。
根据京沪总指确定的最新“京沪⾼铁Ⅱ型轨道板场设置⽅案”,中铁⼀局齐河轨道板场“需要量”为16000块。
轨道板生产厂的设计

CRTSⅡ型轨道板厂建厂方案及工装设备介绍1 概述轨道板制造采用易于保证产品质量的工厂化生产管理模式,配置机械化、自动化程度高的成套装备。
轨道板预制主要由毛坯板生产和承轨面磨削组成,毛坯板生产采用先张法长线台座生产工艺,承轨面磨削引入机加工理念,采用专用高精度数控磨床。
2 建厂设计内容根据总体要求和工程特点确定厂址;根据工程工期确定生产能力及相关技术经济指标;根据原材料及轨道板总体运输规划进行物流设计;根据工艺原理,科学经济实现生产工艺;根据工艺要求,合理配置装备及相关设施;各功能区设计。
3 建厂设计3.1 厂址选择根据运输条件,原材料条件,场地条件等方面的综合评估,确定了轨道板厂厂址3.2 产品结构基本型式轨道板的外形尺寸为6450mm×2550mm×200mm,为预应力混凝土结构,横向施加预应力(先张)、纵向无预应力。
每块用混凝土3.45m3。
预制轨道板采用先张法长线台座工艺生产,混凝土强度等级为C60。
轨道板的横向配有60根10mm预应力钢筋,纵向配有6根20mm精轧螺纹钢筋,板与板之间通过精轧螺纹钢筋进行了传力连接。
为防止轨道扣件处混凝土出现裂缝,在每个承轨台间都预设了预裂缝。
轨道扣件安装在承轨台上。
承轨台精确的几何尺寸是用数控磨床磨削加工出来的,加工精度为0.1mm。
轨道板连接示意图见下图645025503.3 产品工艺流程工艺流程图见下图标准轨道板工艺流程图3.4 设计能力根据工程量及施工工期以及轨道板生产的特点,轨道板生产在厂房内集中预制,实行工厂化施工管理;毛坯板采用先张法长线台座法生产,设三条生产线,每条生产线作业周期为24小时(其中作业时间8h,养护时间约16h),生产能力27块;采用三班作业制,每天生产半成品轨道板81块;成品板生产线以数控磨床为中心,亦采用三班作业制,每班打磨成品轨道板24-30块,每天打磨70-90块,存板能力约8000块(现有轨道板厂)。
广珠城际轨道江门轨道板厂建场方案

中铁二局广珠城际轨道交通工程指挥部第三项目部江门轨道板场建设方案一、工程概况广珠城际轨道交通工程线路位于珠江三角冲积平原区,地貌单元属河流冲积平原,地势平坦开阔。
主线自新广州站引出,经顺德、中山至珠海拱北,线路全长115.625正线公里;支线自小缆站引出,经中山古镇至江门新会站,支线全长26.609正线公里。
本项目贯通线总长(主线+支线)为142.234正线公里。
轨道板场主要负责ZH-2全标段(主线DK43+934.47-DK62+822.49;小缆至江门支线JDK45+233.09-JDK71+265.48)轨道板预制施工任务。
江门轨道板场是江门制梁场整体配套的一部份,位于JDK50+800~JDK51+100支线右侧,此处位于东升站特大桥。
轨道板场位于江门市江海区五邑路边上,交通较便利。
二、设计依据1、广珠高速铁路无碴轨道施工调研报告。
2、广珠城际轨道交通工程招、投标文件,补遗书等。
3、广珠项目部综合性施工组织设计。
4、国家现行及部颁标准、规范及规定。
三、设计说明根据目前设计院的初步意向,轨道板型为日本的非预应力框架型结构,轨道板宽2.4m、高0.19m;鉴于目前图纸迟迟不到位,我场按此种轨道板的生产需求布置场地,并留有充分的余地以应付图纸变动和其它不可遇见的因素;整个设计以统筹安排、服从全局,保证轨道板的均衡生产,全方位考虑制板的总体施工进度,以人为本,综合考虑施工环境的优越性;注重环保,不断引进新技术、新材料、新工艺、新设备等为原则。
全线轨道板预制折合单线为90.927Km,预计各种板型2万多块,混凝土4万多方;结合ZH-2标的整个施工安排,我场计划8月中旬投入生产,预制工期12个月,日生产轨道板60块,月产轨道板1800块。
四、生产生活设施规划轨道板场部位于五邑路中铁二局广珠项目经理部后侧,占地60亩,其中生活办公区占地12亩。
生活区由经理部办公区、板场办公区、试验楼、职工宿舍、食堂、澡堂、娱乐室等公共设施组成。
轨道板建厂方案

沪宁城际铁路工程站前VII标轨道板厂建厂案一、编制依据1.沪宁城际VII标投标文件;2.铁路工程建设通用参考图《CRTS I型板式无砟轨道》通线(2008)2301第一册、第二册3.《铁路桥涵施工规》(TB10203-2002);4.《客运专线无砟轨道铁路工程施工质量验收暂行标准》(铁建设[2007]85号);5.《铁路混凝土工程施工质量验收补充标准》(铁建设[2005]160号);6.《客运专线综合接地技术实施办法(暂行)》(铁集成[2006]220好);7.《铁路工程施工安全技术规程》(上下两册)(TB10401-2003);8.《客运专线无砟轨道铁路工程测量技术暂规定》(铁建设[2006]189号);9.《客运专线铁路CRTS I型板式无砟轨道混凝土轨道板暂行技术条件》(科技基[2008]74号);10.、铁道部、上海市、省有关安全、环境保护、水土保持的法律法规。
二、板厂布置依据1、板厂建设本着“经济实用、相对独立、便于管理、便施工、安全环保”的原则进行科学合理的规划布置,同时按照“工厂化生产、流水线施工、标准化作业”的高标准进行建设,兼顾考虑临时征地在施工任务完成后易于恢复。
2、板厂布置紧凑合理,布局不仅要按制板施工流程进行设计,还要兼顾移板设备的安装和线路走向。
3、根据轨道板预制期、产量和轨道板安装工期、预制工艺流程、场转运式、物流线路、临时工程类型和数量要求布置。
三、工程概况及工程数量沪宁城际铁路站前Ⅶ标段正线起点DK247+298.55,终点DK284+880;虹桥联络线起点HQXDK0+000,终点HQXDK15+800,标段正线总长53.382km,估算总生产量按下式进行:53.382×2(双线)×208=22207块,准确数量应根据下部结构形式配置。
四、板厂的建设设计1、预制工期:2009.4.1-2010.1.15,有效预制工作日9.5月*25天=237.5天平均日预制量:53.382×2×208/237.5=93.5块投入模板套数:93.5/1.3=72套2、轨道板预制区:将72个台座分为6个车间,呈2×3列布置,台座间预留2m工作空间,车间沿桁吊行走向预留3.5m宽通道,台座长5m、宽2.4m。
2024年京沪高铁某特大桥轨道板铺设施工方案

2024年京沪高铁某特大桥轨道板铺设施工方案一、项目背景2024年京沪高铁是我国重大的高速铁路项目,其中某特大桥是其重要部分之一。
特大桥的轨道板铺设是该项目中的关键环节,为确保施工质量和工期进度,我们进行了详细的施工方案规划。
二、施工准备1. 设立专门的施工组织机构,包括项目经理、技术负责人、安全负责人等。
2. 对施工区域进行勘测,确保施工平面和垂直线的准确性。
3. 选购合适的施工材料和设备,包括轨道板、动力机械、运输设备等。
4. 制定详细的施工工序和计划,确保施工顺利进行。
三、施工步骤1. 预处理:清理工地并进行整平,确保施工基础的牢固和平整。
2. 尺寸检查:对特大桥上的轨道板进行尺寸检查,确保与设计要求一致。
3. 预埋道床:在特大桥上适当位置挖槽,然后将轨道板的预埋道床安装到槽中,固定好。
4. 轨道板铺设:将轨道板从运输设备上卸下,并依照设计标高和线形进行精确对位,然后使用动力机械将轨道板一块一块铺设到预埋道床上。
5. 固定轨道板:使用专用的工具对铺设好的轨道板进行固定,确保其稳定性和平整度。
6. 安装附件:根据设计要求,对轨道板上的附件进行安装,例如轨道连接件、翻板等。
7. 精调工序:调整轨道板的水平度和线形,保证施工质量符合设计要求。
8. 轨面修整:使用工具对轨道板表面进行修整,确保平整度和光洁度。
9. 检验验收:对施工质量进行全面检查,确保达到设计要求后进行验收。
四、施工安全措施1. 建立安全管理责任制度,确保施工过程中的安全责任到位。
2. 强化施工现场的安全教育和培训,确保施工人员具备相关安全知识和技能。
3. 制定详细的施工安全操作规程,明确各个工序的安全要求和防护措施。
4. 检查施工设备和工具的安全状况,确保其符合安全标准和规范。
5. 加强施工现场的巡视和监督,及时发现和处理安全隐患。
6. 做好施工现场的安全警示标识,提醒施工人员注意安全。
五、施工质量控制1. 对施工材料进行检验,确保其符合相关标准和规范。
轨道板建厂方案

沪宁城际铁路工程站前VII标轨道板厂建厂案一、编制依据1.沪宁城际VII标投标文件;2.铁路工程建设通用参考图《CRTS I型板式无砟轨道》通线(2008)2301第一册、第二册3.《铁路桥涵施工规》(TB10203-2002);4.《客运专线无砟轨道铁路工程施工质量验收暂行标准》(铁建设[2007]85号);5.《铁路混凝土工程施工质量验收补充标准》(铁建设[2005]160号);6.《客运专线综合接地技术实施办法(暂行)》(铁集成[2006]220好);7.《铁路工程施工安全技术规程》(上下两册)(TB10401-2003);8.《客运专线无砟轨道铁路工程测量技术暂规定》(铁建设[2006]189号);9.《客运专线铁路CRTS I型板式无砟轨道混凝土轨道板暂行技术条件》(科技基[2008]74号);10.、铁道部、上海市、省有关安全、环境保护、水土保持的法律法规。
二、板厂布置依据1、板厂建设本着“经济实用、相对独立、便于管理、便施工、安全环保”的原则进行科学合理的规划布置,同时按照“工厂化生产、流水线施工、标准化作业”的高标准进行建设,兼顾考虑临时征地在施工任务完成后易于恢复。
2、板厂布置紧凑合理,布局不仅要按制板施工流程进行设计,还要兼顾移板设备的安装和线路走向。
3、根据轨道板预制期、产量和轨道板安装工期、预制工艺流程、场转运式、物流线路、临时工程类型和数量要求布置。
三、工程概况及工程数量沪宁城际铁路站前Ⅶ标段正线起点DK247+298.55,终点DK284+880;虹桥联络线起点HQXDK0+000,终点HQXDK15+800,标段正线总长53.382km,估算总生产量按下式进行:53.382×2(双线)×208=22207块,准确数量应根据下部结构形式配置。
四、板厂的建设设计1、预制工期:2009.4.1-2010.1.15,有效预制工作日9.5月*25天=237.5天平均日预制量:53.382×2×208/237.5=93.5块投入模板套数:93.5/1.3=72套2、轨道板预制区:将72个台座分为6个车间,呈2×3列布置,台座间预留2m工作空间,车间沿桁吊行走向预留3.5m宽通道,台座长5m、宽2.4m。
京沪CRTSⅡ型轨道板建场方案

新建京沪高速铁路土建工程六标段八工区苏州板场CRTSⅡ型板建厂方案中国交通建设股份有限公司京沪高速铁路土建工程六标段八工区苏州板场二〇〇八年十一月目录一、编制依据 (1)二、工程概况 (1)三、工期安排 (1)3.1开竣工日期 (1)3.2 阶段工期安排 (2)四、板场的建设设计 (2)4.1板场的平面布置 (2)4.2生产能力的设计 (3)4.3车间规模结构 (3)4.4预制生产线的结构布置 (4)4.5与生产线有关的供热、供气系统 (4)4.6 主要设备工装及物流顺序平面布置 (4)五、主要功能区及物流组织 (4)5.1钢筋加工区 (4)5.2混凝土搅拌及砂石料存放区 (5)5.3轨道板生产区 (5)5.4毛坯板临时存放区 (6)5.5轨道板打磨装配区 (6)5.6轨道板存放区 (7)5.7辅助生产区 (7)5.8办公生活区 (8)六、主要工艺装备进场计划 (8)一、编制依据六标段八工区轨道板场按照CRTSⅡ型板式无砟轨道进行板场建设规划,依据以下有关文件,规范、规程以及工程实际特点进行编制。
1、《新建时速300-350公里客运专线铁路设计暂行规定》(铁建设[2007]47号);2、《客运专线CRTSⅡ型板式无砟轨道混凝土轨道板暂行技术条件》(科技基[2008]74号)3、《铁路混凝土工程施工技术指南》(TZ213-2005);4、《铁路混凝土与砌体工程施工规范》(TB10210-2001);5、《客运专线铁路桥涵工程施工质量验收暂行标准》(铁建设[2005]160号);6、《铁路混凝土工程施工质量验收补充标准》(铁建设[2005]160号);7、《京沪高速铁路Ⅱ型轨道板场设置方案》。
二、工程概况苏州板场负责京沪高速铁DK1150+910~DK1221+421范围内CRTSⅡ型轨道板预制施工,所属地区为常州、无锡、苏州三个地区,正线全长为71.5km,预制CRTSⅡ型轨道板21958块。
根据《京沪高速铁路CRTSⅡ型轨道板场设置方案》要求,苏州板场选在苏州相城区黄埭镇工业园区的嘉乐威公司,在原有的厂房和空地的基础上改建成CRTSⅡ型轨道板场,该场地占地约111亩。
轨道板工程施工方案、施工方法、施工工艺及技术措施

轨道板工程施工方案、施工方法、施工工艺及技术措施1轨道板工程概述本标段无碴轨道344.8Km,共需轨道板143667块,轨道板采用工厂化施工,本标段共设置6处轨道板预制场。
无碴轨道区间轨道板采用Ⅰ型板式,岔区采用长枕埋入式。
2轨道板工程施工方案2.1轨道板工程施工组织方案本标段共设6处轨道板预制场。
根据每场生产轨道板的数量,计划各场均配置57套台座和模板,每天生产57块轨道板,每场配置生产约85人,管理人员15人,共约100人。
轨道板钢筋采用加工台架统一加工;砼采用90m3拌合站统一拌合供应,砼罐车运送;钢模采用优质钢材定型加工模板,模板放置在预制工作基坑基础上,振动器直接安装在钢模底模上,生产时由底模附着式振动器进行振动密实,轨道板表面再用小型振动器进行面振;钢筋骨架安装、砼灌注、拆模等采用绗吊吊装;砼养生采用温控蒸汽养生,蒸汽养护棚罩采用简易可拆装式钢管架,外罩隔热篷布,每块轨道板设置一套养护设备;预制场设3台供气量2t/h蒸汽锅炉,蒸汽管道采用保温管线,铺设在热力管线地沟内;轨道板经蒸养达到移运条件后送后续工序作业台完成张拉等作业,然后移至存板区存放并继续养生;轨道板在存板区采用龙门吊桥吊移。
桥梁下部结构施工完成后的区段,对桥梁施工便道进行处理,作为轨道板临时存放场地,可减轻板场存板区的压力,又可为下一步轨道板的现场运送提前做好准备。
2.2轨道板预制场规划方案本标段每个轨道板预制场生产板量约为23945块,预制场规划如下,可根据现场实际作相应调整:轨道板预制场总面积约为72亩(300×160M),生产规模57块/天,最大存储量约为0.8万块。
预制场构成:根据施工工艺流程和施工工艺特点,将预制场分为既互相独立又沿道路互相联系的几大区域,分别为:骨料存放区;砼搅拌区;钢筋存放、加工及钢筋编架区;轨道板生产区;半成品及产品存放区;轨道板加工区;锅炉房;污水、垃圾处理区;配电室、发电室、试验室;办公与生活区。
京沪高铁轨道板场建场方案综述
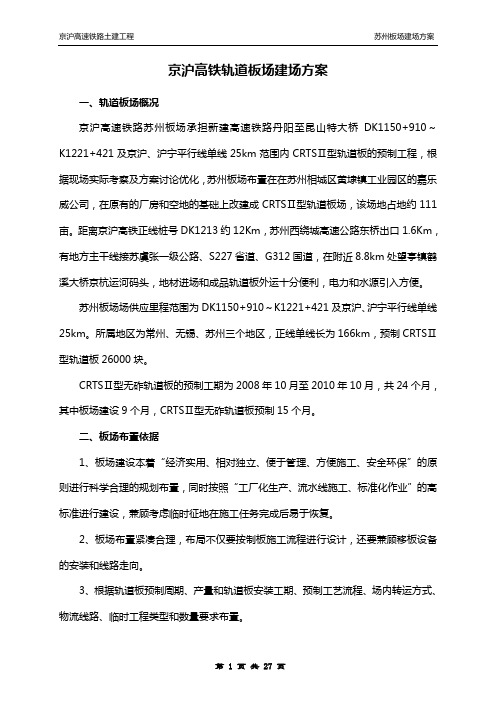
京沪高铁轨道板场建场方案一、轨道板场概况京沪高速铁路苏州板场承担新建高速铁路丹阳至昆山特大桥DK1150+910~K1221+421及京沪、沪宁平行线单线25km范围内CRTSⅡ型轨道板的预制工程,根据现场实际考察及方案讨论优化,苏州板场布置在在苏州相城区黄埭镇工业园区的嘉乐威公司,在原有的厂房和空地的基础上改建成CRTSⅡ型轨道板场,该场地占地约111亩。
距离京沪高铁正线桩号DK1213约12Km,苏州西绕城高速公路东桥出口1.6Km,有地方主干线接苏虞张一级公路、S227省道、G312国道,在附近8.8km处望亭镇鹤溪大桥京杭运河码头,地材进场和成品轨道板外运十分便利,电力和水源引入方便。
苏州板场场供应里程范围为DK1150+910~K1221+421及京沪、沪宁平行线单线25km。
所属地区为常州、无锡、苏州三个地区,正线单线长为166km,预制CRTSⅡ型轨道板26000块。
CRTSⅡ型无砟轨道板的预制工期为2008年10月至2010年10月,共24个月,其中板场建设9个月,CRTSⅡ型无砟轨道板预制15个月。
二、板场布置依据1、板场建设本着“经济实用、相对独立、便于管理、方便施工、安全环保”的原则进行科学合理的规划布置,同时按照“工厂化生产、流水线施工、标准化作业”的高标准进行建设,兼顾考虑临时征地在施工任务完成后易于恢复。
2、板场布置紧凑合理,布局不仅要按制板施工流程进行设计,还要兼顾移板设备的安装和线路走向。
3、根据轨道板预制周期、产量和轨道板安装工期、预制工艺流程、场内转运方式、物流线路、临时工程类型和数量要求布置。
三、板场的建设设计3.1生产能力的设计根据预制CRTSⅡ型轨道板26000块的总工程量,轨道板毛坯板正式生产工期按14个月计算,考虑其他不利因素,每月有效工作日24天,按每天一模计算:26000块÷(14月×24天/月)=77块,拟投入81套模板满足毛坯板生产需要。
- 1、下载文档前请自行甄别文档内容的完整性,平台不提供额外的编辑、内容补充、找答案等附加服务。
- 2、"仅部分预览"的文档,不可在线预览部分如存在完整性等问题,可反馈申请退款(可完整预览的文档不适用该条件!)。
- 3、如文档侵犯您的权益,请联系客服反馈,我们会尽快为您处理(人工客服工作时间:9:00-18:30)。
京沪高铁轨道板场建场方案一、轨道板场概况京沪高速铁路XX板场承担新建高速铁路丹阳至昆山特大桥DK1150+910~K1221+421及京沪、沪宁平行线单线25km范围内CRTSⅡ型轨道板的预制工程,根据现场实际考察及方案讨论优化,XX板场布臵在在XX相城区黄埭镇工业园区的嘉乐威公司,在原有的厂房和空地的基础上改建成CRTSⅡ型轨道板场,该场地占地约111亩。
距离京沪高铁正线桩号DK1213约12Km,XX西绕城高速公路东桥出口1.6Km,有地方主干线接苏虞张一级公路、S227省道、G312国道,在附近8.8km处望亭镇鹤溪大桥京杭运河码头,地材进场和成品轨道板外运十分便利,电力和水源引入方便。
XX板场场供应里程范围为DK1150+910~K1221+421及京沪、沪宁平行线单线25km。
所属地区为常州、无锡、XX三个地区,正线单线长为166km,预制CRTSⅡ型轨道板26000块。
CRTSⅡ型无砟轨道板的预制工期为2008年10月至2010年10月,共24个月,其中板场建设9个月,CRTSⅡ型无砟轨道板预制15个月。
二、板场布臵依据1、板场建设本着“经济实用、相对独立、便于管理、方便施工、安全环保”的原则进行科学合理的规划布臵,同时按照“工厂化生产、流水线施工、标准化作业”的高标准进行建设,兼顾考虑临时征地在施工任务完成后易于恢复。
2、板场布臵紧凑合理,布局不仅要按制板施工流程进行设计,还要兼顾移板设备的安装和线路走向。
3、根据轨道板预制周期、产量和轨道板安装工期、预制工艺流程、场内转运方式、物流线路、临时工程类型和数量要求布臵。
三、板场的建设设计3.1生产能力的设计根据预制CRTSⅡ型轨道板26000块的总工程量,轨道板毛坯板正式生产工期按14个月计算,考虑其他不利因素,每月有效工作日24天,按每天一模计算:26000块÷(14月×24天/月)=77块,拟投入81套模板满足毛坯板生产需要。
在场内投入CRTSⅡ型轨道板打磨机一套进行毛坯板打磨,其设计能力为24小时最大打磨成品板约80块,考虑不利因素,每月有效工作日24天,经计算:26000块÷80块÷24天/月=14月,完工工期为2010年10月31日,要求打磨机在2009年9月以前安装调试结束并正式投入生产,以满足毛坯板打磨需要。
3.2车间规模结构车间依据CRTSⅡ型板生产工艺流程、工序顺序和物流方便进行设计。
原建厂房为5跨宽18m、长78m的钢混结构厂房,车间面积为5跨×18m/跨×78m=7020m2,为充分发挥原厂房的作用并方便物流组织,项目部进行多方案对比,考虑钢筋原材进场、钢筋网片及混凝土入生产区、毛坯板及成品板的运输等物流组织,按厂房由北向南依次排序为1至5跨,将厂房最南侧第5跨用作钢筋加工车间,长 78米,宽18m,总面积为1404m2;将第4跨设为轨道板预制区,为满足预制生产线长条形结构要求,对原建厂房的立柱、基础进行加固,同时把第四跨车间进行延长,延长部分采用钢结构厂房,全长288米,宽18m,内设三条预制生产线;第三跨为毛坯板临时存放区,将毛坯板从轨道板生产车间运输到毛坯板临时存放区静放24h;第二跨为打磨装配厂房,长78米,宽18m;第一跨用作配件库、材料库等辅助生产区。
车间整体结构采用钢框架结构、钢筋混凝土独立柱结合连续地基梁式基础、牛腿钢柱、工字钢走行梁,钢构件间采用高强螺栓连接、彩钢板绝热墙面和顶棚。
厂房总建筑面积为10800平方米。
3.3预制生产线的结构布臵轨道板张拉台座生产线,按生产工艺要求,三个台座沿主厂房顺长方向一字串联布臵,每个张拉台座长度75米,台座间设设备清洗台宽 8.5 米,三个台座总长度共 242米,主厂房两端预留空间堆放钢铰线和配臵张拉设备。
台座结构为钢筋混凝土U型结构,基础顶预埋模具定位地脚螺栓,两边墙顶为施工设备走行轨道,台座两端设自锁式千斤顶及张拉横梁。
3.4与生产线有关的供热、供气系统全厂设热力交换机组一座,供毛坯板预制温度需要。
每个台座都设有供热管道,以保证冬季施工时模型加温和混凝土养护温度需要,夏季施工模具降温和混凝土散热降温需要。
全厂设空气压缩机一台,供台座内毛坯板脱模、临时存放台垂直定位杆及磨床打磨清洁使用。
每个台座都设有压缩空气管道,用于在毛坯板脱模时,在混凝土与模具间充气形成气垫作用,以利脱模。
3.5主要设备工装及物流顺序平面布臵CRTSⅡ型板制作工艺衔接紧密,较多地采用了机械化作业,实现了程序化、标准化作业,各工序间顺序清晰,施工方法、作业任务、工作接口明确。
同时适应工艺流程安排,各工序间物流作业也是互相衔接紧密,设臵了运输轨道,运输小车、电动车、滚轮线等运输设备互相联结,并通过桥式吊车、各种吊架、吊梁以及真空吸盘的配合作业和翻转机对毛坯板的翻转,形成场内完整的物流体系。
四、板场布臵说明按照CRTSⅡ型轨道板制造工艺特点将前期建设的板场改建成现代化制板场,整个板场占地面积111亩,根据生产需要,设臵轨道板生产区、轨道板存放区、拌和站及办公生活区等,各区域紧密连接,场内道路相通,方便运输,减少二次倒运及运输距离。
轨道板生产区从钢筋制作、钢绞线的张拉、灌注、养护、放张、脱模、转移等整体为流水线设计,方便施工;存板区区中毛坯板的移梁、成平板的存放等布局合理,满足施工要求;油库、配电室等危险区远离其它区域,减少安全事故隐患;办公、生产相互独立互不干扰;全板场与外界围墙相隔,安全独立,板场平面布臵图见轨道板场平面布臵图,板场各个区域占地面积见表4-1,板场平面布臵情况如下:表4-1 板场区域占地统计表板场轨道板生产区共占地10800m2,主要包括一条长288米的轨道板预制区、钢筋加工存放区、毛坯板临时存放区、轨道板打磨装配区等。
4.1.1轨道板预制区轨道板生产线主要设在第4跨主厂房内,总长288m,宽18m,采用先张长线台座法。
按生产工艺要求,沿厂房东西长方向一字串联布臵三条轨道板生产线,每条生产线安装27套模具,三个台座共安装81套模具,每个张拉台座长度75m,加上中间的冲洗区及两端设备存放区,台座总长度为242米,车间的剩余部分作为预应力钢丝下料及存放空间。
台座结构为钢筋混凝土结构,台座设计为中心距8400mm,设两排平行的承力墙,在两平行承力墙之间安装制板模型;台座两端设张拉横梁,承力墙与横梁之间安装三套自动张拉系统,实现预应力的同步张拉、放张。
台座顶面设有轨道,作为生产线主要非标设备的走行轨道。
轨道上布臵的主要设备有1台混凝土布料机、2台切割预应力钢筋的锯、1台多功能运输车、1台拉毛机。
台座北侧设1条4m宽的毛坯板运输通道,台座南侧设1条4m宽的钢筋运输通道;第三号台座东侧设臵1台定长裁筋机来实现预应力钢筋的下料。
主厂房内配臵3台16吨行车,跨度16.5米,其中:一台为双钩行车,主要用于吊运混凝土斗,另两台为单钩行车,主要用于钢筋网片入模、挡板安拆、脱模等作业。
蒸汽养护系统采用保温管线,铺设在轨道板模具下,并设蒸汽开关。
轨道板蒸汽养护采用整体养护方式,采用简易隔热篷布外罩养护。
浇注混凝土采用布料机均匀布料,可将混凝土定量投入模板,同时也保证了浇注的均匀性和底板面平整度及轨道板厚度的可控性。
采用模具下安装的附着式振捣器捣固的方法,混凝土浇筑前模板温度要在20-30摄氏度,混凝土入模温度在15-30摄氏度。
拌和好的混凝土,由拌合站卸入混凝土运输罐,拌合站出料口下设横移轨道,混凝土运输罐由卷扬机直接拉入轨道板生产车间,再由行车吊运至布料机,卸入布料斗内,在布料斗装够一块板的混凝土后,开启排料阀门,同时横向走行布料斗,将混凝土均匀倒入模具内。
随后进行混凝土振捣、刮平、拉毛、养护作业。
表4-2 轨道板预制台座占用时间表4.1.2 钢筋加工存放区按最多一天生产81块轨道板的进度计算,每天的钢筋加工量要达到40T,为了便于加快进度、合理布局,在厂房内设臵2个钢筋加工存放区,在靠近轨道板预制区南侧第5车间设1个,面积为1404 m2,设1台10t-16.5m和1台5t-16.5m的行车进行钢筋原材和钢筋网片的吊装;在第1车间设1个,面积为702 m2,设1台10t-16.5m的行车进行钢筋原材和钢筋网片的吊装。
根据京津城际房山和平谷板场的经验,在厂房内设臵12个钢筋编架台位,10个存放台位, 2套钢筋加工设备等。
钢筋加工区主要为钢筋网片制作、绝缘安装检测、钢筋网片存放等功能。
进场钢筋通过道路直接运送到厂房内,用行车装卸。
根据每天生产量,提前编制需要的钢筋网架数量,钢筋网架可以利用编架运输小车横向转运至轨道板生产线南侧的钢筋运输通道,人工推移编架运输小车通过运输通道到每条生产线,用行车吊至轨道板模板内。
4.1.3毛坯板临时存放区为满足毛坯板静放24h要求,用轨道板预制区北侧一跨宽18m、长78m的厂房做毛坯板临时存放区,设2台10t-16.5m行车进行吊装,毛坯板临时存放区布设5排毛坯板存放线,每排可存放8垛24块毛坯板,共可存放毛坯板40垛120块(存放布设可进行调整)。
脱模后的毛坯板放臵到生产线北侧的毛坯板运输通道上的临时存板台上,每垛三块,及时覆盖帆布养护,以保温或防止毛坯板因与环境温差太大而产生裂缝,脱模后的毛坯板采用电动运输车运至毛坯板临时存放区,运输车载重量为30吨,一次可以顶起3块毛坯板,沿生产线上的毛坯板运输通道运到生产线最西侧横移至毛坯板临时存放区,将毛坯板放在临时存放台上静放24h。
毛坯板存放24h后通过轨道小车直接运送至轨道板毛坯板存放区。
4.1.4轨道板打磨装配区轨道板打磨生产线是以数控磨床为中心自动化生产线,设在第2跨长度为78m的厂房内,打磨生产线除配臵一台数控磨床外,还配臵1台翻转机、1套滚轮运输线、1台吸水器、1台定量油脂注射机、1台起重量为16吨的行车。
自然养护28天的毛坯板,经过特制的翻转机翻转至滚轮线位臵,按滚轮托架线启动按钮,将轨道板运送至钢筋切割工位,切割完成后继续前行至打磨室进料口外,等待打磨作业。
数控机床根据打磨程序给出的打磨次数和打磨量,磨轮对轨道板进行打磨行程,直至符合质量标准。
每块轨道板打磨时间约15分钟;打磨时,污水处理、供水、供电、供气系统应保持正常运转。
打磨后的轨道板需雕刻编号、清洗出板,然后一直运往扣件安装工位,由轨道小车运输至轨道板成品区。
轨道板运至扣件安装工位后,首先利用吸尘器对布满水和杂质的螺栓孔进行清洁并吹干,再用注油机定量注入润滑油脂,人工插螺栓和摆放扣件,最后用气动扳手采用固定力矩拧紧每个螺栓。
装配完成后继续由滚轮线运输至横向运输位臵,用横移小车将轨道板运至成品板出场线存放台,用成品板运输电动车沿成品板出场线运输轨道板,经绝缘检测工位对成品板进行整体绝缘性能检测后,将其运至成品板存放区临时存放台,由龙门吊将其一一吊至计划的存放位臵。